Eine Pulverbeschichtungsanlage für Schrauben, Nietköpfe und Bolzen ist eine speziell angepasste Einrichtung zur Beschichtung dieser Kleinteile mit Pulverlacken. Diese Technologie wird in der industriellen Fertigung eingesetzt, um eine hochwertige, dauerhafte Oberflächenbeschichtung zu erzielen, die Korrosionsschutz, Ästhetik und Funktionalität gewährleistet.
Die Pulverbeschichtung bietet viele Vorteile gegenüber herkömmlichen Beschichtungsmethoden wie das Tauchverfahren oder das Sprühverfahren. Sie ist umweltfreundlicher, da sie im Wesentlichen lösungsmittelfrei ist und weniger schädliche Emissionen erzeugt. Zudem erzeugt sie eine gleichmäßige und strapazierfähige Beschichtung, die eine gute Abdeckung und Schutz bietet.
Die Anlage zur Pulverbeschichtung von Schrauben, Nietköpfen und Bolzen besteht typischerweise aus mehreren Komponenten:
- Vorbehandlungssystem: Bevor die Teile beschichtet werden, müssen sie gründlich gereinigt und vorbehandelt werden, um Schmutz, Fett und andere Verunreinigungen zu entfernen. Dies kann durch eine Kombination aus Waschen, Entfetten und chemischer Vorbehandlung erfolgen, um die Haftung der Pulverbeschichtung zu verbessern.
- Pulverapplikationseinheit: In diesem Schritt wird das Pulver auf die vorbehandelten Teile aufgetragen. Typische Methoden umfassen das elektrostatische Sprühen, bei dem das Pulver durch elektrostatische Aufladung auf die Teile aufgebracht wird. Dies ermöglicht eine gleichmäßige Verteilung und Haftung des Pulvers.
- Einbrenn- oder Aushärtungsofen: Nachdem das Pulver aufgetragen wurde, müssen die Teile erhitzt werden, um das Pulver zu schmelzen und zu einer festen Beschichtung zu verschmelzen. Dies geschieht in einem Einbrennofen bei einer definierten Temperatur und für eine bestimmte Zeit.
- Kühleinheit und Handling: Nach dem Aushärten werden die beschichteten Teile gekühlt und aus der Anlage entfernt. Hier ist ein effizientes Handling wichtig, um Beschädigungen der frisch beschichteten Teile zu vermeiden.
Die Wahl der richtigen Pulverbeschichtungsanlage hängt von der Art der Teile, der Produktionskapazität und den spezifischen Anforderungen des Herstellers ab. Kleinteile wie Schrauben, Nietköpfe und Bolzen erfordern spezielle Vorrichtungen, um eine gleichmäßige Beschichtung zu gewährleisten, ohne dass die Gewinde oder andere kritische Bereiche verstopft werden.
Diese Art von Anlagen ist oft in automatisierten Produktionslinien integriert, um eine effiziente und konsistente Beschichtung großer Stückzahlen zu ermöglichen. Modernste Anlagen verfügen über Überwachungs- und Steuerungssysteme, um den Beschichtungsprozess zu optimieren und die Qualität der beschichteten Teile sicherzustellen.
Insgesamt bietet die Pulverbeschichtung von Schrauben, Nietköpfen und Bolzen eine kostengünstige und umweltfreundliche Methode zur Erzielung hochwertiger Oberflächenbeschichtungen, die den Anforderungen der heutigen Industrie gerecht werden.
Eine Pulverbeschichtungsanlage für Schrauben, Nietköpfe und Bolzen ist eine spezialisierte Ausrüstung, die in der Oberflächenbehandlung und -veredelung von Metallteilen wie Schrauben, Bolzen und Nietköpfen eingesetzt wird. Die Pulverbeschichtung ist ein Verfahren, bei dem ein trockenes Pulver auf die Oberfläche des Werkstücks aufgebracht wird, das anschließend durch Erhitzen in einen festen Film übergeht. Dieses Verfahren wird aufgrund seiner hohen Effizienz, Langlebigkeit und Umweltfreundlichkeit in der Industrie sehr geschätzt. Im Folgenden wird das Verfahren der Pulverbeschichtung sowie die Funktionsweise einer Pulverbeschichtungsanlage für Schrauben und ähnliche Komponenten näher beschrieben.
Funktionsweise der Pulverbeschichtungsanlage
Die Pulverbeschichtung erfolgt in mehreren Schritten, die mit einer spezialisierten Pulverbeschichtungsanlage durchgeführt werden. Die grundlegenden Schritte umfassen:
- Vorbehandlung: Vor der Beschichtung müssen die Schrauben, Nietköpfe und Bolzen gründlich gereinigt und entfettet werden. Dies erfolgt meist durch Sandstrahlen oder durch chemische Entfettungsverfahren, um eine saubere und fettfreie Oberfläche zu gewährleisten. Dies ist notwendig, um eine gute Haftung des Pulvers auf der Metalloberfläche zu erreichen.
- Pulverauftrag: Die Pulverbeschichtung erfolgt durch elektrostatische Pulverapplikation. Hierbei wird das Pulver in einer Sprühkammer mit Hilfe von Hochspannung elektrostatisch auf die Werkstücke aufgetragen. Das Pulver haftet aufgrund der elektrischen Aufladung an den Metallteilen.
- Aushärten: Nach dem Auftragen des Pulvers müssen die beschichteten Schrauben, Bolzen oder Nietköpfe in einem Ofen bei Temperaturen zwischen 160 und 200 °C erhitzt werden. Dadurch schmilzt das Pulver und bildet eine feste, gleichmäßige Beschichtung. Diese Schicht härtet nach der Abkühlung aus und schützt die Oberfläche der Teile vor Korrosion, Abrieb und anderen äußeren Einflüssen.
- Abkühlung: Nach dem Aushärten werden die beschichteten Teile aus dem Ofen entnommen und auf Raumtemperatur abgekühlt. Die Beschichtung ist nun vollständig ausgehärtet und bietet den gewünschten Schutz.
2. Vorteile der Pulverbeschichtung für Schrauben, Nietköpfe und Bolzen
Die Pulverbeschichtung bietet im Vergleich zu traditionellen Lackierungen eine Reihe von Vorteilen, insbesondere für kleinere Metallteile wie Schrauben, Bolzen und Nietköpfe:
- Langlebigkeit: Pulverbeschichtungen sind sehr widerstandsfähig gegenüber Kratzern, Abnutzung und chemischen Angriffen, was sie besonders für Teile geeignet macht, die in rauen Umgebungen eingesetzt werden.
- Korrosionsschutz: Eine gut durchgeführte Pulverbeschichtung bietet einen exzellenten Schutz gegen Korrosion und verlängert die Lebensdauer von Schrauben und Bolzen, insbesondere in feuchten oder salzhaltigen Umgebungen.
- Umweltfreundlichkeit: Im Gegensatz zu herkömmlichen Lackierungen, die Lösungsmittel enthalten können, ist die Pulverbeschichtung umweltfreundlicher, da sie keine flüchtigen organischen Verbindungen (VOCs) abgibt und die Abfälle minimiert werden.
- Kosteneffizienz: Die Pulverbeschichtung ist ein wirtschaftliches Verfahren, insbesondere für größere Produktionsmengen, da das Pulver in der Regel recycelbar ist und der Materialverlust minimiert wird.
- Farben und Oberflächenstruktur: Pulverbeschichtungen können in verschiedenen Farben und Oberflächenstrukturen (glänzend, matt, strukturiert) durchgeführt werden, was zusätzliche Designmöglichkeiten für die fertigen Teile bietet.
3. Besondere Anforderungen für die Pulverbeschichtung von Schrauben und Bolzen
Schrauben, Bolzen und Nietköpfe stellen besondere Anforderungen an die Pulverbeschichtung aufgrund ihrer Form und ihrer Einsatzbedingungen:
- Gleichmäßige Beschichtung: Da Schrauben und Bolzen oft komplexe Geometrien und kleine Öffnungen (z. B. Gewinde) aufweisen, muss die Pulverbeschichtung so angewendet werden, dass die gesamte Oberfläche, einschließlich der schwer zugänglichen Stellen, gleichmäßig beschichtet wird. Dies erfordert eine präzise Steuerung des Pulverauftrags.
- Vermeidung von Verstopfungen: Bei der Beschichtung von Bolzen und Schrauben muss darauf geachtet werden, dass keine Pulveransammlungen in den Gewinden oder Bohrungen entstehen, da dies die Funktionalität der Teile beeinträchtigen könnte.
- Haftung auf kleinen Teilen: Für kleinere Teile wie Schrauben oder Nietköpfe ist es wichtig, dass das Pulver gut haftet, um eine gleichmäßige Schichtdicke zu gewährleisten und eine effektive Korrosionsbeständigkeit zu erreichen.
- Wärmebehandlung: Der Ofen, in dem das Pulver gehärtet wird, muss für kleine Teile wie Schrauben und Bolzen präzise gesteuert werden, um eine gleichmäßige Aushärtung der Beschichtung ohne Verzerrungen oder Verformungen zu gewährleisten.
4. Typische Anwendungen der Pulverbeschichtung für Schrauben und Bolzen
Pulverbeschichtete Schrauben, Bolzen und Nietköpfe finden in verschiedenen Branchen Anwendung, darunter:
- Bauindustrie: Pulverbeschichtete Verbindungselemente werden in der Konstruktion eingesetzt, um sicherzustellen, dass sie den Herausforderungen von Witterungseinflüssen und Korrosion standhalten, insbesondere in Außenbereichen oder maritimen Umgebungen.
- Automobilindustrie: In der Fahrzeugfertigung werden viele Schrauben und Bolzen pulverbeschichtet, um sie vor Rost und Abrieb zu schützen und gleichzeitig eine ansprechende Oberfläche zu bieten.
- Maschinenbau: In Maschinen, die hohen mechanischen Belastungen ausgesetzt sind, kommen pulverbeschichtete Verbindungselemente zum Einsatz, um die Lebensdauer und die Leistung der Maschinen zu steigern.
5. Wartung und Pflege der Pulverbeschichtungsanlage
Die regelmäßige Wartung der Pulverbeschichtungsanlage ist entscheidend, um die Qualität und Effizienz des Beschichtungsprozesses sicherzustellen. Wichtige Wartungsmaßnahmen umfassen:
- Reinigung der Sprühdüsen: Da Pulverstaub die Düsen und Sprühkammern verstopfen kann, müssen diese regelmäßig gereinigt werden, um einen konstanten Pulverfluss und eine gleichmäßige Beschichtung zu gewährleisten.
- Kontrolle der Ofentemperatur: Eine konstante Ofentemperatur ist notwendig, um die optimale Aushärtung der Beschichtung zu gewährleisten. Die Temperatur muss regelmäßig überprüft und kalibriert werden.
- Überwachung des Pulververbrauchs: Das verwendete Pulver muss regelmäßig auf seine Qualität hin überprüft werden, um sicherzustellen, dass keine Verunreinigungen vorliegen und die Beschichtungseigenschaften erhalten bleiben.
Fazit
Eine Pulverbeschichtungsanlage für Schrauben, Nietköpfe und Bolzen ist eine hochentwickelte Einrichtung, die durch ihren effizienten und umweltfreundlichen Prozess zur Verbesserung der Haltbarkeit und Korrosionsbeständigkeit von Verbindungselementen beiträgt. Mit der richtigen Wartung und Kontrolle ermöglicht diese Technik eine hochwertige Oberflächenbehandlung, die die Funktionalität und Ästhetik der Teile verbessert und deren Lebensdauer verlängert.
Funktionsweise der Pulverbeschichtungsanlage

Eine Pulverbeschichtungsanlage für Schrauben, Nietköpfe und Bolzen ist eine spezialisierte Ausrüstung, die in der Oberflächenbehandlung und -veredelung von Metallteilen wie Schrauben, Bolzen und Nietköpfen eingesetzt wird. Die Pulverbeschichtung ist ein Verfahren, bei dem ein trockenes Pulver auf die Oberfläche des Werkstücks aufgebracht wird, das anschließend durch Erhitzen in einen festen Film übergeht. Dieses Verfahren wird aufgrund seiner hohen Effizienz, Langlebigkeit und Umweltfreundlichkeit in der Industrie sehr geschätzt.
Die Pulverbeschichtung bietet im Vergleich zu traditionellen Lackierungen eine Reihe von Vorteilen, insbesondere für kleinere Metallteile wie Schrauben, Bolzen und Nietköpfe. Ein wesentlicher Vorteil ist die Langlebigkeit der Beschichtung. Pulverbeschichtungen sind äußerst widerstandsfähig gegenüber Kratzern, Abnutzung und chemischen Angriffen, was sie besonders für Teile geeignet macht, die in rauen Umgebungen oder unter extremen Bedingungen eingesetzt werden. In Verbindung mit der hohen Korrosionsbeständigkeit sind pulverbeschichtete Verbindungselemente ideal für den Einsatz in der Bauindustrie, Maschinenbau oder Automobilindustrie, wo Teile oft verschiedenen Witterungseinflüssen oder aggressiven Substanzen ausgesetzt sind.
Ein weiterer Vorteil der Pulverbeschichtung ist der Korrosionsschutz, den sie bietet. Schrauben, Bolzen und Nietköpfe, die in feuchten, salzhaltigen oder chemisch belasteten Umgebungen eingesetzt werden, profitieren besonders von der Pulverbeschichtung, da sie eine robuste Barriere gegen Rost und andere korrosive Elemente schafft. Diese Schutzwirkung verlängert die Lebensdauer der Teile erheblich, was besonders in sicherheitskritischen Anwendungen von Bedeutung ist.
Zudem ist die Umweltfreundlichkeit der Pulverbeschichtung hervorzuheben. Im Gegensatz zu herkömmlichen Lackierungen, bei denen flüchtige organische Verbindungen (VOCs) freigesetzt werden können, ist die Pulverbeschichtung nahezu frei von Lösungsmitteln und erzeugt deutlich weniger Abfall. Das Pulver kann zudem oft recycelt werden, was den Materialverbrauch minimiert und somit die Umwelt schont. Die Verfahrenstechnologie stellt eine kostengünstige und nachhaltige Alternative dar, insbesondere bei größeren Produktionsmengen, da die Wiederverwendbarkeit von überschüssigem Pulver den Materialverbrauch optimiert.
Die Kosteneffizienz von Pulverbeschichtungsanlagen ergibt sich nicht nur durch den Materialrecyclingprozess, sondern auch durch die hohe Produktivität des Verfahrens. Die schnelle Aushärtung der Pulverbeschichtungen und die Möglichkeit, mehrere Teile gleichzeitig zu beschichten, machen die Technologie besonders attraktiv für die Massenproduktion. Auch die Vielfalt der möglichen Oberflächenbehandlungen – von glänzenden über matte bis hin zu strukturierten Oberflächen – bietet zusätzliche Flexibilität in der Gestaltung von Schrauben, Bolzen und Nietköpfen.
Für kleinere Teile wie Schrauben, Nietköpfe und Bolzen stellt die Haftung des Pulvers auf den Metalloberflächen eine besondere Herausforderung dar. Aufgrund der komplexen Geometrie und der oft schwer zugänglichen Stellen wie Gewinde oder Bohrungen muss der Pulverauftrag so präzise wie möglich erfolgen, um sicherzustellen, dass die gesamte Oberfläche gleichmäßig beschichtet wird. Dies kann durch die Verwendung spezieller Sprühtechniken oder optimierter Anlagensteuerungen erreicht werden, die auch schwierig zu erreichende Stellen gut abdecken.
Ein weiteres kritisches Kriterium ist die Vermeidung von Verstopfungen in Gewinden oder Bohrungen der Teile. Um dies zu verhindern, müssen spezielle Techniken zur Handhabung und zum Design der Beschichtungsstationen angewendet werden, sodass das Pulver nicht in den Gewinden haften bleibt und die Funktionalität der Teile nicht beeinträchtigt wird. Ebenso wichtig ist eine präzise Temperaturregelung im Ofen, der für das Aushärten der Beschichtung verantwortlich ist. Eine gleichmäßige Erwärmung sorgt dafür, dass die Schicht ohne Verzerrungen oder Verformungen aushärtet und eine widerstandsfähige Oberfläche entsteht.
Die Vielseitigkeit der Pulverbeschichtung macht sie zu einem bevorzugten Verfahren in verschiedenen Branchen. In der Automobilindustrie etwa werden pulverbeschichtete Verbindungselemente häufig verwendet, da sie nicht nur eine hohe Haltbarkeit aufweisen, sondern auch optisch ansprechend sind und eine lange Lebensdauer bieten. Die Bauindustrie setzt auf pulverbeschichtete Schrauben und Bolzen, um die Witterungsbeständigkeit und den Schutz gegen Rost zu erhöhen, besonders in Bereichen, die starkem Wetter ausgesetzt sind, wie Brücken oder Außenanlagen. Ebenso sind diese Beschichtungen im Maschinenbau von Bedeutung, wo Verbindungselemente starken mechanischen Belastungen standhalten müssen.
