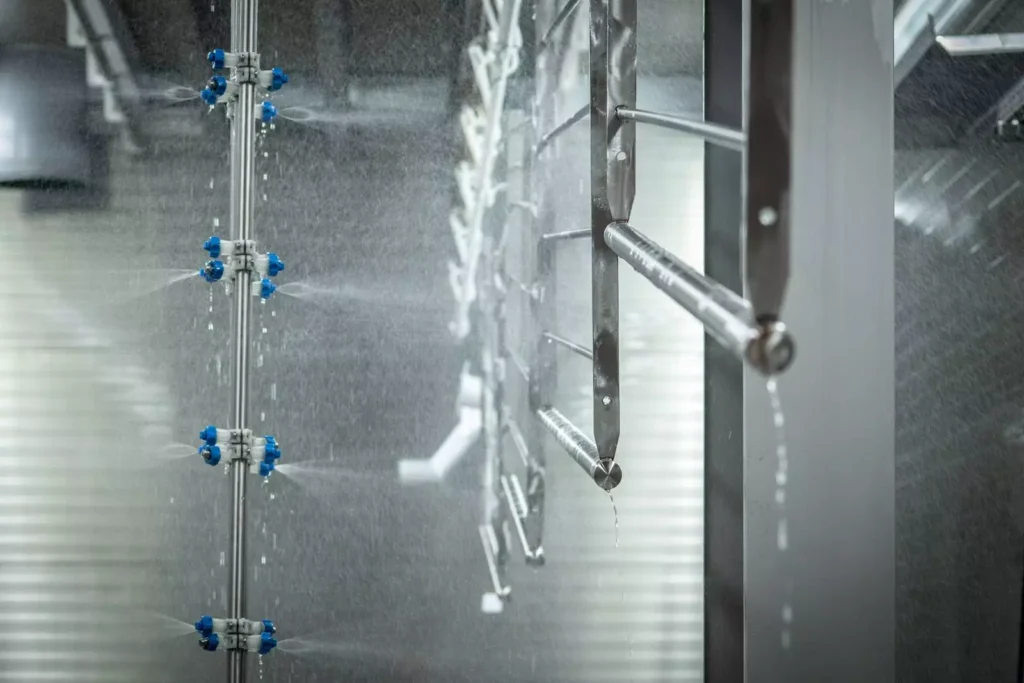
Vorbehandlung Pulverbeschichtung kaufen. Elektro und Gas Brennofen mit Garantie. Pulverofen neu und gebraucht kaufen. Einbrennofen
Die Vorbehandlung ist ein wichtiger Schritt bei der Pulverbeschichtung, der sicherstellt, dass das Pulver auf der Oberfläche des Werkstücks haftet und eine langlebige und qualitativ hochwertige Beschichtung ergibt. Die Vorbehandlung besteht aus mehreren Schritten und kann je nach Material und Anwendung variieren. Hier sind einige der Schritte, die typischerweise bei der Vorbehandlung für die Pulverbeschichtung durchgeführt werden:
- Entfetten: Die Entfernung von Öl, Fett und anderen Verunreinigungen ist entscheidend für eine gute Haftung des Pulvers. Dies wird normalerweise durch eine alkalische Reinigung oder durch Lösemittelreinigung erreicht.
- Beizen: Beizen wird verwendet, um Oberflächenkontaminationen wie Rost oder Schweißschlacke zu entfernen. Eine Säure wird verwendet, um die Oberfläche des Werkstücks zu reinigen und zu entrosten.
- Spülen: Nach dem Entfetten und Beizen muss die Oberfläche des Werkstücks gründlich gespült werden, um alle Verunreinigungen zu entfernen und sicherzustellen, dass das Pulver gleichmäßig aufgetragen werden kann.
- Konversionsbeschichtung: Konversionsbeschichtung ist ein wichtiger Schritt, der eine Schutzschicht auf der Oberfläche des Werkstücks bildet und die Haftung des Pulvers verbessert. Dies wird normalerweise durch eine Phosphatierung oder Chromatierung erreicht.
- Trocknen: Nach der Vorbehandlung muss das Werkstück vollständig getrocknet werden, bevor es mit dem Pulverbeschichtungsprozess fortgesetzt wird. Eine effektive Trocknung ist wichtig, um sicherzustellen, dass das Pulver auf der Oberfläche haftet.
Die Vorbehandlung ist ein kritischer Schritt bei der Pulverbeschichtung und sollte von geschultem Personal durchgeführt werden, um sicherzustellen, dass die Beschichtung qualitativ hochwertig und langlebig ist.
Technische Einzelheiten über Vorbehandlung Pulverbeschichtung
Die technischen Einzelheiten der Vorbehandlung für die Pulverbeschichtung können je nach den spezifischen Anforderungen und Anwendungen variieren. Hier sind einige weitere technische Einzelheiten, die bei der Vorbehandlung für die Pulverbeschichtung berücksichtigt werden:
- Oberflächenvorbereitung: Die Oberfläche des Werkstücks muss für die Vorbehandlung geeignet sein. Es ist wichtig sicherzustellen, dass die Oberfläche sauber, trocken und frei von Schmutz, Öl, Fett, Rost oder anderen Verunreinigungen ist.
- Chemikalien und Konzentrationen: Die Wahl der Chemikalien und Konzentrationen für die Vorbehandlung hängt von der Art des Werkstücks und der gewünschten Beschichtung ab. Es ist wichtig, die richtigen Chemikalien und Konzentrationen zu wählen, um eine effektive Vorbehandlung zu gewährleisten.
- Temperatur und Zeit: Die Vorbehandlung wird normalerweise bei einer bestimmten Temperatur und für eine bestimmte Zeit durchgeführt. Es ist wichtig, die richtige Temperatur und Zeit für die Vorbehandlung zu wählen, um eine effektive Beschichtung zu gewährleisten.
- Wasserqualität: Die Qualität des Wassers, das für die Vorbehandlung verwendet wird, ist ebenfalls wichtig. Es ist wichtig sicherzustellen, dass das Wasser sauber und frei von Verunreinigungen wie Mineralien und Salzen ist, um eine effektive Vorbehandlung zu gewährleisten.
- Qualitätssicherung: Die Qualität der Vorbehandlung kann durch verschiedene Tests und Messungen überwacht werden, um sicherzustellen, dass die Vorbehandlung effektiv ist. Dazu gehören Tests auf Oberflächenrauheit, Schichtdickenmessung und Haftungsprüfung.
Die Vorbehandlung für die Pulverbeschichtung ist ein wichtiger Schritt, der sorgfältige Planung und Durchführung erfordert. Durch die Berücksichtigung der technischen Einzelheiten kann eine effektive Vorbehandlung durchgeführt werden, die zu einer langlebigen und qualitativ hochwertigen Beschichtung führt.
Vorbehandlung Pulverbeschichtung
Die Vorbehandlung ist ein entscheidender Schritt im Pulverbeschichtungsprozess, der dazu dient, die Oberfläche der zu beschichtenden Werkstücke optimal auf die Haftung und Haltbarkeit des Pulverlacks vorzubereiten. Eine gründliche Vorbehandlung ist unerlässlich, um eine qualitativ hochwertige und langlebige Beschichtung zu gewährleisten. Hier sind die wichtigsten Aspekte der Vorbehandlung in der Pulverbeschichtung:
- Reinigung: Der erste Schritt der Vorbehandlung besteht in der gründlichen Reinigung der Werkstücke. Alle Verunreinigungen wie Fett, Öl, Schmutz, Rost, Oxidation, alte Lackierungen oder Beschichtungen müssen entfernt werden. Dies kann durch Verfahren wie Entfetten, Waschen, Strahlen oder Schleifen erreicht werden.
- Entfetten: Wenn die Werkstücke fett- oder ölverschmutzt sind, erfolgt die Entfettung in der Regel durch ein geeignetes Reinigungsmittel oder eine Lösung, die Fette und Öle effektiv entfernt.
- Entrosten: Wenn auf den Werkstücken Rost vorhanden ist, muss er entfernt werden, da Rost die Haftung der Beschichtung beeinträchtigt. Dies kann durch Sandstrahlen, chemisches Entrosten oder mechanisches Entfernen des Rosts erfolgen.
- Phosphatierung: Ein häufig verwendetes Verfahren in der Vorbehandlung ist die Phosphatierung. Dabei werden die Werkstücke in einem Phosphatbad getaucht oder mit einer Phosphatlösung besprüht. Dies bildet eine Phosphatschicht auf der Oberfläche, die die Haftung des Pulverlacks verbessert und gleichzeitig als Rostschutzschicht dient.
- Spülen: Nach dem Entfetten, Entrosten oder Phosphatieren müssen die Werkstücke gründlich gespült werden, um überschüssige Chemikalien oder Verunreinigungen zu entfernen. Dies verhindert, dass sie die Qualität der Beschichtung beeinträchtigen.
- Trocknen: Die Werkstücke müssen vollständig getrocknet werden, bevor der Pulverlack aufgetragen wird. Dies verhindert, dass Feuchtigkeit zwischen die Beschichtung und die Oberfläche gelangt, was zu Haftungsproblemen führen kann.
- Maskierung: In einigen Fällen müssen Teile oder Bereiche der Werkstücke vor der Beschichtung maskiert werden, um sicherzustellen, dass der Pulverlack nur auf bestimmten Flächen aufgetragen wird.
- Qualitätskontrolle: Während des Vorbehandlungsprozesses ist eine Qualitätskontrolle wichtig, um sicherzustellen, dass die Oberfläche ordnungsgemäß vorbereitet wurde. Dies kann visuelle Inspektionen, Dickenmessungen oder Haftungstests umfassen.
Die Art der Vorbehandlung hängt von verschiedenen Faktoren ab, einschließlich der Art des Werkstücks, der vorhandenen Oberflächenbedingungen und der Anforderungen an die Beschichtung. Die Qualität der Vorbehandlung hat einen erheblichen Einfluss auf die Leistung und Haltbarkeit der Pulverbeschichtung. Daher ist es wichtig, die richtigen Vorbehandlungsverfahren gemäß den Herstellerempfehlungen und den Branchenstandards zu wählen und sorgfältig durchzuführen.
Reinigung
Die Reinigung ist ein grundlegender Prozess in vielen Industriezweigen und im Alltag, bei dem Schmutz, Verunreinigungen und Staub von Oberflächen, Materialien oder Geräten entfernt werden, um sie sauber, sicher und funktionsfähig zu halten. Die richtige Reinigungsmethode hängt von der Art des zu reinigenden Objekts oder Materials ab. Hier sind einige grundlegende Aspekte der Reinigung:
- Arten der Reinigung:
- Trockenreinigung: Bei der Trockenreinigung werden Staub, Schmutz und lose Partikel von Oberflächen mit Hilfe von Werkzeugen wie Besen, Bürsten, Staubsaugern oder Druckluft entfernt. Trockenreinigungsmethoden werden oft auf empfindlichen Oberflächen oder elektronischen Geräten angewendet, bei denen Wasser schädlich sein könnte.
- Nassreinigung: Nassreinigung beinhaltet die Verwendung von Wasser oder wässrigen Lösungen in Kombination mit Reinigungsmitteln, um Schmutz, Fett und Verunreinigungen von Oberflächen zu entfernen. Dies kann das Wischen, Waschen, Spülen oder Eintauchen von Objekten umfassen.
- Chemische Reinigung: Die chemische Reinigung verwendet spezielle Lösungsmittel und Reinigungsmittel, um hartnäckige Flecken, Fett, Farben oder andere schwer zu entfernende Verunreinigungen zu behandeln. Es wird häufig in der Textil- und Bekleidungsindustrie sowie in Labors eingesetzt.
- Ultraschallreinigung: Bei der Ultraschallreinigung werden Objekte in ein Flüssigkeitsbad getaucht, das mit Ultraschallschwingungen angereichert ist. Diese Schwingungen erzeugen winzige Kavitationsbläschen, die Schmutz und Verunreinigungen von den Oberflächen lösen.
- Dampfreinigung: Dampfreinigung verwendet Hochtemperaturdampf, um Schmutz und Bakterien von Oberflächen zu lösen und zu desinfizieren. Es wird häufig für die Reinigung von Teppichen, Polstermöbeln und Sanitäranlagen verwendet.
- Reinigungsmittel: Je nach Art der Reinigung und den zu entfernenden Verunreinigungen werden spezielle Reinigungsmittel und Chemikalien verwendet. Diese können alkalisch, sauer, neutral oder enzymatisch sein und helfen, Schmutz zu lösen, Fett zu entfernen oder Oberflächen zu desinfizieren.
- Reinigungswerkzeuge: Zur Durchführung der Reinigung sind verschiedene Werkzeuge erforderlich, darunter Bürsten, Mopp, Schwämme, Tücher, Staubsauger, Dampfreiniger und mehr. Die Auswahl des richtigen Werkzeugs hängt von der Art der Oberfläche und der Art der Verschmutzung ab.
- Hygiene und Gesundheit: In Bereichen, in denen Hygiene und Gesundheit von größter Bedeutung sind, wie in Lebensmittelverarbeitungsbetrieben, Krankenhäusern und Labors, werden strenge Reinigungsprotokolle befolgt, um Keime und Bakterien zu eliminieren.
- Umweltaspekte: Die Wahl der Reinigungsmittel und -verfahren kann Umweltauswirkungen haben. Umweltfreundliche Reinigungsmittel und -verfahren, die weniger schädlich für die Umwelt sind, werden immer häufiger verwendet.
- Sicherheit: Bei der Verwendung von Reinigungsmitteln und Reinigungsverfahren ist es wichtig, die Sicherheitsempfehlungen zu beachten und geeignete Schutzmaßnahmen zu ergreifen, um die Gesundheit derjenigen, die die Reinigung durchführen, zu gewährleisten.
Die Reinigung ist ein vielseitiger Prozess, der in verschiedenen Umgebungen und Branchen eine wichtige Rolle spielt. Sie dient der Pflege von Räumlichkeiten, Maschinen und Produkten sowie der Aufrechterhaltung von Gesundheit und Hygiene. Je nach Kontext und Anforderungen werden unterschiedliche Reinigungsmethoden und -mittel eingesetzt.
Entfetten
Die Entfettung ist ein Reinigungsprozess, bei dem Fett, Öl, Schmiermittel und andere fettige Verunreinigungen von Oberflächen oder Materialien entfernt werden. Dieser Prozess ist in verschiedenen Branchen und Anwendungen weit verbreitet und dient dazu, die Oberfläche für weitere Bearbeitungs- oder Beschichtungsverfahren vorzubereiten. Hier sind einige wichtige Aspekte der Entfettung:
- Warum Entfettung notwendig ist: Fettige Verunreinigungen können die Haftung von Farben, Beschichtungen, Klebstoffen und anderen Materialien auf Oberflächen beeinträchtigen. Sie können auch die Qualität von Schweißverbindungen oder die Haftung von Klebeverbindungen negativ beeinflussen. Aus diesem Grund ist die Entfettung in vielen industriellen Prozessen ein wichtiger Schritt.
- Methoden der Entfettung:
- Chemische Entfettung: Bei der chemischen Entfettung werden spezielle Reinigungslösungen oder Entfettungsmittel verwendet, um Fett und Öl von Oberflächen zu lösen. Diese Lösungen können alkalisch, sauer oder auf Lösungsmitteln basieren, abhängig von den zu entfernenden Verunreinigungen und den Anforderungen der Anwendung.
- Mechanische Entfettung: Mechanische Entfettungsmethoden umfassen das Abbürsten, Abschaben oder Strahlen von fettigen Ablagerungen. Diese Methoden sind effektiv, wenn die Verschmutzung hauptsächlich an der Oberfläche haftet.
- Ultraschall-Entfettung: Bei der Ultraschall-Entfettung werden die zu reinigenden Teile in ein Flüssigkeitsbad getaucht, das mit Ultraschallschwingungen angereichert ist. Diese Schwingungen lösen das Fett von den Oberflächen.
- Dampf- oder Hochdruckreinigung: Dampfreiniger oder Hochdruckreiniger verwenden heißes Wasser oder Dampf, um Fett und Schmutz von Oberflächen zu entfernen. Diese Methode kann besonders effektiv sein, wenn hohe Temperaturen und Drücke erforderlich sind.
- Auswahl des Entfettungsverfahrens: Die Wahl des geeigneten Entfettungsverfahrens hängt von verschiedenen Faktoren ab, darunter die Art der Verunreinigung, die Art der Oberfläche, die Größe und Form der Teile sowie die Anforderungen der weiteren Verarbeitung oder Beschichtung.
- Sicherheit: Bei der Entfettung ist es wichtig, die Sicherheitsrichtlinien zu beachten und geeignete Schutzmaßnahmen zu ergreifen, da einige Entfettungsmittel oder -methoden gesundheitsschädlich sein können.
- Umweltaspekte: Umweltfreundliche Entfettungsmethoden und -mittel, die weniger schädlich für die Umwelt sind, werden immer häufiger eingesetzt. Dies ist besonders wichtig in Branchen, in denen strenge Umweltauflagen gelten.
Die Entfettung ist ein kritischer Schritt in verschiedenen Fertigungs- und Reparaturprozessen, um sicherzustellen, dass Oberflächen sauber und frei von Fett und Öl sind. Dies verbessert die Haftung und Qualität von nachfolgenden Verarbeitungs- und Beschichtungsschritten und trägt zur Herstellung von hochwertigen Produkten bei.
Entfettung
Die Entfettung ist ein wesentlicher Schritt in der Vorbehandlung für die Pulverbeschichtung und bezieht sich auf den Prozess der Entfernung von Öl, Fett, Schmierstoffen und anderen Verunreinigungen von der Oberfläche des zu beschichtenden Substrats. Dieser Schritt ist entscheidend, um eine saubere Oberfläche zu gewährleisten, auf der das Beschichtungspulver gleichmäßig haften kann.
Bedeutung der Entfettung:
Eine gründliche Entfettung ist von entscheidender Bedeutung, da Öl- und Fettreste die Haftung des Beschichtungspulvers auf der Oberfläche beeinträchtigen können. Wenn diese Verunreinigungen nicht entfernt werden, kann dies zu ungleichmäßiger Beschichtungsdicke, Haftungsproblemen und vorzeitiger Beschichtungsversagen führen.
