
Wir sind Hersteller von Pulverbeschichtungsanlage für Kleinteile für unsere Kunden in Deutschland, Österreich und Schweiz. Höhe Qualitet, Niedriger Preis und kostenlose Beratung
Für die Pulverbeschichtung von Kleinteilen gibt es spezielle Anlagen, die für eine hohe Produktivität und Effizienz ausgelegt sind. Diese Anlagen sind in der Regel automatisiert und können große Stückzahlen von Kleinteilen in kurzer Zeit verarbeiten.
Eine solche Anlage besteht in der Regel aus einer Vorbehandlungsanlage, die die zu beschichtenden Kleinteile reinigt und vorbereitet, einer automatisierten Bepuderungsstation, die das Pulver auf die Teile aufträgt, und einem Ofen, in dem das Pulver eingebrannt wird.
Die automatisierte Bepuderungsstation kann je nach Anforderung verschiedene Technologien wie beispielsweise die Corona- oder Tribo-Bepuderungstechnologie verwenden. Zusätzlich können verschiedene Pulversieb- und -rückgewinnungssysteme integriert sein, um den Pulvereinsatz zu minimieren und die Produktivität zu maximieren.
Die Pulverbeschichtungsanlage für Kleinteile kann entweder als Einzelanlage oder als Teil einer größeren Fertigungslinie eingesetzt werden. In jedem Fall ist eine solche Anlage eine zuverlässige und effiziente Lösung für die Beschichtung von Kleinteilen in verschiedenen Branchen und Anwendungen, von der Elektronik- und Automobilindustrie bis hin zur Herstellung von Haushaltsgeräten und Möbeln.
Pulverbeschichtungsanlage für Kleinteile
Eine Pulverbeschichtungsanlage für Kleinteile besteht in der Regel aus einem speziellen Förderband, das die Teile automatisch durch die verschiedenen Prozessschritte transportiert. Das Förderband kann in unterschiedlichen Geschwindigkeiten laufen, je nach Anforderungen an die Prozesszeiten und Beschichtungsdicke.
In der Vorbehandlungszone werden die Kleinteile gereinigt und chemisch behandelt, um die Haftung des Pulvers zu verbessern und die Haltbarkeit der Beschichtung zu erhöhen. Dazu können verschiedene Verfahren wie Entfetten, Beizen oder Phosphatieren eingesetzt werden.
Anschließend gelangen die Kleinteile in die Pulverkabine, wo sie elektrostatisch aufgeladen werden und das Pulver aufgetragen wird. Die Kabine kann dabei speziell für Kleinteile konzipiert sein und beispielsweise über eine Vorrichtung zum Fixieren der Teile verfügen.
Nach der Bepuderung durchläuft das Förderband den Einbrennofen, in dem das Pulver geschmolzen und die Beschichtung auf die Kleinteile aufgebracht wird. Hierbei sind unterschiedliche Temperaturen und Einbrennbedingungen je nach Art des Pulvers und der Kleinteile erforderlich.
Schließlich gelangen die beschichteten Kleinteile in die Kühlzone, in der sie abkühlen und aushärten können. Je nach Anforderungen an die Beschichtung kann auch hier eine spezielle Kühltechnologie zum Einsatz kommen.
Die Anlage kann dabei manuell oder automatisch gesteuert werden und kann für unterschiedliche Produktionsmengen und -größen konzipiert sein.
Pulverbeschichtungsanlage für Kleinteile
Pulverbeschichtungsanlagen für Kleinteile sind eine spezielle Art von Pulverbeschichtungsanlagen, die für die Beschichtung von kleinen Teilen entwickelt wurden. Sie zeichnen sich durch eine Reihe von Merkmalen aus, die sie für diese Anwendung geeignet machen, darunter:
- Kleine Kammergröße: Pulverbeschichtungsanlagen für Kleinteile haben eine kleinere Kammergröße als herkömmliche Pulverbeschichtungsanlagen. Dies ermöglicht es, kleine Teile in der Kammer zu beschichten, ohne dass sie aneinanderstoßen oder blockiert werden.
- Automatisierte Beladung und Entladung: Pulverbeschichtungsanlagen für Kleinteile sind häufig mit automatischen Beladungs- und Entladesystemen ausgestattet. Dies erleichtert die Be- und Entladung von Teilen und erhöht die Effizienz der Beschichtung.
- Spezielle Beschichtungssysteme: Pulverbeschichtungsanlagen für Kleinteile können mit speziellen Beschichtungssystemen ausgestattet sein, die die Beschichtung von kleinen Teilen erleichtern. Dazu gehören beispielsweise Systeme zur Beschichtung von Teilen mit komplexen Formen oder zur Beschichtung von Teilen, die nicht in die Kammer passen.
Pulverbeschichtungsanlagen für Kleinteile werden in einer Vielzahl von Branchen eingesetzt, darunter:
- Automobilindustrie: Pulverbeschichtungsanlagen für Kleinteile werden in der Automobilindustrie zur Beschichtung von Autoteilen wie Türgriffen, Stoßstangen und Scheinwerfern eingesetzt.
- Elektronikindustrie: Pulverbeschichtungsanlagen für Kleinteile werden in der Elektronikindustrie zur Beschichtung von elektronischen Geräten wie Computern, Mobiltelefonen und Fernsehern eingesetzt.
- Medizintechnikindustrie: Pulverbeschichtungsanlagen für Kleinteile werden in der Medizintechnikindustrie zur Beschichtung von medizinischen Geräten wie Implantaten und Beatmungsgeräten eingesetzt.
- Flugzeugindustrie: Pulverbeschichtungsanlagen für Kleinteile werden in der Flugzeugindustrie zur Beschichtung von Flugzeugteilen wie Triebwerkskomponenten und Fahrwerksteilen eingesetzt.
Pulverbeschichtungsanlagen für Kleinteile bieten eine Reihe von Vorteilen gegenüber anderen Beschichtungsverfahren, darunter:
- Hohe Beschichtungsqualität: Pulverbeschichtungen bieten eine hohe Beschichtungsqualität mit einer gleichmäßigen Beschichtungsdicke und einer guten Haftung.
- Lange Lebensdauer: Pulverbeschichtungen sind sehr langlebig und bieten einen guten Schutz vor Korrosion und anderen Umwelteinflüssen.
- Umweltfreundlichkeit: Pulverbeschichtungen sind umweltfreundlich, da sie keine Lösungsmittel oder andere chemische Substanzen erfordern.
Pulverbeschichtungsanlagen für Kleinteile sind eine effektive Möglichkeit, kleine Teile zu beschichten. Sie bieten eine hohe Beschichtungsqualität, eine lange Lebensdauer und sind umweltfreundlich.
Pulveranlage für Felgen
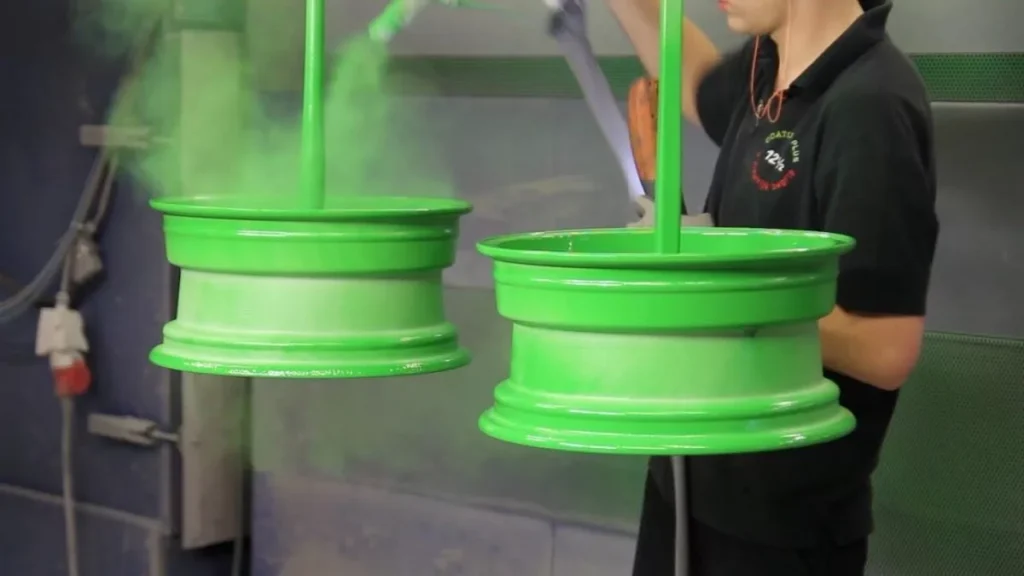
Eine Pulveranlage für Felgen ist eine spezielle Art von Pulverbeschichtungsanlage, die für die Beschichtung von Felgen entwickelt wurde. Sie zeichnet sich durch eine Reihe von Merkmalen aus, die sie für diese Anwendung geeignet machen, darunter:
- Große Kammergröße: Pulveranlagen für Felgen haben eine große Kammergröße, um genügend Platz für die Aufnahme von Felgen aller Größen zu bieten.
- Automatisierte Beladung und Entladung: Pulveranlagen für Felgen sind häufig mit automatischen Beladungs- und Entladesystemen ausgestattet. Dies erleichtert die Be- und Entladung von Felgen und erhöht die Effizienz der Beschichtung.
- Spezielle Beschichtungssysteme: Pulveranlagen für Felgen können mit speziellen Beschichtungssystemen ausgestattet sein, die die Beschichtung von Felgen erleichtern. Dazu gehören beispielsweise Systeme zur Beschichtung von Felgen mit komplexen Formen oder zur Beschichtung von Felgen, die nicht in die Kammer passen.
Pulveranlagen für Felgen werden in einer Vielzahl von Werkstätten und Betrieben eingesetzt, um Felgen aller Art zu beschichten, einschließlich:
- Autowerkstätten: Pulveranlagen für Felgen werden in Autowerkstätten eingesetzt, um Felgen für Autos und andere Fahrzeuge zu beschichten.
- Motorradwerkstätten: Pulveranlagen für Felgen werden in Motorradwerkstätten eingesetzt, um Felgen für Motorräder zu beschichten.
- LKW-Werkstätten: Pulveranlagen für Felgen werden in LKW-Werkstätten eingesetzt, um Felgen für Lastwagen zu beschichten.
- Fahrzeughersteller: Pulveranlagen für Felgen werden von Fahrzeugherstellern eingesetzt, um Felgen für neue Fahrzeuge zu beschichten.
Pulveranlagen für Felgen bieten eine Reihe von Vorteilen gegenüber anderen Beschichtungsverfahren, darunter:
- Hohe Beschichtungsqualität: Pulverbeschichtungen bieten eine hohe Beschichtungsqualität mit einer gleichmäßigen Beschichtungsdicke und einer guten Haftung.
- Lange Lebensdauer: Pulverbeschichtungen sind sehr langlebig und bieten einen guten Schutz vor Korrosion und anderen Umwelteinflüssen.
- Umweltfreundlichkeit: Pulverbeschichtungen sind umweltfreundlich, da sie keine Lösungsmittel oder andere chemische Substanzen erfordern.
Pulveranlagen für Felgen sind eine effektive Möglichkeit, Felgen zu beschichten. Sie bieten eine hohe Beschichtungsqualität, eine lange Lebensdauer und sind umweltfreundlich.
Einbrennofen Einzelheiten
Ein Einbrennofen ist ein spezieller Ofen, der für den Aushärteprozess von Pulverbeschichtungen verwendet wird. Dieser Prozess wird auch als Einbrennen oder Aushärten bezeichnet und ist entscheidend, um eine dauerhafte und qualitativ hochwertige Beschichtung auf Werkstücken zu gewährleisten. Hier sind einige Einzelheiten und Merkmale eines typischen Einbrennofens:
- Erhitzungssystem:
- Einbrennöfen verwenden leistungsstarke Heizsysteme, die oft auf elektrischer oder gasbetriebener Basis arbeiten.