Eine der zentralen Herausforderungen für die Pulverbeschichtung von Schrauben, Bolzen und Nietköpfen ist die Wärmebehandlung, die für das Aushärten des Pulvers erforderlich ist. In der Regel muss das Werkstück nach dem Auftragen der Pulverbeschichtung in einen Ofen eingeführt werden, wo es auf Temperaturen zwischen 160 und 200 °C erhitzt wird. Es ist von entscheidender Bedeutung, dass die Teile gleichmäßig erhitzt werden, um eine konsistente Schichtdicke und eine perfekte Aushärtung zu gewährleisten. Uneinheitliche Temperaturen können dazu führen, dass die Beschichtung nicht ordnungsgemäß aushärtet, was ihre Schutzwirkung beeinträchtigen würde.
Neben den Vorteilen der Pulverbeschichtung gibt es auch spezifische Wartungsanforderungen für die Pulverbeschichtungsanlage, um sicherzustellen, dass die Qualität der Beschichtungen konstant hoch bleibt. Die Sprühdüsen und Kammern müssen regelmäßig gereinigt werden, da sich Pulverreste und Staubansammlungen negativ auf die Qualität des Auftrags auswirken können. Auch die Ofentemperatur muss regelmäßig überprüft werden, um sicherzustellen, dass sie den gewünschten Aushärtungsbedingungen entspricht. Die Überwachung des Pulververbrauchs und die Kontrolle der Materialqualität sind ebenfalls wichtige Wartungsaufgaben, um einen gleichbleibend hohen Standard in der Pulverbeschichtung zu garantieren.
Zusammenfassend lässt sich sagen, dass eine Pulverbeschichtungsanlage für Schrauben, Nietköpfe und Bolzen eine effiziente und umweltfreundliche Möglichkeit zur Verbesserung der Haltbarkeit und Korrosionsbeständigkeit von Metallteilen darstellt. Sie bietet eine kostengünstige Lösung für die Herstellung von langlebigen und widerstandsfähigen Verbindungselementen, die in unterschiedlichsten Industrien Anwendung finden.
Vorteile der Pulverbeschichtung für Schrauben, Nietköpfe und Bolzen
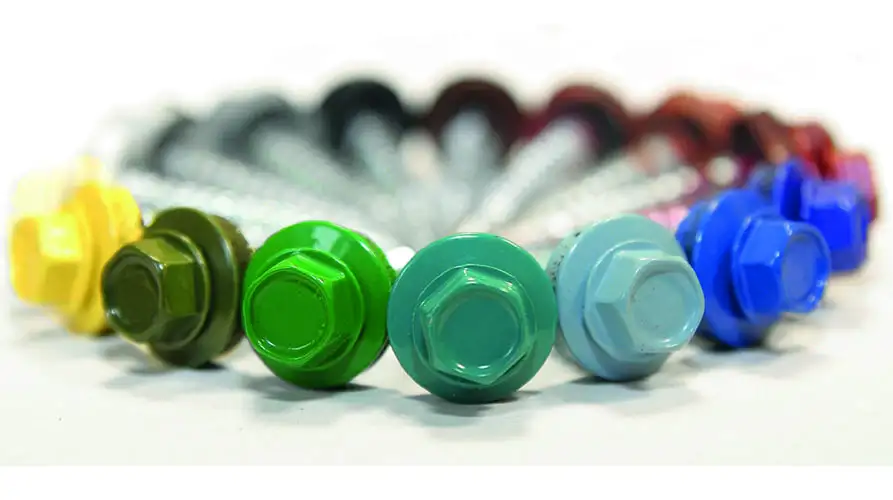
Eine Pulverbeschichtungsanlage für Schrauben, Nietköpfe und Bolzen ist eine spezialisierte Ausrüstung, die in der Oberflächenbehandlung und -veredelung von Metallteilen wie Schrauben, Bolzen und Nietköpfen eingesetzt wird. Die Pulverbeschichtung ist ein Verfahren, bei dem ein trockenes Pulver auf die Oberfläche des Werkstücks aufgebracht wird, das anschließend durch Erhitzen in einen festen Film übergeht. Dieses Verfahren wird aufgrund seiner hohen Effizienz, Langlebigkeit und Umweltfreundlichkeit in der Industrie sehr geschätzt.
Die Pulverbeschichtung ist in vielen Industrien eine bevorzugte Wahl, um Verbindungselemente wie Schrauben und Bolzen zu schützen. Die Beschichtung ermöglicht eine gleichmäßige, widerstandsfähige Oberfläche, die den mechanischen Anforderungen standhält. Besonders in Bereichen wie der Automobilindustrie, Bauindustrie und dem Maschinenbau ist der Einsatz von pulverbeschichteten Schrauben und Bolzen weit verbreitet. Diese Verbindungselemente müssen in der Regel einer Vielzahl von Herausforderungen standhalten, darunter Korrosion, Abrieb und hohe mechanische Belastungen. Pulverbeschichtungen bieten hier eine ausgezeichnete Lösung, indem sie eine schützende Barriere gegen schädliche Umwelteinflüsse bilden und gleichzeitig die Lebensdauer der Teile verlängern.
In der Bauindustrie werden pulverbeschichtete Schrauben und Bolzen häufig für Anwendungen im Außenbereich verwendet, da sie den Witterungsbedingungen besser widerstehen. In maritimen Umgebungen etwa bieten sie einen effektiven Schutz vor Salzwasser, das normalerweise zu schneller Korrosion führt. Auch in der Automobilindustrie sind pulverbeschichtete Verbindungselemente von Bedeutung, da sie nicht nur funktional sind, sondern auch eine ästhetische Oberfläche bieten, die zu einem hochwertigen Erscheinungsbild beiträgt.
Für die Maschinenbauindustrie sind pulverbeschichtete Schrauben, Bolzen und Nietköpfe von entscheidender Bedeutung, da sie eine hohe Widerstandsfähigkeit gegen Verschleiß und mechanische Belastungen bieten. Diese Teile sind oft in Maschinen verbaut, die großen Kräften ausgesetzt sind. Die zusätzliche Schutzschicht der Pulverbeschichtung hilft dabei, die Teile vor Abrieb und Korrosion zu schützen, was die Wartungskosten reduziert und die Lebensdauer der Maschinen verlängert.
Die Haftung des Pulvers auf den Metalloberflächen ist ein wesentlicher Aspekt bei der Pulverbeschichtung von Schrauben und Bolzen. Aufgrund der komplexen Geometrie dieser Teile, die häufig kleine Öffnungen wie Gewinde oder Bohrungen aufweisen, muss der Pulverauftrag so erfolgen, dass auch schwer zugängliche Stellen gleichmäßig beschichtet werden. Hierfür kommen spezialisierte Sprühtechniken und optimierte Anlagensteuerungen zum Einsatz, die eine präzise Applikation des Pulvers ermöglichen.
Besondere Aufmerksamkeit erfordert die Vermeidung von Verstopfungen in den Gewinden oder Bohrungen. Sollte Pulver in diese Stellen gelangen, könnte die Funktionalität der Verbindungselemente beeinträchtigt werden. Daher müssen die Teile während des Beschichtungsprozesses so ausgerichtet werden, dass das Pulver gezielt und gleichmäßig aufgetragen wird, ohne in mechanische Bereiche zu gelangen, die für die Montage oder den Betrieb wichtig sind.
Ein weiterer wichtiger Schritt im Prozess ist die Wärmebehandlung der pulverbeschichteten Teile. Nachdem das Pulver auf die Schrauben, Bolzen oder Nietköpfe aufgetragen wurde, müssen diese in einen Ofen eingeführt werden, in dem die Pulverpartikel bei Temperaturen von etwa 160 bis 200 °C schmelzen und eine stabile, widerstandsfähige Schicht bilden. Eine gleichmäßige Temperaturkontrolle ist entscheidend, um sicherzustellen, dass die Beschichtung nicht nur gut haftet, sondern auch vollständig aushärtet, ohne dass die Teile sich verformen oder ihre Funktionalität verlieren.
Neben der Hauptbehandlung müssen auch Wartungsaspekte berücksichtigt werden, um die Qualität und Effizienz der Pulverbeschichtungsanlage sicherzustellen. Die regelmäßige Reinigung der Sprühdüsen und Sprühkammern ist erforderlich, da Pulverreste und Staubansammlungen die Leistung der Anlage beeinträchtigen können. Eine regelmäßige Überprüfung der Ofentemperatur stellt sicher, dass die Pulverbeschichtung bei den richtigen Bedingungen ausgehärtet wird und keine ungleichmäßigen Oberflächen entstehen. Auch die Kontrolle des Pulververbrauchs und die Wiederverwendbarkeit des überschüssigen Pulvers tragen dazu bei, die Betriebskosten zu senken und die Nachhaltigkeit des Verfahrens zu erhöhen.
Zusammenfassend lässt sich sagen, dass eine Pulverbeschichtungsanlage für Schrauben, Nietköpfe und Bolzen eine effiziente und nachhaltige Methode zur Oberflächenbehandlung von Verbindungselementen darstellt. Sie schützt die Teile vor Umwelteinflüssen, mechanischer Beanspruchung und Korrosion, während sie gleichzeitig eine kostengünstige und umweltfreundliche Lösung für die Industrie bietet. Die sorgfältige Handhabung, die präzise Steuerung des Prozesses und die regelmäßige Wartung sind entscheidend, um die gewünschten Ergebnisse hinsichtlich Haltbarkeit, Funktionalität und Ästhetik der Beschichtungen zu erzielen.
Besondere Anforderungen für die Pulverbeschichtung von Schrauben und Bolzen
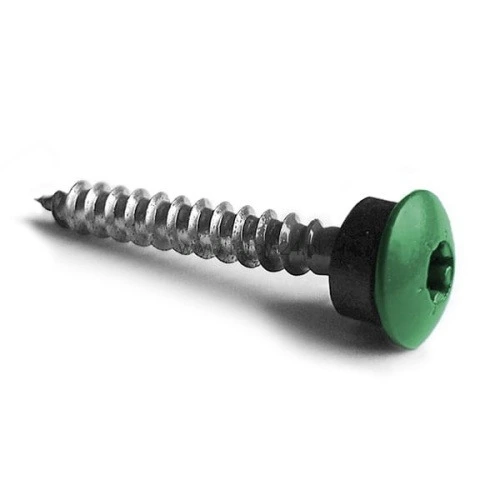
Eine Pulverbeschichtungsanlage für Schrauben, Nietköpfe und Bolzen ist eine spezialisierte Ausrüstung, die in der Oberflächenbehandlung und -veredelung von Metallteilen wie Schrauben, Bolzen und Nietköpfen eingesetzt wird. Das Verfahren der Pulverbeschichtung erfolgt in mehreren Schritten, bei denen ein trockenes Pulver auf die Oberfläche des Werkstücks aufgebracht wird, das anschließend durch Erhitzen in einen festen Film übergeht. Pulverbeschichtung wird aufgrund ihrer Effizienz, Haltbarkeit und Umweltfreundlichkeit besonders geschätzt.
Das Verfahren beginnt mit der Vorbehandlung der Werkstücke. Schrauben, Nietköpfe und Bolzen müssen vor der Pulverbeschichtung gründlich gereinigt und entfettet werden, um eine saubere, fettfreie Oberfläche zu gewährleisten. Dies ist entscheidend für eine gute Haftung der Pulverschicht und verhindert, dass Verunreinigungen die Qualität der Beschichtung beeinträchtigen. In der Regel erfolgt diese Reinigung durch chemische Entfettung oder mechanische Verfahren wie Sandstrahlen.
Im nächsten Schritt wird das Pulver auf die Metalloberfläche aufgetragen. Dabei kommt in der Regel eine elektrostatische Aufladung zum Einsatz. Das Pulver wird mittels eines Sprühgeräts auf die Teile aufgebracht, wobei eine hohe Spannung erzeugt wird, die dafür sorgt, dass das Pulver an der Metalloberfläche haften bleibt. Dieser Vorgang ist besonders wichtig, da eine gleichmäßige Verteilung des Pulvers auf der gesamten Oberfläche der Teile gewährleistet werden muss. Es ist entscheidend, dass auch schwer zugängliche Stellen wie Gewinde oder Bohrungen des Werkstücks gleichmäßig beschichtet werden, um eine hohe Qualität und Funktionalität der Beschichtung zu erzielen.
Nach dem Auftragen des Pulvers müssen die Teile in einen Aushärteofen eingeführt werden. Der Ofen erhitzt die Teile auf Temperaturen zwischen 160 und 200 °C, je nach Art des verwendeten Pulvers. Das Pulver schmilzt und bildet eine gleichmäßige Schicht auf der Oberfläche der Teile, die sich nach dem Abkühlen verfestigt und eine widerstandsfähige, schützende Beschichtung bildet. Die Aushärtung ist ein wesentlicher Schritt im Pulverbeschichtungsprozess, da sie dafür sorgt, dass das Pulver eine dauerhafte, beständige und belastbare Oberfläche bildet. Die genaue Temperaturkontrolle im Ofen ist von großer Bedeutung, um sicherzustellen, dass die Beschichtung gleichmäßig aushärtet und keine Verformungen der Teile auftreten.
Der letzte Schritt im Prozess ist die Abkühlung der beschichteten Teile. Nach dem Erhitzen müssen die Teile auf Raumtemperatur abkühlen, wodurch die Pulverbeschichtung vollständig aushärtet. Eine ordnungsgemäße Abkühlung sorgt dafür, dass die Beschichtung ihre Festigkeit und Widerstandsfähigkeit behält und keine Risse oder Unregelmäßigkeiten entstehen.
Pulverbeschichtete Schrauben, Bolzen und Nietköpfe bieten eine Vielzahl von Vorteilen, insbesondere in Bezug auf ihre Haltbarkeit und Korrosionsbeständigkeit. Die Beschichtung schützt die Teile vor Witterungseinflüssen, Abrieb und chemischen Angriffen, wodurch die Lebensdauer der Verbindungselemente deutlich verlängert wird. Besonders in Umgebungen, in denen Schrauben, Bolzen und Nietköpfe hohen Belastungen oder aggressiven Bedingungen ausgesetzt sind, wie beispielsweise in der Bauindustrie, der Automobilindustrie oder dem Maschinenbau, ist der Einsatz von Pulverbeschichtungen vorteilhaft. Sie bieten einen zuverlässigen Schutz vor Korrosion und tragen dazu bei, die Funktionalität und Zuverlässigkeit der Teile zu gewährleisten.
Darüber hinaus ist die Pulverbeschichtung ein umweltfreundliches Verfahren. Im Gegensatz zu traditionellen Lackierungen, bei denen flüchtige organische Verbindungen (VOCs) freigesetzt werden können, kommt die Pulverbeschichtung ohne Lösungsmittel aus. Dies macht sie umweltfreundlicher und reduziert die Emissionen von Schadstoffen. Auch die Tatsache, dass überschüssiges Pulver recycelt werden kann, trägt zur Nachhaltigkeit des Verfahrens bei.
Für die Wartung einer Pulverbeschichtungsanlage ist es wichtig, regelmäßig die Sprühdüsen und Kammern zu reinigen, um sicherzustellen, dass die Pulververteilung gleichmäßig bleibt und keine Verunreinigungen die Qualität der Beschichtung beeinträchtigen. Auch die Temperaturregelung des Ofens muss kontinuierlich überprüft werden, um sicherzustellen, dass die Aushärtung der Pulverbeschichtung bei den optimalen Bedingungen erfolgt. Eine regelmäßige Kontrolle des Pulververbrauchs und die Reinigung der Pulverabscheider sorgen dafür, dass die Materialverwendung effizient bleibt und die Anlage stets mit hohem Wirkungsgrad arbeitet.
Zusammenfassend lässt sich sagen, dass eine Pulverbeschichtungsanlage für Schrauben, Nietköpfe und Bolzen eine hervorragende Methode zur Oberflächenbehandlung und -veredelung von Verbindungselementen darstellt. Sie sorgt für eine hohe Haltbarkeit, Korrosionsbeständigkeit und Widerstandsfähigkeit der Teile und trägt zur Verlängerung ihrer Lebensdauer bei. Die Anwendung der Pulverbeschichtung in verschiedenen Industrien bietet eine kostengünstige und umweltfreundliche Lösung, die den Anforderungen an Qualität, Leistung und Nachhaltigkeit gerecht wird.