Methoden der Entfettung:
Es gibt verschiedene Methoden zur Entfettung von Oberflächen, darunter mechanische Reinigung, chemische Reinigung und thermische Reinigung. Mechanische Reinigung umfasst das Abkratzen oder Bürsten von Verunreinigungen, während chemische Reinigung die Verwendung von Entfettungslösungen beinhaltet, die die Fett- und Ölrückstände lösen. Thermische Reinigung nutzt Hitze, um die Verunreinigungen zu verdampfen oder zu verbrennen.
Entfettungslösungen:
Entfettungslösungen können alkalisch, sauer oder neutral sein und werden je nach Art der zu entfernenden Verunreinigungen und der Oberflächenbeschaffenheit ausgewählt. Alkalische Entfettungslösungen sind wirksam bei der Entfernung von Ölen und Fetten, während saure Lösungen effektiv sind, um mineralische Ablagerungen zu lösen. Die Auswahl der richtigen Entfettungslösung ist entscheidend für den Erfolg des Entfettungsprozesses.
Entfettungsmethoden in der Praxis:
In industriellen Anwendungen werden häufig Tauchbäder oder Sprühsysteme verwendet, um Bauteile zu entfetten. Tauchbäder ermöglichen eine gründliche Reinigung großer Bauteile, während Sprühsysteme eine kontinuierliche Entfettung von Bauteilen in einem Durchlauf ermöglichen. Die Wahl der Entfettungsmethode hängt von verschiedenen Faktoren ab, einschließlich Bauteilgröße, Material und Produktionsvolumen.
Qualitätssicherung:
Die Überwachung und Kontrolle des Entfettungsprozesses ist entscheidend, um sicherzustellen, dass alle Verunreinigungen effektiv entfernt werden. Dies kann durch regelmäßige Prüfungen der Entfettungslösung, Überwachung der Badtemperatur und -konzentration sowie visuelle Inspektion der entfetteten Bauteile erfolgen. Eine effektive Qualitätssicherung gewährleistet eine konsistente Entfettungsleistung und minimiert das Risiko von Beschichtungsfehlern.
Reinigung
Die Reinigung ist ein grundlegender Schritt in der Vorbehandlung für die Pulverbeschichtung und bezieht sich auf den Prozess der Entfernung von Schmutz, Staub, Oxiden und anderen Verunreinigungen von der Oberfläche des zu beschichtenden Substrats. Eine gründliche Reinigung ist entscheidend, um eine saubere Oberfläche zu gewährleisten, auf der das Beschichtungspulver gleichmäßig haften kann.
Bedeutung der Reinigung:
Eine saubere Oberfläche ist für eine erfolgreiche Pulverbeschichtung unerlässlich. Schmutz, Staub und andere Verunreinigungen können die Haftung des Beschichtungspulvers beeinträchtigen und zu Beschichtungsfehlern wie Blasenbildung, Einschlüssen oder ungleichmäßiger Beschichtungsdicke führen. Durch eine gründliche Reinigung wird sichergestellt, dass die Oberfläche frei von jeglichen Hindernissen ist, die die Haftung des Beschichtungspulvers beeinträchtigen könnten.
Methoden der Reinigung:
Es gibt verschiedene Methoden zur Reinigung von Oberflächen, darunter mechanische Reinigung, chemische Reinigung und Wasserstrahlreinigung. Mechanische Reinigung umfasst das Abkratzen, Bürsten oder Schleifen von Verunreinigungen, während chemische Reinigung die Verwendung von Reinigungslösungen beinhaltet, die die Verunreinigungen lösen oder emulgieren. Wasserstrahlreinigung nutzt einen Hochdruckwasserstrahl, um Verunreinigungen von der Oberfläche zu entfernen.
Reinigungslösungen:
Die Auswahl der richtigen Reinigungslösung hängt von der Art der zu entfernenden Verunreinigungen und der Oberflächenbeschaffenheit ab. Reinigungslösungen können alkalisch, sauer oder neutral sein und werden entsprechend den Anforderungen der Anwendung ausgewählt. Alkalische Reinigungslösungen sind effektiv bei der Entfernung von organischen Verunreinigungen, während saure Lösungen für mineralische Ablagerungen geeignet sind.
Reinigungsmethoden in der Praxis:
In industriellen Anwendungen werden verschiedene Reinigungsmethoden eingesetzt, darunter Tauchbäder, Sprühsysteme und Ultraschallreinigung. Tauchbäder ermöglichen eine gründliche Reinigung großer Bauteile, während Sprühsysteme eine kontinuierliche Reinigung von Bauteilen in einem Durchlauf ermöglichen. Die Wahl der Reinigungsmethode hängt von verschiedenen Faktoren ab, einschließlich Bauteilgröße, Material und Art der Verunreinigungen.
Qualitätssicherung:
Die Überwachung und Kontrolle des Reinigungsprozesses ist entscheidend, um sicherzustellen, dass alle Verunreinigungen effektiv entfernt werden. Dies kann durch regelmäßige Prüfungen der Reinigungslösung, Überwachung der Reinigungstemperatur und -konzentration sowie visuelle Inspektion der gereinigten Bauteile erfolgen. Eine effektive Qualitätssicherung gewährleistet eine konsistente Reinigungsleistung und minimiert das Risiko von Beschichtungsfehlern.
Phosphatierung
Phosphatierung ist ein wichtiger Schritt in der Vorbehandlung für die Pulverbeschichtung und bezieht sich auf den Prozess der Bildung einer Phosphatschicht auf der Metalloberfläche des zu beschichtenden Substrats. Diese Phosphatschicht dient als Haftvermittler für das Beschichtungspulver und verbessert die Haftung, Korrosionsbeständigkeit und Oberflächenqualität der Beschichtung.
Bedeutung der Phosphatierung:
Phosphatierung ist ein entscheidender Schritt, um eine dauerhafte und qualitativ hochwertige Beschichtung zu gewährleisten. Die Phosphatschicht fördert die Adhäsion des Beschichtungspulvers auf der Metalloberfläche, indem sie eine chemische Verbindung zwischen dem Metallsubstrat und der Beschichtung bildet. Darüber hinaus verbessert die Phosphatschicht die Korrosionsbeständigkeit der Beschichtung und trägt zur Bildung einer gleichmäßigen und glatten Oberfläche bei.
Phosphatierungsmethoden:
Es gibt verschiedene Methoden zur Phosphatierung von Metalloberflächen, darunter Sprühphosphatierung, Tauchphosphatierung und Bürstphosphatierung. Bei der Sprühphosphatierung wird eine Phosphatierungslösung auf die Metalloberfläche gesprüht, während bei der Tauchphosphatierung die Bauteile in ein Tauchbad mit Phosphatierungslösung eingetaucht werden. Die Bürstphosphatierung beinhaltet das Auftragen der Phosphatierungslösung mit einer Bürste auf die Metalloberfläche.
Phosphatierungslösungen:
Phosphatierungslösungen enthalten Phosphate, Säuren und Additive, die die Bildung einer gleichmäßigen und gut haftenden Phosphatschicht auf der Metalloberfläche fördern. Die Auswahl der Phosphatierungslösung hängt von verschiedenen Faktoren ab, einschließlich des zu beschichtenden Materials, der gewünschten Oberflächeneigenschaften und der Anforderungen der Anwendung.
Anwendungen der Phosphatierung:
Phosphatierung wird häufig in verschiedenen Branchen und Anwendungen eingesetzt, einschließlich Automobil-, Bau-, Elektronik- und Haushaltsgeräteindustrie. Die verbesserte Haftung und Korrosionsbeständigkeit, die durch die Phosphatierung erreicht werden, machen sie zu einer bevorzugten Vorbehandlungsmethode für viele beschichtete Produkte.
Qualitätssicherung:
Die Überwachung und Kontrolle des Phosphatierungsprozesses ist entscheidend, um eine gleichbleibende und qualitativ hochwertige Phosphatschicht zu gewährleisten. Dies kann durch regelmäßige Überprüfung der Phosphatierungslösung, Kontrolle der Badtemperatur und -konzentration sowie visuelle Inspektion der phosphatierten Bauteile erfolgen. Eine effektive Qualitätssicherung trägt dazu bei, Beschichtungsfehler zu minimieren und die Leistung der beschichteten Produkte zu maximieren.
Chromatierung
Chromatierung ist ein Verfahren in der Vorbehandlung für die Pulverbeschichtung, das dazu dient, die Oberfläche von Metallen zu schützen und die Haftung des Beschichtungspulvers zu verbessern. Es handelt sich um eine chemische Behandlung, bei der eine Chromatierungsschicht auf die Metalloberfläche aufgetragen wird, um Korrosionsschutz zu bieten und die Adhäsion der Beschichtung zu fördern.
Bedeutung der Chromatierung:
Chromatierung ist besonders wichtig für die Vorbehandlung von Aluminium- und Aluminiumlegierungen, da diese Metalle von Natur aus eine oxidierte Oberflächenschicht haben, die die Haftung des Beschichtungspulvers beeinträchtigen kann. Die Chromatierung bildet eine dünnere, gleichmäßigere und besser haftende Schicht auf der Metalloberfläche, was zu einer verbesserten Beschichtungsleistung führt.
Chromatierungsverfahren:
Es gibt verschiedene Chromatierungsverfahren, darunter die herkömmliche Chromatierung mit Chrom(VI)-Verbindungen und alternative Verfahren wie die Chromatierung mit Chrom(III)-Verbindungen, Passivierung und chemische Vorbehandlung ohne Chrom. Chrom(VI)-haltige Chromatierungslösungen sind aufgrund ihrer Effektivität weit verbreitet, aber sie stehen aufgrund ihrer Toxizität und Umweltauswirkungen zunehmend in der Kritik.
Anwendungen der Chromatierung:
Chromatierung wird häufig in verschiedenen Branchen eingesetzt, darunter die Automobilindustrie, Luft- und Raumfahrt, Elektronik und Bauwesen. Beschichtete Aluminiumkomponenten wie Karosserieteile, Aluminiumprofile und Gehäuse von Elektronikgeräten profitieren von der verbesserten Korrosionsbeständigkeit und Haftung, die durch die Chromatierung erreicht werden.
Qualitätssicherung:
Die Überwachung und Kontrolle des Chromatierungsprozesses ist entscheidend, um eine gleichmäßige und qualitativ hochwertige Beschichtung zu gewährleisten. Dies kann durch regelmäßige Überprüfung der Chromatierungslösung, Kontrolle der Badtemperatur und -konzentration sowie visuelle Inspektion der chromatierten Bauteile erfolgen. Eine effektive Qualitätssicherung trägt dazu bei, Beschichtungsfehler zu minimieren und die Leistung der beschichteten Produkte zu maximieren.
Chromatierung ist ein bewährtes Verfahren in der Vorbehandlung für die Pulverbeschichtung, das zu einer verbesserten Leistung und Lebensdauer der beschichteten Produkte beiträgt. Die Entwicklung alternativer Chromatierungsverfahren ohne Chrom(VI) und die Verbesserung der Umweltverträglichkeit sind jedoch wichtige Herausforderungen für die Zukunft.
Vorbehandlungschemikalien
Vorbehandlungschemikalien sind eine wesentliche Komponente in der Vorbehandlung für die Pulverbeschichtung und spielen eine entscheidende Rolle bei der Reinigung, Phosphatierung, Chromatierung oder anderen Vorbehandlungsverfahren. Diese Chemikalien werden verwendet, um die Oberfläche des zu beschichtenden Substrats vorzubereiten, um eine optimale Haftung und Leistung der Beschichtung zu gewährleisten.
Reinigungsmittel:
Reinigungsmittel werden eingesetzt, um Öl, Fett, Schmutz und andere Verunreinigungen von der Oberfläche zu entfernen, bevor das Substrat einer weiteren Vorbehandlung unterzogen wird. Diese Chemikalien können alkalisch, sauer oder neutral sein und werden je nach den spezifischen Anforderungen der Anwendung ausgewählt.
Phosphatierungslösungen:
Phosphatierungslösungen enthalten Phosphate, Säuren und Additive, die die Bildung einer Phosphatschicht auf der Metalloberfläche fördern. Diese Schicht dient als Haftvermittler für das Beschichtungspulver und verbessert die Haftung, Korrosionsbeständigkeit und Oberflächenqualität der Beschichtung.
Chromatierungslösungen:
Chromatierungslösungen enthalten Chromatierungsmittel, die eine Chromatierungsschicht auf der Metalloberfläche bilden, um Korrosionsschutz zu bieten und die Haftung des Beschichtungspulvers zu verbessern. Diese Schicht trägt zur Bildung einer gleichmäßigen und gut haftenden Beschichtung bei.
Entfettungslösungen:
Entfettungslösungen enthalten Tenside und Emulgatoren, die dazu dienen, Öl, Fett und andere organische Verunreinigungen von der Oberfläche zu lösen und zu entfernen. Eine gründliche Entfettung ist entscheidend für eine erfolgreiche Beschichtung und eine optimale Haftung des Beschichtungspulvers.
Passivierungslösungen:
Passivierungslösungen werden nach der Phosphatierung oder Chromatierung eingesetzt, um die gebildete Schicht zu stabilisieren und die Korrosionsbeständigkeit weiter zu verbessern. Diese Chemikalien tragen dazu bei, die Langzeitleistung der Beschichtung zu gewährleisten und die Bildung von Korrosion zu verhindern.
Die Auswahl der richtigen Vorbehandlungschemikalien ist entscheidend für den Erfolg des Beschichtungsprozesses und die Leistung der beschichteten Produkte. Eine sorgfältige Überwachung und Kontrolle der Chemikalien sowie eine regelmäßige Wartung der Vorbehandlungsanlage sind erforderlich, um eine konsistente und qualitativ hochwertige Vorbehandlung zu gewährleisten.
Spülen
Das Spülen ist ein wichtiger Schritt in der Vorbehandlung für die Pulverbeschichtung und bezieht sich auf den Prozess der Entfernung von Rückständen von Reinigungs- oder Vorbehandlungslösungen von der Oberfläche des zu beschichtenden Substrats. Durch das Spülen wird sichergestellt, dass keine chemischen Rückstände auf der Oberfläche verbleiben, die die Haftung oder Leistung der Beschichtung beeinträchtigen könnten.
Bedeutung des Spülens:
Das Spülen ist entscheidend, um sicherzustellen, dass die Oberfläche des Substrats frei von jeglichen Rückständen von Reinigungs- oder Vorbehandlungslösungen ist, bevor das Beschichtungspulver aufgetragen wird. Chemische Rückstände können die Haftung des Beschichtungspulvers beeinträchtigen, zu Beschichtungsfehlern führen oder die Lebensdauer der Beschichtung reduzieren. Das Spülen gewährleistet eine saubere und vorbereitete Oberfläche für eine erfolgreiche Beschichtung.
Spülmethoden:
Es gibt verschiedene Spülmethoden, darunter Sprühsysteme, Tauchbäder und Hochdruckreinigung. Sprühsysteme verwenden Wasser oder eine Spüllösung, die auf die Oberfläche gesprüht wird, um Rückstände zu entfernen. Tauchbäder tauchen die Bauteile in ein Spülbad ein, während Hochdruckreinigung einen starken Wasserstrahl verwendet, um Verunreinigungen zu entfernen.
Spülwasserqualität:
Die Qualität des Spülwassers ist entscheidend für die Wirksamkeit des Spülprozesses. Verunreinigungen im Spülwasser können Rückstände auf der Oberfläche hinterlassen und die Qualität der Beschichtung beeinträchtigen. Daher ist die Verwendung von sauberem und entionisiertem Wasser oder speziell formulierten Spüllösungen wichtig, um optimale Ergebnisse zu erzielen.
Spülzyklus:
Die Dauer und Anzahl der Spülzyklen hängen von verschiedenen Faktoren ab, einschließlich der Art der verwendeten Vorbehandlungslösungen, der Oberflächenbeschaffenheit und den Anforderungen der Anwendung. Ein ausreichender Spülzyklus gewährleistet eine gründliche Entfernung von Rückständen und eine saubere Oberfläche für die nachfolgende Beschichtung.
Qualitätssicherung:
Die Überwachung und Kontrolle des Spülprozesses ist entscheidend, um sicherzustellen, dass alle Rückstände effektiv entfernt werden und die Oberfläche sauber und vorbereitet ist. Dies kann durch regelmäßige Überprüfung der Spülwasserqualität, Kontrolle der Spülzeit und -temperatur sowie visuelle Inspektion der gespülten Bauteile erfolgen. Eine effektive Qualitätssicherung gewährleistet eine konsistente Spülleistung und minimiert das Risiko von Beschichtungsfehlern.
Oberflächenvorbereitung
Die Oberflächenvorbereitung ist ein entscheidender Schritt in der Vorbehandlung für die Pulverbeschichtung und bezieht sich auf die Maßnahmen, die ergriffen werden, um die Oberfläche des zu beschichtenden Substrats für die anschließende Beschichtung vorzubereiten. Eine gründliche Oberflächenvorbereitung ist entscheidend, um eine optimale Haftung, Haltbarkeit und Ästhetik der Beschichtung sicherzustellen.
Bedeutung der Oberflächenvorbereitung:
Eine ordnungsgemäße Oberflächenvorbereitung ist unerlässlich, um eine dauerhafte und hochwertige Beschichtung zu erzielen. Sie entfernt Verunreinigungen, verbessert die Haftung des Beschichtungspulvers und fördert die Bildung einer gleichmäßigen Beschichtung. Eine sorgfältige Oberflächenvorbereitung trägt auch zur Verbesserung der Korrosionsbeständigkeit und zur Verlängerung der Lebensdauer der Beschichtung bei.
Schritte der Oberflächenvorbereitung:
Die Oberflächenvorbereitung umfasst in der Regel mehrere Schritte, darunter Reinigung, Entfettung, Phosphatierung, Chromatierung und Spülung. Jeder Schritt zielt darauf ab, die Oberfläche von Verunreinigungen zu befreien, die Haftung zu verbessern und die Oberfläche für die Beschichtung vorzubereiten. Die Auswahl der spezifischen Vorbehandlungsschritte hängt von verschiedenen Faktoren ab, einschließlich des zu beschichtenden Materials, der gewünschten Oberflächeneigenschaften und der Anforderungen der Anwendung.
Methoden der Oberflächenvorbereitung:
Es gibt verschiedene Methoden zur Oberflächenvorbereitung, darunter mechanische Reinigung, chemische Reinigung, Strahlen und Ätzen. Mechanische Reinigung umfasst das Abkratzen, Bürsten oder Schleifen von Verunreinigungen, während chemische Reinigung die Verwendung von Reinigungs- und Vorbehandlungslösungen beinhaltet. Strahlen nutzt abrasive Partikel, um die Oberfläche zu reinigen und aufzurauen, während Ätzen chemische Lösungen verwendet, um die Oberfläche zu ätzen und zu reinigen.
