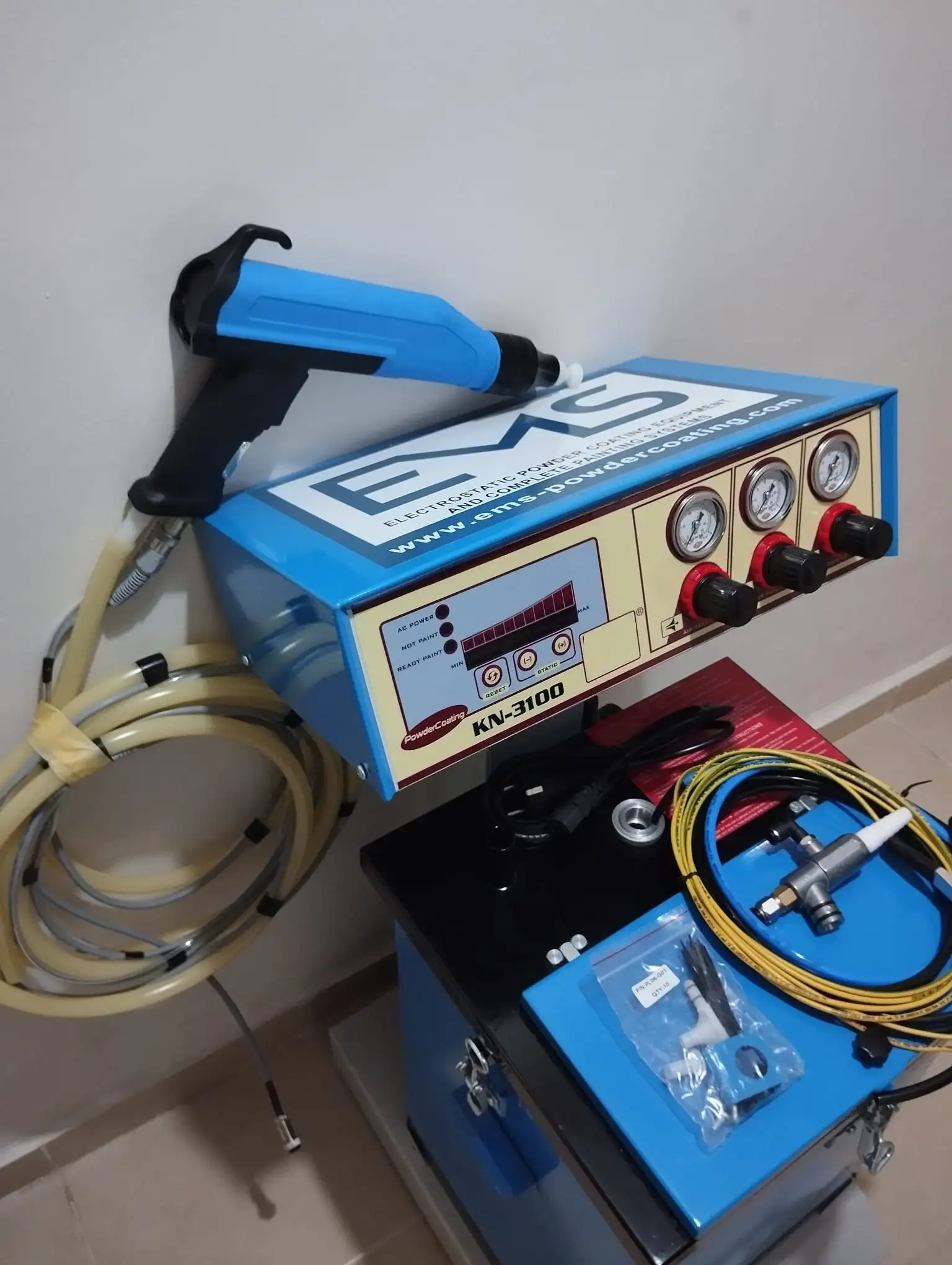
Wir fertigen Pulverlack Handanlage für unsere Kunden in Deutschland, Österreich und der Schweiz. Guter Preis und lange Lebensdauer
Pulverlack Handanlage ist eine manuelle Methode zur Pulverbeschichtung von Oberflächen, die auf kleinen und mittelgroßen Teilen angewendet wird. Dabei wird das Pulver auf die Oberfläche aufgetragen, indem es von Hand aus einem Pulverbeschichtungsgerät gestreut oder gesprüht wird.
Im Gegensatz zur automatisierten Pulverbeschichtung mit einer Pulverbeschichtungsanlage erfordert die Pulverlack Handanlage mehr manuelle Arbeit und Geschicklichkeit, um eine gleichmäßige Beschichtung auf der Oberfläche zu erzielen. Die Qualität der Beschichtung hängt stark von der Erfahrung und Fähigkeit des Bedieners ab.
Die Pulverlack Handanlage ist eine kostengünstige Option für kleinere Stückzahlen oder spezielle Anforderungen an die Beschichtung, bei denen die Investition in eine automatisierte Pulverbeschichtungsanlage nicht gerechtfertigt ist.
Eine Pulverlack Handanlage ist ein Gerät zum Aufbringen von Pulverlack auf Oberflächen. Pulverlack ist ein Trockenbeschichtungspulver, das aus Kunstharzen, Farbpigmenten und Füllstoffen besteht. Es wird elektrostatisch aufgeladen und auf das Werkstück aufgetragen, wo es sich durch die elektrostatische Anziehungskraft haftet. Anschließend wird das Werkstück in einem Einbrennofen erhitzt, wodurch der Pulverlack schmilzt und eine feste, widerstandsfähige Beschichtung bildet.
Pulverlack Handanlagen werden häufig in kleinen und mittleren Unternehmen eingesetzt, da sie relativ kostengünstig und einfach zu bedienen sind. Sie eignen sich für eine Vielzahl von Anwendungen, darunter die Beschichtung von Metallteilen, Kunststoffteilen und Holzteilen.
Funktionsweise einer Pulverlack Handanlage
Eine Pulverlack Handanlage besteht in der Regel aus folgenden Komponenten:
- Pulverpistole: Die Pulverpistole wird verwendet, um das Pulverlack auf das Werkstück aufzutragen.
- Pulverbehälter: Der Pulverbehälter enthält das Pulverlack, das der Pulverpistole zugeführt wird.
- Hochspannungserzeuger: Der Hochspannungserzeuger lädt das Pulverlack elektrostatisch auf.
- Erdungskabel: Das Erdungskabel verbindet das Werkstück mit dem Hochspannungserzeuger, um einen Stromkreis zu bilden.
Um ein Werkstück mit Pulverlack zu beschichten, wird es zunächst an das Erdungskabel angeschlossen. Anschließend wird das Pulverlack mit der Pulverpistole auf das Werkstück aufgetragen. Das elektrostatisch aufgeladene Pulverlack wird vom Werkstück angezogen und haftet an der Oberfläche.
Nachdem das Pulverlack aufgetragen wurde, wird das Werkstück in einem Einbrennofen erhitzt. Dadurch schmilzt das Pulverlack und bildet eine feste, widerstandsfähige Beschichtung.
Vorteile von Pulverlack Handanlagen
Pulverlack Handanlagen bieten eine Reihe von Vorteilen gegenüber anderen Beschichtungsverfahren, darunter:
- Umweltfreundlich: Pulverlack ist ein umweltfreundliches Beschichtungsmaterial, da keine Lösungsmittel verwendet werden.
- Effizient: Pulverlack Handanlagen sind sehr effizient, da das Pulverlack direkt auf das Werkstück aufgetragen wird, ohne dass ein Primer erforderlich ist.
- Qualitativ hochwertig: Pulverlackbeschichtungen sind sehr hochwertig und bieten einen guten Schutz vor Korrosion, Abrieb und anderen Umwelteinflüssen.
Nachteile von Pulverlack Handanlagen
Pulverlack Handanlagen haben auch einige Nachteile, darunter:
- Manuelle Arbeit: Pulverlack Handanlagen müssen manuell bedient werden, was zeitaufwendig sein kann.
- Platzbedarf: Pulverlack Handanlagen benötigen relativ viel Platz.
- Kosten: Pulverlack Handanlagen sind in der Regel teurer als andere Beschichtungsgeräte, wie z. B. Spritzgeräte.
Fazit
Pulverlack Handanlagen sind ein vielseitiges und effizientes Beschichtungsverfahren für kleine und mittlere Unternehmen. Sie bieten eine Reihe von Vorteilen gegenüber anderen Beschichtungsverfahren, wie z. B. Umweltfreundlichkeit, Effizienz und hohe Qualität der Beschichtungen.
Pulverlack Handanlage

Eine Pulverlack-Handanlage ist eine Einrichtung, die für das manuelle Auftragen von Pulverlack auf Oberflächen oder Teile entwickelt wurde. Pulverlack ist eine Beschichtung, die in Form von Pulver aufgetragen wird und dann durch Hitze verschmilzt, um eine dauerhafte und schützende Oberflächenbeschichtung zu bilden. Hier sind einige wichtige Informationen zur Pulverlack-Handanlage:
- Pulverlack: Pulverlack besteht aus feinem Pulver, das aus Kunststoffen, Harzen und Pigmenten hergestellt wird. Es ist eine umweltfreundliche Beschichtungsoption, da sie im Gegensatz zu flüssigen Lacken keine Lösungsmittel enthält und weniger Abfall erzeugt.
- Manueller Betrieb: In einer Pulverlack-Handanlage erfolgt der Lackauftrag manuell durch einen Bediener. Dies ermöglicht eine präzise Kontrolle über den Lackauftrag und eignet sich besonders für kleinere Stückzahlen oder spezielle Anwendungen.
- Ausrüstung: Die Ausrüstung in einer Pulverlack-Handanlage umfasst normalerweise ein Handstück oder eine Pistole, die das Pulver auf die zu beschichtende Oberfläche sprüht. Es gibt verschiedene Arten von Pistolen, darunter Korona- und Tribo-Pistolen, die unterschiedliche elektrostatische Verfahren verwenden.
- Elektrostatische Aufladung: Eine wichtige Eigenschaft von Pulverlack-Handanlagen ist die elektrostatische Aufladung. Das Pulver wird positiv aufgeladen, während die zu lackierende Oberfläche negativ aufgeladen wird. Dies ermöglicht eine gleichmäßige Verteilung des Pulvers und eine effiziente Haftung an der Oberfläche.
- Vorbereitung der Oberfläche: Bevor der Pulverlack aufgetragen wird, muss die Oberfläche sorgfältig vorbereitet werden. Dies kann das Reinigen, Entfetten, Entrosten oder andere Vorbehandlungsverfahren umfassen, um eine optimale Haftung des Lacks sicherzustellen.
- Hitzeeinwirkung: Nachdem das Pulver aufgetragen wurde, werden die beschichteten Teile normalerweise in einen Ofen gebracht, um das Pulver bei hohen Temperaturen zu schmelzen und zu härten. Dieser Prozess wird als Einbrennen bezeichnet und ist entscheidend, um eine haltbare und widerstandsfähige Oberflächenbeschichtung zu gewährleisten.
- Anwendungen: Pulverlack-Handanlagen werden in verschiedenen Branchen eingesetzt, darunter die Automobilindustrie, die Möbelherstellung, die Metallverarbeitung, die Architektur und viele andere. Sie sind vielseitig und können für verschiedene Materialien wie Metall, Holz, Kunststoff und mehr verwendet werden.
Die Verwendung einer Pulverlack-Handanlage erfordert Schulung und Erfahrung, um eine gleichmäßige und hochwertige Beschichtung zu gewährleisten. Es ist auch wichtig, Sicherheitsvorkehrungen zu treffen, da Pulverlack gesundheitliche Risiken darstellen kann, wenn er eingeatmet wird. Daher sollte beim Umgang mit Pulverlacken immer die geeignete Schutzausrüstung getragen werden.
Teile einer Pulverlack Handanlage
Eine Pulverlack-Handanlage besteht in der Regel aus folgenden Teilen:
- Pulverbeschichtungspistole: Dies ist das wichtigste Werkzeug in der Handanlage. Es gibt verschiedene Arten von Pistolen, aber im Allgemeinen sprühen sie das Pulver auf die zu beschichtende Oberfläche.
- Pulverbeschichtungsgerät: Dieses Gerät liefert das Pulver zur Pistole und sorgt dafür, dass es gleichmäßig verteilt wird. Es besteht aus einem Pulverbehälter, einer Pumpe, einer Düse und einem Luftfilter.
- Pulversieb: Das Pulver wird in einem Sieb aufbewahrt, um sicherzustellen, dass es keine Klumpen oder Verunreinigungen gibt. Das Sieb befindet sich normalerweise zwischen dem Pulverbehälter und dem Pulverbeschichtungsgerät.
- Vorbehandlungseinrichtung: Bevor das Teil beschichtet wird, muss es von Schmutz, Fett und Rost befreit werden. Die Vorbehandlungseinrichtung reinigt das Teil und bereitet es auf die Beschichtung vor.
- Ofen: Nachdem das Teil beschichtet wurde, muss es in einem Ofen ausgehärtet werden, um eine haltbare Oberfläche zu gewährleisten. Der Ofen sollte die richtige Temperatur und die richtige Zeit haben, um das Pulver auszuhärten, ohne das Teil zu beschädigen.
- Werkstückaufhängung: Um das Teil zu beschichten, muss es an einer Halterung befestigt werden, damit es während des Beschichtungsprozesses an Ort und Stelle bleibt. Die Werkstückaufhängung kann in verschiedenen Formen und Größen erhältlich sein, je nach dem Teil, das beschichtet werden soll.
- Atemschutzgerät: Bei der Handanlage von Pulverlacken wird eine Menge feiner Staub freigesetzt, was ein Atemrisiko darstellen kann. Es ist daher wichtig, ein Atemschutzgerät zu tragen, um die Gesundheit des Bedieners zu schützen.
Diese Teile bilden zusammen eine vollständige Pulverlack-Handanlage. Es gibt jedoch auch zusätzliche Ausrüstung wie z. B. Spritzkabinen, Absauganlagen und Pulverrückgewinnungssysteme, die in größeren Anlagen verwendet werden können.
Pulverlack

Pulverlack ist eine Art von Beschichtung, die in Form von feinem Pulver auf Oberflächen aufgetragen wird, um sie zu schützen, zu verschönern oder zu veredeln. Im Gegensatz zu flüssigen Lacken enthält Pulverlack keine flüssigen Lösungsmittel, was ihn umweltfreundlicher macht. Hier sind einige wichtige Informationen über Pulverlack:
- Zusammensetzung: Pulverlack besteht aus pulverförmigen Partikeln, die aus einer Mischung von Polymeren, Harzen, Pigmenten und anderen Additiven bestehen. Diese Pulver sind trocken und nicht flüssig.
- Auftrag: Pulverlack wird normalerweise auf die zu beschichtende Oberfläche gesprüht. Der Auftrag kann auf verschiedene Weisen erfolgen, darunter elektrostatisches Auftragen und pneumatisches Auftragen. Bei der elektrostatischen Methode wird das Pulver positiv aufgeladen und haftet dadurch effizient an der negativ geladenen Oberfläche.
- Haftung: Pulverlack haftet sehr gut an Metalloberflächen, was ihn ideal für die Beschichtung von Metallteilen macht. Eine gute Haftung wird durch die elektrostatische Ladung des Pulvers und die Vorbereitung der Oberfläche erreicht.
- Vorbehandlung: Bevor Pulverlack aufgetragen wird, muss die zu beschichtende Oberfläche sorgfältig vorbereitet werden. Dies kann das Entfetten, Entrosten, Sandstrahlen oder andere Vorbehandlungsverfahren umfassen, um eine saubere und haftfähige Oberfläche zu gewährleisten.
- Härtung: Nachdem das Pulverlack aufgetragen wurde, muss es bei erhöhten Temperaturen in einem Ofen eingebrannt werden. Während des Einbrennvorgangs schmilzt das Pulver und bildet eine feste, langlebige Beschichtung auf der Oberfläche.
- Umweltfreundlichkeit: Pulverlacke sind umweltfreundlich, da sie keine flüchtigen organischen Verbindungen (VOCs) enthalten, die die Luftverschmutzung und Gesundheitsprobleme verursachen können. Dies macht Pulverlacke in vielen Industrien und Anwendungen attraktiv, insbesondere wenn strenge Umweltauflagen zu beachten sind.
- Anwendungen: Pulverlacke werden in einer Vielzahl von Branchen eingesetzt, einschließlich der Automobilindustrie, Möbelherstellung, Architektur, Metallverarbeitung, Elektronik, Gartenmöbel und mehr. Sie bieten Schutz vor Korrosion, Abrieb, UV-Strahlen und anderen Umweltbelastungen.
- Farbvielfalt: Pulverlacke sind in einer breiten Palette von Farben und Oberflächeneffekten erhältlich, einschließlich glatt, strukturiert, glänzend, matt und metallisch.
Pulverlacke bieten eine haltbare und ansprechende Oberflächenbeschichtung, die sich für viele Anwendungen eignet. Sie sind besonders beliebt in Branchen, in denen hohe Ansprüche an die Oberflächenqualität und Umweltverträglichkeit gestellt werden.
Manueller Betrieb
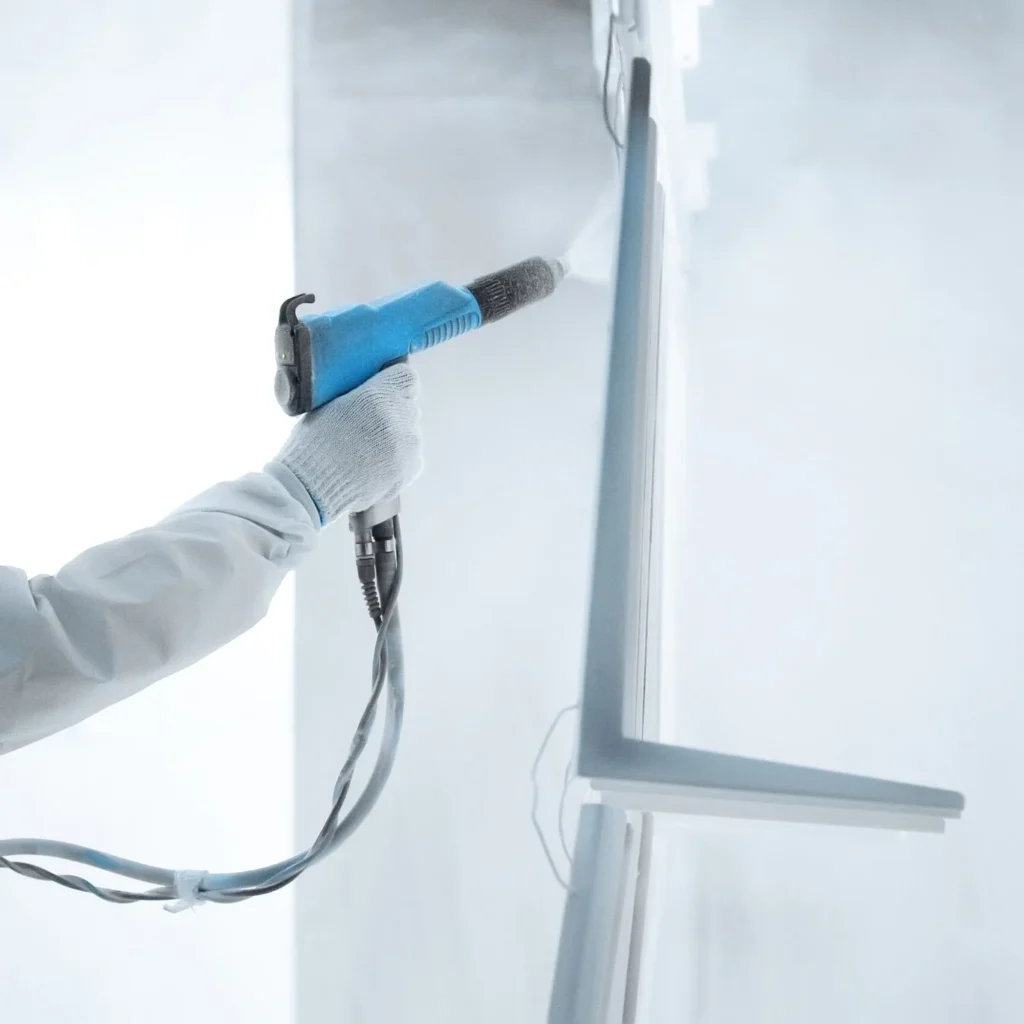
Der Begriff „manueller Betrieb“ bezieht sich auf eine Betriebsweise oder Arbeitsweise, bei der menschliche Arbeitskraft und Steuerung direkt eingesetzt werden, um Aufgaben auszuführen oder Maschinen und Anlagen zu bedienen. Im manuellen Betrieb erfolgt die Steuerung und Ausführung von Aufgaben durch physische Arbeit, Bewegungen oder manuelle Eingriffe von Menschen, im Gegensatz zu automatisierten oder computergesteuerten Prozessen. Hier sind einige wichtige Merkmale und Beispiele für den manuellen Betrieb:
- Menschliche Arbeitskraft: Im manuellen Betrieb sind menschliche Arbeitskraft, Geschicklichkeit und Kontrolle unerlässlich. Die Bediener führen physische Aufgaben aus, steuern Maschinen und Prozesse manuell und treffen Entscheidungen basierend auf ihrer Erfahrung und ihrem Fachwissen.
- Keine Automatisierung: Im Gegensatz zum automatisierten Betrieb, bei dem Maschinen und Computer die Hauptarbeit leisten, erfolgt im manuellen Betrieb die gesamte Arbeit durch menschliche Tätigkeiten. Es gibt keine programmgesteuerten Abläufe oder Robotik, die die Aufgaben übernehmen.
- Vielseitigkeit: Manueller Betrieb kann in verschiedenen Anwendungen und Branchen eingesetzt werden, da er sich oft an wechselnde Anforderungen und Aufgaben anpassen kann. Beispiele reichen von handwerklichen Arbeiten bis hin zu einfachen Produktionsprozessen.
- Kontrolle und Anpassung: Im manuellen Betrieb können Bediener Prozesse in Echtzeit überwachen und bei Bedarf anpassen. Dies ermöglicht eine schnelle Reaktion auf unvorhergesehene Probleme oder Änderungen in den Anforderungen.
- Beispiele für manuellen Betrieb: Hier sind einige Beispiele für manuellen Betrieb in verschiedenen Bereichen:
- Handwerkliche Tätigkeiten wie das Schreinern, Schweißen oder Malen.
- Manuelle Montage und Fertigung, bei der Mitarbeiter Bauteile zusammenbauen oder Produkte herstellen.
- Bedienen von Baumaschinen wie Baggern, Bulldozern oder Gabelstaplern.
- Manuelle Qualitätskontrolle, bei der Produkte visuell überprüft werden, um Mängel zu erkennen.
- Manuelle Bedienung von Maschinen in Kleinbetrieben oder Werkstätten.
- Vor- und Nachteile: Der manuelle Betrieb bietet Flexibilität und die Möglichkeit, komplexe Aufgaben zu bewältigen, kann jedoch in vielen Fällen langsamer sein als automatisierte Prozesse. Er ist auch anfälliger für menschliche Fehler und Ermüdung.
In vielen Bereichen und Anwendungen kann der manuelle Betrieb weiterhin von großer Bedeutung sein, insbesondere wenn es um kreative Arbeiten, Anpassungsfähigkeit und die Erfüllung spezifischer Anforderungen geht. Es ist jedoch wichtig zu beachten, dass viele Branchen zunehmend auf Automatisierung und Digitalisierung setzen, um Effizienz und Präzision zu steigern.
Pulverbeschichtung:
Die Pulverbeschichtungstechnik ist ein vielseitiges Verfahren zur Oberflächenbeschichtung von verschiedenen Werkstücken und findet in einer Vielzahl von Branchen Anwendung. Bei diesem Verfahren wird ein trockenes Pulverlackmaterial verwendet, das elektrostatisch aufgeladen und dann auf das zu beschichtende Werkstück gesprüht oder aufgetragen wird. Der Prozess zeichnet sich durch seine Umweltfreundlichkeit aus, da im Gegensatz zu flüssigen Beschichtungsmethoden keine flüchtigen organischen Verbindungen (VOCs) entstehen.
Das Pulver wird aufgrund der elektrostatischen Ladung gleichmäßig auf der Oberfläche des Werkstücks verteilt. Anschließend wird das Werkstück in einem Ofen erwärmt, wodurch das Pulver schmilzt, zu einer homogenen Beschichtung fusioniert und aushärtet. Das Ergebnis ist eine strapazierfähige und langlebige Oberfläche mit ausgezeichneter Beständigkeit gegenüber Korrosion, Chemikalien und UV-Strahlung.
Die Pulverbeschichtung bietet eine breite Palette von Farben, Oberflächenstrukturen und Effekten, die den individuellen Anforderungen verschiedener Anwendungen gerecht werden. Von glatten und matten Oberflächen bis hin zu metallischen und texturierten Finishs sind den Gestaltungsmöglichkeiten kaum Grenzen gesetzt.
In der Automobilindustrie wird die Pulverbeschichtung zur Beschichtung von Fahrzeugteilen wie Felgen, Stoßstangen und Fahrwerksteilen eingesetzt, um eine ästhetisch ansprechende Oberfläche sowie Schutz vor Korrosion und Abrieb zu gewährleisten. In der Architektur findet sie Anwendung bei der Beschichtung von Fassaden, Geländern und Fensterrahmen, um Gebäuden eine attraktive und langlebige Oberfläche zu verleihen.
Durch ihre Vielseitigkeit, Haltbarkeit und Umweltfreundlichkeit ist die Pulverbeschichtung zu einem beliebten Beschichtungsverfahren in vielen Industriezweigen geworden und wird auch in Zukunft eine wichtige Rolle spielen.
Werkstückvorbereitung:
Die Werkstückvorbereitung ist ein entscheidender Schritt im Pulverbeschichtungsprozess, der maßgeblich die Qualität und Haltbarkeit der Beschichtung beeinflusst. Eine gründliche Vorbereitung der Werkstücke stellt sicher, dass sie frei von Verunreinigungen, Ölen, Fetten, Rost, alten Beschichtungen und anderen Rückständen sind, die die Haftung der Pulverbeschichtung beeinträchtigen könnten.
Der Prozess der Werkstückvorbereitung beginnt oft mit einer gründlichen Reinigung, um jegliche Verunreinigungen von der Oberfläche zu entfernen. Dies kann durch verschiedene Methoden erfolgen, einschließlich Entfettung, Entrostung, Sandstrahlen oder chemische Reinigung. Entfettung ist besonders wichtig, um Öle, Fette und andere organische Verbindungen zu entfernen, die die Haftung der Beschichtung beeinträchtigen könnten.
Nach der Reinigung kann je nach den Anforderungen des spezifischen Projekts eine weitere Vorbehandlung erforderlich sein. Dies kann das Entfernen von Rost und Korrosion, das Auftragen von Phosphatierungs- oder Chromatierungsschichten oder das Anwenden anderer chemischer Behandlungen umfassen, um die Oberfläche zu passivieren und die Haftung der Beschichtung zu verbessern.
Darüber hinaus kann die Werkstückvorbereitung auch das Vorwärmen der Werkstücke umfassen, um die Haftung der Beschichtung zu verbessern und die Aushärtung des Pulvers zu beschleunigen. Maskierung und Abdeckung von Bereichen, die nicht beschichtet werden sollen, gehören ebenfalls zur Vorbereitung der Werkstücke.
Eine sorgfältige und gründliche Werkstückvorbereitung ist entscheidend, um sicherzustellen, dass die Pulverbeschichtung eine gleichmäßige, haltbare und hochwertige Beschichtung bildet. Eine ordnungsgemäße Vorbereitung der Werkstücke trägt dazu bei, die Lebensdauer der Beschichtung zu verlängern und eine hohe Kundenzufriedenheit sicherzustellen.
Pulverlack:
Pulverlacke sind trockene, pulverförmige Beschichtungsmaterialien, die in der Pulverbeschichtungstechnik verwendet werden, um Oberflächen von Werkstücken zu beschichten. Sie bestehen aus einem Gemisch aus pulverförmigen Harzen, Pigmenten, Additiven und gegebenenfalls Füllstoffen. Pulverlacke sind in einer Vielzahl von Farben, Glanzgraden und chemischen Zusammensetzungen erhältlich, um den Anforderungen verschiedener Anwendungen gerecht zu werden.
Der Pulverlack wird elektrostatisch aufgeladen und dann auf das zu beschichtende Werkstück gesprüht oder aufgetragen. Die elektrostatische Aufladung bewirkt, dass das Pulver gleichmäßig auf der Oberfläche des Werkstücks haftet und eine gleichmäßige Beschichtung bildet. Nach dem Auftragen wird das Werkstück in einem Ofen erhitzt, wodurch das Pulver schmilzt, sich zu einer glatten Beschichtung verbindet und aushärtet.
Pulverlacke bieten eine Vielzahl von Vorteilen gegenüber flüssigen Lacken, darunter eine verbesserte Haltbarkeit, chemische Beständigkeit, Witterungsbeständigkeit und UV-Beständigkeit. Sie enthalten in der Regel keine flüchtigen organischen Verbindungen (VOCs) und sind daher umweltfreundlicher. Darüber hinaus ermöglichen Pulverlacke eine effiziente Materialnutzung, da überschüssiges Material wiederverwendet werden kann.
Die Auswahl des richtigen Pulverlacks hängt von verschiedenen Faktoren ab, darunter die Art des zu beschichtenden Substrats, die gewünschte Farbe und Oberflächenbeschaffenheit, die Umgebungsbedingungen und die Anforderungen an die Beschichtung (z. B. Korrosionsbeständigkeit, Chemikalienbeständigkeit). Pulverlacke sind in verschiedenen Formulierungen erhältlich, einschließlich Polyester, Epoxid, Polyurethan, Acryl und Hybridpulvern.
Insgesamt sind Pulverlacke eine vielseitige und effektive Beschichtungslösung, die in einer Vielzahl von Anwendungen eingesetzt werden, darunter Automobil, Architektur, Möbel, Metallverarbeitung und mehr. Ihre Haltbarkeit, Vielseitigkeit und Umweltfreundlichkeit machen sie zu einer attraktiven Wahl für Hersteller und Endverbraucher gleichermaßen.
Elektrostatischer Pulverauftrag:
Der elektrostatische Pulverauftrag ist ein entscheidender Schritt im Pulverbeschichtungsprozess, bei dem das Pulverlackmaterial elektrostatisch aufgeladen und dann auf das zu beschichtende Werkstück aufgetragen wird. Dieser Prozess ermöglicht eine gleichmäßige Verteilung des Pulvers auf der Oberfläche des Werkstücks und eine effiziente Nutzung des Beschichtungsmaterials.
Der elektrostatische Pulverauftrag erfolgt in der Regel mithilfe einer Pulverbeschichtungspistole, die das Pulver durch Druckluft oder pneumatisch erzeugten Luftstrom ausstößt. Beim Verlassen der Pistole wird das Pulver durch einen elektrischen Ladungsimpuls positiv aufgeladen. Das zu beschichtende Werkstück wird gleichzeitig geerdet oder negativ geladen.
Durch die elektrostatische Anziehung zwischen dem positiv geladenen Pulver und dem geerdeten oder negativ geladenen Werkstück haftet das Pulver gleichmäßig und effizient an der Oberfläche des Werkstücks. Dies ermöglicht eine präzise Steuerung des Pulverauftrags und eine hohe Übertragungseffizienz, da nur eine minimale Menge an Pulver verschwendet wird.
Der elektrostatische Pulverauftrag bietet eine Reihe von Vorteilen gegenüber anderen Beschichtungsmethoden, darunter eine verbesserte Beschichtungsqualität, eine gleichmäßige Pulververteilung, eine erhöhte Produktivität und eine geringere Umweltbelastung. Da das Pulver nur auf die zu beschichtende Oberfläche aufgetragen wird und nicht in die Umgebungsluft gelangt, entstehen keine schädlichen Dämpfe oder Emissionen.
Insgesamt ist der elektrostatische Pulverauftrag ein wichtiger Schritt im Pulverbeschichtungsprozess, der dazu beiträgt, hochwertige und langlebige Beschichtungen zu erzeugen. Durch die präzise Steuerung des Pulverauftrags und die effiziente Nutzung des Beschichtungsmaterials ermöglicht er eine kostengünstige und umweltfreundliche Beschichtungslösung für eine Vielzahl von Anwendungen.