- Elektrische Heizelemente oder Gasbrenner erzeugen die erforderliche Wärme für das Schmelzen und Aushärten des Pulvers.
- Isolierung:
- Die Isolierung des Ofens ist entscheidend, um Wärmeverluste zu minimieren und eine gleichmäßige Temperaturverteilung zu gewährleisten.
- Gut isolierte Öfen verbessern die Energieeffizienz und fördern eine gleichmäßige Aushärtung.
- Temperatursteuerung:
- Ein präzises Temperatursteuersystem regelt die Ofentemperatur während des Aushärteprozesses.
- Moderne Einbrennöfen können digitale Steuerungen und Sensoren verwenden, um genaue Temperaturprofile zu gewährleisten.
- Förderanlagen:
- Einbrennöfen verfügen über Förderbänder oder Hängesysteme, um die beschichteten Werkstücke durch den Ofen zu befördern.
- Die Geschwindigkeit der Förderanlage beeinflusst die Verweilzeit der Werkstücke im Ofen und somit den Aushärteprozess.
- Kühlbereich:
- Nach dem Aushärten können die Werkstücke durch einen Kühlbereich geführt werden, um auf sichere Temperaturen abzukühlen.
- Dieser Bereich verbessert die Qualität der Beschichtung und stellt sicher, dass die Werkstücke sicher behandelt werden können.
- Luftzirkulationssystem:
- Ein effizientes Luftzirkulationssystem sorgt für eine gleichmäßige Verteilung der erwärmten Luft im Ofen.
- Eine gute Luftzirkulation minimiert Hotspots und gewährleistet eine konsistente Aushärtung.
- Sicherheitsvorkehrungen:
- Einbrennöfen sollten mit Not-Aus-Schaltern und anderen Sicherheitsvorkehrungen ausgestattet sein, um einen sicheren Betrieb zu gewährleisten.
- Die Ofenkonstruktion sollte den geltenden Sicherheitsstandards entsprechen.
- Abgas- und Filteranlagen:
- Einbrennöfen sollten Abgasanlagen haben, um Verbrennungsgase sicher abzuführen.
- Filteranlagen können dazu beitragen, Pulverreste zu erfassen und für die Wiederverwendung zu recyceln.
- Automatisierungsoptionen:
- Moderne Einbrennöfen können mit automatisierten Steuerungssystemen integriert sein, die den gesamten Aushärteprozess überwachen und steuern.
- Automatisierungsoptionen können auch eine Datenverarbeitung und -überwachung für Effizienz und Qualität umfassen.
Ein Einbrennofen ist ein entscheidender Bestandteil des Pulverbeschichtungsprozesses und trägt dazu bei, eine haltbare und qualitativ hochwertige Oberflächenbeschichtung auf Werkstücken zu erzielen.
Ofengröße
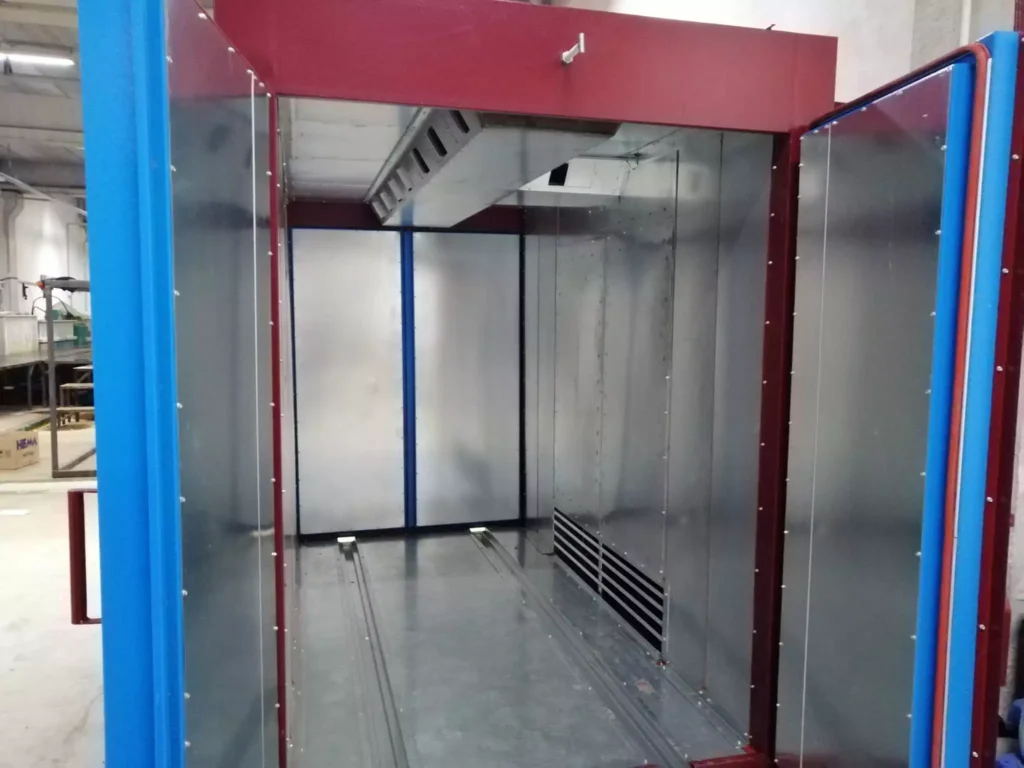
Die Größe eines Ofens wird in der Regel durch das Volumen des Ofenraums angegeben. Das Volumen wird berechnet, indem die Länge, Breite und Höhe des Ofenraums multipliziert werden.
Die richtige Ofengröße hängt von den zu backenden Produkten ab. Kleinere Öfen sind in der Regel für kleinere Produkte geeignet, während größere Öfen für größere Produkte geeignet sind.
Faustregel für die Ofengröße
Eine Faustregel für die Ofengröße besagt, dass die Innenfläche des Ofenraums mindestens doppelt so groß sein sollte wie die Oberfläche des größten zu backenden Produkts.
Beispiel
Wenn Sie einen Kuchen mit einem Durchmesser von 20 cm backen möchten, benötigen Sie einen Ofen mit einem Innenraum von mindestens 400 cm².
Andere Faktoren, die die Ofengröße beeinflussen
Neben der Größe der zu backenden Produkte können auch andere Faktoren die Ofengröße beeinflussen, darunter:
- Die Anzahl der gleichzeitig zu backenden Produkte: Wenn Sie mehrere Produkte gleichzeitig backen möchten, benötigen Sie einen größeren Ofen.
- Die Art des Backens: Einige Backvorgänge erfordern einen größeren Ofen als andere.
- Der Platzbedarf: Sie müssen sicherstellen, dass der Ofen in den vorgesehenen Bereich passt.
Wie man den richtigen Ofen für Ihre Bedürfnisse findet
Wenn Sie einen neuen Ofen kaufen, sollten Sie die Größe des Ofens sorgfältig berücksichtigen. Messen Sie den verfügbaren Platz und überlegen Sie, welche Produkte Sie backen möchten.
Ratschläge für die Auswahl der richtigen Ofengröße
- Wenn Sie nur kleine Produkte backen möchten, benötigen Sie einen kleinen Ofen.
- Wenn Sie große Produkte backen möchten, benötigen Sie einen großen Ofen.
- Wenn Sie mehrere Produkte gleichzeitig backen möchten, benötigen Sie einen größeren Ofen.
- Wenn Sie bestimmte Backvorgänge durchführen möchten, benötigen Sie möglicherweise einen Ofen mit einer bestimmten Größe.
- Überlegen Sie, wie viel Platz Sie für den Ofen haben.
Weitere Informationen zur Ofengröße
Weitere Informationen zur Ofengröße finden Sie in den Produktbeschreibungen von Ofenherstellern. Sie können sich auch von einem Küchenplaner beraten lassen.
Temperaturbereich
Der Temperaturbereich ist der Bereich von Temperaturen, in dem ein Gerät arbeiten kann. Er wird in der Regel in Grad Celsius (°C) oder Grad Fahrenheit (°F) angegeben.
Der Temperaturbereich eines Ofens ist wichtig, da er bestimmt, welche Lebensmittel darin gebacken werden können. Ofen haben in der Regel einen Temperaturbereich von 50 °C bis 250 °C oder 122 °F bis 482 °F.
Arten von Temperaturbereichen
Es gibt zwei Hauptarten von Temperaturbereichen:
- Kontinuierlicher Temperaturbereich: Ein kontinuierlicher Temperaturbereich bedeutet, dass der Ofen jede beliebige Temperatur innerhalb des Bereichs einstellen kann.
- Diskreter Temperaturbereich: Ein diskreter Temperaturbereich bedeutet, dass der Ofen nur bestimmte Temperaturen innerhalb des Bereichs einstellen kann.
Temperaturbereich von Öfen
Die meisten Öfen haben einen kontinuierlichen Temperaturbereich von 50 °C bis 250 °C oder 122 °F bis 482 °F. Einige Öfen haben einen diskreten Temperaturbereich, der nur bestimmte Temperaturen innerhalb dieses Bereichs umfasst.
Temperaturbereich von anderen Geräten
Der Temperaturbereich anderer Geräte kann je nach Art des Geräts variieren. Zum Beispiel haben Kühlschränke einen Temperaturbereich von 0 °C bis 10 °C oder 32 °F bis 50 °F, während Klimaanlagen einen Temperaturbereich von 16 °C bis 32 °C oder 61 °F bis 90 °F haben.
Wie man den richtigen Temperaturbereich für ein Gerät auswählt
Wenn Sie ein neues Gerät kaufen, sollten Sie den Temperaturbereich sorgfältig berücksichtigen. Stellen Sie sicher, dass der Temperaturbereich für die Verwendung des Geräts geeignet ist.
Ratschläge für die Auswahl des richtigen Temperaturbereichs
- Überlegen Sie, welche Produkte Sie mit dem Gerät verarbeiten möchten.
- Lesen Sie die Produktbeschreibung des Geräts, um den Temperaturbereich zu ermitteln.
- Fragen Sie einen Verkäufer oder einen Techniker nach Rat, wenn Sie sich nicht sicher sind, welcher Temperaturbereich für Sie geeignet ist.
Steuerung
Steuerung ist ein Prozess, bei dem eine Eingabe in eine gewünschte Ausgabe umgewandelt wird. In der Technik wird Steuerung häufig verwendet, um Maschinen oder Geräte zu steuern.
Arten von Steuerungen
Es gibt viele verschiedene Arten von Steuerungen, die für verschiedene Zwecke verwendet werden können. Einige der gebräuchlichsten Arten von Steuerungen sind:
- Analoge Steuerungen: Analoge Steuerungen arbeiten mit kontinuierlichen Signalen, die eine Vielzahl von Werten annehmen können.
- Digitale Steuerungen: Digitale Steuerungen arbeiten mit diskreten Signalen, die nur bestimmte Werte annehmen können.
- Automatische Steuerungen: Automatische Steuerungen arbeiten ohne menschliches Eingreifen.
- Manuelle Steuerungen: Manuelle Steuerungen erfordern menschliches Eingreifen.
Bestandteile einer Steuerung
Eine Steuerung besteht in der Regel aus den folgenden Komponenten:
- Eingabe: Die Eingabe ist die Information, die die Steuerung verarbeitet.
- Verarbeitung: Die Verarbeitung ist der Prozess, bei dem die Eingabe in eine Ausgabe umgewandelt wird.
- Ausgabe: Die Ausgabe ist die Information, die die Steuerung erzeugt.
