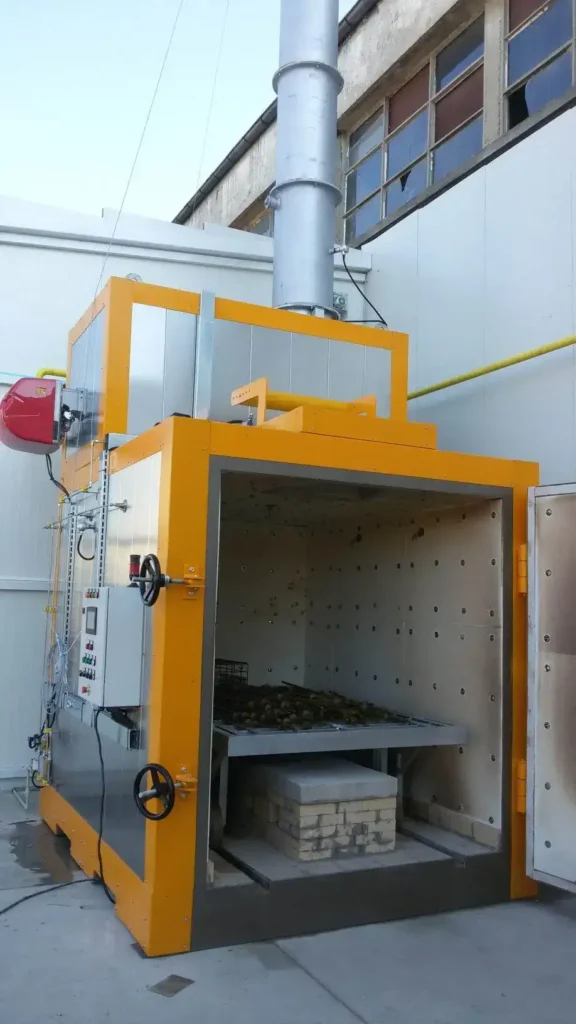
Ein Pyrolyseofen ist ein innovatives Küchengerät, das auf dem Prinzip der Pyrolyse basiert, um eine effiziente und gründliche Reinigung zu ermöglichen. Die Pyrolyse ist ein Prozess, bei dem der Ofen auf extrem hohe Temperaturen erhitzt wird, in der Regel über 500°C. Dies hat den Zweck, alle anhaftenden Rückstände, wie Essensreste, Fett und Verunreinigungen, in Asche zu verwandeln.
Der Reinigungszyklus eines Pyrolyseofens ist einfach zu handhaben. Nachdem der Benutzer den Pyrolysemodus aktiviert hat, erhitzt sich der Ofen automatisch auf die erforderliche Temperatur. Während dieses Prozesses werden organische Rückstände zersetzt und in Asche umgewandelt, wodurch sie leicht zu entfernen sind. Nach Abschluss des Pyrolysezyklus kann die Asche einfach mit einem feuchten Tuch oder Schwamm entfernt werden, und der Ofen erstrahlt wieder in neuem Glanz.
Ein großer Vorteil dieser Reinigungsmethode ist ihre Umweltfreundlichkeit. Da keine chemischen Reinigungsmittel benötigt werden, werden weder schädliche Dämpfe freigesetzt noch Abwasser mit aggressiven Substanzen erzeugt. Dies trägt zu einer nachhaltigeren und umweltbewussteren Haushaltsführung bei.
Die meisten Pyrolyseöfen sind mit modernster Technologie ausgestattet, um den Benutzern maximale Bequemlichkeit zu bieten. Intuitive Bedienfelder, programmierbare Reinigungszyklen und Sicherheitsfunktionen tragen dazu bei, die Nutzung dieser Geräte so einfach und sicher wie möglich zu gestalten.
Es ist jedoch wichtig zu beachten, dass Pyrolyseöfen nicht nur aufgrund ihrer Reinigungsfunktion geschätzt werden. Sie bieten auch erstklassige Back- und Kochergebnisse, da sie oft mit fortschrittlichen Heiztechnologien und präzisen Temperaturregelungen ausgestattet sind.
Insgesamt repräsentiert der Pyrolyseofen einen bedeutenden Fortschritt in der Küchentechnologie, indem er nicht nur effektive Reinigungsmöglichkeiten bietet, sondern auch die Energieeffizienz und Benutzerfreundlichkeit in der Küche verbessert. Mit seinem modernen Design und seinen innovativen Funktionen ist der Pyrolyseofen zweifellos eine Bereicherung für jeden Haushalt.
Pyrolyseofen Ausbrennofen
Die Pyrolyseofen-Technologie hat auch in der Welt der Pulverbeschichtung einen bedeutenden Einfluss und ermöglicht fortschrittliche Verfahren für die Aushärtung von Pulverbeschichtungen. Ein Pyrolyseofen für Pulverbeschichtung ist darauf ausgelegt, die Pulverlacke durch pyrolytische Prozesse zu härten, wodurch eine strapazierfähige und äußerst haltbare Oberflächenbeschichtung entsteht.
Die Kernfunktion eines Pyrolyseofens für Pulverbeschichtung liegt in seiner Fähigkeit, die notwendigen Temperaturen präzise zu erreichen und zu halten. In einem solchen Ofen wird das mit Pulverlack beschichtete Werkstück in eine spezielle Kammer platziert, wo es dann durch den Pyrolyseprozess geleitet wird. Die extremen Temperaturen, die oft über 200°C liegen, bewirken, dass das Pulver schmilzt, fließt und schließlich zu einer homogenen Beschichtung aushärtet.
Der Vorteil der Pyrolyseofen-Technologie in der Pulverbeschichtung liegt nicht nur in der Effizienz des Aushärtungsprozesses, sondern auch in der Umweltfreundlichkeit. Im Vergleich zu herkömmlichen Beschichtungsmethoden mit Lösungsmitteln werden bei der Pulverbeschichtung keine schädlichen Dämpfe freigesetzt. Die Pyrolyse ermöglicht es, dieses umweltfreundliche Verfahren auf einem präzisen und kontrollierten Niveau durchzuführen.
Ein weiterer wichtiger Aspekt ist die Kosteneffizienz, die durch die Verwendung eines Pyrolyseofens für Pulverbeschichtung erzielt wird. Die präzise Temperaturkontrolle und der effiziente Energieverbrauch tragen dazu bei, die Betriebskosten zu minimieren und die Produktivität zu maximieren.
Moderne Pyrolyseöfen für die Pulverbeschichtung sind oft mit fortschrittlichen Steuerungssystemen ausgestattet, die eine einfache Programmierung, Überwachung und Anpassung der Prozessparameter ermöglichen. Dies trägt dazu bei, konsistente und qualitativ hochwertige Ergebnisse sicherzustellen.
Zusammenfassend lässt sich sagen, dass Pyrolyseöfen für die Pulverbeschichtung eine revolutionäre Entwicklung in der Oberflächenbeschichtungsindustrie darstellen. Durch ihre Fähigkeit, präzise Temperaturen zu erreichen und zu halten, ermöglichen sie eine effiziente und umweltfreundliche Pulverhärtung, die zu widerstandsfähigen und attraktiven Oberflächen führt. Mit fortschrittlichen Funktionen und Technologien sind sie ein unverzichtbares Werkzeug in modernen Produktionsstätten, die höchste Qualitätsstandards und Effizienz anstreben.
Ausbrennofen

Ein Ausbrennofen ist ein spezieller Ofen, der in verschiedenen industriellen Anwendungen, Kunsthandwerk und sogar in der Zahnmedizin verwendet wird. Der Begriff „Ausbrennofen“ bezieht sich auf einen Ofen, der dazu dient, Materialien auszubrennen oder zu entfernen, oft um Hohlräume oder negative Formen zu schaffen. Hier sind einige der häufigsten Verwendungszwecke von Ausbrennöfen:
- Dentaltechnik: In der Zahnmedizin wird ein Ausbrennofen verwendet, um Gussformen von Zahnabdrücken herzustellen. Das Verfahren umfasst das Ausbrennen von wachsähnlichem Material aus der Form, um einen leeren Hohlraum zu schaffen, der dann mit einem geeigneten Gießmaterial, wie z.B. Metalllegierungen, gefüllt wird.