Pulverrückgewinnung:
Die Pulverrückgewinnung ist ein wesentlicher Bestandteil des Pulverbeschichtungsprozesses, der darauf abzielt, überschüssiges Pulver, das nicht auf das Werkstück aufgetragen wurde, zu sammeln und wiederzuverwenden. Dieser Schritt trägt nicht nur zur Reduzierung von Abfall und Materialkosten bei, sondern auch zur Umweltfreundlichkeit des Beschichtungsprozesses.
Während des Pulverbeschichtungsvorgangs wird nicht das gesamte aufgeladene Pulver auf das Werkstück übertragen. Ein Teil des Pulvers kann während des Sprühens die Oberfläche des Werkstücks nicht erreichen und wird stattdessen in der Umgebungsluft oder in der Pulverbeschichtungskabine verteilt. Dieses überschüssige Pulver wird als „Überlack“ bezeichnet.
Um das überschüssige Pulver zurückzugewinnen, werden verschiedene Methoden und Systeme eingesetzt. Eine häufig verwendete Methode ist die Verwendung von Pulverrückgewinnungssystemen, die überschüssiges Pulver aus der Luft abscheiden und in einem Auffangbehälter sammeln. Dieses gesammelte Pulver kann dann durch Sieben oder Filtern gereinigt und wieder in den Pulverbeschichtungsprozess zurückgeführt werden.
Ein weiterer Ansatz zur Pulverrückgewinnung besteht darin, das überschüssige Pulver mithilfe von Vibration oder Druckluft von den Oberflächen in der Pulverbeschichtungskabine zu lösen und in ein Rückgewinnungssystem zu leiten. Dies ermöglicht eine effiziente Sammlung und Wiederverwendung des Pulvers, ohne dass zusätzliche Reinigungs- oder Siebungsprozesse erforderlich sind.
Die Pulverrückgewinnung trägt nicht nur zur Reduzierung von Abfall und Materialkosten bei, sondern auch zur Verbesserung der Produktionskosten und -effizienz. Durch die Wiederverwendung von Pulver wird der Materialverbrauch und die Entsorgungskosten reduziert, was zu einer nachhaltigeren und umweltfreundlicheren Produktion beiträgt.
Insgesamt ist die Pulverrückgewinnung ein unverzichtbarer Bestandteil des Pulverbeschichtungsprozesses, der dazu beiträgt, die Effizienz, Wirtschaftlichkeit und Umweltfreundlichkeit der Beschichtungslösung zu verbessern.
Trocknungsofen:
Der Trocknungsofen ist eine wesentliche Komponente im Pulverbeschichtungsprozess, der verwendet wird, um das aufgetragene Pulver auf dem Werkstück zu schmelzen, zu verschmelzen und zu härten. Nachdem das Pulver elektrostatisch aufgeladen und auf das Werkstück aufgetragen wurde, wird das Werkstück in den Trocknungsofen gebracht, wo es einer kontrollierten Erhitzung unterzogen wird.
Die Temperatur und die Verweildauer im Trocknungsofen sind entscheidend für die Qualität und Haltbarkeit der Beschichtung. Typischerweise liegt die Aushärtungstemperatur für Pulverlacke zwischen 140°C und 220°C, je nach den spezifischen Anforderungen des Beschichtungsmaterials und der Werkstücke. Während des Aushärteprozesses schmilzt das Pulver und bildet eine homogene Beschichtung, die sich mit der Oberfläche des Werkstücks verbindet.
Der Trocknungsofen kann verschiedene Konfigurationen und Funktionen aufweisen, um den Anforderungen des Beschichtungsprozesses gerecht zu werden. Einige Öfen sind mit einem Förderband oder einer Aufhängungsvorrichtung ausgestattet, um die Werkstücke durch den Ofen zu transportieren und eine gleichmäßige Erwärmung zu gewährleisten. Andere Öfen können mit Infrarotstrahlern, Heißluftgebläsen oder Konvektionssystemen ausgestattet sein, um die Wärme gleichmäßig zu verteilen und eine schnelle Aushärtung zu ermöglichen.
Die Kontrolle der Temperatur und der Aushärtezeit im Trocknungsofen ist entscheidend, um Überhitzung, Verbrennung des Pulvers oder andere Beschichtungsfehler zu vermeiden. Moderne Trocknungsofen sind oft mit präzisen Temperaturreglern und Zeitsteuerungen ausgestattet, um eine genaue Steuerung des Aushärteprozesses zu ermöglichen und eine gleichbleibende Qualität der Beschichtung sicherzustellen.
Insgesamt ist der Trocknungsofen ein wesentlicher Bestandteil des Pulverbeschichtungsprozesses, der dazu beiträgt, hochwertige und langlebige Beschichtungen zu erzeugen. Durch die kontrollierte Erwärmung und Aushärtung des Pulvers im Ofen werden die gewünschten mechanischen und chemischen Eigenschaften der Beschichtung erreicht, um den Anforderungen verschiedener Anwendungen gerecht zu werden.
Aushärtung:
Die Aushärtung ist ein kritischer Schritt im Pulverbeschichtungsprozess, bei dem das aufgetragene Pulver durch Erhitzen im Trocknungsofen geschmolzen, verschmolzen und ausgehärtet wird. Dieser Prozess bewirkt eine chemische Reaktion im Pulverlack, die zu einer dauerhaften Verbindung mit der Oberfläche des Werkstücks führt und die gewünschten mechanischen und chemischen Eigenschaften der Beschichtung erzeugt.
Während des Aushärteprozesses wird das Werkstück auf eine bestimmte Temperatur erhitzt, die je nach den Anforderungen des verwendeten Pulverlacks und der Werkstücke variieren kann. Die Aushärtungstemperatur liegt typischerweise zwischen 140°C und 220°C und wird für eine bestimmte Zeit gehalten, um sicherzustellen, dass das Pulver vollständig geschmolzen und ausgehärtet ist.
Die Aushärtung bewirkt eine chemische Vernetzung der Moleküle im Pulverlack, was zu einer harten, widerstandsfähigen Beschichtung führt, die eine hohe Beständigkeit gegenüber Kratzern, Abrieb, Chemikalien und UV-Strahlung aufweist. Darüber hinaus verbessert die Aushärtung die Haftung der Beschichtung auf der Oberfläche des Werkstücks und gewährleistet eine gleichmäßige Dicke und Struktur der Beschichtung.
Die Kontrolle der Aushärtungsparameter, einschließlich Temperatur und Verweildauer im Ofen, ist entscheidend, um eine gleichbleibende Qualität der Beschichtung zu gewährleisten und Beschichtungsfehler zu vermeiden. Moderne Trocknungsofen sind mit präzisen Temperaturreglern und Zeitsteuerungen ausgestattet, um eine genaue Steuerung des Aushärteprozesses zu ermöglichen.
Insgesamt ist die Aushärtung ein entscheidender Schritt im Pulverbeschichtungsprozess, der dazu beiträgt, hochwertige und langlebige Beschichtungen zu erzeugen. Durch die chemische Vernetzung des Pulverlacks während der Aushärtung werden die gewünschten Eigenschaften der Beschichtung erreicht, um den Anforderungen verschiedener Anwendungen gerecht zu werden.
Vorbehandlung:
Die Vorbehandlung ist ein entscheidender Schritt im Pulverbeschichtungsprozess, der dazu dient, die Oberfläche des Werkstücks auf die nachfolgende Beschichtung vorzubereiten und die Haftung und Haltbarkeit der Beschichtung zu verbessern. Dieser Schritt ist entscheidend, um sicherzustellen, dass die Beschichtung eine gleichmäßige und dauerhafte Verbindung mit der Oberfläche des Werkstücks eingeht und eine hohe Qualität aufweist.
Die Vorbehandlung kann mehrere Prozesse umfassen, abhängig von den spezifischen Anforderungen des zu beschichtenden Werkstücks und der Beschichtungsanwendung. Zu den gängigen Vorbehandlungsmethoden gehören Entfettung, Entrostung, Phosphatierung, Chromatierung und Passivierung.
Die Entfettung beinhaltet die Entfernung von Ölen, Fetten und anderen Verunreinigungen von der Oberfläche des Werkstücks. Dies kann durch chemische Reinigungsmittel, alkalische Lösungen oder Lösungsmittel erfolgen, um sicherzustellen, dass die Oberfläche sauber und frei von Verunreinigungen ist, die die Haftung der Beschichtung beeinträchtigen könnten.
Die Entrostung ist der Prozess, bei dem Rost und Korrosion von der Oberfläche des Werkstücks entfernt werden. Dies kann durch mechanisches Entfernen, Sandstrahlen oder chemische Entrostungsmittel erfolgen, um eine saubere und rostfreie Oberfläche zu gewährleisten.
Die Phosphatierung und Chromatierung sind Prozesse, bei denen eine chemische Konversionsschicht auf der Oberfläche des Werkstücks erzeugt wird. Diese Schicht verbessert die Haftung und Korrosionsbeständigkeit der Beschichtung, indem sie eine bessere Oberflächenadhäsion und chemische Bindung ermöglicht.
Die Passivierung ist ein Prozess, bei dem eine Schutzschicht auf der Oberfläche des Werkstücks erzeugt wird, um die Oberfläche vor Korrosion und Oxidation zu schützen. Dies kann durch chemische Behandlungen oder das Auftragen von speziellen Beschichtungen erfolgen.
Insgesamt ist die Vorbehandlung ein wesentlicher Schritt im Pulverbeschichtungsprozess, der dazu beiträgt, die Qualität, Haltbarkeit und Leistung der Beschichtung zu verbessern. Durch die sorgfältige Vorbereitung der Oberfläche des Werkstücks können Beschichtungsfehler vermieden und eine hochwertige Beschichtung gewährleistet werden.
Entfettung:
Die Entfettung ist ein wichtiger Schritt in der Vorbehandlung von Werkstücken vor dem Pulverbeschichtungsprozess. Ihr Ziel ist es, alle Öle, Fette, Schmiermittel und andere organische Verunreinigungen von der Oberfläche des Werkstücks zu entfernen, um eine saubere und fettfreie Oberfläche zu schaffen. Eine gründliche Entfettung ist entscheidend, um sicherzustellen, dass die Pulverbeschichtung eine gleichmäßige Haftung aufweist und eine hochwertige Oberflächenfinish liefert.
Es gibt verschiedene Methoden, um die Entfettung durchzuführen, darunter:
- Chemische Entfettung: Dies ist eine häufig verwendete Methode, bei der das Werkstück in einem chemischen Reinigungsmittel oder einer Entfettungslösung eingetaucht oder besprüht wird. Diese Reinigungsmittel lösen und emulgieren die Öle und Fette von der Oberfläche des Werkstücks, die dann mit Wasser abgespült werden.
- Mechanische Entfettung: Bei dieser Methode wird das Werkstück mechanisch gereinigt, um die Öle und Fette zu entfernen. Dies kann durch Bürsten, Schleifen, Strahlen oder Spülen mit Hochdruckwasser erfolgen. Mechanische Entfettungsmethoden sind besonders effektiv bei der Entfernung von fest haftenden Verunreinigungen.
- Lösungsmittelreinigung: Diese Methode beinhaltet das Reinigen des Werkstücks mit organischen Lösungsmitteln, die die Öle und Fette lösen und entfernen. Das Werkstück wird in einem Bad aus Lösungsmittel eingetaucht oder mit einem Lösungsmittel besprüht, um die Verunreinigungen zu lösen, und anschließend getrocknet.
Die Auswahl der geeigneten Entfettungsmethode hängt von verschiedenen Faktoren ab, darunter die Art der Verunreinigungen, die Art des zu beschichtenden Werkstücks und die Anforderungen der spezifischen Anwendung. Eine gründliche Entfettung ist entscheidend, um sicherzustellen, dass die Pulverbeschichtung eine gleichmäßige Haftung aufweist und eine hochwertige Oberflächenfinish liefert.
Entrostung:
Die Entrostung ist ein entscheidender Schritt in der Vorbehandlung von Werkstücken vor dem Pulverbeschichtungsprozess. Ihr Hauptziel ist es, alle Rost- und Korrosionsschichten von der Oberfläche des Werkstücks zu entfernen, um eine saubere, glatte und metallisch reine Oberfläche zu schaffen. Eine gründliche Entrostung ist unerlässlich, um sicherzustellen, dass die Pulverbeschichtung eine gleichmäßige Haftung aufweist und eine langfristige Korrosionsbeständigkeit bietet.
Es gibt verschiedene Methoden, um die Entrostung durchzuführen, abhängig von der Art und dem Ausmaß der Rostbildung sowie den spezifischen Anforderungen des zu beschichtenden Werkstücks:
- Mechanische Entrostung: Diese Methode umfasst das mechanische Entfernen von Rost und Korrosion durch Schleifen, Bürsten, Strahlen oder Sandstrahlen. Mechanische Entrostungsmethoden sind besonders effektiv bei der Entfernung von fest haftenden Rostschichten und können eine saubere und glatte Oberfläche hinterlassen.
- Chemische Entrostung: Bei dieser Methode wird das Werkstück in eine chemische Entrostungslösung eingetaucht oder besprüht, die den Rost chemisch auflöst und von der Oberfläche des Werkstücks entfernt. Chemische Entrostungsmittel können Säuren, Basen oder spezielle Rostlöser enthalten, die den Rost effektiv auflösen, ohne das Werkstück zu beschädigen.
- Elektrolytische Entrostung: Dies ist eine spezialisierte Entrostungsmethode, bei der das Werkstück in eine Elektrolytlösung eingetaucht wird und eine elektrische Spannung angelegt wird. Durch den Elektrolyseprozess wird der Rost von der Oberfläche des Werkstücks abgelöst und in der Elektrolytlösung neutralisiert.
Die Auswahl der geeigneten Entrostungsmethode hängt von verschiedenen Faktoren ab, darunter die Art und das Ausmaß der Rostbildung, die Art des zu beschichtenden Werkstücks und die Anforderungen der spezifischen Anwendung. Eine gründliche Entrostung ist entscheidend, um sicherzustellen, dass die Pulverbeschichtung eine gleichmäßige Haftung aufweist und eine langfristige Korrosionsbeständigkeit bietet.
Phosphatierung:
Die Phosphatierung ist ein wichtiger Prozess in der Vorbehandlung von Werkstücken vor dem Pulverbeschichtungsprozess. Ihr Hauptziel ist es, eine chemische Konversionsschicht auf der Oberfläche des Werkstücks zu erzeugen, die die Haftung und Haltbarkeit der Pulverbeschichtung verbessert und gleichzeitig eine gewisse Korrosionsbeständigkeit bietet.
Während des Phosphatierungsprozesses wird das Werkstück in eine phosphathaltige Lösung eingetaucht oder besprüht. Diese Lösung enthält Phosphorsäure und andere chemische Zusätze, die eine Reaktion mit der Metalloberfläche des Werkstücks eingehen. Durch diese Reaktion entsteht eine dünne, poröse Schicht aus Phosphatverbindungen auf der Oberfläche des Werkstücks.
Die gebildete Phosphatschicht verbessert die Haftung der Pulverbeschichtung, indem sie eine bessere Oberflächenadhäsion und chemische Bindung ermöglicht. Darüber hinaus bietet die Phosphatschicht eine gewisse Korrosionsbeständigkeit, indem sie die Metalloberfläche vor Feuchtigkeit und Korrosion schützt.
Die Phosphatierung kann für verschiedene Metalle wie Stahl, Aluminium und Zinklegierungen durchgeführt werden. Die spezifische Formulierung der Phosphatierungslösung und die Prozessparameter können je nach den Anforderungen der spezifischen Anwendung variieren.
Insgesamt ist die Phosphatierung ein wichtiger Schritt, um die Qualität, Haltbarkeit und Leistung der Pulverbeschichtung zu verbessern. Durch die Bildung einer chemischen Konversionsschicht auf der Oberfläche des Werkstücks trägt die Phosphatierung dazu bei, eine hochwertige und langfristig haltbare Beschichtung zu gewährleisten.
Chromatierung:
Die Chromatierung ist ein wichtiger Prozess in der Vorbehandlung von Werkstücken vor dem Pulverbeschichtungsprozess. Ihr Hauptziel ist es, eine dünnere chemische Konversionsschicht auf der Oberfläche des Werkstücks zu erzeugen, die die Haftung und Haltbarkeit der Pulverbeschichtung verbessert und gleichzeitig eine gewisse Korrosionsbeständigkeit bietet.
Während des Chromatierungsprozesses wird das Werkstück in eine Chromatierungslösung eingetaucht oder besprüht. Diese Lösung enthält Chrom(VI)-Verbindungen oder Chrom(III)-Verbindungen, die eine Reaktion mit der Metalloberfläche des Werkstücks eingehen. Durch diese Reaktion entsteht eine dünne Schicht aus Chromverbindungen auf der Oberfläche des Werkstücks.
Die gebildete Chromatierungsschicht verbessert die Haftung der Pulverbeschichtung, indem sie eine bessere Oberflächenadhäsion und chemische Bindung ermöglicht. Darüber hinaus bietet die Chromatierungsschicht eine gewisse Korrosionsbeständigkeit, indem sie die Metalloberfläche vor Feuchtigkeit und Korrosion schützt.
Die Chromatierung kann für verschiedene Metalle wie Aluminium, Zinklegierungen und verzinkten Stahl durchgeführt werden. Die spezifische Formulierung der Chromatierungslösung und die Prozessparameter können je nach den Anforderungen der spezifischen Anwendung variieren.
Es ist jedoch zu beachten, dass Chromatierungsprozesse aufgrund der Verwendung von Chrom(VI)-Verbindungen zunehmend durch umweltfreundlichere Alternativen ersetzt werden, die keine giftigen Chrom(VI)-Verbindungen enthalten. Alternativen wie Passivierungen mit Titan oder Zirkon bieten ähnliche Verbesserungen der Haftung und Korrosionsbeständigkeit, sind jedoch umweltfreundlicher und sicherer für die Arbeitnehmer.
Insgesamt ist die Chromatierung ein wichtiger Schritt, um die Qualität, Haltbarkeit und Leistung der Pulverbeschichtung zu verbessern. Durch die Bildung einer chemischen Konversionsschicht auf der Oberfläche des Werkstücks trägt die Chromatierung dazu bei, eine hochwertige und langfristig haltbare Beschichtung zu gewährleisten.
Passivierung:
Die Passivierung ist ein wichtiger Schritt in der Vorbehandlung von Werkstücken vor dem Pulverbeschichtungsprozess, insbesondere für Edelstahlwerkstücke. Ihr Hauptziel ist es, eine dünne Schutzschicht auf der Oberfläche des Werkstücks zu erzeugen, um die Korrosionsbeständigkeit zu verbessern und die Bildung von Rost zu verhindern.
Während des Passivierungsprozesses wird das Werkstück in eine Passivierungslösung eingetaucht oder besprüht. Diese Lösung enthält chemische Verbindungen wie Chromate oder Nitrate, die eine Reaktion mit der Metalloberfläche des Werkstücks eingehen. Durch diese Reaktion entsteht eine dünne Schutzschicht aus Oxiden oder Nitriden auf der Oberfläche des Werkstücks.
Die gebildete Passivierungsschicht verbessert die Korrosionsbeständigkeit des Werkstücks, indem sie die Oberfläche vor Feuchtigkeit, Sauerstoff und anderen korrosiven Substanzen schützt. Sie verhindert auch die Bildung von Rost und verlängert so die Lebensdauer des Werkstücks.
Die Passivierung wird häufig für Edelstahlwerkstücke verwendet, da diese aufgrund ihrer Legierungszusammensetzung bereits eine gewisse Korrosionsbeständigkeit aufweisen. Die Passivierung verstärkt diese Eigenschaften jedoch und verbessert die Leistung des Edelstahls in aggressiven Umgebungen.
Es ist wichtig zu beachten, dass die Passivierung nicht nur die Korrosionsbeständigkeit verbessert, sondern auch die Haftung und Haltbarkeit der anschließenden Pulverbeschichtung. Durch die Bildung einer sauberen und chemisch stabilen Oberfläche verbessert die Passivierung die Adhäsion der Beschichtung und verhindert das Auftreten von Beschichtungsfehlern wie Blasenbildung oder Abblättern.
Insgesamt ist die Passivierung ein wichtiger Schritt, um die Qualität, Haltbarkeit und Leistung von Werkstücken vor dem Pulverbeschichtungsprozess zu verbessern. Durch die Bildung einer schützenden Oberflächenschicht trägt die Passivierung dazu bei, eine hochwertige und langfristig haltbare Beschichtung zu gewährleisten.
Vorwärmen:
Das Vorwärmen ist ein wichtiger Schritt im Pulverbeschichtungsprozess, der dazu dient, die Werkstücke vor dem eigentlichen Beschichtungsvorgang auf eine bestimmte Temperatur zu bringen. Diese Vorwärmung kann mehrere Zwecke erfüllen und trägt dazu bei, die Qualität und Haltbarkeit der Pulverbeschichtung zu verbessern.
Ein Hauptzweck des Vorwärmens besteht darin, die Werkstücke auf eine optimale Temperatur zu bringen, um eine bessere Haftung und Verteilung des Pulvers zu ermöglichen. Durch das Vorwärmen werden Feuchtigkeit und Kondensation von der Oberfläche des Werkstücks entfernt, was die Haftung der Beschichtung verbessert und das Risiko von Beschichtungsfehlern wie Blasenbildung oder Abblättern verringert.
Darüber hinaus kann das Vorwärmen dazu beitragen, die Aushärtezeit der Beschichtung zu verkürzen, indem es den Aushärtungsprozess beschleunigt. Indem die Werkstücke vor dem Eintritt in den Trocknungsofen vorgewärmt werden, kann die Zeit, die sie im Ofen verbringen müssen, reduziert werden, was zu einer höheren Produktivität und Effizienz des Beschichtungsprozesses führt.
Das Vorwärmen kann auch dazu beitragen, die thermische Belastung der Werkstücke während des Beschichtungsvorgangs zu verringern, insbesondere bei empfindlichen Materialien wie Kunststoffen oder Kompositen. Indem die Werkstücke allmählich auf die Betriebstemperatur gebracht werden, können Spannungen und Verformungen minimiert werden, was zu einer besseren Qualität der beschichteten Teile führt.
Die genaue Temperatur und die Dauer des Vorwärmens hängen von verschiedenen Faktoren ab, darunter die Art der zu beschichtenden Werkstücke, die Art des verwendeten Pulverlacks und die spezifischen Anforderungen der Beschichtungsanwendung. Insgesamt ist das Vorwärmen ein wichtiger Schritt, um die Qualität, Haltbarkeit und Leistung der Pulverbeschichtung zu verbessern und eine gleichmäßige Beschichtung auf den Werkstücken zu gewährleisten.
Maskierung:
Die Maskierung ist ein entscheidender Schritt im Pulverbeschichtungsprozess, der dazu dient, bestimmte Bereiche oder Teile des Werkstücks vor der Beschichtung zu schützen. Dieser Prozess ist besonders wichtig, wenn bestimmte Bereiche des Werkstücks nicht beschichtet werden sollen oder wenn verschiedene Farben oder Beschichtungstypen auf demselben Werkstück verwendet werden.
Es gibt verschiedene Methoden und Materialien, die für die Maskierung verwendet werden können, je nach den spezifischen Anforderungen der Beschichtungsanwendung:
- Klebeband und Abdeckfolien: Maskierungsfolien und Klebebänder werden verwendet, um bestimmte Bereiche des Werkstücks abzudecken und vor dem Auftragen des Pulvers zu schützen. Diese Materialien sind flexibel und können leicht auf die gewünschten Bereiche aufgetragen und entfernt werden.
- Silikonstopfen und Kaptonbänder: Für präzise Maskierungsanforderungen können Silikonstopfen und Kaptonbänder verwendet werden, um kleine Bohrungen, Gewindebohrungen oder andere komplizierte Bereiche abzudecken. Diese Materialien sind hitzebeständig und bieten eine effektive Abdichtung gegen das Eindringen von Pulver.
- Maskierungslack: Spezielle Maskierungslacke können auf die Oberfläche des Werkstücks aufgetragen und nach dem Trocknen verwendet werden, um bestimmte Bereiche abzudecken. Maskierungslacke bieten eine temporäre Beschichtung, die vor dem Beschichten schützt und nach dem Aushärten leicht entfernt werden kann.
Die Auswahl der geeigneten Maskierungsmethode hängt von verschiedenen Faktoren ab, darunter die Art der zu schützenden Bereiche, die Komplexität des Werkstücks und die Anforderungen der spezifischen Beschichtungsanwendung. Eine sorgfältige Maskierung ist entscheidend, um sicherzustellen, dass die beschichteten Teile die gewünschten Eigenschaften aufweisen und keine unerwünschten Beschichtungsfehler auftreten.
Insgesamt ist die Maskierung ein wichtiger Schritt, um die Qualität und Genauigkeit des Pulverbeschichtungsprozesses zu gewährleisten und sicherzustellen, dass die beschichteten Teile die erforderlichen Spezifikationen erfüllen. Durch die Verwendung geeigneter Maskierungstechniken können hochwertige Beschichtungen erzielt werden, die den Anforderungen verschiedener Anwendungen gerecht werden.
Entlackung:
Die Entlackung ist ein wichtiger Prozess im Pulverbeschichtungsverfahren, der dazu dient, alte Beschichtungen von Werkstücken zu entfernen, um eine saubere Oberfläche für die erneute Beschichtung zu schaffen. Dieser Schritt ist notwendig, wenn alte Beschichtungen abgenutzt, beschädigt oder unerwünscht sind und vor dem Auftragen einer neuen Pulverbeschichtung entfernt werden müssen.
Es gibt verschiedene Methoden zur Entlackung, abhängig von der Art der vorhandenen Beschichtung und den spezifischen Anforderungen des zu bearbeitenden Werkstücks:
- Chemische Entlackung: Bei dieser Methode werden chemische Lösungen oder Entlackungsmittel auf die Oberfläche des Werkstücks aufgetragen, um die alte Beschichtung zu lösen und zu entfernen. Diese Lösungen enthalten oft aggressive Chemikalien, die die Beschichtung auflösen und von der Oberfläche abheben.
- Mechanische Entlackung: Mechanische Methoden wie Schleifen, Sandstrahlen oder Bürsten werden verwendet, um die alte Beschichtung mechanisch von der Oberfläche des Werkstücks zu entfernen. Diese Methoden sind besonders effektiv bei hartnäckigen oder stark haftenden Beschichtungen.
- Thermische Entlackung: Diese Methode beinhaltet das Erhitzen des Werkstücks auf hohe Temperaturen, um die alte Beschichtung zu verbrennen oder zu zerstören. Nach dem Erhitzen kann die abgebrannte Beschichtung einfach entfernt werden, um eine saubere Oberfläche für die erneute Beschichtung zu schaffen.
Die Auswahl der geeigneten Entlackungsmethode hängt von verschiedenen Faktoren ab, darunter die Art der vorhandenen Beschichtung, die Art des zu bearbeitenden Werkstücks und die Anforderungen der spezifischen Beschichtungsanwendung. Eine gründliche Entlackung ist entscheidend, um sicherzustellen, dass die neue Pulverbeschichtung eine gleichmäßige Haftung aufweist und eine hochwertige Oberflächenfinish liefert.
Insgesamt ist die Entlackung ein wichtiger Schritt, um die Qualität und Haltbarkeit von Pulverbeschichtungen zu gewährleisten und sicherzustellen, dass die beschichteten Teile die erforderlichen Spezifikationen erfüllen. Durch die Entfernung alter Beschichtungen können Beschichtungsfehler vermieden und eine optimale Leistung der neuen Beschichtung sichergestellt werden.
Schleifen:
Das Schleifen ist ein grundlegender Schritt im Pulverbeschichtungsprozess, der dazu dient, die Oberfläche des Werkstücks vor der Beschichtung zu glätten, Unregelmäßigkeiten zu entfernen und eine gleichmäßige Oberfläche zu erzeugen. Dieser Prozess ist besonders wichtig, um eine optimale Haftung und ein ästhetisch ansprechendes Finish der Pulverbeschichtung sicherzustellen.
Es gibt verschiedene Arten von Schleifmethoden, die je nach den Anforderungen des Werkstücks und der Beschichtungsanwendung eingesetzt werden können:
- Handschleifen: Bei dieser Methode wird das Werkstück manuell mit Schleifpapier oder Schleifvlies abgeschliffen, um Unebenheiten zu beseitigen und die Oberfläche zu glätten. Handschleifen ermöglicht eine präzise Kontrolle über den Schleifvorgang und ist besonders effektiv bei kleineren Werkstücken oder schwer zugänglichen Bereichen.
- Maschinelles Schleifen: Maschinelle Schleifmaschinen wie Bandschleifer, Schwingschleifer oder Exzenterschleifer werden verwendet, um größere Werkstücke effizient zu schleifen und eine gleichmäßige Oberfläche zu erzielen. Maschinelles Schleifen ist besonders geeignet für Serienproduktionen oder große Werkstücke, da es schneller und gleichmäßiger arbeitet als das Handschleifen.
- Sandstrahlen: Beim Sandstrahlen wird das Werkstück mit einem Strahlmittel wie Sand, Glasperlen oder Korundpartikeln unter hohem Druck abgestrahlt, um die Oberfläche zu reinigen und zu glätten. Sandstrahlen ist besonders effektiv bei der Entfernung von Rost, Farbe oder anderen Beschichtungen und hinterlässt eine saubere und aufgeraute Oberfläche für eine verbesserte Haftung der Pulverbeschichtung.
Die Auswahl der geeigneten Schleifmethode hängt von verschiedenen Faktoren ab, darunter die Art und Beschaffenheit des Werkstücks, die gewünschte Oberflächenqualität und die Anforderungen der spezifischen Beschichtungsanwendung. Durch das Schleifen wird die Oberfläche des Werkstücks vorbereitet und optimiert, um eine hochwertige und haltbare Pulverbeschichtung zu gewährleisten.
Grundierung:
Die Grundierung ist ein wesentlicher Schritt im Pulverbeschichtungsprozess, der dazu dient, die Oberfläche des Werkstücks vorzubereiten und die Haftung sowie die Haltbarkeit der Pulverbeschichtung zu verbessern. Diese Schicht bildet die erste Schicht, die auf das Werkstück aufgetragen wird, und dient als Basis für die nachfolgende Pulverbeschichtung.
Es gibt verschiedene Arten von Grundierungen, die je nach den spezifischen Anforderungen der Beschichtungsanwendung verwendet werden können:
- Epoxy-Grundierung: Epoxy-Grundierungen bieten eine ausgezeichnete Haftung auf verschiedenen Untergründen und sorgen für eine starke Verbindung zwischen dem Werkstück und der Pulverbeschichtung. Sie sind besonders geeignet für die Beschichtung von Metallen, Aluminium und anderen nicht porösen Oberflächen.
- Zinkphosphat-Grundierung: Zinkphosphat-Grundierungen bieten eine hohe Korrosionsbeständigkeit und eignen sich besonders für die Beschichtung von Stahlwerkstücken, die einer hohen Feuchtigkeits- oder Korrosionsbelastung ausgesetzt sind. Sie bilden eine schützende Schicht auf der Metalloberfläche und verbessern die Haltbarkeit der Pulverbeschichtung.
- Chromat-Grundierung: Chromat-Grundierungen enthalten chromatische Verbindungen, die eine chemische Konversionsschicht auf der Metalloberfläche erzeugen und die Haftung der Pulverbeschichtung verbessern. Sie bieten auch eine gewisse Korrosionsbeständigkeit und eignen sich für die Beschichtung von Aluminium und anderen Leichtmetallen.
Die Auswahl der geeigneten Grundierung hängt von verschiedenen Faktoren ab, darunter die Art des zu beschichtenden Werkstücks, die Umgebungsbedingungen und die Anforderungen der spezifischen Beschichtungsanwendung. Eine sorgfältige Auswahl und Anwendung der Grundierung ist entscheidend, um eine optimale Haftung und Haltbarkeit der Pulverbeschichtung zu gewährleisten und die Lebensdauer der beschichteten Teile zu verlängern.
Trocknungsofen:
Der Trocknungsofen ist eine wesentliche Komponente im Pulverbeschichtungsprozess, der dazu dient, die aufgetragene Pulverbeschichtung zu trocknen und zu härten. Nachdem das Pulver auf das Werkstück aufgetragen wurde, wird das Werkstück in den Trocknungsofen transportiert, wo es einer kontrollierten Erwärmung unterzogen wird, um das Pulver zu schmelzen und zu einer festen Beschichtung zu verschmelzen.