Beispiele für Steuerungen
Beispiele für Steuerungen sind:
- Die Steuerung eines Autos: Die Steuerung eines Autos verwendet Sensoren, um die Umgebung des Autos zu erfassen. Diese Informationen werden dann von einem Computer verarbeitet, der das Gaspedal, die Bremse und das Lenkrad steuert.
- Die Steuerung eines Ofens: Die Steuerung eines Ofens verwendet einen Temperatursensor, um die Temperatur im Inneren des Ofens zu erfassen. Diese Informationen werden dann von einem Computer verarbeitet, der die Heizelemente des Ofens steuert, um die gewünschte Temperatur zu erreichen.
- Die Steuerung eines Roboters: Die Steuerung eines Roboters verwendet Sensoren, um die Umgebung des Roboters zu erfassen. Diese Informationen werden dann von einem Computer verarbeitet, der die Bewegungen des Roboters steuert.
Vorteile von Steuerungen
Steuerungen bieten eine Reihe von Vorteilen, darunter:
- Effizienz: Steuerungen können dazu beitragen, die Effizienz von Maschinen oder Geräten zu verbessern.
- Sicherheit: Steuerungen können dazu beitragen, die Sicherheit von Maschinen oder Geräten zu verbessern.
- Komfort: Steuerungen können den Komfort der Bedienung von Maschinen oder Geräten verbessern.
Nachteile von Steuerungen
Steuerungen haben auch einige Nachteile, darunter:
- Kosten: Steuerungen können teuer sein.
- Komplexität: Steuerungen können komplex sein.
- Fehleranfälligkeit: Steuerungen können fehleranfällig sein.
Sicherheit von Steuerungen
Steuerungen müssen so sicher sein, dass sie das Risiko von Verletzungen oder Schäden minimieren. Zu den Sicherheitsmaßnahmen, die bei der Steuerung von Maschinen oder Geräten getroffen werden können, gehören:
- Fehlererkennung und -korrektur: Steuerungen sollten in der Lage sein, Fehler zu erkennen und zu korrigieren, um Verletzungen oder Schäden zu verhindern.
- Not-Aus-Systeme: Steuerungen sollten Not-Aus-Systeme haben, die die Maschine oder das Gerät im Notfall sofort stoppen können.
- Sicherheitsvorkehrungen: Steuerungen sollten Sicherheitsvorkehrungen haben, um den Zugang zu gefährlichen Bereichen zu verhindern.
Fazit
Steuerung ist ein wichtiger Prozess, der in vielen Bereichen der Technik verwendet wird. Steuerungen können dazu beitragen, Maschinen oder Geräte effizienter, sicherer und komfortabler zu machen.
Heizelemente

Elektrische Heizelemente sind ein wichtiger Bestandteil von Pulverbeschichtungsanlagen. Sie werden verwendet, um die Pulverbeschichtung bei einer hohen Temperatur auszuhärten.
Arten von elektrischen Heizelementen in Pulveröfen:
In Pulveröfen werden in der Regel folgende Arten von elektrischen Heizelementen verwendet:
- Heizpatronen: Heizpatronen sind die gebräuchlichste Art von elektrischem Heizelement in Pulveröfen. Sie bestehen aus einem spiralförmigen Draht, der in einem keramischen Rohr eingebettet ist. Heizpatronen sind in der Regel sehr effizient und können eine hohe Temperatur erzeugen.
- Heizkabel: Heizkabel sind eine flexible Art von elektrischem Heizelement. Sie bestehen aus einem Draht, der mit einem Isoliermaterial umgeben ist. Heizkabel sind in der Regel kostengünstiger als Heizpatronen, aber auch weniger effizient.
Funktionsweise von elektrischen Heizelementen in Pulveröfen:
Elektrische Heizelemente in Pulveröfen werden mit Strom versorgt, wodurch sie sich erwärmen. Die Wärme wird dann an das Pulver übertragen, das dadurch aushärtet.
Sicherheit von elektrischen Heizelementen in Pulveröfen:
Elektrische Heizelemente in Pulveröfen können ein Brandrisiko darstellen, wenn sie nicht ordnungsgemäß installiert und verwendet werden. Daher ist es wichtig, die Sicherheitsvorkehrungen zu beachten, die vom Hersteller des Pulverofens angegeben werden.
Wartung von elektrischen Heizelementen in Pulveröfen:
Elektrische Heizelemente in Pulveröfen sollten regelmäßig auf Beschädigungen und Verschleiß überprüft werden. Beschädigte oder verschlissene Heizelemente sollten ersetzt werden, um die Sicherheit zu gewährleisten.
Fazit:
Elektrische Heizelemente sind ein wichtiger Bestandteil von Pulverbeschichtungsanlagen. Sie werden verwendet, um die Pulverbeschichtung bei einer hohen Temperatur auszuhärten.
Lüftungssystem
Ein Lüftungssystem ist ein System, das Luft aus einem Raum abführt und durch frische Luft ersetzt. Lüftungssysteme werden verwendet, um die Luftqualität in Innenräumen zu verbessern und die Gesundheit und das Wohlbefinden der Menschen zu schützen.
Arten von Lüftungssystemen
Es gibt viele verschiedene Arten von Lüftungssystemen, die für verschiedene Zwecke verwendet werden können. Einige der gebräuchlichsten Arten von Lüftungssystemen sind:
- Natürliche Lüftung: Natürliche Lüftung erfolgt durch die Bewegung von Luft durch natürliche Kräfte wie Wind und Temperaturunterschiede.
- Mechanische Lüftung: Mechanische Lüftung erfolgt durch die Verwendung von Ventilatoren oder Pumpen, um Luft zu bewegen.
- Umluftbelüftung: Umluftbelüftung ist ein System, bei dem die Luft in einen Raum eingeführt und dann wieder abgesaugt wird, nachdem sie durch einen Wärmetauscher geleitet wurde, um die Wärme zurückzugewinnen.
Funktionsweise eines Lüftungssystems
Die Funktionsweise eines Lüftungssystems hängt von der Art des Systems ab. Bei natürlichen Lüftungssystemen wird die Luft durch natürliche Kräfte wie Wind und Temperaturunterschiede bewegt. Bei mechanischen Lüftungssystemen wird Luft durch Ventilatoren oder Pumpen bewegt.
Vorteile von Lüftungssystemen
Lüftungssysteme bieten eine Reihe von Vorteilen, darunter:
- Verbesserung der Luftqualität: Lüftungssysteme können dazu beitragen, die Luftqualität in Innenräumen zu verbessern, indem sie verbrauchte Luft abführen und frische Luft einbringen.
- Schutz der Gesundheit: Lüftungssysteme können dazu beitragen, die Gesundheit und das Wohlbefinden der Menschen zu schützen, indem sie Schadstoffe und Allergene aus der Luft entfernen.
- Verbesserung des Komforts: Lüftungssysteme können dazu beitragen, den Komfort in Innenräumen zu verbessern, indem sie die Temperatur und die Luftfeuchtigkeit regulieren.
Nachteile von Lüftungssystemen
Lüftungssysteme haben auch einige Nachteile, darunter:
- Kosten: Lüftungssysteme können teuer sein, sowohl in der Anschaffung als auch im Betrieb.
- Energiebedarf: Lüftungssysteme können einen erheblichen Energiebedarf haben.
- Wartung: Lüftungssysteme müssen regelmäßig gewartet werden, um eine ordnungsgemäße Funktion zu gewährleisten.
Sicherheit von Lüftungssystemen
Lüftungssysteme müssen so sicher sein, dass sie das Risiko von Verletzungen oder Schäden minimieren. Zu den Sicherheitsmaßnahmen, die bei der Installation und Wartung von Lüftungssystemen getroffen werden können, gehören:
- Fehlererkennung und -korrektur: Lüftungssysteme sollten in der Lage sein, Fehler zu erkennen und zu korrigieren, um Verletzungen oder Schäden zu verhindern.
- Not-Aus-Systeme: Lüftungssysteme sollten Not-Aus-Systeme haben, die das System im Notfall sofort stoppen können.
- Sicherheitsvorkehrungen: Lüftungssysteme sollten Sicherheitsvorkehrungen haben, um den Zugang zu gefährlichen Bereichen zu verhindern.
Fazit
Lüftungssysteme sind ein wichtiger Bestandteil einer gesunden und komfortablen Innenraumluftqualität. Durch die Auswahl des richtigen Lüftungssystems für Ihre Bedürfnisse können Sie die Luftqualität in Ihrem Zuhause oder Büro verbessern und Ihre Gesundheit und Ihr Wohlbefinden schützen.
Isolierung
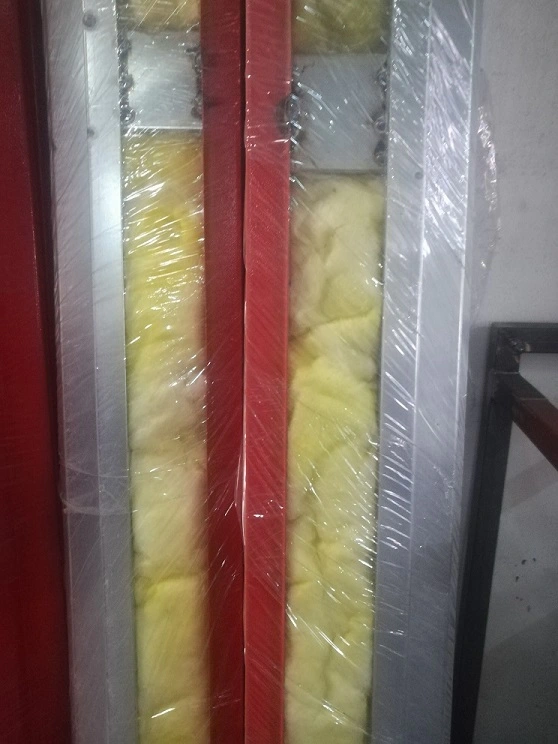
Die Isolierung eines Einbrennofens ist wichtig, um die Energiekosten zu senken und die Sicherheit zu gewährleisten. Die Isolierung verhindert, dass Wärme aus dem Ofen entweicht, wodurch der Ofen weniger Energie benötigt, um die gewünschte Temperatur zu erreichen. Außerdem kann die Isolierung dazu beitragen, dass der Ofen nicht zu heiß wird und sich dadurch keine Brandgefahr ergibt.
Arten von Isolation für Einbrennöfen
Es gibt verschiedene Arten von Isolation, die für Einbrennöfen verwendet werden können. Die gebräuchlichsten Arten sind:
- Mineralwolle: Mineralwolle ist ein faseriges Material, das aus Stein, Glas oder Basalt hergestellt wird. Mineralwolle ist ein guter Wärme- und Schallisolator.
- Polystyrol: Polystyrol ist ein Kunststoff, der aus kleinen, geschlossenen Zellen besteht. Polystyrol ist ein guter Wärmeisolator.
- Dämmwolle: Dämmwolle ist ein faseriges Material, das aus natürlichen oder synthetischen Materialien hergestellt wird. Dämmwolle ist ein guter Wärme- und Schallisolator.
Isolierung eines Einbrennofens
Die Isolierung eines Einbrennofens sollte fachgerecht durchgeführt werden, um die gewünschten Ergebnisse zu erzielen. Die folgenden Schritte sind zu beachten:
- Entfernen Sie die alte Isolierung, falls vorhanden.
- Reinigen Sie die Oberfläche des Ofens gründlich.
- Bringen Sie die neue Isolierung an.
- Verschließen Sie alle Lücken oder Risse.
Sicherheitshinweise
Bei der Isolierung eines Einbrennofens sind folgende Sicherheitshinweise zu beachten:
- Tragen Sie immer geeignete Schutzkleidung, z. B. Schutzbrille, Handschuhe und Atemschutzmaske.
- Achten Sie darauf, dass der Ofen ausgeschaltet und abgekühlt ist, bevor Sie mit der Isolierung beginnen.