- Schmuckherstellung: Ausbrennöfen werden in der Schmuckherstellung eingesetzt, um Wachsmuster von Schmuckstücken zu schmelzen und zu entfernen, bevor das flüssige Metall eingegossen wird. Dies ermöglicht die Herstellung von präzisen, feinen Details in Metallformen.
- Keramikherstellung: In der Keramikindustrie wird ein Ausbrennofen verwendet, um organische Bestandteile aus keramischen Formen zu entfernen. Dies geschieht oft vor dem Brennvorgang, um sicherzustellen, dass die Keramik keine unerwünschten Rückstände enthält.
- 3D-Druck: Bei der Herstellung von Teilen durch 3D-Druck können Ausbrennöfen verwendet werden, um stützendes Material, das während des Druckvorgangs hinzugefügt wurde, zu entfernen. Dies ist besonders relevant bei Verfahren wie dem Wachsmuster-3D-Druck.
- Industrielle Anwendungen: In einigen industriellen Prozessen werden Ausbrennöfen verwendet, um unerwünschte organische Materialien oder Verbindungen aus bestimmten Produkten oder Materialien zu entfernen.
Die Funktionsweise eines Ausbrennofens variiert je nach Anwendung und dem zu behandelnden Material. Einige Ausbrennöfen sind auf bestimmte Temperaturen und Prozesse spezialisiert, um optimale Ergebnisse zu erzielen. Moderne Ausbrennöfen können oft programmierbare Steuerungen und Präzisionsmessgeräte für eine genaue Temperaturkontrolle und Konsistenz bieten.
Ein Ausbrennofen für Pulver wird in industriellen Prozessen eingesetzt, um organische oder flüchtige Bestandteile aus einem pulverförmigen Material zu entfernen. Dieser Prozess ist besonders relevant in der Pulvermetallurgie und der Herstellung von Pulverbeschichtungen. Hier sind einige Schlüsselaspekte im Zusammenhang mit einem Ausbrennofen für Pulver:
- Pulvermetallurgie: In der Herstellung von Metallpulvern werden oft organische Bindemittel oder andere flüchtige Stoffe verwendet, um das Pulver in eine bestimmte Form zu bringen. Ein Ausbrennofen wird dann eingesetzt, um diese Bindemittel zu entfernen und das Metallpulver in seiner reinen Form zu hinterlassen. Dieser Vorgang wird als „Debinding“ bezeichnet und bereitet das Pulver auf den nachfolgenden Sinterprozess vor.
- Pulverbeschichtung: Bei der Herstellung von Pulverbeschichtungen, die auf Metalloberflächen aufgetragen werden, wird ein Ausbrennofen verwendet, um das aufgebrachte Pulver zu schmelzen und zu härten. Während dieses Prozesses werden auch flüchtige Bestandteile, wie Bindemittel und Lösungsmittel, entfernt, um eine dauerhafte und feste Beschichtung zu gewährleisten.
- Keramikpulver: In der Keramikindustrie können Ausbrennöfen verwendet werden, um organische Bestandteile aus keramischen Pulvern zu entfernen, bevor sie zu einem festen Material geformt und gesintert werden.
Die Funktionsweise eines Ausbrennofens für Pulver hängt von den spezifischen Anforderungen des Prozesses ab. In der Regel erfolgt der Vorgang in einem kontrollierten Temperatur- und Zeitrahmen, um sicherzustellen, dass die flüchtigen Bestandteile effizient entfernt werden, ohne das Pulver zu beeinträchtigen.
Moderne Ausbrennöfen können mit fortschrittlichen Steuerungssystemen ausgestattet sein, die eine präzise Regelung der Temperatur und anderer Parameter ermöglichen. Dies trägt dazu bei, konsistente Ergebnisse und eine optimale Qualität des Endprodukts sicherzustellen.
In der Industrie sind Ausbrennöfen für Pulver ein entscheidendes Werkzeug, um hochwertige Pulvermetallurgieprodukte und Pulverbeschichtungen herzustellen, indem sie eine gründliche Entfernung von Bindemitteln und anderen flüchtigen Komponenten ermöglichen.
- Debinding: Der Prozess des Entfernens von organischen Bindemitteln oder flüchtigen Bestandteilen aus dem Pulver im Ausbrennofen.
- Pulvermetallurgie: Die Herstellung von Metallpulvern und deren anschließende Verarbeitung im Ausbrennofen, um das Pulver für den Sinterprozess vorzubereiten.
- Sintervorbereitung: Der Ausbrennofen wird verwendet, um Metallpulver vor dem Sintern von organischen Bindemitteln zu befreien und das Pulver zu reinigen.
- Pulverbeschichtung: Der Ausbrennofen in der Pulverbeschichtungsindustrie, der dazu dient, das aufgebrachte Pulver zu schmelzen und zu härten, während organische Bestandteile entfernt werden.
- Temperaturkontrolle: Ein Schlüsselaspekt des Ausbrennofenprozesses, um die richtige Temperatur für den Debinding- oder Härtevorgang sicherzustellen.
- Entgasung: Der Prozess der Entfernung von Gasen oder flüchtigen Bestandteilen aus dem Pulver während des Ausbrennofens.
- Keramikpulver: Verwendung des Ausbrennofens in der Keramikindustrie, um organische Bestandteile aus keramischen Pulvern zu entfernen.
- Bindemittelentfernung: Der Ausbrennofen spielt eine zentrale Rolle bei der Entfernung von Bindemitteln, die in der Pulvermetallurgie und anderen pulverbasierten Prozessen verwendet werden.
- Pulverentgasung: Der Ausbrennofen wird genutzt, um gasförmige Verunreinigungen oder flüchtige Stoffe aus dem Pulver zu entfernen.
- Sinterprozessvorbereitung: Der Ausbrennofen als entscheidender Schritt, um Pulver für den Sinterprozess vorzubereiten, bei dem das Pulver zu einem festen Material zusammengefügt wird.
Debinding:
Der Begriff „Debinding“ bezieht sich auf den entscheidenden Prozess der Entfernung von organischen Bindemitteln oder flüchtigen Bestandteilen aus einem Pulvermaterial. Dieser Vorgang ist von entscheidender Bedeutung in verschiedenen industriellen Anwendungen, insbesondere in der Pulvermetallurgie und der Herstellung von Pulverbeschichtungen.
In der Pulvermetallurgie wird der Debinding-Prozess verwendet, um Metallpulver von organischen Bindemitteln zu befreien, die während des Formgebungsprozesses verwendet wurden. Diese Bindemittel dienen dazu, das Metallpulver zu einer bestimmten Form zu bringen, bevor es im Ausbrennofen behandelt wird. Während des Debinding-Prozesses werden die organischen Substanzen durch Erhitzen auf eine bestimmte Temperatur entfernt, wodurch das Metallpulver für den nachfolgenden Sinterprozess vorbereitet wird. Der Erfolg dieses Schrittes beeinflusst direkt die Qualität und Eigenschaften des endgültigen metallischen Produkts.
In der Pulverbeschichtung wird der Debinding-Prozess ebenfalls eingesetzt, um Pulverbeschichtungen von organischen Bindemitteln zu befreien, bevor das Pulver geschmolzen und ausgehärtet wird. Dieser Schritt ist entscheidend für die Herstellung strapazierfähiger, hochwertiger Beschichtungen auf Metalloberflächen.
Die Temperaturkontrolle spielt eine Schlüsselrolle im Debinding-Prozess, da sie sicherstellen muss, dass die organischen Bestandteile vollständig entfernt werden, ohne das Pulver zu überhitzen oder zu beschädigen. Moderne Ausbrennöfen sind mit präzisen Temperaturregelungen ausgestattet, um eine optimale Debinding-Leistung zu gewährleisten.
Zusammenfassend lässt sich sagen, dass der Debinding-Prozess ein kritischer Schritt in der Pulververarbeitung ist, der die Grundlage für hochwertige Metallprodukte und Pulverbeschichtungen legt, indem er organische Bindemittel effizient entfernt.
Pulvermetallurgie:
Die Pulvermetallurgie ist ein faszinierender Bereich der Materialwissenschaft und Ingenieurwissenschaft, der die Herstellung von Metallteilen durch die Verwendung von Metallpulvern als Ausgangsmaterial umfasst. Dieser Prozess ermöglicht die Herstellung von Präzisionsteilen mit spezifischen Eigenschaften, die durch herkömmliche Fertigungsmethoden schwer zu erreichen wären.