Typische Anwendungen der Pulverbeschichtung für Schrauben und Bolzen
Eine Pulverbeschichtungsanlage für Schrauben, Nietköpfe und Bolzen ist eine spezialisierte Ausrüstung, die in der Oberflächenbehandlung und -veredelung von Metallteilen wie Schrauben, Bolzen und Nietköpfen eingesetzt wird. Das Verfahren der Pulverbeschichtung ist besonders effizient und umweltfreundlich und bietet eine Reihe von Vorteilen gegenüber herkömmlichen Lackierungsverfahren. Dabei wird ein trockenes Pulver auf die Metalloberfläche aufgebracht und anschließend erhitzt, sodass es zu einer dauerhaften, widerstandsfähigen Schicht aushärtet.
Zu Beginn des Prozesses steht die Vorbehandlung der Werkstücke. Schrauben, Nietköpfe und Bolzen müssen vor der Pulverbeschichtung gründlich gereinigt werden, um sicherzustellen, dass die Oberfläche frei von Fett, Rost oder anderen Verunreinigungen ist. Diese Reinigung ist entscheidend für die Haftung des Pulvers auf der Metalloberfläche. Die Reinigung erfolgt häufig durch chemische Entfettung oder mechanische Verfahren wie Sandstrahlen. Nur so kann gewährleistet werden, dass das Pulver gleichmäßig haftet und die Beschichtung dauerhaft bleibt.
Im nächsten Schritt wird das Pulver auf die Metalloberfläche aufgetragen. Hierbei kommt in der Regel eine elektrostatische Sprühtechnik zum Einsatz. Das Pulver wird durch eine Elektrode aufgeladen, während das Werkstück ebenfalls eine entgegengesetzte elektrostatische Ladung erhält. Dadurch wird das Pulver an der Oberfläche des Werkstücks angezogen und bleibt haften. Dies ermöglicht es, eine gleichmäßige Schicht auf der gesamten Oberfläche der Teile zu erzeugen, auch an schwer zugänglichen Stellen wie Gewinden oder Bohrungen.
Nach dem Auftragen des Pulvers erfolgt die Aushärtung der Beschichtung. Die beschichteten Teile werden in einen speziellen Ofen eingeführt, der sie auf eine Temperatur von etwa 160 bis 200 °C erhitzt. Das Pulver schmilzt und bildet eine gleichmäßige, fest haftende Schicht. Während des Aushärtungsprozesses vernetzen sich die Moleküle im Pulver, wodurch die Beschichtung ihre endgültige Festigkeit und Widerstandsfähigkeit erhält. Eine präzise Temperaturkontrolle ist dabei entscheidend, um eine gleichmäßige und stabile Aushärtung zu gewährleisten.
Nach der Aushärtung erfolgt die Abkühlung der beschichteten Teile. Die Abkühlung muss kontrolliert und gleichmäßig erfolgen, um sicherzustellen, dass die Beschichtung vollständig aushärtet und keine Risse oder Verformungen entstehen. Sobald die Teile abgekühlt sind, ist die Pulverbeschichtung vollständig ausgehärtet und die Schrauben, Bolzen oder Nietköpfe haben eine widerstandsfähige, schützende Schicht, die sie vor Korrosion, Abrieb und anderen Umwelteinflüssen schützt.
Für die Wartung der Pulverbeschichtungsanlage ist es wichtig, regelmäßig die Sprühdüsen und Kammern zu reinigen. Pulverreste und Staubansammlungen können die Effizienz der Anlage beeinträchtigen und die Qualität der Beschichtung negativ beeinflussen. Eine regelmäßige Wartung der Sprühgeräte stellt sicher, dass das Pulver gleichmäßig aufgetragen wird und die gewünschte Beschichtungsqualität erreicht wird. Ebenso muss die Temperaturregelung im Ofen regelmäßig überprüft werden, um sicherzustellen, dass die Aushärtung unter den optimalen Bedingungen erfolgt. Eine kontinuierliche Kontrolle des Pulververbrauchs sowie das Reinigen und Überwachen der Pulverabscheider tragen dazu bei, die Effizienz der Anlage zu steigern und Materialverschwendung zu vermeiden.
Zusammenfassend lässt sich sagen, dass eine Pulverbeschichtungsanlage für Schrauben, Nietköpfe und Bolzen eine hochentwickelte Methode zur Oberflächenveredelung von Verbindungselementen darstellt. Sie sorgt für eine langlebige, widerstandsfähige und korrosionsbeständige Beschichtung, die den Anforderungen der verschiedenen Industrien gerecht wird. Durch die präzise Steuerung des gesamten Prozesses, von der Vorbehandlung über das Auftragen des Pulvers bis hin zur Aushärtung, kann eine gleichmäßige und qualitativ hochwertige Beschichtung erzielt werden. Die umweltfreundliche und kosteneffiziente Natur der Pulverbeschichtung macht sie zu einer bevorzugten Wahl für die Veredelung von Schrauben und Bolzen in einer Vielzahl von Anwendungen.
Wartung und Pflege der Pulverbeschichtungsanlage
Eine Pulverbeschichtungsanlage für Schrauben, Nietköpfe und Bolzen ist eine hochentwickelte Technologie, die in der Oberflächenveredelung von Metallteilen verwendet wird. Bei der Pulverbeschichtung wird ein feines, trockenes Pulver auf die Metalloberfläche aufgetragen, das anschließend durch Erhitzen in eine widerstandsfähige, schützende Schicht übergeht. Dieser Prozess zeichnet sich durch seine Effizienz, Haltbarkeit und Umweltfreundlichkeit aus und ist besonders in der Metallverarbeitung und in der Produktion von Verbindungselementen wie Schrauben, Bolzen und Nietköpfen von großer Bedeutung.
Der Prozess der Pulverbeschichtung beginnt mit der Vorbehandlung der Werkstücke. Um eine optimale Haftung des Pulvers zu gewährleisten, müssen die Teile vorab gründlich gereinigt werden. Diese Reinigung erfolgt in der Regel durch chemische Entfettung oder mechanische Verfahren wie Sandstrahlen. Es ist von entscheidender Bedeutung, dass die Metalloberflächen frei von Fett, Öl, Rost oder anderen Verunreinigungen sind, da diese die Beschichtung negativ beeinflussen und verhindern könnten, dass das Pulver gleichmäßig haftet.
Nach der Vorbehandlung folgt der Schritt des Pulverauftrags. Das Pulver wird in der Regel mit einer elektrostatischen Sprühtechnik aufgebracht. Dabei wird das Pulver elektrostatisch aufgeladen, während das Werkstück eine entgegengesetzte Ladung erhält. Diese Technik sorgt dafür, dass das Pulver an der Metalloberfläche haftet und eine gleichmäßige Schicht bildet. Der Vorteil dieser Technik liegt in der Möglichkeit, auch schwer zugängliche Stellen wie Gewinde oder Bohrungen gleichmäßig zu beschichten, was bei traditionellen Lackierungsverfahren schwieriger zu erreichen ist.
Nach dem Pulverauftrag müssen die beschichteten Teile in einen Aushärtungsofen eingeführt werden. Der Ofen erhitzt die Werkstücke auf eine Temperatur von etwa 160 bis 200 °C, je nach Art des verwendeten Pulvers. In diesem Schritt schmilzt das Pulver und bildet eine gleichmäßige, schützende Schicht auf der Metalloberfläche. Während des Erhitzens vernetzen sich die Moleküle des Pulvers, wodurch eine stabile, dauerhafte Schicht entsteht, die eine hohe Widerstandsfähigkeit gegenüber mechanischen Belastungen und Umwelteinflüssen bietet.
Die Aushärtung des Pulvers ist ein entscheidender Schritt im Prozess, da die Qualität der Beschichtung von der gleichmäßigen und vollständigen Aushärtung abhängt. Um eine hohe Qualität der Beschichtung zu erreichen, ist eine präzise Temperaturregelung im Ofen erforderlich. Nur so kann sichergestellt werden, dass das Pulver optimal aushärtet und keine unregelmäßigen Beschichtungen oder Verformungen der Teile entstehen.
Nach der Aushärtung erfolgt die Abkühlung der beschichteten Teile. Die Abkühlung muss kontrolliert und gleichmäßig erfolgen, um Risse oder Verformungen der Beschichtung zu vermeiden. Nach dem Abkühlen sind die Teile vollständig ausgehärtet und verfügen über eine robuste, widerstandsfähige Schicht, die sie vor Korrosion, Abrieb und anderen äußeren Einflüssen schützt.
Pulverbeschichtete Schrauben, Bolzen und Nietköpfe bieten eine Vielzahl von Vorteilen, die sie zu einer bevorzugten Wahl für die Oberflächenveredelung in vielen Industrien machen. Die Beschichtung schützt die Teile vor Korrosion, was insbesondere in feuchten oder salzhaltigen Umgebungen von Bedeutung ist. Zudem erhöht die Pulverbeschichtung die Widerstandsfähigkeit der Teile gegenüber mechanischen Belastungen und Abrieb, was ihre Lebensdauer verlängert und die Notwendigkeit für häufige Wartungs- oder Ersatzmaßnahmen reduziert. Ein weiterer Vorteil der Pulverbeschichtung ist ihre Umweltfreundlichkeit. Im Gegensatz zu traditionellen Lackierungen, die oft Lösungsmittel und flüchtige organische Verbindungen (VOCs) enthalten, kommt die Pulverbeschichtung ohne diese schädlichen Substanzen aus. Das Pulver kann zudem oft recycelt werden, was den Materialverbrauch reduziert und die Umwelt schont.
Zusammenfassend lässt sich sagen, dass eine Pulverbeschichtungsanlage für Schrauben, Nietköpfe und Bolzen eine effiziente und umweltfreundliche Methode zur Oberflächenbehandlung von Verbindungselementen darstellt. Der Prozess umfasst mehrere Schritte, beginnend mit der Vorbehandlung der Teile, dem Auftragen des Pulvers, der Aushärtung im Ofen und der anschließenden Abkühlung der Teile. Dieser Prozess sorgt für eine gleichmäßige, langlebige und korrosionsbeständige Beschichtung, die die Funktionalität und Lebensdauer der Teile erheblich erhöht. Die Pulverbeschichtung bietet eine kostengünstige, nachhaltige Lösung für die Veredelung von Verbindungselementen in vielen Industrien.
Pulverbeschichtungsanlage für Schrauben, Nietköpfe u. Bolzen
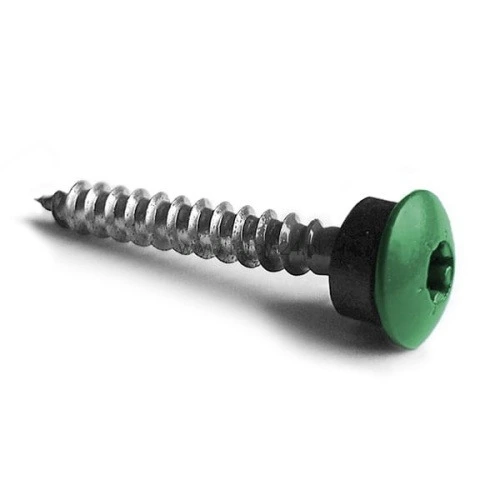
Die Pulverbeschichtung von Schrauben, Nietköpfen und Bolzen ist eine effektive Methode, um diesen Kleinteilen eine haltbare und attraktive Oberflächenbeschichtung zu verleihen. Hier sind die Schritte und Vorteile dieses Prozesses im Detail:
Schritte der Pulverbeschichtung:
- Vorbereitung der Teile: Zuerst müssen die Schrauben, Nietköpfe und Bolzen gründlich gereinigt und vorbehandelt werden. Dies umfasst typischerweise das Entfetten, Spülen und möglicherweise eine Phosphatierung, um die Oberfläche für die Beschichtung vorzubereiten.
- Pulverapplikation: Die vorbereiteten Teile werden in der Pulverbeschichtungsanlage platziert. Das Pulver wird mithilfe eines elektrostatischen Sprühverfahrens auf die Oberfläche der Teile aufgetragen. Die elektrostatische Ladung sorgt dafür, dass das Pulver gleichmäßig an den Teilen haftet, was zu einer gleichmäßigen Beschichtung führt.
- Aushärtung: Nachdem das Pulver aufgetragen wurde, werden die Teile in einem Ofen bei der entsprechenden Temperatur erhitzt. Dabei schmilzt das Pulver und bildet eine dauerhafte Beschichtung auf den Schrauben, Nietköpfen und Bolzen. Die Aushärtezeit und Temperatur sind entscheidend, um eine optimale Haftung und Festigkeit der Beschichtung zu gewährleisten.
- Kühlung und Inspektion: Nach der Aushärtung werden die beschichteten Teile gekühlt und dann einer Inspektion unterzogen, um sicherzustellen, dass die Beschichtung gleichmäßig und fehlerfrei ist.
Vorteile der Pulverbeschichtung:
- Hervorragende Oberflächenqualität: Die Pulverbeschichtung bietet eine glatte, gleichmäßige und attraktive Oberfläche, die Korrosionsschutz und eine ästhetisch ansprechende Optik bietet.
- Umweltfreundlich: Im Vergleich zu anderen Beschichtungsmethoden wie der Nasslackierung enthält die Pulverbeschichtung keine flüchtigen organischen Verbindungen (VOCs) und ist daher umweltfreundlicher.
- Hohe Haltbarkeit: Die Beschichtung ist robust und widerstandsfähig gegenüber Kratzern, Abrieb und Chemikalien, was die Lebensdauer der Teile verlängert.
- Breite Farbauswahl: Pulverbeschichtungen sind in einer Vielzahl von Farben und Oberflächenveredelungen erhältlich, was eine flexible Gestaltung und Anpassung ermöglicht.
- Effiziente Anwendung: Die Verarbeitung von Schrauben, Nietköpfen und Bolzen in einer Pulverbeschichtungsanlage kann automatisiert und effizient durchgeführt werden, was die Produktionskapazität steigert.
Die Pulverbeschichtung ist daher eine bevorzugte Methode für die Oberflächenbehandlung von Schrauben, Nietköpfen und Bolzen in verschiedenen Branchen wie der Automobil-, Möbel- und Baubranche. Sie bietet eine kostengünstige und qualitativ hochwertige Lösung für den Schutz und die Verschönerung dieser wichtigen Kleinteile.
Vorbehandlungssystem
Das Vorbehandlungssystem in einer Pulverbeschichtungsanlage für Schrauben, Nietköpfe und Bolzen ist von entscheidender Bedeutung, da es die Grundlage für eine qualitativ hochwertige Beschichtung bildet. Hier sind die wichtigsten Aspekte eines typischen Vorbehandlungssystems:
- Reinigung: Der erste Schritt im Vorbehandlungsprozess ist die gründliche Reinigung der zu beschichtenden Teile. Dies kann durch Sprühen, Tauchen oder Ultraschallreinigung erfolgen, um Öle, Fette, Schmutz und andere Verunreinigungen zu entfernen. Eine saubere Oberfläche ist entscheidend, um eine gute Haftung des Pulvers zu gewährleisten.
- Entfettung: Nach der Reinigung folgt die Entfettung. Hierbei werden alle verbliebenen Fette und Öle von der Oberfläche der Teile entfernt. Dies kann durch chemische Entfettungsmittel oder spezielle Entfettungsbäder erfolgen. Die Entfettung trägt dazu bei, eine saubere und fettfreie Oberfläche zu schaffen, auf der das Pulver gut haften kann.
- Spülen: Nach der Reinigung und Entfettung werden die Teile gründlich gespült, um alle Rückstände von Reinigungsmitteln oder Verunreinigungen zu entfernen. Ein gründliches Spülen ist wichtig, um sicherzustellen, dass die Oberfläche frei von Rückständen ist, die die Pulverbeschichtung beeinträchtigen könnten.
- Phosphatierung oder Konversionsschichtbildung: Nach dem Spülen können die Teile einer Phosphatierung oder Konversionsschichtbehandlung unterzogen werden. Dieser Prozess trägt dazu bei, die Haftung der Pulverbeschichtung zu verbessern und bietet gleichzeitig einen zusätzlichen Korrosionsschutz.
- Trocknung: Nach der Vorbehandlung müssen die Teile gründlich getrocknet werden, um sicherzustellen, dass keine Feuchtigkeit auf der Oberfläche verbleibt. Eine effektive Trocknung ist entscheidend, um eine optimale Haftung und Qualität der Pulverbeschichtung sicherzustellen.
Ein effizientes Vorbehandlungssystem gewährleistet, dass die Oberfläche der Schrauben, Nietköpfe und Bolzen optimal für die Pulverbeschichtung vorbereitet ist. Eine sorgfältige Durchführung dieses Prozesses trägt dazu bei, eine hochwertige Beschichtung mit guter Haftung, Korrosionsschutz und Ästhetik zu erzielen.
