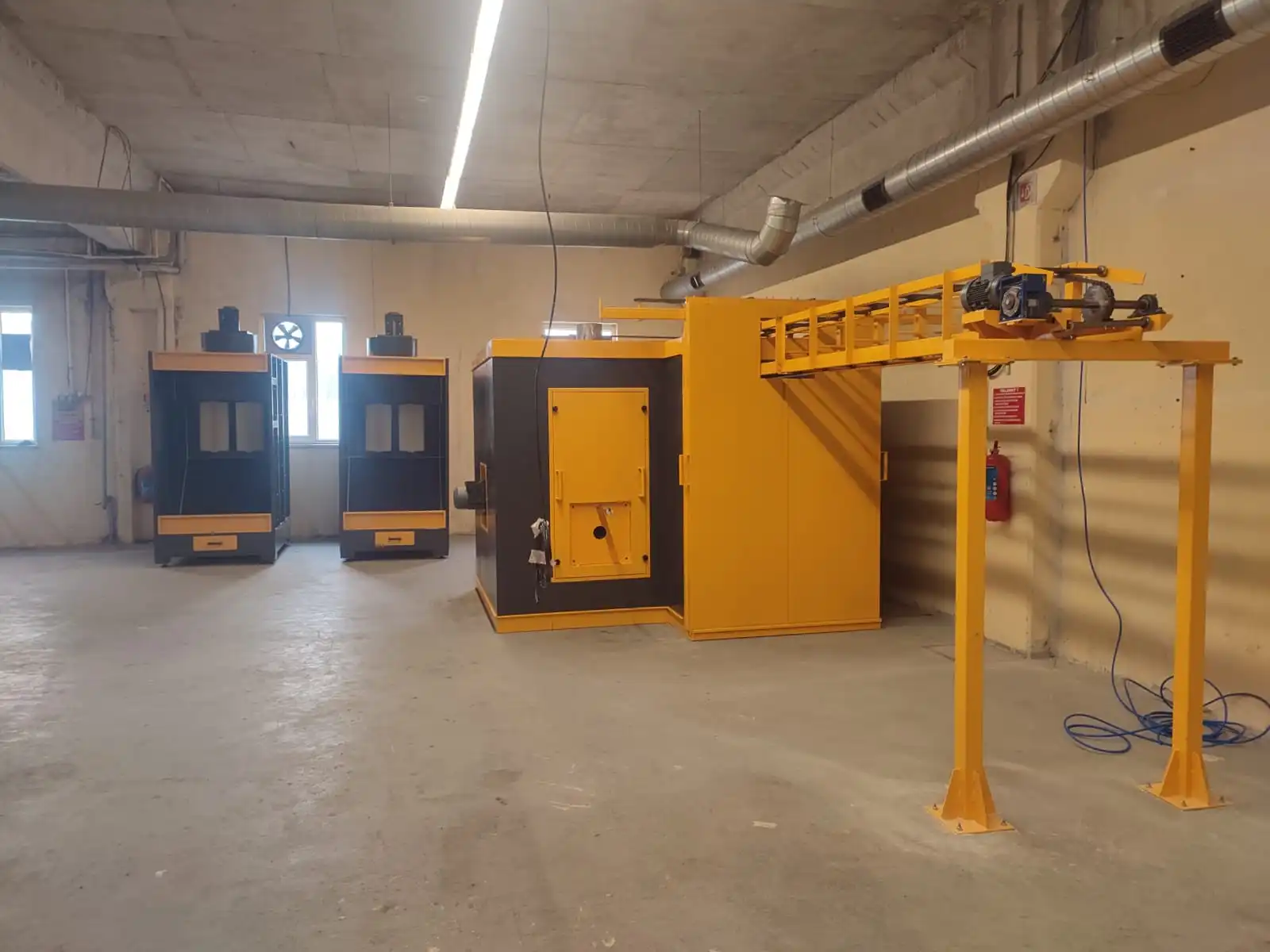
Die Pulverbeschichtungsanlage ist eine Maschine, die zum Auftragen von Pulverlack auf Metallteile verwendet wird. Die Anlage besteht aus drei Hauptkomponenten:
- Pulverkabine: Die Pulverkabine ist ein geschlossener Raum, in dem die Teile beschichtet werden. Die Kabine ist mit einem Luftstromsystem ausgestattet, das das Pulver gleichmäßig auf den Teilen verteilt.
- Pulverbeschichtungsgerät: Das Pulverbeschichtungsgerät verwendet einen elektrostatischen Prozess, um das Pulver auf die Teile zu sprühen.
- Pulvereinbrennofen: Der Pulvereinbrennofen erhitzt die beschichteten Teile auf eine Temperatur, die ausreicht, damit der Pulverlack zu schmelzen und eine feste, haltbare Beschichtung zu bilden.
Der Pulverbeschichtungsprozess ist in drei Schritte unterteilt:
- Vorbehandlung: Die Teile werden gereinigt und entfettet, um sicherzustellen, dass die Beschichtung gut haftet.
- Pulverbeschichtung: Das Pulver wird mithilfe eines elektrostatischen Prozesses auf die Teile gesprüht.
- Pulvereinbrenn: Die beschichteten Teile werden im Ofen erhitzt, um den Pulverlack zu härten.
Pulverbeschichtung ist eine beliebte Methode zur Beschichtung von Metallteilen, da sie eine Reihe von Vorteilen bietet, darunter:
- Lange Lebensdauer: Pulverbeschichtungen sind sehr haltbar und bieten einen hervorragenden Schutz vor Korrosion und Beschädigung.
- Vielseitiges Design: Pulverbeschichtungen sind in einer Vielzahl von Farben und Texturen erhältlich, sodass sie an eine Vielzahl von Designanforderungen angepasst werden können.
- Umweltfreundlich: Pulverbeschichtungen sind im Vergleich zu anderen Beschichtungsmethoden umweltfreundlicher, da sie keine Lösungsmittel oder andere umweltschädliche Chemikalien erfordern.
Wir stellen 2 verschiedene Arten der manuellen Pulverbeschichtungsanlage (mit Behälter und Multicolor) und auch automatischen Pulverbeschichtungsanlage her
Pulverbeschichtungsanlage
Eine Pulverbeschichtungsanlage ist eine industrielle Einrichtung, die für die Anwendung von Pulverbeschichtungen auf Oberflächen von verschiedenen Materialien verwendet wird. Pulverbeschichtung ist ein Verfahren, bei dem trockenes Pulver auf ein Substrat aufgebracht wird und dann durch Hitze oder UV-Licht geschmolzen und ausgehärtet wird. Dieser Prozess führt zu einer strapazierfähigen, gleichmäßigen und hochwertigen Oberflächenbeschichtung. Hier sind die grundlegenden Komponenten und Funktionen einer typischen Pulverbeschichtungsanlage:
- Förder- und Vorbereitungsanlagen:
- Transportbänder oder Hängesysteme: Diese befördern die Werkstücke durch die verschiedenen Phasen des Pulverbeschichtungsprozesses.
- Vorbehandlung: Eine Reinigungs- und Vorbehandlungsstation entfernt Schmutz, Fett und Oxidation von den Oberflächen der Werkstücke und bereitet sie für die Beschichtung vor.
- Pulverapplikationssystem:
- Automatisierte Pulverpistolen: Diese automatisierten Pistolen applizieren das Pulver auf die vorbereiteten Oberflächen der Werkstücke.
- Kontrollierte Pulverzufuhr: Pulver wird aus einem Behälter zugeführt und durch ein System kontrolliert, um eine gleichmäßige Beschichtung zu gewährleisten.
- Trocknungsofen:
- Förderbänder oder Hängesysteme: Transportieren die Werkstücke in den Trocknungsofen.
- Erhitzungssystem: Erhitzt das Pulver auf den Werkstücken, schmilzt es und härtet es aus, um eine dauerhafte Beschichtung zu gewährleisten.
- Kühltunnel:
- Förderbänder oder Hängesysteme: Transportieren die Werkstücke durch einen Kühlbereich, um die Aushärtung des beschichteten Pulvers zu unterstützen und die Qualität zu verbessern.
- Qualitätskontrolle und Inspektion:
- Automatisierte Inspektionssysteme: Überwachen die Qualität der Beschichtung, um sicherzustellen, dass sie den spezifizierten Standards entspricht.
- Manuelle Inspektion: Ergänzt automatisierte Systeme durch visuelle Inspektionen durch geschultes Personal.
- Pulverrückgewinnungssystem:
- Absaug- und Filtersysteme: Erfassen überschüssiges Pulver, filtern es und ermöglichen die Wiederverwendung in der Pulverbeschichtungsanlage.
- Auffangsysteme: Fangen überschüssiges Pulver auf, um Materialverluste zu minimieren.
- Steuerungs- und Automatisierungssysteme:
- Programmierbare Steuerungseinheit (PLC): Koordiniert und steuert den gesamten Pulverbeschichtungsprozess.
- HMI (Human-Machine Interface): Bietet eine Benutzeroberfläche zur Überwachung und Steuerung der Anlage.
- Sicherheitsvorkehrungen:
- Not-Aus-Schalter und Sicherheitssysteme: Gewährleisten die Sicherheit von Bedienungspersonal und Anlage.
- Schutzvorrichtungen: Schützen vor Pulverexplosionen oder anderen sicherheitsrelevanten Gefahren.
Die effiziente Gestaltung und Implementierung einer Pulverbeschichtungsanlage erfordern eine sorgfältige Planung, um sicherzustellen, dass alle Komponenten nahtlos zusammenarbeiten und qualitativ hochwertige Beschichtungsergebnisse erzielt werden. Sicherheitsstandards und Umweltaspekte sollten dabei ebenfalls berücksichtigt werden.
Manuelle Pulverbeschichtungsanlage
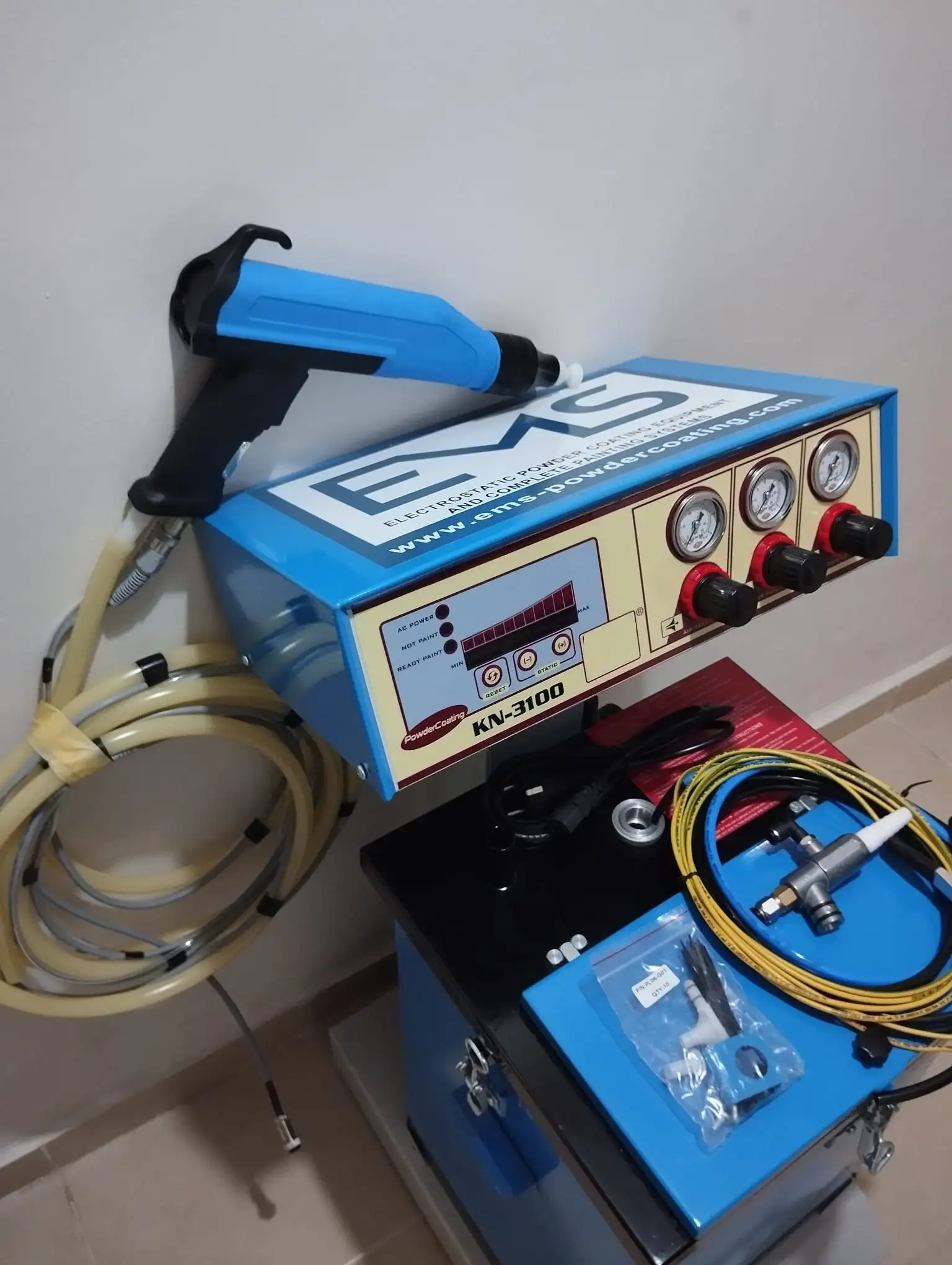
Eine manuelle Pulverbeschichtungsanlage ermöglicht es Bedienungspersonal, den Pulverbeschichtungsprozess manuell durchzuführen. Im Gegensatz zu vollautomatisierten Anlagen erfordert die manuelle Pulverbeschichtung eine direkte Beteiligung von Mitarbeitern für die Applikation des Pulvers und gegebenenfalls andere Prozessschritte. Hier sind die grundlegenden Komponenten und Schritte, die in einer manuellen Pulverbeschichtungsanlage typischerweise vorkommen:
- Vorbereitung der Werkstücke:
- Die Werkstücke werden auf ihre Beschichtung vorbereitet, indem sie gereinigt und gegebenenfalls vorbehandelt werden. Dies kann das Entfernen von Schmutz, Fett oder Rost umfassen.
- Pulverapplikation:
- Manuelle Pulverpistolen werden von Bedienungspersonal verwendet, um das Pulver auf die vorbereiteten Oberflächen der Werkstücke aufzubringen.
- Die Bediener müssen die gleichmäßige Verteilung des Pulvers sicherstellen, um eine qualitativ hochwertige Beschichtung zu gewährleisten.
- Trocknungsofen:
- Die beschichteten Werkstücke werden in einen Trocknungsofen geschoben, um das Pulver zu schmelzen und auszuhärten.
- Die Trocknungszeit und -temperatur sind entscheidende Parameter, die manuell überwacht werden müssen.
- Kühlbereich:
- Nach dem Aushärten werden die Werkstücke durch einen Kühlbereich transportiert, um die Qualität der Beschichtung zu verbessern und eine ausreichende Aushärtung sicherzustellen.
- Qualitätskontrolle und Inspektion:
- Manuelle Inspektionen durch Bedienungspersonal sind erforderlich, um sicherzustellen, dass die Beschichtung den Qualitätsstandards entspricht.
- Dies kann visuelle Inspektionen, Prüfung der Beschichtungsdicke und andere Qualitätsparameter umfassen.
- Pulverrückgewinnungssystem:
- Überschüssiges Pulver muss gesammelt und recycelt werden, um Materialverluste zu minimieren.
- Bedienungspersonal muss sicherstellen, dass das Rückgewinnungssystem ordnungsgemäß funktioniert.
- Steuerungs- und Automatisierungssysteme:
- Obwohl die Anlage manuell betrieben wird, können einfache Steuerungen und Anzeigetafeln verwendet werden, um den Bedienern Informationen über den Prozess zu geben.
- Sicherheitsvorkehrungen:
- Not-Aus-Schalter, persönliche Schutzausrüstung (wie Atemschutzgeräte und Schutzhandschuhe) und andere Sicherheitsmaßnahmen sind entscheidend, um die Sicherheit der Bedienungspersonals zu gewährleisten.
Die manuelle Pulverbeschichtung bietet Flexibilität bei der Handhabung unterschiedlicher Werkstücke und kann kosteneffektiver sein, besonders wenn die Produktionsvolumina nicht sehr hoch sind. Allerdings erfordert sie eine geschulte und aufmerksame Bedienung, um konsistente Ergebnisse zu erzielen. Die Einhaltung von Sicherheitsvorschriften und Qualitätskontrollverfahren ist in manuellen Anlagen besonders wichtig.
Eine manuelle Pulverpistole ist ein Gerät, das zum Auftragen von Pulverlack auf Metallteile verwendet wird. Manuelle Pulverpistolen arbeiten mit einem elektrostatischen Prozess, um das Pulver auf die Teile zu sprühen. Die Pistole erzeugt ein elektrisches Feld, das das Pulver anzieht und auf die Teile haftet.
Manuelle Pulverpistolen bestehen aus den folgenden Komponenten:
- Düse: Die Düse ist der Teil der Pistole, der das Pulver ausstößt.
- Luftstromkanal: Der Luftstromkanal liefert Luft zum Antrieb der Düse und zum gleichmäßigen Verteilen des Pulvers.
- Elektrode: Die Elektrode erzeugt das elektrische Feld, das das Pulver anzieht.
- Handgriff: Der Handgriff dient zur Befestigung der Pistole an der Hand des Bedieners.
Manuelle Pulverpistolen sind in verschiedenen Größen und Ausführungen erhältlich, um den unterschiedlichen Anforderungen der Beschichter gerecht zu werden. Einige gängige Arten von manuellen Pulverpistolen sind:
- Hochleistungspistolen: Hochleistungspistolen sind für die Beschichtung großer Teile geeignet.
- Niederdruckpistolen: Niederdruckpistolen sind für die Beschichtung kleinerer Teile geeignet.
- Rotationspistolen: Rotationspistolen verwenden eine rotierende Düse, um das Pulver gleichmäßig auf die Teile zu verteilen.
Die Wahl der richtigen manuellen Pulverpistole hängt von einer Reihe von Faktoren ab, darunter die Größe und Art der zu beschichtenden Teile, die gewünschte Produktionskapazität und das Budget.
Pulverbeschichtungsanlage mit Multicolor Quick-Farbwechseloption

Eine Pulverbeschichtungsanlage mit einer Multicolor Quick-Farbwechseloption ermöglicht es, schnell und effizient zwischen verschiedenen Farben zu wechseln, ohne dass lange Stillstandszeiten für Reinigung und Umrüstung erforderlich sind. Dies ist besonders nützlich in Situationen, in denen eine Vielzahl von Werkstücken mit unterschiedlichen Farbanforderungen bearbeitet wird. Hier sind einige Schlüsselkomponenten und Merkmale, die in einer solchen Anlage enthalten sein könnten:
- Schnellwechselpistolen:
- Automatisierte Pulverpistolen mit Schnellwechselmöglichkeiten für die Pulverfarben.
- Schnellwechseladapter ermöglichen es, die Pulverpistolen ohne aufwendige Demontage oder Reinigung zu tauschen.
- Modulares Pulverversorgungssystem:
- Ein modulares System für die Pulverzufuhr, das den schnellen Austausch von Pulverbehältern oder Pulverleitungen ermöglicht.
- Schnellkupplungen und spezielle Ventile können den Farbwechselprozess beschleunigen.
- Automatisierte Reinigungseinrichtungen:
- Automatisierte Reinigungssysteme für die Pulverpistolen und Pulverleitungen, um Farbkontaminationen zwischen den Farbwechseln zu minimieren.
- Schnelle Reinigungszyklen ermöglichen einen reibungslosen Übergang von einer Farbe zur nächsten.
- Förderbänder mit schnellen Umrüstmöglichkeiten:
- Schnellwechselbare Förderband- oder Hängesysteme, um Werkstücke effizient durch den Beschichtungsprozess zu befördern.
- Ein einfacher Wechsel zwischen verschiedenen Werkstückgrößen und -formen.
- Automatisierte Steuerungssoftware:
- Eine intelligente Steuerungssoftware, die den Farbwechselprozess koordiniert.
- Diese Software kann den Pulverfluss, die Pistolenpositionen und andere Parameter automatisch anpassen.
- Sensortechnologie für Qualitätskontrolle:
- Sensoren und Inspektionssysteme, die die Qualität der Beschichtung überwachen.
- Feedbacksysteme, um sicherzustellen, dass jede Farbänderung zu qualitativ hochwertigen Ergebnissen führt.
- Farbmanagement- und Dosierungssysteme:
- Systeme zur genauen Dosierung und Verwaltung von Pulverfarben.
- Die Möglichkeit, verschiedene Farbnuancen zu reproduzieren und präzise Farbmengen zu dosieren.
- Sicherheitsvorkehrungen:
- Not-Aus-Schalter und Sicherheitssysteme, um den sicheren Betrieb während des Farbwechselprozesses zu gewährleisten.
- Schulungen für Bedienungspersonal zur sicheren Handhabung und Wartung der Anlage.
Die Multicolor Quick-Farbwechseloption erhöht die Flexibilität der Pulverbeschichtungsanlage erheblich und ermöglicht eine schnellere Anpassung an wechselnde Produktionsanforderungen. Die Implementierung erfordert jedoch sorgfältige Schulung des Bedienungspersonals und eine präzise Steuerungstechnologie, um qualitativ hochwertige und konsistente Ergebnisse sicherzustellen.
Eine Pulverbeschichtungsanlage mit Multicolor Quick-Farbwechseloption ist eine Anlage, die zum Auftragen von Pulverlack auf Metallteile in mehreren Farben verwendet wird. Die Anlage verfügt über eine Schnellwechselvorrichtung, die es ermöglicht, die Farbbehälter schnell und einfach zu wechseln. Dies ermöglicht es den Beschichtern, Teile in mehreren Farben schnell und effizient zu beschichten.
Die Multicolor Quick-Farbwechseloption besteht aus den folgenden Komponenten:
- Farbbehälter: Die Farbbehälter enthalten das Pulverlack in den gewünschten Farben.
- Schnellwechselvorrichtung: Die Schnellwechselvorrichtung ermöglicht es, die Farbbehälter schnell und einfach zu wechseln.
- Pulverbeschichtungsgerät: Das Pulverbeschichtungsgerät verwendet einen elektrostatischen Prozess, um das Pulver auf die Teile zu sprühen.
Die Multicolor Quick-Farbwechseloption bietet eine Reihe von Vorteilen, darunter:
- Erhöhte Produktivität: Die Schnellwechselvorrichtung ermöglicht es den Beschichtern, Teile in mehreren Farben schnell und effizient zu beschichten.
- Flexibilität: Die Anlage kann zum Beschichten einer Vielzahl von Teilen in mehreren Farben verwendet werden.
- Einfache Bedienung: Die Schnellwechselvorrichtung ist einfach zu bedienen und erfordert keine spezielle Schulung.
Pulverbeschichtungsanlagen mit Multicolor Quick-Farbwechseloption werden häufig in Unternehmen verwendet, die Teile in mehreren Farben beschichten müssen. Sie sind auch eine gute Option für Unternehmen, die ihre Produktivität und Flexibilität steigern möchten.
Hier sind einige Beispiele für Pulverbeschichtungsanlagen mit Multicolor Quick-Farbwechseloption:
- Graco Pinnacle 9500 Multicolor: Diese Anlage ist für die Beschichtung von großen Teilen in mehreren Farben geeignet.
- Nordson SPX 2000 Multicolor: Diese Anlage ist für die Beschichtung von kleinen Teilen in mehreren Farben geeignet.
- Amann Girrbach Pulverlackieranlage P 2000 Multicolor: Diese Anlage ist für die Beschichtung von einer Vielzahl von Teilen in mehreren Farben geeignet.
Die Wahl der richtigen Pulverbeschichtungsanlage mit Multicolor Quick-Farbwechseloption hängt von einer Reihe von Faktoren ab, darunter die Größe und Art der zu beschichtenden Teile, die gewünschte Produktionskapazität und das Budget.
Automatische Pulverbeschichtungsanlage
Eine automatische Pulverbeschichtungsanlage ist eine Anlage, die zum Auftragen von Pulverlack auf Metallteile verwendet wird. Die Anlage wird von Robotern oder anderen Automatisierungsgeräten gesteuert, um den Pulverbeschichtungsprozess zu beschleunigen und zu vereinfachen.
Automatische Pulverbeschichtungsanlagen bestehen aus den folgenden Komponenten:
- Pulverkabine: Die Pulverkabine ist ein geschlossener Raum, in dem die Teile beschichtet werden. Die Kabine ist mit einem Luftstromsystem ausgestattet, das das Pulver gleichmäßig auf den Teilen verteilt.
- Pulverbeschichtungsgerät: Das Pulverbeschichtungsgerät verwendet einen elektrostatischen Prozess, um das Pulver auf die Teile zu sprühen.
- Pulvereinbrennofen: Der Pulvereinbrennofen erhitzt die beschichteten Teile auf eine Temperatur, die ausreicht, damit der Pulverlack zu schmelzen und eine feste, haltbare Beschichtung zu bilden.
- Automatisierungssysteme: Die Automatisierungssysteme steuern den Pulverbeschichtungsprozess und bewegen die Teile durch die Anlage.
Der Pulverbeschichtungsprozess mit einer automatischen Pulverbeschichtungsanlage ist in drei Schritte unterteilt:
- Vorbehandlung: Die Teile werden gereinigt und entfettet, um sicherzustellen, dass die Beschichtung gut haftet.
- Pulverbeschichtung: Das Pulver wird mithilfe eines elektrostatischen Prozesses auf die Teile gesprüht.
- Pulvereinbrenn: Die beschichteten Teile werden im Ofen erhitzt, um den Pulverlack zu härten.
Automatische Pulverbeschichtungsanlagen bieten eine Reihe von Vorteilen, darunter:
- Erhöhte Produktivität: Automatische Pulverbeschichtungsanlagen können Teile schneller und effizienter beschichten als manuelle Pulverbeschichtungsanlagen.
- Verbesserte Qualität: Automatische Pulverbeschichtungsanlagen können eine gleichmäßigere und gleichmäßigere Beschichtung erzielen als manuelle Pulverbeschichtungsanlagen.
- Erhöhte Sicherheit: Automatische Pulverbeschichtungsanlagen reduzieren die Exposition der Bediener gegenüber schädlichen Chemikalien und Partikeln.
Automatische Pulverbeschichtungsanlagen werden häufig in Unternehmen verwendet, die eine hohe Produktionskapazität und eine gleichbleibend hohe Qualität benötigen. Sie sind auch eine gute Option für Unternehmen, die die Sicherheit ihrer Mitarbeiter verbessern möchten.
Automatikpistolen

In der Pulverbeschichtungskabine werden Automatikpistolen eingesetzt. Diese Pistolen wurden speziell für eine automatische, einfache Reinigung entwickelt.
Die Anschlüsse für den Pulverschlauch, die Hochspannung und die Elektrodenspülluft befinden sich ausserhalb der Beschichtungskabine. Diese Zuleitungen sind in der Pistole integriert, daher können die Pistolen mittels Abblasdüsen automatisch abgereinigt werden. Der Pulverschlauchanschluss ermöglicht durch die Klemmvorrichtung eine einwandfreie Befestigung des Pulverschlauches.
Dies ist eine Grundvoraussetzung beim automatischen Durchspülen der Pulvertransportvorrichtung (weitere Informationen über Automatikpistolen, siehe in der entsprechenden Betriebsanleitung).
Bei der Pulverbeschichtungskabine wird grundsätzlich
zwischen hellen und dunklen Farbtönen unterschieden. Demzufolge werden die Pulverschläuche vom Pulverzentrum aus zweifach verlegt.

Pistolenreinigung
Die Automatikpistolen können sehr einfach und schnell gereinigt werden. Die Reinigung der Automatikpistolen erfolgt durch die Pistolenabblasvorrichtung an der Beschichtungskabine. Mit der Aktivierung der Reinigungsfunktion an der Steuereinheit fahren
die Hubgeräte, bzw. die Pistolen aus der Kabine heraus.
Gleichzeitig wird jede Pistole von aussen mittels je vier Flachstrahl-Abblasdüsen sauber abgeblasen. Diese Flachstrahl-Abblasdüsen befinden sich an den Pistolenschlitzen ausserhalb der Kabine. Falls erforderlich, lässt sich dieser Reinigungsvorgang wiederholen.
Die Beschichtungsgeräte – Pistolen
Aufgrund von Versuchen im Technik um des Anlagenbauers oder Pulverherstellers sind die einzusetzenden Pistolentypen und deren Zahl zu ermitteln. Die Korona-Pistole ist eine Hochspannungs pistole, die für alle Pulverarten eingesetzt werden kann.
Mit der ionenarmen oder ionenreduzierten Aufladeform stehen Pistolen zur Verfügung, die eine Applikation dickerer Pulverschichten ohne die Ausbildung der unerwünschten Orangenhaut ermöglichen.
Für die Beschichtung von Emailpulvern werden ebenfalls diese Pistolenarten eingesetzt, jedoch aufgrund der abrasiven Eigenschaften des Emailpulvers sind diese aus an de ren Materialien hergestellt. Die Tribo-Pistole braucht ein speziell behandeltes Pulver.
Die Pulverglocke wird sinnvollerweise nur dann eingesetzt, wenn in einer Kabine ausschließlich Flachteile beschichtet werden. Für die verschiedenen Applikationen stehen, je nach den Anforderungen, die das zu beschichtende Objekt an die Beschichtung stellt, auch verschiedene Mundstücke für die Pistolen zur Verfügung.
Anordnung von Applikationsgeraten und Bestimmung der Pistolenzahl
Für die automatische Lackierung werden die Pistolen starr oder auf Hubgeräten angeordnet. Da der Pulverausstoß eines Sprühgerätes nur in gewissen Grenzen variabel ist, müssen mehrere Pistolen gleichzeitig eingesetzt werden. Vorteilhaft ist dabei die variable Anordnung der
Geräte zueinander, wobei darauf geachtet werden muss, dass sich die gleichpoligen Sprühwolken gegenseitig abstoßen.
Eine versetzte Anordnung und/oder das Oszillieren quer zur Bewegungsrichtung der zu beschichtenden Werkstücke, beugt einer Streifenbildung vor. Da bei einer Mehrfach anordnung die Größe und Form der Sprühwolken. ihre Raumladung, der Abstand der Sprühköpfe untereinander, der Abstand zum Werkstück und das den Pistolen zugewandte Oberflächenprofil Einfluss nehmen, gibt in der Regel nur der experimentelle Versuch hinreichend Aufschluss über das zu erwartende Ergebnis.
Voraussetzung für ein gleichbleibendes Lackierergebnis ist eine konstante Dosierung des Pulvers zu den Pistolen und eine ausreichende Aufladung. Eine Messung bzw. Kontrolle der Pulverförderung ist bisher sehr aufwändig. Eine Ausnahme bildet die Messung des Aufladestroms bei Pistolen mit Triboaufladung, da hier bei konstantem Luft volumenstrom der Ableitstrom der Tribopistole eine pulverspezifische Maßzahl für den Pulverausstoß ist.
Bei Verfahren mit Rückgewinnung ist auch die Veränderung von Frisch- zu Kreislaufpulver bei den Beschichtungsversuchen zu berücksichtigen. Bild zeigt mögliche Anordnungen von Sprühgeräten und Bild ist die starre Mehrfachanordnung von Sprühpistolen zur Beschichtung der Karosserie zu sehen.
Die Pulverbeschichtung ist ein weit verbreitetes Verfahren zur Oberflächenveredelung, das sich durch seine umweltfreundlichen Eigenschaften und Langlebigkeit der Beschichtung auszeichnet. Im Gegensatz zu herkömmlichen flüssigen Beschichtungen werden bei der Pulverbeschichtung trockene Pulverpartikel elektrostatisch auf die Oberfläche eines Werkstücks aufgebracht. Anschließend wird das Pulver in einem Ofen erhitzt, wodurch es schmilzt und eine gleichmäßige, dauerhafte Beschichtung bildet.
Vorteile der Pulverbeschichtung umfassen:
- Umweltfreundlichkeit: Keine Lösungsmittel und geringere Emissionen von flüchtigen organischen Verbindungen (VOC).
- Effizienz: Hohe Materialausnutzung und weniger Abfall.
- Robustheit: Gute Beständigkeit gegen chemische, mechanische und Witterungseinflüsse.
Pulverbeschichtungsanlagen

Pulverbeschichtungsanlagen sind zentraler Bestandteil des Pulverbeschichtungsprozesses und umfassen die komplette Infrastruktur, die zur Anwendung von Pulverbeschichtungen erforderlich ist. Diese Anlagen sind in verschiedenen Größen und Ausführungen erhältlich, um unterschiedlichen industriellen Anforderungen gerecht zu werden.
Typen von Pulverbeschichtungsanlagen:
- Manuelle Pulverbeschichtungsanlagen:
Ideal für kleinere Betriebe oder spezialisierte Anwendungen, bei denen Flexibilität gefordert ist. Sie bestehen aus einer Pulverkabine, einem Pulvergerät und einem Einbrennofen. - Halbautomatische Anlagen:
Kombinieren manuelle und automatische Prozesse, um eine höhere Effizienz bei mittleren Produktionsvolumina zu erreichen. Diese Anlagen bieten eine gute Balance zwischen Flexibilität und Automatisierung. - Vollautomatische Pulverbeschichtungsanlagen:
Entwickelt für Großserienproduktionen. Diese Anlagen sind vollständig automatisiert und beinhalten Fördersysteme, automatische Pistolen und integrierte Steuerungssysteme, um hohe Produktionsgeschwindigkeiten und gleichbleibende Qualität zu gewährleisten.
Pulverkabinen
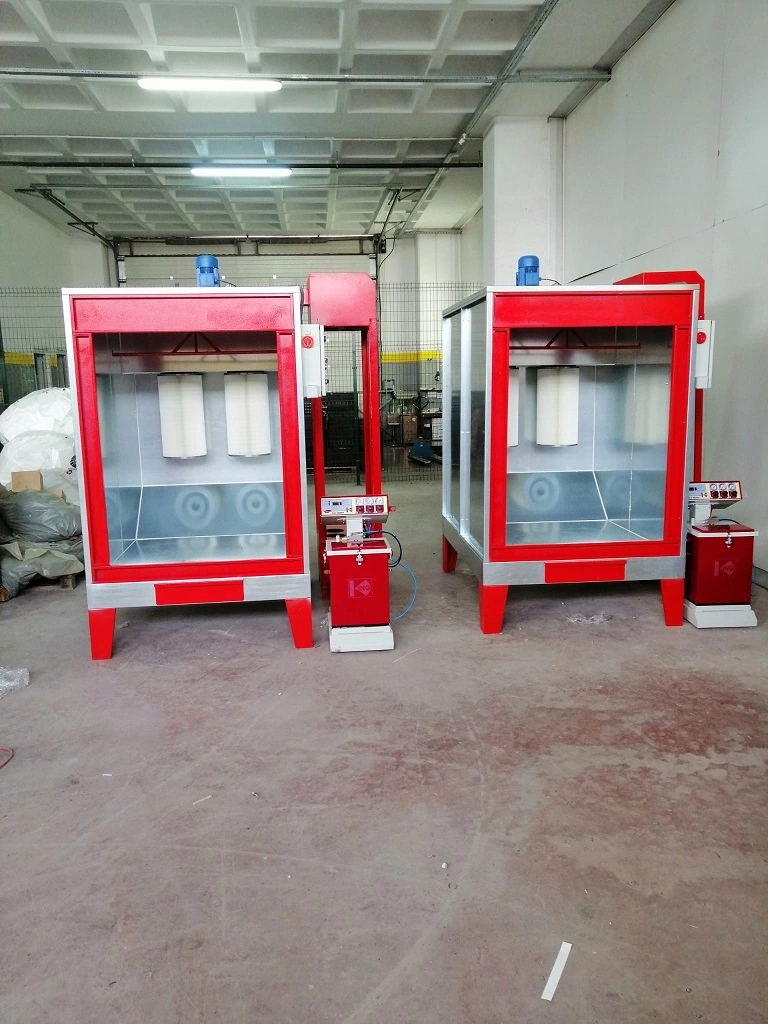
Pulverkabinen sind spezielle Räume oder Gehäuse, in denen der Pulverbeschichtungsprozess stattfindet. Sie spielen eine entscheidende Rolle bei der Gewährleistung einer sauberen und kontrollierten Umgebung für die Pulverbeschichtung.
Typen von Pulverkabinen:
- Offene Kabinen:
Diese Kabinen sind ideal für kleine bis mittlere Anwendungen. Sie bieten einen offenen Zugang für den Bediener, sind jedoch weniger effektiv bei der Kontrolle von Overspray. - Geschlossene Kabinen:
Bieten eine kontrollierte Umgebung und minimieren Overspray durch integrierte Luftführungssysteme. Geschlossene Kabinen sind in der Regel effizienter und sicherer. - Selbstreinigende Kabinen:
Ausgestattet mit automatischen Reinigungssystemen, die den Farbwechsel und die Wartung erleichtern. Diese Kabinen sind besonders nützlich in Anwendungen mit häufigem Farbwechsel.
Sicherheits- und Umweltaspekte: Pulverkabinen sind so konzipiert, dass sie die Sicherheit der Bediener gewährleisten und die Umweltbelastung minimieren. Dazu gehören Belüftungssysteme, Filter zur Partikelabscheidung und Schutzvorrichtungen, die den Kontakt mit dem Pulver verhindern.
Einbrennöfen
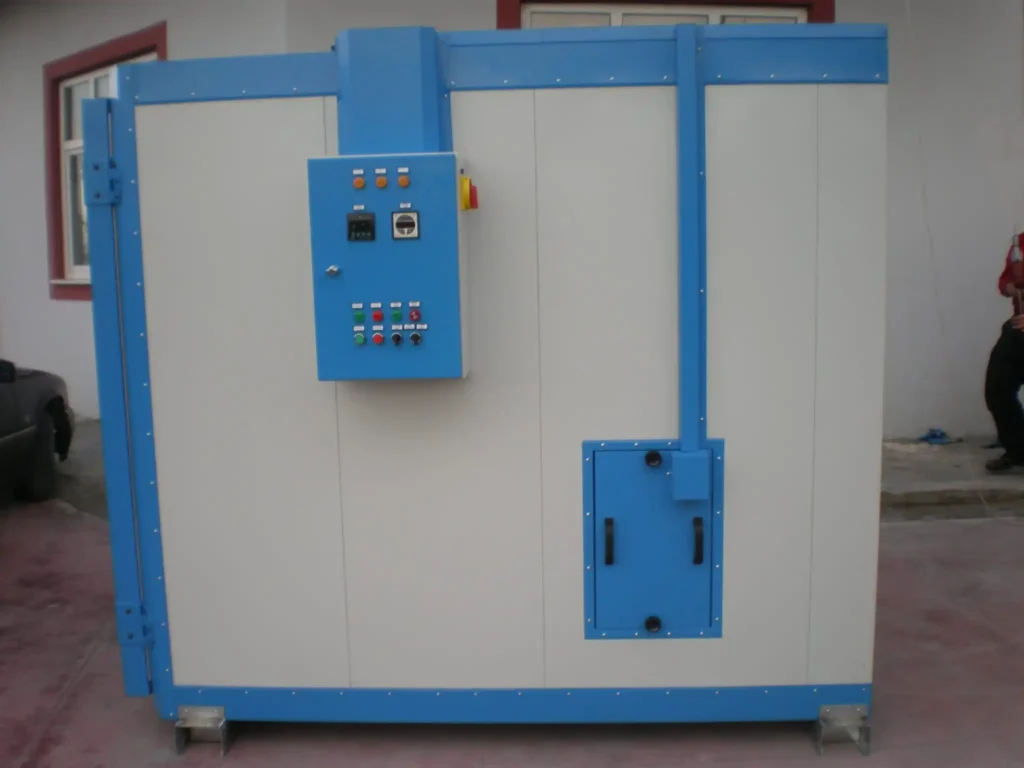
Der Einbrennofen ist ein unverzichtbarer Bestandteil des Pulverbeschichtungsprozesses, da er die notwendigen Temperaturen bereitstellt, um das aufgetragene Pulver zu einer harten, widerstandsfähigen Oberfläche zu verschmelzen.
Typen von Einbrennöfen:
- Chargenöfen:
Ideal für kleinere Produktionen oder variierende Chargengrößen. Diese Öfen sind flexibel und können unterschiedliche Teile gleichzeitig verarbeiten. - Durchlauföfen:
Entwickelt für kontinuierliche Produktionslinien, bei denen hohe Durchsatzraten erforderlich sind. Teile werden auf einem Förderband durch den Ofen transportiert, was eine konstante Verarbeitung ermöglicht.
Energieeffizienz und Temperatursteuerung: Moderne Einbrennöfen sind energieeffizient und bieten präzise Temperaturregelung, um gleichbleibende Beschichtungsqualität zu gewährleisten. Technologien wie Wärmerückgewinnungssysteme und fortschrittliche Isolierung tragen zur Reduzierung des Energieverbrauchs bei.
Pulvergeräte
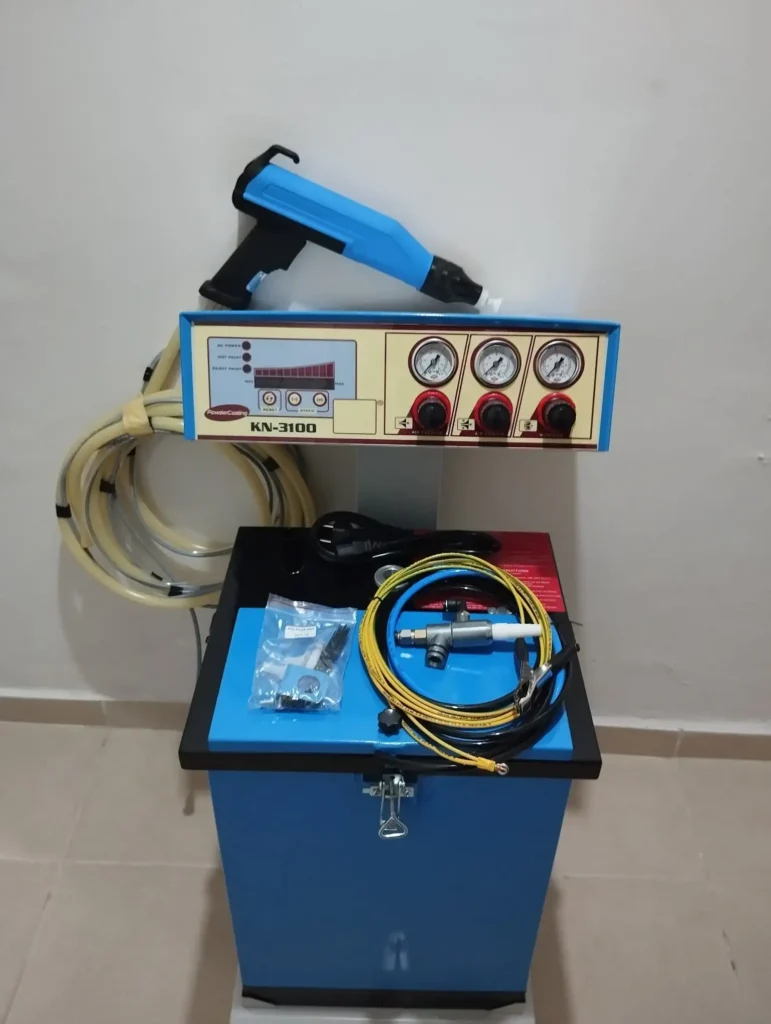
Pulvergeräte sind für die Anwendung der Pulverbeschichtung unerlässlich. Sie bestehen aus verschiedenen Komponenten, die zusammenarbeiten, um das Pulver gleichmäßig und effizient auf die Oberfläche des Werkstücks aufzubringen.
Arten von Pulvergeräten:
- Elektrostatische Sprühpistolen:
Verwenden Hochspannung, um Pulverpartikel elektrostatisch aufzuladen, was eine gleichmäßige Verteilung und Haftung auf dem Werkstück fördert. - Pulverförderer:
Transportieren das Pulver vom Vorratsbehälter zur Sprühpistole. Sie sind entscheidend für die Konsistenz und Effizienz des Beschichtungsprozesses.
Elektrostatik spielt eine zentrale Rolle bei der Pulverbeschichtung, da sie die Anziehungskraft zwischen den Pulverpartikeln und der Oberfläche erhöht und so eine gleichmäßige Beschichtung ermöglicht.
Auswahlkriterien für Pulvergeräte umfassen:
- Kompatibilität: Passend für die spezifischen Anforderungen der Anwendung.
- Flexibilität: Anpassungsfähigkeit an unterschiedliche Werkstückgrößen und -formen.
- Effizienz: Hohe Materialausnutzung und minimierter Pulververbrauch.
Automatische Pulverbeschichtungsanlagen
Automatische Pulverbeschichtungsanlagen bieten zahlreiche Vorteile, insbesondere in Bezug auf Effizienz und Konsistenz. Sie sind ideal für Großserienproduktionen und tragen zur Senkung der Betriebskosten bei.
Vorteile der Automatisierung:
- Erhöhte Produktivität: Automatische Systeme können kontinuierlich arbeiten und so die Produktionskapazität erheblich steigern.
- Gleichbleibende Qualität: Minimierung von Fehlern und Variabilität durch präzise Steuerung der Beschichtungsparameter.
- Kostenersparnis: Reduzierung der Arbeitskosten und des Materialverbrauchs durch optimierte Prozesse.
Komponenten und Funktionsweise:
- Fördersysteme: Transportieren Werkstücke automatisch durch den Beschichtungsprozess.
- Automatische Sprühpistolen: Verteilen das Pulver gleichmäßig auf den Werkstücken.
- Integrierte Steuerungssysteme: Überwachen und steuern alle Aspekte des Beschichtungsprozesses, einschließlich Temperatur, Sprühzeit und Pulvermenge.
Ersatzteile für Pulverbeschichtungsanlagen
Ersatzteile sind entscheidend für die Wartung und Langlebigkeit von Pulverbeschichtungsanlagen. Regelmäßige Wartung und der rechtzeitige Austausch von Verschleißteilen sind unerlässlich, um Ausfallzeiten zu minimieren und die Effizienz der Anlagen aufrechtzuerhalten.
Wichtige Ersatzteile und ihre Funktionen:
- Sprühdüsen: Stellen die gleichmäßige Verteilung des Pulvers sicher.
- Filter: Entfernen überschüssige Pulverpartikel aus der Kabinenluft.
- Förderbänder: Transportieren die Werkstücke durch den Beschichtungsprozess.
Wartung und Instandhaltung:
- Regelmäßige Inspektionen: Identifizieren potenzielle Probleme frühzeitig und ermöglichen rechtzeitige Reparaturen.
- Ersatzteilmanagement: Sicherstellung der Verfügbarkeit von Ersatzteilen zur Minimierung von Ausfallzeiten.
Zukunft der Pulverbeschichtungstechnologie
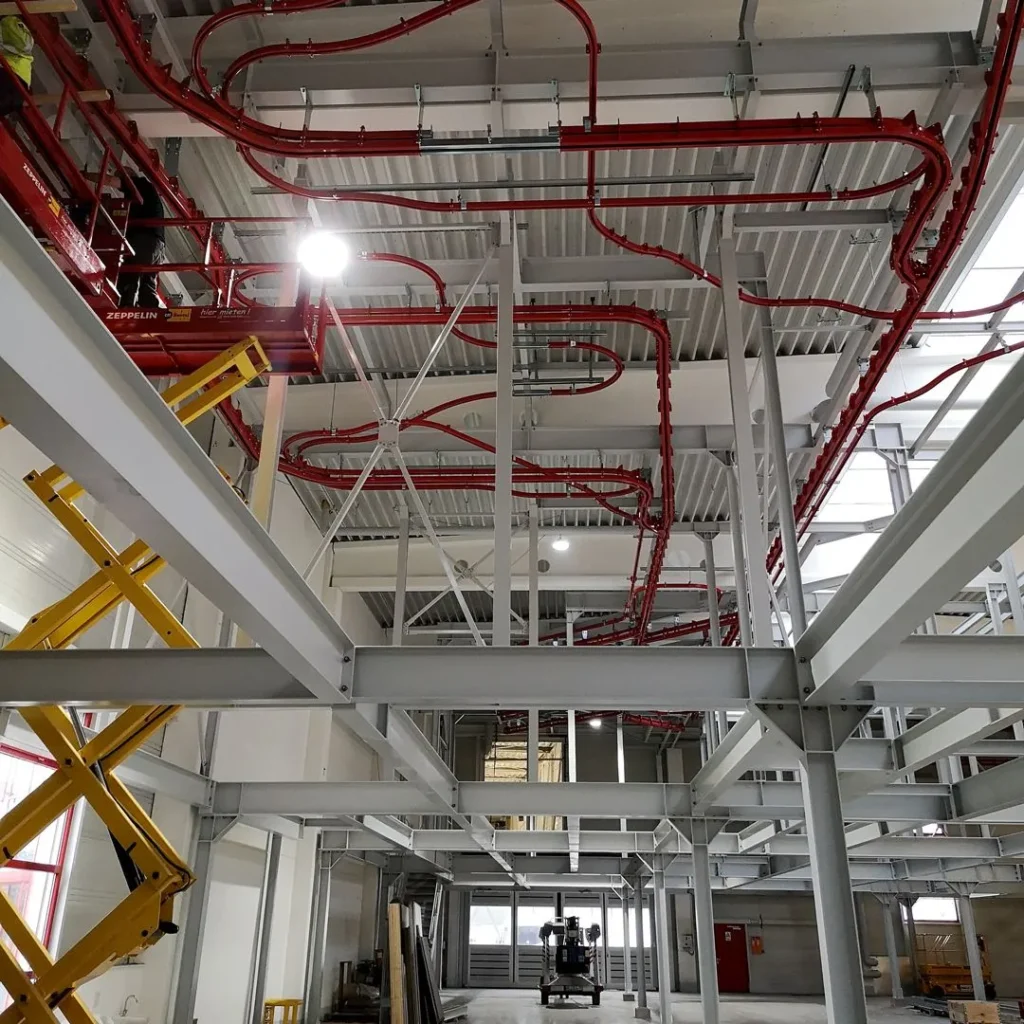
Die Pulverbeschichtungstechnologie entwickelt sich kontinuierlich weiter, um den steigenden Anforderungen der Industrie gerecht zu werden. Zu den wichtigsten Trends und Entwicklungen gehören:
- Nachhaltigkeit: Einsatz umweltfreundlicher Materialien und Verfahren zur Reduzierung des ökologischen Fußabdrucks.
- Fortschrittliche Materialien: Entwicklung neuer Pulverformeln, die verbesserte Eigenschaften wie Korrosionsbeständigkeit und UV-Stabilität bieten.
- Digitalisierung: Integration von IoT und datenbasierten Lösungen zur Optimierung des Beschichtungsprozesses und zur Verbesserung der Qualitätssicherung.
Fazit
Pulverbeschichtungsanlagen und ihre Komponenten sind ein wesentlicher Bestandteil moderner Produktionsprozesse. Sie bieten eine umweltfreundliche, effiziente und langlebige Lösung für die Oberflächenveredelung. Durch die ständige Weiterentwicklung der Technologie und den Einsatz von Automatisierung können Unternehmen ihre Effizienz steigern und gleichzeitig die Qualität ihrer Produkte sicherstellen.
Ich hoffe, dieser umfassende Überblick über Pulverbeschichtungsanlagen und verwandte Komponenten ist hilfreich. Wenn Sie weitere Informationen oder spezifische Details zu einem bestimmten Abschnitt wünschen, lassen Sie es mich bitte wissen!
Wie lange hält Pulverbeschichtung?
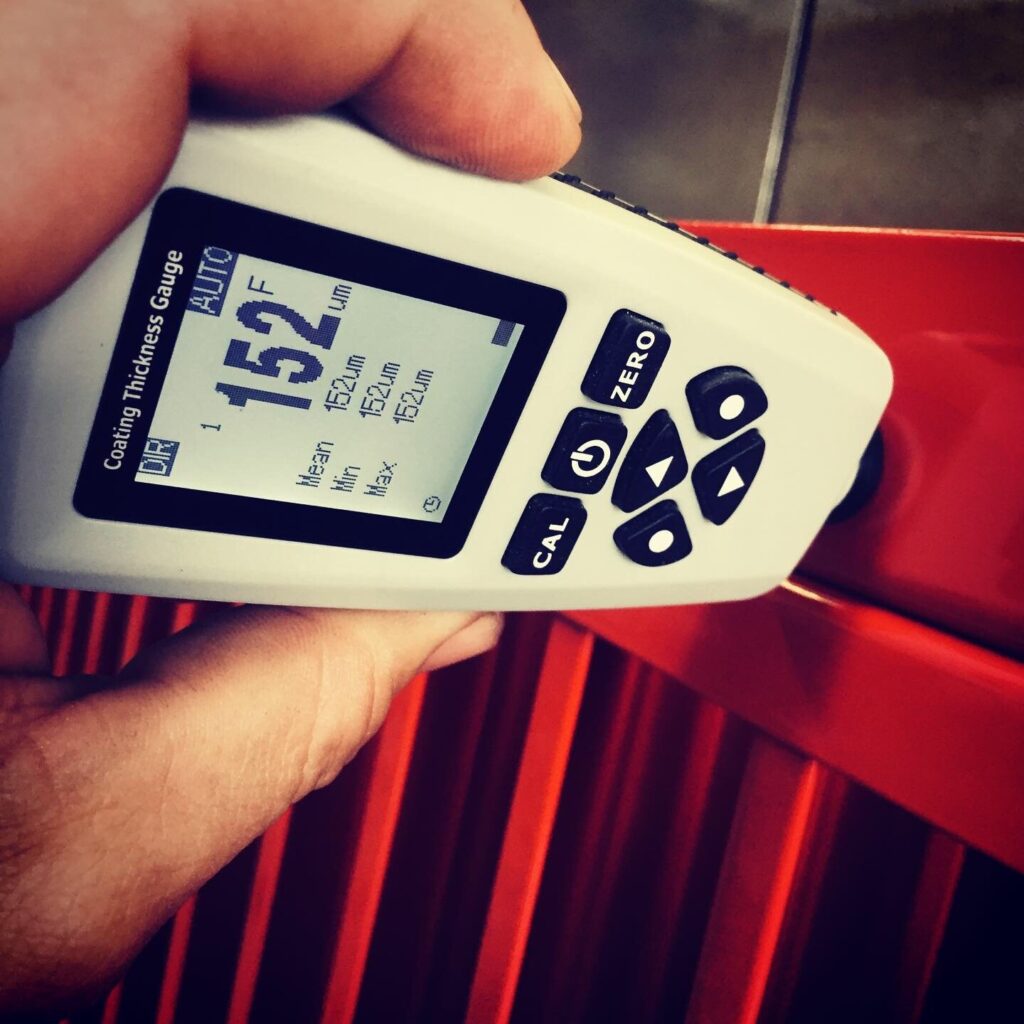
Die Haltbarkeit einer Pulverbeschichtung kann je nach Anwendung, Umgebung und Qualität der Beschichtung stark variieren. Hier sind einige Faktoren, die die Lebensdauer einer Pulverbeschichtung beeinflussen können:
Faktoren, die die Haltbarkeit beeinflussen:
- Qualität des Pulvers:
- Pulverformulierung: Hochwertige Pulverlacke bieten in der Regel eine längere Haltbarkeit und bessere Widerstandsfähigkeit gegen Umwelteinflüsse.
- UV-Stabilität: Speziell formulierte Pulverlacke mit UV-Schutz verlängern die Lebensdauer bei Anwendungen im Freien.
- Vorbereitung der Oberfläche:
- Reinigung: Eine gründliche Reinigung der Oberfläche vor der Beschichtung ist entscheidend, um eine gute Haftung des Pulvers zu gewährleisten.
- Vorbehandlung: Verfahren wie das Phosphatieren oder Sandstrahlen verbessern die Haftung und Korrosionsbeständigkeit.
- Bedingungen der Anwendung:
- Innen- vs. Außenanwendung: Pulverbeschichtungen im Innenbereich können Jahrzehnte halten, während Beschichtungen im Außenbereich stärker durch UV-Strahlung, Feuchtigkeit und Temperaturschwankungen beansprucht werden.
- Mechanische Belastung: Starke mechanische Belastungen oder Abnutzung können die Lebensdauer der Beschichtung verkürzen.
- Betriebsumgebung:
- Korrosive Umgebungen: In Industriegebieten oder maritimen Umgebungen kann die Lebensdauer aufgrund der erhöhten Korrosionsgefahr kürzer sein.
- Witterungseinflüsse: Regionen mit extremen Wetterbedingungen können die Lebensdauer der Pulverbeschichtung verkürzen.
- Beschichtungsdicke:
- Eine angemessene Schichtdicke ist wichtig, um eine gleichmäßige Abdeckung und ausreichenden Schutz zu gewährleisten.
Typische Lebensdauer
- Innenanwendungen:
Pulverbeschichtungen, die in Innenbereichen aufgebracht werden, können oft 15-20 Jahre oder länger halten, da sie weniger extremen Bedingungen ausgesetzt sind. - Außenanwendungen:
Bei Außenanwendungen hängt die Lebensdauer stark von den Umweltbedingungen ab, kann jedoch typischerweise zwischen 5 und 10 Jahren liegen. Hochwertige Pulverbeschichtungen, die speziell für den Außenbereich entwickelt wurden, können bis zu 15 Jahre oder länger halten, wenn sie regelmäßig gewartet werden. - Industrieanwendungen:
In industriellen Anwendungen, die häufig aggressiven Chemikalien oder starker mechanischer Beanspruchung ausgesetzt sind, kann die Lebensdauer kürzer sein und erfordert häufigere Inspektionen und Wartungen.
Verlängerung der Haltbarkeit
Um die Lebensdauer der Pulverbeschichtung zu maximieren, sind folgende Maßnahmen empfehlenswert:
- Regelmäßige Inspektion und Wartung: Frühe Erkennung von Schäden und rechtzeitige Reparaturen können die Haltbarkeit erheblich verlängern.
- Vermeidung von physikalischen Schäden: Sorgfältiger Umgang mit beschichteten Oberflächen reduziert das Risiko von Kratzern und Abplatzungen.
- Schutz vor chemischen Einflüssen: Vermeidung von Kontakt mit aggressiven Chemikalien und Reinigungsmitteln, die die Beschichtung angreifen könnten.
Fazit
Die Pulverbeschichtung ist eine langlebige und widerstandsfähige Methode zur Oberflächenveredelung, die bei richtiger Anwendung und Wartung viele Jahre halten kann. Die tatsächliche Lebensdauer hängt jedoch von zahlreichen Faktoren ab, einschließlich der Qualität des Pulvers, der Vorbereitung der Oberfläche und den Umgebungsbedingungen, denen die beschichteten Teile ausgesetzt sind.
Wartungstipps für Anlagen
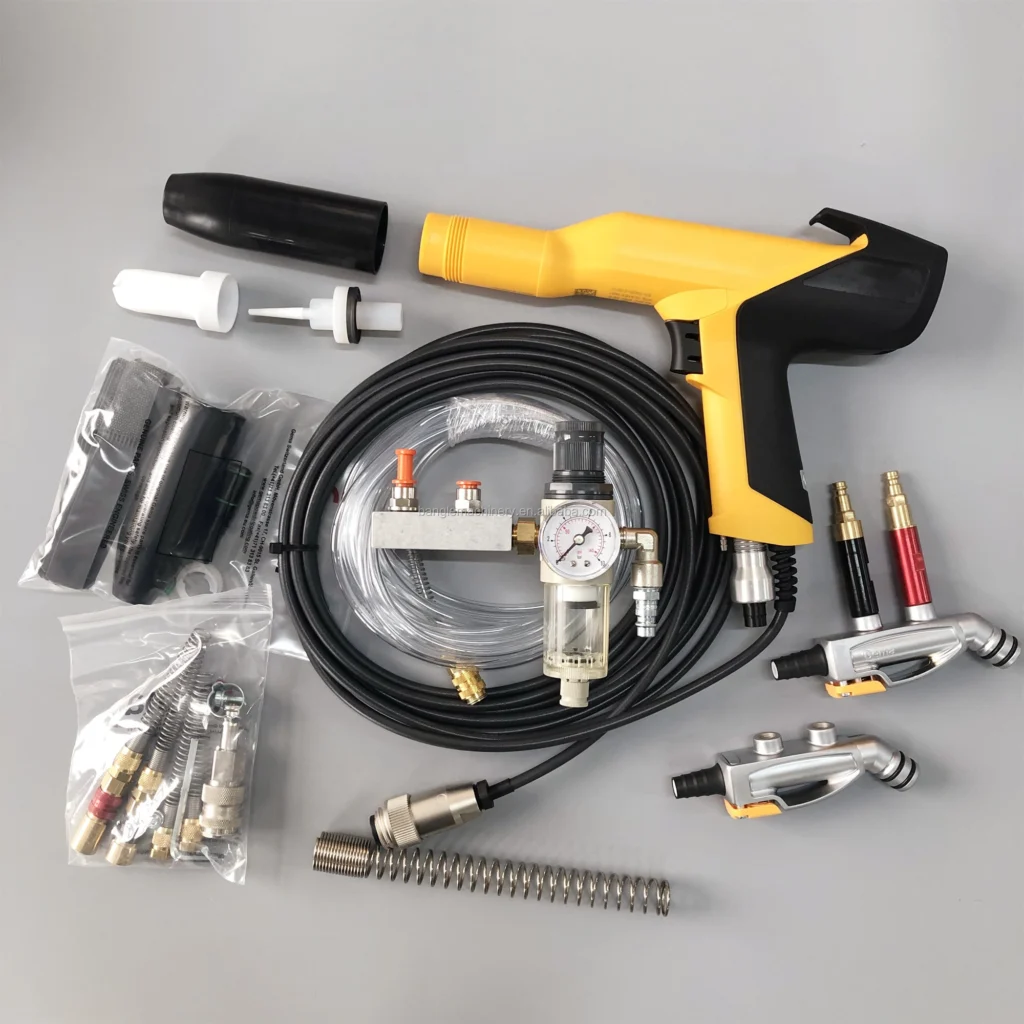
Um die Langlebigkeit und Effizienz von Pulverbeschichtungsanlagen zu gewährleisten, ist eine regelmäßige Wartung entscheidend. Hier sind einige Wartungstipps, die Ihnen helfen, die Leistung Ihrer Anlagen zu maximieren und Ausfallzeiten zu minimieren:
1. Allgemeine Inspektion
- Regelmäßige Überprüfungen: Führen Sie wöchentliche oder monatliche Inspektionen der gesamten Anlage durch, um sicherzustellen, dass alle Komponenten ordnungsgemäß funktionieren.
- Sichtprüfung: Überprüfen Sie auf sichtbare Abnutzung, Schäden oder lose Teile, die die Funktion beeinträchtigen könnten.
2. Pulverkabinen
- Filterwartung:
- Reinigung oder Austausch: Reinigen oder ersetzen Sie die Filter regelmäßig, um eine effiziente Luftführung und Partikelabscheidung zu gewährleisten.
- Filtertypen beachten: Verwenden Sie immer die vom Hersteller empfohlenen Filtertypen.
- Kabinenreinigung:
- Regelmäßige Reinigung: Halten Sie die Kabinenwände und -böden sauber, um Ansammlungen von überschüssigem Pulver zu vermeiden.
- Staubabsaugung: Stellen Sie sicher, dass die Absauganlage regelmäßig geleert und gewartet wird, um eine optimale Funktion zu gewährleisten.
3. Einbrennöfen
- Temperaturüberwachung:
- Regelmäßige Kalibrierung: Überprüfen Sie regelmäßig die Kalibrierung der Temperatursteuerung, um eine gleichbleibende Beschichtungsqualität sicherzustellen.
- Thermoelemente prüfen: Überprüfen Sie die Thermoelemente auf Genauigkeit und Funktionstüchtigkeit.
- Ofenreinigung:
- Innenreinigung: Entfernen Sie regelmäßig Rückstände und Ablagerungen im Inneren des Ofens, um die Effizienz zu erhalten.
- Dichtungen überprüfen: Überprüfen Sie die Dichtungen an Türen und Durchgängen auf Abnutzung und tauschen Sie sie bei Bedarf aus.
4. Pulvergeräte
- Sprühpistolenwartung:
- Düsenreinigung: Reinigen Sie die Düsen regelmäßig, um Verstopfungen und ungleichmäßige Sprühmuster zu vermeiden.
- Ersatzteile prüfen: Halten Sie Ersatzdüsen und andere Verschleißteile bereit, um Ausfallzeiten zu minimieren.
- Pulverförderer:
- Reinigungsintervalle: Reinigen Sie die Pulverförderer, um Blockaden zu verhindern und eine gleichmäßige Pulverzufuhr zu gewährleisten.
- Antriebssysteme warten: Überprüfen Sie regelmäßig die Antriebe und Lager auf Verschleiß und tauschen Sie sie bei Bedarf aus.
5. Fördersysteme
- Kettenspannung und Schmierung:
- Spannung überprüfen: Kontrollieren Sie die Spannung der Förderketten und passen Sie sie bei Bedarf an, um einen reibungslosen Betrieb zu gewährleisten.
- Schmierung: Schmieren Sie alle beweglichen Teile regelmäßig, um Verschleiß zu minimieren.
- Lagerwartung:
- Überprüfung der Lager: Überprüfen Sie die Lager auf Abnutzung und tauschen Sie sie bei Bedarf aus.
- Schmiermittel verwenden: Verwenden Sie die vom Hersteller empfohlenen Schmiermittel, um die Lebensdauer der Lager zu verlängern.
6. Automatisierte Systeme
- Steuerungssysteme:
- Software-Updates: Halten Sie die Software der Steuerungssysteme auf dem neuesten Stand, um Effizienz und Sicherheit zu gewährleisten.
- Fehlerprotokollierung: Überwachen Sie Fehlerprotokolle, um potenzielle Probleme frühzeitig zu erkennen.
- Sensoren und Aktoren:
- Funktionsprüfung: Überprüfen Sie regelmäßig die Sensoren und Aktoren auf ihre Funktionsfähigkeit und ersetzen Sie defekte Teile.
- Kalibrierung: Führen Sie regelmäßige Kalibrierungen durch, um die Genauigkeit der automatisierten Systeme zu gewährleisten.
7. Ersatzteile und Lagerhaltung
- Ersatzteilmanagement:
- Bestandskontrolle: Führen Sie eine genaue Bestandskontrolle der Ersatzteile, um Ausfallzeiten durch fehlende Teile zu vermeiden.
- Qualität der Ersatzteile: Verwenden Sie stets hochwertige Originalersatzteile, um die Funktionalität der Anlagen zu gewährleisten.
8. Schulung des Personals
- Regelmäßige Schulungen: Schulen Sie Ihr Personal regelmäßig in der Bedienung und Wartung der Anlagen, um Bedienfehler zu vermeiden und die Sicherheit zu erhöhen.
- Notfallverfahren: Stellen Sie sicher, dass alle Mitarbeiter mit den Notfallverfahren vertraut sind, um im Falle eines Ausfalls schnell reagieren zu können.
9. Dokumentation
- Wartungsprotokolle: Führen Sie detaillierte Wartungsprotokolle, um den Wartungsverlauf und alle durchgeführten Arbeiten zu dokumentieren.
- Checklisten verwenden: Nutzen Sie Wartungschecklisten, um sicherzustellen, dass alle erforderlichen Maßnahmen regelmäßig durchgeführt werden.
Fazit
Durch die Einhaltung dieser Wartungstipps können Sie die Effizienz und Lebensdauer Ihrer Pulverbeschichtungsanlagen maximieren. Eine gut gewartete Anlage führt zu einer höheren Produktqualität, weniger Ausfallzeiten und einer längeren Lebensdauer der Geräte. Regelmäßige Wartung ist eine Investition, die sich durch verbesserte Leistung und geringere Betriebskosten auszahlt.
Automatisierungsoptionen
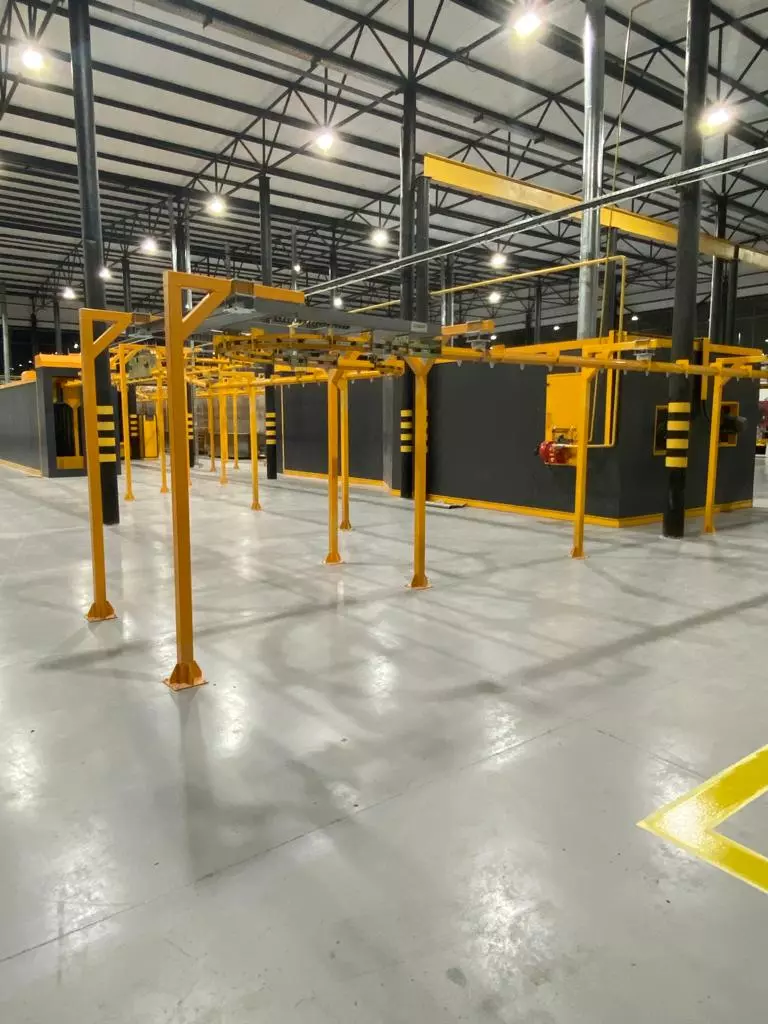
Automatisierungsoptionen in der Pulverbeschichtung bieten zahlreiche Vorteile, darunter erhöhte Effizienz, gleichbleibende Qualität und reduzierte Betriebskosten. Im Folgenden werden verschiedene Automatisierungsoptionen erläutert, die in modernen Pulverbeschichtungsanlagen eingesetzt werden können:
1. Automatische Sprühsysteme
Automatische Sprühsysteme sind eine wesentliche Komponente für die Automatisierung der Pulverbeschichtung und bieten präzise und gleichmäßige Beschichtungen. Sie bestehen aus mehreren automatisierten Sprühpistolen, die auf robotergesteuerten Armen montiert sind.
- Robotergestützte Sprühpistolen:
Diese Pistolen sind an Roboterarmen befestigt, die programmierbar sind, um komplexe Bewegungsmuster auszuführen und die Sprühwinkel für unterschiedliche Werkstückgeometrien zu optimieren. - Pulvermengensteuerung:
Automatisierte Systeme ermöglichen die genaue Steuerung der Pulvermengen, was zu einer gleichmäßigen Schichtdicke und weniger Abfall führt. - Adaptive Technologie:
Moderne Systeme nutzen Sensoren, um die Werkstückgeometrie in Echtzeit zu erfassen und die Sprühmuster entsprechend anzupassen.
2. Fördersysteme
Automatisierte Fördersysteme transportieren die Werkstücke durch die verschiedenen Phasen des Beschichtungsprozesses und tragen dazu bei, den Durchsatz zu erhöhen.
- Overhead-Fördersysteme:
Diese Systeme transportieren die Teile über Kopf durch die Kabinen und Öfen, was den Bodenraum frei hält und die Effizienz erhöht. - Ketten- und Schienensysteme:
Förderbänder und Schienensysteme bieten Flexibilität bei der Gestaltung der Produktionslinie und können an unterschiedliche Anforderungen angepasst werden. - Variable Geschwindigkeit:
Einige Fördersysteme ermöglichen die Anpassung der Geschwindigkeit je nach Werkstückgröße und Prozessanforderungen.
3. Einbrennöfen mit Automatisierung
Einbrennöfen können durch Automatisierung effizienter und präziser arbeiten, was die Qualität der Beschichtung verbessert.
- Automatisierte Temperaturregelung:
Intelligente Steuerungssysteme passen die Ofentemperatur in Echtzeit an, um die optimale Aushärtung der Pulverbeschichtung zu gewährleisten. - Zeitschaltuhren und Sensoren:
Integrierte Timer und Sensoren helfen dabei, den Aushärtungsprozess genau zu überwachen und die Energieeffizienz zu maximieren. - Automatische Türsteuerung:
Automatische Türen öffnen und schließen sich synchron mit dem Ein- und Ausgang der Werkstücke, um den Wärmeverlust zu minimieren.
4. Qualitätskontrollsysteme
Automatisierte Qualitätskontrollsysteme sorgen dafür, dass die Beschichtungen den festgelegten Standards entsprechen und verringern den Bedarf an manueller Inspektion.
- Visuelle Inspektionssysteme:
Kameras und Bildverarbeitungstechnologien prüfen die Beschichtungsqualität und identifizieren sofort Fehler oder Unregelmäßigkeiten. - Schichtdickenmessung:
Berührungslose Messsysteme können die Dicke der Pulverbeschichtung präzise messen und Daten zur weiteren Analyse bereitstellen. - Echtzeit-Datenanalyse:
Datenerfassungs- und Analysesysteme ermöglichen die Überwachung des gesamten Prozesses und helfen bei der Identifizierung von Optimierungspotenzialen.
5. Software-Integration
Softwarelösungen spielen eine entscheidende Rolle bei der Automatisierung, indem sie verschiedene Systeme integrieren und den Betrieb effizienter gestalten.
- Leitsysteme (SCADA):
Supervisory Control and Data Acquisition (SCADA) Systeme bieten eine zentrale Steuerung und Überwachung aller Anlagenkomponenten. - IoT-Integration:
Internet of Things (IoT) Technologien ermöglichen die Vernetzung der Geräte und die Fernüberwachung sowie -steuerung der Prozesse. - Produktionsmanagement-Software:
Diese Softwarelösungen helfen bei der Planung und Verwaltung von Produktionsabläufen, indem sie Daten aus verschiedenen Quellen konsolidieren.
6. Automatisierte Farbwechsel
Für Betriebe, die häufige Farbwechsel durchführen müssen, bieten automatisierte Farbwechselsysteme erhebliche Vorteile.
- Schneller Farbwechsel:
Automatisierte Systeme reduzieren die Zeit, die für den Farbwechsel benötigt wird, was die Produktionsausfallzeiten minimiert. - Minimierung von Pulverabfall:
Durch den Einsatz von selbstreinigenden Sprühpistolen und Kabinen wird der Pulververbrauch optimiert.
7. Wartungsautomatisierung
Auch die Wartung von Anlagen kann automatisiert werden, um die Betriebszeiten zu maximieren und unvorhergesehene Ausfälle zu reduzieren.
- Vorausschauende Wartung:
Sensoren überwachen den Zustand der Anlagenkomponenten in Echtzeit und prognostizieren Wartungsbedarf, bevor Probleme auftreten. - Automatisierte Fehlerdiagnose:
Diagnose-Tools identifizieren Probleme und bieten Lösungsvorschläge, die die Wartungseffizienz erhöhen.
Vorteile der Automatisierung in der Pulverbeschichtung
- Erhöhte Produktivität:
Automatisierte Systeme ermöglichen eine höhere Produktionsrate bei gleichzeitig konsistenter Qualität. - Geringere Betriebskosten:
Durch die Optimierung des Materialverbrauchs und die Reduzierung des Arbeitsaufwands senken Automatisierungssysteme die Betriebskosten. - Verbesserte Qualität:
Gleichbleibende Beschichtungsqualität und reduzierte Fehlerraten durch präzise Steuerung und Überwachung. - Umweltfreundlichkeit:
Automatisierung reduziert den Pulverabfall und verbessert die Energieeffizienz der Anlagen.
Fazit
Automatisierungsoptionen in der Pulverbeschichtung bieten eine Vielzahl von Vorteilen und sind entscheidend für die Steigerung der Effizienz und Qualität in der Produktion. Die Integration von Robotik, fortschrittlicher Software und intelligenter Steuerung ermöglicht es Unternehmen, wettbewerbsfähig zu bleiben und gleichzeitig die Umweltbelastung zu reduzieren. Die Entscheidung für die richtige Kombination von Automatisierungstechnologien hängt von den spezifischen Anforderungen und Zielen des Unternehmens ab.
Automatisierungsvorteile

