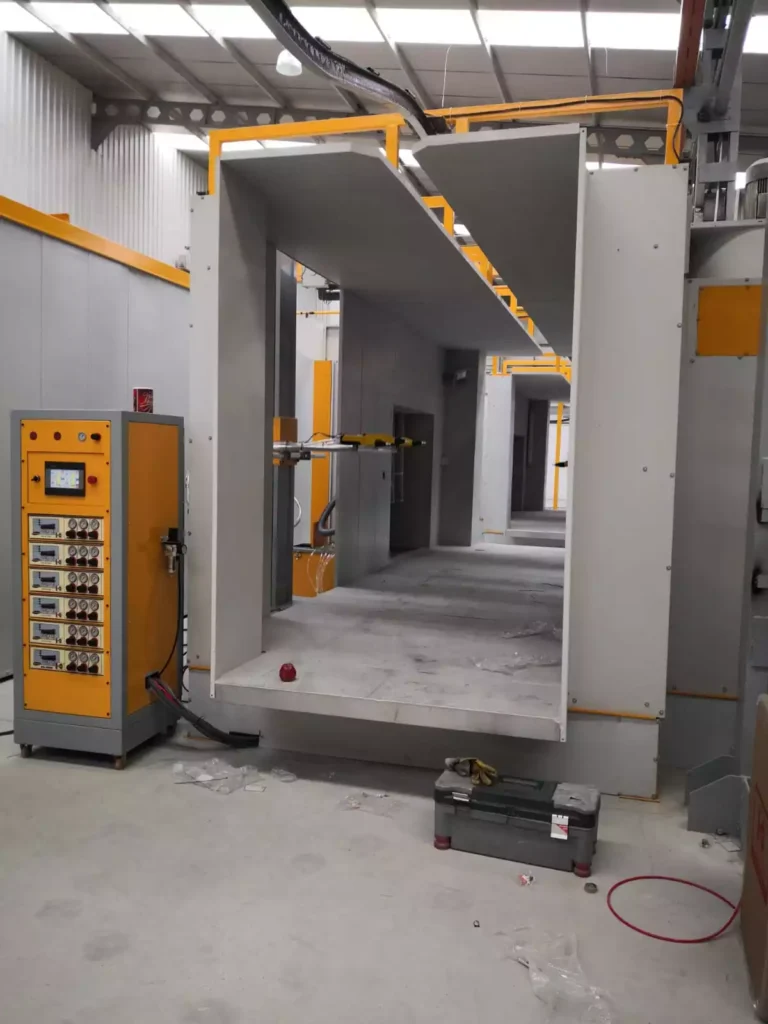
Unsere Schnellfarbwechsel Pulverbeschichtungskabine eignen sich dank ihrer robusten und pflegeleichten Bauart speziell für den Einsatz in einer rauen Arbeitsumgebung. Automatik-Kunststoffkabinen aus PVC werden heute überwiegend in modernen Pulverbeschichtungsanlagen verwendet.
PVC eignet sich sowohl wegen seiner mechanischen Eigenschaften (robust, reparierbar), als auch insbesondere durch seine elektrostatischen Eigenschaften für den Aufbau eines kompletten Systems
Die schnellfarbwechsel Pulverbeschichtungskabine arbeitet beidseitig mit 2 Hubgeräten, deren Arbeitshöhe entsprechend der Höhe der Werkstücke bestimmt werden kann. Automatische Pulverbeschichtungskabinen können aus verzinktem Blech, Edelstahl und auch PVC für schnelle Reinigungsoptionen hergestellt werden.
Die Innenluft wird nach dem Platzbedarf innerhalb der Kabine berechnet und die Umluft innerhalb der Kabine bestimmt auch die Zyklonleistung. Für weitere Informationen senden Sie bitte Ihre Anfrage an unsere E-Mail-Adresse
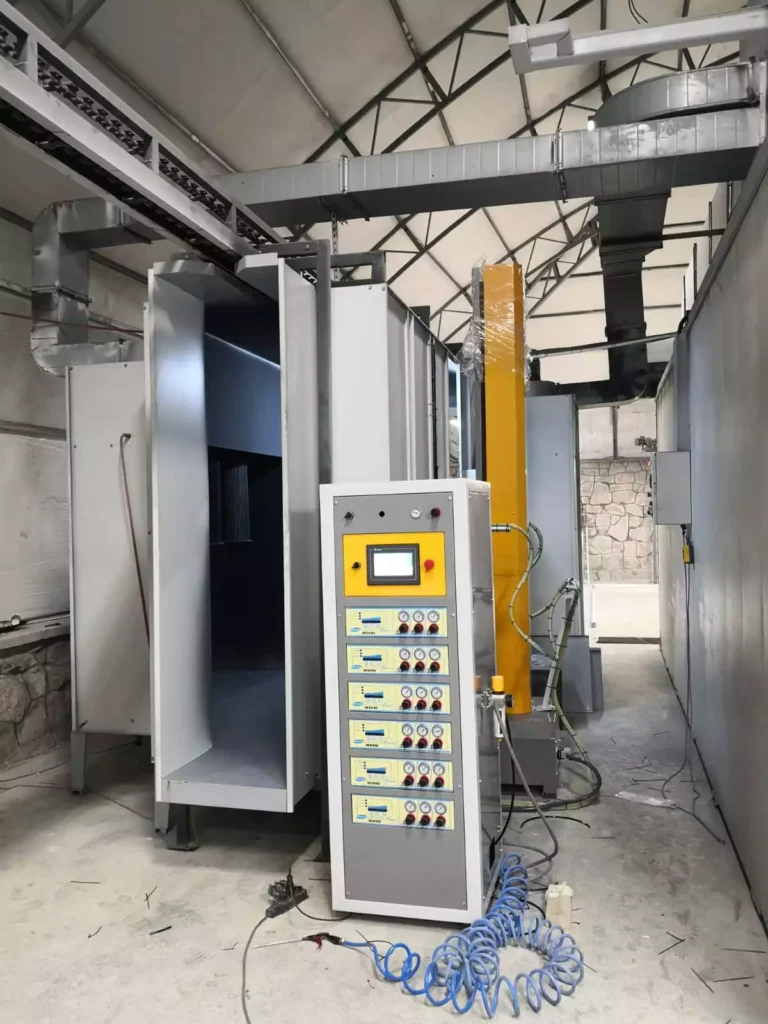
Der Schnellfarbwechsel ist eine der entscheidenden Innovationen in modernen Pulverbeschichtungsanlagen, insbesondere in automatisierten Pulverbeschichtungskabinen. Diese Technologie ermöglicht es, die Farbe der Beschichtung schnell und effizient zu wechseln, was die Produktivität und Flexibilität in der Produktion erheblich steigert. Besonders in Bereichen, in denen häufige Farbwechsel erforderlich sind, wie beispielsweise in der Automobilindustrie oder in Fertigungsprozessen, die unterschiedliche Produktchargen mit verschiedenen Farben umfassen, ist der Schnellfarbwechsel ein entscheidender Wettbewerbsvorteil.
Funktionsweise eines Schnellfarbwechselsystems
In einer traditionellen Pulverbeschichtungsanlage kann der Farbwechsel eine aufwendige und zeitintensive Aufgabe sein. Es erfordert in der Regel das Reinigen der Sprühpistolen, Schläuche und Filtersysteme, um Rückstände der alten Farbe zu entfernen, bevor eine neue Farbe aufgetragen werden kann. Bei einem Schnellfarbwechselsystem sind jedoch fortschrittliche automatisierte Reinigungsmechanismen integriert, die diesen Prozess erheblich beschleunigen.
- Automatische Reinigung der Kabinen: Bei einem Schnellfarbwechsel wird das Pulver aus den Sprühpistolen und den Zyklonabscheidern automatisch entfernt. Moderne Systeme verwenden Luftdüsen, Vibrationsmechanismen oder Luftkompressoren, um Pulverreste aus den Schläuchen, Düsen und anderen Komponenten zu blasen. Dies geschieht in einem geschlossenen Kreislaufsystem, um sicherzustellen, dass das Pulver effizient zurückgewonnen und für den nächsten Produktionslauf genutzt werden kann.
- Schnellreinigung der Sprühpistolen: Die Sprühpistolen sind so konzipiert, dass sie mit wenigen Handgriffen oder automatisch gereinigt werden können. Einige Systeme bieten automatische Reinigungsprogramme, bei denen die Pistolen mit Luft oder speziellen Reinigungsmitteln durchgespült werden, um alte Farbpartikel zu entfernen. Dies reduziert den Materialverlust und sorgt für einen schnelleren Wechsel zwischen den Farben.
- Einstellen der neuen Farbe: Ein weiterer Vorteil des Schnellfarbwechselsystems ist, dass die Farbmischung und der Pulverdurchfluss automatisch an die neue Farbe angepasst werden. Einige Systeme verfügen über intelligente Sensoren, die die Eigenschaften der neuen Farbe (wie Viskosität und Fließeigenschaften) erkennen und die Pulvermengen entsprechend optimieren. Dies gewährleistet eine gleichmäßige Beschichtung und eine präzise Farbabstimmung.
- Dynamische Anpassung des Beschichtungsprozesses: In einigen fortschrittlichen Schnellfarbwechselsystemen wird der gesamte Beschichtungsprozess, einschließlich der Sprühtechnik, Sprühparameter (wie Luftdruck und Pulvermenge) und Bodenabstände, angepasst. Diese Anpassungen erfolgen in Echtzeit, basierend auf der jeweiligen Farb- und Oberflächenanforderung, was eine konstant hohe Beschichtungsqualität gewährleistet.
Vorteile des Schnellfarbwechselsystems
- Erhöhte Produktionsgeschwindigkeit: Einer der größten Vorteile des Schnellfarbwechsels ist die signifikante Reduktion der Ausfallzeiten zwischen den Produktionsläufen. Da der Wechsel zwischen den Farben in wenigen Minuten abgeschlossen ist, anstatt Stunden zu dauern, wird der gesamte Produktionsprozess erheblich beschleunigt. Dies ist besonders vorteilhaft in Branchen, die eine hohe Produktionsdichte mit häufigen Farbwechseln benötigen.
- Weniger Abfall und Materialverschwendung: Durch die automatische Pulverrückgewinnung und die präzise Steuerung der Pulvermengen wird die Materialverschwendung auf ein Minimum reduziert. Das überschüssige Pulver wird effektiv gesammelt und kann in den nächsten Farbwechselprozess integriert werden, was zu Kostenersparnissen und einer umweltfreundlicheren Produktion führt.
- Geringerer Wartungsaufwand: Die automatische Reinigung und die Integration fortschrittlicher Filtertechnologien sorgen dafür, dass die Pulverkabinen auch nach mehreren Farbwechseln sauber und funktionsfähig bleiben. Dies reduziert den Wartungsaufwand und verlängert die Lebensdauer der Komponenten, was langfristig zu einer Reduzierung der Betriebskosten führt.