Moderne Pulverbeschichtungsanlagen können oft automatisierte Vorbehandlungssysteme integrieren, die den Prozess optimieren und die Konsistenz der Beschichtung verbessern. Überwachungs- und Steuerungssysteme ermöglichen es, den Vorbehandlungsprozess genau zu überwachen und sicherzustellen, dass die Teile die erforderlichen Qualitätsstandards erfüllen, bevor sie beschichtet werden.
Ein effektives Vorbehandlungssystem ist somit ein wesentlicher Bestandteil jeder Pulverbeschichtungsanlage, um hochwertige und langlebige Beschichtungen auf Schrauben, Nietköpfen und Bolzen zu erzielen.
Pulverapplikationseinheit
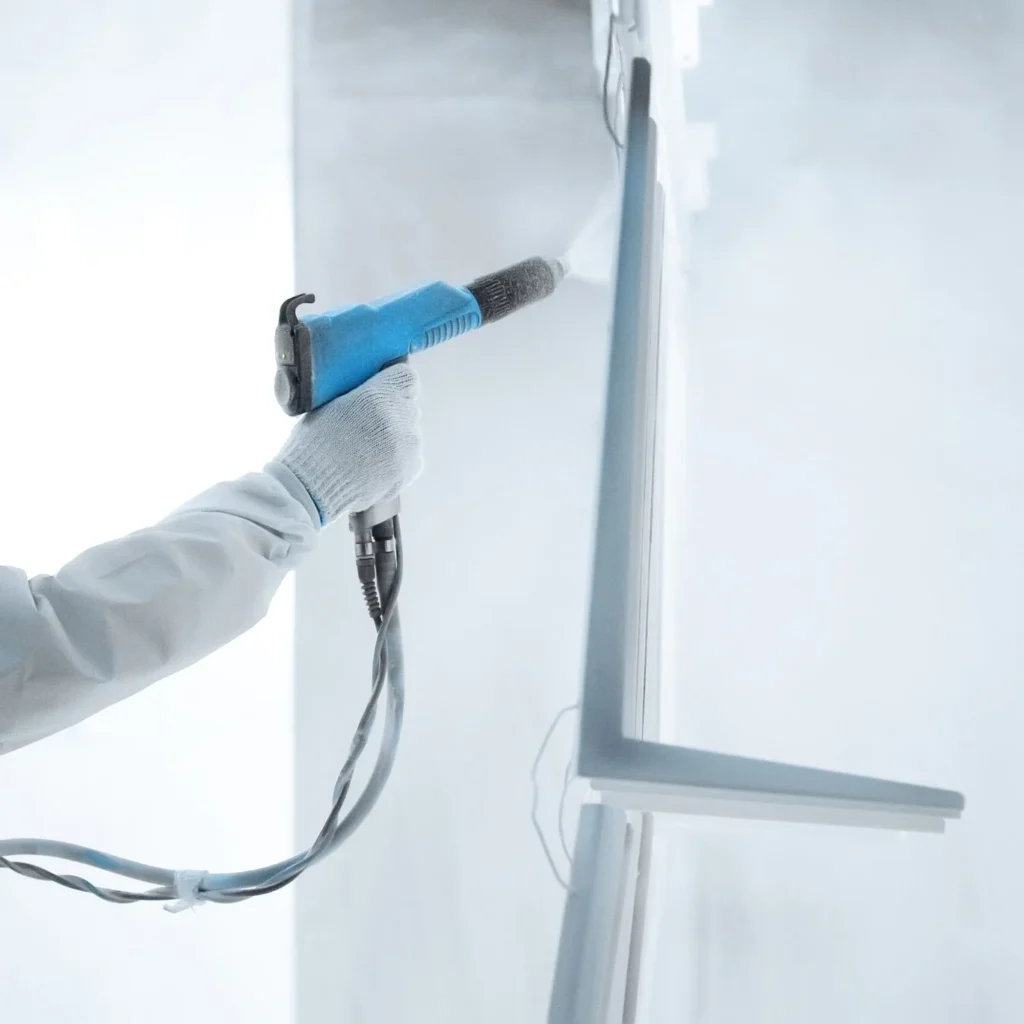
Die Pulverapplikationseinheit ist ein wesentlicher Bestandteil einer Pulverbeschichtungsanlage für Schrauben, Nietköpfe und Bolzen. Diese Einheit ermöglicht die präzise und effiziente Auftragung des Pulverlacks auf die Oberflächen der Kleinteile. Hier sind die wichtigen Aspekte und Funktionen der Pulverapplikationseinheit:
Funktionen der Pulverapplikationseinheit:
- Elektrostatischer Pulverauftrag: In der Pulverapplikationseinheit wird das Pulver durch ein elektrostatisches Sprühverfahren auf die Oberfläche der Schrauben, Nietköpfe und Bolzen aufgetragen. Dabei wird das Pulverpulver mittels elektrischer Ladung positiv aufgeladen, während die Teile geerdet sind. Dies führt zu einer effizienten und gleichmäßigen Verteilung des Pulvers auf den Oberflächen.
- Pulvernebelabscheidung: Die Einheit verfügt über Mechanismen zur Kontrolle und Abscheidung von Pulvernebel, der beim Sprühvorgang entstehen kann. Dies hilft, den Pulververbrauch zu minimieren und eine saubere Arbeitsumgebung zu gewährleisten.
- Justierbare Sprühparameter: Moderne Pulverapplikationseinheiten bieten die Möglichkeit, verschiedene Sprühparameter wie Pulvermenge, Sprühmuster und Luftdruck einzustellen. Dies ermöglicht eine präzise Anpassung an die spezifischen Anforderungen der Beschichtung und der Teile.
- Effizienz und Durchsatz: Die Einheit ist darauf ausgelegt, den Beschichtungsprozess effizient und mit hoher Produktionskapazität durchzuführen. Dies bedeutet eine schnelle Beschichtung der Teile bei gleichzeitig niedrigem Pulververbrauch.
Komponenten der Pulverapplikationseinheit:
- Pulverpistole: Die Pulverpistole ist das zentrale Werkzeug für den Pulverauftrag. Sie enthält die elektrostatische Ladungseinrichtung und den Sprühkopf, der das Pulver gleichmäßig auf die Teile aufträgt.
- Pulverversorgungssystem: Das System umfasst einen Pulverbehälter, aus dem das Pulver zur Pistole gefördert wird. Es kann eine Pulverförderleitung und eine Pulverzufuhrsteuerung umfassen, um eine kontinuierliche Zufuhr des Pulvers sicherzustellen.
- Steuerungseinheit: Die Steuerungseinheit der Pulverapplikationseinheit ermöglicht die Einstellung und Überwachung der Sprühparameter sowie die Integration in den Gesamtprozess der Pulverbeschichtungsanlage.
Vorteile der Pulverapplikationseinheit:
- Gleichmäßige Beschichtung: Durch den elektrostatischen Pulverauftrag wird eine gleichmäßige Beschichtung ohne Tropfenbildung oder Ungleichmäßigkeiten erzielt.
- Hohe Produktivität: Die Einheit ermöglicht eine schnelle Beschichtung großer Mengen von Schrauben, Nietköpfen und Bolzen, was die Produktivität steigert.
- Pulververbrauchsoptimierung: Die präzise Steuerung der Pulvermenge reduziert den Pulververbrauch und spart Kosten.
- Flexibilität: Moderne Pulverapplikationseinheiten bieten Flexibilität in Bezug auf die Anpassung an verschiedene Teilegrößen, Formen und Beschichtungsanforderungen.
Die Pulverapplikationseinheit ist somit ein entscheidender Teil einer effizienten und qualitativ hochwertigen Pulverbeschichtungsanlage für Schrauben, Nietköpfe und Bolzen. Sie trägt dazu bei, eine dauerhafte, attraktive und schützende Oberflächenbeschichtung auf diesen Kleinteilen zu erzielen.
Einbrenn- oder Aushärtungsofen
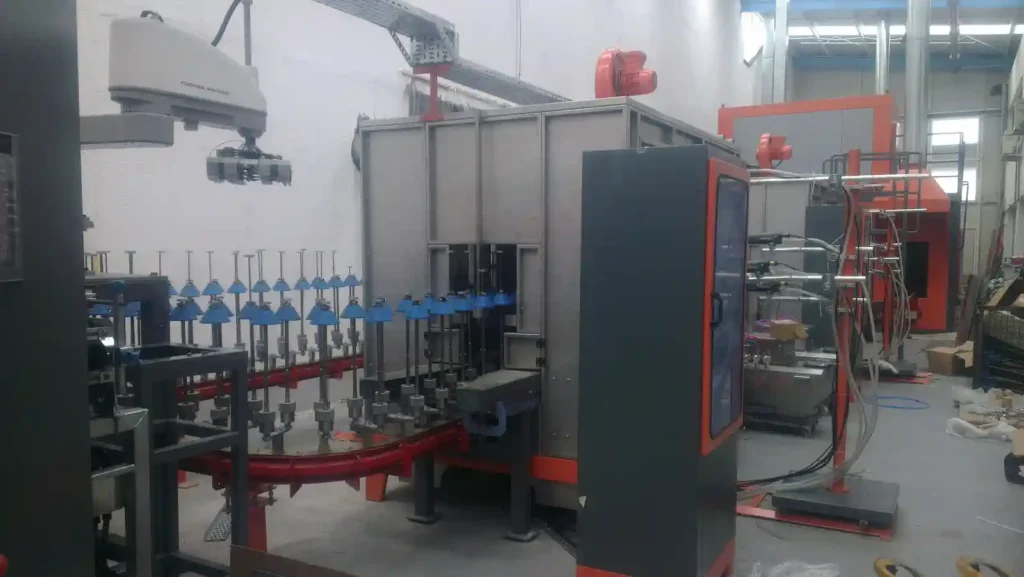
Der Einbrenn- oder Aushärtungsofen spielt eine entscheidende Rolle im Prozess der Pulverbeschichtung von Schrauben, Nietköpfen und Bolzen. Nachdem das Pulver auf die Oberflächen der Teile aufgetragen wurde, müssen sie in einem speziellen Ofen erhitzt werden, um das Pulver zu schmelzen, zu fließen und zu einer dauerhaften Beschichtung zu verbinden. Hier sind die wichtigen Aspekte des Einbrenn- oder Aushärtungsofens:
Funktionsweise des Einbrenn- oder Aushärtungsofens:
- Temperaturkontrolle: Der Ofen ist so konstruiert, dass er eine genau kontrollierte Temperatur aufrechterhalten kann, die ausreichend ist, um das Pulver zu schmelzen und zu aushärten, aber nicht zu hoch, um die Teile zu beschädigen.
- Aushärtezeit: Die Teile verbleiben für eine bestimmte Zeitdauer im Ofen, um sicherzustellen, dass das Pulver vollständig geschmolzen ist und sich zu einer festen Beschichtung auf den Oberflächen der Schrauben, Nietköpfe und Bolzen verbindet. Die Aushärtezeit hängt von der Art des Pulvers und den Herstellerempfehlungen ab.
- Luftzirkulation: Ein guter Einbrennofen verfügt über eine effiziente Luftzirkulation, um eine gleichmäßige Temperaturverteilung im gesamten Ofen sicherzustellen. Dies ist wichtig, um eine konsistente Qualität der Beschichtung zu gewährleisten und Hotspots zu vermeiden.
- Abkühlung: Nach der Aushärtung werden die Teile im Ofen langsam abgekühlt, bevor sie aus dem Ofen entfernt werden. Eine kontrollierte Abkühlung ist wichtig, um eine Verformung der Teile oder Beschädigung der Beschichtung zu verhindern.
Typen von Einbrenn- oder Aushärtungsöfen:
- Konvektionsofen: In einem Konvektionsofen wird die Wärme durch Konvektion erzeugt, wobei warme Luft im Ofen zirkuliert. Dies ermöglicht eine gleichmäßige Erwärmung der Teile.
- Infrarotofen: Ein Infrarotofen verwendet Infrarotstrahlung, um die Teile zu erwärmen. Dies kann zu einer schnelleren Aufheizung und Aushärtung führen, insbesondere bei empfindlichen Teilen.
- Gas- oder Elektroofen: Einbrennöfen können entweder mit Gas oder elektrisch betrieben werden, abhängig von den spezifischen Anforderungen und Verfügbarkeiten vor Ort.
Vorteile des Einbrenn- oder Aushärtungsofens:
- Qualitätsbeschichtung: Der Ofen gewährleistet eine vollständige Aushärtung des Pulvers, was zu einer robusten und haltbaren Beschichtung führt.
- Effizienz: Moderne Einbrennöfen bieten eine schnelle und effiziente Aushärtung, was die Produktivität steigert.
- Kontrollierte Prozessparameter: Die Temperatur- und Zeitparameter können genau kontrolliert werden, um die Qualität der Beschichtung zu optimieren und Ausschuss zu minimieren.
- Vielseitigkeit: Einbrennöfen können für eine Vielzahl von Teilen und Pulverbeschichtungen eingesetzt werden, was ihre Vielseitigkeit in der industriellen Anwendung erhöht.
Der Einbrenn- oder Aushärtungsofen ist somit ein wesentlicher Bestandteil einer Pulverbeschichtungsanlage für Schrauben, Nietköpfe und Bolzen. Er trägt dazu bei, eine hochwertige und langlebige Oberflächenbeschichtung zu erzielen, die den Anforderungen verschiedener Industrien gerecht wird.
Kühleinheit und Handling
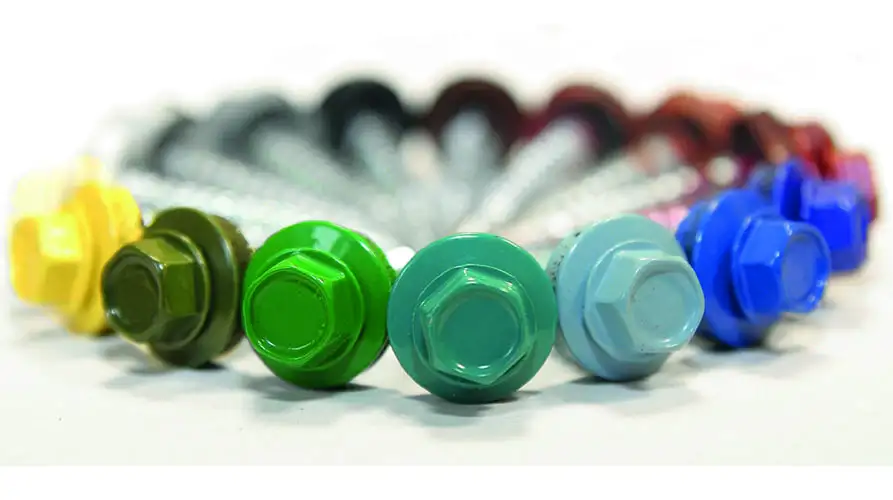
Die Kühleinheit und das Handling sind entscheidende Schritte im Prozess der Pulverbeschichtung von Schrauben, Nietköpfen und Bolzen, die nach dem Aushärtungsprozess im Ofen durchgeführt werden. Diese Schritte dienen dazu, die fertig beschichteten Teile abzukühlen, zu handhaben und für die Weiterverarbeitung oder den Versand vorzubereiten. Hier sind die wichtigen Aspekte der Kühleinheit und des Handlings:
Kühleinheit:
- Kontrollierte Abkühlung: Die Kühleinheit stellt sicher, dass die beschichteten Teile nach dem Aushärtungsprozess im Ofen langsam und kontrolliert abgekühlt werden. Dies ist wichtig, um thermische Spannungen zu minimieren und eine Verformung der Teile zu verhindern.
- Luftzirkulation: Eine effiziente Luftzirkulation in der Kühleinheit sorgt für eine gleichmäßige Abkühlung der Teile und verhindert lokale Überhitzungsbereiche.
- Schnelle Abkühlung: Moderne Kühleinheiten können eine schnelle Abkühlung ermöglichen, um den gesamten Beschichtungsprozess zu beschleunigen und die Produktivität zu steigern.
Handling:
- Entfernung aus dem Ofen: Nach dem Abkühlen werden die Teile aus dem Ofen entnommen. Dies erfordert spezielle Vorkehrungen, um Beschädigungen an den frisch beschichteten Oberflächen zu vermeiden.
- Inspektion: Die Teile werden auf mögliche Defekte oder Unregelmäßigkeiten in der Beschichtung inspiziert, um sicherzustellen, dass die Qualitätsstandards eingehalten werden.
- Verpackung und Lagerung: Die fertig beschichteten Teile werden für den Versand oder die Lagerung vorbereitet. Dies kann das Verpacken in speziellen Behältern oder das Stapeln auf Paletten umfassen, um die Teile vor Beschädigungen zu schützen.