Automatisierung in der Pulverbeschichtungsindustrie bietet zahlreiche Vorteile, die sowohl die Effizienz als auch die Qualität der Produktion steigern können. Hier sind die wichtigsten Vorteile der Automatisierung erklärt:
1. Erhöhte Effizienz
- Höhere Produktionsraten:
Automatisierte Systeme können kontinuierlich ohne Unterbrechungen arbeiten, was zu höheren Durchsatzraten führt. Dies bedeutet, dass mehr Teile in kürzerer Zeit beschichtet werden können, was die Gesamtproduktivität steigert. - Schnellere Zykluszeiten:
Automatisierung reduziert die Bearbeitungszeit pro Werkstück erheblich, da Maschinen schneller und präziser arbeiten können als Menschen. - Minimierte Stillstandszeiten:
Automatisierte Wartung und vorausschauende Diagnose minimieren ungeplante Ausfallzeiten, was die Verfügbarkeit der Anlage erhöht.
2. Gleichbleibende Qualität
- Präzise Beschichtungsanwendung:
Automatisierte Sprühsysteme sorgen für eine gleichmäßige Schichtdicke und reduzieren menschliche Fehler, die zu Qualitätsabweichungen führen können. - Wiederholgenauigkeit:
Automatisierte Systeme wiederholen dieselben Bewegungen und Prozesse mit hoher Genauigkeit, was zu konsistenter Produktqualität führt, unabhängig von der Produktionsmenge. - Echtzeit-Qualitätskontrolle:
Durch den Einsatz von Sensoren und Kameras können automatisierte Systeme kontinuierlich die Qualität der Beschichtung überwachen und sofort Anpassungen vornehmen.
3. Reduzierte Betriebskosten
- Materialeinsparungen:
Automatisierung optimiert den Einsatz von Pulvermaterialien, wodurch Abfall reduziert und die Materialnutzung verbessert wird. - Geringere Arbeitskosten:
Der Bedarf an manueller Arbeit wird verringert, was die Personalkosten senkt. Mitarbeiter können in anderen Bereichen eingesetzt werden, wo menschliches Urteilsvermögen und Kreativität erforderlich sind. - Energieeffizienz:
Automatisierte Systeme sind oft energieeffizienter, da sie optimierte Prozesse und Technologien verwenden, um den Energieverbrauch zu minimieren.
4. Verbesserte Sicherheit
- Reduzierte Exposition gegenüber Gefahrenstoffen:
Automatisierung minimiert den direkten Kontakt der Mitarbeiter mit potenziell gefährlichen Chemikalien und Pulvern, was das Risiko von Gesundheitsproblemen reduziert. - Sicherheitsüberwachung:
Automatisierte Anlagen sind häufig mit Sicherheitssensoren ausgestattet, die Unfälle verhindern und im Notfall schnelle Reaktionen ermöglichen. - Ergonomische Vorteile:
Mitarbeiter müssen weniger körperlich anspruchsvolle Aufgaben erledigen, was das Risiko von arbeitsbedingten Verletzungen verringert.
5. Flexibilität und Anpassungsfähigkeit
- Schnelle Anpassung an Produktänderungen:
Automatisierte Systeme können schnell neu programmiert werden, um auf Änderungen im Produktdesign oder der Produktion umzustellen, was die Flexibilität erhöht. - Einfache Integration neuer Technologien:
Durch modulare Designs können neue Technologien oder Prozesse problemlos in bestehende Systeme integriert werden. - Vielfältige Anwendungsmöglichkeiten:
Automatisierung kann an eine Vielzahl von Werkstückgrößen, -formen und -materialien angepasst werden, was die Vielseitigkeit der Produktion erhöht.
6. Nachhaltigkeit und Umweltfreundlichkeit
- Reduzierung von Abfall und Emissionen:
Automatisierte Systeme optimieren den Materialverbrauch und reduzieren den Überspray, was zu weniger Abfall und geringeren Emissionen führt. - Ressourceneffizienz:
Durch die optimale Nutzung von Energie und Materialien tragen automatisierte Systeme zu nachhaltigeren Produktionsprozessen bei. - Verbesserte Umweltbilanz:
Unternehmen können ihre Umweltziele leichter erreichen und ihre ökologische Verantwortung wahrnehmen.
7. Daten- und Prozessoptimierung
- Datengesteuerte Entscheidungsfindung:
Automatisierte Systeme sammeln kontinuierlich Daten, die zur Analyse und Optimierung der Produktionsprozesse verwendet werden können. - Prozessoptimierung durch IoT:
Internet of Things (IoT) Technologien ermöglichen die Echtzeitüberwachung und -steuerung von Prozessen, was die Effizienz und Transparenz erhöht. - Vorausschauende Wartung:
Durch die Analyse von Maschinendaten können Probleme frühzeitig erkannt und behoben werden, bevor sie zu größeren Ausfällen führen.
Fazit
Die Automatisierung in der Pulverbeschichtung bietet zahlreiche Vorteile, die sowohl die Effizienz als auch die Qualität der Produktion erheblich steigern. Durch den Einsatz modernster Technologien können Unternehmen ihre Betriebskosten senken, die Produktsicherheit erhöhen und gleichzeitig ihre Umweltbilanz verbessern. Die Investition in Automatisierungslösungen zahlt sich langfristig durch höhere Produktivität, verbesserte Qualität und größere Flexibilität aus. Unternehmen, die Automatisierungstechnologien integrieren, positionieren sich besser im Wettbewerb und sind in der Lage, schneller auf Marktveränderungen zu reagieren.
Beispiele für Automatisierung

Hier sind einige konkrete Beispiele für Automatisierung in der Pulverbeschichtungsindustrie, die verdeutlichen, wie moderne Technologien den Beschichtungsprozess optimieren und verbessern können:
1. Robotergesteuerte Sprühapplikationen
- Automatisierte Spritzroboter:
Diese Roboterarme sind mit elektrostatischen Sprühpistolen ausgestattet und können komplexe Bewegungsmuster programmieren, um Teile unterschiedlicher Formen und Größen effizient zu beschichten. Durch die Robotersteuerung wird eine gleichmäßige Schichtdicke erreicht, und es gibt weniger Overspray.Beispiel: In der Automobilindustrie werden Karosserieteile oft mit robotergestützten Sprühsystemen beschichtet, um eine gleichmäßige und hochwertige Oberfläche zu gewährleisten. Ein Unternehmen wie ABB Robotics bietet Lösungen, die auf die spezifischen Anforderungen der Automobilindustrie zugeschnitten sind.
2. Automatische Fördersysteme
- Overhead-Kettenförderer:
Diese Systeme transportieren die Teile durch verschiedene Prozessschritte wie Reinigung, Beschichtung und Aushärtung. Sie ermöglichen einen kontinuierlichen Produktionsfluss und minimieren manuelle Eingriffe.Beispiel: Bei der Herstellung von Metallmöbeln werden Teile oft auf Förderbändern bewegt, die sie durch alle Beschichtungsphasen führen. Unternehmen wie Nordson bieten komplexe Fördersysteme an, die an verschiedene Produktionslayouts angepasst werden können.
3. Automatisierte Farbwechselsysteme
- Schnellwechselkabinen:
Diese Kabinen sind darauf ausgelegt, den Farbwechselprozess zu beschleunigen. Sie verfügen über automatische Reinigungszyklen und programmierbare Steuerungen, die den Farbwechsel effizienter machen.Beispiel: In der Fahrradindustrie, wo häufig Farbvarianten angeboten werden, nutzen Hersteller automatisierte Systeme, um den Farbwechsel schnell durchzuführen, ohne die Produktion zu verlangsamen. Systeme von Gema Switzerland bieten automatische Farbwechseltechnologien, die in der Branche weit verbreitet sind.
4. Intelligente Einbrennöfen
- Automatisierte Temperatur- und Zeitsteuerung:
Einbrennöfen sind mit Sensoren ausgestattet, die die Temperatur und den Durchsatz in Echtzeit überwachen und anpassen, um die optimale Aushärtung der Beschichtung zu gewährleisten.Beispiel: In der Elektronikindustrie, wo präzise Temperaturkontrollen entscheidend sind, verwenden Hersteller automatisierte Öfen, um die empfindlichen Komponenten richtig zu behandeln. Unternehmen wie Despatch Industries bieten Öfen an, die auf solche spezifischen Anforderungen abgestimmt sind.
5. Echtzeit-Qualitätskontrollsysteme
- Vision-Systeme für die Inspektion:
Kameras und Bildverarbeitungstechnologien erfassen die Beschichtungsqualität in Echtzeit, erkennen Fehler und ermöglichen sofortige Korrekturmaßnahmen.Beispiel: In der Luftfahrtindustrie, wo höchste Qualitätsstandards gelten, werden Vision-Systeme eingesetzt, um die Beschichtungen auf Flugzeugteilen zu überprüfen. Anbieter wie Cognex bieten fortschrittliche Bildverarbeitungslösungen an, die in diesen Anwendungen genutzt werden.
6. Datenanalyse und IoT-Integration
- IoT-gestützte Prozessüberwachung:
Sensoren an verschiedenen Stellen der Produktionslinie sammeln Daten, die zur Optimierung des gesamten Beschichtungsprozesses genutzt werden können. IoT-Plattformen ermöglichen eine zentrale Überwachung und Anpassung der Systeme in Echtzeit.Beispiel: Ein Hersteller von landwirtschaftlichen Maschinen nutzt IoT-Daten, um die Effizienz der Pulverbeschichtungsanlage zu verbessern und Wartungszyklen zu optimieren. Unternehmen wie Siemens bieten umfassende IoT-Lösungen an, die solche Anwendungen unterstützen.
7. Vorausschauende Wartung
- Condition Monitoring:
Automatisierte Überwachungssysteme analysieren kontinuierlich den Zustand von Anlagenkomponenten und prognostizieren Wartungsbedarf, bevor Ausfälle auftreten.Beispiel: Ein Hersteller von Haushaltsgeräten implementiert vorausschauende Wartung, um die Lebensdauer seiner Beschichtungsanlagen zu verlängern und die Verfügbarkeit zu maximieren. Lösungen von GE Digital bieten solche Condition-Monitoring-Tools an.
8. Automatisierte Reinigungssysteme
- Selbstreinigende Kabinen:
Diese Kabinen verfügen über automatische Reinigungszyklen, die das Entfernen von Pulverrückständen und die Vorbereitung für den nächsten Durchgang erleichtern.Beispiel: In der Herstellung von Baukomponenten, die unterschiedliche Beschichtungen erfordern, helfen selbstreinigende Systeme, die Wechselzeiten zwischen den verschiedenen Pulverlacken zu verkürzen. Systeme von Wagner bieten effiziente Reinigungsoptionen, die in solchen Anwendungen zum Einsatz kommen.
Fazit
Automatisierung in der Pulverbeschichtungsindustrie bietet vielfältige Möglichkeiten, die Produktion zu optimieren und gleichzeitig die Qualität zu steigern. Durch den Einsatz von robotergesteuerten Sprühsystemen, automatisierten Fördersystemen, intelligenten Einbrennöfen und fortschrittlichen Überwachungs- und Wartungstechnologien können Unternehmen ihre Effizienz erhöhen und ihre Wettbewerbsfähigkeit verbessern. Die Investition in Automatisierungstechnologien ermöglicht es Unternehmen, sich schnell an Marktveränderungen anzupassen und gleichzeitig ihre Produktionskosten zu senken.
Komponenten einer Komplette Pulverbeschichtungsanlage
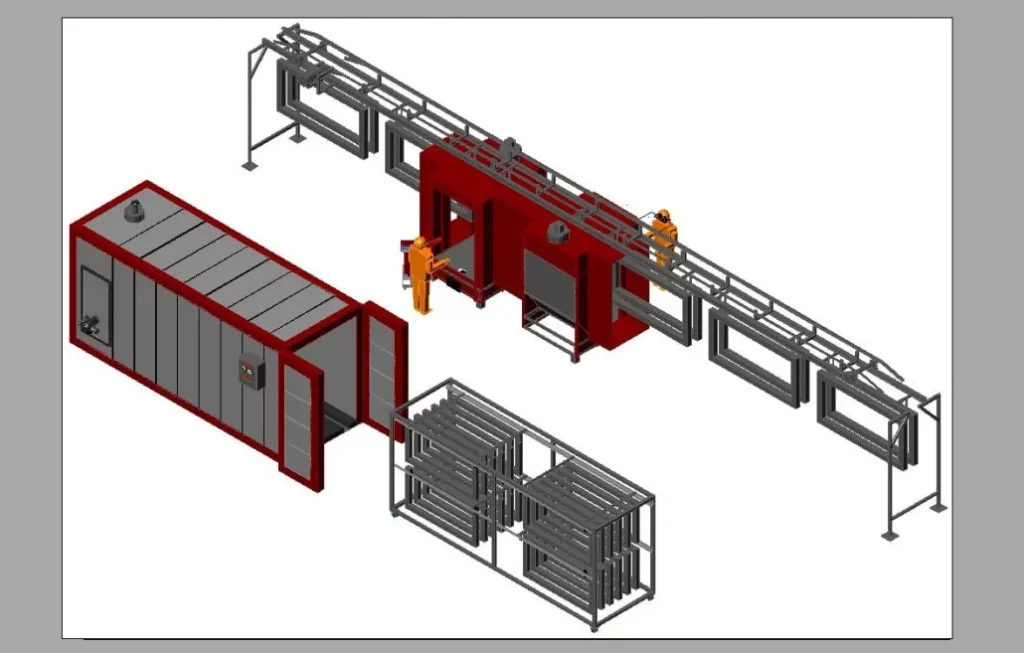
Eine komplette Pulverbeschichtungsanlage besteht aus mehreren wesentlichen Komponenten, die zusammenarbeiten, um eine effiziente und qualitativ hochwertige Beschichtung von Werkstücken zu gewährleisten. Hier sind die Hauptkomponenten einer solchen Anlage und ihre Funktionen:
1. Vorbehandlungssystem
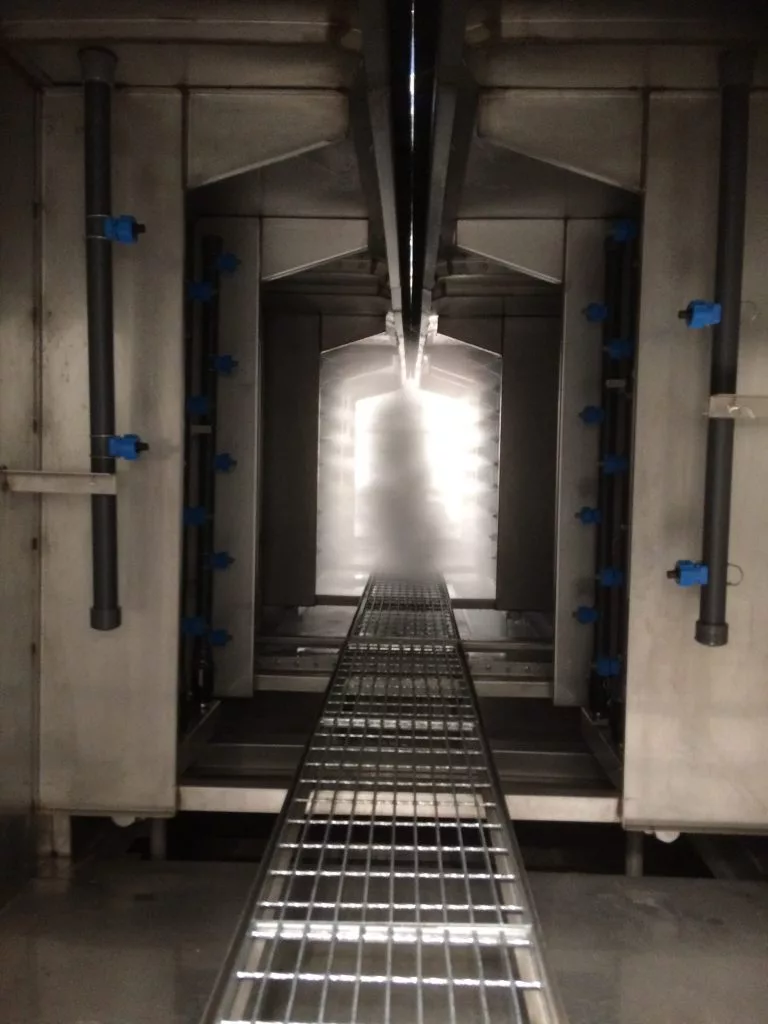
Die Vorbehandlung ist ein entscheidender Schritt, um sicherzustellen, dass die Oberfläche des Werkstücks sauber und bereit für die Beschichtung ist. Die Vorbehandlung verbessert die Haftung der Pulverbeschichtung und erhöht die Korrosionsbeständigkeit.
- Reinigungsstationen: Entfernen Öl, Fett, Staub und andere Verunreinigungen von der Oberfläche des Werkstücks.
- Phosphatier- oder Chromatierstationen: Bilden eine Schutzschicht, die die Haftung verbessert und die Korrosionsbeständigkeit erhöht.
- Spül- und Trocknungsstationen: Stellen sicher, dass das Werkstück frei von chemischen Rückständen und trocken ist, bevor es zur Beschichtung weitergeleitet wird.
2. Pulverkabinen
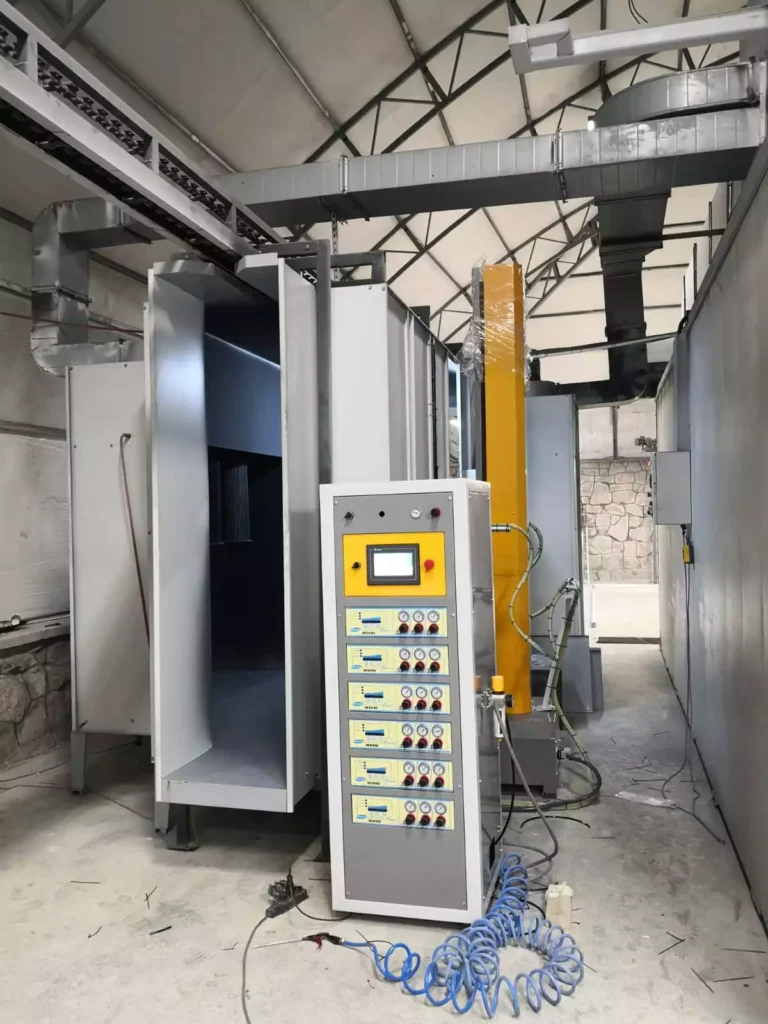
Die Pulverkabine ist der Bereich, in dem das Pulver elektrostatisch auf die Werkstücke aufgetragen wird. Sie ist so konzipiert, dass sie eine saubere und kontrollierte Umgebung bietet, um überschüssiges Pulver effizient zurückzugewinnen.
- Offene Kabinen: Geeignet für kleinere, manuelle Anwendungen, wo der Bediener direkten Zugang benötigt.
- Geschlossene Kabinen: Bieten eine kontrollierte Umgebung und sind effizienter bei der Kontrolle und Rückgewinnung von Overspray.
- Selbstreinigende Kabinen: Diese Kabinen verfügen über automatische Reinigungssysteme, die den Farbwechsel und die Wartung erleichtern.
3. Pulverauftragsgeräte

Diese Geräte sind für die eigentliche Anwendung des Pulvers auf die Werkstücke verantwortlich und bestehen aus verschiedenen Komponenten, die den Pulverauftrag optimieren.
- Elektrostatische Sprühpistolen: Laden die Pulverpartikel elektrostatisch auf, damit sie gleichmäßig auf der Werkstückoberfläche haften.
- Pulverförderer: Transportieren das Pulver von den Vorratsbehältern zur Sprühpistole und sorgen für eine gleichmäßige Pulverzufuhr.
- Steuerungseinheiten: Erlauben die Anpassung der Auftragsparameter wie Spannung, Pulverfluss und Sprühzeit.
4. Fördersysteme

Fördersysteme transportieren die Werkstücke durch die verschiedenen Stationen der Beschichtungsanlage, von der Vorbehandlung bis zur Aushärtung.
- Kettenförderer: Bieten kontinuierliche Bewegung und sind ideal für die Massenproduktion.
- Schienen- und Rollensysteme: Ermöglichen Flexibilität bei der Anordnung der Produktionslinie.
- Pufferzonen: Bereiche, in denen Werkstücke zwischengelagert werden können, um den Produktionsfluss zu optimieren.
5. Einbrennöfen
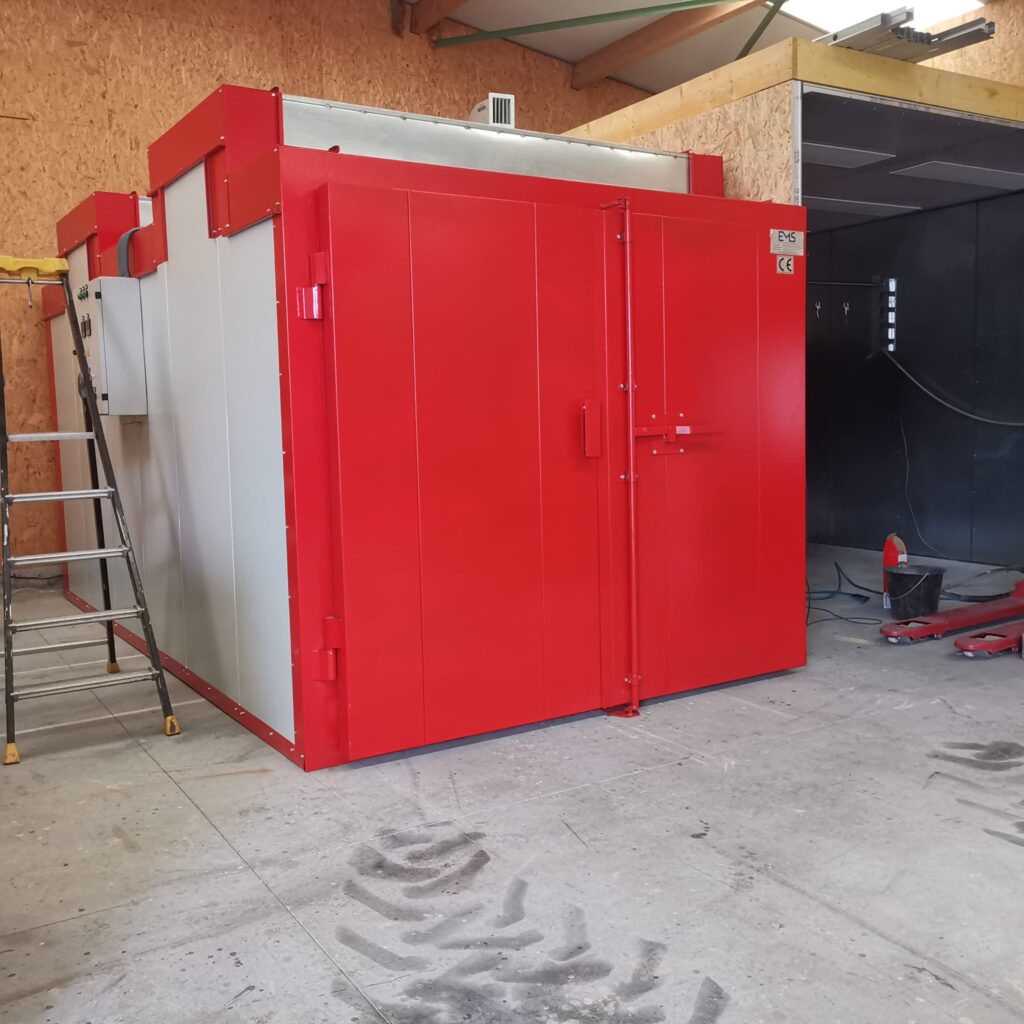
Einbrennöfen sind entscheidend für die Aushärtung der Pulverbeschichtung, da sie die erforderliche Wärme bereitstellen, um das Pulver zu schmelzen und eine dauerhafte Oberfläche zu schaffen.
- Chargenöfen: Ideal für kleinere Produktionen mit variablen Chargengrößen; sie bieten Flexibilität und können verschiedene Teile gleichzeitig verarbeiten.
- Durchlauföfen: Entwickelt für kontinuierliche Produktionslinien mit hohen Durchsatzraten. Teile werden auf einem Förderband durch den Ofen transportiert.
- Konvektions- und Infrarotöfen: Verschiedene Technologien bieten spezifische Vorteile in Bezug auf Aufheizgeschwindigkeit und Energieeffizienz.
6. Rückgewinnungs- und Recycling-Systeme
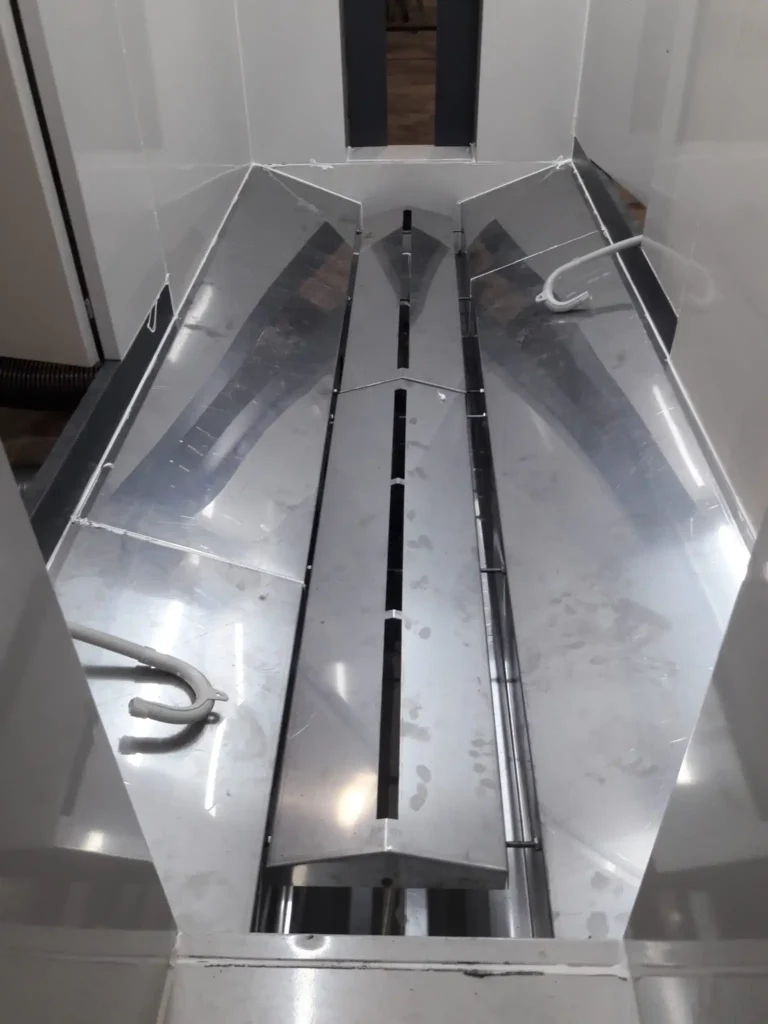
Diese Systeme sind darauf ausgelegt, überschüssiges Pulver aufzufangen und wiederzuverwenden, um Abfall zu minimieren und die Effizienz zu maximieren.
- Zyklonabscheider: Trennen überschüssiges Pulver aus der Luft und führen es zurück in den Beschichtungsprozess.
- Filtersysteme: Entfernen Feinstaub aus der Luft und stellen sicher, dass nur saubere Luft in die Umgebung abgegeben wird.
- Siebsysteme: Stellen sicher, dass nur qualitativ hochwertiges Pulver erneut verwendet wird, indem sie Verunreinigungen entfernen.
7. Steuerungs- und Überwachungssysteme
Moderne Steuerungssysteme ermöglichen die Überwachung und Anpassung aller Aspekte des Beschichtungsprozesses in Echtzeit.
- Prozessleitsysteme (PLS): Überwachen und steuern den gesamten Produktionsablauf und bieten Echtzeit-Daten zur Optimierung der Prozesse.
- Benutzeroberflächen: Intuitive Bedienpanels ermöglichen eine einfache Steuerung und Anpassung der Systemeinstellungen.
- Datenanalyse-Tools: Erfassen und analysieren Daten zur Prozessoptimierung und Fehlererkennung.
8. Kühlzonen
Nach dem Aushärtungsprozess müssen die Werkstücke auf Raumtemperatur abgekühlt werden, bevor sie weiterverarbeitet oder verpackt werden können.
- Luftkühlungssysteme: Nutzen Luftzirkulation, um die Werkstücke effizient abzukühlen.
- Wasserkühlungssysteme: In speziellen Anwendungen, wo schnelle Abkühlung erforderlich ist, können Wasserkühlungssysteme eingesetzt werden.
9. Materialhandling-Systeme
Diese Systeme unterstützen das Be- und Entladen von Werkstücken und die Bewegung innerhalb der Anlage.
- Robotiksysteme: Automatisierte Roboterarme, die Werkstücke präzise positionieren und handhaben.
- Hubsysteme: Unterstützen beim Transport schwerer Werkstücke innerhalb der Anlage.
10. Wartungseinrichtungen
Regelmäßige Wartung ist entscheidend, um die Effizienz und Lebensdauer der Anlage zu gewährleisten.
- Integrierte Wartungstools: Sensoren und Software zur vorausschauenden Wartung, die den Zustand der Anlage überwachen und Wartungsbedarf identifizieren.
- Zugängliche Wartungsbereiche: Einfache Zugänglichkeit für regelmäßige Inspektionen und Reparaturen.
Fazit
Eine komplette Pulverbeschichtungsanlage besteht aus vielen Komponenten, die zusammenarbeiten, um eine effiziente, qualitativ hochwertige und umweltfreundliche Beschichtung zu gewährleisten. Jede Komponente spielt eine entscheidende Rolle im Beschichtungsprozess, von der Vorbereitung der Werkstücke bis zur Aushärtung der Beschichtung. Die Wahl der richtigen Technologien und die Integration von Automatisierungslösungen können den Betrieb optimieren und die Produktionsziele eines Unternehmens effektiv unterstützen.
Anlagengröße

Die Größe von Pulverbeschichtungsanlagen kann je nach den spezifischen Anforderungen eines Unternehmens stark variieren. Die Anlagengröße hängt von mehreren Faktoren ab, darunter die Art und Größe der zu beschichtenden Werkstücke, das Produktionsvolumen und die verfügbaren räumlichen Gegebenheiten. Hier sind einige wichtige Überlegungen und Optionen zur Variation der Anlagengröße:
Faktoren, die die Anlagengröße beeinflussen
- Art der zu beschichtenden Werkstücke
- Kleinere Teile: Bei der Beschichtung von kleineren Teilen, wie z. B. Elektrokomponenten oder kleinen Metallteilen, können kompaktere Anlagen eingesetzt werden.
- Große Werkstücke: Für größere Teile, wie Automobilkarosserien oder große Maschinenteile, sind größere Anlagen mit geräumigen Kabinen und Öfen erforderlich.
- Produktionsvolumen
- Kleinserienproduktion: Unternehmen, die kleinere Produktionsvolumen handhaben, können mit einfacheren und kleineren Anlagen auskommen.
- Massenproduktion: Für hohe Produktionsvolumen sind größere und komplexere Anlagen notwendig, die einen kontinuierlichen Betrieb ermöglichen.
- Verfügbare Fläche
- Kompakte Lösungen: In begrenzten Räumlichkeiten können platzsparende Designs und integrierte Systeme genutzt werden, um den verfügbaren Platz optimal zu nutzen.
- Großflächige Anlagen: In größeren Einrichtungen kann eine weitläufige Anordnung von Vorbehandlung, Beschichtung und Aushärtung erfolgen, um einen reibungslosen Produktionsablauf zu gewährleisten.
- Prozessanforderungen
- Vielseitigkeit: Anlagen, die verschiedene Beschichtungsarten und Materialien verarbeiten müssen, erfordern möglicherweise eine modulare Struktur, die Anpassungen erlaubt.
- Spezialanforderungen: Bestimmte Anwendungen, wie z. B. die Beschichtung von hitzeempfindlichen Materialien, erfordern spezifische Anpassungen der Anlagengröße und -konfiguration.
Optionen zur Variation der Anlagengröße
1. Modulare Anlagen
Modulare Anlagen sind flexibel und können an unterschiedliche Produktionsanforderungen angepasst werden. Sie bestehen aus separaten Modulen, die nach Bedarf hinzugefügt oder entfernt werden können.
- Vorteile:
- Flexibilität: Einfaches Anpassen und Erweitern der Anlage, um auf wechselnde Produktionsanforderungen zu reagieren.
- Kosteneffizienz: Investitionen können nach und nach getätigt werden, indem nur die notwendigen Module erworben werden.
- Einfache Wartung: Einzelne Module können leicht gewartet oder ausgetauscht werden, ohne den gesamten Betrieb zu unterbrechen.
- Beispiele:
- Modulare Kabinen: Erlauben die Anpassung der Kabinengröße je nach Werkstückgröße.
- Erweiterbare Fördersysteme: Zusätzliche Förderstrecken können hinzugefügt werden, um den Produktionsfluss zu erweitern.
2. Kompakte Anlagen
Kompakte Anlagen sind ideal für Unternehmen mit begrenztem Platzangebot oder für kleinere Produktionsvolumen.
- Vorteile:
- Platzsparend: Effektive Nutzung des verfügbaren Raums.
- Geringere Investitionskosten: Reduzierte Anfangsinvestitionen durch den kleineren Maßstab der Anlage.
- Schnellere Installation: Einfachere und schnellere Implementierung.
- Beispiele:
- Mini-Kabinen: Kleinere Beschichtungskabinen für spezialisierte Anwendungen.
- Integrierte Systeme: Anlagen, die Vorbehandlung, Beschichtung und Aushärtung in einem kompakten Layout vereinen.
3. Großflächige Anlagen
Für Unternehmen mit hohen Produktionsanforderungen oder großen Werkstücken sind großflächige Anlagen notwendig.
- Vorteile:
- Hohe Kapazität: Eignen sich für die Massenproduktion und den gleichzeitigen Betrieb mehrerer Linien.
- Vielseitigkeit: Möglichkeit, mehrere Prozesse gleichzeitig durchzuführen.
- Effizienz: Optimierte Produktionsabläufe durch die großzügige Gestaltung der Anlage.
- Beispiele:
- Mehrere Kabinen und Öfen: Separate Bereiche für unterschiedliche Farben oder Materialien.
- Erweiterte Fördersysteme: Lange Förderstrecken für den Transport großer oder zahlreicher Teile.
Planungsüberlegungen bei der Anlagengrößenauswahl
- Zukunftsprognosen
- Marktentwicklung: Berücksichtigen Sie mögliche Expansionen oder Veränderungen in der Nachfrage.
- Technologische Fortschritte: Planen Sie für zukünftige Anpassungen oder Upgrades der Anlage.
- Kostenüberlegungen
- Anfangsinvestition vs. Betriebskosten: Wägen Sie die Anfangsinvestitionen gegen die langfristigen Betriebskosten ab.
- Finanzielle Flexibilität: Planen Sie die Finanzierung der Anlage im Einklang mit den finanziellen Möglichkeiten und Zielen des Unternehmens.
- Integration und Kompatibilität
- Bestehende Infrastruktur: Überprüfen Sie die Kompatibilität der neuen Anlage mit bestehenden Systemen und Einrichtungen.
- Erweiterungsmöglichkeiten: Planen Sie die Integration zukünftiger Erweiterungen oder Module.
- Umwelt- und Sicherheitsstandards
- Regulierungen: Stellen Sie sicher, dass die Anlage alle relevanten Umwelt- und Sicherheitsstandards erfüllt.
- Nachhaltigkeit: Berücksichtigen Sie umweltfreundliche Technologien und Praktiken bei der Planung und dem Betrieb der Anlage.
Fazit
Die Größe einer Pulverbeschichtungsanlage kann an die spezifischen Bedürfnisse und Anforderungen eines Unternehmens angepasst werden. Durch die Auswahl der richtigen Anlagengröße und -konfiguration können Unternehmen ihre Produktionsziele effizient erreichen, die Qualität ihrer Produkte verbessern und die Betriebskosten optimieren. Ob modular, kompakt oder großflächig, jede Anlagengröße hat ihre eigenen Vorteile und Herausforderungen, die sorgfältig abgewogen werden müssen, um die besten Ergebnisse zu erzielen.
Benötigte Mitarbeiterzahl
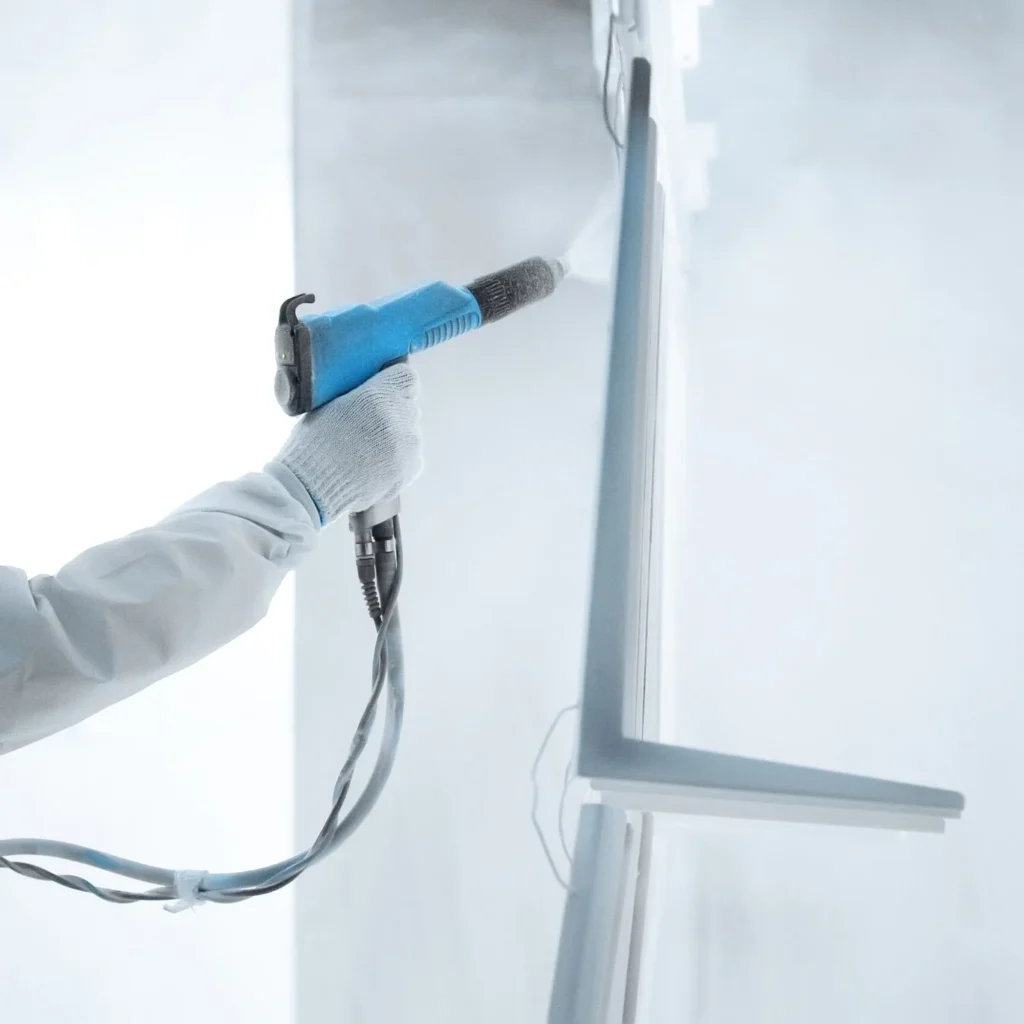
Die Anzahl der benötigten Mitarbeiter für den Betrieb einer Pulverbeschichtungsanlage hängt von mehreren Faktoren ab, darunter die Größe und Automatisierung der Anlage, das Produktionsvolumen, die Art der zu beschichtenden Werkstücke und die spezifischen betrieblichen Anforderungen. Hier sind einige Überlegungen, um die optimale Mitarbeiterzahl für den Betrieb einer Pulverbeschichtungsanlage zu bestimmen:
1. Faktoren, die die Mitarbeiterzahl beeinflussen
a. Größe der Anlage
- Kleine Anlagen:
- Typischerweise weniger Mitarbeiter erforderlich.
- Häufig eine Mischung aus manuellen und halbautomatisierten Prozessen.
- Große Anlagen:
- Mehr Mitarbeiter erforderlich, insbesondere bei einer hohen Produktionskapazität.
- Automatisierte Systeme können jedoch den Bedarf an Personal verringern.
b. Automatisierungsgrad
- Hochautomatisierte Anlagen:
- Reduzierter Bedarf an manueller Arbeit.
- Erfordern jedoch technisches Personal für die Überwachung, Wartung und Programmierung der Anlagen.
- Manuelle oder halbautomatisierte Anlagen:
- Höherer Personalbedarf für die Bedienung und Überwachung der Anlagen.
c. Produktionsvolumen
- Niedriges Produktionsvolumen:
- Geringerer Personalbedarf.
- Mehr Flexibilität bei der Planung von Schichten.
- Hohes Produktionsvolumen:
- Mehr Mitarbeiter erforderlich, um den Produktionsfluss aufrechtzuerhalten.
- Möglicherweise mehrere Schichten zur Maximierung der Betriebszeit.
d. Werkstücktypen
- Komplexe oder große Werkstücke:
- Erfordern möglicherweise mehr Personal für die Handhabung und Inspektion.
- Spezialisierte Mitarbeiter für die Anpassung der Beschichtungsparameter.
- Kleine oder standardisierte Teile:
- Weniger Personal für die Handhabung erforderlich.
- Prozessabläufe sind oft einfacher und standardisiert.
2. Typische Rollen in einer Pulverbeschichtungsanlage
a. Produktionsmitarbeiter
- Bediener der Beschichtungsanlagen:
- Verantwortlich für das Auftragen der Pulverbeschichtung.
- Überwachung der Qualität und Sicherstellung der richtigen Parameter.
- Vorbehandlungsmitarbeiter:
- Durchführung von Reinigungs- und Vorbehandlungsprozessen.
- Sicherstellung, dass die Werkstücke ordnungsgemäß vorbereitet sind.
b. Technisches Personal
- Wartungstechniker:
- Regelmäßige Wartung und Reparatur der Anlagen.
- Überwachung der Systemleistung und Durchführung von Fehlerbehebungen.
- Automatisierungs- und Steuerungstechniker:
- Programmierung und Überwachung automatisierter Systeme.
- Anpassung der Steuerungsparameter und Optimierung der Prozesse.
c. Qualitätssicherung
- Qualitätsinspektoren:
- Durchführung von Qualitätskontrollen zur Sicherstellung der Einhaltung von Standards.
- Verwendung von Messgeräten zur Überprüfung der Schichtdicke und Oberflächenqualität.
- Prozessoptimierer:
- Analyse von Produktionsdaten zur Verbesserung der Effizienz und Qualität.
- Implementierung von Verbesserungsmaßnahmen.
d. Management und Verwaltung
- Produktionsleiter:
- Überwachung der gesamten Produktionslinie.
- Koordination der Mitarbeiter und Sicherstellung der Zielerreichung.
- Logistik- und Materialplaner:
- Verwaltung der Materialflüsse und Bestände.
- Planung der Produktion auf Basis von Nachfrage und Kapazität.
3. Beispiel einer Mitarbeiterverteilung
Hier ist ein Beispiel für die Mitarbeiterverteilung in einer mittelgroßen, teilautomatisierten Pulverbeschichtungsanlage:
Rolle | Anzahl der Mitarbeiter | Beschreibung |
---|---|---|
Bediener der Vorbehandlung | 2-3 | Verantwortlich für Reinigung und Vorbereitung der Werkstücke. |
Pulverbeschichtungsbediener | 3-4 | Durchführung des Beschichtungsprozesses. |
Wartungstechniker | 1-2 | Wartung und Reparatur der Anlagen. |
Automatisierungstechniker | 1-2 | Überwachung der automatisierten Systeme und Prozesssteuerung. |
Qualitätsinspektoren | 1-2 | Überprüfung der Qualität der beschichteten Teile. |
Produktionsleiter | 1 | Leitung der Produktion und Koordination der Schichten. |
Logistik- und Materialplaner | 1 | Verwaltung der Materialbestände und Produktionsplanung. |
4. Optimierung der Mitarbeiterzahl
Um die Mitarbeiterzahl effizient zu nutzen, können Unternehmen folgende Strategien in Betracht ziehen:
- Schulung und Weiterbildung: Regelmäßige Schulungen, um die Qualifikation der Mitarbeiter zu verbessern und sie auf mehrere Aufgaben vorzubereiten.
- Einsatz von Zeitarbeitern: Flexible Personalplanung durch den Einsatz von Zeitarbeitskräften, um bei Bedarf Spitzenbelastungen abzufangen.
- Prozessoptimierung: Einsatz von Lean-Management-Prinzipien, um Prozesse zu optimieren und den Personalbedarf zu reduzieren.
- Investition in Automatisierung: Einsatz von Automatisierungstechnologien zur Reduzierung des manuellen Arbeitsaufwands und Verbesserung der Effizienz.
Fazit
Die optimale Anzahl der Mitarbeiter in einer Pulverbeschichtungsanlage hängt von vielen Faktoren ab, darunter die Größe der Anlage, der Automatisierungsgrad und das Produktionsvolumen. Durch den Einsatz von Automatisierung, Schulung und Prozessoptimierung können Unternehmen ihre Personalkosten minimieren und gleichzeitig die Effizienz und Qualität ihrer Produktion maximieren. Eine sorgfältige Planung und Anpassung der Personalressourcen ist entscheidend, um den Erfolg der Anlage zu gewährleisten.
Einführung in die Pulverbeschichtung