Qualitätssicherung:
Die Überwachung und Kontrolle der Oberflächenvorbereitung ist entscheidend, um sicherzustellen, dass alle Schritte ordnungsgemäß durchgeführt werden und die Oberfläche sauber und vorbereitet ist. Dies kann durch regelmäßige Inspektionen, Überprüfung der Vorbehandlungslösungen und Kontrolle der Prozessparameter erfolgen. Eine effektive Qualitätssicherung gewährleistet eine konsistente Oberflächenvorbereitung und minimiert das Risiko von Beschichtungsfehlern.
Vorbehandlungstemperatur
Die Vorbehandlungstemperatur ist ein wichtiger Parameter in der Vorbehandlung für die Pulverbeschichtung und bezieht sich auf die Temperatur, bei der das zu beschichtende Substrat vor der eigentlichen Beschichtung behandelt wird. Die richtige Vorbehandlungstemperatur ist entscheidend, um eine optimale Haftung, Haltbarkeit und Ästhetik der Beschichtung zu gewährleisten.
Bedeutung der Vorbehandlungstemperatur:
Die Vorbehandlungstemperatur beeinflusst die Wirksamkeit der Vorbehandlungslösungen und ihre Fähigkeit, Verunreinigungen von der Oberfläche zu entfernen und eine Haftung des Beschichtungspulvers zu fördern. Eine zu niedrige Temperatur kann die Aktivität der Vorbehandlungslösungen verringern und zu unzureichender Reinigung oder Phosphatierung führen, während eine zu hohe Temperatur die Beschichtung beschädigen oder ihre Leistung beeinträchtigen kann.
Optimale Vorbehandlungstemperatur:
Die optimale Vorbehandlungstemperatur hängt von verschiedenen Faktoren ab, einschließlich der Art der zu beschichtenden Materialien, der verwendeten Vorbehandlungslösungen und den Anforderungen der Anwendung. In der Regel liegen die Vorbehandlungstemperaturen im Bereich von 50°C bis 70°C, können jedoch je nach spezifischer Anwendung variieren.
Einfluss auf die Beschichtungsleistung:
Die Vorbehandlungstemperatur beeinflusst direkt die Haftung, Haltbarkeit und Ästhetik der Beschichtung. Eine ordnungsgemäß durchgeführte Vorbehandlung bei der richtigen Temperatur ermöglicht eine effektive Reinigung und Vorbehandlung der Oberfläche, was zu einer verbesserten Haftung des Beschichtungspulvers und einer gleichmäßigen Beschichtung führt. Eine unzureichende Vorbehandlungstemperatur kann zu Beschichtungsfehlern wie Blasenbildung, Einschlüssen oder ungleichmäßiger Beschichtungsdicke führen.
Überwachung und Kontrolle:
Die Überwachung und Kontrolle der Vorbehandlungstemperatur ist entscheidend, um sicherzustellen, dass alle Vorbehandlungsschritte ordnungsgemäß durchgeführt werden und die Oberfläche sauber und vorbereitet ist. Dies kann durch regelmäßige Überprüfung der Badtemperatur, Kalibrierung der Temperaturfühler und Überwachung der Prozessparameter erfolgen. Eine effektive Überwachung und Kontrolle gewährleistet eine konsistente Vorbehandlungsleistung und minimiert das Risiko von Beschichtungsfehlern.
Vorbehandlungszeit
Die Vorbehandlungszeit ist ein entscheidender Parameter in der Vorbehandlung für die Pulverbeschichtung und bezieht sich auf die Dauer, für die das zu beschichtende Substrat in den Vorbehandlungslösungen eingetaucht oder damit behandelt wird. Die richtige Vorbehandlungszeit ist entscheidend, um eine optimale Reinigung, Phosphatierung, Chromatierung oder andere Vorbehandlungsprozesse zu gewährleisten.
Bedeutung der Vorbehandlungszeit:
Die Vorbehandlungszeit beeinflusst die Wirksamkeit der Vorbehandlungslösungen und ihre Fähigkeit, Verunreinigungen von der Oberfläche zu entfernen und eine Haftung des Beschichtungspulvers zu fördern. Eine ausreichende Vorbehandlungszeit ermöglicht eine gründliche Reinigung und Vorbehandlung der Oberfläche, während eine unzureichende Zeit zu unvollständiger Reinigung oder Vorbehandlung führen kann.
Optimale Vorbehandlungszeit:
Die optimale Vorbehandlungszeit hängt von verschiedenen Faktoren ab, einschließlich der Art der zu beschichtenden Materialien, der verwendeten Vorbehandlungslösungen und den Anforderungen der Anwendung. In der Regel liegen die Vorbehandlungszeiten im Bereich von wenigen Minuten bis zu mehreren Stunden, je nach den spezifischen Anforderungen der Vorbehandlung.
Einfluss auf die Beschichtungsleistung:
Die Vorbehandlungszeit beeinflusst direkt die Haftung, Haltbarkeit und Ästhetik der Beschichtung. Eine angemessene Vorbehandlungszeit ermöglicht eine effektive Reinigung und Vorbehandlung der Oberfläche, was zu einer verbesserten Haftung des Beschichtungspulvers und einer gleichmäßigen Beschichtung führt. Eine zu kurze Vorbehandlungszeit kann zu Beschichtungsfehlern wie unzureichender Haftung, ungleichmäßiger Beschichtungsdicke oder Korrosion führen.
Überwachung und Kontrolle:
Die Überwachung und Kontrolle der Vorbehandlungszeit ist entscheidend, um sicherzustellen, dass alle Vorbehandlungsschritte ordnungsgemäß durchgeführt werden und die Oberfläche sauber und vorbereitet ist. Dies kann durch regelmäßige Überprüfung der Prozesszeiten, Kalibrierung der Zeitgeber und Überwachung der Prozessparameter erfolgen. Eine effektive Überwachung und Kontrolle gewährleistet eine konsistente Vorbehandlungsleistung und minimiert das Risiko von Beschichtungsfehlern.
Trocknung
Die Trocknung ist ein entscheidender Schritt in der Vorbehandlung für die Pulverbeschichtung und bezieht sich auf den Prozess, bei dem das zu beschichtende Substrat nach der Vorbehandlung auf eine bestimmte Temperatur erhitzt wird, um Feuchtigkeit zu entfernen und die Oberfläche für die Beschichtung vorzubereiten.
Bedeutung der Trocknung:
Die Trocknung ist entscheidend, um sicherzustellen, dass die Oberfläche des Substrats frei von Feuchtigkeit ist, bevor das Beschichtungspulver aufgetragen wird. Feuchtigkeit auf der Oberfläche kann zu Beschichtungsfehlern wie Blasenbildung, Einschlüssen oder ungleichmäßiger Beschichtungsdicke führen. Durch die Trocknung wird die Oberfläche für eine erfolgreiche Beschichtung vorbereitet und die Haftung des Beschichtungspulvers verbessert.
Trocknungsmethoden:
Es gibt verschiedene Trocknungsmethoden, darunter Lufttrocknung, Ofentrocknung und Infrarottrocknung. Lufttrocknung erfolgt durch natürliche Luftzirkulation und ist kostengünstig, erfordert jedoch längere Trocknungszeiten. Ofentrocknung verwendet spezielle Trockenöfen, um das Substrat auf die erforderliche Temperatur zu erwärmen und Feuchtigkeit zu entfernen. Infrarottrocknung nutzt Infrarotstrahlen, um das Substrat schnell aufzuheizen und die Trocknungszeit zu verkürzen.
Optimale Trocknungstemperatur und -zeit:
Die optimale Trocknungstemperatur und -zeit hängen von verschiedenen Faktoren ab, einschließlich der Art der zu beschichtenden Materialien, der Dicke der Beschichtung und den Anforderungen der Anwendung. In der Regel liegen die Trocknungstemperaturen im Bereich von 80°C bis 120°C, und die Trocknungszeiten können von wenigen Minuten bis zu mehreren Stunden variieren, je nach den spezifischen Anforderungen der Vorbehandlung.
Qualitätssicherung:
Die Überwachung und Kontrolle der Trocknungsparameter ist entscheidend, um sicherzustellen, dass die Trocknung ordnungsgemäß durchgeführt wird und die Oberfläche sauber und vorbereitet ist. Dies kann durch regelmäßige Überprüfung der Trocknungstemperatur und -zeit, Kalibrierung der Trockenöfen und Überwachung der Trocknungsparameter erfolgen. Eine effektive Qualitätssicherung gewährleistet eine konsistente Trocknungsleistung und minimiert das Risiko von Beschichtungsfehlern.
Entfettung
Die Entfettung ist ein grundlegender Schritt in der Vorbehandlung für die Pulverbeschichtung und bezieht sich auf den Prozess der Entfernung von Öl, Fett, Schmutz und anderen organischen Verunreinigungen von der Oberfläche des zu beschichtenden Substrats. Eine gründliche Entfettung ist entscheidend, um eine optimale Haftung und Leistung der Beschichtung zu gewährleisten.
Bedeutung der Entfettung:
Öl, Fett und andere organische Verunreinigungen können auf der Oberfläche des Substrats vorhanden sein und die Haftung des Beschichtungspulvers beeinträchtigen. Die Entfettung entfernt diese Verunreinigungen und reinigt die Oberfläche, um eine gleichmäßige und haftende Beschichtung zu ermöglichen. Eine gründliche Entfettung ist besonders wichtig für Substrate, die mit Öl oder anderen Schmierstoffen behandelt wurden, sowie für Aluminium und Aluminiumlegierungen, die von Natur aus eine ölige Oberfläche haben können.
Entfettungsmethoden:
Es gibt verschiedene Methoden zur Entfettung, darunter mechanische Reinigung, Lösungsmittelreinigung und alkalische Reinigung. Mechanische Reinigung umfasst das Abkratzen, Bürsten oder Schleifen von Öl und Fett von der Oberfläche. Lösungsmittelreinigung verwendet chemische Lösungsmittel, um organische Verunreinigungen zu lösen und zu entfernen. Alkalische Reinigung verwendet alkalische Reinigungslösungen, um Öl, Fett und Schmutz von der Oberfläche zu emulgieren und zu entfernen.
Auswahl des Entfettungsmittels:
Die Auswahl des geeigneten Entfettungsmittels hängt von verschiedenen Faktoren ab, einschließlich der Art der zu entfettenden Verunreinigungen, der Art des zu beschichtenden Substrats und den Anforderungen der Anwendung. Die Verwendung eines falschen Entfettungsmittels kann zu unzureichender Reinigung oder Beschichtungsfehlern führen. Es ist wichtig, das richtige Entfettungsmittel entsprechend den spezifischen Anforderungen der Vorbehandlung auszuwählen.
Qualitätssicherung:
Die Überwachung und Kontrolle des Entfettungsprozesses ist entscheidend, um sicherzustellen, dass alle Verunreinigungen effektiv entfernt werden und die Oberfläche sauber und vorbereitet ist. Dies kann durch regelmäßige Überprüfung der Entfettungslösung, Kontrolle der Entfettungszeit und -temperatur sowie visuelle Inspektion der entfetteten Bauteile erfolgen. Eine effektive Qualitätssicherung gewährleistet eine konsistente Entfettungsleistung und minimiert das Risiko von Beschichtungsfehlern.
Phosphatierung
Die Phosphatierung ist ein wichtiger Schritt in der Vorbehandlung für die Pulverbeschichtung und bezieht sich auf den Prozess der Bildung einer Phosphatschicht auf der Metalloberfläche des zu beschichtenden Substrats. Diese Phosphatschicht dient als Haftvermittler für das Beschichtungspulver und verbessert die Haftung, Korrosionsbeständigkeit und Oberflächenqualität der Beschichtung.
Bedeutung der Phosphatierung:
Die Phosphatierung ist entscheidend, um eine gute Haftung und Haltbarkeit der Beschichtung zu gewährleisten. Die Phosphatschicht verbessert die Haftung des Beschichtungspulvers auf der Metalloberfläche und bildet eine chemische Bindung zwischen der Beschichtung und dem Substrat. Darüber hinaus erhöht die Phosphatschicht die Korrosionsbeständigkeit des beschichteten Bauteils und verbessert die Oberflächenqualität der Beschichtung.
Phosphatierungsprozess:
Der Phosphatierungsprozess umfasst typischerweise mehrere Schritte, darunter Reinigung, Spülung und Phosphatierung. Zunächst wird das zu beschichtende Substrat gereinigt, um Öl, Fett und andere Verunreinigungen zu entfernen. Anschließend wird das Substrat gründlich gespült, um alle Rückstände zu entfernen. Danach wird das Substrat in eine Phosphatierungslösung getaucht oder damit besprüht, um die Phosphatschicht zu bilden. Die Phosphatierung kann je nach den Anforderungen der Anwendung in einem einzigen Schritt oder in mehreren Schritten erfolgen.
Arten von Phosphatierungslösungen:
Es gibt verschiedene Arten von Phosphatierungslösungen, darunter Zinkphosphat, Eisenphosphat und Manganphosphat. Die Auswahl der Phosphatierungslösung hängt von verschiedenen Faktoren ab, einschließlich des zu beschichtenden Materials, der gewünschten Oberflächeneigenschaften und den Anforderungen der Anwendung. Jede Art von Phosphatierungslösung hat ihre eigenen Vor- und Nachteile hinsichtlich der Haftung, Korrosionsbeständigkeit und Kosten.
Qualitätssicherung:
Die Überwachung und Kontrolle des Phosphatierungsprozesses ist entscheidend, um sicherzustellen, dass eine gleichmäßige und gut haftende Phosphatschicht gebildet wird. Dies kann durch regelmäßige Überprüfung der Phosphatierungslösung, Kontrolle der Prozesstemperatur und -zeit sowie visuelle Inspektion der phosphatierten Bauteile erfolgen. Eine effektive Qualitätssicherung gewährleistet eine konsistente Phosphatierung und minimiert das Risiko von Beschichtungsfehlern.
Chromatierung
Die Chromatierung ist ein wichtiger Schritt in der Vorbehandlung für die Pulverbeschichtung und bezieht sich auf den Prozess der Bildung einer Chromatschicht auf der Metalloberfläche des zu beschichtenden Substrats. Diese Chromatschicht dient als Haftvermittler für das Beschichtungspulver und verbessert die Haftung, Korrosionsbeständigkeit und Oberflächenqualität der Beschichtung.
Bedeutung der Chromatierung:
Die Chromatierung spielt eine entscheidende Rolle bei der Verbesserung der Haftung und Haltbarkeit der Beschichtung. Die Chromatschicht verbessert die Haftung des Beschichtungspulvers auf der Metalloberfläche und bildet eine chemische Bindung zwischen der Beschichtung und dem Substrat. Darüber hinaus erhöht die Chromatschicht die Korrosionsbeständigkeit des beschichteten Bauteils und verbessert die Oberflächenqualität der Beschichtung.
Chromatierungsprozess:
Der Chromatierungsprozess umfasst typischerweise mehrere Schritte, darunter Reinigung, Spülung und Chromatierung. Zunächst wird das zu beschichtende Substrat gereinigt, um Öl, Fett und andere Verunreinigungen zu entfernen. Anschließend wird das Substrat gründlich gespült, um alle Rückstände zu entfernen. Danach wird das Substrat in eine Chromatierungslösung getaucht oder damit besprüht, um die Chromatschicht zu bilden. Die Chromatierung kann je nach den Anforderungen der Anwendung in einem einzigen Schritt oder in mehreren Schritten erfolgen.
Arten von Chromatierungslösungen:
Es gibt verschiedene Arten von Chromatierungslösungen, darunter hexavalentes Chromat, trivalentes Chromat und chromfreie Chromatierung. Die Auswahl der Chromatierungslösung hängt von verschiedenen Faktoren ab, einschließlich des zu beschichtenden Materials, der gewünschten Oberflächeneigenschaften und den Anforderungen der Anwendung. Jede Art von Chromatierungslösung hat ihre eigenen Vor- und Nachteile hinsichtlich der Haftung, Korrosionsbeständigkeit und Umweltverträglichkeit.
Qualitätssicherung:
Die Überwachung und Kontrolle des Chromatierungsprozesses ist entscheidend, um sicherzustellen, dass eine gleichmäßige und gut haftende Chromatschicht gebildet wird. Dies kann durch regelmäßige Überprüfung der Chromatierungslösung, Kontrolle der Prozesstemperatur und -zeit sowie visuelle Inspektion der chromatierten Bauteile erfolgen. Eine effektive Qualitätssicherung gewährleistet eine konsistente Chromatierung und minimiert das Risiko von Beschichtungsfehlern.
Spülung
Die Spülung ist ein wichtiger Schritt in der Vorbehandlung für die Pulverbeschichtung und bezieht sich auf den Prozess der gründlichen Reinigung des zuvor behandelten Substrats, um alle Rückstände von Reinigungs- und Vorbehandlungslösungen zu entfernen. Eine ordnungsgemäße Spülung ist entscheidend, um sicherzustellen, dass die Oberfläche sauber und frei von Verunreinigungen ist, bevor das Beschichtungspulver aufgetragen wird.
Bedeutung der Spülung:
Die Spülung dient dazu, alle Rückstände von Reinigungs- und Vorbehandlungslösungen von der Oberfläche des Substrats zu entfernen, um eine saubere und vorbereitete Oberfläche für die Beschichtung zu gewährleisten. Unzureichende Spülung kann zu Beschichtungsfehlern wie ungleichmäßiger Beschichtung, Haftungsproblemen oder Korrosion führen. Eine gründliche Spülung ist daher entscheidend für die Qualität und Leistung der Beschichtung.
Spülverfahren:
Die Spülung kann mit Wasser oder speziellen Spülungslösungen durchgeführt werden. Das zuvor behandelte Substrat wird in einem Tank mit Spülwasser eingetaucht oder mit Wasser besprüht, um alle Rückstände zu entfernen. Die Spülung sollte gründlich und vollständig sein, um sicherzustellen, dass keine Rückstände von Reinigungs- oder Vorbehandlungslösungen auf der Oberfläche verbleiben.