Vorteile der Kühleinheit und des Handlings:
- Qualitätssicherung: Durch eine kontrollierte Abkühlung und sorgfältige Handhabung wird sichergestellt, dass die Beschichtung intakt bleibt und die Teile frei von Defekten sind.
- Effizienz: Ein effektives Handling minimiert die Stillstandszeiten und optimiert den Produktionsfluss.
- Schutz der Beschichtung: Sorgfältige Handhabung minimiert das Risiko von Beschädigungen an den frisch beschichteten Oberflächen während des Verarbeitungs- und Verpackungsprozesses.
- Vorbereitung für den Versand: Ein effizientes Handling bereitet die Teile für den Versand vor, was die Logistik und Lieferkette optimiert.
Die Kühleinheit und das Handling sind somit kritische Schritte in der Gesamtabwicklung der Pulverbeschichtung von Schrauben, Nietköpfen und Bolzen. Durch eine sorgfältige Umsetzung dieser Schritte wird sichergestellt, dass die beschichteten Teile den erforderlichen Qualitätsstandards entsprechen und bereit sind, in verschiedenen Industriezweigen eingesetzt zu werden.
Einführung in die Pulverbeschichtung

Die Pulverbeschichtung ist eine Technik der Oberflächenveredelung, bei der pulverförmige Farben oder Beschichtungsmaterialien auf ein Substrat (meist Metall) aufgetragen werden. Im Gegensatz zu herkömmlichen Flüssigbeschichtungen wird bei der Pulverbeschichtung kein Lösungsmittel verwendet, was die Technik umweltfreundlicher macht. Das Pulver wird auf die Oberfläche des Objekts gesprüht und anschließend erhitzt, wodurch es zu einer glatten und dauerhaften Beschichtung schmilzt.
Pulverbeschichtungen werden hauptsächlich in der Automobil-, Bau- und Möbelindustrie sowie in der Elektronik verwendet. Es ist ein beliebtes Verfahren, da es robuste, widerstandsfähige Beschichtungen bietet, die gegen Kratzer, Korrosion und chemische Einflüsse beständig sind.
1.2. Geschichte der Pulverbeschichtung
Die Pulverbeschichtung wurde in den 1950er Jahren entwickelt und in den 1960er Jahren in der industriellen Produktion populär. Der Wunsch nach einer umweltfreundlicheren und effizienteren Alternative zu traditionellen Flüssigfarben führte zur Entwicklung von Pulverlacken, die ohne Lösungsmittel auskommen. Im Laufe der Jahrzehnte wurde die Technologie kontinuierlich weiterentwickelt, und heute sind Pulverbeschichtungen aus vielen industriellen Anwendungen nicht mehr wegzudenken.
Die Funktionsweise der Pulverbeschichtung
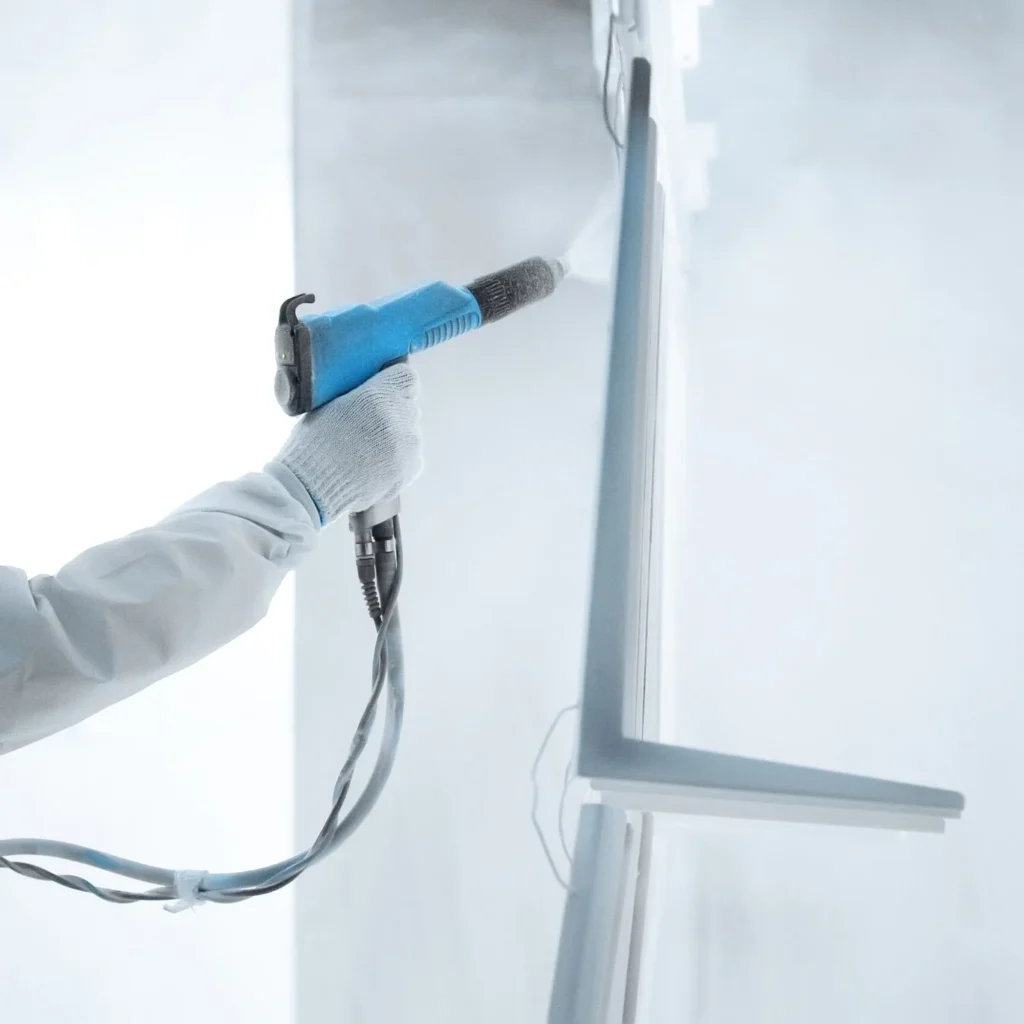
Die Pulverbeschichtung umfasst mehrere wichtige Schritte, die in einem genauen Prozess ablaufen. Jeder Schritt ist entscheidend, um eine gleichmäßige und langlebige Beschichtung zu erreichen.
2.1. Vorbereitung der Oberfläche
Die Vorbereitung der Oberfläche ist ein wesentlicher Schritt, bevor das Pulver aufgetragen werden kann. Eine unzureichende Vorbereitung kann zu schlechter Haftung und Defekten in der Endbeschichtung führen. Der Prozess der Oberflächenvorbereitung umfasst mehrere Schritte:
- Reinigung: Das Entfernen von Schmutz, Öl, Fett, Rost und alten Beschichtungen ist notwendig, um sicherzustellen, dass das Pulver gut haftet. Hierzu werden oft chemische Reiniger oder Entfetter verwendet.
- Strahlen oder Schleifen: Um eine optimale Haftung des Pulvers zu gewährleisten, wird die Oberfläche oft sandgestrahlt oder geschliffen, um eine raue Textur zu schaffen, die das Pulver besser haften lässt.
- Vorbehandlung: Metalloberflächen werden häufig vorbehandelt, z.B. durch Phosphatierung oder Chromatierung, um Korrosion zu verhindern und die Haftung zu verbessern.
2.2. Auftragen des Pulvers
Das Auftragen des Pulvers erfolgt mittels eines elektrostatischen Sprühsystems. Das Pulverlackierverfahren funktioniert auf der Basis von elektrostatischen Kräften:
- Pulversprühpistole: Das Pulver wird durch eine Sprühpistole auf das Werkstück aufgetragen. Die Pistole lädt die Pulverpartikel elektrostatisch auf, während das zu beschichtende Objekt geerdet wird. Dies führt dazu, dass das Pulver durch elektrostatische Anziehung gleichmäßig auf der Oberfläche haftet.
- Automatische und manuelle Beschichtungsverfahren: Je nach Anwendung und Produktionsumgebung können automatische Sprühanlagen oder manuelle Pistolen verwendet werden. Automatische Systeme bieten eine höhere Effizienz bei der Massenproduktion, während manuelle Systeme flexibler und für kleinere Serien oder komplexe Geometrien geeignet sind.
2.3. Einbrennen des Pulvers im Pulverofen
Nach dem Auftragen des Pulvers wird das beschichtete Werkstück in einen Pulverofen gebracht, um das Pulver zu schmelzen und aushärten zu lassen. Dieser Vorgang, der als „Aushärtung“ bezeichnet wird, sorgt dafür, dass das Pulver eine feste, haltbare und glatte Schicht auf dem Werkstück bildet.
- Temperatur und Zeit: Typische Temperaturen für das Einbrennen von Pulverlacken liegen zwischen 150°C und 200°C, und die Aushärtezeit beträgt in der Regel 10 bis 20 Minuten. Diese Parameter variieren jedoch je nach Art des verwendeten Pulvers und der Materialstärke des Werkstücks.
- Verschiedene Ofentypen: Es gibt verschiedene Arten von Öfen für die Pulverbeschichtung, darunter konventionelle Umluftöfen, Infrarotöfen und Gasöfen. Jeder Typ hat seine eigenen Vorteile und ist für bestimmte Anwendungen besser geeignet.
Typen von Pulverbeschichtungen

Es gibt verschiedene Arten von Pulverbeschichtungen, die je nach Anwendung und gewünschten Eigenschaften ausgewählt werden. Die zwei Haupttypen von Pulverbeschichtungen sind Thermoplaste und Duroplaste.
3.1. Thermoplastische Pulverbeschichtungen
Thermoplaste sind Kunststoffe, die beim Erhitzen schmelzen und beim Abkühlen wieder fest werden, ohne dass eine chemische Veränderung stattfindet. Zu den thermoplastischen Pulverbeschichtungen gehören:
- Polyethylen (PE): Wird oft für Beschichtungen auf Metallteilen verwendet, die Flexibilität und Schlagfestigkeit erfordern.
- Polyamid (PA): Wird häufig in der Automobilindustrie eingesetzt, da es eine hohe Beständigkeit gegen Chemikalien und Abrieb aufweist.
- Polyvinylchlorid (PVC): Bietet hervorragende Korrosionsbeständigkeit und wird in der Elektro- und Bauindustrie verwendet.
3.2. Duroplastische Pulverbeschichtungen
Duroplaste, auch als „härtende“ Kunststoffe bekannt, durchlaufen eine chemische Reaktion während des Aushärtens, die irreversible Verbindungen bildet. Die häufigsten duroplastischen Beschichtungen sind:
- Epoxidharze: Bieten eine ausgezeichnete Haftung und chemische Beständigkeit und werden häufig für industrielle Beschichtungen und Korrosionsschutz verwendet.
- Polyester: Diese Beschichtungen sind UV-beständig und eignen sich ideal für Außenanwendungen wie Geländer, Fensterrahmen und Möbel.
- Acrylpulver: Wird verwendet, wenn eine glatte, glänzende Oberfläche benötigt wird. Diese Pulverbeschichtungen bieten eine hervorragende Witterungsbeständigkeit und werden häufig in der Automobilindustrie eingesetzt.
Pulveranlagen: Aufbau und Funktionsweise
Pulveranlagen sind technische Anlagen, die speziell für die Durchführung von Pulverbeschichtungsprozessen konzipiert sind. Sie bestehen aus mehreren Komponenten, die gemeinsam eine effiziente und sichere Durchführung des Beschichtungsprozesses gewährleisten.
4.1. Komponenten einer Pulveranlage
Eine typische Pulveranlage umfasst die folgenden Hauptkomponenten:
- Pulversprühsystem: Besteht aus der Pulversprühpistole, dem Pulverbehälter und dem Zufuhrsystem, das das Pulver zur Pistole führt.
- Fördertechnik: Förderbänder oder Schienensysteme transportieren die Werkstücke durch die verschiedenen Stationen der Anlage, von der Vorbehandlung über die Beschichtung bis zum Aushärten im Ofen.
- Pulverrückgewinnungssysteme: Diese Systeme fangen überschüssiges Pulver auf, das nicht auf das Werkstück aufgetragen wurde, und führen es dem Prozess wieder zu. Dies erhöht die Effizienz und reduziert den Materialverbrauch.
- Steuerungssysteme: Moderne Pulveranlagen sind oft mit computergesteuerten Systemen ausgestattet, die den gesamten Prozess überwachen und steuern. Dies ermöglicht eine präzise Steuerung von Parametern wie Sprühmenge, Luftdruck, Temperatur und Aushärtezeit.
4.2. Automatische und manuelle Pulveranlagen
Es gibt sowohl automatische als auch manuelle Pulveranlagen, die je nach Produktionsvolumen und spezifischen Anforderungen der Beschichtung eingesetzt werden.
- Automatische Pulveranlagen: Diese Systeme sind ideal für die Massenproduktion, da sie eine gleichmäßige Beschichtung mit minimalem Arbeitsaufwand ermöglichen. Sie verwenden Roboterarme oder fest montierte Sprühsysteme, um die Pulverbeschichtung automatisch auf die Werkstücke aufzutragen.
- Manuelle Pulveranlagen: Diese Anlagen sind flexibler und eignen sich besser für kleinere Serien oder Einzelstücke. Der Bediener hat mehr Kontrolle über den Beschichtungsprozess und kann auf komplexe Geometrien oder spezifische Anforderungen eingehen.
5. Pulveröfen: Arten und Funktionsweise
Pulveröfen spielen eine zentrale Rolle im Pulverbeschichtungsprozess, da sie das Pulver erhitzen und die chemische Reaktion einleiten, die für die Bildung einer harten, beständigen Beschichtung erforderlich ist. Es gibt verschiedene Arten von Öfen, die je nach Anwendungsanforderungen und Produktionsumgebung verwendet werden.
5.1. Arten von Pulveröfen
Es gibt mehrere Arten von Öfen, die in der Pulverbeschichtung verwendet werden, darunter:
- Konvektionsöfen: Diese Öfen verwenden heiße Luft, die gleichmäßig durch den Ofen zirkuliert, um das Pulver zu erhitzen. Konvektionsöfen sind die gebräuchlichste Art von Pulveröfen und eignen sich für eine Vielzahl von Anwendungen.
- Infrarotöfen: Infrarotstrahler erhitzen das Pulver schnell, indem sie elektromagnetische Strahlung abgeben, die direkt auf die Oberfläche des Werkstücks wirkt. Diese Art von Ofen eignet sich besonders für schnelle Produktionszyklen oder dünnwandige Teile.
- Gasöfen: Gasbefeuerte Öfen sind oft energieeffizienter und kostengünstiger im Betrieb als elektrische Öfen. Sie sind ideal für große Produktionsanlagen, in denen eine hohe Wärmeleistung erforderlich ist.
- Kombinationsöfen: Diese Öfen kombinieren Konvektions- und Infrarottechnologien, um die Vorteile beider Systeme zu nutzen. Sie bieten eine schnelle Erwärmung und gleichmäßige Wärmeverteilung und sind besonders effizient.
5.2. Aushärteprozess in Pulveröfen
Der Aushärteprozess in einem Pulverofen ist entscheidend für die Bildung der Beschichtung. Wenn das beschichtete Werkstück in den Ofen kommt, schmilzt das Pulver allmählich und vernetzt sich chemisch zu einer festen Schicht. Die Temperatur und die Dauer des Aushärtens hängen von der Art des Pulvers und dem Material des Werkstücks ab.
- Typische Aushärtetemperaturen: Pulverlacke werden in der Regel bei Temperaturen zwischen 150°C und 200°C ausgehärtet. Zu niedrige Temperaturen können dazu führen, dass das Pulver nicht vollständig schmilzt, während zu hohe Temperaturen das Werkstück beschädigen können.
- Aushärtezeit: Die Aushärtezeit liegt normalerweise zwischen 10 und 20 Minuten, kann aber je nach Größe und Dicke des Werkstücks sowie der Art des Pulvers variieren. Eine längere Aushärtezeit kann erforderlich sein, um eine vollständige Vernetzung zu gewährleisten und die mechanischen Eigenschaften der Beschichtung zu maximieren.
5.3. Energieeffizienz von Pulveröfen
Moderne Pulveröfen sind oft darauf ausgelegt, den Energieverbrauch zu minimieren. Gasöfen bieten in der Regel eine höhere Energieeffizienz im Vergleich zu elektrisch betriebenen Öfen. Einige Öfen sind zudem mit Wärmerückgewinnungssystemen ausgestattet, die die Abwärme aus dem Aushärtungsprozess nutzen, um den Energieverbrauch weiter zu senken.