- Erhöhte Flexibilität und Kundenzufriedenheit: Die Fähigkeit, schnell zwischen verschiedenen Farben zu wechseln, ermöglicht es Unternehmen, auf schnell wechselnde Kundenanforderungen zu reagieren und maßgeschneiderte Lösungen für eine Vielzahl von Produkttypen anzubieten. Diese Flexibilität wird besonders in Branchen geschätzt, die eine hohe Produktvielfalt bieten, wie etwa die Automobilindustrie oder der Maschinenbau.
- Verbesserte Farbgenauigkeit: Durch die automatische Anpassung der Sprühparameter und Pulvermenge wird eine konsistente Farbqualität sichergestellt. Die präzise Steuerung trägt dazu bei, dass die Farbdeckung gleichmäßig und ohne Fehler erfolgt, was die Produktqualität erheblich verbessert.
Weitere Technologien und Entwicklungen
Neben der automatischen Reinigung und der Farbregelung entwickeln Hersteller von Pulverbeschichtungsanlagen immer ausgeklügeltere Systeme, die den Schnellfarbwechsel noch effizienter gestalten. Dazu gehören unter anderem:
- Intelligente Überwachungssysteme: Systeme, die den gesamten Prozess in Echtzeit überwachen, um sicherzustellen, dass jeder Farbwechsel korrekt ausgeführt wird und die Beschichtungseigenschaften konstant bleiben.
- Farbvorhersagemodelle: Durch den Einsatz von Big Data und Künstlicher Intelligenz können in Zukunft noch präzisere Modelle entwickelt werden, die voraussagen, welche Farbmischungen und Pulverarten am besten geeignet sind, um optimale Ergebnisse zu erzielen.
- Hybridtechnologien: Die Kombination von Pulverbeschichtung mit anderen Beschichtungsverfahren wie Flüssiglackierung oder Beschichtungen mit speziellen Nanomaterialien kann ebenfalls in Schnellfarbwechselsysteme integriert werden, um noch vielseitigere Lösungen anzubieten.
Zusammenfassend lässt sich sagen, dass der Schnellfarbwechsel eine entscheidende Technologie in der modernen automatisierten Pulverbeschichtung darstellt. Die kontinuierliche Verbesserung dieser Systeme führt zu einer höheren Flexibilität, effizienteren Produktionsprozessen und einer nachhaltigeren Nutzung von Ressourcen. Besonders in wettbewerbsintensiven Industrien, in denen eine schnelle Reaktionsfähigkeit erforderlich ist, wird diese Technologie zunehmend unverzichtbar.
Die fortschreitende Entwicklung von Schnellfarbwechselsystemen in Pulverbeschichtungsanlagen wird zunehmend von innovativen Technologien begleitet, die den Prozess weiter optimieren und die Leistung der gesamten Beschichtungsanlage steigern. Einige dieser Entwicklungen beinhalten nicht nur die Verbesserung der Effizienz und Flexibilität, sondern auch die Nachhaltigkeit und Kostenkontrolle der Pulverbeschichtungsprozesse.
Integration von Künstlicher Intelligenz (KI) und Maschinellem Lernen
Ein großer Schritt nach vorn in der Schnellfarbwechseltechnologie ist die Nutzung von KI und Maschinellem Lernen. Durch die Analyse von Produktionsdaten und -parametern können Algorithmen Muster erkennen und die Prozesssteuerung optimieren. KI-basierte Systeme können beispielsweise den idealsten Zeitpunkt für den Farbwechsel bestimmen oder automatisch die optimalen Sprühparameter einstellen, um den Farbwechsel effizienter zu gestalten. Diese Art von intelligenter Automatisierung ermöglicht eine noch genauere und schnellere Anpassung an die Produktionsanforderungen, ohne die Notwendigkeit für manuelle Eingriffe.
KI kann auch dazu verwendet werden, den gesamten Produktionsprozess zu überwachen und Fehlerquellen frühzeitig zu erkennen. Durch die vorausschauende Wartung und das Sammeln von Daten in Echtzeit können etwaige Probleme, die zu Verzögerungen oder Qualitätsverlusten führen könnten, identifiziert und behoben werden, bevor sie den Produktionsablauf beeinträchtigen.
Verbesserte Energieeffizienz und Nachhaltigkeit
Ein weiterer wichtiger Trend in der Entwicklung von Schnellfarbwechselsystemen ist der Fokus auf Energieeffizienz und Nachhaltigkeit. Durch die Rückgewinnung und Wiederverwendung von überschüssigem Pulver und den optimierten Energieverbrauch von Sprühpistolen und Heizsystemen wird der ökologische Fußabdruck der Pulverbeschichtungsanlagen erheblich verringert. Zudem sorgen moderne Zyklonabscheider und Filtrationssysteme dafür, dass weniger Pulver in die Luft abgegeben wird, was zu einer geringeren Belastung der Umwelt führt.
Viele Unternehmen setzen zunehmend auf die Nutzung von erneuerbaren Energien und energieeffizienten Komponenten wie LED-Beleuchtung, hochisolierten Öfen und Energie-Rückgewinnungssystemen, die während der Beschichtung und dem Einbrennvorgang Wärme zurückgewinnen. Solche Maßnahmen tragen nicht nur zur Senkung der Betriebskosten bei, sondern auch zur Erfüllung immer strengerer Umweltvorgaben und zur Verbesserung der Öko-Bilanz der Produktionsstätten.
Automatisierte Farbklassifizierung und -überwachung
Eine zusätzliche Technologie, die den Schnellfarbwechsel noch weiter verfeinert, ist die automatische Farbklassifizierung und -überwachung. In vielen modernen Pulverbeschichtungsanlagen kommen Kamerasysteme zum Einsatz, die die Qualität der aufgetragenen Farbe in Echtzeit überwachen. Diese Systeme sind in der Lage, Abweichungen in der Farbgebung sofort zu erkennen, die Farbgenauigkeit zu überprüfen und gegebenenfalls Korrekturen vorzunehmen. Dies hilft dabei, Farbfehler zu vermeiden und sicherzustellen, dass die Endprodukte immer den hohen Qualitätsstandards entsprechen.
Flexibilität und Anpassungsfähigkeit
Die Flexibilität des Schnellfarbwechselsystems ist ein weiterer entscheidender Vorteil, insbesondere in der Mass Customization-Ära, in der Unternehmen häufig kleinere Auftragsmengen mit spezifischen Kundenanforderungen produzieren. Schnellfarbwechselsysteme bieten die Möglichkeit, innerhalb kürzester Zeit zwischen verschiedenen Farben und Pulverarten zu wechseln. Einige Systeme sind in der Lage, nicht nur zwischen verschiedenen Standardfarben zu wechseln, sondern auch spezielle Metallfarben oder Effektpulver zu verarbeiten, die in der Industrie zunehmend gefragt sind.
Diese Vielseitigkeit ermöglicht es den Herstellern, eine breitere Palette von Produkten mit unterschiedlichen Beschichtungseigenschaften und Designs anzubieten, was besonders in Bereichen wie der Automobilindustrie oder Möbelproduktion von Vorteil ist. Ein modulares Design der Pulverbeschichtungsanlagen sorgt dafür, dass das System je nach Bedarf angepasst oder erweitert werden kann, ohne dass es zu größeren Investitionskosten kommt.
Zukunftsaussichten für Schnellfarbwechselsysteme
Die Zukunft der Schnellfarbwechseltechnologie ist vielversprechend, da immer fortschrittlichere automatisierte Systeme und intelligente Technologien zur Verfügung stehen, die die Effizienz, Flexibilität und Nachhaltigkeit weiter steigern. Die Integration von IoT (Internet of Things) ermöglicht eine noch detailliertere Analyse und Kontrolle der Produktionsprozesse in Echtzeit, wodurch Unternehmen ihre Prozesse noch stärker optimieren können.
Durch die zunehmende Vernetzung und den Datenaustausch zwischen verschiedenen Maschinen und Produktionslinien können Unternehmen ihre Wartungszyklen optimieren, die Produktqualität weiter verbessern und Ausfallzeiten minimieren. In Kombination mit robotergestützten Systemen und kollaborativen Robotern wird der Schnellfarbwechsel noch effizienter und nahtloser in die Gesamtproduktionsumgebung integriert.
Ein weiterer wichtiger Trend ist die Entwicklung von intelligenten Farbsystemen, die in der Lage sind, die benötigte Farbe basierend auf Kundenvorgaben oder den spezifischen Anforderungen des Produkts automatisch zu erzeugen. Solche Systeme könnten in der Zukunft die Notwendigkeit für manuelle Farbwechsel oder die Lagerung von großen Mengen unterschiedlicher Farbpulver überflüssig machen.
Zusammenfassend lässt sich sagen, dass der Schnellfarbwechsel in Pulverbeschichtungsanlagen eine Schlüsseltechnologie für die Zukunft der Industrie darstellt. Mit kontinuierlichen Verbesserungen und der Integration von neuen Technologien wird die Effizienz dieser Systeme weiter gesteigert, was zu einer höheren Produktivität, geringeren Kosten und einer noch nachhaltigeren Produktion führt.
Die fortschreitende Entwicklung und Integration neuer Technologien im Bereich der Schnellfarbwechsel-Pulverbeschichtungssysteme wird weiterhin durch die zunehmende Automatisierung und Digitalisierung vorangetrieben. Diese Veränderungen verbessern nicht nur die Effizienz und Produktivität, sondern tragen auch zu einer größeren Wettbewerbsfähigkeit und Kundenzufriedenheit bei, indem sie es Unternehmen ermöglichen, sich besser an marktspezifische Anforderungen und Individualisierungswünsche anzupassen.
Einsatz von Robotik und kollaborativen Robotern
Eine der markantesten Entwicklungen im Bereich der Pulverbeschichtung ist der zunehmende Einsatz von Robotern in der Produktion. Insbesondere kollaborative Roboter (Cobots) werden zunehmend in Pulverbeschichtungsanlagen integriert. Diese Roboter arbeiten Hand in Hand mit den menschlichen Bedienern und übernehmen Aufgaben wie das Bewegen von Werkstücken, das Zuführen von Materialien oder das Führen von Sprühpistolen. Durch diese enge Zusammenarbeit zwischen Mensch und Maschine wird der Arbeitsaufwand reduziert und gleichzeitig die Präzision und Geschwindigkeit des Farbwechsels verbessert.
Kollaborative Roboter sind in der Lage, präzise und wiederholbare Bewegungen auszuführen, die für einen schnellen und fehlerfreien Farbwechsel entscheidend sind. Sie können schnell zwischen verschiedenen Farbprojekten umschalten, indem sie die Sprühparameter anpassen, die Farbdüse wechseln oder sogar die Pistolensteuerung übernehmen, ohne dass die gesamte Anlage neu kalibriert werden muss. Dies ermöglicht eine flexible und effiziente Produktion, bei der eine Vielzahl von Farboptionen und Designs mit minimalem Aufwand realisiert werden kann.