Die Pulverbeschichtung ist eine Technik der Oberflächenveredelung, bei der pulverförmige Farben oder Beschichtungsmaterialien auf ein Substrat (meist Metall) aufgetragen werden. Im Gegensatz zu herkömmlichen Flüssigbeschichtungen wird bei der Pulverbeschichtung kein Lösungsmittel verwendet, was die Technik umweltfreundlicher macht. Das Pulver wird auf die Oberfläche des Objekts gesprüht und anschließend erhitzt, wodurch es zu einer glatten und dauerhaften Beschichtung schmilzt.
Pulverbeschichtungen werden hauptsächlich in der Automobil-, Bau- und Möbelindustrie sowie in der Elektronik verwendet. Es ist ein beliebtes Verfahren, da es robuste, widerstandsfähige Beschichtungen bietet, die gegen Kratzer, Korrosion und chemische Einflüsse beständig sind.
1.2. Geschichte der Pulverbeschichtung
Die Pulverbeschichtung wurde in den 1950er Jahren entwickelt und in den 1960er Jahren in der industriellen Produktion populär. Der Wunsch nach einer umweltfreundlicheren und effizienteren Alternative zu traditionellen Flüssigfarben führte zur Entwicklung von Pulverlacken, die ohne Lösungsmittel auskommen. Im Laufe der Jahrzehnte wurde die Technologie kontinuierlich weiterentwickelt, und heute sind Pulverbeschichtungen aus vielen industriellen Anwendungen nicht mehr wegzudenken.
Die Funktionsweise der Pulverbeschichtung
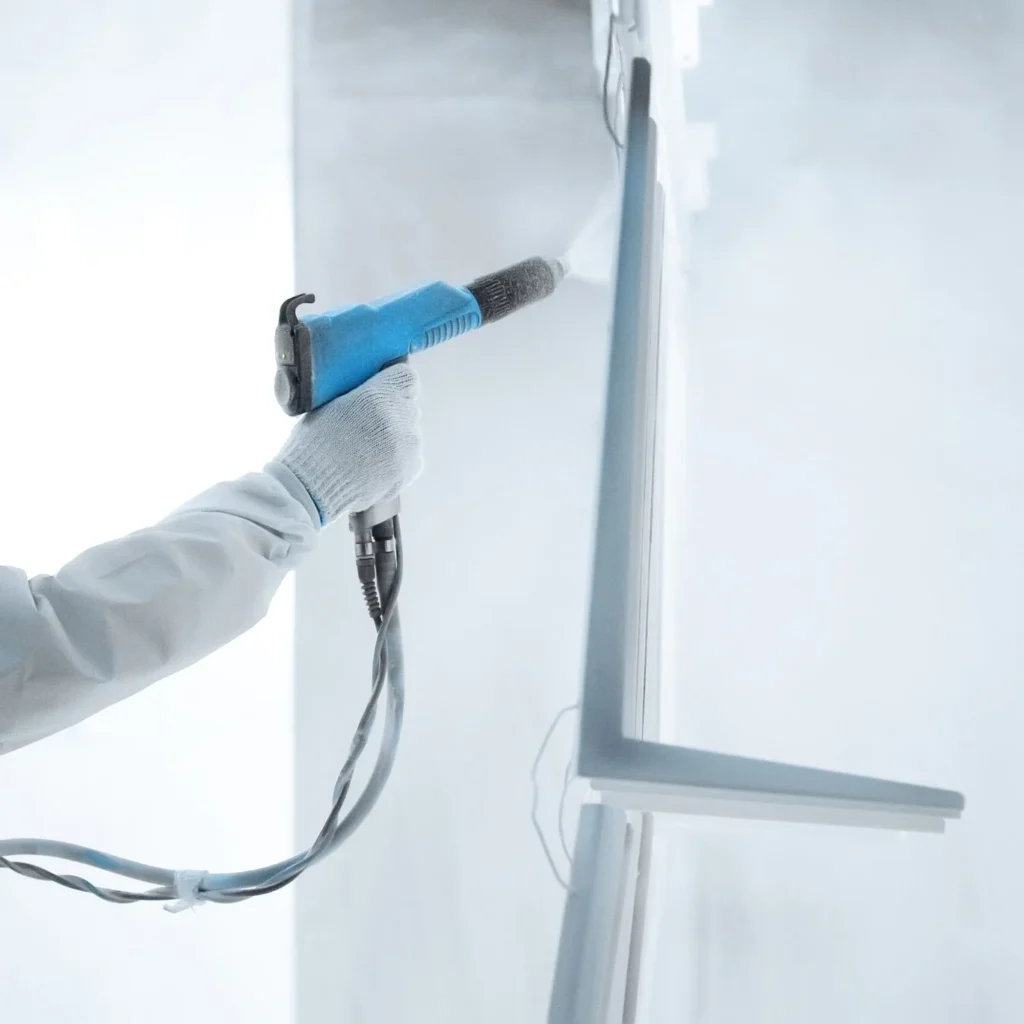
Die Pulverbeschichtung umfasst mehrere wichtige Schritte, die in einem genauen Prozess ablaufen. Jeder Schritt ist entscheidend, um eine gleichmäßige und langlebige Beschichtung zu erreichen.
2.1. Vorbereitung der Oberfläche
Die Vorbereitung der Oberfläche ist ein wesentlicher Schritt, bevor das Pulver aufgetragen werden kann. Eine unzureichende Vorbereitung kann zu schlechter Haftung und Defekten in der Endbeschichtung führen. Der Prozess der Oberflächenvorbereitung umfasst mehrere Schritte:
- Reinigung: Das Entfernen von Schmutz, Öl, Fett, Rost und alten Beschichtungen ist notwendig, um sicherzustellen, dass das Pulver gut haftet. Hierzu werden oft chemische Reiniger oder Entfetter verwendet.
- Strahlen oder Schleifen: Um eine optimale Haftung des Pulvers zu gewährleisten, wird die Oberfläche oft sandgestrahlt oder geschliffen, um eine raue Textur zu schaffen, die das Pulver besser haften lässt.
- Vorbehandlung: Metalloberflächen werden häufig vorbehandelt, z.B. durch Phosphatierung oder Chromatierung, um Korrosion zu verhindern und die Haftung zu verbessern.
2.2. Auftragen des Pulvers
Das Auftragen des Pulvers erfolgt mittels eines elektrostatischen Sprühsystems. Das Pulverlackierverfahren funktioniert auf der Basis von elektrostatischen Kräften:
- Pulversprühpistole: Das Pulver wird durch eine Sprühpistole auf das Werkstück aufgetragen. Die Pistole lädt die Pulverpartikel elektrostatisch auf, während das zu beschichtende Objekt geerdet wird. Dies führt dazu, dass das Pulver durch elektrostatische Anziehung gleichmäßig auf der Oberfläche haftet.
- Automatische und manuelle Beschichtungsverfahren: Je nach Anwendung und Produktionsumgebung können automatische Sprühanlagen oder manuelle Pistolen verwendet werden. Automatische Systeme bieten eine höhere Effizienz bei der Massenproduktion, während manuelle Systeme flexibler und für kleinere Serien oder komplexe Geometrien geeignet sind.
2.3. Einbrennen des Pulvers im Pulverofen
Nach dem Auftragen des Pulvers wird das beschichtete Werkstück in einen Pulverofen gebracht, um das Pulver zu schmelzen und aushärten zu lassen. Dieser Vorgang, der als „Aushärtung“ bezeichnet wird, sorgt dafür, dass das Pulver eine feste, haltbare und glatte Schicht auf dem Werkstück bildet.
- Temperatur und Zeit: Typische Temperaturen für das Einbrennen von Pulverlacken liegen zwischen 150°C und 200°C, und die Aushärtezeit beträgt in der Regel 10 bis 20 Minuten. Diese Parameter variieren jedoch je nach Art des verwendeten Pulvers und der Materialstärke des Werkstücks.
- Verschiedene Ofentypen: Es gibt verschiedene Arten von Öfen für die Pulverbeschichtung, darunter konventionelle Umluftöfen, Infrarotöfen und Gasöfen. Jeder Typ hat seine eigenen Vorteile und ist für bestimmte Anwendungen besser geeignet.
Typen von Pulverbeschichtungen

Es gibt verschiedene Arten von Pulverbeschichtungen, die je nach Anwendung und gewünschten Eigenschaften ausgewählt werden. Die zwei Haupttypen von Pulverbeschichtungen sind Thermoplaste und Duroplaste.
3.1. Thermoplastische Pulverbeschichtungen
Thermoplaste sind Kunststoffe, die beim Erhitzen schmelzen und beim Abkühlen wieder fest werden, ohne dass eine chemische Veränderung stattfindet. Zu den thermoplastischen Pulverbeschichtungen gehören:
- Polyethylen (PE): Wird oft für Beschichtungen auf Metallteilen verwendet, die Flexibilität und Schlagfestigkeit erfordern.
- Polyamid (PA): Wird häufig in der Automobilindustrie eingesetzt, da es eine hohe Beständigkeit gegen Chemikalien und Abrieb aufweist.
- Polyvinylchlorid (PVC): Bietet hervorragende Korrosionsbeständigkeit und wird in der Elektro- und Bauindustrie verwendet.
3.2. Duroplastische Pulverbeschichtungen
Duroplaste, auch als „härtende“ Kunststoffe bekannt, durchlaufen eine chemische Reaktion während des Aushärtens, die irreversible Verbindungen bildet. Die häufigsten duroplastischen Beschichtungen sind:
- Epoxidharze: Bieten eine ausgezeichnete Haftung und chemische Beständigkeit und werden häufig für industrielle Beschichtungen und Korrosionsschutz verwendet.
- Polyester: Diese Beschichtungen sind UV-beständig und eignen sich ideal für Außenanwendungen wie Geländer, Fensterrahmen und Möbel.
- Acrylpulver: Wird verwendet, wenn eine glatte, glänzende Oberfläche benötigt wird. Diese Pulverbeschichtungen bieten eine hervorragende Witterungsbeständigkeit und werden häufig in der Automobilindustrie eingesetzt.
Pulveranlagen: Aufbau und Funktionsweise

Pulveranlagen sind technische Anlagen, die speziell für die Durchführung von Pulverbeschichtungsprozessen konzipiert sind. Sie bestehen aus mehreren Komponenten, die gemeinsam eine effiziente und sichere Durchführung des Beschichtungsprozesses gewährleisten.
4.1. Komponenten einer Pulveranlage
Eine typische Pulveranlage umfasst die folgenden Hauptkomponenten:
- Pulversprühsystem: Besteht aus der Pulversprühpistole, dem Pulverbehälter und dem Zufuhrsystem, das das Pulver zur Pistole führt.
- Fördertechnik: Förderbänder oder Schienensysteme transportieren die Werkstücke durch die verschiedenen Stationen der Anlage, von der Vorbehandlung über die Beschichtung bis zum Aushärten im Ofen.
- Pulverrückgewinnungssysteme: Diese Systeme fangen überschüssiges Pulver auf, das nicht auf das Werkstück aufgetragen wurde, und führen es dem Prozess wieder zu. Dies erhöht die Effizienz und reduziert den Materialverbrauch.
- Steuerungssysteme: Moderne Pulveranlagen sind oft mit computergesteuerten Systemen ausgestattet, die den gesamten Prozess überwachen und steuern. Dies ermöglicht eine präzise Steuerung von Parametern wie Sprühmenge, Luftdruck, Temperatur und Aushärtezeit.
4.2. Automatische und manuelle Pulveranlagen
Es gibt sowohl automatische als auch manuelle Pulveranlagen, die je nach Produktionsvolumen und spezifischen Anforderungen der Beschichtung eingesetzt werden.
- Automatische Pulveranlagen: Diese Systeme sind ideal für die Massenproduktion, da sie eine gleichmäßige Beschichtung mit minimalem Arbeitsaufwand ermöglichen. Sie verwenden Roboterarme oder fest montierte Sprühsysteme, um die Pulverbeschichtung automatisch auf die Werkstücke aufzutragen.
- Manuelle Pulveranlagen: Diese Anlagen sind flexibler und eignen sich besser für kleinere Serien oder Einzelstücke. Der Bediener hat mehr Kontrolle über den Beschichtungsprozess und kann auf komplexe Geometrien oder spezifische Anforderungen eingehen.
5. Pulveröfen: Arten und Funktionsweise
Pulveröfen spielen eine zentrale Rolle im Pulverbeschichtungsprozess, da sie das Pulver erhitzen und die chemische Reaktion einleiten, die für die Bildung einer harten, beständigen Beschichtung erforderlich ist. Es gibt verschiedene Arten von Öfen, die je nach Anwendungsanforderungen und Produktionsumgebung verwendet werden.
5.1. Arten von Pulveröfen
Es gibt mehrere Arten von Öfen, die in der Pulverbeschichtung verwendet werden, darunter:
- Konvektionsöfen: Diese Öfen verwenden heiße Luft, die gleichmäßig durch den Ofen zirkuliert, um das Pulver zu erhitzen. Konvektionsöfen sind die gebräuchlichste Art von Pulveröfen und eignen sich für eine Vielzahl von Anwendungen.
- Infrarotöfen: Infrarotstrahler erhitzen das Pulver schnell, indem sie elektromagnetische Strahlung abgeben, die direkt auf die Oberfläche des Werkstücks wirkt. Diese Art von Ofen eignet sich besonders für schnelle Produktionszyklen oder dünnwandige Teile.
- Gasöfen: Gasbefeuerte Öfen sind oft energieeffizienter und kostengünstiger im Betrieb als elektrische Öfen. Sie sind ideal für große Produktionsanlagen, in denen eine hohe Wärmeleistung erforderlich ist.
- Kombinationsöfen: Diese Öfen kombinieren Konvektions- und Infrarottechnologien, um die Vorteile beider Systeme zu nutzen. Sie bieten eine schnelle Erwärmung und gleichmäßige Wärmeverteilung und sind besonders effizient.
5.2. Aushärteprozess in Pulveröfen
Der Aushärteprozess in einem Pulverofen ist entscheidend für die Bildung der Beschichtung. Wenn das beschichtete Werkstück in den Ofen kommt, schmilzt das Pulver allmählich und vernetzt sich chemisch zu einer festen Schicht. Die Temperatur und die Dauer des Aushärtens hängen von der Art des Pulvers und dem Material des Werkstücks ab.
- Typische Aushärtetemperaturen: Pulverlacke werden in der Regel bei Temperaturen zwischen 150°C und 200°C ausgehärtet. Zu niedrige Temperaturen können dazu führen, dass das Pulver nicht vollständig schmilzt, während zu hohe Temperaturen das Werkstück beschädigen können.
- Aushärtezeit: Die Aushärtezeit liegt normalerweise zwischen 10 und 20 Minuten, kann aber je nach Größe und Dicke des Werkstücks sowie der Art des Pulvers variieren. Eine längere Aushärtezeit kann erforderlich sein, um eine vollständige Vernetzung zu gewährleisten und die mechanischen Eigenschaften der Beschichtung zu maximieren.
5.3. Energieeffizienz von Pulveröfen
Moderne Pulveröfen sind oft darauf ausgelegt, den Energieverbrauch zu minimieren. Gasöfen bieten in der Regel eine höhere Energieeffizienz im Vergleich zu elektrisch betriebenen Öfen. Einige Öfen sind zudem mit Wärmerückgewinnungssystemen ausgestattet, die die Abwärme aus dem Aushärtungsprozess nutzen, um den Energieverbrauch weiter zu senken.
6. Vorteile der Pulverbeschichtung
Die Pulverbeschichtung bietet gegenüber herkömmlichen Flüssiglackierverfahren zahlreiche Vorteile. Diese Vorteile betreffen nicht nur die Qualität und Haltbarkeit der Beschichtung, sondern auch Umweltaspekte und Kosteneffizienz.
6.1. Umweltfreundlichkeit
Einer der größten Vorteile der Pulverbeschichtung ist ihre Umweltfreundlichkeit. Da Pulverbeschichtungen keine Lösungsmittel enthalten, werden keine flüchtigen organischen Verbindungen (VOCs) freigesetzt, die zu Luftverschmutzung beitragen können. Dies macht Pulverbeschichtungen zu einer umweltfreundlichen Alternative zu herkömmlichen Flüssiglacken.
- Weniger Abfall: Das überschüssige Pulver kann aufgefangen und wiederverwendet werden, was den Materialverbrauch reduziert und Abfall minimiert.
- Sicher für Arbeiter: Da keine Lösungsmittel verwendet werden, sind Pulverbeschichtungen auch sicherer für die Arbeiter, da keine giftigen Dämpfe freigesetzt werden, die eingeatmet werden könnten.
6.2. Haltbarkeit und Widerstandsfähigkeit
Pulverbeschichtungen bieten eine extrem widerstandsfähige Oberfläche, die gegen Abnutzung, Kratzer, Korrosion und chemische Einflüsse beständig ist. Diese Eigenschaften machen Pulverbeschichtungen besonders attraktiv für industrielle Anwendungen, bei denen Langlebigkeit und Widerstandsfähigkeit entscheidend sind.
- Korrosionsschutz: Pulverbeschichtungen bieten einen hervorragenden Korrosionsschutz, der sie ideal für Anwendungen im Außenbereich macht, z.B. bei Möbeln, Fassaden und Fahrzeugen.
- Beständigkeit gegen Chemikalien: Pulverbeschichtungen sind auch gegen viele Chemikalien beständig, was sie zu einer idealen Wahl für industrielle Anlagen und Maschinen macht, die aggressiven Substanzen ausgesetzt sind.
6.3. Kosteneffizienz
Obwohl die Anschaffung von Pulveranlagen und Öfen zunächst mit höheren Kosten verbunden ist, amortisieren sich diese Investitionen schnell aufgrund der zahlreichen Kosteneinsparungen, die die Pulverbeschichtung bietet:
- Materialeinsparungen: Dank der Möglichkeit, überschüssiges Pulver wiederzuverwenden, werden Materialkosten gesenkt.
- Weniger Nacharbeiten: Da Pulverbeschichtungen eine gleichmäßige und hochwertige Oberfläche bieten, sind weniger Nacharbeiten oder Korrekturen erforderlich.
- Längere Lebensdauer: Die Haltbarkeit der Beschichtung reduziert die Notwendigkeit für häufige Wartung oder Neubeschichtung, was langfristig Kosten spart.
6.4. Ästhetische Vielfalt
Pulverbeschichtungen bieten eine breite Palette an Farben und Texturen. Im Gegensatz zu Flüssiglacken, die oft in ihrer Farbauswahl begrenzt sind, können Pulverbeschichtungen in nahezu jeder gewünschten Farbe hergestellt werden, einschließlich Glanz-, Matt- und Metallic-Finishes. Auch strukturierte Beschichtungen wie Hammerschlag oder Samtoberflächen sind problemlos umsetzbar.
- UV-Beständigkeit: Polyesterpulverlacke bieten eine hervorragende UV-Beständigkeit und sind ideal für den Einsatz im Außenbereich, da sie nicht verblassen oder vergilben.
- Glatte oder strukturierte Oberflächen: Pulverbeschichtungen ermöglichen es, eine Vielzahl von Oberflächenstrukturen zu erzielen, von glatten und glänzenden bis hin zu rauen und strukturierten Oberflächen.
7. Anwendungsgebiete der Pulverbeschichtung
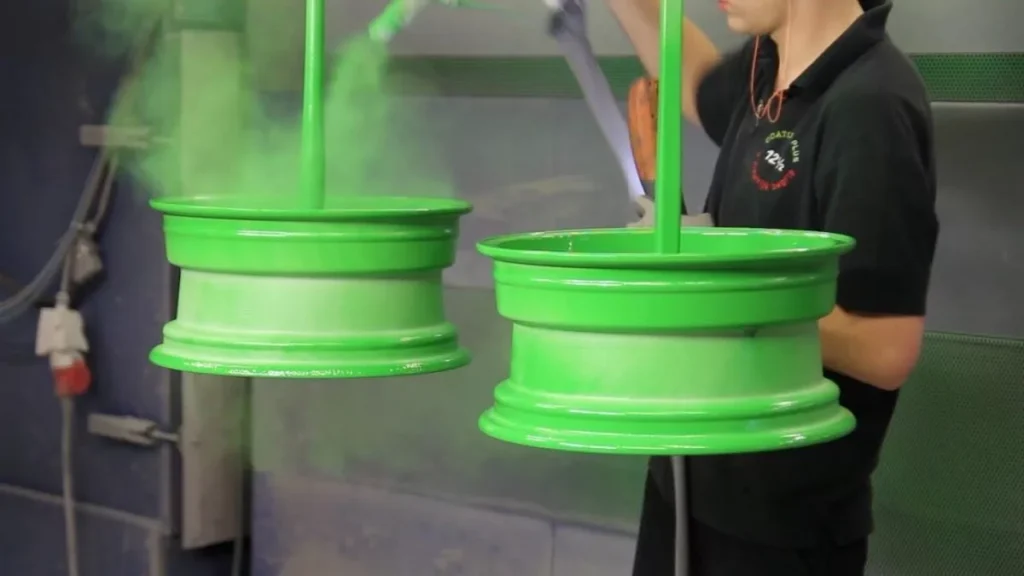
Die Pulverbeschichtung wird in einer Vielzahl von Branchen und Anwendungen eingesetzt. Ihre Vielseitigkeit und Haltbarkeit machen sie zur idealen Wahl für eine breite Palette von Projekten, von industriellen Maschinen bis hin zu Konsumgütern.
7.1. Automobilindustrie
Die Automobilindustrie ist einer der größten Anwender von Pulverbeschichtungen. Fahrzeugteile wie Felgen, Fahrgestelle, Stoßstangen und Außenverkleidungen werden oft mit Pulverbeschichtungen behandelt, um sie vor Korrosion und Verschleiß zu schützen. Pulverbeschichtungen bieten auch die Möglichkeit, Fahrzeugteile in einer Vielzahl von Farben und Oberflächenstrukturen zu gestalten.
7.2. Architektur und Bauwesen
Im Bauwesen werden Pulverbeschichtungen für die Beschichtung von Metallkonstruktionen, Fassaden, Türen, Fensterrahmen und Geländern verwendet. Ihre Witterungsbeständigkeit und Korrosionsschutz machen sie ideal für Anwendungen im Außenbereich. Außerdem bieten Pulverbeschichtungen eine große Farbauswahl, was Architekten und Designern zusätzliche Flexibilität bei der Gestaltung von Gebäuden gibt.
7.3. Möbelindustrie
Die Möbelindustrie verwendet Pulverbeschichtungen, um Metallmöbel vor Korrosion zu schützen und ihnen ein ästhetisch ansprechendes Aussehen zu verleihen. Gartenmöbel, Büromöbel und Designermöbel profitieren gleichermaßen von der Langlebigkeit und Widerstandsfähigkeit der Pulverbeschichtung.
7.4. Haushaltsgeräte
Viele Haushaltsgeräte, wie Waschmaschinen, Kühlschränke und Öfen, werden mit Pulverbeschichtungen versehen, um sie vor Abnutzung und Korrosion zu schützen. Pulverbeschichtungen bieten nicht nur Schutz, sondern auch ein attraktives Finish, das in einer Vielzahl von Farben und Oberflächen erhältlich ist.
7.5. Elektronikindustrie
In der Elektronikindustrie werden Pulverbeschichtungen oft für Gehäuse und Komponenten verwendet, die Schutz vor elektromagnetischen Störungen (EMI) bieten müssen. Pulverbeschichtungen schützen die empfindlichen elektronischen Komponenten vor äußeren Einflüssen und tragen zur Langlebigkeit der Produkte bei.
8. Zukunft der Pulverbeschichtungstechnologie
Die Technologie der Pulverbeschichtung entwickelt sich kontinuierlich weiter, um den Anforderungen moderner Industrieprozesse gerecht zu werden. Nachhaltigkeit, Effizienz und neue Materialien sind zentrale Treiber der technologischen Weiterentwicklung.
8.1. Nachhaltigkeit und Umweltbewusstsein
Mit zunehmendem Fokus auf Umweltschutz wird die Pulverbeschichtung weiterhin als bevorzugte Alternative zu Flüssiglacken an Bedeutung gewinnen. Forscher arbeiten kontinuierlich an der Entwicklung neuer Pulverformeln, die noch umweltfreundlicher sind, indem sie den Energieverbrauch und die Produktionsabfälle weiter reduzieren.
8.2. Fortschritte in der Materialwissenschaft
Die Entwicklung neuer Beschichtungsmaterialien bietet der Pulverbeschichtungstechnologie großes Potenzial. Die Einführung von Nanopartikeln in Pulverlacke könnte beispielsweise zu noch widerstandsfähigeren und leistungsfähigeren Beschichtungen führen, die überlegene Eigenschaften in Bezug auf Kratzfestigkeit, UV-Beständigkeit und Selbstreinigung bieten.
8.3. Digitalisierung und Automatisierung
Moderne Produktionsanlagen werden zunehmend automatisiert und digitalisiert. Dies gilt auch für Pulverbeschichtungsanlagen, die mit fortschrittlichen Steuerungssystemen und Robotik ausgestattet sind, um den Beschichtungsprozess noch effizienter und präziser zu gestalten. Datenanalyse und Sensorik ermöglichen es, die Qualität in Echtzeit zu überwachen und den Energieverbrauch zu optimieren.
9. Fazit
Die Pulverbeschichtung ist eine vielseitige und kosteneffiziente Methode zur Oberflächenveredelung, die in vielen Branchen breite Anwendung findet. Sie bietet Vorteile in Bezug auf Umweltfreundlichkeit, Langlebigkeit, Ästhetik und Kosteneinsparungen. Pulveranlagen und Pulveröfen sind wesentliche Bestandteile dieses Verfahrens und tragen maßgeblich zur Qualität und Effizienz des Beschichtungsprozesses bei.
Mit kontinuierlichen technologischen Fortschritten in Bereichen wie Nachhaltigkeit, Automatisierung und Materialwissenschaft bleibt die Pulverbeschichtung eine führende Technik in der Oberflächenveredelung und wird auch in Zukunft eine entscheidende Rolle in der industriellen Fertigung spielen.
Eine Pulverbeschichtungsanlage ist eine industrielle Anlage, die zur Oberflächenbehandlung von Werkstücken und Materialien eingesetzt wird. Bei diesem Verfahren wird eine trockene Pulverbeschichtung auf eine Oberfläche aufgetragen und anschließend durch Hitze gehärtet, um eine langlebige, gleichmäßige Beschichtung zu schaffen. Diese Technik wird häufig für Metallteile, aber auch für andere Materialien eingesetzt, die hohe Anforderungen an die Oberflächenqualität, Korrosionsbeständigkeit und Farbtreue erfüllen müssen.
Aufbau und Funktionsweise einer Pulverbeschichtungsanlage

Eine typische Pulverbeschichtungsanlage besteht aus mehreren Abschnitten und Komponenten, die speziell auf das Verfahren abgestimmt sind:
- Vorbehandlung:
- Hier werden die Werkstücke gereinigt und entfettet, um die Haftung der Pulverbeschichtung zu verbessern. Die Vorbehandlung kann chemisch oder mechanisch erfolgen und umfasst oft Schritte wie Entfettung, Phosphatierung oder Sandstrahlen.
- Trocknung:
- Nach der Vorbehandlung werden die Teile getrocknet, um sicherzustellen, dass keine Feuchtigkeit die Haftung der Pulverbeschichtung beeinträchtigt. Ein Trocknungsofen wird oft für diesen Schritt verwendet.
- Pulverbeschichtungskabine:
- In dieser Kabine wird das Pulver auf die Werkstücke gesprüht. Dabei wird das Pulver durch elektrische Aufladung an die Oberfläche des Bauteils gezogen. Das Beschichtungspulver haftet somit gleichmäßig und mit hoher Präzision.
- Einbrennofen:
- Die beschichteten Werkstücke werden in einen Einbrennofen geführt, wo das Pulver bei Temperaturen zwischen 160°C und 200°C schmilzt und aushärtet. Dadurch entsteht eine robuste, glatte und gleichmäßige Beschichtung.
- Abkühlzone:
- Nach dem Einbrennvorgang werden die Teile langsam abgekühlt, bevor sie weiterverarbeitet oder verpackt werden.
Vorteile der Pulverbeschichtung
- Umweltfreundlich: Da keine Lösungsmittel verwendet werden, entstehen weniger schädliche Emissionen.
- Hohe Beständigkeit: Pulverbeschichtungen sind besonders robust und widerstandsfähig gegen Korrosion, Chemikalien und Witterungseinflüsse.
- Vielfältige Farb- und Strukturauswahl: Es gibt eine breite Palette an Farben und Texturen, die den Anforderungen verschiedener Branchen gerecht werden.
Einsatzbereiche
Pulverbeschichtungsanlagen finden Anwendung in verschiedenen Industrien, wie beispielsweise:
- Automobilindustrie (z. B. bei Felgen und Karosserieteilen),
- Möbelindustrie (insbesondere bei Metallmöbeln und -gestellen),
- Bauindustrie (z. B. Fensterrahmen, Fassadenelemente),
- Haushaltsgeräte (z. B. Beschichtung von Geräten, die hohe Widerstandsfähigkeit erfordern).
Fazit
Pulverbeschichtungsanlagen sind unverzichtbare Anlagen in der industriellen Fertigung und bieten eine umweltfreundliche, kosteneffiziente und langlebige Lösung für die Oberflächenbeschichtung.
Vorbehandlung in der Pulverbeschichtung – Ein umfassender Leitfaden
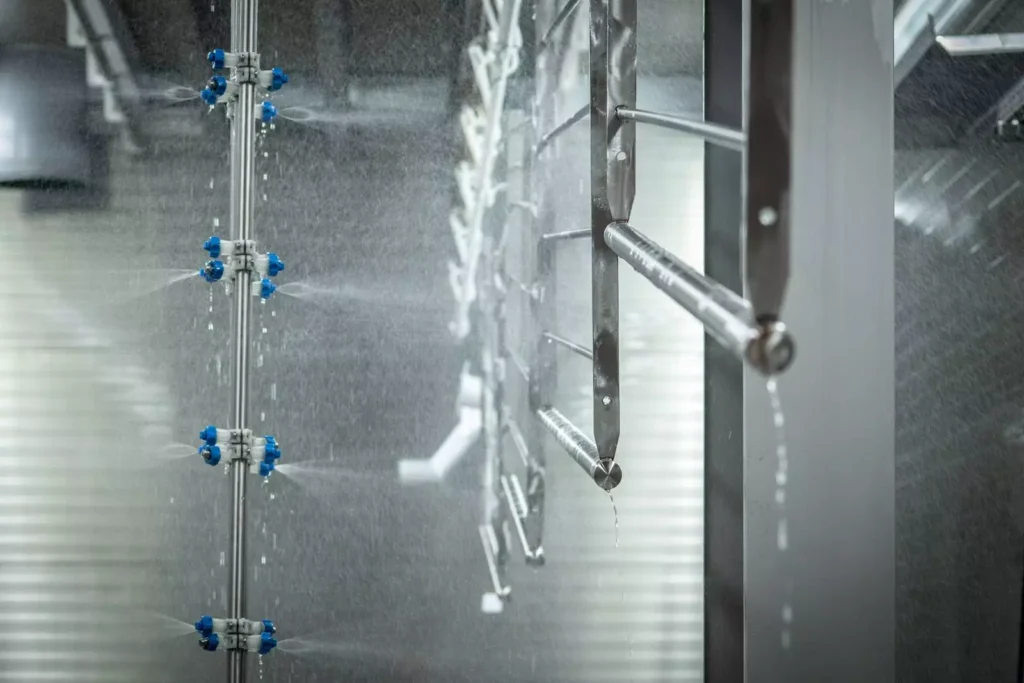
Die Vorbehandlung ist ein entscheidender Schritt in der Pulverbeschichtung und sorgt dafür, dass die Oberflächen der Werkstücke optimal vorbereitet werden, bevor die Pulverbeschichtung aufgetragen wird. Sie gewährleistet eine langlebige Haftung der Beschichtung und schützt das Material vor Korrosion und anderen schädlichen Einflüssen. Die richtige Vorbehandlung steigert die Qualität der Beschichtung erheblich und trägt zur Langlebigkeit und Widerstandsfähigkeit der beschichteten Teile bei. Dieser Leitfaden behandelt die Bedeutung, die verschiedenen Methoden und den gesamten Prozess der Vorbehandlung, um eine maximale Effizienz und Qualität zu erreichen.
1. Bedeutung der Vorbehandlung
Die Vorbehandlung ist ein Prozess, der die Oberfläche eines Werkstücks für die Pulverbeschichtung vorbereitet, indem sie gereinigt, entfettet und gegebenenfalls chemisch modifiziert wird. Diese Schritte sind notwendig, um:
- Optimale Haftung zu gewährleisten, da die Pulverbeschichtung nur auf einer sauberen, vorbereiteten Oberfläche eine dauerhafte Verbindung eingeht.
- Korrosionsschutz zu verbessern, da Verunreinigungen wie Öle, Fette, Staub oder Oxidschichten die Beschichtung schwächen und zum frühzeitigen Versagen führen könnten.
- Ästhetische Qualität sicherzustellen, denn eine saubere Oberfläche verhindert Oberflächenfehler wie Blasenbildung, ungleichmäßige Schichtdicken oder Farbunterschiede.
Der gesamte Vorbehandlungsprozess sorgt somit für eine hohe Oberflächenqualität und trägt zur Wirtschaftlichkeit des Pulverbeschichtungsprozesses bei.
2. Schritte der Vorbehandlung
Die Vorbehandlung besteht aus mehreren Schritten, die nacheinander durchgeführt werden. Diese Schritte variieren in Abhängigkeit von Material, Verunreinigungsgrad und Anforderungen an die Beschichtung.
2.1 Reinigung und Entfettung
Der erste Schritt der Vorbehandlung ist die Reinigung und Entfettung, die dazu dient, alle unerwünschten Substanzen von der Oberfläche zu entfernen, wie etwa:
- Öle und Fette: Diese sind oft Rückstände von vorhergehenden Bearbeitungsprozessen wie Stanzen, Schneiden oder Biegen und können die Haftung der Beschichtung beeinträchtigen.
- Schmutz und Staub: Verunreinigungen durch Staubpartikel können die Oberfläche uneben machen und die Beschichtungsqualität mindern.
- Oxidschichten: Besonders bei Metallen wie Stahl und Aluminium bildet sich oft eine dünne Oxidschicht, die die Beschichtung stören kann.
Die Reinigung und Entfettung kann auf verschiedene Arten erfolgen:
- Lösungsmittelreinigung: Hierbei werden organische Lösungsmittel verwendet, um Fette und Öle aufzulösen. Diese Methode ist zwar effektiv, hat jedoch umwelttechnische Nachteile und wird daher zunehmend durch umweltfreundlichere Verfahren ersetzt.
- Wässrige Reinigung: Wasserbasierte Reinigungsmittel, die Tenside enthalten, werden verwendet, um Fette und Öle zu emulgieren und abzutragen. Diese Methode ist umweltfreundlicher als Lösungsmittel und wird häufig in modernen Anlagen bevorzugt.
- Ultraschallreinigung: Bei diesem Verfahren werden Ultraschallwellen durch ein Reinigungsbad geleitet. Die Wellen erzeugen Kavitation, was kleine Blasen auf der Werkstückoberfläche bildet und Schmutzpartikel entfernt.
- Mechanische Reinigung: In einigen Fällen, insbesondere bei stark verschmutzten oder korrodierten Oberflächen, kann eine mechanische Reinigung (z. B. durch Bürsten oder Schleifen) erforderlich sein, um grobe Verunreinigungen zu entfernen.
2.2 Entrostung und Oxidentfernung
Nach der Reinigung und Entfettung muss eventuell vorhandener Rost oder Oxid von der Oberfläche entfernt werden. Oxide und Rostschichten verschlechtern die Haftung der Pulverbeschichtung und können zu Defekten führen. Methoden zur Entfernung dieser Verunreinigungen umfassen:
- Chemisches Beizen: Hierbei wird die Oberfläche mit einer sauren Lösung behandelt, um Oxide und Rost aufzulösen. Typische Säuren sind Phosphor-, Salz- oder Schwefelsäure. Dieses Verfahren eignet sich besonders für stark oxidierte Metalle.
- Sandstrahlen: Ein mechanisches Verfahren, bei dem die Oberfläche mit Schleifmitteln (z. B. Sand, Glasperlen oder Korund) beschossen wird, um Rost und Oxide zu entfernen und eine saubere, leicht raue Oberfläche zu erzeugen. Diese leichte Rauheit verbessert die Haftung der Pulverbeschichtung.
- Schleifen: Bei kleineren oder gezielten Bereichen kann Schleifen mit Schleifpapier oder Bürsten die Oxid- und Rostschicht entfernen.
2.3 Phosphatierung und Passivierung
Nach der Entfernung von Oxiden und Rost wird oft eine Phosphatierung oder Passivierung durchgeführt, um die Oberfläche für die Pulverbeschichtung vorzubereiten. Diese Schritte bieten zusätzlichen Korrosionsschutz und verbessern die Haftung der Beschichtung.
- Phosphatierung: Bei der Phosphatierung wird eine Phosphatschicht auf die Metalloberfläche aufgebracht. Diese Schicht bietet nicht nur Korrosionsschutz, sondern erhöht auch die Oberflächenrauigkeit und verbessert die Haftung der Pulverbeschichtung. Typische Phosphatierungen umfassen Zink-, Eisen- oder Manganphosphatierungen.
- Chromatierung: Chromatierungen werden vor allem bei Aluminium und Zink angewendet. Hier wird die Oberfläche mit Chromverbindungen behandelt, um eine Schutzschicht zu bilden, die die Korrosionsbeständigkeit erhöht. Da Chrom umwelt- und gesundheitsschädlich ist, wird es zunehmend durch alternative Passivierungen ersetzt.
- Nanobeschichtungen: Moderne Vorbehandlungen nutzen oft nanotechnologische Lösungen. Diese auf Silizium oder Zirkonium basierenden Beschichtungen sind umweltfreundlicher und bieten vergleichbaren Korrosionsschutz ohne den Einsatz giftiger Chemikalien wie Chrom.
3. Unterschiedliche Vorbehandlungsmethoden für verschiedene Werkstoffe
Je nach Material des Werkstücks sind unterschiedliche Vorbehandlungen erforderlich, da die Haftung und der Korrosionsschutz von der spezifischen Oberfläche abhängen.
3.1 Stahl und Eisen
Stahl und Eisen sind besonders anfällig für Rost, weshalb eine gründliche Entfettung und Rostentfernung notwendig sind. Typische Vorbehandlungen umfassen:
- Alkalische Reinigung zur Entfernung von Fetten.
- Beizen und Sandstrahlen zur Entfernung von Oxiden und zur Erzeugung einer sauberen Oberfläche.
- Zinkphosphatierung zur Verbesserung der Korrosionsbeständigkeit und der Haftung der Beschichtung.
3.2 Aluminium
Aluminium hat die Eigenschaft, eine natürliche Oxidschicht zu bilden, die sich oft negativ auf die Haftung auswirkt. Daher werden spezielle Schritte angewendet:
- Entfettung mit milden Lösungen, um die Oberfläche nicht anzugreifen.
- Beizen oder leichtes Sandstrahlen zur Entfernung der Oxidschicht.
- Chromatierung oder Alternativpassivierung zur Erhöhung der Haftung und Korrosionsbeständigkeit.
3.3 Zink und verzinkte Oberflächen
Verzinkte Oberflächen müssen sorgfältig vorbereitet werden, um die Schicht nicht zu beschädigen:
- Leichtes Beizen oder Schleifen zur Reinigung der Oberfläche und zur Entfernung von Zinkoxiden.
- Phosphatierung oder Chromatierung, um die Haftung zu verbessern und einen zusätzlichen Korrosionsschutz zu bieten.
4. Umwelt- und Sicherheitsaspekte
Ein wichtiger Aspekt bei der Vorbehandlung ist die Berücksichtigung der Umwelt- und Sicherheitsvorschriften. Viele der verwendeten Chemikalien können umweltbelastend und gesundheitsschädlich sein. Daher ist es wichtig, dass:
- Abfallprodukte ordnungsgemäß entsorgt und Abwässer gereinigt werden.
- Schutzkleidung und Belüftung für das Personal bereitgestellt werden, insbesondere bei der Arbeit mit aggressiven Säuren und Lösungsmitteln.
- Alternativen zu giftigen Chemikalien wie Chrom und Lösungsmitteln bevorzugt eingesetzt werden, um die Umweltbelastung zu reduzieren.
In modernen Anlagen wird zunehmend auf umweltfreundliche Verfahren gesetzt, wie zum Beispiel die Verwendung von Nanobeschichtungen oder die Kombination mechanischer und chemischer Verfahren, um den Einsatz schädlicher Stoffe zu minimieren.
5. Automatisierung und Effizienzsteigerung in der Vorbehandlung
In der industriellen Produktion ist die Effizienz der Vorbehandlung entscheidend. Moderne Pulverbeschichtungsanlagen setzen zunehmend auf automatisierte Vorbehandlungssysteme, die eine gleichmäßige und effiziente Bearbeitung der Werkstücke ermöglichen. Zu den Vorteilen zählen:
- Höhere Produktivität durch schnellere Bearbeitung großer Mengen.
- Konstante Qualität durch präzise Steuerung der Prozessparameter (z. B. Temperatur, Chemikalienkonzentration).
- Geringere Arbeitskosten, da manuelle Schritte reduziert werden.
- Nachhaltigkeit, da durch genau dosierte Chemikalien und optimierten Wasserverbrauch Abfälle und Emissionen verringert werden.
6. Qualitätssicherung und Kontrolle in der Vorbehandlung
Um sicherzustellen, dass die Vorbehandlung den Anforderungen entspricht, ist eine strenge Qualitätskontrolle erforderlich. Diese kann folgende Maßnahmen umfassen:
- Oberflächenanalyse: Messungen der Rauheit und Reinheit der Oberfläche, um die Haftung zu überprüfen.
- Kontrolle der Chemikalienkonzentration in Beiz- oder Phosphatierbädern, um eine gleichmäßige Behandlung zu gewährleisten.
- Korrosionstests: Testverfahren wie der Salzsprühtest können die Wirksamkeit der Vorbehandlung in Bezug auf den Korrosionsschutz bewerten.
- Protokollierung und Dokumentation der Vorbehandlungsprozesse, um die Rückverfolgbarkeit und Qualitätssicherung sicherzustellen.
7. Fazit
Die Vorbehandlung ist ein entscheidender Prozessschritt in der Pulverbeschichtung und legt den Grundstein für eine hochwertige, langlebige Beschichtung. Durch die Kombination aus Reinigung, Entrostung, Phosphatierung und anderen Verfahren wird die Oberfläche optimal vorbereitet. Moderne Methoden und Automatisierung tragen zur Effizienz und Nachhaltigkeit des Verfahrens bei und ermöglichen gleichzeitig eine verbesserte Qualität der Endprodukte.
Trocknung in der Pulverbeschichtung – Ein umfassender Überblick
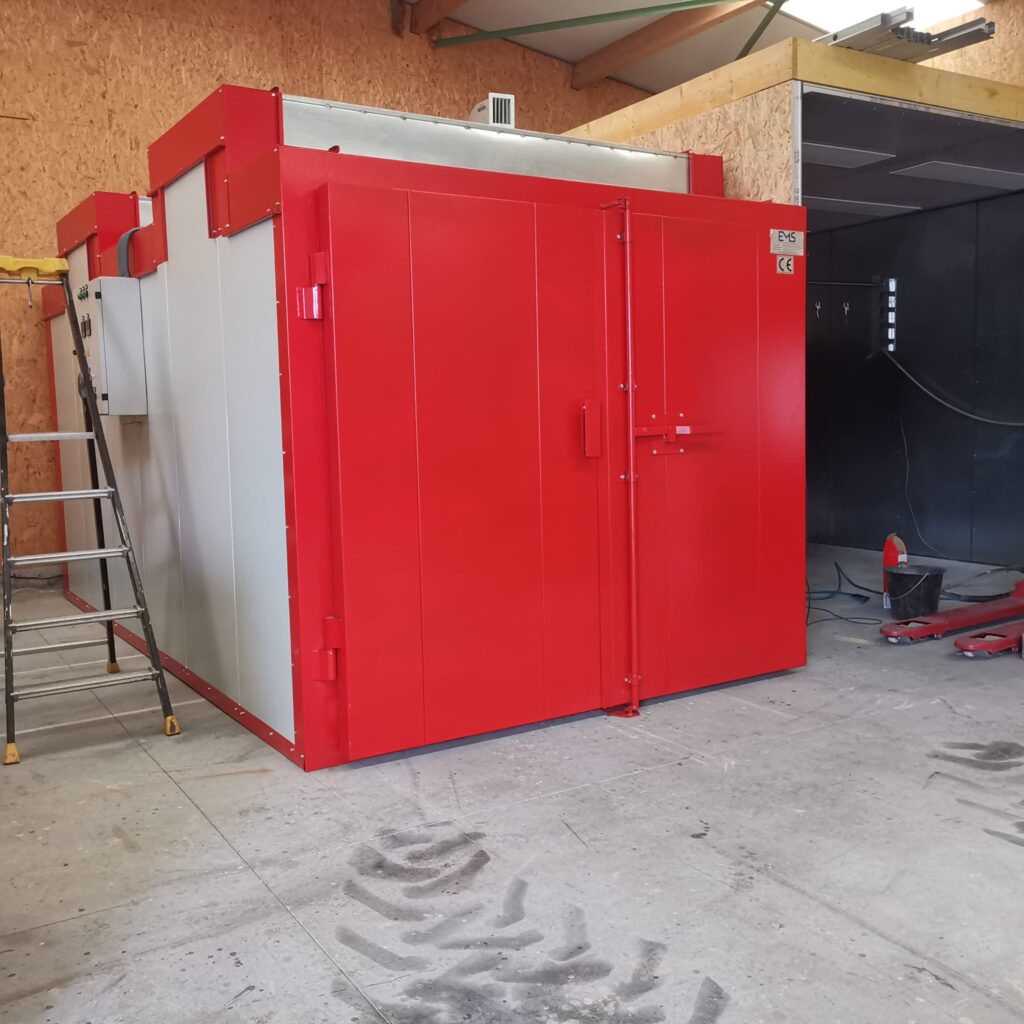
Die Trocknung ist ein zentraler Bestandteil des Pulverbeschichtungsprozesses und erfolgt nach der Vorbehandlung und vor dem eigentlichen Pulverbeschichtungsverfahren. Die Aufgabe der Trocknung besteht darin, die gereinigten und behandelten Werkstücke vollständig von Feuchtigkeit zu befreien, um eine optimale Haftung und Qualität der Pulverbeschichtung zu gewährleisten. Unvollständig getrocknete Oberflächen können zu schwerwiegenden Defekten in der Beschichtung führen, wie Blasenbildung, ungleichmäßige Farbverteilung und verminderte Korrosionsbeständigkeit. In diesem Leitfaden betrachten wir die verschiedenen Trocknungsverfahren, die physikalischen und chemischen Grundlagen, moderne Technologien und wichtige Qualitätskontrollmaßnahmen.
1. Bedeutung der Trocknung in der Pulverbeschichtung
Die Trocknung der Werkstücke nach der Vorbehandlung ist aus mehreren Gründen essenziell:
- Verhinderung von Korrosion: Restfeuchtigkeit kann dazu führen, dass die Oberfläche bereits vor der Beschichtung wieder oxidiert, was sich negativ auf die Haftung der Pulverschicht und die Haltbarkeit der Beschichtung auswirkt.
- Verbesserung der Haftung: Eine vollkommen trockene Oberfläche verbessert die Haftung des Pulvers, da das Pulver gleichmäßig haftet und keine Feuchtigkeitsbarriere die Verbindung stört.
- Qualitätssicherung: Eine unvollständige Trocknung kann während des Einbrennvorgangs zur Blasenbildung führen, die die optische und funktionelle Qualität der Beschichtung beeinträchtigt.
2. Grundlagen der Trocknung: Physikalische und Chemische Prozesse
Die Trocknung beruht auf dem Verdampfen der Restfeuchtigkeit von der Werkstückoberfläche. Dabei werden physikalische und thermische Prinzipien genutzt:
- Verdunstung: Durch die Erhöhung der Temperatur wird die Feuchtigkeit an der Oberfläche in Dampf umgewandelt und verdampft.
- Diffusion: Bei porösen Materialien, wie z.B. bestimmten Metalllegierungen, dringt die Feuchtigkeit tiefer in das Material ein und muss durch Diffusion zur Oberfläche gelangen, bevor sie verdunsten kann.
- Konvektion: Die heiße Luft, die an der Oberfläche entlangströmt, transportiert die verdampfte Feuchtigkeit ab und beschleunigt die Trocknung.
Die Effizienz dieser Prozesse wird durch die Wahl des Trocknungsverfahrens beeinflusst.
3. Verschiedene Trocknungsverfahren und deren Vor- und Nachteile
Je nach Werkstoff, Produktionsvolumen und Energieeffizienzanforderungen können unterschiedliche Trocknungsverfahren eingesetzt werden. Die gängigsten Trocknungsmethoden in der Pulverbeschichtung sind:
3.1 Umluft-Trocknung (Konvektionstrocknung)
Bei der Umluft-Trocknung werden die Werkstücke in einen Umluftofen gelegt, in dem erhitzte Luft zirkuliert. Die Temperatur liegt typischerweise zwischen 100°C und 150°C, je nach Werkstückmaterial und Feuchtigkeitsmenge.
Vorteile:
- Effizient bei großen Mengen und großen Werkstücken.
- Gleichmäßige Temperaturverteilung durch die Luftzirkulation.
Nachteile:
- Längerer Trocknungsprozess im Vergleich zu anderen Verfahren.
- Hoher Energieverbrauch, da die gesamte Luft erhitzt und konstant in Bewegung gehalten wird.
3.2 Infrarot-Trocknung
Die Infrarot-Trocknung nutzt Infrarotstrahler, um die Oberfläche des Werkstücks direkt zu erhitzen. Diese Strahlen durchdringen das Material nicht tief, sondern wirken nur an der Oberfläche, was zu einer schnellen Trocknung führt.
Vorteile:
- Schnelle Trocknung, da die Energie direkt auf die Oberfläche trifft.
- Energieeffizienter als Umlufttrockner, da nur das Werkstück und nicht die gesamte Luft erhitzt wird.
Nachteile:
- Ungeeignet für Materialien mit unregelmäßigen Oberflächen, da Schattenbereiche möglicherweise ungetrocknet bleiben.
- Höherer Wartungsaufwand für die Infrarotstrahler.
3.3 Mikrowellen-Trocknung
Mikrowellenstrahlung erzeugt Wärme direkt im Material, indem sie die Wassermoleküle anregt, was die Verdampfung beschleunigt. Die Mikrowellen-Trocknung wird in der Pulverbeschichtung jedoch selten eingesetzt und bleibt eine Nischenmethode.
Vorteile:
- Schnelle und tiefgehende Trocknung, auch für dicke oder dichte Materialien.
- Geringer Energieverbrauch, da gezielte Erhitzung im Material.
Nachteile:
- Hohe Anschaffungskosten und spezifische Anforderungen an das Material.
- Schwierige Steuerung, da unterschiedliche Materialien unterschiedlich auf Mikrowellen reagieren.
3.4 Vakuumtrocknung
In der Vakuumtrocknung wird das Werkstück in eine Kammer gelegt, in der der Luftdruck stark reduziert ist. Dadurch sinkt der Siedepunkt des Wassers, und die Feuchtigkeit verdampft bei niedrigen Temperaturen.
Vorteile:
- Sehr schonendes Verfahren, ideal für temperaturempfindliche Materialien.
- Minimierung von Oxidationsgefahr, da die Trocknung unter Ausschluss von Sauerstoff erfolgt.
Nachteile:
- Längere Trocknungszeit im Vergleich zu anderen Methoden.
- Sehr hohe Investitionskosten und aufwändige Wartung.
3.5 Hochfrequenz- oder Radiowellen-Trocknung
Dieses Verfahren ähnelt der Mikrowellen-Trocknung, jedoch werden Radiowellen statt Mikrowellen verwendet. Die Radiowellen erzeugen Wärme durch die Bewegung von Wasser- und Ionenmolekülen im Werkstück.
Vorteile:
- Gleichmäßige Erwärmung und Trocknung auch bei komplex geformten Werkstücken.
- Effizient bei Werkstücken mit unterschiedlichen Materialdichten.
Nachteile:
- Komplizierte Steuerung und teure Geräte.
- Besonders hohe Anforderungen an die Werkstoffzusammensetzung.
4. Trocknungsparameter und Prozesssteuerung
Die Effizienz und Qualität der Trocknung wird maßgeblich von den Trocknungsparametern bestimmt. Eine präzise Steuerung dieser Parameter ist entscheidend für eine optimale Trocknung:
- Temperatur: Eine höhere Trocknungstemperatur verkürzt die Trocknungszeit, kann jedoch temperaturempfindliche Materialien schädigen.
- Luftfeuchtigkeit: Eine niedrige relative Luftfeuchtigkeit unterstützt die Trocknung, da die trockene Luft die verdampfte Feuchtigkeit besser aufnimmt.
- Luftgeschwindigkeit: Eine höhere Luftgeschwindigkeit transportiert die Feuchtigkeit schneller ab, ist jedoch energieintensiv.
- Dauer: Die Verweildauer des Werkstücks im Trocknungsofen muss optimal eingestellt werden, um sicherzustellen, dass auch tiefer liegende Feuchtigkeit verdampft ist.
Moderne Trocknungssysteme setzen zunehmend auf automatische Steuerung und Sensorik, die die Parameter in Echtzeit überwachen und anpassen. Beispielsweise können Feuchtigkeits- und Temperatursensoren den Trocknungsprozess optimal regeln und so Energieverbrauch und Trocknungszeit minimieren.
5. Nachhaltigkeit und Energieeffizienz in der Trocknung
Die Trocknung ist einer der energieintensivsten Schritte im Pulverbeschichtungsprozess. Daher ist es wichtig, Maßnahmen zur Nachhaltigkeit und Energieeffizienz zu ergreifen:
- Wärmerückgewinnung: Die Abwärme des Trocknungsofens kann genutzt werden, um andere Bereiche der Anlage zu beheizen oder die Vorwärmung der Werkstücke zu unterstützen.
- Optimierung der Ofentemperatur: Durch präzise Steuerung kann die Temperatur auf das nötige Minimum gesenkt werden, was Energie spart und die Umweltbelastung reduziert.
- Nutzung erneuerbarer Energien: Immer mehr Unternehmen setzen auf den Einsatz von Solarenergie oder anderen erneuerbaren Energiequellen, um den Energiebedarf der Trocknung zu decken.
- Regelmäßige Wartung: Eine gute Wartung und Reinigung der Trocknungsanlagen gewährleistet eine gleichbleibende Effizienz und verlängert die Lebensdauer der Anlagen.
6. Qualitätskontrolle in der Trocknung
Um die Qualität des Trocknungsprozesses sicherzustellen, sind verschiedene Qualitätskontrollen notwendig:
- Feuchtigkeitsprüfung: Nach der Trocknung wird die Restfeuchtigkeit im Werkstück gemessen, um sicherzustellen, dass das Material vollständig trocken ist.
- Temperaturprotokollierung: Die Temperaturkurven werden aufgezeichnet, um sicherzustellen, dass die vorgegebenen Temperaturbereiche eingehalten wurden.
- Optische Inspektion: Visuelle Kontrollen auf mögliche Trocknungsdefekte wie Flecken oder Verfärbungen.
- Testbeschichtungen: In manchen Fällen wird eine Testbeschichtung aufgebracht, um die Qualität des Trocknungsergebnisses zu überprüfen.
7. Automatisierung und moderne Technologien in der Trocknung
In modernen Produktionsanlagen werden zunehmend automatisierte Trocknungssysteme eingesetzt, die für höhere Präzision, Geschwindigkeit und Energieeffizienz sorgen:
- Automatische Trocknungsöfen: Diese Öfen verfügen über programmierbare Steuerungen, die die Trocknungstemperatur, -zeit und -geschwindigkeit exakt regeln.
- Sensorintegrierte Trocknungssysteme: Sensoren messen die Feuchtigkeit in Echtzeit und passen die Trocknungsparameter automatisch an.
- Datengestützte Prozessoptimierung: Moderne Anlagen verwenden Datenanalysen, um den Trocknungsprozess kontinuierlich zu verbessern und den Energieverbrauch zu minimieren.
- Integration mit IoT und Industrie 4.0: Vernetzte Trocknungssysteme ermöglichen eine Fernüberwachung und -steuerung sowie die Integration in größere Fertigungssysteme für eine nahtlose Produktionskette.
8. Herausforderungen und Innovationen in der Trocknungstechnik
Die Anforderungen an die Trocknungstechnik wachsen stetig, da neue Materialien und Beschichtungsverfahren immer spezifischere Trocknungsbedingungen erfordern:
- Hochfeste Legierungen und Verbundwerkstoffe benötigen angepasste Trocknungsparameter, da sie oft temperaturempfindlicher sind.
- Spezialbeschichtungen erfordern eine besonders gleichmäßige und restfeuchtefreie Trocknung, um ihre Haftung und Qualität sicherzustellen.
- Neue, energieeffiziente Technologien wie Mikrowellen- oder Radiowellentrocknung werden weiter erforscht und könnten zukünftig eine größere Rolle in der industriellen Beschichtung spielen.
- Nachhaltige Materialien und umweltfreundliche Chemikalien verlangen oft besondere Trocknungsbedingungen, um ihre umweltfreundlichen Eigenschaften zu erhalten.
Fazit
Die Trocknung ist ein unverzichtbarer Bestandteil des Pulverbeschichtungsprozesses und stellt sicher, dass die Oberflächen perfekt für die Beschichtung vorbereitet sind. Durch die Wahl des richtigen Trocknungsverfahrens, die präzise Steuerung der Parameter und den Einsatz moderner Technologien kann der Trocknungsprozess effizient, energiesparend und in höchster Qualität durchgeführt werden. Mit der richtigen Kombination aus Technologie, Prozesssteuerung und Qualitätskontrolle sorgt die Trocknung für eine hochwertige und langlebige Pulverbeschichtung.
Die Pulverbeschichtungskabine – Ein Leitfaden für Aufbau, Funktionsweise und Innovationen
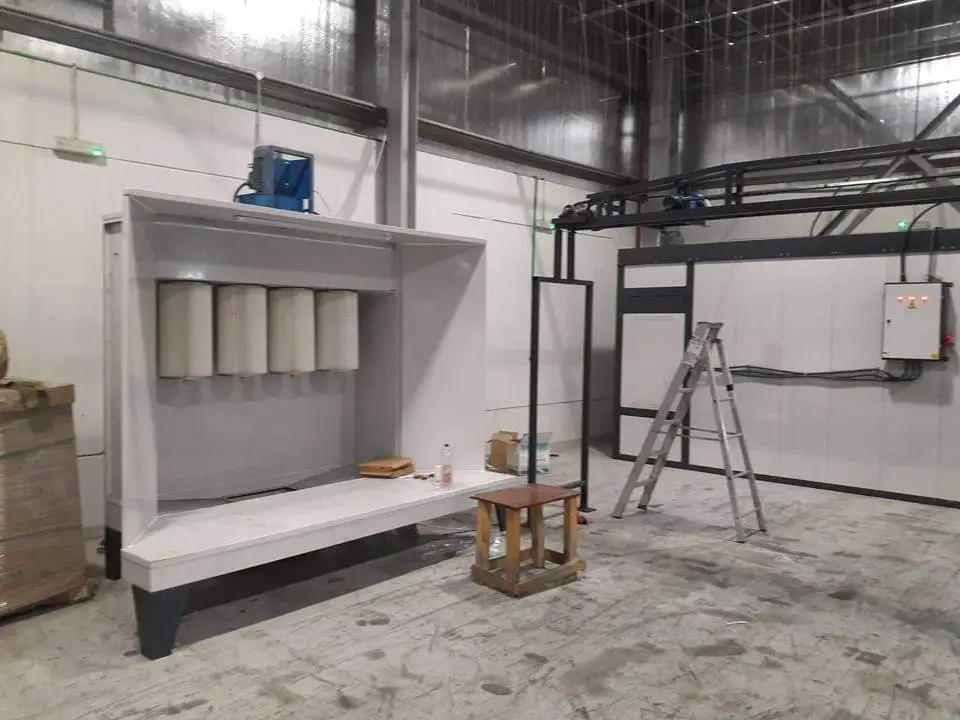
Die Pulverbeschichtungskabine ist ein Herzstück des Pulverbeschichtungsprozesses. In dieser speziellen Kabine wird das Beschichtungspulver auf die Werkstücke aufgetragen, bevor sie in den Einbrennofen gelangen. Eine effektive Beschichtungskabine stellt sicher, dass das Pulver gleichmäßig und präzise aufgebracht wird, um eine hochwertige, haltbare und ästhetische Beschichtung zu gewährleisten. Darüber hinaus wird in der Kabine überschüssiges Pulver kontrolliert und zurückgewonnen, was sowohl die Effizienz erhöht als auch die Umweltbelastung minimiert. Dieser Leitfaden beleuchtet die Funktionsweise, die verschiedenen Kabinentypen, technische Details, Umweltaspekte sowie moderne Entwicklungen und Innovationen in der Pulverbeschichtungskabinentechnologie.
1. Bedeutung und Funktion der Pulverbeschichtungskabine
Die Pulverbeschichtungskabine hat mehrere entscheidende Funktionen:
- Effizientes Auftragen des Pulvers: Die Kabine ermöglicht es, das Pulver gleichmäßig auf die Oberfläche des Werkstücks zu sprühen. Das Pulver wird dabei elektrostatisch aufgeladen, sodass es sich optimal auf der Oberfläche anlagert.
- Sicherheitskontrolle und Emissionsschutz: Pulverbeschichtungskabinen sind so konzipiert, dass sie das Austreten von Pulverpartikeln in die Umgebung minimieren und das Pulver sicher und effizient handhaben.
- Pulverrückgewinnung und Recycling: Durch spezielle Filtersysteme wird überschüssiges Pulver aufgefangen, gereinigt und für eine erneute Verwendung aufbereitet.
Eine hochwertige Beschichtungskabine ist somit wesentlich für die Qualität der Beschichtung und trägt gleichzeitig zu einem wirtschaftlichen und nachhaltigen Produktionsprozess bei.
2. Aufbau und Komponenten einer Pulverbeschichtungskabine
Eine Pulverbeschichtungskabine besteht aus mehreren Komponenten, die jeweils spezifische Aufgaben übernehmen, um eine einwandfreie Beschichtung zu gewährleisten:
2.1 Gehäuse und Kabinenwände
Das Gehäuse besteht aus robusten Materialien, die eine hohe Abriebfestigkeit aufweisen und leicht zu reinigen sind. Typische Materialien sind Edelstahl oder verzinktes Stahlblech, das mit einer speziellen Beschichtung versehen ist, um die Haftung von Pulverrückständen zu minimieren.
2.2 Pulverpistolen und Applikationssystem
Die Pulverpistolen sprühen das Pulver elektrostatisch aufgeladen auf die Werkstücke. Die wichtigsten Komponenten hierbei sind:
- Elektrostatische Aufladung: Diese wird entweder über Tribo- oder Koronapistolen erzeugt. Koronapistolen verwenden eine Hochspannungselektrode, die das Pulver auflädt, während es die Pistole verlässt. Tribopistolen laden das Pulver durch Reibung auf.
- Automatische oder manuelle Pistolen: Je nach Anwendung und Anforderungen können Pulverbeschichtungskabinen mit automatischen oder manuellen Pulverpistolen ausgestattet sein.
- Steuerungssystem: Moderne Beschichtungskabinen verfügen über computergesteuerte Systeme, die den Pulverauftrag überwachen und steuern, um die gleichmäßige Schichtdicke und Präzision der Beschichtung sicherzustellen.
2.3 Pulverrückgewinnungssystem
Ein zentrales Merkmal vieler Pulverbeschichtungskabinen ist das Pulverrückgewinnungssystem. Hierbei wird überschüssiges Pulver abgesaugt, gefiltert und wiederverwendet. Die Rückgewinnungssysteme umfassen:
- Filtersysteme: Filtersysteme wie Zyklon- und Kassettenfilter filtern das überschüssige Pulver aus der Kabinenluft und sammeln es in speziellen Behältern.
- Pulverbehälter und Fördersysteme: Das zurückgewonnene Pulver wird in Pulverbehältern gesammelt und anschließend in das Fördersystem zurückgeleitet, um erneut aufgetragen zu werden.
2.4 Absaugsystem und Lüftung
Ein leistungsfähiges Absaugsystem sorgt dafür, dass das überschüssige Pulver und der Pulverdampf aus der Kabine entfernt werden, ohne die Werkstücke zu beeinträchtigen oder den Arbeitsbereich zu verunreinigen. Das Absaugsystem arbeitet in der Regel mit einem leistungsstarken Ventilator und Filtern, die die Partikel abscheiden und die Luft reinigen.
2.5 Steuerung und Automatisierung
Die Steuerungseinheit umfasst das Bedienfeld und die Steuersoftware, die alle Komponenten der Kabine miteinander verbindet. Moderne Kabinen setzen auf computergestützte Steuerungssysteme, die den Pulverfluss, die Elektrostatische Ladung und die Absaugung präzise regeln, um die höchste Effizienz und Qualität zu erzielen.
3. Typen von Pulverbeschichtungskabinen
Je nach Art der Beschichtungsaufgabe und den Anforderungen der Fertigung kommen unterschiedliche Kabinentypen zum Einsatz:
3.1 Manuelle Pulverbeschichtungskabine
Manuelle Kabinen sind häufig in kleineren Produktionsstätten oder für Einzelstückfertigungen anzutreffen. Die Bedienung erfolgt durch einen Mitarbeiter, der die Pulverpistole manuell führt und die Beschichtung auf das Werkstück aufbringt.
Vorteile:
- Flexibilität und Anpassungsfähigkeit für kleine Serien und individuelle Beschichtungen.
- Geringe Investitionskosten im Vergleich zu automatisierten Kabinen.
Nachteile:
- Geringere Produktivität und höhere Abhängigkeit von der Geschicklichkeit des Bedieners.
- Keine kontinuierliche Pulverrückgewinnung bei älteren Modellen.
3.2 Automatische Pulverbeschichtungskabine
Automatische Kabinen werden für die Großserienproduktion eingesetzt und sind mit automatischen Pulverpistolen ausgestattet, die computergesteuert den Pulverauftrag präzise steuern.
Vorteile:
- Hohe Effizienz und gleichbleibende Beschichtungsqualität durch automatisierten Auftrag.
- Integration in automatisierte Fertigungslinien und kontinuierliche Pulverrückgewinnung.
Nachteile:
- Höhere Anschaffungskosten und höhere Anforderungen an Wartung und Bedienung.
- Geringe Flexibilität bei kleineren Aufträgen.
3.3 Schnellwechsel-Kabinen
Diese Kabinen sind speziell für die schnelle Farbwechselproduktion konzipiert, was sie ideal für Produktionslinien mit vielen Farbvariationen macht. Schnellwechsel-Kabinen verfügen über ein automatisiertes Reinigungssystem, das das alte Pulver effizient entfernt, bevor ein neuer Farbton aufgetragen wird.
Vorteile:
- Effizienter und schneller Farbwechsel ohne Produktionsunterbrechung.
- Reduzierung des Pulververlustes durch präzise Reinigung und Rückgewinnung.
Nachteile:
- Höherer Investitionsaufwand und aufwändige Technik.
- Aufwändigere Wartung und Reinigung.
4. Verfahren und Arbeitsweise der Pulverbeschichtungskabine
Der Ablauf innerhalb der Pulverbeschichtungskabine erfolgt in mehreren Schritten, die präzise aufeinander abgestimmt sind, um eine gleichmäßige und haltbare Pulverbeschichtung zu gewährleisten.
4.1 Vorbereitung der Werkstücke
Die Werkstücke werden auf speziellen Gestellen oder Haken in die Kabine eingeführt. Der Einsatz von Haltevorrichtungen sorgt dafür, dass die Werkstücke optimal positioniert und elektrisch geerdet sind, um die elektrostatische Aufladung und Anhaftung des Pulvers zu verbessern.
4.2 Pulverbeschichtung durch elektrostatische Aufladung
In der Kabine wird das Pulver elektrostatisch aufgeladen und auf das Werkstück aufgesprüht. Die elektrostatische Aufladung sorgt dafür, dass das Pulver gleichmäßig verteilt und angezogen wird. Dabei werden verschiedene Methoden zur Aufladung verwendet:
- Koronaverfahren: Hier wird das Pulver mit Hilfe einer Elektrode aufgeladen, die ein elektrisches Feld erzeugt.
- Triboverfahren: Das Pulver wird durch Reibung an der Pistolenwand aufgeladen, was eine präzise Steuerung des Pulverauftrags ermöglicht.
4.3 Rückgewinnung von überschüssigem Pulver
Überschüssiges Pulver wird durch das Rückgewinnungssystem abgesaugt, gefiltert und in speziellen Sammelbehältern gesammelt. Dieses Pulver kann gereinigt und wiederverwendet werden, was sowohl die Kosten reduziert als auch die Umwelt schont.
4.4 Luftreinigung und Filterung
Um ein Austreten von Pulverstaub zu verhindern, werden Luft und Pulverpartikel durch Filtersysteme gereinigt und von der Kabine abgesaugt. Diese Filter müssen regelmäßig gewartet werden, um ihre Effizienz zu gewährleisten und ein sauberes Arbeitsumfeld sicherzustellen.
5. Qualitätskontrolle und Wartung der Pulverbeschichtungskabine
Eine regelmäßige Qualitätskontrolle und Wartung ist entscheidend, um eine hohe Beschichtungsqualität und Effizienz aufrechtzuerhalten. Die Wartungsmaßnahmen umfassen:
- Reinigung der Kabinenwände: Regelmäßige Reinigung der Wände verhindert, dass Pulverreste sich ablagern und die Beschichtungsqualität beeinträchtigen.
- Überprüfung der Pulverpistolen: Die Pistolen müssen regelmäßig auf Funktion und Abnutzung überprüft werden.
- Filterwechsel: Die Filter im Rückgewinnungssystem müssen in regelmäßigen Abständen ausgetauscht werden, um die Effizienz des Systems zu gewährleisten.
- Überprüfung der Steuerungseinheit: Die Steuerungseinheit sollte regelmäßig auf ordnungsgemäße Funktion und Kalibrierung kontrolliert werden.
6. Nachhaltigkeit und Umweltaspekte
Umweltfreundliche Beschichtungsprozesse spielen eine zunehmende Rolle in der Industrie. Moderne Pulverbeschichtungskabinen tragen zur Nachhaltigkeit bei:
- Effiziente Pulverrückgewinnung: Das Rückgewinnungssystem reduziert den Pulververlust und verringert den Materialverbrauch.
- Weniger Emissionen: Pulverbeschichtungskabinen minimieren den Einsatz von Lösungsmitteln und erzeugen daher weniger flüchtige organische Verbindungen (VOC).
- Energieeffizienz: Fortschrittliche Steuerungen und Isolierungstechniken reduzieren den Energieverbrauch der Kabine.
7. Zukunft und Innovationen in der Pulverbeschichtungskabinentechnologie
Die Pulverbeschichtungstechnologie entwickelt sich stetig weiter, und neue Innovationen verbessern die Effizienz, Umweltfreundlichkeit und Qualität des Beschichtungsprozesses:
- Automatisierte und Roboter-Pulverbeschichtung: Moderne Kabinen können mit Robotern ausgestattet werden, die die Beschichtung vollautomatisch und präzise ausführen, was die Effizienz und Konsistenz der Beschichtung erhöht.
- KI-gestützte Steuerungssysteme: Künstliche Intelligenz wird zunehmend in Steuerungssystemen integriert, um den Pulverauftrag zu optimieren, die Rückgewinnung zu maximieren und den Energieverbrauch zu minimieren.
- Energieeffiziente Infrarot- und UV-Trocknung: Die Kombination von Pulverbeschichtung und energiesparenden Trocknungstechniken reduziert den Energiebedarf und sorgt für eine schnellere und gleichmäßigere Aushärtung.
- Umweltfreundliche Beschichtungsmaterialien: Neue Pulverformulierungen mit geringem Schadstoffgehalt und ohne toxische Bestandteile tragen zur Nachhaltigkeit bei und bieten weiterhin hohen Korrosionsschutz und Farbvielfalt.
Fazit
Die Pulverbeschichtungskabine ist ein zentraler Baustein für eine hochwertige und nachhaltige Pulverbeschichtung. Durch den gezielten Einsatz moderner Technologie, automatisierter Steuerung und effizienter Rückgewinnungssysteme bieten Pulverbeschichtungskabinen heute eine hohe Qualität, Wirtschaftlichkeit und Umweltfreundlichkeit. Zukünftige Innovationen und Entwicklungen in der Robotertechnik, Künstlichen Intelligenz und Nachhaltigkeit werden den Nutzen und die Effizienz von Pulverbeschichtungskabinen weiter steigern und die Branche nachhaltig prägen.
Der Einbrennofen in der Pulverbeschichtung – Technik, Funktionsweise und Innovationen
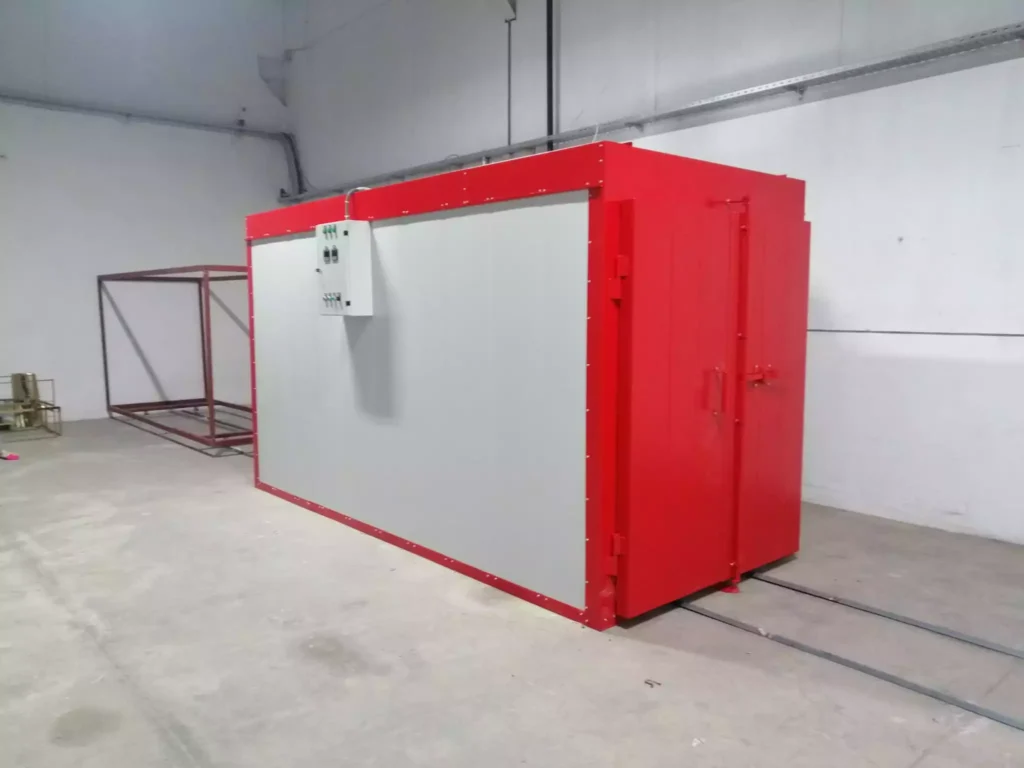
Der Einbrennofen ist eine wesentliche Komponente im Pulverbeschichtungsprozess und übernimmt die Aufgabe, das aufgetragene Pulverbeschichtungsmaterial zu härten. In einem kontrollierten Erhitzungsprozess wird das Pulver geschmolzen und zu einer gleichmäßigen, dauerhaften Schicht auf dem Werkstück ausgehärtet. Ein qualitativ hochwertiger Einbrennofen sorgt dafür, dass die Beschichtung optimal haftet, widerstandsfähig ist und auch ästhetisch ansprechend aussieht. Dieser Leitfaden bietet einen umfassenden Überblick über die Funktionsweise, die verschiedenen Ofentypen, technische Besonderheiten, wichtige Steuerungsparameter sowie neue Innovationen im Bereich Einbrenntechnik.
1. Die Bedeutung des Einbrennofens in der Pulverbeschichtung
Der Einbrennofen ist der letzte Verarbeitungsschritt im Pulverbeschichtungsprozess, in dem das aufgesprühte Pulver unter hoher Temperatur geschmolzen und vernetzt wird, um eine feste Beschichtung zu schaffen. Die Hauptaufgaben des Einbrennofens sind:
- Aushärtung der Pulverbeschichtung: Durch kontrolliertes Erhitzen wird das Pulver geschmolzen und chemisch vernetzt, was zu einer robusten, einheitlichen Beschichtung führt.
- Erhöhung der Widerstandsfähigkeit: Eine optimal gehärtete Beschichtung ist widerstandsfähig gegenüber Korrosion, Kratzern und chemischen Einflüssen.
- Optische Qualität: Ein gleichmäßiger Einbrennprozess verhindert Blasenbildung, ungleichmäßige Farbverteilung und andere Oberflächendefekte.
Eine effektive Einbrennphase ist somit entscheidend für die Langlebigkeit und die Ästhetik der Beschichtung.
2. Aufbau und Funktionsweise eines Einbrennofens
Ein Einbrennofen besteht aus mehreren Komponenten, die auf eine präzise Steuerung der Temperatur, Luftzirkulation und Verweilzeit ausgelegt sind, um die optimale Aushärtung des Pulvers zu gewährleisten.
2.1 Ofengehäuse und Isolierung
Das Gehäuse besteht in der Regel aus robustem, hitzebeständigem Material, das zusätzlich mit einer Isolationsschicht versehen ist, um Wärmeverluste zu minimieren und Energie zu sparen. Hochwertige Isolierung verhindert zudem, dass die Außentemperatur der Anlage die Arbeitsumgebung aufheizt.
2.2 Heizsystem
Ein zentraler Bestandteil des Einbrennofens ist das Heizsystem, das die erforderliche Temperatur im Innenraum erzeugt. Je nach Art des Ofens kann die Wärme durch verschiedene Quellen erzeugt werden:
- Gasheizung: Gasbrenner sind häufig in größeren Anlagen und Produktionslinien zu finden, da sie schnelle Aufheizzeiten und konstante Temperaturen bieten.
- Elektroheizung: Elektrische Heizelemente eignen sich besonders für kleinere und präzise Steuerung. Sie erzeugen Wärme durch elektrischen Strom und können schneller und präziser reguliert werden.
- Infrarot-Heizung: Infrarotheizelemente erzeugen Wärme durch Strahlung, die direkt auf die Oberfläche des Werkstücks trifft. Diese Methode ist energieeffizient und ermöglicht eine schnelle Erwärmung.
2.3 Luftzirkulationssystem
Die gleichmäßige Verteilung der Wärme ist entscheidend für eine konsistente Aushärtung. Das Luftzirkulationssystem, bestehend aus Ventilatoren und Kanälen, verteilt die heiße Luft gleichmäßig im Ofen, um Temperaturabweichungen zu minimieren und eine gleichmäßige Erwärmung der Werkstücke zu erreichen.
2.4 Steuerung und Temperaturregelung
Moderne Einbrennöfen sind mit präzisen Steuerungseinheiten ausgestattet, die die Temperatur im Ofen kontrollieren und überwachen. Die Steuerungseinheit regelt die Heizintensität und die Verweilzeit der Werkstücke im Ofen und gewährleistet eine exakte Einhaltung der gewünschten Temperaturkurven. Die meisten Steuerungen erlauben es, verschiedene Programme für unterschiedliche Materialien und Beschichtungsarten einzurichten.
3. Typen von Einbrennöfen
Einbrennöfen gibt es in verschiedenen Ausführungen, die jeweils für unterschiedliche Anforderungen und Produktionsmengen optimiert sind. Die gängigsten Typen sind:
3.1 Durchlaufofen
Durchlauföfen sind kontinuierliche Öfen, in denen die Werkstücke auf Förderbändern oder in Hängegestellen durch den Ofen transportiert werden. Sie eignen sich besonders für große Produktionsmengen, da sie einen schnellen und gleichmäßigen Durchlauf ermöglichen.
Vorteile:
- Hohe Produktivität, da die Werkstücke ohne Unterbrechung durch den Ofen transportiert werden.
- Gleichmäßige Erwärmung und konstante Produktionsgeschwindigkeit.
Nachteile:
- Hohe Anschaffungskosten.
- Begrenzte Flexibilität bei wechselnden Beschichtungsaufträgen.
3.2 Kammerofen (Batch-Ofen)
Kammeröfen, auch Batch-Öfen genannt, sind geschlossene Öfen, in die die Werkstücke manuell oder automatisch eingeschoben und für eine festgelegte Zeit erhitzt werden. Sie sind für kleinere Produktionsmengen oder Einzelanfertigungen geeignet.
Vorteile:
- Flexibel und anpassungsfähig, da verschiedene Chargen und unterschiedliche Werkstücke verarbeitet werden können.
- Geringere Investitionskosten im Vergleich zu Durchlauföfen.
Nachteile:
- Geringere Produktivität, da der Ofen nach jeder Charge neu geladen werden muss.
- Unregelmäßige Temperaturverteilung bei großen Werkstücken oder -mengen.
3.3 Infrarot-Ofen
Infrarot-Öfen nutzen Infrarotstrahler, um die Beschichtung durch Wärmestrahlung zu erhitzen. Diese Öfen sind effizient und bieten eine schnelle Erwärmung, besonders für dünne oder leicht zugängliche Werkstücke.
Vorteile:
- Energieeffizient und schnell, da die Strahlung direkt auf das Werkstück wirkt.
- Geringerer Platzbedarf und kürzere Prozesszeiten.
Nachteile:
- Geringere Flexibilität für Werkstücke mit komplexen Formen, da Schattenbereiche ungleichmäßig erhitzt werden können.
- Höherer Wartungsaufwand für Infrarotstrahler.
3.4 Hybridofen
Hybridöfen kombinieren verschiedene Heiztechnologien, z. B. Infrarot und Konvektion, um die Vorteile beider Ansätze zu nutzen. Diese Öfen ermöglichen eine schnelle Aufheizzeit und eine gleichmäßige Aushärtung, auch bei komplexen Werkstücken.
Vorteile:
- Hohe Flexibilität und anpassungsfähig an unterschiedliche Werkstückgeometrien.
- Effizientere Energieausnutzung durch Kombination von Technologien.
Nachteile:
- Hohe Investitionskosten.
- Erhöhte Anforderungen an Wartung und Steuerung.
4. Steuerungsparameter und Prozessüberwachung
Für eine optimale Beschichtung ist die präzise Steuerung der Aushärteparameter entscheidend. Die wichtigsten Steuerungsparameter umfassen:
- Temperatur: Die meisten Pulverbeschichtungen erfordern Temperaturen zwischen 160°C und 220°C. Eine genaue Steuerung stellt sicher, dass das Pulver nicht über- oder unterhärtet wird.
- Verweilzeit: Die Zeit, die das Werkstück im Ofen verbringt, muss an die Materialdicke und die spezifischen Anforderungen der Beschichtung angepasst sein.
- Luftzirkulation: Eine gleichmäßige Luftzirkulation vermeidet Temperaturunterschiede und sorgt für eine konsistente Erwärmung des Werkstücks.
Moderne Einbrennöfen verfügen über Sensoren und automatisierte Steuerungssysteme, die die Parameter kontinuierlich überwachen und anpassen, um optimale Bedingungen zu gewährleisten. Durch die Datenprotokollierung und Prozessüberwachung können Qualitätsmängel frühzeitig erkannt und vermieden werden.
5. Wartung und Qualitätssicherung im Einbrennofen
Regelmäßige Wartung und Qualitätssicherung sind entscheidend, um eine hohe Produktqualität und Betriebseffizienz aufrechtzuerhalten. Wichtige Maßnahmen sind:
- Überprüfung der Isolierung: Die Isolierung sollte regelmäßig auf Abnutzung oder Beschädigung kontrolliert werden, um Wärmeverluste zu vermeiden.
- Kalibrierung der Temperaturfühler: Regelmäßige Kalibrierungen stellen sicher, dass die gemessenen Temperaturen präzise sind und den Prozessanforderungen entsprechen.
- Reinigung der Heizsysteme: Ablagerungen oder Verunreinigungen in Heizsystemen können die Heizleistung beeinträchtigen. Regelmäßige Reinigung ist erforderlich, um eine gleichmäßige Wärmeverteilung zu gewährleisten.
- Überprüfung des Luftzirkulationssystems: Ventilatoren und Filter sollten gereinigt und auf Funktionsfähigkeit überprüft werden, um eine gleichmäßige Wärmeverteilung zu gewährleisten.
Qualitätssicherungstests, wie die Kontrolle der Schichtdicke und Haftung der Beschichtung, werden an den ausgehärteten Werkstücken durchgeführt, um sicherzustellen, dass der Einbrennprozess den Anforderungen entspricht.
6. Nachhaltigkeit und Energieeffizienz im Einbrennofen
Einbrennöfen verbrauchen aufgrund der hohen Temperaturen erhebliche Mengen an Energie. Daher gewinnen Energieeffizienz und Nachhaltigkeit zunehmend an Bedeutung. Wichtige Maßnahmen zur Energieeinsparung sind:
- Wärmerückgewinnungssysteme: Die Abwärme des Ofens kann zur Vorwärmung der Werkstücke oder für andere Produktionsbereiche genutzt werden.
- Isolierte Ofenwände: Hochwertige Isolierungen reduzieren Wärmeverluste und senken den Energieverbrauch.
- Intelligente Steuerungssysteme: Durch bedarfsgesteuerte Heizsysteme und Echtzeitüberwachung der Temperaturen kann der Energieverbrauch optimal angepasst werden.
- Nutzung erneuerbarer Energien: Der Betrieb der Öfen kann, je nach Standort und Verfügbarkeit, durch erneuerbare Energien wie Solar- oder Windenergie unterstützt werden.
Diese Maßnahmen reduzieren nicht nur die Betriebskosten, sondern leisten auch einen Beitrag zur Nachhaltigkeit der Produktionskette.
7. Zukunft und Innovationen im Bereich Einbrennofen
Die Entwicklung im Bereich Einbrennöfen zeigt klare Trends in Richtung Effizienz, Automatisierung und Umweltfreundlichkeit. Neue Technologien und innovative Lösungen bieten bereits jetzt beeindruckende Potenziale für die Zukunft der Pulverbeschichtung.
- Automatisierung und Robotik: Moderne Anlagen setzen zunehmend auf Robotertechnologie, die das Beladen und Entladen der Öfen automatisiert und die Effizienz steigert.
- KI-gesteuerte Temperaturregelung: Künstliche Intelligenz wird eingesetzt, um Temperaturmuster und -verläufe zu analysieren und die Prozessparameter kontinuierlich zu optimieren.
- Schnellheiztechnologien: Neue Heizmethoden wie Hochfrequenz- oder Mikrowellentechnologie ermöglichen extrem kurze Aufheizzeiten, was den Energieverbrauch und die Durchlaufzeit erheblich reduziert.
- Grünere Alternativen: Der Einsatz umweltfreundlicher Pulverformeln, die bei niedrigeren Temperaturen ausgehärtet werden können, trägt zur Verringerung des Energiebedarfs und der Umweltbelastung bei.
Diese Entwicklungen tragen dazu bei, die Pulverbeschichtungsindustrie effizienter, umweltfreundlicher und zukunftssicher zu gestalten.
Fazit
Einbrennöfen sind essenzielle Anlagen in der Pulverbeschichtung und spielen eine zentrale Rolle in der Qualität und Langlebigkeit der Beschichtung. Durch den präzisen Einsatz moderner Steuerungstechnologien, den Fokus auf Energieeffizienz und die Integration neuer Technologien kann der Einbrennprozess optimiert werden. Innovationen wie KI-gesteuerte Steuerungen, hybride Heiztechniken und nachhaltigere Pulverformulierungen markieren die Zukunft der Pulverbeschichtung und eröffnen neue Möglichkeiten zur Verbesserung des Produktionsprozesses. Ein gut gewarteter und moderner Einbrennofen sichert nicht nur eine hochwertige Endbeschichtung, sondern trägt auch zur Nachhaltigkeit und Effizienz der gesamten Produktionskette bei.
Die Abkühlzone in der Pulverbeschichtung – Aufbau, Funktionsweise und Effizienzsteigerung

