Die Kopflackierung von Schrauben, Nietköpfen und Bolzen kann in spezialisierten Anlagen durchgeführt werden, die für diesen Zweck entwickelt wurden. Diese Anlagen sind darauf ausgelegt, den Beschichtungsprozess effizient und präzise zu gestalten, um eine gleichmäßige Beschichtung auf den Kopf- oder Endbereichen der Befestigungselemente zu erreichen. Hier sind typische Komponenten und Funktionen solcher Anlagen:
Komponenten von Anlagen zur Kopflackierung:
- Vorbereitungsbereich:
- Vor der Lackierung müssen die Schrauben, Nietköpfe oder Bolzen möglicherweise gereinigt und vorbehandelt werden, um eine optimale Haftung der Lackierung zu gewährleisten. Dies kann Reinigungs- und Entfettungssysteme umfassen.
- Beschichtungseinheit:
- Die eigentliche Kopflackierung erfolgt in dieser Einheit. Abhängig von der Art der Beschichtung können verschiedene Technologien eingesetzt werden:
- Tauchbeschichtung: Die Befestigungselemente werden in einen Lacktank getaucht, um die Köpfe oder Enden zu beschichten.
- Sprühbeschichtung: Automatisierte Sprühsysteme werden verwendet, um die Lackierung gleichmäßig auf die Oberflächen aufzutragen.
- Pulverbeschichtung: Bei Bedarf kann auch die Pulverbeschichtung eingesetzt werden, insbesondere für spezielle Anforderungen an die Beschichtungsdicke und Haltbarkeit.
- Die eigentliche Kopflackierung erfolgt in dieser Einheit. Abhängig von der Art der Beschichtung können verschiedene Technologien eingesetzt werden:
- Aushärteofen:
- Nach dem Lackieren müssen die Befestigungselemente in einem Ofen oder Trockner ausgehärtet werden, um die Lackierung zu trocknen und zu härten. Dies gewährleistet eine dauerhafte Haftung der Beschichtung.
- Kühl- und Handhabungsbereich:
- Nach dem Aushärten werden die beschichteten Schrauben, Nietköpfe oder Bolzen gekühlt und für die weitere Handhabung vorbereitet. Automatisierte Förderbänder oder Handhabungssysteme erleichtern den Transport zur Inspektion oder Verpackung.
- Qualitätskontrolle und Überwachung:
- Moderne Anlagen sind mit Überwachungs- und Kontrollsystemen ausgestattet, um sicherzustellen, dass die Lackierung gleichmäßig und qualitativ hochwertig ist. Dies umfasst die Überwachung der Lackierdicke, Trocknungszeiten und visuelle Inspektionen.
Funktionen und Vorteile von Kopflackieranlagen
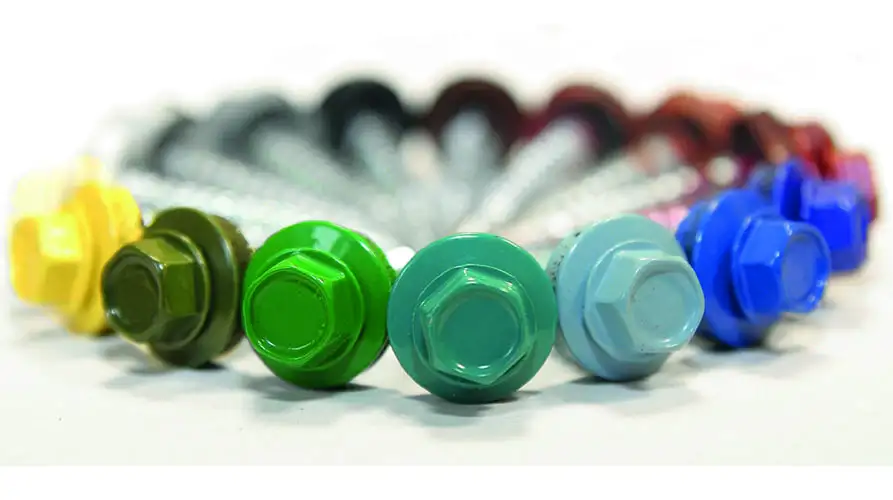
- Präzise Lackierung: Die Anlagen ermöglichen eine präzise und gleichmäßige Lackierung der Köpfe oder Enden von Schrauben, Nietköpfen und Bolzen, was die ästhetische Qualität verbessert.