Optimierung durch Vernetzung (IoT)
Ein weiterer bahnbrechender Trend in der Schnellfarbwechselsystemtechnologie ist der Einsatz von Internet of Things (IoT), das die Vernetzung von Maschinen und Prozessen ermöglicht. Durch die Verwendung von intelligenten Sensoren und Vernetzungssystemen können Pulverbeschichtungsanlagen in Echtzeit überwacht werden, sodass die Prozesssteuerung kontinuierlich optimiert wird. IoT-fähige Systeme sammeln ständig Daten zu Farbqualität, Pulververbrauch, Temperatur, Luftdruck und anderen wichtigen Parametern und senden diese an ein zentrales Steuerungssystem.
Diese Datenanalyse in Echtzeit ermöglicht nicht nur eine präzisere Steuerung der Pulverbeschichtung während des Farbwechsels, sondern auch eine umfassende Fehlerdiagnose und Wartungsplanung. Maschinenfehler können frühzeitig erkannt und behoben werden, bevor sie zu Produktionsausfällen führen. Darüber hinaus kann das System vorausschauend Wartungsbedarf feststellen und automatisch einen Termin für die Wartung ansetzen, was zu einer weiteren Reduzierung der Ausfallzeiten führt.
Automatisierte Farb- und Pulverspeicherung
Eine weitere Entwicklung, die den Farbwechselprozess in Pulverbeschichtungsanlagen revolutioniert, ist die automatisierte Farb- und Pulverspeicherung. Modernste Systeme ermöglichen es, dass Pulver in verschiedenen Farben und Formulierungen in intelligente Lagersysteme eingespeichert werden, die das Pulver in der richtigen Menge und Qualität für den nächsten Auftrag bereitstellen. Diese automatische Vorratshaltung reduziert nicht nur den Arbeitsaufwand, sondern stellt auch sicher, dass stets die richtige Pulverqualität zur Verfügung steht, was zu einer konstanten Beschichtungsqualität führt.
Durch den Einsatz von intelligenten Lagersystemen kann auch der Lagerplatz optimiert werden. Die Pulvervorräte werden effizient verwaltet, sodass der Wechsel zwischen verschiedenen Farben schneller und ohne Fehler durchgeführt werden kann. Dieses System trägt nicht nur zur Effizienzsteigerung bei, sondern senkt auch den Materialverlust und steigert die Kosteneffizienz in der Produktion.
Energieeffiziente Pulverbeschichtungssysteme
Die Energieeffizienz von Pulverbeschichtungsanlagen wird zunehmend zu einem entscheidenden Faktor, da die Industrie immer stärker unter ökologischen und wirtschaftlichen Druck steht. Der Energieverbrauch in der Pulverbeschichtung ist typischerweise hoch, insbesondere bei der Erhitzung des Einbrennofens und der Luftzirkulation innerhalb der Kabinen. Eine Verbesserung der Energieeffizienz kann jedoch nicht nur die Betriebskosten senken, sondern auch zur Nachhaltigkeit der gesamten Produktion beitragen.
Moderne Pulverbeschichtungsanlagen verfügen über optimierte Heizsysteme, die die notwendige Wärme effizienter erzeugen und verteilen. Technologien wie Wärmerückgewinnungssysteme ermöglichen es, die Abwärme aus dem Einbrennofen oder der Pulverkabine zurückzugewinnen und für den Prozess erneut zu nutzen, was den Gesamtenergieverbrauch der Anlage reduziert. Darüber hinaus können energieeffiziente Lüftungs- und Belüftungssysteme helfen, die Luftzirkulation zu verbessern und die Energieverluste zu minimieren.
Ein weiteres Beispiel für die Energieoptimierung ist der Einsatz von LED-Beleuchtung und anderen niedrigenergieverbrauchenden Technologien, die die Betriebskosten erheblich senken und gleichzeitig die Arbeitsumgebung verbessern.
Zukunft der Schnellfarbwechselsysteme
Mit dem kontinuierlichen Fortschritt in der Technologie werden Schnellfarbwechselsysteme in der Pulverbeschichtung immer leistungsfähiger, effizienter und flexibler. Die Integration von AI, IoT und Robotik wird nicht nur die Produktivität erhöhen, sondern auch die Qualität und Zuverlässigkeit der Beschichtungsprozesse weiter verbessern.
Ein vielversprechender Trend ist die zunehmende Entwicklung von smarten Pulverbeschichtungslösungen, bei denen eine vollständige Automatisierung des gesamten Prozesses angestrebt wird. Mit selbstlernenden Systemen könnte die Pulverbeschichtung in der Zukunft nahezu ohne menschliche Intervention ablaufen. Dies würde nicht nur den Farbwechsel weiter beschleunigen, sondern auch zu einer absoluten Fehlerfreiheit bei der Beschichtung führen.
Mit der ständigen Weiterentwicklung von automatisierten Systemen, intelligenten Steuerungen und energiesparenden Technologien ist es wahrscheinlich, dass Schnellfarbwechselsysteme in den kommenden Jahren noch flexibler und umweltfreundlicher werden. Dies wird dazu beitragen, die Wettbewerbsfähigkeit der Unternehmen in der Pulverbeschichtungsindustrie zu sichern und gleichzeitig den ökologischen Fußabdruck der Produktion zu verringern.
Schnellfarbwechsel Pulverbeschichtungskabine
Eine Schnellfarbwechsel Pulverbeschichtungskabine ist eine Pulverbeschichtungskabine, die einen schnellen und effizienten Farbwechsel ermöglicht. Dies ist wichtig für Unternehmen, die eine Vielzahl von Farben verarbeiten oder die schnell zwischen verschiedenen Farbaufträgen wechseln müssen.
Schnellfarbwechsel Pulverbeschichtungskabinen verfügen über verschiedene Funktionen, die den Farbwechsel beschleunigen. Dazu gehören:
- Automatisierte Reinigungssysteme: Automatisierte Reinigungssysteme können die Kabine schnell und gründlich von Pulverresten reinigen.
- Schnelle Filterwechsel: Schnelle Filterwechsel ermöglichen es, die Kabine schnell von Pulverlackpartikeln zu befreien.
- Intelligente Steuerungssysteme: Intelligente Steuerungssysteme können den Farbwechsel automatisch steuern und optimieren.
Die verschiedenen Funktionen einer Schnellfarbwechsel Pulverbeschichtungskabine können in Kombination oder einzeln eingesetzt werden. Die Wahl der richtigen Funktionen hängt von den individuellen Anforderungen des Unternehmens ab.
Die Vorteile einer Schnellfarbwechsel Pulverbeschichtungskabine sind:
- Erhöhte Produktivität: Schnellfarbwechsel Pulverbeschichtungskabinen ermöglichen es, Farbaufträge schneller zu bearbeiten.
- Geringere Ausfallzeiten: Schnellfarbwechsel Pulverbeschichtungskabinen verringern die Ausfallzeiten, da der Farbwechsel schneller durchgeführt werden kann.
- Verbesserte Arbeitssicherheit: Schnellfarbwechsel Pulverbeschichtungskabinen reduzieren das Risiko von Gesundheitsproblemen, da die Kabine schneller von Pulverresten gereinigt werden kann.
Die Nachteile einer Schnellfarbwechsel Pulverbeschichtungskabine sind:
- Höhere Anschaffungskosten: Schnellfarbwechsel Pulverbeschichtungskabinen sind teurer als herkömmliche Pulverbeschichtungskabinen.
- Komplexere Bedienung: Schnellfarbwechsel Pulverbeschichtungskabinen sind komplexer zu bedienen als herkömmliche Pulverbeschichtungskabinen.
Schnellfarbwechsel Pulverbeschichtungskabinen sind eine gute Investition für Unternehmen, die eine Vielzahl von Farben verarbeiten oder die schnell zwischen verschiedenen Farbaufträgen wechseln müssen. Sie können die Produktivität, die Arbeitssicherheit und die Effizienz verbessern.
Welche Werkstoffe können pulverbeschichtet werden?
Grundsätzlich können alle metallischen Werkstoffe pulverbeschichtet werden. Dazu gehören unter anderem:
- Stahl: Stahl ist der am häufigsten pulverbeschichtete Werkstoff. Er ist in verschiedenen Legierungen erhältlich und kann für eine Vielzahl von Anwendungen verwendet werden.
- Aluminium: Aluminium ist ein leichtes und korrosionsbeständiges Material. Es wird häufig in der Automobilindustrie und im Bauwesen verwendet.
- Messing: Messing ist ein dekoratives und korrosionsbeständiges Material. Es wird häufig in der Sanitärindustrie und im Möbelbau verwendet.
- Kupfer: Kupfer ist ein elektrisch leitfähiges und korrosionsbeständiges Material. Es wird häufig in der Elektroindustrie und im Maschinenbau verwendet.
Weiterhin können auch Kunststoffe und Verbundwerkstoffe pulverbeschichtet werden. Dazu gehören unter anderem:
- Polyester: Polyester ist ein vielseitiger Kunststoff, der für eine Vielzahl von Anwendungen verwendet werden kann.
- Polyurethan: Polyurethan ist ein strapazierfähiger und wasserabweisender Kunststoff. Es wird häufig in der Möbelindustrie und im Bauwesen verwendet.
- PVC: PVC ist ein kostengünstiger und wetterbeständiger Kunststoff. Es wird häufig in der Bauindustrie und im Gartenbau verwendet.
Die Wahl des geeigneten Werkstoffes hängt von den individuellen Anforderungen ab. Soll die Beschichtung beispielsweise besonders kratzfest sein, ist ein Stahlwerkstoff mit hoher Härte zu empfehlen. Soll die Beschichtung hingegen besonders korrosionsbeständig sein, ist ein Aluminiumwerkstoff oder ein Kunststoff mit guter Witterungsbeständigkeit zu empfehlen.
Bei der Pulverbeschichtung von Werkstoffen ist es wichtig, dass die Oberfläche sauber und fettfrei ist. Andernfalls kann die Beschichtung nicht ordnungsgemäß haften. Die Oberfläche kann mit verschiedenen Methoden gereinigt werden, z. B. mit einem Hochdruckreiniger, einem chemischen Reinigungsmittel oder einer Strahlanlage.
Nach der Pulverbeschichtung wird das Werkstück in einem Ofen ausgehärtet. Die Aushärtungstemperatur hängt von der Art des Pulverlacks ab. In der Regel beträgt die Aushärtungstemperatur 180 bis 200 Grad Celsius.
Es können alle elektrisch leitfähigen metallischen Werkstoffe pulverbeschichtet werden, die die notwendige Temperaturbeständigkeit von 200°C aufweisen. Ferner eigenen sich zum Pulverbeschichten mit speziellen Anlagen und Pulvern auch Glas, Keramik und Holz. (MDF-Platten).
Für Stahl, Stahlguss und Aluminiumknetlegierungen (Profile usw.) sind geeignete chemische Vorbehandlungen für eine dauerhafte Außenanwendung vorhanden.
Aluminium-Sand- und Kokillengussteile sowie Aluminium-Druckgussteile sind für einen Außeneinsatz nur bedingt geeignet. Alle übrigen Nichteisenmetalle (Kupfer, Messing) können nur für den Inneneinsatz beschichtet werden.