- Verwenden Sie nur Isoliermaterial, das für den Einsatz in Einbrennöfen geeignet ist.
Fazit
Die Isolierung eines Einbrennofens ist eine wichtige Maßnahme, um die Energiekosten zu senken und die Sicherheit zu gewährleisten. Durch die fachgerechte Durchführung der Isolierung können Sie die gewünschten Ergebnisse erzielen und den Ofen über viele Jahre hinweg nutzen.
Transport
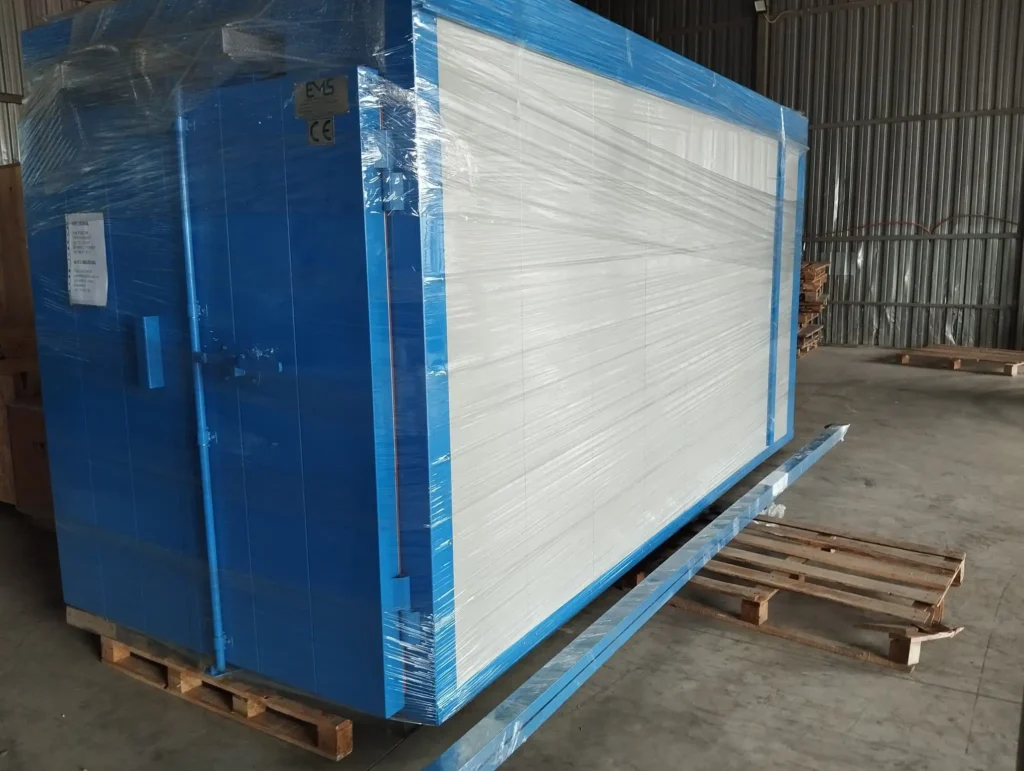
Der Transport eines Einbrennofens ist eine Aufgabe, die mit Vorsicht und Sorgfalt durchgeführt werden sollte. Der Ofen ist ein schweres und sperriges Gerät, das leicht beschädigt werden kann, wenn er nicht richtig transportiert wird.
Vorbereitung
Bevor Sie mit dem Transport des Ofens beginnen, sollten Sie folgende Vorbereitungen treffen:
- Stellen Sie sicher, dass der Ofen vollständig abgekühlt ist.
- Entfernen Sie alle losen Teile, wie z. B. die Türen und die Schubladen.
- Sichern Sie alle beweglichen Teile, wie z. B. die Heizelemente.
- Besorgen Sie sich geeignetes Transportmaterial, wie z. B. eine Palette und Spanngurte.
Transport
Der Ofen sollte auf einer stabilen Palette transportiert werden. Verwenden Sie Spanngurte, um den Ofen auf der Palette zu sichern. Achten Sie darauf, dass die Spanngurte fest genug angezogen sind, um den Ofen zu sichern, aber nicht so fest, dass sie ihn beschädigen.
Wenn der Ofen auf der Palette befestigt ist, können Sie ihn zum Transportfahrzeug fahren. Achten Sie darauf, dass der Ofen beim Transport nicht herunterfällt oder umkippt.
Lieferung
Bei der Lieferung des Ofens sollten Sie folgende Schritte beachten:
- Stellen Sie sicher, dass der Lieferant den Ofen sicher anliefert.
- Überprüfen Sie den Ofen nach der Lieferung auf Schäden.
Sicherheitshinweise
Beim Transport eines Einbrennofens sollten Sie folgende Sicherheitshinweise beachten:
- Tragen Sie immer geeignete Schutzkleidung, wie z. B. Handschuhe und Schutzbrille.
- Achten Sie darauf, dass der Ofen nicht herunterfällt oder umkippt.
- Vermeiden Sie, dass der Ofen in Kontakt mit Wasser oder anderen Flüssigkeiten kommt.
Fazit
Der Transport eines Einbrennofens ist eine Aufgabe, die mit Vorsicht und Sorgfalt durchgeführt werden sollte. Durch die Einhaltung der oben genannten Schritte können Sie den Ofen sicher und unbeschädigt transportieren.
Zusätzliche Tipps
Wenn der Ofen über eine lange Strecke transportiert werden muss, sollten Sie ihn in einem geschlossenen Fahrzeug transportieren, um ihn vor Witterungseinflüssen zu schützen.
Wenn der Ofen in einem Gebäude transportiert werden muss, sollten Sie die Türen und Gänge überprüfen, um sicherzustellen, dass der Ofen durchpasst.
Wenn Sie den Ofen selbst transportieren, sollten Sie sich von einem Freund oder Verwandten helfen lassen.
Sicherheitsfunktionen
Einbrennöfen sind große und komplexe Geräte, die bei unsachgemäßer Verwendung zu Verletzungen oder Schäden führen können. Aus diesem Grund sind Einbrennöfen mit einer Reihe von Sicherheitsfunktionen ausgestattet, um die Sicherheit der Benutzer zu gewährleisten.
Die wichtigsten Sicherheitsfunktionen eines Einbrennofens sind:
- Temperaturregler: Der Temperaturregler ermöglicht es dem Benutzer, die Temperatur des Ofens genau zu steuern. Dies ist wichtig, um zu verhindern, dass das Material im Ofen überhitzt und beschädigt wird.
- Thermostat: Das Thermostat schaltet den Ofen automatisch ab, wenn die eingestellte Temperatur erreicht ist. Dies verhindert, dass das Material im Ofen zu lange erhitzt wird und beschädigt wird.
- Überhitzungsschutz: Der Überhitzungsschutz schaltet den Ofen automatisch ab, wenn die Temperatur im Ofen zu hoch wird. Dies kann durch einen Stromausfall oder einen anderen Fehler verursacht werden.
- Sicherheitsthermostat: Der Sicherheitsthermostat schaltet den Ofen automatisch ab, wenn die Temperatur im Ofen zu hoch wird. Dies kann durch einen Brand oder einen anderen Notfall verursacht werden.
- Sicherheitstür: Die Sicherheitstür verhindert, dass der Benutzer den Ofen während des Betriebs öffnet. Dies ist wichtig, um Verbrennungen zu vermeiden.
- Sicherheitsschalter: Der Sicherheitsschalter schaltet den Ofen automatisch ab, wenn die Tür geöffnet wird. Dies ist wichtig, um zu verhindern, dass der Ofen eingeschaltet bleibt, wenn die Tür geöffnet ist.
Zusätzliche Sicherheitsfunktionen:
- Feuerlöscher: Ein Feuerlöscher sollte in der Nähe des Ofens aufbewahrt werden, um im Brandfall schnell reagieren zu können.
- Not-Aus-Schalter: Der Not-Aus-Schalter schaltet den Ofen sofort ab. Er sollte in greifbarer Nähe des Ofens angebracht sein.
- Warnhinweise: Der Ofen sollte mit Warnhinweisen versehen sein, die den Benutzer vor Gefahren warnen.
Sicherheitshinweise:
- Lesen Sie die Bedienungsanleitung des Ofens sorgfältig durch, bevor Sie ihn verwenden.
- Befolgen Sie die Sicherheitshinweise, die in der Bedienungsanleitung angegeben sind.
- Lassen Sie den Ofen niemals unbeaufsichtigt.
- Verwenden Sie den Ofen nur für den vorgesehenen Zweck.
- Reinigen Sie den Ofen regelmäßig, um Brandgefahr zu vermeiden.
Durch die Einhaltung der oben genannten Sicherheitshinweise können Sie die Sicherheit beim Umgang mit Einbrennöfen gewährleisten.
Hier ist ein längerer Text ohne Abschnitt über eine Pulverbeschichtungsanlage für Kleinteile:
Die Pulverbeschichtung ist ein Verfahren, das zur Herstellung von robusten, langlebigen Oberflächen auf verschiedenen Metall- und Kunststoffmaterialien eingesetzt wird. Im Gegensatz zu herkömmlichen Lackierverfahren, bei denen flüssige Farben verwendet werden, kommt bei der Pulverbeschichtung trockenes Pulver zum Einsatz, das auf die Oberfläche des Werkstücks aufgebracht wird. Das Pulver besteht meist aus Epoxidharzen, Polyesterharzen oder einer Mischung aus beiden, die mit verschiedenen Farbstoffen und Additiven kombiniert sind, um unterschiedliche Oberflächen und Eigenschaften zu erzielen.
Das Verfahren beginnt mit der Vorbereitung der Oberfläche des Werkstücks, das durch Reinigung, Entfettung und gegebenenfalls Schleifen auf die Beschichtung vorbereitet wird. Hierdurch wird eine optimale Haftung des Pulvers gewährleistet. In der Regel erfolgt die Reinigung durch chemische Bäder oder durch Sandstrahlen. Danach wird das Pulver mittels eines elektrostatischen Verfahrens auf das Werkstück aufgetragen. Das Werkstück wird dabei mit einer negativen Ladung versehen, während das Pulver positiv geladen ist, was zu einer starken Anziehung führt.
Nach dem Auftragen des Pulvers wird das Werkstück in einem Ofen erhitzt, wodurch das Pulver schmilzt und eine gleichmäßige, dauerhafte Schicht bildet. Die Temperatur und Dauer des Backvorgangs hängen vom verwendeten Pulver und der Art des Werkstücks ab, liegen jedoch normalerweise im Bereich von 160 bis 200 Grad Celsius und können zwischen 10 und 30 Minuten variieren.
Die Pulverbeschichtung bietet zahlreiche Vorteile, darunter eine hohe Beständigkeit gegenüber mechanischen und chemischen Belastungen sowie eine ausgezeichnete Korrosionsbeständigkeit. Sie ist umweltfreundlicher als herkömmliche Lackierverfahren, da keine Lösungsmittel verwendet werden und keine schädlichen Dämpfe entstehen. Zudem entstehen durch den Einsatz von Pulvern keine giftigen Abfallprodukte, was die Pulverbeschichtung zu einer nachhaltigeren Wahl für industrielle Anwendungen macht.
Ein weiterer Vorteil der Pulverbeschichtung ist die Vielseitigkeit hinsichtlich der Oberflächenstruktur. Sie kann nicht nur als matte, glänzende oder satinierte Oberfläche ausgeführt werden, sondern auch mit besonderen Effekten wie Metalloptiken oder Texturen versehen werden. Darüber hinaus ist die Pulverbeschichtung in einer breiten Palette von Farben und Oberflächenfinishs erhältlich, was eine hohe Gestaltungsfreiheit ermöglicht.