Im Kern der Pulvermetallurgie steht die Verwendung von Metallpulvern, die durch Mahlen von Metalllegierungen oder anderen Metallquellen gewonnen werden. Diese Pulver werden dann zu einer bestimmten Form gebracht, häufig durch Pressen oder Spritzgießen, um das gewünschte Bauteil vorzubereiten.
Ein entscheidender Schritt in der Pulvermetallurgie ist der Debinding-Prozess, der organische Bindemittel aus dem Pulver entfernt, um es für den nachfolgenden Sinterprozess vorzubereiten. Dieser Sinterprozess umfasst das Erhitzen des Pulvers auf hohe Temperaturen, wodurch die Partikel miteinander verschmelzen und das endgültige Bauteil entsteht.
Die Pulvermetallurgie bietet zahlreiche Vorteile, darunter die Möglichkeit, komplexe Formen mit hoher Präzision herzustellen, eine verbesserte Materialhomogenität und die Fähigkeit, Materialien mit spezifischen mechanischen Eigenschaften zu entwickeln. Durch den Einsatz fortschrittlicher Technologien, wie beispielsweise Ausbrennöfen für den Debinding-Prozess, wird die Pulvermetallurgie immer präziser und effizienter.
Diese fortschrittliche Fertigungstechnik findet Anwendung in verschiedenen Branchen, darunter Automobilbau, Luft- und Raumfahrt, Medizintechnik und Elektronik. Die Pulvermetallurgie ermöglicht die Herstellung von Teilen mit hoher Festigkeit, ausgezeichneter Verschleißfestigkeit und anderen maßgeschneiderten Eigenschaften, was sie zu einer vielseitigen und leistungsstarken Methode in der modernen Produktion macht.
Sintervorbereitung:
Die Sintervorbereitung ist ein entscheidender Schritt in der Pulvermetallurgie, bei dem das vorbereitete Metallpulver durch Hitzebehandlung zu einem festen, dichten Werkstück verschmolzen wird. Dieser Prozess, als Sintern bekannt, führt zu einer erhöhten Dichte, mechanischen Festigkeit und anderen gewünschten Eigenschaften des Endprodukts.
Bevor das Pulver gesintert wird, muss es jedoch einer Sintervorbereitung unterzogen werden, und hier kommt der Ausbrennofen ins Spiel. Der Ausbrennofen wird verwendet, um organische Bindemittel oder flüchtige Bestandteile aus dem Pulver zu entfernen, in einem Prozess, der als „Debinding“ bekannt ist. Diese organischen Bindemittel werden zuvor verwendet, um das Pulver in eine bestimmte Form zu bringen.
Der Debinding-Prozess ist entscheidend, da er sicherstellen muss, dass das Pulver frei von organischen Materialien ist, bevor es dem Sinterprozess unterzogen wird. Wenn organische Bindemittel während des Sinterns vorhanden sind, können unerwünschte Gase freigesetzt werden, was zu Defekten im Endprodukt führen kann.
Ein gut gesteuerter Ausbrennofen sorgt dafür, dass die organischen Bestandteile bei genau kontrollierten Temperaturen entfernt werden, wodurch das Pulver optimal auf den Sinterprozess vorbereitet wird. Dieser Vorbereitungsschritt beeinflusst direkt die Qualität, Festigkeit und Homogenität des endgültigen Metallteils.
Die Sintervorbereitung ist somit ein kritischer Schritt in der Pulvermetallurgie, der die Grundlage für hochwertige, maßgeschneiderte Metallteile legt. Mit modernen Ausbrennöfen und präzisen Temperaturkontrollen wird dieser Prozess effizienter und ermöglicht die Herstellung von qualitativ hochwertigen Metallkomponenten in verschiedenen Industriezweigen.
Pulverbeschichtung:
Die Pulverbeschichtung ist eine weit verbreitete Methode zur Oberflächenveredelung von Metallteilen und anderen Substraten. Bei diesem Verfahren wird trockenes Pulver auf die zu beschichtende Oberfläche aufgetragen und anschließend durch Wärme oder UV-Licht geschmolzen und gehärtet. Ein wesentlicher Bestandteil dieses Prozesses ist der Einsatz eines Ausbrennofens, der mehrere Schlüsselrollen spielt.
Der erste Schritt in der Pulverbeschichtung ist das Aufbringen des Pulvers auf das Substrat. Dies kann durch Sprühen, Tauchen oder elektrostatische Aufladung erfolgen. Das aufgebrachte Pulver enthält in der Regel Bindemittel und gegebenenfalls auch Farbstoffe oder andere Zusätze, um spezifische Eigenschaften zu erzielen.
Nach dem Auftragen des Pulvers erfolgt der Übergang in den Ausbrennofen. Hier wird das Substrat auf Temperaturen erhitzt, die ausreichen, um das Pulver zu schmelzen und zu härten. Während dieses Prozesses werden organische Bindemittel und flüchtige Bestandteile aus dem Pulver entfernt, und das geschmolzene Pulver bildet eine gleichmäßige und haltbare Beschichtung auf der Oberfläche des Substrats.
Die Temperaturkontrolle im Ausbrennofen ist entscheidend, um sicherzustellen, dass die Beschichtung die gewünschten mechanischen Eigenschaften, Haftfestigkeit und Ästhetik aufweist. Moderne Ausbrennöfen bieten präzise Steuerungsoptionen, um den Temperaturverlauf während des Prozesses zu überwachen und anzupassen.
Die Pulverbeschichtung hat zahlreiche Vorteile, darunter eine hohe Beständigkeit gegenüber Chemikalien, UV-Strahlung und Kratzern. Sie wird in verschiedenen Branchen eingesetzt, einschließlich der Automobilindustrie, Architektur, Elektronik und Möbelherstellung, um hochwertige Oberflächen mit einer breiten Palette von Farben und Effekten zu erzielen. Der Ausbrennofen spielt eine zentrale Rolle bei der Gewährleistung der Qualität und Haltbarkeit von Pulverbeschichtungen.
Temperaturkontrolle:
Die Temperaturkontrolle ist ein grundlegender Aspekt in verschiedenen industriellen Prozessen und spielt eine entscheidende Rolle in der Gewährleistung von Qualität, Effizienz und Sicherheit. Insbesondere in Zusammenhang mit Ausbrennöfen, wie sie in der Pulvermetallurgie oder der Pulverbeschichtung verwendet werden, ist eine präzise Temperaturkontrolle von essenzieller Bedeutung.
In der Pulvermetallurgie wird die Temperaturkontrolle während des Debinding- und Sinterprozesses gewährleistet, um sicherzustellen, dass organische Bindemittel effizient entfernt werden und das Metallpulver optimal verschmolzen wird. Der Ausbrennofen spielt hierbei eine Schlüsselrolle, indem er die eingestellten Temperaturen präzise erreicht und aufrechterhält. Eine fehlerhafte Temperaturkontrolle könnte zu unvollständigem Debonding oder unsachgemäßem Sintern führen, was die Qualität der hergestellten Metallteile beeinträchtigen würde.
In der Pulverbeschichtung ist die Temperaturkontrolle im Ausbrennofen entscheidend für die richtige Aushärtung des aufgebrachten Pulvers. Unterschiedliche Pulverzusammensetzungen erfordern spezifische Temperaturen, um die gewünschten mechanischen Eigenschaften und die Haftfestigkeit der Beschichtung zu gewährleisten. Eine exakte Temperaturführung im Ausbrennofen ist notwendig, um Überhitzung oder Unterhitzung zu vermeiden, was zu Mängeln in der Beschichtung führen kann.
Moderne Ausbrennöfen verfügen über fortschrittliche Steuerungssysteme, die eine präzise Einstellung und Überwachung der Temperatur ermöglichen. Dies gewährleistet nicht nur die Qualität der Endprodukte, sondern trägt auch zur Energieeffizienz und Sicherheit der Fertigungsprozesse bei.
Insgesamt ist die Temperaturkontrolle ein unerlässlicher Faktor für die erfolgreiche Anwendung von Ausbrennöfen in verschiedenen industriellen Anwendungen, und sie spielt eine zentrale Rolle in der Erzielung qualitativ hochwertiger und konsistenter Ergebnisse.