Qualitätssicherung:
Die Überwachung und Kontrolle des Spülprozesses ist entscheidend, um sicherzustellen, dass alle Rückstände von Reinigungs- und Vorbehandlungslösungen ordnungsgemäß entfernt werden. Dies kann durch regelmäßige Überprüfung der Spülwasserqualität, Kontrolle der Spülzeit und -temperatur sowie visuelle Inspektion der gespülten Bauteile erfolgen. Eine effektive Qualitätssicherung gewährleistet eine konsistente Spülleistung und minimiert das Risiko von Beschichtungsfehlern.
Dekontamination
Die Dekontamination ist ein kritischer Schritt in der Vorbehandlung für die Pulverbeschichtung und bezieht sich auf den Prozess der Entfernung von Verunreinigungen, die potenziell die Beschichtung beeinträchtigen könnten. Dies umfasst die Beseitigung von Ölen, Fetten, Staub, Fingerabdrücken und anderen Partikeln von der Oberfläche des zu beschichtenden Substrats, um eine optimale Haftung und Leistung der Beschichtung sicherzustellen.
Bedeutung der Dekontamination:
Die Dekontamination ist entscheidend, um sicherzustellen, dass die Oberfläche des Substrats frei von jeglichen Verunreinigungen ist, die die Haftung oder Qualität der Beschichtung beeinträchtigen könnten. Öle, Fetten und Staubpartikel können beispielsweise eine Barriere zwischen der Beschichtung und dem Substrat bilden, was zu Haftungsproblemen oder Beschichtungsfehlern führen kann. Die Dekontamination stellt sicher, dass die Oberfläche sauber und vorbereitet ist, um eine hochwertige Beschichtung zu ermöglichen.
Dekontaminationsmethoden:
Es gibt verschiedene Methoden zur Dekontamination, einschließlich mechanischer Reinigung, Lösungsmittelreinigung und Oberflächenbehandlung. Mechanische Reinigung umfasst das Abwischen, Schleifen oder Sandstrahlen der Oberfläche, um Verunreinigungen zu entfernen. Lösungsmittelreinigung verwendet chemische Lösungsmittel, um Öl, Fett und andere organische Verunreinigungen zu lösen und zu entfernen. Oberflächenbehandlungen wie Plasmareinigung oder Plasmaätzen können auch zur Dekontamination eingesetzt werden, um die Oberfläche zu reinigen und zu aktivieren.
Qualitätssicherung:
Die Überwachung und Kontrolle der Dekontaminationsprozesse ist entscheidend, um sicherzustellen, dass alle Verunreinigungen ordnungsgemäß entfernt werden und die Oberfläche sauber und vorbereitet ist. Dies kann durch regelmäßige Überprüfung der Reinigungsergebnisse, Kontrolle der Reinigungszeit und -methode sowie visuelle Inspektion der dekontaminierten Oberfläche erfolgen. Eine effektive Qualitätssicherung gewährleistet eine konsistente Dekontaminationsleistung und minimiert das Risiko von Beschichtungsfehlern.
Vorbehandlungslösungen
Vorbehandlungslösungen sind chemische Zusammensetzungen, die zur Reinigung, Aktivierung und Vorbereitung der Oberfläche des zu beschichtenden Substrats für die Pulverbeschichtung verwendet werden. Diese Lösungen spielen eine entscheidende Rolle bei der Entfernung von Verunreinigungen, der Verbesserung der Haftung des Beschichtungspulvers und der Förderung der Korrosionsbeständigkeit des beschichteten Bauteils.
Arten von Vorbehandlungslösungen:
- Entfettungslösungen: Entfettungslösungen werden verwendet, um Öle, Fette und andere organische Verunreinigungen von der Oberfläche des Substrats zu entfernen. Sie können alkalische oder saure Lösungen sein, die die Verunreinigungen emulgieren und von der Oberfläche abspülen.
- Phosphatierungslösungen: Phosphatierungslösungen bilden eine Phosphatschicht auf der Metalloberfläche, die als Haftvermittler für das Beschichtungspulver dient und die Korrosionsbeständigkeit verbessert. Sie können Zinkphosphat, Eisenphosphat oder Manganphosphat enthalten.
- Chromatierungslösungen: Chromatierungslösungen bilden eine Chromatschicht auf der Metalloberfläche, die die Haftung des Beschichtungspulvers verbessert und die Korrosionsbeständigkeit erhöht. Sie können hexavalentes Chromat, trivalentes Chromat oder chromfreie Chromatierung enthalten.
- Spülungslösungen: Spülungslösungen werden verwendet, um alle Rückstände von Reinigungs- und Vorbehandlungslösungen von der Oberfläche des Substrats zu entfernen. Sie sind in der Regel Wasser oder spezielle Spülungslösungen.
Auswahl der Vorbehandlungslösung:
Die Auswahl der geeigneten Vorbehandlungslösung hängt von verschiedenen Faktoren ab, einschließlich des zu beschichtenden Materials, der Art der Verunreinigungen, der gewünschten Oberflächeneigenschaften und den Anforderungen der Anwendung. Es ist wichtig, die richtige Vorbehandlungslösung entsprechend den spezifischen Anforderungen der Vorbehandlung zu wählen, um eine optimale Leistung der Beschichtung zu gewährleisten.
Anwendung und Qualitätssicherung:
Die Vorbehandlungslösungen sollten gemäß den Herstelleranweisungen angewendet und kontrolliert werden, um eine effektive Reinigung und Vorbehandlung der Oberfläche zu gewährleisten. Die Überwachung der Lösungskonzentration, Temperatur und Einwirkzeit ist entscheidend, um sicherzustellen, dass die Vorbehandlung ordnungsgemäß durchgeführt wird. Eine effektive Qualitätssicherung minimiert das Risiko von Beschichtungsfehlern und gewährleistet eine konsistente Leistung der Beschichtung.
Oberflächenprofil
Das Oberflächenprofil bezieht sich auf die Beschaffenheit und Textur der Oberfläche eines Substrats nach der Vorbehandlung für die Pulverbeschichtung. Ein geeignetes Oberflächenprofil ist entscheidend für die Haftung und Haltbarkeit der Beschichtung und wird durch die Vorbehandlungsmethoden und -parameter beeinflusst.
Bedeutung des Oberflächenprofils:
Ein angemessenes Oberflächenprofil ist wichtig, um eine gute Haftung zwischen dem Beschichtungspulver und dem Substrat zu gewährleisten. Eine zu glatte Oberfläche kann dazu führen, dass das Beschichtungspulver nicht ausreichend haftet und sich leicht ablöst, während eine zu raue Oberfläche die Beschichtung ungleichmäßig machen kann und zu Haftungsproblemen führen kann.
Einflussfaktoren auf das Oberflächenprofil:
- Vorbehandlungsmethoden: Die Auswahl der Vorbehandlungsmethoden wie Schleifen, Sandstrahlen oder Chemikalienbehandlung beeinflusst das Oberflächenprofil maßgeblich. Jede Methode erzeugt unterschiedliche Oberflächentexturen und -strukturen.
- Substratmaterial: Verschiedene Materialien wie Metalle, Kunststoffe oder Holz haben unterschiedliche Oberflächeneigenschaften und erfordern daher unterschiedliche Vorbehandlungsverfahren, um das gewünschte Oberflächenprofil zu erreichen.
- Vorbehandlungsparameter: Parameter wie Strahlmittelgröße, Strahlmittelmenge, Strahlgeschwindigkeit, Temperatur und Druck haben einen direkten Einfluss auf das resultierende Oberflächenprofil. Die Anpassung dieser Parameter ermöglicht es, das gewünschte Profil zu erzielen.
Kontrolle und Qualitätssicherung:
Die Überwachung und Kontrolle des Oberflächenprofils ist entscheidend, um sicherzustellen, dass es den Anforderungen der spezifischen Anwendung entspricht. Dies kann durch visuelle Inspektion, Einsatz von Oberflächenprofilmessgeräten und regelmäßige Überprüfung der Vorbehandlungsparameter erfolgen. Eine effektive Qualitätssicherung gewährleistet eine konsistente Oberflächenqualität und minimiert das Risiko von Beschichtungsfehlern.
Trocknung
Die Trocknung ist ein wesentlicher Schritt in der Vorbehandlung für die Pulverbeschichtung und bezieht sich auf den Prozess der Entfernung von Feuchtigkeit von der Oberfläche des zu beschichtenden Substrats nach der Reinigung oder Vorbehandlung. Eine ordnungsgemäße Trocknung ist entscheidend, um eine optimale Haftung und Leistung der Beschichtung sicherzustellen.
Bedeutung der Trocknung:
Feuchtigkeit auf der Oberfläche des Substrats kann die Haftung und Haltbarkeit der Beschichtung beeinträchtigen. Durch die Trocknung wird die Feuchtigkeit von der Oberfläche entfernt, wodurch eine saubere und trockene Oberfläche entsteht, auf der das Beschichtungspulver gleichmäßig haften kann. Eine gründliche Trocknung ist besonders wichtig, um die Bildung von Blasen, Fehlstellen oder Haftungsproblemen zu vermeiden.
Trocknungsmethoden:
Es gibt verschiedene Methoden zur Trocknung, einschließlich Lufttrocknung, Ofentrocknung, Infrarottrocknung und Warmluftgebläsetrocknung. Lufttrocknung beinhaltet das Trocknen der Oberfläche durch natürliche Luftzirkulation, während Ofentrocknung das Substrat in einem Ofen bei erhöhter Temperatur trocknet. Infrarottrocknung nutzt Infrarotstrahlung, um die Oberfläche effizient zu trocknen, während Warmluftgebläsetrocknung heiße Luftströme verwendet, um die Feuchtigkeit zu verdampfen.
Trocknungsparameter:
Die Trocknungsparameter wie Temperatur, Luftfeuchtigkeit, Trocknungszeit und Luftströmungsgeschwindigkeit müssen sorgfältig kontrolliert und angepasst werden, um eine effektive Trocknung zu gewährleisten. Die Trocknungsparameter können je nach den Eigenschaften des Substrats, der Vorbehandlungsmethode und den Anforderungen der Beschichtung variieren. Eine Über- oder Untertrocknung kann zu Beschichtungsfehlern führen und die Qualität der Beschichtung beeinträchtigen.
Qualitätssicherung:
Die Überwachung und Kontrolle des Trocknungsprozesses ist entscheidend, um sicherzustellen, dass das Substrat ordnungsgemäß getrocknet wird. Dies kann durch regelmäßige Überprüfung der Trocknungsparameter, visuelle Inspektion der getrockneten Oberfläche und Einsatz von Feuchtigkeitsmessgeräten erfolgen. Eine effektive Qualitätssicherung gewährleistet eine konsistente Trocknungsleistung und minimiert das Risiko von Beschichtungsfehlern.
Oberflächenreinigung
Die Oberflächenreinigung ist ein entscheidender Schritt in der Vorbehandlung für die Pulverbeschichtung und bezieht sich auf den Prozess der Entfernung von Schmutz, Fett, Öl, Rost, Oxidationsschichten und anderen Verunreinigungen von der Oberfläche des zu beschichtenden Substrats. Eine gründliche Oberflächenreinigung ist unerlässlich, um eine optimale Haftung und Haltbarkeit der Beschichtung zu gewährleisten.
Bedeutung der Oberflächenreinigung:
Verunreinigungen auf der Oberfläche des Substrats können die Haftung und Haltbarkeit der Beschichtung beeinträchtigen. Fett, Öl und andere organische Verunreinigungen bilden eine Barriere zwischen dem Beschichtungspulver und dem Substrat, was zu Haftungsproblemen führen kann. Rost, Oxidationsschichten und andere Anhaftungen können die Beschichtung ungleichmäßig machen und die Haltbarkeit der Beschichtung beeinträchtigen.
Reinigungsmethoden:
Es gibt verschiedene Methoden zur Oberflächenreinigung, darunter mechanische Reinigung, chemische Reinigung und Lösungsmittelreinigung. Mechanische Reinigung umfasst das Abwischen, Schleifen oder Sandstrahlen der Oberfläche, um Verunreinigungen zu entfernen. Chemische Reinigung verwendet spezielle Reinigungslösungen, um Fett, Öl und andere organische Verunreinigungen zu lösen und zu entfernen. Lösungsmittelreinigung nutzt chemische Lösungsmittel, um bestimmte Verunreinigungen zu lösen und zu entfernen.
Reinigungsparameter:
Die Auswahl der geeigneten Reinigungsmethode und -parameter hängt von verschiedenen Faktoren ab, einschließlich des zu beschichtenden Materials, der Art der Verunreinigungen und den Anforderungen der Anwendung. Die Reinigungsparameter wie Reinigungsmittelkonzentration, Temperatur, Einwirkzeit und Reinigungsmethode müssen sorgfältig kontrolliert und angepasst werden, um eine effektive Reinigung zu gewährleisten.
Qualitätssicherung:
Die Überwachung und Kontrolle des Reinigungsprozesses ist entscheidend, um sicherzustellen, dass die Oberfläche des Substrats gründlich gereinigt wird. Dies kann durch regelmäßige Überprüfung der Reinigungsergebnisse, Kontrolle der Reinigungsparameter und visuelle Inspektion der gereinigten Oberfläche erfolgen. Eine effektive Qualitätssicherung gewährleistet eine konsistente Reinigungsleistung und minimiert das Risiko von Beschichtungsfehlern.
Vorbehandlung
Die Vorbehandlung ist ein wesentlicher Schritt in der Pulverbeschichtung und bezeichnet den Prozess der Vorbereitung der Oberfläche des zu beschichtenden Substrats, um eine optimale Haftung und Leistung der Beschichtung zu gewährleisten.
Bedeutung der Vorbehandlung:
Die Vorbehandlung spielt eine entscheidende Rolle bei der Qualität und Haltbarkeit der Beschichtung. Sie entfernt Verunreinigungen wie Fett, Öl, Rost, Staub und andere Partikel von der Oberfläche des Substrats, was die Haftung des Beschichtungspulvers verbessert und die Korrosionsbeständigkeit des beschichteten Bauteils erhöht.
Vorbehandlungsmethoden:
- Mechanische Vorbehandlung: Hierbei wird die Oberfläche des Substrats mechanisch gereinigt, um Verunreinigungen zu entfernen. Dies kann durch Schleifen, Bürsten, Sandstrahlen oder Schleuderradstrahlen erfolgen.
- Chemische Vorbehandlung: Chemische Vorbehandlung umfasst die Verwendung von Reinigungslösungen, die Verunreinigungen lösen und entfernen. Dies kann durch Entfetten, Phosphatieren, Chromatieren oder andere chemische Prozesse geschehen.
- Kombinierte Vorbehandlung: Oft werden mechanische und chemische Vorbehandlungsmethoden kombiniert, um eine gründliche Reinigung und Vorbereitung der Oberfläche zu erreichen.
Vorbehandlungsparameter:
Die Vorbehandlungsparameter wie Reinigungsmittelkonzentration, Temperatur, Einwirkzeit, Druck und Geschwindigkeit müssen sorgfältig kontrolliert und angepasst werden, um eine effektive Vorbehandlung zu gewährleisten. Die richtige Einstellung dieser Parameter hängt von den Eigenschaften des zu beschichtenden Materials, der Art der Verunreinigungen und den Anforderungen der Beschichtung ab.
Qualitätssicherung:
Die Überwachung und Kontrolle des Vorbehandlungsprozesses ist entscheidend, um sicherzustellen, dass die Oberfläche des Substrats ordnungsgemäß vorbereitet wird. Dies kann durch regelmäßige Überprüfung der Vorbehandlungsergebnisse, Kontrolle der Vorbehandlungsparameter und visuelle Inspektion der behandelten Oberfläche erfolgen. Eine effektive Qualitätssicherung gewährleistet eine konsistente Vorbehandlungsleistung und minimiert das Risiko von Beschichtungsfehlern.
Phosphatierung
Die Phosphatierung ist eine wichtige Vorbehandlungsmethode für die Pulverbeschichtung, bei der eine Phosphatschicht auf der Metalloberfläche erzeugt wird. Diese Schicht verbessert die Haftung des Beschichtungspulvers auf dem Substrat und erhöht die Korrosionsbeständigkeit des beschichteten Bauteils.
Bedeutung der Phosphatierung:
Die Phosphatierung dient dazu, eine saubere, korrosionsbeständige Oberfläche zu schaffen und die Haftung des Beschichtungspulvers zu verbessern. Die Phosphatschicht bildet eine chemische Verbindung mit dem Metallsubstrat, die als Haftvermittler für das Beschichtungspulver dient. Dadurch wird eine feste Verbindung zwischen Beschichtung und Substrat erreicht.
Phosphatierungsprozess:
Der Phosphatierungsprozess umfasst typischerweise mehrere Schritte, darunter Entfetten, Spülen, Phosphatieren und Spülen. Zuerst wird das Substrat gründlich gereinigt, um alle Verunreinigungen zu entfernen. Anschließend wird es in einem Phosphatierungsbad getaucht oder besprüht, wo eine Phosphatschicht auf der Oberfläche erzeugt wird. Nach dem Phosphatieren wird das Bauteil erneut gespült, um überschüssiges Phosphat zu entfernen.
Arten von Phosphatierung:
Es gibt verschiedene Arten von Phosphatierung, darunter Zinkphosphatierung, Eisenphosphatierung und Manganphosphatierung. Jede Art von Phosphatierung bietet unterschiedliche Eigenschaften und Leistungen je nach den Anforderungen der Anwendung.
- Zinkphosphatierung: Geeignet für die Vorbehandlung von Stahl- und Eisenwerkstoffen. Bietet eine gute Korrosionsbeständigkeit und Haftung für die Beschichtung.
- Eisenphosphatierung: Häufig verwendet für die Vorbehandlung von Aluminium- und Zinkdruckgussteilen. Bietet eine gute Haftung und Korrosionsbeständigkeit.
- Manganphosphatierung: Wird für die Vorbehandlung von Werkzeugen und Maschinenteilen verwendet. Bietet eine verbesserte Verschleißfestigkeit und Schmierwirkung.
Qualitätssicherung:
Die Überwachung und Kontrolle des Phosphatierungsprozesses ist entscheidend, um eine gleichbleibende Beschichtungsqualität zu gewährleisten. Dies kann durch regelmäßige Überprüfung der Phosphatierschichtdicke, Kontrolle der Bädertemperatur und -konzentration sowie visuelle Inspektion der behandelten Oberfläche erfolgen. Eine effektive Qualitätssicherung minimiert das Risiko von Beschichtungsfehlern und gewährleistet eine konsistente Leistung der Beschichtung.