- Effizienz: Durch den Einsatz automatisierter Prozesse können große Mengen an Befestigungselementen schnell und effizient lackiert werden.
- Vielseitigkeit: Je nach Anforderungen können verschiedene Lackiertechnologien und Farben in einer einzigen Anlage integriert werden.
- Konsistente Qualität: Die Anlagen gewährleisten eine gleichbleibende Lackierqualität über die gesamte Produktion hinweg, was die Zuverlässigkeit und Leistung der beschichteten Befestigungselemente verbessert.
- Umweltfreundlichkeit: Moderne Beschichtungsanlagen verwenden oft umweltfreundliche Lackmaterialien und minimieren den Abfall.
Die Verwendung von spezialisierten Kopflackieranlagen bietet eine effektive Lösung für Unternehmen, die hochwertige und ästhetisch ansprechende Befestigungselemente herstellen oder verwenden. Die Anlagen tragen dazu bei, die Produktleistung zu optimieren und die Kundenzufriedenheit zu steigern, indem sie eine hochwertige und konsistente Beschichtung gewährleisten.
Vorbereitungsbereich
Der Vorbereitungsbereich in Anlagen zur Beschichtung von Schrauben, Nietköpfen und Bolzen spielt eine entscheidende Rolle, um sicherzustellen, dass die Oberflächen der Befestigungselemente optimal vorbereitet sind, bevor sie beschichtet werden. Eine gründliche Vorbereitung ist entscheidend, um eine gute Haftung der Beschichtung zu gewährleisten und die Qualität der Endprodukte zu verbessern. Hier sind die wichtigen Aspekte und Prozesse, die im Vorbereitungsbereich durchgeführt werden:
1. Reinigung:
- Die Schrauben, Nietköpfe oder Bolzen werden zuerst gründlich gereinigt, um Oberflächenverunreinigungen wie Staub, Fett, Öl, Rost oder andere Verschmutzungen zu entfernen.
- Die Reinigung kann durch verschiedene Methoden erfolgen, einschließlich mechanischer Reinigung (z. B. Bürsten, Strahlen) oder chemischer Reinigung (z. B. Entfettung, Beizen).
2. Entfettung:
- Nach der Reinigung folgt oft der Entfettungsschritt, um sämtliches Fett und Öl von den Oberflächen zu entfernen. Dies ist wichtig, da Fettfilme die Haftung der Beschichtung beeinträchtigen können.
- Die Entfettung kann durch Tauchen in spezielle Entfettungsbäder oder durch den Einsatz von Reinigungslösungen und Sprühgeräten erfolgen.
3. Vorbehandlung:
- Nach der Reinigung und Entfettung kann eine Vorbehandlung der Oberflächen durchgeführt werden, um die Haftung und Korrosionsbeständigkeit der Beschichtung zu verbessern.
- Typische Vorbehandlungsprozesse umfassen Phosphatierung, Chromatierung oder Aufbringen von Konversionsbeschichtungen, die die Oberfläche für die anschließende Beschichtung vorbereiten.
4. Trocknung:
- Nach der Reinigung, Entfettung und gegebenenfalls Vorbehandlung müssen die Befestigungselemente gründlich getrocknet werden, um Feuchtigkeit von der Oberfläche zu entfernen.
- Die Trocknung kann durch Lufttrocknung, Einsatz von Trockenöfen oder anderen Trocknungsverfahren erfolgen.
Bedeutung des Vorbereitungsbereichs:
Der Vorbereitungsbereich spielt eine entscheidende Rolle im Beschichtungsprozess und hat direkten Einfluss auf die Qualität und Haltbarkeit der Beschichtung auf den Schrauben, Nietköpfen und Bolzen. Eine gründliche Vorbereitung der Oberflächen entfernt Verunreinigungen, verbessert die Haftung der Beschichtung und trägt dazu bei, dass die beschichteten Befestigungselemente den spezifischen Anforderungen der Anwendung entsprechen.
Durch einen effektiven Vorbereitungsbereich können Unternehmen sicherstellen, dass die beschichteten Produkte eine hohe Leistung und Zuverlässigkeit bieten und den erwarteten Standards und Spezifikationen entsprechen.