Die Abkühlzone ist der letzte Schritt im Pulverbeschichtungsprozess und spielt eine entscheidende Rolle für die Qualität und Haltbarkeit der Endbeschichtung. Nachdem das Werkstück im Einbrennofen erhitzt und die Beschichtung vollständig gehärtet wurde, muss das Werkstück kontrolliert abgekühlt werden, bevor es weiterverarbeitet, verpackt oder gelagert werden kann. Eine gleichmäßige und kontrollierte Abkühlung ist wichtig, um thermische Spannungen, Verformungen und mögliche Oberflächendefekte zu vermeiden. In diesem umfassenden Leitfaden werden die Funktionen, der Aufbau und die verschiedenen Technologien der Abkühlzone sowie innovative Ansätze zur Effizienzsteigerung und Nachhaltigkeit vorgestellt.
1. Bedeutung der Abkühlzone in der Pulverbeschichtung
Die Abkühlzone ist ein zentraler Schritt, der dazu beiträgt, die Qualität und die physikalischen Eigenschaften der beschichteten Oberfläche zu sichern:
- Vermeidung von Spannungen und Rissen: Eine kontrollierte Abkühlung verhindert das Entstehen von thermischen Spannungen und minimiert das Risiko von Rissen oder Abplatzungen.
- Oberflächenqualität und Ästhetik: Zu schnelle oder ungleichmäßige Abkühlung kann zu Oberflächenfehlern wie Blasen, Unebenheiten oder Farbveränderungen führen.
- Energieeffizienz: Durch die richtige Gestaltung der Abkühlzone kann Abwärme für andere Prozesse genutzt werden, was zur Gesamtenergieeffizienz der Anlage beiträgt.
Eine präzise kontrollierte Abkühlzone trägt somit entscheidend zur Qualität der Beschichtung und zur Energieoptimierung bei.
2. Aufbau und Funktionsweise der Abkühlzone
Die Abkühlzone ist so konzipiert, dass sie die Temperatur der Werkstücke nach dem Einbrennen schrittweise und gleichmäßig senkt. Der Aufbau und die Funktionsweise variieren je nach Anlage, Werkstück und Anforderungen an die Abkühlgeschwindigkeit.
2.1 Gehäuse und Isolierung
Die Abkühlzone besteht aus einem isolierten Gehäuse, das die Restwärme der Werkstücke kontrolliert abführt. Eine gute Isolierung ist wichtig, um sicherzustellen, dass die warme Luft nicht in die Umgebung entweicht und die Abkühlzone energieeffizient arbeitet.
2.2 Luftzirkulationssystem
Die gleichmäßige Verteilung der kühlen Luft ist entscheidend, um eine kontrollierte und einheitliche Abkühlung zu gewährleisten. Ein Luftzirkulationssystem mit Ventilatoren oder Gebläsen wird oft eingesetzt, um die gekühlte Luft über die Werkstücke zu führen und so die Temperatur langsam und gleichmäßig zu senken.
2.3 Kühlsysteme
Verschiedene Kühlsysteme können in der Abkühlzone zum Einsatz kommen, abhängig von den spezifischen Anforderungen und der Größe der Produktionsanlage:
- Natürliche Luftkühlung: Die einfachste Form der Abkühlung, bei der die Werkstücke an die Umgebungsluft abgegeben werden und so langsam abkühlen.
- Gebläsekühlung: Hierbei wird die Umgebungsluft durch Gebläse beschleunigt und gezielt über die Werkstücke geführt. Diese Methode bietet eine effizientere Abkühlung als die natürliche Luftkühlung.
- Wassergekühlte Systeme: In einigen Anlagen wird Wasser zur Kühlung der Luft verwendet, um eine präzisere Temperaturregelung und eine schnellere Abkühlung zu erreichen. Wassergekühlte Systeme sind oft in größeren Anlagen zu finden, in denen eine schnellere Abkühlung erforderlich ist.
2.4 Steuerung und Temperaturregelung
Moderne Abkühlzonen verfügen über computergesteuerte Regelungssysteme, die die Temperatur in der Zone überwachen und kontrollieren. Diese Systeme ermöglichen eine präzise Steuerung des Abkühlverlaufs und passen die Gebläse- und Kühlsysteme automatisch an, um die optimale Temperaturkurve einzuhalten.
3. Verschiedene Arten von Abkühlzonen
Abkühlzonen können in unterschiedliche Typen unterteilt werden, je nachdem, welche Abkühlmethode und welche Geschwindigkeit erforderlich sind. Die gängigsten Typen sind:
3.1 Natürliche Abkühlung (Ambient Cooling)
Bei der natürlichen Abkühlung werden die Werkstücke an die Umgebungsluft abgegeben und kühlen sich auf natürliche Weise ab. Diese Methode wird häufig für kleinere Werkstücke oder Materialien verwendet, die keine spezifischen Abkühlanforderungen haben.
Vorteile:
- Geringe Kosten und einfache Umsetzung.
- Kein zusätzlicher Energieverbrauch, da keine aktiven Kühlsysteme erforderlich sind.
Nachteile:
- Langsame Abkühlung und wenig Kontrolle über den Abkühlprozess.
- Temperaturabweichungen bei wechselnden Umgebungsbedingungen.
3.2 Luftgekühlte Abkühlzone (Forced Air Cooling)
Luftgekühlte Abkühlzonen verwenden Gebläse, um die kühle Luft gezielt über die Werkstücke zu führen und so den Abkühlprozess zu beschleunigen. Diese Methode ist effizienter und bietet eine bessere Kontrolle über die Abkühlgeschwindigkeit.
Vorteile:
- Schnellere Abkühlung als bei der natürlichen Methode.
- Bessere Kontrolle der Abkühlgeschwindigkeit.
Nachteile:
- Höherer Energieverbrauch durch die Gebläse.
- Erfordert regelmäßige Wartung des Luftzirkulationssystems.
3.3 Wassergekühlte Abkühlzone (Water Cooling)
Wassergekühlte Abkühlzonen verwenden wassergekühlte Wärmetauscher, um die Luft in der Zone abzukühlen. Dies ermöglicht eine präzise Steuerung der Temperatur und ist ideal für Werkstücke, die eine schnelle Abkühlung erfordern.
Vorteile:
- Präzise Kontrolle der Abkühltemperatur und -geschwindigkeit.
- Schnelle Abkühlung auch bei großen oder komplex geformten Werkstücken.
Nachteile:
- Hohe Investitions- und Betriebskosten.
- Höherer Wartungsaufwand und Wasserverbrauch.
3.4 Hybrid-Abkühlzonen
Hybrid-Abkühlzonen kombinieren mehrere Kühlsysteme, wie Luft- und Wassergekühlung, um die Vorteile beider Ansätze zu nutzen. Diese Zonen ermöglichen eine flexible Steuerung und Anpassung an unterschiedliche Werkstückanforderungen.
Vorteile:
- Hohe Flexibilität und Anpassungsfähigkeit an verschiedene Materialien.
- Effizientere Nutzung von Ressourcen und Energie.
Nachteile:
- Komplexere Steuerung und höherer Wartungsaufwand.
- Erhöhte Investitionskosten.
4. Steuerungsparameter und Prozessüberwachung in der Abkühlzone
Die Prozessüberwachung und die präzise Steuerung der Abkühlparameter sind entscheidend, um eine hohe Qualität und Effizienz sicherzustellen. Zu den wichtigsten Steuerungsparametern gehören:
- Temperaturkontrolle: Die Temperatur der Luft oder des Wassers wird kontrolliert, um eine konstante und gleichmäßige Abkühlung zu gewährleisten.
- Luftzirkulationsgeschwindigkeit: Die Geschwindigkeit der Gebläse wird angepasst, um die Abkühlgeschwindigkeit zu steuern.
- Verweilzeit: Die Verweilzeit der Werkstücke in der Abkühlzone kann je nach Anforderungen des Materials und der Beschichtung variiert werden.
- Feuchtigkeitskontrolle: Besonders bei wassergekühlten Systemen ist es wichtig, die Feuchtigkeit zu regulieren, um mögliche Korrosionsrisiken zu minimieren.
Moderne Abkühlzonen sind oft mit Sensoren und automatisierten Steuerungssystemen ausgestattet, die alle Parameter kontinuierlich überwachen und bei Bedarf anpassen. Durch Datenprotokollierung können Abweichungen frühzeitig erkannt und behoben werden.
5. Nachhaltigkeit und Energieeffizienz in der Abkühlzone
Die Abkühlzone bietet mehrere Möglichkeiten zur Verbesserung der Nachhaltigkeit und Energieeffizienz in der Pulverbeschichtung:
- Wärmerückgewinnung: Die Restwärme der Werkstücke kann zur Vorwärmung von Werkstücken oder zur Unterstützung des Heizprozesses in anderen Bereichen der Anlage genutzt werden.
- Energieoptimierte Luftführung: Die Verwendung von energieeffizienten Gebläsen und optimierten Luftführungssystemen reduziert den Energieverbrauch der Abkühlzone.
- Wasserrecycling in wassergekühlten Systemen: Wassergekühlte Abkühlzonen können so gestaltet werden, dass das Wasser gereinigt und wiederverwendet wird, was den Wasserverbrauch senkt.
- Nachhaltige Materialien und Beschichtungen: Die Entwicklung neuer Beschichtungen, die bei niedrigeren Temperaturen ausgehärtet werden können, senkt den Energiebedarf im gesamten Abkühl- und Einbrennprozess.
Diese Maßnahmen helfen, die Betriebskosten zu senken und die Umweltbelastung zu verringern.
6. Wartung und Qualitätskontrolle der Abkühlzone
Eine regelmäßige Wartung und Qualitätskontrolle sind erforderlich, um die Funktion und Effizienz der Abkühlzone sicherzustellen. Wichtige Wartungsmaßnahmen umfassen:
- Reinigung der Kühlsysteme: Die Lüftungs- und Kühlsysteme sollten regelmäßig gereinigt werden, um Verstopfungen und Leistungseinbußen zu vermeiden.
- Überprüfung der Temperatursteuerung: Die Temperaturregelung sollte regelmäßig kalibriert und auf ihre Genauigkeit überprüft werden.
- Kontrolle der Luftzirkulationssysteme: Ventilatoren und Gebläse müssen auf Verschleiß geprüft und bei Bedarf ausgetauscht werden.
- Feuchtigkeits- und Korrosionsschutzmaßnahmen: Bei wassergekühlten Systemen sollte auf eine ordnungsgemäße Feuchtigkeitskontrolle geachtet werden, um Korrosion zu verhindern.
Durch regelmäßige Wartung und die Einhaltung von Qualitätskontrollstandards lässt sich die Lebensdauer der Abkühlzone verlängern und die Effizienz der gesamten Anlage steigern.
7. Zukunft und Innovationen in der Abkühlzonentechnologie
Technologische Fortschritte und innovative Konzepte verändern die Art und Weise, wie Abkühlzonen in der Pulverbeschichtung gestaltet und betrieben werden. Einige der bedeutendsten Trends und Innovationen umfassen:
- Automatisierung und Prozessintegration: Moderne Abkühlzonen können in automatisierte Produktionslinien integriert werden und mit anderen Prozessschritten wie Einbrennofen oder Qualitätskontrollsystemen kommunizieren.
- KI-gestützte Steuerungssysteme: Künstliche Intelligenz und maschinelles Lernen ermöglichen eine präzise Anpassung der Abkühlparameter in Echtzeit, um die Qualität und Effizienz zu maximieren.
- Intelligente Kühlsysteme: Die Entwicklung intelligenter Kühlsysteme, die ihre Leistung automatisch an den Zustand der Werkstücke anpassen, verbessert die Energieeffizienz und Prozesssteuerung.
- Umweltfreundliche Materialien: Neue, umweltfreundliche Materialien und Beschichtungen, die weniger Energie beim Abkühlen und Aushärten benötigen, könnten in Zukunft den Energiebedarf der Abkühlzone reduzieren.
Diese technologischen Entwicklungen eröffnen neue Möglichkeiten, die Abkühlzone effizienter und umweltfreundlicher zu gestalten.
Fazit
Die Abkühlzone ist ein essenzieller Bestandteil des Pulverbeschichtungsprozesses, der sicherstellt, dass die beschichteten Werkstücke kontrolliert und gleichmäßig abkühlen. Durch eine präzise Steuerung der Abkühlparameter, den Einsatz moderner Kühltechnologien und eine optimale Prozessüberwachung kann die Qualität der Beschichtung maximiert und die Effizienz gesteigert werden. Fortschritte in der Automatisierung, Künstlichen Intelligenz und der Entwicklung nachhaltiger Kühlsysteme tragen dazu bei, die Abkühlzone zukunftssicher zu gestalten und gleichzeitig die Umweltbelastung zu reduzieren. Eine gut geplante und gewartete Abkühlzone verbessert die Gesamtqualität der Pulverbeschichtung und stellt sicher, dass der Prozess energieeffizient und nachhaltig durchgeführt werden kann.
Aufbau und Funktionsweise einer Pulverbeschichtungsanlage
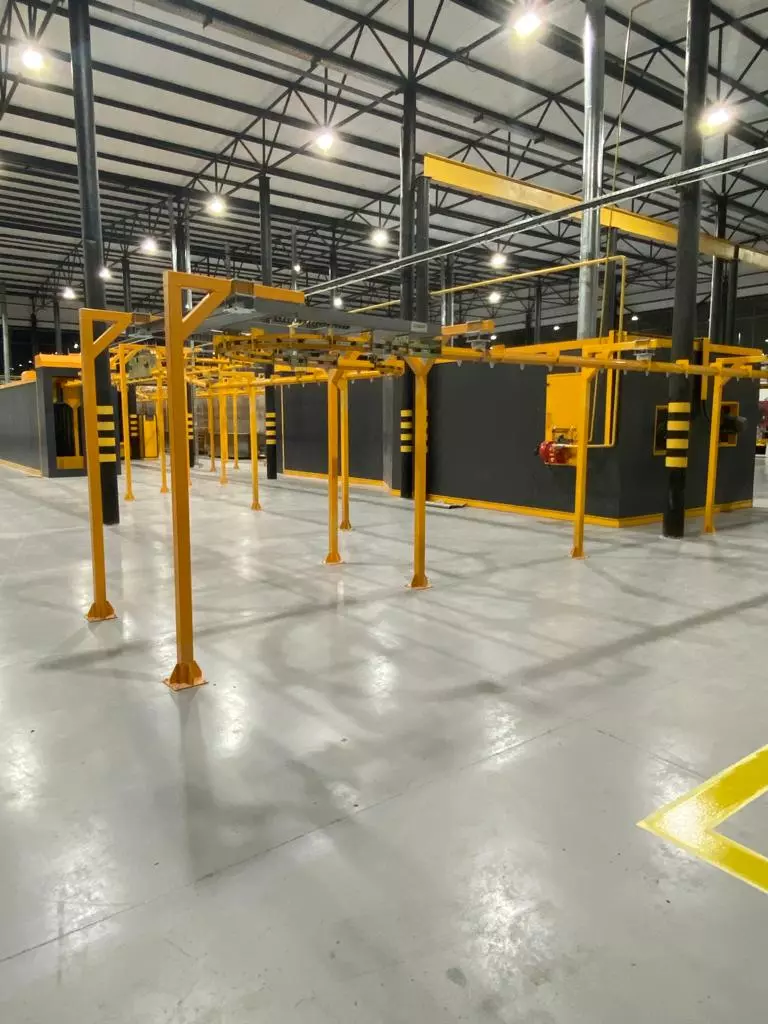
Die Pulverbeschichtungsanlage ist eine industrielle Anlage, die für die Beschichtung von Oberflächen, meist aus Metall, genutzt wird. Die Beschichtung erfolgt durch das Aufsprühen eines Pulvers, das anschließend durch Erhitzung zu einer widerstandsfähigen Schicht verschmilzt. Pulverbeschichtung ist eine gängige Methode, da sie eine langlebige, beständige Oberfläche schafft, die Korrosion und Abnutzung standhält. Die Anlage umfasst mehrere zentrale Bereiche und durchläuft verschiedene Stufen, um eine gleichmäßige, haftfeste und ästhetische Beschichtung zu gewährleisten.
In diesem Überblick betrachten wir den Aufbau und die Funktionsweise einer typischen Pulverbeschichtungsanlage, die wichtigsten Komponenten und Prozessschritte.
1. Aufbau einer Pulverbeschichtungsanlage
Eine Pulverbeschichtungsanlage besteht aus mehreren Hauptkomponenten, die aufeinander abgestimmt sind, um eine gleichmäßige und qualitativ hochwertige Beschichtung zu erzielen. Die wichtigsten Teile sind:
1.1 Vorbehandlungsstation
Die Vorbehandlungsstation ist der erste Schritt des Beschichtungsprozesses und stellt sicher, dass die Oberfläche des Werkstücks sauber und frei von Verunreinigungen ist. Sie umfasst:
- Reinigungs- und Entfettungsstationen: Entfernt Öl, Fett und andere Rückstände.
- Entrostungs- und Oxidationsentfernung: Diese Schritte verhindern, dass Rost die Beschichtung beeinträchtigt.
- Phosphatierung oder Passivierung: Erzeugt eine Schicht, die die Haftung des Pulvers verbessert und zusätzlichen Korrosionsschutz bietet.
1.2 Trocknungsstation
Nach der Vorbehandlung muss die Oberfläche getrocknet werden, um eine gute Haftung des Pulvers sicherzustellen. Die Trocknung erfolgt oft in einem speziellen Ofen, in dem die Teile schonend auf Temperatur gebracht werden, um Restfeuchtigkeit vollständig zu entfernen.
1.3 Pulverbeschichtungskabine
In der Pulverbeschichtungskabine wird das Beschichtungspulver elektrostatisch aufgeladen und auf die Oberfläche des Werkstücks aufgebracht. Hier kommen spezielle Pulverpistolen und Filtersysteme zum Einsatz:
- Pulverpistolen und Applikationssysteme: Diese sind für das gleichmäßige Auftragen des Pulvers zuständig und arbeiten mit elektrostatischer Aufladung, damit das Pulver an der Oberfläche haftet.
- Filtersystem und Pulverrückgewinnung: Die Kabine verfügt über ein System, das überschüssiges Pulver auffängt und für eine erneute Verwendung zurückführt, was Kosten spart und die Umwelt schont.
1.4 Einbrennofen
Der Einbrennofen härtet die Beschichtung bei hohen Temperaturen (typisch zwischen 160°C und 220°C) aus. Im Ofen schmilzt das Pulver, vernetzt sich chemisch und bildet eine glatte, strapazierfähige Schicht. Die konstante Temperatur und Luftzirkulation sind entscheidend für eine gleichmäßige Aushärtung.
1.5 Abkühlzone
In der Abkühlzone wird das Werkstück nach dem Einbrennen kontrolliert heruntergekühlt. Durch eine präzise Abkühlung werden thermische Spannungen vermieden, und die Qualität der Beschichtung bleibt erhalten. Die Abkühlung kann durch Luftzirkulation oder in speziellen wassergekühlten Kammern erfolgen.
1.6 Förderbandsystem
Die meisten Pulverbeschichtungsanlagen sind mit einem Förderbandsystem ausgestattet, das die Werkstücke von einer Station zur nächsten transportiert. Ein automatisiertes Fördersystem erhöht die Effizienz und gewährleistet eine konsistente Produktionsgeschwindigkeit.
2. Funktionsweise der Pulverbeschichtungsanlage
Die Funktionsweise der Pulverbeschichtungsanlage erfolgt in mehreren Schritten, die präzise aufeinander abgestimmt sind, um eine hochwertige und langlebige Beschichtung zu gewährleisten.
2.1 Vorbehandlung
- Reinigung und Entfettung: Die Werkstücke werden gereinigt, um alle Öle, Fette und Verunreinigungen zu entfernen, die die Haftung des Pulvers beeinträchtigen könnten.
- Oxidentfernung und Phosphatierung: In einem chemischen oder mechanischen Prozess werden Oxide und Rost entfernt, bevor eine Phosphatschicht aufgetragen wird. Diese verbessert die Haftung und den Korrosionsschutz.
2.2 Trocknung
Nach der Vorbehandlung werden die Werkstücke getrocknet, um restliche Feuchtigkeit zu entfernen. In einem Trocknungsofen wird das Wasser verdampft, was wichtig ist, um Defekte bei der Beschichtung zu verhindern.
2.3 Pulverbeschichtung
In der Pulverbeschichtungskabine werden die Werkstücke elektrostatisch aufgeladen und mit dem Pulverlack besprüht. Das Pulver haftet an der Oberfläche, da das Werkstück und das Pulver entgegengesetzte elektrische Ladungen haben.
- Auftragen des Pulvers: Das Pulver wird in der Kabine durch Pulverpistolen aufgesprüht. Die elektrostatische Aufladung sorgt für eine gleichmäßige Verteilung.
- Pulverrückgewinnung: Überschüssiges Pulver wird abgesaugt und im Filtersystem aufgefangen, damit es recycelt werden kann.
2.4 Einbrennen der Beschichtung
Der beschichtete Gegenstand wird in den Einbrennofen geleitet, wo das Pulver bei Temperaturen von 160–220 °C schmilzt und chemisch aushärtet. Durch die Temperatur und die Einbrenndauer wird eine stabile, homogene Beschichtung erzeugt.
- Kontrollierte Luftzirkulation: Ein Ventilationssystem sorgt dafür, dass die Hitze gleichmäßig verteilt wird, sodass das Pulver gleichmäßig aushärtet.
- Aushärtung der Pulverschicht: Das Pulver schmilzt und vernetzt sich zu einer robusten Schicht, die Witterungseinflüssen und mechanischer Belastung standhält.
2.5 Abkühlung
Nach dem Einbrennvorgang durchlaufen die Werkstücke die Abkühlzone, in der die Beschichtung kontrolliert abgekühlt wird, um Spannungen zu vermeiden.
- Luft- oder Wassergekühlte Systeme: Die Abkühlung erfolgt durch Luftzirkulation oder, bei sehr großen Teilen, auch durch wassergekühlte Systeme.
- Vermeidung von Oberflächendefekten: Durch die kontrollierte Abkühlung wird verhindert, dass sich die Oberfläche verzieht oder Risse und Blasen entstehen.
2.6 Inspektion und Qualitätskontrolle
Nach der Abkühlung wird die Qualität der Beschichtung geprüft. Typische Tests umfassen die Kontrolle der Schichtdicke, Haftung, Farbechtheit und das optische Erscheinungsbild der Beschichtung.
- Schichtdickenmessung: Um sicherzustellen, dass die Beschichtung die festgelegte Dicke hat.
- Oberflächenprüfung: Sichtprüfung, um Defekte wie Blasen oder Farbabweichungen zu erkennen.
3. Vorteile und Herausforderungen der Pulverbeschichtungsanlage
Die Pulverbeschichtung hat sich aufgrund ihrer zahlreichen Vorteile etabliert, doch gibt es auch Herausforderungen, die berücksichtigt werden müssen.
Vorteile
- Umweltfreundlich: Im Vergleich zur Nasslackierung entstehen keine flüchtigen organischen Verbindungen (VOCs), und das Pulver kann recycelt werden.
- Hohe Widerstandsfähigkeit: Pulverbeschichtungen sind besonders widerstandsfähig gegen Korrosion, Chemikalien und physikalische Beanspruchung.
- Vielfältige Oberflächen: Es sind verschiedene Farben, Texturen und Glanzeffekte möglich, die sich an unterschiedliche Designanforderungen anpassen lassen.
Herausforderungen
- Hochwertige Vorbehandlung erforderlich: Eine unzureichende Reinigung oder Phosphatierung kann die Haftung der Beschichtung beeinträchtigen.
- Hoher Energieverbrauch: Das Einbrennen erfordert hohe Temperaturen, was zu einem hohen Energieverbrauch führt.
- Komplexe Wartung: Filtersysteme und Kabinen müssen regelmäßig gereinigt und gewartet werden, um eine hohe Effizienz und Qualität sicherzustellen.
4. Neue Entwicklungen und Innovationen in der Pulverbeschichtungstechnologie
Mit fortschreitender Technologie verbessern sich auch Pulverbeschichtungsanlagen. Einige der bemerkenswerten Entwicklungen und Trends sind:
- Automatisierte Anlagen: Durch Roboter und computergestützte Systeme wird die Effizienz gesteigert und die Bedienung vereinfacht.
- Effizientere Einbrenntechniken: Neue Ofentechnologien wie Infrarot- und Hybridöfen reduzieren den Energieverbrauch und erhöhen die Geschwindigkeit des Aushärtevorgangs.
- Intelligente Steuerungssysteme: Sensoren und IoT-Technologien ermöglichen die Echtzeitüberwachung der Anlage und Optimierung des Pulverauftrags, was die Qualität verbessert und den Pulververbrauch reduziert.
- Nachhaltigere Materialien: Entwicklung von Pulvern, die bei niedrigeren Temperaturen aushärten, was den Energieverbrauch senkt und die Umwelt schont.
Fazit
Die Pulverbeschichtungsanlage ist eine hochentwickelte Produktionsanlage, die den gesamten Prozess der Pulverbeschichtung automatisiert und optimiert. Durch die einzelnen Prozessschritte – Vorbehandlung, Trocknung, Beschichtung, Einbrennen und Abkühlung – wird eine langlebige und ästhetische Beschichtung erzeugt, die auch hohen Anforderungen standhält. Neue Technologien und Innovationen tragen dazu bei, die Effizienz und Umweltfreundlichkeit weiter zu verbessern. Die Pulverbeschichtung wird daher weiterhin ein wichtiger Bestandteil der Oberflächenbearbeitung sein, besonders in Branchen, die auf dauerhafte und hochwertige Beschichtungen angewiesen sind.
Vorteile der Pulverbeschichtung – Effizienz, Qualität und Nachhaltigkeit
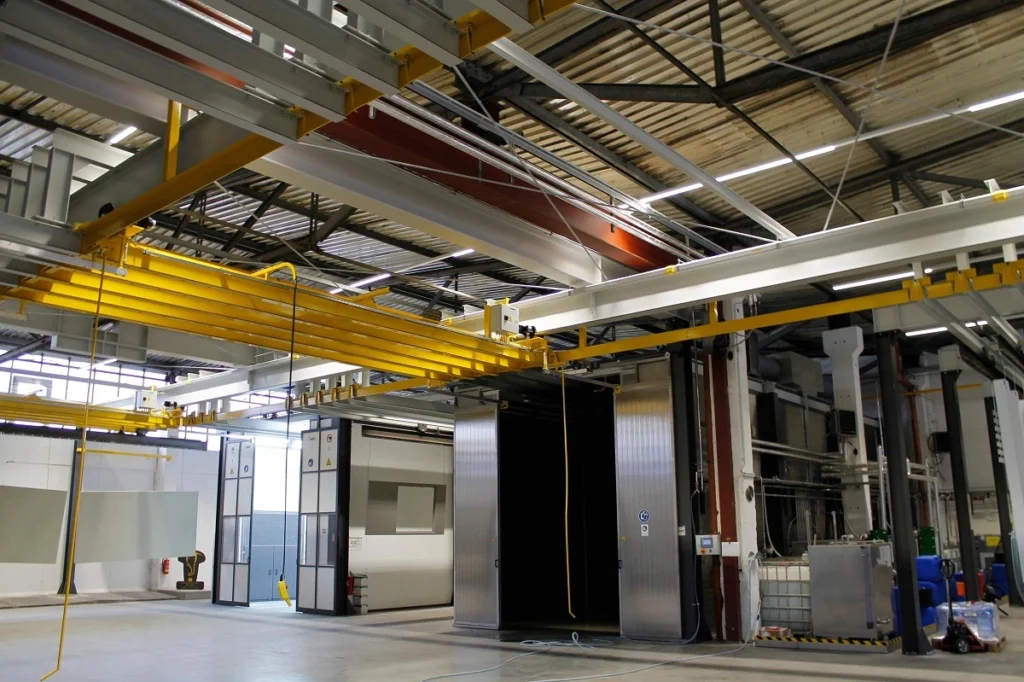
1. Umweltfreundlichkeit und Nachhaltigkeit
- Kein Einsatz von Lösungsmitteln: Die Pulverbeschichtung enthält keine flüchtigen organischen Verbindungen (VOCs), die bei anderen Verfahren wie der Nasslackierung freigesetzt werden. Dies bedeutet eine geringere Luftverschmutzung und weniger Gesundheitsrisiken für die Arbeiter.
- Reduzierter Abfall: Überschüssiges Pulver kann in den meisten Pulverbeschichtungsanlagen zurückgewonnen, gereinigt und wiederverwendet werden. Dadurch wird weniger Abfall produziert, was die Umweltbelastung minimiert.
- Energieeinsparung: Moderne Pulverbeschichtungen können bei niedrigeren Temperaturen ausgehärtet werden, was den Energieverbrauch im Einbrennofen reduziert. Zusätzlich ermöglicht die Pulverbeschichtung eine hohe Effizienz bei der Materialverwendung, da bis zu 95 % des aufgetragenen Pulvers am Werkstück haften bleiben.
2. Hohe Widerstandsfähigkeit und Haltbarkeit
- Hervorragender Korrosionsschutz: Die Pulverbeschichtung bietet eine äußerst dichte und beständige Schicht, die Metalle und andere Materialien zuverlässig vor Korrosion schützt. Dadurch ist sie besonders geeignet für den Einsatz in anspruchsvollen Umgebungen, etwa in der Automobil- oder Bauindustrie.
- Mechanische Belastbarkeit: Die Schicht, die durch die Pulverbeschichtung erzeugt wird, ist widerstandsfähig gegenüber Kratzern, Stößen und Abnutzung. Diese Robustheit macht sie ideal für Oberflächen, die starken mechanischen Beanspruchungen ausgesetzt sind.
- Chemikalien- und Witterungsbeständigkeit: Pulverbeschichtungen bieten Schutz vor Chemikalien, UV-Strahlung, Feuchtigkeit und Temperaturschwankungen. Sie eignen sich daher für den Einsatz im Außenbereich sowie für industrielle Anwendungen, in denen der Kontakt mit Chemikalien häufig vorkommt.
3. Hohe Effizienz und Kosteneinsparung
- Effiziente Beschichtungsprozesse: Die Pulverbeschichtung ist ein schneller Prozess, da das Pulver in einem Schritt aufgetragen wird und sofort haftet. Im Vergleich zur Nasslackierung entfallen Trockenzeiten zwischen den Schichten, was die Produktivität erhöht.
- Niedrigere Betriebskosten: Die Fähigkeit, überschüssiges Pulver zurückzugewinnen und erneut zu verwenden, senkt die Materialkosten erheblich. Außerdem reduzieren sich die Entsorgungskosten, da weniger gefährliche Abfälle anfallen.
- Längere Wartungsintervalle: Durch die hohe Beständigkeit der Pulverbeschichtung sind die beschichteten Oberflächen weniger wartungsintensiv. In Anwendungen, in denen regelmäßig gewartet und nachbeschichtet werden müsste, bietet die Pulverbeschichtung somit langfristig Kosteneinsparungen.
4. Ästhetische Vielseitigkeit und Designfreiheit
- Breite Farbauswahl und Oberflächenvarianten: Pulverbeschichtungspulver ist in einer nahezu unbegrenzten Farbauswahl erhältlich und bietet verschiedene Effekte wie Metallic-, Glanz- oder Matt-Optik. Diese Flexibilität erfüllt viele ästhetische Anforderungen und macht das Verfahren in der Design- und Möbelindustrie besonders attraktiv.
- Gleichmäßige und makellose Oberfläche: Die elektrostatische Aufladung des Pulvers sorgt dafür, dass das Pulver gleichmäßig auf die Werkstücke verteilt wird. Dadurch entstehen keine Farbunterschiede, Tropfen oder ungleichmäßige Oberflächen, wie sie bei Nasslackierungen vorkommen können.
- Texturen und Spezialeffekte: Pulverbeschichtungen können so formuliert werden, dass sie spezielle Oberflächeneffekte wie Struktur, Hammerschlag oder andere Texturen erzeugen, die sowohl optische als auch haptische Akzente setzen.
5. Sicherheit und Gesundheitsschutz
- Geringere Gesundheitsrisiken: Da die Pulverbeschichtung ohne Lösungsmittel auskommt, entsteht kein gesundheitsschädlicher Dampf. Die Arbeiter sind weniger gefährlichen Chemikalien ausgesetzt, und es gibt eine geringere Belastung durch giftige Emissionen.
- Weniger Gefahr von Feuer- oder Explosionsrisiken: Lösungsmittelbasierte Lackierungen sind leicht entflammbar, während die Pulverbeschichtung ein trockenes Pulver verwendet, das kein Feuer- oder Explosionsrisiko darstellt. Dies erhöht die Sicherheit in der Produktionsstätte.
- Weniger Arbeitsunfälle: Pulverbeschichtungen erfordern in der Regel keine zusätzliche persönliche Schutzausrüstung wie Atemschutzmasken, da das Pulver nicht inhaliert werden kann. Die Rückgewinnungssysteme fangen überschüssiges Pulver direkt auf, was die Luftqualität in der Produktionsstätte verbessert.
6. Einfache Anwendung und Effizienzsteigerung durch Automatisierung
- Vereinfachte Automatisierung: Pulverbeschichtungsanlagen können leicht automatisiert werden, was zu einer höheren Produktionsgeschwindigkeit und gleichbleibend hohen Qualität führt. Automatisierte Systeme tragen zur Minimierung des Pulververbrauchs und zur Effizienzsteigerung bei.
- Schneller Farbwechsel: Moderne Pulverbeschichtungsanlagen sind so konzipiert, dass Farbwechsel schnell und einfach durchgeführt werden können, was den Produktionsprozess flexibler gestaltet.
- Geringerer Schulungsaufwand: Da das Pulver in einem Schritt aufgetragen wird und weniger Erfahrung erforderlich ist, um ein gutes Ergebnis zu erzielen, benötigen die Bediener weniger Schulung als bei traditionellen Nasslackverfahren.
Fazit
Die Pulverbeschichtung bietet zahlreiche Vorteile, die sie zur bevorzugten Wahl für eine Vielzahl von Anwendungen machen. Die Umweltfreundlichkeit, hohe Widerstandsfähigkeit, Kosteneffizienz, ästhetische Flexibilität und Sicherheit tragen dazu bei, dass sich die Pulverbeschichtung in der Industrie zunehmend durchsetzt. Zudem eröffnen neue Innovationen, wie energiesparende Technologien und fortschrittliche Steuerungssysteme, weiteres Potenzial für eine zukunftsorientierte und nachhaltige Produktion.
Einsatzbereiche der Pulverbeschichtung – Von Industrie bis Architektur