Beschichtungskabine für Schnellfarbwechsel

Eine Beschichtungskabine für Schnellfarbwechsel ist eine Anlage, die zum Auftragen von Pulverlack auf Werkstücke verwendet wird und einen schnellen und effizienten Farbwechsel ermöglicht. Dies ist wichtig für Unternehmen, die eine Vielzahl von Farben verarbeiten oder die schnell zwischen verschiedenen Farbaufträgen wechseln müssen.
Schnellfarbwechsel-Beschichtungskabinen verfügen über verschiedene Funktionen, die den Farbwechsel beschleunigen. Dazu gehören:
- Automatisierte Reinigungssysteme: Automatisierte Reinigungssysteme können die Kabine schnell und gründlich von Pulverresten reinigen.
- Schnelle Filterwechsel: Schnelle Filterwechsel ermöglichen es, die Kabine schnell von Pulverlackpartikeln zu befreien.
- Intelligente Steuerungssysteme: Intelligente Steuerungssysteme können den Farbwechsel automatisch steuern und optimieren.
Die verschiedenen Funktionen einer Schnellfarbwechsel-Beschichtungskabine können in Kombination oder einzeln eingesetzt werden. Die Wahl der richtigen Funktionen hängt von den individuellen Anforderungen des Unternehmens ab.
Die Vorteile einer Schnellfarbwechsel-Beschichtungskabine sind:
- Erhöhte Produktivität: Schnellfarbwechsel-Beschichtungskabinen ermöglichen es, Farbaufträge schneller zu bearbeiten.
- Geringere Ausfallzeiten: Schnellfarbwechsel-Beschichtungskabinen verringern die Ausfallzeiten, da der Farbwechsel schneller durchgeführt werden kann.
- Verbesserte Arbeitssicherheit: Schnellfarbwechsel-Beschichtungskabinen reduzieren das Risiko von Gesundheitsproblemen, da die Kabine schneller von Pulverresten gereinigt werden kann.
Die Nachteile einer Schnellfarbwechsel-Beschichtungskabine sind:
- Höhere Anschaffungskosten: Schnellfarbwechsel-Beschichtungskabinen sind teurer als herkömmliche Beschichtungskabinen.
- Komplexere Bedienung: Schnellfarbwechsel-Beschichtungskabinen sind komplexer zu bedienen als herkömmliche Beschichtungskabinen.
Schnellfarbwechsel-Beschichtungskabinen sind eine gute Investition für Unternehmen, die eine Vielzahl von Farben verarbeiten oder die schnell zwischen verschiedenen Farbaufträgen wechseln müssen. Sie können die Produktivität, die Arbeitssicherheit und die Effizienz verbessern.
Die wichtigsten Komponenten einer Schnellfarbwechsel-Beschichtungskabine sind:
- Kabine: Die Kabine ist der geschlossene Raum, in dem das Werkstück mit Pulverlack besprüht wird. Sie sollte aus einem feuerfesten Material bestehen, um die Bildung von Funken oder Bränden zu verhindern.
- Abluftsystem: Das Abluftsystem dient dazu, den Pulverlack aus der Kabine abzusaugen und zu filtern. Es sollte so dimensioniert sein, dass es die gesamte Luft aus der Kabine absaugen kann.
- Filteranlage: Die Filteranlage dient dazu, den Pulverlack aus der Luft zu filtern. Sie sollte aus einem Filtermaterial bestehen, das den Pulverlack effektiv zurückhält.
- Reinigungssystem: Das Reinigungssystem dient dazu, die Kabine von Pulverresten zu reinigen. Es kann ein manuelles oder automatisches System sein.
- Steuerungssystem: Das Steuerungssystem steuert den gesamten Farbwechselprozess. Es kann ein manuelles oder automatisches System sein.
Die Wahl der richtigen Schnellfarbwechsel-Beschichtungskabine hängt von den individuellen Anforderungen des Unternehmens ab. Zu berücksichtigende Faktoren sind unter anderem:
- Art der zu beschichtenden Werkstücke: Die Größe und Form der Werkstücke bestimmen die Art des Transportsystems und des Beschichtungssystems.
- Anzahl der Werkstücke: Die Anzahl der Werkstücke, die beschichtet werden sollen, bestimmt die Größe der Kabine.
- Anzahl der Farben: Die Anzahl der Farben, die verarbeitet werden sollen, bestimmt die Art des Reinigungssystems und des Steuerungssystems.
- Budget: Schnellfarbwechsel-Beschichtungskabinen sind teurer als herkömmliche Beschichtungskabinen.
Eine geschlossene Beschichtungskabine ist ein an allen Seiten während des Sprühens des Beschichtungsstoffes geschlossener räumlicher Bereich, mit Ausnahme der Öffnungen für den Ein- und Auslauf der Werkstücke. Diese Bauweise, die die Applikationsgeräte, Zuleitungen und Bewegungsautomaten umfasst, ist üblich für Flüssig lackbeschichtungen.
Eine teilweise geschlossene Beschichtungskabine ist ein an allen Seiten geschlossener räumlicher Bereich mit Ausnahme der Öffnungen für die automatischen elektrostatischen Sprühvorrichtungen und/oder die Arbeitsöffnungen für die Handbeschichtung.
Diese Kabine wird vor allem für pulverförmige Beschichtungsstoffe eingesetzt. Alle Beschichtungskabinen müssen während des Sprühens des Beschichtungsstoffes technisch belüftet werden.
Diese Forderung resultiert aus der Notwendigkeit, explosive Gemische weitgehend auszuschließen, Gefährdungen durch das Einatmen der Teilchen-Luft-Gemische zu vermeiden und die Verschmutzung des Kabinenumfelds mit Pulver zu minimieren.
Automatische Kunststoff-PVC-Schnellfarbwechsel-Pulverbeschichtungskabine
Eine automatische Kunststoff-PVC-Schnellfarbwechsel-Pulverbeschichtungskabine ist eine Anlage, die zum Auftragen von Pulverlack auf Kunststoff- und PVC-Werkstücke verwendet wird und einen schnellen und effizienten Farbwechsel ermöglicht.
Diese Art von Kabine besteht aus folgenden Komponenten:
- Kabine: Die Kabine ist der geschlossene Raum, in dem das Werkstück mit Pulverlack besprüht wird. Sie sollte aus einem feuerfesten Material bestehen, um die Bildung von Funken oder Bränden zu verhindern.
- Abluftsystem: Das Abluftsystem dient dazu, den Pulverlack aus der Kabine abzusaugen und zu filtern. Es sollte so dimensioniert sein, dass es die gesamte Luft aus der Kabine absaugen kann.
- Filteranlage: Die Filteranlage dient dazu, den Pulverlack aus der Luft zu filtern. Sie sollte aus einem Filtermaterial bestehen, das den Pulverlack effektiv zurückhält.
- Reinigungssystem: Das Reinigungssystem dient dazu, die Kabine von Pulverresten zu reinigen. Es ist in der Regel ein automatisches System, das die Kabine mit Hochdruckreinigern oder Dampfstrahlern reinigt.
- Transportsystem: Das Transportsystem dient dazu, die Werkstücke in die Kabine zu bringen und aus der Kabine zu entfernen. Es ist in der Regel ein automatisches System, das die Werkstücke mit Ketten oder Förderbändern transportiert.
- Pulverbeschichtungssystem: Das Pulverbeschichtungssystem dient dazu, den Pulverlack auf das Werkstück aufzutragen. Es ist in der Regel ein elektrostatisches System, das den Pulverlack mithilfe von elektrostatischer Anziehung auf das Werkstück aufbringt.
- Steuerungssystem: Das Steuerungssystem steuert den gesamten Farbwechselprozess. Es ist in der Regel ein computergesteuertes System, das den Farbwechsel automatisch ablaufen lässt.
Die Vorteile einer automatischen Kunststoff-PVC-Schnellfarbwechsel-Pulverbeschichtungskabine sind:
- Erhöhte Produktivität: Automatische Kabinen ermöglichen es, Farbaufträge schneller zu bearbeiten.
- Geringere Ausfallzeiten: Automatische Kabinen verringern die Ausfallzeiten, da der Farbwechsel schneller durchgeführt werden kann.
- Verbesserte Arbeitssicherheit: Automatische Kabinen reduzieren das Risiko von Gesundheitsproblemen, da die Kabine schneller von Pulverresten gereinigt werden kann.
Die Nachteile einer automatischen Kunststoff-PVC-Schnellfarbwechsel-Pulverbeschichtungskabine sind:
- Höhere Anschaffungskosten: Automatische Kabinen sind teurer als manuelle Kabinen.
- Komplexere Bedienung: Automatische Kabinen sind komplexer zu bedienen als manuelle Kabinen.
Automatische Kunststoff-PVC-Schnellfarbwechsel-Pulverbeschichtungskabinen sind eine gute Investition für Unternehmen, die eine hohe Produktivität und Arbeitssicherheit bei der Pulverbeschichtung von Kunststoff- und PVC-Werkstücken gewährleisten möchten.
Weitere Vorteile von Kunststoff-PVC-Schnellfarbwechsel-Pulverbeschichtungskabinen sind:
- Sie können für eine Vielzahl von Kunststoff- und PVC-Werkstücken verwendet werden.
- Sie sind relativ leicht zu reinigen und zu warten.
- Sie sind in verschiedenen Größen und Ausführungen erhältlich, um den individuellen Anforderungen gerecht zu werden.
Bei der Auswahl einer automatischen Kunststoff-PVC-Schnellfarbwechsel-Pulverbeschichtungskabine sind folgende Faktoren zu berücksichtigen:
- Art der zu beschichtenden Werkstücke: Die Größe und Form der Werkstücke bestimmen die Art des Transportsystems und des Beschichtungssystems.
- Anzahl der Werkstücke: Die Anzahl der Werkstücke, die beschichtet werden sollen, bestimmt die Größe der Kabine.
- Anzahl der Farben: Die Anzahl der Farben, die verarbeitet werden sollen, bestimmt die Art des Reinigungssystems und des Steuerungssystems.
- Budget: Automatische Kabinen sind teurer als manuelle Kabinen.
Als Werkstoffe für Kabinenwände werden Metall. Glas oder Kunststoff eingesetzt. Die Abstände zum eigentlichen Beschichtungsbereich müssen groß sein, damit die Wände selbst nicht zum Beschichtungsteil werden , denn alle leitfähigen Teile sind wie das Werkstück zu erden. Heute werden vielfach Kunststoffkabinen eingesetzt.
Als elektrischer Nichtleiter hat Kunststoff den Vorteil, sich mit dem ersten Pulveranflug aufzuladen, die nachfolgenden Pulverteilchen abzustoßen und damit selbst als Drückerelektrode auf die Sprühwolke zu wirken. Dies ist umso wirkungsvoller, je dichter die Kabinenwände um den Beschichtungsbereich angeordnet sind.
