Der Aufbau einer Pulverbeschichtungsanlage für Felgen erfordert eine sorgfältige Planung, um sicherzustellen, dass Sie hochwertige und gleichmäßig beschichtete Felgen produzieren können. Hier sind die grundlegenden Schritte und Überlegungen für den Aufbau einer solchen Anlage:
1. Standortauswahl:
Wählen Sie einen geeigneten Standort für Ihre Pulverbeschichtungsanlage. Dieser sollte ausreichend Platz für die Installation der Anlagen und Arbeitsbereiche bieten. Stellen Sie sicher, dass der Standort den örtlichen Vorschriften und Umweltauflagen entspricht.
2. Beschichtungsausrüstung:
Beschaffen Sie die notwendige Beschichtungsausrüstung. Dazu gehören:
- Pulverbeschichtungskabine: Dies ist der Hauptarbeitsbereich, in dem die Felgen beschichtet werden. Die Kabine sollte gut belüftet sein und über eine geeignete Filterung verfügen, um überschüssiges Pulver aufzufangen.
- Pulverbeschichtungspistolen: Sie benötigen Pulverbeschichtungspistolen, um das Pulver auf die Felgen aufzutragen. Stellen Sie sicher, dass die Pistolen von hoher Qualität sind und eine gleichmäßige Beschichtung ermöglichen.
- Hängevorrichtungen: Um die Felgen während des Beschichtungsprozesses aufzuhängen und zu transportieren, benötigen Sie geeignete Hängevorrichtungen.
- Ofen: Ein Aushärtungsofen ist unerlässlich, um die beschichteten Felgen zu härten. Stellen Sie sicher, dass der Ofen die erforderlichen Temperaturen und Aushärtungszeiten erreichen kann.
3. Pulverbeschichtungspulver:
Beschaffen Sie das Pulverbeschichtungspulver in den gewünschten Farben und Qualitäten. Unterschiedliche Pulverbeschichtungen können für unterschiedliche Felgentypen und Anwendungen erforderlich sein.
4. Vorbereitung der Felgen:
Die Felgen müssen vor dem Beschichtungsprozess sorgfältig vorbereitet werden. Dies umfasst das Reinigen, Entfetten und Entfernen von alten Beschichtungen oder Verschmutzungen. Ein Strahlverfahren, wie das Sandstrahlen, kann erforderlich sein, um die Oberfläche der Felgen aufzurauen und eine gute Haftung des Pulvers zu gewährleisten.
5. Beschichtungsprozess:
Der eigentliche Beschichtungsprozess umfasst das Auftragen des Pulvers auf die vorbereiteten Felgen mithilfe der Beschichtungspistolen. Stellen Sie sicher, dass die Pulverbeschichtung gleichmäßig und in der richtigen Dicke aufgetragen wird.
6. Aushärtung:
Die beschichteten Felgen müssen in einem Ofen bei den empfohlenen Temperaturen und Zeiten ausgehärtet werden. Dieser Schritt ist entscheidend, um eine dauerhafte und widerstandsfähige Beschichtung zu gewährleisten.
7. Qualitätskontrolle:
Führen Sie eine Qualitätskontrolle durch, um sicherzustellen, dass die beschichteten Felgen den erforderlichen Standards entsprechen. Dies umfasst die Überprüfung der Beschichtungsdicke, der Haftung und der Oberflächenqualität.
8. Verpackung und Versand:
Nach der Qualitätskontrolle können die fertigen Felgen verpackt und versandt werden.
9. Sicherheit und Umweltschutz:
Stellen Sie sicher, dass Ihre Pulverbeschichtungsanlage den geltenden Sicherheits- und Umweltauflagen entspricht. Dies umfasst die ordnungsgemäße Entsorgung von Pulverüberschüssen und die Einhaltung von Sicherheitsvorschriften für Arbeitskräfte.
10. Marketing und Vertrieb:
Entwickeln Sie eine Strategie für Marketing und Vertrieb, um Ihre beschichteten Felgen auf dem Markt zu positionieren und Kunden zu gewinnen.
Der Aufbau einer Pulverbeschichtungsanlage erfordert Investitionen in Ausrüstung und Ressourcen, aber mit der richtigen Planung und Durchführung können Sie hochwertige beschichtete Felgen herstellen und in den Markt eintreten. Denken Sie daran, sich mit Experten in der Pulverbeschichtungstechnologie in Verbindung zu setzen, um sicherzustellen, dass Sie die besten Ergebnisse erzielen.
Pulverbeschichtungsanlage für Felgen
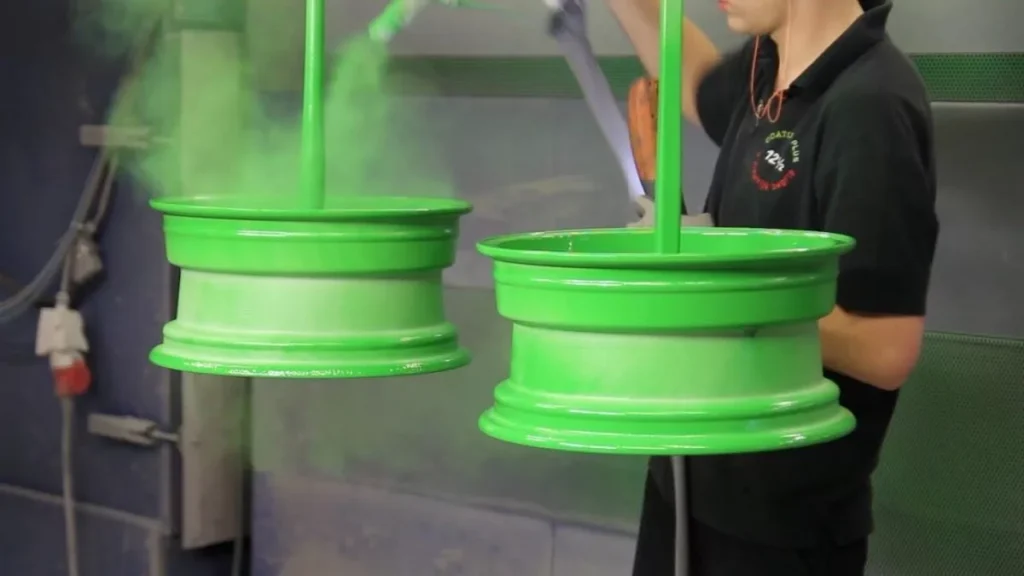
Eine Pulverbeschichtungsanlage für Felgen ist eine Anlage, die für die Pulverbeschichtung von Felgen geeignet ist. Sie besteht in der Regel aus einem Vorbehandlungsraum, einem Beschichtungsraum und einem Ofen.
Im Vorbehandlungsraum werden die Felgen gereinigt und entfettet. Dies ist wichtig, um eine gute Haftung des Pulverlacks zu gewährleisten. Im Beschichtungsraum werden die Felgen mit einem Pulverlack beschichtet. Der Pulverlack wird mithilfe einer Elektrostatikpistole auf die Felgen aufgetragen. Der Pulverlack kann in verschiedenen Farben und Effekten gewählt werden. Im Ofen wird der Pulverlack bei einer Temperatur von etwa 200 °C eingebrannt. Durch das Einbrennen härtet der Pulverlack aus und wird zu einer robusten und langlebigen Beschichtung.
Pulverbeschichtungsanlagen für Felgen sind in der Regel vollautomatisch. Dies bedeutet, dass die Felgen in der Anlage von einem Roboter bearbeitet werden. Dadurch wird eine gleichmäßige und hochwertige Beschichtung gewährleistet.
Vorteile einer Pulverbeschichtungsanlage für Felgen
- Hohe Qualität der Beschichtung: Pulverbeschichtungen sind in der Regel sehr hochwertig und langlebig.
- Hohe Effizienz: Pulverbeschichtungsanlagen ermöglichen eine hohe Produktionsleistung.
- Umweltfreundlich: Pulverbeschichtungen sind umweltfreundlicher als andere Beschichtungsverfahren, z. B. Nasslackierungen.
Nachteile einer Pulverbeschichtungsanlage für Felgen
- Kosten: Pulverbeschichtungsanlagen sind in der Regel relativ teuer.
- Platzbedarf: Pulverbeschichtungsanlagen benötigen viel Platz.
- Sicherheit: Pulverbeschichtungsanlagen können gefährlich sein, wenn sie nicht sachgerecht betrieben werden.
Fazit
Pulverbeschichtungsanlagen für Felgen sind eine gute Möglichkeit, Alufelgen zu veredeln und zu schützen. Das Verfahren ist robust und langlebig und bietet eine Vielzahl von Gestaltungsmöglichkeiten.
Pulverabsaugung für Felgen
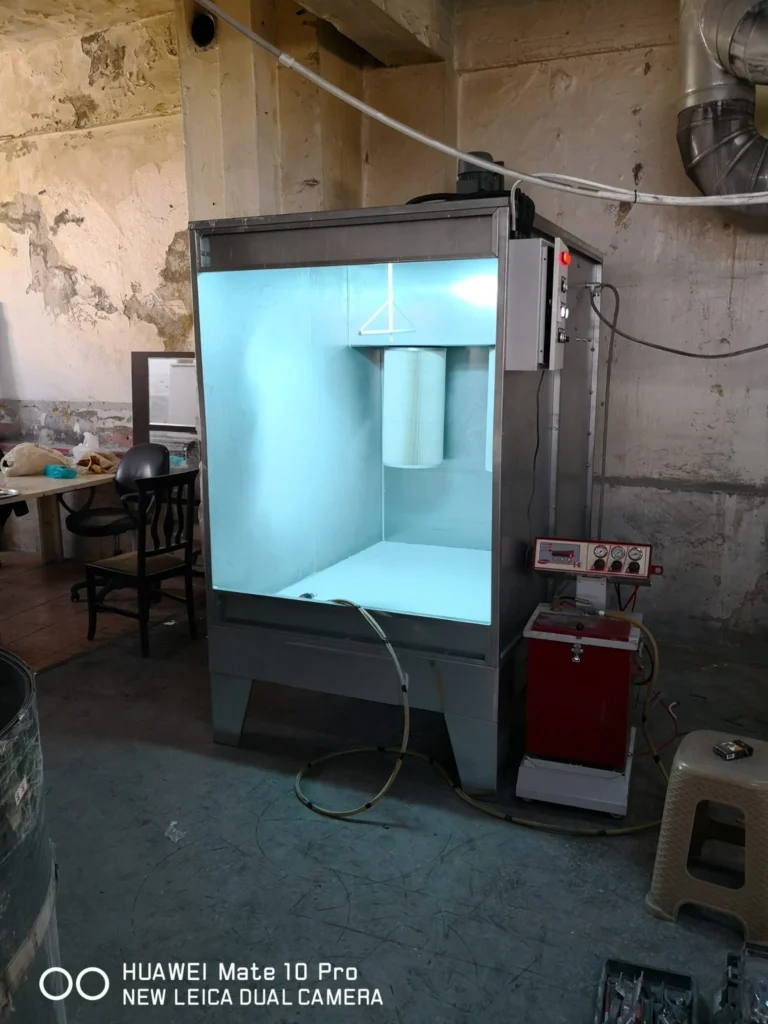
Pulverabsaugung für Felgen ist ein Verfahren, bei dem pulverförmiger Lack aus der Luft abgesaugt wird, bevor er sich auf Oberflächen absetzen kann. Dies ist wichtig, um die Gesundheit und Sicherheit der Arbeiter in Pulverbeschichtungsanlagen zu schützen und die Umwelt zu schützen.
Pulverabsaugung für Felgen erfolgt in der Regel mithilfe eines Zyklonsystems. Das Zyklonsystem besteht aus einem Gehäuse mit einem konischen Boden. Der pulverförmige Lack wird durch das Gehäuse gesaugt und in den konischen Boden geleitet. Im konischen Boden wird der pulverförmige Lack durch die Zentrifugalkraft abgeschieden und in einem Auffangbehälter gesammelt.
Pulverabsaugung für Felgen ist ein wichtiger Bestandteil der Pulverbeschichtung von Felgen. Sie trägt dazu bei, die Gesundheit und Sicherheit der Arbeiter zu schützen und die Umwelt zu schützen.
Vorteile der Pulverabsaugung für Felgen
- Schutz der Gesundheit und Sicherheit der Arbeiter: Pulverabsaugung verhindert, dass pulverförmiger Lack in die Atemwege der Arbeiter gelangt. Dies kann zu Lungenerkrankungen wie Asthma führen.
- Schutz der Umwelt: Pulverabsaugung verhindert, dass pulverförmiger Lack in die Umwelt gelangt. Dies kann die Luftqualität beeinträchtigen und die Umwelt verschmutzen.
- Verbesserte Arbeitsbedingungen: Pulverabsaugung trägt zu verbesserten Arbeitsbedingungen bei, indem sie die Luft in Pulverbeschichtungsanlagen sauberer macht.
Nachteile der Pulverabsaugung für Felgen
- Kosten: Pulverabsaugung kann teuer sein, insbesondere für große Pulverbeschichtungsanlagen.
- Platzbedarf: Pulverabsaugung benötigt Platz, insbesondere für große Zyklonsysteme.
- Wartung: Pulverabsaugungssysteme müssen regelmäßig gewartet und gereinigt werden, um eine optimale Funktion zu gewährleisten.
Fazit
Pulverabsaugung für Felgen ist ein wichtiger Bestandteil der Pulverbeschichtung von Felgen. Sie trägt dazu bei, die Gesundheit und Sicherheit der Arbeiter zu schützen und die Umwelt zu schützen.
Pulverofen für Felgen
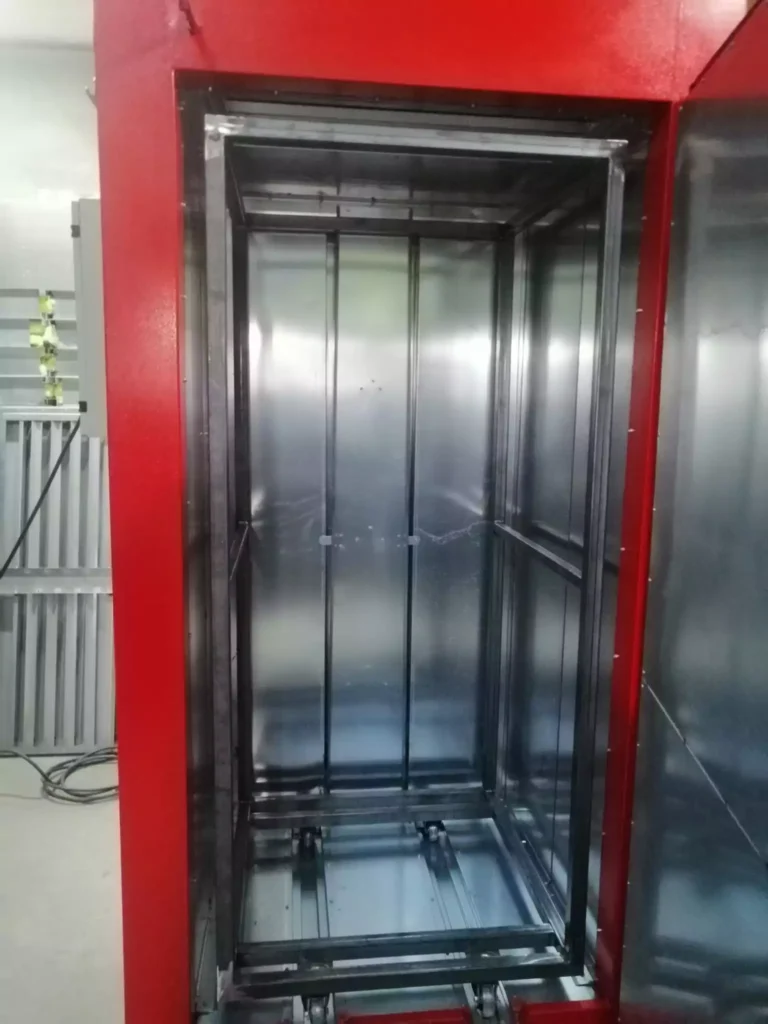
Ein Pulverofen für Felgen ist ein Ofen, in dem Pulverlack auf Felgen eingebrannt wird. Pulverbeschichtungen sind für Felgen besonders geeignet, da sie eine hohe Widerstandsfähigkeit gegen Kratzer, Rost und andere Beschädigungen bieten. Außerdem sind Pulverbeschichtungen lichtecht und UV-beständig, so dass die Farbe der Beschichtung auch bei starker Sonneneinstrahlung nicht verblasst.
Pulveröfen für Felgen sind in der Regel vollautomatisch und bestehen aus einem Vorbehandlungsraum, einem Beschichtungsraum und einem Ofen. Im Vorbehandlungsraum werden die Felgen gereinigt und entfettet. Im Beschichtungsraum werden die Felgen mit einem Pulverlack beschichtet. Der Pulverlack wird mithilfe einer Elektrostatikpistole auf die Felgen aufgetragen. Im Ofen wird der Pulverlack bei einer Temperatur von etwa 200 °C eingebrannt. Durch das Einbrennen härtet der Pulverlack aus und wird zu einer robusten und langlebigen Beschichtung.
Vorteile eines Pulverofens für Felgen
- Hohe Qualität der Beschichtung: Pulverbeschichtungen sind in der Regel sehr hochwertig und langlebig.
- Hohe Effizienz: Pulveröfen ermöglichen eine hohe Produktionsleistung.
- Umweltfreundlich: Pulverbeschichtungen sind umweltfreundlicher als andere Beschichtungsverfahren, z. B. Nasslackierungen.
Nachteile eines Pulverofens für Felgen
- Kosten: Pulveröfen sind in der Regel relativ teuer.
- Platzbedarf: Pulveröfen benötigen viel Platz.
- Sicherheit: Pulveröfen können gefährlich sein, wenn sie nicht sachgerecht betrieben werden.
Fazit
Pulveröfen für Felgen sind eine wichtige Anlage für die Pulverbeschichtung von Felgen. Sie bieten eine hohe Qualität der Beschichtung, hohe Effizienz und Umweltfreundlichkeit.
Technische Daten
Pulveröfen für Felgen sind in der Regel in verschiedenen Größen und Leistungsklassen erhältlich. Die Größe des Ofens bestimmt die Anzahl der Felgen, die gleichzeitig beschichtet werden können. Die Leistungsklasse des Ofens bestimmt die Temperatur und die Einbrennzeit.