Für die Anwendung auf großen Serien von Bauteilen, die eine gleichbleibende Qualität und hohe Effizienz erfordern, bieten moderne Pulverbeschichtungsanlagen fortschrittliche Technologien zur Automatisierung und Optimierung des Prozesses. Dabei kommen oft Roboter zum Einsatz, die das Pulver gleichmäßig auftragen und für eine konstante Schichtdicke sorgen. Besonders in der Automobil- und Möbelindustrie, aber auch in der Maschinenbau- und Elektroindustrie wird dieses Verfahren geschätzt.

Die Pulverbeschichtung hat sich als äußerst kosteneffizient erwiesen, insbesondere für die Serienproduktion, da sie geringe Materialverluste aufweist und die Wiederverwendbarkeit des überschüssigen Pulvers ermöglicht. Das Pulver, das beim Beschichten eines Werkstücks nicht haftet, kann durch spezielle Systeme wieder aufgefangen und erneut verwendet werden. Dies trägt nicht nur zur Reduzierung der Betriebskosten bei, sondern auch zur Minimierung von Abfall und Ressourcenverbrauch.
Ein weiterer Aspekt der Pulverbeschichtung ist ihre Fähigkeit, unterschiedliche Materialien zu beschichten. Obwohl sie hauptsächlich für Metalle verwendet wird, ist sie auch auf einigen Kunststoffen und anderen Substraten anwendbar, die vorher entsprechend behandelt wurden. Dies erweitert das Anwendungsspektrum und ermöglicht den Einsatz der Technologie in verschiedenen Industriezweigen.
Zudem ist die Pulverbeschichtung aufgrund ihrer hohen mechanischen Festigkeit und Widerstandsfähigkeit gegen Kratzer und Abrieb besonders für Produkte geeignet, die hohen Beanspruchungen ausgesetzt sind. Die resultierende Schicht schützt nicht nur vor physischen Schäden, sondern auch vor UV-Strahlung und Witterungseinflüssen, wodurch das Produkt auch im Außeneinsatz eine längere Lebensdauer hat. Dies macht sie besonders attraktiv für die Beschichtung von Bauteilen in der Automobilindustrie, im Maschinenbau sowie für Außenmöbel und Fassaden.
Die Flexibilität in der Farbwahl und Oberflächenstruktur von Pulverbeschichtungen trägt ebenfalls dazu bei, dass sie häufig in der Architektur und im Design verwendet wird. Ob es sich um dekorative Elemente oder funktionale Bauteile handelt, die Pulverbeschichtung ermöglicht es, sowohl ästhetische als auch praktische Anforderungen zu erfüllen.
Ein wichtiger Trend in der Pulverbeschichtungstechnologie ist die Weiterentwicklung von Verfahren, die eine noch höhere Energieeffizienz und bessere Umweltverträglichkeit bieten. Durch den Einsatz innovativer Technologien, wie z. B. Niedertemperatur-Pulver, können die Anforderungen an die Temperaturprofile in den Ofenprozessen gesenkt werden, was zu geringeren Energieverbrauch und kürzeren Durchlaufzeiten führt. Auch die Entwicklung von Pulvern auf Basis erneuerbarer Rohstoffe oder mit verbesserten recyclingfähigen Eigenschaften ist ein vielversprechender Ansatz, der das Potenzial hat, die Umweltfreundlichkeit des gesamten Beschichtungsprozesses weiter zu steigern.
Insgesamt zeigt sich, dass die Pulverbeschichtung eine äußerst vielseitige, effiziente und nachhaltige Lösung für die Oberflächenbehandlung von Bauteilen darstellt. Sie verbindet hohe technologische Anforderungen mit ökologischen und wirtschaftlichen Vorteilen und bleibt ein zentraler Bestandteil moderner Fertigungsprozesse in vielen Branchen.
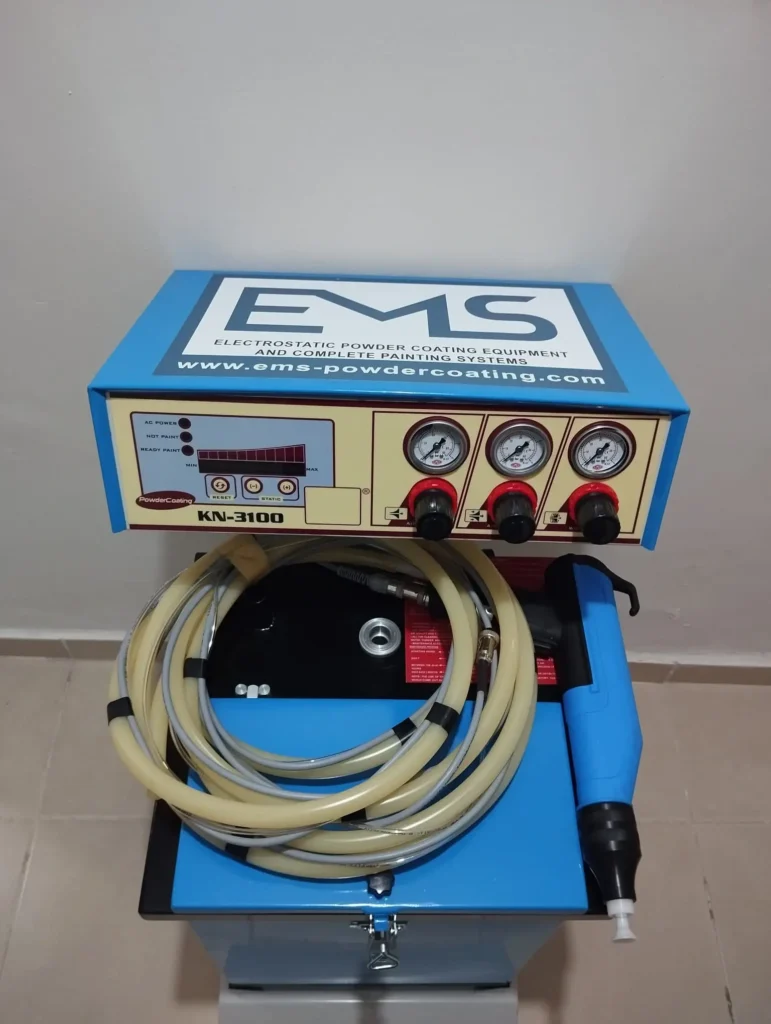
Ein weiterer bedeutender Vorteil der Pulverbeschichtung ist ihre ausgezeichnete Beständigkeit gegenüber Korrosion, die vor allem in Umgebungen von Vorteil ist, in denen Bauteile starkem Feuchtigkeits- oder Witterungseinfluss ausgesetzt sind. Diese Eigenschaft macht die Pulverbeschichtung besonders attraktiv für Anwendungen im Außenbereich, wie etwa bei der Herstellung von Zäunen, Geländern, Fensterrahmen und Außenmöbeln. Durch die stabile Schutzschicht wird die Lebensdauer solcher Produkte erheblich verlängert, wodurch sowohl die Wartungskosten als auch die Notwendigkeit eines häufigen Austauschs gesenkt werden.
Die Korrosionsbeständigkeit der Pulverbeschichtung wird durch die Art des verwendeten Pulvers bestimmt. Epoxidharz-basierte Pulverlacke bieten besonders guten Schutz in Innenräumen und bei Produkten, die keiner intensiven UV-Bestrahlung ausgesetzt sind. Polyester-basierte Pulver hingegen sind aufgrund ihrer UV-Beständigkeit und besseren Farbbeständigkeit besonders für Außeneinsätze geeignet, da sie länger farbintensiv bleiben und weniger anfällig für Verblassen sind.
Im Vergleich zu anderen Oberflächenbehandlungen wie Galvanisieren oder Verzinken bietet die Pulverbeschichtung eine gleichmäßigere, dickere und widerstandsfähigere Schicht ohne die Notwendigkeit von gefährlichen Chemikalien oder aufwendigen Nachbehandlungsprozessen. Diese einfache Handhabung und die Flexibilität im Designprozess machen sie zu einer bevorzugten Wahl für viele Fertigungsbetriebe. Die Schichtdicke kann präzise eingestellt werden, was zu einer gleichmäßigen Abdeckung führt, die besonders in der Automobilindustrie oder bei technischen Geräten von großer Bedeutung ist, wo eine hohe Oberflächenqualität erforderlich ist.
Neben den bereits genannten Vorteilen hat die Pulverbeschichtung auch in der Automatisierungstechnik ihren Platz gefunden. Durch den Einsatz von Robotern und automatisierten Sprühanlagen können Produktionsprozesse optimiert und personalintensive Arbeitsschritte reduziert werden. Diese Technologie bietet eine hohe Wiederholgenauigkeit und ermöglicht es, große Stückzahlen in kurzer Zeit zu beschichten. Bei der Verwendung von High-Tech-Anlagen können sogar komplexe Bauteile, die schwer zugängliche Stellen aufweisen, effizient und gleichmäßig beschichtet werden.
Auch in der Lebensmittel- und Pharmaindustrie hat die Pulverbeschichtung an Bedeutung gewonnen, insbesondere bei der Beschichtung von Geräten, die in hygienischen Bereichen eingesetzt werden. Durch die Verwendung von speziellen, für den Lebensmittelkontakt zugelassenen Pulvern und die Möglichkeit, die Oberflächen so zu gestalten, dass sie leicht zu reinigen sind, trägt die Pulverbeschichtung dazu bei, die Hygieneanforderungen in diesen Industrien zu erfüllen.
Ein zunehmend wichtigerer Aspekt in der Pulverbeschichtung ist die Nachhaltigkeit. Die Industrie entwickelt kontinuierlich neue Pulversysteme, die weniger schädliche Auswirkungen auf die Umwelt haben, wie zum Beispiel Pulverbeschichtungen ohne VOCs (flüchtige organische Verbindungen) oder solche, die auf nachwachsenden Rohstoffen basieren. Diese nachhaltigen Alternativen verringern die Umweltauswirkungen der Produktion und helfen den Herstellern, ihre ökologischen Fußabdrücke zu reduzieren, ohne auf die Leistungsfähigkeit der Beschichtungen zu verzichten.
In der Zukunft dürfte die Pulverbeschichtungstechnologie weiter an Bedeutung gewinnen, da die Industrie verstärkt auf umweltfreundliche, effiziente und langlebige Lösungen setzt. Insbesondere in Bezug auf die Anpassung an moderne Fertigungsanforderungen und die Integration von innovativen Technologien wird die Pulverbeschichtung eine zentrale Rolle spielen, um sowohl den ökologischen als auch den wirtschaftlichen Herausforderungen der Industrie gerecht zu werden.
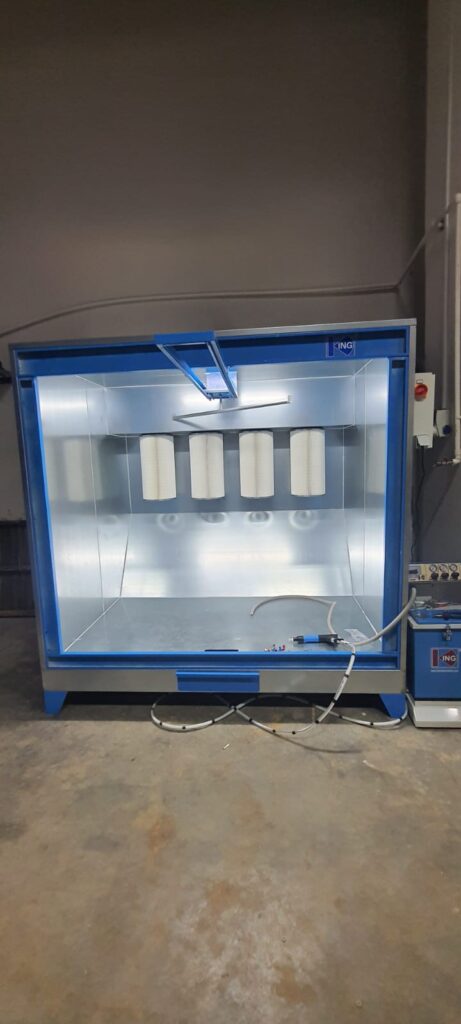
Die Zukunft der Pulverbeschichtungstechnologie wird auch durch den zunehmenden Einsatz von Digitalisierung und Smart Manufacturing beeinflusst. Durch die Integration von IoT (Internet of Things) und Echtzeit-Überwachungssystemen können Unternehmen die Effizienz des gesamten Beschichtungsprozesses erheblich verbessern. Sensoren und Datenanalysen ermöglichen eine präzise Kontrolle der Prozessparameter wie Temperatur, Luftfeuchtigkeit und Pulvermenge, wodurch die Qualität der Beschichtung noch weiter optimiert und Fehlerquellen minimiert werden können.