Der Trocknungsofen arbeitet in mehreren Schritten, um eine ordnungsgemäße Trocknung und Aushärtung der Pulverbeschichtung sicherzustellen:
- Vortrocknung: In diesem ersten Schritt wird das Werkstück langsam auf eine moderate Temperatur erhitzt, um überschüssiges Lösungsmittel oder Wasser aus der Pulverbeschichtung zu verdampfen. Dies hilft, Blasenbildung und andere Beschichtungsfehler zu vermeiden und eine gleichmäßige Trocknung der Beschichtung zu gewährleisten.
- Erhitzung und Aushärtung: Nach der Vortrocknung wird das Werkstück auf eine höhere Temperatur erhitzt, um das Pulver zu schmelzen und zu einer festen Beschichtung zu verschmelzen. Diese Aushärtephase kann je nach den spezifischen Anforderungen der verwendeten Pulverbeschichtung und des Werkstücks unterschiedliche Temperaturen und Zeiten erfordern.
- Abkühlung: Nach der Aushärtephase wird das Werkstück langsam abgekühlt, um eine gleichmäßige Aushärtung der Beschichtung zu gewährleisten und Spannungen im Werkstück zu minimieren. Eine kontrollierte Abkühlung kann dazu beitragen, das Risiko von Beschichtungsfehlern wie Verformungen oder Rissen zu verringern.
Der Trocknungsofen kann verschiedene Konfigurationen und Merkmale aufweisen, darunter:
- Konvektionsofen: Ein Konvektionsofen verwendet geblasene Luft oder heiße Gase, um das Werkstück zu erwärmen und die Pulverbeschichtung zu trocknen und auszuhärten. Diese Öfen bieten eine gleichmäßige Temperaturverteilung und eine schnelle Trocknungs- und Aushärtezeit.
- Infrarotofen: Ein Infrarotofen verwendet Infrarotstrahlung, um das Werkstück zu erwärmen und die Pulverbeschichtung zu trocknen und auszuhärten. Infrarotöfen können eine schnellere Aushärtezeit bieten und sind besonders effektiv für die Beschichtung von dünnen Werkstücken oder empfindlichen Materialien.
Die Auswahl des geeigneten Trocknungsofens hängt von verschiedenen Faktoren ab, darunter die Größe und Form des Werkstücks, die Anforderungen der spezifischen Beschichtungsanwendung und die verfügbaren Ressourcen. Ein effizienter und zuverlässiger Trocknungsofen ist entscheidend, um eine hochwertige und haltbare Pulverbeschichtung zu gewährleisten und die Produktivität des Beschichtungsprozesses zu maximieren.
Vorbehandlung:
Die Vorbehandlung ist ein kritischer Schritt im Pulverbeschichtungsprozess, der dazu dient, die Oberfläche des Werkstücks auf die Beschichtung vorzubereiten und eine optimale Haftung sowie Haltbarkeit der Pulverbeschichtung sicherzustellen. Dieser Schritt umfasst eine Reihe von Prozessen, die darauf abzielen, die Oberfläche zu reinigen, zu entfetten, zu entrosten und gegebenenfalls zu phosphatieren oder zu chromatieren.
Reinigung:
Die Reinigung ist der erste Schritt der Vorbehandlung und beinhaltet die Entfernung von Schmutz, Fett, Ölen und anderen Verunreinigungen von der Oberfläche des Werkstücks. Dies kann durch chemische Reinigungsmittel, Lösungsmittelbäder, Entfettungstanks oder mechanische Reinigungsmethoden wie Bürsten oder Waschen mit Hochdruckwasser erfolgen.
Entfettung:
Die Entfettung ist ein wichtiger Schritt, um Fett- und Ölrückstände von der Oberfläche des Werkstücks zu entfernen. Dies kann durch alkalische oder saure Entfettungslösungen erreicht werden, die Fette und Öle emulgieren und von der Oberfläche abheben. Die Entfettung ist entscheidend, um eine gute Haftung der Pulverbeschichtung zu gewährleisten.
Entrostung:
Die Entrostung beinhaltet die Entfernung von Rost und Korrosion von der Metalloberfläche des Werkstücks. Dies kann durch mechanische Methoden wie Schleifen oder Sandstrahlen erfolgen, um den Rost abzutragen, sowie durch chemische Entrostungslösungen, die den Rost chemisch auflösen und entfernen.
Phosphatierung/Chromatierung:
Die Phosphatierung oder Chromatierung ist ein weiterer wichtiger Schritt, um die Oberfläche des Werkstücks vor der Beschichtung zu behandeln. Diese Prozesse beinhalten die Bildung einer chemischen Konversionsschicht auf der Metalloberfläche, die die Haftung und Haltbarkeit der Pulverbeschichtung verbessert und gleichzeitig eine gewisse Korrosionsbeständigkeit bietet.
Insgesamt ist die Vorbehandlung ein entscheidender Schritt, um die Qualität und Leistung der Pulverbeschichtung zu verbessern. Eine sorgfältige Vorbehandlung stellt sicher, dass die Oberfläche des Werkstücks sauber, glatt und frei von Verunreinigungen ist, was zu einer gleichmäßigen und dauerhaften Beschichtung führt.
Rückgewinnungssystem:
Ein Rückgewinnungssystem ist eine Schlüsselkomponente in einer Pulverbeschichtungsanlage, das dazu dient, überschüssiges Pulver aufzufangen, zu recyclen und die Effizienz des Pulverbeschichtungsprozesses zu verbessern. Es gibt verschiedene Arten von Rückgewinnungssystemen, die je nach den Anforderungen der Anlage und dem Umfang der Pulverbeschichtungsanwendung eingesetzt werden können:
- Zyklonabscheider: Zyklonabscheider sind weit verbreitete Rückgewinnungssysteme, die auf Zentrifugalkraft basieren, um das überschüssige Pulver aus der Luftströmung zu trennen. Das Pulver wird durch den Zyklonabscheider gesaugt, wo es aufgrund der Zentrifugalkraft an den Wänden des Abscheiders abgeschieden wird. Das gereinigte Luftstrom wird dann in die Umgebung abgegeben, während das abgeschiedene Pulver in einem Auffangbehälter gesammelt wird und für die Wiederverwendung vorbereitet wird.
- Filtersysteme: Filtersysteme verwenden verschiedene Arten von Filtern, wie z. B. Patronenfilter oder Taschenfilter, um das überschüssige Pulver aus der Luft zu filtern und zurückzugewinnen. Das Pulver wird durch den Filter gefangen, während die gereinigte Luftströmung in die Umgebung abgegeben wird. Die gefangenen Pulverpartikel werden dann entweder automatisch oder manuell gesammelt und für die Wiederverwendung vorbereitet.
- Rückschlagventile: Rückschlagventile werden häufig in Kombination mit anderen Rückgewinnungssystemen eingesetzt, um den Pulverfluss zu steuern und sicherzustellen, dass das überschüssige Pulver effizient gesammelt wird. Diese Ventile können in den Rohrleitungen des Rückgewinnungssystems installiert werden und öffnen und schließen sich je nach Bedarf, um den Pulverfluss zu lenken und sicherzustellen, dass das Pulver in die Rückgewinnungseinheit gelangt.
Die Auswahl des geeigneten Rückgewinnungssystems hängt von verschiedenen Faktoren ab, darunter die Größe und Kapazität der Pulverbeschichtungsanlage, die Art und Menge des zu verarbeitenden Pulvers und die spezifischen Anforderungen der Anwendung. Ein effektives Rückgewinnungssystem trägt dazu bei, den Pulververbrauch zu reduzieren, die Produktivität der Anlage zu steigern und die Kosten für die Pulverbeschichtung zu senken.
Pulverlack:
Pulverlack ist das Hauptmaterial, das im Pulverbeschichtungsprozess verwendet wird und auf die Oberfläche des Werkstücks aufgetragen wird, um eine schützende und dekorative Beschichtung zu erzeugen. Pulverlack besteht aus einem Gemisch aus feinen Pulverpartikeln aus Polymerharzen, Pigmenten, Füllstoffen und Additiven, die eine Vielzahl von Eigenschaften und Farben bieten können.
Eigenschaften von Pulverlack:
- Haltbarkeit: Pulverlacke bieten eine ausgezeichnete Haltbarkeit und Beständigkeit gegenüber Abrieb, Kratzern, Chemikalien, Witterungseinflüssen und UV-Strahlung. Sie sind besonders geeignet für den Einsatz in anspruchsvollen Umgebungen, wie im Freien oder in industriellen Anwendungen.
- Umweltfreundlichkeit: Pulverlacke enthalten im Allgemeinen keine flüchtigen organischen Verbindungen (VOCs) oder Lösungsmittel, was sie umweltfreundlicher macht als andere Beschichtungsmaterialien. Sie sind frei von giftigen Dämpfen und Emissionen und tragen zur Reduzierung der Umweltbelastung bei.
- Vielseitigkeit: Pulverlacke sind in einer breiten Palette von Farben, Glanzgraden, Texturen und Effekten erhältlich, was eine Vielzahl von dekorativen und funktionalen Möglichkeiten bietet. Sie können für verschiedene Substrate wie Metalle, Kunststoffe, Holz und Glas verwendet werden und bieten eine gleichmäßige und attraktive Oberflächenfinish.
- Effizienz: Der Pulverbeschichtungsprozess ist effizienter als herkömmliche Beschichtungsmethoden wie das Nasslackieren, da keine Trocknungszeiten erforderlich sind und überschüssiges Material wiederverwendet werden kann. Dies führt zu einer Reduzierung von Materialverlusten, Energieverbrauch und Produktionszeit.
Anwendung von Pulverlack:
Pulverlacke werden in einer Vielzahl von Branchen und Anwendungen eingesetzt, darunter:
- Architektur und Bauwesen: Beschichtung von Fassaden, Fensterrahmen, Geländern und anderen Bauteilen.
- Automobilindustrie: Beschichtung von Fahrzeugteilen wie Felgen, Stoßstangen und Karosserieteilen.
- Elektroindustrie: Beschichtung von Gehäusen, Schaltschränken und elektronischen Komponenten.
- Möbelindustrie: Beschichtung von Möbelteilen wie Tischen, Stühlen und Schränken.
Insgesamt ist Pulverlack ein vielseitiges und effektives Beschichtungsmaterial, das eine hohe Leistungsfähigkeit, Haltbarkeit und Umweltfreundlichkeit bietet und in einer Vielzahl von Anwendungen eingesetzt wird, um Oberflächen zu schützen und zu verschönern.
Vorbehandlung
Die Vorbehandlung ist ein entscheidender Schritt im Pulverbeschichtungsprozess, der die Oberfläche des Werkstücks auf die nachfolgende Beschichtung vorbereitet und eine optimale Haftung sowie langfristige Beständigkeit gewährleistet. Diese Phase beinhaltet eine Reihe von Verfahren zur Reinigung und Behandlung der Werkstückoberfläche, um Schmutz, Fett, Rost und andere Verunreinigungen zu entfernen.
Schritte der Vorbehandlung:
- Reinigung: Der erste Schritt besteht darin, die Oberfläche des Werkstücks gründlich zu reinigen, um Schmutz, Öl, Fett und andere Verunreinigungen zu entfernen. Dies kann durch Waschen mit alkalischen oder sauren Reinigungsmitteln, Entfetten mit Lösungsmitteln oder durch Sandstrahlen erfolgen.
- Entfettung: Nach der Reinigung wird das Werkstück einer Entfettung unterzogen, um alle Rückstände von Fett und Öl zu entfernen. Dies ist entscheidend, um eine gute Haftung der Pulverbeschichtung sicherzustellen und das Risiko von Beschichtungsfehlern wie Blasenbildung oder Delamination zu verringern.
- Entrostung: Bei Metallwerkstücken ist die Entrostung ein wichtiger Schritt, um Rost und Korrosion von der Oberfläche zu entfernen. Dies kann durch mechanische Methoden wie Schleifen oder Sandstrahlen erfolgen oder durch chemische Entrostungslösungen, die den Rost chemisch auflösen.
- Phosphatierung/Chromatierung: Nach der Reinigung und Entfettung kann das Werkstück einer Phosphatierung oder Chromatierung unterzogen werden, um eine chemische Konversionsschicht auf der Metalloberfläche zu erzeugen. Diese Schicht verbessert die Haftung und Korrosionsbeständigkeit der Pulverbeschichtung und bietet eine zusätzliche Schutzschicht.
Bedeutung der Vorbehandlung:
Eine gründliche Vorbehandlung ist entscheidend, um eine hochwertige und haltbare Pulverbeschichtung zu gewährleisten. Eine saubere und vorbereitete Oberfläche ermöglicht eine bessere Haftung des Pulvers, eine gleichmäßige Verteilung und eine verbesserte Beständigkeit gegenüber Umwelteinflüssen. Eine sorgfältige Vorbehandlung trägt auch dazu bei, Beschichtungsfehler zu minimieren und die Lebensdauer der beschichteten Teile zu verlängern.
Insgesamt ist die Vorbehandlung ein wesentlicher Schritt im Pulverbeschichtungsprozess, der die Grundlage für eine erfolgreiche Beschichtung bildet und die Qualität und Leistung der beschichteten Teile maßgeblich beeinflusst.
Vorwärmen:
Das Vorwärmen ist ein wichtiger Schritt im Pulverbeschichtungsprozess, der dazu dient, das Werkstück auf eine optimale Temperatur vor dem Auftragen des Pulverlacks vorzubereiten. Dieser Prozess trägt dazu bei, die Haftung und Haltbarkeit der Pulverbeschichtung zu verbessern und eine gleichmäßige Verteilung des Pulverlacks auf der Werkstückoberfläche zu gewährleisten.
Zweck des Vorwärmens:
- Entfernung von Feuchtigkeit: Durch das Vorwärmen wird Feuchtigkeit aus der Werkstückoberfläche und den darunter liegenden Schichten verdampft. Dies ist besonders wichtig, um Blasenbildung oder Delamination der Pulverbeschichtung zu vermeiden, die durch eingeschlossene Feuchtigkeit verursacht werden können.
- Verbesserung der Haftung: Das Vorwärmen des Werkstücks verbessert die Haftung des Pulverlacks, indem es die Oberfläche für die Aufnahme des Pulverlacks vorbereitet. Eine warme Oberfläche ermöglicht eine bessere Durchdringung des Pulvers in die Mikrorillen und Unebenheiten der Oberfläche, was zu einer verbesserten Haftung führt.
- Erhöhung der Pulverbeschichtungseffizienz: Durch das Vorwärmen wird der Pulverbeschichtungsprozess effizienter, da das aufgebrachte Pulver schneller schmilzt und sich auf der Oberfläche des Werkstücks ausbreitet. Dies führt zu einer gleichmäßigeren Beschichtung und reduziert die Anzahl der erforderlichen Beschichtungszyklen.
Methoden des Vorwärmens:
- Konvektionsofen: Ein Konvektionsofen verwendet erwärmte Luft oder Gas, um das Werkstück auf die gewünschte Temperatur zu bringen. Das Werkstück wird in den Ofen platziert und von allen Seiten gleichmäßig beheizt.
- Infrarot-Strahler: Infrarot-Strahler verwenden Infrarotstrahlung, um das Werkstück zu erwärmen. Diese Methode ist besonders effizient, da sie das Werkstück schnell aufheizt und eine präzise Temperaturkontrolle ermöglicht.
- Vorheizen im Pulverbeschichtungs-Ofen: Einige Pulverbeschichtungsöfen verfügen über eine Vorheizzone, in der das Werkstück vor dem Beschichtungsprozess vorgewärmt wird. Diese Methode integriert den Vorwärmprozess nahtlos in den gesamten Beschichtungsprozess und optimiert die Effizienz des Verfahrens.
Bedeutung des Vorwärmens:
Das Vorwärmen ist entscheidend, um eine hochwertige und haltbare Pulverbeschichtung zu gewährleisten. Durch die Vorbereitung der Werkstückoberfläche und die Optimierung der Haftung des Pulverlacks trägt das Vorwärmen dazu bei, Beschichtungsfehler zu minimieren und die Qualität der beschichteten Teile zu verbessern. Es ist ein wichtiger Schritt, der sorgfältige Planung und Kontrolle erfordert, um optimale Ergebnisse zu erzielen.
Applikationssystem:
Das Applikationssystem ist ein zentraler Bestandteil einer Pulverbeschichtungsanlage, das für das Auftragen des Pulverlacks auf die Werkstücke verantwortlich ist. Es gibt verschiedene Arten von Applikationssystemen, die jeweils ihre eigenen Vor- und Nachteile haben und für unterschiedliche Anwendungen geeignet sind.
Elektrostatisches Pulverbeschichtungssystem:
Das elektrostatische Pulverbeschichtungssystem ist das am häufigsten verwendete Applikationssystem in der Pulverbeschichtungsindustrie. Es basiert auf dem Prinzip der elektrostatischen Aufladung, bei dem das Pulver durch einen elektrischen Ladungseffekt auf das Werkstück aufgetragen wird.
- Pulverpistole: Die Pulverpistole ist das Hauptwerkzeug im elektrostatischen Pulverbeschichtungssystem. Das Pulver wird in die Pistole geladen und durch Druckluft oder elektrostatische Kräfte auf das Werkstück gesprüht.
- Elektrostatische Ladung: Während des Sprühvorgangs wird das Pulver durch eine Hochspannungsladung elektrostatisch aufgeladen. Das geladene Pulver wird zum Werkstück angezogen, das eine Gegenelektrode oder Masse darstellt, und haftet gleichmäßig an der Oberfläche.
- Farbwechsel: Moderne Pulverbeschichtungssysteme ermöglichen einen schnellen und einfachen Farbwechsel durch den Einsatz von Schnellwechselsystemen oder Farbsprüheinrichtungen.
Fluidbett-Pulverbeschichtungssystem:
Das Fluidbett-Pulverbeschichtungssystem verwendet ein Becken mit einem Pulverreservoir, das elektrisch aufgeladen ist. Das Werkstück wird in das Pulverbett eingetaucht, wodurch das Pulver am Werkstück haftet.
- Tauchverfahren: Das Werkstück wird in das Pulverbett getaucht, wodurch das Pulver am Werkstück haftet. Überschüssiges Pulver wird abgeschüttelt oder abgeblasen, bevor das Werkstück in den Trocknungsofen gelangt.
- Geeignet für komplexe Formen: Das Fluidbett-Pulverbeschichtungssystem eignet sich besonders gut für komplexe Werkstücke mit schwer zugänglichen Bereichen, da das Pulver gleichmäßig auf alle Oberflächen aufgetragen wird.
Vorteile von Applikationssystemen:
- Hohe Effizienz: Applikationssysteme ermöglichen eine schnelle und effiziente Beschichtung großer Mengen von Werkstücken.
- Gleichmäßige Beschichtung: Durch die Verwendung elektrostatischer Aufladung oder des Tauchverfahrens wird eine gleichmäßige Beschichtung auf allen Oberflächen des Werkstücks erzielt.
- Vielseitigkeit: Applikationssysteme sind vielseitig einsetzbar und können für eine Vielzahl von Werkstücken und Beschichtungsanwendungen verwendet werden.
Die Auswahl des geeigneten Applikationssystems hängt von verschiedenen Faktoren ab, darunter die Art der Werkstücke, die Beschichtungsanforderungen und die Produktionskapazität der Anlage. Ein effektives Applikationssystem ist entscheidend für die Qualität und Effizienz des Pulverbeschichtungsprozesses.
Pulverrückgewinnung:
Die Pulverrückgewinnung ist ein wesentlicher Aspekt des Pulverbeschichtungsprozesses, der dazu dient, überschüssiges Pulver aufzufangen, zu recyceln und wiederzuverwenden. Dies trägt nicht nur zur Reduzierung von Materialverschwendung und Kosten bei, sondern auch zur Verbesserung der Umweltfreundlichkeit des Beschichtungsprozesses.
Funktionen der Pulverrückgewinnung:
- Aufnahme überschüssigen Pulvers: Während des Sprühvorgangs wird nicht das gesamte aufgetragene Pulver auf dem Werkstück haften bleiben. Ein Teil des Pulvers wird die Oberfläche passieren und sich in der Umgebung ablagern. Das Pulverrückgewinnungssystem sammelt dieses überschüssige Pulver ein, um es zu recyceln.
- Recycling und Wiederverwendung: Das gesammelte Pulver wird einem Sieb- oder Filtersystem zugeführt, um Verunreinigungen zu entfernen und das Pulver für die Wiederverwendung aufzubereiten. Dies reduziert den Bedarf an frischem Pulver und senkt die Materialkosten.
- Reduzierung von Materialverschwendung: Durch die Wiederverwendung von überschüssigem Pulver wird die Menge an Materialverschwendung reduziert, was sowohl ökonomische als auch ökologische Vorteile mit sich bringt.
Arten von Pulverrückgewinnungssystemen:
- Zyklonabscheider: Zyklonabscheider nutzen die Zentrifugalkraft, um das Pulver von der Luft zu trennen. Das Pulver wird in einem Behälter gesammelt, während die gereinigte Luft abgeführt wird.
- Filtersysteme: Filtersysteme verwenden verschiedene Arten von Filtern, wie z. B. Patronenfilter oder Taschenfilter, um das Pulver aus der Luft zu filtern. Das Pulver wird dann von den Filtern abgeschüttelt oder abgeblasen und in einem Behälter gesammelt.
- Fluidbett-Rückgewinnung: Beim Fluidbett-Rückgewinnungssystem wird das überschüssige Pulver in einem flüssigen Medium gesammelt und anschließend recycelt. Das Pulver wird auf der Oberfläche des Mediums gesammelt und kann dann abgetrennt und wiederverwendet werden.
Die Auswahl des geeigneten Pulverrückgewinnungssystems hängt von verschiedenen Faktoren ab, einschließlich der Größe der Anlage, der Art der zu beschichtenden Werkstücke und der spezifischen Anforderungen der Anwendung. Ein effektives Pulverrückgewinnungssystem trägt dazu bei, die Kosten zu senken, die Produktivität zu steigern und die Umweltbelastung zu reduzieren.
Pulverbeschichtungslinie:
Eine Pulverbeschichtungslinie ist eine automatisierte Anlage, die entwickelt wurde, um den gesamten Pulverbeschichtungsprozess von der Vorbereitung der Werkstücke bis zur Endbearbeitung zu ermöglichen. Diese Linien können je nach den Anforderungen der Produktion und den spezifischen Anwendungen maßgeschneidert werden.
Komponenten einer Pulverbeschichtungslinie:
- Vorbereitungsbereich: Dieser Bereich umfasst verschiedene Stationen zur Vorbereitung der Werkstücke für die Beschichtung. Dazu gehören Entfettungs-, Reinigungs- und Entrostungsstationen, in denen die Werkstücke gründlich gereinigt und von Verunreinigungen befreit werden.
- Vorbehandlungsanlage: Die Vorbehandlungsanlage besteht aus Vorbehandlungstanks und -systemen, die die Werkstücke auf die Aufnahme des Pulverlacks vorbereiten. Dies kann das Aufbringen von Konversionsschichten wie Phosphatierung oder Chromatierung umfassen.
- Pulverbeschichtungskabine: In der Pulverbeschichtungskabine wird der Pulverlack auf die Werkstücke aufgetragen. Dies kann manuell mit Pulverpistolen oder automatisiert mit Robotern erfolgen, je nach den Anforderungen der Produktion.
- Trocknungsofen: Nach dem Auftragen des Pulverlacks werden die Werkstücke in einem Trocknungsofen erwärmt, um das Pulver zu schmelzen und zu aushärten. Dies stellt sicher, dass die Beschichtung eine gleichmäßige Dicke und Haftung aufweist.
- Kühlbereich: Nach dem Aushärten werden die Werkstücke in einem Kühlbereich abgekühlt, um die Beschichtung zu stabilisieren und eine gleichmäßige Aushärtung sicherzustellen.
- Inspektions- und Qualitätskontrollbereich: In diesem Bereich werden die beschichteten Werkstücke auf Qualität und Fehler überprüft. Dies kann visuelle Inspektionen, Dickeprüfungen und Adhäsionstests umfassen.
Vorteile einer Pulverbeschichtungslinie:
- Effizienz: Pulverbeschichtungslinien ermöglichen eine kontinuierliche und effiziente Produktion großer Mengen von beschichteten Werkstücken.
- Konsistenz: Durch die Automatisierung des Prozesses wird eine hohe Konsistenz und Qualität der Beschichtung gewährleistet.
- Flexibilität: Pulverbeschichtungslinien können für eine Vielzahl von Werkstücken und Beschichtungsanwendungen angepasst werden.
- Umweltfreundlichkeit: Durch die Reduzierung von Materialverschwendung und Emissionen tragen Pulverbeschichtungslinien zur Verbesserung der Umweltbilanz bei.
Insgesamt bieten Pulverbeschichtungslinien eine effektive und wirtschaftliche Lösung für die Massenproduktion von beschichteten Werkstücken und werden in einer Vielzahl von Branchen eingesetzt, darunter Automobilindustrie, Möbelherstellung, Architektur und Elektronik.
Pulverbeschichtungsprozess:
Der Pulverbeschichtungsprozess ist ein Verfahren zur Beschichtung von Oberflächen mit Pulverlacken, das eine attraktive und langlebige Oberflächenfinish bietet. Dieser Prozess umfasst mehrere Schritte, die sorgfältig ausgeführt werden müssen, um eine qualitativ hochwertige Beschichtung zu erzielen.
Schritte im Pulverbeschichtungsprozess:
- Vorbereitung der Oberfläche: Der Prozess beginnt mit der Vorbereitung der Oberfläche des Werkstücks. Dies umfasst die Reinigung, Entfettung und Entrostung, um sicherzustellen, dass die Oberfläche frei von Verunreinigungen ist und eine optimale Haftung des Pulverlacks gewährleistet ist.
- Applikation des Pulverlacks: Nach der Vorbereitung der Oberfläche wird der Pulverlack mithilfe eines Applikationssystems auf das Werkstück aufgetragen. Dies kann manuell mit einer Pulverpistole oder automatisiert mit einem Roboter erfolgen. Der Pulverlack wird elektrostatisch aufgeladen, um eine gleichmäßige Verteilung auf der Oberfläche zu gewährleisten.
- Trocknung und Aushärtung: Nach dem Auftragen des Pulverlacks werden die Werkstücke in einem Trocknungsofen erwärmt, um das Pulver zu schmelzen und zu aushärten. Dies stellt sicher, dass die Beschichtung eine gleichmäßige Dicke und Haftung aufweist und eine dauerhafte Oberfläche bildet.
- Kühlung und Endbearbeitung: Nach dem Aushärten werden die Werkstücke abgekühlt, um die Beschichtung zu stabilisieren und eine gleichmäßige Aushärtung sicherzustellen. Anschließend können sie einer Endbearbeitung unterzogen werden, wie z. B. dem Entfernen von Maskierungsmaterialien oder dem Anbringen von Dekorationsdetails.
Vorteile des Pulverbeschichtungsprozesses:
- Haltbarkeit: Pulverbeschichtungen bieten eine hohe Beständigkeit gegenüber Abrieb, Kratzern, Chemikalien und Witterungseinflüssen, was zu einer langlebigen Oberfläche führt.
- Umweltfreundlichkeit: Pulverbeschichtungen enthalten keine flüchtigen organischen Verbindungen (VOCs) oder Lösungsmittel, was sie umweltfreundlicher macht als andere Beschichtungsmethoden.
- Vielseitigkeit: Pulverbeschichtungen sind in einer Vielzahl von Farben, Texturen und Glanzgraden erhältlich und können auf verschiedene Substrate wie Metall, Holz, Kunststoff und Glas aufgetragen werden.
- Effizienz: Der Pulverbeschichtungsprozess ist effizienter als herkömmliche Beschichtungsmethoden wie das Nasslackieren, da keine Trocknungszeiten erforderlich sind und überschüssiges Material wiederverwendet werden kann.
Insgesamt ist der Pulverbeschichtungsprozess eine effektive und wirtschaftliche Methode zur Beschichtung von Oberflächen mit langlebigen und attraktiven Oberflächenfinish. Er wird in einer Vielzahl von Branchen und Anwendungen eingesetzt, darunter Automobilindustrie, Architektur, Möbelherstellung und Elektronik.
Pulverbeschichtungsvorrichtung:
Eine Pulverbeschichtungsvorrichtung ist eine spezialisierte Einrichtung, die für das Auftragen von Pulverlacken auf Werkstücke verwendet wird. Diese Vorrichtungen spielen eine entscheidende Rolle im Pulverbeschichtungsprozess, da sie eine präzise und gleichmäßige Beschichtung gewährleisten und die Effizienz des Beschichtungsprozesses verbessern.
Komponenten einer Pulverbeschichtungsvorrichtung:
- Pulverpistole: Die Pulverpistole ist das Hauptwerkzeug in einer Pulverbeschichtungsvorrichtung. Sie ist mit einer Düse ausgestattet, durch die der Pulverlack auf die Werkstücke gesprüht wird. Moderne Pulverpistolen verfügen über Funktionen wie einstellbare Pulvermengen, verschiedene Sprühmuster und elektrostatische Aufladung für eine präzise und gleichmäßige Beschichtung.
- Hochspannungsgenerator: Der Hochspannungsgenerator erzeugt die elektrische Ladung, die verwendet wird, um das Pulver elektrostatisch aufzuladen. Diese Ladung bewirkt, dass das Pulver zu den geerdeten Werkstücken hin gezogen wird, was zu einer verbesserten Haftung und einer gleichmäßigen Beschichtung führt.
- Steuerungssystem: Das Steuerungssystem überwacht und steuert die verschiedenen Parameter der Pulverbeschichtungsvorrichtung, wie z. B. die Pulvermenge, die Luftströmung und die Spannung. Dies ermöglicht eine präzise Einstellung der Beschichtungsparameter und eine Optimierung der Beschichtungsqualität.
- Filtersystem: Das Filtersystem sorgt dafür, dass das aufgetragene Pulver frei von Verunreinigungen und Partikeln ist. Dies kann durch den Einsatz von Patronenfiltern, Taschenfiltern oder Zyklonabscheidern erfolgen, die das überschüssige Pulver aus der Luft filtern und reinigen.
Vorteile einer Pulverbeschichtungsvorrichtung:
- Präzise und gleichmäßige Beschichtung: Pulverbeschichtungsvorrichtungen ermöglichen eine präzise Steuerung der Pulvermenge und Sprühmuster, was zu einer gleichmäßigen und konsistenten Beschichtung führt.
- Effizienz: Durch die Verwendung elektrostatischer Aufladung und präziser Steuerung der Beschichtungsparameter wird eine hohe Effizienz des Beschichtungsprozesses erreicht, was zu geringeren Material- und Energieverlusten führt.
- Vielseitigkeit: Pulverbeschichtungsvorrichtungen sind vielseitig einsetzbar und können für eine Vielzahl von Werkstücken und Beschichtungsanwendungen verwendet werden.
- Umweltfreundlichkeit: Pulverbeschichtungsvorrichtungen tragen zur Reduzierung von Materialverschwendung und Emissionen bei und sind daher umweltfreundlicher als andere Beschichtungsmethoden.
Insgesamt spielen Pulverbeschichtungsvorrichtungen eine entscheidende Rolle im Pulverbeschichtungsprozess und ermöglichen eine präzise, effiziente und qualitativ hochwertige Beschichtung von Werkstücken.
Vorbehandlung
Die Vorbehandlung ist ein wesentlicher Schritt im Pulverbeschichtungsprozess, der die Oberfläche des Werkstücks für die Beschichtung vorbereitet und eine optimale Haftung sowie langfristige Beständigkeit gewährleistet. Dieser Schritt ist entscheidend für die Qualität und Haltbarkeit der Pulverbeschichtung und umfasst mehrere wichtige Unterprozesse.
Reinigung:
Die Reinigung der Werkstückoberfläche ist der erste Schritt in der Vorbehandlung. Es werden alle Arten von Verunreinigungen wie Schmutz, Fett, Öl, Rost und andere Rückstände entfernt. Dies kann durch verschiedene Methoden wie Waschen mit Reinigungslösungen, Entfetten mit Lösungsmitteln oder mechanisches Entfernen von Rost durch Schleifen oder Sandstrahlen erfolgen.
Entfettung:
Die Entfettung ist ein spezieller Teil der Reinigung, der darauf abzielt, alle Rückstände von Öl und Fett von der Oberfläche zu entfernen. Dies ist entscheidend, um eine gute Haftung des Pulverlacks zu gewährleisten. Entfettungslösungen oder Lösungsmittel werden verwendet, um diese Rückstände effektiv zu entfernen.