Entgasung:
Der Begriff „Entgasung“ bezieht sich auf den Prozess der Entfernung von Gasen oder flüchtigen Bestandteilen aus einem Material oder einer Substanz. In verschiedenen industriellen Anwendungen, darunter die Pulvermetallurgie und die Herstellung von Beschichtungen, spielt die Entgasung eine entscheidende Rolle für die Qualität und Leistung der Endprodukte.
In der Pulvermetallurgie wird der Ausbrennofen häufig zur Entgasung eingesetzt, insbesondere während des Debinding-Prozesses. Hier werden organische Bindemittel und flüchtige Bestandteile aus dem Metallpulver entfernt. Während dieses Vorgangs werden nicht nur die organischen Komponenten, sondern auch Gase, die während des Herstellungsprozesses eingefangen wurden, aus dem Pulver ausgetrieben. Eine effektive Entgasung ist entscheidend, um die Bildung von Poren oder Lunkerstellen in den gesinterten Metallteilen zu minimieren.
In der Pulverbeschichtung spielt die Entgasung ebenfalls eine wichtige Rolle. Bei der Erhitzung des aufgebrachten Pulvers im Ausbrennofen werden nicht nur organische Bindemittel entfernt, sondern auch eingeschlossene Gase. Dies ist wichtig, um sicherzustellen, dass die Beschichtung gleichmäßig und ohne Blasen oder Hohlräume aushärtet. Eine effiziente Entgasung trägt somit zur Qualität und Haltbarkeit der Pulverbeschichtung bei.
Moderne Ausbrennöfen werden oft mit speziellen Entgasungsfunktionen ausgestattet, um sicherzustellen, dass während des thermischen Prozesses Gase effektiv entfernt werden. Dies verbessert nicht nur die Qualität der Endprodukte, sondern trägt auch zur Prozessstabilität und -effizienz bei.
Zusammenfassend lässt sich sagen, dass die Entgasung eine kritische Komponente in verschiedenen Herstellungsprozessen ist, in denen Ausbrennöfen verwendet werden. Sie hilft, Defekte zu minimieren, die Qualität zu verbessern und sicherzustellen, dass die hergestellten Produkte den gewünschten Spezifikationen entsprechen.
Keramikpulver:
Keramikpulver spielt eine entscheidende Rolle in verschiedenen industriellen Anwendungen, insbesondere in der Keramikherstellung. Keramik wird oft aus feinen Pulvern hergestellt, die durch Sintern zu festen und oft sehr haltbaren Strukturen geformt werden. Der Einsatz eines Ausbrennofens in Verbindung mit Keramikpulver ist bei verschiedenen Prozessen von großer Bedeutung.
In der Keramikherstellung wird Keramikpulver häufig zu einer spezifischen Form gebracht, sei es durch Pressen, Gießen oder Sprühen. Um eine homogene und robuste Struktur zu erreichen, werden organische Bindemittel oder flüchtige Bestandteile dem Pulver hinzugefügt. Hier kommt der Ausbrennofen ins Spiel, um diese organischen Bestandteile zu entfernen.
Während des Ausbrennprozesses im Ofen werden die organischen Bestandteile bei hohen Temperaturen durch Pyrolyse in Gas umgewandelt und aus dem Keramikpulver ausgetrieben. Dieser Debinding-Prozess bereitet das Keramikpulver auf das anschließende Sintern vor, bei dem das Pulver zu einem festen und dichten Keramikmaterial verschmolzen wird.
Die Temperaturkontrolle im Ausbrennofen ist von entscheidender Bedeutung, um sicherzustellen, dass die organischen Bestandteile vollständig entfernt werden, ohne das Keramikpulver zu überhitzen oder zu beschädigen. Moderne Ausbrennöfen bieten präzise Steuerungsoptionen, um die Temperatur sorgfältig zu überwachen und anzupassen.
Die Verwendung von Keramikpulver in Verbindung mit einem Ausbrennofen ermöglicht die Herstellung von präzisen, formstabilen keramischen Teilen mit unterschiedlichen Eigenschaften. Dies findet Anwendung in Branchen wie der Elektronik, Medizintechnik, Raumfahrt und vielen anderen, wo hochwertige Keramikkomponenten benötigt werden.
Bindemittelentfernung:
Die Bindemittelentfernung ist ein zentraler Schritt in verschiedenen industriellen Prozessen, bei denen Pulver in eine bestimmte Form gebracht wird, bevor es thermischen Behandlungen unterzogen wird. In diesem Kontext bezieht sich die Bindemittelentfernung auf den Prozess, bei dem organische Bindemittel oder flüchtige Bestandteile aus einem pulverförmigen Material entfernt werden. Dieser Schritt ist entscheidend für die Qualität und Integrität der Endprodukte.
In der Pulvermetallurgie wird die Bindemittelentfernung durchgeführt, um Metallpulver von den organischen Bindemitteln zu befreien, die während des Formgebungsprozesses hinzugefügt wurden. Diese Bindemittel dienen dazu, das Metallpulver in eine bestimmte Form zu bringen, sei es durch Pressen oder Spritzgießen. Der Ausbrennofen spielt hierbei eine entscheidende Rolle, indem er das pulverförmige Material auf hohe Temperaturen erhitzt, wodurch die organischen Bestandteile verdampfen oder pyrolysiert werden.
In der Pulverbeschichtung wird die Bindemittelentfernung ebenfalls durch den Ausbrennofen durchgeführt. Das aufgebrachte Pulver enthält Bindemittel, die ihm die notwendige Haftfestigkeit verleihen. Durch Erhitzen im Ausbrennofen schmilzt und härtet das Pulver, und die organischen Bindemittel werden entfernt. Dieser Prozess ist entscheidend, um eine gleichmäßige und strapazierfähige Beschichtung auf der Oberfläche zu erzielen.
Die genaue Kontrolle der Temperatur im Ausbrennofen ist entscheidend, um sicherzustellen, dass die Bindemittel vollständig entfernt werden, ohne das Pulver zu überhitzen oder zu beschädigen. Eine erfolgreiche Bindemittelentfernung legt den Grundstein für hochwertige Endprodukte in der Pulvermetallurgie und Pulverbeschichtungstechnologie.
Pulverentgasung:
Die Pulverentgasung ist ein wichtiger Prozess in verschiedenen industriellen Anwendungen, insbesondere in der Pulvermetallurgie und Pulverbeschichtung. Dieser Vorgang bezieht sich auf die Entfernung von Gasen oder flüchtigen Bestandteilen aus einem pulverförmigen Material, um die Qualität und Eigenschaften der Endprodukte zu verbessern.
In der Pulvermetallurgie wird der Ausbrennofen oft für die Pulverentgasung verwendet, insbesondere während des Debinding-Prozesses. Während dieses Schrittes werden organische Bindemittel und flüchtige Bestandteile aus dem Metallpulver entfernt. Gleichzeitig erfolgt die Aushärtung des Pulvers für den nachfolgenden Sinterprozess. Die Pulverentgasung hilft, unerwünschte Gasblasen oder Poren in den gesinterten Metallteilen zu minimieren, was die mechanischen Eigenschaften und die Qualität der Endprodukte verbessert.
In der Pulverbeschichtung spielt die Pulverentgasung ebenfalls eine bedeutende Rolle. Wenn das aufgebrachte Pulver im Ausbrennofen geschmolzen und gehärtet wird, können eingeschlossene Gase freigesetzt werden. Durch die Pulverentgasung werden diese Gase entfernt, was zu einer gleichmäßigen und blasenfreien Pulverbeschichtung führt. Dies ist entscheidend für die Haftfestigkeit und die Ästhetik der beschichteten Oberflächen.
Die moderne Technologie ermöglicht die Integration von speziellen Entgasungsfunktionen in Ausbrennöfen, um eine effiziente Pulverentgasung zu gewährleisten. Die präzise Steuerung der Temperatur und des Prozesses spielt dabei eine entscheidende Rolle, um die gewünschten Ergebnisse zu erzielen.
Zusammenfassend ist die Pulverentgasung ein kritischer Schritt in der Pulververarbeitungstechnologie, um die Qualität, Homogenität und Ästhetik von Metallteilen und beschichteten Oberflächen zu optimieren.