Entfettung
Die Entfettung ist ein wesentlicher Schritt in der Vorbehandlung für die Pulverbeschichtung und bezieht sich auf den Prozess der Entfernung von Ölen, Fetten und anderen organischen Verunreinigungen von der Oberfläche des zu beschichtenden Substrats.
Bedeutung der Entfettung:
Öle, Fette und andere organische Verunreinigungen können die Haftung und Haltbarkeit der Beschichtung beeinträchtigen, indem sie eine Barriere zwischen dem Beschichtungspulver und dem Substrat bilden. Eine gründliche Entfettung gewährleistet eine saubere Oberfläche, auf der das Beschichtungspulver gleichmäßig haften kann.
Entfettungsmethoden:
- Mechanische Entfettung: Hierbei wird die Oberfläche des Substrats mechanisch gereinigt, um Öle und Fette zu entfernen. Dies kann durch Abwischen, Bürsten oder Schleifen erfolgen.
- Chemische Entfettung: Chemische Entfettung umfasst die Verwendung von Reinigungslösungen, die Öle und Fette lösen und von der Oberfläche abspülen. Die Lösungen können alkalisch, sauer oder lösungsmittelbasiert sein, je nach den Anforderungen der Anwendung.
- Ultraschall-Entfettung: Ultraschall-Entfettung nutzt hochfrequente Schallwellen, um Öle und Fette von der Oberfläche des Substrats zu lösen und zu entfernen. Dies ist besonders effektiv für Teile mit komplexen Geometrien oder schwer zugänglichen Bereichen.
Qualitätssicherung:
Die Überwachung und Kontrolle des Entfettungsprozesses ist entscheidend, um sicherzustellen, dass alle Öle und Fette gründlich von der Oberfläche entfernt werden. Dies kann durch regelmäßige Überprüfung der Reinigungsergebnisse, Kontrolle der Entfettungsmethoden und visuelle Inspektion der gereinigten Oberfläche erfolgen. Eine effektive Qualitätssicherung gewährleistet eine konsistente Entfettungsleistung und minimiert das Risiko von Beschichtungsfehlern.
Chromatierung
Die Chromatierung ist eine wichtige Vorbehandlungsmethode für die Pulverbeschichtung, bei der eine Chromatschicht auf der Metalloberfläche erzeugt wird. Diese Schicht dient als Haftvermittler für das Beschichtungspulver und verbessert die Korrosionsbeständigkeit des beschichteten Bauteils.
Bedeutung der Chromatierung:
Chromatierung bietet mehrere Vorteile für die Beschichtung, darunter verbesserte Haftung des Beschichtungspulvers auf dem Substrat, erhöhte Korrosionsbeständigkeit und verbesserte elektrische Leitfähigkeit. Die Chromatschicht bildet eine chemische Verbindung mit dem Metallsubstrat, die eine starke Verbindung zwischen Beschichtung und Substrat gewährleistet.
Chromatierungsprozess:
Der Chromatierungsprozess umfasst typischerweise mehrere Schritte, darunter Reinigung, Chromatierung und Spülung. Zuerst wird das Substrat gründlich gereinigt, um alle Verunreinigungen zu entfernen. Anschließend wird es in einem Chromatierungsbad getaucht oder besprüht, wo eine Chromatschicht auf der Oberfläche erzeugt wird. Nach der Chromatierung wird das Bauteil erneut gespült, um überschüssiges Chromat zu entfernen.
Arten von Chromatierung:
Es gibt verschiedene Arten von Chromatierung, darunter hexavalentes Chromat, trivalentes Chromat und chromfreie Chromatierung. Jede Art von Chromatierung bietet unterschiedliche Eigenschaften und Leistungen je nach den Anforderungen der Anwendung.
- Hexavalentes Chromat: Bietet eine ausgezeichnete Haftung und Korrosionsbeständigkeit, ist jedoch aufgrund seiner toxischen Natur und Umweltauswirkungen zunehmend unerwünscht.
- Trivalentes Chromat: Bietet ähnliche Leistung wie hexavalentes Chromat, ist jedoch umweltfreundlicher und weniger toxisch.
- Chromfreie Chromatierung: Verwendet alternative Chemikalien wie Titan oder Zirkonium, um ähnliche Leistungen wie Chromatierung zu erzielen, ohne Chrom zu verwenden.
Qualitätssicherung:
Die Überwachung und Kontrolle des Chromatierungsprozesses ist entscheidend, um eine gleichbleibende Beschichtungsqualität zu gewährleisten. Dies kann durch regelmäßige Überprüfung der Chromatschichtdicke, Kontrolle der Bädertemperatur und -konzentration sowie visuelle Inspektion der behandelten Oberfläche erfolgen. Eine effektive Qualitätssicherung minimiert das Risiko von Beschichtungsfehlern und gewährleistet eine konsistente Leistung der Beschichtung.
Sandstrahlen
Sandstrahlen ist eine effektive mechanische Vorbehandlungsmethode für die Pulverbeschichtung, bei der abrasive Partikel mit Druck auf die Oberfläche des zu beschichtenden Substrats gestrahlt werden. Dieser Prozess entfernt Verunreinigungen, Rost, alte Beschichtungen und andere Oberflächenfehler, um eine saubere und raue Oberfläche für die Haftung des Beschichtungspulvers zu schaffen.
Bedeutung des Sandstrahlens:
Sandstrahlen ist eine der effektivsten Methoden zur Vorbereitung der Oberfläche für die Pulverbeschichtung, insbesondere bei stark verschmutzten oder rostigen Substraten. Durch den Einsatz von abrasiven Partikeln wie Sand, Glasperlen oder Aluminiumoxid wird die Oberfläche gründlich gereinigt und gleichzeitig eine rauere Textur erzeugt, die die Haftung des Beschichtungspulvers verbessert.
Sandstrahlprozess:
- Vorbereitung des Substrats: Das zu beschichtende Substrat wird vorbereitet, indem alle losen Verunreinigungen und Rost entfernt werden.
- Sandstrahlen: Ein Strahlmittel, wie Sand oder andere abrasive Partikel, wird mit Druck auf die Oberfläche des Substrats gestrahlt. Die abrasive Wirkung des Strahlmittels entfernt Verunreinigungen und erzeugt eine raue Oberfläche.
- Reinigung: Nach dem Sandstrahlen wird das Substrat gründlich gereinigt, um alle Rückstände des Strahlmittels zu entfernen und eine saubere Oberfläche zu erhalten.
Arten von Strahlmitteln:
- Siliziumkarbid: Geeignet für harte Oberflächen und aggressive Reinigung.
- Aluminiumoxid: Vielseitiges Strahlmittel für verschiedene Oberflächen.
- Glasperlen: Verwendet für eine feinere Strukturierung der Oberfläche und zur Entfernung von Farbe.
Qualitätssicherung:
Die Überwachung und Kontrolle des Sandstrahlprozesses ist entscheidend, um sicherzustellen, dass die Oberfläche gleichmäßig gestrahlt wird und alle Verunreinigungen effektiv entfernt werden. Dies kann durch regelmäßige Überprüfung der Strahlmittelflussrate, Strahldruck, Strahlzeit und visuelle Inspektion der gestrahlten Oberfläche erfolgen. Eine effektive Qualitätssicherung gewährleistet eine konsistente Oberflächenqualität und minimiert das Risiko von Beschichtungsfehlern.
Beizen
Beizen ist ein chemischer Vorbehandlungsprozess für die Pulverbeschichtung, der dazu dient, Metalloberflächen von Oxidationsschichten und anderen Verunreinigungen zu reinigen und gleichzeitig die Oberfläche für die Haftung des Beschichtungspulvers vorzubereiten.
Bedeutung des Beizens:
Beizen ist besonders wichtig für die Vorbehandlung von rostfreien Stählen, Aluminium und anderen Metallen, die zur Bildung von Oxidationsschichten neigen. Durch den Beizprozess werden diese Oxidationsschichten entfernt und die Oberfläche gereinigt, um eine optimale Haftung der Beschichtung zu gewährleisten.
Beizprozess:
- Vorbereitung des Substrats: Das zu beschichtende Substrat wird vor dem Beizen vorbereitet, indem lose Verunreinigungen und Fette entfernt werden.
- Beizlösung: Das Substrat wird dann in eine Beizlösung getaucht oder besprüht, die saure oder alkalische Chemikalien enthält, um die Oxidationsschichten zu lösen und zu entfernen.
- Spülung: Nach dem Beizen wird das Substrat gründlich gespült, um alle Rückstände der Beizlösung zu entfernen und die Oberfläche zu neutralisieren.
Arten von Beizlösungen:
- Saure Beizlösungen: Enthalten saure Chemikalien wie Salzsäure oder Schwefelsäure, um Oxidationsschichten zu entfernen.
- Alkalische Beizlösungen: Enthalten alkalische Chemikalien wie Natronlauge oder Kaliumhydroxid, um eine effektive Reinigung und Entfettung zu gewährleisten.
Qualitätssicherung:
Die Überwachung und Kontrolle des Beizprozesses ist entscheidend, um sicherzustellen, dass die Oberfläche gründlich gereinigt wird und alle Oxidationsschichten effektiv entfernt werden. Dies kann durch regelmäßige Überprüfung der Beizlösungskonzentration, Einwirkzeit, Spülverfahren und visuelle Inspektion der behandelten Oberfläche erfolgen. Eine effektive Qualitätssicherung gewährleistet eine konsistente Oberflächenqualität und minimiert das Risiko von Beschichtungsfehlern.
Passivierung
Passivierung ist ein wichtiger Prozess in der Vorbehandlung für die Pulverbeschichtung von rostfreiem Stahl. Dieser Prozess zielt darauf ab, die Oxidschicht auf der Oberfläche des rostfreien Stahls zu verbessern und gleichzeitig die Korrosionsbeständigkeit zu erhöhen.
Bedeutung der Passivierung:
Rostfreier Stahl bildet von Natur aus eine dünne Oxidschicht auf seiner Oberfläche, die ihn vor Korrosion schützt. Durch die Passivierung wird diese Oxidschicht verstärkt und verdichtet, was zu einer verbesserten Korrosionsbeständigkeit führt. Dies ist besonders wichtig, da rostfreier Stahl empfindlich auf Umweltfaktoren wie Feuchtigkeit und aggressive Chemikalien reagiert.
Passivierungsprozess:
- Vorbereitung des Substrats: Das zu beschichtende rostfreie Stahlsubstrat wird vorbereitet, indem alle Verunreinigungen und Öle von der Oberfläche entfernt werden.
- Passivierungslösung: Das Substrat wird dann in eine Passivierungslösung getaucht oder besprüht, die saure oder alkalische Chemikalien enthält, um die Oxidschicht zu stärken und zu verdichten.
- Spülung: Nach der Passivierung wird das Substrat gründlich gespült, um alle Rückstände der Passivierungslösung zu entfernen und die Oberfläche zu neutralisieren.
Arten von Passivierung:
- Säurepassivierung: Verwendet saure Chemikalien wie Salpetersäure oder Phosphorsäure, um die Oxidschicht zu verstärken und zu verdichten.
- Alkalische Passivierung: Verwendet alkalische Chemikalien wie Natronlauge oder Kaliumhydroxid, um ähnliche Effekte wie säurehaltige Passivierung zu erzielen.
Qualitätssicherung:
Die Überwachung und Kontrolle des Passivierungsprozesses ist entscheidend, um sicherzustellen, dass die Oxidschicht auf der Oberfläche des rostfreien Stahls ordnungsgemäß verstärkt und verdichtet wird. Dies kann durch regelmäßige Überprüfung der Passivierungslösungskonzentration, Einwirkzeit, Spülverfahren und visuelle Inspektion der behandelten Oberfläche erfolgen. Eine effektive Qualitätssicherung gewährleistet eine konsistente Oberflächenqualität und minimiert das Risiko von Beschichtungsfehlern.
Chemische Reinigung
Die chemische Reinigung ist ein wichtiger Schritt in der Vorbehandlung für die Pulverbeschichtung, bei dem chemische Lösungen verwendet werden, um Verunreinigungen, Öle, Fette und andere organische Substanzen von der Oberfläche des zu beschichtenden Substrats zu entfernen.
Bedeutung der chemischen Reinigung:
Chemische Reinigungsmethoden bieten eine effektive Möglichkeit, Oberflächen gründlich zu reinigen und gleichzeitig eine saubere Oberfläche für die Haftung des Beschichtungspulvers zu schaffen. Dies ist besonders wichtig für Substrate, die empfindlich auf mechanische Reinigungsmethoden reagieren oder schwer zugängliche Bereiche aufweisen.
Chemische Reinigungsprozesse:
- Entfettung: Verwendung von alkalischen oder lösungsmittelbasierten Reinigungslösungen, um Öle, Fette und andere organische Verunreinigungen zu entfernen.
- Entrosten: Verwendung von sauren Reinigungslösungen, um Rost und andere metallische Verunreinigungen zu entfernen und die Oberfläche zu reinigen.
- Phosphatierung: Verwendung von Phosphatlösungen, um eine Phosphatschicht auf der Oberfläche zu erzeugen und die Haftung des Beschichtungspulvers zu verbessern.
Arten von Reinigungslösungen:
- Alkalische Reinigungslösungen: Enthalten alkalische Chemikalien wie Natronlauge oder Kaliumhydroxid, um Fette und Öle zu lösen und zu entfernen.
- Säurehaltige Reinigungslösungen: Enthalten saure Chemikalien wie Salzsäure oder Schwefelsäure, um Rost und andere metallische Verunreinigungen zu entfernen.
- Lösungsmittelbasierte Reinigungslösungen: Enthalten organische Lösungsmittel wie Aceton oder Alkohole, um organische Verunreinigungen zu lösen und zu entfernen.
Qualitätssicherung:
Die Überwachung und Kontrolle des chemischen Reinigungsprozesses ist entscheidend, um sicherzustellen, dass alle Verunreinigungen gründlich von der Oberfläche entfernt werden und eine saubere Oberfläche für die Beschichtung vorhanden ist. Dies kann durch regelmäßige Überprüfung der Reinigungslösungskonzentration, Einwirkzeit, Spülverfahren und visuelle Inspektion der behandelten Oberfläche erfolgen. Eine effektive Qualitätssicherung gewährleistet eine konsistente Oberflächenqualität und minimiert das Risiko von Beschichtungsfehlern.
Mechanische Reinigung
Die mechanische Reinigung ist ein grundlegender Schritt in der Vorbehandlung für die Pulverbeschichtung, der verschiedene mechanische Verfahren umfasst, um Verunreinigungen, Rost, alte Beschichtungen und andere Oberflächenfehler von der Oberfläche des zu beschichtenden Substrats zu entfernen.
Bedeutung der mechanischen Reinigung:
Die mechanische Reinigung bietet eine effektive Möglichkeit, Oberflächen gründlich zu reinigen und gleichzeitig eine raue Textur zu erzeugen, die die Haftung des Beschichtungspulvers verbessert. Dies ist besonders wichtig für stark verschmutzte oder rostige Substrate, bei denen chemische oder andere Reinigungsmethoden möglicherweise nicht ausreichen.
Mechanische Reinigungsmethoden:
- Bürsten: Verwendung von rotierenden Bürsten oder Drahtbürsten, um Verunreinigungen von der Oberfläche zu entfernen und gleichzeitig eine raue Textur zu erzeugen.
- Schleifen: Verwendung von Schleifmaschinen oder Schleifpapier, um Rost, alte Beschichtungen und andere Oberflächenfehler zu entfernen und die Oberfläche zu glätten.
- Strahlen: Verwendung von Strahlmitteln wie Sand, Glasperlen oder Aluminiumoxid, die unter Druck auf die Oberfläche gestrahlt werden, um Verunreinigungen zu entfernen und eine raue Textur zu erzeugen.
Vorteile der mechanischen Reinigung:
- Entfernung von hartnäckigen Verunreinigungen und Rost.
- Erzeugung einer raue Textur, die die Haftung des Beschichtungspulvers verbessert.
- Möglichkeit, schwer zugängliche Bereiche zu reinigen.
Qualitätssicherung:
Die Überwachung und Kontrolle des mechanischen Reinigungsprozesses ist entscheidend, um sicherzustellen, dass die Oberfläche gleichmäßig gereinigt wird und alle Verunreinigungen effektiv entfernt werden. Dies kann durch regelmäßige Überprüfung der Reinigungsmethoden, Strahlmittelflussrate, Bürstendruck und visuelle Inspektion der behandelten Oberfläche erfolgen. Eine effektive Qualitätssicherung gewährleistet eine konsistente Oberflächenqualität und minimiert das Risiko von Beschichtungsfehlern.
Spülen
Das Spülen ist ein kritischer Schritt in der Vorbehandlung für die Pulverbeschichtung, der nach der Reinigung oder Behandlung der Oberfläche durchgeführt wird, um überschüssige Chemikalien, Verunreinigungen und Rückstände zu entfernen und die Oberfläche auf die Beschichtung vorzubereiten.
Bedeutung des Spülens:
Das Spülen ist entscheidend, um sicherzustellen, dass alle Rückstände von Reinigungslösungen, Beizmitteln, Passivierungslösungen oder anderen Vorbehandlungsmethoden vollständig von der Oberfläche entfernt werden. Unzureichendes Spülen kann zu Haftungsproblemen, Korrosion und Beschichtungsfehlern führen.
Spülmethoden:
- Wasser spülen: Das Substrat wird gründlich mit Wasser gespült, um alle Rückstände der Reinigungs- oder Behandlungslösungen zu entfernen. Dies kann durch Tauchen, Sprühen oder Strömen erfolgen.
- Neutralisieren: In einigen Fällen ist es erforderlich, die Oberfläche nach dem Spülen zu neutralisieren, um sicherzustellen, dass alle verbleibenden Chemikalien neutralisiert werden und keine Reaktionen mit dem Beschichtungspulver auftreten.
- Trocknen: Nach dem Spülen muss das Substrat gründlich getrocknet werden, um Feuchtigkeit zu entfernen und eine optimale Haftung des Beschichtungspulvers zu gewährleisten. Dies kann durch Lufttrocknung, Ofentrocknung oder andere Trocknungsmethoden erfolgen.
Vorteile des Spülens:
- Entfernung von Rückständen und Verunreinigungen von der Oberfläche.