Die Pulverbeschichtung ist eine vielseitige Beschichtungstechnologie, die aufgrund ihrer Langlebigkeit, Widerstandsfähigkeit und umweltfreundlichen Eigenschaften in zahlreichen Branchen eingesetzt wird. Sie bietet Schutz vor Korrosion, chemischen Einflüssen und mechanischer Abnutzung und eröffnet durch die große Farb- und Strukturvielfalt breite Gestaltungsmöglichkeiten.
Hier ist ein Überblick über die wichtigsten Einsatzbereiche der Pulverbeschichtung:
1. Automobilindustrie
Die Pulverbeschichtung ist in der Automobilindustrie weit verbreitet, da sie optimalen Korrosionsschutz und eine hohe Beständigkeit gegenüber mechanischer Beanspruchung bietet. Typische Anwendungsbereiche sind:
- Felgen und Karosserieteile: Pulverbeschichtungen bieten eine widerstandsfähige, kratzfeste Oberfläche, die gegenüber Steinschlag und Witterungseinflüssen beständig ist.
- Fahrwerkskomponenten: Durch die hohe Resistenz gegen Salze und Feuchtigkeit sind pulverbeschichtete Teile ideal für den Unterboden- und Fahrwerksbereich.
- Zubehörteile und Innenraumkomponenten: Pulverbeschichtung sorgt für ein hochwertiges Finish bei Zierleisten, Armaturen oder Sitzgestellen und steigert die Langlebigkeit der Komponenten.
2. Bau- und Architekturbranche
In der Bau- und Architekturbranche ist die Pulverbeschichtung eine bevorzugte Wahl für die Oberflächenveredelung und den Schutz von Metallbauteilen. Sie ist für den Außen- und Innenbereich geeignet und hält hohen Witterungsbelastungen stand.
- Fassaden und Fassadenelemente: Pulverbeschichtete Fassadenelemente sind beständig gegenüber UV-Strahlung, Feuchtigkeit und Temperaturschwankungen und behalten ihre Farbe und Glanz über viele Jahre.
- Fenster- und Türrahmen: Pulverbeschichtungen bieten Schutz vor Korrosion und Witterungseinflüssen, was sie ideal für Fensterrahmen und Türen aus Aluminium und Stahl macht.
- Geländer und Zäune: Die Beschichtung verhindert Rost und verleiht Geländern und Zäunen im Innen- und Außenbereich eine langlebige, ansprechende Optik.
- Bauprofile und Tragwerke: Durch die hohe Belastbarkeit und den Schutz vor Korrosion eignet sich die Pulverbeschichtung auch für die Veredelung von Bauprofilen und Stahlträgern.
3. Möbelindustrie
Die Möbelindustrie nutzt die Pulverbeschichtung sowohl für den Innen- als auch für den Außenbereich, da sie eine große Designflexibilität und Widerstandsfähigkeit gegen mechanische und chemische Belastungen bietet.
- Metallmöbel: Pulverbeschichtete Metallmöbel für Innenräume, wie Stühle, Tische und Regale, erhalten eine kratzfeste und langlebige Oberfläche, die in verschiedenen Farben und Strukturen erhältlich ist.
- Gartenmöbel: Für den Außenbereich sind pulverbeschichtete Gartenmöbel ideal, da sie rostfrei und unempfindlich gegenüber Feuchtigkeit und Temperaturschwankungen sind.
- Wohnaccessoires und Dekoration: Auch bei Dekorationsgegenständen aus Metall bietet die Pulverbeschichtung zahlreiche Farb- und Strukturmöglichkeiten und trägt zu einer edlen Optik bei.
4. Elektronik- und Elektroindustrie
In der Elektronik- und Elektroindustrie wird die Pulverbeschichtung häufig eingesetzt, um Komponenten und Gehäuse vor Korrosion und äußeren Einflüssen zu schützen. Beispiele hierfür sind:
- Gehäuse und Schaltschränke: Pulverbeschichtete Gehäuse schützen empfindliche Elektronik vor Feuchtigkeit und chemischen Einflüssen und bieten gleichzeitig eine ansprechende Optik.
- Leuchten und Lampen: Pulverbeschichtungen verbessern die Widerstandsfähigkeit und das Design von Leuchten, insbesondere von Außenleuchten, die Witterungsbedingungen ausgesetzt sind.
- Kühlgeräte und Haushaltsgeräte: Auch Haushaltsgeräte wie Kühlschränke oder Waschmaschinen profitieren von der Beschichtung, da sie Oberflächen vor Rost, Schmutz und Verfärbung schützt.
5. Haushaltswaren und Geräte
In der Herstellung von Haushaltswaren wird die Pulverbeschichtung verwendet, um den Produkten eine strapazierfähige und optisch ansprechende Oberfläche zu verleihen.
- Küchengeräte: Pulverbeschichtete Oberflächen an Geräten wie Öfen, Mikrowellen und Kühlschränken sind widerstandsfähig gegen hohe Temperaturen, Feuchtigkeit und chemische Reinigung.
- Werkzeuge und Gartengeräte: Pulverbeschichtungen bieten zusätzlichen Schutz und eine längere Lebensdauer für Werkzeuge und Gartengeräte, die stark beansprucht und oft äußeren Einflüssen ausgesetzt sind.
- Regale und Aufbewahrungssysteme: In Garagen oder Werkstätten eingesetzte Regalsysteme profitieren von der widerstandsfähigen und kratzfesten Beschichtung.
6. Medizin- und Laborgeräte
Die Medizin- und Laborbranche stellt hohe Anforderungen an die Oberflächenbeschaffenheit und Hygiene von Geräten und Instrumenten, weshalb die Pulverbeschichtung eine geeignete Wahl ist.
- Medizinische Geräte: Pulverbeschichtete Oberflächen sind widerstandsfähig gegen Desinfektionsmittel und Chemikalien, was sie ideal für medizinische Geräte und Apparate macht.
- Labormöbel und Ausrüstung: Im Laborbereich sind pulverbeschichtete Werkbänke und Aufbewahrungssysteme robust und beständig gegen chemische Einflüsse und Abrieb.
- Krankenhausausstattung: Möbel und Geräte in Krankenhäusern, wie Bettrahmen und Rollstühle, profitieren von der langlebigen und hygienischen Beschichtung.
7. Luftfahrt und Schifffahrt
Die Luftfahrt- und Schifffahrtsindustrie setzen die Pulverbeschichtung aufgrund ihrer hohen Korrosionsbeständigkeit und Widerstandsfähigkeit gegen extreme Bedingungen ein.
- Flugzeugkomponenten: Pulverbeschichtete Komponenten in Flugzeugen, wie Sitze, Gepäckablagen und Verkleidungsteile, sind beständig gegenüber extremen Temperaturen und Feuchtigkeit.
- Schiffbau: Pulverbeschichtungen werden auch in der Schifffahrt verwendet, um Metallteile vor Korrosion durch Salzwasser und UV-Strahlung zu schützen.
- Ausrüstungen und Zubehör: Von Leitern und Geländern bis hin zu Werkzeugen und Zubehörteilen profitieren verschiedene Bereiche in der Schifffahrt von der langlebigen Beschichtung.
8. Maschinenbau und Schwerindustrie
Im Maschinenbau und in der Schwerindustrie ist die Pulverbeschichtung aufgrund ihrer Robustheit und des hervorragenden Korrosionsschutzes eine beliebte Methode zur Oberflächenveredelung.
- Maschinenkomponenten: Teile wie Gehäuse, Ständer und Abdeckungen sind durch Pulverbeschichtung vor Abnutzung und Korrosion geschützt.
- Landwirtschafts- und Baufahrzeuge: Komponenten von Traktoren, Mähdreschern und Baggern werden durch Pulverbeschichtung vor Schmutz, Feuchtigkeit und Chemikalien geschützt.
- Rohre und Tanks: In der Öl-, Gas- und Chemieindustrie sind pulverbeschichtete Rohre und Tanks resistent gegen Korrosion und chemische Belastungen.
9. Sport- und Freizeitgeräte
Die Pulverbeschichtung wird auch im Bereich Sport- und Freizeitgeräte verwendet, da sie Schutz und Ästhetik für eine Vielzahl von Produkten bietet.
- Fahrräder und Zubehör: Pulverbeschichtete Fahrradrahmen und -teile sind besonders widerstandsfähig gegen Kratzer, Feuchtigkeit und UV-Strahlung.
- Fitnessgeräte: Fitnessgeräte im Innen- und Außenbereich profitieren von der langlebigen und kratzfesten Beschichtung, die auch Schweiß und Reinigungsmitteln standhält.
- Spielplatzgeräte: Pulverbeschichtete Oberflächen sind ideal für Spielgeräte im Freien, da sie widerstandsfähig gegen Sonne, Regen und Abnutzung sind.
Fazit
Die Pulverbeschichtung ist eine vielseitige und zuverlässige Methode zur Oberflächenveredelung, die in zahlreichen Branchen und für unterschiedlichste Anwendungen eingesetzt wird. Durch ihre Korrosionsbeständigkeit, Langlebigkeit und das breite Spektrum an Farben und Texturen ist sie ideal für Anwendungen im Innen- und Außenbereich, bei denen sowohl Schutz als auch Ästhetik gefragt sind. Mit der steigenden Nachfrage nach nachhaltigen und umweltfreundlichen Beschichtungsverfahren wird die Pulverbeschichtung auch in Zukunft in vielen Bereichen eine zentrale Rolle spielen.
Schritte der Vorbehandlung in der Pulverbeschichtung – Ein gründlicher Überblick
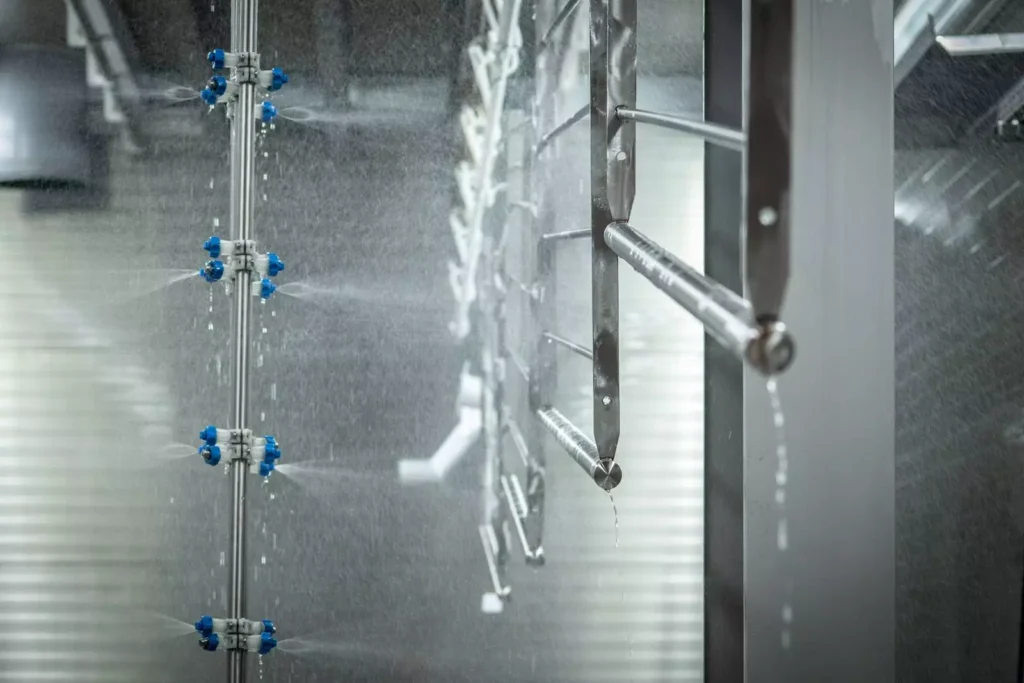
Die Vorbehandlung ist ein essenzieller Prozessschritt in der Pulverbeschichtung, der sicherstellt, dass die Werkstücke optimal für das Beschichtungsverfahren vorbereitet werden. Eine saubere, fettfreie und vorbereitete Oberfläche ist entscheidend, um eine starke Haftung der Pulverbeschichtung zu gewährleisten und Oberflächenmängel zu vermeiden. Die Vorbehandlung umfasst mehrere Schritte, die je nach Werkstoff und Verwendungszweck der Werkstücke variieren können.
Hier ist ein detaillierter Überblick über die wichtigsten Schritte der Vorbehandlung in der Pulverbeschichtung:
1. Reinigung und Entfettung
Die Reinigung und Entfettung sind die ersten Schritte, um Verunreinigungen wie Öl, Fett, Staub und Schmutz zu entfernen, die oft während der Produktion oder Lagerung auf den Werkstücken zurückbleiben. Eine gründliche Reinigung sorgt dafür, dass die Pulverbeschichtung gleichmäßig und dauerhaft auf der Oberfläche haften kann.
- Lösungsmittelreinigung: Organische Lösungsmittel können verwendet werden, um Fette und Öle von der Oberfläche zu lösen. Diese Methode ist effektiv, wird jedoch zunehmend durch umweltfreundlichere Alternativen ersetzt.
- Wässrige Reinigung: Wasserbasierte Reiniger, die Tenside enthalten, lösen Fett und Öl in einem emulgierten Zustand, der anschließend abgespült werden kann. Diese Methode ist sowohl effizient als auch umweltfreundlicher.
- Ultraschallreinigung: In einem Reinigungsbad mit Ultraschallwellen wird die Oberfläche durch Vibration gereinigt. Diese Methode eignet sich besonders gut für kleine oder komplex geformte Werkstücke, bei denen eine manuelle Reinigung nicht möglich ist.
- Mechanische Reinigung: In einigen Fällen wird eine mechanische Vorreinigung durch Bürsten, Schleifen oder Sandstrahlen durchgeführt, insbesondere wenn grobe Verunreinigungen entfernt werden müssen.
2. Entrostung und Oxidentfernung
Die Entfernung von Rost und Oxidschichten ist entscheidend, um eine reaktionsfähige und saubere Oberfläche zu schaffen. Metallische Werkstoffe, die durch Luftfeuchtigkeit oder Umwelteinflüsse oxidiert wurden, müssen gründlich behandelt werden, um eine optimale Haftung der Pulverbeschichtung zu gewährleisten.
- Chemisches Beizen: Durch den Einsatz von Säuren, wie Phosphor- oder Salzsäure, wird eine Oxidschicht aufgelöst und die metallische Oberfläche freigelegt. Diese Methode eignet sich besonders gut für Stahl und Eisen, die stark oxidieren.
- Sandstrahlen: Mit einem Schleifmittel, z. B. Sand, Glasperlen oder Korund, werden die Oberflächen mechanisch bearbeitet. Das Sandstrahlen entfernt Rost und Oxide und hinterlässt eine leicht raue Oberfläche, die die Haftung des Pulvers verbessert.
- Schleifen: Für gezielte Rostentfernungen, vor allem bei kleineren Bereichen, wird manchmal manuell oder maschinell geschliffen, um eine saubere Metalloberfläche freizulegen.
3. Spülen und Neutralisieren
Nach dem Einsatz chemischer Reinigungsmittel, z. B. bei der Säurereinigung, ist es notwendig, die Werkstücke gründlich zu spülen, um Rückstände zu entfernen, die die Haftung des Pulvers beeinträchtigen könnten.
- Wasserbäder und Hochdruckspülen: Werkstücke werden in einem Wasserbad gespült oder mit Hochdruck gereinigt, um alle Rückstände abzuspülen. Mehrere Spülschritte sind dabei häufig notwendig, um sicherzustellen, dass alle chemischen Rückstände entfernt sind.
- Neutralisationsbad: Nach der Behandlung mit sauren oder basischen Reinigern kann ein Neutralisationsbad erforderlich sein, um den pH-Wert der Oberfläche wiederherzustellen und Korrosionsgefahr zu vermeiden.
4. Phosphatierung oder Konversionsbeschichtung
Die Phosphatierung ist ein wichtiger Schritt, der nicht nur zur Verbesserung der Haftung dient, sondern auch einen zusätzlichen Korrosionsschutz bietet. Je nach Werkstoff und Anwendungsbereich können verschiedene Arten der Konversionsbeschichtung aufgebracht werden:
- Zinkphosphatierung: Diese Art der Phosphatierung wird vor allem bei Eisen- und Stahloberflächen verwendet und bildet eine kristalline Phosphatschicht. Diese Schicht verbessert die Haftung des Pulvers und schützt vor Korrosion.
- Eisenphosphatierung: Diese Methode ist eine weniger intensive Alternative zur Zinkphosphatierung und wird hauptsächlich für Aluminium und Zink verwendet. Sie bietet eine dünnere Schutzschicht und eignet sich gut für Oberflächen mit geringem Korrosionsrisiko.
- Chromatierung: Chromatierung, insbesondere die Hexavalente Chromatierung, ist eine Konversionsbeschichtung für Aluminium und Zink, die eine exzellente Haftung und Korrosionsbeständigkeit bietet. Aufgrund der Umweltrisiken wird sie zunehmend durch Chrom(III)-basierte und andere umweltfreundliche Verfahren ersetzt.
- Nanobeschichtungen: Umweltfreundliche Nanobeschichtungen auf Zirkon- oder Siliziumbasis werden immer häufiger als Alternative zur traditionellen Phosphatierung verwendet. Sie bieten eine ähnliche Haft- und Korrosionsschutzwirkung, sind jedoch umweltfreundlicher.
5. Trocknung der Werkstücke
Nach der Vorbehandlung müssen die Werkstücke getrocknet werden, um jegliche Feuchtigkeit zu entfernen. Feuchtigkeit auf der Oberfläche kann die Haftung der Pulverbeschichtung erheblich beeinträchtigen und zu Defekten wie Blasen oder Ablösungen führen.
- Trocknung im Ofen: Die Werkstücke werden in einem Trocknungsofen erhitzt, um die Feuchtigkeit vollständig zu entfernen. Die Temperatur variiert je nach Material und beträgt in der Regel zwischen 60 und 100 Grad Celsius.
- Heißlufttrocknung: In manchen Fällen wird die Trocknung durch Luftströme durchgeführt, die über die Werkstücke geleitet werden. Diese Methode ist besonders effektiv, wenn eine schnelle Trocknung erforderlich ist.
- Raumtrocknung: In weniger anspruchsvollen Anwendungen, in denen eine längere Trockenzeit möglich ist, kann auch eine natürliche Trocknung bei Raumtemperatur erfolgen. Diese Methode ist jedoch selten und wird nur für spezielle Anwendungen genutzt.
6. Qualitätskontrolle und Inspektion
Nach der Vorbehandlung erfolgt eine sorgfältige Inspektion und Qualitätskontrolle der Werkstücke, um sicherzustellen, dass die Oberfläche sauber, gleichmäßig und frei von Verunreinigungen ist. Ein gut durchgeführter Vorbehandlungsprozess ist die Grundlage für eine langlebige und haftstarke Pulverbeschichtung.
- Oberflächenanalyse: Die Oberfläche wird visuell oder mit optischen Geräten auf Verunreinigungen, Flecken oder Unebenheiten untersucht, die die Qualität der Pulverbeschichtung beeinträchtigen könnten.
- Phosphatschicht-Dickenmessung: Nach der Phosphatierung wird oft die Dicke der Phosphatschicht gemessen, um sicherzustellen, dass sie den Spezifikationen entspricht.
- Benetzbarkeitstest: In manchen Fällen wird ein Benetzbarkeitstest durchgeführt, um sicherzustellen, dass die Oberfläche gleichmäßig befeuchtet werden kann, was ein Hinweis auf eine gute Haftung ist.
7. Zusammenfassung: Der vollständige Vorbehandlungsprozess
Der gesamte Vorbehandlungsprozess in der Pulverbeschichtung besteht also aus einer sorgfältigen Sequenz von Reinigung, Entfettung, Oxidentfernung, Spülung, chemischer Konversionsbeschichtung (wie Phosphatierung) und Trocknung, gefolgt von einer umfassenden Qualitätskontrolle. Diese Schritte sind entscheidend, um eine perfekte Grundlage für die Pulverbeschichtung zu schaffen.
Fazit
Eine gründliche und präzise Vorbehandlung ist entscheidend für die Qualität und Langlebigkeit der Pulverbeschichtung. Durch die Kombination aus Reinigung, Oxidentfernung, Phosphatierung und Trocknung wird die Oberfläche optimal vorbereitet, sodass das Pulver gleichmäßig haftet und seine vollen Schutz- und ästhetischen Eigenschaften entfalten kann. Moderne Verfahren wie die Nanobeschichtung oder umweltfreundliche Alternativen zur Chromatierung erweitern das Spektrum der Vorbehandlungsmethoden und tragen zur Nachhaltigkeit der gesamten Beschichtungstechnologie bei.
Reinigung und Entfettung in der Pulverbeschichtung – Ein wesentlicher Schritt für perfekte Haftung
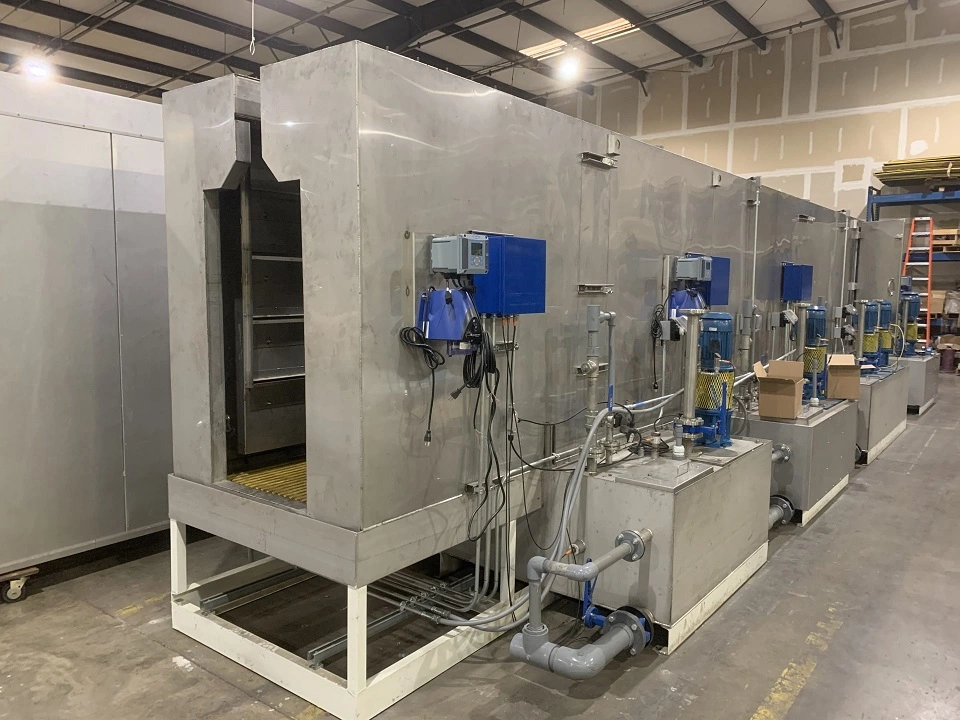
Die Reinigung und Entfettung ist der erste und einer der wichtigsten Schritte in der Vorbehandlung der Pulverbeschichtung. Eine saubere und fettfreie Oberfläche ist entscheidend, um eine optimale Haftung der Pulverbeschichtung sicherzustellen und Defekte wie Blasen, Ablösungen oder ungleichmäßige Schichten zu verhindern. Die Vorbereitung der Werkstückoberfläche beginnt daher mit der gründlichen Entfernung von Ölen, Fetten, Staub, Rost und anderen Verunreinigungen, die während der Produktion oder Lagerung entstehen.
Hier finden Sie einen detaillierten Überblick über die verschiedenen Methoden und Prozesse der Reinigung und Entfettung in der Pulverbeschichtung:
1. Ziele der Reinigung und Entfettung
Der primäre Zweck der Reinigung und Entfettung ist es, alle Substanzen zu entfernen, die die Haftung der Pulverbeschichtung beeinträchtigen könnten. Das umfasst:
- Entfernung von Ölen und Fetten: Diese Rückstände stammen meist von vorhergehenden Bearbeitungsprozessen wie Schneiden, Stanzen oder Umformen und verhindern die gleichmäßige Verteilung der Pulverbeschichtung.
- Beseitigung von Staub und Schmutz: Staubpartikel und andere Ablagerungen auf der Oberfläche können die Beschichtungsqualität und -ästhetik beeinträchtigen.
- Entfernung von Oxiden: Speziell bei Metallen wie Stahl und Aluminium bildet sich oft eine Oxidschicht, die die Haftung des Pulvers stört und zu Korrosion führen kann, wenn sie nicht beseitigt wird.
2. Methoden der Reinigung und Entfettung
Es gibt verschiedene Reinigungs- und Entfettungsverfahren, die je nach Material und Verschmutzungsgrad des Werkstücks angewendet werden können. Zu den gängigsten Verfahren gehören:
2.1 Wässrige Reinigung
Die wässrige Reinigung ist die meistverwendete Methode und kombiniert Tenside, Alkalien oder saure Reinigungsmittel mit Wasser, um Fette und Öle zu emulgieren und abzutragen.
- Alkalische Reiniger: Alkalische Reinigungsmittel werden häufig verwendet, um organische Verschmutzungen wie Öle und Fette zu entfernen. Die Alkalien brechen die Fettmoleküle auf und machen sie wasserlöslich.
- Säurereiniger: Für bestimmte Materialien, insbesondere Aluminium, werden milde Säurereiniger verwendet, die die Oxidschicht lösen und den Oberflächenschmutz effektiv entfernen.
- Tenside und Emulgatoren: Tenside und Emulgatoren helfen, die Verschmutzungen in der Reinigungsflüssigkeit zu emulgieren und zu suspendieren, sodass sie abgewaschen werden können.
Prozessablauf:
- Werkstücke werden in ein Reinigungsbad eingetaucht oder in einer Sprühreinigungsstation behandelt.
- Nach dem Einweichen und Lösen der Verunreinigungen wird die Oberfläche gründlich mit Wasser abgespült, um Rückstände der Reinigungsmittel zu entfernen.
Vorteile:
- Umweltfreundlicher als Lösungsmittel.
- Eignet sich für viele Werkstoffe und Oberflächenarten.
Nachteile:
- Hoher Wasserverbrauch.
- Rückstände der Reinigungsmittel müssen gründlich entfernt werden, um keine Haftungsprobleme zu verursachen.
2.2 Lösungsmittelreinigung
Die Lösungsmittelreinigung wird häufig für Teile verwendet, die mit besonders hartnäckigen Ölen oder Fetten belastet sind. Die Lösungsmittel lösen organische Stoffe, die dann verdampfen oder abgewischt werden können.
- Organische Lösungsmittel: Stoffe wie Aceton, Alkohol oder Kohlenwasserstoff-Lösungsmittel lösen Fette und Öle sehr effektiv.
- Lösemittel-Dampfreinigung: Das Werkstück wird in ein Reinigungsbad mit Lösungsmittel eingetaucht und durch Dampf gereinigt. Der entstehende Dampf kondensiert auf der Oberfläche und löst die Verunreinigungen, die dann abfließen.
Prozessablauf:
- Werkstücke werden in Lösungsmittel getaucht oder mit einem Lösungsmittel besprüht.
- Bei Dampfreinigungssystemen werden sie anschließend erhitzt, um das Lösungsmittel vollständig zu verdampfen und Rückstände zu entfernen.
Vorteile:
- Effektiv bei der Entfernung hartnäckiger Fette und Öle.
- Bietet schnelle Reinigung und schnelle Trocknung.
Nachteile:
- Hohe Umwelt- und Gesundheitsbelastung durch die Lösungsmittel.
- Entsorgung und Rückgewinnung von Lösungsmitteln sind kostenintensiv.
2.3 Mechanische Reinigung
Bei der mechanischen Reinigung werden die Werkstücke manuell oder maschinell bearbeitet, um Verunreinigungen zu entfernen. Diese Methode eignet sich besonders für stark verschmutzte Teile oder Materialien mit groben Verunreinigungen.
- Sandstrahlen: Sand- oder Glasperlenstrahlen wird verwendet, um Schmutz und Rost von der Oberfläche zu entfernen. Diese Methode erzeugt eine leicht raue Oberfläche, die die Haftung der Pulverbeschichtung verbessert.
- Schleifen und Bürsten: Oberflächen werden mechanisch gebürstet oder geschliffen, um grobe Rückstände zu entfernen. Diese Methode wird oft für kleine Flächen oder stark verschmutzte Teile angewendet.
- Rotationsentgratung: In speziellen Anlagen werden die Werkstücke in einer Trommel mit Schleifkörpern rotierend bearbeitet. Dadurch wird die Oberfläche gereinigt und gleichzeitig geglättet.
Prozessablauf:
- Werkstücke werden in eine Strahlanlage oder Schleifstation gebracht und mechanisch behandelt.
- Nach der Behandlung wird die Oberfläche gesäubert, um restliche Partikel zu entfernen.
Vorteile:
- Eignet sich gut für stark verunreinigte oder verrostete Teile.
- Verbessert die Haftung durch leichte Oberflächenrauheit.
Nachteile:
- Kann das Werkstück verformen oder beschädigen, wenn es nicht korrekt ausgeführt wird.
- Teils hoher Materialabtrag, der je nach Material nicht gewünscht ist.
2.4 Ultraschallreinigung
Die Ultraschallreinigung ist eine hochmoderne Methode, bei der Schallwellen eingesetzt werden, um Verunreinigungen von der Werkstückoberfläche zu lösen. Sie ist besonders effektiv für empfindliche oder komplex geformte Teile, bei denen andere Reinigungsmethoden nicht geeignet sind.
- Ultraschallwellen: Diese erzeugen Kavitation, das heißt kleine Blasen, die auf der Oberfläche implodieren und Schmutzpartikel entfernen.
- Reinigungsflüssigkeit: Meist wird ein wasserbasiertes Reinigungsmittel verwendet, das die Ultraschallwirkung verstärkt und Fett und Schmutz löst.
Prozessablauf:
- Werkstücke werden in ein Ultraschallbad getaucht, das Schallwellen erzeugt und Verunreinigungen löst.
- Anschließend werden die Werkstücke abgespült und getrocknet, um restliche Reinigungsmittel zu entfernen.
Vorteile:
- Besonders effektiv für kleine oder komplex geformte Teile.
- Keine mechanische Belastung, was es sicher für empfindliche Werkstücke macht.
Nachteile:
- Hohe Anschaffungskosten für Ultraschallgeräte.
- Nur für bestimmte Werkstücke und Materialien geeignet.
3. Prozesskontrolle und Qualitätsprüfung
Um sicherzustellen, dass die Oberfläche frei von Verunreinigungen ist, sind regelmäßige Qualitätsprüfungen und eine strenge Prozesskontrolle erforderlich:
- Kontrolle der Reinigungsmittelkonzentration: Die Konzentration der Reinigungsmittel in den Bädern muss regelmäßig überwacht und gegebenenfalls angepasst werden, um eine konsistente Reinigung zu gewährleisten.
- Oberflächeninspektion: Visuelle und optische Inspektionen auf Rückstände, Schmutzpartikel oder Flecken gewährleisten eine gleichmäßige Oberfläche.
- Benetzbarkeitstest: Ein Benetzbarkeitstest kann durchgeführt werden, um sicherzustellen, dass die Oberfläche gleichmäßig befeuchtet wird. Dies zeigt, dass keine Rückstände vorhanden sind, die die Haftung beeinträchtigen könnten.
4. Umwelt- und Arbeitssicherheitsaspekte
Die Reinigung und Entfettung umfasst oft den Umgang mit Chemikalien und Lösungsmitteln, weshalb Umwelt- und Sicherheitsmaßnahmen wichtig sind:
- Sicherheitsausrüstung: Das Personal sollte geeignete Schutzausrüstung tragen, insbesondere bei der Arbeit mit Lösungsmitteln und Chemikalien.
- Lösungsmittelrückgewinnung und -entsorgung: Lösungsmittel sollten, wenn möglich, recycelt und umweltgerecht entsorgt werden, um die Umweltbelastung zu minimieren.
- Luftreinhaltung: In Anlagen mit Lösungsmittelreinigung sollten effektive Lüftungs- und Filtersysteme installiert sein, um gesundheitsschädliche Dämpfe zu vermeiden.
Fazit
Die Reinigung und Entfettung ist ein essenzieller Schritt, der eine starke, langlebige Haftung der Pulverbeschichtung sicherstellt. Durch den Einsatz unterschiedlicher Methoden – von der wässrigen Reinigung über Lösungsmittel bis hin zur mechanischen und Ultraschallreinigung – wird das Werkstück gründlich vorbereitet. Die Wahl der Methode hängt dabei von der Art des Werkstücks, der Art der Verunreinigung und den Umweltauswirkungen ab. Eine sorgfältige Prozesskontrolle und Einhaltung von Sicherheitsstandards sind unabdingbar, um sowohl die Beschichtungsqualität als auch die Arbeitssicherheit zu gewährleisten.
Entrostung und Oxidentfernung in der Pulverbeschichtung – Methoden, Prozesse und Technologien
Die Entrostung und Oxidentfernung ist ein zentraler Schritt in der Vorbehandlung der Pulverbeschichtung. Korrosion und Oxidschichten, die sich durch Umwelteinflüsse oder den natürlichen Oxidationsprozess auf Metalloberflächen bilden, können die Haftung der Pulverbeschichtung beeinträchtigen und die Lebensdauer der Beschichtung erheblich verkürzen. Um eine gleichmäßige, dauerhafte und ästhetisch ansprechende Pulverbeschichtung zu erreichen, müssen diese Schichten gründlich entfernt werden.
Dieser Leitfaden bietet einen umfassenden Überblick über die verschiedenen Methoden und Technologien zur Entrostung und Oxidentfernung, ihre Funktionsweise sowie deren Vor- und Nachteile.
1. Die Bedeutung der Entrostung und Oxidentfernung
Die Hauptaufgabe der Entrostung und Oxidentfernung besteht darin, eine reine, metallische Oberfläche freizulegen, die eine optimale Grundlage für die Pulverbeschichtung bietet. Eine saubere Oberfläche verbessert die Haftung der Beschichtung und schützt die Werkstücke vor weiterer Korrosion und Oxidation.
Wesentliche Gründe für die Entrostung und Oxidentfernung sind:
- Verbesserte Haftung: Eine metallisch reine Oberfläche gewährleistet, dass die Pulverbeschichtung besser an der Oberfläche haftet, was die Lebensdauer und Beständigkeit erhöht.
- Vermeidung von Oberflächendefekten: Rost und Oxidschichten können Unebenheiten und Haftungsschwächen verursachen, die zu Blasenbildung, Rissen oder Abplatzungen führen.
- Korrosionsschutz: Durch die vollständige Entfernung von Rost und Oxiden wird die Korrosionsbeständigkeit erhöht und das Werkstück optimal geschützt.
2. Methoden der Entrostung und Oxidentfernung
Es gibt verschiedene Methoden, um Rost und Oxidschichten zu entfernen, die sich je nach Werkstoff, Verunreinigungsgrad und Produktionsanforderungen unterscheiden. Die gängigsten Methoden umfassen mechanische und chemische Verfahren sowie Kombinationen aus beiden.
2.1 Mechanische Verfahren
Mechanische Verfahren zur Entrostung und Oxidentfernung sind besonders bei stark verrosteten Oberflächen effektiv. Sie arbeiten durch Abrieb und tragen die obere Schicht des Werkstücks ab, um eine saubere Oberfläche freizulegen.
- Sandstrahlen: Sandstrahlen ist ein abrasives Verfahren, bei dem Schleifmittel wie Sand, Glasperlen oder Korund mit hoher Geschwindigkeit auf die Oberfläche geschossen werden. Der Abrieb entfernt Rost und Oxidschichten und hinterlässt eine leicht raue Oberfläche, die die Haftung des Pulvers verbessert.
- Vorteile:
- Effektiv bei stark verrosteten Oberflächen.
- Schafft eine ideale Haftgrundlage durch Rauigkeit.
- Nachteile:
- Kann bei empfindlichen Werkstücken Materialverlust verursachen.
- Erfordert strenge Sicherheitsmaßnahmen wegen des entstehenden Staubs.
- Vorteile:
- Kugelstrahlen (Shot Blasting): Beim Kugelstrahlen werden kleine Stahlkugeln oder andere kugelförmige Schleifmittel auf die Oberfläche geschossen, um Rost und Oxide zu entfernen. Dieses Verfahren ist besonders effektiv bei großen und widerstandsfähigen Werkstücken.
- Vorteile:
- Entfernt Rost schnell und hinterlässt eine saubere, haftfähige Oberfläche.
- Hohe Effizienz bei der Behandlung von großflächigen Werkstücken.
- Nachteile:
- Kann die Oberfläche bei dünnen Materialien beschädigen.
- Höherer Wartungsaufwand der Strahlmittel.
- Vorteile:
- Schleifen und Bürsten: Bei weniger stark verrosteten Werkstücken oder gezielten Bereichen kann die Oxidschicht manuell oder maschinell durch Schleifen oder Bürsten entfernt werden. Hierfür werden Schleifpapier, Bürsten oder spezielle Schleifmaschinen verwendet.
- Vorteile:
- Genaue Kontrolle der zu behandelnden Bereiche.
- Eignet sich gut für kleine Flächen und gezielte Anwendungen.
- Nachteile:
- Zeitaufwendig und oft ineffizient für große Flächen.
- Hoher Materialabtrag, insbesondere bei empfindlichen Werkstücken.
- Vorteile:
2.2 Chemische Verfahren
Chemische Verfahren zur Entrostung und Oxidentfernung kommen oft bei Materialien zum Einsatz, die eine schonendere Behandlung benötigen oder wenn die Oxidschicht besonders stark ist. Diese Verfahren arbeiten mit Säuren oder Laugen, die die Oxidschicht chemisch auflösen.
- Chemisches Beizen: Beim Beizen werden die Werkstücke in ein Säurebad getaucht, das die Rost- und Oxidschicht löst und entfernt. Häufig verwendete Säuren sind Phosphorsäure, Salzsäure und Schwefelsäure. Das chemische Beizen ist besonders wirksam bei Stahl und anderen Metallen, die stark oxidieren.
- Vorteile:
- Sehr effektiv bei der Entfernung dicker Rostschichten.
- Geringe mechanische Belastung der Werkstücke.
- Nachteile:
- Hohe Umwelt- und Sicherheitsauflagen aufgrund der Verwendung von starken Säuren.
- Erfordert eine gründliche Nachbehandlung (Spülen und Neutralisieren), um Säurerückstände zu entfernen.
- Vorteile:
- Säurereinigung (Pickling): Bei der Säurereinigung werden mildere Säuren verwendet, die die Oxidschicht ablösen, ohne das Grundmaterial anzugreifen. Diese Methode eignet sich gut für empfindlichere Materialien, bei denen eine vollständige Beizung zu aggressiv wäre.
- Vorteile:
- Schont empfindliche Werkstücke und greift das Material nicht an.
- Bietet eine schonendere Alternative zur konventionellen Beizung.
- Nachteile:
- Geringere Effektivität bei stark verrosteten Oberflächen.
- Aufwendige Entsorgung und Sicherheitsmaßnahmen erforderlich.
- Vorteile:
- Phosphatierung: Die Phosphatierung ist eine chemische Vorbehandlung, die nicht nur Rost entfernt, sondern eine Schutzschicht auf der Oberfläche erzeugt. Diese Schicht verbessert die Haftung der Pulverbeschichtung und bietet zusätzlichen Korrosionsschutz.
- Vorteile:
- Entfernt Rost und schützt die Oberfläche zugleich.
- Hohe Haftungsförderung für die Pulverbeschichtung.
- Nachteile:
- Etwas längere Prozessdauer als konventionelles Beizen.
- Bei starkem Rost nicht immer ausreichend.
- Vorteile:
2.3 Thermische Verfahren
Thermische Verfahren zur Oxidentfernung setzen hohe Temperaturen ein, um die Oxidschicht auf der Oberfläche zu zersetzen. Diese Methoden sind besonders wirksam für Materialien, die sehr hohe Temperaturen vertragen.
- Flammspritzen: Beim Flammspritzen wird eine heiße Flamme oder ein Plasma verwendet, um die Oxidschicht auf der Oberfläche zu verbrennen. Danach kann der Rost oder das Oxid leicht mechanisch entfernt werden.
- Vorteile:
- Schnelle und effektive Entfernung von Rost bei hitzebeständigen Materialien.
- Oft in Kombination mit einer mechanischen Nachbearbeitung angewendet.
- Nachteile:
- Hoher Energieaufwand und Kosten.
- Ungeeignet für temperaturempfindliche Werkstoffe.
- Vorteile:
- Induktionsbehandlung: Induktionsspulen erzeugen Wärme durch elektromagnetische Induktion, die gezielt auf bestimmte Bereiche der Werkstücke wirkt. Diese Methode eignet sich gut für Werkstücke, die selektiv von Rost und Oxiden befreit werden sollen.
- Vorteile:
- Kontrollierte Wärmebehandlung, die auf bestimmte Bereiche angewendet werden kann.
- Schnell und effizient.
- Nachteile:
- Hohe Investitionskosten für Induktionsanlagen.
- Aufwändige Einstellung und Anpassung für unterschiedliche Werkstückgrößen.
- Vorteile:
3. Kombinierte Verfahren
In vielen Fällen wird eine Kombination aus mechanischen und chemischen Verfahren eingesetzt, um die Oxidentfernung und Entrostung zu optimieren. Ein Beispiel hierfür ist das kombinierte Sandstrahlen und Beizen, bei dem das Sandstrahlen zunächst die gröberen Oxidschichten entfernt und das chemische Beizen anschließend die Oberfläche vollständig reinigt.
Vorteile der kombinierten Verfahren:
- Effektivere Rostentfernung: Kombinierte Verfahren entfernen sowohl grobe als auch feine Oxidschichten und hinterlassen eine metallisch saubere Oberfläche.
- Zeit- und Kosteneinsparungen: Durch die Kombination der Verfahren können Zeit und Ressourcen gespart werden, da die Werkstücke oft in einem Arbeitsschritt vollständig gereinigt werden.
4. Prozessüberwachung und Qualitätskontrolle
Um die Qualität und Effektivität der Entrostung und Oxidentfernung sicherzustellen, sind Prozessüberwachung und Qualitätskontrolle entscheidend:
- Visuelle Inspektion: Nach der Entrostung und Oxidentfernung wird die Oberfläche visuell auf Reste von Rost oder Oxid überprüft.
- Oberflächenanalysen: Spezielle Analysegeräte messen die Sauberkeit und Rauheit der Oberfläche, um sicherzustellen, dass sie optimal für die Pulverbeschichtung vorbereitet ist.
- Schichtdickenmessung: Nach der Phosphatierung oder anderen chemischen Verfahren wird die Dicke der Schutzschicht gemessen, um die Haftungsförderung zu kontrollieren.
5. Umwelt- und Sicherheitsaspekte
Die Entrostung und Oxidentfernung kann chemische Stoffe und abrasive Mittel erfordern, die Umwelt- und Sicherheitsmaßnahmen nötig machen:
- Abgasreinigung und Luftfiltersysteme: Anlagen mit Sandstrahlverfahren oder thermischen Verfahren sollten mit Staub- und Abgasfiltersystemen ausgestattet sein, um die Belastung der Luft zu minimieren.
- Sicherheitsausrüstung: Besonders bei der Arbeit mit Chemikalien und abrasiven Verfahren ist persönliche Schutzausrüstung wie Atemschutzmasken und Schutzbrillen unerlässlich.
- Chemikalienmanagement: Bei der chemischen Oxidentfernung müssen Entsorgung und Aufbereitung der Säuren umweltgerecht erfolgen, um Wasser und Böden zu schützen.
Fazit
Die Entrostung und Oxidentfernung ist ein unverzichtbarer Schritt im Pulverbeschichtungsprozess und erfordert eine sorgfältige Auswahl der richtigen Methode, abhängig vom Material und der Art des Rosts oder der Oxidschicht. Mechanische, chemische und thermische Verfahren bieten jeweils spezifische Vorteile und können oft kombiniert werden, um eine metallisch reine und haftfähige Oberfläche zu schaffen. Die Qualität der Entrostung und Oxidentfernung ist entscheidend für die Langlebigkeit und Beständigkeit der Pulverbeschichtung und trägt wesentlich zur Endqualität des Produkts bei.
Spülen und Neutralisieren in der Pulverbeschichtung – Verfahren, Prozessschritte und Qualitätskontrolle
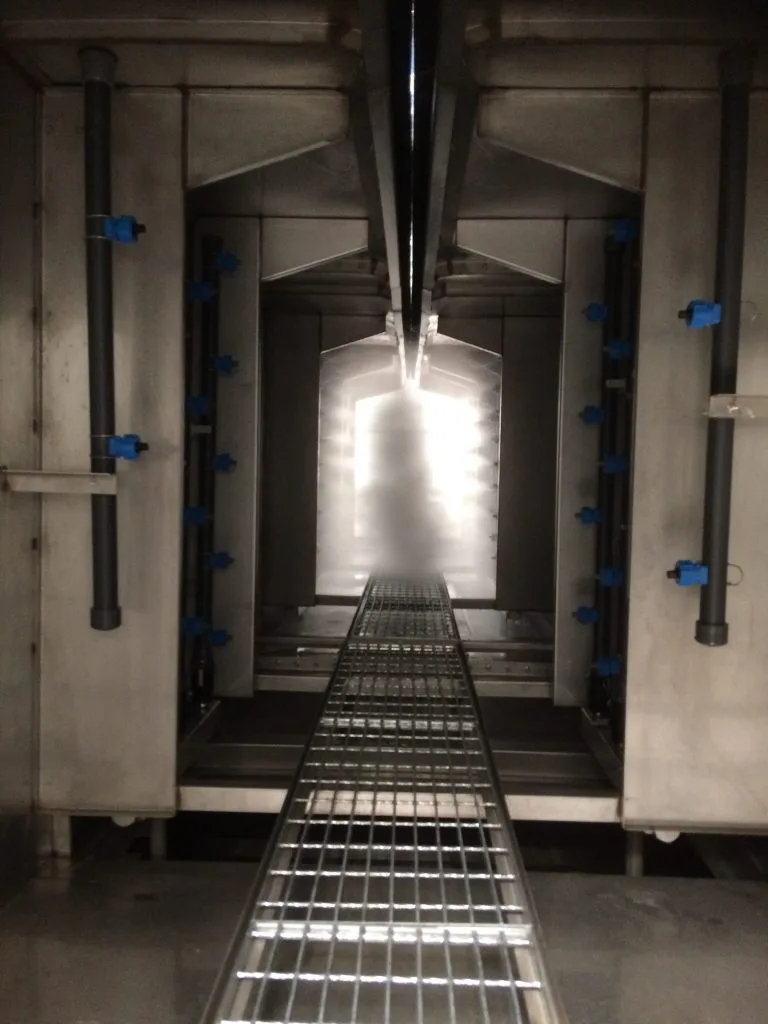
Das Spülen und Neutralisieren sind entscheidende Schritte in der Vorbehandlung für die Pulverbeschichtung, die unmittelbar nach den Prozessen der Entrostung, Reinigung und chemischen Vorbehandlung (wie der Phosphatierung) stattfinden. Diese Schritte sorgen dafür, dass Rückstände von Chemikalien und Verunreinigungen entfernt werden, die später die Haftung und Qualität der Pulverbeschichtung beeinträchtigen könnten. Ein gründliches Spülen und eine anschließende Neutralisierung sind wichtig, um eine saubere, gleichmäßige und haftfähige Oberfläche zu schaffen und eine hochwertige, langlebige Pulverbeschichtung sicherzustellen.
Dieser Leitfaden beschreibt die Notwendigkeit, die Verfahren und die Technik der Spül- und Neutralisationsschritte sowie die Maßnahmen zur Prozesskontrolle und Qualitätssicherung.
1. Bedeutung von Spülen und Neutralisieren
Die Schritte Spülen und Neutralisieren in der Pulverbeschichtung dienen verschiedenen Zwecken:
- Entfernung von Chemikalienrückständen: Nach der Entrostung oder chemischen Behandlungen können Säuren, Alkalien oder Tensidrückstände auf der Oberfläche verbleiben, die die Haftung der Pulverbeschichtung stören.
- Korrosionsschutz: Rückstände von Säuren oder anderen Chemikalien können die Werkstückoberfläche angreifen und zu vorzeitigem Korrosionsschaden führen, wenn sie nicht vollständig neutralisiert werden.
- Optimierung der Haftung: Saubere, chemikalienfreie Oberflächen verbessern die Haftung der Pulverbeschichtung und reduzieren das Risiko von Defekten wie Blasenbildung oder Ablösungen.
Eine gründliche Spülung und Neutralisation vor der Pulverbeschichtung sichert daher die Endqualität der Beschichtung und die Langlebigkeit des Werkstücks.
2. Der Spülprozess – Methoden und Techniken
Das Spülen erfolgt in mehreren Schritten, um die Werkstückoberflächen vollständig von chemischen Rückständen zu befreien. Dabei werden verschiedene Techniken angewendet:
2.1 Tauchspülen
Das Tauchspülen ist eine gängige Methode, bei der die Werkstücke vollständig in ein Wasserbad eingetaucht werden. Es wird in der Regel in einer Reihe von Tauchbecken durchgeführt, wobei jedes Becken eine spezifische Reinigungsstufe darstellt.
- Ablauf:
- Die Werkstücke werden in das erste Spülbad eingetaucht, wo die groben Chemikalienrückstände gelöst werden.
- Die Werkstücke durchlaufen weitere Spülbäder, bis die Oberflächen vollständig gereinigt sind.
- Vorteile:
- Effizient bei großflächigen Werkstücken.
- Sorgt für eine vollständige Bedeckung der Oberfläche.
- Nachteile:
- Hoher Wasserverbrauch, da die Bäder regelmäßig erneuert werden müssen.
- Große Spülbecken und Tauchvorrichtungen sind erforderlich, was Platz und Ressourcen benötigt.
2.2 Sprühspülen
Beim Sprühspülen werden die Werkstücke mit Wasser oder einer Spüllösung aus Düsen besprüht. Diese Methode wird häufig für kleinere Werkstücke oder bei kontinuierlichen Prozessen verwendet, in denen die Werkstücke auf einem Förderband durch die Spülstationen transportiert werden.
- Ablauf:
- Die Werkstücke werden durch mehrere Sprühstationen geleitet, wo die Chemikalienrückstände mit hohem Wasserdruck entfernt werden.
- In der Regel wird demineralisiertes Wasser verwendet, um Kalkflecken und Rückstände zu vermeiden.
- Vorteile:
- Reduziert den Wasserverbrauch im Vergleich zum Tauchspülen.
- Schnell und gut in automatisierte Systeme integrierbar.
- Nachteile:
- Eventuell weniger effektiv bei komplex geformten Werkstücken.
- Höherer Wartungsaufwand der Düsen und Sprühanlage.
2.3 Ultraschallspülen
Das Ultraschallspülen ist eine spezielle Methode, die Ultraschallwellen nutzt, um die Reinigungskraft des Spülbades zu verstärken. Diese Methode ist besonders effektiv bei komplex geformten Werkstücken und empfindlichen Oberflächen.
- Ablauf:
- Die Werkstücke werden in ein Ultraschallbad eingetaucht, in dem die Ultraschallwellen kleine Bläschen (Kavitation) erzeugen. Diese Bläschen implodieren an der Oberfläche und lösen so die chemischen Rückstände.
- Vorteile:
- Effizient bei kleinen und komplexen Werkstücken.
- Hohe Reinigungsleistung und gründliche Entfernung von Rückständen.
- Nachteile:
- Höherer Energieverbrauch und kostenintensive Ausstattung.
- Für großflächige Werkstücke oft weniger wirtschaftlich.
2.4 Einsatz von demineralisiertem Wasser
Demineralisiertes oder entionisiertes Wasser wird häufig für die letzten Spülschritte verwendet, um sicherzustellen, dass keine Mineralien oder Kalkablagerungen auf den Werkstücken zurückbleiben, die die Pulverbeschichtung beeinträchtigen könnten.
- Vorteile:
- Reduziert Rückstände und verhindert Fleckenbildung.
- Bessere Haftung der Beschichtung.
- Nachteile:
- Höhere Kosten für die Wasseraufbereitung.
- Regelmäßige Überprüfung und Wartung des demineralisierten Wassersystems erforderlich.
3. Neutralisation – Methoden und Techniken
Nach dem Spülen wird häufig eine Neutralisation durchgeführt, um eventuell verbleibende saure oder alkalische Rückstände auszugleichen und den pH-Wert der Werkstückoberfläche zu stabilisieren. Je nach Vorbehandlung kommen unterschiedliche Neutralisationsmethoden zum Einsatz.
3.1 Säure- oder Laugenneutralisation
Um eine verbleibende Alkalität oder Säure auszugleichen, kann eine leichte Säure oder Base eingesetzt werden, die den pH-Wert neutralisiert und die Oberfläche für die Beschichtung vorbereitet.
- Beispiel:
- Wenn die Vorbehandlung mit einer Säurelösung erfolgt ist, kann eine basische Lösung (Laugenbad) verwendet werden, um die Oberfläche zu neutralisieren und zu stabilisieren.
- Vorteile:
- Schnelle und effiziente Neutralisation.
- Flexibel einsetzbar und an verschiedene Materialien anpassbar.
- Nachteile:
- Erfordert eine genaue Überwachung der Konzentration, um die Oberfläche nicht zu schädigen.
- Chemische Neutralisationsmittel müssen sicher gehandhabt und entsorgt werden.
3.2 Wasserneutralisation (pH-stabiles Wasserbad)
Ein neutralisierendes Wasserbad, das im neutralen pH-Bereich (um 7) gehalten wird, kann dazu beitragen, die Restchemikalien vollständig zu entfernen und die Oberfläche zu stabilisieren.
- Ablauf:
- Die Werkstücke werden in das Wasserbad getaucht, in dem verbliebene Rückstände abgespült und neutralisiert werden.
- Vorteile:
- Umweltfreundliche Methode ohne zusätzliche Chemikalien.
- Reduziert das Risiko von Überneutralisation.
- Nachteile:
- Weniger effektiv bei stark säure- oder basenbelasteten Oberflächen.
- Regelmäßige Überwachung des pH-Werts im Wasserbad erforderlich.
3.3 CO₂-Neutralisation
Ein innovativeres Verfahren ist die Neutralisation durch Kohlendioxid (CO₂), das im Wasser gelöst wird und eine leicht saure Lösung bildet. Diese Methode ist besonders umweltfreundlich und stabilisiert die Werkstückoberfläche.
- Vorteile:
- Umweltfreundlich und sicher in der Anwendung.
- Vermeidet die Verwendung zusätzlicher Chemikalien.
- Nachteile:
- Spezielle Ausrüstung erforderlich.
- Hohe Kosten im Vergleich zu herkömmlichen Neutralisationsverfahren.
4. Qualitätskontrolle und Prozessüberwachung
Um die Wirksamkeit von Spülen und Neutralisieren sicherzustellen, sind verschiedene Kontrollmaßnahmen notwendig:
- pH-Wert-Messung: Der pH-Wert der Werkstückoberfläche sollte nach dem Neutralisieren neutral bis leicht sauer sein (pH 6–7), um eine gleichmäßige Haftung der Beschichtung zu gewährleisten.
- Leitfähigkeitsmessung: Die Leitfähigkeit des Spülwassers wird gemessen, um den Verschmutzungsgrad zu überwachen. Niedrige Leitfähigkeit weist auf eine geringe Konzentration von Rückständen hin.
- Oberflächenprüfung: Die Oberfläche wird optisch und mit Testmethoden (z. B. Benetzbarkeitstest) untersucht, um sicherzustellen, dass keine Flecken, Rückstände oder chemische Verunreinigungen vorliegen.
- Bakterien- und Keimkontrolle: Bei Wasserbädern wird der Keimgehalt überwacht, um sicherzustellen, dass keine Verunreinigungen die Oberflächenqualität beeinträchtigen.
5. Umwelt- und Sicherheitsaspekte
Das Spülen und Neutralisieren bringt gewisse Umwelt- und Sicherheitsanforderungen mit sich:
- Abwassermanagement: Chemisch belastete Spülwässer müssen aufbereitet und umweltgerecht entsorgt werden. Hierzu gehören Filteranlagen und chemische Neutralisationssysteme.
- Einsatz von Recycling-Systemen: Wasserrecycling-Systeme senken den Wasserverbrauch und verringern die Betriebskosten.
- Sicherheitsvorkehrungen: Arbeitssicherheitsmaßnahmen wie die Bereitstellung von Schutzausrüstung für das Personal sind unerlässlich, besonders wenn aggressive Chemikalien eingesetzt werden.
Fazit
Die Schritte des Spülens und Neutralisierens sind essenziell, um eine optimale Oberfläche für die Pulverbeschichtung zu schaffen. Sie gewährleisten, dass chemische Rückstände vollständig entfernt und die Werkstücke für den weiteren Beschichtungsprozess vorbereitet sind. Durch die richtige Auswahl von Spül- und Neutralisationsverfahren sowie eine strikte Prozessüberwachung und Qualitätskontrolle wird die Qualität und Langlebigkeit der Pulverbeschichtung nachhaltig verbessert. Innovative Techniken wie CO₂-Neutralisation und Wasserrecycling tragen zur Umweltfreundlichkeit und Effizienz des Verfahrens bei und ermöglichen so eine moderne, nachhaltige Produktionsweise.
Phosphatierung und Konversionsbeschichtung in der Pulverbeschichtung – Verfahren, Anwendung und Vorteile
Die Phosphatierung und andere Formen der Konversionsbeschichtung sind zentrale Schritte in der Vorbehandlung von Werkstücken für die Pulverbeschichtung. Diese Verfahren erzeugen eine dünne, haftungsfördernde Schicht auf der Metalloberfläche, die eine wesentliche Grundlage für die Pulverbeschichtung schafft. Die Schicht, die durch die Phosphatierung oder Konversionsbeschichtung entsteht, schützt das Werkstück vor Korrosion und verbessert die Haftung der Pulverbeschichtung.
Dieser umfassende Leitfaden gibt einen Überblick über die Funktionsweise, die verschiedenen Methoden und Anwendungen sowie die Vorteile der Phosphatierung und alternativer Konversionsbeschichtungen.
1. Bedeutung der Phosphatierung und Konversionsbeschichtung
Die Hauptaufgaben der Phosphatierung und Konversionsbeschichtung sind:
- Verbesserung der Haftung: Die Beschichtung erzeugt eine mikroraue Oberfläche, die das Pulverbeschichtungsmaterial besser anhaften lässt.
- Korrosionsschutz: Phosphat- oder Konversionsschichten schützen die Metalloberfläche und verlängern die Lebensdauer des Werkstücks.
- Vermeidung von Blasenbildung: Durch die Reduktion von Reaktionen an der Metalloberfläche verhindert die Phosphatierung Blasenbildung und andere Defekte in der Pulverbeschichtung.
2. Arten der Phosphatierung
Es gibt verschiedene Arten der Phosphatierung, die jeweils spezifische Eigenschaften und Anwendungen haben. Die wichtigsten Verfahren sind:
2.1 Zinkphosphatierung
Die Zinkphosphatierung ist eine der gebräuchlichsten Formen der Phosphatierung und wird häufig in der Automobil- und Maschinenbauindustrie eingesetzt. Sie erzeugt eine dichte, kristalline Schicht auf Eisen- und Stahloberflächen.
- Vorteile:
- Bietet exzellenten Korrosionsschutz.
- Ideal für anspruchsvolle Anwendungen, z. B. in der Automobil- und Schwerindustrie.
- Hohe Haftungsverbesserung für Pulverbeschichtungen.
- Nachteile:
- Höhere Prozesskosten als andere Phosphatierungen.
- Erfordert strenge Umwelt- und Sicherheitsmaßnahmen wegen der verwendeten Chemikalien.
- Prozessablauf:
- Die Werkstücke werden zunächst entfettet und entrostet.
- Die Zinkphosphatschicht wird durch ein Bad mit Zinkphosphatlösung erzeugt, das eine kristalline Struktur auf der Oberfläche bildet.
- Anschließend werden die Werkstücke gründlich gespült und getrocknet.
2.2 Eisenphosphatierung
Die Eisenphosphatierung ist ein einfacheres Verfahren und wird häufig für weniger korrosionsanfällige Anwendungen verwendet. Diese Methode ist kostengünstiger und weniger aufwendig.
- Vorteile:
- Kostengünstiger und einfacherer Prozess.
- Ausreichend für Innenanwendungen oder Anwendungen mit geringem Korrosionsrisiko.
- Nachteile:
- Bietet geringeren Korrosionsschutz als Zinkphosphatierung.
- Nicht für stark beanspruchte Werkstücke geeignet.
- Prozessablauf:
- Die Werkstücke werden durch ein Bad mit Eisenphosphatlösung geführt.
- Die dünne Phosphatschicht bildet sich als Haftgrund und Korrosionsschutz.
- Nach der Behandlung werden die Werkstücke gespült und getrocknet.
2.3 Manganphosphatierung
Die Manganphosphatierung wird speziell für Anwendungen verwendet, bei denen hohe mechanische Beanspruchungen auftreten. Diese Methode findet sich oft in der Automobilindustrie und bei Motorenkomponenten.
- Vorteile:
- Hohe Verschleißfestigkeit und ideal für stark beanspruchte Werkstücke.
- Reduziert Reibung und Verschleiß bei beweglichen Teilen.
- Nachteile:
- Kostenintensiver als Eisen- oder Zinkphosphatierung.
- Hoher Aufwand in der Prozesssteuerung und Qualitätskontrolle.
- Prozessablauf:
- Die Oberfläche wird entfettet und entrostet.
- Die Manganphosphatschicht wird durch ein Bad mit Manganphosphatlösung erzeugt.
- Anschließend erfolgt eine Trocknung und in einigen Fällen eine Nachbehandlung zur Optimierung der Korrosionsbeständigkeit.
3. Alternative Konversionsbeschichtungen
Neben der klassischen Phosphatierung gibt es andere Verfahren der Konversionsbeschichtung, die zunehmend an Bedeutung gewinnen, insbesondere wegen ihrer umweltfreundlicheren Eigenschaften.
3.1 Chromatierung
Die Chromatierung, speziell die Chrom(III)-Basierte Chromatierung, wird hauptsächlich bei Aluminium und Zink angewendet. Sie bildet eine widerstandsfähige Schicht und bietet einen hervorragenden Korrosionsschutz.
- Vorteile:
- Exzellenter Korrosionsschutz und Haftgrund für die Pulverbeschichtung.
- Chrom(III)-Verbindungen sind weniger umweltbelastend als das inzwischen weitgehend verbotene Chrom(VI).
- Nachteile:
- Chromhaltige Verfahren sind trotz Fortschritten in der Umweltfreundlichkeit immer noch streng reguliert.
- Höhere Kosten und Einschränkungen im Umgang mit Chrom.
- Prozessablauf:
- Die Werkstücke werden gereinigt und entfettet.
- Sie werden in eine Chromatlösung getaucht, die die Schutzschicht bildet.
- Die Teile werden gespült und getrocknet.
3.2 Nanokeramische Beschichtungen
Nanokeramische oder nanopartikuläre Beschichtungen basieren auf Zirkonium oder Silizium und bieten eine umweltfreundliche Alternative zur Phosphatierung und Chromatierung. Diese Technologien entwickeln sich stetig und bieten vielfältige Anwendungsmöglichkeiten.
- Vorteile:
- Umweltfreundlich und wenig gefährliche Abfallprodukte.
- Bietet hohen Korrosionsschutz und gute Haftungsförderung für die Pulverbeschichtung.
- Nachteile:
- Höhere Kosten als klassische Phosphatierungen.
- Erfordert spezialisierte Anlagen und Prozesssteuerung.
- Prozessablauf:
- Werkstücke werden gereinigt und entfettet.
- Die Beschichtung erfolgt durch ein Nanokeramik-Bad, das eine schützende Schicht auf der Oberfläche bildet.
- Die Werkstücke werden gespült und getrocknet.
3.3 Silanbasierte Konversionsbeschichtungen
Silanbeschichtungen sind eine neuere Alternative, die sich durch ihre einfache Anwendung und die umweltfreundlichen Eigenschaften auszeichnet. Sie bieten ausreichenden Korrosionsschutz und eine gute Grundlage für die Pulverbeschichtung.
- Vorteile:
- Umweltfreundlich und leicht anwendbar.
- Gute Haftung und Beständigkeit, ideal für viele Metalle.
- Nachteile:
- Der Korrosionsschutz ist bei extremen Bedingungen nicht so effektiv wie bei Zinkphosphatierung.
- Noch wenig verbreitet und in der Anwendung weniger erforscht.
- Prozessablauf:
- Werkstücke werden gereinigt und entfettet.
- Eine Silanlösung wird aufgetragen oder die Teile werden darin getaucht.
- Anschließend werden die Werkstücke getrocknet und können direkt beschichtet werden.
4. Prozesssteuerung und Qualitätskontrolle
Eine präzise Prozesssteuerung und Qualitätskontrolle sind entscheidend für den Erfolg der Phosphatierung und Konversionsbeschichtung. Folgende Maßnahmen werden häufig durchgeführt:
- Schichtdickenmessung: Die Dicke der Phosphat- oder Konversionsschicht wird gemessen, um die Einhaltung der Spezifikationen sicherzustellen.
- pH-Wert-Überwachung: Der pH-Wert der Chemikalienbäder wird regelmäßig überprüft, um eine konstante Qualität der Beschichtung zu gewährleisten.