Der verwendete Kunststoff muss schwer brennbar und die Außenseite der Kunststoffwand oder Teilbereiche dürfen nur im Abstand von > 9 mm mit einem leitfähigen Material hinterlegt sein, um Gleitstielbüschelentladungen auszuschließen. Ein wichtiger Punkt ist die Luftführung in der Kabine.
Der Luftvolumenstrom errechnet sich aus der Menge des pro Zeiteinheit versprühten Beschichtungsstoffes. An den Kabinen öffnungen sind Luftgeschwindigkeiten von 0,4 bis 0,7 m/s zu erfüllen. ln der Regel wird eine Einströmgeschwindigkeit vo n 0,5 m/ s angestrebt.
Der Schnellfarbwechselablauf
- Türen schließen. Ein-/Auslauf/Hand beschichtung = 1 min.
- Pistolen zum Referenzpunktfahren, Tiefenachsen ausfahren , gleichzeitig Pistolen außen abblasen, bei Bedarf wiederholen. Während dieses Vorganges wird das Gebinde entfernt =0,4 min.
- Pistoleninnenreinigung, Absenken des Injektorblockes. Pulsierendes Durchblasen von Tauchrohr, Injektor, Pulverschlauch und Pistole. Dieser Vorgang wird für den linken und rechten Pistolensatz unabhängig durchgeführt. Während dieses Vorganges werden die
Tauchrohre und Injektoren außen mit Druckluftgereinigt = 1,5 min. - Pistolen außenreinigung wird wiederholt = 0,3 min.
- Kabinenreinigung unter Abluftbetrieb. Für alle Kabinentypengültig: Reinigung der Pistolenschlitze. Reinigung der Handbeschichtungsöffnungen, manuel= 1 min.
- Kabineninnenreinigung, manuell oder mit Automat = 4 bis 6 min.
- Zyklon, Siebmaschine und Schubförderung reinigen, Konus absenken, Siebausschwenken und abblasen = 0,5 min.
- Reinigung der Schubförderung mit Gegenblasen und Konus ausblasen = 0,6 min.
- Konus ausschwenken, Zyklon auslaufpartie kontrollieren und abblasen = 0.2 min.
- Tauchrohrkontrolle, evtl. 1 x täglich abblasen, Konus einschwenken, Sieb hochfahren. Während dieses Vorganges wird das neue Farbgebinde im Pulverzentrum platziert, und die Injektoren werden abgetaucht. Hiermit ist der Farbwechselvorgang beendet = 0, 1 min
Werden sehr hohe Qualitätsansprüche gefordert, ist die Kontrolle der Pistolenmundstücke sowie das Austauschen der Pulverschläuche unumgänglich. Für 10 Pistolen rechnet man mit einem Zeitaufwand von ca. 5 min.
Die Wahl des Kabinentyps für Schnellfarbwechsel
Grundsätzlich unterscheidet man bei den Kabinentypen zwischen Kabinen für den Einfarben-, den Mehrfarben- und Schnellfarbwechsel-Einsatz.
In der Regel sind die Anlagenelemente heute in Modulbauweise aufgebaut. So sind die einzelnen Systemelemente, je nach Bedürfnis und Anwendungsfall, untereinander austauschbar.
Materialien für Pulverkabinen können je nach Hersteller beschichtetes oder rostfreies Metall, einwandige oder doppelwandige Kunststoffausführung oder Glas sein. Für die Kabinenbaumaterialien Stahl und Kunststoff gibt das Bild einen Eindruck hinsichtlich der Reinigungszeiten und der Pulveran sammlung.
Bei Kunststoffkabinen wird die Kabinenwand durch die negativ oder positiv geladenen Pulverteilchen ebenfalls negativ oder positiv aufgeladen und diese werden dadurch zurückgestoßen. Der Unte rschied im Verlauf der elektrostatischen Feldlinien bei einer Stahl- und Kunststoffkabine ist in Bild dargestellt. Die elektrischen Feldlinien beginnen immer an der Elektrode und enden an einem geerdeten Teil.
Im Folgenden sollen die Vor- und Nachteile der verschiedenen Kabinenmaterialien bzw. verschiedene Bauformen von Kabinen aufgezeigt werden.
Die Stahlkabine für Pulverbeschichtung

Stahlkabinen für Pulverbeschichtung sind eine Art von Beschichtungskabinen, die aus Stahl bestehen. Sie sind in verschiedenen Größen und Ausführungen erhältlich und können für eine Vielzahl von Werkstücken verwendet werden.
Die Vorteile von Stahlkabinen für Pulverbeschichtung sind:
- Sie sind robust und langlebig.
- Sie sind feuerfest und können Funken oder Bränden standhalten.
- Sie sind in verschiedenen Größen und Ausführungen erhältlich, um den individuellen Anforderungen gerecht zu werden.
Die Nachteile von Stahlkabinen für Pulverbeschichtung sind:
- Sie sind schwerer als Kabinen aus anderen Materialien.
- Sie können bei hohen Temperaturen verformt werden.
Die wichtigsten Komponenten einer Stahlkabine für Pulverbeschichtung sind:
- Kabine: Die Kabine ist der geschlossene Raum, in dem das Werkstück mit Pulverlack besprüht wird. Sie sollte aus einem feuerfesten Material bestehen, um die Bildung von Funken oder Bränden zu verhindern.
- Abluftsystem: Das Abluftsystem dient dazu, den Pulverlack aus der Kabine abzusaugen und zu filtern. Es sollte so dimensioniert sein, dass es die gesamte Luft aus der Kabine absaugen kann.
- Filteranlage: Die Filteranlage dient dazu, den Pulverlack aus der Luft zu filtern. Sie sollte aus einem Filtermaterial bestehen, das den Pulverlack effektiv zurückhält.
- Reinigungssystem: Das Reinigungssystem dient dazu, die Kabine von Pulverresten zu reinigen. Es kann ein manuelles oder automatisches System sein.
- Steuerungssystem: Das Steuerungssystem steuert den gesamten Beschichtungsprozess. Es kann ein manuelles oder automatisches System sein.
Die Wahl der richtigen Stahlkabine für Pulverbeschichtung hängt von den individuellen Anforderungen des Unternehmens ab. Zu berücksichtigende Faktoren sind unter anderem:
- Art der zu beschichtenden Werkstücke: Die Größe und Form der Werkstücke bestimmen die Art des Transportsystems und des Beschichtungssystems.
- Anzahl der Werkstücke: Die Anzahl der Werkstücke, die beschichtet werden sollen, bestimmt die Größe der Kabine.
- Anzahl der Farben: Die Anzahl der Farben, die verarbeitet werden sollen, bestimmt die Art des Reinigungssystems und des Steuerungssystems.
- Budget: Stahlkabinen sind in der Regel teurer als Kabinen aus anderen Materialien.
Bei der Auswahl einer Stahlkabine für Pulverbeschichtung sollten folgende Faktoren beachtet werden:
- Die Qualität des Stahls: Die Kabine sollte aus hochwertigem Stahl bestehen, der robust und langlebig ist.
- Die Dicke des Stahls: Die Kabine sollte aus ausreichend dickem Stahl bestehen, um bei hohen Temperaturen nicht zu verformen.
- Die Verarbeitung des Stahls: Die Kabine sollte sauber und gut verarbeitet sein, um eine gute Qualität der Beschichtung zu gewährleisten.
Stahlkabinen für Pulverbeschichtung sind eine gute Wahl für Unternehmen, die eine robuste und langlebige Kabine für die Pulverbeschichtung von Werkstücken suchen.
Vorteile
- Kostengünstig
- Einfache Montage
- Elementbauweise
- Beliebige Formgebung
- Harte Oberfläche
- Erfüllung der Sicherheitsanforderungen
Nachteile
- Viele Fugen
- Wände pulveranziehend
- Pulveransammlungen nach längerer Betriebszeit
- Reinigung (Schaben. Blasen) kompliziert und teuer
- Zeitaufwändiger Farbwechsel
- Je nach Konstruktio n zusätzliche Bodenreinigung notwendig
Stahlkabinen eignen sich für den Einsatz in Einfarbenanlagen oder bei Beschichtung auf Verlust. Längere Produktionszeiten führen zu großen Pulveransammlungen. die auch im Einfarbenbetrieb regelmäßig entfernt werden müssen, Bei Rückgewinnungsbetrieb und Farbwechsel muss die Kabinenreinigung in zwei Schritten erfolgen: zuerst Schaben, dann Blasen. Dadurch erhöht sich die Reinigungszeit erheblich.
Die Kunststoffkabine für Pulverbeschichtung

Kunststoffkabinen für Pulverbeschichtung sind eine Art von Beschichtungskabinen, die aus Kunststoff bestehen. Sie sind in verschiedenen Größen und Ausführungen erhältlich und können für eine Vielzahl von Werkstücken verwendet werden.
Die Vorteile von Kunststoffkabinen für Pulverbeschichtung sind:
- Sie sind leicht und einfach zu transportieren.
- Sie sind relativ kostengünstig.
- Sie sind leicht zu reinigen und zu warten.
Die Nachteile von Kunststoffkabinen für Pulverbeschichtung sind:
- Sie sind nicht so robust und langlebig wie Stahlkabinen.
- Sie sind nicht so feuerfest wie Stahlkabinen.
Die wichtigsten Komponenten einer Kunststoffkabine für Pulverbeschichtung sind:
- Kabine: Die Kabine ist der geschlossene Raum, in dem das Werkstück mit Pulverlack besprüht wird. Sie sollte aus einem feuerfesten Material bestehen, um die Bildung von Funken oder Bränden zu verhindern.
- Abluftsystem: Das Abluftsystem dient dazu, den Pulverlack aus der Kabine abzusaugen und zu filtern. Es sollte so dimensioniert sein, dass es die gesamte Luft aus der Kabine absaugen kann.
- Filteranlage: Die Filteranlage dient dazu, den Pulverlack aus der Luft zu filtern. Sie sollte aus einem Filtermaterial bestehen, das den Pulverlack effektiv zurückhält.
- Reinigungssystem: Das Reinigungssystem dient dazu, die Kabine von Pulverresten zu reinigen. Es kann ein manuelles oder automatisches System sein.
- Steuerungssystem: Das Steuerungssystem steuert den gesamten Beschichtungsprozess. Es kann ein manuelles oder automatisches System sein.
Die Wahl der richtigen Kunststoffkabine für Pulverbeschichtung hängt von den individuellen Anforderungen des Unternehmens ab. Zu berücksichtigende Faktoren sind unter anderem:
- Art der zu beschichtenden Werkstücke: Die Größe und Form der Werkstücke bestimmen die Art des Transportsystems und des Beschichtungssystems.
- Anzahl der Werkstücke: Die Anzahl der Werkstücke, die beschichtet werden sollen, bestimmt die Größe der Kabine.
- Anzahl der Farben: Die Anzahl der Farben, die verarbeitet werden sollen, bestimmt die Art des Reinigungssystems und des Steuerungssystems.
- Budget: Kunststoffkabinen sind in der Regel günstiger als Kabinen aus anderen Materialien.