Typische technische Daten für Pulveröfen für Felgen sind:
- Länge: 1,5 bis 6 Meter
- Breite: 1 bis 2 Meter
- Höhe: 1 bis 2 Meter
- Temperatur: 150 bis 250 °C
- Einbrennzeit: 15 bis 30 Minuten
Sicherheit
Pulveröfen für Felgen können gefährlich sein, wenn sie nicht sachgerecht betrieben werden. Daher ist es wichtig, die Sicherheitsvorschriften zu beachten. Dazu gehören:
- Verwendung von Schutzkleidung, z. B. Schutzhelm, Schutzbrille, Schutzhandschuhe und Schutzkleidung
- Einhaltung der Betriebsvorschriften
- Wartung und Inspektion des Ofens durch einen Fachmann
Fazit
Pulveröfen für Felgen sind eine wichtige Anlage für die Pulverbeschichtung von Felgen. Sie bieten eine hohe Qualität der Beschichtung, hohe Effizienz und Umweltfreundlichkeit.
Pulverlack
Pulverlack ist ein vielseitiges Beschichtungsmaterial, das häufig in der Industrie für die elektrostatische Pulverbeschichtung verwendet wird. Es besteht aus feinen pulverförmigen Partikeln, die eine Mischung aus Harzen, Pigmenten, Füllstoffen und Additiven enthalten. Diese Pulverpartikel sind in einer breiten Palette von Farben, Oberflächeneffekten und chemischen Formulierungen erhältlich, um den Anforderungen verschiedener Anwendungen gerecht zu werden. Pulverlacke bieten eine Reihe von Vorteilen, darunter hohe Haltbarkeit, Beständigkeit gegenüber UV-Strahlung, Chemikalien und Abrieb, sowie eine schnelle Aushärtung bei niedrigen Temperaturen. Sie werden in vielen Branchen eingesetzt, darunter Automobil-, Architektur-, Möbel-, Haushaltsgeräte- und Industrieanwendungen, um Oberflächenschutz, Ästhetik und Funktionalität zu verbessern. Die Verwendung von Pulverlack trägt auch zur Reduzierung von VOC-Emissionen (flüchtige organische Verbindungen) und Lösungsmitteln bei, was zu einer umweltfreundlicheren Beschichtungslösung im Vergleich zu traditionellen Lacken führt.
Koronaaufladung
Die Koronaaufladung ist ein entscheidender Schritt im Prozess der elektrostatischen Pulverbeschichtung. Dabei wird ein Hochspannungsfeld erzeugt, um die Pulverpartikel elektrostatisch aufzuladen, bevor sie auf das zu beschichtende Werkstück aufgebracht werden. Ein typisches Setup umfasst eine Koronaelektrode, die in der Nähe der Pulverbeschichtungspistole positioniert ist, und eine Hochspannungsquelle. Wenn die Spannung an die Koronaelektrode angelegt wird, ionisiert die Luft um sie herum und bildet eine Koronadischarge. Diese Entladung erzeugt eine hohe elektrische Feldstärke, die dazu führt, dass die Pulverpartikel negativ aufgeladen werden, wenn sie durch das Feld hindurchströmen. Die negativ geladenen Pulverpartikel werden dann zur positiv geladenen Oberfläche des Werkstücks angezogen und haften dort während des Beschichtungsprozesses. Die Koronaaufladung ermöglicht eine effiziente und gleichmäßige Verteilung der Pulverpartikel auf der Oberfläche des Werkstücks, was zu einer hochwertigen und haltbaren Beschichtung führt.
Triboaufladung
Die Triboaufladung ist ein alternativer Ansatz zur elektrostatischen Pulverbeschichtung, der auf dem Prinzip der Reibung basiert. Im Gegensatz zur Koronaaufladung, bei der Pulverpartikel durch ein Hochspannungsfeld elektrostatisch aufgeladen werden, erfolgt die Aufladung bei der Triboaufladung durch Reibungseffekte. Dies geschieht, indem das Pulvermaterial beim Durchlaufen eines Rohrs oder einer Schlauchleitung an der Innenwand des Behälters oder an anderen Oberflächen reibt. Während des Reibungsvorgangs werden Elektronen zwischen den Partikeln und den Oberflächen übertragen, was zu einer elektrostatischen Aufladung der Partikel führt. Die triboaufgeladenen Pulverpartikel haben tendenziell eine niedrigere Ladungsdichte als koronaaufgeladene Partikel, was zu unterschiedlichen Beschichtungseigenschaften führen kann. Die Triboaufladung bietet jedoch den Vorteil, dass sie keine Hochspannung erfordert und daher einfacher in verschiedenen Umgebungen einzusetzen ist. Sie wird häufig bei Anwendungen eingesetzt, bei denen eine feinere Kontrolle über die Ladungsdichte der Partikel erforderlich ist oder wenn Hochspannung nicht praktikabel ist.
Pulverbeschichtungspistole
Die Pulverbeschichtungspistole ist ein unverzichtbares Werkzeug in einem elektrostatischen Pulverbeschichtungssystem. Sie dient dazu, das Pulverlackmaterial auf das zu beschichtende Werkstück aufzutragen und dabei eine gleichmäßige und präzise Beschichtung zu gewährleisten. Die Pistole besteht typischerweise aus einem Pistolenkörper, einem Pulverbehälter, einer Hochspannungseinheit und einem Pulveraustragssystem.
Der Pistolenkörper ist ergonomisch gestaltet, um eine komfortable Handhabung während des Beschichtungsprozesses zu ermöglichen. Der Pulverbehälter enthält das Pulverlackmaterial und ist so konstruiert, dass es einfach nachgefüllt werden kann, um Unterbrechungen im Beschichtungsprozess zu minimieren.
Die Hochspannungseinheit erzeugt das elektrostatische Feld, das benötigt wird, um die Pulverpartikel aufzuladen. Dies geschieht entweder durch Koronaaufladung oder Triboaufladung, abhängig von der spezifischen Konfiguration der Pulverbeschichtungspistole.
Das Pulveraustragssystem steuert den Fluss des Pulverlackmaterials und die Verteilung der Pulverpartikel auf der Oberfläche des Werkstücks. Moderne Pulverbeschichtungspistolen bieten verschiedene Einstellmöglichkeiten, um den Pulverfluss, die Sprühmustergröße und andere Parameter anzupassen, um den Anforderungen verschiedener Beschichtungsanwendungen gerecht zu werden.
Insgesamt spielt die Pulverbeschichtungspistole eine entscheidende Rolle bei der Erzielung hochwertiger und haltbarer Beschichtungsergebnisse und trägt wesentlich zur Effizienz und Produktivität des Beschichtungsprozesses bei.
Hochspannung
Hochspannung ist ein wesentlicher Bestandteil des elektrostatischen Pulverbeschichtungsprozesses. Sie wird verwendet, um eine elektrische Ladung an den Pulverpartikeln zu erzeugen, bevor sie auf das zu beschichtende Werkstück aufgebracht werden. Typischerweise liegt die Spannung in einem Bereich von 20.000 bis 100.000 Volt, je nach den spezifischen Anforderungen des Beschichtungsprozesses und der Art des zu beschichtenden Materials.
Die Hochspannung wird entweder durch Koronaaufladung oder Triboaufladung erzeugt. Bei der Koronaaufladung wird ein Hochspannungsfeld erzeugt, indem eine Koronaelektrode in der Nähe der Pulverbeschichtungspistole platziert wird. Die Spannung ionisiert die Luft und bildet eine Koronadischarge, die die Pulverpartikel negativ auflädt. Bei der Triboaufladung hingegen entsteht die Hochspannung durch Reibungseffekte zwischen den Pulverpartikeln und den Oberflächen, an denen sie entlanggleiten.
Die Hochspannung spielt eine entscheidende Rolle bei der erfolgreichen elektrostatischen Pulverbeschichtung, da sie die Pulverpartikel dazu bringt, sich gleichmäßig auf der Oberfläche des Werkstücks zu verteilen und dort zu haften. Eine präzise Steuerung der Hochspannung ist wichtig, um eine konsistente Beschichtungsqualität und eine effiziente Pulverübertragung zu gewährleisten.
Darüber hinaus ist es wichtig, Sicherheitsvorkehrungen zu treffen, um das Risiko von Stromschlägen oder anderen Unfällen im Zusammenhang mit Hochspannung zu minimieren. Dies umfasst die Verwendung von isolierten Materialien, die ordnungsgemäße Erdung von Ausrüstung und Werkstücken sowie die Schulung des Bedienpersonals in sicheren Arbeitspraktiken im Umgang mit Hochspannungssystemen.
Negativ geladenes Pulver
Negativ geladenes Pulver spielt eine zentrale Rolle im Prozess der elektrostatischen Pulverbeschichtung. In diesem Verfahren werden die Pulverpartikel negativ aufgeladen, bevor sie auf das zu beschichtende Werkstück aufgebracht werden. Die negativen Ladungen bewirken, dass die Partikel zur positiv geladenen Oberfläche des Werkstücks gezogen werden, wo sie während des Beschichtungsprozesses haften bleiben.
Die negative Ladung der Pulverpartikel wird typischerweise durch Koronaaufladung oder Triboaufladung erzeugt. Bei der Koronaaufladung erfolgt die Ladung durch die Einwirkung eines Hochspannungsfelds auf das Pulver, während bei der Triboaufladung die Reibung zwischen den Partikeln und den Oberflächen zu einer Ladungsübertragung führt.
Negativ geladenes Pulver bietet mehrere Vorteile für den Beschichtungsprozess. Erstens ermöglicht es eine effiziente Anziehung und Haftung der Partikel an der Oberfläche des Werkstücks, was zu einer gleichmäßigen und hochwertigen Beschichtung führt. Zweitens erleichtert die negative Ladung die Steuerung und Lenkung der Pulverpartikel während des Beschichtungsprozesses, was zu einer präzisen Applikation und minimalen Überlappungen führt. Schließlich trägt die Verwendung von negativ geladenem Pulver dazu bei, die Wahrscheinlichkeit von Pulverablagerungen oder unerwünschten Nebelbildungen in der Umgebung zu verringern, was die Arbeitsumgebung sauberer und sicherer macht.
Insgesamt ist negativ geladenes Pulver ein wesentliches Element für die erfolgreiche Durchführung der elektrostatischen Pulverbeschichtung und spielt eine wichtige Rolle bei der Erzielung hochwertiger und haltbarer Beschichtungsergebnisse.
Farbnebel
Farbnebel ist ein unvermeidliches Nebenprodukt des Pulverbeschichtungsprozesses, das entsteht, wenn überschüssiges Pulver während des Auftragsvorgangs in der Luft schwebt und sich um die zu beschichtende Oberfläche herum ansammelt. Während des Beschichtungsvorgangs wird das Pulverlackmaterial durch die Pulverbeschichtungspistole auf das Werkstück aufgebracht. Ein Teil des Pulvers wird jedoch nicht sofort auf der Oberfläche haften und bildet stattdessen einen feinen Nebel in der Umgebung.
Der Farbnebel kann verschiedene Probleme verursachen, darunter eine ungleichmäßige Beschichtung, Pulverablagerungen auf benachbarten Oberflächen und eine Verschwendung von Beschichtungsmaterial. Darüber hinaus kann eine hohe Konzentration von Farbnebel in der Luft die Arbeitsumgebung verschmutzen und die Gesundheit und Sicherheit der Beschäftigten beeinträchtigen.
Um die Auswirkungen von Farbnebel zu minimieren, werden in Pulverbeschichtungsanlagen in der Regel effektive Absaug- und Filtrationssysteme eingesetzt. Diese Systeme saugen den Farbnebel ab und leiten ihn durch Filter, die die Pulverpartikel aus der Luft herausfiltern. Dadurch wird die Luft gereinigt, und das überschüssige Pulver kann für die Wiederverwendung gesammelt werden.
Darüber hinaus können verschiedene Maßnahmen ergriffen werden, um die Entstehung von Farbnebel zu reduzieren, wie z.B. die Optimierung der Sprühtechnik, die Verwendung von Sprühvorrichtungen mit niedrigem Druck und die Kontrolle des Pulverflusses. Durch die Kombination dieser Maßnahmen können Pulverbeschichtungsanlagen eine saubere und sichere Arbeitsumgebung schaffen und gleichzeitig eine effiziente und qualitativ hochwertige Beschichtung gewährleisten.
Übertragungseffizienz
Die Übertragungseffizienz ist ein wichtiger Parameter in der Pulverbeschichtungstechnik und beschreibt das Verhältnis zwischen der aufgetragenen Pulvermenge und der tatsächlichen Menge, die auf der Oberfläche des Werkstücks haften bleibt. Eine hohe Übertragungseffizienz ist entscheidend für einen effizienten und wirtschaftlichen Beschichtungsprozess, da sie den Pulververbrauch reduziert, Abfall minimiert und die Produktivität erhöht.
Eine effektive Übertragungseffizienz wird durch mehrere Faktoren beeinflusst, darunter die Sprühtechnik, die Pulverbeschichtungsausrüstung, die Einstellungen der Pulverbeschichtungspistole, die Qualität des Pulverlackmaterials und die Oberflächenbeschaffenheit des Werkstücks. Eine optimale Sprühtechnik und die Verwendung hochwertiger Ausrüstung können dazu beitragen, eine gleichmäßige Verteilung des Pulvers zu gewährleisten und Überlappungen zu minimieren, was zu einer verbesserten Übertragungseffizienz führt.
Die Überwachung und Kontrolle der Übertragungseffizienz ist ein wichtiger Bestandteil des Qualitätsmanagements in der Pulverbeschichtungsindustrie. Durch regelmäßige Messungen und Analysen können Betreiber die Leistung ihrer Beschichtungsanlagen optimieren und sicherstellen, dass die Beschichtungsdicke und -qualität den Anforderungen entsprechen.
Darüber hinaus kann die Verbesserung der Übertragungseffizienz dazu beitragen, die Umweltbelastung zu reduzieren, indem weniger Pulverabfall entsteht und der Einsatz von Beschichtungsmaterialien minimiert wird. Dies trägt zur Nachhaltigkeit und Umweltverträglichkeit des Beschichtungsprozesses bei und unterstützt die Bemühungen um eine grüne und nachhaltige Produktion.
Pulverflussregelung
Die Pulverflussregelung ist ein entscheidender Aspekt der Pulverbeschichtungstechnik, der die Dosierung und Verteilung des Beschichtungspulvers steuert. Ein präzises Pulverflussregelsystem ermöglicht es, die Menge des aufgetragenen Pulvers genau zu kontrollieren, um eine gleichmäßige Beschichtungsdicke und Qualität zu gewährleisten.
Moderne Pulverbeschichtungsanlagen sind mit verschiedenen Mechanismen zur Pulverflussregelung ausgestattet, die je nach den Anforderungen des Beschichtungsprozesses und der Art des zu beschichtenden Materials variieren können. Ein häufig verwendetes System zur Pulverflussregelung besteht aus einer Pulverdosiereinheit, die den Pulverfluss über ein Regelventil oder eine Schneckenfördereinheit steuert. Diese Einheit kann manuell oder automatisch betrieben werden und ermöglicht eine präzise Einstellung des Pulverflusses entsprechend den Anforderungen des Beschichtungsvorgangs.
Darüber hinaus können fortschrittliche Pulverbeschichtungsanlagen mit computergestützten Steuersystemen ausgestattet sein, die eine automatische Regelung des Pulverflusses in Echtzeit ermöglichen. Diese Systeme überwachen kontinuierlich den Beschichtungsprozess und passen den Pulverfluss dynamisch an, um eine gleichmäßige Beschichtungsdicke und Qualität zu gewährleisten. Dies trägt dazu bei, die Produktivität zu steigern, Ausschuss zu reduzieren und die Effizienz des Beschichtungsprozesses insgesamt zu verbessern.
Eine präzise Pulverflussregelung ist entscheidend für die Erzielung konsistenter und hochwertiger Beschichtungsergebnisse und spielt eine wichtige Rolle bei der Optimierung der Leistung von Pulverbeschichtungsanlagen. Durch die Verbesserung der Pulverflussregelung können Betreiber die Beschichtungsqualität optimieren, den Pulververbrauch reduzieren und die Gesamteffizienz ihres Beschichtungsprozesses steigern.
Pulverbeschichtungskabine
Die Pulverbeschichtungskabine ist eine spezielle Arbeitsumgebung, die für den Pulverbeschichtungsprozess konstruiert ist. Sie dient dazu, eine kontrollierte Umgebung zu schaffen, in der das Pulverlackmaterial auf das zu beschichtende Werkstück aufgetragen wird, während gleichzeitig die Umgebungsluft vor Pulvernebel geschützt wird.
Eine typische Pulverbeschichtungskabine besteht aus einer geschlossenen Kabine oder einem Gehäuse, das mit einer Einlassöffnung für das Werkstück, einer Abluftöffnung für die Abführung von überschüssigem Pulver und einem Filtersystem für die Reinigung der Abluft ausgestattet ist. Die Kabine kann verschiedene Größen und Konfigurationen aufweisen, um den Anforderungen verschiedener Beschichtungsanwendungen gerecht zu werden.
Die Innenwände der Pulverbeschichtungskabine sind in der Regel mit glatten und leicht zu reinigenden Materialien ausgekleidet, um eine einfache Wartung und Reinigung zu ermöglichen. Darüber hinaus können verschiedene Zusatzausstattungen wie Beleuchtungssysteme, Sprühdüsenhalterungen, Arbeitsplattformen und Handschuheinsätze installiert werden, um den Bedienkomfort und die Effizienz des Beschichtungsprozesses zu verbessern.
Das Hauptziel einer Pulverbeschichtungskabine besteht darin, eine saubere und sichere Arbeitsumgebung zu schaffen, in der der Beschichtungsprozess kontrolliert und effizient durchgeführt werden kann. Durch die Verwendung einer Kabine wird verhindert, dass Pulvernebel in die Umgebungsluft gelangt und sich auf benachbarten Oberflächen absetzt, was zu einer besseren Luftqualität und einer reduzierten Gefahr von Beschichtungsfehlern führt.
Insgesamt spielt die Pulverbeschichtungskabine eine entscheidende Rolle bei der Optimierung der Beschichtungsqualität, der Produktivität und der Sicherheit in Pulverbeschichtungsanlagen und trägt wesentlich zur Effizienz und Zuverlässigkeit des Beschichtungsprozesses bei.
Farbwechsel
Der Farbwechsel ist ein wichtiger Prozessschritt in der Pulverbeschichtung, der es ermöglicht, die Beschichtungsfarbe schnell und effizient zu wechseln, um unterschiedliche Werkstücke oder Designanforderungen zu erfüllen. Ein effektiver Farbwechsel ist entscheidend, um Stillstandzeiten zu minimieren und die Produktionsflexibilität zu erhöhen.