Die Vernetzung von Maschinen und Anlagen in einem smarten Produktionsumfeld erleichtert es außerdem, den Zustand der Ausrüstung zu überwachen und Wartungsbedarf frühzeitig zu erkennen, was unvorhergesehene Ausfallzeiten reduziert und die Lebensdauer der Anlagen verlängert. Ein weiterer Vorteil der Digitalisierung ist die Möglichkeit, die Produktionsdaten zu analysieren und daraus Muster und Optimierungspotentiale abzuleiten. So können Hersteller kontinuierlich ihre Prozesse verbessern und die Produktionskosten weiter senken.
Im Bereich der Forschung und Entwicklung wird ebenfalls intensiv an neuen Pulversystemen und Technologien gearbeitet. Hierbei geht es nicht nur um die Verbesserung der mechanischen und chemischen Eigenschaften von Pulverbeschichtungen, sondern auch um die Weiterentwicklung von Pulvern, die in der Lage sind, besondere Anforderungen zu erfüllen, wie etwa eine höhere Widerstandsfähigkeit gegenüber extremen Temperaturen oder aggressiven Chemikalien. Auch die Entwicklung von Pulvern mit besonderen funktionalen Eigenschaften, etwa antibakteriellen oder selbstheilenden Eigenschaften, gewinnt zunehmend an Bedeutung. Diese Innovationen eröffnen neue Anwendungsmöglichkeiten und erweitern das Spektrum der Pulverbeschichtung für eine noch größere Vielfalt an Industrien.
Ein weiterer wachsender Trend ist die Verlagerung hin zu noch nachhaltigeren Lösungen. Neben der Nutzung umweltfreundlicher Pulversysteme werden auch alternative Verfahren zur Energieoptimierung in den Fokus genommen. Beispielsweise können energieeffiziente Öfen und fortschrittliche Heiztechnologien helfen, den Energieverbrauch während des Beschichtungsprozesses zu senken. Darüber hinaus werden auch Systeme zur Rückgewinnung und Wiederverwertung von Pulvern und anderen Materialien weiterentwickelt, um die Kreislaufwirtschaft zu fördern und den Ressourcenverbrauch zu minimieren.
Die fortschreitende Entwicklung von Pulverbeschichtungstechnologien eröffnet auch neue Märkte und Anwendungsbereiche. Beispielsweise finden sich zunehmend Anwendungen in der Elektronikindustrie, insbesondere bei der Herstellung von Gehäusen für elektronische Geräte. In diesem Sektor sind Beschichtungen gefragt, die nicht nur ästhetische Anforderungen erfüllen, sondern auch funktionale Eigenschaften wie Antistatik, Wärmeableitung oder elektrische Isolierung bieten.
Zusammenfassend lässt sich sagen, dass die Pulverbeschichtung auch in Zukunft eine Schlüsseltechnologie für die Oberflächenbehandlung von Bauteilen und Produkten bleiben wird. Durch die kontinuierliche Weiterentwicklung der Verfahren, die Einführung neuer Pulvertypen und die Integration moderner Technologien wird sie sich an die immer komplexeren Anforderungen der Industrie und des Marktes anpassen. In einer zunehmend umweltbewussten und digitalisierten Welt wird die Pulverbeschichtungstechnologie weiterhin eine wichtige Rolle bei der Herstellung von langlebigen, funktionalen und ästhetisch ansprechenden Produkten spielen.
Die zunehmende Vernetzung von Produktionssystemen wird auch den Bereich der Pulverbeschichtung nachhaltig beeinflussen. In modernen Fertigungsanlagen ermöglichen intelligente Steuerungssysteme eine präzisere Überwachung und Steuerung des gesamten Beschichtungsprozesses. Dies führt zu einer deutlichen Reduzierung von Fehlerquellen und ermöglicht eine höhere Reproduzierbarkeit der Beschichtungsqualität. Die automatische Anpassung der Parameter in Echtzeit auf Basis von Sensordaten sorgt dafür, dass das Pulver gleichmäßig aufgebracht wird und die gewünschte Schichtdicke und Oberflächenstruktur erreicht wird. Dieser Grad an Automatisierung verbessert nicht nur die Effizienz, sondern auch die Wirtschaftlichkeit des Prozesses, indem Material- und Energieverluste verringert werden.
Ein weiterer bedeutender Schritt in der Weiterentwicklung der Pulverbeschichtungstechnologie ist die Forschung an Pulvern, die noch spezifischere Anforderungen erfüllen. So werden derzeit Pulverbeschichtungen entwickelt, die nicht nur robust und korrosionsbeständig sind, sondern auch besondere funktionale Eigenschaften bieten. Beispielsweise gibt es Bestrebungen, Pulverbeschichtungen mit selbstheilenden Eigenschaften zu entwickeln. Diese Schichten könnten kleine Kratzer oder Beschädigungen automatisch reparieren, was insbesondere in hochbeanspruchten Bereichen wie der Automobilindustrie oder bei Baukomponenten von Vorteil wäre. Ebenso wird an antimikrobiellen Pulverbeschichtungen geforscht, die vor allem in medizinischen und lebensmittelverarbeitenden Bereichen Anwendung finden könnten, um die Hygiene zu verbessern.
Die steigende Nachfrage nach nachhaltigen Lösungen hat dazu geführt, dass die Pulverbeschichtungsindustrie vermehrt auf die Verwendung von umweltfreundlicheren Pulvern und energieeffizienteren Prozessen setzt. Moderne Pulversysteme sind nicht nur frei von Lösungsmitteln und flüchtigen organischen Verbindungen (VOCs), sondern auch so formuliert, dass sie auf niedrigeren Temperaturen gebacken werden können. Dies trägt nicht nur zur Reduzierung des Energieverbrauchs bei, sondern auch zu einer verringerten CO₂-Emission. Darüber hinaus wird in der Industrie immer mehr Wert auf die Recyclingfähigkeit der verwendeten Materialien gelegt. Pulver, die beim Beschichtungsprozess nicht verwendet werden, können effizient zurückgewonnen und erneut genutzt werden, was die Ressourcennutzung optimiert und Abfall reduziert.
Mit der zunehmenden Globalisierung und den damit verbundenen Anforderungen an die Produktionsgeschwindigkeit und Flexibilität werden auch in der Pulverbeschichtungstechnologie zunehmend modulare und skalierbare Anlagen entwickelt. Diese ermöglichen es Unternehmen, sich schnell an veränderte Marktnachfragen oder spezifische Kundenanforderungen anzupassen. Durch die Integration von flexiblen Fördersystemen, anpassbaren Sprühkabinen und effizienteren Ofensystemen können Hersteller ihre Produktionslinien rasch umkonfigurieren, um unterschiedliche Produkte zu beschichten. Diese Flexibilität ist besonders wichtig in Märkten, in denen kürzere Produktlebenszyklen und hohe Innovationsraten vorherrschen.
Die Anwendung von Pulverbeschichtungen in der Elektrotechnik und Elektronikindustrie wächst stetig. Hier sind nicht nur ästhetische und schützende Eigenschaften gefragt, sondern auch funktionelle Merkmale wie Wärmeableitung oder elektromagnetische Abschirmung. Pulverbeschichtungen bieten eine hervorragende Möglichkeit, Elektronikgehäuse vor äußeren Einflüssen zu schützen und gleichzeitig die Wärmeabführung zu verbessern, was zur Vermeidung von Überhitzung und damit zu einer längeren Lebensdauer der Geräte beiträgt. In der Zukunft könnten Pulverbeschichtungen noch gezielter auf die spezifischen Anforderungen der Elektronikindustrie abgestimmt werden, zum Beispiel durch die Entwicklung von Pulvern, die die leitfähigen oder isolierenden Eigenschaften anpassen.
Zusammengefasst lässt sich sagen, dass die Pulverbeschichtungstechnologie kontinuierlich voranschreitet und zunehmend als Schlüsseltechnologie in einer Vielzahl von Industrien eingesetzt wird. Durch die fortlaufende Forschung und Entwicklung in den Bereichen Materialwissenschaft, Automatisierung und Nachhaltigkeit bleibt die Pulverbeschichtung ein wesentlicher Bestandteil moderner Fertigungsprozesse. Die kontinuierliche Verbesserung der Prozesskontrolle, die Entwicklung neuer funktionaler Pulversysteme und die Integration innovativer Technologien tragen dazu bei, dass die Pulverbeschichtung in Zukunft noch vielseitiger, effizienter und umweltfreundlicher wird.
Pulverbeschichtung

Pulverbeschichtung ist ein Verfahren zur Oberflächenbehandlung von Werkstücken, bei dem ein trockenes Pulver auf die zu beschichtende Oberfläche aufgebracht und anschließend erhitzt wird, um eine dauerhafte, schützende und dekorative Schicht zu bilden. Im Gegensatz zu herkömmlichen Lackierverfahren, bei denen flüssige Farben verwendet werden, wird bei der Pulverbeschichtung ein fein gemahlenes Pulver eingesetzt, das ohne Lösungsmittel oder flüssige Komponenten auskommt.
Die Hauptvorteile der Pulverbeschichtung sind:
- Langlebigkeit: Die resultierende Schicht ist äußerst widerstandsfähig gegenüber Kratzern, Korrosion und anderen mechanischen Belastungen.
- Umweltfreundlichkeit: Das Verfahren verwendet keine Lösungsmittel, was die Freisetzung von flüchtigen organischen Verbindungen (VOCs) vermeidet und die Umweltbelastung reduziert.
- Effizienz: Überschüssiges Pulver kann gesammelt und wiederverwendet werden, was zu geringen Materialverlusten führt.
- Vielseitigkeit: Pulverbeschichtungen können auf eine breite Palette von Materialien angewendet werden, insbesondere auf Metalle, aber auch auf Kunststoffe.
Der Prozess umfasst mehrere Schritte:
- Vorbereitung der Oberfläche: Reinigung und Entfettung der Werkstücke, oft durch Sandstrahlen oder chemische Bäder.
- Pulverauftrag: Das Pulver wird elektrostatisch auf die Werkstückoberfläche aufgetragen, indem das Werkstück eine negative Ladung erhält und das Pulver positiv geladen wird, was zu einer starken Anziehung führt.
- Erhitzung und Aushärtung: Das beschichtete Werkstück wird in einem Ofen erhitzt, sodass das Pulver schmilzt und eine gleichmäßige, stabile Schicht bildet.
Pulverbeschichtung findet breite Anwendung in der Automobilindustrie, Möbelproduktion, Maschinenbau, Architektur und vielen anderen Bereichen, da sie nicht nur schützend wirkt, sondern auch ästhetische Gestaltungsmöglichkeiten bietet.