Bei der Auswahl einer Kunststoffkabine für Pulverbeschichtung sollten folgende Faktoren beachtet werden:
- Die Qualität des Kunststoffs: Die Kabine sollte aus hochwertigem Kunststoff bestehen, der robust und langlebig ist.
- Die Dicke des Kunststoffs: Die Kabine sollte aus ausreichend dickem Kunststoff bestehen, um bei hohen Temperaturen nicht zu verformen.
- Die Verarbeitung des Kunststoffs: Die Kabine sollte sauber und gut verarbeitet sein, um eine gute Qualität der Beschichtung zu gewährleisten.
Kunststoffkabinen für Pulverbeschichtung sind eine gute Wahl für Unternehmen, die eine leichte und kostengünstige Kabine für die Pulverbeschichtung von Werkstücken suchen.
Hier sind einige Beispiele für Unternehmen, die Kunststoffkabinen für Pulverbeschichtung verwenden:
- Unternehmen, die Metallteile für die Automobilindustrie herstellen.
- Unternehmen, die Möbel aus Kunststoff herstellen.
- Unternehmen, die Gartenmöbel aus Kunststoff herstellen.
Kunststoffkabinen für Pulverbeschichtung sind eine gute Wahl für eine Vielzahl von Anwendungen.
Vorteile
- Praktisch fugenfrei
- Pulverabstoßend
- Reinigung durch Blasen
- Schnelle Farbwechsel
Nachteile
- Höhere Anschaffungskosten
- Oberfläche nicht kratzfest
- Sicherheitsvor schriften erfordern aufwändige Konstruktion
- Regelmässige Wartung erforderlich
Schnellfarbwechsel Kunststoffkabinen im Vergleich
Bei Kunststoffkabinen sind die grundsätzlichen Vorteile gegenüber einer Blech kabine immer dieselben . Jedoch die Bauform der Kabine führt zu Unterschieden , z. B. bei der Reinigungsdauer. Generell unterscheidet man zwischen den klassischen Rechteckkabinen. Rundkabinen und Kabinen in Tropfenform.
Kabine mit Reinigungsautomat
Vorteile
- Automatische Innenreinigung
- Kürzeste Reinigungszeit unabhängig von Kabinenhöhe
- Absaugung auf der ganzen Kabinenlänge
- Einfacher Rohrleitungsanschluss
- Kein Zerkratzen der Wände
- Geringe Pulveranhaftungen
- Kabinen hell, bessere Einsichtmöglichkeit im gereinigten Zustand
- Arbeitsfreundlich. speziell bei hellen Farben
Nachteile
- Hohe Investitionskosten
- Große Bauhöhe, normalerweise Grube erforderlich
- Hoher Druckluft- und Energieverbrauch
Schnellfarbwechselkabinen
Ab fünf Farbwechsel pro Tag lohnt sich der Einsatz eines Schnellfarbwechselsystems mit einer speziell für diese Anwendung konstruierten Kabine. Diese sind wahlweise ganz ohne oder mit
bis zu zwei Handbeschichtungsöffnungen. die als Vor- oder Nachbeschichtungsstation ausgelegt werden, ausgestattet.
Eine vertikale Pistolenanordnung vereinfacht eine objektbezogene Einstellung und spart Platz. Die Kunststoffwände der Kabinen verhindern eine Pulveransammlung, was durch eine zentrale Absaugung unterstützt wird. Die Reinigung der Kabine erfolgt in der Regel manuell mit einer Luftdüsenlanze: Systeme mit Reinigungsautomaten sind ebenfalls
möglich.
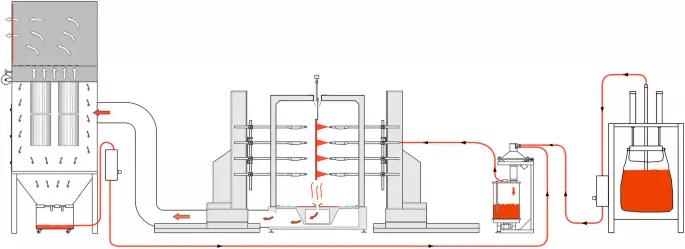
Rückgewinnung bei Schnellwechselkabinen
Bei Schnellwechselkabinen werden in der Regel Monozyklone mit Vibrationssieb. Auslaufkonus und Schubforderung eingesetzt. Sie sind praktisch „selbstreinigend“. Die Reinigung beschränkt sich auf die Auslaufpartie und den konischen Auslaufteil. Der Abscheidegrad variiert je nach Pulverbeaufschlag ung zwischen 95-97 %. Die Unterschiede der einzelnen Lieferanten sind in den Details zu suchen. Die Zyklone unterscheiden sich in Bauhöhe und Durchmesser.
Aus Platzgründen müssen teilweise Kompromisse eingegangen werden. Bei größeren Durchmessern sinkt die Umfangsgeschwindigkeit, und der Abscheidegrad verschlechtert sich. Niedrige Geschwindigkeiten verhindern die Ansinterung von Pulverpartikel. Kleinere Durchmesser erhöhen den Abscheidegrad. Die höhere Umfangsgeschwindigkeit kann zu Ansinterungen führen.
Die Luft bewegungen auf der Höhe der Siebmaschine sollten möglichst gering gehalten werden, um Ansinterurigen auf dem Siebgewebe zu verhindern. Bei kurzer Bauhöhe bleibt der Luft eine zu geringe Beruhigungsstrecke, was zu Pulververlusten sowie Pulveransinterungen
auf dem Sieb und im konischen Auslaufteil fuhren kann.
Monozyklon mit Nachfilter
Vorteile
- Große Bandbreite
- Mehrfarbenbetrieb
- Einfache Konstruktion
Nachteile
- Große Bauhöhe
- Wirkungsgrad-Verluste
Filtersystem
- Einfaches System mit hohem Abscheidegrad
- Kompakte Bauweise
- Platzsparend
- Keine Rohrverbindungen
Nachteile
- Nur Einfarbenbetrieb
- Standzeiten der Patronen oder Platten
- Für jede Farbe eine Filtereinheit erforderlich
Der Wirkungsgrad von Pulverruckgewinnungsanlagen beim Schnellfarbwechsel
Je nach Rückgewinnungssystem beträgt der Pulverabscheidegrad ca. 90 – 99 %. Vom versprühten Pulver bleiben je nach Teileart ca. 15 – 80 % auf dem Beschichtungsobjekt haften. Das Arbeitsblatt gibt eine Hilfestellung welche Kriterien bei der Wahl des Rückgewinnungssystems zu beachten sind.
Einführung in die Pulverbeschichtung

Die Pulverbeschichtung ist eine Technik der Oberflächenveredelung, bei der pulverförmige Farben oder Beschichtungsmaterialien auf ein Substrat (meist Metall) aufgetragen werden. Im Gegensatz zu herkömmlichen Flüssigbeschichtungen wird bei der Pulverbeschichtung kein Lösungsmittel verwendet, was die Technik umweltfreundlicher macht. Das Pulver wird auf die Oberfläche des Objekts gesprüht und anschließend erhitzt, wodurch es zu einer glatten und dauerhaften Beschichtung schmilzt.
Pulverbeschichtungen werden hauptsächlich in der Automobil-, Bau- und Möbelindustrie sowie in der Elektronik verwendet. Es ist ein beliebtes Verfahren, da es robuste, widerstandsfähige Beschichtungen bietet, die gegen Kratzer, Korrosion und chemische Einflüsse beständig sind.
1.2. Geschichte der Pulverbeschichtung
Die Pulverbeschichtung wurde in den 1950er Jahren entwickelt und in den 1960er Jahren in der industriellen Produktion populär. Der Wunsch nach einer umweltfreundlicheren und effizienteren Alternative zu traditionellen Flüssigfarben führte zur Entwicklung von Pulverlacken, die ohne Lösungsmittel auskommen. Im Laufe der Jahrzehnte wurde die Technologie kontinuierlich weiterentwickelt, und heute sind Pulverbeschichtungen aus vielen industriellen Anwendungen nicht mehr wegzudenken.
Die Funktionsweise der Pulverbeschichtung
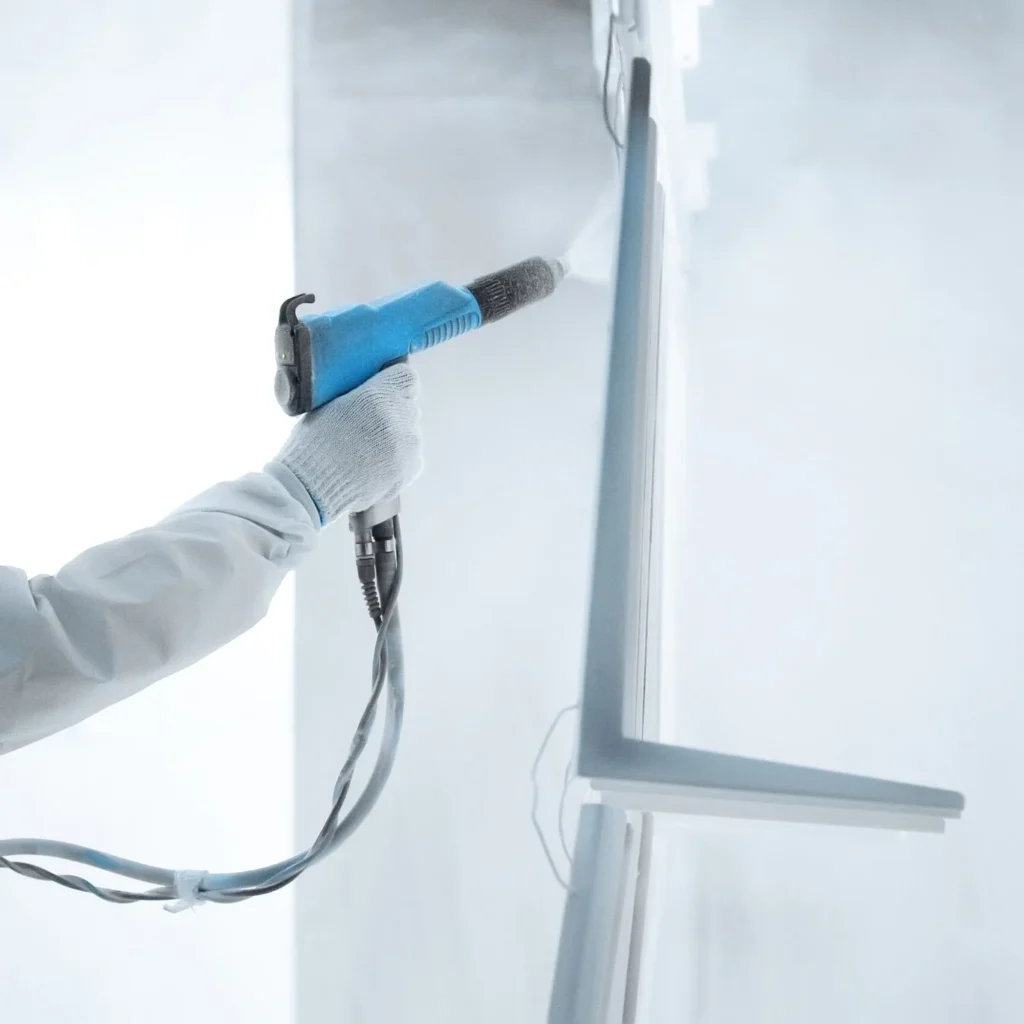
Die Pulverbeschichtung umfasst mehrere wichtige Schritte, die in einem genauen Prozess ablaufen. Jeder Schritt ist entscheidend, um eine gleichmäßige und langlebige Beschichtung zu erreichen.