6. Vorteile der Pulverbeschichtung
Die Pulverbeschichtung bietet gegenüber herkömmlichen Flüssiglackierverfahren zahlreiche Vorteile. Diese Vorteile betreffen nicht nur die Qualität und Haltbarkeit der Beschichtung, sondern auch Umweltaspekte und Kosteneffizienz.
6.1. Umweltfreundlichkeit
Einer der größten Vorteile der Pulverbeschichtung ist ihre Umweltfreundlichkeit. Da Pulverbeschichtungen keine Lösungsmittel enthalten, werden keine flüchtigen organischen Verbindungen (VOCs) freigesetzt, die zu Luftverschmutzung beitragen können. Dies macht Pulverbeschichtungen zu einer umweltfreundlichen Alternative zu herkömmlichen Flüssiglacken.
- Weniger Abfall: Das überschüssige Pulver kann aufgefangen und wiederverwendet werden, was den Materialverbrauch reduziert und Abfall minimiert.
- Sicher für Arbeiter: Da keine Lösungsmittel verwendet werden, sind Pulverbeschichtungen auch sicherer für die Arbeiter, da keine giftigen Dämpfe freigesetzt werden, die eingeatmet werden könnten.
6.2. Haltbarkeit und Widerstandsfähigkeit
Pulverbeschichtungen bieten eine extrem widerstandsfähige Oberfläche, die gegen Abnutzung, Kratzer, Korrosion und chemische Einflüsse beständig ist. Diese Eigenschaften machen Pulverbeschichtungen besonders attraktiv für industrielle Anwendungen, bei denen Langlebigkeit und Widerstandsfähigkeit entscheidend sind.
- Korrosionsschutz: Pulverbeschichtungen bieten einen hervorragenden Korrosionsschutz, der sie ideal für Anwendungen im Außenbereich macht, z.B. bei Möbeln, Fassaden und Fahrzeugen.
- Beständigkeit gegen Chemikalien: Pulverbeschichtungen sind auch gegen viele Chemikalien beständig, was sie zu einer idealen Wahl für industrielle Anlagen und Maschinen macht, die aggressiven Substanzen ausgesetzt sind.
6.3. Kosteneffizienz
Obwohl die Anschaffung von Pulveranlagen und Öfen zunächst mit höheren Kosten verbunden ist, amortisieren sich diese Investitionen schnell aufgrund der zahlreichen Kosteneinsparungen, die die Pulverbeschichtung bietet:
- Materialeinsparungen: Dank der Möglichkeit, überschüssiges Pulver wiederzuverwenden, werden Materialkosten gesenkt.
- Weniger Nacharbeiten: Da Pulverbeschichtungen eine gleichmäßige und hochwertige Oberfläche bieten, sind weniger Nacharbeiten oder Korrekturen erforderlich.
- Längere Lebensdauer: Die Haltbarkeit der Beschichtung reduziert die Notwendigkeit für häufige Wartung oder Neubeschichtung, was langfristig Kosten spart.
6.4. Ästhetische Vielfalt
Pulverbeschichtungen bieten eine breite Palette an Farben und Texturen. Im Gegensatz zu Flüssiglacken, die oft in ihrer Farbauswahl begrenzt sind, können Pulverbeschichtungen in nahezu jeder gewünschten Farbe hergestellt werden, einschließlich Glanz-, Matt- und Metallic-Finishes. Auch strukturierte Beschichtungen wie Hammerschlag oder Samtoberflächen sind problemlos umsetzbar.
- UV-Beständigkeit: Polyesterpulverlacke bieten eine hervorragende UV-Beständigkeit und sind ideal für den Einsatz im Außenbereich, da sie nicht verblassen oder vergilben.
- Glatte oder strukturierte Oberflächen: Pulverbeschichtungen ermöglichen es, eine Vielzahl von Oberflächenstrukturen zu erzielen, von glatten und glänzenden bis hin zu rauen und strukturierten Oberflächen.
7. Anwendungsgebiete der Pulverbeschichtung
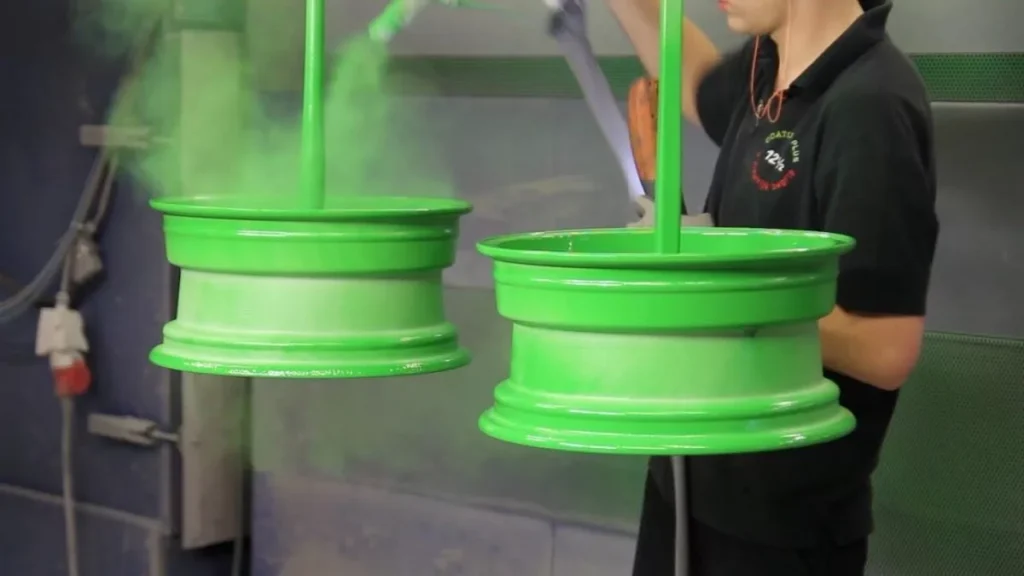
Die Pulverbeschichtung wird in einer Vielzahl von Branchen und Anwendungen eingesetzt. Ihre Vielseitigkeit und Haltbarkeit machen sie zur idealen Wahl für eine breite Palette von Projekten, von industriellen Maschinen bis hin zu Konsumgütern.
7.1. Automobilindustrie
Die Automobilindustrie ist einer der größten Anwender von Pulverbeschichtungen. Fahrzeugteile wie Felgen, Fahrgestelle, Stoßstangen und Außenverkleidungen werden oft mit Pulverbeschichtungen behandelt, um sie vor Korrosion und Verschleiß zu schützen. Pulverbeschichtungen bieten auch die Möglichkeit, Fahrzeugteile in einer Vielzahl von Farben und Oberflächenstrukturen zu gestalten.
7.2. Architektur und Bauwesen
Im Bauwesen werden Pulverbeschichtungen für die Beschichtung von Metallkonstruktionen, Fassaden, Türen, Fensterrahmen und Geländern verwendet. Ihre Witterungsbeständigkeit und Korrosionsschutz machen sie ideal für Anwendungen im Außenbereich. Außerdem bieten Pulverbeschichtungen eine große Farbauswahl, was Architekten und Designern zusätzliche Flexibilität bei der Gestaltung von Gebäuden gibt.
7.3. Möbelindustrie
Die Möbelindustrie verwendet Pulverbeschichtungen, um Metallmöbel vor Korrosion zu schützen und ihnen ein ästhetisch ansprechendes Aussehen zu verleihen. Gartenmöbel, Büromöbel und Designermöbel profitieren gleichermaßen von der Langlebigkeit und Widerstandsfähigkeit der Pulverbeschichtung.
7.4. Haushaltsgeräte
Viele Haushaltsgeräte, wie Waschmaschinen, Kühlschränke und Öfen, werden mit Pulverbeschichtungen versehen, um sie vor Abnutzung und Korrosion zu schützen. Pulverbeschichtungen bieten nicht nur Schutz, sondern auch ein attraktives Finish, das in einer Vielzahl von Farben und Oberflächen erhältlich ist.
7.5. Elektronikindustrie
In der Elektronikindustrie werden Pulverbeschichtungen oft für Gehäuse und Komponenten verwendet, die Schutz vor elektromagnetischen Störungen (EMI) bieten müssen. Pulverbeschichtungen schützen die empfindlichen elektronischen Komponenten vor äußeren Einflüssen und tragen zur Langlebigkeit der Produkte bei.
8. Zukunft der Pulverbeschichtungstechnologie
Die Technologie der Pulverbeschichtung entwickelt sich kontinuierlich weiter, um den Anforderungen moderner Industrieprozesse gerecht zu werden. Nachhaltigkeit, Effizienz und neue Materialien sind zentrale Treiber der technologischen Weiterentwicklung.
8.1. Nachhaltigkeit und Umweltbewusstsein
Mit zunehmendem Fokus auf Umweltschutz wird die Pulverbeschichtung weiterhin als bevorzugte Alternative zu Flüssiglacken an Bedeutung gewinnen. Forscher arbeiten kontinuierlich an der Entwicklung neuer Pulverformeln, die noch umweltfreundlicher sind, indem sie den Energieverbrauch und die Produktionsabfälle weiter reduzieren.
8.2. Fortschritte in der Materialwissenschaft
Die Entwicklung neuer Beschichtungsmaterialien bietet der Pulverbeschichtungstechnologie großes Potenzial. Die Einführung von Nanopartikeln in Pulverlacke könnte beispielsweise zu noch widerstandsfähigeren und leistungsfähigeren Beschichtungen führen, die überlegene Eigenschaften in Bezug auf Kratzfestigkeit, UV-Beständigkeit und Selbstreinigung bieten.
8.3. Digitalisierung und Automatisierung
Moderne Produktionsanlagen werden zunehmend automatisiert und digitalisiert. Dies gilt auch für Pulverbeschichtungsanlagen, die mit fortschrittlichen Steuerungssystemen und Robotik ausgestattet sind, um den Beschichtungsprozess noch effizienter und präziser zu gestalten. Datenanalyse und Sensorik ermöglichen es, die Qualität in Echtzeit zu überwachen und den Energieverbrauch zu optimieren.
9. Fazit
Die Pulverbeschichtung ist eine vielseitige und kosteneffiziente Methode zur Oberflächenveredelung, die in vielen Branchen breite Anwendung findet. Sie bietet Vorteile in Bezug auf Umweltfreundlichkeit, Langlebigkeit, Ästhetik und Kosteneinsparungen. Pulveranlagen und Pulveröfen sind wesentliche Bestandteile dieses Verfahrens und tragen maßgeblich zur Qualität und Effizienz des Beschichtungsprozesses bei.
Mit kontinuierlichen technologischen Fortschritten in Bereichen wie Nachhaltigkeit, Automatisierung und Materialwissenschaft bleibt die Pulverbeschichtung eine führende Technik in der Oberflächenveredelung und wird auch in Zukunft eine entscheidende Rolle in der industriellen Fertigung spielen.
Eine Pulverbeschichtungsanlage und eine Kopflackierungsanlage für Schrauben sind essenzielle Einrichtungen zur Veredelung und Beschichtung von Verbindungselementen wie Schrauben, Bolzen oder Muttern. Diese Anlagen ermöglichen es, die Oberflächen dieser Bauteile mit einer Schutz- und/oder Dekorschicht zu versehen, um Korrosionsschutz, Verschleißfestigkeit und eine ansprechende Optik zu gewährleisten.
Pulverbeschichtungsanlagen arbeiten mit einem trockenen Pulverlack, der aus feinen Partikeln besteht. Diese Partikel werden in der Regel durch ein elektrostatisches Verfahren auf die Schrauben aufgetragen. Dabei werden die Schrauben zuerst gründlich gereinigt, entfettet und vorbehandelt, um eine optimale Haftung des Pulvers zu gewährleisten. Anschließend wird das Pulverlackpulver elektrostatisch aufgeladen und auf die Schrauben gesprüht. Die elektrostatische Ladung sorgt dafür, dass das Pulver gleichmäßig an der Metalloberfläche haftet. Im nächsten Schritt werden die beschichteten Schrauben in einen Einbrennofen transportiert, wo das Pulver bei Temperaturen von etwa 160 bis 200 Grad Celsius schmilzt und eine homogene, harte Schicht bildet. Dieses Verfahren ist umweltfreundlich, da es kaum Lösemittel benötigt, und es bietet eine hohe Flexibilität in Bezug auf Farbgestaltung und Schichtdicke.
Die Kopflackierungsanlage hingegen ist speziell darauf ausgelegt, die Köpfe der Schrauben gezielt zu lackieren. Dies ist besonders dann von Bedeutung, wenn der Schraubenkopf sichtbar bleibt und eine dekorative Funktion erfüllen soll, beispielsweise bei Möbeln, Fahrzeugen oder Designprodukten. Die Kopflackierung kann durch Sprühverfahren, Tauchlackierung oder durch ein Rotationsverfahren erfolgen, bei dem der Schraubenkopf in die Lackierzone eingeführt wird. Diese Anlagen erlauben es, präzise und wirtschaftlich Lackschichten aufzutragen, ohne die Gewinde oder andere Funktionsbereiche der Schrauben zu beeinträchtigen. Je nach Anforderung können verschiedene Lackarten verwendet werden, darunter wasserbasierte, lösemittelbasierte oder UV-härtende Lacke.
Ein großer Vorteil dieser Technologien besteht darin, dass sie sowohl technische als auch ästhetische Anforderungen erfüllen können. Die Beschichtungen schützen die Schrauben nicht nur vor äußeren Einflüssen wie Feuchtigkeit, Chemikalien oder UV-Strahlung, sondern bieten auch eine Möglichkeit, Schrauben individuell zu gestalten und an spezifische Kundenwünsche anzupassen. Dies ist besonders wichtig in Branchen wie der Automobilindustrie, dem Bauwesen oder der Elektronik, wo höchste Qualitätsstandards gefragt sind.
Zusammenfassend lässt sich sagen, dass Pulverbeschichtungs- und Kopflackierungsanlagen für Schrauben eine unverzichtbare Rolle in der modernen Fertigung spielen. Sie kombinieren Effizienz, Vielseitigkeit und Umweltfreundlichkeit und tragen dazu bei, die Lebensdauer und Funktionalität der beschichteten Verbindungselemente erheblich zu steigern.
Die Implementierung von Pulverbeschichtungs- und Kopflackierungsanlagen in der Fertigung ermöglicht nicht nur eine höhere Produktqualität, sondern auch eine verbesserte Produktionsgeschwindigkeit und -kostenkontrolle. Die Automatisierung dieser Prozesse spielt hierbei eine Schlüsselrolle. Mit modernen Anlagen können große Mengen an Schrauben in kurzer Zeit beschichtet werden, was die Produktionskapazität steigert und gleichzeitig den Bedarf an manueller Arbeit verringert. Automatisierte Fördersysteme, präzise Steuerungen der Lackierapplikation und optimierte Trocknungsprozesse sorgen dafür, dass die Schrauben gleichmäßig und effizient behandelt werden, ohne dass die Qualität darunter leidet.
Ein weiterer Vorteil ist die Möglichkeit der Prozesskontrolle und Qualitätsüberwachung. In vielen modernen Anlagen kommen hochentwickelte Sensoren und Kamerasysteme zum Einsatz, die eine kontinuierliche Überwachung der Beschichtungsdicke und -qualität ermöglichen. Dies garantiert, dass alle Schrauben die festgelegten Standards erfüllen, was insbesondere in kritischen Industrien wie der Luftfahrt oder der Medizintechnik von entscheidender Bedeutung ist. Zusätzlich können Protokolle erstellt werden, die die Einhaltung von Normen und Vorschriften nachweisen und somit für Transparenz und Vertrauen bei den Kunden sorgen.
Die Effizienz dieser Anlagen hat auch positive Auswirkungen auf die Nachhaltigkeit der Produktion. Da Pulverbeschichtungen in der Regel ohne Lösungsmittel auskommen, entfallen umweltschädliche Emissionen, die bei herkömmlichen Lackierverfahren entstehen könnten. Zudem kann überschüssiges Pulver in vielen Fällen wiederverwendet werden, wodurch Materialverschwendung reduziert wird. Auch der Energieverbrauch wird durch moderne Trocknungssysteme und Wärmerückgewinnungstechnologien minimiert.
Neben den praktischen Aspekten der Fertigung bieten Pulverbeschichtungs- und Kopflackierungsanlagen den Herstellern die Flexibilität, Schrauben und andere Verbindungselemente an die Anforderungen der jeweiligen Branche oder des Endkunden anzupassen. In der Möbelindustrie können beispielsweise spezielle Farbtöne oder Effekte erzeugt werden, die das Design des Produkts unterstreichen. In der Automobilindustrie sind oft individuelle Lackierungen erforderlich, um Fahrzeugkomponenten in spezifischen Farben oder mit besonderen Oberflächeneffekten auszustatten.