Sinterprozessvorbereitung:
Die Sinterprozessvorbereitung ist ein wesentlicher Schritt in der Pulvermetallurgie, der die Grundlage für die Herstellung von hochfesten und präzisen Metallteilen legt. Der Sinterprozess selbst bezieht sich auf das Erhitzen von Metallpulver auf Temperaturen unterhalb ihres Schmelzpunkts, wodurch die Partikel miteinander verschmelzen und ein festes, dichtes Werkstück entsteht. Die Sinterprozessvorbereitung beinhaltet oft den vorangehenden Debinding-Prozess im Ausbrennofen.
Nach der Entfernung von organischen Bindemitteln und flüchtigen Bestandteilen im Ausbrennofen ist das Metallpulver bereit für den Sinterprozess. Die Sinterprozessvorbereitung ist entscheidend, um sicherzustellen, dass das Pulver frei von Verunreinigungen ist und die richtige Porosität und Dichte für das Endprodukt aufweist.
Der Ausbrennofen spielt dabei eine zentrale Rolle, indem er das Pulver auf die optimale Temperatur erhitzt und die organischen Bestandteile entfernt, ohne das Metallpulver zu beschädigen. Die Temperaturkontrolle ist entscheidend, um sicherzustellen, dass der Sinterprozess effizient und mit konsistenten Ergebnissen durchgeführt wird.
Der Sinterprozess selbst ist für verschiedene Anwendungen von entscheidender Bedeutung. In der Pulvermetallurgie wird er verwendet, um komplexe Bauteile mit hoher Präzision und Festigkeit herzustellen. Die Sinterprozessvorbereitung gewährleistet dabei eine homogene Struktur und minimiert Defekte im Endprodukt.
Die Sinterprozessvorbereitung spielt auch eine Rolle in anderen Bereichen, wie der Keramikherstellung, wo ähnliche Prinzipien gelten. Die richtige Vorbereitung durch den Ausbrennofen ist entscheidend für die erfolgreiche Umsetzung des Sinterprozesses und die Erzielung der gewünschten Materialeigenschaften.
Zusammenfassend ist die Sinterprozessvorbereitung durch die Entfernung von Bindemitteln und die Einstellung des Pulvers für den Sinterprozess ein kritischer Schritt in der Pulvermetallurgie, der mit Präzision und Sorgfalt im Ausbrennofen durchgeführt wird.
Die Entfernung von Pulverbeschichtung mithilfe eines Ausbrennofens ist ein spezifischer Prozess, der als Pulverbeschichtungsentfernung oder auch als Entlackung bezeichnet wird. Dieser Vorgang wird angewendet, wenn eine vorhandene Pulverbeschichtung von einem Werkstück entfernt werden muss, sei es aufgrund von Fehlern in der Beschichtung, Renovierungsarbeiten oder anderen Gründen.
Hier sind die grundlegenden Schritte für die Entfernung von Pulverbeschichtung mit einem Ausbrennofen:
- Vorbereitung des Werkstücks: Zunächst wird das Werkstück vorbereitet, indem es in den Ausbrennofen platziert wird. Es ist wichtig sicherzustellen, dass das Werkstück für den Temperaturzyklus, der beim Entfernen der Pulverbeschichtung verwendet wird, geeignet ist.
- Erhitzen im Ausbrennofen: Das Werkstück wird dann im Ausbrennofen auf Temperaturen erhitzt, die ausreichen, um die Pulverbeschichtung zu schmelzen und zu brechen. Der genaue Temperaturbereich hängt von der Art der Pulverbeschichtung und den Eigenschaften des Substrats ab.
- Abkühlung und Entfernung: Nachdem die Pulverbeschichtung durch das Erhitzen beeinträchtigt wurde, erfolgt die Abkühlung des Werkstücks. Anschließend kann die gelockerte oder aufgebrochene Beschichtung mechanisch entfernt werden, beispielsweise durch Bürsten, Schaben oder Strahlen.
- Wiederholung bei Bedarf: Je nach der Dicke und der Art der vorhandenen Pulverbeschichtung kann es erforderlich sein, den Prozess zu wiederholen, um sicherzustellen, dass alle Beschichtungsrückstände entfernt werden.
Es ist wichtig zu beachten, dass die genauen Bedingungen und der Erfolg dieses Prozesses von verschiedenen Faktoren abhängen, darunter die Art der Pulverbeschichtung, das Substratmaterial des Werkstücks, die Dicke der Beschichtung und die Temperaturkontrolle im Ausbrennofen. Daher ist es ratsam, den Prozess sorgfältig zu überwachen, um das gewünschte Ergebnis zu erzielen, ohne das Substrat zu beschädigen.
Elektro Ausbrennofen – Pulverausbrennofen
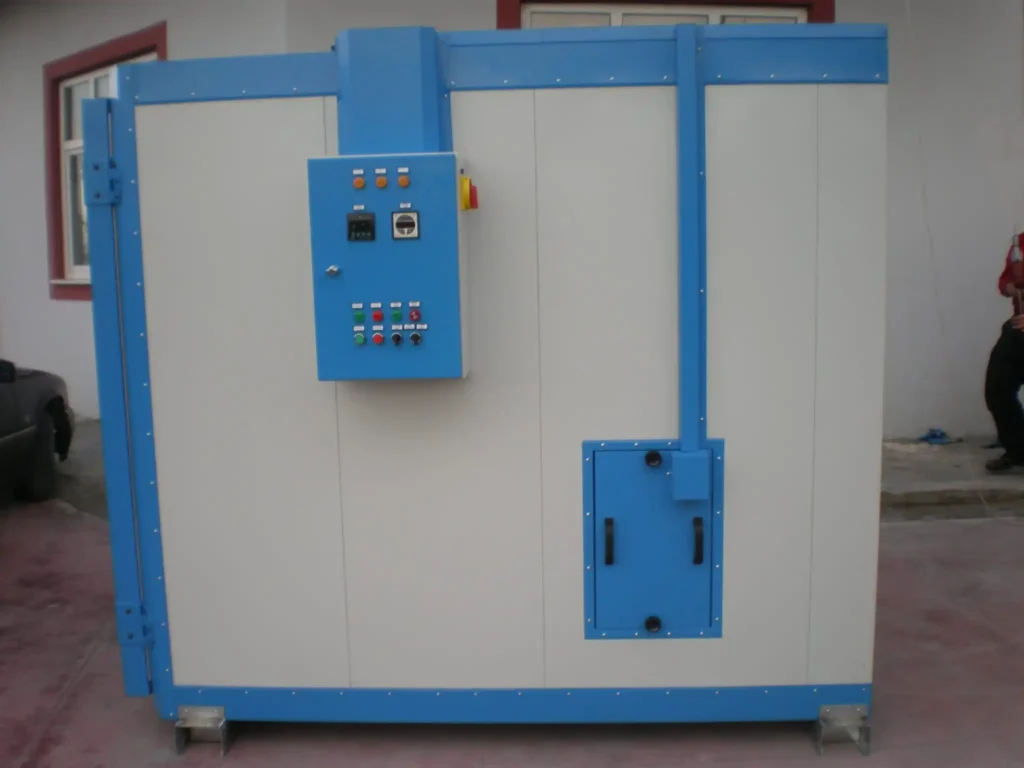
Die zur Trocknung und Einbrennung benutzte Temperatur wird durch Gas-, Öl- oder elektrische Heizung gesichert. Bei dem gasbeheizten Pulverofen unterscheiden wir zwischen direkter und indirekter Beheizung.
Abhängig von der Ausführung und der Technologie gibt es Systeme in A- und U-Form, Blockofen, Trocknerbecken und entsprechend den Kundenwünschen können auch andere Ausführungen verwirklicht werden.
Abhängig von der Gestaltung kommen die Werkstücke entweder mit Bodenförderer oder mittels Hängeförderer in den Pulverofen. Zur Effektivität der Anlage tragen auch die dicke Isolierung, die unabhängigen Türbewegungen, die Luftvorhänge und die Wärmerückgewinnung bei.
Aufgabe des EMS Einbrennofens ist die Einbrennung vom EMS-Lack auf der Werkstückoberfläche. Der Pulverofen besteht aus Sandwichpanelen, innerer Tragkonstruktion, Lufterhitzer, interner und externer Lufttechnik. Abhängig von der Ausführung sind sie mit Türen, bzw. Luftvorhang versehen. Die innere Luftumwälzung des EMS Einbrennofens ist intensiver als die des Pulvereinbrennofens.