- Vorbereitung der Oberfläche für eine optimale Haftung des Beschichtungspulvers.
- Minimierung von Beschichtungsfehlern und Korrosion.
Qualitätssicherung:
Die Überwachung und Kontrolle des Spülprozesses ist entscheidend, um sicherzustellen, dass alle Rückstände gründlich von der Oberfläche entfernt werden. Dies kann durch regelmäßige Überprüfung der Spülzeit, Spülwassertemperatur, Wasserqualität und visuelle Inspektion der behandelten Oberfläche erfolgen. Eine effektive Qualitätssicherung gewährleistet eine konsistente Oberflächenqualität und minimiert das Risiko von Beschichtungsfehlern.
Trocknung
Die Trocknung ist ein wesentlicher Schritt in der Vorbehandlung für die Pulverbeschichtung, der nach dem Spülen erfolgt, um die Oberfläche des Substrats gründlich zu trocknen und eine optimale Haftung des Beschichtungspulvers zu gewährleisten.
Bedeutung der Trocknung:
Die Trocknung ist entscheidend, um Feuchtigkeit von der Oberfläche des Substrats zu entfernen, da feuchte Oberflächen die Haftung des Beschichtungspulvers beeinträchtigen und zu Beschichtungsfehlern führen können. Ein gründlicher Trocknungsprozess ist daher unerlässlich, um eine hochwertige und dauerhafte Beschichtung zu gewährleisten.
Trocknungsmethoden:
- Lufttrocknung: Das Substrat wird an der Luft getrocknet, indem es an einem gut belüfteten Ort platziert wird. Dies ist die einfachste und kostengünstigste Methode der Trocknung, erfordert jedoch längere Trocknungszeiten.
- Ofentrocknung: Das Substrat wird in einem Ofen getrocknet, der auf eine bestimmte Temperatur eingestellt ist. Diese Methode bietet eine schnellere Trocknung und ermöglicht eine präzise Kontrolle der Trocknungsbedingungen.
- Infrarottrocknung: Diese Methode verwendet Infrarotstrahlung, um die Oberfläche des Substrats zu erwärmen und die Trocknungszeit zu verkürzen. Es ist besonders effektiv für schnell trocknende Beschichtungen oder empfindliche Substrate.
Vorteile der Trocknung:
- Entfernung von Feuchtigkeit von der Oberfläche des Substrats.
- Verbesserung der Haftung des Beschichtungspulvers.
- Minimierung von Beschichtungsfehlern und Korrosion.
Qualitätssicherung:
Die Überwachung und Kontrolle des Trocknungsprozesses ist entscheidend, um sicherzustellen, dass das Substrat vollständig getrocknet ist und keine Feuchtigkeit zurückbleibt. Dies kann durch regelmäßige Überprüfung der Trocknungszeit, Trocknungstemperatur, Luftfeuchtigkeit und visuelle Inspektion der behandelten Oberfläche erfolgen. Eine effektive Qualitätssicherung gewährleistet eine konsistente Oberflächenqualität und minimiert das Risiko von Beschichtungsfehlern.
Entfetten
Entfetten ist ein grundlegender Schritt in der Vorbehandlung für die Pulverbeschichtung, bei dem Öle, Fette und andere organische Verunreinigungen von der Oberfläche des zu beschichtenden Substrats entfernt werden, um eine optimale Haftung des Beschichtungspulvers zu gewährleisten.
Bedeutung des Entfettens:
Entfetten ist entscheidend, um sicherzustellen, dass die Oberfläche des Substrats frei von jeglichen Verunreinigungen ist, die die Haftung des Beschichtungspulvers beeinträchtigen könnten. Öle und Fette können die Oberfläche glatt machen und die Haftung des Beschichtungspulvers reduzieren, was zu Beschichtungsfehlern und einer geringeren Haltbarkeit der Beschichtung führen kann.
Entfettungsprozess:
- Vorbereitung des Substrats: Das zu beschichtende Substrat wird vorbereitet, indem lose Verunreinigungen und grober Schmutz von der Oberfläche entfernt werden.
- Entfettungslösung: Das Substrat wird dann in eine Entfettungslösung getaucht oder besprüht, die alkalische oder lösungsmittelbasierte Chemikalien enthält, um Öle, Fette und andere organische Verunreinigungen zu lösen und zu entfernen.
- Spülung: Nach dem Entfetten wird das Substrat gründlich gespült, um alle Rückstände der Entfettungslösung zu entfernen und die Oberfläche zu reinigen.
Arten von Entfettungslösungen:
- Alkalische Entfettungslösungen: Enthalten alkalische Chemikalien wie Natronlauge oder Kaliumhydroxid, um Öle und Fette zu emulgieren und zu entfernen.
- Lösungsmittelbasierte Entfettungslösungen: Enthalten organische Lösungsmittel wie Aceton oder Alkohole, um Öle und Fette zu lösen und zu entfernen.
Qualitätssicherung:
Die Überwachung und Kontrolle des Entfettungsprozesses ist entscheidend, um sicherzustellen, dass alle Verunreinigungen gründlich von der Oberfläche entfernt werden. Dies kann durch regelmäßige Überprüfung der Entfettungslösungskonzentration, Einwirkzeit, Spülverfahren und visuelle Inspektion der behandelten Oberfläche erfolgen. Eine effektive Qualitätssicherung gewährleistet eine konsistente Oberflächenqualität und minimiert das Risiko von Beschichtungsfehlern.
Phosphatierung
Phosphatierung ist ein wichtiger Schritt in der Vorbehandlung für die Pulverbeschichtung, bei dem eine Phosphatschicht auf der Oberfläche des zu beschichtenden Substrats erzeugt wird, um die Haftung des Beschichtungspulvers zu verbessern und die Korrosionsbeständigkeit zu erhöhen.
Bedeutung der Phosphatierung:
Phosphatierung bietet mehrere Vorteile, darunter die Verbesserung der Haftung des Beschichtungspulvers auf der Oberfläche des Substrats, die Erhöhung der Korrosionsbeständigkeit und die Förderung der Lackhaftung. Phosphatschichten dienen auch als Zwischenschicht zwischen dem Metallsubstrat und der Beschichtung, die zusätzlichen Schutz bietet.
Phosphatierungsprozess:
- Vorbereitung des Substrats: Das zu beschichtende Substrat wird vorbereitet, indem es gründlich gereinigt und von Verunreinigungen befreit wird.
- Phosphatierungslösung: Das Substrat wird dann in eine Phosphatierungslösung getaucht oder besprüht, die Phosphorsäure oder Phosphatverbindungen enthält, um eine Phosphatschicht auf der Oberfläche zu bilden.
- Spülung: Nach der Phosphatierung wird das Substrat gründlich gespült, um überschüssige Phosphatierungslösung zu entfernen und die Oberfläche zu reinigen.
Arten von Phosphatierung:
- Zinkphosphatierung: Bildet eine Zinkphosphatbeschichtung, die die Korrosionsbeständigkeit verbessert und die Haftung des Beschichtungspulvers erhöht.
- Eisenphosphatierung: Bildet eine Eisenphosphatbeschichtung, die eine gute Haftung und Korrosionsbeständigkeit bietet, jedoch weniger wirksam ist als Zinkphosphatierung.
Qualitätssicherung:
Die Überwachung und Kontrolle des Phosphatierungsprozesses ist entscheidend, um sicherzustellen, dass eine gleichmäßige und adhäsive Phosphatschicht auf der Oberfläche des Substrats gebildet wird. Dies kann durch regelmäßige Überprüfung der Phosphatierungslösungskonzentration, Einwirkzeit, Spülverfahren und visuelle Inspektion der behandelten Oberfläche erfolgen. Eine effektive Qualitätssicherung gewährleistet eine konsistente Oberflächenqualität und minimiert das Risiko von Beschichtungsfehlern.
Dekapieren
Dekapieren ist ein Verfahren in der Vorbehandlung für die Pulverbeschichtung, das verwendet wird, um alte Beschichtungen, Farben oder Verunreinigungen von der Oberfläche des zu beschichtenden Substrats zu entfernen.
Bedeutung des Dekapierens:
Das Dekapieren ist notwendig, um alte Beschichtungen oder Verunreinigungen zu entfernen, die die Haftung des neuen Beschichtungspulvers beeinträchtigen könnten. Es ermöglicht auch die Vorbereitung der Oberfläche für eine neue Beschichtung und kann dazu beitragen, Beschichtungsfehler zu vermeiden.
Dekapierungsprozess:
- Vorbereitung des Substrats: Das zu beschichtende Substrat wird vorbereitet, indem lose Verunreinigungen entfernt werden, um den Dekapierungsprozess zu erleichtern.
- Dekapierlösung: Das Substrat wird dann in eine Dekapierlösung getaucht oder besprüht, die chemische oder alkalische Lösungen enthält, um alte Beschichtungen oder Verunreinigungen zu lösen und zu entfernen.
- Entfernen der alten Beschichtung: Nach dem Einweichen oder Behandeln in der Dekapierlösung wird die alte Beschichtung manuell oder durch Spülen mit Wasser entfernt.
Arten von Dekapierlösungen:
- Chemische Dekapierlösungen: Enthalten Chemikalien wie Säuren oder Lösemittel, um alte Beschichtungen zu lösen und zu entfernen.
- Alkalische Dekapierlösungen: Enthalten alkalische Chemikalien wie Natronlauge, um alte Beschichtungen zu emulgieren und zu entfernen.
Qualitätssicherung:
Die Überwachung und Kontrolle des Dekapierungsprozesses ist entscheidend, um sicherzustellen, dass alle alten Beschichtungen oder Verunreinigungen vollständig von der Oberfläche entfernt werden. Dies kann durch regelmäßige Überprüfung der Dekapierlösungskonzentration, Einwirkzeit, Spülverfahren und visuelle Inspektion der behandelten Oberfläche erfolgen. Eine effektive Qualitätssicherung gewährleistet eine konsistente Oberflächenqualität und minimiert das Risiko von Beschichtungsfehlern.
Passivierung
Passivierung ist ein wichtiger Schritt in der Vorbehandlung für die Pulverbeschichtung, der nach dem Reinigen oder Behandeln der Oberfläche durchgeführt wird, um die Korrosionsbeständigkeit zu erhöhen und die Haftung des Beschichtungspulvers zu verbessern.
Bedeutung der Passivierung:
Passivierung ist wichtig, um die Korrosionsbeständigkeit von metallischen Oberflächen zu erhöhen, indem eine Schutzschicht auf der Oberfläche erzeugt wird. Diese Schicht verhindert, dass das Metall mit der Umgebung reagiert und Korrosion verursacht. Darüber hinaus kann eine Passivierung die Haftung des Beschichtungspulvers verbessern und die Haltbarkeit der Beschichtung erhöhen.
Passivierungsprozess:
- Vorbereitung des Substrats: Das zu beschichtende Substrat wird vorbereitet, indem es gründlich gereinigt und von Verunreinigungen befreit wird.
- Passivierungslösung: Das Substrat wird dann in eine Passivierungslösung getaucht oder besprüht, die chemische Verbindungen wie Chromat, Phosphat oder Nitrat enthält, um eine Schutzschicht auf der Oberfläche zu bilden.
- Spülung: Nach der Passivierung wird das Substrat gründlich gespült, um überschüssige Passivierungslösung zu entfernen und die Oberfläche zu reinigen.
Arten von Passivierung:
- Chromatierung: Bildet eine Chromatschicht auf der Oberfläche, die die Korrosionsbeständigkeit erhöht und die Haftung des Beschichtungspulvers verbessert.
- Phosphatierung: Bildet eine Phosphatschicht auf der Oberfläche, die Korrosionsbeständigkeit bietet und die Haftung des Beschichtungspulvers verbessern kann.
Qualitätssicherung:
Die Überwachung und Kontrolle des Passivierungsprozesses ist entscheidend, um sicherzustellen, dass eine gleichmäßige und adhäsive Schutzschicht auf der Oberfläche des Substrats gebildet wird. Dies kann durch regelmäßige Überprüfung der Passivierungslösungskonzentration, Einwirkzeit, Spülverfahren und visuelle Inspektion der behandelten Oberfläche erfolgen. Eine effektive Qualitätssicherung gewährleistet eine konsistente Oberflächenqualität und minimiert das Risiko von Beschichtungsfehlern.
Phosphatfreie Vorbehandlung
Die phosphatfreie Vorbehandlung ist eine Alternative zur herkömmlichen Phosphatierung in der Pulverbeschichtungsvorbereitung und bietet verschiedene Vorteile in Bezug auf Umweltfreundlichkeit, Effizienz und Kosten.
Bedeutung der phosphatfreien Vorbehandlung:
Die phosphatfreie Vorbehandlung umfasst Technologien und Prozesse, die keine Phosphate verwenden, um eine Oberfläche für die Pulverbeschichtung vorzubereiten. Dies kann durch den Einsatz von chemischen Vorbehandlungslösungen erreicht werden, die umweltfreundlicher sind und gleichzeitig eine gute Haftung und Korrosionsbeständigkeit bieten.
Vorteile der phosphatfreien Vorbehandlung:
- Umweltfreundlichkeit: Phosphatfreie Vorbehandlungslösungen sind weniger umweltschädlich und tragen zur Reduzierung von Schadstoffemissionen und Abfällen bei.
- Energieeffizienz: Einige phosphatfreie Vorbehandlungsmethoden erfordern weniger Energie für die Heiz- und Trocknungsprozesse, was zu einer Verringerung des Energieverbrauchs führt.
- Kosteneffizienz: Der Einsatz phosphatfreier Vorbehandlungslösungen kann zu Kosteneinsparungen führen, da sie oft weniger teuer sind als phosphathaltige Alternativen und weniger Wartungsaufwand erfordern.
- Verbesserte Haftung: Moderne phosphatfreie Vorbehandlungstechnologien bieten eine ausgezeichnete Haftung des Beschichtungspulvers auf der Oberfläche und gewährleisten eine gleichmäßige und dauerhafte Beschichtung.
Phosphatfreie Vorbehandlungstechnologien:
- Chromfreie Vorbehandlung: Verwendet chromfreie chemische Lösungen wie Titanate, Zirkonate oder Silane, um eine Vorbehandlungsschicht auf der Oberfläche zu bilden.
- Nano-Vorbehandlung: Nutzt nanotechnologische Verfahren, um eine dünne, chemisch aktive Schicht auf der Oberfläche zu erzeugen, die die Haftung des Beschichtungspulvers verbessert.
- Nanokeramik-Beschichtung: Bietet eine alternative Beschichtungstechnologie, bei der eine dünne Schicht aus Nanokeramikpartikeln auf die Oberfläche aufgebracht wird, um eine ausgezeichnete Haftung und Korrosionsbeständigkeit zu gewährleisten.
Qualitätssicherung:
Die Qualitätssicherung bei der phosphatfreien Vorbehandlung umfasst die Überwachung und Kontrolle der Vorbehandlungsprozesse, um sicherzustellen, dass eine hochwertige Oberfläche für die Pulverbeschichtung bereitgestellt wird. Dies kann durch regelmäßige Überprüfung der Vorbehandlungslösungskonzentration, Einwirkzeit, Spülverfahren und visuelle Inspektion der behandelten Oberfläche erfolgen. Eine effektive Qualitätssicherung gewährleistet eine konsistente Oberflächenqualität und minimiert das Risiko von Beschichtungsfehlern.
Chromatierung
Chromatierung ist ein Verfahren in der Vorbehandlung für die Pulverbeschichtung, bei dem eine Chromatschicht auf der Oberfläche des zu beschichtenden Substrats erzeugt wird, um die Korrosionsbeständigkeit zu erhöhen und die Haftung des Beschichtungspulvers zu verbessern.
Bedeutung der Chromatierung:
Chromatierung ist ein bewährtes Verfahren zur Verbesserung der Korrosionsbeständigkeit von metallischen Oberflächen. Die Chromatschicht bildet eine Schutzbarriere gegen Feuchtigkeit, Chemikalien und andere schädliche Umwelteinflüsse und erhöht gleichzeitig die Haftung des Beschichtungspulvers.
Chromatierungsprozess:
- Vorbereitung des Substrats: Das zu beschichtende Substrat wird vorbereitet, indem es gründlich gereinigt und von Verunreinigungen befreit wird.
- Chromatierungslösung: Das Substrat wird dann in eine Chromatierungslösung getaucht oder besprüht, die Chromsäure oder Chromverbindungen enthält, um eine Chromatschicht auf der Oberfläche zu bilden.
- Spülung: Nach der Chromatierung wird das Substrat gründlich gespült, um überschüssige Chromatierungslösung zu entfernen und die Oberfläche zu reinigen.
Arten von Chromatierung:
- Gelbchromatierung: Bildet eine gelbliche Chromatschicht auf der Oberfläche, die eine gute Korrosionsbeständigkeit bietet und häufig in der Automobilindustrie verwendet wird.
- Blau- oder Schwarzchromatierung: Bildet eine bläuliche oder schwarze Chromatschicht, die eine verbesserte Korrosionsbeständigkeit und ästhetische Eigenschaften bietet.
Qualitätssicherung:
Die Überwachung und Kontrolle des Chromatierungsprozesses ist entscheidend, um sicherzustellen, dass eine gleichmäßige und adhäsive Chromatschicht auf der Oberfläche des Substrats gebildet wird. Dies kann durch regelmäßige Überprüfung der Chromatierungslösungskonzentration, Einwirkzeit, Spülverfahren und visuelle Inspektion der behandelten Oberfläche erfolgen. Eine effektive Qualitätssicherung gewährleistet eine konsistente Oberflächenqualität und minimiert das Risiko von Beschichtungsfehlern.
Silanbehandlung
Die Silanbehandlung ist ein Verfahren in der Vorbehandlung für die Pulverbeschichtung, bei dem Silanverbindungen auf die Oberfläche des zu beschichtenden Substrats aufgetragen werden, um die Haftung des Beschichtungspulvers zu verbessern und die Korrosionsbeständigkeit zu erhöhen.
Bedeutung der Silanbehandlung:
Die Silanbehandlung bietet mehrere Vorteile, darunter die Verbesserung der Haftung des Beschichtungspulvers auf der Oberfläche des Substrats und die Erhöhung der Korrosionsbeständigkeit. Silanbeschichtungen sind bekannt für ihre ausgezeichnete chemische Beständigkeit und Haftungsfähigkeit auf verschiedenen Substraten.