2.1. Vorbereitung der Oberfläche
Die Vorbereitung der Oberfläche ist ein wesentlicher Schritt, bevor das Pulver aufgetragen werden kann. Eine unzureichende Vorbereitung kann zu schlechter Haftung und Defekten in der Endbeschichtung führen. Der Prozess der Oberflächenvorbereitung umfasst mehrere Schritte:
- Reinigung: Das Entfernen von Schmutz, Öl, Fett, Rost und alten Beschichtungen ist notwendig, um sicherzustellen, dass das Pulver gut haftet. Hierzu werden oft chemische Reiniger oder Entfetter verwendet.
- Strahlen oder Schleifen: Um eine optimale Haftung des Pulvers zu gewährleisten, wird die Oberfläche oft sandgestrahlt oder geschliffen, um eine raue Textur zu schaffen, die das Pulver besser haften lässt.
- Vorbehandlung: Metalloberflächen werden häufig vorbehandelt, z.B. durch Phosphatierung oder Chromatierung, um Korrosion zu verhindern und die Haftung zu verbessern.
2.2. Auftragen des Pulvers
Das Auftragen des Pulvers erfolgt mittels eines elektrostatischen Sprühsystems. Das Pulverlackierverfahren funktioniert auf der Basis von elektrostatischen Kräften:
- Pulversprühpistole: Das Pulver wird durch eine Sprühpistole auf das Werkstück aufgetragen. Die Pistole lädt die Pulverpartikel elektrostatisch auf, während das zu beschichtende Objekt geerdet wird. Dies führt dazu, dass das Pulver durch elektrostatische Anziehung gleichmäßig auf der Oberfläche haftet.
- Automatische und manuelle Beschichtungsverfahren: Je nach Anwendung und Produktionsumgebung können automatische Sprühanlagen oder manuelle Pistolen verwendet werden. Automatische Systeme bieten eine höhere Effizienz bei der Massenproduktion, während manuelle Systeme flexibler und für kleinere Serien oder komplexe Geometrien geeignet sind.
2.3. Einbrennen des Pulvers im Pulverofen
Nach dem Auftragen des Pulvers wird das beschichtete Werkstück in einen Pulverofen gebracht, um das Pulver zu schmelzen und aushärten zu lassen. Dieser Vorgang, der als „Aushärtung“ bezeichnet wird, sorgt dafür, dass das Pulver eine feste, haltbare und glatte Schicht auf dem Werkstück bildet.
- Temperatur und Zeit: Typische Temperaturen für das Einbrennen von Pulverlacken liegen zwischen 150°C und 200°C, und die Aushärtezeit beträgt in der Regel 10 bis 20 Minuten. Diese Parameter variieren jedoch je nach Art des verwendeten Pulvers und der Materialstärke des Werkstücks.
- Verschiedene Ofentypen: Es gibt verschiedene Arten von Öfen für die Pulverbeschichtung, darunter konventionelle Umluftöfen, Infrarotöfen und Gasöfen. Jeder Typ hat seine eigenen Vorteile und ist für bestimmte Anwendungen besser geeignet.
Typen von Pulverbeschichtungen

Es gibt verschiedene Arten von Pulverbeschichtungen, die je nach Anwendung und gewünschten Eigenschaften ausgewählt werden. Die zwei Haupttypen von Pulverbeschichtungen sind Thermoplaste und Duroplaste.
3.1. Thermoplastische Pulverbeschichtungen
Thermoplaste sind Kunststoffe, die beim Erhitzen schmelzen und beim Abkühlen wieder fest werden, ohne dass eine chemische Veränderung stattfindet. Zu den thermoplastischen Pulverbeschichtungen gehören:
- Polyethylen (PE): Wird oft für Beschichtungen auf Metallteilen verwendet, die Flexibilität und Schlagfestigkeit erfordern.
- Polyamid (PA): Wird häufig in der Automobilindustrie eingesetzt, da es eine hohe Beständigkeit gegen Chemikalien und Abrieb aufweist.
- Polyvinylchlorid (PVC): Bietet hervorragende Korrosionsbeständigkeit und wird in der Elektro- und Bauindustrie verwendet.
3.2. Duroplastische Pulverbeschichtungen
Duroplaste, auch als „härtende“ Kunststoffe bekannt, durchlaufen eine chemische Reaktion während des Aushärtens, die irreversible Verbindungen bildet. Die häufigsten duroplastischen Beschichtungen sind:
- Epoxidharze: Bieten eine ausgezeichnete Haftung und chemische Beständigkeit und werden häufig für industrielle Beschichtungen und Korrosionsschutz verwendet.
- Polyester: Diese Beschichtungen sind UV-beständig und eignen sich ideal für Außenanwendungen wie Geländer, Fensterrahmen und Möbel.
- Acrylpulver: Wird verwendet, wenn eine glatte, glänzende Oberfläche benötigt wird. Diese Pulverbeschichtungen bieten eine hervorragende Witterungsbeständigkeit und werden häufig in der Automobilindustrie eingesetzt.
Pulveranlagen: Aufbau und Funktionsweise

Pulveranlagen sind technische Anlagen, die speziell für die Durchführung von Pulverbeschichtungsprozessen konzipiert sind. Sie bestehen aus mehreren Komponenten, die gemeinsam eine effiziente und sichere Durchführung des Beschichtungsprozesses gewährleisten.
4.1. Komponenten einer Pulveranlage
Eine typische Pulveranlage umfasst die folgenden Hauptkomponenten:
- Pulversprühsystem: Besteht aus der Pulversprühpistole, dem Pulverbehälter und dem Zufuhrsystem, das das Pulver zur Pistole führt.
- Fördertechnik: Förderbänder oder Schienensysteme transportieren die Werkstücke durch die verschiedenen Stationen der Anlage, von der Vorbehandlung über die Beschichtung bis zum Aushärten im Ofen.
- Pulverrückgewinnungssysteme: Diese Systeme fangen überschüssiges Pulver auf, das nicht auf das Werkstück aufgetragen wurde, und führen es dem Prozess wieder zu. Dies erhöht die Effizienz und reduziert den Materialverbrauch.
- Steuerungssysteme: Moderne Pulveranlagen sind oft mit computergesteuerten Systemen ausgestattet, die den gesamten Prozess überwachen und steuern. Dies ermöglicht eine präzise Steuerung von Parametern wie Sprühmenge, Luftdruck, Temperatur und Aushärtezeit.
4.2. Automatische und manuelle Pulveranlagen
Es gibt sowohl automatische als auch manuelle Pulveranlagen, die je nach Produktionsvolumen und spezifischen Anforderungen der Beschichtung eingesetzt werden.
- Automatische Pulveranlagen: Diese Systeme sind ideal für die Massenproduktion, da sie eine gleichmäßige Beschichtung mit minimalem Arbeitsaufwand ermöglichen. Sie verwenden Roboterarme oder fest montierte Sprühsysteme, um die Pulverbeschichtung automatisch auf die Werkstücke aufzutragen.
- Manuelle Pulveranlagen: Diese Anlagen sind flexibler und eignen sich besser für kleinere Serien oder Einzelstücke. Der Bediener hat mehr Kontrolle über den Beschichtungsprozess und kann auf komplexe Geometrien oder spezifische Anforderungen eingehen.
5. Pulveröfen: Arten und Funktionsweise
Pulveröfen spielen eine zentrale Rolle im Pulverbeschichtungsprozess, da sie das Pulver erhitzen und die chemische Reaktion einleiten, die für die Bildung einer harten, beständigen Beschichtung erforderlich ist. Es gibt verschiedene Arten von Öfen, die je nach Anwendungsanforderungen und Produktionsumgebung verwendet werden.
5.1. Arten von Pulveröfen
Es gibt mehrere Arten von Öfen, die in der Pulverbeschichtung verwendet werden, darunter:
- Konvektionsöfen: Diese Öfen verwenden heiße Luft, die gleichmäßig durch den Ofen zirkuliert, um das Pulver zu erhitzen. Konvektionsöfen sind die gebräuchlichste Art von Pulveröfen und eignen sich für eine Vielzahl von Anwendungen.
- Infrarotöfen: Infrarotstrahler erhitzen das Pulver schnell, indem sie elektromagnetische Strahlung abgeben, die direkt auf die Oberfläche des Werkstücks wirkt. Diese Art von Ofen eignet sich besonders für schnelle Produktionszyklen oder dünnwandige Teile.
- Gasöfen: Gasbefeuerte Öfen sind oft energieeffizienter und kostengünstiger im Betrieb als elektrische Öfen. Sie sind ideal für große Produktionsanlagen, in denen eine hohe Wärmeleistung erforderlich ist.
- Kombinationsöfen: Diese Öfen kombinieren Konvektions- und Infrarottechnologien, um die Vorteile beider Systeme zu nutzen. Sie bieten eine schnelle Erwärmung und gleichmäßige Wärmeverteilung und sind besonders effizient.
5.2. Aushärteprozess in Pulveröfen
Der Aushärteprozess in einem Pulverofen ist entscheidend für die Bildung der Beschichtung. Wenn das beschichtete Werkstück in den Ofen kommt, schmilzt das Pulver allmählich und vernetzt sich chemisch zu einer festen Schicht. Die Temperatur und die Dauer des Aushärtens hängen von der Art des Pulvers und dem Material des Werkstücks ab.
- Typische Aushärtetemperaturen: Pulverlacke werden in der Regel bei Temperaturen zwischen 150°C und 200°C ausgehärtet. Zu niedrige Temperaturen können dazu führen, dass das Pulver nicht vollständig schmilzt, während zu hohe Temperaturen das Werkstück beschädigen können.
- Aushärtezeit: Die Aushärtezeit liegt normalerweise zwischen 10 und 20 Minuten, kann aber je nach Größe und Dicke des Werkstücks sowie der Art des Pulvers variieren. Eine längere Aushärtezeit kann erforderlich sein, um eine vollständige Vernetzung zu gewährleisten und die mechanischen Eigenschaften der Beschichtung zu maximieren.
5.3. Energieeffizienz von Pulveröfen
Moderne Pulveröfen sind oft darauf ausgelegt, den Energieverbrauch zu minimieren. Gasöfen bieten in der Regel eine höhere Energieeffizienz im Vergleich zu elektrisch betriebenen Öfen. Einige Öfen sind zudem mit Wärmerückgewinnungssystemen ausgestattet, die die Abwärme aus dem Aushärtungsprozess nutzen, um den Energieverbrauch weiter zu senken.