Beschichtungseinheit
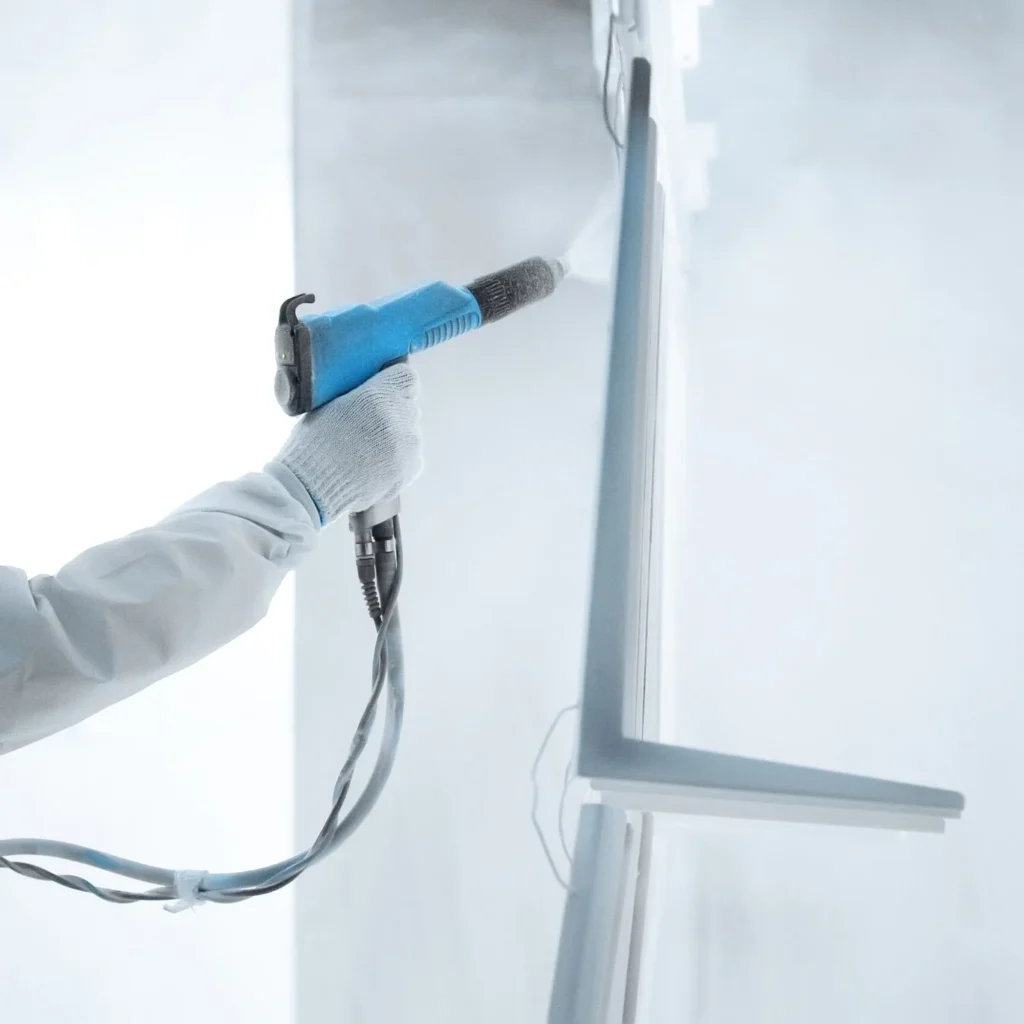
Die Beschichtungseinheit in Anlagen zur Beschichtung von Schrauben, Nietköpfen und Bolzen ist der zentrale Bereich, in dem die eigentliche Beschichtung der Befestigungselemente erfolgt. Diese Einheit ist speziell dafür ausgelegt, die Beschichtungsmaterialien auf die Oberflächen der Schraubenköpfe, Nietköpfe oder Bolzen aufzutragen, um sie vor Korrosion zu schützen, ihre Haltbarkeit zu verbessern oder ästhetische Anforderungen zu erfüllen. Hier sind die wichtigen Aspekte und Prozesse, die in der Beschichtungseinheit durchgeführt werden:
1. Pulverbeschichtung:
- Pulverapplikation: Bei der Pulverbeschichtung wird das Pulvermaterial auf die Oberflächen der Befestigungselemente aufgetragen. Dies kann durch elektrostatische Aufladung des Pulvers erfolgen, um eine gleichmäßige Verteilung zu gewährleisten.