Der Farbwechselprozess umfasst in der Regel mehrere Schritte, darunter die Reinigung der Pulverbeschichtungspistole, das Entleeren des Pulverbehälters, das Reinigen der Pulverförderleitungen und das Spülen der Pulverbeschichtungskabine. Diese Schritte dienen dazu, sicherzustellen, dass keine Rückstände der vorherigen Beschichtung verbleiben und dass die neue Farbe ordnungsgemäß aufgetragen werden kann.
Moderne Pulverbeschichtungsanlagen sind oft mit automatisierten Farbwechselsystemen ausgestattet, die den Farbwechselprozess beschleunigen und vereinfachen können. Diese Systeme ermöglichen es, die verschiedenen Schritte des Farbwechsels automatisch durchzuführen, einschließlich der Reinigung der Pistole, des Spülens der Leitungen und des Befüllens des Pulverbehälters mit der neuen Farbe. Dadurch wird die Stillstandszeit zwischen den Farbwechseln minimiert und die Produktionskapazität optimiert.
Ein effizienter Farbwechsel ist besonders wichtig in Umgebungen mit häufigen Farbwechseln oder bei der Verarbeitung kleiner Losgrößen, da er die Flexibilität erhöht und die Gesamtproduktionszeit verkürzt. Durch die Implementierung effektiver Farbwechselsysteme können Pulverbeschichtungsanlagen ihre Produktivität steigern und gleichzeitig die Kosten und den Arbeitsaufwand reduzieren, die mit dem Wechseln von Farben verbunden sind.
Pulveraushärtungsofen
Der Pulveraushärtungsofen ist ein wesentlicher Bestandteil des Pulverbeschichtungsprozesses und dient dazu, das aufgetragene Pulverlackmaterial zu schmelzen und zu einer festen Beschichtung zu verschmelzen. Der Ofen spielt eine entscheidende Rolle bei der Erzielung einer dauerhaften und hochwertigen Beschichtung und beeinflusst maßgeblich die Endqualität des beschichteten Werkstücks.
Ein typischer Pulveraushärtungsofen besteht aus einer isolierten Kammer, die auf eine definierte Temperatur erhitzt wird, um das Pulverlackmaterial zu schmelzen und zu härten. Die Temperatur und die Aufheizgeschwindigkeit werden sorgfältig kontrolliert, um sicherzustellen, dass das Pulver gleichmäßig schmilzt und eine vollständige Vernetzung der Beschichtung erreicht wird.
Moderne Pulveraushärtungsofen sind oft mit fortschrittlichen Steuerungssystemen ausgestattet, die eine präzise Überwachung und Regelung der Ofentemperatur ermöglichen. Diese Systeme bieten auch Funktionen wie programmierbare Heizprofile, Vorheizzyklen und Kühlphasen, um eine optimale Aushärtung der Beschichtung zu gewährleisten und Beschädigungen an empfindlichen Werkstücken zu vermeiden.
Die Aushärtungszeit und Temperatur sind abhängig von der Art des verwendeten Pulverlackmaterials und den spezifischen Anforderungen der Beschichtungsanwendung. Ein typischer Aushärtungszyklus kann Temperaturen von 150°C bis 220°C und Zeiten von 10 bis 30 Minuten umfassen, je nach den Empfehlungen des Pulverlackherstellers und den Anforderungen des Werkstücks.
Insgesamt spielt der Pulveraushärtungsofen eine entscheidende Rolle bei der Erzielung einer hochwertigen und haltbaren Pulverbeschichtung und trägt wesentlich zur Qualität und Haltbarkeit des beschichteten Werkstücks bei. Durch die sorgfältige Auswahl und Steuerung des Ofens können Betreiber sicherstellen, dass ihre Beschichtungen die erforderlichen Leistungsanforderungen erfüllen und den Erwartungen ihrer Kunden entsprechen.
Vorbehandlung
Die Vorbehandlung ist ein kritischer Schritt im Pulverbeschichtungsprozess, der darauf abzielt, die Oberfläche des Werkstücks vor der eigentlichen Beschichtung vorzubereiten. Sie ist entscheidend für die Haftung und Haltbarkeit der Beschichtung und trägt maßgeblich zur Qualität des Endprodukts bei.
Typischerweise umfasst die Vorbehandlung mehrere Schritte, darunter Reinigung, Entfettung, Entrostung und/oder Phosphatierung der Oberfläche. Diese Schritte dienen dazu, Schmutz, Fett, Öl, Rost und andere Verunreinigungen zu entfernen, die die Haftung der Beschichtung beeinträchtigen könnten. Eine saubere und vorbereitete Oberfläche gewährleistet eine optimale Adhäsion und ermöglicht eine gleichmäßige Verteilung des Beschichtungsmaterials.
Die Auswahl des Vorbehandlungsverfahrens hängt von verschiedenen Faktoren ab, darunter das Material des Werkstücks, die Art der Verunreinigungen und die Anforderungen der Endanwendung. Zu den gängigen Vorbehandlungsmethoden gehören chemische Vorbehandlungen wie Beizen, Entfetten und Phosphatieren sowie mechanische Verfahren wie Sandstrahlen oder Schleifen.
Eine effektive Vorbehandlung ist entscheidend für die Langzeitbeständigkeit der Beschichtung und trägt dazu bei, Korrosion, Haftungsprobleme und vorzeitiges Versagen der Beschichtung zu verhindern. Sie ist ein wesentlicher Bestandteil eines jeden hochwertigen Pulverbeschichtungsprozesses und sollte sorgfältig geplant und durchgeführt werden, um die bestmöglichen Ergebnisse zu erzielen.
Pulverbeschichtungsausrüstung
Die Pulverbeschichtungsausrüstung umfasst eine Vielzahl von Geräten und Werkzeugen, die für die Durchführung des Pulverbeschichtungsprozesses benötigt werden. Diese Ausrüstung spielt eine entscheidende Rolle bei der Vorbereitung, Anwendung und Aushärtung des Pulverlackmaterials, um eine hochwertige Beschichtung auf dem Werkstück zu erzielen. Hier sind einige wichtige Komponenten der Pulverbeschichtungsausrüstung:
- Pulverbeschichtungspistole: Die Pulverbeschichtungspistole ist das Hauptwerkzeug, das verwendet wird, um das Pulverlackmaterial auf das Werkstück aufzutragen. Sie ist mit einem Hochspannungssystem ausgestattet, um die Pulverpartikel elektrostatisch aufzuladen, bevor sie auf die Oberfläche des Werkstücks gesprüht werden.
- Pulverbeschichtungskabine: Die Pulverbeschichtungskabine ist eine spezielle Arbeitsumgebung, die dazu dient, den Beschichtungsprozess zu kontrollieren und zu schützen. Sie verhindert, dass Pulvernebel in die Umgebungsluft gelangt und sammelt überschüssiges Pulver für die Wiederverwendung.
- Pulveraushärtungsofen: Der Pulveraushärtungsofen wird verwendet, um das aufgetragene Pulverlackmaterial zu schmelzen und zu härten, um eine dauerhafte Beschichtung zu erzeugen. Er spielt eine entscheidende Rolle bei der Erzielung einer gleichmäßigen und haltbaren Beschichtung.
- Vorbehandlungsausrüstung: Die Vorbehandlungsausrüstung umfasst verschiedene Geräte und Chemikalien, die zur Reinigung und Vorbereitung der Werkstückoberfläche vor der Beschichtung verwendet werden. Dies kann Entfettungsanlagen, Entrostungsgeräte, Phosphatierungsanlagen und andere Einrichtungen umfassen.
- Pulverrückgewinnungssystem: Das Pulverrückgewinnungssystem sammelt überschüssiges Pulver während des Beschichtungsprozesses und ermöglicht seine Wiederverwendung. Dies trägt zur Reduzierung von Abfall und Kosten bei und optimiert die Effizienz des Beschichtungsprozesses.
Zusammen bilden diese Komponenten die Grundlage für einen effizienten und hochwertigen Pulverbeschichtungsprozess. Die Auswahl und Installation der richtigen Pulverbeschichtungsausrüstung ist entscheidend für die erfolgreiche Durchführung von Beschichtungsprojekten in verschiedenen Branchen und Anwendungen.
Pulverrückgewinnungssystem
Das Pulverrückgewinnungssystem ist eine essentielle Komponente in der Pulverbeschichtungstechnologie, das dafür verantwortlich ist, überschüssiges Pulver, das während des Beschichtungsprozesses nicht auf dem Werkstück haftet, aufzufangen und für die Wiederverwendung zu sammeln. Es spielt eine wichtige Rolle bei der Reduzierung von Abfall, der Optimierung der Pulverausnutzung und der Senkung der Betriebskosten in einer Pulverbeschichtungsanlage.
Das Pulverrückgewinnungssystem besteht typischerweise aus mehreren Elementen:
- Pulversammelkabine: Diese spezielle Kabine oder Kammer dient dazu, das überschüssige Pulver während des Beschichtungsprozesses aufzufangen und zu sammeln. Sie ist so konstruiert, dass sie eine effiziente Abscheidung des Pulvers ermöglicht, während gleichzeitig eine gute Luftzirkulation innerhalb der Kabine gewährleistet wird.
- Filtersystem: Das Filtersystem ist dafür verantwortlich, das aufgefangene Pulver von der Luft zu trennen. Es besteht aus Filtern, die die Pulverpartikel herausfiltern und die gereinigte Luft wieder in die Umgebung abgeben. Dies ermöglicht es, die Luft in der Arbeitsumgebung sauber zu halten und das Risiko von Pulvernebelbildung zu minimieren.
- Pulverrückgewinnungseinheit: Diese Einheit sammelt das aufgefangene Pulver aus der Pulversammelkabine und führt es zurück in den Pulverkreislauf. Dies kann durch einen Rückförderer, eine Vakuumeinheit oder andere Mechanismen erfolgen, die das Pulver zu einem Lagerbehälter oder einem anderen Speicherort transportieren, von wo aus es für die Wiederverwendung zur Verfügung steht.
Die Effizienz des Pulverrückgewinnungssystems beeinflusst direkt die Betriebskosten und die Umweltfreundlichkeit einer Pulverbeschichtungsanlage. Ein effektives Rückgewinnungssystem maximiert die Nutzung des Pulvermaterials, reduziert den Bedarf an Nachschub und minimiert den Abfall, der entsorgt werden muss. Dadurch wird nicht nur die Wirtschaftlichkeit des Beschichtungsprozesses verbessert, sondern auch die Umweltbelastung verringert.
Pulverbeschichtungsschichtdickenmessgerät
Das Pulverbeschichtungsschichtdickenmessgerät ist ein Instrument, das zur Messung der Dicke der aufgetragenen Pulverbeschichtung auf einem Werkstück verwendet wird. Es spielt eine wichtige Rolle bei der Qualitätssicherung und Kontrolle des Beschichtungsprozesses, indem es sicherstellt, dass die Beschichtungsdicke den spezifizierten Anforderungen entspricht.
Das Messgerät arbeitet typischerweise auf der Basis von berührungslosen Messtechnologien wie Wirbelstrom- oder Wirbelstromverfahren. Diese Methoden ermöglichen es, die Dicke der Pulverbeschichtung präzise und zuverlässig zu messen, ohne dass ein direkter Kontakt mit dem Werkstück erforderlich ist. Das Gerät kann entweder als Handgerät oder als fest installiertes Messsystem ausgelegt sein, je nach den Anforderungen und den Gegebenheiten der Produktionsumgebung.
Die Verwendung eines Pulverbeschichtungsschichtdickenmessgeräts bietet mehrere Vorteile:
- Qualitätskontrolle: Das Messgerät ermöglicht es, die Dicke der Pulverbeschichtung während des Beschichtungsprozesses in Echtzeit zu überwachen und sicherzustellen, dass sie den festgelegten Spezifikationen entspricht. Dadurch können Fehler frühzeitig erkannt und korrigiert werden, bevor sie zu Qualitätsproblemen führen.
- Effizienzsteigerung: Durch die kontinuierliche Überwachung der Beschichtungsdicke können Betriebsabläufe optimiert und die Effizienz des Beschichtungsprozesses verbessert werden. Dies kann dazu beitragen, den Verbrauch von Beschichtungsmaterial zu reduzieren und die Produktionskosten zu senken.
- Dokumentation und Rückverfolgbarkeit: Das Messgerät ermöglicht es, genaue Aufzeichnungen über die Beschichtungsdicke zu führen und eine vollständige Rückverfolgbarkeit der Beschichtungsprozesse zu gewährleisten. Dies ist besonders wichtig in Branchen mit strengen Qualitäts- und Compliance-Anforderungen.
Insgesamt ist das Pulverbeschichtungsschichtdickenmessgerät ein unverzichtbares Instrument für die Qualitätskontrolle und Prozessoptimierung in der Pulverbeschichtungsindustrie. Durch die präzise Messung der Beschichtungsdicke trägt es dazu bei, hochwertige und haltbare Beschichtungen zu erzeugen und die Effizienz des Beschichtungsprozesses zu steigern.
Pulverbeschichtungsanlagenhersteller
Pulverbeschichtungsanlagenhersteller sind Unternehmen, die sich auf die Entwicklung, Herstellung und Installation von Anlagen und Ausrüstungen für die Pulverbeschichtung spezialisiert haben. Sie spielen eine entscheidende Rolle in der Pulverbeschichtungsindustrie, indem sie hochwertige und maßgeschneiderte Lösungen für eine Vielzahl von Anwendungen und Branchen bereitstellen.
Diese Hersteller entwerfen und produzieren verschiedene Arten von Pulverbeschichtungsanlagen, darunter Pulverbeschichtungskabinen, Pulveraushärtungsofen, Pulverrückgewinnungssysteme, Vorbehandlungsausrüstung, Pulverbeschichtungspistolen und andere Komponenten. Diese Anlagen können für unterschiedliche Anforderungen und Kapazitäten ausgelegt sein, von kleinen Handwerksbetrieben bis hin zu großen industriellen Produktionsanlagen.
Die Pulverbeschichtungsanlagenhersteller bieten in der Regel maßgeschneiderte Lösungen, die auf die spezifischen Anforderungen und Anwendungen ihrer Kunden zugeschnitten sind. Dies umfasst die Beratung, Planung, Konstruktion und Installation von Pulverbeschichtungsanlagen sowie Schulungen und technischen Support während des gesamten Lebenszyklus der Anlage.
Einige der wichtigsten Aufgaben und Verantwortlichkeiten von Pulverbeschichtungsanlagenherstellern umfassen:
- Entwicklung von innovativen und effizienten Pulverbeschichtungstechnologien und -lösungen.
- Bereitstellung von maßgeschneiderten Anlagen, die den spezifischen Anforderungen und Bedürfnissen der Kunden entsprechen.
- Unterstützung der Kunden bei der Planung, Installation und Inbetriebnahme der Pulverbeschichtungsanlagen.
- Schulung des Bedienpersonals und technischer Support während des Betriebs der Anlage.
- Kontinuierliche Weiterentwicklung und Verbesserung der Pulverbeschichtungstechnologien, um den sich wandelnden Anforderungen und Trends in der Industrie gerecht zu werden.
Insgesamt spielen Pulverbeschichtungsanlagenhersteller eine entscheidende Rolle bei der Unterstützung von Unternehmen und Organisationen bei der Umsetzung hochwertiger und effizienter Pulverbeschichtungsprozesse. Durch ihre Fachkenntnisse, Erfahrung und technische Expertise tragen sie dazu bei, die Produktivität zu steigern, die Qualität zu verbessern und die Wettbewerbsfähigkeit ihrer Kunden zu stärken.
Pulverbeschichtungspulver
Pulverbeschichtungspulver ist das Beschichtungsmaterial, das bei der Pulverbeschichtung verwendet wird, um eine Schutz- oder Dekorbeschichtung auf verschiedenen Substraten aufzutragen. Es handelt sich um ein feines Pulver, das aus einer Mischung von Harzen, Pigmenten, Füllstoffen und Additiven besteht und in einer Vielzahl von Farben, Texturen und Oberflächeneffekten erhältlich ist.
Die Auswahl des richtigen Pulverbeschichtungspulvers ist entscheidend für die Qualität und Leistung der Beschichtung sowie für das ästhetische Erscheinungsbild des Endprodukts. Es gibt verschiedene Arten von Pulverbeschichtungspulvern, die für unterschiedliche Anwendungen und Umgebungsbedingungen geeignet sind, darunter:
- Epoxidpulverbeschichtung: Epoxidpulverbeschichtungen bieten eine hervorragende chemische Beständigkeit und werden häufig für Anwendungen verwendet, die eine hohe Korrosionsbeständigkeit erfordern, wie z.B. im Automobil- und Maschinenbau.
- Polyesterpulverbeschichtung: Polyesterpulverbeschichtungen sind bekannt für ihre ausgezeichnete Wetterbeständigkeit und UV-Beständigkeit und werden oft für Außenanwendungen wie Fassaden, Geländer und Gartenmöbel eingesetzt.
- Polyurethanpulverbeschichtung: Polyurethanpulverbeschichtungen bieten eine hohe Flexibilität und Kratzfestigkeit und eignen sich besonders gut für Anwendungen, die eine hohe Abriebbeständigkeit erfordern, wie z.B. im Bereich der Möbel- und Gerätebeschichtung.
- Fluorpolymerpulverbeschichtung: Fluorpolymerpulverbeschichtungen bieten eine außergewöhnliche Witterungsbeständigkeit und Chemikalienbeständigkeit und werden häufig in anspruchsvollen Umgebungen wie der Architektur- und Chemieindustrie eingesetzt.
Pulverbeschichtungspulver wird typischerweise elektrostatisch aufgeladen und auf das zu beschichtende Werkstück gesprüht, bevor es in einem Pulveraushärtungsofen erhitzt wird, um eine feste und dauerhafte Beschichtung zu erzeugen. Durch die Verwendung von Pulverbeschichtungspulvern können hochwertige, langlebige und ästhetisch ansprechende Beschichtungen auf einer Vielzahl von Substraten realisiert werden.
Pulverbeschichtungspistole
Die Pulverbeschichtungspistole ist das zentrale Werkzeug in einem Pulverbeschichtungsprozess. Sie wird verwendet, um das Pulverbeschichtungsmaterial auf das Werkstück aufzutragen, indem es elektrostatisch aufgeladen und auf die Oberfläche des Substrats gesprüht wird. Die Pistole spielt eine entscheidende Rolle bei der Erzielung einer gleichmäßigen Beschichtungsdicke und -qualität und beeinflusst maßgeblich das Endergebnis des Beschichtungsprozesses.