Der Aufbau ist luftdicht, damit wird der Wärmeverlust minimalisiert. Der EMS Einbrennofen kann in Durchlauf- oder Taktbetrieb funktionieren. Von jeder einzelnen Einbrennung wird ein Diagramm hergestellt. Die Steuerung erfolgt entweder durch Relais (bei den kleineren, einfacheren Öfen) oder durch Steurung.
Bei der Steuerung kann auch die Fernwartung gesichert werden. Der Aufbau der Anlage (Panelelemente) basiert auf einer min. 3-schichtigen, Steinwollisolierung mit 120 kg/m3 Dichtigkeit. Darüber hinaus wird der Haftwassertrockner mit weiterem Panelanschluss-Schutz hergestellt, wodurch Wärmeverlust und Aufwärmedefizit minimalisiert werden.
Branchen, in denen Pulverbeschichtung verwendet wird
- Pulverbeschichtung von Aluminiumprofilen
- Pulverbeschichtung von Stahl- oder Metalltüren
- Ölfilter pulverbeschichtung
- Pulverbeschichtung von Alufelgen und Felgen
- Pulverbeschichtung von Straßenlaternenmasten
- Automobilindustrie: Pulverbeschichtung wird häufig für Autoteile wie Felgen, Stoßstangen und andere Komponenten eingesetzt.
- Architektur: Pulverbeschichtung wird oft für Fensterrahmen, Geländer, Türen und andere Metallbauteile verwendet.
- Möbelindustrie: Pulverbeschichtung wird bei der Herstellung von Möbeln wie Stühlen, Tischen und Regalen eingesetzt.
- Elektronikindustrie: Pulverbeschichtung wird in der Elektronikindustrie zur Beschichtung von Gehäusen und anderen Komponenten verwendet.