6. Vorteile der Pulverbeschichtung
Die Pulverbeschichtung bietet gegenüber herkömmlichen Flüssiglackierverfahren zahlreiche Vorteile. Diese Vorteile betreffen nicht nur die Qualität und Haltbarkeit der Beschichtung, sondern auch Umweltaspekte und Kosteneffizienz.
6.1. Umweltfreundlichkeit
Einer der größten Vorteile der Pulverbeschichtung ist ihre Umweltfreundlichkeit. Da Pulverbeschichtungen keine Lösungsmittel enthalten, werden keine flüchtigen organischen Verbindungen (VOCs) freigesetzt, die zu Luftverschmutzung beitragen können. Dies macht Pulverbeschichtungen zu einer umweltfreundlichen Alternative zu herkömmlichen Flüssiglacken.
- Weniger Abfall: Das überschüssige Pulver kann aufgefangen und wiederverwendet werden, was den Materialverbrauch reduziert und Abfall minimiert.
- Sicher für Arbeiter: Da keine Lösungsmittel verwendet werden, sind Pulverbeschichtungen auch sicherer für die Arbeiter, da keine giftigen Dämpfe freigesetzt werden, die eingeatmet werden könnten.
6.2. Haltbarkeit und Widerstandsfähigkeit
Pulverbeschichtungen bieten eine extrem widerstandsfähige Oberfläche, die gegen Abnutzung, Kratzer, Korrosion und chemische Einflüsse beständig ist. Diese Eigenschaften machen Pulverbeschichtungen besonders attraktiv für industrielle Anwendungen, bei denen Langlebigkeit und Widerstandsfähigkeit entscheidend sind.
- Korrosionsschutz: Pulverbeschichtungen bieten einen hervorragenden Korrosionsschutz, der sie ideal für Anwendungen im Außenbereich macht, z.B. bei Möbeln, Fassaden und Fahrzeugen.
- Beständigkeit gegen Chemikalien: Pulverbeschichtungen sind auch gegen viele Chemikalien beständig, was sie zu einer idealen Wahl für industrielle Anlagen und Maschinen macht, die aggressiven Substanzen ausgesetzt sind.
6.3. Kosteneffizienz
Obwohl die Anschaffung von Pulveranlagen und Öfen zunächst mit höheren Kosten verbunden ist, amortisieren sich diese Investitionen schnell aufgrund der zahlreichen Kosteneinsparungen, die die Pulverbeschichtung bietet:
- Materialeinsparungen: Dank der Möglichkeit, überschüssiges Pulver wiederzuverwenden, werden Materialkosten gesenkt.
- Weniger Nacharbeiten: Da Pulverbeschichtungen eine gleichmäßige und hochwertige Oberfläche bieten, sind weniger Nacharbeiten oder Korrekturen erforderlich.
- Längere Lebensdauer: Die Haltbarkeit der Beschichtung reduziert die Notwendigkeit für häufige Wartung oder Neubeschichtung, was langfristig Kosten spart.
6.4. Ästhetische Vielfalt
Pulverbeschichtungen bieten eine breite Palette an Farben und Texturen. Im Gegensatz zu Flüssiglacken, die oft in ihrer Farbauswahl begrenzt sind, können Pulverbeschichtungen in nahezu jeder gewünschten Farbe hergestellt werden, einschließlich Glanz-, Matt- und Metallic-Finishes. Auch strukturierte Beschichtungen wie Hammerschlag oder Samtoberflächen sind problemlos umsetzbar.
- UV-Beständigkeit: Polyesterpulverlacke bieten eine hervorragende UV-Beständigkeit und sind ideal für den Einsatz im Außenbereich, da sie nicht verblassen oder vergilben.
- Glatte oder strukturierte Oberflächen: Pulverbeschichtungen ermöglichen es, eine Vielzahl von Oberflächenstrukturen zu erzielen, von glatten und glänzenden bis hin zu rauen und strukturierten Oberflächen.
7. Anwendungsgebiete der Pulverbeschichtung
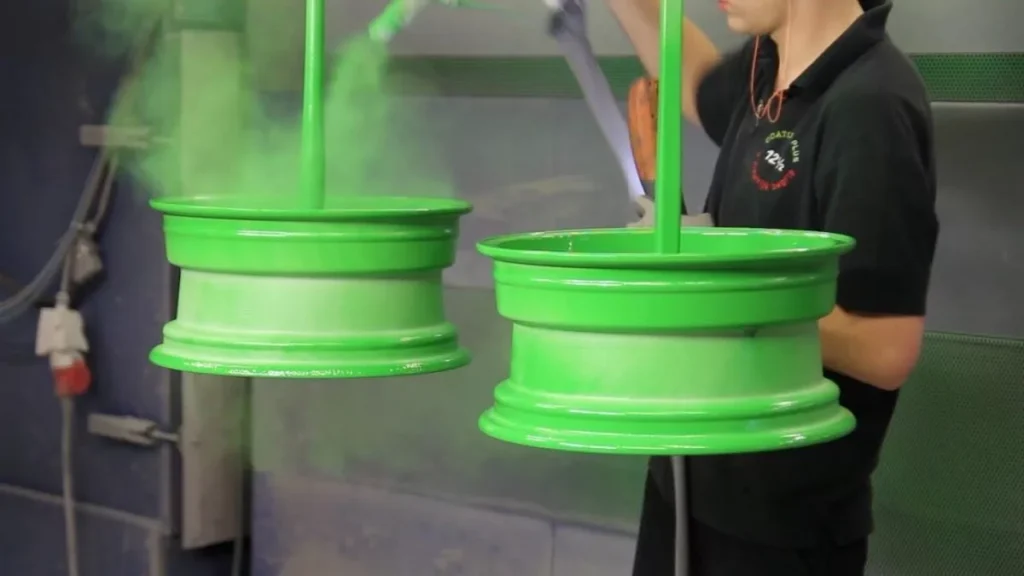
Die Pulverbeschichtung wird in einer Vielzahl von Branchen und Anwendungen eingesetzt. Ihre Vielseitigkeit und Haltbarkeit machen sie zur idealen Wahl für eine breite Palette von Projekten, von industriellen Maschinen bis hin zu Konsumgütern.
7.1. Automobilindustrie
Die Automobilindustrie ist einer der größten Anwender von Pulverbeschichtungen. Fahrzeugteile wie Felgen, Fahrgestelle, Stoßstangen und Außenverkleidungen werden oft mit Pulverbeschichtungen behandelt, um sie vor Korrosion und Verschleiß zu schützen. Pulverbeschichtungen bieten auch die Möglichkeit, Fahrzeugteile in einer Vielzahl von Farben und Oberflächenstrukturen zu gestalten.
7.2. Architektur und Bauwesen
Im Bauwesen werden Pulverbeschichtungen für die Beschichtung von Metallkonstruktionen, Fassaden, Türen, Fensterrahmen und Geländern verwendet. Ihre Witterungsbeständigkeit und Korrosionsschutz machen sie ideal für Anwendungen im Außenbereich. Außerdem bieten Pulverbeschichtungen eine große Farbauswahl, was Architekten und Designern zusätzliche Flexibilität bei der Gestaltung von Gebäuden gibt.
7.3. Möbelindustrie
Die Möbelindustrie verwendet Pulverbeschichtungen, um Metallmöbel vor Korrosion zu schützen und ihnen ein ästhetisch ansprechendes Aussehen zu verleihen. Gartenmöbel, Büromöbel und Designermöbel profitieren gleichermaßen von der Langlebigkeit und Widerstandsfähigkeit der Pulverbeschichtung.
7.4. Haushaltsgeräte
Viele Haushaltsgeräte, wie Waschmaschinen, Kühlschränke und Öfen, werden mit Pulverbeschichtungen versehen, um sie vor Abnutzung und Korrosion zu schützen. Pulverbeschichtungen bieten nicht nur Schutz, sondern auch ein attraktives Finish, das in einer Vielzahl von Farben und Oberflächen erhältlich ist.
7.5. Elektronikindustrie
In der Elektronikindustrie werden Pulverbeschichtungen oft für Gehäuse und Komponenten verwendet, die Schutz vor elektromagnetischen Störungen (EMI) bieten müssen. Pulverbeschichtungen schützen die empfindlichen elektronischen Komponenten vor äußeren Einflüssen und tragen zur Langlebigkeit der Produkte bei.
8. Zukunft der Pulverbeschichtungstechnologie
Die Technologie der Pulverbeschichtung entwickelt sich kontinuierlich weiter, um den Anforderungen moderner Industrieprozesse gerecht zu werden. Nachhaltigkeit, Effizienz und neue Materialien sind zentrale Treiber der technologischen Weiterentwicklung.
8.1. Nachhaltigkeit und Umweltbewusstsein
Mit zunehmendem Fokus auf Umweltschutz wird die Pulverbeschichtung weiterhin als bevorzugte Alternative zu Flüssiglacken an Bedeutung gewinnen. Forscher arbeiten kontinuierlich an der Entwicklung neuer Pulverformeln, die noch umweltfreundlicher sind, indem sie den Energieverbrauch und die Produktionsabfälle weiter reduzieren.
8.2. Fortschritte in der Materialwissenschaft
Die Entwicklung neuer Beschichtungsmaterialien bietet der Pulverbeschichtungstechnologie großes Potenzial. Die Einführung von Nanopartikeln in Pulverlacke könnte beispielsweise zu noch widerstandsfähigeren und leistungsfähigeren Beschichtungen führen, die überlegene Eigenschaften in Bezug auf Kratzfestigkeit, UV-Beständigkeit und Selbstreinigung bieten.
8.3. Digitalisierung und Automatisierung
Moderne Produktionsanlagen werden zunehmend automatisiert und digitalisiert. Dies gilt auch für Pulverbeschichtungsanlagen, die mit fortschrittlichen Steuerungssystemen und Robotik ausgestattet sind, um den Beschichtungsprozess noch effizienter und präziser zu gestalten. Datenanalyse und Sensorik ermöglichen es, die Qualität in Echtzeit zu überwachen und den Energieverbrauch zu optimieren.
9. Fazit
Die Pulverbeschichtung ist eine vielseitige und kosteneffiziente Methode zur Oberflächenveredelung, die in vielen Branchen breite Anwendung findet. Sie bietet Vorteile in Bezug auf Umweltfreundlichkeit, Langlebigkeit, Ästhetik und Kosteneinsparungen. Pulveranlagen und Pulveröfen sind wesentliche Bestandteile dieses Verfahrens und tragen maßgeblich zur Qualität und Effizienz des Beschichtungsprozesses bei.
Mit kontinuierlichen technologischen Fortschritten in Bereichen wie Nachhaltigkeit, Automatisierung und Materialwissenschaft bleibt die Pulverbeschichtung eine führende Technik in der Oberflächenveredelung und wird auch in Zukunft eine entscheidende Rolle in der industriellen Fertigung spielen.