Die Anpassungsfähigkeit dieser Anlagen geht jedoch über die ästhetischen Anforderungen hinaus. In vielen Fällen erfordern spezielle Anwendungen auch funktionale Beschichtungen, die zusätzlich zu den dekorativen Aspekten eine technische Bedeutung haben. Beispielsweise können Schrauben für den Einsatz in korrosiven Umgebungen mit speziellen Pulverbeschichtungen ausgestattet werden, die ihre Beständigkeit gegenüber Rost und chemischen Einflüssen erhöhen. Weitere Funktionen wie eine verbesserte Griffigkeit oder der Schutz vor Abrieb können ebenfalls durch die Wahl des richtigen Lackes oder der Pulverbeschichtung erzielt werden.
Zusammenfassend lässt sich sagen, dass Pulverbeschichtungs- und Kopflackierungsanlagen für Schrauben nicht nur aus technischer Sicht eine wertvolle Investition darstellen, sondern auch aus wirtschaftlicher und ökologischer Perspektive. Sie bieten eine effiziente, umweltfreundliche und kostengünstige Möglichkeit, Schrauben zu veredeln und an die spezifischen Anforderungen verschiedenster Industrien anzupassen. Durch kontinuierliche Weiterentwicklungen in der Technologie werden diese Anlagen noch leistungsfähiger und flexibler, was sie zu einem unverzichtbaren Bestandteil in der modernen Fertigung von Verbindungselementen macht.
Automatisierung und Effizienzsteigerung
Die Automatisierung von Pulverbeschichtungs- und Kopflackierungsanlagen hat eine signifikante Effizienzsteigerung in der Fertigung zur Folge. Roboter und Fördersysteme übernehmen den Transport der Schrauben durch verschiedene Prozessphasen – von der Vorbehandlung über die Beschichtung bis hin zum Trocknen. Automatisierte Applikationssysteme sorgen dafür, dass das Pulverbeschichten und Lackieren präzise und gleichmäßig erfolgt, wodurch Fehler und Ausschuss minimiert werden. Die genaue Steuerung der Beschichtungsdicke durch moderne Software und Sensoren optimiert den Materialverbrauch und reduziert Abfall. Auch die Trocknungszeiten und -temperaturen werden durch smarte Steuerungssysteme geregelt, was zu einer schnelleren Durchlaufzeit und höheren Produktionskapazität führt.
Qualitätskontrolle und Prozessüberwachung
Die Qualität der beschichteten Schrauben ist von höchster Bedeutung, insbesondere in Anwendungen, in denen die Schrauben eine tragende oder sicherheitsrelevante Funktion haben. Daher ist eine kontinuierliche Qualitätskontrolle unerlässlich. In modernen Anlagen werden dafür hochentwickelte Kamerasysteme und Sensoren eingesetzt, die während des gesamten Beschichtungsprozesses die Oberflächenqualität überwachen. Diese Systeme können Fehler wie ungleichmäßige Beschichtungen, Blasen oder Staubeinschlüsse frühzeitig erkennen und sofort Korrekturmaßnahmen einleiten. Zudem ermöglichen digitale Protokollierungen eine lückenlose Rückverfolgbarkeit, die für Zertifizierungen und Audits erforderlich ist. Eine solche Qualitätssicherung trägt nicht nur zur Erfüllung der Industriestandards bei, sondern stärkt auch das Vertrauen der Kunden in die Langlebigkeit und Sicherheit der Produkte.
Nachhaltigkeit und Umweltfreundlichkeit
Die Nachfrage nach umweltfreundlichen Fertigungslösungen nimmt kontinuierlich zu, und Pulverbeschichtungs- sowie Kopflackierungsanlagen bieten hier erhebliche Vorteile. Da Pulverlacke keine Lösungsmittel enthalten, entfallen schädliche Emissionen, die bei herkömmlichen Lackierverfahren entstehen könnten. Darüber hinaus ist Pulverlack in der Regel vollständig recycelbar – überschüssiges oder abfallendes Pulver kann wiederverwendet werden, was den Materialverbrauch optimiert und die Abfallmenge reduziert. In vielen modernen Anlagen werden auch energieeffiziente Heizsysteme eingesetzt, die den Energieverbrauch beim Trocknen der Beschichtung minimieren. So trägt die Verwendung von Pulverbeschichtungs- und Lackierungsanlagen nicht nur zur Steigerung der Produktqualität bei, sondern auch zur Verbesserung der ökologischen Bilanz des Unternehmens.
Anpassungsfähigkeit und Vielseitigkeit
Ein weiterer bedeutender Vorteil der Pulverbeschichtungs- und Kopflackierungsanlagen ist ihre hohe Anpassungsfähigkeit an verschiedene Branchenanforderungen. Schrauben werden in einer Vielzahl von Anwendungen verwendet – von der Automobilindustrie über die Möbelproduktion bis hin zur Medizintechnik. In jedem dieser Bereiche können die Beschichtungsanforderungen stark variieren, sei es in Bezug auf Farbe, Oberflächenstruktur oder Schutzfunktionen. Moderne Anlagen ermöglichen es, verschiedene Lackarten und Pulversysteme zu verwenden, um den individuellen Anforderungen gerecht zu werden. So können beispielsweise spezielle Korrosionsschutzbeschichtungen für den Einsatz im Außenbereich, farbige Beschichtungen für dekorative Anwendungen oder auch rutschhemmende Oberflächen für mechanische Anwendungen realisiert werden.
Anwendung in verschiedenen Industrien
Pulverbeschichtungs- und Kopflackierungsanlagen finden in einer breiten Palette von Industrien Anwendung. In der Automobilindustrie sind beispielsweise Schrauben, die sowohl funktional als auch ästhetisch ansprechend sein müssen, von großer Bedeutung. Hier kommen Pulverbeschichtungen zum Einsatz, um sowohl Korrosionsschutz als auch visuelle Anforderungen zu erfüllen. In der Möbelindustrie wiederum ist es oft wichtig, Schraubenköpfe in bestimmten Farben oder mit speziellen Oberflächeneffekten zu lackieren, um das Design des Endprodukts zu ergänzen. Auch in der Medizintechnik, wo höchste Anforderungen an die Hygiene und Materialbeständigkeit gestellt werden, ist die Pulverbeschichtung eine ideale Lösung, um Schrauben vor chemischen Einflüssen zu schützen und gleichzeitig eine glatte, leicht zu reinigende Oberfläche zu bieten.
Zukunftsperspektiven und Weiterentwicklungen
Die Technologie von Pulverbeschichtungs- und Kopflackierungsanlagen hat sich in den letzten Jahren rasant weiterentwickelt, und auch in Zukunft wird mit weiteren Innovationen zu rechnen sein. Es wird erwartet, dass neue, umweltfreundlichere Pulverbeschichtungsoptionen auf den Markt kommen, die noch geringere Emissionen verursachen und gleichzeitig verbesserte Materialeigenschaften bieten. Auch die Automatisierung wird weiter zunehmen – durch den Einsatz von Künstlicher Intelligenz und maschinellem Lernen könnte der gesamte Prozess optimiert werden, von der Vorbehandlung bis hin zur Lackierung und Qualitätskontrolle. Die Weiterentwicklung von digitalen Steuerungssystemen wird zudem die Flexibilität und Anpassungsfähigkeit der Anlagen weiter steigern, sodass diese für noch spezifischere Anforderungen genutzt werden können.
Insgesamt lässt sich sagen, dass Pulverbeschichtungs- und Kopflackierungsanlagen eine Schlüsselrolle in der modernen Fertigung von Schrauben spielen. Sie bieten zahlreiche Vorteile in Bezug auf Qualität, Effizienz und Umweltfreundlichkeit und sind sowohl in der industriellen Produktion als auch in spezialisierten Anwendungsbereichen unverzichtbar. Mit den kontinuierlichen Innovationen in diesen Technologien werden sie auch in Zukunft eine wichtige Rolle spielen.
Automatisierung und Effizienzsteigerung
Automatisierung und Effizienzsteigerung in Pulverbeschichtungs- und Kopflackierungsanlagen
Die Automatisierung ist ein zentraler Faktor bei der Steigerung der Effizienz und Qualität in Pulverbeschichtungs- und Kopflackierungsanlagen. Durch den Einsatz modernster Technologien und Automatisierungssysteme können Produktionsprozesse erheblich beschleunigt, Fehlerquellen minimiert und die gesamte Fertigungskostenstruktur optimiert werden. Dies hat nicht nur Auswirkungen auf die Produktionsgeschwindigkeit, sondern auch auf die Konsistenz der Beschichtung, die Qualität der Endprodukte und die Ressourcennutzung.
Automatisierte Fördertechniken
Eine der wichtigsten Technologien, die die Effizienz in Pulverbeschichtungs- und Lackierungsprozessen verbessert, ist der Einsatz automatisierter Fördersysteme. Diese Systeme transportieren die Schrauben während des gesamten Prozesses automatisch von einer Station zur nächsten – beginnend bei der Vorbehandlung, über das Auftragen der Beschichtung bis hin zum Trocknen. Die Verwendung von Förderbändern, Drehvorrichtungen und Roboterarmen sorgt für eine kontinuierliche, gleichmäßige Bewegung der Schrauben durch die einzelnen Prozessabschnitte. Dies reduziert menschliche Eingriffe und sorgt für eine stabile und konstante Produktionsrate, was die Durchlaufzeit deutlich verringert und die Produktionskapazität erhöht.
Robotertechnik für präzise Applikation
Moderne Pulverbeschichtungs- und Lackieranlagen setzen zunehmend Robotertechnik ein, um die Pulver- oder Lackapplikation auf Schrauben präzise zu steuern. Roboterarme sind in der Lage, eine gleichmäßige und fehlerfreie Schichtdicke zu gewährleisten, indem sie die Schrauben in exakt der richtigen Position sprühen. Roboter können mit hoher Geschwindigkeit und Wiederholgenauigkeit arbeiten, wodurch die Produktionsrate und die Beschichtungsqualität verbessert werden. Zudem ermöglichen sie es, auch komplexe Geometrien oder schwer zugängliche Bereiche der Schraubenköpfe effizient zu beschichten, was mit manuellen Verfahren schwierig oder zeitaufwändig wäre.
Optimierte Steuerungssysteme und Software
Ein weiterer entscheidender Aspekt der Automatisierung in modernen Beschichtungsanlagen ist der Einsatz fortschrittlicher Steuerungssysteme und Softwarelösungen. Diese Systeme überwachen und steuern alle relevanten Parameter des Beschichtungsprozesses, wie die Beschichtungsdichte, den Luftdruck, die Sprühgeschwindigkeit, die Trocknungstemperatur und -zeit sowie den Energieverbrauch. Die Verwendung von Echtzeit-Datenanalysen und Feedback-Mechanismen ermöglicht es den Anlagenbetreibern, die Prozesse kontinuierlich zu optimieren und bei Bedarf sofort einzugreifen. Dadurch wird die Effizienz des gesamten Systems erhöht, und gleichzeitig können Abweichungen von den gewünschten Parametern sofort korrigiert werden, bevor sie zu Qualitätsproblemen führen.
Vernetzte Systeme und Predictive Maintenance
Ein wachsender Trend in der Automatisierung von Fertigungsprozessen ist die Vernetzung der Anlagen. In modernen Pulverbeschichtungs- und Kopflackierungsanlagen sind Maschinen und Geräte zunehmend miteinander verknüpft, um Daten auszutauschen und gemeinsame Prozesse zu steuern. Durch die Integration von Industrie 4.0-Technologien können die Maschinen in Echtzeit überwacht werden, was eine proaktive Wartung und Fehlerdiagnose ermöglicht. Predictive Maintenance (vorausschauende Wartung) ist ein hervorragendes Beispiel für diese Entwicklung. Sensoren messen kontinuierlich den Zustand der Maschinen und Anlagen, und die Software analysiert die Daten, um potenzielle Ausfälle vorherzusagen. Auf diese Weise können Wartungsarbeiten geplant und unerwartete Produktionsausfälle vermieden werden, was die Gesamtproduktionseffizienz weiter steigert.
Automatisierung in der Qualitätskontrolle
Die Qualitätskontrolle wird ebenfalls durch Automatisierung optimiert. Kameras und Sensoren sind in modernen Anlagen integriert, um die Oberflächen der beschichteten Schrauben kontinuierlich zu überwachen. Diese Systeme können Mängel wie unregelmäßige Beschichtungen, Blasen, Kratzer oder Staubeinschlüsse schnell erkennen und die betroffenen Teile aus der Produktion aussortieren. Automatisierte Inspektionssysteme verbessern nicht nur die Fehlererkennung, sondern auch die Dokumentation und Rückverfolgbarkeit, die für die Qualitätssicherung und Zertifizierung erforderlich sind. Solche Systeme tragen dazu bei, den Ausschuss zu verringern und die Wiederverwendbarkeit von fehlerhaften Bauteilen zu optimieren, was sowohl die Materialkosten als auch den Arbeitsaufwand senkt.
Reduzierung des Materialverbrauchs
Durch die Automatisierung können auch Materialverschwendung und der Verbrauch von Ressourcen optimiert werden. Beispielsweise sorgt die präzise Steuerung der Pulverbeschichtung dafür, dass nur die notwendige Menge an Pulver auf die Schrauben aufgetragen wird, was den Materialverbrauch reduziert. Überschüssiges Pulver, das bei älteren, manuellen Verfahren häufig verschwendet wurde, kann in vielen modernen Anlagen wiederverwendet werden. Dies führt nicht nur zu einer Reduktion der Produktionskosten, sondern auch zu einer geringeren Umweltbelastung, da weniger Abfall entsteht.
Flexibilität und Anpassungsfähigkeit
Ein weiterer Vorteil der Automatisierung in Pulverbeschichtungs- und Kopflackierungsanlagen ist die hohe Flexibilität der Systeme. In modernen Anlagen können verschiedene Schraubentypen und Beschichtungsanforderungen ohne größere Umbauten oder manuelle Eingriffe verarbeitet werden. Automatisierte Systeme können schnell umgestellt werden, um unterschiedliche Farben, Pulversorten oder Lacke zu verarbeiten. Dies bedeutet, dass auch kleine Losgrößen oder maßgeschneiderte Produkte effizient gefertigt werden können, was für viele Industrien, insbesondere in der Möbel- oder Automobilindustrie, von großer Bedeutung ist. Die Anpassungsfähigkeit der Systeme ermöglicht es Unternehmen, flexibel auf Kundenwünsche oder Änderungen in der Produktion zu reagieren.
Fazit: Automatisierung als Schlüssel zur Effizienzsteigerung
Zusammenfassend lässt sich sagen, dass die Automatisierung von Pulverbeschichtungs- und Kopflackierungsanlagen zu einer erheblichen Effizienzsteigerung führt. Durch den Einsatz automatisierter Fördersysteme, Robotertechnik, präziser Steuerungssysteme und Vernetzungstechnologien werden Produktionsprozesse optimiert, Fehler reduziert und Material verschwendet. Die Automatisierung trägt nicht nur dazu bei, die Produktionskapazität zu erhöhen, sondern verbessert auch die Qualität und Flexibilität der Endprodukte. Unternehmen, die auf moderne automatisierte Anlagen setzen, können ihre Produktionskosten senken, die Produktqualität sichern und gleichzeitig eine hohe Anpassungsfähigkeit an die Anforderungen des Marktes gewährleisten.
Qualitätskontrolle und Prozessüberwachung in Pulverbeschichtungs- und Kopflackierungsanlagen
Die Qualität der beschichteten Schrauben spielt eine entscheidende Rolle für die Leistung, Haltbarkeit und Ästhetik des Endprodukts. Besonders in Industrien, in denen Schrauben sicherheitskritische Funktionen übernehmen, wie in der Automobil- oder Luftfahrtindustrie, sind präzise Qualitätskontrollen unerlässlich. Die moderne Qualitätskontrolle und Prozessüberwachung in Pulverbeschichtungs- und Kopflackierungsanlagen nutzt fortschrittliche Technologien, um sicherzustellen, dass jede Schraube die gewünschten Spezifikationen erfüllt und die Produktionsprozesse effizient sowie fehlerfrei ablaufen.
Echtzeit-Überwachung und Fehlererkennung
Ein zentrales Element der Qualitätskontrolle in modernen Beschichtungsanlagen ist die Echtzeit-Überwachung des gesamten Prozesses. Durch den Einsatz fortschrittlicher Sensoren und Kamerasysteme wird jeder Schritt der Beschichtung überwacht, angefangen von der Vorbehandlung bis hin zum Trocknungsprozess. Diese Systeme sind in der Lage, Abweichungen in der Beschichtungsdicke, Farbtonabweichungen oder das Vorhandensein von Fehlern wie Blasen, Kratzern oder Staubeinschlüssen sofort zu erkennen. Durch automatisierte Inspektionstechnologien können fehlerhafte Produkte in Echtzeit aussortiert und vom Förderband entfernt werden, wodurch die Wahrscheinlichkeit von Ausschuss oder fehlerhaften Endprodukten drastisch reduziert wird.