- Temperaturkontrolle: Die Temperatur der Bäder beeinflusst die Qualität und Dicke der Schicht. Eine konstante Temperatur ist wichtig für ein gleichmäßiges Ergebnis.
- Sichtkontrolle und Haftungstests: Nach der Beschichtung wird die Oberfläche visuell inspiziert und ggf. durch Tests wie den Gitterschnitt-Test auf Haftungsfestigkeit geprüft.
5. Umwelt- und Sicherheitsaspekte
Die Phosphatierung und Konversionsbeschichtung bringen einige Herausforderungen in Bezug auf Umwelt- und Arbeitssicherheit mit sich:
- Abfallentsorgung: Die Bäder der Phosphatierung enthalten oft Schwermetalle und müssen nach der Verwendung sorgfältig entsorgt werden. Moderne Recycling- und Filtrationssysteme können helfen, Abfall zu reduzieren.
- Schutzmaßnahmen für das Personal: Besonders bei der Chromatierung oder der Behandlung mit Nanopartikeln sind persönliche Schutzausrüstung und gute Belüftung erforderlich, um die Exposition gegenüber Chemikalien zu minimieren.
- Einsatz von umweltfreundlicheren Verfahren: Die Entwicklung neuer Konversionsbeschichtungen wie Nanokeramik oder Silanbeschichtungen trägt dazu bei, die Umweltbelastung der Vorbehandlung zu verringern.
6. Anwendung und Einsatzbereiche
Die Phosphatierung und Konversionsbeschichtungen finden in zahlreichen Branchen Anwendung:
- Automobilindustrie: Zinkphosphatierung und Manganphosphatierung werden für Karosserieteile, Motorenkomponenten und andere Teile eingesetzt, die besonders korrosionsanfällig sind.
- Maschinenbau: Konversionsbeschichtungen schützen Maschinenkomponenten vor Korrosion und verbessern die Haftung von Pulverbeschichtungen in der Schwerindustrie.
- Bau- und Architekturbranche: Aluminium- und Stahlbauteile werden häufig mit Chrom- oder Nanobeschichtungen behandelt, bevor sie pulverbeschichtet und für Fassaden, Fensterrahmen und Türsysteme verwendet werden.
Fazit
Die Phosphatierung und Konversionsbeschichtung sind entscheidende Schritte in der Vorbehandlung zur Pulverbeschichtung. Sie fördern die Haftung der Pulverschicht und bieten zugleich einen hervorragenden Korrosionsschutz. Die Wahl des richtigen Verfahrens – ob Zinkphosphatierung, Chromatierung, Nanokeramik- oder Silanbeschichtungen – hängt von den spezifischen Anforderungen und Einsatzbereichen ab. Umweltfreundliche Alternativen wie nanokeramische Beschichtungen und Silanverfahren gewinnen zunehmend an Bedeutung, da sie eine geringere Umweltbelastung und hohe Effizienz bieten. Die fortschreitende Entwicklung dieser Verfahren trägt zu einer nachhaltigeren und sichereren Pulverbeschichtung bei und sichert gleichzeitig die hohe Qualität der Endprodukte.
Trocknung der Werkstücke in der Pulverbeschichtung – Methoden, Prozesse und Innovationen
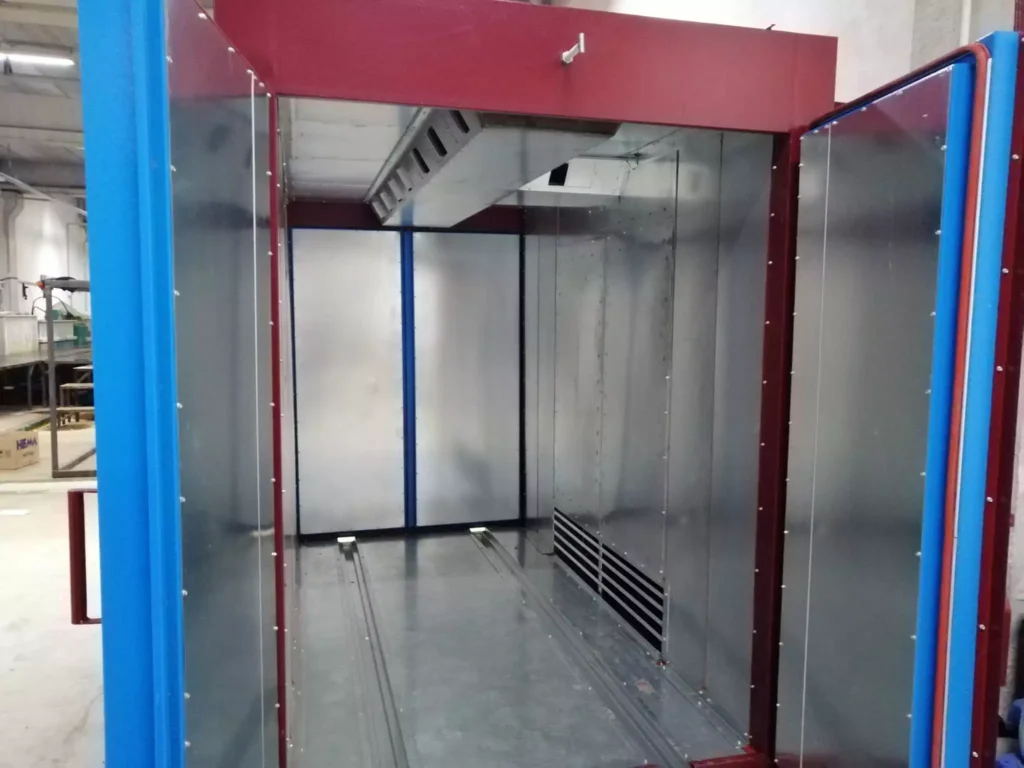
Die Trocknung der Werkstücke ist ein entscheidender Schritt im Pulverbeschichtungsprozess, der direkt nach der Vorbehandlung und vor der Beschichtung stattfindet. Eine gründliche Trocknung sorgt dafür, dass alle Restfeuchtigkeit und Rückstände von Reinigungs- oder Spüllösungen entfernt werden. Dies ist notwendig, um optimale Haftungsbedingungen für die Pulverbeschichtung zu schaffen und Defekte wie Blasenbildung oder Ablösungen zu vermeiden. Die Qualität und Effizienz der Trocknung beeinflussen maßgeblich das Endergebnis der Beschichtung und die Langlebigkeit der Werkstücke.
Dieser Leitfaden erläutert die Bedeutung der Trocknung, verschiedene Trocknungsmethoden, moderne Technologien sowie wichtige Aspekte der Prozesssteuerung und Qualitätssicherung.
1. Bedeutung der Trocknung im Pulverbeschichtungsprozess
Die Trocknung der Werkstücke ist notwendig, um optimale Voraussetzungen für die Pulverbeschichtung zu schaffen. Restfeuchtigkeit oder Verunreinigungen auf der Oberfläche können schwerwiegende Auswirkungen auf die Qualität der Beschichtung haben:
- Verbesserte Haftung: Die Pulverbeschichtung haftet nur auf trockenen, fett- und feuchtigkeitsfreien Oberflächen optimal. Restfeuchtigkeit führt zu schlechter Haftung, was die Lebensdauer der Beschichtung reduziert.
- Vermeidung von Blasenbildung: Feuchtigkeit, die während der Beschichtung oder des Einbrennens in der Oberfläche eingeschlossen bleibt, kann zu Blasen und anderen Oberflächendefekten führen.
- Korrosionsschutz: Eine feuchte Oberfläche kann bereits vor der Beschichtung oxidieren, was später zu Korrosionsproblemen führen kann.
2. Trocknungsmethoden für Werkstücke
Je nach Material, Größe der Werkstücke und den Produktionsanforderungen kommen unterschiedliche Trocknungsmethoden zum Einsatz. Zu den gängigsten Verfahren gehören Umlufttrocknung, Infrarot- und Mikrowellentrocknung sowie Vakuumtrocknung.
2.1 Umlufttrocknung
Die Umlufttrocknung ist das am häufigsten eingesetzte Trocknungsverfahren in der Pulverbeschichtung. Hierbei werden die Werkstücke in einen Ofen oder eine Trockenkammer gebracht, in der heiße Luft zirkuliert.
- Funktionsweise: Warme Luft wird gleichmäßig im Trocknungsraum verteilt und verdampft die Feuchtigkeit auf der Oberfläche der Werkstücke. Ein Lüftungssystem sorgt für die Abfuhr der feuchten Luft und das Nachführen trockener, heißer Luft.
- Vorteile:
- Ideal für große Werkstücke und Massentrocknung.
- Gleichmäßige Erwärmung und zuverlässige Trocknung.
- Nachteile:
- Hoher Energieverbrauch durch Beheizung und Luftzirkulation.
- Längere Trocknungszeiten als bei Infrarot- oder Mikrowellenverfahren.
2.2 Infrarottrocknung
Die Infrarottrocknung nutzt Infrarotstrahlung, um die Oberfläche der Werkstücke direkt zu erwärmen. Diese Methode ist besonders effizient, da die Strahlung nur die äußere Schicht des Materials erhitzt und so eine schnelle Trocknung ermöglicht.
- Funktionsweise: Infrarotstrahler senden Wärmestrahlen aus, die direkt auf die Werkstückoberfläche treffen und die Feuchtigkeit verdampfen lassen. Die Strahlung dringt nur wenige Millimeter ein, sodass das Material selbst kaum erhitzt wird.
- Vorteile:
- Energieeffizient und kurze Trocknungszeiten.
- Besonders geeignet für dünne Werkstücke oder beschichtete Oberflächen.
- Nachteile:
- Schattenbereiche werden ungleichmäßig erwärmt, was zu unvollständiger Trocknung führen kann.
- Erfordert regelmäßige Wartung der Infrarotstrahler.
2.3 Mikrowellentrocknung
Die Mikrowellentrocknung ist ein schnelles und energieeffizientes Verfahren, bei dem Mikrowellenstrahlung zur Erwärmung und Verdampfung der Feuchtigkeit eingesetzt wird. Diese Methode ist in der Pulverbeschichtung jedoch weniger verbreitet und wird hauptsächlich für spezielle Materialien eingesetzt.
- Funktionsweise: Mikrowellen regen die Wassermoleküle in der Werkstückoberfläche an, wodurch die Feuchtigkeit direkt im Material erhitzt und verdampft wird.
- Vorteile:
- Schnelle und gleichmäßige Trocknung, selbst bei komplexen Werkstückformen.
- Energieeffizient, da nur die Wassermoleküle direkt erhitzt werden.
- Nachteile:
- Hohe Anschaffungskosten und spezieller Anwendungsbereich.
- Schwierige Steuerung und Materialkompatibilität notwendig.
2.4 Vakuumtrocknung
Die Vakuumtrocknung ist ein schonendes Verfahren, das besonders für temperaturempfindliche Werkstoffe geeignet ist. Unter Vakuum sinkt der Siedepunkt des Wassers, sodass die Feuchtigkeit bei niedrigeren Temperaturen verdampfen kann.
- Funktionsweise: Das Werkstück wird in eine Vakuumkammer gebracht, in der der Druck gesenkt wird. Bei niedrigem Druck verdampft die Feuchtigkeit bereits bei geringen Temperaturen und wird anschließend aus der Kammer abgeführt.
- Vorteile:
- Schonendes Verfahren für empfindliche Materialien.
- Verhindert Oxidation, da im Vakuum keine Sauerstoffzufuhr vorhanden ist.
- Nachteile:
- Hohe Kosten für Anschaffung und Betrieb.
- Langsamere Trocknung als bei anderen Verfahren.
3. Steuerung der Trocknungsparameter und Prozessüberwachung
Die Trocknungsparameter wie Temperatur, Luftzirkulation und Trocknungszeit haben einen erheblichen Einfluss auf die Qualität der Trocknung und müssen präzise gesteuert und überwacht werden.
- Temperaturkontrolle: Je nach Werkstoff und Trocknungsverfahren wird eine Temperatur zwischen 60°C und 120°C verwendet. Zu hohe Temperaturen können Materialien beschädigen, während zu niedrige Temperaturen eine unvollständige Trocknung verursachen können.
- Luftzirkulation: Eine gleichmäßige Luftverteilung sorgt dafür, dass die gesamte Oberfläche der Werkstücke gleichmäßig erwärmt und die Feuchtigkeit effektiv abtransportiert wird.
- Trocknungsdauer: Die Dauer des Trocknungsprozesses wird an die Materialart, die Feuchtigkeitsmenge und die Anforderungen der Pulverbeschichtung angepasst.
- Feuchtigkeitsüberwachung: Sensoren können den Feuchtigkeitsgehalt in der Trockenkammer und auf der Werkstückoberfläche überwachen, um die Prozessparameter automatisch anzupassen.
Moderne Trocknungssysteme verfügen über automatisierte Steuerungen, die Parameter wie Temperatur, Luftzirkulation und Feuchtigkeit in Echtzeit anpassen, um eine effiziente und gleichmäßige Trocknung sicherzustellen.
4. Nachhaltigkeit und Energieeffizienz in der Trocknung
Da die Trocknung einer der energieintensivsten Schritte im Pulverbeschichtungsprozess ist, gewinnen Maßnahmen zur Nachhaltigkeit und Energieeinsparung zunehmend an Bedeutung.
- Wärmerückgewinnung: Die Abwärme der Trocknung kann genutzt werden, um die Vorbehandlung oder andere Bereiche der Produktionsanlage zu unterstützen, wodurch der Gesamtenergieverbrauch sinkt.
- Optimierung der Ofentemperatur: Moderne Steuerungen sorgen dafür, dass die Temperatur nur so hoch ist wie nötig und senken die Temperatur, sobald die gewünschte Trocknung erreicht ist.
- Einsatz von Infrarot- und Mikrowellentechnologie: Diese energieeffizienten Trocknungsverfahren können gezielt eingesetzt werden, um Energie zu sparen und die Trocknungszeiten zu reduzieren.
- Isolierung der Trockenkammern: Eine gute Isolierung minimiert den Energieverlust und sorgt dafür, dass die Wärme im Trocknungsbereich verbleibt.
Diese Maßnahmen tragen dazu bei, den Energieverbrauch zu senken, die Betriebskosten zu reduzieren und die Umweltbelastung zu minimieren.
5. Qualitätskontrolle und Inspektion
Nach der Trocknung wird die Oberfläche der Werkstücke auf eventuelle Mängel oder Feuchtigkeitsreste überprüft, um sicherzustellen, dass sie für die Pulverbeschichtung vorbereitet ist.
- Feuchtigkeitsprüfung: Feuchtigkeitsmessgeräte können eingesetzt werden, um sicherzustellen, dass keine Restfeuchtigkeit auf der Oberfläche vorhanden ist.
- Temperaturprotokollierung: Die Temperaturen in der Trockenkammer werden aufgezeichnet, um sicherzustellen, dass die Werkstücke die optimale Temperatur erreicht haben und einheitlich getrocknet sind.
- Visuelle Inspektion: Die Werkstücke werden auf mögliche Trocknungsdefekte wie Flecken, Rückstände oder Verfärbungen überprüft, die durch ungleichmäßige Trocknung oder Restfeuchtigkeit verursacht sein könnten.
- Testbeschichtung: In einigen Fällen wird eine Testbeschichtung aufgebracht, um die Qualität der Trocknung und die Haftung zu überprüfen.
6. Zukunft und Innovationen in der Trocknungstechnologie
Neue Entwicklungen und Technologien verbessern die Effizienz und Qualität des Trocknungsprozesses in der Pulverbeschichtung und tragen zur Nachhaltigkeit bei.
- Automatisierte Trocknungssysteme: Fortschritte in der Automatisierungstechnik ermöglichen die exakte Steuerung von Trocknungsparametern in Echtzeit. Sensoren und Steuerungen können automatisch auf veränderte Werkstückbedingungen reagieren und den Trocknungsprozess optimieren.
- KI-gestützte Prozesssteuerung: Künstliche Intelligenz wird zunehmend eingesetzt, um Daten aus dem Trocknungsprozess zu analysieren und die Parameter kontinuierlich anzupassen, um Energieverbrauch und Trocknungszeit zu minimieren.
- Hochfrequenz- und Hybridtrocknungstechnologien: Neue Trocknungstechnologien wie die Hochfrequenz- oder Hybridtrocknung kombinieren verschiedene Trocknungsverfahren, um eine schnellere und effizientere Trocknung bei reduziertem Energieverbrauch zu erreichen.
- Einsatz umweltfreundlicher Materialien: Die Entwicklung von Pulverbeschichtungsmaterialien, die bei niedrigeren Temperaturen aufgetragen und gehärtet werden können, trägt ebenfalls zur Energieeinsparung und Reduzierung der Trocknungskosten bei.
Fazit
Die Trocknung der Werkstücke ist ein unverzichtbarer Schritt im Pulverbeschichtungsprozess, der die Grundlage für eine hochwertige, haftfähige und langlebige Beschichtung schafft. Die Wahl des Trocknungsverfahrens, eine präzise Steuerung der Trocknungsparameter und innovative Technologien sind entscheidend für eine effiziente und nachhaltige Trocknung. Fortschritte wie automatisierte Steuerungssysteme, KI-gestützte Prozesssteuerung und die Nutzung energieeffizienter Verfahren tragen dazu bei, die Qualität der Pulverbeschichtung zu maximieren und gleichzeitig Energieverbrauch und Umweltbelastung zu minimieren.
Trocknung im Pulverbeschichtungsprozess – Ein Überblick über Verfahren, Technologien und Prozessoptimierung
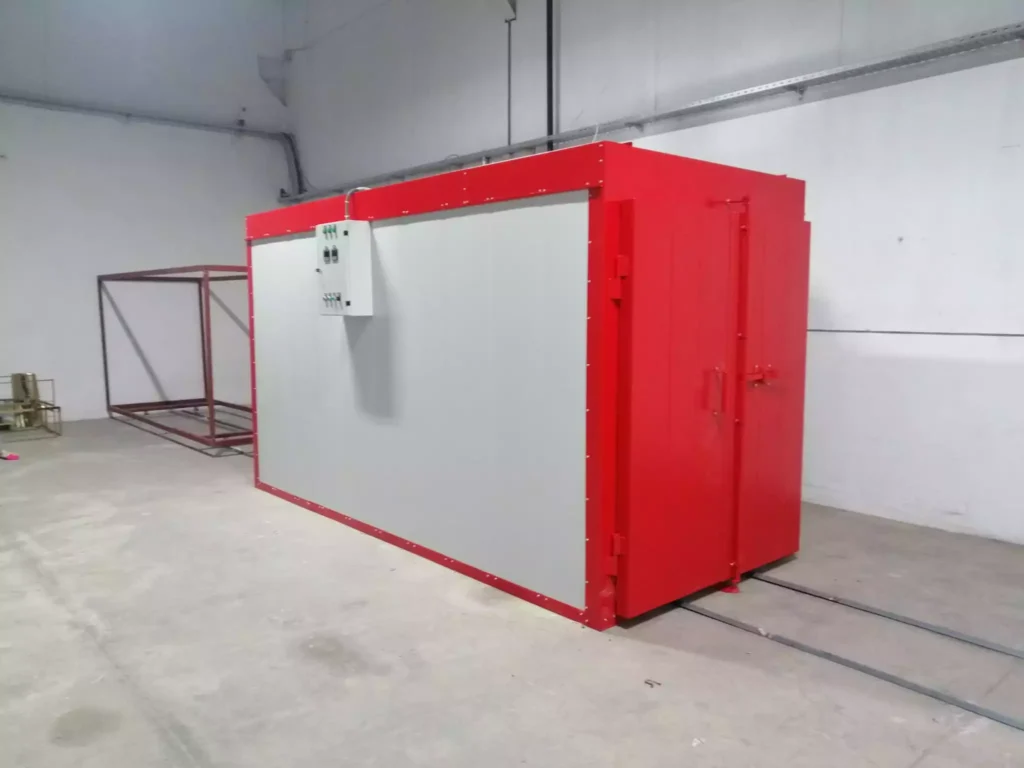
Die Trocknung ist ein wichtiger Prozessschritt in der Pulverbeschichtung, der unmittelbar nach der Vorbehandlung und vor dem Beschichten erfolgt. Durch die Trocknung werden Restfeuchte, chemische Rückstände und andere Verunreinigungen von den Werkstücken entfernt, was die Grundlage für eine optimale Haftung der Pulverbeschichtung schafft. Die Qualität und Effizienz der Trocknung beeinflussen maßgeblich die Beschichtungsqualität, die Haltbarkeit der Werkstücke und die Energieeffizienz der gesamten Produktionsanlage.
In diesem Überblick wird die Bedeutung der Trocknung, die verschiedenen Trocknungsverfahren, die Prozessüberwachung und Innovationen in der Trocknungstechnologie erläutert.
1. Bedeutung der Trocknung in der Pulverbeschichtung
Die Trocknung stellt sicher, dass die Werkstücke vor dem Auftragen der Pulverbeschichtung völlig frei von Feuchtigkeit und Chemikalien sind. Wenn Rückstände oder Feuchtigkeit auf der Oberfläche verbleiben, kann dies zu verschiedenen Problemen führen:
- Verbesserte Haftung: Trockene, saubere Oberflächen bieten bessere Bedingungen für die Pulverbeschichtung. Restfeuchte würde die Haftung beeinträchtigen und die Qualität der Beschichtung mindern.
- Vermeidung von Defekten: Feuchtigkeit oder Chemikalienreste auf der Oberfläche können während des Beschichtungs- und Aushärteprozesses verdampfen und Blasen oder andere Defekte verursachen.
- Korrosionsschutz: Eine vollständige Trocknung verhindert, dass Korrosion bereits vor dem Beschichten entsteht, was den langfristigen Schutz des Werkstücks erhöht.
2. Trocknungsverfahren für Werkstücke
Je nach Material, Werkstückgröße und Produktionsanforderungen kommen verschiedene Trocknungsverfahren zum Einsatz. Die gängigsten Verfahren sind:
2.1 Umlufttrocknung
Die Umlufttrocknung ist eines der am häufigsten eingesetzten Verfahren in der Pulverbeschichtung. Hierbei wird das Werkstück in einer Trockenkammer oder einem Ofen erwärmt und Feuchtigkeit durch zirkulierende Heißluft entfernt.
- Funktionsweise: Warme Luft wird im Trocknungsraum verteilt, wodurch die Feuchtigkeit auf der Werkstückoberfläche verdampft. Ein Belüftungssystem führt die feuchte Luft ab und trockene Luft nach.
- Vorteile:
- Besonders geeignet für große Werkstücke und hohe Durchsatzraten.
- Gleichmäßige Trocknung durch konstante Luftzirkulation.
- Nachteile:
- Hoher Energieverbrauch, da die Luft kontinuierlich erhitzt und zirkuliert werden muss.
- Längere Trocknungszeiten als bei Infrarot- oder Mikrowellenverfahren.
2.2 Infrarottrocknung
Die Infrarottrocknung ist ein energieeffizientes Verfahren, bei dem Infrarotstrahlen die Oberfläche der Werkstücke direkt erwärmen und die Feuchtigkeit verdampfen lassen.
- Funktionsweise: Infrarotstrahler erzeugen Wärmestrahlen, die auf die Werkstückoberfläche treffen und gezielt die äußeren Schichten erwärmen. Die Feuchtigkeit wird verdampft und verdunstet aus der Oberfläche.
- Vorteile:
- Schnelle und gleichmäßige Trocknung bei niedrigerem Energieverbrauch.
- Besonders geeignet für dünne Werkstücke oder Materialien, die eine gleichmäßige Erwärmung benötigen.
- Nachteile:
- Schattenbereiche auf der Oberfläche könnten weniger gut getrocknet werden.
- Regelmäßige Wartung und Kalibrierung der Infrarotstrahler erforderlich.
2.3 Mikrowellentrocknung
Mikrowellentrocknung ist ein modernes und schnelles Verfahren, bei dem Mikrowellenstrahlung verwendet wird, um die Feuchtigkeit direkt zu verdampfen.
- Funktionsweise: Mikrowellenstrahlen regen die Wassermoleküle in der Oberfläche an, wodurch die Feuchtigkeit gleichmäßig und schnell verdampft.
- Vorteile:
- Sehr effizient und kurze Trocknungszeiten, da nur die Wassermoleküle erhitzt werden.
- Eignet sich gut für dicke Werkstücke oder Werkstücke mit komplexen Formen.
- Nachteile:
- Höhere Kosten für Mikrowellenanlagen und spezielle Anforderungen an die Steuerung.
- Die Methode ist in der Pulverbeschichtung noch weniger verbreitet.
2.4 Vakuumtrocknung
Die Vakuumtrocknung ist ein schonendes Verfahren, das für temperaturempfindliche Materialien geeignet ist. Unter Vakuum sinkt der Siedepunkt des Wassers, sodass die Feuchtigkeit bei niedrigeren Temperaturen verdampft.
- Funktionsweise: In einer Vakuumkammer wird der Druck gesenkt, wodurch das Wasser schon bei geringen Temperaturen verdampft. Die Feuchtigkeit wird anschließend aus der Kammer entfernt.
- Vorteile:
- Eignet sich für empfindliche Materialien, die keine hohen Temperaturen vertragen.
- Verhindert Oxidation durch das Fehlen von Sauerstoff.
- Nachteile:
- Höhere Anschaffungs- und Betriebskosten.
- Der Prozess dauert länger als andere Trocknungsverfahren.
3. Prozesssteuerung und Qualitätskontrolle in der Trocknung
Eine präzise Steuerung der Trocknungsparameter wie Temperatur, Luftzirkulation und Trocknungsdauer ist für eine optimale Trocknung notwendig. Moderne Trocknungsanlagen sind häufig mit Steuerungssystemen ausgestattet, die die Prozessparameter überwachen und anpassen können.
- Temperatursteuerung: Die Temperatur wird an die Eigenschaften des Werkstücks angepasst. Zu hohe Temperaturen können Materialien beschädigen, während zu niedrige Temperaturen eine unvollständige Trocknung verursachen können.
- Luftzirkulation: Eine gleichmäßige Luftverteilung und Zirkulation stellen sicher, dass die gesamte Oberfläche gleichmäßig trocknet. Ventilatoren und Lüftungssysteme regulieren die Luftströme in der Trockenkammer.
- Feuchtigkeitsüberwachung: Sensoren messen den Feuchtigkeitsgehalt der Werkstücke und der Trocknungsluft. Die Daten können in Echtzeit ausgewertet werden, um sicherzustellen, dass die Oberfläche vollständig getrocknet ist.
- Trocknungszeit: Die Trocknungszeit wird an das Material und den Feuchtigkeitsgehalt der Werkstücke angepasst. Automatisierte Systeme passen die Trocknungszeit in Abhängigkeit von den gemessenen Werten automatisch an.
4. Nachhaltigkeit und Energieeffizienz in der Trocknung
Da die Trocknung im Pulverbeschichtungsprozess energieintensiv ist, sind Maßnahmen zur Verbesserung der Energieeffizienz und Nachhaltigkeit von großer Bedeutung.
- Wärmerückgewinnung: Die Abwärme, die während des Trocknens entsteht, kann zurückgeführt und für andere Prozessschritte wie die Vorbehandlung oder das Aufheizen des Trocknungsofens wiederverwendet werden.
- Isolierung der Trockenkammern: Eine gute Isolierung der Trocknungseinheiten verhindert Energieverluste und sorgt dafür, dass die Wärme effizient im System bleibt.
- Einsatz energieeffizienter Technologien: Der Einsatz von Infrarotstrahlern oder Mikrowellen kann den Energieverbrauch erheblich senken und die Trocknungszeiten verkürzen.
- Optimierung der Prozesssteuerung: Durch den Einsatz von Sensoren und automatisierter Steuerung können Trocknungsparameter wie Temperatur und Luftzirkulation so eingestellt werden, dass der Energieverbrauch minimiert wird.
Diese Maßnahmen tragen dazu bei, den Energieverbrauch zu reduzieren, die Betriebskosten zu senken und die Umweltbelastung zu minimieren.
5. Qualitätskontrolle nach der Trocknung
Nach dem Trocknungsprozess werden die Werkstücke auf Feuchtigkeitsrückstände und mögliche Trocknungsdefekte untersucht. Diese Inspektion ist entscheidend, um sicherzustellen, dass die Werkstücke optimal für die Pulverbeschichtung vorbereitet sind.
- Feuchtigkeitsprüfung: Die Feuchtigkeit auf der Oberfläche kann mit speziellen Messgeräten überprüft werden, um sicherzustellen, dass keine Restfeuchte vorhanden ist.
- Visuelle Inspektion: Sichtkontrollen können Defekte wie Flecken, Verfärbungen oder Rückstände auf der Oberfläche aufzeigen.
- Testbeschichtung: Bei Bedarf wird eine Testbeschichtung aufgebracht, um die Haftung und Qualität der Trocknung zu überprüfen.
6. Innovationen und Zukunftstrends in der Trocknungstechnologie
Neue Technologien und Innovationen treiben die Entwicklung effizienterer und umweltfreundlicherer Trocknungsverfahren in der Pulverbeschichtung voran.
- Automatisierte Steuerungssysteme: Fortschritte in der Automatisierung ermöglichen eine präzisere Steuerung der Trocknungsparameter in Echtzeit. Sensoren und Steuerungen passen die Bedingungen kontinuierlich an.
- KI-gestützte Prozessoptimierung: Künstliche Intelligenz wird zunehmend eingesetzt, um die Daten aus dem Trocknungsprozess zu analysieren und die Parameter anzupassen, um Energieverbrauch und Trocknungszeit zu optimieren.
- Hybridtrocknungstechnologien: Die Kombination von Verfahren wie Infrarot- und Konvektionstrocknung oder Mikrowellen- und Vakuumtrocknung kann die Effizienz weiter steigern.
- Entwicklung energieeffizienter Materialien: Neue Beschichtungsmaterialien, die bei niedrigeren Temperaturen aufgetragen und gehärtet werden können, senken die Trocknungskosten und verbessern die Energieeffizienz.
Fazit
Die Trocknung der Werkstücke ist ein zentraler Prozessschritt in der Pulverbeschichtung und beeinflusst maßgeblich die Qualität, Haftung und Langlebigkeit der Beschichtung. Eine präzise Steuerung der Trocknungsparameter, der Einsatz moderner Technologien wie Infrarot- und Mikrowellentrocknung und die Prozessoptimierung durch Automatisierung und Sensorik tragen dazu bei, eine gleichmäßige und effektive Trocknung sicherzustellen. Energieeffiziente Maßnahmen wie Wärmerückgewinnung und gute Isolierung leisten zudem einen wichtigen Beitrag zur Nachhaltigkeit und Kosteneffizienz. Durch die kontinuierliche Weiterentwicklung der Trocknungstechnologie wird die Pulverbeschichtung zunehmend umweltfreundlicher und wirtschaftlicher gestaltet.
Pulverbeschichtungskabine – Aufbau, Funktionsweise und Innovationen für eine optimale Pulverbeschichtung
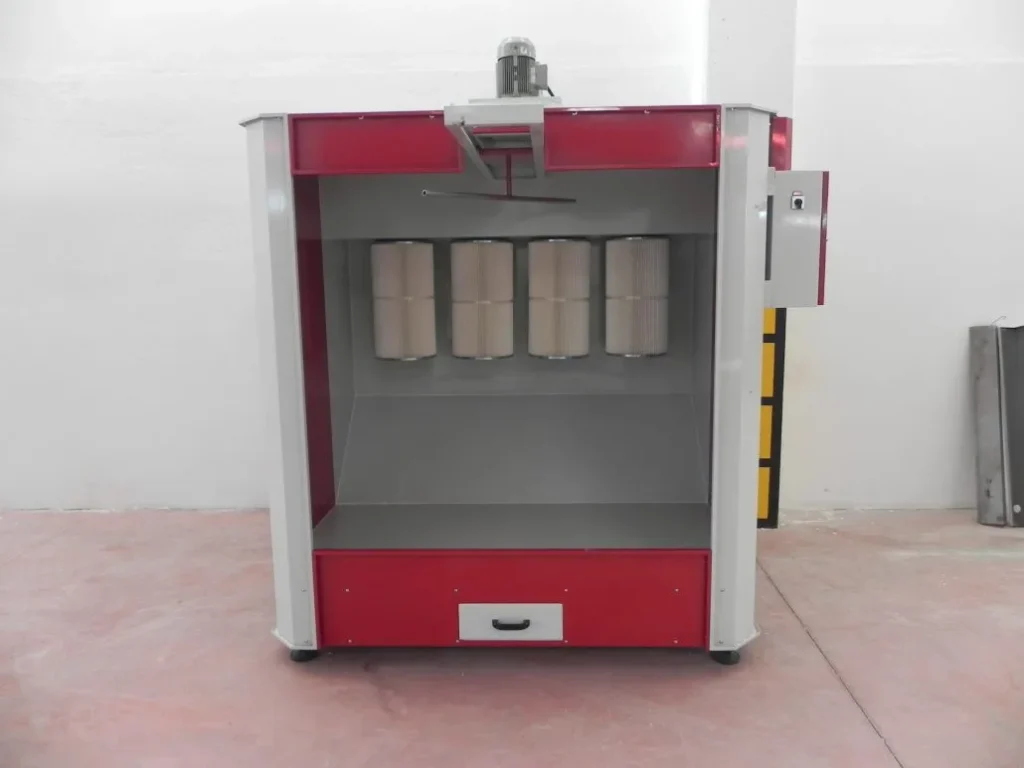
Die Pulverbeschichtungskabine ist ein zentrales Element im Pulverbeschichtungsprozess und entscheidend für die Qualität und Effizienz des Beschichtungsverfahrens. In der Kabine wird das Beschichtungspulver elektrostatisch aufgeladen und auf die Werkstücke gesprüht, um eine gleichmäßige und haftfeste Schicht zu erzeugen. Moderne Pulverbeschichtungskabinen sind mit fortschrittlichen Technologien zur Pulverrückgewinnung, Filterung und Prozesssteuerung ausgestattet, die eine nachhaltige und wirtschaftliche Beschichtung gewährleisten.
In diesem Leitfaden wird die Pulverbeschichtungskabine detailliert beschrieben – von ihrem Aufbau und der Funktionsweise bis hin zu innovativen Technologien und Aspekten der Prozessoptimierung.
1. Bedeutung der Pulverbeschichtungskabine im Beschichtungsprozess
Die Pulverbeschichtungskabine spielt eine entscheidende Rolle, um sicherzustellen, dass die aufgetragene Pulverschicht gleichmäßig, haftfest und ästhetisch ansprechend ist. Die Kabine ist dafür verantwortlich:
- Gleichmäßigen Pulverauftrag zu gewährleisten: In der Kabine wird das Pulver elektrostatisch aufgeladen und auf die Werkstücke aufgebracht, wodurch eine gleichmäßige Schicht erzielt wird.
- Überschüssiges Pulver aufzufangen und zu recyceln: Moderne Kabinen verfügen über Rückgewinnungssysteme, die das überschüssige Pulver auffangen und zur Wiederverwendung aufbereiten.
- Sicherheits- und Umweltstandards einzuhalten: Durch ausgeklügelte Filtersysteme werden Pulverpartikel und Staub aus der Luft gefiltert, um die Kabine und die Umgebung sauber und sicher zu halten.
Eine hochwertige Kabine trägt somit zur Langlebigkeit, Effizienz und Nachhaltigkeit des gesamten Pulverbeschichtungsprozesses bei.
2. Aufbau der Pulverbeschichtungskabine
Die Pulverbeschichtungskabine besteht aus mehreren funktionalen Komponenten, die zusammenarbeiten, um eine präzise und effiziente Beschichtung zu ermöglichen:
2.1 Gehäuse und Struktur der Kabine
Das Gehäuse der Pulverbeschichtungskabine ist meist aus robusten Materialien gefertigt und so gestaltet, dass es Pulverrückstände in der Kabine hält und gleichzeitig die Umgebung schützt. Die Kabinenstruktur umfasst:
- Kabinenwände: Oft aus Metall oder speziellem Kunststoff gefertigt, verhindern die Kabinenwände das Entweichen des Pulvers und erleichtern die Reinigung.
- Boden und Deckensysteme: Diese sind so konstruiert, dass überschüssiges Pulver schnell aufgefangen und zur Rückgewinnung transportiert wird.
- Beleuchtung: Die Kabine ist mit speziellen Beleuchtungssystemen ausgestattet, die eine gleichmäßige Beleuchtung sicherstellen und es den Bedienern erleichtern, den Pulverauftrag zu überwachen.
2.2 Pulverauftragsystem
Das Pulverauftragsystem ist das Kernstück der Kabine und umfasst:
- Pulverpistolen: Diese sprühen das Pulver auf die Werkstücke und laden es elektrostatisch auf, sodass es an der Metalloberfläche haftet. Pulversprühpistolen gibt es als manuelle und automatische Varianten.
- Steuerung der Pulvermenge: Die Menge des aufgetragenen Pulvers wird präzise reguliert, um eine gleichmäßige Schichtdicke zu gewährleisten und Material zu sparen.
- Automatische Applikationssysteme: Moderne Kabinen sind häufig mit Robotern oder automatisierten Systemen ausgestattet, die den Pulverauftrag gleichmäßig und konsistent ausführen.
2.3 Luftführungssystem und Filtersystem
Um das überschüssige Pulver abzuführen und eine saubere Luftzirkulation zu gewährleisten, ist die Kabine mit einem Luftführungssystem und Filtersystem ausgestattet.
- Absaugsystem: Ein leistungsstarkes Absaugsystem zieht überschüssiges Pulver und Partikel aus der Luft und leitet sie in das Filtersystem weiter.
- Filtermodule: HEPA-Filter oder spezielle Patronenfilter fangen die Pulverpartikel auf, bevor die Luft in die Kabine zurückgeführt wird. Diese Filter müssen regelmäßig gewartet und ausgetauscht werden.
- Luftzirkulation: Ein kontrolliertes Luftzirkulationssystem sorgt dafür, dass die Luft gleichmäßig durch die Kabine strömt und das Pulver effizient aufgefangen wird.
2.4 Pulverrückgewinnungssystem
Ein wesentlicher Bestandteil moderner Pulverbeschichtungskabinen ist das Rückgewinnungssystem, das überschüssiges Pulver aufnimmt und zur Wiederverwendung aufbereitet.
- Auffangbehälter: Der Boden der Kabine ist so gestaltet, dass überschüssiges Pulver automatisch in Auffangbehälter geleitet wird.
- Recyclingmodul: Das aufgefangene Pulver wird in einem speziellen Modul gefiltert und von Verunreinigungen befreit, bevor es erneut in das Pulverauftragssystem eingespeist wird.
- Pulverförderung: Das aufbereitete Pulver wird durch ein Fördersystem zurück zur Sprühpistole transportiert, um eine nahtlose Wiederverwendung zu ermöglichen.
3. Funktionsweise der Pulverbeschichtungskabine
Der Beschichtungsprozess in der Pulverkabine folgt einem klar strukturierten Ablauf, der die Qualität und Effizienz der Beschichtung maximiert.
3.1 Pulverauftrag und elektrostatische Aufladung
- Elektrostatische Aufladung: Die Pulversprühpistolen laden das Pulver elektrostatisch auf, sodass es sich gleichmäßig auf der Werkstückoberfläche verteilt und daran haftet. Metallische Werkstücke sind leitfähig, was die elektrostatische Anziehung unterstützt.
- Auftrag des Pulvers: Das Pulver wird über die Sprühpistolen aufgetragen, die entweder manuell oder automatisiert betrieben werden. Der Bediener oder das Automationssystem passt die Geschwindigkeit und den Winkel des Sprühvorgangs an, um eine gleichmäßige Schichtdicke zu erzielen.
3.2 Überschüssiges Pulver und Rückgewinnung
- Auffangen von Pulver: Überschüssiges Pulver, das die Werkstücke nicht erreicht, wird sofort vom Absaugsystem aufgenommen.
- Filterung und Recycling: Das Pulver wird in Filteranlagen von Partikeln und Verunreinigungen befreit und dem Pulverauftragssystem erneut zugeführt. Durch diese Rückgewinnung wird Material gespart und die Umweltbelastung reduziert.
3.3 Abluftreinigung und Luftzirkulation
- Filtrierung der Luft: Die Luft, die durch die Kabine strömt, wird durch HEPA- oder Patronenfilter gereinigt. Pulverpartikel, die nicht zur Wiederverwendung geeignet sind, werden in speziellen Behältern gesammelt.
- Gereinigte Luft: Die gefilterte Luft wird entweder in den Raum zurückgeführt oder kontrolliert abgelassen, um die Kabine und die Umgebung sauber und sicher zu halten.
4. Steuerung und Automatisierung der Pulverbeschichtungskabine
Moderne Pulverbeschichtungskabinen verfügen über automatisierte Steuerungssysteme, die den Prozess präzise regeln und optimieren.
- Intelligente Steuerungssysteme: Mit Sensoren und Steuergeräten kann der gesamte Prozess überwacht werden, von der Pulvermenge und Sprühgeschwindigkeit bis hin zur Luftzirkulation und Rückgewinnung.
- Programmierbare Roboter: Automatisierte Roboter können Werkstücke in gleichmäßiger Qualität und Geschwindigkeit beschichten, was besonders für Serienproduktionen vorteilhaft ist.
- Farbschnellwechsel-Systeme: Bei der Verarbeitung mehrerer Farben können Farbschnellwechsel-Systeme den Farbwechsel automatisieren und damit die Produktionszeit reduzieren.
5. Wartung und Reinigung der Pulverbeschichtungskabine
Um die Effizienz und Lebensdauer der Pulverbeschichtungskabine zu gewährleisten, sind regelmäßige Wartungs- und Reinigungsmaßnahmen erforderlich.
- Filterwechsel und -reinigung: Die Filtermodule müssen regelmäßig gereinigt oder ausgetauscht werden, um eine optimale Luftzirkulation und Pulverrückgewinnung zu gewährleisten.
- Pulverleitungen und Sprühpistolen: Pulverleitungen und Sprühpistolen sollten regelmäßig gereinigt werden, um Verstopfungen und Pulveransammlungen zu vermeiden.
- Sicherheitsprüfungen: Regelmäßige Sicherheitsinspektionen sind notwendig, um sicherzustellen, dass die Kabine in einwandfreiem Zustand ist und die Sicherheitsstandards einhält.
6. Nachhaltigkeit und Umweltaspekte in der Pulverbeschichtungskabine
Moderne Pulverbeschichtungskabinen tragen maßgeblich zur Umweltfreundlichkeit des Beschichtungsprozesses bei:
- Effiziente Pulverrückgewinnung: Durch die Wiederverwendung des Pulvers wird der Materialverbrauch erheblich reduziert.
- Geringe Emissionen: Die Kabinen arbeiten ohne flüchtige organische Verbindungen (VOCs) und belasten die Umwelt daher weniger als herkömmliche Nasslackierungen.
- Energieeffizienz: Fortschrittliche Kabinentechnologien mit optimierten Luftzirkulations- und Filtersystemen senken den Energieverbrauch und tragen zur Nachhaltigkeit des gesamten Prozesses bei.
7. Innovationen und Zukunftstrends in der Pulverbeschichtungskabine
Die Technologie der Pulverbeschichtungskabinen entwickelt sich ständig weiter, um höhere Effizienz und bessere Qualität zu erreichen. Zu den aktuellen Innovationen gehören:
- KI-gesteuerte Prozessoptimierung: Künstliche Intelligenz wird zunehmend eingesetzt, um Parameter wie Luftzirkulation, Pulvermenge und Sprühwinkel in Echtzeit anzupassen und so die Beschichtungsqualität zu optimieren.
- Smart-Sensor-Technologie: Sensoren überwachen die Pulverdichte, Luftqualität und Temperatur in der Kabine und passen die Bedingungen an, um eine konstante Beschichtungsqualität sicherzustellen.
- Robotik und Automatisierung: Robotertechnologie ermöglicht es, komplexe Geometrien mit hoher Präzision zu beschichten und sorgt für eine einheitliche Schichtdicke und hohe Produktivität.
- Farbschnellwechsel-Systeme der nächsten Generation: Neue Systeme bieten noch schnellere Farbwechselmöglichkeiten und reduzieren die Stillstandzeiten, was die Produktivität in Mehrfarbenprozessen erhöht.
Fazit
Die Pulverbeschichtungskabine ist ein unverzichtbarer Bestandteil moderner Beschichtungsprozesse und entscheidend für die Qualität, Effizienz und Nachhaltigkeit der Pulverbeschichtung. Mit fortschrittlichen Technologien zur Pulverauftragung, Rückgewinnung, Luftreinigung und Automatisierung bieten heutige Kabinen eine zuverlässige und umweltfreundliche Lösung für verschiedenste Branchen. Innovationen wie KI-gesteuerte Steuerung, intelligente Sensorik und Robotik tragen dazu bei, die Pulverbeschichtung noch präziser, effizienter und wirtschaftlicher zu gestalten. Die Pulverbeschichtungskabine bleibt somit eine zentrale Komponente für hochwertige und nachhaltige Beschichtungsverfahren.
Aufbau, Funktionsweise und Innovationen für eine optimale Pulverbeschichtung
Die Pulverbeschichtung ist ein hochmodernes Verfahren zur Oberflächenveredelung, das in zahlreichen Industrien verwendet wird, darunter die Automobilindustrie, der Maschinenbau, die Möbelbranche und die Bauindustrie. Sie bietet eine strapazierfähige, umweltfreundliche und ästhetisch ansprechende Oberflächenbeschichtung, die sowohl vor Korrosion schützt als auch verschiedene Designanforderungen erfüllt. Die Qualität der Pulverbeschichtung hängt stark von der Technologie der Anlage, den einzelnen Prozessschritten und den verwendeten Materialien ab.
In diesem Leitfaden wird die Pulverbeschichtung im Detail erläutert – von Aufbau und Funktionsweise einer typischen Pulverbeschichtungsanlage bis hin zu aktuellen Innovationen, die Effizienz und Qualität weiter steigern.
1. Aufbau einer Pulverbeschichtungsanlage
Eine typische Pulverbeschichtungsanlage besteht aus verschiedenen Komponenten, die aufeinander abgestimmt sind, um den Beschichtungsprozess effizient und präzise durchzuführen.
1.1 Vorbehandlungseinheit
Die Vorbehandlung ist ein entscheidender Schritt, der die Oberfläche des Werkstücks auf die Pulverbeschichtung vorbereitet. Sie umfasst Reinigung, Entfettung, Entrostung und gegebenenfalls eine Konversionsbeschichtung wie die Phosphatierung.
- Reinigungs- und Entfettungseinheit: Diese Einheit entfernt Fette, Öle und andere Verunreinigungen, die die Haftung der Pulverschicht beeinträchtigen könnten.
- Oxidentfernung und Phosphatierung: Für Metalle wie Stahl und Aluminium wird oft eine Phosphatierung oder eine alternative Konversionsschicht aufgetragen, die die Haftung verbessert und Korrosionsschutz bietet.
1.2 Trocknungsofen
Nach der Vorbehandlung müssen die Werkstücke gründlich getrocknet werden, da Restfeuchtigkeit die Haftung der Pulverbeschichtung beeinträchtigen könnte.
- Umluft- oder Infrarottrockner: Abhängig vom Material und der Größe des Werkstücks wird die Trocknung mit einem Umlufttrockner oder einer energieeffizienten Infrarottrocknung durchgeführt.
- Feuchtigkeitsüberwachung: Sensoren überwachen die Restfeuchtigkeit und passen die Temperatur automatisch an, um eine gleichmäßige Trocknung sicherzustellen.
1.3 Pulverbeschichtungskabine
Die Pulverbeschichtungskabine ist das Herzstück der Anlage, in der das Pulver elektrostatisch aufgeladen und auf die Werkstücke aufgesprüht wird.
- Pulverauftragsysteme: Die Pulversprühpistolen laden das Pulver elektrostatisch auf und sorgen dafür, dass es gleichmäßig auf der Oberfläche haftet.
- Rückgewinnungssystem: Überschüssiges Pulver wird im Rückgewinnungssystem aufgefangen, gefiltert und zur Wiederverwendung aufbereitet.
- Luftfiltersystem: Patronenfilter oder HEPA-Filter fangen Staubpartikel auf und halten die Luft in der Kabine sauber, was die Effizienz der Beschichtung steigert.
1.4 Einbrennofen
Im Einbrennofen wird das Pulver bei hohen Temperaturen (zwischen 160°C und 220°C) geschmolzen und zu einer widerstandsfähigen Schicht gehärtet.
- Temperaturkontrolle: Eine exakte Temperatursteuerung ist wichtig, um die Pulverschicht gleichmäßig zu härten und eine optimale Oberfläche zu erzeugen.
- Luftzirkulation: Ein kontrolliertes Luftzirkulationssystem sorgt dafür, dass die Temperatur im gesamten Ofen gleichmäßig verteilt wird.
1.5 Abkühlzone
Nach dem Einbrennvorgang wird das Werkstück in einer kontrollierten Abkühlzone gleichmäßig heruntergekühlt, um Spannungen und Defekte zu vermeiden.
- Luftkühlung oder wassergekühlte Systeme: Abhängig von den Anforderungen kann die Abkühlung durch Luftzirkulation oder wassergekühlte Systeme erfolgen.
2. Funktionsweise des Pulverbeschichtungsprozesses
Der Pulverbeschichtungsprozess folgt einem systematischen Ablauf, der die hohe Qualität und Haltbarkeit der Beschichtung gewährleistet.
2.1 Vorbehandlung und Reinigung
Eine gründliche Vorbehandlung sorgt für eine saubere, haftfähige Oberfläche:
- Entfettung und Entrostung: Fette, Öle, Rost und andere Verunreinigungen werden vollständig entfernt, damit das Pulver an der Oberfläche haftet.
- Konversionsbeschichtung: Eine Phosphatschicht oder eine alternative Konversionsschicht fördert die Haftung und bietet zusätzlichen Korrosionsschutz.
2.2 Auftragen des Pulvers
In der Pulverbeschichtungskabine wird das Pulver elektrostatisch auf die Werkstücke gesprüht:
- Elektrostatische Aufladung: Die Pulversprühpistolen laden das Pulver auf, wodurch es gleichmäßig auf der metallischen Oberfläche haftet.
- Pulverauftrag: Das Pulver verteilt sich gleichmäßig auf der Oberfläche. Durch die elektrostatische Anziehung bleibt es haften, bis es im Ofen gehärtet wird.
2.3 Einbrennen der Pulverschicht
Im Einbrennofen wird das Pulver durch hohe Temperaturen zu einer widerstandsfähigen und gleichmäßigen Schicht verschmolzen:
- Schmelzen und Aushärten: Das Pulver schmilzt und verbindet sich zu einer homogenen Schicht, die eine hohe Festigkeit und Widerstandsfähigkeit bietet.
- Exakte Temperatursteuerung: Die Temperatur und Dauer des Einbrennens werden präzise überwacht und angepasst, um eine hochwertige Oberfläche zu gewährleisten.
2.4 Abkühlen und Inspektion
Nach dem Einbrennen wird das Werkstück in der Abkühlzone kontrolliert heruntergekühlt und auf Qualität geprüft:
- Qualitätskontrolle: Die Schichtdicke, Haftung und das optische Erscheinungsbild werden überprüft, um sicherzustellen, dass die Beschichtung den Anforderungen entspricht.
3. Innovationen in der Pulverbeschichtungstechnologie
Die Pulverbeschichtungstechnologie entwickelt sich kontinuierlich weiter, um höhere Effizienz, verbesserte Qualität und eine umweltfreundlichere Produktion zu ermöglichen. Zu den wichtigsten Innovationen gehören:
3.1 Automatisierung und Robotik
Moderne Pulverbeschichtungsanlagen setzen zunehmend auf Automatisierung und Robotik:
- Automatische Beschichtungsroboter: Roboterarme, die präzise Pulver auftragen und sich an verschiedene Werkstückgeometrien anpassen können, sorgen für eine gleichbleibende Beschichtungsqualität.
- Programmierbare Steuerung: Automatisierte Systeme ermöglichen die Anpassung der Parameter an unterschiedliche Werkstücke und Materialien und erhöhen die Produktionsflexibilität.
3.2 Effiziente Pulversysteme und Farbschnellwechsel-Technologien
Die Weiterentwicklung der Pulversysteme steigert die Effizienz und ermöglicht einen schnellen Farbwechsel:
- Pulverrückgewinnungssysteme: Überschüssiges Pulver wird in der Kabine aufgefangen, gefiltert und erneut verwendet, wodurch der Materialverbrauch gesenkt und Kosten reduziert werden.
- Farbschnellwechsel-Systeme: Durch spezielle Kabinensysteme und Fördertechniken kann der Farbwechsel in wenigen Minuten durchgeführt werden, was die Flexibilität in der Produktion erhöht.
3.3 Künstliche Intelligenz und Sensorik
Der Einsatz von Künstlicher Intelligenz (KI) und Sensorik ermöglicht eine präzise Steuerung und Anpassung der Prozessparameter in Echtzeit:
- KI-gestützte Prozessoptimierung: KI-Algorithmen analysieren die Beschichtungsparameter und optimieren den Pulverauftrag, um Material zu sparen und gleichbleibend hohe Qualität zu gewährleisten.
- Sensorüberwachung: Intelligente Sensoren überwachen die Pulverdichte, Luftzirkulation und Temperatur und passen diese Parameter automatisch an, um optimale Bedingungen zu gewährleisten.
3.4 Umweltfreundliche Materialien und energiesparende Verfahren
Innovationen im Bereich umweltfreundlicher Materialien und energieeffizienter Technologien tragen dazu bei, die Pulverbeschichtung nachhaltiger zu gestalten:
- Pulver mit niedrigeren Aushärtetemperaturen: Neu entwickelte Pulver können bei niedrigeren Temperaturen gehärtet werden, was den Energieverbrauch senkt und die Umweltbelastung reduziert.
- Energieeffiziente Trocknung und Einbrenntechnologien: Moderne Infrarot- und Mikrowellentechnologien ermöglichen eine schnelle, gezielte Erwärmung und sparen Energie im Vergleich zu herkömmlichen Verfahren.
3.5 Digitalisierung und Industrie 4.0
Die digitale Vernetzung und Datenerfassung in der Produktion ermöglicht die Integration der Pulverbeschichtung in Industrie-4.0-Systeme:
- Digitalisierte Prozessüberwachung: Echtzeitdaten aus dem Beschichtungsprozess werden erfasst und analysiert, um Fehler zu erkennen und den Produktionsablauf zu optimieren.
- Vernetzte Anlagen: Pulverbeschichtungsanlagen, die mit anderen Produktionssystemen vernetzt sind, verbessern den Informationsfluss und steigern die Effizienz in der gesamten Fertigung.
4. Nachhaltigkeit und Umweltaspekte der Pulverbeschichtung
Die Pulverbeschichtung ist ein umweltfreundliches Verfahren, da sie im Vergleich zur Nasslackierung keine flüchtigen organischen Verbindungen (VOCs) freisetzt und weniger Abfall produziert. Weitere Maßnahmen tragen zur Nachhaltigkeit der Pulverbeschichtung bei:
- Pulverrückgewinnung: Das überschüssige Pulver wird aufgefangen und wiederverwendet, was den Materialverbrauch reduziert und die Umweltbelastung senkt.
- Energiesparende Prozesse: Durch die Nutzung energiesparender Technologien wie Infrarot- und Mikrowellenheizung wird der Energieverbrauch gesenkt.
- Nachhaltige Beschichtungsmaterialien: Umweltfreundliche Pulverformulierungen, die bei niedrigeren Temperaturen gehärtet werden, tragen zu einer ressourcenschonenden Produktion bei.
Fazit
Die Pulverbeschichtung ist eine vielseitige und wirtschaftliche Methode zur Oberflächenveredelung, die sich durch Langlebigkeit, Ästhetik und Umweltfreundlichkeit auszeichnet. Der Erfolg des Pulverbeschichtungsprozesses hängt jedoch stark von der Qualität der Anlage und den Prozessparametern ab. Durch den Einsatz innovativer Technologien wie Automatisierung, KI-gestützte Steuerung, energiesparende Verfahren und nachhaltige Materialien wird die Pulverbeschichtung kontinuierlich optimiert. Mit diesen Fortschritten wird die Pulverbeschichtung auch in Zukunft eine bedeutende Rolle in der industriellen Fertigung spielen und noch umweltfreundlicher, effizienter und flexibler gestaltet.
Die Bedeutung der Pulverbeschichtungskabine im Beschichtungsprozess – Effizienz, Qualität und Nachhaltigkeit
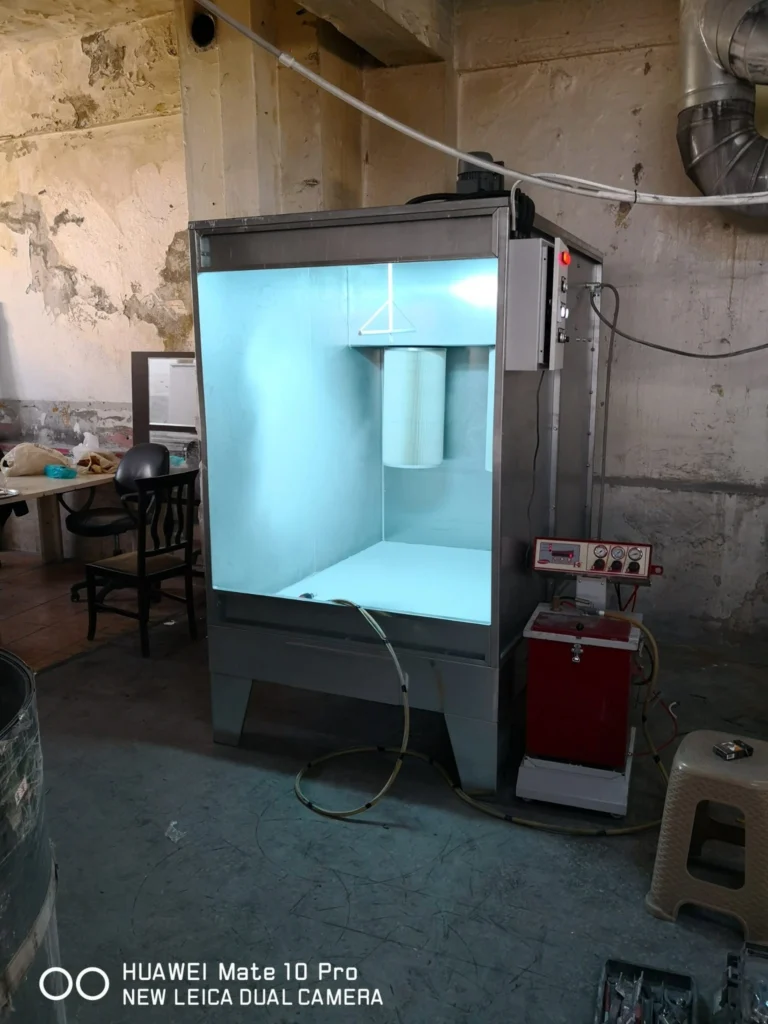
Die Pulverbeschichtungskabine ist das zentrale Element einer Pulverbeschichtungsanlage und spielt eine entscheidende Rolle für die Effizienz, Qualität und Nachhaltigkeit des gesamten Beschichtungsprozesses. In der Kabine wird das Beschichtungspulver elektrostatisch aufgeladen und auf die Werkstücke gesprüht. Die Kabine sorgt für eine präzise, gleichmäßige Beschichtung und ermöglicht die Rückgewinnung von überschüssigem Pulver, wodurch Materialkosten gesenkt und die Umwelt geschont werden.
Dieser umfassende Überblick beschreibt die wesentlichen Funktionen und Vorteile der Pulverbeschichtungskabine, ihre technischen Anforderungen sowie innovative Technologien, die die Qualität und Effizienz des Beschichtungsprozesses steigern.
1. Rolle der Pulverbeschichtungskabine im Beschichtungsprozess
Die Pulverbeschichtungskabine stellt sicher, dass das Beschichtungspulver gleichmäßig und haftfest auf die Werkstücke aufgetragen wird. Ihre Hauptaufgaben umfassen:
- Präziser Pulverauftrag: Die Kabine ermöglicht es, dass das Pulver elektrostatisch aufgeladen und gleichmäßig auf die Werkstücke gesprüht wird.
- Einhaltung von Umwelt- und Sicherheitsstandards: Die Kabine schützt die Arbeitsumgebung vor freigesetztem Pulver und filtert die Luft, um die Belastung für das Personal und die Umwelt zu reduzieren.
- Rückgewinnung von überschüssigem Pulver: Moderne Pulverbeschichtungskabinen sind mit Rückgewinnungssystemen ausgestattet, die das überschüssige Pulver auffangen und zur Wiederverwendung aufbereiten.
2. Aufbau und Komponenten der Pulverbeschichtungskabine
Eine Pulverbeschichtungskabine besteht aus verschiedenen technischen Komponenten, die zusammenarbeiten, um eine hohe Beschichtungsqualität zu gewährleisten.
2.1 Kabinenstruktur und Gehäuse
Die Struktur und das Gehäuse der Kabine sorgen dafür, dass Pulverrückstände in der Kabine bleiben und die Umwelt vor dem Pulver geschützt wird.
- Kabinenwände und Boden: Die Wände und der Boden der Kabine sind meist aus Stahl oder speziellem Kunststoff gefertigt, der Pulverrückstände zurückhält und leicht zu reinigen ist.
- Beleuchtung: Eine gleichmäßige und blendfreie Beleuchtung ist erforderlich, um die Sichtbarkeit der Werkstücke zu verbessern und eine präzise Kontrolle des Pulverauftrags zu ermöglichen.
- Boden- und Deckensysteme: Die Kabine verfügt oft über spezielle Auffangbehälter am Boden, um überschüssiges Pulver aufzunehmen und zum Rückgewinnungssystem zu leiten.
2.2 Pulverauftragsysteme
Das Pulverauftragsystem umfasst die Pulversprühpistolen und die Steuerung der Pulvermenge.
- Pulversprühpistolen: Die Pistolen laden das Pulver elektrostatisch auf und sprühen es auf die Werkstücke. Sie sind das Herzstück des Auftragsystems und können manuell oder automatisch betrieben werden.
- Automatisierte Systeme: In modernen Anlagen kommen Roboter oder andere automatisierte Systeme zum Einsatz, die das Pulver gleichmäßig auftragen und eine einheitliche Schichtdicke sicherstellen.
2.3 Filtersystem und Luftführung
Filtersysteme und eine kontrollierte Luftführung sorgen dafür, dass das überschüssige Pulver effizient entfernt und die Luft in der Kabine gereinigt wird.
- Absaugsystem: Ein leistungsstarkes Absaugsystem zieht überschüssiges Pulver und Partikel ab und leitet sie zum Filtersystem.
- Filtermodule: HEPA- oder Patronenfilter fangen die Pulverpartikel auf und verhindern, dass Staub in die Umgebung gelangt. Die Filter müssen regelmäßig gewartet und gewechselt werden.
- Luftzirkulationssystem: Das Luftzirkulationssystem sorgt für eine gleichmäßige Strömung, die das Pulver gleichmäßig verteilt und Ablagerungen verhindert.
2.4 Pulverrückgewinnungssystem
Ein Rückgewinnungssystem ist ein wesentlicher Bestandteil moderner Kabinen und trägt zur Reduzierung des Pulververbrauchs bei.
- Auffangsystem für überschüssiges Pulver: Das überschüssige Pulver, das die Werkstücke nicht erreicht, wird vom Boden und den Wänden aufgefangen.
- Recyclingmodul: Das aufgesammelte Pulver wird gefiltert und in das Pulversystem zurückgeführt, sodass es erneut verwendet werden kann.
3. Funktionsweise der Pulverbeschichtungskabine
Die Pulverbeschichtungskabine erfüllt mehrere wesentliche Funktionen im Beschichtungsprozess.
3.1 Elektrostatische Aufladung und Pulverauftrag
In der Kabine wird das Pulver elektrostatisch aufgeladen und dann auf die Werkstücke gesprüht.
- Elektrostatische Aufladung: Die Pulversprühpistolen laden das Pulver auf, sodass es durch elektrostatische Anziehung gleichmäßig auf den Werkstücken haftet.
- Auftrag des Pulvers: Die Pistolen tragen das Pulver präzise auf, indem sie Winkel und Sprühweite steuern, um eine gleichmäßige Schichtdicke zu erreichen.
3.2 Pulverrückgewinnung und Recycling
Das Rückgewinnungssystem sorgt dafür, dass überschüssiges Pulver wiederverwendet wird.
- Auffangen des Pulvers: Pulver, das die Werkstücke nicht erreicht, wird sofort durch das Absaugsystem aufgefangen.
- Filtrierung und Recycling: Das überschüssige Pulver wird gefiltert, um Verunreinigungen zu entfernen, und in das Pulverauftragsystem zurückgeführt.
3.3 Luftreinigung und Filtrierung
Die Luftreinigung in der Kabine verhindert die Freisetzung von Staub und Pulverpartikeln in die Umgebung.
- Filtersystem: Die Luft, die aus der Kabine abgeführt wird, wird durch Patronen- oder HEPA-Filter gereinigt. Diese Filter entfernen Pulverpartikel und Staub und verhindern, dass sie in die Umgebung gelangen.
- Gereinigte Luft: Nach der Filtration wird die gereinigte Luft wieder in die Kabine oder in die Umgebung zurückgeführt.
4. Steuerung und Automatisierung der Kabine
Moderne Pulverbeschichtungskabinen verfügen über fortschrittliche Steuerungssysteme, die die Effizienz und Präzision des Beschichtungsprozesses erhöhen.
- Intelligente Steuerungssysteme: Automatisierte Steuerungen regeln die Pulvermenge, Sprühgeschwindigkeit und Luftzirkulation, um eine gleichmäßige Beschichtung zu gewährleisten.
- Automatisierte Beschichtungsroboter: Roboterarme tragen das Pulver gleichmäßig auf, was besonders für Werkstücke mit komplexer Geometrie vorteilhaft ist.
- Sensorik und Echtzeitüberwachung: Sensoren überwachen die Luftqualität, Pulvermenge und Schichtdicke und passen die Parameter in Echtzeit an, um die Effizienz zu maximieren.
5. Vorteile der Pulverbeschichtungskabine
Die Verwendung einer Pulverbeschichtungskabine bietet zahlreiche Vorteile:
- Hohe Effizienz: Durch die Rückgewinnung und Wiederverwendung des Pulvers wird der Materialverbrauch minimiert und die Kosten gesenkt.
- Umweltfreundlichkeit: Da die Kabine das Pulver zurückhält und recycelt, wird die Emission von Schadstoffen in die Umwelt reduziert.
- Verbesserte Qualität: Eine gleichmäßige Beschichtung ohne Defekte ist leichter zu erreichen, da die Kabine die Bedingungen für den Pulverauftrag optimiert.
- Flexibilität und Anpassungsfähigkeit: Dank moderner Automatisierungssysteme können unterschiedliche Werkstücke beschichtet und schnelle Farbwechsel durchgeführt werden.
6. Innovationen in der Pulverbeschichtungskabinentechnologie
Technologische Fortschritte verbessern die Effizienz und Qualität der Pulverbeschichtungskabine und tragen zur Nachhaltigkeit des Prozesses bei.
6.1 Automatisierung und Robotik
- Robotergestützte Beschichtung: Roboterarme können komplexe Werkstücke gleichmäßig beschichten und verbessern die Produktivität in Serienproduktionen.
- Automatisierte Farbwechsel: Farbwechsel-Systeme ermöglichen es, Farben in kurzer Zeit zu wechseln, ohne die Kabine gründlich reinigen zu müssen.
6.2 Effiziente Pulverrückgewinnungssysteme
- Optimierte Filtertechnologie: Neue Filtertechnologien verbessern die Pulverrückgewinnung und filtern kleinere Partikel, was die Qualität des recycelten Pulvers steigert.
- Pulverrückführsysteme: Systeme zur automatischen Rückführung des aufgefangenen Pulvers direkt in das Pulversystem sparen Zeit und reduzieren Abfall.
6.3 Intelligente Sensorik und Künstliche Intelligenz (KI)