Entrostung:
Für metallische Werkstücke ist die Entrostung ein wichtiger Schritt, um Rost und Korrosion von der Oberfläche zu entfernen. Dies kann durch mechanisches Schleifen, Sandstrahlen oder chemische Entrostungslösungen erfolgen. Eine saubere und rostfreie Oberfläche ist entscheidend für die langfristige Beständigkeit der Pulverbeschichtung.
Phosphatierung/Chromatierung:
Nach der Reinigung und Entfettung kann das Werkstück einer Phosphatierung oder Chromatierung unterzogen werden. Diese Prozesse erzeugen eine chemische Konversionsschicht auf der Metalloberfläche, die die Haftung und Korrosionsbeständigkeit der Pulverbeschichtung verbessert. Sie bieten auch eine verbesserte Oberfläche für die Haftung des Pulverlacks.
Trocknung:
Nach der Vorbehandlung wird das Werkstück sorgfältig getrocknet, um sicherzustellen, dass keine Feuchtigkeit mehr auf der Oberfläche vorhanden ist. Eine gründliche Trocknung ist entscheidend, um Beschichtungsfehler wie Blasenbildung oder Delamination zu vermeiden und eine optimale Haftung des Pulverlacks zu gewährleisten.
Die Vorbehandlung ist ein kritischer Schritt im Pulverbeschichtungsprozess, der die Grundlage für eine hochwertige und langlebige Beschichtung bildet. Eine sorgfältige Durchführung der Vorbehandlung trägt wesentlich zur Verbesserung der Qualität und Leistung der beschichteten Teile bei.
Schleifen
Schleifen ist ein wichtiger Schritt im Pulverbeschichtungsprozess, der dazu dient, die Oberfläche des Werkstücks vorzubereiten, Unebenheiten zu beseitigen und eine glatte Oberfläche für die Pulverbeschichtung zu schaffen. Dieser Prozess ist besonders wichtig für metallische Werkstücke, die Unebenheiten, Rost oder andere Oberflächenfehler aufweisen können.
Zweck des Schleifens:
- Entfernung von Unebenheiten: Durch das Schleifen werden Unebenheiten wie Schweißnähte, Kratzer, Rost oder andere Oberflächenfehler entfernt. Dies führt zu einer glatten Oberfläche, die für die Pulverbeschichtung geeignet ist.
- Verbesserung der Haftung: Eine glatte und saubere Oberfläche verbessert die Haftung des Pulverlacks und trägt dazu bei, eine gleichmäßige und haltbare Beschichtung zu gewährleisten.
- Vorbereitung auf Vorbehandlung: Das Schleifen bereitet die Oberfläche des Werkstücks auf die Vorbehandlung vor, indem es Verunreinigungen entfernt und eine saubere Oberfläche für die anschließende Reinigung und Entfettung bietet.
Methoden des Schleifens:
- Handschleifen: Diese traditionelle Methode verwendet Schleifpapier oder Schleifvlies, das von Hand auf die Oberfläche des Werkstücks aufgetragen wird. Sie ermöglicht eine präzise Kontrolle über den Schleifprozess, ist jedoch zeitaufwändig und erfordert manuelle Arbeit.
- Maschinelles Schleifen: Maschinelle Schleifgeräte wie Bandschleifer, Schwingschleifer oder Rotationswerkzeuge können für effizientes und schnelles Schleifen größerer Werkstücke eingesetzt werden. Sie bieten eine höhere Produktivität und können für verschiedene Oberflächenprofile angepasst werden.
- Sandstrahlen: Beim Sandstrahlen wird ein Strahl von abrasivem Material mit hoher Geschwindigkeit auf die Oberfläche des Werkstücks gerichtet, um Verunreinigungen und Unebenheiten zu entfernen. Diese Methode ist besonders effektiv für die Entfernung von Rost und Schweißnähten auf metallischen Oberflächen.
Bedeutung des Schleifens:
Ein gründliches Schleifen ist entscheidend für die Qualität und Haltbarkeit der Pulverbeschichtung. Eine sorgfältige Vorbereitung der Oberfläche durch Schleifen trägt dazu bei, Beschichtungsfehler wie Blasenbildung, Delamination oder ungleichmäßige Beschichtung zu minimieren und eine hochwertige Oberflächenfinish zu gewährleisten. Daher ist das Schleifen ein unverzichtbarer Schritt im Pulverbeschichtungsprozess, der sorgfältige Planung, Vorbereitung und Ausführung erfordert.
Maskierung
Die Maskierung ist ein wichtiger Schritt im Pulverbeschichtungsprozess, der dazu dient, bestimmte Bereiche des Werkstücks vor der Beschichtung zu schützen oder abzudecken. Dies ist notwendig, um sicherzustellen, dass nur die gewünschten Bereiche beschichtet werden und andere Bereiche frei von Beschichtung bleiben.
Zweck der Maskierung:
- Schutz empfindlicher Bereiche: Einige Teile des Werkstücks, wie z. B. Gewinde, Lager oder Dichtflächen, müssen möglicherweise vor der Beschichtung geschützt werden, um ihre Funktionalität nicht zu beeinträchtigen. Die Maskierung schützt diese empfindlichen Bereiche vor Pulverbeschichtung.
- Erzeugung von Designs oder Muster: Die Maskierung kann auch verwendet werden, um bestimmte Designs, Muster oder Logos auf die Oberfläche des Werkstücks zu erzeugen. Indem bestimmte Bereiche abgedeckt bleiben, während andere beschichtet werden, können interessante visuelle Effekte erzielt werden.
- Vermeidung von Beschichtungsfehlern: Durch die präzise Maskierung von Bereichen, die nicht beschichtet werden sollen, können Beschichtungsfehler wie Überlappungen, Läufer oder unerwünschte Beschichtungen vermieden werden.
Methoden der Maskierung:
- Abdeckbänder: Spezielle Klebebänder wie Malerkrepp oder Hochtemperaturmaskierbänder werden verwendet, um bestimmte Bereiche des Werkstücks abzudecken und vor der Beschichtung zu schützen. Diese Bänder bieten eine einfache und effektive Möglichkeit, gerade Linien und klare Kanten zu erzeugen.
- Maskierungsfolie: Spezielle Maskierungsfolien werden auf die Oberfläche des Werkstücks aufgetragen, um größere Bereiche abzudecken und zu schützen. Diese Folien sind flexibel und können an verschiedene Formen angepasst werden, um eine vollständige Abdeckung zu gewährleisten.
- Stecker und Stopfen: Für Bohrungen, Gewinde oder andere Hohlräume können spezielle Stecker oder Stopfen verwendet werden, um sie vor der Beschichtung zu schützen. Diese Stecker sind in verschiedenen Größen und Formen erhältlich und bieten eine einfache Möglichkeit, empfindliche Bereiche abzudecken.
Bedeutung der Maskierung:
Eine sorgfältige Maskierung ist entscheidend für die Qualität und Ästhetik der Pulverbeschichtung. Eine unzureichende Maskierung kann zu Beschichtungsfehlern, unerwünschten Beschichtungen oder Beschädigungen von empfindlichen Bereichen führen. Daher erfordert die Maskierung eine genaue Planung, sorgfältige Vorbereitung und präzise Ausführung, um eine hochwertige und professionelle Beschichtung zu gewährleisten.
Pulverbeschichtungsanlage
Eine Pulverbeschichtungsanlage ist eine spezialisierte Einrichtung, die für das Auftragen von Pulverlacken auf Werkstücke verwendet wird. Diese Anlagen sind darauf ausgelegt, eine effiziente, präzise und qualitativ hochwertige Beschichtung von Werkstücken in verschiedenen Größen und Formen zu ermöglichen.
Komponenten einer Pulverbeschichtungsanlage:
- Pulverbeschichtungskabine: Die Pulverbeschichtungskabine ist der zentrale Ort, an dem der eigentliche Beschichtungsprozess stattfindet. Sie ist mit Pulverpistolen ausgestattet, die den Pulverlack auf die Werkstücke sprühen. Moderne Kabinen verfügen über elektrostatische Aufladungssysteme, Filter zur Luftreinigung und Steuerungen zur Überwachung des Beschichtungsprozesses.
- Trocknungsofen: Nach dem Auftragen des Pulverlacks werden die Werkstücke in einem Trocknungsofen erwärmt, um das Pulver zu schmelzen und zu aushärten. Dies stellt sicher, dass die Beschichtung eine gleichmäßige Dicke und Haftung aufweist und eine dauerhafte Oberfläche bildet.
- Fördersystem: Ein Fördersystem transportiert die Werkstücke durch die verschiedenen Stationen der Pulverbeschichtungsanlage, vom Vorbereitungsbereich über die Beschichtungskabine bis zum Trocknungsofen. Dies kann ein Förderband, ein Hängeförderer oder ein Kettenförderer sein, je nach den Anforderungen der Produktion und der Größe der Werkstücke.
- Vorbehandlungseinrichtungen: Die Vorbehandlungseinrichtungen umfassen Reinigungs-, Entfettungs- und Entrostungsstationen, in denen die Werkstücke gründlich vorbereitet werden, um eine optimale Haftung des Pulverlacks zu gewährleisten. Dies ist ein entscheidender Schritt, um eine hochwertige Beschichtung zu erzielen.
Vorteile einer Pulverbeschichtungsanlage:
- Effizienz: Pulverbeschichtungsanlagen ermöglichen eine kontinuierliche und effiziente Beschichtung großer Mengen von Werkstücken.
- Präzision: Durch die Verwendung moderner Steuerungen und Technologien können Pulverbeschichtungsanlagen eine präzise und gleichmäßige Beschichtung gewährleisten.
- Vielseitigkeit: Pulverbeschichtungsanlagen können für eine Vielzahl von Werkstücken und Beschichtungsanwendungen angepasst werden, von kleinen Bauteilen bis hin zu großen Strukturen.
- Umweltfreundlichkeit: Pulverbeschichtungsanlagen sind umweltfreundlicher als andere Beschichtungsmethoden, da sie keine flüchtigen organischen Verbindungen (VOCs) emittieren und überschüssiges Pulver recycelt werden kann.
Insgesamt bieten Pulverbeschichtungsanlagen eine effektive und wirtschaftliche Lösung für die Beschichtung von Werkstücken und werden in einer Vielzahl von Branchen eingesetzt, darunter Automobilindustrie, Metallverarbeitung, Möbelherstellung und Architektur.
Beschichtungsdicke
Die Beschichtungsdicke ist ein wichtiges Maß für die Qualität und Leistungsfähigkeit einer Pulverbeschichtung. Sie bezieht sich auf die Dicke der aufgetragenen Pulverlackschicht auf der Oberfläche des Werkstücks und hat einen direkten Einfluss auf verschiedene Aspekte der Beschichtung, einschließlich ihrer Haltbarkeit, Schutzfunktion und Ästhetik.
Bedeutung der Beschichtungsdicke:
- Haltbarkeit: Eine ausreichende Beschichtungsdicke ist entscheidend für die Haltbarkeit der Beschichtung. Eine zu dünn aufgetragene Beschichtung kann leicht beschädigt werden und bietet keinen ausreichenden Schutz vor Korrosion, Abrieb oder anderen Umwelteinflüssen.
- Korrosionsschutz: Eine ausreichend dicke Beschichtung bildet eine Schutzschicht auf der Oberfläche des Werkstücks, die es vor Korrosion durch Feuchtigkeit, Chemikalien oder andere aggressive Substanzen schützt. Eine gleichmäßige Beschichtungsdicke ist entscheidend, um eine wirksame Barriere gegen Korrosion zu gewährleisten.
- Schutz vor mechanischen Belastungen: Eine dicke Beschichtung kann das Werkstück auch vor mechanischen Belastungen wie Kratzern, Stößen oder Abrieb schützen. Sie dient als Schutzschicht, die die darunter liegende Oberfläche vor Beschädigungen bewahrt.
- Ästhetik: Die Beschichtungsdicke kann auch die ästhetische Erscheinung der Beschichtung beeinflussen. Eine gleichmäßige und angemessene Beschichtungsdicke trägt zu einem glatten, gleichmäßigen Finish bei, während eine ungleichmäßige oder zu dicke Beschichtung zu unerwünschten Oberflächenfehlern führen kann.
Messung der Beschichtungsdicke:
Die Beschichtungsdicke kann mit verschiedenen Messmethoden gemessen werden, darunter:
- Zerstörungsfreie Messung: Dies umfasst Methoden wie magnetische Induktion oder Wirbelstromprüfung, bei denen ein Sensor verwendet wird, um die Dicke der Beschichtung zu messen, ohne sie zu beschädigen.
- Zerstörende Messung: Hier wird die Beschichtung entfernt, um die Dicke direkt zu messen. Dies kann durch Schneiden und Wiegen oder durch spezielle Mikroskopie- und Messtechniken erfolgen.
Qualitätskontrolle:
Eine regelmäßige Überprüfung und Kontrolle der Beschichtungsdicke ist entscheidend, um sicherzustellen, dass die Beschichtung den erforderlichen Standards entspricht. Durch eine präzise Kontrolle der Beschichtungsdicke können Fehler frühzeitig erkannt und behoben werden, um die Qualität der Beschichtung zu gewährleisten und Ausschuss zu minimieren.
Haftfestigkeit
Die Haftfestigkeit ist ein entscheidender Parameter im Pulverbeschichtungsprozess, der die Fähigkeit des Pulverlacks, auf der Oberfläche des Werkstücks zu haften, beschreibt. Eine gute Haftfestigkeit ist entscheidend für die Haltbarkeit und Leistung der Beschichtung, da sie sicherstellt, dass die Beschichtung fest an der Oberfläche haftet und nicht abblättert oder sich löst.
Bedeutung der Haftfestigkeit:
- Schutz vor Ablösung: Eine ausreichende Haftfestigkeit verhindert, dass die Beschichtung von der Oberfläche des Werkstücks abblättert oder sich löst. Dies ist besonders wichtig in Umgebungen mit hohen mechanischen Belastungen, Vibrationen oder Temperaturschwankungen.
- Korrosionsschutz: Eine gute Haftfestigkeit gewährleistet, dass die Beschichtung eine wirksame Barriere gegen Korrosion bildet, indem sie das Eindringen von Feuchtigkeit, Chemikalien oder anderen schädlichen Substanzen in das Substrat verhindert.
- Langfristige Leistung: Eine Beschichtung mit hoher Haftfestigkeit bietet eine langfristige Leistung und Haltbarkeit, da sie auch unter widrigen Bedingungen intakt bleibt und eine zuverlässige Schutzschicht auf dem Werkstück bildet.
- Optische Qualität: Eine gute Haftfestigkeit trägt auch zur optischen Qualität der Beschichtung bei, indem sie ein glattes, gleichmäßiges Finish gewährleistet, das frei von Blasen, Rissen oder anderen Oberflächenfehlern ist.
Faktoren, die die Haftfestigkeit beeinflussen:
- Vorbereitung der Oberfläche: Eine gründliche Reinigung, Entfettung und Entrostung der Oberfläche ist entscheidend, um eine optimale Haftfestigkeit zu gewährleisten. Eine saubere und vorbereitete Oberfläche bietet eine bessere Haftgrundlage für den Pulverlack.
- Adhäsionsfördernde Schichten: Phosphatierungs- oder Chromatierungsverfahren können auf die Oberfläche aufgetragen werden, um die Haftfestigkeit der Beschichtung zu verbessern, indem sie die Adhäsion zwischen Beschichtung und Substrat erhöhen.
- Beschichtungsverfahren: Die Art und Weise, wie der Pulverlack aufgetragen wird, kann ebenfalls die Haftfestigkeit beeinflussen. Eine gleichmäßige Applikation und eine ordnungsgemäße Aushärtung des Pulverlacks sind wichtig, um eine gute Haftung zu gewährleisten.
Qualitätskontrolle:
Die Haftfestigkeit wird in der Regel durch Zug- oder Scherfestigkeitstests gemessen, bei denen die Beschichtung einer bestimmten Belastung ausgesetzt wird, um ihre Haftfestigkeit zu bestimmen. Eine regelmäßige Überprüfung der Haftfestigkeit ist entscheidend, um die Qualität der Beschichtung zu gewährleisten und mögliche Probleme frühzeitig zu erkennen und zu beheben.
Elektrostatische Aufladung
Die elektrostatische Aufladung ist ein entscheidender Prozess im Pulverbeschichtungsverfahren, bei dem die Pulverpartikel durch elektrische Ladung aufgeladen werden, um sie effizient auf die zu beschichtende Oberfläche anzuziehen. Dieser Prozess spielt eine wichtige Rolle bei der Verbesserung der Beschichtungsqualität und -effizienz.
Funktionsweise der elektrostatischen Aufladung:
- Ladungserzeugung: Durch einen Hochspannungsgenerator werden elektrische Ladungen erzeugt und auf die Pulverpartikel übertragen. Dies geschieht in der Regel durch Reibung oder Induktion.
- Anziehung zum Werkstück: Die elektrisch geladenen Pulverpartikel werden durch elektrostatische Anziehungskräfte zum geerdeten Werkstück gezogen. Dies führt zu einer gleichmäßigen Verteilung der Partikel auf der Oberfläche und einer verbesserten Haftung.
- Effizienzsteigerung: Durch die elektrostatische Aufladung werden die Pulverpartikel gezielt zum Werkstück gelenkt, wodurch weniger Pulver verschwendet wird und eine höhere Übertragungseffizienz erreicht wird. Dies führt zu geringeren Material- und Energieverlusten.
Vorteile der elektrostatischen Aufladung:
- Gleichmäßige Beschichtung: Die elektrostatische Aufladung ermöglicht eine gleichmäßige Verteilung der Pulverpartikel auf der Oberfläche des Werkstücks, was zu einer gleichmäßigen Beschichtung und einem glatten Finish führt.
- Verbesserte Haftung: Durch die elektrostatische Anziehungskraft werden die Pulverpartikel fest an die Oberfläche des Werkstücks angehaftet, was zu einer verbesserten Haftung und Haltbarkeit der Beschichtung führt.
- Reduzierte Materialverschwendung: Da die Pulverpartikel gezielt zum Werkstück gelenkt werden, wird weniger Pulver verschwendet, was zu geringeren Materialkosten und geringerer Umweltbelastung führt.
- Höhere Produktionsgeschwindigkeit: Die elektrostatische Aufladung ermöglicht eine schnellere und effizientere Beschichtung großer Mengen von Werkstücken, was die Produktionsgeschwindigkeit erhöht und die Gesamtleistung der Anlage verbessert.
Anwendungen:
Die elektrostatische Aufladung wird in einer Vielzahl von Branchen eingesetzt, darunter Automobilindustrie, Metallverarbeitung, Möbelherstellung und Architektur. Sie ist eine bewährte Methode zur Beschichtung von Werkstücken mit hoher Qualität, Präzision und Effizienz.
Vorbehandlung
Die Vorbehandlung ist ein wesentlicher Schritt im Pulverbeschichtungsprozess, der die Oberfläche des Werkstücks für die Beschichtung vorbereitet und eine optimale Haftung sowie langfristige Beständigkeit gewährleistet. Dieser Schritt ist entscheidend für die Qualität und Haltbarkeit der Pulverbeschichtung und umfasst mehrere wichtige Unterprozesse.
Reinigung:
Die Reinigung der Werkstückoberfläche ist der erste Schritt in der Vorbehandlung. Es werden alle Arten von Verunreinigungen wie Schmutz, Fett, Öl, Rost und andere Rückstände entfernt. Dies kann durch verschiedene Methoden wie Waschen mit Reinigungslösungen, Entfetten mit Lösungsmitteln oder mechanisches Entfernen von Rost durch Schleifen oder Sandstrahlen erfolgen.
Entfettung:
Die Entfettung ist ein spezieller Teil der Reinigung, der darauf abzielt, alle Rückstände von Öl und Fett von der Oberfläche zu entfernen. Dies ist entscheidend, um eine gute Haftung des Pulverlacks zu gewährleisten. Entfettungslösungen oder Lösungsmittel werden verwendet, um diese Rückstände effektiv zu entfernen.
Entrostung:
Für metallische Werkstücke ist die Entrostung ein wichtiger Schritt, um Rost und Korrosion von der Oberfläche zu entfernen. Dies kann durch mechanisches Schleifen, Sandstrahlen oder chemische Entrostungslösungen erfolgen. Eine saubere und rostfreie Oberfläche ist entscheidend für die langfristige Beständigkeit der Pulverbeschichtung.
Phosphatierung/Chromatierung:
Nach der Reinigung und Entfettung kann das Werkstück einer Phosphatierung oder Chromatierung unterzogen werden. Diese Prozesse erzeugen eine chemische Konversionsschicht auf der Metalloberfläche, die die Haftung und Korrosionsbeständigkeit der Pulverbeschichtung verbessert. Sie bieten auch eine verbesserte Oberfläche für die Haftung des Pulverlacks.
Trocknung:
Nach der Vorbehandlung wird das Werkstück sorgfältig getrocknet, um sicherzustellen, dass keine Feuchtigkeit mehr auf der Oberfläche vorhanden ist. Eine gründliche Trocknung ist entscheidend, um Beschichtungsfehler wie Blasenbildung oder Delamination zu vermeiden und eine optimale Haftung des Pulverlacks zu gewährleisten.
Die Vorbehandlung ist ein kritischer Schritt im Pulverbeschichtungsprozess, der die Grundlage für eine hochwertige und langlebige Beschichtung bildet. Eine sorgfältige Durchführung der Vorbehandlung trägt wesentlich zur Verbesserung der Qualität und Leistung der beschichteten Teile bei.
Chemische Vorbehandlung
Die chemische Vorbehandlung ist ein wichtiger Schritt im Pulverbeschichtungsprozess, der darauf abzielt, die Oberfläche des Werkstücks für die Beschichtung vorzubereiten und eine optimale Haftung sowie langfristige Beständigkeit zu gewährleisten. Im Gegensatz zu mechanischen Methoden wie Schleifen oder Sandstrahlen basiert die chemische Vorbehandlung auf chemischen Reaktionen, um eine saubere und vorbereitete Oberfläche zu erzeugen.
Prozess der chemischen Vorbehandlung:
- Entfettung: Der erste Schritt in der chemischen Vorbehandlung ist die Entfettung, bei der alle Öl- und Fettspuren von der Oberfläche des Werkstücks entfernt werden. Dies erfolgt durch das Eintauchen des Werkstücks in Entfettungslösungen oder durch das Auftragen von Lösungsmitteln, um die Oberfläche gründlich zu reinigen.
- Entrostung: Nach der Entfettung wird das Werkstück einer Entrostung unterzogen, um alle Rost- und Korrosionsspuren zu entfernen. Dies kann durch chemische Entrostungslösungen erfolgen, die die Oxidschicht auf der Metalloberfläche lösen und eine saubere Oberfläche freilegen.
- Phosphatierung/Chromatierung: Nach der Reinigung und Entrostung kann das Werkstück einer Phosphatierungs- oder Chromatierungsbehandlung unterzogen werden. Diese Prozesse erzeugen eine chemische Konversionsschicht auf der Metalloberfläche, die die Haftung und Korrosionsbeständigkeit der Pulverbeschichtung verbessert.
Vorteile der chemischen Vorbehandlung:
- Effektive Reinigung: Die chemische Vorbehandlung ermöglicht eine gründliche Reinigung der Werkstückoberfläche, um alle Arten von Verunreinigungen zu entfernen, die die Haftung der Beschichtung beeinträchtigen könnten.
- Verbesserte Haftung: Durch die Bildung einer chemischen Konversionsschicht wird die Haftung des Pulverlacks auf der Oberfläche des Werkstücks verbessert, was zu einer gleichmäßigen und dauerhaften Beschichtung führt.
- Korrosionsschutz: Die chemische Vorbehandlung bietet einen zusätzlichen Korrosionsschutz, indem sie eine Schutzschicht auf der Metalloberfläche erzeugt, die das Eindringen von Feuchtigkeit und anderen schädlichen Substanzen verhindert.
- Vielseitigkeit: Chemische Vorbehandlungsmethoden können an verschiedene Materialien und Beschichtungsanforderungen angepasst werden, um optimale Ergebnisse zu erzielen und die Leistung der Beschichtung zu maximieren.
Die chemische Vorbehandlung ist ein bewährter und effektiver Schritt im Pulverbeschichtungsprozess, der dazu beiträgt, hochwertige und langlebige Beschichtungen zu erzeugen. Durch eine sorgfältige Durchführung der chemischen Vorbehandlung können Beschichtungsfehler minimiert und die Gesamtqualität der beschichteten Teile verbessert werden.
Phosphatierung
Die Phosphatierung ist ein wichtiger Schritt im Pulverbeschichtungsprozess, der dazu dient, die Oberfläche des Werkstücks für die Beschichtung vorzubereiten und die Haftung sowie die Korrosionsbeständigkeit der Beschichtung zu verbessern. Dieser Prozess beinhaltet die Bildung einer chemischen Konversionsschicht auf der Metalloberfläche durch chemische Reaktionen mit Phosphatierungschemikalien.
Ablauf der Phosphatierung:
- Vorbereitung der Oberfläche: Bevor der Phosphatierungsprozess beginnt, muss die Oberfläche des Werkstücks gründlich gereinigt und von allen Verunreinigungen wie Öl, Fett, Rost und Schmutz befreit werden. Dies ist entscheidend für die Bildung einer gleichmäßigen und haltbaren Phosphatierungsschicht.
- Phosphatierungsbad: Das Werkstück wird dann in ein Phosphatierungsbad eingetaucht, das eine Lösung enthält, die Phosphatierungschemikalien wie Phosphorsäure, Phosphate und andere Additive enthält. Diese Chemikalien reagieren mit der Metalloberfläche und bilden eine chemische Konversionsschicht aus Phosphaten.
- Reaktionszeit: Die Dauer des Phosphatierungsprozesses hängt von verschiedenen Faktoren ab, einschließlich der Art des Metalls, der Temperatur des Phosphatierungsbad und der gewünschten Dicke der Phosphatierungsschicht. Typischerweise dauert der Prozess einige Minuten bis mehrere Stunden.
- Spülung: Nach Abschluss des Phosphatierungsprozesses wird das Werkstück gründlich gespült, um alle überschüssigen Phosphatierungschemikalien zu entfernen und die Oberfläche zu neutralisieren.
Vorteile der Phosphatierung:
- Verbesserte Haftung: Die Phosphatierung bildet eine raue Oberfläche auf der Metalloberfläche, die die Haftung des Pulverlacks verbessert und eine bessere mechanische Verankerung ermöglicht.
- Korrosionsschutz: Die Phosphatierungsschicht bietet einen zusätzlichen Korrosionsschutz, indem sie eine Barriere gegen Feuchtigkeit und andere schädliche Substanzen bildet, die in das Metall eindringen könnten.
- Verbesserte Lackierbarkeit: Die Phosphatierung bereitet die Oberfläche des Werkstücks optimal auf die nachfolgende Lackierung vor, indem sie eine gleichmäßige und gut haftende Oberfläche schafft.
- Verbesserte Oberflächeneigenschaften: Die Phosphatierung kann auch die Oberflächenbeschaffenheit des Werkstücks verbessern, indem sie die Textur und Haptik der Oberfläche verändert und eine gleichmäßige Struktur erzeugt.
Die Phosphatierung ist ein bewährter und effektiver Prozess zur Vorbehandlung von Werkstücken vor der Pulverbeschichtung, der dazu beiträgt, hochwertige und langlebige Beschichtungen zu erzeugen. Durch eine sorgfältige Durchführung der Phosphatierung können Beschichtungsfehler minimiert und die Gesamtqualität der beschichteten Teile verbessert werden.
Chromatierung
Die Chromatierung, auch als Chromatierungsbehandlung oder Chromatüberzug bekannt, ist ein Prozess der Oberflächenbehandlung, der dazu dient, die Korrosionsbeständigkeit von Metalloberflächen zu verbessern und eine Haftgrundlage für nachfolgende Beschichtungen zu schaffen. Dieser Prozess beinhaltet die Bildung einer dünnen Schicht aus Chromverbindungen auf der Metalloberfläche durch chemische Reaktionen.
Ablauf der Chromatierung:
- Vorbereitung der Oberfläche: Vor dem Chromatierungsprozess muss die Oberfläche des Werkstücks gründlich gereinigt und von allen Verunreinigungen wie Öl, Fett, Rost und Schmutz befreit werden. Dies ist entscheidend für die Bildung einer gleichmäßigen und haltbaren Chromatierungsschicht.
- Chromatierungsbad: Das Werkstück wird dann in ein Chromatierungsbad eingetaucht, das eine Lösung enthält, die Chromverbindungen wie Chromsäure, Chrom(III)-verbindungen oder andere Chromatierungschemikalien enthält. Diese Chemikalien reagieren mit der Metalloberfläche und bilden eine chemische Konversionsschicht aus Chromverbindungen.
- Reaktionszeit: Die Dauer des Chromatierungsprozesses hängt von verschiedenen Faktoren ab, einschließlich der Art des Metalls, der Temperatur des Chromatierungsbad und der gewünschten Dicke der Chromatierungsschicht. Typischerweise dauert der Prozess einige Minuten bis mehrere Stunden.
- Spülung: Nach Abschluss des Chromatierungsprozesses wird das Werkstück gründlich gespült, um alle überschüssigen Chromatierungschemikalien zu entfernen und die Oberfläche zu neutralisieren.
Vorteile der Chromatierung:
- Korrosionsschutz: Die Chromatierungsschicht bietet einen effektiven Korrosionsschutz, indem sie eine Barriere gegen Feuchtigkeit und andere schädliche Substanzen bildet, die in das Metall eindringen könnten.
- Haftung: Die Chromatierung verbessert die Haftung von nachfolgenden Beschichtungen wie Pulverlacken oder Farben, indem sie eine gut haftende Oberfläche schafft.
- Verbesserte elektrische Eigenschaften: Chromatierung kann die elektrischen Eigenschaften der Oberfläche verbessern, was insbesondere für elektrische und elektronische Anwendungen von Vorteil ist.
- Ästhetische Verbesserung: Chromatierung kann auch dazu beitragen, das Aussehen der Metalloberfläche zu verbessern, indem sie eine glänzende oder satinierte Oberfläche erzeugt.
Die Chromatierung ist ein bewährter und effektiver Prozess zur Verbesserung der Korrosionsbeständigkeit und Haftung von Metalloberflächen und wird in einer Vielzahl von Branchen eingesetzt, einschließlich der Automobilindustrie, der Luft- und Raumfahrt, der Elektronik und der Bauindustrie. Durch eine sorgfältige Durchführung der Chromatierung können Beschichtungsfehler minimiert und die Gesamtqualität der beschichteten Teile verbessert werden.
Entlackung
Die Entlackung ist ein wichtiger Schritt im Pulverbeschichtungsprozess, der darauf abzielt, alte Beschichtungen, Farben oder Lacke von der Oberfläche des Werkstücks zu entfernen, um eine saubere und vorbereitete Oberfläche für die erneute Beschichtung zu schaffen. Dieser Prozess ist entscheidend, um eine optimale Haftung und Haltbarkeit der neuen Beschichtung sicherzustellen.
Methoden der Entlackung:
- Chemische Entlackung: Diese Methode beinhaltet die Verwendung chemischer Lösungen oder Entlackungsmittel, um alte Beschichtungen von der Oberfläche des Werkstücks zu lösen und zu entfernen. Die Chemikalien werden auf die Oberfläche aufgetragen und lösen die Bindungen der alten Beschichtung, sodass sie leicht abgewaschen oder abgekratzt werden kann.
- Mechanische Entlackung: Bei dieser Methode wird die alte Beschichtung durch mechanische Einwirkung von der Oberfläche entfernt. Dies kann durch Schleifen, Sandstrahlen, Bürsten oder Abkratzen erfolgen. Mechanische Entlackungsmethoden eignen sich besonders für dicke oder stark haftende Beschichtungen.
- Thermische Entlackung: Diese Methode beinhaltet die Erwärmung des Werkstücks auf hohe Temperaturen, um die Bindungen der alten Beschichtung zu brechen und sie von der Oberfläche zu entfernen. Thermische Entlackung kann durch Erhitzen in einem Ofen oder durch Flammenbehandlung erfolgen.
Vorteile der Entlackung:
- Verbesserte Haftung: Die Entlackung entfernt alle Rückstände von alten Beschichtungen, Farben oder Lacken von der Oberfläche des Werkstücks, wodurch eine saubere und vorbereitete Oberfläche geschaffen wird, die eine optimale Haftung der neuen Beschichtung ermöglicht.