Kamerasysteme und Bildverarbeitung
Moderne Pulverbeschichtungs- und Lackieranlagen setzen auf hochauflösende Kamerasysteme, die die Oberflächenqualität jeder Schraube überwachen. Bildverarbeitungssoftware analysiert die aufgenommenen Bilder und vergleicht sie mit den festgelegten Qualitätsstandards. Jegliche Unregelmäßigkeiten – sei es in der Farbe, der Oberflächenstruktur oder der gleichmäßigen Verteilung der Beschichtung – werden sofort identifiziert. Diese Systeme bieten eine hohe Genauigkeit und ermöglichen es, auch kleinste Fehler zu erkennen, die mit bloßem Auge nicht sichtbar wären. Die Fähigkeit, Fehler frühzeitig zu erkennen, sorgt dafür, dass die Fehlerquote minimiert und die Produktqualität konstant hoch bleibt.
Prozessparameter und kontinuierliche Überwachung
Ein weiterer wichtiger Aspekt der Prozessüberwachung ist die Kontrolle der wichtigsten Prozessparameter, die die Beschichtungsqualität beeinflussen. Hierzu gehören Faktoren wie die Pulverauftragungsrate, die Luftdruckeinstellungen, die Sprühgeschwindigkeit, die Trocknungstemperatur und die Einbrenndauer. Durch die Integration von Sensoren und Steuerungssystemen können diese Parameter in Echtzeit überwacht und gegebenenfalls angepasst werden. Automatisierte Systeme bieten die Möglichkeit, die Parameter ständig zu kontrollieren, sodass Schwankungen sofort erkannt und behoben werden können. Dadurch wird sichergestellt, dass jede Schraube eine gleichbleibend hohe Beschichtungsqualität erhält.
Datenanalyse und Rückverfolgbarkeit
Moderne Pulverbeschichtungs- und Kopflackierungsanlagen bieten umfangreiche Möglichkeiten zur Datenerfassung und -analyse. Alle relevanten Prozessdaten – von den verwendeten Materialchargen bis hin zu den einzelnen Maschineneinstellungen – werden kontinuierlich aufgezeichnet und gespeichert. Dies ermöglicht eine lückenlose Rückverfolgbarkeit der Produktion, die sowohl für interne Qualitätsmanagement-Systeme als auch für externe Zertifizierungen erforderlich ist. Bei auftretenden Problemen können durch die detaillierte Dokumentation schnell die Ursachen ermittelt und Maßnahmen zur Behebung ergriffen werden. Diese Daten können auch zur kontinuierlichen Verbesserung des Produktionsprozesses genutzt werden, um die Effizienz zu steigern und Fehlerquellen zu minimieren.
Automatisierte Inspektion und Fehlerdiagnose
Die Qualitätskontrolle in modernen Anlagen wird zunehmend automatisiert, was nicht nur die Fehlererkennung beschleunigt, sondern auch die Präzision und Konsistenz erhöht. Automatisierte Inspektionssysteme nutzen eine Kombination aus Kameras, Laserscannern und anderen optischen Geräten, um die Schrauben während des gesamten Prozesses zu überwachen. Diese Systeme können genaue Messungen der Beschichtungsdicke vornehmen, Unregelmäßigkeiten im Finish feststellen und sogar die Oberflächenstruktur analysieren. Wenn Fehler auftreten, wird automatisch eine Diagnose erstellt, die aufzeigt, welche Parameter oder Maschinenkomponenten möglicherweise die Ursache des Problems sind. Diese schnellen, präzisen Diagnosen minimieren Ausfallzeiten und ermöglichen eine schnelle Behebung der Probleme.
Statistische Prozesskontrolle (SPC)
Ein weiteres wichtiges Werkzeug in der Qualitätskontrolle von Pulverbeschichtungs- und Lackierungsanlagen ist die statistische Prozesskontrolle (SPC). Diese Methode nutzt statistische Analysen, um den Produktionsprozess kontinuierlich zu überwachen und Abweichungen von den Sollwerten zu identifizieren. Durch die Anwendung von SPC-Techniken lassen sich systematische Fehler oder Unregelmäßigkeiten frühzeitig erkennen, bevor sie zu größeren Qualitätsproblemen führen. Dies ermöglicht es, den Prozess in Echtzeit anzupassen und sicherzustellen, dass die Produktion innerhalb der festgelegten Toleranzen bleibt.
Fehlerbehebung und kontinuierliche Verbesserung
Die kontinuierliche Verbesserung der Produktionsprozesse ist ein wesentliches Ziel in der modernen Fertigung. Die Qualitätskontrolle und Prozessüberwachung in Pulverbeschichtungs- und Kopflackierungsanlagen bieten umfangreiche Daten, die für die Analyse und Optimierung von Prozessen genutzt werden können. Wenn regelmäßig bestimmte Fehler auftreten, kann der gesamte Prozess in Frage gestellt und gegebenenfalls neu konzipiert werden, um diese Probleme zu lösen. Diese kontinuierliche Verbesserung hilft dabei, die Effizienz der Produktion zu steigern, die Kosten zu senken und gleichzeitig die Produktqualität zu erhöhen.
Integration von Künstlicher Intelligenz (KI) und Machine Learning
Ein innovativer Ansatz, der zunehmend in der Prozessüberwachung eingesetzt wird, ist die Nutzung von Künstlicher Intelligenz (KI) und Machine Learning. Durch den Einsatz dieser Technologien können Produktionsdaten in Echtzeit analysiert und Muster erkannt werden, die auf potenzielle Qualitätsprobleme hinweisen. KI-Algorithmen lernen im Laufe der Zeit, Fehlerquellen immer genauer vorherzusagen, und ermöglichen eine vorausschauende Qualitätskontrolle. Diese Technologien verbessern die Fehlererkennung und -vermeidung und tragen dazu bei, dass die Anlagen autonomer arbeiten, indem sie sich selbst optimieren und potenzielle Qualitätsprobleme frühzeitig identifizieren.
Fazit: Die Rolle der Qualitätskontrolle in der Pulverbeschichtung
Die Qualitätssicherung und Prozessüberwachung sind wesentliche Bestandteile in Pulverbeschichtungs- und Kopflackierungsanlagen. Durch den Einsatz fortschrittlicher Technologien wie Echtzeit-Überwachung, Bildverarbeitung, statistische Prozesskontrolle und KI werden Fehlerquellen schnell identifiziert, die Qualität konstant auf hohem Niveau gehalten und der Produktionsprozess kontinuierlich optimiert. Diese Technologien tragen nicht nur zur Reduktion von Ausschuss und Materialverschwendung bei, sondern auch zur Verbesserung der Gesamtproduktivität und Kundenzufriedenheit. In einer zunehmend wettbewerbsorientierten Fertigungslandschaft sind präzise Qualitätskontrollen und eine effiziente Prozessüberwachung entscheidend, um eine hohe Qualität und Zuverlässigkeit der Produkte zu gewährleisten.
Optimierung der Prozessqualität durch Automatisierung und Analyse
Die Integration von fortschrittlicher Analyse und Automatisierungstechnologien in die Qualitätskontrolle und Prozessüberwachung in Pulverbeschichtungs- und Kopflackierungsanlagen ermöglicht eine umfassende Optimierung der Prozessqualität. Die fortlaufende Erfassung von Daten und die Analyse dieser Informationen in Echtzeit liefern wertvolle Einblicke in die Produktionseffizienz und die Qualität der Beschichtungen. So können nicht nur Fehlerquellen identifiziert werden, sondern auch potenzielle Verbesserungspotenziale aufgedeckt werden, bevor sie zu größeren Problemen führen.
Automatisierte Justierung von Prozessparametern
Ein entscheidender Vorteil der Automatisierung in der Qualitätskontrolle ist die Fähigkeit, Prozessparameter automatisch anzupassen, um eine konstant hohe Produktqualität zu gewährleisten. Wenn beispielsweise ein Sensor eine Unregelmäßigkeit in der Beschichtungsdicke oder der Temperatur feststellt, können Korrekturen sofort vorgenommen werden. Durch die präzise Steuerung der Parameter wie Luftdruck, Pulverdurchfluss und Trocknungstemperatur können Inkonsistenzen in der Beschichtung reduziert werden, was die Notwendigkeit für manuelle Eingriffe minimiert. Dies sorgt nicht nur für eine höhere Prozessstabilität, sondern auch für eine gleichbleibende Beschichtungsqualität über den gesamten Produktionszeitraum.
Rückverfolgbarkeit und Nachverfolgbarkeit für eine bessere Qualitätssicherung
In modernen Pulverbeschichtungs- und Kopflackierungsanlagen wird durch die Digitalisierung und Vernetzung der Maschinen eine vollständige Rückverfolgbarkeit des gesamten Produktionsprozesses gewährleistet. Jeder Schritt, von der Pulverauftragung bis zum Trocknungsprozess, wird digital erfasst und gespeichert. Im Falle eines Qualitätsproblems können die betroffenen Produkte anhand von Produktionsdaten, Materialchargen und Maschinenparametern exakt nachverfolgt werden. Diese umfassende Nachverfolgbarkeit ermöglicht eine schnelle Identifikation von Problemursachen und eine schnelle Reaktion auf eventuelle Störungen im Prozess. Darüber hinaus ist sie für die Einhaltung von Industriestandards und für Audits durch Zertifizierungsstellen von entscheidender Bedeutung, da eine lückenlose Dokumentation der Produktionsprozesse erforderlich ist.
Vorausschauende Wartung und Fehlerprävention
Durch den Einsatz von Predictive Maintenance (vorausschauender Wartung) wird auch der Wartungsprozess optimiert. Sensoren überwachen kontinuierlich den Zustand von Maschinenkomponenten und identifizieren frühzeitig Verschleiß oder potenzielle Ausfälle. Diese Daten ermöglichen es den Unternehmen, Wartungsmaßnahmen proaktiv zu planen, bevor es zu Ausfällen kommt, die den Produktionsprozess unterbrechen könnten. Indem potenzielle Probleme vor ihrer Entstehung erkannt werden, kann der gesamte Produktionsprozess aufrechterhalten und die Notwendigkeit für kurzfristige Reparaturen oder Produktionsausfälle minimiert werden. Dies führt zu einer höheren Maschinenverfügbarkeit, weniger Ausfallzeiten und einer konstanten Qualität.
Optimierung des Materialverbrauchs
Die Qualitätskontrolle und Prozessüberwachung tragen auch zur Reduktion des Materialverbrauchs bei. Da jede Schraube während der Produktion überwacht wird, kann die Pulverbeschichtung gezielt und präzise aufgetragen werden. Dies reduziert nicht nur die Abfallmenge, sondern sorgt auch für eine effiziente Nutzung der Rohstoffe, da überschüssiges Pulver zurückgewonnen und wiederverwendet werden kann. Eine präzise Materialkontrolle bedeutet, dass weniger Abfall entsteht, was nicht nur die Produktionskosten senkt, sondern auch zu einer besseren ökologischen Bilanz führt.
Fehlerdiagnose und kontinuierliche Prozessverbesserung
Durch den Einsatz moderner Datenanalytik können Fehlerquellen schneller diagnostiziert und die Ursachen genauer bestimmt werden. Wenn wiederkehrende Probleme auftreten, bieten die Daten aus der Prozessüberwachung eine detaillierte Analyse und ermöglichen es, systematische Fehler zu identifizieren und zu beheben. Diese Fähigkeit zur Fehlerdiagnose trägt dazu bei, den Produktionsprozess kontinuierlich zu verbessern, sodass die Qualität der beschichteten Schrauben langfristig stabil und hoch bleibt. Mit der Zeit lassen sich durch die kontinuierliche Analyse der Prozessdaten neue Muster und Trends erkennen, die dazu beitragen, den gesamten Fertigungsprozess noch weiter zu optimieren.
Integration von KI und maschinellem Lernen
Künstliche Intelligenz (KI) und maschinelles Lernen (ML) bieten im Bereich der Qualitätskontrolle und Prozessüberwachung zusätzliche Potenziale. Durch den Einsatz von KI-Algorithmen können große Mengen an Produktionsdaten analysiert und Muster identifiziert werden, die für den Menschen schwer nachvollziehbar sind. KI-Systeme können helfen, Probleme bereits im frühen Stadium zu erkennen, indem sie aus vergangenen Produktionen lernen und die Ergebnisse vorhersagen. Dies führt zu einer weiteren Steigerung der Prozessgenauigkeit und einer Reduzierung von Ausschuss und Fehlern.
Visuelle Inspektion und Automatisierung der Fehlererkennung
Ein besonders fortschrittlicher Aspekt der modernen Qualitätskontrolle ist die visuelle Inspektion durch Automatisierung. Kamerasysteme und optische Sensoren werden in vielen modernen Anlagen eingesetzt, um die Schrauben während des gesamten Prozesses zu überwachen. Durch hochentwickelte Bildverarbeitungssoftware werden automatisch fehlerhafte Produkte aus der Produktion aussortiert. Diese Systeme können nicht nur physische Mängel wie Kratzer oder Unebenheiten auf der Oberfläche erkennen, sondern auch optische Inkonsistenzen wie Farbabgleich oder unterschiedliche Beschichtungsdicken feststellen. Diese Art der Inspektion ist schneller und genauer als manuelle Kontrollen und ermöglicht es, Fehler sofort zu erkennen und auszumerzen, bevor sie den Produktionsfluss beeinträchtigen.
Vermeidung von Qualitätsabweichungen durch präzise Prozesskontrolle
Die präzise Steuerung der Pulverbeschichtung ist von entscheidender Bedeutung, um Qualitätsschwankungen zu vermeiden. Kleinste Abweichungen in den Prozessparametern, wie Luftfeuchtigkeit, Pulverdichte oder Sprühdruck, können die Endbeschichtung erheblich beeinflussen. Durch die kontinuierliche Überwachung dieser Parameter in Echtzeit können Abweichungen sofort korrigiert werden. In vielen Fällen können Maschinensteuerungen automatisch Anpassungen vornehmen, um die Qualität konstant hoch zu halten und Produktionsverzögerungen oder Ausschuss zu vermeiden.
Fazit: Qualitätssicherung als Schlüssel für erfolgreiche Beschichtungsprozesse
Zusammenfassend lässt sich sagen, dass die Qualitätskontrolle und Prozessüberwachung in modernen Pulverbeschichtungs- und Kopflackierungsanlagen von entscheidender Bedeutung für den Erfolg der Produktion sind. Durch den Einsatz automatisierter Inspektionssysteme, Echtzeit-Datenanalysen und fortschrittlicher Prozesskontrollen können Fehler frühzeitig erkannt, Ausschuss minimiert und die Prozessqualität konstant auf hohem Niveau gehalten werden. Die Integration von Predictive Maintenance, KI und maschinellem Lernen trägt dazu bei, dass Fehler noch schneller und präziser diagnostiziert werden können und die Effizienz der Produktion weiter gesteigert wird. In einer zunehmend globalisierten und wettbewerbsintensiven Fertigungsumgebung ist eine präzise Qualitätskontrolle entscheidend, um sich einen Wettbewerbsvorteil zu sichern und Produkte mit hoher Zuverlässigkeit und Langlebigkeit zu gewährleisten.
EMS Pulverbeschichtungsanlagen
Unsere Pulverbeschichtungsanlage wird in Übereinstimmung mit den globalen fortschrittlichen Standards hergestellt und wurden mit vollem Vertrauen sowohl auf dem heimischen als auch auf dem weltweiten Markt bevorzugt.
Unsere Kapazität ist täglich gewachsen, wobei die Kundenzufriedenheit zusammen mit unserem gemeinsamen Vertriebs- und Servicenetz an erster Stelle steht.
Unser Unternehmen ist ein führendes türkisches Unternehmen, das sich auf die Herstellung von „Elektrostatischen Pulverbeschichtungsanlagen und kompletten Lackiersystemen“ mit 20 Jahren Wissen und praktischer Erfahrung spezialisiert hat.
Alle unsere Maschinen sind CE-gekennzeichnet, garantiert und können von potenziellen Kunden persönlich besichtigt werden. Es gibt auch Bilder und Videos auf dieser Seite, die die verwendeten Maschinen zeigen.
Wir entwerfen, fertigen und montieren Pulverbeschichtungsöfen, automatische und manuelle Kabinen, automatische und manuelle Pulverbeschichtungsanlagen, Pistolen, automatische und Stangentransfer-Pulverbeschichtungslinien, Pulverbeschichtungsfilter und Ersatzteile für Pulverbeschichtungspistolen