Die Pulverbeschichtung hat sich aufgrund ihrer Vielzahl an Vorteilen, wie der hohen Beständigkeit gegenüber Witterungseinflüssen und der langen Haltbarkeit, als bevorzugte Lösung für viele Industrien etabliert. Insbesondere in der Außenanwendung, wie bei Fensterrahmen, Zäunen und anderen baulichen Elementen, sorgt sie für einen langanhaltenden Schutz gegen Korrosion und UV-Strahlung. Auch in der Automobilindustrie wird sie für eine Vielzahl von Bauteilen eingesetzt, um sowohl Schutz als auch ein ansprechendes Finish zu gewährleisten.
Ein weiterer wichtiger Vorteil der Pulverbeschichtung ist ihre Kosteneffizienz. Durch die Wiederverwendbarkeit des überschüssigen Pulvers werden Materialkosten gesenkt, und die hohe Materialnutzung reduziert Abfall. Dies führt nicht nur zu Einsparungen für den Hersteller, sondern unterstützt auch die Nachhaltigkeit des gesamten Prozesses. Die Tatsache, dass keine flüchtigen organischen Verbindungen (VOCs) freigesetzt werden, trägt zudem zur Reduzierung der Luftverschmutzung und der Belastung für die Umwelt bei, was das Verfahren umweltfreundlicher macht als traditionelle Lackierungen.
Das breite Spektrum an verfügbaren Pulvern ermöglicht eine große Auswahl an Oberflächenfinishs, von glänzend bis matt, von strukturiert bis glatt. Diese Vielseitigkeit in der Gestaltung ist ein weiterer Grund, warum Pulverbeschichtung in der Möbel- und Architekturindustrie so populär ist. Die Möglichkeit, individuelle Farbtöne und Oberflächenstrukturen zu erzeugen, erlaubt es, kreative und funktionale Designs zu realisieren, die sowohl ästhetische Anforderungen als auch technische Eigenschaften erfüllen.
Technologische Innovationen und Fortschritte im Bereich der Pulverbeschichtung zielen darauf ab, den Prozess noch effizienter und umweltfreundlicher zu gestalten. Neue Pulverarten, die auf erneuerbaren Ressourcen basieren oder besonders widerstandsfähig gegenüber extremen Bedingungen sind, eröffnen neue Anwendungsfelder und bieten noch bessere Schutzfunktionen. Zudem werden die Heizprozesse in modernen Ofenanlagen kontinuierlich optimiert, um den Energieverbrauch zu senken, was sowohl der Umwelt zugutekommt als auch die Betriebskosten reduziert.
Insgesamt bleibt die Pulverbeschichtung ein zentraler Bestandteil moderner Fertigungsprozesse, da sie eine perfekte Kombination aus Funktionalität, Ästhetik und Nachhaltigkeit bietet. Angesichts der fortschreitenden Entwicklung von Technologien und Materialien wird erwartet, dass ihre Anwendungsmöglichkeiten weiter zunehmen und neue Industrien von ihren Vorteilen profitieren werden.
Automatisierung
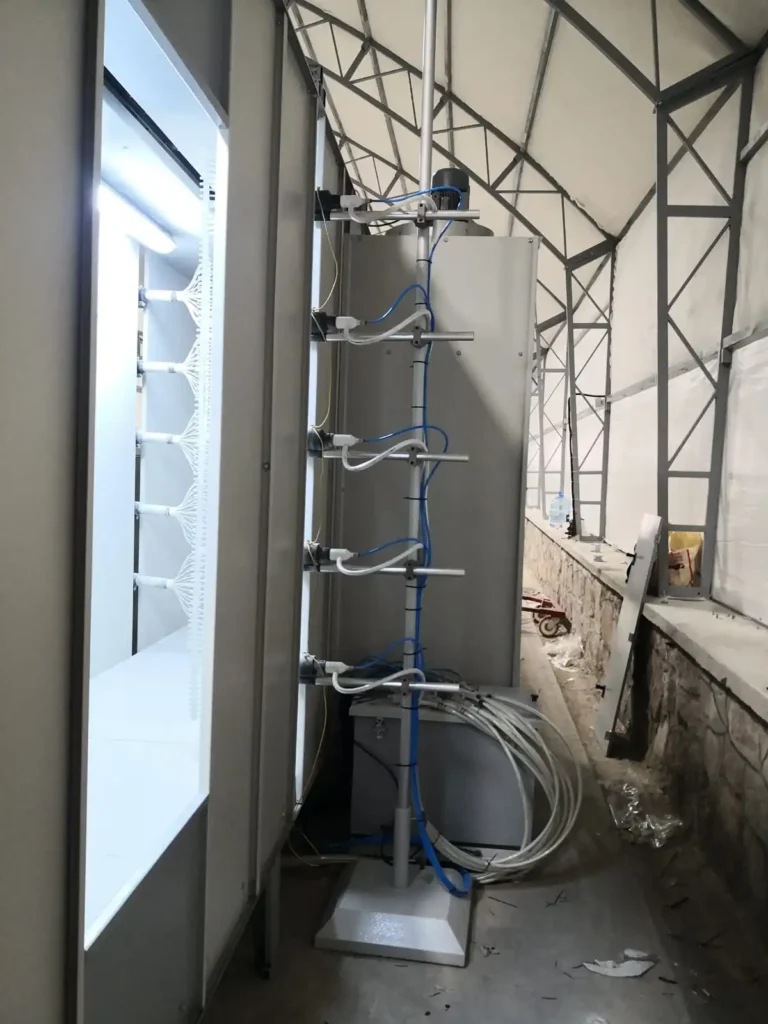
Automatisierung bezeichnet den Einsatz von Technologien, Systemen und Prozessen, die Aufgaben ohne oder mit minimaler menschlicher Intervention ausführen. Ziel ist es, Effizienz, Präzision und Produktivität zu steigern und dabei Kosten zu senken sowie Fehlerquellen zu minimieren. Automatisierung spielt eine zentrale Rolle in zahlreichen Branchen, von der Fertigungsindustrie über die Logistik bis hin zur Informations- und Kommunikationstechnologie.
In der Fertigung ermöglicht die Automatisierung durch den Einsatz von Robotern, Sensoren und Steuerungssystemen eine hochpräzise Produktion. Insbesondere in der Serienfertigung tragen automatisierte Prozesse dazu bei, gleichbleibende Qualität zu gewährleisten und die Durchlaufzeiten erheblich zu verkürzen. Moderne Systeme integrieren oft maschinelles Lernen und künstliche Intelligenz, um sich dynamisch an Veränderungen anzupassen, was die Flexibilität der Produktionslinien erhöht.
Ein wesentlicher Vorteil der Automatisierung ist die Steigerung der Sicherheit am Arbeitsplatz. Durch den Einsatz von Robotern und automatisierten Maschinen können gefährliche oder körperlich anstrengende Tätigkeiten von Maschinen übernommen werden, wodurch die Risiken für Arbeitsunfälle reduziert werden. Gleichzeitig können Mitarbeiter sich auf anspruchsvollere Aufgaben konzentrieren, wie die Überwachung und Wartung der Systeme.
Im Bereich der Logistik und des Transports ermöglicht Automatisierung eine effiziente Verwaltung von Lagerbeständen, optimierte Lieferketten und den Einsatz autonomer Fahrzeuge. Lagerroboter, wie sie in modernen Distributionszentren eingesetzt werden, können Bestellungen schnell und präzise zusammenstellen und so die Bearbeitungszeit verkürzen. In der Transportbranche kommen selbstfahrende Fahrzeuge und Drohnen immer häufiger zum Einsatz, um Lieferungen schneller und kostengünstiger zu gestalten.
Durch die Digitalisierung und Vernetzung von Maschinen und Systemen im Rahmen von Industrie 4.0 wird Automatisierung noch umfassender und intelligenter. Daten aus Produktionsprozessen werden in Echtzeit gesammelt, analysiert und genutzt, um Abläufe zu optimieren, Wartungsbedarf vorherzusagen und Ressourcen effizienter einzusetzen. Dies führt nicht nur zu einer Reduzierung der Betriebskosten, sondern trägt auch dazu bei, die Nachhaltigkeit der Produktionsprozesse zu verbessern.
Die Bedeutung der Automatisierung wird in den kommenden Jahren weiter zunehmen, da Unternehmen zunehmend auf smarte, datengetriebene Lösungen setzen. Während die Effizienzvorteile unbestritten sind, stellt die Integration dieser Technologien auch Herausforderungen dar, insbesondere in Bezug auf die Anpassung der Arbeitskräfte an neue Anforderungen und die Sicherstellung von Datensicherheit und Systemstabilität. Dennoch bleibt Automatisierung ein entscheidender Treiber für Innovation und Wettbewerbsfähigkeit in der modernen Wirtschaft.
Nachhaltigkeit
Nachhaltigkeit bezeichnet die verantwortungsvolle Nutzung natürlicher Ressourcen, um ökologische, ökonomische und soziale Bedürfnisse sowohl der heutigen als auch der zukünftigen Generationen zu erfüllen. Im Mittelpunkt steht das Ziel, wirtschaftliches Wachstum, Umweltschutz und soziale Gerechtigkeit in Einklang zu bringen. Dieses Konzept hat in den letzten Jahrzehnten zunehmend an Bedeutung gewonnen und beeinflusst zahlreiche Bereiche wie Industrie, Energie, Landwirtschaft und Konsumverhalten.
In der Industrie spielt Nachhaltigkeit eine zentrale Rolle bei der Entwicklung umweltfreundlicher Produktionsmethoden. Der Einsatz energieeffizienter Maschinen, die Nutzung erneuerbarer Energien und die Minimierung von Abfällen sind wesentliche Schritte, um den ökologischen Fußabdruck von Unternehmen zu reduzieren. Durch den Einsatz von Kreislaufwirtschaftskonzepten wird angestrebt, Materialien wiederzuverwenden und den Ressourcenverbrauch zu senken. Beispielsweise gewinnen Recyclingverfahren oder die Verwendung biologisch abbaubarer Materialien immer mehr an Bedeutung.
Auch in der Energieversorgung ist Nachhaltigkeit ein entscheidendes Ziel. Der Übergang von fossilen Brennstoffen zu erneuerbaren Energien wie Solar-, Wind- und Wasserkraft ist ein zentraler Bestandteil, um die CO₂-Emissionen zu verringern und die Auswirkungen des Klimawandels zu begrenzen. Fortschritte in der Speichertechnologie, etwa durch Batterien oder Wasserstoff, ermöglichen eine stabilere Versorgung mit erneuerbaren Energien und fördern den Ausbau nachhaltiger Energiesysteme.
Im sozialen Kontext bedeutet Nachhaltigkeit, faire Arbeitsbedingungen, den Schutz der Menschenrechte und den Zugang zu Bildung und Gesundheitsversorgung sicherzustellen. Unternehmen und Organisationen, die soziale Nachhaltigkeit priorisieren, setzen sich für Gleichberechtigung, Diversität und die Förderung lokaler Gemeinschaften ein. Diese Aspekte sind nicht nur ethisch relevant, sondern tragen auch zur langfristigen Stabilität und Akzeptanz von Geschäftsmodellen bei.
Nachhaltigkeit hat auch einen starken Einfluss auf das Konsumverhalten. Verbraucher legen zunehmend Wert auf Produkte, die umweltfreundlich hergestellt, fair gehandelt und langlebig sind. Dieser Trend hat dazu geführt, dass viele Unternehmen ihre Lieferketten überprüfen und nachhaltige Alternativen anbieten, um den Erwartungen der Kunden gerecht zu werden. Zertifizierungen wie Fairtrade, FSC oder das EU-Ecolabel helfen Verbrauchern dabei, nachhaltige Entscheidungen zu treffen.
Insgesamt ist Nachhaltigkeit ein komplexes und interdisziplinäres Konzept, das eine enge Zusammenarbeit zwischen Regierungen, Unternehmen und der Gesellschaft erfordert. Durch Innovation, Bildung und bewusstes Handeln kann die Transformation hin zu einer nachhaltigen Welt gelingen. Angesichts globaler Herausforderungen wie dem Klimawandel, der Ressourcenknappheit und sozialen Ungleichheiten ist Nachhaltigkeit nicht nur eine Notwendigkeit, sondern auch eine Chance für eine zukunftsfähige und gerechte Entwicklung.