Die Pulverbeschichtungspistole besteht typischerweise aus mehreren Komponenten:
- Pistolenkörper: Der Pistolenkörper beherbergt den Pulverbehälter und die elektrostatischen Ladungselemente. Er ist ergonomisch gestaltet, um eine komfortable Handhabung während des Beschichtungsvorgangs zu gewährleisten.
- Pulverbehälter: Der Pulverbehälter enthält das Pulverbeschichtungsmaterial, das auf das Werkstück aufgetragen wird. Er kann verschiedene Größen haben, um den Anforderungen unterschiedlicher Beschichtungsanwendungen gerecht zu werden.
- Hochspannungsgenerator: Der Hochspannungsgenerator erzeugt die elektrostatische Ladung, die dazu dient, das Pulverbeschichtungsmaterial aufzuladen, bevor es auf das Werkstück gesprüht wird. Dadurch wird eine verbesserte Haftung und eine gleichmäßige Verteilung des Pulvers erreicht.
- Sprühkopf und Düse: Der Sprühkopf und die Düse sind verantwortlich für die Zerstäubung und Verteilung des Pulverbeschichtungsmaterials auf der Oberfläche des Werkstücks. Sie sind in der Regel so konstruiert, dass sie eine gleichmäßige und präzise Sprühmuster erzeugen.
Moderne Pulverbeschichtungspistolen können mit verschiedenen Funktionen und Einstellungen ausgestattet sein, um eine optimale Leistung und Anpassungsfähigkeit an unterschiedliche Beschichtungsanforderungen zu gewährleisten. Dazu gehören Einstellungen für die Pulvermenge, die Sprühmusterbreite, den Sprühdruck und andere Parameter, die den Beschichtungsprozess beeinflussen.
Insgesamt ist die Pulverbeschichtungspistole ein unverzichtbares Werkzeug für die Pulverbeschichtungsindustrie und spielt eine wesentliche Rolle bei der Erzielung hochwertiger und haltbarer Beschichtungen auf einer Vielzahl von Substraten. Durch die Auswahl der richtigen Pistole und die optimale Einstellung können Betreiber die Effizienz und Qualität ihres Beschichtungsprozesses verbessern.
Pulverbeschichtungsfarben
Pulverbeschichtungsfarben sind spezielle Beschichtungsmaterialien, die für die Anwendung im Pulverbeschichtungsprozess entwickelt wurden. Diese Farben bestehen aus einer Mischung aus Harzen, Pigmenten, Füllstoffen und Additiven, die in pulverförmiger Form vorliegen. Sie werden elektrostatisch aufgeladen und auf das zu beschichtende Werkstück gesprüht, bevor sie im Pulveraushärtungsofen geschmolzen und zu einer festen Beschichtung verschmolzen werden.
Es gibt eine breite Palette von Pulverbeschichtungsfarben, die in verschiedenen Branchen und Anwendungen eingesetzt werden. Einige der häufigsten Arten von Pulverbeschichtungsfarben sind:
- Standardfarben: Diese umfassen eine Vielzahl von Farben, einschließlich Grundfarben wie Weiß, Schwarz, Grau und verschiedene Farbtöne von Rot, Blau, Grün und Gelb. Standardfarben werden häufig für allgemeine Anwendungen verwendet, bei denen keine spezifischen Farbanforderungen bestehen.
- Metallic-Farben: Metallic-Farben enthalten spezielle Pigmente, die einen metallischen Glanz und eine glänzende Oberfläche erzeugen. Sie werden oft für dekorative Anwendungen verwendet, bei denen ein glänzendes oder metallisches Finish gewünscht wird, wie z.B. bei Automobilteilen, Möbeln und Haushaltsgeräten.
- Texturierte Farben: Texturierte Farben enthalten Füllstoffe oder Additive, die eine strukturierte oder texturierte Oberfläche erzeugen. Diese Oberflächenfinishs reichen von leicht strukturiert bis zu grob strukturiert und können verwendet werden, um die Griffigkeit, Haptik oder ästhetische Wirkung der Beschichtung zu verbessern.
- Glänzende und matte Farben: Pulverbeschichtungsfarben sind in verschiedenen Glanzgraden erhältlich, von hochglänzend bis matt. Die Auswahl des Glanzgrades hängt von den ästhetischen Präferenzen des Kunden und den Anforderungen der Anwendung ab.
Die Auswahl der richtigen Pulverbeschichtungsfarbe ist entscheidend für die Ästhetik, Leistung und Haltbarkeit der Beschichtung. Faktoren wie UV-Beständigkeit, Chemikalienbeständigkeit, Wetterbeständigkeit und Abriebfestigkeit müssen berücksichtigt werden, um sicherzustellen, dass die Beschichtung den spezifischen Anforderungen der Anwendung gerecht wird.
Pulverbeschichtungsschichtdickenmessgerät
Ein Pulverbeschichtungsschichtdickenmessgerät ist ein Messinstrument, das speziell zur Bestimmung der Dicke von Pulverbeschichtungen auf verschiedenen Oberflächen entwickelt wurde. Diese Geräte spielen eine wichtige Rolle in der Qualitätskontrolle und Sicherstellung der Einhaltung von Spezifikationen in der Pulverbeschichtungsindustrie.
Ein typisches Pulverbeschichtungsschichtdickenmessgerät verwendet eine berührungslose Messmethode, um die Dicke der Beschichtung zu bestimmen. Hier sind einige wichtige Merkmale und Funktionen eines solchen Geräts:
- Messprinzip: Pulverbeschichtungsschichtdickenmessgeräte arbeiten oft nach dem Wirbelstrom- oder Wirbelstromverfahren. Bei diesen Methoden erzeugt das Gerät ein elektromagnetisches Feld, das durch die Beschichtung und das Substrat dringt. Die Dicke der Beschichtung beeinflusst die Stärke des zurückgestreuten Signals, das vom Messgerät detektiert wird.
- Genauigkeit und Auflösung: Hochwertige Pulverbeschichtungsschichtdickenmessgeräte bieten eine präzise Messung mit hoher Auflösung. Sie können auch kleine Unterschiede in der Beschichtungsdicke erkennen, um eine genaue Qualitätskontrolle zu gewährleisten.
- Messbereich: Diese Geräte sind in der Lage, Beschichtungsdicken in einem breiten Bereich zu messen, von wenigen Mikrometern bis zu mehreren Millimetern. Dies ermöglicht die Anpassung an verschiedene Beschichtungsanwendungen und -materialien.
- Benutzerfreundlichkeit: Pulverbeschichtungsschichtdickenmessgeräte sind oft einfach zu bedienen und erfordern keine speziellen Kenntnisse oder Schulungen. Sie verfügen über intuitive Bedienoberflächen und können schnell und einfach Messungen durchführen.
- Datenaufzeichnung und -speicherung: Fortgeschrittene Pulverbeschichtungsschichtdickenmessgeräte bieten Funktionen zur Aufzeichnung und Speicherung von Messdaten. Dies ermöglicht eine nachträgliche Analyse und Dokumentation der Messergebnisse für Qualitätskontrollzwecke.
Die Verwendung eines Pulverbeschichtungsschichtdickenmessgeräts bietet mehrere Vorteile, darunter die Sicherstellung einer gleichmäßigen Beschichtungsdicke, die Verbesserung der Produktqualität und die Einhaltung von branchenspezifischen Standards und Vorschriften. Diese Geräte sind unverzichtbare Werkzeuge für Pulverbeschichtungsbetriebe, um die Qualität und Leistung ihrer Beschichtungen zu maximieren.
Pulverbeschichtungskabine
Eine Pulverbeschichtungskabine ist eine spezielle Arbeitsumgebung, die für die Durchführung von Pulverbeschichtungsprozessen entwickelt wurde. Sie spielt eine entscheidende Rolle bei der Kontrolle und Sicherheit des Beschichtungsvorgangs, indem sie die Umgebung vor Pulvernebel schützt und eine kontrollierte Umgebung für die Beschichtung bietet.
Hier sind einige wichtige Merkmale und Funktionen einer Pulverbeschichtungskabine:
- Konstruktion und Materialien: Pulverbeschichtungskabinen sind in der Regel aus robusten Materialien wie Stahl oder Aluminium hergestellt und verfügen über eine spezielle Beschichtung, die korrosionsbeständig ist und eine lange Lebensdauer gewährleistet. Die Konstruktion der Kabine ist so gestaltet, dass sie eine effiziente Abscheidung von Pulvernebel ermöglicht und eine gute Luftzirkulation innerhalb der Kabine gewährleistet.
- Absaug- und Filtersystem: Die Pulverbeschichtungskabine ist mit einem leistungsstarken Absaug- und Filtersystem ausgestattet, das überschüssigen Pulvernebel aus der Luft entfernt und die Arbeitsumgebung sauber hält. Dieses System besteht typischerweise aus Filtern, die den Pulvernebel einfangen, und einem Abluftventilator, der die gereinigte Luft aus der Kabine abführt.
- Beleuchtung: Eine gute Beleuchtung ist entscheidend für die Durchführung von Präzisionsarbeiten in der Pulverbeschichtungskabine. Die Kabine ist mit speziellen Beleuchtungseinrichtungen ausgestattet, die eine gleichmäßige Ausleuchtung der Arbeitsfläche gewährleisten und eine klare Sicht auf das zu beschichtende Werkstück ermöglichen.
- Zugangstüren und Eingänge: Pulverbeschichtungskabinen verfügen über spezielle Zugangstüren und Eingänge, die eine einfache Beladung und Entladung von Werkstücken ermöglichen. Diese Türen sind oft mit Dichtungen ausgestattet, um ein Eindringen von Pulvernebel in die Umgebung zu verhindern.
- Sicherheitsvorkehrungen: Pulverbeschichtungskabinen sind mit verschiedenen Sicherheitsvorkehrungen ausgestattet, um die Sicherheit der Bediener und die Einhaltung von Vorschriften zu gewährleisten. Dazu gehören Notausschalter, Sicherheitsverriegelungen, Brand- und Explosionsvorkehrungen sowie Warnschilder und -markierungen.
Insgesamt bietet eine Pulverbeschichtungskabine eine sichere und kontrollierte Umgebung für die Durchführung von Pulverbeschichtungsprozessen. Durch ihre spezielle Konstruktion und Ausstattung tragen sie dazu bei, die Qualität und Effizienz der Beschichtungsarbeiten zu maximieren und die Gesundheit und Sicherheit der Bediener zu gewährleisten.
Pulveraushärtungsofen
Ein Pulveraushärtungsofen ist ein wesentlicher Bestandteil einer Pulverbeschichtungsanlage, der dazu dient, das aufgetragene Pulverbeschichtungsmaterial zu schmelzen und zu härten, um eine dauerhafte Beschichtung auf dem Werkstück zu erzeugen. Diese Öfen spielen eine entscheidende Rolle im Pulverbeschichtungsprozess, indem sie die Beschichtungsmaterialien auf eine definierte Temperatur erhitzen, um eine chemische Reaktion zu initiieren, die zur Aushärtung der Beschichtung führt.
Hier sind einige wichtige Merkmale und Funktionen eines Pulveraushärtungsofens:
- Temperaturkontrolle: Pulveraushärtungsofen sind mit präzisen Temperaturregelungssystemen ausgestattet, die es ermöglichen, die Ofentemperatur genau zu steuern und auf die spezifischen Anforderungen des Beschichtungsmaterials abzustimmen. Dies gewährleistet eine gleichmäßige und konsistente Aushärtung der Beschichtung auf dem gesamten Werkstück.
- Luftzirkulation: Ein effektives Luftzirkulationssystem im Ofen sorgt für eine gleichmäßige Verteilung der Wärme im gesamten Ofenraum und verhindert Hot-Spots oder ungleichmäßige Aushärtung der Beschichtung. Dies ist besonders wichtig für die Erzielung einer gleichmäßigen Beschichtungsdicke und Qualität.
- Aushärtezeit: Die Aushärtezeit, also die Zeit, die das Werkstück im Ofen verbringt, hängt von verschiedenen Faktoren ab, einschließlich der Art des Beschichtungsmaterials, der Dicke der Beschichtung und der Ofentemperatur. Pulveraushärtungsofen sind so konstruiert, dass sie eine optimale Aushärtezeit gewährleisten und eine übermäßige oder unzureichende Aushärtung vermeiden.
- Sicherheitsvorkehrungen: Pulveraushärtungsofen sind mit verschiedenen Sicherheitsvorkehrungen ausgestattet, um die Sicherheit der Bediener und die Einhaltung von Vorschriften zu gewährleisten. Dazu gehören Notausschalter, Temperatursensoren, Überhitzungsschutzvorrichtungen und Lüftungssysteme, um die Freisetzung von Dämpfen oder Gasen zu kontrollieren.
- Energieeffizienz: Moderne Pulveraushärtungsofen sind so konstruiert, dass sie energieeffizient arbeiten und den Energieverbrauch optimieren. Dies kann durch die Verwendung von Wärmedämmmaterialien, effiziente Wärmeübertragungssysteme und programmierbare Steuerungen erreicht werden.
Insgesamt sind Pulveraushärtungsofen entscheidende Komponenten in der Pulverbeschichtungsindustrie, die dazu beitragen, hochwertige und dauerhafte Beschichtungen auf einer Vielzahl von Werkstücken zu erzeugen. Durch ihre präzise Temperaturkontrolle, gleichmäßige Luftzirkulation und Sicherheitsvorkehrungen spielen sie eine wesentliche Rolle bei der Optimierung des Beschichtungsprozesses und der Maximierung der Produktqualität.
Pulverbeschichtungsausrüstung
Die Pulverbeschichtungsausrüstung umfasst eine Vielzahl von Geräten und Werkzeugen, die für die Durchführung des Pulverbeschichtungsprozesses benötigt werden. Diese Ausrüstung spielt eine entscheidende Rolle bei der Vorbereitung, Anwendung und Aushärtung des Pulverlackmaterials, um eine hochwertige Beschichtung auf dem Werkstück zu erzielen. Hier sind einige wichtige Komponenten der Pulverbeschichtungsausrüstung:
- Pulverbeschichtungspistole: Die Pulverbeschichtungspistole ist das Hauptwerkzeug, das verwendet wird, um das Pulverlackmaterial auf das Werkstück aufzutragen. Sie ist mit einem Hochspannungssystem ausgestattet, um die Pulverpartikel elektrostatisch aufzuladen, bevor sie auf die Oberfläche des Werkstücks gesprüht werden.
- Pulverbeschichtungskabine: Die Pulverbeschichtungskabine ist eine spezielle Arbeitsumgebung, die dazu dient, den Beschichtungsprozess zu kontrollieren und zu schützen. Sie verhindert, dass Pulvernebel in die Umgebungsluft gelangt und sammelt überschüssiges Pulver für die Wiederverwendung.
- Pulveraushärtungsofen: Der Pulveraushärtungsofen wird verwendet, um das aufgetragene Pulverlackmaterial zu schmelzen und zu härten, um eine dauerhafte Beschichtung zu erzeugen. Er spielt eine entscheidende Rolle bei der Erzielung einer gleichmäßigen und haltbaren Beschichtung.
- Vorbehandlungsausrüstung: Die Vorbehandlungsausrüstung umfasst verschiedene Geräte und Chemikalien, die zur Reinigung und Vorbereitung der Werkstückoberfläche vor der Beschichtung verwendet werden. Dies kann Entfettungsanlagen, Entrostungsgeräte, Phosphatierungsanlagen und andere Einrichtungen umfassen.
- Pulverrückgewinnungssystem: Das Pulverrückgewinnungssystem sammelt überschüssiges Pulver während des Beschichtungsprozesses und ermöglicht seine Wiederverwendung. Dies trägt zur Reduzierung von Abfall und Kosten bei und optimiert die Effizienz des Beschichtungsprozesses.
Zusammen bilden diese Komponenten die Grundlage für einen effizienten und hochwertigen Pulverbeschichtungsprozess. Die Auswahl und Installation der richtigen Pulverbeschichtungsausrüstung ist entscheidend für die erfolgreiche Durchführung von Beschichtungsprojekten in verschiedenen Branchen und Anwendungen.
Pulverbeschichtungszubehör
Pulverbeschichtungszubehör umfasst eine Vielzahl von Hilfsmitteln und Zusatzausrüstungen, die bei der Durchführung von Pulverbeschichtungsprozessen verwendet werden, um die Effizienz zu steigern, die Qualität zu verbessern und die Sicherheit zu gewährleisten. Hier sind einige wichtige Arten von Pulverbeschichtungszubehör:
- Hängevorrichtungen und Gestelle: Hängevorrichtungen und Gestelle werden verwendet, um die zu beschichtenden Werkstücke während des Beschichtungsprozesses sicher und stabil zu halten. Sie ermöglichen es, mehrere Werkstücke gleichzeitig zu beschichten und eine gleichmäßige Beschichtung auf allen Seiten zu erzielen.
- Maskierungs- und Abdeckmaterialien: Maskierungs- und Abdeckmaterialien werden verwendet, um bestimmte Bereiche des Werkstücks während des Beschichtungsprozesses abzudecken und zu schützen. Dies kann dazu beitragen, Überbeschichtung zu vermeiden und präzise Beschichtungsergebnisse zu erzielen.
- Temperaturindikatoren und Thermometer: Temperaturindikatoren und Thermometer werden verwendet, um die Temperatur in der Pulverbeschichtungskabine und im Pulveraushärtungsofen zu überwachen und zu steuern. Dies ist entscheidend für die Einhaltung der spezifizierten Prozesstemperaturen und die Gewährleistung einer gleichmäßigen und effektiven Beschichtung.
- Reinigungs- und Wartungswerkzeuge: Reinigungs- und Wartungswerkzeuge werden verwendet, um Pulverbeschichtungsausrüstung und -anlagen sauber zu halten und in gutem Zustand zu halten. Dies umfasst Bürsten, Reinigungsmittel, Druckluftgeräte und andere Werkzeuge zur Entfernung von Pulverrückständen und zur Wartung von Komponenten.
- Schutz- und Sicherheitsausrüstung: Schutz- und Sicherheitsausrüstung ist unerlässlich, um die Sicherheit der Bediener während des Beschichtungsprozesses zu gewährleisten. Dazu gehören persönliche Schutzausrüstung wie Schutzbrillen, Handschuhe, Atemschutzmasken und Schutzkleidung, um vor Pulvernebel, Chemikalien und anderen Gefahren zu schützen.