- KI-gestützte Steuerung: KI-Technologien analysieren den Pulverauftrag und optimieren die Parameter automatisch, um Material zu sparen und gleichbleibend hohe Qualität zu gewährleisten.
- Echtzeitüberwachung: Sensoren messen den Feuchtigkeits- und Partikelgehalt in der Kabine, um optimale Bedingungen zu gewährleisten.
6.4 Energieeffizienz und Umweltaspekte
- Energieoptimierte Kabinensysteme: Fortschrittliche Technologien zur Temperatur- und Luftzirkulationssteuerung tragen zur Senkung des Energieverbrauchs bei.
- Nachhaltige Materialien: Umweltfreundliche Pulverbeschichtungen mit niedrigeren Härtetemperaturen ermöglichen eine energieeffiziente Verarbeitung.
7. Zukunft der Pulverbeschichtungskabine
Mit weiteren technologischen Entwicklungen wird die Pulverbeschichtungskabine zunehmend präziser, energieeffizienter und flexibler.
- Verwendung smarter Sensoren und IoT: Vernetzte Sensoren und das Internet der Dinge (IoT) verbessern die Datenanalyse und ermöglichen eine umfassende Steuerung des gesamten Pulverbeschichtungsprozesses.
- KI-gestützte Optimierungen: Zukünftige Kabinen könnten vollständig von KI-Systemen gesteuert werden, die automatisch die beste Strategie für jeden Auftrag entwickeln.
- Größere Umweltfreundlichkeit: Neue Materialien und Verfahren werden die Umweltbelastung weiter reduzieren und die Pulverbeschichtung zu einer noch nachhaltigeren Methode machen.
Fazit
Die Pulverbeschichtungskabine ist das zentrale Element im Beschichtungsprozess und trägt maßgeblich zur Qualität, Effizienz und Nachhaltigkeit der Pulverbeschichtung bei. Mit innovativen Technologien zur Rückgewinnung, Filtrierung, Automatisierung und Echtzeitsteuerung bietet die Kabine eine leistungsfähige Lösung für moderne industrielle Anforderungen. Fortschritte in der Automatisierung, künstlichen Intelligenz und energieeffizienten Technologien werden die Rolle der Pulverbeschichtungskabine in den kommenden Jahren noch bedeutender machen, da sie zu einem nachhaltigen und wirtschaftlichen Produktionsprozess beiträgt.
Aufbau der Pulverbeschichtungskabine – Komponenten, Funktionen und technische Anforderungen
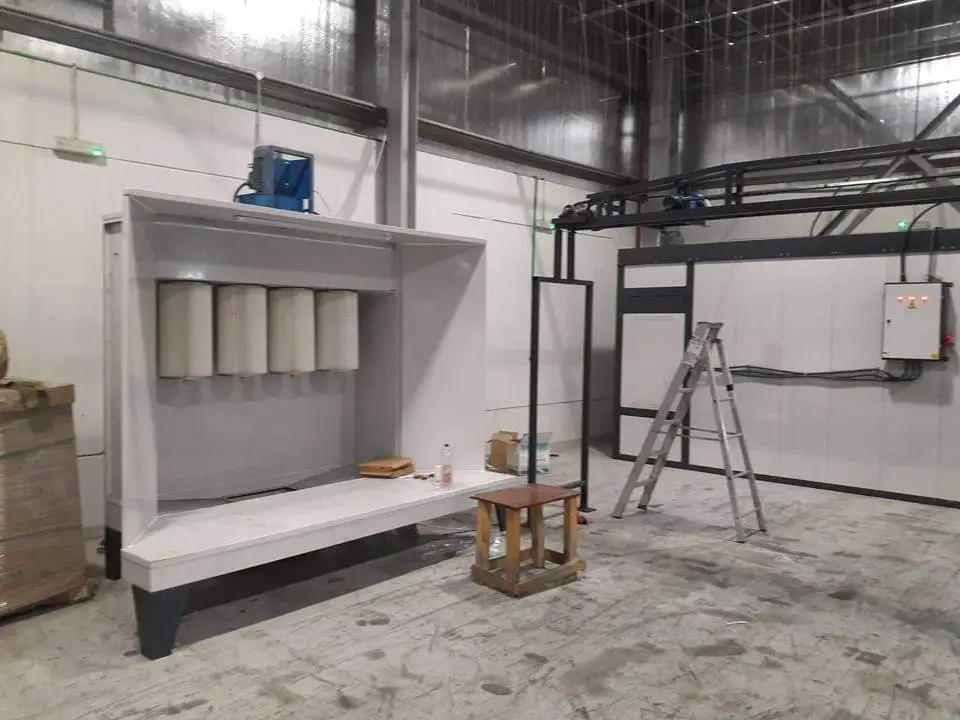
Die Pulverbeschichtungskabine ist das Herzstück einer Pulverbeschichtungsanlage. Sie ermöglicht das präzise und kontrollierte Auftragen von Pulverlacken auf Werkstücke und sorgt dafür, dass überschüssiges Pulver effizient aufgefangen und recycelt wird. Eine gut konstruierte Kabine trägt zur Qualität, Nachhaltigkeit und Effizienz des gesamten Beschichtungsprozesses bei. Der Aufbau der Kabine ist komplex und umfasst mehrere funktionale Komponenten, die zusammenarbeiten, um eine gleichmäßige und umweltfreundliche Pulverbeschichtung zu gewährleisten.
Dieser Leitfaden beschreibt die wichtigsten Bauteile und die technische Struktur einer Pulverbeschichtungskabine, ihre Funktionen und ihre Rolle im Beschichtungsprozess.
1. Gehäuse und Struktur der Kabine
Das Gehäuse und die strukturelle Gestaltung der Kabine sind für den sicheren und sauberen Betrieb entscheidend. Das Gehäuse schützt den Arbeitsbereich vor der Ausbreitung von Pulver und ermöglicht eine kontrollierte Luftzirkulation.
1.1 Kabinenwände und Boden
Die Wände und der Boden der Kabine bestehen meist aus robustem Metall oder Kunststoff, das leicht zu reinigen ist und Pulverpartikel effektiv zurückhält.
- Kabinenwände: Die Wände sind glatt und aus nicht haftenden Materialien gefertigt, um das Anhaften von Pulver zu vermeiden und die Reinigung zu erleichtern.
- Boden: Der Boden ist meist geneigt oder speziell geformt, um überschüssiges Pulver in Richtung der Pulverrückgewinnungseinheit zu leiten.
1.2 Zugang und Sichtfenster
Um den Beschichtungsprozess zu überwachen und bei Bedarf einzugreifen, verfügt die Kabine über Zugangsmöglichkeiten und transparente Sichtfenster.
- Türsysteme: Die Kabine ist mit Schiebetüren oder Klapptüren ausgestattet, die es ermöglichen, Werkstücke problemlos in die Kabine zu bringen und herauszunehmen.
- Sichtfenster: Hochwertige Kabinen haben transparente und kratzfeste Sichtfenster, die dem Bediener eine gute Sicht auf den Beschichtungsprozess ermöglichen.
1.3 Beleuchtung
Eine gleichmäßige und blendfreie Beleuchtung ist essenziell für eine präzise Überwachung des Pulverauftrags.
- Lichtquellen: LED-Leuchten oder spezielle Beleuchtungssysteme, die außerhalb der Kabine montiert sind, beleuchten den Arbeitsbereich, um Schattenbildung zu vermeiden.
- Sicherheitsglas: Die Beleuchtung wird oft durch Sicherheitsglas geschützt, um die Leuchten vor Staub und Pulver zu schützen.
2. Pulverauftragsystem
Das Pulverauftragsystem umfasst die Pulversprühpistolen, die Aufladeeinheit und die Steuerung der Pulvermenge. Dieser Teil der Kabine ist entscheidend für die Qualität und Gleichmäßigkeit der Beschichtung.
2.1 Pulversprühpistolen
Die Sprühpistolen tragen das Pulver elektrostatisch auf die Werkstücke auf. Sie sind das zentrale Element des Auftragsystems und können manuell oder automatisiert betrieben werden.
- Manuelle Pistolen: Diese werden von einem Bediener gesteuert und sind besonders geeignet für kleinere Serien oder Werkstücke mit komplexen Geometrien.
- Automatische Pistolen: In industriellen Anwendungen sind automatische Pistolen oder Roboterarme im Einsatz, die eine gleichmäßige Schichtdicke sicherstellen.
2.2 Elektrostatische Aufladung
Um das Pulver gleichmäßig und haftfest auf der Oberfläche zu verteilen, wird es elektrostatisch aufgeladen.
- Aufladeeinheit: Eine Hochspannungsquelle erzeugt ein elektrisches Feld, das das Pulver auflädt, sodass es sich an der metallischen Oberfläche anlagert.
- Anpassung der Aufladung: Die Intensität der Aufladung kann an die Geometrie und das Material des Werkstücks angepasst werden, um eine optimale Haftung zu erreichen.
2.3 Steuerung der Pulvermenge
Die Menge des aufgetragenen Pulvers wird durch ein Steuerungssystem reguliert, um eine gleichmäßige Beschichtung zu gewährleisten.
- Regelventile und Druckregelung: Ventile und Druckregler sorgen dafür, dass die Pulvermenge konstant bleibt und keine ungleichmäßigen Schichten entstehen.
- Automatische Anpassung: Moderne Kabinen verfügen über Systeme, die den Pulverauftrag automatisch an verschiedene Werkstücke anpassen können.
3. Luftführung und Filtersystem
Das Luftführungssystem und die Filtermodule sind essenziell, um eine saubere Luftzirkulation in der Kabine aufrechtzuerhalten und überschüssiges Pulver effektiv zu entfernen.
3.1 Absaugsystem
Das Absaugsystem ist für das Auffangen von überschüssigem Pulver und die Filterung der Luft verantwortlich.
- Leistungsstarke Ventilatoren: Diese Ventilatoren sorgen für eine ständige Luftzirkulation und leiten überschüssiges Pulver in das Filtersystem.
- Luftströmungsregulierung: Die Luftströmung in der Kabine wird so eingestellt, dass das Pulver gezielt zum Filtersystem geführt wird, ohne dass es auf den Boden fällt oder sich an den Kabinenwänden absetzt.
3.2 Filtermodule
Filtermodule sind entscheidend für die Reinigung der Luft und die Rückführung sauberer Luft in die Kabine oder die Umgebung.
- HEPA-Filter und Patronenfilter: Hochleistungsfilter fangen Partikel bis in den Mikrometerbereich auf und verhindern, dass Pulver in die Arbeitsumgebung gelangt.
- Austausch und Wartung: Die Filter müssen regelmäßig gereinigt oder ausgetauscht werden, um eine gleichmäßige Luftzirkulation und hohe Filterleistung sicherzustellen.
3.3 Luftzirkulationssystem
Das Luftzirkulationssystem sorgt dafür, dass die Luft gleichmäßig durch die Kabine strömt und das Pulver effizient abgeführt wird.
- Geregelte Strömung: Die Luftströmung wird so angepasst, dass eine konstante Geschwindigkeit beibehalten wird, die verhindert, dass sich Pulver in der Kabine absetzt.
- Rückführung der gereinigten Luft: Nach der Filtration kann die gereinigte Luft zurück in die Kabine geleitet oder kontrolliert abgelassen werden, um die Kabine sauber zu halten und den Energieverbrauch zu reduzieren.
4. Pulverrückgewinnungssystem
Ein zentrales Merkmal moderner Pulverbeschichtungskabinen ist das Rückgewinnungssystem, das überschüssiges Pulver aufnimmt und zur Wiederverwendung aufbereitet.
4.1 Auffangsystem für überschüssiges Pulver
Überschüssiges Pulver, das die Werkstücke nicht erreicht, wird im Bodenbereich der Kabine aufgefangen und zur Rückgewinnung weitergeleitet.
- Auffangbehälter und Leitungen: Der Boden der Kabine ist so konstruiert, dass überschüssiges Pulver automatisch in Auffangbehälter oder Rohrleitungen geleitet wird.
- Automatisierte Pulverförderung: Fördermechanismen transportieren das Pulver zur Rückgewinnungseinheit.
4.2 Pulverrecyclingmodul
Das Pulverrecyclingmodul bereitet das überschüssige Pulver auf, indem es gefiltert und von Verunreinigungen befreit wird.
- Filterung des Pulvers: Das Pulver wird durch feine Filter geleitet, um Staub und Verunreinigungen zu entfernen, bevor es wiederverwendet wird.
- Pulverförderung: Nach der Reinigung wird das Pulver in das Auftragsystem zurückgeführt, sodass es direkt wieder auf die Werkstücke aufgetragen werden kann.
4.3 Rückführsystem
Das rückgewonnene Pulver wird über ein Rückführsystem in den Kreislauf zurückgebracht, um eine nahtlose Wiederverwendung zu ermöglichen.
- Luftdruck oder mechanische Förderung: Das gereinigte Pulver wird durch ein luft- oder mechanikgesteuertes System wieder zur Sprühpistole geführt.
- Automatische Anpassung an den Beschichtungsprozess: Das Rückführsystem ist so programmiert, dass es nur die benötigte Pulvermenge zurückleitet und die Schichtdicke konstant hält.
5. Steuerung und Automatisierung
Moderne Pulverbeschichtungskabinen sind häufig mit automatisierten Steuerungssystemen ausgestattet, die eine präzise Kontrolle der Beschichtungsparameter ermöglichen.
5.1 Intelligente Steuerungssysteme
Automatisierte Steuerungen sorgen dafür, dass alle Prozesse der Kabine reibungslos ablaufen und konstant überwacht werden.
- Echtzeitüberwachung: Sensoren erfassen Parameter wie Pulvermenge, Sprühwinkel, Luftdruck und Luftqualität und passen sie automatisch an.
- Programmierbare Steuerung: Die Steuerung kann an verschiedene Werkstücke angepasst werden, um Effizienz und Flexibilität in der Produktion zu erhöhen.
5.2 Automatische Beschichtungsroboter
Roboterarme können an der Kabine installiert werden, um den Pulverauftrag gleichmäßig und präzise durchzuführen.
- Flexible Bewegungsmuster: Roboter können sich an verschiedene Geometrien anpassen und Werkstücke aus verschiedenen Winkeln beschichten.
- Verbesserte Produktivität: Die Roboter erhöhen die Geschwindigkeit und Präzision des Pulverauftrags, was die Produktionszeit reduziert.
5.3 Farbschnellwechsel-Systeme
Für den Mehrfarbenbetrieb bieten moderne Kabinen Farbschnellwechsel-Systeme, die eine effiziente und schnelle Reinigung der Kabine ermöglichen.
- Automatischer Farbwechsel: Systeme zum automatischen Farbwechsel ermöglichen es, die Farbe in kürzester Zeit zu wechseln, ohne den gesamten Betrieb anzuhalten.
- Minimierung von Farbkontamination: Farbschnellwechsel-Systeme reduzieren Farbverunreinigungen und verbessern die Effizienz bei Produktionen, die mehrere Farbschichten erfordern.
6. Reinigung und Wartung der Kabine
Um die Lebensdauer und Effizienz der Kabine zu gewährleisten, sind regelmäßige Reinigungs- und Wartungsarbeiten unerlässlich.
- Reinigung der Filter und Luftkanäle: Filter müssen regelmäßig gereinigt oder ausgetauscht werden, um eine gleichbleibende Filterleistung zu gewährleisten.
- Inspektion der Pulversprühpistolen: Die Sprühpistolen müssen auf Verstopfungen und Abnutzung überprüft werden, um eine gleichmäßige Pulverabgabe sicherzustellen.
- Sicherheitsprüfungen: Regelmäßige Sicherheitsinspektionen sind notwendig, um sicherzustellen, dass die Kabine sicher arbeitet und die geltenden Standards erfüllt.
Fazit
Die Pulverbeschichtungskabine ist eine hochkomplexe Anlage, die mehrere Komponenten und Systeme integriert, um den Beschichtungsprozess effizient und umweltfreundlich zu gestalten. Von der Struktur der Kabine über das Pulverauftragsystem bis hin zu Rückgewinnung und Automatisierung spielt jeder Teil eine entscheidende Rolle für die Qualität und Nachhaltigkeit der Pulverbeschichtung. Mit modernster Technologie und automatisierten Steuerungssystemen werden Pulverbeschichtungskabinen kontinuierlich weiterentwickelt, um den Anforderungen der Industrie gerecht zu werden und die Effizienz sowie die Umweltverträglichkeit des Beschichtungsprozesses zu verbessern.
Funktionsweise der Pulverbeschichtungskabine – Schritte, Technologie und Optimierung für eine perfekte Beschichtung
Die Pulverbeschichtungskabine ist ein zentrales Element des Pulverbeschichtungsprozesses und spielt eine entscheidende Rolle bei der Qualität und Effizienz der Oberflächenbeschichtung. In der Kabine wird das Beschichtungspulver elektrostatisch aufgeladen und auf die Werkstücke gesprüht, um eine gleichmäßige, haftfeste und langlebige Beschichtung zu erzeugen. Der Funktionsprozess in der Kabine umfasst verschiedene Schritte, die zusammenarbeiten, um ein optimales Ergebnis zu erzielen und die Nachhaltigkeit des Prozesses zu fördern.
Dieser umfassende Überblick beschreibt die Funktionsweise der Pulverbeschichtungskabine im Detail, von der Vorbereitung bis zur Rückgewinnung und dem Recycling überschüssigen Pulvers.
1. Vorbereitung des Beschichtungsprozesses
Bevor das Pulver aufgetragen wird, ist es wichtig, die Werkstücke und das Pulverauftragssystem entsprechend vorzubereiten, um ein gleichmäßiges Ergebnis zu erzielen.
1.1 Reinigung und Vorbehandlung
Die Werkstücke müssen gründlich gereinigt und vorbehandelt werden, bevor sie in die Kabine kommen. Dies ist notwendig, um Verunreinigungen zu entfernen, die die Haftung des Pulvers beeinträchtigen könnten.
- Entfettung und Entrostung: Öle, Fette und Rostpartikel werden entfernt, um eine saubere und haftfähige Oberfläche zu schaffen.
- Phosphatierung oder Konversionsbeschichtung: Bei metallischen Werkstücken wird oft eine Konversionsschicht aufgetragen, die die Haftung und den Korrosionsschutz der Pulverbeschichtung verbessert.
1.2 Positionierung der Werkstücke in der Kabine
Die Werkstücke werden in die Kabine gebracht und entweder auf speziellen Halterungen positioniert oder durch Förderbänder in der Kabine bewegt. Die richtige Positionierung ist entscheidend, um sicherzustellen, dass alle Seiten gleichmäßig beschichtet werden.
- Fixierung: Werkstücke werden so fixiert, dass sie während des gesamten Beschichtungsprozesses stabil und zugänglich bleiben.
- Fördertechnik: In automatisierten Anlagen kommen Förderbänder oder Hängebahnsysteme zum Einsatz, die die Werkstücke gleichmäßig durch die Kabine transportieren.
2. Pulverauftrag und elektrostatische Aufladung
Der Hauptschritt in der Pulverbeschichtungskabine ist der präzise Auftrag des Pulvers auf die Werkstücke, der durch elektrostatische Aufladung unterstützt wird.
2.1 Elektrostatische Aufladung des Pulvers
Die elektrostatische Aufladung ist das zentrale Prinzip der Pulverbeschichtung, das für eine gleichmäßige und haftfeste Schicht sorgt.
- Pulverauftragsysteme: Pulversprühpistolen laden das Pulver elektrostatisch auf und sprühen es gleichmäßig auf die Werkstücke. Die Aufladung erfolgt durch eine Hochspannungsquelle, die zwischen der Pistole und dem Werkstück ein elektrisches Feld erzeugt.
- Anpassung der Ladungsintensität: Die Stärke der Aufladung kann an die Materialbeschaffenheit und die Geometrie der Werkstücke angepasst werden. Metallische Oberflächen, die leitfähig sind, ziehen das Pulver besonders gut an, was eine gleichmäßige Schicht ermöglicht.
2.2 Pulverauftrag durch Sprühpistolen
Die Pulversprühpistolen sind entweder manuell oder automatisch gesteuert und tragen das Pulver gleichmäßig auf die Werkstücke auf.
- Automatische Sprühpistolen: In großen Beschichtungsanlagen sind die Pistolen meist automatisiert und an Roboterarmen befestigt, um eine gleichmäßige Schichtdicke auf allen Seiten der Werkstücke zu gewährleisten.
- Steuerung des Pulverauftrags: Die Menge und der Winkel des Pulverauftrags werden präzise eingestellt, um eine gleichmäßige Schichtdicke zu erreichen und Pulververschwendung zu vermeiden.
3. Überschüssiges Pulver und Rückgewinnung
Ein wichtiges Merkmal der Pulverbeschichtungskabine ist das System zur Rückgewinnung von überschüssigem Pulver, das nicht an den Werkstücken haften bleibt.
3.1 Auffangen des überschüssigen Pulvers
Das überschüssige Pulver wird durch das Luftzirkulationssystem der Kabine aufgefangen und zur Filterung geleitet.
- Absaugsystem: Ein starkes Absaugsystem erzeugt eine kontrollierte Luftströmung, die überschüssiges Pulver in Richtung der Filteranlage lenkt.
- Rückgewinnungseinheit: Der Boden der Kabine ist so konstruiert, dass das überschüssige Pulver in Auffangbehältern gesammelt wird, um eine effiziente Rückgewinnung zu ermöglichen.
3.2 Filterung und Recycling des Pulvers
Das aufgefangene Pulver wird gefiltert, um es von Verunreinigungen zu befreien und für die Wiederverwendung aufzubereiten.
- Filtermodule: HEPA-Filter oder Patronenfilter entfernen feine Partikel und Staub aus dem Pulver, sodass es sauber bleibt und seine ursprüngliche Qualität behält.
- Rückführung des Pulvers: Nach der Filtration wird das gereinigte Pulver in das Pulversystem zurückgeführt, um es erneut aufzutragen. Dies reduziert den Materialverbrauch und die Umweltbelastung erheblich.
4. Luftführung und Filtersystem
Ein effektives Luftführungssystem ist entscheidend, um eine gleichmäßige Verteilung des Pulvers und eine saubere Arbeitsumgebung zu gewährleisten.
4.1 Luftzirkulation in der Kabine
Die Luftzirkulation muss präzise gesteuert werden, um das Pulver gleichmäßig zu verteilen und überschüssiges Pulver aufzufangen.
- Strömungssteuerung: Die Luftströmung in der Kabine wird so reguliert, dass das Pulver effizient auf die Werkstücke aufgetragen wird und überschüssiges Pulver in Richtung der Filtereinheit strömt.
- Verhinderung von Pulverablagerungen: Durch die kontrollierte Luftführung wird verhindert, dass sich Pulver auf den Kabinenwänden oder anderen Oberflächen absetzt, was die Reinigung erleichtert.
4.2 Luftreinigung und Filtration
Das Filtersystem entfernt feine Partikel und überschüssiges Pulver aus der Luft, bevor diese wieder in die Kabine oder die Umgebung geleitet wird.
- HEPA-Filter und Patronenfilter: Diese Filtertypen sind in der Lage, feine Pulverpartikel effektiv aufzufangen und eine saubere Luftzirkulation zu gewährleisten.
- Wartung und Austausch der Filter: Die Filter müssen regelmäßig gereinigt oder ausgetauscht werden, um eine hohe Filterleistung aufrechtzuerhalten und die Umweltbelastung zu minimieren.
5. Steuerung und Automatisierung der Kabine
Moderne Pulverbeschichtungskabinen sind häufig mit automatisierten Steuerungssystemen ausgestattet, die eine präzise Kontrolle des Pulverauftrags und der Luftführung ermöglichen.
5.1 Intelligente Steuerungssysteme
Steuerungssysteme überwachen den Beschichtungsprozess in Echtzeit und passen die Parameter automatisch an, um eine konstante Beschichtungsqualität zu gewährleisten.
- Sensorüberwachung: Sensoren messen den Pulverauftrag, die Luftströmung und die elektrostatische Aufladung und passen die Parameter in Echtzeit an, um eine gleichmäßige Beschichtung sicherzustellen.
- Programmierbare Steuerungen: Die Steuerungssysteme sind programmierbar und können an unterschiedliche Werkstücke und Materialien angepasst werden, was die Flexibilität und Effizienz in der Produktion steigert.
5.2 Automatisierte Robotersysteme
In modernen Anlagen kommen Roboterarme zum Einsatz, die das Pulver präzise und gleichmäßig auftragen und sich an verschiedene Werkstückformen anpassen.
- Roboterbeschichtung: Die Roboterarme sind so programmiert, dass sie gleichmäßige Bewegungen ausführen und die Schichtdicke auf allen Seiten der Werkstücke konstant halten.
- Produktionsgeschwindigkeit und Präzision: Durch die Automatisierung wird die Geschwindigkeit und Präzision des Pulverauftrags erhöht, was besonders bei hohen Stückzahlen vorteilhaft ist.
6. Vorteile der Pulverbeschichtungskabine im Beschichtungsprozess
Die Pulverbeschichtungskabine bietet zahlreiche Vorteile, die zur Effizienz, Qualität und Nachhaltigkeit des Beschichtungsprozesses beitragen.
6.1 Effiziente Pulververwendung und Kosteneinsparungen
Durch die Rückgewinnung und Wiederverwendung des überschüssigen Pulvers wird der Materialverbrauch erheblich reduziert, was die Betriebskosten senkt.
- Wiederverwendung des Pulvers: Das Rückgewinnungssystem ermöglicht eine nahtlose Wiederverwendung des Pulvers, was den Materialverbrauch minimiert.
- Kosteneffizienz: Die Wiederverwendung und präzise Steuerung der Pulvermenge senkt die Kosten und steigert die Effizienz des Prozesses.
6.2 Umweltfreundlichkeit und Sicherheit
Die Kabine schützt die Umwelt und das Bedienpersonal vor dem Einatmen von Pulverpartikeln und reduziert die Belastung durch Abfälle und Emissionen.
- Reduktion der Emissionen: Das Filtersystem fängt überschüssiges Pulver auf und verhindert, dass es in die Luft gelangt.
- Sicherheitsmaßnahmen: Durch die geschlossene Kabine und das Filtersystem wird das Personal vor schädlichen Partikeln und Staub geschützt.
6.3 Qualitätsverbesserung und Präzision
Durch die kontrollierte elektrostatische Aufladung und die präzise Steuerung des Pulverauftrags wird eine hohe Qualität der Beschichtung erreicht.
- Gleichmäßige Schichtdicke: Die automatisierte Steuerung sorgt dafür, dass die Schichtdicke konstant bleibt und keine Defekte entstehen.
- Hohe Haftung und Langlebigkeit: Die elektrostatische Aufladung verbessert die Haftung des Pulvers, wodurch die Beschichtung widerstandsfähiger und langlebiger wird.
Fazit
Die Pulverbeschichtungskabine ist ein unverzichtbarer Bestandteil im modernen Beschichtungsprozess und trägt maßgeblich zur Qualität, Effizienz und Umweltfreundlichkeit der Pulverbeschichtung bei. Ihre Funktionsweise basiert auf präzise gesteuerten Schritten – von der elektrostatischen Aufladung und dem Pulverauftrag bis hin zur Luftführung, Filterung und Rückgewinnung des Pulvers. Mit innovativen Technologien wie Automatisierung, Robotik und intelligenten Steuerungssystemen wird die Pulverbeschichtungskabine kontinuierlich weiterentwickelt, um die Produktionsanforderungen der Industrie zu erfüllen und eine umweltfreundlichere und kosteneffizientere Beschichtung zu ermöglichen.
Steuerung und Automatisierung der Pulverbeschichtungskabine – Technologien, Vorteile und Zukunftstrends
Die Steuerung und Automatisierung einer Pulverbeschichtungskabine ist ein entscheidender Aspekt, der maßgeblich zur Effizienz, Qualität und Nachhaltigkeit des Pulverbeschichtungsprozesses beiträgt. Durch automatisierte Steuerungssysteme und den Einsatz intelligenter Sensorik wird eine präzise Kontrolle der Beschichtungsparameter ermöglicht, was zu einer gleichmäßigen Schichtdicke, geringem Pulververlust und einer höheren Produktionsgeschwindigkeit führt. Die Integration moderner Automatisierungstechnik und roboterunterstützter Systeme hilft dabei, die Pulverbeschichtung noch wirtschaftlicher und umweltfreundlicher zu gestalten.
Dieser Leitfaden beschreibt die Steuerungs- und Automatisierungskomponenten der Pulverbeschichtungskabine im Detail, von den grundlegenden Funktionen über innovative Technologien bis hin zu zukünftigen Trends in der Pulverbeschichtung.
1. Bedeutung der Steuerung und Automatisierung für die Pulverbeschichtung
Automatisierte Steuerungssysteme und eine präzise Regelung der Kabinenparameter spielen eine entscheidende Rolle im Pulverbeschichtungsprozess. Sie tragen dazu bei, die Effizienz des Prozesses zu maximieren und eine hohe Beschichtungsqualität zu gewährleisten.
- Effizienzsteigerung: Automatisierte Steuerungen reduzieren die Rüstzeiten, steigern die Geschwindigkeit des Pulverauftrags und senken den Materialverbrauch.
- Qualitätskontrolle: Durch präzise Steuerung wird die Schichtdicke konstant gehalten, was Defekte und Materialverschwendung minimiert.
- Kostensenkung: Automatisierte Systeme sorgen für eine optimale Nutzung des Pulvers und verringern die Betriebskosten durch geringeren Materialverbrauch und reduzierten Arbeitsaufwand.
- Umweltfreundlichkeit: Durch die Minimierung von Materialverlusten und die Wiederverwendung von Pulver trägt die Automatisierung zur Reduzierung des Abfalls und der Emissionen bei.
2. Automatisierte Steuerungssysteme in der Pulverbeschichtungskabine
Automatisierte Steuerungssysteme sind das Rückgrat der Pulverbeschichtungskabine und steuern wichtige Parameter wie Pulvermenge, Luftzirkulation, Temperatur und Aufladung des Pulvers. Diese Systeme verwenden Sensoren und Algorithmen, um die Parameter in Echtzeit zu überwachen und zu optimieren.
2.1 Steuerung der Pulvermengen und des Sprühdrucks
Die exakte Kontrolle der Pulvermengen und des Sprühdrucks ist entscheidend, um eine gleichmäßige Schichtdicke zu gewährleisten und Pulververluste zu minimieren.
- Pulvermenge und Dosierung: Das Steuerungssystem reguliert die Menge des aufgetragenen Pulvers, um sicherzustellen, dass die richtige Schichtdicke auf die Werkstücke aufgebracht wird.
- Druckregelung: Der Luftdruck, der das Pulver zur Sprühpistole befördert, wird ebenfalls präzise gesteuert, um eine gleichmäßige Verteilung des Pulvers zu gewährleisten.
- Automatische Anpassung: Intelligente Steuerungen passen die Pulverdosierung und den Sprühdruck automatisch an die Geometrie und Größe der Werkstücke an.
2.2 Steuerung der elektrostatischen Aufladung
Die elektrostatische Aufladung ist ein entscheidender Faktor für die Haftung des Pulvers auf der Oberfläche der Werkstücke. Die Aufladung wird ebenfalls automatisch überwacht und angepasst.
- Anpassung der Spannung: Das Steuerungssystem reguliert die Spannung, mit der das Pulver aufgeladen wird, um eine optimale Haftung zu gewährleisten.
- Ladungsstabilität: Durch die ständige Überwachung der elektrostatischen Parameter wird sichergestellt, dass die Ladung konstant bleibt und keine Spannungsabfälle auftreten, die zu einer ungleichmäßigen Schichtdicke führen könnten.
2.3 Luftführung und Luftzirkulation
Die Luftzirkulation innerhalb der Kabine beeinflusst die Qualität der Beschichtung und die Effizienz des Rückgewinnungssystems.
- Luftströmungskontrolle: Automatisierte Steuerungen regeln die Geschwindigkeit und Richtung der Luftströmung, um überschüssiges Pulver direkt zur Rückgewinnungseinheit zu leiten.
- Kontinuierliche Überwachung: Sensoren messen die Luftqualität und die Partikeldichte in der Kabine und passen die Luftzirkulation entsprechend an.
- Filterüberwachung: Die Filter werden kontinuierlich überwacht und die Steuerungssysteme benachrichtigen das Personal bei Bedarf, um eine gleichbleibende Filterleistung zu gewährleisten.
3. Roboter und Automatisierung in der Pulverbeschichtung
Der Einsatz von Robotern in der Pulverbeschichtung bietet eine Reihe von Vorteilen, die sowohl die Qualität als auch die Geschwindigkeit des Beschichtungsprozesses erhöhen. Roboter können präzise Bewegungen und gleichmäßige Schichtdicken gewährleisten, was die Produktionseffizienz und die Beschichtungsqualität steigert.
3.1 Roboterbeschichtung und Bewegungsmuster
Industrieroboter, die an automatisierten Armen befestigt sind, tragen das Pulver gleichmäßig auf und sind besonders nützlich für Werkstücke mit komplexen Geometrien.
- Programmierte Bewegungsmuster: Roboterarme können programmiert werden, um das Pulver gleichmäßig aufzutragen und dabei alle Seiten und Winkel des Werkstücks zu erreichen.
- Automatische Anpassung an Werkstückgeometrie: Roboter können automatisch unterschiedliche Werkstückformen erkennen und ihre Bewegungen entsprechend anpassen, um eine gleichmäßige Beschichtung sicherzustellen.
3.2 Flexible Anpassung an Produktionsanforderungen
Roboter in der Pulverbeschichtungskabine bieten Flexibilität bei der Anpassung an verschiedene Werkstücke und Produktionsanforderungen.
- Schnelle Umstellung: Roboter lassen sich schnell für unterschiedliche Werkstücke programmieren, wodurch Stillstandzeiten reduziert und der Produktionsfluss gesteigert werden.
- Mehrfarbenfähigkeit: Für Werkstücke, die mit mehreren Farbschichten beschichtet werden sollen, kann der Roboter für verschiedene Farben programmiert werden, um eine effiziente Farbwechselintegration zu ermöglichen.
4. Sensorik und Echtzeitüberwachung
Die Sensorik ist ein wichtiger Bestandteil der Steuerung und Automatisierung und ermöglicht eine Echtzeitüberwachung und Anpassung der Beschichtungsparameter.
4.1 Überwachung des Pulverauftrags und der Schichtdicke
Sensoren überwachen kontinuierlich die aufgetragene Pulverschicht und erkennen, ob die Schichtdicke den Anforderungen entspricht.
- Laser- und Ultraschallsensoren: Diese Sensoren messen die Schichtdicke des aufgetragenen Pulvers und gewährleisten eine gleichmäßige Verteilung.
- Korrektur der Schichtdicke: Bei Abweichungen passen die Sensoren die Pulvermengen oder die Sprühintensität automatisch an.
4.2 Partikel- und Luftqualitätssensoren
Luftqualitätssensoren messen die Partikeldichte in der Kabine, um sicherzustellen, dass die Umgebung sauber und sicher bleibt.
- Staubüberwachung: Sensoren überwachen den Staubgehalt und sorgen dafür, dass die Partikelkonzentration unter den zulässigen Grenzwerten bleibt.
- Feuchtigkeits- und Temperaturüberwachung: Die Überwachung der Luftfeuchtigkeit und Temperatur sorgt für eine stabile Aufladung und gleichmäßige Beschichtung.
5. Automatisierte Farbwechsel- und Reinigungssysteme
Farbwechsel- und Reinigungssysteme sind entscheidend für die Flexibilität und Produktivität der Pulverbeschichtungskabine.
5.1 Farbschnellwechselsysteme
Farbschnellwechselsysteme sind besonders wichtig in Produktionen, in denen mehrere Farbschichten oder schnelle Farbwechsel erforderlich sind.
- Automatisierte Farbwechsel: Farbschnellwechselsysteme reinigen die Pulverleitungen automatisch und führen die neue Farbe ein, ohne den gesamten Betrieb anzuhalten.
- Minimierung von Farbverunreinigungen: Durch das automatisierte Reinigungssystem wird das Risiko von Farbverunreinigungen verringert und die Beschichtungsqualität aufrechterhalten.
5.2 Automatische Reinigung der Kabine
Automatisierte Reinigungssysteme entfernen überschüssiges Pulver und Staub aus der Kabine, um die Effizienz und Qualität des Beschichtungsprozesses zu gewährleisten.
- Luftdüsen und Bürstenreinigung: Die Reinigung erfolgt häufig durch Luftdüsen oder Bürstensysteme, die Pulverreste von den Kabinenwänden entfernen.
- Automatisierter Filterwechsel: Bei Bedarf werden die Filter automatisch ausgetauscht oder gereinigt, um die Pulverrückgewinnung und Luftqualität sicherzustellen.
6. Vorteile der Steuerung und Automatisierung
Die Vorteile der Steuerung und Automatisierung in der Pulverbeschichtungskabine sind zahlreich und beeinflussen die Effizienz, Qualität und Umweltverträglichkeit des gesamten Prozesses.
- Verbesserte Beschichtungsqualität: Die präzise Steuerung und Echtzeitüberwachung sorgen für eine gleichmäßige Schichtdicke und eine hohe Haftung der Beschichtung.
- Erhöhte Produktionsgeschwindigkeit: Automatisierte Systeme reduzieren die Stillstandzeiten und steigern die Effizienz, indem sie die Prozesszeiten verkürzen und die Pulvermenge optimal steuern.
- Kosteneffizienz: Durch die Rückgewinnung von Pulver und die exakte Steuerung der Parameter werden die Betriebskosten gesenkt und der Materialverbrauch reduziert.
- Umweltschutz: Automatisierung reduziert den Materialabfall und den Energieverbrauch, was zur Nachhaltigkeit des Beschichtungsprozesses beiträgt.
7. Zukünftige Entwicklungen und Trends in der Automatisierung
Die Zukunft der Pulverbeschichtungskabine wird von neuen Technologien und der Digitalisierung geprägt sein, die die Effizienz und Nachhaltigkeit weiter steigern.
7.1 Integration von Künstlicher Intelligenz (KI)
KI-gesteuerte Systeme werden zunehmend in die Steuerung und Automatisierung der Kabine integriert und ermöglichen eine intelligente Anpassung und Optimierung der Beschichtungsparameter.
- Selbstlernende Algorithmen: KI kann den Beschichtungsprozess analysieren und die optimalen Parameter für verschiedene Werkstücke und Materialien ermitteln.
- Prädiktive Wartung: KI analysiert die Nutzungsdaten der Kabine und schlägt Wartungsmaßnahmen vor, bevor Probleme auftreten.
7.2 Vernetzte Systeme und Industrie 4.0
Die Digitalisierung und Vernetzung der Anlagen ermöglicht eine datengestützte Steuerung und verbessert die Effizienz und Flexibilität des Prozesses.
- Echtzeit-Datenerfassung und -Analyse: Vernetzte Sensoren und Steuerungssysteme liefern kontinuierlich Daten, die zur Optimierung der Prozesse genutzt werden können.
- Fernüberwachung und -steuerung: Vernetzte Systeme ermöglichen es, den Beschichtungsprozess remote zu überwachen und zu steuern, was die Flexibilität und Kontrolle erhöht.
7.3 Entwicklung energieeffizienter Systeme
Die zunehmende Nachfrage nach energieeffizienten Systemen führt zur Entwicklung neuer Technologien, die den Energieverbrauch reduzieren und die Nachhaltigkeit fördern.
- Energieoptimierte Roboter und Luftsysteme: Neue, energieeffiziente Roboter und Luftsysteme reduzieren den Stromverbrauch und tragen zur Senkung der Betriebskosten bei.
- Niedrigtemperatur-Pulverbeschichtung: Fortschritte in der Pulverbeschichtungstechnologie ermöglichen es, bei niedrigeren Temperaturen zu beschichten, was den Energieverbrauch senkt.
Fazit
Die Steuerung und Automatisierung der Pulverbeschichtungskabine spielt eine entscheidende Rolle für die Qualität, Effizienz und Nachhaltigkeit des Beschichtungsprozesses. Durch den Einsatz von Sensorik, Robotik, automatisierten Steuerungssystemen und innovativen Technologien wie Künstlicher Intelligenz und Industrie 4.0 wird die Pulverbeschichtung kontinuierlich optimiert. Diese Entwicklungen tragen dazu bei, die Pulverbeschichtung wirtschaftlicher, umweltfreundlicher und flexibler zu gestalten und somit den Anforderungen der modernen Industrie gerecht zu werden.
Innovationen in der Pulverbeschichtungskabinentechnologie – Fortschritte für Effizienz, Qualität und Nachhaltigkeit
Die Pulverbeschichtungskabinentechnologie hat sich in den letzten Jahren erheblich weiterentwickelt. Innovative Technologien und intelligente Automatisierungslösungen verbessern die Effizienz, erhöhen die Beschichtungsqualität und tragen zu einer nachhaltigeren Produktion bei. Von hochpräziser Sensorik und KI-gestützter Steuerung bis hin zu neuen Pulverrückgewinnungssystemen und Farbschnellwechsel-Technologien ermöglichen moderne Pulverbeschichtungskabinen eine optimale Nutzung der Ressourcen, reduzieren Emissionen und senken die Betriebskosten.
Dieser Leitfaden beschreibt die neuesten Innovationen und zukünftigen Trends in der Pulverbeschichtungskabinentechnologie und zeigt auf, wie diese Technologien die industrielle Pulverbeschichtung revolutionieren.
1. Automatisierung und Robotik in der Pulverbeschichtung
Die Einführung von Robotik und Automatisierung hat den Beschichtungsprozess in den letzten Jahren maßgeblich verändert und bietet erhebliche Vorteile hinsichtlich Effizienz und Präzision.
1.1 Automatisierte Beschichtungsroboter
Automatisierte Roboter tragen das Pulver präzise und gleichmäßig auf und sind insbesondere bei großen Produktionsvolumen oder Werkstücken mit komplexer Geometrie von Vorteil.
- Bewegungskontrolle und Programmierung: Roboterarme lassen sich so programmieren, dass sie gleichmäßige Bewegungsmuster und eine konsistente Schichtdicke gewährleisten.
- Adaptivität: Moderne Roboter können auf unterschiedliche Werkstücke programmiert und an verschiedene Formen und Größen angepasst werden, was die Flexibilität im Beschichtungsprozess erhöht.
1.2 Kollaborative Robotik (Cobots)
Die Integration kollaborativer Roboter (Cobots) ermöglicht es, dass Roboter direkt mit Menschen zusammenarbeiten und flexibel eingesetzt werden können, ohne umfassende Schutzvorrichtungen zu benötigen.
- Flexibilität und einfache Programmierung: Cobots sind leicht programmierbar und eignen sich für kleine Serien oder häufig wechselnde Beschichtungsanforderungen.
- Sicherheit: Mit speziellen Sensoren ausgestattet, können Cobots sicher neben menschlichen Mitarbeitern arbeiten und erhöhen somit die Flexibilität und Effizienz.
2. Intelligente Sensorik und KI-gestützte Steuerung
Intelligente Sensoren und Künstliche Intelligenz (KI) bieten neue Möglichkeiten zur Überwachung und Optimierung des Beschichtungsprozesses in Echtzeit.
2.1 Echtzeitüberwachung durch Sensoren
Die Echtzeitüberwachung der Beschichtungsparameter wie Schichtdicke, Partikeldichte und Luftqualität ist entscheidend, um eine konstante Qualität zu gewährleisten und Materialverluste zu minimieren.
- Schichtdickensensoren: Laser- und Ultraschallsensoren messen die Schichtdicke des aufgetragenen Pulvers und passen die Parameter automatisch an, um eine gleichmäßige Beschichtung zu gewährleisten.
- Partikel- und Luftqualitätssensoren: Sensoren messen die Partikelkonzentration in der Kabine und kontrollieren die Luftqualität, um die Betriebssicherheit zu erhöhen und den Materialverlust zu reduzieren.
2.2 KI-gestützte Steuerung und Automatisierung
Künstliche Intelligenz analysiert Daten aus dem Beschichtungsprozess und optimiert die Parameter automatisch, um Materialverbrauch und Energie zu reduzieren.
- Selbstlernende Algorithmen: KI-Systeme können aus vergangenen Produktionszyklen lernen und die Beschichtungsparameter kontinuierlich verbessern.
- Prädiktive Wartung: KI-gestützte Systeme überwachen die Leistung der Kabine und können vorhersagen, wann Wartung oder Filterwechsel erforderlich sind, um Ausfallzeiten zu vermeiden und die Effizienz zu maximieren.
3. Effiziente Pulverrückgewinnung und Recycling-Systeme
Innovative Rückgewinnungssysteme tragen zur Kostensenkung und zur Reduzierung von Abfällen bei, indem überschüssiges Pulver effizient aufgefangen und recycelt wird.
3.1 Hochleistungsrückgewinnungssysteme
Moderne Rückgewinnungssysteme bieten eine sehr hohe Rückgewinnungsrate, indem sie überschüssiges Pulver auffangen und reinigen, bevor es wiederverwendet wird.
- Mehrstufige Filterung: Fortschrittliche Filtersysteme entfernen Feinstaub und Verunreinigungen, sodass das aufgefangene Pulver sauber und wiederverwendbar bleibt.
- Automatische Rückführung: Das gereinigte Pulver wird automatisch in den Kreislauf zurückgeführt, was die Effizienz erhöht und den Materialverbrauch senkt.
3.2 Zyklonabscheider
Der Einsatz von Zyklonabscheidern in der Pulverrückgewinnung hat sich als besonders effizient erwiesen. Zyklonabscheider entfernen überschüssiges Pulver aus der Luft, bevor sie gefiltert wird.
- Energieeinsparung: Zyklonabscheider sind sehr energieeffizient und können große Mengen an Pulver verarbeiten, ohne den Stromverbrauch wesentlich zu erhöhen.
- Hohe Trennrate: Sie bieten eine hohe Trennrate für überschüssiges Pulver, was die Rückgewinnungsrate und Materialeinsparungen erhöht.
4. Farbschnellwechsel-Systeme
Ein schneller Farbwechsel ist in vielen Produktionsprozessen unverzichtbar und trägt zu einer flexiblen und effizienten Produktion bei.
4.1 Automatisierte Farbwechsel
Automatisierte Farbschnellwechsel-Systeme ermöglichen es, Farben innerhalb weniger Minuten zu wechseln, ohne dass die Kabine vollständig gereinigt werden muss.
- Reduzierte Stillstandzeiten: Die schnelle Umstellung auf eine andere Farbe reduziert die Stillstandzeiten und erhöht die Produktivität erheblich.
- Minimierung von Farbverunreinigungen: Spezielle Reinigungssysteme verhindern die Vermischung der Farben, was die Qualität der Beschichtung steigert.
4.2 Schnellwechselsysteme für Kleinserien
Für Unternehmen, die häufig kleine Chargen oder Sonderfarben benötigen, bieten Schnellwechselsysteme eine kosteneffiziente Lösung, ohne große Mengen Pulver zu verschwenden.
- Flexibilität für Kleinserien: Diese Systeme ermöglichen eine effiziente Anpassung an unterschiedliche Farben und sind besonders für Kleinserien oder Sonderbeschichtungen von Vorteil.
- Schnelle Reinigung: Die Systeme verfügen über automatische Reinigungseinheiten, die das Pulverleitungssystem in kürzester Zeit spülen und vorbereiten.
5. Energieeffiziente Systeme und Nachhaltigkeit
Mit dem steigenden Fokus auf Nachhaltigkeit und Ressourcenschonung gewinnen energieeffiziente Systeme und umweltfreundliche Technologien in der Pulverbeschichtung an Bedeutung.
5.1 Energieoptimierte Trocknungs- und Einbrenntechnologien
Moderne Trocknungs- und Einbrenntechnologien nutzen Infrarotstrahlung oder Mikrowellen, um das Pulver schnell und energieeffizient zu härten.
- Infrarot-Trocknung: Infrarotstrahlung ermöglicht eine gezielte Erwärmung der Oberfläche, die die Aushärtungszeit verkürzt und den Energieverbrauch senkt.
- Mikrowellentechnologie: Mikrowellenanlagen heizen das Werkstück von innen nach außen auf und sorgen für eine gleichmäßige und schnelle Aushärtung.
5.2 Einsatz von Niedrigtemperaturpulvern
Neue Pulvertechnologien, die bei niedrigeren Temperaturen aushärten, tragen erheblich zur Energieeinsparung bei und ermöglichen es, temperaturempfindliche Materialien zu beschichten.
- Niedrigere Aushärtetemperaturen: Niedrigtemperaturpulver können bei Temperaturen zwischen 120 und 140 °C gehärtet werden, was den Energieverbrauch deutlich senkt.
- Materialvielfalt: Durch die niedrigeren Temperaturen wird die Pulverbeschichtung für eine größere Bandbreite an Werkstoffen anwendbar, darunter Kunststoffe und andere empfindliche Materialien.
6. Vernetzte Systeme und Industrie 4.0 in der Pulverbeschichtung
Die Digitalisierung und Vernetzung von Pulverbeschichtungsanlagen bieten zahlreiche Möglichkeiten zur Optimierung und Steigerung der Effizienz des gesamten Produktionsprozesses.
6.1 Echtzeit-Datenüberwachung und -Analyse
Moderne Anlagen erfassen kontinuierlich Daten zu den Prozessparametern und stellen sie in Echtzeit zur Verfügung. Diese Daten werden zur Prozessoptimierung und Fehlerbehebung genutzt.
- Datenanalyse: Die Analyse der Daten ermöglicht es, den Pulverbeschichtungsprozess zu verbessern und die Parameter automatisch anzupassen.
- Fehlermanagement: Anomalien und Fehler können frühzeitig erkannt und behoben werden, was die Ausfallzeiten reduziert und die Produktivität steigert.
6.2 Fernüberwachung und Fernsteuerung
Die Integration von IoT-Technologien (Internet der Dinge) ermöglicht die Fernüberwachung und -steuerung der Pulverbeschichtungsanlagen.
- Remote-Zugriff: Produktionsleiter und Techniker können die Anlagenparameter überwachen und anpassen, selbst wenn sie sich nicht vor Ort befinden.
- Flexibilität und Anpassung: Änderungen in der Produktion können in Echtzeit vorgenommen werden, was besonders bei wechselnden Anforderungen von Vorteil ist.
7. Prädiktive Wartung und intelligente Wartungsstrategien
Intelligente Wartungsstrategien und prädiktive Wartung verbessern die Zuverlässigkeit der Anlagen und verlängern deren Lebensdauer.
7.1 Einsatz von KI in der Wartung
Durch den Einsatz von KI können Daten analysiert werden, um den Zustand der Anlage zu bewerten und Wartungsmaßnahmen zu planen.
- Prädiktive Wartung: KI-Systeme analysieren Betriebsdaten und identifizieren potenzielle Probleme, bevor sie zu Ausfällen führen.
- Automatische Wartungsbenachrichtigungen: Wenn Verschleiß oder Probleme erkannt werden, sendet das System eine automatische Benachrichtigung an das Wartungsteam, um eine zeitnahe Reaktion zu ermöglichen.
7.2 Reduzierung der Ausfallzeiten
Durch die prädiktive Wartung und regelmäßige Überwachung der Anlagenparameter lassen sich Ausfallzeiten erheblich reduzieren, was die Produktivität und Effizienz steigert.
- Geplante Wartung: Anlagen werden gezielt gewartet, wenn die Daten auf einen Bedarf hinweisen, was die Lebensdauer der Kabine verlängert.
- Effizientere Betriebszeit: Die Reduzierung ungeplanter Ausfälle erhöht die Betriebszeit und verbessert die Produktionskapazität.
Fazit
Die Innovationen in der Pulverbeschichtungskabinentechnologie revolutionieren die Oberflächenbehandlung und bieten vielfältige Vorteile hinsichtlich Qualität, Effizienz und Nachhaltigkeit. Durch den Einsatz von Automatisierung, intelligenter Sensorik, KI-gestützter Steuerung und energieeffizienten Technologien wird die Pulverbeschichtung nicht nur wirtschaftlicher, sondern auch umweltfreundlicher und flexibler. Zukünftige Trends wie vernetzte Systeme und prädiktive Wartung werden die Pulverbeschichtung weiter optimieren und zu einer effizienteren, nachhaltigeren und ressourcenschonenden Produktion beitragen.
Der Einbrennofen in der Pulverbeschichtung – Aufbau, Funktionsweise und innovative Technologien
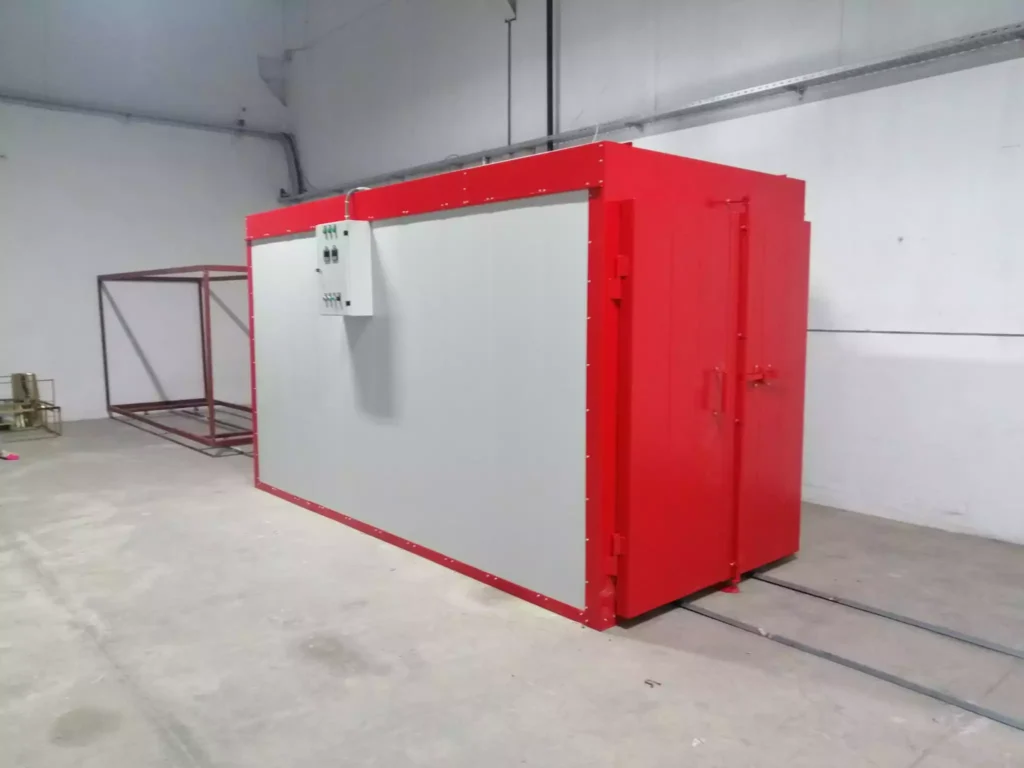
Der Einbrennofen ist ein unverzichtbarer Bestandteil des Pulverbeschichtungsprozesses und dient dazu, das zuvor aufgetragene Pulver bei hohen Temperaturen zu schmelzen und zu einer gleichmäßigen, widerstandsfähigen Beschichtung auszuhärten. Ein hochwertiger Einbrennofen gewährleistet eine präzise Steuerung der Temperatur und eine gleichmäßige Verteilung der Wärme, was entscheidend für die Qualität und Langlebigkeit der Beschichtung ist. Moderne Einbrennöfen integrieren zunehmend energieeffiziente Technologien und innovative Steuerungssysteme, um die Effizienz zu steigern und die Umweltbelastung zu reduzieren.
Dieser Leitfaden bietet eine detaillierte Beschreibung des Einbrennofens in der Pulverbeschichtung, einschließlich seines Aufbaus, seiner Funktionsweise, der verschiedenen Ofentypen und innovativer Technologien, die den Beschichtungsprozess optimieren.
1. Bedeutung des Einbrennofens im Pulverbeschichtungsprozess
Der Einbrennofen spielt eine zentrale Rolle in der Pulverbeschichtung, da er die Pulverschicht auf den Werkstücken schmilzt und aushärtet. Die Beschichtung erreicht dadurch eine hohe Festigkeit und Beständigkeit gegenüber Umwelteinflüssen.
- Aushärtung des Pulvers: Das aufgetragene Pulver wird im Einbrennofen erhitzt, bis es schmilzt und eine glatte, durchgehende Schicht bildet.
- Optimale Haftung: Durch den kontrollierten Aushärtungsprozess wird eine starke Haftung der Pulverschicht auf der Werkstückoberfläche gewährleistet.
- Widerstandsfähigkeit und Langlebigkeit: Die Beschichtung wird durch den Härtungsprozess beständig gegen mechanische Belastungen, Chemikalien und Witterungseinflüsse.
2. Aufbau eines Einbrennofens
Ein Einbrennofen ist so konstruiert, dass er eine gleichmäßige Temperaturverteilung, effiziente Energieübertragung und präzise Steuerung ermöglicht. Der Aufbau umfasst mehrere Komponenten, die in enger Zusammenarbeit die erforderlichen Temperaturen und Luftzirkulationen erzeugen.
2.1 Gehäuse und Wärmedämmung
Das Gehäuse des Einbrennofens ist mit einer hochwertigen Wärmedämmung versehen, um den Wärmeverlust zu minimieren und die Effizienz zu steigern.
- Wärmedämmende Materialien: Hochtemperaturfeste Isolierungen halten die Wärme im Inneren des Ofens, reduzieren den Energieverbrauch und schützen die Umgebung vor Hitze.
- Robuste Gehäusestruktur: Der Einbrennofen besteht meist aus rostfreiem Stahl oder hitzebeständigen Materialien, die eine lange Lebensdauer und Stabilität garantieren.
2.2 Heizsystem
Das Heizsystem ist das Herzstück des Einbrennofens und bestimmt, wie schnell und gleichmäßig die Temperatur erreicht wird.
- Gasbefeuerte Heizsysteme: Gasheizungen sind in Einbrennöfen weit verbreitet und bieten eine kosteneffiziente Möglichkeit zur schnellen Erwärmung großer Ofenräume.
- Elektrische Heizsysteme: Elektrische Heizungen ermöglichen eine präzise Steuerung der Temperatur und sind in Umgebungen mit strengen Emissionsanforderungen besonders beliebt.
2.3 Luftzirkulationssystem
Die Luftzirkulation im Ofen sorgt für eine gleichmäßige Verteilung der Hitze und stellt sicher, dass die Beschichtung gleichmäßig aushärtet.
- Umluftsysteme: Umluftventilatoren verteilen die Wärme gleichmäßig im Ofen und ermöglichen eine gleichmäßige Erwärmung der Werkstücke.
- Direkte und indirekte Luftführung: Einbrennöfen können mit direkter oder indirekter Luftführung ausgestattet sein, je nach Anforderung an die Produktqualität und den Energieverbrauch.
2.4 Fördersystem
Das Fördersystem transportiert die Werkstücke durch den Ofen und sorgt dafür, dass sie während des gesamten Einbrennprozesses in Bewegung bleiben.
- Hängebahnsysteme: Hängebahnen transportieren die Werkstücke durch den Ofen und eignen sich besonders für großformatige oder hängende Teile.
- Bodenförderbänder: Für kleine bis mittelgroße Werkstücke werden Bodenförderbänder verwendet, die eine schnelle und gleichmäßige Bewegung gewährleisten.
3. Funktionsweise des Einbrennofens
Der Einbrennprozess im Ofen folgt einem strukturierten Ablauf, der sicherstellt, dass das Pulver vollständig schmilzt und sich gleichmäßig auf der Oberfläche verteilt. Die Funktionsweise umfasst mehrere Schritte:
3.1 Vorwärmphase
In der Vorwärmphase wird die Temperatur im Ofen schrittweise erhöht, um die Werkstücke und das Pulver gleichmäßig zu erwärmen.
- Langsame Temperatursteigerung: Eine langsame Erhöhung der Temperatur reduziert Spannungen im Material und stellt sicher, dass die Pulverschicht gleichmäßig erhitzt wird.
- Vermeidung von Defekten: Die Vorwärmphase verhindert, dass das Pulver zu schnell schmilzt und Blasen oder Risse in der Beschichtung entstehen.
3.2 Schmelz- und Aushärtungsphase
Sobald die gewünschte Temperatur erreicht ist, schmilzt das Pulver und verbindet sich zu einer einheitlichen, glatten Schicht.
- Schmelzen des Pulvers: Das Pulver schmilzt bei Temperaturen zwischen 160 °C und 220 °C und bildet eine gleichmäßige Oberfläche.
- Aushärtung: Nach dem Schmelzen wird die Beschichtung bei konstanter Temperatur gehärtet, wodurch eine beständige und widerstandsfähige Schicht entsteht.
3.3 Abkühlungsphase
In der letzten Phase werden die Werkstücke langsam abgekühlt, um Spannungen zu vermeiden und die Endhärte der Beschichtung zu gewährleisten.
- Langsame Abkühlung: Durch die kontrollierte Abkühlung werden Spannungsrisse oder Verformungen der Schicht vermieden.
- Transport zur Abkühlzone: Nach dem Ofen werden die Werkstücke in eine Abkühlzone transportiert, in der sie auf Umgebungstemperatur abkühlen können.
4. Arten von Einbrennöfen
Es gibt verschiedene Ofentypen, die jeweils für unterschiedliche Produktionsanforderungen und Werkstückarten geeignet sind.
4.1 Umluft-Einbrennöfen
Umluftöfen verteilen die Hitze mithilfe von Ventilatoren gleichmäßig und eignen sich für eine Vielzahl von Werkstücken und Beschichtungsmaterialien.
- Vorteile: Gleichmäßige Wärmeverteilung, hohe Energieeffizienz, geeignet für große Werkstücke.
- Nachteile: Erfordert regelmäßige Wartung der Umluftventilatoren.
4.2 Infrarot-Einbrennöfen
Infrarotöfen nutzen Infrarotstrahlen, um die Oberfläche der Werkstücke direkt zu erwärmen und sind besonders energieeffizient.
- Vorteile: Schnelle Erwärmung, energieeffizient, ideal für dünne oder temperaturempfindliche Materialien.
- Nachteile: Nicht geeignet für dicke oder stark wärmeleitende Materialien.