- Qualitätsverbesserung: Durch die Entfernung alter Beschichtungen werden Oberflächenfehler wie Blasen, Risse oder Delaminationen beseitigt, was zu einer verbesserten Ästhetik und Haltbarkeit der neuen Beschichtung führt.
- Erneuerung: Die Entlackung ermöglicht die Erneuerung von Werkstücken, die bereits beschichtet waren, indem alte oder beschädigte Beschichtungen entfernt und durch neue ersetzt werden, ohne dass das Werkstück ersetzt werden muss.
- Umweltfreundlichkeit: Viele Entlackungsmethoden verwenden umweltfreundliche oder biologisch abbaubare Chemikalien, die weniger schädlich für die Umwelt sind als herkömmliche Lösungsmittel oder Entlackungsmittel.
Die Entlackung ist ein wichtiger Schritt im Pulverbeschichtungsprozess, der dazu beiträgt, die Qualität und Haltbarkeit der Beschichtung zu verbessern und die Lebensdauer der behandelten Werkstücke zu verlängern. Durch die Auswahl der geeigneten Entlackungsmethode und die sorgfältige Durchführung des Entlackungsprozesses können optimale Ergebnisse erzielt werden.
Vorbehandlungslinie
Eine Vorbehandlungslinie ist ein Schlüsselelement in einer Pulverbeschichtungsanlage, das für die Vorbereitung der Werkstückoberflächen vor dem Beschichtungsprozess verantwortlich ist. Sie besteht aus einer Reihe von Maschinen und Einrichtungen, die verschiedene Vorbehandlungsschritte durchführen, um eine optimale Haftung und Haltbarkeit der Beschichtung zu gewährleisten.
Komponenten einer Vorbehandlungslinie:
- Reinigungsstation: Die Reinigungsstation ist der erste Schritt in der Vorbehandlungslinie und beinhaltet die Entfernung von Schmutz, Fett, Öl und anderen Verunreinigungen von der Oberfläche der Werkstücke. Dies kann durch Waschen, Entfetten oder andere Reinigungsmethoden erfolgen.
- Entrostungsstation: Nach der Reinigung werden die Werkstücke in die Entrostungsstation weitergeleitet, wo alle Rost- und Korrosionsspuren von der Oberfläche entfernt werden. Dies kann durch Sandstrahlen, chemische Entrostung oder andere mechanische Methoden erfolgen.
- Phosphatierungsstation: Nach der Entrostung können die Werkstücke einer Phosphatierungsbehandlung unterzogen werden, um die Haftung und Korrosionsbeständigkeit der Beschichtung zu verbessern. Diese Station beinhaltet das Eintauchen der Werkstücke in ein Phosphatierungsbad, das eine chemische Konversionsschicht auf der Oberfläche bildet.
- Chromatierungsstation: Alternativ zur Phosphatierung kann eine Chromatierungsbehandlung durchgeführt werden, um die Oberflächeneigenschaften der Werkstücke zu verbessern und eine bessere Haftung der Beschichtung zu gewährleisten. Diese Station beinhaltet das Eintauchen der Werkstücke in ein Chromatierungsbad, das eine dünnen Schicht aus Chromverbindungen erzeugt.
- Trocknungsstation: Nach Abschluss der Vorbehandlungsschritte werden die Werkstücke in einer Trocknungsstation getrocknet, um sicherzustellen, dass keine Feuchtigkeit mehr auf der Oberfläche vorhanden ist. Dies ist entscheidend für eine optimale Haftung und Haltbarkeit der Beschichtung.
Vorteile einer Vorbehandlungslinie:
- Verbesserte Beschichtungsqualität: Eine Vorbehandlungslinie gewährleistet eine gründliche Vorbereitung der Werkstückoberflächen, was zu einer verbesserten Haftung, Haltbarkeit und Ästhetik der Beschichtung führt.
- Effizienzsteigerung: Durch die Automatisierung und Integration der Vorbehandlungsschritte in eine Linie wird die Produktionsgeschwindigkeit erhöht und der Gesamtprozess optimiert.
- Konsistenz: Eine Vorbehandlungslinie gewährleistet eine gleichbleibende Qualität und Konsistenz der Vorbehandlungsschritte für alle Werkstücke, unabhängig von ihrer Größe oder Form.
- Umweltfreundlichkeit: Moderne Vorbehandlungslinien verwenden häufig umweltfreundliche Chemikalien und Verfahren, die die Umweltbelastung minimieren und den Anforderungen an Umweltschutz und Nachhaltigkeit gerecht werden.
Eine gut konzipierte und betriebene Vorbehandlungslinie ist entscheidend für den Erfolg einer Pulverbeschichtungsanlage und trägt wesentlich zur Qualität, Effizienz und Umweltfreundlichkeit des Beschichtungsprozesses bei. Durch die Investition in eine hochwertige Vorbehandlungslinie können Hersteller die Leistung ihrer Beschichtungsanlagen optimieren und wettbewerbsfähige Produkte von höchster Qualität liefern.
Pulverbeschichtungsofen
Ein Pulverbeschichtungsofen ist eine zentrale Komponente in einer Pulverbeschichtungsanlage, die für das Aushärten und Verschmelzen des aufgetragenen Pulverlacks verantwortlich ist. Der Ofen spielt eine entscheidende Rolle bei der Erzeugung einer dauerhaften, gleichmäßigen und hochwertigen Beschichtung auf den Werkstücken.
Funktionsweise eines Pulverbeschichtungsofens:
- Erhitzung: Der Ofen verfügt über Heizelemente, die die Luft im Ofeninneren auf die erforderliche Temperatur erhitzten. Diese Temperatur liegt typischerweise zwischen 150°C und 220°C, je nach den Anforderungen des verwendeten Pulverlacks und des zu beschichtenden Materials.
- Aushärten des Pulverlacks: Nachdem die gewünschte Temperatur erreicht ist, werden die Werkstücke in den Ofen eingeführt, wo der aufgetragene Pulverlack schmilzt, sich ausbreitet und aushärtet. Dieser Vorgang dauert in der Regel einige Minuten und bewirkt eine chemische Reaktion im Pulverlack, die zu einer vollständigen Vernetzung und Aushärtung führt.
- Abkühlung: Nach dem Aushärten verlassen die Werkstücke den Ofen und werden abgekühlt, entweder durch natürliche Luftzirkulation oder durch spezielle Kühlvorrichtungen. Eine angemessene Abkühlung ist wichtig, um sicherzustellen, dass die Beschichtung vollständig ausgehärtet ist und ihre endgültigen mechanischen und optischen Eigenschaften erreicht.
Arten von Pulverbeschichtungsofen:
- Konvektionsofen: Dies ist die häufigste Art von Pulverbeschichtungsofen, bei dem die Luft im Ofen durch Konvektion erwärmt wird. Dies ermöglicht eine gleichmäßige Erwärmung der Werkstücke und eine gleichmäßige Aushärtung des Pulverlacks.
- Infrarotofen: Infrarotöfen verwenden Infrarotstrahlung, um die Werkstücke direkt zu erwärmen. Diese Methode ermöglicht eine schnellere Erwärmung und Aushärtung, eignet sich jedoch möglicherweise nicht für alle Arten von Beschichtungen und Materialien.
- Induktionsofen: Induktionsöfen erzeugen Wärme durch elektromagnetische Induktion, indem sie elektrische Ströme in den Werkstücken erzeugen. Diese Methode ermöglicht eine präzise und effiziente Erwärmung, ist jedoch oft teurer und komplexer als andere Optionen.
Vorteile eines Pulverbeschichtungsofens:
- Effizienz: Ein Pulverbeschichtungsofen ermöglicht eine schnelle und effiziente Aushärtung des Pulverlacks, was zu einer hohen Produktionsgeschwindigkeit und niedrigeren Betriebskosten führt.
- Qualität: Durch die präzise Steuerung der Temperatur und anderer Prozessparameter gewährleistet der Ofen eine gleichbleibende Qualität und Haltbarkeit der Beschichtung.
- Vielseitigkeit: Pulverbeschichtungsofen können an verschiedene Beschichtungsanforderungen angepasst werden und sind für eine Vielzahl von Materialien und Beschichtungstypen geeignet.
- Umweltfreundlichkeit: Im Vergleich zu anderen Beschichtungsverfahren wie der Nasslackierung erzeugt die Pulverbeschichtung weniger Abfall und Emissionen, was zu einer geringeren Umweltbelastung führt.
Ein hochwertiger Pulverbeschichtungsofen ist entscheidend für den Erfolg einer Pulverbeschichtungsanlage und trägt wesentlich zur Qualität, Effizienz und Wirtschaftlichkeit des Beschichtungsprozesses bei. Durch die Auswahl des geeigneten Ofentyps und die sorgfältige Steuerung der Prozessparameter können Hersteller optimale Ergebnisse erzielen und wettbewerbsfähige Produkte von höchster Qualität liefern.
Pulverbeschichtungskabine
Eine Pulverbeschichtungskabine, auch als Pulverbeschichtungskammer oder Pulverkabine bekannt, ist eine geschlossene Umgebung, in der der eigentliche Beschichtungsprozess stattfindet. Sie spielt eine entscheidende Rolle bei der Erzielung einer gleichmäßigen, hochwertigen und kontrollierten Beschichtung auf den Werkstücken.
Funktionsweise einer Pulverbeschichtungskabine:
- Auftragen des Pulverlacks: In der Pulverbeschichtungskabine wird der Pulverlack auf die zu beschichtenden Werkstücke aufgetragen. Dies kann durch verschiedene Methoden erfolgen, darunter elektrostatisches Sprühen, Tribosprühverfahren oder manuelles Auftragen.
- Elektrostatische Aufladung: In vielen Pulverbeschichtungskabinen wird der Pulverlack elektrostatisch aufgeladen, um eine gleichmäßige Verteilung auf den Werkstücken zu gewährleisten. Durch die elektrostatische Aufladung haftet der Pulverlack effizienter an den Werkstücken und bildet eine gleichmäßige Beschichtung.
- Abscheidung des überschüssigen Pulvers: Nach dem Auftragen des Pulverlacks wird das überschüssige Pulver in der Kabine gesammelt und wiederverwendet. Dies kann durch Rückgewinnungssysteme erfolgen, die das überschüssige Pulver abscheiden und für den erneuten Gebrauch aufbereiten.
- Aushärtung des Pulverlacks: Nachdem der Pulverlack aufgetragen wurde, werden die Werkstücke in einen Pulverbeschichtungsofen oder einen Trockenbereich transportiert, wo der Lack bei erhöhter Temperatur ausgehärtet wird.
Arten von Pulverbeschichtungskabinen:
- Manuelle Pulverbeschichtungskabine: Diese Art von Kabine wird von einem Bediener manuell betrieben, der den Pulverlack auf die Werkstücke aufträgt. Sie eignet sich besonders für kleinere Produktionsmengen und spezielle Anwendungen.
- Automatische Pulverbeschichtungskabine: Automatische Pulverbeschichtungskabinen sind für den Betrieb ohne menschliches Eingreifen ausgelegt. Sie verwenden automatisierte Sprüh- und Transportsysteme, um den Beschichtungsprozess zu optimieren und die Produktivität zu steigern.
- Sprühkabine mit Spritzwänden: Diese Art von Kabine verfügt über spezielle Spritzwände, die das überschüssige Pulver beim Auftragen des Pulverlacks abscheiden und zurückhalten. Dies ermöglicht eine saubere und kontrollierte Arbeitsumgebung.
Vorteile einer Pulverbeschichtungskabine:
- Gleichmäßige Beschichtung: Eine Pulverbeschichtungskabine gewährleistet eine gleichmäßige Verteilung des Pulverlacks auf den Werkstücken, was zu einer hochwertigen und ästhetisch ansprechenden Beschichtung führt.
- Effizienz: Durch die Verwendung von Rückgewinnungssystemen und automatisierten Prozessen ermöglicht eine Pulverbeschichtungskabine eine effiziente Nutzung von Materialien und Ressourcen.
- Flexibilität: Pulverbeschichtungskabinen können an verschiedene Werkstückgrößen und -formen angepasst werden, um eine Vielzahl von Beschichtungsanwendungen zu unterstützen.
- Umweltfreundlichkeit: Im Vergleich zu anderen Beschichtungsverfahren wie der Nasslackierung erzeugt die Pulverbeschichtung weniger Abfall und Emissionen, was zu einer geringeren Umweltbelastung führt.
Eine gut konzipierte und betriebene Pulverbeschichtungskabine ist entscheidend für den Erfolg einer Pulverbeschichtungsanlage und trägt wesentlich zur Qualität, Effizienz und Wirtschaftlichkeit des Beschichtungsprozesses bei. Durch die Auswahl der geeigneten Kabine und die sorgfältige Steuerung der Prozessparameter können Hersteller optimale Ergebnisse erzielen und wettbewerbsfähige Produkte von höchster Qualität liefern.
Pulverbeschichtungspistole
Die Pulverbeschichtungspistole ist ein wesentliches Werkzeug in einer Pulverbeschichtungsanlage, das für das Auftragen des Pulverlacks auf die zu beschichtenden Werkstücke verantwortlich ist. Sie spielt eine entscheidende Rolle bei der Erzielung einer gleichmäßigen, hochwertigen und kontrollierten Beschichtung.
Funktionsweise einer Pulverbeschichtungspistole:
- Pulveraufnahme: Die Pistole verfügt über einen Behälter oder eine Kammer, in der das Pulverlackmaterial aufgenommen wird. Das Pulver wird durch Druckluft oder eine andere Gasquelle aus der Kammer herausgedrückt und zur Düse der Pistole geführt.
- Elektrostatische Aufladung: In vielen Pulverbeschichtungspistolen wird der Pulverlack elektrostatisch aufgeladen, um eine gleichmäßige Verteilung auf den Werkstücken zu gewährleisten. Durch die elektrostatische Aufladung haftet der Pulverlack effizienter an den Werkstücken und bildet eine gleichmäßige Beschichtung.
- Sprühvorgang: Das Pulverlackmaterial wird durch die Düse der Pistole gesprüht und auf die zu beschichtenden Werkstücke aufgetragen. Die Pistole kann verschiedene Sprühmuster erzeugen, um eine gleichmäßige Beschichtung auch auf komplex geformten Teilen zu gewährleisten.
- Luftstrom: Neben dem Pulverlack wird auch ein Luftstrom durch die Pistole geleitet, der dazu dient, das Pulver zu verteilen und überschüssiges Material zu entfernen. Dies trägt zur Kontrolle der Beschichtungsdicke und zur Vermeidung von Überlappungen oder Unregelmäßigkeiten bei.
Arten von Pulverbeschichtungspistolen:
- Manuelle Pulverbeschichtungspistole: Diese Art von Pistole wird von einem Bediener manuell gehalten und bedient. Sie eignet sich besonders für kleinere Produktionsmengen und spezielle Anwendungen, bei denen Flexibilität und Kontrolle erforderlich sind.
- Automatische Pulverbeschichtungspistole: Automatische Pistolen sind für den Betrieb ohne menschliches Eingreifen ausgelegt. Sie sind Teil eines automatisierten Beschichtungssystems und können an Roboterarme oder andere mechanisierte Vorrichtungen montiert werden.
- Handheld Pulverbeschichtungspistole: Diese Pistolen sind tragbar und können direkt von Hand gehalten werden. Sie eignen sich besonders für die Beschichtung kleinerer Teile oder für Arbeiten an schwer zugänglichen Stellen.
Vorteile einer Pulverbeschichtungspistole:
- Präzision: Eine Pulverbeschichtungspistole ermöglicht eine präzise Steuerung des Beschichtungsprozesses und eine gezielte Applikation des Pulverlacks auf den Werkstücken.
- Effizienz: Durch die Verwendung von Pulverbeschichtungspistolen können Material- und Arbeitskosten gesenkt werden, da weniger Material verschwendet wird und die Beschichtungsgeschwindigkeit erhöht wird.
- Flexibilität: Pulverbeschichtungspistolen sind an verschiedene Werkstückgrößen und -formen anpassbar und eignen sich für eine Vielzahl von Beschichtungsanwendungen.
- Umweltfreundlichkeit: Im Vergleich zu anderen Beschichtungsverfahren wie der Nasslackierung erzeugt die Pulverbeschichtung weniger Abfall und Emissionen, was zu einer geringeren Umweltbelastung führt.
Eine gut gewartete und kalibrierte Pulverbeschichtungspistole ist entscheidend für den Erfolg einer Pulverbeschichtungsanlage und trägt wesentlich zur Qualität, Effizienz und Wirtschaftlichkeit des Beschichtungsprozesses bei. Durch die Auswahl der geeigneten Pistole und die Schulung des Bedienpersonals können Hersteller optimale Ergebnisse erzielen und wettbewerbsfähige Produkte von höchster Qualität liefern.
Pulverrückgewinnungssystem
Ein Pulverrückgewinnungssystem ist eine wichtige Komponente in einer Pulverbeschichtungsanlage, das dazu dient, überschüssiges Pulverlackmaterial zu sammeln, zu sieben und für den erneuten Gebrauch aufzubereiten. Diese Systeme spielen eine entscheidende Rolle bei der Reduzierung von Abfall, Materialkosten und Umweltbelastungen in der Beschichtungsindustrie.
Funktionsweise eines Pulverrückgewinnungssystems:
- Pulversammlung: Nach dem Auftragen des Pulverlacks in der Beschichtungskabine oder mit der Beschichtungspistole wird überschüssiges Material abgeschieden und gesammelt. Dies kann durch spezielle Abscheidesysteme oder Rückgewinnungskammern erfolgen, die das überschüssige Pulver auffangen und in ein Sammelbehältnis leiten.
- Siebung: Das gesammelte Pulverlackmaterial wird durch ein Siebsystem geführt, um Verunreinigungen wie Schmutz, Farbpartikel oder agglomerierte Pulverklumpen zu entfernen. Dies stellt sicher, dass nur sauberes und verwendbares Pulverlackmaterial für den erneuten Gebrauch aufbereitet wird.
- Aufbereitung: Nach dem Sieben wird das gereinigte Pulverlackmaterial in einem Pulverbeschichtungsofen oder einer speziellen Aufbereitungseinheit erhitzt, um eventuelle Feuchtigkeit zu entfernen und die Partikel zu reaktivieren. Dies stellt sicher, dass das aufbereitete Pulverlackmaterial die erforderlichen Fließeigenschaften und Haftungsmerkmale für den erneuten Einsatz hat.
- Wiederverwendung: Das aufbereitete Pulverlackmaterial kann dann in der Pulverbeschichtungsanlage für neue Beschichtungsanwendungen wiederverwendet werden. Dies reduziert den Bedarf an frischem Pulverlackmaterial und senkt somit die Materialkosten und Abfallmengen.
Arten von Pulverrückgewinnungssystemen:
- Zyklonabscheider: Diese Systeme verwenden Zentrifugalkräfte, um das überschüssige Pulver aus der Luft zu trennen und in einem Sammelbehälter zu sammeln. Sie sind effektiv und kostengünstig, aber weniger effizient bei der Rückgewinnung von feinem Pulverlack.
- Filtersysteme: Filtersysteme verwenden spezielle Filtermedien wie Kartuschenfilter oder Staubfilter, um das überschüssige Pulver aus der Luft zu filtern und zurückzugewinnen. Sie sind effizienter bei der Rückgewinnung von feinem Pulverlack, erfordern jedoch regelmäßige Wartung und Reinigung der Filter.
- Elektrostatische Rückgewinnung: Diese Systeme nutzen elektrostatische Prinzipien, um das überschüssige Pulver zu sammeln und zurückzugewinnen. Sie sind besonders effektiv bei der Rückgewinnung von feinem Pulverlack und können in Kombination mit anderen Rückgewinnungstechnologien eingesetzt werden.
Vorteile eines Pulverrückgewinnungssystems:
- Abfallreduzierung: Durch die Rückgewinnung und Wiederverwendung von überschüssigem Pulverlackmaterial reduziert ein Pulverrückgewinnungssystem Abfallmengen und senkt die Entsorgungskosten.
- Kosteneffizienz: Die Wiederverwendung von Pulverlackmaterial verringert den Bedarf an frischem Material und senkt somit die Materialkosten für die Beschichtung.
- Umweltfreundlichkeit: Die Reduzierung von Abfall und die Wiederverwendung von Materialien machen Pulverrückgewinnungssysteme zu einer umweltfreundlichen Option für Beschichtungsanwendungen.
- Qualitätssicherung: Durch die Verwendung von aufbereitetem Pulverlackmaterial kann die Beschichtungsqualität verbessert werden, da das Material bereits für die Anwendung optimiert ist.
Ein gut konzipiertes und betriebenes Pulverrückgewinnungssystem ist entscheidend für den Erfolg einer Pulverbeschichtungsanlage und trägt wesentlich zur Effizienz, Wirtschaftlichkeit und Umweltverträglichkeit des Beschichtungsprozesses bei. Durch die Auswahl des geeigneten Rückgewinnungssystems und die regelmäßige Wartung können Hersteller optimale Ergebnisse erzielen und die Lebensdauer ihrer Beschichtungsanlagen maximieren.
Farbspektrometer
Ein Farbspektrometer ist ein Messgerät, das verwendet wird, um die Farbe eines Objekts zu analysieren und quantitativ zu messen. In einer Pulverbeschichtungsanlage spielt das Farbspektrometer eine wichtige Rolle bei der Überwachung und Steuerung der Farbgenauigkeit und -konsistenz während des Beschichtungsprozesses.
Funktionsweise eines Farbspektrometers:
- Lichtquelle: Das Farbspektrometer sendet Lichtstrahlen unterschiedlicher Wellenlängen aus, die auf die Oberfläche des zu messenden Objekts treffen.
- Reflexion: Das Licht wird von der Oberfläche des Objekts reflektiert und in das Spektrometer zurückgeleitet.
- Spektroskopie: Das Spektrometer analysiert das reflektierte Licht und zerlegt es in seine spektralen Bestandteile. Auf diese Weise wird die Farbzusammensetzung des Objekts gemessen.
- Farbmessung: Basierend auf den spektralen Daten berechnet das Farbspektrometer verschiedene Farbparameter wie Farbton, Sättigung und Helligkeit. Diese Parameter werden häufig in standardisierten Farbsystemen wie CIE LAB oder RGB ausgedrückt.
Anwendungen eines Farbspektrometers in der Pulverbeschichtung:
- Farbprüfung: Das Farbspektrometer ermöglicht es, die Farbe des aufgetragenen Pulverlacks zu messen und mit dem gewünschten Farbton zu vergleichen. Auf diese Weise können Farbabweichungen frühzeitig erkannt und korrigiert werden.
- Farbformulierung: Durch die Messung der Farbe von Referenzmustern oder Farbkarten kann das Farbspektrometer bei der Formulierung neuer Farbtöne oder der Anpassung bestehender Farbrezepturen helfen.
- Qualitätskontrolle: Das Farbspektrometer wird zur Überwachung der Farbkonsistenz während des Beschichtungsprozesses eingesetzt. Es kann dazu beitragen, Abweichungen in der Farbe von Chargen oder Werkstücken zu identifizieren und zu korrigieren.
- Farbkalibrierung: Vor der Beschichtung kann das Farbspektrometer dazu verwendet werden, die Farbgenauigkeit und -konsistenz der Pulverlacke zu überprüfen und sicherzustellen, dass sie den spezifizierten Farbstandards entsprechen.
Vorteile eines Farbspektrometers:
- Präzision: Ein Farbspektrometer bietet eine präzise und objektive Messung der Farbe eines Objekts, ohne die subjektiven Einflüsse des menschlichen Auges.
- Effizienz: Durch die automatisierte Messung und Auswertung können Farbprüfungen schneller durchgeführt werden, was die Produktivität und Effizienz des Beschichtungsprozesses erhöht.
- Qualitätsverbesserung: Durch die kontinuierliche Überwachung und Steuerung der Farbgenauigkeit und -konsistenz kann das Farbspektrometer zur Verbesserung der Produktqualität beitragen und Ausschuss reduzieren.
- Dokumentation: Die Messergebnisse können dokumentiert und archiviert werden, um die Rückverfolgbarkeit von Produktionschargen zu gewährleisten und Qualitätsstandards einzuhalten.
Ein Farbspektrometer ist ein unverzichtbares Instrument in einer Pulverbeschichtungsanlage, das zur Sicherstellung einer konsistenten und hochwertigen Farbgebung beiträgt. Durch die Integration von Farbspektrometern in den Beschichtungsprozess können Hersteller die Farbgenauigkeit verbessern, Kosten senken und die Kundenzufriedenheit steigern.
Beschichtungsdicke
Die Beschichtungsdicke ist ein wichtiger Parameter in der Pulverbeschichtung, der die Menge an aufgetragenem Pulverlack auf der Oberfläche eines Werkstücks angibt. Die genaue Kontrolle der Beschichtungsdicke ist entscheidend für die Qualität und Haltbarkeit der Beschichtung sowie für die Einhaltung von technischen Standards und Spezifikationen.
Bedeutung der Beschichtungsdicke:
- Schutz vor Korrosion und Verschleiß: Die Dicke der Pulverbeschichtung beeinflusst direkt ihre Schutzeigenschaften gegenüber Korrosion, Verschleiß und anderen Umwelteinflüssen. Eine ausreichende Beschichtungsdicke gewährleistet einen wirksamen Schutz der Oberfläche des Werkstücks.
- Ästhetisches Erscheinungsbild: Die Beschichtungsdicke kann auch das ästhetische Erscheinungsbild des beschichteten Werkstücks beeinflussen, insbesondere wenn es um gleichmäßige Farbgebung und Glanz geht. Eine zu dicke Beschichtung kann zu Unebenheiten oder Lackläufen führen, während eine zu dünne Beschichtung möglicherweise nicht ausreichend Schutz bietet.
- Mechanische Eigenschaften: Die Dicke der Pulverbeschichtung kann auch die mechanischen Eigenschaften des beschichteten Werkstücks beeinflussen, einschließlich der Festigkeit, Härte und Flexibilität der Beschichtung. Eine optimale Beschichtungsdicke ist erforderlich, um die gewünschten mechanischen Leistungsmerkmale zu erreichen.
Messung der Beschichtungsdicke:
- Zerstörungsfreie Messmethoden: Dazu gehören Methoden wie Wirbelstromprüfung und Ultraschallprüfung, bei denen die Beschichtungsdicke durch Messung von elektrischen oder akustischen Eigenschaften des beschichteten Substrats bestimmt wird. Diese Methoden eignen sich besonders für die Qualitätskontrolle und Inspektion von fertigen Beschichtungen.
- Zerstörende Messmethoden: Hierzu gehören Methoden wie Schichtdickenmessung durch Schnitte oder chemische Analyse, bei denen Proben des beschichteten Werkstücks entnommen und die Beschichtungsdicke direkt gemessen wird. Diese Methoden sind genauer, erfordern jedoch die Entnahme von Proben und können das Werkstück beschädigen.
Einflussfaktoren auf die Beschichtungsdicke:
- Sprühtechnik: Die Wahl der Sprühtechnik und die Einstellung der Sprühparameter wie Sprühdruck, Düsenöffnung und Sprühmuster können die Beschichtungsdicke beeinflussen.
- Substratvorbereitung: Die Oberflächenbeschaffenheit und Sauberkeit des Substrats können die Haftung und die Dicke der aufgetragenen Beschichtung beeinflussen.
- Pulverlackeigenschaften: Die Viskosität, Fließeigenschaften und chemische Zusammensetzung des verwendeten Pulverlacks können ebenfalls die Beschichtungsdicke beeinflussen.
Bedeutung der Kontrolle der Beschichtungsdicke:
- Qualitätssicherung: Eine genaue Kontrolle der Beschichtungsdicke ermöglicht eine Qualitätskontrolle und -sicherung während des gesamten Beschichtungsprozesses.
- Kostenoptimierung: Durch die Optimierung der Beschichtungsdicke können Materialkosten gesenkt und Ausschuss minimiert werden.
- Normenkonformität: Viele technische Standards und Spezifikationen legen Mindest- oder Maximalwerte für die Beschichtungsdicke fest, um die Einhaltung von Qualitätsstandards sicherzustellen.
Die genaue Kontrolle und Messung der Beschichtungsdicke ist entscheidend für die Herstellung hochwertiger, langlebiger und ästhetisch ansprechender Beschichtungen in der Pulverbeschichtungsindustrie. Durch die Auswahl geeigneter Messmethoden und die Implementierung effektiver Qualitätskontrollverfahren können Hersteller optimale Ergebnisse erzielen und die Leistungsfähigkeit ihrer Beschichtungsanlagen maximieren.
Aushärtungsofen
Ein Aushärtungsofen ist eine zentrale Komponente in einer Pulverbeschichtungsanlage, die für die Aushärtung des aufgetragenen Pulverlacks verantwortlich ist. Die Aushärtung erfolgt durch Erhitzen der beschichteten Werkstücke auf eine bestimmte Temperatur, um eine dauerhafte und widerstandsfähige Beschichtung zu gewährleisten.
Funktionsweise eines Aushärtungsofens:
- Temperatursteuerung: Der Aushärtungsofen verfügt über ein Heizsystem, das die Temperatur im Inneren des Ofens präzise steuert. Die Temperatur wird auf die spezifischen Anforderungen des verwendeten Pulverlacks eingestellt, um eine vollständige Aushärtung zu gewährleisten.
- Luftzirkulation: Durch die Luftzirkulation im Ofen wird die Wärme gleichmäßig über die Oberfläche der beschichteten Werkstücke verteilt. Dies gewährleistet eine gleichmäßige Aushärtung und verhindert lokale Überhitzung oder ungleichmäßige Trocknung.
- Aushärtungszeit: Die Werkstücke verbleiben für eine bestimmte Zeit in dem Aushärtungsofen, um die erforderliche Aushärtungstemperatur und -dauer zu erreichen. Die Aushärtungszeit hängt von verschiedenen Faktoren ab, einschließlich der Art des Pulverlacks, der Schichtdicke und der Werkstückmaterialien.
- Kühlung: Nach der Aushärtung werden die Werkstücke im Ofen abgekühlt, bevor sie aus dem Ofen entfernt werden. Dies dient dazu, die Beschichtung zu stabilisieren und sicherzustellen, dass sie die gewünschten mechanischen und optischen Eigenschaften aufweist.
Arten von Aushärtungsofen:
- Konvektionsofen: Diese Öfen verwenden konventionelle Heizelemente, um die Luft im Ofen zu erwärmen, die dann die Werkstücke umgibt und erwärmt. Sie sind kostengünstig und einfach in der Handhabung, erfordern jedoch möglicherweise längere Aushärtungszeiten.
- Infrarotofen: Infrarotöfen verwenden Infrarotstrahlung, um die Oberfläche der Werkstücke direkt zu erwärmen, anstatt die umgebende Luft zu erwärmen. Sie bieten eine schnellere und gleichmäßigere Aushärtung, sind jedoch oft teurer in der Anschaffung und erfordern eine präzise Steuerung.
- Umluftofen: Umluftöfen verwenden einen Ventilator, um die Luft im Ofen gleichmäßig zu zirkulieren und eine gleichmäßige Wärmeverteilung zu gewährleisten. Sie sind besonders effektiv für große oder komplexe Werkstücke, bei denen eine gleichmäßige Wärmeübertragung erforderlich ist.
Vorteile eines Aushärtungsofens:
- Qualitätssicherung: Ein Aushärtungsofen gewährleistet eine gleichmäßige und vollständige Aushärtung des Pulverlacks, was zu einer hochwertigen und langlebigen Beschichtung führt.
- Effizienz: Durch die Verwendung eines Aushärtungsofens können Aushärtungszeiten optimiert und Produktionsdurchlaufzeiten verkürzt werden, was die Effizienz des Beschichtungsprozesses erhöht.
- Flexibilität: Aushärtungsofen können an verschiedene Werkstückgrößen und -formen angepasst werden, um eine Vielzahl von Beschichtungsanwendungen zu unterstützen.
- Energieeffizienz: Moderne Aushärtungsofen sind oft energieeffizienter und umweltfreundlicher, was zu geringeren Betriebskosten und einer geringeren Umweltbelastung führt.