- Mess- und Prüfgeräte: Mess- und Prüfgeräte werden verwendet, um die Qualität und Leistung der Pulverbeschichtung zu überwachen und zu überprüfen. Dazu gehören Schichtdickenmessgeräte, Haftprüfgeräte, Oberflächenprofilmessgeräte und andere Instrumente zur Qualitätskontrolle und -prüfung.
Insgesamt trägt hochwertiges Pulverbeschichtungszubehör dazu bei, die Effizienz, Qualität und Sicherheit von Pulverbeschichtungsprozessen zu verbessern und die Gesamtleistung der Anlagen zu optimieren. Die Auswahl und Verwendung des richtigen Zubehörs ist entscheidend für den Erfolg von Pulverbeschichtungsprojekten in verschiedenen Branchen und Anwendungen.
Pulverbeschichtungsschablonen
Pulverbeschichtungsschablonen sind spezielle Vorlagen oder Schablonen, die verwendet werden, um Muster, Designs oder Grafiken auf Werkstücke während des Pulverbeschichtungsprozesses aufzubringen. Sie ermöglichen es, präzise und wiederholbare Dekoreffekte zu erzielen und bieten eine vielseitige Möglichkeit, die Ästhetik von beschichteten Teilen zu verbessern. Hier sind einige wichtige Aspekte von Pulverbeschichtungsschablonen:
- Materialien: Pulverbeschichtungsschablonen werden typischerweise aus robusten Materialien wie Kunststoff, Gummi, Metall oder flexiblen Folien hergestellt, die eine präzise Formgebung und Haltbarkeit ermöglichen. Die Wahl des Materials hängt von der Art des gewünschten Designs, der Anwendungsmethode und der Wiederverwendbarkeit ab.
- Designs und Muster: Pulverbeschichtungsschablonen sind in einer Vielzahl von Designs, Mustern und Größen erhältlich, um den unterschiedlichen Anforderungen und Vorlieben der Benutzer gerecht zu werden. Dies reicht von einfachen geometrischen Formen bis hin zu komplexen Grafiken und Bildern.
- Anwendungsmethoden: Es gibt verschiedene Methoden, um Pulverbeschichtungsschablonen auf Werkstücke aufzubringen, darunter manuelles Platzieren, Kleben, Magnetbefestigung oder die Verwendung von speziellen Halterungen oder Rahmen. Die Auswahl der Anwendungsmethode hängt von der Größe, Form und Oberfläche des Werkstücks sowie von den Eigenschaften der Schablone ab.
- Wiederverwendbarkeit: Einige Pulverbeschichtungsschablonen sind wiederverwendbar und können für mehrere Beschichtungsprojekte verwendet werden, während andere Einwegschablonen sind, die nach einmaliger Verwendung entsorgt werden müssen. Die Wiederverwendbarkeit hängt von der Qualität des Materials und der Anwendungsmethode ab.
- Präzision und Passgenauigkeit: Hochwertige Pulverbeschichtungsschablonen bieten eine präzise Passform und ermöglichen eine genaue Platzierung und Ausrichtung auf dem Werkstück. Dies gewährleistet eine klare und konsistente Übertragung des Designs oder Musters auf die beschichtete Oberfläche.
Pulverbeschichtungsschablonen bieten eine effektive Möglichkeit, individuelle und kreative Designs auf beschichteten Teilen zu realisieren und können in einer Vielzahl von Anwendungen eingesetzt werden, darunter Automobilteile, Möbel, Haushaltsgeräte, Beschilderungen und mehr. Durch ihre Vielseitigkeit und Anpassungsfähigkeit tragen sie dazu bei, die ästhetischen Möglichkeiten von Pulverbeschichtungen zu erweitern und die Anforderungen verschiedener Branchen und Kunden zu erfüllen.
Pulverbeschichtungsvorbehandlung
Die Pulverbeschichtungsvorbehandlung ist ein wichtiger Schritt im Pulverbeschichtungsprozess, der dazu dient, die Oberfläche des Werkstücks vor der Beschichtung vorzubereiten. Diese Vorbehandlung ist entscheidend für die Haftung, Haltbarkeit und Qualität der Pulverbeschichtung und umfasst verschiedene Reinigungs- und Oberflächenbehandlungsschritte. Hier sind einige wichtige Aspekte der Pulverbeschichtungsvorbehandlung:
- Reinigung: Der erste Schritt der Vorbehandlung besteht in der gründlichen Reinigung der Werkstückoberfläche, um Schmutz, Öl, Fett, Rost, Korrosion und andere Verunreinigungen zu entfernen. Dies kann durch Waschen mit Wasser, Entfetten mit speziellen Reinigungsmitteln oder chemische Reinigungsverfahren erfolgen.
- Entrostung: Bei Werkstücken, die Rost oder Korrosion aufweisen, ist es erforderlich, die Oberfläche zu entrosten, um eine saubere und gleichmäßige Beschichtung zu ermöglichen. Dies kann durch mechanische Methoden wie Sandstrahlen, Schleifen oder Bürsten oder chemische Entrostungsverfahren erreicht werden.
- Phosphatierung: Die Phosphatierung ist ein wichtiger Schritt der Vorbehandlung, der dazu dient, die Oberfläche des Werkstücks zu passivieren und die Haftung und Haltbarkeit der Beschichtung zu verbessern. Dabei wird eine Phosphatbeschichtung auf die Oberfläche aufgetragen, die eine chemische Verbindung mit dem Metall eingeht und eine gute Basis für die Pulverbeschichtung bildet.
- Spülung und Trocknung: Nach der Reinigung, Entrostung und Phosphatierung wird das Werkstück gründlich gespült, um Rückstände von Reinigungsmitteln oder Chemikalien zu entfernen, und anschließend getrocknet, um sicherzustellen, dass die Oberfläche sauber und trocken ist, bevor die Beschichtung aufgetragen wird.
- Vorbehandlungsmethoden: Es gibt verschiedene Methoden und Verfahren zur Durchführung der Pulverbeschichtungsvorbehandlung, darunter manuelle Reinigung, Tauchbäder, Sprühsysteme, automatisierte Vorbehandlungsanlagen und mehr. Die Auswahl der geeigneten Vorbehandlungsmethode hängt von verschiedenen Faktoren ab, einschließlich der Art des Werkstücks, der Beschichtungsmaterialien und der Produktionsanforderungen.
Die Pulverbeschichtungsvorbehandlung ist ein entscheidender Schritt, um die Qualität und Leistung der Pulverbeschichtung zu maximieren und sicherzustellen, dass die Beschichtung den spezifizierten Anforderungen und Standards entspricht. Durch eine sorgfältige und effektive Vorbehandlung kann die Haftung und Haltbarkeit der Beschichtung verbessert werden, was zu hochwertigen und langlebigen Beschichtungen führt.
Pulverbeschichtungsqualitätssicherung
Die Qualitätssicherung in der Pulverbeschichtung ist ein entscheidender Prozess, der dazu dient, sicherzustellen, dass die hergestellten Beschichtungen den festgelegten Anforderungen und Standards entsprechen. Eine effektive Qualitätssicherung trägt dazu bei, die Produktqualität zu verbessern, Ausschuss zu reduzieren und die Kundenzufriedenheit zu erhöhen. Hier sind einige wichtige Aspekte der Pulverbeschichtungsqualitätssicherung:
- Prozesskontrolle: Die Prozesskontrolle umfasst die Überwachung und Steuerung aller Schritte des Pulverbeschichtungsprozesses, einschließlich Vorbereitung, Beschichtung, Aushärtung und Nachbehandlung. Dies umfasst die Überwachung von Parametern wie Temperatur, Luftfeuchtigkeit, Beschichtungsdicke, Sprühmuster und Aushärtungszeit, um sicherzustellen, dass der Prozess konsistent und reproduzierbar ist.
- Qualitätsprüfung: Die Qualitätsprüfung beinhaltet die Bewertung der Beschichtungen auf ihre physikalischen, mechanischen und ästhetischen Eigenschaften, um sicherzustellen, dass sie den Spezifikationen und Standards entsprechen. Dies umfasst die Überprüfung der Beschichtungsdicke, Haftung, Oberflächenbeschaffenheit, Farbgenauigkeit, Glanzgrad, Textur und chemischen Beständigkeit.
- Prüfmethoden: Es gibt verschiedene Prüfmethoden und -techniken, die zur Bewertung der Qualität von Pulverbeschichtungen verwendet werden, darunter Schichtdickenmessung, Haftprüfung, Abriebprüfung, UV-Beständigkeitsprüfung, Salzsprühtest, Kreuzschnitttest und visuelle Inspektion. Die Auswahl der geeigneten Prüfmethoden hängt von den Anforderungen der Anwendung und den spezifischen Eigenschaften der Beschichtung ab.
- Qualitätsmanagement: Ein effektives Qualitätsmanagementsystem umfasst die Festlegung von Qualitätsstandards, -verfahren und -richtlinien, die Schulung von Mitarbeitern, die Durchführung von regelmäßigen Audits und Überprüfungen, die Fehleranalyse und -korrektur sowie die kontinuierliche Verbesserung der Prozesse und Verfahren.
- Rückverfolgbarkeit: Die Rückverfolgbarkeit von Pulverbeschichtungen ist wichtig, um sicherzustellen, dass Produkte und Prozesse nachvollziehbar sind und Qualitätsprobleme identifiziert und behoben werden können. Dies umfasst die Dokumentation von Prozessparametern, Prüfergebnissen, Chargennummern und anderen relevanten Informationen.
Eine effektive Qualitätssicherung in der Pulverbeschichtung ist unerlässlich, um hochwertige und zuverlässige Beschichtungen zu erzeugen und die Anforderungen und Erwartungen der Kunden zu erfüllen. Durch die Implementierung von robusten Qualitätskontrollverfahren und -systemen können Pulverbeschichtungsbetriebe ihre Wettbewerbsfähigkeit stärken und langfristigen Erfolg sicherstellen.
Pulverbeschichtungsprozessoptimierung
Die Optimierung des Pulverbeschichtungsprozesses ist ein kontinuierlicher Verbesserungsprozess, der darauf abzielt, die Effizienz, Qualität und Rentabilität des Beschichtungsprozesses zu maximieren. Durch die Identifizierung von Engpässen, Schwachstellen und Verbesserungspotenzialen können Pulverbeschichtungsbetriebe ihre Produktionsabläufe optimieren und ihre Wettbewerbsfähigkeit steigern. Hier sind einige wichtige Aspekte der Pulverbeschichtungsprozessoptimierung:
- Prozessanalyse: Die Prozessanalyse umfasst die gründliche Bewertung aller Schritte des Pulverbeschichtungsprozesses, von der Vorbereitung der Werkstücke bis zur Endbearbeitung. Dabei werden Daten zu Durchlaufzeiten, Materialverbrauch, Ausbeute, Ausschussraten, Beschichtungsqualität und anderen Leistungskennzahlen gesammelt und analysiert, um Schwachstellen und Optimierungspotenziale zu identifizieren.
- Lean-Prinzipien: Die Anwendung von Lean-Prinzipien wie Kaizen, 5S, Wertstromanalyse und kontinuierlicher Verbesserung kann dazu beitragen, Verschwendung zu reduzieren, Durchlaufzeiten zu verkürzen und die Effizienz des Pulverbeschichtungsprozesses zu steigern. Dies umfasst die Optimierung von Arbeitsabläufen, Layouts, Materialflüssen und Lagerbeständen.
- Technologische Innovationen: Die Integration neuer Technologien und Ausrüstungen kann den Pulverbeschichtungsprozess optimieren und verbessern. Dies kann die Einführung automatisierter Beschichtungsanlagen, Robotik, fortschrittlicher Pulverbeschichtungspistolen, verbesserte Pulverrückgewinnungssysteme, digitale Steuerungen und Überwachungssysteme sowie fortschrittliche Prüftechnologien umfassen.
- Schulung und Qualifikation: Die Schulung und Qualifikation von Mitarbeitern ist entscheidend für die Optimierung des Pulverbeschichtungsprozesses. Durch die Schulung von Mitarbeitern in den Bereichen Prozessverbesserung, Sicherheit, Qualitätskontrolle, Wartung und Bedienung von Ausrüstungen können Betriebe die Leistung ihrer Mitarbeiter verbessern und das Potenzial ihres Teams voll ausschöpfen.
- Kundenfeedback und Zusammenarbeit: Die Einbindung von Kundenfeedback und die enge Zusammenarbeit mit Kunden und Lieferanten können dazu beitragen, den Pulverbeschichtungsprozess kontinuierlich zu verbessern und auf die spezifischen Anforderungen und Erwartungen der Kunden einzugehen. Dies umfasst die Bewertung von Kundenanfragen, Rückmeldungen zur Produktqualität und Zusammenarbeit bei der Entwicklung neuer Produkte und Lösungen.
Durch die kontinuierliche Optimierung des Pulverbeschichtungsprozesses können Betriebe ihre Effizienz steigern, Kosten senken, die Qualität verbessern und ihre Wettbewerbsfähigkeit stärken. Durch die Implementierung von Best Practices, Lean-Prinzipien und innovativen Technologien können Pulverbeschichtungsbetriebe ihre Produktionsabläufe optimieren und langfristigen Erfolg sicherstellen.
Pulverbeschichtungsfehleranalyse
Die Fehleranalyse in der Pulverbeschichtung ist ein wichtiger Prozess, der dazu dient, die Ursachen von Beschichtungsfehlern zu identifizieren, zu verstehen und zu beheben, um die Qualität der Beschichtungen zu verbessern und Ausschuss zu reduzieren. Eine gründliche Fehleranalyse ermöglicht es, wiederkehrende Probleme zu erkennen, effektive Lösungen zu entwickeln und die Prozessstabilität zu erhöhen. Hier sind einige wichtige Aspekte der Pulverbeschichtungsfehleranalyse:
- Fehleridentifikation: Der erste Schritt bei der Fehleranalyse besteht darin, die Art und den Umfang des Beschichtungsfehlers zu identifizieren. Dies kann durch visuelle Inspektion, Prüfungen der Beschichtungseigenschaften, Kundenrückmeldungen oder Rückverfolgbarkeit von Produktionschargen erfolgen.
- Ursachenanalyse: Nach der Fehleridentifikation ist es wichtig, die Ursachen des Beschichtungsfehlers zu analysieren und zu verstehen. Dies kann durch die Untersuchung verschiedener Faktoren wie Prozessparameter, Materialqualität, Umgebungsbedingungen, Ausrüstungszustand und menschliche Fehler erfolgen.
- Fehlerklassifizierung: Beschichtungsfehler können in verschiedene Kategorien eingeteilt werden, einschließlich Haftungsprobleme, Blasenbildung, Farbabweichungen, Kratzer, Unregelmäßigkeiten der Oberfläche, Haarrisse, Delamination und andere. Die Klassifizierung der Fehler ermöglicht eine gezielte Analyse und Lösungssuche.
- Prüfmethoden: Zur Fehleranalyse können verschiedene Prüfmethoden und -techniken eingesetzt werden, darunter visuelle Inspektion, Schichtdickenmessung, Haftprüfung, Mikroskopie, Röntgeninspektion, Abriebprüfung und chemische Analysen. Die Auswahl der geeigneten Prüfmethoden hängt von der Art des Fehlers und den spezifischen Anforderungen der Analyse ab.
- Lösungsfindung und -umsetzung: Nach der Ursachenanalyse ist es wichtig, geeignete Lösungen zu entwickeln und umzusetzen, um den Beschichtungsfehler zu beheben und zukünftige Probleme zu vermeiden. Dies kann die Anpassung von Prozessparametern, die Verbesserung der Materialqualität, die Wartung oder Aktualisierung von Ausrüstungen, die Schulung von Mitarbeitern oder die Änderung von Verfahren umfassen.
- Kontinuierliche Verbesserung: Die Fehleranalyse ist ein iterativer Prozess, der kontinuierliche Verbesserungen ermöglicht. Durch die Implementierung von Korrekturmaßnahmen, die Überwachung der Wirksamkeit dieser Maßnahmen und die Anpassung des Prozesses können Betriebe ihre Leistung steigern und die Qualität ihrer Beschichtungen kontinuierlich verbessern.
Durch eine systematische und gründliche Fehleranalyse können Betriebe die Qualität ihrer Pulverbeschichtungen verbessern, die Ausschussraten reduzieren und die Kundenzufriedenheit erhöhen. Eine proaktive Fehleranalyse und -behebung trägt dazu bei, die Effizienz und Zuverlässigkeit des Pulverbeschichtungsprozesses zu steigern und langfristigen Erfolg zu gewährleisten.
Pulverbeschichtungsschichtdicke
Die Schichtdicke bei der Pulverbeschichtung ist ein entscheidender Parameter, der die Qualität, Haltbarkeit und Funktionalität der Beschichtung beeinflusst. Die genaue Kontrolle und Überwachung der Schichtdicke ist entscheidend, um sicherzustellen, dass die Beschichtung den spezifizierten Anforderungen entspricht und eine gleichmäßige und zuverlässige Abdeckung auf dem Werkstück gewährleistet. Hier sind einige wichtige Aspekte der Pulverbeschichtungsschichtdicke:
- Definition: Die Schichtdicke bei der Pulverbeschichtung bezieht sich auf die Dicke der aufgetragenen Pulverschicht auf der Oberfläche des Werkstücks. Sie wird üblicherweise in Mikrometern (µm) oder Mil (Tausendstel Zoll) gemessen.
- Mindest- und Maximalwerte: Für verschiedene Anwendungen und Werkstücke können Mindest- und Maximalwerte für die Schichtdicke festgelegt werden, um sicherzustellen, dass die Beschichtung die erforderliche Leistung und Funktionalität bietet. Diese Werte können durch Branchenstandards, Kundenspezifikationen oder Anforderungen für bestimmte Anwendungen festgelegt werden.
- Einflussfaktoren: Die Schichtdicke kann von verschiedenen Faktoren beeinflusst werden, darunter die Art des Beschichtungsmaterials, die Sprühtechnik, die Sprühentfernung, die Sprühgeschwindigkeit, die Werkstückgeometrie, die Oberflächenbeschaffenheit und die Prozesstemperatur.
- Messung und Prüfung: Die Messung der Schichtdicke erfolgt typischerweise mit speziellen Messgeräten wie Schichtdickenmessgeräten, die die Beschichtungsdicke berührungslos und zerstörungsfrei messen können. Es gibt verschiedene Techniken und Methoden zur Messung der Schichtdicke, darunter magnetische Induktion, Wirbelstrom, Ultraschall und optische Verfahren.