Silanbehandlungsprozess:
- Vorbereitung des Substrats: Das zu beschichtende Substrat wird vorbereitet, indem es gründlich gereinigt und von Verunreinigungen befreit wird.
- Silanbeschichtung: Die Silanverbindung wird auf die Oberfläche des Substrats aufgetragen, entweder durch Tauchen, Sprühen oder Auftragen mit einem Pinsel.
- Aushärtung: Die Silanbeschichtung wird dann durch Wärme oder Lufttrocknung ausgehärtet, um eine dauerhafte Haftung auf der Oberfläche zu gewährleisten.
Vorteile der Silanbehandlung:
- Verbesserte Haftung: Silanbeschichtungen bieten eine ausgezeichnete Haftung des Beschichtungspulvers auf einer Vielzahl von Substraten, einschließlich Metallen, Kunststoffen und Glas.
- Korrosionsbeständigkeit: Silanbeschichtungen können die Korrosionsbeständigkeit des Substrats verbessern, indem sie eine Schutzschicht bilden, die Feuchtigkeit und Chemikalien abhält.
- Vielseitigkeit: Silanbeschichtungen können auf verschiedene Arten von Oberflächen aufgetragen werden und bieten eine breite Palette von Anwendungsmöglichkeiten in verschiedenen Branchen.
Qualitätssicherung:
Die Überwachung und Kontrolle des Silanbehandlungsprozesses ist entscheidend, um sicherzustellen, dass eine gleichmäßige und adhäsive Beschichtung auf der Oberfläche des Substrats erzeugt wird. Dies kann durch regelmäßige Überprüfung der Silanbeschichtungskonzentration, Auftragstechnik, Aushärtungsverfahren und visuelle Inspektion der behandelten Oberfläche erfolgen. Eine effektive Qualitätssicherung gewährleistet eine konsistente Oberflächenqualität und minimiert das Risiko von Beschichtungsfehlern.
Vorbehandlung mit Nano-Keramikbeschichtung
Die Vorbehandlung mit Nano-Keramikbeschichtung ist ein fortschrittliches Verfahren in der Pulverbeschichtungsvorbereitung, bei dem eine dünnste Schicht aus Nanokeramikpartikeln auf der Oberfläche des zu beschichtenden Substrats erzeugt wird, um die Haftung des Beschichtungspulvers zu verbessern und die Korrosionsbeständigkeit zu erhöhen.
Bedeutung der Nano-Keramikbeschichtung:
Die Nano-Keramikbeschichtung bietet eine innovative Lösung für die Oberflächenvorbereitung in der Pulverbeschichtung, indem sie eine ultradünne, chemisch aktive Schicht erzeugt, die eine hervorragende Haftung des Beschichtungspulvers gewährleistet und gleichzeitig eine hohe Korrosionsbeständigkeit bietet.
Nano-Keramikbeschichtungsprozess:
- Vorbereitung des Substrats: Das zu beschichtende Substrat wird vorbereitet, indem es gründlich gereinigt und von Verunreinigungen befreit wird.
- Nano-Keramikbeschichtung: Die Nano-Keramikpartikel werden auf die Oberfläche des Substrats aufgebracht, entweder durch Tauchen, Sprühen oder Beschichten mit einer speziellen Beschichtungsmaschine.
- Aushärtung: Die Nano-Keramikbeschichtung wird durch Wärme oder UV-Licht ausgehärtet, um eine dauerhafte Verbindung mit der Oberfläche des Substrats zu gewährleisten.
Vorteile der Nano-Keramikbeschichtung:
- Hervorragende Haftung: Die Nano-Keramikbeschichtung bietet eine außergewöhnliche Haftung des Beschichtungspulvers auf der Oberfläche des Substrats, was zu einer gleichmäßigen und langlebigen Beschichtung führt.
- Hohe Korrosionsbeständigkeit: Die Nano-Keramikbeschichtung bildet eine Schutzschicht auf der Oberfläche des Substrats, die es vor Korrosion durch Feuchtigkeit, Chemikalien und andere Umwelteinflüsse schützt.
- Geringer Materialverbrauch: Aufgrund der ultradünnen Schichtdicke der Nano-Keramikbeschichtung ist der Materialverbrauch im Vergleich zu herkömmlichen Beschichtungsverfahren geringer, was zu Kostenersparnissen führt.
Qualitätssicherung:
Die Überwachung und Kontrolle des Nano-Keramikbeschichtungsprozesses ist entscheidend, um sicherzustellen, dass eine gleichmäßige und adhäsive Beschichtung auf der Oberfläche des Substrats erzeugt wird. Dies kann durch regelmäßige Überprüfung der Beschichtungsdicke, Aushärtungsverfahren und visuelle Inspektion der behandelten Oberfläche erfolgen. Eine effektive Qualitätssicherung gewährleistet eine konsistente Oberflächenqualität und minimiert das Risiko von Beschichtungsfehlern.
Entfetten
Entfetten ist ein entscheidender Schritt in der Vorbehandlung für die Pulverbeschichtung, der darauf abzielt, Fett, Öl, Schmiermittel und andere Verunreinigungen von der Oberfläche des zu beschichtenden Substrats zu entfernen.
Bedeutung des Entfettens:
Entfetten ist entscheidend, um eine saubere Oberfläche zu schaffen, die frei von Verunreinigungen ist und eine optimale Haftung des Beschichtungspulvers ermöglicht. Fett, Öl und Schmiermittel können die Haftung des Beschichtungspulvers beeinträchtigen und zu Beschichtungsfehlern führen.
Entfettungsprozess:
- Vorbereitung des Substrats: Das zu beschichtende Substrat wird vorbereitet, indem grobe Verschmutzungen und Rückstände von der Oberfläche entfernt werden.
- Entfettungslösung: Das Substrat wird dann in eine Entfettungslösung getaucht oder besprüht, die chemische Reinigungsmittel oder Lösungsmittel enthält, um Fett, Öl und Schmiermittel zu lösen und zu entfernen.
- Spülung: Nach der Entfettung wird das Substrat gründlich gespült, um überschüssige Entfettungslösung zu entfernen und die Oberfläche zu reinigen.
Arten der Entfettung:
- Alkalische Entfettung: Verwendet alkalische Reinigungsmittel wie Natronlauge, um Fett und Öl zu emulgieren und zu entfernen.
- Lösungsmittelentfettung: Verwendet organische Lösungsmittel wie Kohlenwasserstoffe oder Alkohole, um Fett und Öl von der Oberfläche zu lösen und zu entfernen.
Qualitätssicherung:
Die Überwachung und Kontrolle des Entfettungsprozesses ist entscheidend, um sicherzustellen, dass alle Verunreinigungen von der Oberfläche des Substrats entfernt werden. Dies kann durch regelmäßige Überprüfung der Entfettungslösungskonzentration, Einwirkzeit, Spülverfahren und visuelle Inspektion der behandelten Oberfläche erfolgen. Eine effektive Qualitätssicherung gewährleistet eine konsistente Oberflächenqualität und minimiert das Risiko von Beschichtungsfehlern.
Reinigen
Reinigen ist ein grundlegender Schritt in der Vorbehandlung für die Pulverbeschichtung, der darauf abzielt, Schmutz, Staub, Oxidationsschichten und andere Verunreinigungen von der Oberfläche des zu beschichtenden Substrats zu entfernen.
Bedeutung des Reinigens:
Das Reinigen ist entscheidend, um eine saubere Oberfläche zu schaffen, die frei von Verunreinigungen ist und eine optimale Haftung des Beschichtungspulvers ermöglicht. Schmutz, Staub und Oxidationsschichten können die Haftung des Beschichtungspulvers beeinträchtigen und zu Beschichtungsfehlern führen.
Reinigungsprozess:
- Vorbereitung des Substrats: Das zu beschichtende Substrat wird vorbereitet, indem grobe Verschmutzungen und Rückstände von der Oberfläche entfernt werden.
- Reinigungslösung: Das Substrat wird dann in eine Reinigungslösung getaucht oder besprüht, die chemische Reinigungsmittel oder Lösungsmittel enthält, um Schmutz, Staub und Oxidationsschichten zu lösen und zu entfernen.
- Spülung: Nach dem Reinigen wird das Substrat gründlich gespült, um überschüssige Reinigungslösung zu entfernen und die Oberfläche zu reinigen.
Arten der Reinigung:
- Wasserbasierter Reiniger: Verwendet Wasser und alkalische Reinigungsmittel, um Schmutz und Staub von der Oberfläche zu lösen und zu entfernen.
- Lösungsmittelreinigung: Verwendet organische Lösungsmittel wie Kohlenwasserstoffe oder Alkohole, um hartnäckige Verunreinigungen wie Öl oder Fett zu lösen und zu entfernen.
Qualitätssicherung:
Die Überwachung und Kontrolle des Reinigungsprozesses ist entscheidend, um sicherzustellen, dass alle Verunreinigungen von der Oberfläche des Substrats entfernt werden. Dies kann durch regelmäßige Überprüfung der Reinigungslösungskonzentration, Einwirkzeit, Spülverfahren und visuelle Inspektion der behandelten Oberfläche erfolgen. Eine effektive Qualitätssicherung gewährleistet eine konsistente Oberflächenqualität und minimiert das Risiko von Beschichtungsfehlern.
Phosphatierung
Phosphatierung ist ein wichtiger Schritt in der Vorbehandlung für die Pulverbeschichtung, bei dem eine Phosphatschicht auf der Oberfläche des zu beschichtenden Substrats erzeugt wird, um die Korrosionsbeständigkeit zu erhöhen und die Haftung des Beschichtungspulvers zu verbessern.
Bedeutung der Phosphatierung:
Phosphatierung ist ein bewährtes Verfahren zur Verbesserung der Korrosionsbeständigkeit von metallischen Oberflächen. Die Phosphatschicht bildet eine Schutzbarriere gegen Feuchtigkeit, Chemikalien und andere schädliche Umwelteinflüsse und erhöht gleichzeitig die Haftung des Beschichtungspulvers.
Phosphatierungsprozess:
- Vorbereitung des Substrats: Das zu beschichtende Substrat wird vorbereitet, indem grobe Verschmutzungen und Rückstände von der Oberfläche entfernt werden.
- Phosphatierungslösung: Das Substrat wird dann in eine Phosphatierungslösung getaucht oder besprüht, die Phosphorsäure oder Phosphatverbindungen enthält, um eine Phosphatschicht auf der Oberfläche zu bilden.
- Spülung: Nach der Phosphatierung wird das Substrat gründlich gespült, um überschüssige Phosphatierungslösung zu entfernen und die Oberfläche zu reinigen.
Arten der Phosphatierung:
- Zinkphosphatierung: Bildet eine Zinkschicht zusammen mit der Phosphatschicht, die eine verbesserte Korrosionsbeständigkeit bietet und häufig in der Automobilindustrie verwendet wird.
- Eisenphosphatierung: Bildet eine Eisenphosphatschicht, die eine gute Korrosionsbeständigkeit bietet und häufig für industrielle Anwendungen verwendet wird.
Qualitätssicherung:
Die Überwachung und Kontrolle des Phosphatierungsprozesses ist entscheidend, um sicherzustellen, dass eine gleichmäßige und adhäsive Phosphatschicht auf der Oberfläche des Substrats gebildet wird. Dies kann durch regelmäßige Überprüfung der Phosphatierungslösungskonzentration, Einwirkzeit, Spülverfahren und visuelle Inspektion der behandelten Oberfläche erfolgen. Eine effektive Qualitätssicherung gewährleistet eine konsistente Oberflächenqualität und minimiert das Risiko von Beschichtungsfehlern.
Chromfreie Vorbehandlung
Die chromfreie Vorbehandlung ist eine umweltfreundliche Alternative zur herkömmlichen Chromatierung in der Vorbehandlung für die Pulverbeschichtung. Sie dient dazu, eine Oberfläche für die Beschichtung vorzubereiten, ohne dabei Chromverbindungen zu verwenden.
Bedeutung der chromfreien Vorbehandlung:
Die chromfreie Vorbehandlung ist eine Reaktion auf Umweltbedenken hinsichtlich der Verwendung von Chromverbindungen in Beschichtungsprozessen. Sie bietet eine umweltfreundlichere Möglichkeit, eine Oberfläche für die Pulverbeschichtung vorzubereiten, ohne dabei auf die Qualität der Beschichtungsergebnisse zu verzichten.
Chromfreie Vorbehandlungsprozesse:
- Vorbereitung des Substrats: Das zu beschichtende Substrat wird gründlich gereinigt und von Schmutz, Fett und anderen Verunreinigungen befreit.
- Anwendung der chromfreien Vorbehandlungslösung: Das Substrat wird in eine chromfreie Vorbehandlungslösung getaucht oder mit dieser besprüht. Diese Lösungen können verschiedene chemische Verbindungen enthalten, die die Oberfläche für die Beschichtung vorbereiten, wie z. B. Titanate, Zirkonate oder Silane.
- Spülung und Trocknung: Nach der Vorbehandlung wird das Substrat gründlich gespült, um überschüssige Vorbehandlungslösung zu entfernen. Anschließend wird es getrocknet, um es für die Beschichtung vorzubereiten.
Vorteile der chromfreien Vorbehandlung:
- Umweltfreundlichkeit: Durch den Verzicht auf Chromverbindungen trägt die chromfreie Vorbehandlung zur Reduzierung von Umweltbelastungen bei und entspricht den zunehmenden Umweltschutzstandards.
- Verbesserte Gesundheit und Sicherheit: Chromverbindungen gelten als potenziell gesundheitsschädlich. Die Verwendung chromfreier Vorbehandlungslösungen trägt dazu bei, die Gesundheit und Sicherheit der Beschäftigten zu verbessern.
- Gute Haftung und Korrosionsbeständigkeit: Moderne chromfreie Vorbehandlungstechnologien bieten eine ausgezeichnete Haftung des Beschichtungspulvers auf der Oberfläche sowie eine gute Korrosionsbeständigkeit.
Qualitätssicherung:
Die Qualitätssicherung bei der chromfreien Vorbehandlung umfasst die Überwachung und Kontrolle der Vorbehandlungsprozesse, um sicherzustellen, dass eine hochwertige Oberfläche für die Pulverbeschichtung bereitgestellt wird. Dies kann durch regelmäßige Überprüfung der Vorbehandlungslösungskonzentration, Einwirkzeit, Spülverfahren und visuelle Inspektion der behandelten Oberfläche erfolgen. Eine effektive Qualitätssicherung gewährleistet eine konsistente Oberflächenqualität und minimiert das Risiko von Beschichtungsfehlern.
Passivierung
Passivierung ist ein wichtiger Schritt in der Vorbehandlung für die Pulverbeschichtung, bei dem eine dünne Schutzschicht auf der Oberfläche des zu beschichtenden Metallsubstrats erzeugt wird, um die Korrosionsbeständigkeit zu erhöhen und die Haftung des Beschichtungspulvers zu verbessern.
Bedeutung der Passivierung:
Passivierung ist ein bewährtes Verfahren zur Verbesserung der Korrosionsbeständigkeit von metallischen Oberflächen. Die passivierte Schicht bildet eine Schutzbarriere gegen Feuchtigkeit, Chemikalien und andere schädliche Umwelteinflüsse und erhöht gleichzeitig die Haftung des Beschichtungspulvers.
Passivierungsprozess:
- Vorbereitung des Substrats: Das zu beschichtende Substrat wird vorbereitet, indem grobe Verschmutzungen und Rückstände von der Oberfläche entfernt werden.
- Passivierungslösung: Das Substrat wird dann in eine Passivierungslösung getaucht oder besprüht, die Säuren, Basen oder andere chemische Verbindungen enthält, um eine Schutzschicht auf der Oberfläche zu bilden.
- Spülung: Nach der Passivierung wird das Substrat gründlich gespült, um überschüssige Passivierungslösung zu entfernen und die Oberfläche zu reinigen.
Arten der Passivierung:
- Chromatpassivierung: Verwendet Chromverbindungen, um eine chromatische Schutzschicht auf der Oberfläche zu bilden, die eine gute Korrosionsbeständigkeit bietet.
- Aminpassivierung: Verwendet Aminverbindungen, um eine aminische Schutzschicht auf der Oberfläche zu bilden, die eine verbesserte Haftung des Beschichtungspulvers ermöglicht.
Qualitätssicherung:
Die Überwachung und Kontrolle des Passivierungsprozesses ist entscheidend, um sicherzustellen, dass eine gleichmäßige und adhäsive Passivierungsschicht auf der Oberfläche des Substrats gebildet wird. Dies kann durch regelmäßige Überprüfung der Passivierungslösungskonzentration, Einwirkzeit, Spülverfahren und visuelle Inspektion der behandelten Oberfläche erfolgen. Eine effektive Qualitätssicherung gewährleistet eine konsistente Oberflächenqualität und minimiert das Risiko von Beschichtungsfehlern.
Sandstrahlen
Sandstrahlen, auch als Strahlreinigung oder Strahltechnik bezeichnet, ist ein Verfahren in der Vorbehandlung für die Pulverbeschichtung, das darauf abzielt, die Oberfläche des zu beschichtenden Substrats durch den Einsatz von Druckluft und abrasiven Materialien zu reinigen und aufzurauen.
Bedeutung des Sandstrahlens:
Sandstrahlen ist ein effektives Verfahren zur Entfernung von Rost, Farbe, Beschichtungen, Schmutz und anderen Verunreinigungen von der Oberfläche des Substrats. Es bereitet die Oberfläche für die Pulverbeschichtung vor, indem es eine saubere, raue Oberfläche schafft, auf der das Beschichtungspulver haften kann.
Sandstrahlprozess:
- Vorbereitung des Substrats: Das zu beschichtende Substrat wird vorbereitet, indem grobe Verschmutzungen entfernt werden und gegebenenfalls alte Beschichtungen abgetragen werden.
- Sandstrahlen: Das Substrat wird in einer Strahlanlage platziert, wo es mit einem Strahlmittel wie Sand, Korund oder Glasperlen unter Druckluft oder Wasserkraft bearbeitet wird. Das Strahlmittel wird auf die Oberfläche des Substrats geblasen, um Verunreinigungen zu entfernen und die Oberfläche aufzurauen.
- Reinigung und Vorbereitung für die Beschichtung: Nach dem Sandstrahlen wird das Substrat gründlich gereinigt, um überschüssiges Strahlmittel und Verunreinigungen zu entfernen. Anschließend ist die Oberfläche bereit für die Pulverbeschichtung.