- Sprühsysteme: Automatisierte Sprühsysteme können verwendet werden, um das Pulver gleichmäßig auf die Schrauben, Nietköpfe oder Bolzen aufzutragen.
- Überschussentfernung: Nach der Pulverapplikation wird überschüssiges Pulver entfernt, um eine gleichmäßige Beschichtung zu gewährleisten und Materialverluste zu minimieren.
2. Nasslackbeschichtung:
- Tauchbeschichtung: Die Befestigungselemente werden in einen Tank mit flüssigem Lack getaucht, um die Oberflächen zu beschichten.
- Sprühsysteme: Automatisierte Sprühsysteme können auch für die Nasslackbeschichtung verwendet werden, um eine gleichmäßige Beschichtung auf den Oberflächen zu erzielen.
3. Trocknung und Aushärtung:
- Nach der Beschichtung müssen die Befestigungselemente getrocknet und ausgehärtet werden, um die Beschichtung zu stabilisieren und eine gute Haftung auf der Oberfläche zu gewährleisten.
- Dies kann durch den Einsatz von Trocknungsöfen oder speziellen Aushärteöfen erfolgen, je nach den Anforderungen des Beschichtungsmaterials.
4. Qualitätskontrolle:
- Während des Beschichtungsprozesses werden die beschichteten Befestigungselemente oft einer Qualitätskontrolle unterzogen, um sicherzustellen, dass die Beschichtung gleichmäßig und fehlerfrei ist.
- Visuelle Inspektionen oder Prüfungen der Beschichtungsdicke können durchgeführt werden, um die Qualität der beschichteten Produkte sicherzustellen.
Funktionen und Vorteile der Beschichtungseinheit:
- Effiziente Beschichtung: Die Beschichtungseinheit ermöglicht eine effiziente und automatisierte Beschichtung großer Mengen von Schrauben, Nietköpfen oder Bolzen in kurzer Zeit.
- Gleichmäßige Beschichtung: Durch den Einsatz automatisierter Sprühsysteme oder Pulverapplikationstechniken wird eine gleichmäßige Beschichtung auf den Befestigungselementen erzielt.
- Vielseitigkeit: Die Beschichtungseinheit kann für verschiedene Beschichtungsmaterialien und Anwendungen angepasst werden, um den spezifischen Anforderungen verschiedener Branchen und Kunden gerecht zu werden.
- Qualitätssicherung: Durch die Integration von Qualitätskontrollen in den Beschichtungsprozess wird die Konsistenz und Qualität der beschichteten Produkte sichergestellt.
Eine effektive Beschichtungseinheit spielt eine entscheidende Rolle bei der Herstellung hochwertiger und funktionaler beschichteter Befestigungselemente für verschiedene Industrien und Anwendungen. Durch den Einsatz moderner Beschichtungstechnologien und automatisierter Prozesse können Unternehmen die Produktivität steigern und die Kundenzufriedenheit verbessern.
EMS Pulverbeschichtungsanlagen
Unsere Pulverbeschichtungsanlage wird in Übereinstimmung mit den globalen fortschrittlichen Standards hergestellt und wurden mit vollem Vertrauen sowohl auf dem heimischen als auch auf dem weltweiten Markt bevorzugt.
Unsere Kapazität ist täglich gewachsen, wobei die Kundenzufriedenheit zusammen mit unserem gemeinsamen Vertriebs- und Servicenetz an erster Stelle steht.
Unser Unternehmen ist ein führendes türkisches Unternehmen, das sich auf die Herstellung von „Elektrostatischen Pulverbeschichtungsanlagen und kompletten Lackiersystemen“ mit 20 Jahren Wissen und praktischer Erfahrung spezialisiert hat.
Alle unsere Maschinen sind CE-gekennzeichnet, garantiert und können von potenziellen Kunden persönlich besichtigt werden. Es gibt auch Bilder und Videos auf dieser Seite, die die verwendeten Maschinen zeigen.
Wir entwerfen, fertigen und montieren Pulverbeschichtungsöfen, automatische und manuelle Kabinen, automatische und manuelle Pulverbeschichtungsanlagen, Pistolen, automatische und Stangentransfer-Pulverbeschichtungslinien, Pulverbeschichtungsfilter und Ersatzteile für Pulverbeschichtungspistolen