- Qualitätskontrolle: Die genaue Kontrolle der Schichtdicke ist entscheidend für die Qualitätssicherung in der Pulverbeschichtung. Durch regelmäßige Überwachung, Prüfung und Kalibrierung der Messgeräte können Abweichungen von den spezifizierten Schichtdicken rechtzeitig erkannt und behoben werden.
- Anpassung: Bei Bedarf können Anpassungen an den Beschichtungsparametern vorgenommen werden, um die Schichtdicke zu optimieren und den Anforderungen zu entsprechen. Dies kann die Anpassung von Sprühparametern, die Änderung der Beschichtungsmaterialien oder die Überarbeitung des Beschichtungsprozesses umfassen.
Die genaue Kontrolle und Überwachung der Schichtdicke ist ein wesentlicher Bestandteil der Pulverbeschichtung, um eine hochwertige und zuverlässige Beschichtung zu gewährleisten. Durch die Einhaltung von Mindest- und Maximalwerten, die Verwendung geeigneter Messgeräte und die Implementierung von Qualitätskontrollverfahren können Betriebe sicherstellen, dass ihre Pulverbeschichtungen den erforderlichen Standards und Anforderungen entsprechen.
Pulverbeschichtungsausrüstung
Die Pulverbeschichtungsausrüstung umfasst eine Vielzahl von Geräten und Werkzeugen, die für die Durchführung des Pulverbeschichtungsprozesses benötigt werden. Diese Ausrüstung spielt eine entscheidende Rolle bei der Vorbereitung, Anwendung und Aushärtung des Pulverlackmaterials, um eine hochwertige Beschichtung auf dem Werkstück zu erzielen. Hier sind einige wichtige Komponenten der Pulverbeschichtungsausrüstung:
- Pulverbeschichtungspistole: Die Pulverbeschichtungspistole ist das Hauptwerkzeug, das verwendet wird, um das Pulverlackmaterial auf das Werkstück aufzutragen. Sie ist mit einem Hochspannungssystem ausgestattet, um die Pulverpartikel elektrostatisch aufzuladen, bevor sie auf die Oberfläche des Werkstücks gesprüht werden.
- Pulverbeschichtungskabine: Die Pulverbeschichtungskabine ist eine spezielle Arbeitsumgebung, die dazu dient, den Beschichtungsprozess zu kontrollieren und zu schützen. Sie verhindert, dass Pulvernebel in die Umgebungsluft gelangt und sammelt überschüssiges Pulver für die Wiederverwendung.
- Pulveraushärtungsofen: Der Pulveraushärtungsofen wird verwendet, um das aufgetragene Pulverlackmaterial zu schmelzen und zu härten, um eine dauerhafte Beschichtung zu erzeugen. Er spielt eine entscheidende Rolle bei der Erzielung einer gleichmäßigen und haltbaren Beschichtung.
- Vorbehandlungsausrüstung: Die Vorbehandlungsausrüstung umfasst verschiedene Geräte und Chemikalien, die zur Reinigung und Vorbereitung der Werkstückoberfläche vor der Beschichtung verwendet werden. Dies kann Entfettungsanlagen, Entrostungsgeräte, Phosphatierungsanlagen und andere Einrichtungen umfassen.
- Pulverrückgewinnungssystem: Das Pulverrückgewinnungssystem sammelt überschüssiges Pulver während des Beschichtungsprozesses und ermöglicht seine Wiederverwendung. Dies trägt zur Reduzierung von Abfall und Kosten bei und optimiert die Effizienz des Beschichtungsprozesses.
Zusammen bilden diese Komponenten die Grundlage für einen effizienten und hochwertigen Pulverbeschichtungsprozess. Die Auswahl und Installation der richtigen Pulverbeschichtungsausrüstung ist entscheidend für die erfolgreiche Durchführung von Beschichtungsprojekten in verschiedenen Branchen und Anwendungen.
Pulverbeschichtungspulver
Pulverbeschichtungspulver sind spezielle Beschichtungsmaterialien in Pulverform, die elektrostatisch aufgeladen und auf die Oberfläche eines Werkstücks aufgetragen werden, um eine dauerhafte und attraktive Beschichtung zu erzeugen. Diese Pulver bestehen aus verschiedenen Harzen, Pigmenten, Füllstoffen und Additiven, die eine Vielzahl von Eigenschaften und Anwendungen ermöglichen. Hier sind einige wichtige Aspekte von Pulverbeschichtungspulvern:
- Zusammensetzung: Pulverbeschichtungspulver bestehen in der Regel aus einem Harzsystem, das als Bindemittel dient, Pigmenten für die Farbe und Deckkraft, Füllstoffen für die Textur und Härtern oder Vernetzern für die Aushärtung. Die genaue Zusammensetzung variiert je nach den Anforderungen der Anwendung und den spezifischen Eigenschaften, die erzielt werden sollen.
- Harzsysteme: Die Harzsysteme in Pulverbeschichtungspulvern können auf Epoxid-, Polyester-, Polyurethan-, Acryl- oder Hybridbasis basieren. Jedes Harzsystem bietet unterschiedliche Eigenschaften in Bezug auf Haltbarkeit, Flexibilität, chemische Beständigkeit, UV-Beständigkeit und Temperaturbeständigkeit, die je nach Anwendung berücksichtigt werden müssen.
- Pigmente und Farben: Pulverbeschichtungspulver sind in einer breiten Palette von Farben und Effekten erhältlich, von Standardfarben bis hin zu Metallics, Perlmuttfarben, Glanz-, Matt- und Struktureffekten. Die Auswahl der Farbe und des Effekts richtet sich nach den ästhetischen Anforderungen der Anwendung und den Vorlieben des Kunden.
- Partikelgröße und Textur: Die Partikelgröße und Textur des Pulverbeschichtungspulvers beeinflussen die Oberflächenstruktur und -aussehen der Beschichtung. Feinere Partikel erzeugen glattere Oberflächen, während gröbere Partikel strukturierte oder texturierte Oberflächen erzeugen können. Die Auswahl der Partikelgröße und Textur hängt von der gewünschten Oberflächengestaltung und Funktionalität ab.
- Anwendungstechniken: Pulverbeschichtungspulver können mit verschiedenen Sprüh- und Applikationstechniken aufgetragen werden, darunter elektrostatische Sprühen, Tribo-Ladungssprühen, Fluidbettbeschichtung und Wirbelschichtbeschichtung. Die Auswahl der geeigneten Anwendungstechnik hängt von der Art des Pulverbeschichtungspulvers, der Werkstückgeometrie und den Produktionsanforderungen ab.
Pulverbeschichtungspulver bieten eine Vielzahl von Vorteilen gegenüber anderen Beschichtungsmaterialien, darunter hohe Haltbarkeit, Umweltverträglichkeit, geringe VOC-Emissionen, schnelle Aushärtungszeiten und eine breite Auswahl an Farben und Effekten. Durch die Auswahl des richtigen Pulverbeschichtungspulvers können Betriebe hochwertige Beschichtungen erzeugen, die den Anforderungen ihrer Kunden entsprechen und eine lange Lebensdauer haben.
Pulverbeschichtungsanlage
Eine Pulverbeschichtungsanlage ist eine spezielle Produktionsanlage, die für die Durchführung des Pulverbeschichtungsprozesses ausgelegt ist. Diese Anlagen umfassen verschiedene Komponenten und Ausrüstungen, die zur Vorbereitung, Anwendung, Aushärtung und Nachbehandlung von Pulverbeschichtungen benötigt werden. Hier sind einige wichtige Aspekte einer Pulverbeschichtungsanlage:
- Pulverbeschichtungskabine: Die Pulverbeschichtungskabine ist ein geschlossener Arbeitsbereich, der dazu dient, den Beschichtungsprozess zu kontrollieren und zu schützen. Sie ist mit Filtersystemen ausgestattet, um Pulvernebel zu erfassen und zu recyceln, sowie mit Belüftungs- und Absaugvorrichtungen, um die Luftqualität in der Umgebung zu erhalten.
- Pulverbeschichtungspistolen: Pulverbeschichtungspistolen sind das Hauptwerkzeug, das verwendet wird, um das Pulverlackmaterial auf die Oberfläche des Werkstücks aufzutragen. Sie sind mit einem Hochspannungssystem ausgestattet, um die Pulverpartikel elektrostatisch aufzuladen und eine gleichmäßige Beschichtung zu erzeugen.
- Pulveraushärtungsofen: Der Pulveraushärtungsofen ist ein beheizter Ofen, der dazu dient, das aufgetragene Pulverlackmaterial zu schmelzen und zu härten, um eine dauerhafte Beschichtung zu erzeugen. Die Temperatur und Aushärtungszeit im Ofen werden entsprechend den Anforderungen des Beschichtungsmaterials und der Werkstücke eingestellt.
- Vorbehandlungseinrichtungen: Vorbehandlungseinrichtungen umfassen verschiedene Anlagen und Geräte zur Reinigung und Vorbereitung der Werkstückoberfläche vor der Beschichtung. Dies kann Entfettungsanlagen, Entrostungsgeräte, Phosphatierungsanlagen und andere Einrichtungen umfassen, die dazu beitragen, die Haftung und Haltbarkeit der Beschichtung zu verbessern.
- Pulverrückgewinnungssystem: Das Pulverrückgewinnungssystem sammelt überschüssiges Pulver während des Beschichtungsprozesses und ermöglicht seine Wiederverwendung. Dies trägt zur Reduzierung von Abfall und Kosten bei und optimiert die Effizienz des Beschichtungsprozesses.
- Steuerungs- und Überwachungssysteme: Pulverbeschichtungsanlagen sind mit Steuerungs- und Überwachungssystemen ausgestattet, die die verschiedenen Prozessparameter überwachen und steuern. Dies umfasst die Überwachung der Ofentemperatur, Sprühparameter, Luftströmung, Pulverrückgewinnung und anderen wichtigen Prozessvariablen.
Eine gut ausgelegte und gepflegte Pulverbeschichtungsanlage ist entscheidend für die effiziente und zuverlässige Durchführung von Beschichtungsprojekten. Durch die richtige Auswahl, Installation und Wartung der Ausrüstung können Betriebe hochwertige Beschichtungen erzeugen, die den Anforderungen ihrer Kunden entsprechen und eine lange Lebensdauer haben.
Pulverbeschichtungsvorbehandlung
Die Pulverbeschichtungsvorbehandlung ist ein wesentlicher Schritt im Pulverbeschichtungsprozess, der dazu dient, die Oberfläche des Werkstücks auf die Beschichtung vorzubereiten. Eine gründliche Vorbehandlung ist entscheidend für die Haftung, Haltbarkeit und Qualität der Pulverbeschichtung. Hier sind einige Schlüsselaspekte der Pulverbeschichtungsvorbehandlung:
- Reinigung: Die gründliche Reinigung der Werkstückoberfläche ist der erste Schritt der Vorbehandlung. Dies umfasst die Entfernung von Schmutz, Fett, Ölen, Rost, Korrosion und anderen Verunreinigungen, die die Haftung der Beschichtung beeinträchtigen könnten. Die Reinigung kann durch Waschen mit Wasser, Entfetten mit speziellen Reinigungsmitteln oder andere chemische Reinigungsverfahren erfolgen.
- Entfettung: Entfettung ist ein wichtiger Schritt, um Öle, Fette und andere organische Verunreinigungen von der Werkstückoberfläche zu entfernen. Dies kann durch Tauchen in Entfettungslösungen, Sprühen von Entfettungsmitteln oder andere Methoden erfolgen, um eine saubere Oberfläche für die Beschichtung sicherzustellen.
- Entrostung: Wenn das Werkstück Rost oder Korrosion aufweist, ist es notwendig, die Oberfläche zu entrosten, um eine gleichmäßige und haftende Beschichtung zu gewährleisten. Dies kann durch mechanische Methoden wie Sandstrahlen, Schleifen oder Bürsten oder durch chemische Entrostungsverfahren erfolgen.
- Phosphatierung: Die Phosphatierung ist ein wichtiger Schritt, um die Oberfläche zu passivieren und die Haftung und Haltbarkeit der Beschichtung zu verbessern. Dabei wird eine Phosphatbeschichtung auf die Oberfläche aufgetragen, die eine chemische Verbindung mit dem Metall eingeht und eine gute Basis für die Pulverbeschichtung bildet.
- Spülung und Trocknung: Nach der Vorbehandlung wird das Werkstück gründlich gespült, um Rückstände von Reinigungsmitteln oder Chemikalien zu entfernen, und anschließend getrocknet, um sicherzustellen, dass die Oberfläche sauber und trocken ist, bevor die Beschichtung aufgetragen wird.
Die Pulverbeschichtungsvorbehandlung ist ein kritischer Schritt, um die Qualität und Leistung der Pulverbeschichtung zu maximieren. Durch eine sorgfältige und effektive Vorbehandlung kann die Haftung und Haltbarkeit der Beschichtung verbessert werden, was zu hochwertigen und langlebigen Beschichtungen führt.
Pulverbeschichtungssystem
Ein Pulverbeschichtungssystem ist eine komplexe Einrichtung, die speziell für die Durchführung des Pulverbeschichtungsprozesses konzipiert ist. Es besteht aus einer Vielzahl von Komponenten, die zusammenarbeiten, um Pulverlack auf Werkstücke aufzutragen und eine dauerhafte Beschichtung zu erzeugen. Hier sind einige Schlüsselaspekte eines Pulverbeschichtungssystems:
- Pulverbeschichtungskabine: Die Pulverbeschichtungskabine ist der zentrale Arbeitsbereich des Systems, in dem das Pulverlackmaterial auf die Werkstücke aufgetragen wird. Sie ist mit Absaug- und Filtervorrichtungen ausgestattet, um Pulvernebel zu erfassen und zu recyceln und die Umgebungsluft sauber zu halten.
- Pulverbeschichtungspistolen: Die Pulverbeschichtungspistolen sind die Werkzeuge, die verwendet werden, um das Pulverlackmaterial elektrostatisch aufzuladen und auf die Werkstückoberfläche zu sprühen. Sie sind in der Lage, das Pulver gleichmäßig zu verteilen und eine konsistente Beschichtung zu erzeugen.
- Pulverbeschichtungsofen: Der Pulverbeschichtungsofen ist ein beheizter Ofen, der dazu dient, das aufgetragene Pulverlackmaterial zu schmelzen und zu härten, um eine dauerhafte Beschichtung zu erzeugen. Die Temperatur und die Aushärtungszeit im Ofen werden entsprechend den Anforderungen des Beschichtungsmaterials und der Werkstücke eingestellt.
- Vorbehandlungseinrichtungen: Vorbehandlungseinrichtungen werden verwendet, um die Werkstückoberfläche vor der Beschichtung zu reinigen und vorzubereiten. Dies kann die Entfettung, Entrostung, Phosphatierung und andere Prozesse umfassen, um sicherzustellen, dass die Beschichtung eine gute Haftung hat und dauerhaft ist.
- Pulverrückgewinnungssystem: Das Pulverrückgewinnungssystem sammelt überschüssiges Pulver während des Beschichtungsprozesses und ermöglicht seine Wiederverwendung. Dies trägt zur Reduzierung von Abfall und Kosten bei und optimiert die Effizienz des Beschichtungsprozesses.
- Steuerungs- und Überwachungssysteme: Pulverbeschichtungssysteme sind mit Steuerungs- und Überwachungssystemen ausgestattet, die die verschiedenen Prozessparameter überwachen und steuern. Dies umfasst die Überwachung der Ofentemperatur, Sprühparameter, Luftströmung, Pulverrückgewinnung und anderen wichtigen Prozessvariablen.
Ein gut ausgelegtes und gepflegtes Pulverbeschichtungssystem ist entscheidend für die effiziente und zuverlässige Durchführung von Beschichtungsprojekten. Durch die richtige Auswahl, Installation und Wartung der Ausrüstung können Betriebe hochwertige Beschichtungen erzeugen, die den Anforderungen ihrer Kunden entsprechen und eine lange Lebensdauer haben.
Pulverbeschichtungsqualitätssicherung
Die Qualitätssicherung bei der Pulverbeschichtung ist ein entscheidender Prozess, der sicherstellt, dass die hergestellten Beschichtungen den erforderlichen Standards und Spezifikationen entsprechen. Eine effektive Qualitätssicherung hilft dabei, Fehler zu minimieren, die Produktionskosten zu senken und die Kundenzufriedenheit zu erhöhen. Hier sind einige Schlüsselaspekte der Qualitätssicherung bei der Pulverbeschichtung:
- Prozesskontrolle: Die Prozesskontrolle beinhaltet die Überwachung und Steuerung der verschiedenen Prozessparameter während des Beschichtungsprozesses. Dies umfasst die Überwachung der Pulverbeschichtungspistolen, der Sprühparameter, der Ofentemperatur, der Luftströmung, der Pulverrückgewinnung und anderer relevanter Parameter, um sicherzustellen, dass die Beschichtung gemäß den Spezifikationen erfolgt.
- Inspektion und Prüfung: Die Inspektion und Prüfung der beschichteten Werkstücke ist ein wichtiger Schritt, um die Qualität der Beschichtung zu überprüfen und sicherzustellen, dass sie den Anforderungen entspricht. Dies umfasst visuelle Inspektionen, Schichtdickenmessungen, Haftprüfungen, Farbprüfungen, Oberflächenprüfungen und andere Qualitätsprüfungen gemäß den Kundenspezifikationen und Branchenstandards.
- Qualitätskontrollverfahren: Qualitätskontrollverfahren sind systematische Methoden und Protokolle, die zur Überprüfung und Sicherstellung der Qualität der Pulverbeschichtung eingesetzt werden. Dies kann die Entwicklung von Prüfplänen, Prüfverfahren, Prüfmitteln, Qualitätsaufzeichnungen und anderen Dokumentationen umfassen, um die Einhaltung der Qualitätsstandards sicherzustellen.
- Schulung und Qualifikation: Die Schulung und Qualifikation von Mitarbeitern ist entscheidend für die Qualitätssicherung bei der Pulverbeschichtung. Durch Schulungen in den Bereichen Prozesskontrolle, Inspektionstechniken, Qualitätskontrollverfahren, Sicherheit und anderen relevanten Themen können Mitarbeiter dazu befähigt werden, ihre Aufgaben effektiv auszuführen und zur Qualitätssicherung beizutragen.