Ein gut gewarteter und kalibrierter Aushärtungsofen ist entscheidend für den Erfolg einer Pulverbeschichtungsanlage und trägt wesentlich zur Qualität, Effizienz und Wirtschaftlichkeit des Beschichtungsprozesses bei. Durch die Auswahl des geeigneten Ofentyps und die sorgfältige Steuerung der Aushärtungsparameter können Hersteller optimale Ergebnisse erzielen und wettbewerbsfähige Produkte von höchster Qualität liefern.
Farbbeständigkeit
Die Farbbeständigkeit ist ein wichtiger Aspekt in der Pulverbeschichtung und bezieht sich auf die Fähigkeit des aufgetragenen Pulverlacks, seine Farbe und optische Erscheinung über einen längeren Zeitraum unter verschiedenen Umweltbedingungen zu erhalten. Eine hohe Farbbeständigkeit ist entscheidend für die Qualität und Langlebigkeit der Beschichtung, insbesondere bei Anwendungen im Freien oder in anspruchsvollen Umgebungen.
Faktoren, die die Farbbeständigkeit beeinflussen:
- UV-Beständigkeit: Die Belichtung durch ultraviolette (UV) Strahlung kann zu Verblassung und Farbveränderungen des Pulverlacks führen. UV-stabile Pigmente und Harzsysteme können die Farbbeständigkeit verbessern und die Auswirkungen von UV-Strahlung minimieren.
- Witterungsbeständigkeit: Extreme Witterungsbedingungen wie Sonneneinstrahlung, Regen, Schnee und Temperaturschwankungen können die Farbe und Oberflächenbeschaffenheit des Pulverlacks beeinträchtigen. Wetterfeste Beschichtungssysteme bieten einen verbesserten Schutz vor Umwelteinflüssen.
- Chemikalienbeständigkeit: Kontakt mit Chemikalien wie Reinigungsmitteln, Lösungsmitteln oder industriellen Verschmutzungen kann die Farbe des Pulverlacks verändern oder beschädigen. Chemikalienbeständige Beschichtungssysteme sind für Anwendungen in aggressiven Umgebungen erforderlich.
- Abriebfestigkeit: Mechanische Beanspruchung und Abrieb können die Oberfläche des Pulverlacks beschädigen und zu Farbverlust führen. Abriebfeste Beschichtungssysteme bieten einen verbesserten Schutz vor Kratzern, Abrieb und Verschleiß.
Methoden zur Bewertung der Farbbeständigkeit:
- Beschleunigte Witterungstests: Standardisierte Testverfahren wie ASTM G155 oder ISO 4892 ermöglichen die Simulation von Langzeitbelichtung und Witterungseinflüssen in kurzer Zeit, um die Farbbeständigkeit zu bewerten.
- Natürliche Exposition: Langfristige Beobachtung und Überwachung von beschichteten Proben in realen Umgebungsbedingungen können wertvolle Informationen über die Langzeitbeständigkeit des Pulverlacks liefern.
- Laborprüfungen: Chemische Analysen, Kratzfestigkeitstests, Haftungstests und andere Laborprüfungen können die Farbbeständigkeit unter spezifischen Bedingungen bewerten und potenzielle Schwachstellen identifizieren.
Bedeutung der Farbbeständigkeit:
- Langfristige Ästhetik: Eine hohe Farbbeständigkeit gewährleistet, dass die beschichteten Oberflächen über einen längeren Zeitraum ihr ästhetisches Erscheinungsbild und ihre Farbintensität behalten, was zu zufriedenen Kunden führt.
- Langlebigkeit und Schutz: Ein farbbeständiger Pulverlack bietet einen dauerhaften Schutz vor Umwelteinflüssen und mechanischer Beanspruchung, was die Lebensdauer der beschichteten Bauteile verlängert.
- Qualitätsindikator: Die Farbbeständigkeit ist ein wichtiger Qualitätsindikator für Pulverlacke und Beschichtungssysteme und kann die Zuverlässigkeit und Leistungsfähigkeit eines Produkts widerspiegeln.
- Wirtschaftlichkeit: Farbbeständige Beschichtungen erfordern weniger häufige Nacharbeiten oder Neubeschichtungen, was zu geringeren Wartungs- und Instandhaltungskosten führt und die Gesamtbetriebskosten senkt.
Die Verbesserung der Farbbeständigkeit ist ein kontinuierlicher Entwicklungsprozess in der Pulverbeschichtungsindustrie und erfordert die Auswahl hochwertiger Rohstoffe, die Optimierung von Beschichtungsprozessen und die kontinuierliche Überwachung und Bewertung der Beschichtungsleistung unter realen Einsatzbedingungen. Durch die Investition in farbbeständige Beschichtungssysteme können Hersteller hochwertige Produkte liefern, die den anspruchsvollen Anforderungen ihrer Kunden gerecht werden.
Die Pulverbeschichtung ist ein weit verbreitetes Verfahren zur Oberflächenveredelung, das sich durch seine umweltfreundlichen Eigenschaften und Langlebigkeit der Beschichtung auszeichnet. Im Gegensatz zu herkömmlichen flüssigen Beschichtungen werden bei der Pulverbeschichtung trockene Pulverpartikel elektrostatisch auf die Oberfläche eines Werkstücks aufgebracht. Anschließend wird das Pulver in einem Ofen erhitzt, wodurch es schmilzt und eine gleichmäßige, dauerhafte Beschichtung bildet.
Vorteile der Pulverbeschichtung umfassen:
- Umweltfreundlichkeit: Keine Lösungsmittel und geringere Emissionen von flüchtigen organischen Verbindungen (VOC).
- Effizienz: Hohe Materialausnutzung und weniger Abfall.
- Robustheit: Gute Beständigkeit gegen chemische, mechanische und Witterungseinflüsse.
Pulverbeschichtungsanlagen

Pulverbeschichtungsanlagen sind zentraler Bestandteil des Pulverbeschichtungsprozesses und umfassen die komplette Infrastruktur, die zur Anwendung von Pulverbeschichtungen erforderlich ist. Diese Anlagen sind in verschiedenen Größen und Ausführungen erhältlich, um unterschiedlichen industriellen Anforderungen gerecht zu werden.
Typen von Pulverbeschichtungsanlagen:
- Manuelle Pulverbeschichtungsanlagen:
Ideal für kleinere Betriebe oder spezialisierte Anwendungen, bei denen Flexibilität gefordert ist. Sie bestehen aus einer Pulverkabine, einem Pulvergerät und einem Einbrennofen. - Halbautomatische Anlagen:
Kombinieren manuelle und automatische Prozesse, um eine höhere Effizienz bei mittleren Produktionsvolumina zu erreichen. Diese Anlagen bieten eine gute Balance zwischen Flexibilität und Automatisierung. - Vollautomatische Pulverbeschichtungsanlagen:
Entwickelt für Großserienproduktionen. Diese Anlagen sind vollständig automatisiert und beinhalten Fördersysteme, automatische Pistolen und integrierte Steuerungssysteme, um hohe Produktionsgeschwindigkeiten und gleichbleibende Qualität zu gewährleisten.
Pulverkabinen
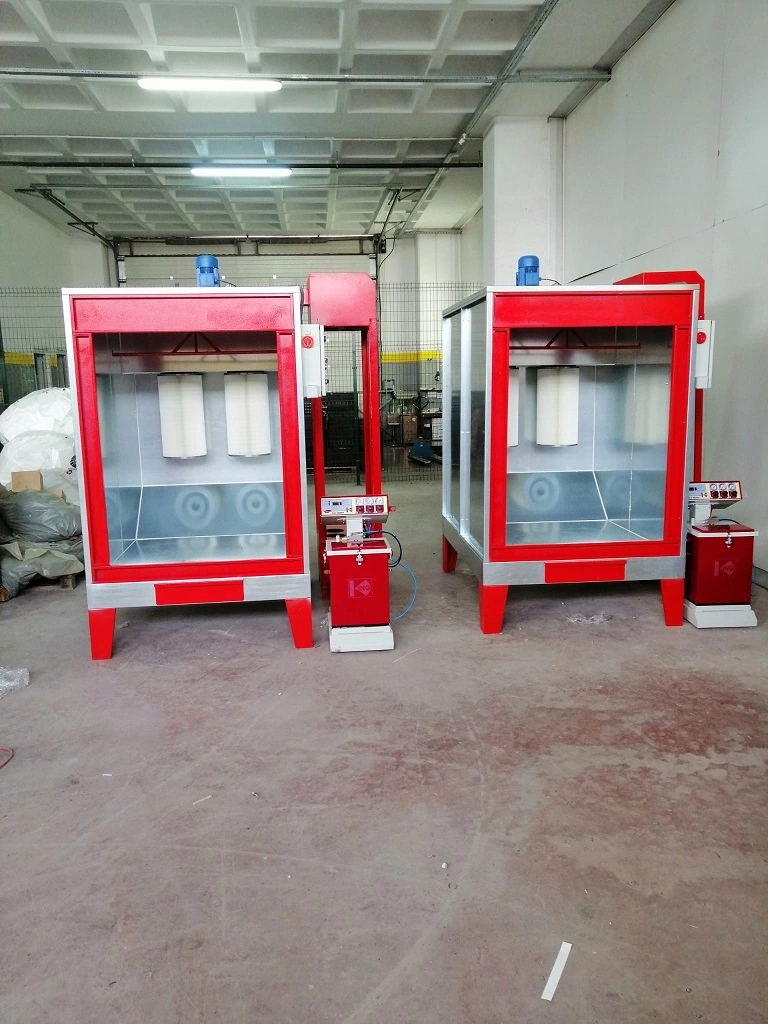
Pulverkabinen sind spezielle Räume oder Gehäuse, in denen der Pulverbeschichtungsprozess stattfindet. Sie spielen eine entscheidende Rolle bei der Gewährleistung einer sauberen und kontrollierten Umgebung für die Pulverbeschichtung.
Typen von Pulverkabinen:
- Offene Kabinen:
Diese Kabinen sind ideal für kleine bis mittlere Anwendungen. Sie bieten einen offenen Zugang für den Bediener, sind jedoch weniger effektiv bei der Kontrolle von Overspray. - Geschlossene Kabinen:
Bieten eine kontrollierte Umgebung und minimieren Overspray durch integrierte Luftführungssysteme. Geschlossene Kabinen sind in der Regel effizienter und sicherer. - Selbstreinigende Kabinen:
Ausgestattet mit automatischen Reinigungssystemen, die den Farbwechsel und die Wartung erleichtern. Diese Kabinen sind besonders nützlich in Anwendungen mit häufigem Farbwechsel.
Sicherheits- und Umweltaspekte: Pulverkabinen sind so konzipiert, dass sie die Sicherheit der Bediener gewährleisten und die Umweltbelastung minimieren. Dazu gehören Belüftungssysteme, Filter zur Partikelabscheidung und Schutzvorrichtungen, die den Kontakt mit dem Pulver verhindern.
Einbrennöfen
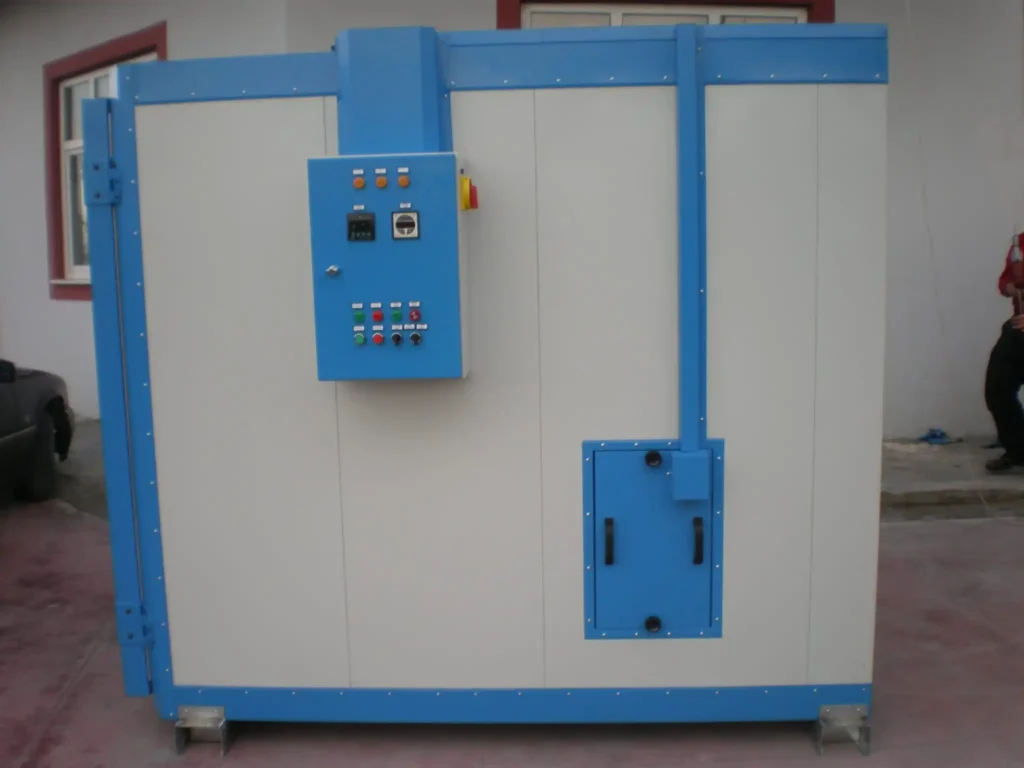
Der Einbrennofen ist ein unverzichtbarer Bestandteil des Pulverbeschichtungsprozesses, da er die notwendigen Temperaturen bereitstellt, um das aufgetragene Pulver zu einer harten, widerstandsfähigen Oberfläche zu verschmelzen.
Typen von Einbrennöfen:
- Chargenöfen:
Ideal für kleinere Produktionen oder variierende Chargengrößen. Diese Öfen sind flexibel und können unterschiedliche Teile gleichzeitig verarbeiten. - Durchlauföfen:
Entwickelt für kontinuierliche Produktionslinien, bei denen hohe Durchsatzraten erforderlich sind. Teile werden auf einem Förderband durch den Ofen transportiert, was eine konstante Verarbeitung ermöglicht.
Energieeffizienz und Temperatursteuerung: Moderne Einbrennöfen sind energieeffizient und bieten präzise Temperaturregelung, um gleichbleibende Beschichtungsqualität zu gewährleisten. Technologien wie Wärmerückgewinnungssysteme und fortschrittliche Isolierung tragen zur Reduzierung des Energieverbrauchs bei.
Pulvergeräte
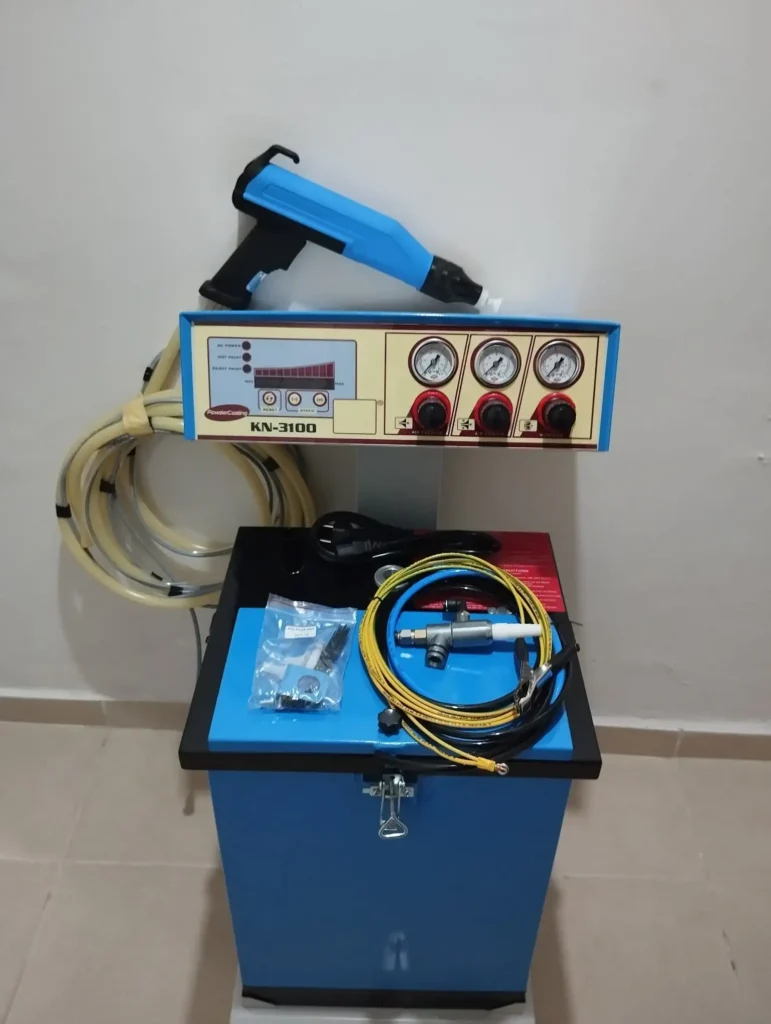
Pulvergeräte sind für die Anwendung der Pulverbeschichtung unerlässlich. Sie bestehen aus verschiedenen Komponenten, die zusammenarbeiten, um das Pulver gleichmäßig und effizient auf die Oberfläche des Werkstücks aufzubringen.
Arten von Pulvergeräten:
- Elektrostatische Sprühpistolen:
Verwenden Hochspannung, um Pulverpartikel elektrostatisch aufzuladen, was eine gleichmäßige Verteilung und Haftung auf dem Werkstück fördert. - Pulverförderer:
Transportieren das Pulver vom Vorratsbehälter zur Sprühpistole. Sie sind entscheidend für die Konsistenz und Effizienz des Beschichtungsprozesses.
Elektrostatik spielt eine zentrale Rolle bei der Pulverbeschichtung, da sie die Anziehungskraft zwischen den Pulverpartikeln und der Oberfläche erhöht und so eine gleichmäßige Beschichtung ermöglicht.
Auswahlkriterien für Pulvergeräte umfassen:
- Kompatibilität: Passend für die spezifischen Anforderungen der Anwendung.
- Flexibilität: Anpassungsfähigkeit an unterschiedliche Werkstückgrößen und -formen.
- Effizienz: Hohe Materialausnutzung und minimierter Pulververbrauch.
Automatische Pulverbeschichtungsanlagen
Automatische Pulverbeschichtungsanlagen bieten zahlreiche Vorteile, insbesondere in Bezug auf Effizienz und Konsistenz. Sie sind ideal für Großserienproduktionen und tragen zur Senkung der Betriebskosten bei.
Vorteile der Automatisierung:
- Erhöhte Produktivität: Automatische Systeme können kontinuierlich arbeiten und so die Produktionskapazität erheblich steigern.
- Gleichbleibende Qualität: Minimierung von Fehlern und Variabilität durch präzise Steuerung der Beschichtungsparameter.
- Kostenersparnis: Reduzierung der Arbeitskosten und des Materialverbrauchs durch optimierte Prozesse.
Komponenten und Funktionsweise:
- Fördersysteme: Transportieren Werkstücke automatisch durch den Beschichtungsprozess.
- Automatische Sprühpistolen: Verteilen das Pulver gleichmäßig auf den Werkstücken.
- Integrierte Steuerungssysteme: Überwachen und steuern alle Aspekte des Beschichtungsprozesses, einschließlich Temperatur, Sprühzeit und Pulvermenge.
Ersatzteile für Pulverbeschichtungsanlagen
Ersatzteile sind entscheidend für die Wartung und Langlebigkeit von Pulverbeschichtungsanlagen. Regelmäßige Wartung und der rechtzeitige Austausch von Verschleißteilen sind unerlässlich, um Ausfallzeiten zu minimieren und die Effizienz der Anlagen aufrechtzuerhalten.
Wichtige Ersatzteile und ihre Funktionen:
- Sprühdüsen: Stellen die gleichmäßige Verteilung des Pulvers sicher.
- Filter: Entfernen überschüssige Pulverpartikel aus der Kabinenluft.
- Förderbänder: Transportieren die Werkstücke durch den Beschichtungsprozess.
Wartung und Instandhaltung:
- Regelmäßige Inspektionen: Identifizieren potenzielle Probleme frühzeitig und ermöglichen rechtzeitige Reparaturen.
- Ersatzteilmanagement: Sicherstellung der Verfügbarkeit von Ersatzteilen zur Minimierung von Ausfallzeiten.
Zukunft der Pulverbeschichtungstechnologie
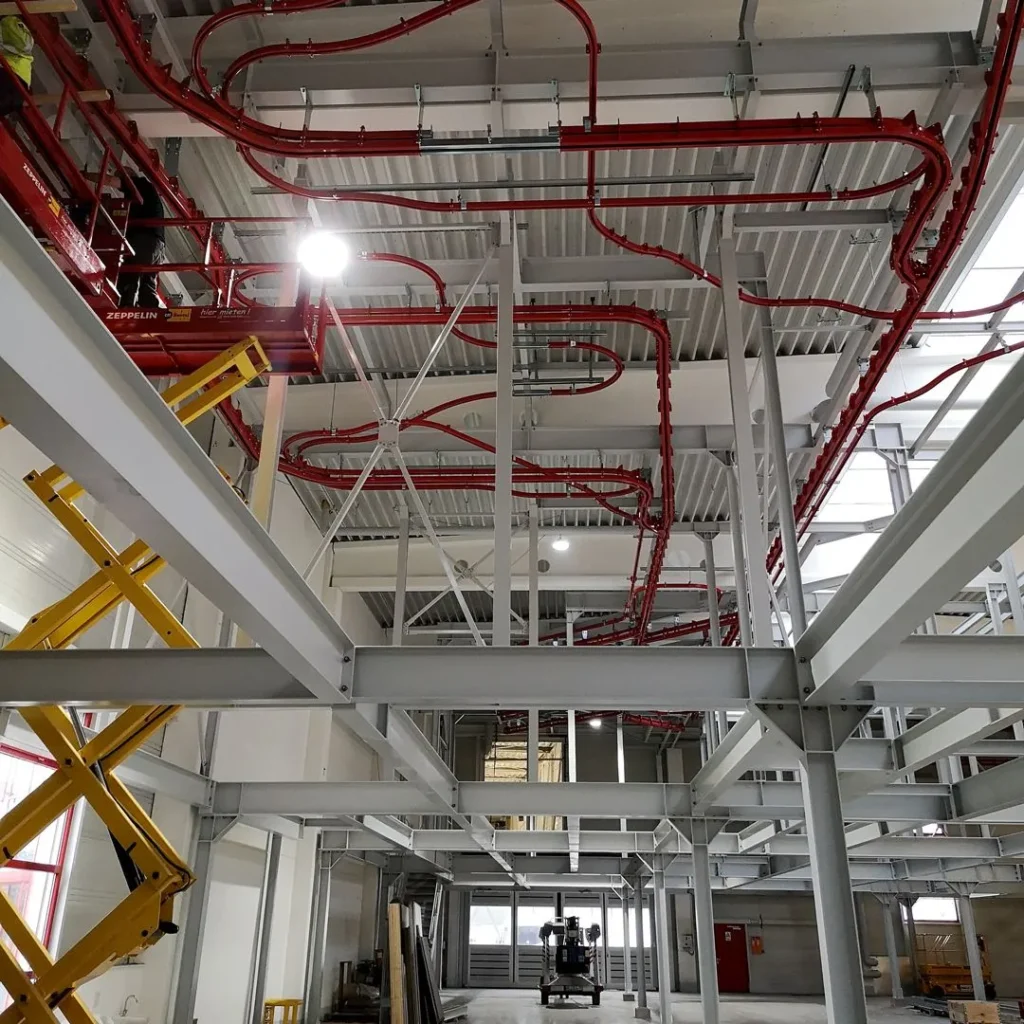
Die Pulverbeschichtungstechnologie entwickelt sich kontinuierlich weiter, um den steigenden Anforderungen der Industrie gerecht zu werden. Zu den wichtigsten Trends und Entwicklungen gehören:
- Nachhaltigkeit: Einsatz umweltfreundlicher Materialien und Verfahren zur Reduzierung des ökologischen Fußabdrucks.
- Fortschrittliche Materialien: Entwicklung neuer Pulverformeln, die verbesserte Eigenschaften wie Korrosionsbeständigkeit und UV-Stabilität bieten.
- Digitalisierung: Integration von IoT und datenbasierten Lösungen zur Optimierung des Beschichtungsprozesses und zur Verbesserung der Qualitätssicherung.
Fazit
Pulverbeschichtungsanlagen und ihre Komponenten sind ein wesentlicher Bestandteil moderner Produktionsprozesse. Sie bieten eine umweltfreundliche, effiziente und langlebige Lösung für die Oberflächenveredelung. Durch die ständige Weiterentwicklung der Technologie und den Einsatz von Automatisierung können Unternehmen ihre Effizienz steigern und gleichzeitig die Qualität ihrer Produkte sicherstellen.
Ich hoffe, dieser umfassende Überblick über Pulverbeschichtungsanlagen und verwandte Komponenten ist hilfreich. Wenn Sie weitere Informationen oder spezifische Details zu einem bestimmten Abschnitt wünschen, lassen Sie es mich bitte wissen!
Wie lange hält Pulverbeschichtung?
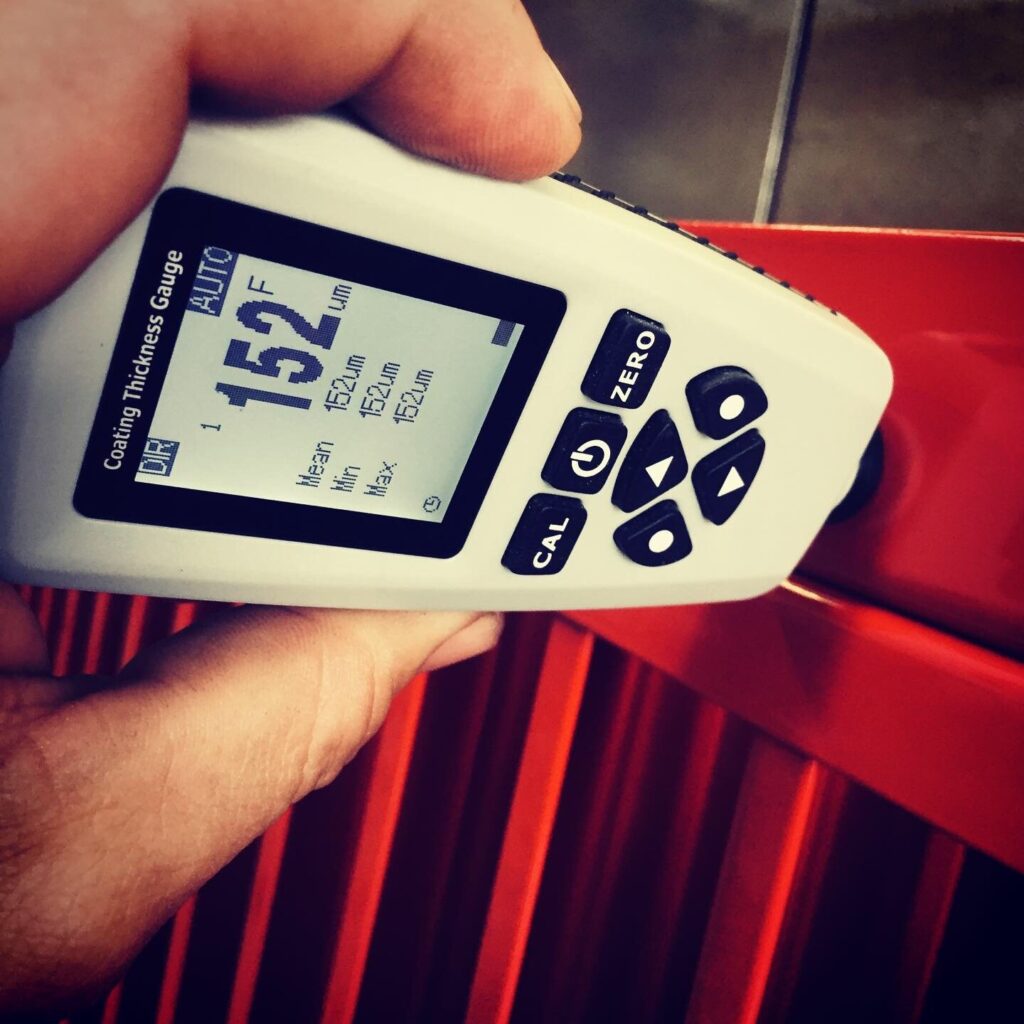
Die Haltbarkeit einer Pulverbeschichtung kann je nach Anwendung, Umgebung und Qualität der Beschichtung stark variieren. Hier sind einige Faktoren, die die Lebensdauer einer Pulverbeschichtung beeinflussen können:
Faktoren, die die Haltbarkeit beeinflussen:
- Qualität des Pulvers:
- Pulverformulierung: Hochwertige Pulverlacke bieten in der Regel eine längere Haltbarkeit und bessere Widerstandsfähigkeit gegen Umwelteinflüsse.
- UV-Stabilität: Speziell formulierte Pulverlacke mit UV-Schutz verlängern die Lebensdauer bei Anwendungen im Freien.
- Vorbereitung der Oberfläche:
- Reinigung: Eine gründliche Reinigung der Oberfläche vor der Beschichtung ist entscheidend, um eine gute Haftung des Pulvers zu gewährleisten.
- Vorbehandlung: Verfahren wie das Phosphatieren oder Sandstrahlen verbessern die Haftung und Korrosionsbeständigkeit.
- Bedingungen der Anwendung:
- Innen- vs. Außenanwendung: Pulverbeschichtungen im Innenbereich können Jahrzehnte halten, während Beschichtungen im Außenbereich stärker durch UV-Strahlung, Feuchtigkeit und Temperaturschwankungen beansprucht werden.
- Mechanische Belastung: Starke mechanische Belastungen oder Abnutzung können die Lebensdauer der Beschichtung verkürzen.
- Betriebsumgebung:
- Korrosive Umgebungen: In Industriegebieten oder maritimen Umgebungen kann die Lebensdauer aufgrund der erhöhten Korrosionsgefahr kürzer sein.
- Witterungseinflüsse: Regionen mit extremen Wetterbedingungen können die Lebensdauer der Pulverbeschichtung verkürzen.
- Beschichtungsdicke:
- Eine angemessene Schichtdicke ist wichtig, um eine gleichmäßige Abdeckung und ausreichenden Schutz zu gewährleisten.
Typische Lebensdauer
- Innenanwendungen:
Pulverbeschichtungen, die in Innenbereichen aufgebracht werden, können oft 15-20 Jahre oder länger halten, da sie weniger extremen Bedingungen ausgesetzt sind. - Außenanwendungen:
Bei Außenanwendungen hängt die Lebensdauer stark von den Umweltbedingungen ab, kann jedoch typischerweise zwischen 5 und 10 Jahren liegen. Hochwertige Pulverbeschichtungen, die speziell für den Außenbereich entwickelt wurden, können bis zu 15 Jahre oder länger halten, wenn sie regelmäßig gewartet werden. - Industrieanwendungen:
In industriellen Anwendungen, die häufig aggressiven Chemikalien oder starker mechanischer Beanspruchung ausgesetzt sind, kann die Lebensdauer kürzer sein und erfordert häufigere Inspektionen und Wartungen.
Verlängerung der Haltbarkeit
Um die Lebensdauer der Pulverbeschichtung zu maximieren, sind folgende Maßnahmen empfehlenswert:
- Regelmäßige Inspektion und Wartung: Frühe Erkennung von Schäden und rechtzeitige Reparaturen können die Haltbarkeit erheblich verlängern.
- Vermeidung von physikalischen Schäden: Sorgfältiger Umgang mit beschichteten Oberflächen reduziert das Risiko von Kratzern und Abplatzungen.
- Schutz vor chemischen Einflüssen: Vermeidung von Kontakt mit aggressiven Chemikalien und Reinigungsmitteln, die die Beschichtung angreifen könnten.
Fazit
Die Pulverbeschichtung ist eine langlebige und widerstandsfähige Methode zur Oberflächenveredelung, die bei richtiger Anwendung und Wartung viele Jahre halten kann. Die tatsächliche Lebensdauer hängt jedoch von zahlreichen Faktoren ab, einschließlich der Qualität des Pulvers, der Vorbereitung der Oberfläche und den Umgebungsbedingungen, denen die beschichteten Teile ausgesetzt sind.