- Haushaltsgeräte: Pulverbeschichtung wird bei der Herstellung von Haushaltsgeräten wie Kühlschränken, Waschmaschinen und Trocknern eingesetzt.
- Sportgeräte: Pulverbeschichtung wird oft bei der Herstellung von Sportgeräten wie Fahrrädern, Skiern und Snowboards verwendet.
- Medizinische Geräte: Pulverbeschichtung wird in der Medizintechnik zur Beschichtung von Geräten wie Krankenhausbetten, Stühlen und Tischen eingesetzt.
- Bauwesen: Pulverbeschichtung wird oft in der Bauindustrie zur Beschichtung von Stahlträgern und anderen Komponenten eingesetzt.
Wir versenden nach Deutschland, Österreich und in die Schweiz
Wir sind nicht nur die Hersteller Ihrer Pulverbeschichtungsanlagen, sondern auch Ihr weltweiter Lieferpartner.
Bei EMS verstehen wir, dass es genauso wichtig ist, Ihre Pulverbeschichtungsanlagen schnell und sicher zu Ihnen zu bringen, wie sie nach höchsten Standards herzustellen. Deshalb bieten wir all unseren Kunden weltweit Lieferdienste an.
Wir arbeiten mit einem Netzwerk erfahrener und zuverlässiger Versandpartner zusammen, um sicherzustellen, dass Ihre Ausrüstung pünktlich und in einwandfreiem Zustand ankommt. Wir bieten auch eine Vielzahl von Versandoptionen an, um Ihrem Budget und Ihren Bedürfnissen gerecht zu werden.