- Fehleranalyse und -behebung: Die Fehleranalyse und -behebung ist ein wichtiger Aspekt der Qualitätssicherung, um wiederkehrende Probleme zu identifizieren, ihre Ursachen zu verstehen und geeignete Maßnahmen zur Fehlerbehebung zu ergreifen. Dies umfasst die Analyse von Beschichtungsfehlern, die Identifizierung von Ursachen, die Implementierung von Korrekturmaßnahmen und die Überwachung der Wirksamkeit dieser Maßnahmen.
Durch die Implementierung eines umfassenden Qualitätssicherungssystems können Betriebe die Qualität ihrer Pulverbeschichtungen sicherstellen, die Kundenzufriedenheit erhöhen und langfristigen Erfolg sicherstellen. Eine kontinuierliche Verbesserung der Qualitätssicherungsprozesse ermöglicht es Betrieben, effizienter zu arbeiten, Kosten zu senken und ihre Wettbewerbsfähigkeit zu stärken.
Pulverbeschichtungsauftrag
Ein Pulverbeschichtungsauftrag bezieht sich auf den Prozess, bei dem ein Unternehmen oder eine Einrichtung den Dienstleister beauftragt, Pulverbeschichtungsarbeiten an Werkstücken oder Bauteilen durchzuführen. Dieser Auftrag kann verschiedene Schritte umfassen, von der Vorbereitung der Werkstückoberfläche bis zur Lieferung der fertigen beschichteten Teile. Hier sind einige Schlüsselaspekte eines Pulverbeschichtungsauftrags:
- Anfrage und Angebot: Der Auftraggeber (Kunde) sendet eine Anfrage an den Pulverbeschichtungsdienstleister, die Angaben zu den zu beschichtenden Teilen, den gewünschten Spezifikationen, Mengen und Lieferterminen enthält. Der Dienstleister erstellt daraufhin ein Angebot mit den geschätzten Kosten und Bedingungen für die Durchführung des Auftrags.
- Auftragserteilung: Nachdem das Angebot genehmigt wurde, erfolgt die formelle Auftragserteilung durch den Kunden an den Dienstleister. Dies kann durch Unterzeichnung eines Vertrags oder einer Auftragsbestätigung erfolgen, in der die spezifischen Details des Auftrags festgehalten werden, einschließlich der technischen Anforderungen, der Lieferbedingungen und der Zahlungsbedingungen.
- Werkstückvorbereitung: Vor dem Beschichtungsprozess müssen die Werkstücke gründlich gereinigt und vorbereitet werden, um eine gute Haftung und Qualität der Beschichtung zu gewährleisten. Dies kann die Entfettung, Entrostung, Phosphatierung und andere Vorbehandlungsschritte umfassen, je nach den Anforderungen des Kunden und der Art der Werkstücke.
- Beschichtungsprozess: Nach der Vorbereitung der Werkstücke werden sie in die Pulverbeschichtungsanlage gebracht, wo das Pulverlackmaterial auf die Oberfläche aufgetragen wird. Dies erfolgt in der Regel durch elektrostatisches Sprühen, wobei die Beschichtung anschließend im Aushärtungsofen erhitzt wird, um eine dauerhafte Beschichtung zu erzeugen.
- Qualitätskontrolle: Während des Beschichtungsprozesses werden die beschichteten Teile regelmäßig auf Qualität und Konformität mit den Spezifikationen überprüft. Dies umfasst visuelle Inspektionen, Schichtdickenmessungen, Haftprüfungen und andere Qualitätsprüfungen, um sicherzustellen, dass die Beschichtung den Anforderungen entspricht.
- Verpackung und Lieferung: Nach Abschluss des Beschichtungsprozesses werden die fertigen Teile sorgfältig verpackt und für den Versand vorbereitet. Dies kann die Verwendung von Schutzverpackungen, Etikettierung und Dokumentation umfassen, bevor die Teile an den Kunden geliefert werden.
Ein effizienter Pulverbeschichtungsauftrag erfordert eine enge Zusammenarbeit zwischen dem Kunden und dem Dienstleister sowie eine sorgfältige Planung, Durchführung und Qualitätskontrolle während des gesamten Prozesses. Durch klare Kommunikation, Einhaltung von Terminen und Qualitätsstandards kann ein erfolgreicher Auftrag abgeschlossen werden, der die Erwartungen des Kunden erfüllt.
Pulverbeschichtungsvorteile
Die Pulverbeschichtung bietet eine Vielzahl von Vorteilen gegenüber anderen Beschichtungsverfahren, die sie zu einer beliebten Wahl in verschiedenen Branchen und Anwendungen machen. Hier sind einige der wichtigsten Vorteile der Pulverbeschichtung:
- Umweltfreundlichkeit: Pulverbeschichtungen enthalten im Gegensatz zu herkömmlichen Lacken keine flüchtigen organischen Verbindungen (VOCs), die schädlich für die Umwelt und die Gesundheit sein können. Sie tragen zur Reduzierung von Luftverschmutzung und Umweltbelastung bei und entsprechen den strengen Umweltvorschriften.
- Langlebigkeit und Haltbarkeit: Pulverbeschichtungen bieten eine dauerhafte und robuste Oberflächenbeschichtung, die beständig gegenüber Kratzern, Abrieb, Chemikalien, Korrosion, UV-Strahlung und Witterungseinflüssen ist. Sie bieten eine lange Lebensdauer und erfordern weniger häufige Nachbesserungen oder Wartung.
- Vielseitigkeit: Pulverbeschichtungen sind in einer breiten Palette von Farben, Effekten und Oberflächenstrukturen erhältlich, darunter glänzende, matte, strukturierte, metallische und perlmuttfarbene Oberflächen. Dies ermöglicht eine individuelle Gestaltung und Anpassung an verschiedene Designanforderungen und Ästhetiken.
- Gleichmäßige Beschichtung: Durch elektrostatische Aufladung der Pulverpartikel während des Sprühvorgangs wird eine gleichmäßige Verteilung und Haftung des Beschichtungsmaterials auf der Werkstückoberfläche erreicht. Dies führt zu einer glatten und konsistenten Beschichtung ohne Laufnasen, Tropfen oder Pinselstriche.
- Wirtschaftlichkeit: Pulverbeschichtungen können effizient aufgetragen werden, wodurch Material- und Arbeitskosten gesenkt werden. Da überschüssiges Pulver recycelt werden kann und weniger Abfall entsteht, trägt dies auch zur Kostenreduzierung bei. Darüber hinaus entfallen oft teure Lösungsmittelrückgewinnungs- und Entsorgungssysteme.
- Schnelle Aushärtung: Pulverbeschichtungen können in kurzer Zeit bei niedrigen bis mittleren Temperaturen ausgehärtet werden, was zu schnelleren Produktionszyklen und höherer Effizienz führt. Dies ermöglicht eine schnellere Bearbeitung von Teilen und reduziert die Durchlaufzeiten.
Insgesamt bietet die Pulverbeschichtung eine Reihe von bedeutenden Vorteilen, darunter Umweltfreundlichkeit, Langlebigkeit, Vielseitigkeit, Wirtschaftlichkeit und schnelle Aushärtung. Diese Vorteile machen sie zu einer attraktiven Wahl für eine Vielzahl von Anwendungen in Bereichen wie Automobilindustrie, Architektur, Möbelherstellung, Metallverarbeitung und mehr.
Pulverbeschichtungsfehler
Obwohl die Pulverbeschichtung viele Vorteile bietet, können auch Fehler auftreten, die die Qualität der Beschichtung beeinträchtigen können. Hier sind einige häufige Pulverbeschichtungsfehler und mögliche Ursachen:
- Blasenbildung oder Lufteinschlüsse: Blasenbildung oder Lufteinschlüsse in der Beschichtung können durch Feuchtigkeit, Öl oder Verunreinigungen auf der Werkstückoberfläche verursacht werden. Auch eine zu hohe Ofentemperatur während des Aushärtungsprozesses kann dazu führen.
- Farbabweichungen oder Farbunregelmäßigkeiten: Farbabweichungen oder Farbunregelmäßigkeiten können durch ungleichmäßiges Mischen des Pulverbeschichtungspulvers, unzureichende Vorbehandlung der Werkstückoberfläche oder Probleme mit dem Beschichtungsprozess selbst verursacht werden.
- Haftungsprobleme: Haftungsprobleme treten auf, wenn die Beschichtung nicht richtig auf der Werkstückoberfläche haftet. Dies kann durch unzureichende Vorbehandlung, schlechte Haftgrundierung oder unsachgemäße Aushärtungsbedingungen verursacht werden.
- Schichtdickenprobleme: Schwankungen in der Schichtdicke können durch ungleichmäßiges Sprühen, falsche Einstellungen der Pulverbeschichtungspistole oder unzureichende Vorbehandlung der Werkstückoberfläche verursacht werden. Dies kann zu unerwünschten Variationen in der Farbe, Textur und Leistung der Beschichtung führen.
- Kraterbildung: Kraterbildung tritt auf, wenn sich kleine Löcher oder Vertiefungen in der Beschichtung bilden. Dies kann durch Verunreinigungen auf der Werkstückoberfläche, ölige Substanzen oder unzureichende Entgasung des Beschichtungsmaterials verursacht werden.
- Orange-Schalen-Effekt: Der Orange-Schalen-Effekt tritt auf, wenn die Beschichtung eine unebene oder texturierte Oberfläche aufweist, die der Oberfläche einer Orange ähnelt. Dies kann durch zu niedrige Viskosität des Pulverbeschichtungspulvers, zu hohe Sprühdistanz oder falsche Ofentemperaturen verursacht werden.
Um Pulverbeschichtungsfehler zu vermeiden, ist es wichtig, sorgfältig auf alle Aspekte des Beschichtungsprozesses zu achten, einschließlich der Werkstückvorbereitung, der Materialauswahl, der Anwendungstechniken und der Aushärtungsbedingungen. Durch eine gründliche Qualitätskontrolle und kontinuierliche Prozessverbesserung können potenzielle Fehler frühzeitig erkannt und behoben werden, um hochwertige und zuverlässige Beschichtungen sicherzustellen.
Pulverbeschichtungsfarben
Pulverbeschichtungsfarben sind spezielle Beschichtungsmaterialien in Pulverform, die für die Anwendung im Pulverbeschichtungsprozess entwickelt wurden. Sie bieten eine breite Palette von Farben, Effekten und Oberflächenstrukturen für verschiedene Anwendungen und Branchen. Hier sind einige wichtige Aspekte von Pulverbeschichtungsfarben:
- Farbauswahl: Pulverbeschichtungsfarben sind in einer Vielzahl von Farbtönen erhältlich, darunter Standardfarben wie Weiß, Schwarz, Grau und verschiedene RAL-Farben. Darüber hinaus bieten sie eine breite Palette von Spezialfarben, einschließlich Metallics, Perlmuttfarben, Neonfarben und kundenspezifischen Farbtönen.
- Effekte: Pulverbeschichtungsfarben können verschiedene Effekte erzeugen, um ästhetische und funktionale Anforderungen zu erfüllen. Dazu gehören Glanz-, Matt-, Struktur-, Hammerschlag-, Antik- und Glittereffekte, die je nach Anwendung und Designpräferenzen ausgewählt werden können.
- Oberflächenstrukturen: Pulverbeschichtungsfarben können verschiedene Oberflächenstrukturen erzeugen, von glatten und glänzenden Oberflächen bis hin zu strukturierten und texturierten Oberflächen. Diese Strukturen können durch die Auswahl des richtigen Pulverbeschichtungspulvers und die Anpassung der Sprühparameter kontrolliert werden.
- UV-Beständigkeit: Hochwertige Pulverbeschichtungsfarben sind UV-beständig und bieten Schutz vor Verblassen, Verfärbungen und Verschlechterung durch Sonneneinstrahlung. Dies ist besonders wichtig für Anwendungen im Freien oder in Umgebungen mit intensiver Sonneneinstrahlung.
- Chemische Beständigkeit: Pulverbeschichtungsfarben können auch chemisch beständig sein und Schutz vor Verschleiß, Korrosion, Chemikalien und anderen Umwelteinflüssen bieten. Dies macht sie ideal für Anwendungen in industriellen Umgebungen, Chemieanlagen, Automobil- und Schiffsbau und anderen anspruchsvollen Anwendungen.
- Umweltverträglichkeit: Pulverbeschichtungsfarben enthalten keine flüchtigen organischen Verbindungen (VOCs) oder andere umweltschädliche Substanzen, die die Luftqualität beeinträchtigen könnten. Sie sind umweltfreundlich und entsprechen den strengen Umweltschutzvorschriften und -standards.
Die Auswahl der richtigen Pulverbeschichtungsfarbe hängt von den spezifischen Anforderungen der Anwendung, den ästhetischen Präferenzen des Kunden und den Leistungsanforderungen des beschichteten Teils ab. Durch die Auswahl hochwertiger Farben und die ordnungsgemäße Anwendung können Betriebe hochwertige und langlebige Beschichtungen erzeugen, die den Anforderungen ihrer Kunden entsprechen.
Pulverbeschichtungsvorbereitung
Die Pulverbeschichtungsvorbereitung ist ein kritischer Schritt im Pulverbeschichtungsprozess, der darauf abzielt, die Werkstückoberfläche optimal auf die Beschichtung vorzubereiten. Eine gründliche Vorbereitung ist entscheidend für die Haftung, Haltbarkeit und Qualität der Pulverbeschichtung. Hier sind einige wichtige Aspekte der Pulverbeschichtungsvorbereitung:
- Reinigung: Die Reinigung der Werkstückoberfläche ist der erste und wichtigste Schritt der Vorbereitung. Alle Verunreinigungen wie Fett, Öl, Schmutz, Rost, Korrosion und alte Beschichtungen müssen entfernt werden, um eine gute Haftung der Pulverbeschichtung sicherzustellen. Dies kann durch Waschen, Entfetten, chemische Reinigungsmethoden oder mechanische Reinigung erfolgen.
- Entfettung: Entfettung ist ein spezieller Reinigungsschritt, um Fette, Öle und andere organische Verunreinigungen von der Werkstückoberfläche zu entfernen. Dies kann durch Tauchen in Entfettungslösungen, Sprühen von Entfettungsmitteln oder andere Reinigungsmethoden erfolgen, um eine saubere Oberfläche für die Beschichtung sicherzustellen.
- Entrostung: Wenn das Werkstück Rost oder Korrosion aufweist, ist es notwendig, die Oberfläche zu entrosten, um eine gleichmäßige und haftende Beschichtung zu gewährleisten. Dies kann durch Sandstrahlen, Schleifen, Bürsten oder chemische Entrostungsverfahren erfolgen, je nach dem Grad der Korrosion und den Anforderungen der Anwendung.
- Phosphatierung: Die Phosphatierung ist ein wichtiger Schritt, um die Oberfläche zu passivieren und die Haftung und Haltbarkeit der Beschichtung zu verbessern. Dabei wird eine Phosphatbeschichtung auf die Oberfläche aufgetragen, die eine chemische Verbindung mit dem Metall eingeht und eine gute Basis für die Pulverbeschichtung bildet.
- Trocknung: Nach der Reinigung und Vorbereitung der Werkstückoberfläche ist es wichtig, dass diese gründlich getrocknet wird, bevor die Beschichtung aufgetragen wird. Feuchtigkeit auf der Oberfläche kann die Haftung und Qualität der Beschichtung beeinträchtigen, daher ist eine gründliche Trocknung erforderlich.
Eine sorgfältige und gründliche Pulverbeschichtungsvorbereitung ist entscheidend für den Erfolg des Beschichtungsprozesses und die Qualität der Endprodukte. Durch die richtige Reinigung, Entfettung, Entrostung, Phosphatierung und Trocknung der Werkstückoberfläche können Betriebe hochwertige Beschichtungen erzeugen, die den Anforderungen ihrer Kunden entsprechen und eine lange Lebensdauer haben.
Pulverbeschichtungsprozess
Der Pulverbeschichtungsprozess ist ein Verfahren zur Beschichtung von Werkstücken oder Bauteilen mit einem Pulverlackmaterial, um eine dauerhafte, attraktive und schützende Oberfläche zu erzeugen. Der Prozess umfasst mehrere Schritte, die sorgfältig durchgeführt werden müssen, um eine hochwertige Beschichtung zu gewährleisten. Hier sind die wichtigsten Schritte des Pulverbeschichtungsprozesses:
- Werkstückvorbereitung: Der Prozess beginnt mit der gründlichen Reinigung und Vorbereitung der Werkstückoberfläche. Dies umfasst die Entfernung von Schmutz, Fett, Ölen, Rost, Korrosion und anderen Verunreinigungen, um eine gute Haftung der Beschichtung zu gewährleisten. Je nach Bedarf können auch Entfettungs-, Entrostungs- und Phosphatierungsverfahren angewendet werden.
- Pulverauftrag: Nach der Vorbereitung wird das Pulverlackmaterial auf die Werkstückoberfläche aufgetragen. Dies erfolgt in der Regel durch elektrostatisches Sprühen, bei dem das Pulver elektrostatisch aufgeladen und dann auf das geerdete Werkstück gesprüht wird. Dies ermöglicht eine gleichmäßige Verteilung des Pulvers und eine gute Haftung auf der Oberfläche.
- Trocknung: Nach dem Auftragen des Pulvers wird das Werkstück in einen Ofen oder Trockner gebracht, um das Pulver zu schmelzen und zu einer gleichmäßigen Beschichtung zu verschmelzen. Die Trocknungstemperatur und -zeit werden entsprechend den Anforderungen des verwendeten Pulverlackmaterials und der Werkstücke eingestellt.
- Aushärtung: Nach dem Schmelzen des Pulvers im Ofen wird das Werkstück weiter erhitzt, um eine vollständige Aushärtung der Beschichtung zu gewährleisten. Dies verbessert die Haltbarkeit, Beständigkeit und mechanischen Eigenschaften der Beschichtung und ermöglicht es, dass sie den Anforderungen verschiedener Anwendungen gerecht wird.
- Qualitätskontrolle: Während des gesamten Prozesses werden die beschichteten Werkstücke regelmäßig auf Qualität und Konformität mit den Spezifikationen überprüft. Dies umfasst visuelle Inspektionen, Schichtdickenmessungen, Haftprüfungen und andere Qualitätsprüfungen, um sicherzustellen, dass die Beschichtung den Anforderungen entspricht.