Wartungstipps für Anlagen
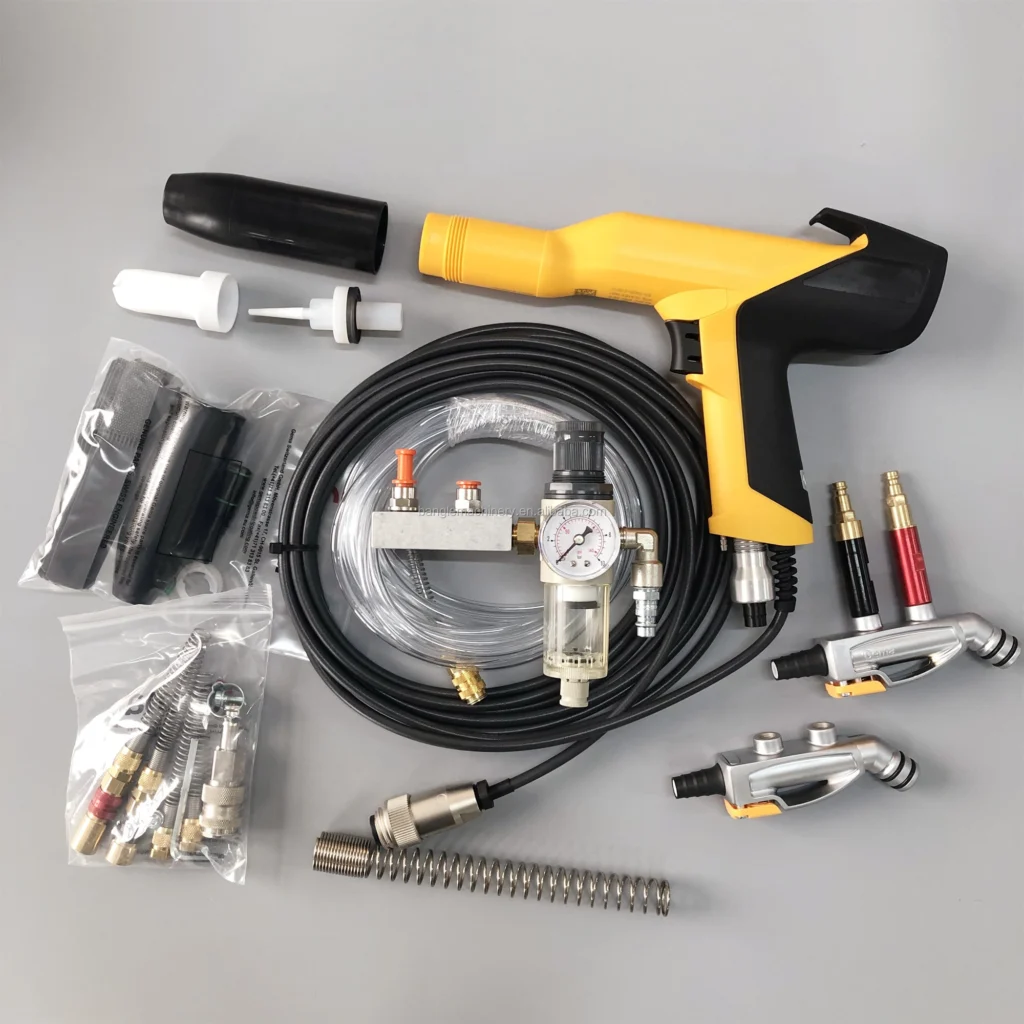
Um die Langlebigkeit und Effizienz von Pulverbeschichtungsanlagen zu gewährleisten, ist eine regelmäßige Wartung entscheidend. Hier sind einige Wartungstipps, die Ihnen helfen, die Leistung Ihrer Anlagen zu maximieren und Ausfallzeiten zu minimieren:
1. Allgemeine Inspektion
- Regelmäßige Überprüfungen: Führen Sie wöchentliche oder monatliche Inspektionen der gesamten Anlage durch, um sicherzustellen, dass alle Komponenten ordnungsgemäß funktionieren.
- Sichtprüfung: Überprüfen Sie auf sichtbare Abnutzung, Schäden oder lose Teile, die die Funktion beeinträchtigen könnten.
2. Pulverkabinen
- Filterwartung:
- Reinigung oder Austausch: Reinigen oder ersetzen Sie die Filter regelmäßig, um eine effiziente Luftführung und Partikelabscheidung zu gewährleisten.
- Filtertypen beachten: Verwenden Sie immer die vom Hersteller empfohlenen Filtertypen.
- Kabinenreinigung:
- Regelmäßige Reinigung: Halten Sie die Kabinenwände und -böden sauber, um Ansammlungen von überschüssigem Pulver zu vermeiden.
- Staubabsaugung: Stellen Sie sicher, dass die Absauganlage regelmäßig geleert und gewartet wird, um eine optimale Funktion zu gewährleisten.
3. Einbrennöfen
- Temperaturüberwachung:
- Regelmäßige Kalibrierung: Überprüfen Sie regelmäßig die Kalibrierung der Temperatursteuerung, um eine gleichbleibende Beschichtungsqualität sicherzustellen.
- Thermoelemente prüfen: Überprüfen Sie die Thermoelemente auf Genauigkeit und Funktionstüchtigkeit.
- Ofenreinigung:
- Innenreinigung: Entfernen Sie regelmäßig Rückstände und Ablagerungen im Inneren des Ofens, um die Effizienz zu erhalten.
- Dichtungen überprüfen: Überprüfen Sie die Dichtungen an Türen und Durchgängen auf Abnutzung und tauschen Sie sie bei Bedarf aus.
4. Pulvergeräte
- Sprühpistolenwartung:
- Düsenreinigung: Reinigen Sie die Düsen regelmäßig, um Verstopfungen und ungleichmäßige Sprühmuster zu vermeiden.
- Ersatzteile prüfen: Halten Sie Ersatzdüsen und andere Verschleißteile bereit, um Ausfallzeiten zu minimieren.
- Pulverförderer:
- Reinigungsintervalle: Reinigen Sie die Pulverförderer, um Blockaden zu verhindern und eine gleichmäßige Pulverzufuhr zu gewährleisten.
- Antriebssysteme warten: Überprüfen Sie regelmäßig die Antriebe und Lager auf Verschleiß und tauschen Sie sie bei Bedarf aus.
5. Fördersysteme
- Kettenspannung und Schmierung:
- Spannung überprüfen: Kontrollieren Sie die Spannung der Förderketten und passen Sie sie bei Bedarf an, um einen reibungslosen Betrieb zu gewährleisten.
- Schmierung: Schmieren Sie alle beweglichen Teile regelmäßig, um Verschleiß zu minimieren.
- Lagerwartung:
- Überprüfung der Lager: Überprüfen Sie die Lager auf Abnutzung und tauschen Sie sie bei Bedarf aus.
- Schmiermittel verwenden: Verwenden Sie die vom Hersteller empfohlenen Schmiermittel, um die Lebensdauer der Lager zu verlängern.
6. Automatisierte Systeme
- Steuerungssysteme:
- Software-Updates: Halten Sie die Software der Steuerungssysteme auf dem neuesten Stand, um Effizienz und Sicherheit zu gewährleisten.
- Fehlerprotokollierung: Überwachen Sie Fehlerprotokolle, um potenzielle Probleme frühzeitig zu erkennen.
- Sensoren und Aktoren:
- Funktionsprüfung: Überprüfen Sie regelmäßig die Sensoren und Aktoren auf ihre Funktionsfähigkeit und ersetzen Sie defekte Teile.
- Kalibrierung: Führen Sie regelmäßige Kalibrierungen durch, um die Genauigkeit der automatisierten Systeme zu gewährleisten.
7. Ersatzteile und Lagerhaltung
- Ersatzteilmanagement:
- Bestandskontrolle: Führen Sie eine genaue Bestandskontrolle der Ersatzteile, um Ausfallzeiten durch fehlende Teile zu vermeiden.
- Qualität der Ersatzteile: Verwenden Sie stets hochwertige Originalersatzteile, um die Funktionalität der Anlagen zu gewährleisten.
8. Schulung des Personals
- Regelmäßige Schulungen: Schulen Sie Ihr Personal regelmäßig in der Bedienung und Wartung der Anlagen, um Bedienfehler zu vermeiden und die Sicherheit zu erhöhen.
- Notfallverfahren: Stellen Sie sicher, dass alle Mitarbeiter mit den Notfallverfahren vertraut sind, um im Falle eines Ausfalls schnell reagieren zu können.
9. Dokumentation
- Wartungsprotokolle: Führen Sie detaillierte Wartungsprotokolle, um den Wartungsverlauf und alle durchgeführten Arbeiten zu dokumentieren.
- Checklisten verwenden: Nutzen Sie Wartungschecklisten, um sicherzustellen, dass alle erforderlichen Maßnahmen regelmäßig durchgeführt werden.
Fazit
Durch die Einhaltung dieser Wartungstipps können Sie die Effizienz und Lebensdauer Ihrer Pulverbeschichtungsanlagen maximieren. Eine gut gewartete Anlage führt zu einer höheren Produktqualität, weniger Ausfallzeiten und einer längeren Lebensdauer der Geräte. Regelmäßige Wartung ist eine Investition, die sich durch verbesserte Leistung und geringere Betriebskosten auszahlt.
Automatisierungsoptionen
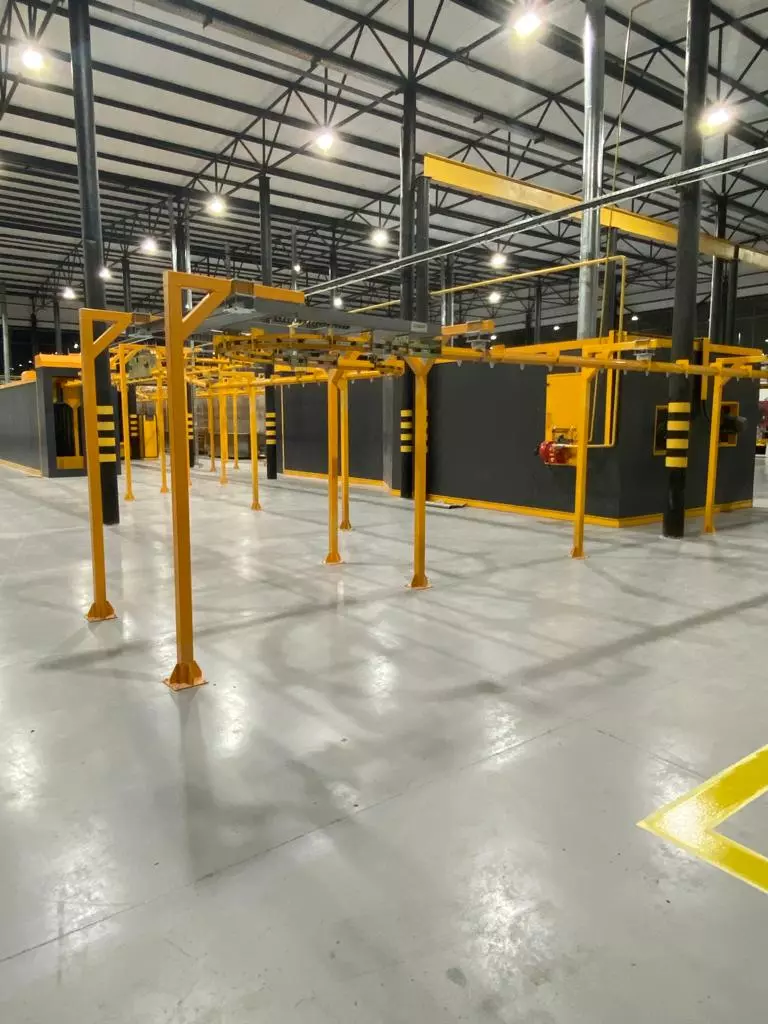
Automatisierungsoptionen in der Pulverbeschichtung bieten zahlreiche Vorteile, darunter erhöhte Effizienz, gleichbleibende Qualität und reduzierte Betriebskosten. Im Folgenden werden verschiedene Automatisierungsoptionen erläutert, die in modernen Pulverbeschichtungsanlagen eingesetzt werden können:
1. Automatische Sprühsysteme
Automatische Sprühsysteme sind eine wesentliche Komponente für die Automatisierung der Pulverbeschichtung und bieten präzise und gleichmäßige Beschichtungen. Sie bestehen aus mehreren automatisierten Sprühpistolen, die auf robotergesteuerten Armen montiert sind.
- Robotergestützte Sprühpistolen:
Diese Pistolen sind an Roboterarmen befestigt, die programmierbar sind, um komplexe Bewegungsmuster auszuführen und die Sprühwinkel für unterschiedliche Werkstückgeometrien zu optimieren. - Pulvermengensteuerung:
Automatisierte Systeme ermöglichen die genaue Steuerung der Pulvermengen, was zu einer gleichmäßigen Schichtdicke und weniger Abfall führt. - Adaptive Technologie:
Moderne Systeme nutzen Sensoren, um die Werkstückgeometrie in Echtzeit zu erfassen und die Sprühmuster entsprechend anzupassen.
2. Fördersysteme
Automatisierte Fördersysteme transportieren die Werkstücke durch die verschiedenen Phasen des Beschichtungsprozesses und tragen dazu bei, den Durchsatz zu erhöhen.
- Overhead-Fördersysteme:
Diese Systeme transportieren die Teile über Kopf durch die Kabinen und Öfen, was den Bodenraum frei hält und die Effizienz erhöht. - Ketten- und Schienensysteme:
Förderbänder und Schienensysteme bieten Flexibilität bei der Gestaltung der Produktionslinie und können an unterschiedliche Anforderungen angepasst werden. - Variable Geschwindigkeit:
Einige Fördersysteme ermöglichen die Anpassung der Geschwindigkeit je nach Werkstückgröße und Prozessanforderungen.
3. Einbrennöfen mit Automatisierung
Einbrennöfen können durch Automatisierung effizienter und präziser arbeiten, was die Qualität der Beschichtung verbessert.
- Automatisierte Temperaturregelung:
Intelligente Steuerungssysteme passen die Ofentemperatur in Echtzeit an, um die optimale Aushärtung der Pulverbeschichtung zu gewährleisten. - Zeitschaltuhren und Sensoren:
Integrierte Timer und Sensoren helfen dabei, den Aushärtungsprozess genau zu überwachen und die Energieeffizienz zu maximieren. - Automatische Türsteuerung:
Automatische Türen öffnen und schließen sich synchron mit dem Ein- und Ausgang der Werkstücke, um den Wärmeverlust zu minimieren.
4. Qualitätskontrollsysteme
Automatisierte Qualitätskontrollsysteme sorgen dafür, dass die Beschichtungen den festgelegten Standards entsprechen und verringern den Bedarf an manueller Inspektion.
- Visuelle Inspektionssysteme:
Kameras und Bildverarbeitungstechnologien prüfen die Beschichtungsqualität und identifizieren sofort Fehler oder Unregelmäßigkeiten. - Schichtdickenmessung:
Berührungslose Messsysteme können die Dicke der Pulverbeschichtung präzise messen und Daten zur weiteren Analyse bereitstellen. - Echtzeit-Datenanalyse:
Datenerfassungs- und Analysesysteme ermöglichen die Überwachung des gesamten Prozesses und helfen bei der Identifizierung von Optimierungspotenzialen.
5. Software-Integration
Softwarelösungen spielen eine entscheidende Rolle bei der Automatisierung, indem sie verschiedene Systeme integrieren und den Betrieb effizienter gestalten.
- Leitsysteme (SCADA):
Supervisory Control and Data Acquisition (SCADA) Systeme bieten eine zentrale Steuerung und Überwachung aller Anlagenkomponenten. - IoT-Integration:
Internet of Things (IoT) Technologien ermöglichen die Vernetzung der Geräte und die Fernüberwachung sowie -steuerung der Prozesse. - Produktionsmanagement-Software:
Diese Softwarelösungen helfen bei der Planung und Verwaltung von Produktionsabläufen, indem sie Daten aus verschiedenen Quellen konsolidieren.
6. Automatisierte Farbwechsel
Für Betriebe, die häufige Farbwechsel durchführen müssen, bieten automatisierte Farbwechselsysteme erhebliche Vorteile.
- Schneller Farbwechsel:
Automatisierte Systeme reduzieren die Zeit, die für den Farbwechsel benötigt wird, was die Produktionsausfallzeiten minimiert. - Minimierung von Pulverabfall:
Durch den Einsatz von selbstreinigenden Sprühpistolen und Kabinen wird der Pulververbrauch optimiert.
7. Wartungsautomatisierung
Auch die Wartung von Anlagen kann automatisiert werden, um die Betriebszeiten zu maximieren und unvorhergesehene Ausfälle zu reduzieren.
- Vorausschauende Wartung:
Sensoren überwachen den Zustand der Anlagenkomponenten in Echtzeit und prognostizieren Wartungsbedarf, bevor Probleme auftreten. - Automatisierte Fehlerdiagnose:
Diagnose-Tools identifizieren Probleme und bieten Lösungsvorschläge, die die Wartungseffizienz erhöhen.
Vorteile der Automatisierung in der Pulverbeschichtung
- Erhöhte Produktivität:
Automatisierte Systeme ermöglichen eine höhere Produktionsrate bei gleichzeitig konsistenter Qualität. - Geringere Betriebskosten:
Durch die Optimierung des Materialverbrauchs und die Reduzierung des Arbeitsaufwands senken Automatisierungssysteme die Betriebskosten. - Verbesserte Qualität:
Gleichbleibende Beschichtungsqualität und reduzierte Fehlerraten durch präzise Steuerung und Überwachung. - Umweltfreundlichkeit:
Automatisierung reduziert den Pulverabfall und verbessert die Energieeffizienz der Anlagen.
Fazit
Automatisierungsoptionen in der Pulverbeschichtung bieten eine Vielzahl von Vorteilen und sind entscheidend für die Steigerung der Effizienz und Qualität in der Produktion. Die Integration von Robotik, fortschrittlicher Software und intelligenter Steuerung ermöglicht es Unternehmen, wettbewerbsfähig zu bleiben und gleichzeitig die Umweltbelastung zu reduzieren. Die Entscheidung für die richtige Kombination von Automatisierungstechnologien hängt von den spezifischen Anforderungen und Zielen des Unternehmens ab.
Automatisierungsvorteile

Automatisierung in der Pulverbeschichtungsindustrie bietet zahlreiche Vorteile, die sowohl die Effizienz als auch die Qualität der Produktion steigern können. Hier sind die wichtigsten Vorteile der Automatisierung erklärt:
1. Erhöhte Effizienz
- Höhere Produktionsraten:
Automatisierte Systeme können kontinuierlich ohne Unterbrechungen arbeiten, was zu höheren Durchsatzraten führt. Dies bedeutet, dass mehr Teile in kürzerer Zeit beschichtet werden können, was die Gesamtproduktivität steigert. - Schnellere Zykluszeiten:
Automatisierung reduziert die Bearbeitungszeit pro Werkstück erheblich, da Maschinen schneller und präziser arbeiten können als Menschen. - Minimierte Stillstandszeiten:
Automatisierte Wartung und vorausschauende Diagnose minimieren ungeplante Ausfallzeiten, was die Verfügbarkeit der Anlage erhöht.
2. Gleichbleibende Qualität
- Präzise Beschichtungsanwendung:
Automatisierte Sprühsysteme sorgen für eine gleichmäßige Schichtdicke und reduzieren menschliche Fehler, die zu Qualitätsabweichungen führen können. - Wiederholgenauigkeit:
Automatisierte Systeme wiederholen dieselben Bewegungen und Prozesse mit hoher Genauigkeit, was zu konsistenter Produktqualität führt, unabhängig von der Produktionsmenge. - Echtzeit-Qualitätskontrolle:
Durch den Einsatz von Sensoren und Kameras können automatisierte Systeme kontinuierlich die Qualität der Beschichtung überwachen und sofort Anpassungen vornehmen.
3. Reduzierte Betriebskosten
- Materialeinsparungen:
Automatisierung optimiert den Einsatz von Pulvermaterialien, wodurch Abfall reduziert und die Materialnutzung verbessert wird. - Geringere Arbeitskosten:
Der Bedarf an manueller Arbeit wird verringert, was die Personalkosten senkt. Mitarbeiter können in anderen Bereichen eingesetzt werden, wo menschliches Urteilsvermögen und Kreativität erforderlich sind. - Energieeffizienz:
Automatisierte Systeme sind oft energieeffizienter, da sie optimierte Prozesse und Technologien verwenden, um den Energieverbrauch zu minimieren.
4. Verbesserte Sicherheit
- Reduzierte Exposition gegenüber Gefahrenstoffen:
Automatisierung minimiert den direkten Kontakt der Mitarbeiter mit potenziell gefährlichen Chemikalien und Pulvern, was das Risiko von Gesundheitsproblemen reduziert. - Sicherheitsüberwachung:
Automatisierte Anlagen sind häufig mit Sicherheitssensoren ausgestattet, die Unfälle verhindern und im Notfall schnelle Reaktionen ermöglichen. - Ergonomische Vorteile:
Mitarbeiter müssen weniger körperlich anspruchsvolle Aufgaben erledigen, was das Risiko von arbeitsbedingten Verletzungen verringert.
5. Flexibilität und Anpassungsfähigkeit
- Schnelle Anpassung an Produktänderungen:
Automatisierte Systeme können schnell neu programmiert werden, um auf Änderungen im Produktdesign oder der Produktion umzustellen, was die Flexibilität erhöht. - Einfache Integration neuer Technologien:
Durch modulare Designs können neue Technologien oder Prozesse problemlos in bestehende Systeme integriert werden. - Vielfältige Anwendungsmöglichkeiten:
Automatisierung kann an eine Vielzahl von Werkstückgrößen, -formen und -materialien angepasst werden, was die Vielseitigkeit der Produktion erhöht.
6. Nachhaltigkeit und Umweltfreundlichkeit
- Reduzierung von Abfall und Emissionen:
Automatisierte Systeme optimieren den Materialverbrauch und reduzieren den Überspray, was zu weniger Abfall und geringeren Emissionen führt. - Ressourceneffizienz:
Durch die optimale Nutzung von Energie und Materialien tragen automatisierte Systeme zu nachhaltigeren Produktionsprozessen bei. - Verbesserte Umweltbilanz:
Unternehmen können ihre Umweltziele leichter erreichen und ihre ökologische Verantwortung wahrnehmen.
7. Daten- und Prozessoptimierung
- Datengesteuerte Entscheidungsfindung:
Automatisierte Systeme sammeln kontinuierlich Daten, die zur Analyse und Optimierung der Produktionsprozesse verwendet werden können. - Prozessoptimierung durch IoT:
Internet of Things (IoT) Technologien ermöglichen die Echtzeitüberwachung und -steuerung von Prozessen, was die Effizienz und Transparenz erhöht. - Vorausschauende Wartung:
Durch die Analyse von Maschinendaten können Probleme frühzeitig erkannt und behoben werden, bevor sie zu größeren Ausfällen führen.
Fazit
Die Automatisierung in der Pulverbeschichtung bietet zahlreiche Vorteile, die sowohl die Effizienz als auch die Qualität der Produktion erheblich steigern. Durch den Einsatz modernster Technologien können Unternehmen ihre Betriebskosten senken, die Produktsicherheit erhöhen und gleichzeitig ihre Umweltbilanz verbessern. Die Investition in Automatisierungslösungen zahlt sich langfristig durch höhere Produktivität, verbesserte Qualität und größere Flexibilität aus. Unternehmen, die Automatisierungstechnologien integrieren, positionieren sich besser im Wettbewerb und sind in der Lage, schneller auf Marktveränderungen zu reagieren.
Beispiele für Automatisierung

Hier sind einige konkrete Beispiele für Automatisierung in der Pulverbeschichtungsindustrie, die verdeutlichen, wie moderne Technologien den Beschichtungsprozess optimieren und verbessern können:
1. Robotergesteuerte Sprühapplikationen
- Automatisierte Spritzroboter:
Diese Roboterarme sind mit elektrostatischen Sprühpistolen ausgestattet und können komplexe Bewegungsmuster programmieren, um Teile unterschiedlicher Formen und Größen effizient zu beschichten. Durch die Robotersteuerung wird eine gleichmäßige Schichtdicke erreicht, und es gibt weniger Overspray.Beispiel: In der Automobilindustrie werden Karosserieteile oft mit robotergestützten Sprühsystemen beschichtet, um eine gleichmäßige und hochwertige Oberfläche zu gewährleisten. Ein Unternehmen wie ABB Robotics bietet Lösungen, die auf die spezifischen Anforderungen der Automobilindustrie zugeschnitten sind.
2. Automatische Fördersysteme
- Overhead-Kettenförderer:
Diese Systeme transportieren die Teile durch verschiedene Prozessschritte wie Reinigung, Beschichtung und Aushärtung. Sie ermöglichen einen kontinuierlichen Produktionsfluss und minimieren manuelle Eingriffe.Beispiel: Bei der Herstellung von Metallmöbeln werden Teile oft auf Förderbändern bewegt, die sie durch alle Beschichtungsphasen führen. Unternehmen wie Nordson bieten komplexe Fördersysteme an, die an verschiedene Produktionslayouts angepasst werden können.
3. Automatisierte Farbwechselsysteme
- Schnellwechselkabinen:
Diese Kabinen sind darauf ausgelegt, den Farbwechselprozess zu beschleunigen. Sie verfügen über automatische Reinigungszyklen und programmierbare Steuerungen, die den Farbwechsel effizienter machen.Beispiel: In der Fahrradindustrie, wo häufig Farbvarianten angeboten werden, nutzen Hersteller automatisierte Systeme, um den Farbwechsel schnell durchzuführen, ohne die Produktion zu verlangsamen. Systeme von Gema Switzerland bieten automatische Farbwechseltechnologien, die in der Branche weit verbreitet sind.
4. Intelligente Einbrennöfen
- Automatisierte Temperatur- und Zeitsteuerung:
Einbrennöfen sind mit Sensoren ausgestattet, die die Temperatur und den Durchsatz in Echtzeit überwachen und anpassen, um die optimale Aushärtung der Beschichtung zu gewährleisten.Beispiel: In der Elektronikindustrie, wo präzise Temperaturkontrollen entscheidend sind, verwenden Hersteller automatisierte Öfen, um die empfindlichen Komponenten richtig zu behandeln. Unternehmen wie Despatch Industries bieten Öfen an, die auf solche spezifischen Anforderungen abgestimmt sind.
5. Echtzeit-Qualitätskontrollsysteme
- Vision-Systeme für die Inspektion:
Kameras und Bildverarbeitungstechnologien erfassen die Beschichtungsqualität in Echtzeit, erkennen Fehler und ermöglichen sofortige Korrekturmaßnahmen.Beispiel: In der Luftfahrtindustrie, wo höchste Qualitätsstandards gelten, werden Vision-Systeme eingesetzt, um die Beschichtungen auf Flugzeugteilen zu überprüfen. Anbieter wie Cognex bieten fortschrittliche Bildverarbeitungslösungen an, die in diesen Anwendungen genutzt werden.
6. Datenanalyse und IoT-Integration
- IoT-gestützte Prozessüberwachung:
Sensoren an verschiedenen Stellen der Produktionslinie sammeln Daten, die zur Optimierung des gesamten Beschichtungsprozesses genutzt werden können. IoT-Plattformen ermöglichen eine zentrale Überwachung und Anpassung der Systeme in Echtzeit.Beispiel: Ein Hersteller von landwirtschaftlichen Maschinen nutzt IoT-Daten, um die Effizienz der Pulverbeschichtungsanlage zu verbessern und Wartungszyklen zu optimieren. Unternehmen wie Siemens bieten umfassende IoT-Lösungen an, die solche Anwendungen unterstützen.
7. Vorausschauende Wartung
- Condition Monitoring:
Automatisierte Überwachungssysteme analysieren kontinuierlich den Zustand von Anlagenkomponenten und prognostizieren Wartungsbedarf, bevor Ausfälle auftreten.Beispiel: Ein Hersteller von Haushaltsgeräten implementiert vorausschauende Wartung, um die Lebensdauer seiner Beschichtungsanlagen zu verlängern und die Verfügbarkeit zu maximieren. Lösungen von GE Digital bieten solche Condition-Monitoring-Tools an.
8. Automatisierte Reinigungssysteme
- Selbstreinigende Kabinen:
Diese Kabinen verfügen über automatische Reinigungszyklen, die das Entfernen von Pulverrückständen und die Vorbereitung für den nächsten Durchgang erleichtern.Beispiel: In der Herstellung von Baukomponenten, die unterschiedliche Beschichtungen erfordern, helfen selbstreinigende Systeme, die Wechselzeiten zwischen den verschiedenen Pulverlacken zu verkürzen. Systeme von Wagner bieten effiziente Reinigungsoptionen, die in solchen Anwendungen zum Einsatz kommen.
Fazit
Automatisierung in der Pulverbeschichtungsindustrie bietet vielfältige Möglichkeiten, die Produktion zu optimieren und gleichzeitig die Qualität zu steigern. Durch den Einsatz von robotergesteuerten Sprühsystemen, automatisierten Fördersystemen, intelligenten Einbrennöfen und fortschrittlichen Überwachungs- und Wartungstechnologien können Unternehmen ihre Effizienz erhöhen und ihre Wettbewerbsfähigkeit verbessern. Die Investition in Automatisierungstechnologien ermöglicht es Unternehmen, sich schnell an Marktveränderungen anzupassen und gleichzeitig ihre Produktionskosten zu senken.
Komponenten einer Komplette Pulverbeschichtungsanlage
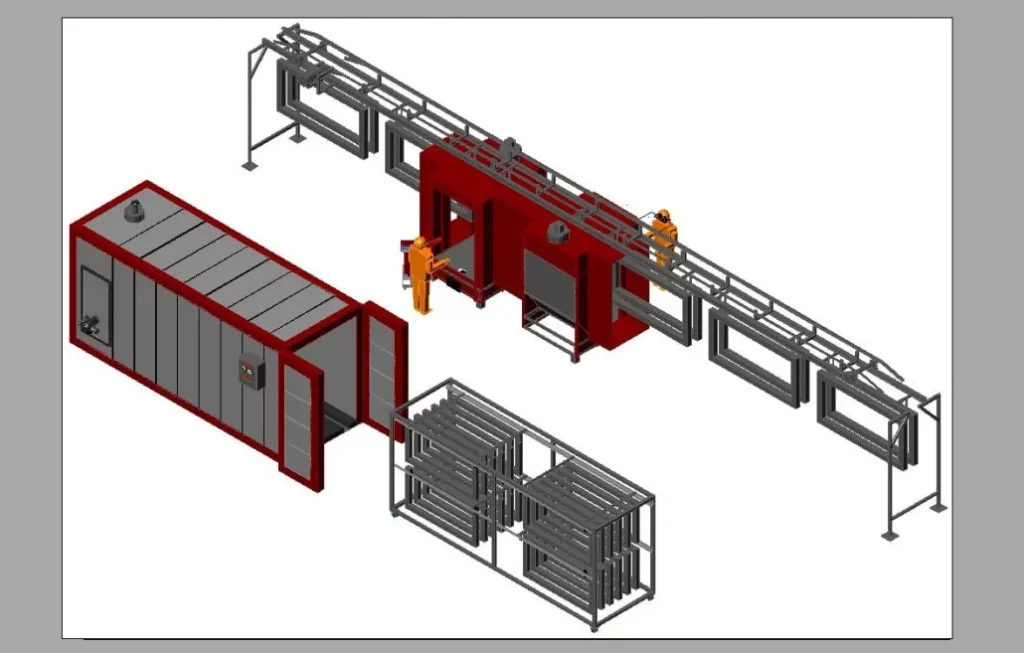
Eine komplette Pulverbeschichtungsanlage besteht aus mehreren wesentlichen Komponenten, die zusammenarbeiten, um eine effiziente und qualitativ hochwertige Beschichtung von Werkstücken zu gewährleisten. Hier sind die Hauptkomponenten einer solchen Anlage und ihre Funktionen:
1. Vorbehandlungssystem
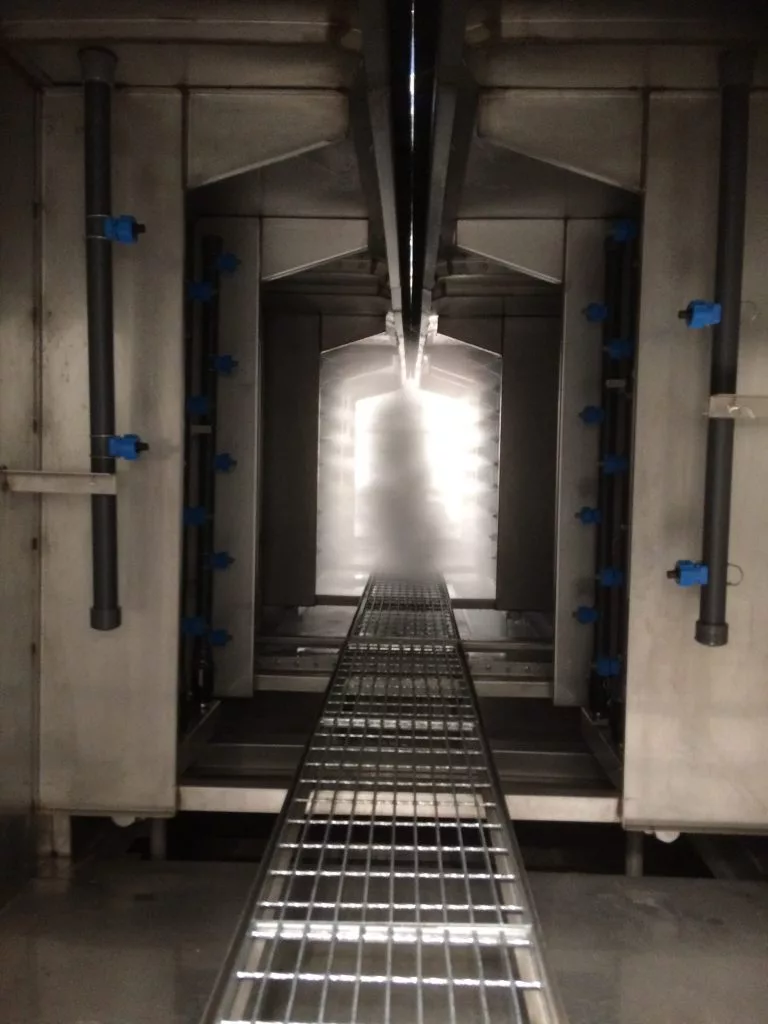
Die Vorbehandlung ist ein entscheidender Schritt, um sicherzustellen, dass die Oberfläche des Werkstücks sauber und bereit für die Beschichtung ist. Die Vorbehandlung verbessert die Haftung der Pulverbeschichtung und erhöht die Korrosionsbeständigkeit.