Egal, ob Sie Ihre Ausrüstung an eine lokale Adresse oder an einen internationalen Bestimmungsort versenden müssen, wir können Ihnen helfen. Wir arbeiten mit Ihnen zusammen, um die beste Versandoption für Ihre Bedürfnisse auszuwählen und Sie während des gesamten Versandprozesses über den Status Ihrer Sendung zu informieren.
Wenn Sie sich also für EMS für Ihre Pulverbeschichtungsanlagen entscheiden, erhalten Sie nicht nur die besten Produkte auf dem Markt, sondern auch das bestmögliche Liefererlebnis.
Kontaktieren Sie uns noch heute, um mehr über unsere weltweiten Lieferdienste zu erfahren.
Auch beim Versand, setzen wir auf bewährte Partner. Und auf Nachhaltigkeit. Nicht nur in Deutschland und Österreich sondern in der ganzen EU und der Schweiz wird ihre Pulverbeschichtungsanlage mit unseren Transtportfirmen zu ihnen gebracht.
Die Lieferung ihrer Ware erfolgt innerhalb Deutschlands, Österreichs und der Schweiz spätestens innerhalb von 7-8 Werktagen. Die Lieferung in weitere Länder der EU erfolgt spätestens innerhalb von 10 Werktagen.
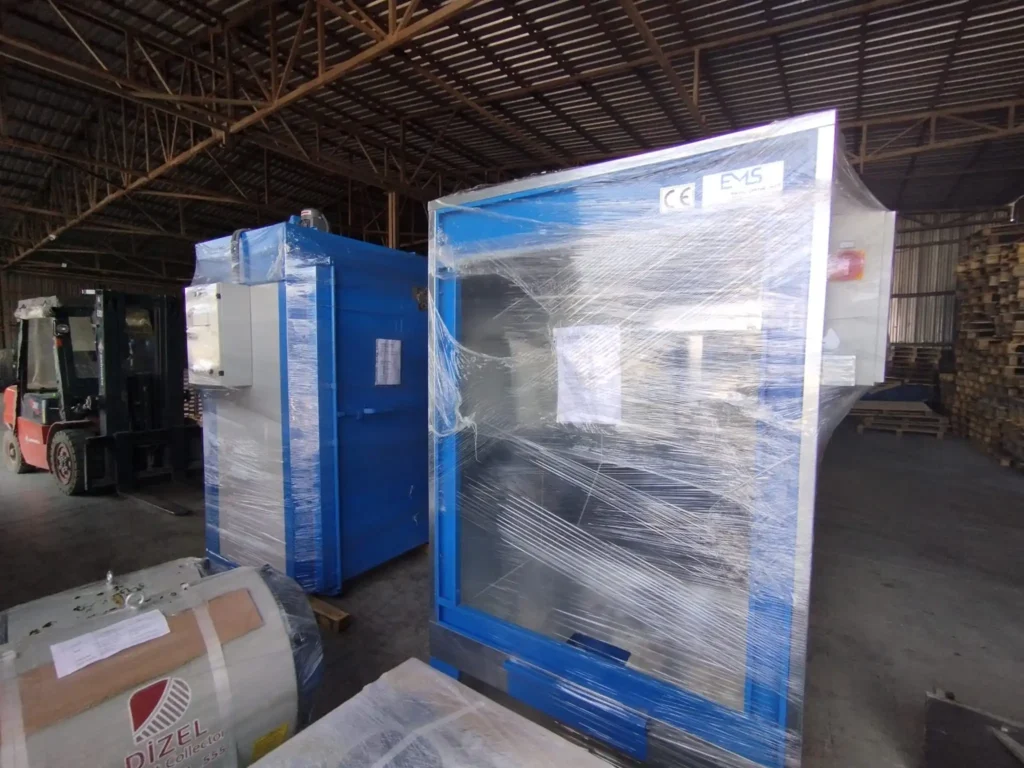

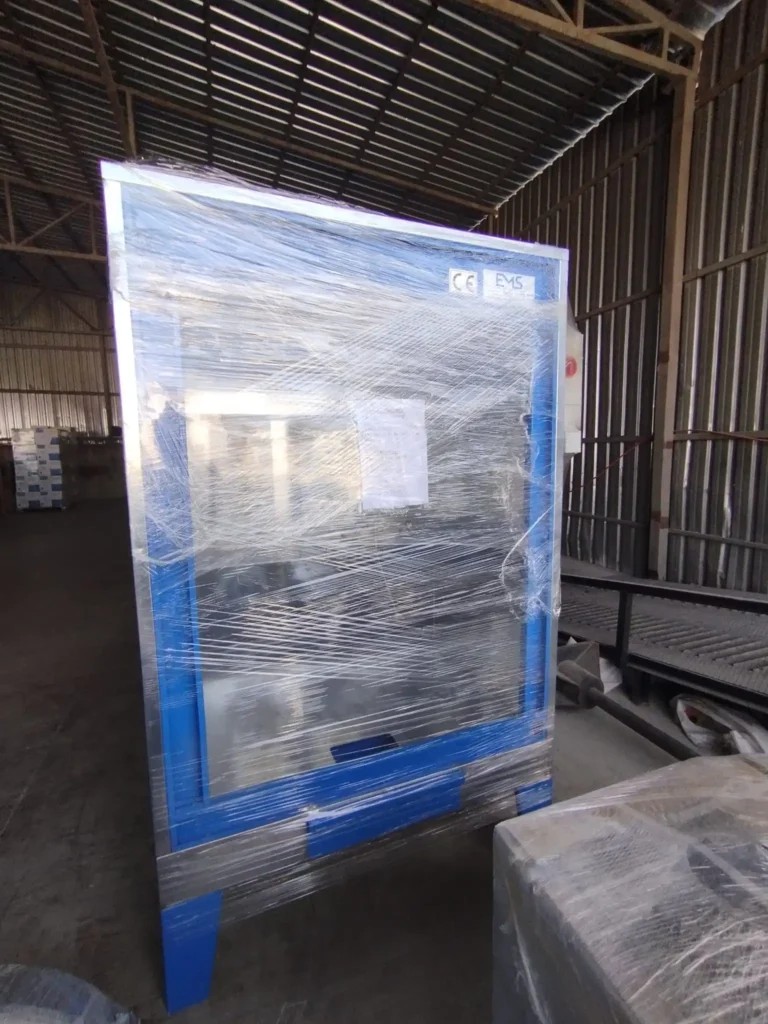
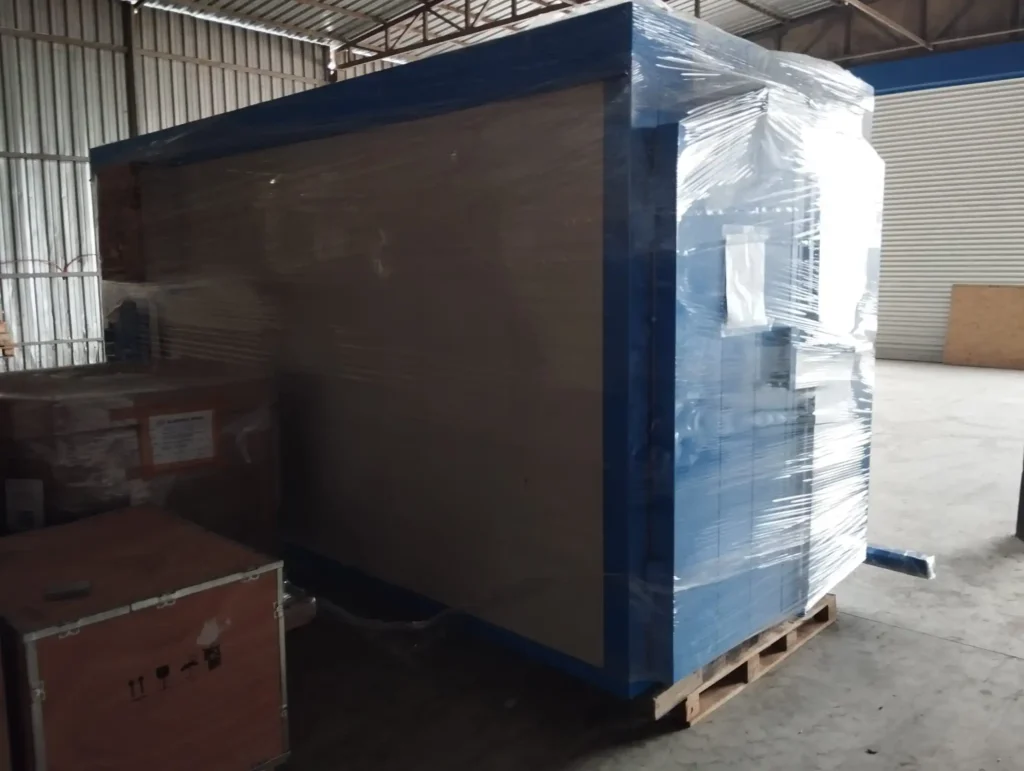
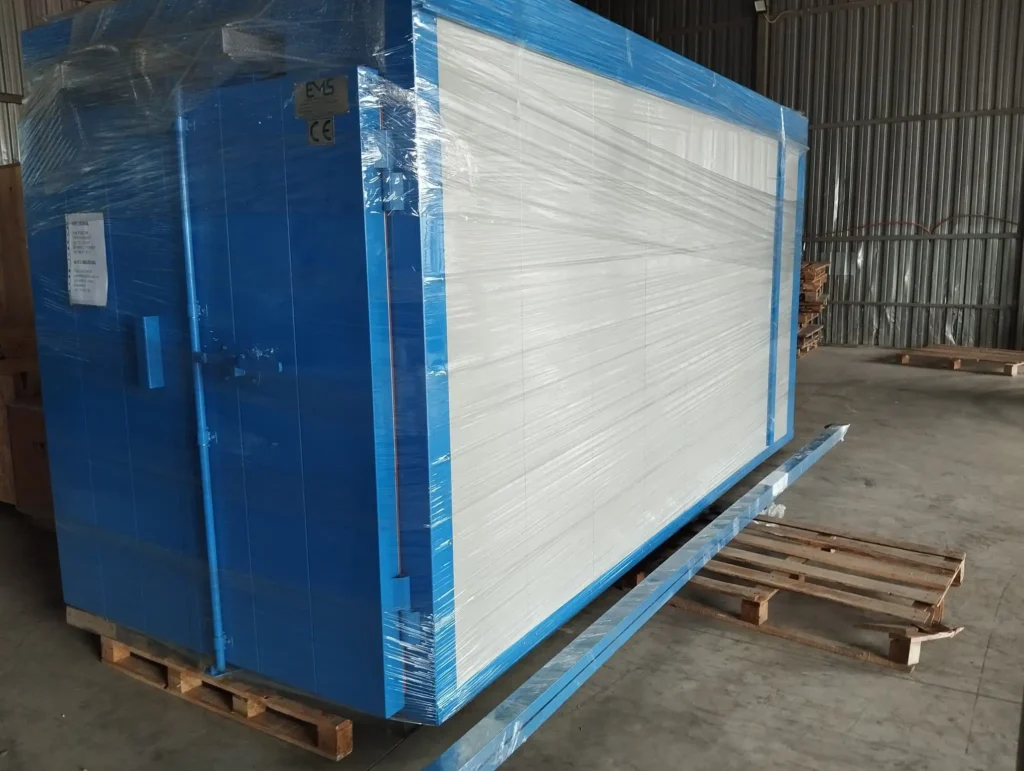
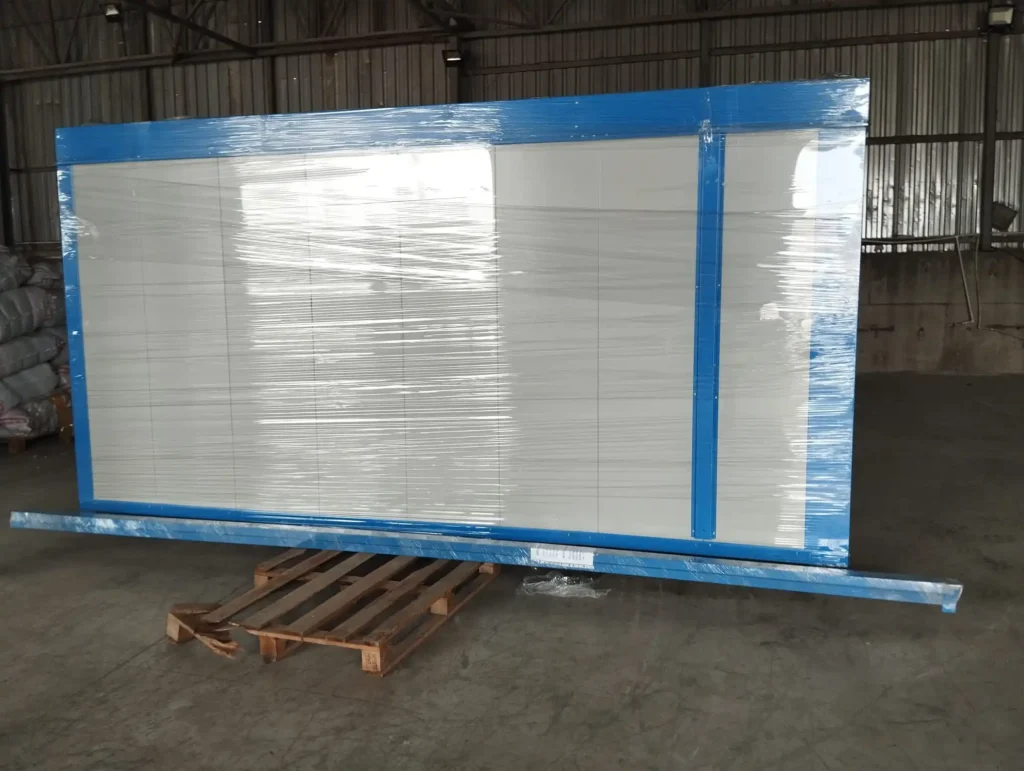
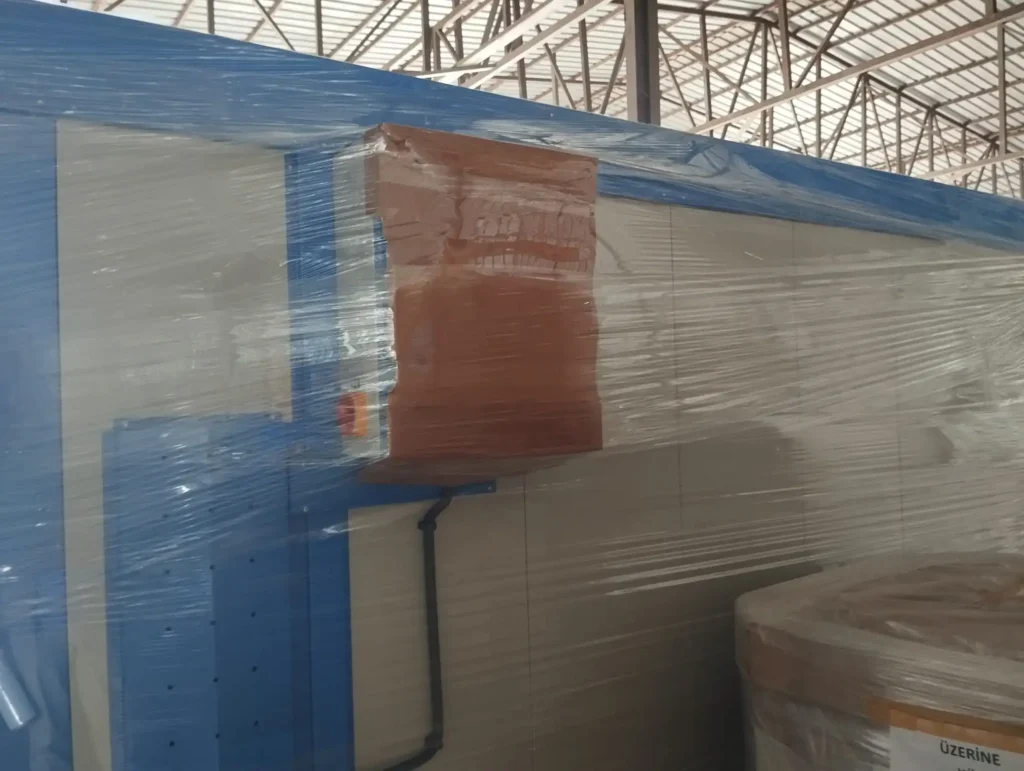
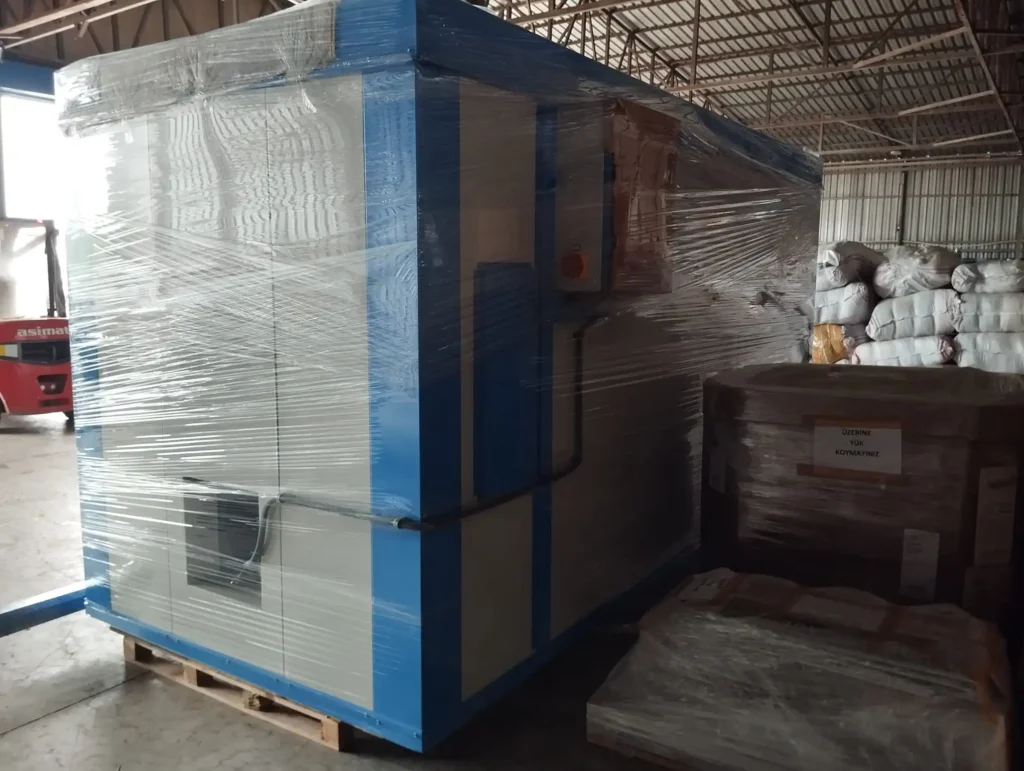
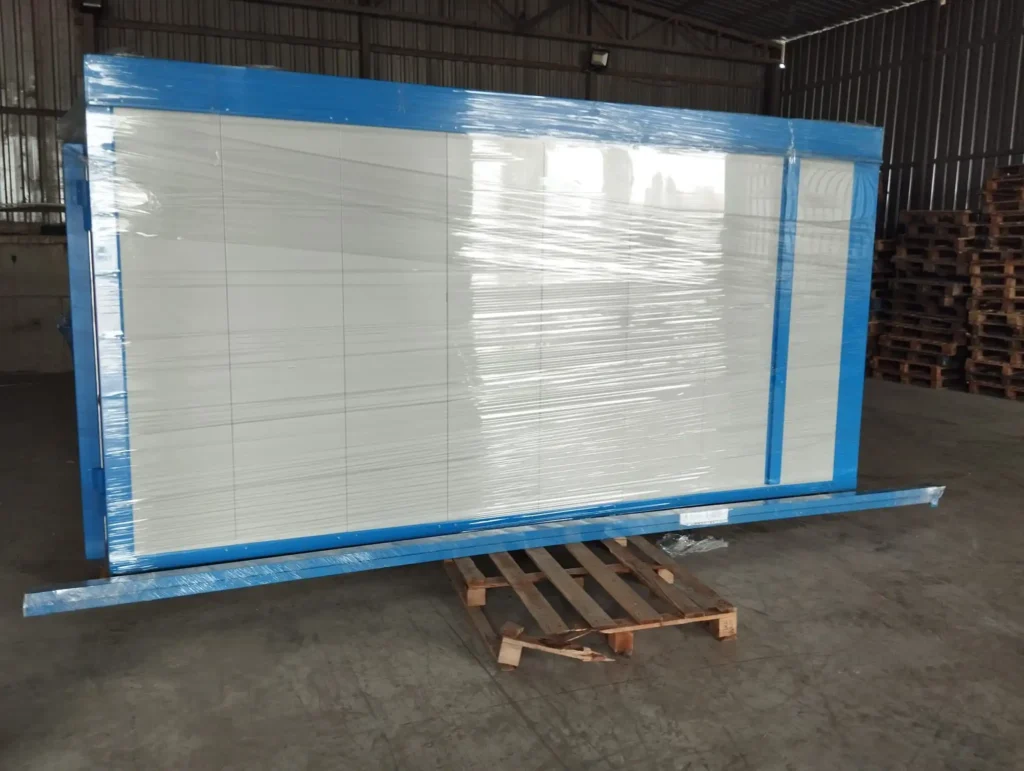