- Verpackung und Lieferung: Nach Abschluss des Beschichtungsprozesses werden die fertigen Teile sorgfältig verpackt und für den Versand vorbereitet. Dies kann die Verwendung von Schutzverpackungen, Etikettierung und Dokumentation umfassen, bevor die Teile an den Kunden geliefert werden.
Der Pulverbeschichtungsprozess ist ein effizientes und umweltfreundliches Verfahren zur Beschichtung von Werkstücken mit einer Vielzahl von Farben und Effekten. Durch die sorgfältige Durchführung jedes Schrittes können Betriebe hochwertige Beschichtungen erzeugen, die den Anforderungen ihrer Kunden entsprechen und eine lange Lebensdauer haben.
Pulverbeschichtungsanlagenwartung
Die Wartung von Pulverbeschichtungsanlagen ist entscheidend, um einen reibungslosen Betrieb, eine hohe Produktqualität und eine lange Lebensdauer der Anlagen sicherzustellen. Eine regelmäßige Wartung hilft dabei, potenzielle Probleme frühzeitig zu erkennen, Ausfallzeiten zu minimieren und die Effizienz der Anlage zu optimieren. Hier sind einige wichtige Aspekte der Pulverbeschichtungsanlagenwartung:
- Reinigung: Regelmäßige Reinigung der Pulverbeschichtungskabine, Pulverrückgewinnungssysteme, Sprühpistolen und anderen Komponenten der Anlage, um Pulverablagerungen, Verunreinigungen und Rückstände zu entfernen. Dies trägt zur Aufrechterhaltung einer gleichmäßigen Beschichtungsqualität und einer effizienten Betriebsweise bei.
- Überprüfung der Sprühpistolen: Überprüfen Sie regelmäßig die Sprühpistolen auf Abnutzung, Beschädigungen oder Verstopfungen und reinigen Sie sie gegebenenfalls gründlich. Stellen Sie sicher, dass die Pistolen ordnungsgemäß funktionieren und eine gleichmäßige Pulververteilung gewährleisten.
- Filterwechsel: Wechseln Sie regelmäßig die Filter in der Pulverbeschichtungskabine und im Pulverrückgewinnungssystem, um eine effektive Abscheidung von Pulvernebel zu gewährleisten und die Luftqualität in der Anlage zu verbessern.
- Überprüfung der Ofenleistung: Überprüfen Sie regelmäßig die Leistung des Aushärtungsofens, einschließlich der Temperatur- und Luftstromsteuerung, um sicherzustellen, dass die Beschichtungen ordnungsgemäß aushärten und die erforderlichen Qualitätsstandards erfüllen.
- Inspektion der Förderbänder und Aufhängesysteme: Überprüfen Sie die Förderbänder und Aufhängesysteme auf Verschleiß, Beschädigungen oder Verformungen und führen Sie bei Bedarf Wartungs- oder Reparaturarbeiten durch, um einen reibungslosen Materialtransport und eine gleichmäßige Beschichtung sicherzustellen.
- Schulung des Bedienpersonals: Schulen Sie das Bedienpersonal regelmäßig in der ordnungsgemäßen Bedienung, Wartung und Sicherheit der Pulverbeschichtungsanlage, um Unfälle zu vermeiden und die Effizienz des Betriebs zu steigern.
Durch eine sorgfältige und regelmäßige Wartung können Betriebe die Lebensdauer ihrer Pulverbeschichtungsanlagen verlängern, die Betriebskosten senken und die Qualität ihrer Beschichtungen verbessern. Eine gut gewartete Anlage trägt auch zur Sicherheit der Mitarbeiter und zur Einhaltung von Umweltvorschriften bei.
Pulverbeschichtungsvorbehandlung
Die Pulverbeschichtungsvorbehandlung ist ein wichtiger Schritt im Pulverbeschichtungsprozess, der darauf abzielt, die Werkstückoberfläche optimal auf die Beschichtung vorzubereiten. Eine gründliche Vorbehandlung ist entscheidend für die Haftung, Haltbarkeit und Qualität der Pulverbeschichtung. Hier sind einige wichtige Aspekte der Pulverbeschichtungsvorbehandlung:
- Reinigung: Die Reinigung der Werkstückoberfläche ist der erste Schritt der Vorbehandlung. Alle Verunreinigungen wie Fett, Öl, Schmutz, Rost, Korrosion und alte Beschichtungen müssen entfernt werden, um eine gute Haftung der Beschichtung zu gewährleisten. Dies kann durch Waschen, Entfetten, chemische Reinigungsmethoden oder mechanische Reinigung erfolgen.
- Entfettung: Entfettung ist ein spezieller Reinigungsschritt, um Fette, Öle und andere organische Verunreinigungen von der Werkstückoberfläche zu entfernen. Dies kann durch Tauchen in Entfettungslösungen, Sprühen von Entfettungsmitteln oder andere Reinigungsmethoden erfolgen, um eine saubere Oberfläche für die Beschichtung sicherzustellen.
- Entrostung: Wenn das Werkstück Rost oder Korrosion aufweist, ist es notwendig, die Oberfläche zu entrosten, um eine gleichmäßige und haftende Beschichtung zu gewährleisten. Dies kann durch Sandstrahlen, Schleifen, Bürsten oder chemische Entrostungsverfahren erfolgen, je nach dem Grad der Korrosion und den Anforderungen der Anwendung.
- Phosphatierung: Die Phosphatierung ist ein wichtiger Schritt, um die Oberfläche zu passivieren und die Haftung und Haltbarkeit der Beschichtung zu verbessern. Dabei wird eine Phosphatbeschichtung auf die Oberfläche aufgetragen, die eine chemische Verbindung mit dem Metall eingeht und eine gute Basis für die Pulverbeschichtung bildet.
- Chromatierung: In einigen Fällen kann eine Chromatierung der Werkstückoberfläche durchgeführt werden, um die Haftung der Beschichtung zu verbessern und die Korrosionsbeständigkeit zu erhöhen. Dieser Prozess beinhaltet die Bildung einer dünnen Chromatierschicht auf der Oberfläche, die als Grundierung für die Pulverbeschichtung dient.
Eine sorgfältige Pulverbeschichtungsvorbehandlung ist entscheidend für den Erfolg des Beschichtungsprozesses und die Qualität der Endprodukte. Durch die richtige Reinigung, Entfettung, Entrostung, Phosphatierung und gegebenenfalls Chromatierung der Werkstückoberfläche können Betriebe hochwertige Beschichtungen erzeugen, die den Anforderungen ihrer Kunden entsprechen und eine lange Lebensdauer haben.
Pulverbeschichtungsqualitätssicherung
Die Qualitätssicherung bei der Pulverbeschichtung ist entscheidend, um sicherzustellen, dass die beschichteten Teile die erforderlichen Standards hinsichtlich Aussehen, Haltbarkeit, Leistung und Funktion erfüllen. Eine effektive Qualitätssicherung umfasst mehrere Maßnahmen, die während des gesamten Beschichtungsprozesses durchgeführt werden. Hier sind einige wichtige Aspekte der Pulverbeschichtungsqualitätssicherung:
- Qualitätskontrolle während der Vorbereitung: Überprüfen Sie die Werkstücke vor dem Beschichtungsprozess auf Verunreinigungen, Beschädigungen oder Unregelmäßigkeiten und stellen Sie sicher, dass die Oberfläche gründlich gereinigt und vorbereitet wurde, um eine gute Haftung der Beschichtung zu gewährleisten.
- Überwachung des Pulverauftrags: Überwachen Sie den Pulverauftrag während des Beschichtungsprozesses, um sicherzustellen, dass eine gleichmäßige und konsistente Beschichtung aufgetragen wird. Dies kann durch visuelle Inspektionen, Schichtdickenmessungen und Haftprüfungen erfolgen.
- Überprüfung der Ofenleistung: Überprüfen Sie regelmäßig die Leistung des Aushärtungsofens, einschließlich der Temperatur- und Zeitsteuerung, um sicherzustellen, dass die Beschichtungen ordnungsgemäß aushärten und die erforderlichen Qualitätsstandards erfüllen.
- Qualitätskontrolle nach dem Beschichtungsprozess: Überprüfen Sie die fertigen beschichteten Teile auf Aussehen, Farbübereinstimmung, Oberflächenstruktur, Schichtdicke und Haftung. Führen Sie gegebenenfalls zusätzliche Qualitätsprüfungen durch, um sicherzustellen, dass die Teile den Spezifikationen entsprechen.
- Rückverfolgbarkeit und Dokumentation: Verfolgen Sie die einzelnen Chargen von beschichteten Teilen und dokumentieren Sie alle relevanten Prozessparameter, Inspektionsergebnisse und Qualitätsprüfungen. Dies erleichtert die Identifizierung von Problemen, die Rückverfolgbarkeit von Produkten und die kontinuierliche Verbesserung des Prozesses.
- Schulung des Personals: Schulen Sie das Bedienpersonal regelmäßig in den Verfahren zur Qualitätssicherung und Sensibilisierung für die Bedeutung von Qualität und Kundenanforderungen. Schulungen können dazu beitragen, die Qualitätsstandards zu verbessern und die Fehlerquote zu reduzieren.
Durch eine gründliche Qualitätssicherung können Betriebe hochwertige Pulverbeschichtungen erzeugen, die den Anforderungen ihrer Kunden entsprechen und eine hohe Kundenzufriedenheit gewährleisten. Eine kontinuierliche Überwachung, Bewertung und Verbesserung des Qualitätssicherungssystems ist entscheidend für den langfristigen Erfolg des Unternehmens in der Pulverbeschichtungsbranche.
Pulverbeschichtungstrends
Die Pulverbeschichtungsbranche unterliegt ständig neuen Trends und Entwicklungen, die die Art und Weise beeinflussen, wie Beschichtungen angewendet, gestaltet und verwendet werden. Hier sind einige aktuelle Trends in der Pulverbeschichtungsindustrie:
- Nachhaltigkeit und Umweltfreundlichkeit: Ein zunehmender Trend in der Pulverbeschichtungsbranche ist die verstärkte Nachfrage nach umweltfreundlichen Beschichtungslösungen. Hersteller setzen vermehrt auf pulverbasierte Beschichtungssysteme, die keine flüchtigen organischen Verbindungen (VOCs) enthalten und weniger Abfall und Emissionen verursachen.
- Hochleistungsbereich: Es gibt eine steigende Nachfrage nach hochleistungsfähigen Pulverbeschichtungen, die den Anforderungen anspruchsvoller Anwendungen in Branchen wie Automobil, Architektur, Industrie und maritimen Anwendungen gerecht werden. Dies umfasst Beschichtungen mit verbesserten mechanischen Eigenschaften, Korrosionsbeständigkeit, Witterungsbeständigkeit und Chemikalienbeständigkeit.
- Farb- und Oberflächenvielfalt: Die Pulverbeschichtungsbranche bietet eine immer größere Vielfalt an Farben, Effekten und Oberflächenstrukturen. Von metallischen und perlmutterartigen Effekten bis hin zu strukturierten und texturierten Oberflächen gibt es zahlreiche Möglichkeiten für individuelle Gestaltung und Designanpassung.
- Digitalisierung und Automatisierung: Die Einführung digitaler Technologien und automatisierter Prozesse in der Pulverbeschichtungsindustrie nimmt zu. Dies umfasst den Einsatz von Robotern und automatisierten Anlagen für den Pulverauftrag und die Aushärtung, sowie die Integration von Datenmanagement- und Überwachungssystemen zur Verbesserung der Produktionsleistung und Qualitätssicherung.
- Funktionsbeschichtungen: Neben ästhetischen Eigenschaften gewinnen auch funktionale Beschichtungen an Bedeutung. Dazu gehören Antihaftbeschichtungen, Wärmeisolierbeschichtungen, Gleitbeschichtungen, leitfähige Beschichtungen und antimikrobielle Beschichtungen, die spezifische Leistungsanforderungen erfüllen.
- Anpassung an neue Materialien: Mit der Entwicklung neuer Materialien wie Verbundwerkstoffen, Leichtmetallen und Glas gewinnt auch die Anpassung der Pulverbeschichtungstechnologie an diese Materialien an Bedeutung. Dies umfasst die Entwicklung spezifischer Vorbehandlungsverfahren und Beschichtungssysteme, um eine optimale Haftung und Leistung zu gewährleisten.
Diese Trends prägen die Weiterentwicklung und Innovation in der Pulverbeschichtungsbranche und beeinflussen die Art und Weise, wie Beschichtungen angewendet, entwickelt und verwendet werden. Unternehmen, die auf dem neuesten Stand der Technik bleiben und sich diesen Trends anpassen, können ihre Wettbewerbsfähigkeit stärken und neue Chancen für Wachstum und Differenzierung nutzen.
Pulverbeschichtungsrobotik
Die Integration von Robotik in den Pulverbeschichtungsprozess gewinnt zunehmend an Bedeutung und bietet eine Vielzahl von Vorteilen für Effizienz, Präzision und Produktqualität. Hier sind einige wichtige Aspekte der Pulverbeschichtungsrobotik:
- Automatisierter Pulverauftrag: Roboter werden häufig eingesetzt, um den Pulverauftrag auf Werkstücke zu automatisieren. Sie bieten eine präzise und gleichmäßige Pulververteilung, die eine konsistente Beschichtungsqualität gewährleistet und den Pulververbrauch optimiert.
- Programmierbare Bewegungen: Pulverbeschichtungsroboter sind programmierbar und können eine Vielzahl von Bewegungen und Beschichtungspfaden ausführen. Dies ermöglicht die Anpassung an komplexe Werkstückgeometrien und die Durchführung von Mehrschichtbeschichtungen mit hoher Präzision.
- Reduzierung von Ausschuss und Materialverlust: Durch die präzisen und kontrollierten Beschichtungsbewegungen können Pulverbeschichtungsroboter den Ausschuss reduzieren und den Materialverlust minimieren. Dies trägt zur Kosteneffizienz und Nachhaltigkeit des Beschichtungsprozesses bei.
- Flexibilität und Anpassungsfähigkeit: Pulverbeschichtungsroboter sind flexibel einsetzbar und können schnell zwischen verschiedenen Werkstücken und Beschichtungsaufgaben umgestellt werden. Dies ermöglicht eine effiziente Nutzung der Anlagenkapazität und eine schnelle Reaktion auf sich ändernde Produktionsanforderungen.
- Verbesserung der Arbeitsbedingungen: Die Automatisierung des Pulverbeschichtungsprozesses durch Roboter kann dazu beitragen, die Arbeitsbedingungen für die Mitarbeiter zu verbessern, indem sie sie von repetitiven und körperlich belastenden Aufgaben entlasten. Dies trägt zur Steigerung der Mitarbeiterzufriedenheit und -sicherheit bei.
- Qualitätskontrolle und Rückverfolgbarkeit: Pulverbeschichtungsroboter können mit Qualitätskontrollsystemen und Datenerfassungssystemen integriert werden, um den Beschichtungsprozess zu überwachen und Daten für die Rückverfolgbarkeit und Prozessoptimierung zu erfassen.
Die Integration von Robotik in den Pulverbeschichtungsprozess bietet eine Vielzahl von Vorteilen für Hersteller, darunter verbesserte Effizienz, Präzision, Flexibilität und Qualität. Unternehmen, die in Pulverbeschichtungsrobotik investieren, können ihre Wettbewerbsfähigkeit stärken, die Produktionsleistung steigern und neue Möglichkeiten für Wachstum und Differenzierung erschließen.
Pulverbeschichtungsanlagenoptimierung
Die Optimierung von Pulverbeschichtungsanlagen ist ein kontinuierlicher Prozess, der darauf abzielt, die Effizienz, Qualität und Wirtschaftlichkeit des Beschichtungsprozesses zu verbessern. Hier sind einige wichtige Aspekte der Pulverbeschichtungsanlagenoptimierung:
- Prozessanalyse: Führen Sie eine umfassende Analyse des bestehenden Beschichtungsprozesses durch, um Schwachstellen, Engpässe und Verbesserungspotenziale zu identifizieren. Dies kann die Bewertung der Anlagenauslastung, der Produktionsgeschwindigkeit, der Materialverluste, der Beschichtungsqualität und anderer Leistungsindikatoren umfassen.
- Effizienzsteigerung: Implementieren Sie Maßnahmen zur Steigerung der Anlageneffizienz, wie z. B. die Optimierung der Beschichtungsparameter, die Reduzierung von Stillstandszeiten, die Maximierung der Anlagenauslastung und die Optimierung der Materialnutzung. Dies kann dazu beitragen, die Produktionskosten zu senken und die Wettbewerbsfähigkeit zu verbessern.
- Qualitätsverbesserung: Implementieren Sie Qualitätskontrollmaßnahmen und Prozessverbesserungen, um die Qualität der beschichteten Teile zu verbessern. Dies umfasst die Überwachung und Optimierung der Beschichtungsparameter, die Implementierung von Qualitätsprüfungen und die Schulung des Bedienpersonals in den besten Praktiken zur Qualitätssicherung.
- Material- und Ressourceneffizienz: Implementieren Sie Maßnahmen zur Optimierung des Materialverbrauchs und der Ressourcennutzung in der Pulverbeschichtungsanlage. Dies kann die Reduzierung von Materialverschwendung, die Wiederverwendung und das Recycling von Materialien, die Optimierung des Energieverbrauchs und die Minimierung von Abfall und Emissionen umfassen.
- Automatisierung und Robotik: Erwägen Sie die Integration von Automatisierungs- und Robotiklösungen in den Beschichtungsprozess, um die Produktionsleistung zu steigern, die Arbeitsbedingungen zu verbessern und die Qualität der Beschichtungen zu erhöhen. Dies kann den Einsatz von Robotern für den Pulverauftrag, automatisierte Qualitätskontrollsysteme und die Implementierung von Datenmanagement- und Überwachungssystemen umfassen.
- Kontinuierliche Verbesserung: Implementieren Sie ein kontinuierliches Verbesserungsprogramm, um den Beschichtungsprozess kontinuierlich zu optimieren und zu verbessern. Dies umfasst die regelmäßige Überwachung und Bewertung der Leistungsindikatoren, die Identifizierung von Verbesserungsmöglichkeiten und die Implementierung von Maßnahmen zur Prozessoptimierung.
Durch die Optimierung von Pulverbeschichtungsanlagen können Betriebe ihre Produktionsleistung steigern, die Produktqualität verbessern und ihre Wettbewerbsfähigkeit stärken. Eine effiziente und hochwertige Beschichtungsanlage ermöglicht es Unternehmen, die Anforderungen ihrer Kunden zu erfüllen und langfristigen Erfolg in der Pulverbeschichtungsbranche zu sichern.