- Reinigungsstationen: Entfernen Öl, Fett, Staub und andere Verunreinigungen von der Oberfläche des Werkstücks.
- Phosphatier- oder Chromatierstationen: Bilden eine Schutzschicht, die die Haftung verbessert und die Korrosionsbeständigkeit erhöht.
- Spül- und Trocknungsstationen: Stellen sicher, dass das Werkstück frei von chemischen Rückständen und trocken ist, bevor es zur Beschichtung weitergeleitet wird.
2. Pulverkabinen
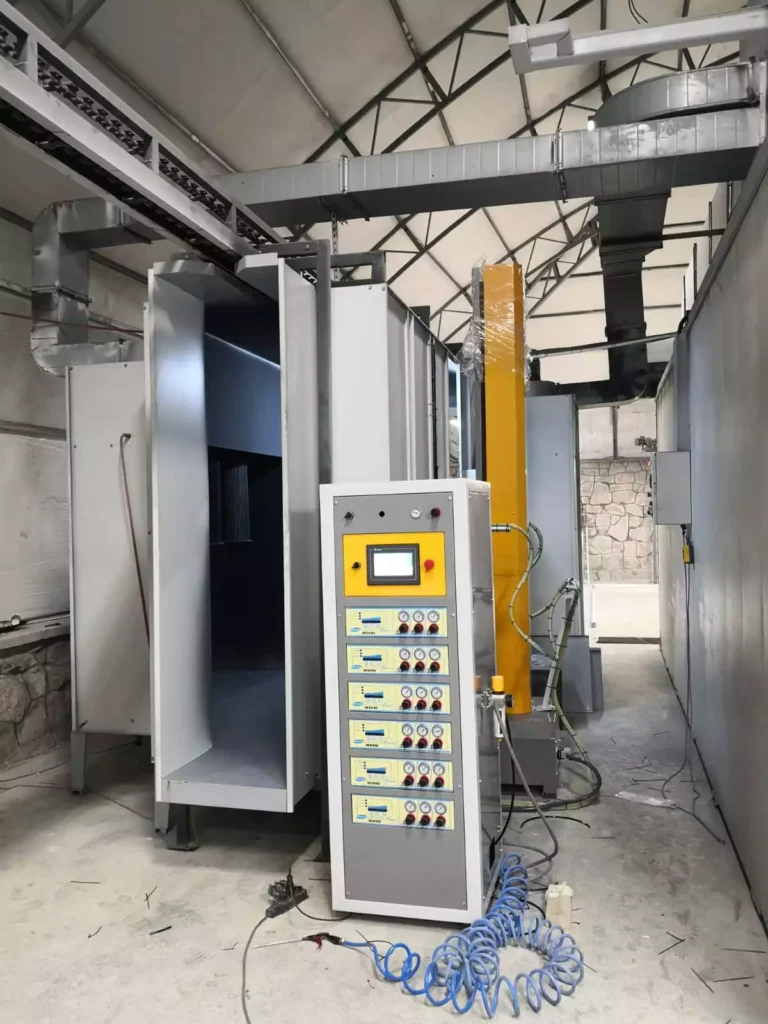
Die Pulverkabine ist der Bereich, in dem das Pulver elektrostatisch auf die Werkstücke aufgetragen wird. Sie ist so konzipiert, dass sie eine saubere und kontrollierte Umgebung bietet, um überschüssiges Pulver effizient zurückzugewinnen.
- Offene Kabinen: Geeignet für kleinere, manuelle Anwendungen, wo der Bediener direkten Zugang benötigt.
- Geschlossene Kabinen: Bieten eine kontrollierte Umgebung und sind effizienter bei der Kontrolle und Rückgewinnung von Overspray.
- Selbstreinigende Kabinen: Diese Kabinen verfügen über automatische Reinigungssysteme, die den Farbwechsel und die Wartung erleichtern.
3. Pulverauftragsgeräte

Diese Geräte sind für die eigentliche Anwendung des Pulvers auf die Werkstücke verantwortlich und bestehen aus verschiedenen Komponenten, die den Pulverauftrag optimieren.
- Elektrostatische Sprühpistolen: Laden die Pulverpartikel elektrostatisch auf, damit sie gleichmäßig auf der Werkstückoberfläche haften.
- Pulverförderer: Transportieren das Pulver von den Vorratsbehältern zur Sprühpistole und sorgen für eine gleichmäßige Pulverzufuhr.
- Steuerungseinheiten: Erlauben die Anpassung der Auftragsparameter wie Spannung, Pulverfluss und Sprühzeit.
4. Fördersysteme

Fördersysteme transportieren die Werkstücke durch die verschiedenen Stationen der Beschichtungsanlage, von der Vorbehandlung bis zur Aushärtung.
- Kettenförderer: Bieten kontinuierliche Bewegung und sind ideal für die Massenproduktion.
- Schienen- und Rollensysteme: Ermöglichen Flexibilität bei der Anordnung der Produktionslinie.
- Pufferzonen: Bereiche, in denen Werkstücke zwischengelagert werden können, um den Produktionsfluss zu optimieren.
5. Einbrennöfen
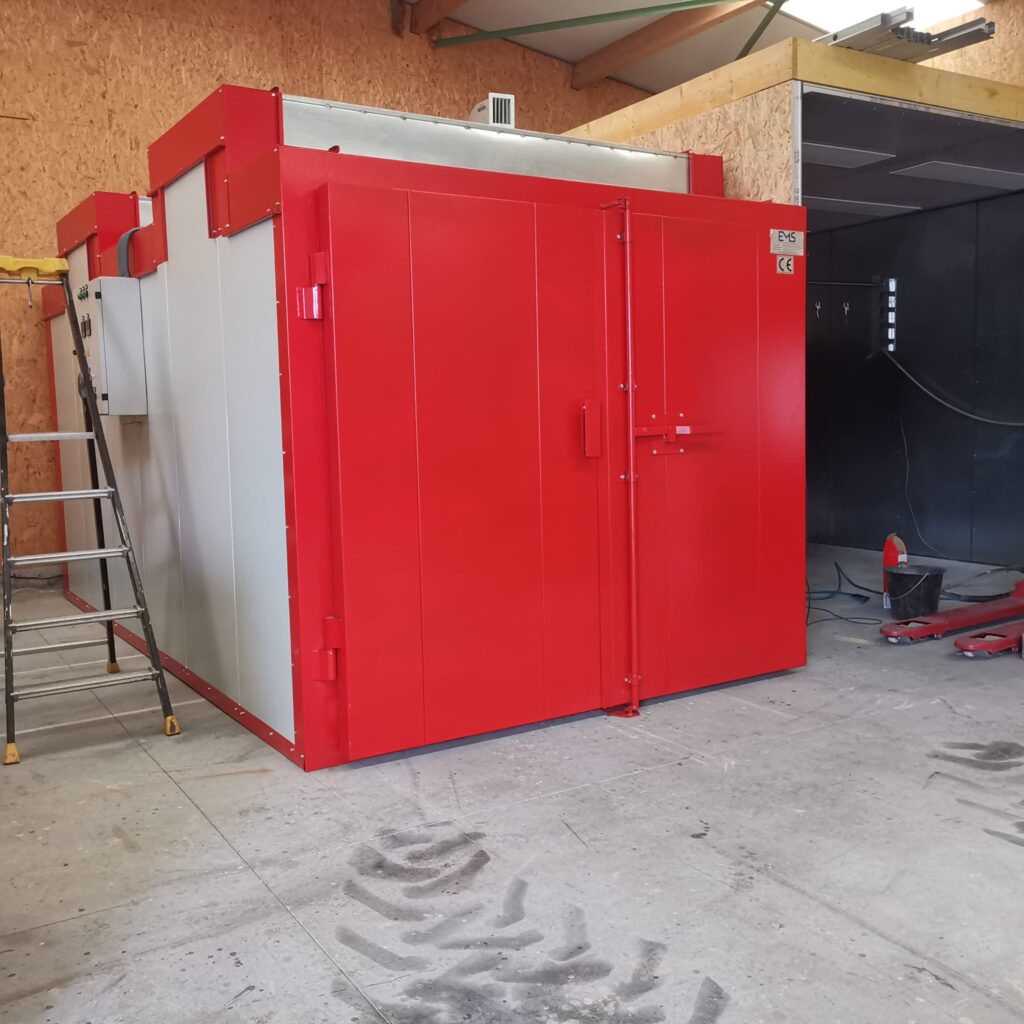
Einbrennöfen sind entscheidend für die Aushärtung der Pulverbeschichtung, da sie die erforderliche Wärme bereitstellen, um das Pulver zu schmelzen und eine dauerhafte Oberfläche zu schaffen.
- Chargenöfen: Ideal für kleinere Produktionen mit variablen Chargengrößen; sie bieten Flexibilität und können verschiedene Teile gleichzeitig verarbeiten.
- Durchlauföfen: Entwickelt für kontinuierliche Produktionslinien mit hohen Durchsatzraten. Teile werden auf einem Förderband durch den Ofen transportiert.
- Konvektions- und Infrarotöfen: Verschiedene Technologien bieten spezifische Vorteile in Bezug auf Aufheizgeschwindigkeit und Energieeffizienz.
6. Rückgewinnungs- und Recycling-Systeme
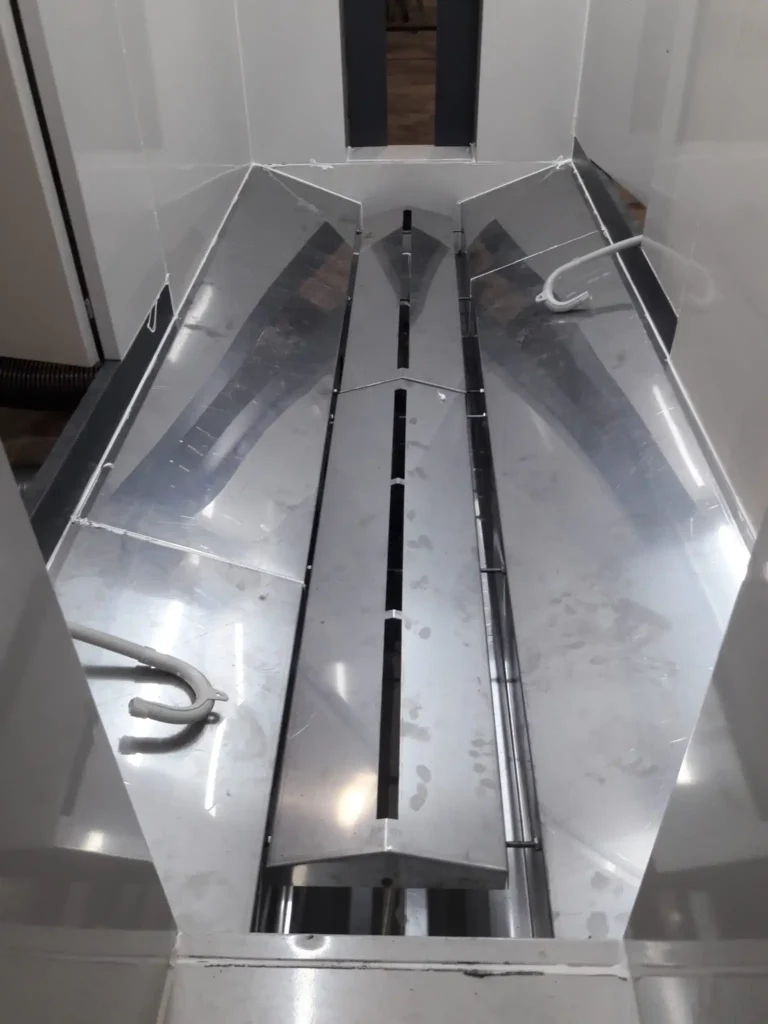
Diese Systeme sind darauf ausgelegt, überschüssiges Pulver aufzufangen und wiederzuverwenden, um Abfall zu minimieren und die Effizienz zu maximieren.
- Zyklonabscheider: Trennen überschüssiges Pulver aus der Luft und führen es zurück in den Beschichtungsprozess.
- Filtersysteme: Entfernen Feinstaub aus der Luft und stellen sicher, dass nur saubere Luft in die Umgebung abgegeben wird.
- Siebsysteme: Stellen sicher, dass nur qualitativ hochwertiges Pulver erneut verwendet wird, indem sie Verunreinigungen entfernen.
7. Steuerungs- und Überwachungssysteme
Moderne Steuerungssysteme ermöglichen die Überwachung und Anpassung aller Aspekte des Beschichtungsprozesses in Echtzeit.
- Prozessleitsysteme (PLS): Überwachen und steuern den gesamten Produktionsablauf und bieten Echtzeit-Daten zur Optimierung der Prozesse.
- Benutzeroberflächen: Intuitive Bedienpanels ermöglichen eine einfache Steuerung und Anpassung der Systemeinstellungen.
- Datenanalyse-Tools: Erfassen und analysieren Daten zur Prozessoptimierung und Fehlererkennung.
8. Kühlzonen
Nach dem Aushärtungsprozess müssen die Werkstücke auf Raumtemperatur abgekühlt werden, bevor sie weiterverarbeitet oder verpackt werden können.
- Luftkühlungssysteme: Nutzen Luftzirkulation, um die Werkstücke effizient abzukühlen.
- Wasserkühlungssysteme: In speziellen Anwendungen, wo schnelle Abkühlung erforderlich ist, können Wasserkühlungssysteme eingesetzt werden.
9. Materialhandling-Systeme
Diese Systeme unterstützen das Be- und Entladen von Werkstücken und die Bewegung innerhalb der Anlage.
- Robotiksysteme: Automatisierte Roboterarme, die Werkstücke präzise positionieren und handhaben.
- Hubsysteme: Unterstützen beim Transport schwerer Werkstücke innerhalb der Anlage.
10. Wartungseinrichtungen
Regelmäßige Wartung ist entscheidend, um die Effizienz und Lebensdauer der Anlage zu gewährleisten.
- Integrierte Wartungstools: Sensoren und Software zur vorausschauenden Wartung, die den Zustand der Anlage überwachen und Wartungsbedarf identifizieren.
- Zugängliche Wartungsbereiche: Einfache Zugänglichkeit für regelmäßige Inspektionen und Reparaturen.
Fazit
Eine komplette Pulverbeschichtungsanlage besteht aus vielen Komponenten, die zusammenarbeiten, um eine effiziente, qualitativ hochwertige und umweltfreundliche Beschichtung zu gewährleisten. Jede Komponente spielt eine entscheidende Rolle im Beschichtungsprozess, von der Vorbereitung der Werkstücke bis zur Aushärtung der Beschichtung. Die Wahl der richtigen Technologien und die Integration von Automatisierungslösungen können den Betrieb optimieren und die Produktionsziele eines Unternehmens effektiv unterstützen.
Anlagengröße

Die Größe von Pulverbeschichtungsanlagen kann je nach den spezifischen Anforderungen eines Unternehmens stark variieren. Die Anlagengröße hängt von mehreren Faktoren ab, darunter die Art und Größe der zu beschichtenden Werkstücke, das Produktionsvolumen und die verfügbaren räumlichen Gegebenheiten. Hier sind einige wichtige Überlegungen und Optionen zur Variation der Anlagengröße:
Faktoren, die die Anlagengröße beeinflussen
- Art der zu beschichtenden Werkstücke
- Kleinere Teile: Bei der Beschichtung von kleineren Teilen, wie z. B. Elektrokomponenten oder kleinen Metallteilen, können kompaktere Anlagen eingesetzt werden.
- Große Werkstücke: Für größere Teile, wie Automobilkarosserien oder große Maschinenteile, sind größere Anlagen mit geräumigen Kabinen und Öfen erforderlich.
- Produktionsvolumen
- Kleinserienproduktion: Unternehmen, die kleinere Produktionsvolumen handhaben, können mit einfacheren und kleineren Anlagen auskommen.
- Massenproduktion: Für hohe Produktionsvolumen sind größere und komplexere Anlagen notwendig, die einen kontinuierlichen Betrieb ermöglichen.
- Verfügbare Fläche
- Kompakte Lösungen: In begrenzten Räumlichkeiten können platzsparende Designs und integrierte Systeme genutzt werden, um den verfügbaren Platz optimal zu nutzen.
- Großflächige Anlagen: In größeren Einrichtungen kann eine weitläufige Anordnung von Vorbehandlung, Beschichtung und Aushärtung erfolgen, um einen reibungslosen Produktionsablauf zu gewährleisten.
- Prozessanforderungen
- Vielseitigkeit: Anlagen, die verschiedene Beschichtungsarten und Materialien verarbeiten müssen, erfordern möglicherweise eine modulare Struktur, die Anpassungen erlaubt.
- Spezialanforderungen: Bestimmte Anwendungen, wie z. B. die Beschichtung von hitzeempfindlichen Materialien, erfordern spezifische Anpassungen der Anlagengröße und -konfiguration.
Optionen zur Variation der Anlagengröße
1. Modulare Anlagen
Modulare Anlagen sind flexibel und können an unterschiedliche Produktionsanforderungen angepasst werden. Sie bestehen aus separaten Modulen, die nach Bedarf hinzugefügt oder entfernt werden können.
- Vorteile:
- Flexibilität: Einfaches Anpassen und Erweitern der Anlage, um auf wechselnde Produktionsanforderungen zu reagieren.
- Kosteneffizienz: Investitionen können nach und nach getätigt werden, indem nur die notwendigen Module erworben werden.
- Einfache Wartung: Einzelne Module können leicht gewartet oder ausgetauscht werden, ohne den gesamten Betrieb zu unterbrechen.
- Beispiele:
- Modulare Kabinen: Erlauben die Anpassung der Kabinengröße je nach Werkstückgröße.
- Erweiterbare Fördersysteme: Zusätzliche Förderstrecken können hinzugefügt werden, um den Produktionsfluss zu erweitern.
2. Kompakte Anlagen
Kompakte Anlagen sind ideal für Unternehmen mit begrenztem Platzangebot oder für kleinere Produktionsvolumen.
- Vorteile:
- Platzsparend: Effektive Nutzung des verfügbaren Raums.
- Geringere Investitionskosten: Reduzierte Anfangsinvestitionen durch den kleineren Maßstab der Anlage.
- Schnellere Installation: Einfachere und schnellere Implementierung.
- Beispiele:
- Mini-Kabinen: Kleinere Beschichtungskabinen für spezialisierte Anwendungen.
- Integrierte Systeme: Anlagen, die Vorbehandlung, Beschichtung und Aushärtung in einem kompakten Layout vereinen.
3. Großflächige Anlagen
Für Unternehmen mit hohen Produktionsanforderungen oder großen Werkstücken sind großflächige Anlagen notwendig.
- Vorteile:
- Hohe Kapazität: Eignen sich für die Massenproduktion und den gleichzeitigen Betrieb mehrerer Linien.
- Vielseitigkeit: Möglichkeit, mehrere Prozesse gleichzeitig durchzuführen.
- Effizienz: Optimierte Produktionsabläufe durch die großzügige Gestaltung der Anlage.
- Beispiele:
- Mehrere Kabinen und Öfen: Separate Bereiche für unterschiedliche Farben oder Materialien.
- Erweiterte Fördersysteme: Lange Förderstrecken für den Transport großer oder zahlreicher Teile.
Planungsüberlegungen bei der Anlagengrößenauswahl
- Zukunftsprognosen
- Marktentwicklung: Berücksichtigen Sie mögliche Expansionen oder Veränderungen in der Nachfrage.
- Technologische Fortschritte: Planen Sie für zukünftige Anpassungen oder Upgrades der Anlage.
- Kostenüberlegungen
- Anfangsinvestition vs. Betriebskosten: Wägen Sie die Anfangsinvestitionen gegen die langfristigen Betriebskosten ab.
- Finanzielle Flexibilität: Planen Sie die Finanzierung der Anlage im Einklang mit den finanziellen Möglichkeiten und Zielen des Unternehmens.
- Integration und Kompatibilität
- Bestehende Infrastruktur: Überprüfen Sie die Kompatibilität der neuen Anlage mit bestehenden Systemen und Einrichtungen.
- Erweiterungsmöglichkeiten: Planen Sie die Integration zukünftiger Erweiterungen oder Module.
- Umwelt- und Sicherheitsstandards
- Regulierungen: Stellen Sie sicher, dass die Anlage alle relevanten Umwelt- und Sicherheitsstandards erfüllt.
- Nachhaltigkeit: Berücksichtigen Sie umweltfreundliche Technologien und Praktiken bei der Planung und dem Betrieb der Anlage.
Fazit
Die Größe einer Pulverbeschichtungsanlage kann an die spezifischen Bedürfnisse und Anforderungen eines Unternehmens angepasst werden. Durch die Auswahl der richtigen Anlagengröße und -konfiguration können Unternehmen ihre Produktionsziele effizient erreichen, die Qualität ihrer Produkte verbessern und die Betriebskosten optimieren. Ob modular, kompakt oder großflächig, jede Anlagengröße hat ihre eigenen Vorteile und Herausforderungen, die sorgfältig abgewogen werden müssen, um die besten Ergebnisse zu erzielen.
Benötigte Mitarbeiterzahl
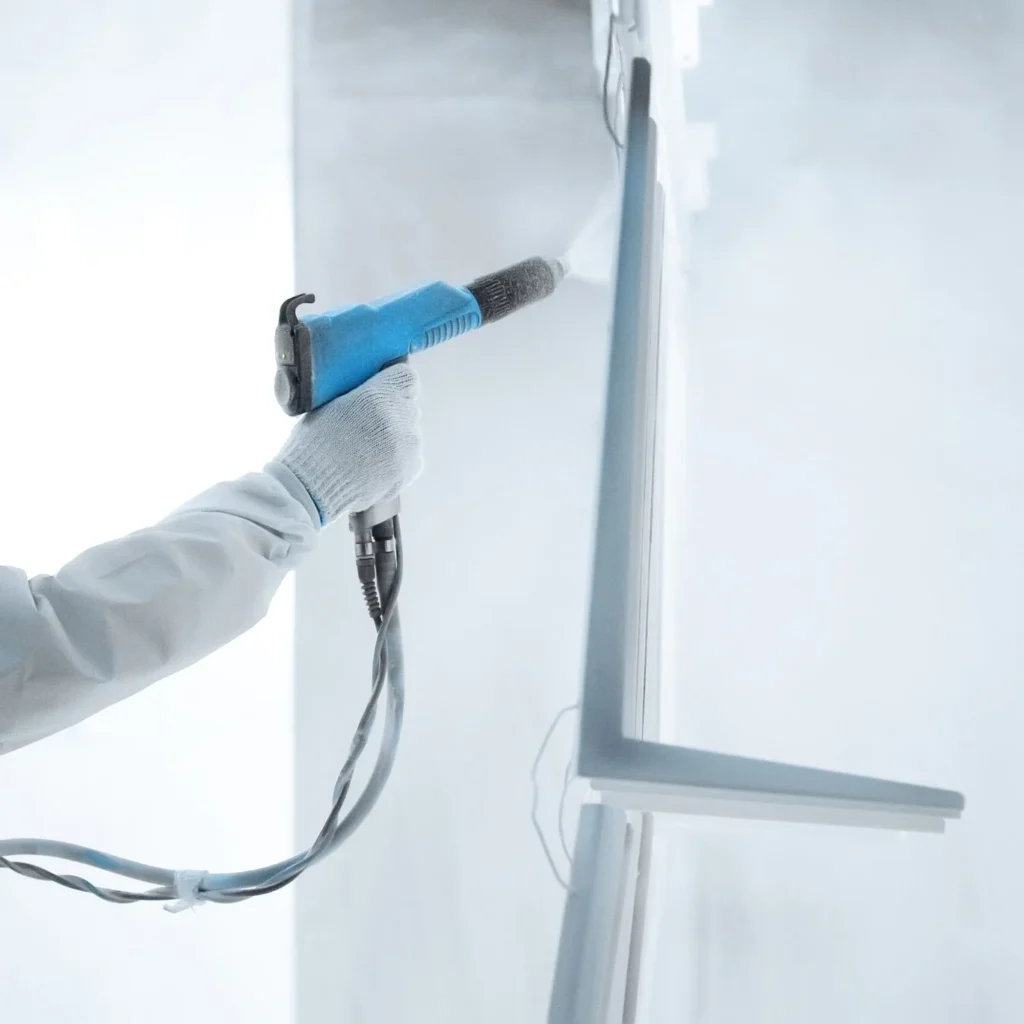
Die Anzahl der benötigten Mitarbeiter für den Betrieb einer Pulverbeschichtungsanlage hängt von mehreren Faktoren ab, darunter die Größe und Automatisierung der Anlage, das Produktionsvolumen, die Art der zu beschichtenden Werkstücke und die spezifischen betrieblichen Anforderungen. Hier sind einige Überlegungen, um die optimale Mitarbeiterzahl für den Betrieb einer Pulverbeschichtungsanlage zu bestimmen:
1. Faktoren, die die Mitarbeiterzahl beeinflussen
a. Größe der Anlage
- Kleine Anlagen:
- Typischerweise weniger Mitarbeiter erforderlich.
- Häufig eine Mischung aus manuellen und halbautomatisierten Prozessen.
- Große Anlagen:
- Mehr Mitarbeiter erforderlich, insbesondere bei einer hohen Produktionskapazität.
- Automatisierte Systeme können jedoch den Bedarf an Personal verringern.
b. Automatisierungsgrad
- Hochautomatisierte Anlagen:
- Reduzierter Bedarf an manueller Arbeit.
- Erfordern jedoch technisches Personal für die Überwachung, Wartung und Programmierung der Anlagen.
- Manuelle oder halbautomatisierte Anlagen:
- Höherer Personalbedarf für die Bedienung und Überwachung der Anlagen.
c. Produktionsvolumen
- Niedriges Produktionsvolumen:
- Geringerer Personalbedarf.
- Mehr Flexibilität bei der Planung von Schichten.
- Hohes Produktionsvolumen:
- Mehr Mitarbeiter erforderlich, um den Produktionsfluss aufrechtzuerhalten.
- Möglicherweise mehrere Schichten zur Maximierung der Betriebszeit.
d. Werkstücktypen
- Komplexe oder große Werkstücke:
- Erfordern möglicherweise mehr Personal für die Handhabung und Inspektion.
- Spezialisierte Mitarbeiter für die Anpassung der Beschichtungsparameter.
- Kleine oder standardisierte Teile:
- Weniger Personal für die Handhabung erforderlich.
- Prozessabläufe sind oft einfacher und standardisiert.
2. Typische Rollen in einer Pulverbeschichtungsanlage
a. Produktionsmitarbeiter
- Bediener der Beschichtungsanlagen:
- Verantwortlich für das Auftragen der Pulverbeschichtung.
- Überwachung der Qualität und Sicherstellung der richtigen Parameter.
- Vorbehandlungsmitarbeiter:
- Durchführung von Reinigungs- und Vorbehandlungsprozessen.
- Sicherstellung, dass die Werkstücke ordnungsgemäß vorbereitet sind.
b. Technisches Personal
- Wartungstechniker:
- Regelmäßige Wartung und Reparatur der Anlagen.
- Überwachung der Systemleistung und Durchführung von Fehlerbehebungen.
- Automatisierungs- und Steuerungstechniker:
- Programmierung und Überwachung automatisierter Systeme.
- Anpassung der Steuerungsparameter und Optimierung der Prozesse.
c. Qualitätssicherung
- Qualitätsinspektoren:
- Durchführung von Qualitätskontrollen zur Sicherstellung der Einhaltung von Standards.
- Verwendung von Messgeräten zur Überprüfung der Schichtdicke und Oberflächenqualität.
- Prozessoptimierer:
- Analyse von Produktionsdaten zur Verbesserung der Effizienz und Qualität.
- Implementierung von Verbesserungsmaßnahmen.
d. Management und Verwaltung
- Produktionsleiter:
- Überwachung der gesamten Produktionslinie.
- Koordination der Mitarbeiter und Sicherstellung der Zielerreichung.
- Logistik- und Materialplaner:
- Verwaltung der Materialflüsse und Bestände.
- Planung der Produktion auf Basis von Nachfrage und Kapazität.
3. Beispiel einer Mitarbeiterverteilung
Hier ist ein Beispiel für die Mitarbeiterverteilung in einer mittelgroßen, teilautomatisierten Pulverbeschichtungsanlage:
Rolle | Anzahl der Mitarbeiter | Beschreibung |
---|---|---|
Bediener der Vorbehandlung | 2-3 | Verantwortlich für Reinigung und Vorbereitung der Werkstücke. |
Pulverbeschichtungsbediener | 3-4 | Durchführung des Beschichtungsprozesses. |
Wartungstechniker | 1-2 | Wartung und Reparatur der Anlagen. |
Automatisierungstechniker | 1-2 | Überwachung der automatisierten Systeme und Prozesssteuerung. |
Qualitätsinspektoren | 1-2 | Überprüfung der Qualität der beschichteten Teile. |
Produktionsleiter | 1 | Leitung der Produktion und Koordination der Schichten. |
Logistik- und Materialplaner | 1 | Verwaltung der Materialbestände und Produktionsplanung. |
4. Optimierung der Mitarbeiterzahl
Um die Mitarbeiterzahl effizient zu nutzen, können Unternehmen folgende Strategien in Betracht ziehen:
- Schulung und Weiterbildung: Regelmäßige Schulungen, um die Qualifikation der Mitarbeiter zu verbessern und sie auf mehrere Aufgaben vorzubereiten.
- Einsatz von Zeitarbeitern: Flexible Personalplanung durch den Einsatz von Zeitarbeitskräften, um bei Bedarf Spitzenbelastungen abzufangen.
- Prozessoptimierung: Einsatz von Lean-Management-Prinzipien, um Prozesse zu optimieren und den Personalbedarf zu reduzieren.
- Investition in Automatisierung: Einsatz von Automatisierungstechnologien zur Reduzierung des manuellen Arbeitsaufwands und Verbesserung der Effizienz.
Fazit
Die optimale Anzahl der Mitarbeiter in einer Pulverbeschichtungsanlage hängt von vielen Faktoren ab, darunter die Größe der Anlage, der Automatisierungsgrad und das Produktionsvolumen. Durch den Einsatz von Automatisierung, Schulung und Prozessoptimierung können Unternehmen ihre Personalkosten minimieren und gleichzeitig die Effizienz und Qualität ihrer Produktion maximieren. Eine sorgfältige Planung und Anpassung der Personalressourcen ist entscheidend, um den Erfolg der Anlage zu gewährleisten.