Arten des Sandstrahlens:
- Trockenstrahlen: Verwendet Druckluft, um das Strahlmittel auf die Oberfläche zu blasen, ohne Wasser zu verwenden. Es ist effektiv bei der Entfernung von Farbe, Rost und Beschichtungen.
- Nassstrahlen: Verwendet Wasser zusammen mit dem Strahlmittel, um die Entfernung von Verunreinigungen zu erleichtern und Staubbildung zu reduzieren. Es ist besonders geeignet für empfindliche Oberflächen und zur Verringerung von Staubbelastungen.
Qualitätssicherung:
Die Qualitätssicherung beim Sandstrahlen umfasst die Überwachung und Kontrolle des Strahlprozesses, um sicherzustellen, dass die Oberfläche des Substrats gründlich gereinigt und aufgeraut wird, ohne beschädigt zu werden. Dies kann durch regelmäßige Überprüfung der Strahlmittelkörnung, Strahlmittelgeschwindigkeit, Strahldruck und visuelle Inspektion der behandelten Oberfläche erfolgen. Eine effektive Qualitätssicherung gewährleistet eine konsistente Oberflächenqualität und minimiert das Risiko von Beschichtungsfehlern.
Vorbehandlung
Die Vorbehandlung ist ein essenzieller Schritt in der Vorbereitung für die Pulverbeschichtung, der darauf abzielt, die Oberfläche des zu beschichtenden Substrats zu reinigen, vorzubereiten und zu verbessern, um eine optimale Haftung und Haltbarkeit der Beschichtung zu gewährleisten.
Bedeutung der Vorbehandlung:
Die Vorbehandlung spielt eine entscheidende Rolle, um eine qualitativ hochwertige Pulverbeschichtung zu erzielen. Sie entfernt Verunreinigungen wie Fett, Öl, Rost, Schmutz und alte Beschichtungen von der Oberfläche des Substrats und schafft eine saubere, gleichmäßige Oberfläche, auf der das Beschichtungspulver haften kann. Darüber hinaus kann die Vorbehandlung die Korrosionsbeständigkeit verbessern und die Lebensdauer der Beschichtung verlängern.
Vorbehandlungsprozess:
- Reinigung: Das zu beschichtende Substrat wird gründlich gereinigt, um Fett, Öl, Schmutz und andere Verunreinigungen zu entfernen. Dies kann durch chemische Reinigung, Entfettung, Sandstrahlen oder andere Reinigungsmethoden erfolgen.
- Entrostung: Bei metallischen Substraten wird Rost entfernt, um die Oberfläche zu reinigen und die Haftung des Beschichtungspulvers zu verbessern. Dies kann durch Sandstrahlen, Schleifen, Beizen oder andere Entrostungsmethoden erfolgen.
- Phosphatierung oder Passivierung: Eine Phosphatierung oder Passivierung kann durchgeführt werden, um die Oberfläche weiter zu verbessern und die Haftung des Beschichtungspulvers zu optimieren. Diese Prozesse bilden eine dünnen Schutzschicht auf der Oberfläche, die die Korrosionsbeständigkeit erhöht.
- Trocknung: Nach der Vorbehandlung wird das Substrat gründlich getrocknet, um überschüssiges Wasser oder Feuchtigkeit zu entfernen und die Oberfläche für die Pulverbeschichtung vorzubereiten.
Qualitätssicherung:
Die Qualitätssicherung der Vorbehandlung umfasst die Überwachung und Kontrolle jedes Schrittes des Vorbehandlungsprozesses, um sicherzustellen, dass die Oberfläche des Substrats ordnungsgemäß gereinigt, entrostet und vorbereitet wird. Dies kann durch regelmäßige Überprüfung der Reinigungsmethoden, Phosphatierungskonzentration, Passivierung, Trocknungsverfahren und visuelle Inspektion der behandelten Oberfläche erfolgen. Eine effektive Qualitätssicherung gewährleistet eine konsistente Oberflächenqualität und minimiert das Risiko von Beschichtungsfehlern.
Entlacken
Entlacken ist ein wichtiger Schritt in der Vorbehandlung für die Pulverbeschichtung, der darauf abzielt, alte Farbschichten, Beschichtungen oder Lacke von der Oberfläche des zu beschichtenden Substrats zu entfernen.
Bedeutung des Entlackens:
Das Entlacken ist entscheidend, um eine saubere Oberfläche zu schaffen, auf der das Beschichtungspulver optimal haften kann. Durch das Entfernen alter Farbschichten oder Beschichtungen wird eine gleichmäßige Oberfläche geschaffen, die die Haftung des Beschichtungspulvers verbessert und Beschichtungsfehler verhindert.
Entlackungsprozess:
- Vorbereitung des Substrats: Das zu beschichtende Substrat wird vorbereitet, indem grobe Verschmutzungen und Rückstände von der Oberfläche entfernt werden.
- Entlackungsmethode: Es gibt verschiedene Methoden zum Entlacken, darunter thermisches Entlacken, chemisches Entlacken, mechanisches Entlacken und Strahlen. Die Wahl der Methode hängt von der Art der Farbschicht, der Beschichtung und dem Substratmaterial ab.
- Durchführung des Entlackungsprozesses: Je nach gewählter Methode wird das Substrat entweder erhitzt, chemisch behandelt, mechanisch bearbeitet oder mit abrasiven Materialien gestrahlt, um die alte Farbschicht oder Beschichtung zu entfernen.
- Reinigung und Vorbereitung für die Beschichtung: Nach dem Entlacken wird das Substrat gründlich gereinigt, um überschüssige Entlackungsrückstände zu entfernen, und auf die Pulverbeschichtung vorbereitet.
Arten des Entlackens:
- Thermisches Entlacken: Verwendet Hitze, um die Farbschicht oder Beschichtung zu verbrennen oder zu schmelzen, damit sie leicht entfernt werden kann.
- Chemisches Entlacken: Verwendet chemische Lösungen oder Beizen, um die Farbschicht oder Beschichtung aufzulösen oder zu entfernen.
- Mechanisches Entlacken: Verwendet Schleifen, Bürsten oder Fräsen, um die Farbschicht oder Beschichtung mechanisch von der Oberfläche zu entfernen.
- Strahlen: Verwendet abrasive Materialien wie Sand, Korund oder Glasperlen, um die Farbschicht oder Beschichtung von der Oberfläche zu sprengen.
Qualitätssicherung:
Die Qualitätssicherung beim Entlacken umfasst die Überwachung und Kontrolle des Entlackungsprozesses, um sicherzustellen, dass die alte Farbschicht oder Beschichtung vollständig entfernt wird, ohne das Substrat zu beschädigen. Dies kann durch regelmäßige Überprüfung der Entlackungsmethode, Einwirkzeit, Reinigungsmethoden und visuelle Inspektion der behandelten Oberfläche erfolgen. Eine effektive Qualitätssicherung gewährleistet eine konsistente Oberflächenqualität und minimiert das Risiko von Beschichtungsfehlern.
Chromatierung
Chromatierung ist ein wichtiger Schritt in der Vorbehandlung für die Pulverbeschichtung, der dazu dient, eine Chromschicht auf der Oberfläche des zu beschichtenden Substrats zu erzeugen, um die Korrosionsbeständigkeit zu erhöhen und die Haftung des Beschichtungspulvers zu verbessern.
Bedeutung der Chromatierung:
Chromatierung ist ein bewährtes Verfahren zur Verbesserung der Korrosionsbeständigkeit von metallischen Oberflächen. Die chromatierte Schicht bildet eine Schutzbarriere gegen Feuchtigkeit, Chemikalien und andere schädliche Umwelteinflüsse und erhöht gleichzeitig die Haftung des Beschichtungspulvers.
Chromatierungsprozess:
- Vorbereitung des Substrats: Das zu beschichtende Substrat wird vorbereitet, indem grobe Verschmutzungen und Rückstände von der Oberfläche entfernt werden.
- Chromatierungslösung: Das Substrat wird dann in eine Chromatierungslösung getaucht oder besprüht, die Chromsäure oder Chromatverbindungen enthält, um eine Chromschicht auf der Oberfläche zu bilden.
- Spülung: Nach der Chromatierung wird das Substrat gründlich gespült, um überschüssige Chromatierungslösung zu entfernen und die Oberfläche zu reinigen.
Arten der Chromatierung:
- Gelbchromatierung: Bildet eine gelbliche Chromschicht, die eine gute Korrosionsbeständigkeit bietet und häufig in der Automobilindustrie verwendet wird.
- Blau- oder Schwarzchromatierung: Bildet eine bläuliche oder schwarze Chromschicht, die eine verbesserte Korrosionsbeständigkeit bietet und häufig für industrielle Anwendungen verwendet wird.
Qualitätssicherung:
Die Überwachung und Kontrolle des Chromatierungsprozesses ist entscheidend, um sicherzustellen, dass eine gleichmäßige und adhäsive Chromschicht auf der Oberfläche des Substrats gebildet wird. Dies kann durch regelmäßige Überprüfung der Chromatierungslösungskonzentration, Einwirkzeit, Spülverfahren und visuelle Inspektion der behandelten Oberfläche erfolgen. Eine effektive Qualitätssicherung gewährleistet eine konsistente Oberflächenqualität und minimiert das Risiko von Beschichtungsfehlern.
Phosphatierung
Die Phosphatierung ist ein wichtiger Schritt in der Vorbehandlung für die Pulverbeschichtung, bei dem eine dünne Phosphatschicht auf der Oberfläche des zu beschichtenden Substrats erzeugt wird, um die Haftung des Beschichtungspulvers zu verbessern und die Korrosionsbeständigkeit zu erhöhen.
Bedeutung der Phosphatierung:
Die Phosphatierung ist ein bewährtes Verfahren zur Verbesserung der Haftung und Haltbarkeit von Pulverbeschichtungen. Die phosphatierte Schicht bildet eine chemische Verbindung mit dem Substrat, die eine verbesserte Haftung des Beschichtungspulvers ermöglicht und gleichzeitig die Korrosionsbeständigkeit erhöht.
Phosphatierungsprozess:
- Vorbereitung des Substrats: Das zu beschichtende Substrat wird vorbereitet, indem grobe Verschmutzungen und Rückstände von der Oberfläche entfernt werden.
- Phosphatierungslösung: Das Substrat wird dann in eine Phosphatierungslösung getaucht oder besprüht, die Phosphorsäure oder Phosphatverbindungen enthält, um eine Phosphatschicht auf der Oberfläche zu bilden.
- Einwirkzeit und Spülung: Die Dauer der Einwirkung der Phosphatierungslösung hängt von der Art des Substrats und der gewünschten Phosphatschichtdicke ab. Nach der Einwirkung wird das Substrat gründlich gespült, um überschüssige Phosphatierungslösung zu entfernen.
- Trocknung: Nach dem Spülvorgang wird das Substrat getrocknet, um überschüssiges Wasser zu entfernen und die Oberfläche für die Pulverbeschichtung vorzubereiten.
Arten der Phosphatierung:
- Zinkphosphatierung: Bildet eine Zinkschicht, die eine gute Korrosionsbeständigkeit bietet und häufig in der Automobilindustrie verwendet wird.
- Eisenphosphatierung: Bildet eine Eisenphosphatschicht, die eine verbesserte Haftung des Beschichtungspulvers ermöglicht und häufig für industrielle Anwendungen verwendet wird.
Qualitätssicherung:
Die Qualitätssicherung der Phosphatierung umfasst die Überwachung und Kontrolle jedes Schrittes des Phosphatierungsprozesses, um sicherzustellen, dass eine gleichmäßige und adhäsive Phosphatschicht auf der Oberfläche des Substrats gebildet wird. Dies kann durch regelmäßige Überprüfung der Phosphatierungslösungskonzentration, Einwirkzeit, Spülverfahren und visuelle Inspektion der behandelten Oberfläche erfolgen. Eine effektive Qualitätssicherung gewährleistet eine konsistente Oberflächenqualität und minimiert das Risiko von Beschichtungsfehlern.
Reinigung
Die Reinigung ist ein grundlegender Schritt in der Vorbehandlung für die Pulverbeschichtung, der darauf abzielt, Verschmutzungen, Fette, Öle und andere Verunreinigungen von der Oberfläche des zu beschichtenden Substrats zu entfernen.
Bedeutung der Reinigung:
Eine gründliche Reinigung ist entscheidend, um eine optimale Haftung und Haltbarkeit der Pulverbeschichtung zu gewährleisten. Verschmutzungen, Fette und Öle können die Haftung des Beschichtungspulvers beeinträchtigen und zu Beschichtungsfehlern führen. Durch eine gründliche Reinigung wird eine saubere Oberfläche geschaffen, auf der das Beschichtungspulver gleichmäßig haften kann.
Reinigungsprozess:
- Vorbereitung des Substrats: Das zu beschichtende Substrat wird vorbereitet, indem grobe Verschmutzungen von der Oberfläche entfernt werden.
- Reinigungsmethode: Es gibt verschiedene Methoden zur Reinigung, darunter chemische Reinigung, Entfettung, mechanische Reinigung und Wasserstrahlreinigung. Die Wahl der Methode hängt von der Art der Verschmutzung, der Beschaffenheit des Substrats und den Anforderungen der Pulverbeschichtung ab.
- Durchführung der Reinigung: Die gewählte Reinigungsmethode wird angewendet, um Verschmutzungen, Fette, Öle und andere Verunreinigungen von der Oberfläche zu entfernen. Dies kann durch Auftragen von Reinigungslösungen, Bürsten, Schrubben oder Sprühen erfolgen.
- Spülung und Trocknung: Nach der Reinigung wird das Substrat gründlich gespült, um überschüssige Reinigungslösung und Verunreinigungen zu entfernen. Anschließend wird das Substrat getrocknet, um überschüssiges Wasser zu entfernen und die Oberfläche für die Pulverbeschichtung vorzubereiten.
Qualitätssicherung:
Die Qualitätssicherung der Reinigung umfasst die Überwachung und Kontrolle jedes Schrittes des Reinigungsprozesses, um sicherzustellen, dass die Oberfläche des Substrats gründlich gereinigt wird und frei von Verschmutzungen, Fetten und Ölen ist. Dies kann durch regelmäßige Überprüfung der Reinigungsmethode, Reinigungslösungskonzentration, Einwirkzeit, Spülverfahren und visuelle Inspektion der behandelten Oberfläche erfolgen. Eine effektive Qualitätssicherung gewährleistet eine konsistente Oberflächenqualität und minimiert das Risiko von Beschichtungsfehlern.
Entfettung
Die Entfettung ist ein entscheidender Schritt in der Vorbehandlung für die Pulverbeschichtung, der darauf abzielt, Fette, Öle und andere organische Verunreinigungen von der Oberfläche des zu beschichtenden Substrats zu entfernen.
Bedeutung der Entfettung:
Eine gründliche Entfettung ist unerlässlich, um eine optimale Haftung und Haltbarkeit der Pulverbeschichtung zu gewährleisten. Fette, Öle und andere organische Verunreinigungen können die Haftung des Beschichtungspulvers beeinträchtigen und zu Beschichtungsfehlern führen. Durch die Entfernung dieser Verunreinigungen wird eine saubere Oberfläche geschaffen, auf der das Beschichtungspulver gleichmäßig haften kann.
Entfettungsprozess:
- Vorbereitung des Substrats: Das zu beschichtende Substrat wird vorbereitet, indem grobe Verschmutzungen von der Oberfläche entfernt werden.
- Entfettungsmethode: Es gibt verschiedene Methoden zur Entfettung, darunter chemische Entfettung, Dampfreinigung, Ultraschallreinigung und Lösungsmittelreinigung. Die Wahl der Methode hängt von der Art der Verschmutzung, der Beschaffenheit des Substrats und den Anforderungen der Pulverbeschichtung ab.
- Durchführung der Entfettung: Die gewählte Entfettungsmethode wird angewendet, um Fette, Öle und andere organische Verunreinigungen von der Oberfläche zu entfernen. Dies kann durch Auftragen von Entfettungslösungen, Dampfreinigung, Ultraschallbehandlung oder Tauchen in Lösungsmittel erfolgen.
- Spülung und Trocknung: Nach der Entfettung wird das Substrat gründlich gespült, um überschüssige Entfettungslösung und Verunreinigungen zu entfernen. Anschließend wird das Substrat getrocknet, um überschüssiges Wasser oder Lösungsmittel zu entfernen und die Oberfläche für die Pulverbeschichtung vorzubereiten.
Qualitätssicherung:
Die Qualitätssicherung der Entfettung umfasst die Überwachung und Kontrolle jedes Schrittes des Entfettungsprozesses, um sicherzustellen, dass die Oberfläche des Substrats gründlich entfettet wird und frei von Fett, Öl und anderen organischen Verunreinigungen ist. Dies kann durch regelmäßige Überprüfung der Entfettungsmethode, Entfettungslösungskonzentration, Einwirkzeit, Spülverfahren und visuelle Inspektion der behandelten Oberfläche erfolgen. Eine effektive Qualitätssicherung gewährleistet eine konsistente Oberflächenqualität und minimiert das Risiko von Beschichtungsfehlern.
EMS Pulverbeschichtungsanlagen
Unsere Pulverbeschichtungsanlage wird in Übereinstimmung mit den globalen fortschrittlichen Standards hergestellt und wurden mit vollem Vertrauen sowohl auf dem heimischen als auch auf dem weltweiten Markt bevorzugt.
Unsere Kapazität ist täglich gewachsen, wobei die Kundenzufriedenheit zusammen mit unserem gemeinsamen Vertriebs- und Servicenetz an erster Stelle steht.
Unser Unternehmen ist ein führendes türkisches Unternehmen, das sich auf die Herstellung von „Elektrostatischen Pulverbeschichtungsanlagen und kompletten Lackiersystemen“ mit 20 Jahren Wissen und praktischer Erfahrung spezialisiert hat.
Alle unsere Maschinen sind CE-gekennzeichnet, garantiert und können von potenziellen Kunden persönlich besichtigt werden. Es gibt auch Bilder und Videos auf dieser Seite, die die verwendeten Maschinen zeigen.
Wir entwerfen, fertigen und montieren Pulverbeschichtungsöfen, automatische und manuelle Kabinen, automatische und manuelle Pulverbeschichtungsanlagen, Pistolen, automatische und Stangentransfer-Pulverbeschichtungslinien, Pulverbeschichtungsfilter und Ersatzteile für Pulverbeschichtungspistolen