Prozessoptimierung
Prozessoptimierung bezeichnet die systematische Analyse, Verbesserung und Anpassung von Arbeits- und Produktionsprozessen, um Effizienz, Qualität und Rentabilität zu steigern. Ziel ist es, Abläufe so zu gestalten, dass Ressourcen optimal genutzt, Durchlaufzeiten verkürzt und Fehler oder Verschwendungen minimiert werden. Dieser Ansatz findet Anwendung in nahezu allen Branchen und Organisationen, da er direkt zur Wettbewerbsfähigkeit und Leistungssteigerung beiträgt.
Ein zentraler Aspekt der Prozessoptimierung ist die Identifikation von Engpässen und ineffizienten Abläufen. Mit Methoden wie der Wertstromanalyse, Prozessmodellierung oder dem Einsatz von Datenanalysen können Schwachstellen aufgedeckt und gezielt adressiert werden. In der Produktion werden beispielsweise Maschinenlaufzeiten, Materialflüsse oder Energieverbräuche überwacht, um Potenziale zur Verbesserung zu erkennen. Durch die Beseitigung von redundanten Aufgaben oder die Automatisierung manueller Schritte können Kosten gesenkt und die Produktivität erhöht werden.
Die Digitalisierung spielt eine entscheidende Rolle bei der Prozessoptimierung. Moderne Technologien wie das Internet der Dinge (IoT), Big Data und Künstliche Intelligenz (KI) ermöglichen eine präzise Überwachung und Steuerung von Prozessen in Echtzeit. So können Unternehmen schneller auf Änderungen reagieren und Entscheidungen auf Basis fundierter Daten treffen. Predictive Maintenance, also die vorausschauende Wartung von Maschinen, ist ein Beispiel für die Anwendung solcher Technologien, um ungeplante Ausfallzeiten zu vermeiden und die Effizienz zu maximieren.
Neben der technischen Optimierung umfasst Prozessoptimierung auch organisatorische und menschliche Aspekte. Die Anpassung von Arbeitsabläufen, Schulungen der Mitarbeiter und die Förderung einer Kultur der kontinuierlichen Verbesserung (Kaizen) sind essenziell, um langfristige Erfolge sicherzustellen. Eine transparente Kommunikation und die Einbindung der Belegschaft tragen dazu bei, Akzeptanz für Veränderungen zu schaffen und die Effektivität der Maßnahmen zu erhöhen.
Im Rahmen der Nachhaltigkeit gewinnt Prozessoptimierung zusätzlich an Bedeutung. Durch die Reduzierung von Energieverbrauch, Materialeinsatz und Abfall kann nicht nur die Umweltbelastung gesenkt, sondern auch die Wirtschaftlichkeit gesteigert werden. Beispiele hierfür sind energieeffiziente Produktionsverfahren oder der Übergang zur Kreislaufwirtschaft, bei der Ressourcen wiederverwendet werden.
Zusammengefasst ist Prozessoptimierung ein kontinuierlicher und dynamischer Ansatz, der Unternehmen hilft, auf sich ändernde Marktbedingungen und technologische Fortschritte zu reagieren. Durch die Kombination von Technologie, Strategie und menschlichem Engagement wird es möglich, Prozesse nicht nur effizienter, sondern auch nachhaltiger und zukunftssicher zu gestalten.
Funktionale Eigenschaften
Funktionale Eigenschaften beziehen sich auf die spezifischen, oft technischen Merkmale, die ein Material oder Produkt besitzt, um eine bestimmte Aufgabe oder Funktion effektiv zu erfüllen. Diese Eigenschaften gehen über ästhetische Merkmale hinaus und betreffen Aspekte wie Leistung, Haltbarkeit, Widerstandsfähigkeit oder spezielle physikalische und chemische Fähigkeiten, die den Nutzen eines Produkts in bestimmten Anwendungen erhöhen.
In der Materialwissenschaft spielen funktionale Eigenschaften eine Schlüsselrolle, da sie die Eignung eines Materials für verschiedene Anwendungen bestimmen. Zu den häufigsten funktionalen Eigenschaften gehören:
- Mechanische Eigenschaften: Diese beinhalten die Festigkeit, Zähigkeit, Härte und Elastizität eines Materials. Sie bestimmen, wie gut das Material Belastungen standhält, ohne zu versagen oder sich zu verformen. Beispiele sind die Festigkeit von Stahl, die Flexibilität von Gummi oder die Härte von Diamanten.
- Korrosionsbeständigkeit: Materialien, die in Umgebungen mit Feuchtigkeit, Chemikalien oder extremen Temperaturen eingesetzt werden, müssen korrosionsbeständig sein. Eine hohe Korrosionsbeständigkeit ist für Produkte wie Maschinenbauteile, Rohre oder Bauelemente, die im Freien oder in aggressiven Umgebungen arbeiten, entscheidend.
- Elektrische Eigenschaften: Diese betreffen die Leitfähigkeit oder Isolierung eines Materials. Metalle wie Kupfer oder Aluminium sind aufgrund ihrer hervorragenden elektrischen Leitfähigkeit in der Elektronikindustrie weit verbreitet, während Isoliermaterialien wie Kunststoff oder Glas in elektrischen Leitungen und Geräten verwendet werden.
- Thermische Eigenschaften: Materialien müssen häufig spezifische Anforderungen in Bezug auf Wärmeleitung, Wärmespeicherung oder Wärmebeständigkeit erfüllen. Beispielsweise sind hitzebeständige Materialien in der Automobilindustrie oder in der Luftfahrt entscheidend, um extremen Temperaturen standzuhalten.
- Optische Eigenschaften: Diese betreffen die Fähigkeit eines Materials, Licht zu absorbieren, zu reflektieren oder zu durchlassen. Glas, Kunststoff und spezielle Beschichtungen mit optischen Eigenschaften finden Anwendung in der Herstellung von Fenstern, Linsen, Displays und Solarzellen.
- Chemische Stabilität: Materialien müssen in der Lage sein, in Kontakt mit verschiedenen Chemikalien zu bestehen, ohne ihre strukturellen oder funktionalen Eigenschaften zu verlieren. Dies ist besonders wichtig für Produkte, die in der chemischen Industrie oder in der Lebensmittelverarbeitung eingesetzt werden.
- Akustische Eigenschaften: Materialien mit bestimmten akustischen Eigenschaften werden verwendet, um Schall zu dämpfen oder zu reflektieren. In der Bauindustrie werden z. B. schallabsorbierende Materialien für die Verbesserung der Raumakustik eingesetzt.
- Biokompatibilität: Für medizinische Produkte ist es wichtig, dass Materialien mit dem menschlichen Körper kompatibel sind, ohne eine schädliche Reaktion hervorzurufen. Materialien für Implantate, medizinische Geräte oder Prothesen müssen biokompatibel sein, um eine sichere Anwendung zu gewährleisten.
Funktionale Eigenschaften sind daher von zentraler Bedeutung bei der Auswahl von Materialien und der Gestaltung von Produkten. Sie beeinflussen nicht nur die Leistungsfähigkeit und Effizienz eines Produkts, sondern auch seine Eignung für den vorgesehenen Zweck, seine Haltbarkeit und seine Kosten. Diese Eigenschaften sind auch ein wichtiger Aspekt bei der Entwicklung innovativer Produkte, da sie neue Funktionalitäten oder Verbesserungen bieten können, die den Wert und die Anwendungsmöglichkeiten eines Produkts erheblich erweitern.
Funktionale Eigenschaften sind nicht nur entscheidend für die Leistung eines Produkts, sondern auch für die Entwicklung neuer Technologien und die Verbesserung bestehender Produkte. Durch Forschung und Innovation werden fortlaufend neue Materialien mit speziellen funktionalen Eigenschaften entwickelt, die den Anforderungen anspruchsvollster Anwendungen gerecht werden. Dies ist besonders in hochentwickelten Bereichen wie der Luft- und Raumfahrt, der Medizintechnik und der Elektronikindustrie von Bedeutung, wo sogar kleinste Verbesserungen in den funktionalen Eigenschaften eines Materials oder Produkts zu erheblichen Fortschritten führen können.
Ein weiteres wichtiges Konzept im Zusammenhang mit funktionalen Eigenschaften ist die multifunktionale Materialentwicklung. Hierbei handelt es sich um Materialien, die mehrere funktionale Eigenschaften kombinieren, um verschiedene Anforderungen gleichzeitig zu erfüllen. Ein Beispiel sind intelligente Materialien, die auf äußere Reize wie Temperatur, Druck oder Feuchtigkeit reagieren und ihre Eigenschaften entsprechend anpassen können. Solche Materialien finden Anwendung in Bereichen wie der Medizintechnik, der Automobilindustrie und der Bauindustrie, wo sich Anforderungen häufig ändern und flexible Lösungen benötigt werden.
In der Fertigungstechnik bedeutet die Berücksichtigung funktionaler Eigenschaften, dass die Auswahl von Materialien und die Gestaltung von Produktionsprozessen Hand in Hand gehen müssen. Durch den Einsatz fortschrittlicher Fertigungstechniken, wie etwa der additiven Fertigung (3D-Druck), können Materialien mit maßgeschneiderten funktionalen Eigenschaften hergestellt werden, die für spezifische Anwendungen optimiert sind. So können etwa Bauteile mit integrierten Funktionen wie Kühlung, Elektronik oder Sensorik in einem einzigen Produktionsschritt erzeugt werden, was sowohl die Komplexität als auch die Produktionskosten reduziert.
In der Nachhaltigkeit spielt die Verbesserung der funktionalen Eigenschaften von Materialien ebenfalls eine zentrale Rolle. Zum Beispiel können Materialien mit verbesserten thermischen oder elektrischen Eigenschaften dazu beitragen, den Energieverbrauch in Gebäuden oder elektronischen Geräten zu senken. Ebenso können nachhaltigere Produktionsmethoden entwickelt werden, die auf die Erhaltung der funktionalen Eigenschaften von Materialien ausgerichtet sind, ohne die Umwelt unnötig zu belasten. Ein weiteres Beispiel ist die Entwicklung von Materialien mit selbstheilenden Eigenschaften, die ihre Funktionalität nach Schäden automatisch wiederherstellen und so die Lebensdauer von Produkten verlängern.
Zusätzlich sind funktionale Eigenschaften auch im Kontext der Sicherheit von großer Bedeutung. Materialien und Produkte, die in sicherheitskritischen Bereichen eingesetzt werden, müssen besondere Anforderungen in Bezug auf Festigkeit, Chemikalienbeständigkeit und thermische Stabilität erfüllen. Beispielsweise sind in der Luftfahrt oder im Fahrzeugbau Materialien erforderlich, die extremen Belastungen standhalten, ohne ihre strukturelle Integrität zu verlieren. Hier spielen funktionale Eigenschaften eine entscheidende Rolle, um die Sicherheit und Verlässlichkeit von Produkten zu gewährleisten.
Zusammenfassend lässt sich sagen, dass funktionale Eigenschaften eine fundamentale Rolle bei der Auswahl von Materialien und der Produktentwicklung spielen. Sie beeinflussen nicht nur die Leistung und Lebensdauer eines Produkts, sondern auch seine Eignung für bestimmte Anwendungen, seine Nachhaltigkeit und seine Innovationspotenziale. Die kontinuierliche Weiterentwicklung und Kombination funktionaler Eigenschaften eröffnen neue Möglichkeiten für die Herstellung von Produkten, die den Anforderungen einer zunehmend technologisierten und umweltbewussten Gesellschaft gerecht werden.