4.3 Kombinationseinbrennöfen (Hybridöfen)
Hybridöfen kombinieren Umluft- und Infrarottechnologie und ermöglichen eine präzise Temperatursteuerung bei hoher Energieeffizienz.
- Vorteile: Flexibel einsetzbar, schnelle Erwärmung und Aushärtung, geeignet für komplexe Werkstücke.
- Nachteile: Höhere Anschaffungskosten und komplexere Wartung.
5. Innovationen und Technologien im Einbrennofen
Moderne Einbrennöfen integrieren fortschrittliche Technologien, die den Energieverbrauch senken, die Umweltbelastung reduzieren und die Produktionsqualität erhöhen.
5.1 Automatisierte Temperatursteuerung
Durch intelligente Steuerungssysteme wird die Temperatur im Ofen präzise kontrolliert und an die Anforderungen der Werkstücke angepasst.
- Intelligente Sensoren: Sensoren überwachen die Temperatur in Echtzeit und passen die Heizleistung automatisch an, um Energie zu sparen und die Qualität zu sichern.
- Automatische Anpassung: Die Steuerungssysteme können auf verschiedene Materialien und Schichtdicken eingestellt werden und garantieren so eine gleichmäßige Aushärtung.
5.2 Energiemanagementsysteme
Neue Energiemanagementsysteme reduzieren den Energieverbrauch des Ofens, indem sie die Energie effizient nutzen und Verluste minimieren.
- Wärmerückgewinnung: Die Abwärme des Ofens kann in anderen Produktionsschritten genutzt werden, um den Gesamtenergieverbrauch zu senken.
- Optimierte Luftzirkulation: Fortschrittliche Umluftsysteme minimieren den Energieverbrauch, indem sie die Wärme gleichmäßig verteilen und Verluste reduzieren.
5.3 KI-gestützte Steuerung und prädiktive Wartung
Künstliche Intelligenz (KI) wird zunehmend in Einbrennöfen eingesetzt, um den Betrieb zu optimieren und Wartungsbedarfe zu erkennen, bevor es zu Problemen kommt.
- KI-basierte Prozessoptimierung: KI-Systeme analysieren die Betriebsdaten und passen die Temperaturregelung kontinuierlich an, um Energie zu sparen und die Beschichtungsqualität zu verbessern.
- Prädiktive Wartung: KI-Systeme erkennen Anzeichen von Verschleiß oder Leistungsabfall und empfehlen Wartungsmaßnahmen, bevor Ausfälle auftreten.
5.4 Umweltfreundliche Technologien
Einbrennöfen werden zunehmend mit umweltfreundlichen Technologien ausgestattet, um den CO₂-Ausstoß zu reduzieren und die Umweltbelastung zu minimieren.
- Energieeffiziente Brenner: Moderne Brenner reduzieren den Energieverbrauch und senken die Emissionen.
- Emissionstechnologien: Neue Filter- und Abgassysteme minimieren die Emissionen und verbessern die Luftqualität in der Produktionsumgebung.
6. Steuerung und Automatisierung im Einbrennofen
Moderne Einbrennöfen sind mit hochentwickelten Steuerungssystemen ausgestattet, die eine präzise Überwachung und Anpassung des Einbrennprozesses ermöglichen.
- Automatisierte Prozesssteuerung: Automatisierte Steuerungen passen die Temperatur und Luftzirkulation automatisch an die Anforderungen der Beschichtung an.
- Überwachung und Fernsteuerung: Über Netzwerkschnittstellen können Anlagenbetreiber den Ofen aus der Ferne überwachen und steuern, was die Flexibilität und Kontrolle erhöht.
- Echtzeitüberwachung: Temperatur, Luftstrom und Heizleistung werden in Echtzeit überwacht und bei Bedarf sofort angepasst.
7. Zukünftige Entwicklungen in der Einbrennofentechnologie
Zukünftige Einbrennöfen werden voraussichtlich noch effizienter und umweltfreundlicher gestaltet, um den steigenden Anforderungen an Nachhaltigkeit und Qualität gerecht zu werden.
7.1 Integration von Industrie 4.0 und IoT
Die Digitalisierung wird es ermöglichen, Einbrennöfen in vernetzte Produktionssysteme zu integrieren und Daten in Echtzeit zu analysieren.
- Datenanalyse und -optimierung: Echtzeitdaten aus dem Betrieb des Ofens können analysiert werden, um den Energieverbrauch und die Qualität zu optimieren.
- IoT-fähige Komponenten: Intelligente Sensoren und Netzwerkschnittstellen ermöglichen eine vollständige Integration des Ofens in Industrie-4.0-Produktionssysteme.
7.2 Weiterentwicklung der Energieeffizienz
Neue Brenner- und Isolationssysteme sowie optimierte Luftführungssysteme werden den Energieverbrauch weiter reduzieren und die Betriebskosten senken.
- Niedrigenergie-Einbrennöfen: Fortschrittliche Materialien und Techniken ermöglichen es, die Wärmeverluste zu minimieren und die Effizienz zu maximieren.
- Alternative Energiequellen: In Zukunft könnten Einbrennöfen durch erneuerbare Energien betrieben werden, um den ökologischen Fußabdruck weiter zu verringern.
Fazit
Der Einbrennofen ist ein entscheidender Bestandteil des Pulverbeschichtungsprozesses und beeinflusst maßgeblich die Qualität und Beständigkeit der Beschichtung. Fortschritte in der Technologie, wie intelligente Steuerungssysteme, KI-gestützte Optimierung und energieeffiziente Lösungen, machen den Einbrennofen zu einem noch präziseren und nachhaltigeren Instrument für die industrielle Oberflächenbehandlung. Diese Innovationen tragen dazu bei, die Kosten zu senken, die Umweltbelastung zu reduzieren und die Produktionsqualität weiter zu steigern. In einer zunehmend digitalisierten und umweltbewussten Industrie wird der Einbrennofen auch in Zukunft eine zentrale Rolle spielen und sich kontinuierlich weiterentwickeln.
Die Bedeutung des Einbrennofens im Pulverbeschichtungsprozess – Qualität, Beständigkeit und Nachhaltigkeit
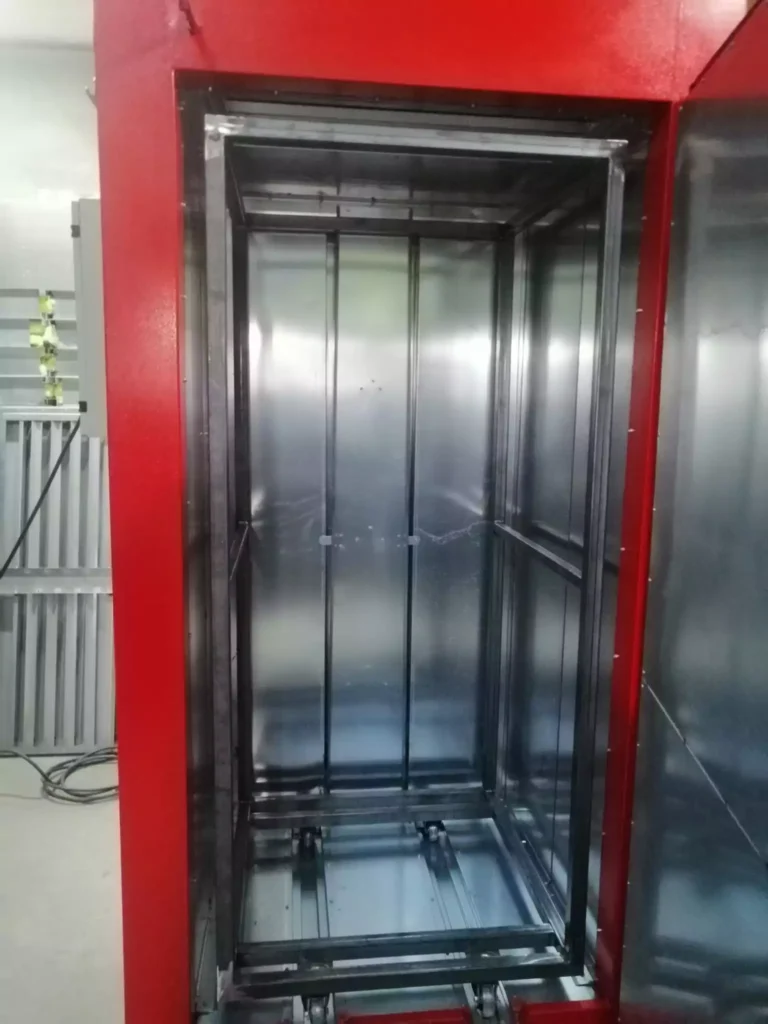
Der Einbrennofen ist ein zentraler Bestandteil des Pulverbeschichtungsprozesses und entscheidend für die Qualität und Beständigkeit der Beschichtung. Er härtet das aufgetragene Pulver durch eine exakte Temperaturführung und präzise Zeitsteuerung aus und schafft damit eine gleichmäßige, widerstandsfähige und optisch ansprechende Oberfläche. Die Bedeutung des Einbrennofens geht jedoch über die reine Aushärtung hinaus: Moderne Einbrennöfen bieten energiesparende Technologien und innovative Steuerungssysteme, die die Effizienz steigern und die Umweltbelastung senken.
Dieser umfassende Leitfaden beschreibt die Rolle des Einbrennofens im Pulverbeschichtungsprozess, seine Funktionsweise, die Auswirkungen auf die Beschichtungsqualität und die Bedeutung innovativer Technologien für eine nachhaltigere Produktion.
1. Aufgaben und Funktionen des Einbrennofens im Pulverbeschichtungsprozess
Der Einbrennofen hat mehrere wesentliche Funktionen im Pulverbeschichtungsprozess, die zur Qualität und Beständigkeit der Pulverschicht beitragen.
1.1 Schmelzen und Aushärten der Pulverschicht
Der Hauptzweck des Einbrennofens ist das Schmelzen und Aushärten des Pulvers, das zuvor elektrostatisch auf die Werkstückoberfläche aufgetragen wurde.
- Schmelzen des Pulvers: Bei Temperaturen zwischen 160 °C und 220 °C schmilzt das Pulver und verbindet sich zu einer glatten, gleichmäßigen Schicht.
- Aushärten der Beschichtung: Nach dem Schmelzen härtet die Beschichtung bei konstanter Temperatur, was ihre mechanische Festigkeit und chemische Beständigkeit erhöht.
1.2 Sicherstellen der Haftung und Glätte
Die kontrollierte Temperaturführung im Ofen sorgt für eine optimale Haftung des Pulvers auf der Oberfläche und verhindert, dass sich Defekte oder Risse bilden.
- Adhäsion und Kohäsion: Durch die Wärme verbindet sich das Pulver dauerhaft mit dem Werkstück und bildet eine haftfeste Schicht, die auch äußeren Einflüssen standhält.
- Glatte Oberfläche: Der Einbrennofen stellt sicher, dass die Oberfläche glatt und frei von Blasen, Rissen oder Unebenheiten ist, was die optische Qualität verbessert.
1.3 Gewährleistung von Beständigkeit und Schutz
Die Aushärtung im Einbrennofen verleiht der Beschichtung ihre Widerstandsfähigkeit gegen mechanische Belastungen, Chemikalien und Witterungseinflüsse.
- Korrosionsschutz: Durch den Einbrennprozess wird die Beschichtung widerstandsfähig gegen Korrosion, wodurch die Lebensdauer der beschichteten Werkstücke verlängert wird.
- Schlag- und Abriebfestigkeit: Die thermische Behandlung im Ofen verleiht der Pulverschicht eine erhöhte Härte und macht sie widerstandsfähig gegen Schläge und Abnutzung.
2. Funktionsweise des Einbrennofens
Der Einbrennofen durchläuft mehrere Phasen, die eine gleichmäßige Aushärtung der Pulverschicht sicherstellen und die Qualität der Beschichtung beeinflussen.
2.1 Vorwärmphase
In der Vorwärmphase wird die Temperatur im Ofen schrittweise erhöht, um die Werkstücke und die Pulverschicht gleichmäßig zu erwärmen.
- Langsame Temperatursteigerung: Durch eine schrittweise Erhöhung der Temperatur werden Spannungen im Werkstück und in der Pulverschicht reduziert.
- Reduktion von Defekten: Die kontrollierte Erwärmung verhindert, dass das Pulver zu schnell schmilzt und Blasen oder Risse entstehen.
2.2 Schmelz- und Aushärtungsphase
Sobald die Zieltemperatur erreicht ist, schmilzt das Pulver und bildet eine homogene, glatte Schicht auf der Werkstückoberfläche.
- Schmelzen des Pulvers: Das Pulver wird bei hoher Temperatur geschmolzen und legt sich gleichmäßig auf der Oberfläche ab.
- Aushärten: In dieser Phase wird die Pulverschicht bei konstanter Temperatur gehärtet, was ihre Widerstandsfähigkeit und Oberflächenqualität optimiert.
2.3 Abkühlungsphase
Die Abkühlung erfolgt schrittweise, um Spannungen zu vermeiden und die Endhärte der Beschichtung zu gewährleisten.
- Langsame Abkühlung: Die kontrollierte Abkühlung verhindert Spannungsrisse und Verformungen in der Pulverschicht.
- Transport zur Abkühlzone: Nach dem Ofen werden die Werkstücke in eine Abkühlzone transportiert, in der sie auf Umgebungstemperatur abkühlen.
3. Einbrennofentypen und ihre Auswirkungen auf den Beschichtungsprozess
Je nach Anwendung und Werkstücktyp stehen verschiedene Einbrennofentypen zur Verfügung, die jeweils spezifische Vorteile bieten.
3.1 Umluft-Einbrennöfen
Umluftöfen verteilen die Wärme gleichmäßig und eignen sich für eine Vielzahl von Werkstücken und Beschichtungsmaterialien.
- Vorteile: Gleichmäßige Wärmeverteilung, hohe Energieeffizienz und gleichmäßige Erwärmung auch bei großen Werkstücken.
- Einsatzbereich: Für komplexe Geometrien und unterschiedlich große Werkstücke, die eine gleichmäßige Erwärmung benötigen.
3.2 Infrarot-Einbrennöfen
Infrarotöfen nutzen Infrarotstrahlung, um die Werkstückoberfläche direkt zu erwärmen. Diese Art von Ofen ist besonders energieeffizient und schnell.
- Vorteile: Schnelle Erwärmung, hoher Wirkungsgrad und niedriger Energieverbrauch.
- Einsatzbereich: Ideal für Werkstücke mit dünnen Schichten oder temperaturempfindliche Materialien.
3.3 Kombinations- oder Hybridöfen
Hybridöfen kombinieren Umluft- und Infrarottechnologie, um die Vorteile beider Systeme zu nutzen.
- Vorteile: Vielseitigkeit, präzise Temperaturkontrolle und schnelle Aushärtung.
- Einsatzbereich: Für Werkstücke mit komplexen Anforderungen oder variable Materialeigenschaften.
4. Innovationspotenziale in der Einbrennofentechnologie
Moderne Einbrennöfen integrieren zunehmend innovative Technologien, die den Pulverbeschichtungsprozess optimieren und die Nachhaltigkeit erhöhen.
4.1 Energieeffizienz und Wärmerückgewinnung
Die Optimierung des Energieverbrauchs ist eine wesentliche Zielsetzung moderner Einbrennöfen, um den ökologischen Fußabdruck der Produktion zu reduzieren.
- Wärmerückgewinnungssysteme: Abwärme wird in anderen Bereichen der Produktion genutzt, was den Energiebedarf des Einbrennofens senkt.
- Verbesserte Isolierung: Fortschrittliche Dämmmaterialien verringern den Wärmeverlust und steigern die Energieeffizienz.
4.2 Automatisierte Steuerung und Überwachung
Moderne Steuerungssysteme erlauben eine präzise Überwachung und Steuerung der Ofenparameter, um die Temperatur konstant zu halten und die Qualität zu sichern.
- Automatische Temperaturregelung: Sensoren überwachen die Temperatur im Ofen und passen die Heizleistung automatisch an.
- Prozessüberwachung in Echtzeit: Echtzeitdaten sorgen für eine präzise Kontrolle und ermöglichen eine schnelle Anpassung der Parameter.
4.3 Prädiktive Wartung und Künstliche Intelligenz
Mit KI-gestützten Systemen wird der Betrieb des Einbrennofens analysiert und optimiert, um die Effizienz zu steigern und Wartungsbedarf vorherzusagen.
- Selbstlernende Algorithmen: KI-Systeme lernen aus vergangenen Produktionszyklen und passen die Parameter kontinuierlich an.
- Prädiktive Wartung: KI erkennt Anzeichen von Verschleiß und Wartungsbedarf frühzeitig und verhindert so ungeplante Ausfallzeiten.
4.4 Umweltfreundliche Technologien
Der Einsatz emissionsarmer Brenner und umweltfreundlicher Filtertechnologien trägt zur Reduzierung des CO₂-Ausstoßes und zur Verbesserung der Luftqualität bei.
- Energieeffiziente Brenner: Moderne Brenner verbrauchen weniger Energie und reduzieren die Emissionen.
- Abgasfilterung: Filtertechnologien sorgen dafür, dass die Abgase des Ofens gereinigt werden, bevor sie in die Umwelt gelangen.
5. Qualitätskontrolle und Prozessoptimierung im Einbrennofen
Die präzise Steuerung des Einbrennofens und die kontinuierliche Überwachung der Parameter sind entscheidend, um eine hohe Beschichtungsqualität sicherzustellen.
5.1 Überwachung der Temperatur und Luftzirkulation
Die Kontrolle der Temperatur und Luftzirkulation ist für die Qualität der Pulverschicht entscheidend.
- Gleichmäßige Erwärmung: Durch die präzise Steuerung der Umluft wird eine gleichmäßige Erwärmung des Pulvers erreicht, was eine homogene Beschichtung gewährleistet.
- Temperaturregelung in Echtzeit: Sensoren überwachen die Temperaturen und sorgen dafür, dass die eingestellten Werte während des gesamten Prozesses konstant bleiben.
5.2 Kontrolle der Aushärtungszeit
Die Dauer des Einbrennprozesses beeinflusst die Härte und Widerstandsfähigkeit der Beschichtung und muss präzise gesteuert werden.
- Optimale Aushärtungszeit: Automatisierte Steuerungssysteme stellen sicher, dass die Werkstücke nur so lange wie nötig im Ofen bleiben, um eine perfekte Beschichtung zu erzielen.
- Anpassung an Materialeigenschaften: Die Aushärtungszeit kann an die Materialeigenschaften angepasst werden, um Spannungen zu vermeiden und Defekte zu reduzieren.
5.3 Qualitätssicherung nach dem Einbrennvorgang
Nach der Aushärtung im Einbrennofen wird die Qualität der Beschichtung überprüft, um sicherzustellen, dass sie den Anforderungen entspricht.
- Visuelle Kontrolle: Nach dem Einbrennen werden die Werkstücke auf optische Defekte wie Blasen oder Risse untersucht.
- Messung der Schichtdicke und Haftung: Die Dicke der Pulverschicht und die Haftung auf dem Werkstück werden gemessen, um die Beständigkeit und Qualität zu gewährleisten.
Fazit
Der Einbrennofen ist ein unverzichtbarer Bestandteil des Pulverbeschichtungsprozesses, der entscheidend zur Qualität, Beständigkeit und Nachhaltigkeit der Beschichtung beiträgt. Die genaue Steuerung der Temperatur und Aushärtungszeit sowie innovative Technologien wie KI-gestützte Prozessoptimierung und energiesparende Wärmerückgewinnung tragen dazu bei, den Pulverbeschichtungsprozess effizienter und umweltfreundlicher zu gestalten. Die kontinuierliche Weiterentwicklung der Einbrennofentechnologie bietet neue Möglichkeiten, die Produktion zu verbessern, Betriebskosten zu senken und die Umweltbelastung zu reduzieren. In einer sich wandelnden Industrie wird der Einbrennofen auch zukünftig eine zentrale Rolle spielen und den Anforderungen nach hoher Beschichtungsqualität und Nachhaltigkeit gerecht werden.
Aufbau eines Einbrennofens im Pulverbeschichtungsprozess – Struktur, Komponenten und technische Anforderungen
Der Einbrennofen ist eine zentrale Komponente in der Pulverbeschichtung, in dem das aufgetragene Pulver auf Werkstücken erhitzt, geschmolzen und anschließend gehärtet wird. Der Aufbau eines Einbrennofens ist komplex und vereint mehrere technische Komponenten, die eine präzise Temperaturführung und eine gleichmäßige Wärmeverteilung ermöglichen. Ein gut konzipierter Einbrennofen ist energieeffizient, gewährleistet eine hohe Produktqualität und erfüllt zugleich hohe Sicherheits- und Umweltstandards.
Dieser Leitfaden beschreibt den detaillierten Aufbau eines Einbrennofens für die Pulverbeschichtung und beleuchtet die wichtigsten Komponenten und ihre jeweilige Funktion im Beschichtungsprozess.
1. Gehäuse und Wärmedämmung des Einbrennofens
Das Gehäuse und die Wärmedämmung sind zentrale Bestandteile des Einbrennofens, die die Wärme im Inneren halten und die Effizienz des Ofens verbessern.
1.1 Gehäusestruktur und Materialien
Das Gehäuse schützt die äußere Umgebung vor Hitze und sichert den Ofen gegen äußere Einflüsse ab.
- Hochtemperaturbeständige Materialien: Das Gehäuse besteht in der Regel aus rostfreiem Stahl oder anderen hitzebeständigen Materialien, die Stabilität und Langlebigkeit garantieren.
- Robustes Design: Die Struktur ist so gestaltet, dass der Ofen langlebig ist und den mechanischen und thermischen Belastungen im Dauerbetrieb standhält.
1.2 Wärmedämmung
Die Wärmedämmung ist entscheidend, um Energieverluste zu minimieren und die Temperatur im Inneren des Ofens konstant zu halten.
- Hochleistungsdämmstoffe: Für die Dämmung kommen spezielle Hochleistungsdämmstoffe zum Einsatz, die hohen Temperaturen standhalten und die Wärmeübertragung reduzieren.
- Mehrschichtige Konstruktion: Oft wird eine mehrschichtige Isolierung verwendet, die die Wärmeverluste weiter verringert und die Effizienz des Einbrennofens steigert.
2. Heizsystem des Einbrennofens
Das Heizsystem ist das Herzstück des Einbrennofens und verantwortlich für die Erzeugung und Aufrechterhaltung der erforderlichen Temperaturen für den Beschichtungsprozess.
2.1 Heizmethoden
Einbrennöfen nutzen verschiedene Heizmethoden, die jeweils Vor- und Nachteile bieten und sich an unterschiedliche Produktionsanforderungen anpassen lassen.
- Gasbeheizung: Gasbefeuerte Einbrennöfen sind energieeffizient und ermöglichen eine schnelle Erwärmung großer Ofenräume. Diese Methode wird oft in industriellen Anwendungen eingesetzt.
- Elektroheizung: Elektrische Heizsysteme bieten eine präzise Temperatursteuerung und sind besonders geeignet für Umgebungen mit strengen Emissionsanforderungen.
- Infrarotstrahlung: Infrarot-Heizsysteme nutzen Strahlungswärme, um die Werkstücke direkt zu erwärmen. Diese Methode ist energieeffizient und besonders geeignet für dünne Werkstücke oder temperaturempfindliche Materialien.
2.2 Heizquellen und Brenner
Die Heizquellen erzeugen die notwendige Wärme und verteilen sie gleichmäßig im Ofen.
- Gasbrenner: Gasbrenner sind so ausgelegt, dass sie die Wärme gleichmäßig und effizient im gesamten Ofen verteilen.
- Elektroheizelemente: Elektrische Heizelemente sind präzise steuerbar und ermöglichen eine gleichmäßige und konstante Temperaturführung.
- Infrarotstrahler: Infrarotstrahler erzeugen gezielte Wärme, die die Oberfläche der Werkstücke direkt erwärmt und die Energieeffizienz erhöht.
3. Luftzirkulationssystem im Einbrennofen
Ein effektives Luftzirkulationssystem sorgt für eine gleichmäßige Verteilung der Wärme im Einbrennofen und verhindert Überhitzungen oder Kältezonen.
3.1 Umluftsystem
Das Umluftsystem ist der Hauptbestandteil der Luftzirkulation und verteilt die Hitze gleichmäßig im Ofenraum.
- Umluftventilatoren: Leistungsstarke Ventilatoren bewegen die Luft im Ofen und sorgen dafür, dass alle Bereiche die gleiche Temperatur haben.
- Luftkanäle und Verteilsysteme: Die Luft wird durch spezielle Kanäle geleitet und gleichmäßig im Ofen verteilt, um sicherzustellen, dass alle Werkstücke die gleiche Wärme erhalten.
3.2 Direkt- und Indirektluftführung
Einbrennöfen können mit direkter oder indirekter Luftführung ausgestattet sein, je nach den Anforderungen der Beschichtung und der gewünschten Energieeffizienz.
- Direkte Luftführung: Bei direkter Luftführung wird die erwärmte Luft direkt auf die Werkstücke geleitet, was eine schnelle und intensive Erwärmung ermöglicht.
- Indirekte Luftführung: Bei indirekter Luftführung wird die Luft erst im Ofenraum zirkuliert und erreicht die Werkstücke indirekt. Diese Methode eignet sich besonders für empfindliche Beschichtungen.
4. Fördersystem des Einbrennofens
Das Fördersystem ist entscheidend für den kontinuierlichen Transport der Werkstücke durch den Einbrennofen und sorgt für eine gleichmäßige Behandlung der Beschichtung.
4.1 Typen von Fördersystemen
Je nach Art und Größe der Werkstücke kommen unterschiedliche Fördersysteme zum Einsatz.
- Hängebahnsysteme: Hängebahnen sind ideal für größere Werkstücke, die vertikal transportiert werden können. Sie ermöglichen einen kontinuierlichen Fluss durch den Ofen.
- Bodenförderbänder: Für kleinere Werkstücke werden oft Bodenförderbänder verwendet, die eine präzise Bewegung und stabile Platzierung gewährleisten.
- Kombinierte Systeme: In einigen Fällen wird ein hybrides System genutzt, das sowohl Hängebahnen als auch Bodenförderbänder kombiniert, um flexibel auf unterschiedliche Werkstücke zu reagieren.
4.2 Temperaturbeständige Fördermechanismen
Die Fördersysteme sind für den Einsatz bei hohen Temperaturen ausgelegt, um den kontinuierlichen Betrieb des Einbrennofens zu gewährleisten.
- Hitzebeständige Materialien: Die Förderketten und -bänder bestehen aus hitzebeständigen Materialien, die eine hohe Lebensdauer und Stabilität bieten.
- Kontinuierliche Bewegung: Die Geschwindigkeit des Fördersystems wird automatisch gesteuert, um die Verweildauer der Werkstücke im Ofen zu regulieren und eine gleichmäßige Aushärtung zu gewährleisten.
5. Steuerungs- und Überwachungssysteme
Moderne Einbrennöfen sind mit fortschrittlichen Steuerungs- und Überwachungssystemen ausgestattet, die die präzise Kontrolle des gesamten Prozesses ermöglichen.
5.1 Temperaturüberwachung und -steuerung
Die Temperatur im Einbrennofen muss genau überwacht und gesteuert werden, um optimale Aushärtungsbedingungen zu gewährleisten.
- Thermoelemente und Temperatursensoren: Diese Sensoren messen die Temperatur im Ofen und senden Echtzeitdaten an das Steuerungssystem.
- Automatische Temperaturregelung: Die Heizleistung wird in Abhängigkeit von den Sensorwerten automatisch angepasst, um die eingestellte Temperatur konstant zu halten.
5.2 Luftzirkulations- und Feuchtigkeitskontrolle
Die Steuerung der Luftzirkulation und Feuchtigkeit im Ofenraum ist entscheidend für die Qualität der Beschichtung.
- Luftzirkulationskontrolle: Die Luftzirkulation wird kontinuierlich überwacht und bei Bedarf angepasst, um die gleichmäßige Wärmeverteilung sicherzustellen.
- Feuchtigkeitsmanagement: Einige Beschichtungen erfordern eine bestimmte Luftfeuchtigkeit, die im Ofen überwacht und gesteuert wird, um die Oberflächenqualität zu optimieren.
5.3 Prozessüberwachung und Fehlermanagement
Das Steuerungssystem erkennt Abweichungen im Prozess und ermöglicht eine schnelle Fehlerbehebung.
- Echtzeitüberwachung: Alle wichtigen Parameter werden in Echtzeit überwacht und angezeigt, was eine sofortige Reaktion auf Änderungen ermöglicht.
- Alarm- und Fehlermanagement: Bei Abweichungen von den Sollwerten wird das Bedienpersonal sofort informiert, um Korrekturmaßnahmen zu ergreifen.
6. Sicherheits- und Umweltschutzkomponenten
Ein Einbrennofen muss nicht nur effizient arbeiten, sondern auch strenge Sicherheits- und Umweltauflagen erfüllen.
6.1 Sicherheitseinrichtungen
Sicherheitseinrichtungen sind erforderlich, um den Betrieb des Ofens sicher und zuverlässig zu gestalten.
- Brandschutzvorrichtungen: In den Ofen sind Feuerlöschsysteme integriert, um Brände zu verhindern und die Sicherheit der Anlage zu gewährleisten.
- Überdruckventile: Diese Ventile sorgen dafür, dass ein eventueller Druckanstieg im Ofen sicher abgebaut wird, um Schäden zu vermeiden.
6.2 Umwelt- und Emissionskontrolle
Moderne Einbrennöfen sind mit Technologien ausgestattet, die Emissionen minimieren und die Umwelt schützen.
- Abgasreinigung: Die Abgase werden durch Filteranlagen geleitet, um Schadstoffe und Partikel auszufiltern, bevor sie in die Umwelt entlassen werden.
- Wärmerückgewinnung: Viele Öfen sind mit Systemen zur Wärmerückgewinnung ausgestattet, die die Energie aus der Abwärme zurückgewinnen und in anderen Bereichen der Produktion nutzen.
7. Innovationen und technologische Fortschritte im Einbrennofenbau
Moderne Technologien und Innovationen tragen dazu bei, die Effizienz und Nachhaltigkeit von Einbrennöfen zu erhöhen und die Anforderungen an die Beschichtungsqualität zu verbessern.
7.1 Energiesparende Heizsysteme
Durch den Einsatz moderner Heizsysteme wird der Energieverbrauch von Einbrennöfen gesenkt.
- Hocheffiziente Brenner: Neue Brennertechnologien reduzieren den Energieverbrauch und bieten eine hohe Energieausbeute.
- Infrarot- und Hybridheizung: Hybridöfen kombinieren konventionelle Heizmethoden mit Infrarotstrahlung, was die Effizienz steigert und die Produktionskosten senkt.
7.2 KI-gestützte Prozesssteuerung
Künstliche Intelligenz ermöglicht eine präzise Steuerung und kontinuierliche Optimierung des Einbrennprozesses.
- Selbstlernende Steuerungssysteme: KI analysiert die Betriebsdaten und optimiert die Temperaturführung und Luftzirkulation kontinuierlich.
- Prädiktive Wartung: KI erkennt Verschleiß und potenzielle Störungen frühzeitig und schlägt Wartungsmaßnahmen vor, bevor Probleme auftreten.
7.3 Umweltfreundliche Technologien
Die Entwicklung umweltfreundlicher Komponenten im Einbrennofenbau trägt zur Reduzierung des CO₂-Ausstoßes und zur Erfüllung strenger Umweltvorschriften bei.
- Emissionsarme Verbrennung: Die Nutzung emissionsarmer Brennstoffe und Brennertechnologien senkt den CO₂-Ausstoß und schont die Umwelt.
- Fortschrittliche Filtertechnologien: Filteranlagen für Abgase entfernen Schadstoffe und Partikel, um eine saubere Produktion zu gewährleisten.
Fazit
Der Aufbau eines Einbrennofens für die Pulverbeschichtung ist technisch anspruchsvoll und umfasst eine Vielzahl von Komponenten, die präzise aufeinander abgestimmt sind. Von der robusten Gehäusestruktur über das effiziente Heiz- und Luftzirkulationssystem bis hin zu modernen Steuerungs- und Sicherheitsmechanismen – jede Komponente trägt zur Funktionalität und Effizienz des Einbrennofens bei. Innovative Technologien wie KI-gestützte Prozesssteuerung und energiesparende Heizsysteme machen den Einbrennofen zu einem nachhaltigen und effizienten Werkzeug für die industrielle Oberflächenbehandlung. Die kontinuierliche Weiterentwicklung dieser Technologien verspricht eine noch höhere Effizienz, verbesserte Qualitätsstandards und eine umweltfreundlichere Pulverbeschichtung in der Zukunft.
Funktionsweise des Einbrennofens im Pulverbeschichtungsprozess – Phasen, Technologien und Prozessoptimierung
Der Einbrennofen ist eine zentrale Komponente im Pulverbeschichtungsprozess. Er sorgt dafür, dass das aufgebrachte Pulver unter Einwirkung von Hitze schmilzt und sich gleichmäßig über die Oberfläche des Werkstücks verteilt, bevor es zu einer widerstandsfähigen, schützenden Schicht aushärtet. Die Funktionsweise des Einbrennofens ist komplex und umfasst mehrere Phasen und technologisch unterstützte Prozesse, die eine exakte Temperaturführung und Luftzirkulation erfordern, um eine gleichmäßige Aushärtung und hohe Beschichtungsqualität zu gewährleisten.
Dieser Leitfaden beschreibt die Funktionsweise eines Einbrennofens im Detail, von der Vorbereitung bis hin zur Abkühlungsphase, und erläutert dabei auch die Rolle moderner Steuerungstechnologien und innovativer Heizsysteme.
1. Bedeutung und Ziele des Einbrennprozesses
Der Einbrennofen erfüllt eine Vielzahl wichtiger Funktionen, die den Pulverbeschichtungsprozess abrunden und zur Qualität und Beständigkeit der Beschichtung beitragen.
- Schmelzen und Aushärten: Der Ofen erhitzt das Pulver so, dass es auf der Oberfläche des Werkstücks schmilzt und gleichmäßig verteilt, um dann auszuhärten.
- Haftung und Schutz: Durch den Einbrennprozess verbindet sich die Beschichtung fest mit dem Werkstück und wird widerstandsfähig gegen mechanische Belastungen, Chemikalien und Witterungseinflüsse.
- Optische Qualität und Langlebigkeit: Eine gleichmäßige Härtung im Ofen sorgt für eine glatte Oberfläche ohne Risse oder Blasen und verbessert so das optische Erscheinungsbild und die Langlebigkeit der Beschichtung.
2. Funktionsphasen im Einbrennofen
Die Funktionsweise des Einbrennofens lässt sich in mehrere Phasen unterteilen, die sich jeweils ergänzen und für das Endergebnis der Beschichtung entscheidend sind.
2.1 Vorwärmphase
Die Vorwärmphase ist die erste Stufe im Einbrennprozess und dient dazu, die Werkstücke auf eine gleichmäßige Temperatur zu bringen, bevor das Pulver schmilzt.
- Kontrollierte Temperatursteigerung: In dieser Phase wird die Temperatur im Ofen langsam erhöht, um Spannungen in der Pulverschicht zu minimieren und ein gleichmäßiges Schmelzen des Pulvers zu gewährleisten.
- Vermeidung von Defekten: Ein allmählicher Temperaturanstieg verhindert, dass das Pulver zu schnell schmilzt und Blasen oder Risse in der Beschichtung entstehen.
2.2 Schmelz- und Aushärtungsphase
In der Hauptphase des Einbrennprozesses wird die Temperatur konstant gehalten, damit das Pulver vollständig schmilzt und anschließend gleichmäßig aushärtet.
- Schmelzen des Pulvers: Die Schmelztemperatur liegt in der Regel zwischen 160 °C und 220 °C, je nach Material und Pulverart. Das Pulver schmilzt und bildet eine homogene Schicht auf der Oberfläche.
- Aushärtung der Beschichtung: Durch das konstante Halten der Temperatur härtet das Pulver aus und bildet eine feste, widerstandsfähige Schicht. Diese Phase ist entscheidend für die mechanische und chemische Beständigkeit der Beschichtung.
2.3 Abkühlungsphase
Nach dem Aushärten muss das Werkstück langsam abkühlen, um Spannungsrisse und Verformungen zu vermeiden.
- Langsame Abkühlung: Die Temperatur wird kontrolliert gesenkt, damit die Schicht gleichmäßig abkühlt und keine Spannungen entstehen.
- Transport zur Abkühlzone: Nach dem Verlassen des Einbrennofens werden die Werkstücke in eine separate Abkühlzone transportiert, in der sie auf Raumtemperatur gebracht werden.
3. Steuerungs- und Regelungssysteme im Einbrennofen
Die präzise Steuerung und Regelung der Temperatur und Luftzirkulation sind für eine gleichmäßige Aushärtung und hohe Produktqualität essenziell.
3.1 Temperatursteuerung und -regelung
Die Steuerung der Temperatur ist das Herzstück der Funktionsweise des Einbrennofens und beeinflusst maßgeblich die Qualität der Beschichtung.
- Thermoelemente und Temperatursensoren: Diese Sensoren messen die Temperatur im gesamten Ofen und liefern Echtzeitdaten an das Steuerungssystem.
- Automatisierte Temperaturregelung: Die Heizleistung wird je nach gemessener Temperatur angepasst, um eine konstante Wärmeverteilung sicherzustellen und die Effizienz zu steigern.
- Mehrzonensteuerung: Einige Öfen verfügen über eine Mehrzonensteuerung, bei der verschiedene Bereiche des Ofens individuell beheizt werden können, um die Temperaturverteilung weiter zu optimieren.
3.2 Luftzirkulation und Luftstromregelung
Ein effektives Luftzirkulationssystem verteilt die Hitze gleichmäßig im Ofen und sorgt für eine gleichmäßige Aushärtung der Pulverschicht.
- Umluftventilatoren: Leistungsstarke Ventilatoren sorgen dafür, dass die heiße Luft gleichmäßig verteilt wird, wodurch Kältezonen vermieden und eine gleichmäßige Beschichtung erreicht wird.
- Luftkanäle und Steuerung: Spezielle Luftkanäle leiten die heiße Luft gezielt an die Werkstücke, während die Luftzirkulation automatisch reguliert wird, um eine konstante Temperatur beizubehalten.
3.3 Prozessüberwachung und Fehlermanagement
Die Prozessüberwachung ermöglicht eine Echtzeitkontrolle der Funktionsweise des Einbrennofens und ermöglicht eine schnelle Anpassung bei Abweichungen.
- Echtzeitüberwachung: Alle wichtigen Parameter wie Temperatur, Luftzirkulation und Heizleistung werden kontinuierlich überwacht, um eine schnelle Reaktion bei Veränderungen zu gewährleisten.
- Alarm- und Fehlermanagement: Bei Abweichungen von den Sollwerten informiert das System das Bedienpersonal automatisch, sodass schnell korrigierende Maßnahmen ergriffen werden können.
4. Heizsysteme im Einbrennofen
Verschiedene Heizsysteme kommen in Einbrennöfen zum Einsatz, je nach Anforderungen an die Effizienz und die Beschichtung.
4.1 Gasbefeuerte Heizsysteme
Gasheizungen bieten eine kosteneffiziente Lösung und eine schnelle Erwärmung, weshalb sie in vielen industriellen Einbrennöfen zum Einsatz kommen.
- Energieeffizienz: Gasbefeuerte Heizsysteme sind oft effizienter als elektrische Systeme und eignen sich für Anwendungen, bei denen große Ofenräume schnell aufgewärmt werden müssen.
- Wärmeverteilung: Moderne Gasbrenner verteilen die Wärme gleichmäßig und ermöglichen eine präzise Temperatursteuerung.
4.2 Elektrische Heizsysteme
Elektrische Heizsysteme ermöglichen eine präzise Temperaturkontrolle und sind ideal für Umgebungen mit strengen Emissionsanforderungen.
- Präzision: Elektrische Heizungen lassen sich sehr genau steuern und sind daher besonders geeignet für Anwendungen, bei denen die Temperatur stabil bleiben muss.
- Umweltfreundlichkeit: Da sie keine Abgase produzieren, sind elektrische Heizsysteme umweltfreundlich und in emissionssensiblen Bereichen vorteilhaft.
4.3 Infrarot-Heizsysteme
Infrarotstrahler sind eine energieeffiziente Methode zur direkten Erwärmung der Werkstücke und eignen sich besonders für dünne oder temperaturempfindliche Materialien.
- Gezielte Erwärmung: Infrarotstrahlen erwärmen nur die Oberfläche der Werkstücke, wodurch Energie eingespart und die Aushärtungszeit verkürzt wird.
- Flexibilität: Diese Systeme lassen sich schnell ein- und ausschalten und bieten damit eine hohe Flexibilität im Betrieb.
5. Innovationen und technologische Fortschritte in der Funktionsweise des Einbrennofens
Die Technologie der Einbrennöfen entwickelt sich ständig weiter, um Energieverbrauch und Produktionskosten zu senken und die Qualität der Beschichtung zu verbessern.
5.1 Energieeffizienz und Wärmerückgewinnung
Die Wärmerückgewinnung ist ein zentraler Aspekt moderner Einbrennöfen, da sie den Energieverbrauch erheblich senken kann.
- Wärmerückgewinnungssysteme: Abwärme aus dem Ofen wird genutzt, um andere Produktionsschritte wie die Vorbehandlung oder die Vorwärmphase zu unterstützen.
- Verbesserte Isolierung: Hochleistungsdämmstoffe reduzieren den Wärmeverlust und steigern die Effizienz des Einbrennofens.
5.2 KI-gestützte Prozesssteuerung und prädiktive Wartung
Durch die Integration künstlicher Intelligenz kann der Einbrennprozess optimiert und Wartungsbedarf vorhergesagt werden.
- Selbstlernende Steuerung: KI-Systeme analysieren die Daten aus dem Ofenbetrieb und passen die Parameter kontinuierlich an, um den Energieverbrauch zu minimieren und die Produktivität zu erhöhen.
- Prädiktive Wartung: KI-gestützte Wartungssysteme erkennen frühzeitig Anzeichen von Verschleiß und schlagen Wartungsmaßnahmen vor, bevor es zu Ausfällen kommt.
5.3 Automatisierte Temperatur- und Luftzirkulationssteuerung
Automatisierte Steuerungssysteme verbessern die Effizienz des Einbrennofens, indem sie die Parameter an die jeweilige Pulverschicht und Werkstückgeometrie anpassen.
- Automatische Anpassung an Werkstücke: Die Steuerung passt die Heizleistung und Luftzirkulation automatisch an unterschiedliche Werkstückformen an, um eine gleichmäßige Aushärtung zu gewährleisten.
- Echtzeitoptimierung: Sensoren überwachen die Temperatur und Luftzirkulation kontinuierlich und passen die Einstellungen automatisch an, um Schwankungen zu vermeiden.
5.4 Umweltfreundliche Technologien und Emissionsreduzierung
Umweltfreundliche Technologien in modernen Einbrennöfen reduzieren die Emissionen und tragen zur Nachhaltigkeit bei.
- Emissionstechnologien: Filter und Abgassysteme reinigen die Luft und reduzieren schädliche Emissionen.
- Energieoptimierte Brenner: Neue Brennertechnologien nutzen den Brennstoff effizienter und senken den CO₂-Ausstoß.
Fazit
Die Funktionsweise des Einbrennofens im Pulverbeschichtungsprozess ist ein komplexes Zusammenspiel verschiedener Phasen und Technologien, die den Prozess der Pulverbeschichtung auf hohem Qualitätsniveau ermöglichen. Von der Vorwärm- und Schmelzphase bis hin zur Abkühlung – jede Phase des Einbrennprozesses spielt eine entscheidende Rolle für das Endergebnis und die Qualität der Beschichtung. Fortschritte in der Automatisierung, KI-gestützte Prozesssteuerung und energieeffiziente Heizsysteme machen den Einbrennofen zu einem unverzichtbaren und zunehmend nachhaltigen Bestandteil der modernen Beschichtungstechnologie.
Arten von Einbrennöfen im Pulverbeschichtungsprozess – Typen, Eigenschaften und Einsatzbereiche
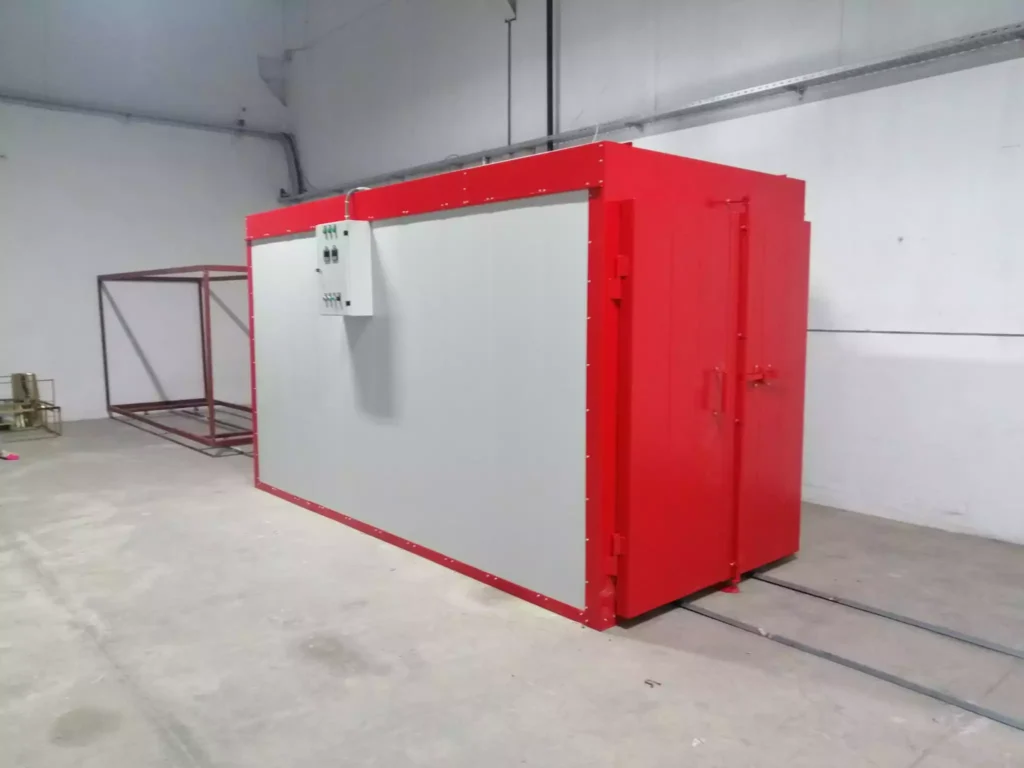
Einbrennöfen sind essenzielle Bestandteile im Pulverbeschichtungsprozess. Sie sorgen dafür, dass das aufgetragene Pulver unter Hitzeeinwirkung schmilzt, sich gleichmäßig verteilt und zu einer beständigen und schützenden Beschichtung aushärtet. Es gibt verschiedene Arten von Einbrennöfen, die jeweils unterschiedliche Eigenschaften und Vorteile bieten und sich für unterschiedliche Anwendungen und Materialien eignen. Von klassischen Umluftöfen über moderne Infrarotöfen bis hin zu Hybridsystemen ermöglicht die Vielfalt an Einbrennöfen eine optimale Anpassung an spezifische Anforderungen.
Dieser Leitfaden beschreibt die verschiedenen Arten von Einbrennöfen im Detail und geht auf ihre Funktionsweise, spezifische Merkmale und die typischen Einsatzgebiete ein.
1. Umluft-Einbrennöfen
Der Umluft-Einbrennofen ist einer der am weitesten verbreiteten Ofentypen in der Pulverbeschichtung und wird wegen seiner gleichmäßigen Wärmeverteilung und hohen Energieeffizienz geschätzt.
1.1 Funktionsweise des Umluft-Einbrennofens
Im Umluftofen wird die Wärme mithilfe von Ventilatoren und Luftführungssystemen gleichmäßig im gesamten Ofenraum verteilt.
- Wärmeverteilung: Umluftventilatoren sorgen dafür, dass die heiße Luft in einem gleichmäßigen Kreislauf zirkuliert und die Werkstücke aus allen Richtungen gleichmäßig erhitzt werden.
- Luftführungssysteme: Spezielle Kanäle leiten die Luft so, dass sie alle Bereiche des Ofens erreicht, was eine gleichmäßige Aushärtung ermöglicht.
1.2 Vorteile und Nachteile des Umluftofens
- Vorteile:
- Gleichmäßige Erwärmung auch bei komplexen Werkstückgeometrien
- Hohe Energieeffizienz durch Umluftsysteme
- Flexibilität für verschiedene Pulverbeschichtungsmaterialien
- Nachteile:
- Benötigt längere Aufheizzeit im Vergleich zu Strahlungsöfen
- Höherer Wartungsaufwand für Umluftventilatoren und Filter
1.3 Einsatzgebiete des Umluftofens
Umluftöfen sind ideal für große und komplex geformte Werkstücke, die eine gleichmäßige Erwärmung benötigen, und kommen in der Automobilindustrie, im Maschinenbau sowie in der Elektro- und Bauindustrie zum Einsatz.
2. Infrarot-Einbrennöfen
Infrarot-Einbrennöfen nutzen Infrarotstrahlung, um die Werkstücke direkt zu erwärmen. Diese Art von Ofen wird vor allem wegen ihrer schnellen Aufheizzeit und Energieeffizienz geschätzt.
2.1 Funktionsweise des Infrarotofens
Infrarotöfen erzeugen Strahlungswärme, die das Pulver auf der Oberfläche des Werkstücks direkt erwärmt.
- Gezielte Erwärmung: Infrarotstrahler erhitzen das Werkstück direkt, ohne dass die gesamte Luft im Ofenraum aufgeheizt werden muss. Dies spart Energie und verkürzt die Aufheizzeit.
- Schnelle Temperaturregelung: Die Strahlungswärme lässt sich präzise und schnell anpassen, was die Effizienz und Flexibilität des Prozesses erhöht.
2.2 Vorteile und Nachteile des Infrarotofens
- Vorteile:
- Sehr schnelle Aufheiz- und Abkühlzeiten
- Geringer Energieverbrauch durch gezielte Erwärmung der Oberfläche
- Ideal für dünne oder temperaturempfindliche Materialien
- Nachteile:
- Weniger geeignet für dickwandige oder große Werkstücke, da die Erwärmung oft nur oberflächlich erfolgt
- Höhere Anschaffungskosten im Vergleich zu Umluftöfen
2.3 Einsatzgebiete des Infrarotofens
Infrarotöfen eignen sich hervorragend für kleine bis mittelgroße Werkstücke, die schnelle Aufheizzeiten erfordern, und werden häufig in der Elektronikindustrie, Möbelindustrie und bei der Beschichtung von Kunststoffteilen verwendet.
3. Hybrid- oder Kombiöfen
Hybridöfen kombinieren Umluft- und Infrarottechnologie, um die Vorteile beider Heizsysteme zu nutzen. Sie sind besonders vielseitig und bieten eine hohe Flexibilität für verschiedene Beschichtungsanforderungen.
3.1 Funktionsweise des Hybridofens
Ein Hybridofen verwendet sowohl Umluft- als auch Infrarotwärme, um eine schnelle und gleichmäßige Erwärmung der Werkstücke zu gewährleisten.
- Kombinierte Erwärmung: Der Ofen beginnt oft mit einer schnellen Erwärmung durch Infrarotstrahlung und schaltet dann auf Umluftbetrieb um, um eine gleichmäßige Aushärtung sicherzustellen.
- Anpassbare Einstellungen: Die Heizmethoden können je nach Werkstückgröße und Material individuell angepasst werden.
3.2 Vorteile und Nachteile des Hybridofens
- Vorteile:
- Flexibilität, um verschiedene Werkstückgrößen und -materialien zu verarbeiten
- Energieeinsparung durch gezielte Nutzung beider Heizmethoden
- Hohe Produktionsgeschwindigkeit durch schnelle Aufheizzeit und gleichmäßige Aushärtung
- Nachteile:
- Höhere Anschaffungskosten und komplexere Wartung
- Benötigt mehr Platz aufgrund der integrierten Heizsysteme
3.3 Einsatzgebiete des Hybridofens
Hybridöfen sind ideal für Produktionsanlagen mit einem breiten Spektrum an Werkstücken und Materialien. Sie finden häufig in der Automobilindustrie, im Maschinenbau und bei der Beschichtung von Haushaltsgeräten Anwendung.
4. Durchlauföfen
Durchlauföfen sind kontinuierlich betriebene Öfen, die mit einem Fördersystem ausgestattet sind und einen ununterbrochenen Materialfluss ermöglichen. Sie sind besonders geeignet für große Produktionsvolumen und Serienfertigung.
4.1 Funktionsweise des Durchlaufofens
In einem Durchlaufofen werden die Werkstücke auf einem Förderband oder an einer Hängebahn durch den Ofen transportiert.
- Kontinuierliche Erwärmung: Die Werkstücke durchlaufen den Ofen in einem kontinuierlichen Fluss und werden dabei gleichmäßig erhitzt und gehärtet.
- Temperaturzonen: Der Ofen ist häufig in verschiedene Temperaturzonen unterteilt, um eine gleichmäßige Erwärmung, Aushärtung und Abkühlung zu gewährleisten.
4.2 Vorteile und Nachteile des Durchlaufofens
- Vorteile:
- Hohe Produktionsgeschwindigkeit und Effizienz durch kontinuierlichen Betrieb
- Ideal für große Produktionsmengen und Serienfertigung
- Reduzierte Handhabungszeiten und nahtloser Produktionsfluss
- Nachteile:
- Weniger flexibel für unterschiedliche Werkstückgrößen und -formen
- Hohe Investitionskosten und größerer Platzbedarf
4.3 Einsatzgebiete des Durchlaufofens
Durchlauföfen sind optimal für die Massenproduktion und werden in der Automobilindustrie, der Bauindustrie und bei der Herstellung von Konsumgütern eingesetzt, die in großen Stückzahlen beschichtet werden.
5. Kammer- oder Chargenöfen
Kammeröfen, auch Chargenöfen genannt, sind geschlossene Einheiten, die speziell für kleinere Produktionsvolumen und spezielle Anwendungen entwickelt wurden. Sie ermöglichen die Verarbeitung einer definierten Anzahl von Werkstücken in einem abgeschlossenen Raum.
5.1 Funktionsweise des Kammerofens
Kammeröfen arbeiten im Batch-Betrieb, das heißt, die Werkstücke werden in die Kammer geladen, erhitzt und nach dem Aushärten entnommen.
- Batch-Verfahren: Die Werkstücke werden in Chargen behandelt, was eine gezielte Steuerung und Anpassung der Parameter für jede Charge ermöglicht.
- Präzise Steuerung: Die Temperatur und Aushärtungszeit lassen sich genau steuern, um eine hohe Qualität für spezielle Beschichtungsanforderungen sicherzustellen.
5.2 Vorteile und Nachteile des Kammerofens
- Vorteile:
- Hohe Flexibilität für kleine Serien und Sonderbeschichtungen
- Präzise Steuerung der Temperatur und Aushärtungszeit
- Geringer Platzbedarf und kostengünstigere Anschaffung im Vergleich zu Durchlauföfen
- Nachteile:
- Geringere Produktionsgeschwindigkeit, da der Batch-Betrieb zusätzliche Lade- und Entladezeiten erfordert
- Begrenzte Kapazität und nicht geeignet für Massenproduktion
5.3 Einsatzgebiete des Kammerofens
Kammeröfen werden in Werkstätten und spezialisierten Produktionsanlagen eingesetzt, die kleinere Stückzahlen oder beschichtete Prototypen herstellen. Sie sind ideal für die Luft- und Raumfahrtindustrie, medizinische Geräte und andere spezialisierte Anwendungen.
6. Hochtemperatur-Einbrennöfen
Hochtemperaturöfen sind speziell für Anwendungen ausgelegt, die extrem hohe Temperaturen erfordern, etwa für Pulverlacke, die bei höheren Temperaturen aushärten müssen oder bei Anwendungen, bei denen spezielle Beschichtungen eine hohe Temperaturbeständigkeit erfordern.
6.1 Funktionsweise des Hochtemperaturofens
Diese Öfen erreichen Temperaturen weit über den üblichen Aushärtungsgraden und werden sorgfältig überwacht, um eine stabile Wärmeverteilung zu gewährleisten.
- Erweiterter Temperaturbereich: Hochtemperaturöfen erreichen Temperaturen bis zu 400 °C oder höher und ermöglichen so die Aushärtung spezieller Beschichtungsmaterialien.
- Präzise Temperaturkontrolle: Eine genaue Steuerung ist notwendig, um Überhitzung und Schäden an empfindlichen Materialien zu vermeiden.
6.2 Vorteile und Nachteile des Hochtemperaturofens
- Vorteile:
- Geeignet für spezielle Anwendungen, die hohe Temperaturen erfordern
- Ermöglicht die Verarbeitung hochtemperaturbeständiger Pulverlacke
- Nachteile:
- Hoher Energieverbrauch und erhöhter Wartungsaufwand
- Hohe Anschaffungskosten und größere Sicherheitsanforderungen
6.3 Einsatzgebiete des Hochtemperaturofens
Hochtemperaturöfen werden vor allem in Industrien eingesetzt, die spezialisierte Beschichtungen benötigen, wie die Luft- und Raumfahrt, die Elektronikbranche und der Energiesektor, wo hitzebeständige Materialien eine Rolle spielen.
Fazit
Die verschiedenen Arten von Einbrennöfen im Pulverbeschichtungsprozess bieten eine breite Palette an Optionen, die es ermöglichen, den Aushärtungsprozess optimal an die spezifischen Anforderungen von Werkstücken und Beschichtungsmaterialien anzupassen. Von den energieeffizienten Umluft- und Infrarotöfen bis zu den spezialisierten Hybrid- und Hochtemperaturöfen ist für jede Anwendung und Produktionsanforderung ein passender Ofentyp verfügbar. Die kontinuierliche Weiterentwicklung der Ofentechnologie und der Einsatz moderner Steuerungssysteme tragen dazu bei, die Effizienz zu steigern, die Qualität der Beschichtungen zu verbessern und die Nachhaltigkeit in der Pulverbeschichtungsindustrie zu fördern.
Innovationen und Technologien im Einbrennofen – Fortschritte zur Effizienzsteigerung, Qualitätsverbesserung und Nachhaltigkeit
Die Einbrennöfen, die im Pulverbeschichtungsprozess verwendet werden, haben sich in den letzten Jahren aufgrund technologischer Fortschritte und innovativer Entwicklungen stark gewandelt. Neue Technologien und Systeme verbessern die Effizienz, verringern den Energieverbrauch und fördern eine nachhaltigere Produktion. Intelligente Steuerungen, innovative Heiztechnologien, umweltfreundliche Systeme und automatisierte Prozesse sorgen dafür, dass moderne Einbrennöfen höhere Qualitätsstandards erreichen und zugleich die Betriebskosten und den ökologischen Fußabdruck verringern.
In diesem Leitfaden werden die wesentlichen Innovationen und Technologien im Bereich der Einbrennöfen vorgestellt, die zur Verbesserung des Pulverbeschichtungsprozesses beitragen.
1. Intelligente Steuerungssysteme und Automatisierung
Die Steuerung der Temperatur und Luftzirkulation im Einbrennofen ist entscheidend für die gleichmäßige Aushärtung und die Qualität der Beschichtung. Intelligente Steuerungssysteme ermöglichen eine präzise Überwachung und Anpassung der Parameter.
1.1 Automatisierte Temperatur- und Luftstromsteuerung
Moderne Steuerungssysteme passen die Heizleistung und Luftzirkulation automatisch an die jeweiligen Anforderungen des Beschichtungsprozesses an.
- Temperaturkontrolle in Echtzeit: Sensoren überwachen die Temperatur kontinuierlich und passen die Heizleistung in Echtzeit an, um Schwankungen zu vermeiden und die ideale Aushärtungsbedingung aufrechtzuerhalten.
- Mehrzonensteuerung: Die Möglichkeit, den Ofen in mehrere Temperaturzonen zu unterteilen, sorgt für eine präzisere Steuerung. Jede Zone kann individuell beheizt werden, um die Temperatur je nach Position im Ofen zu regulieren und Energie zu sparen.
1.2 KI-gestützte Prozesssteuerung
Künstliche Intelligenz (KI) bietet neue Möglichkeiten zur Steuerung und Optimierung des Einbrennofens und kann zur Effizienzsteigerung beitragen.
- Selbstlernende Systeme: KI-Algorithmen analysieren Betriebsdaten und passen die Steuerung automatisch an, um die optimale Aushärtungstemperatur und -zeit zu finden. Dies minimiert Energieverbrauch und Materialabfall.
- Prädiktive Wartung: KI-Systeme können frühzeitig Verschleiß oder Probleme erkennen und vorausschauende Wartungsmaßnahmen empfehlen, bevor es zu Ausfällen kommt. Das erhöht die Betriebssicherheit und minimiert Ausfallzeiten.
2. Energieeffiziente Heizsysteme und Wärmerückgewinnung
Die Reduktion des Energieverbrauchs ist eine zentrale Herausforderung moderner Einbrennöfen, da das Erhitzen von Werkstücken einen erheblichen Teil der Produktionskosten ausmacht.
2.1 Infrarot-Heiztechnologie
Infrarotstrahler ermöglichen eine direkte Erwärmung der Werkstückoberfläche, wodurch der Energieverbrauch erheblich reduziert werden kann.
- Schnelle Erwärmung: Infrarotstrahler erwärmen das Werkstück direkt, ohne dass der gesamte Ofenraum erhitzt werden muss. Dies führt zu einer schnelleren Aufheizzeit und spart Energie.
- Temperaturpräzision: Die Strahlungswärme lässt sich gezielt steuern, was besonders für temperaturempfindliche Werkstücke vorteilhaft ist.
2.2 Wärmerückgewinnungssysteme
Wärmerückgewinnungssysteme nutzen die Abwärme des Ofens, um andere Produktionsschritte zu unterstützen, was den Gesamtenergieverbrauch reduziert.
- Wiederverwendung der Abwärme: Die Abwärme wird in anderen Prozessen, wie beispielsweise der Vorwärmphase oder der Werkstücktrocknung, genutzt. Dadurch kann der Energieverbrauch erheblich gesenkt werden.
- Integrierte Wärmespeicherung: Einige Systeme speichern die überschüssige Wärme und geben sie bei Bedarf an andere Produktionsbereiche ab.
2.3 Hocheffiziente Brenner
Neue Brennertechnologien tragen dazu bei, den Brennstoffverbrauch zu reduzieren und den Wirkungsgrad des Einbrennofens zu erhöhen.
- Moderne Gasbrenner: Gasbrenner mit optimierter Verbrennungstechnik ermöglichen eine gleichmäßige Wärmeverteilung und einen niedrigeren Gasverbrauch.
- Elektrische Heizungen mit hoher Präzision: Elektrische Heizelemente bieten eine präzise Steuerung der Temperatur und eignen sich besonders für Umgebungen mit strengen Emissionsanforderungen.
3. Umweltfreundliche Technologien und Emissionskontrolle
In Zeiten zunehmender Umweltanforderungen und gesetzlicher Vorgaben wird die Entwicklung umweltfreundlicher Einbrennöfen immer wichtiger.
3.1 Abgasreinigung und Filtertechnologien
Die Minimierung von Emissionen ist ein zentrales Ziel moderner Einbrennöfen, insbesondere in energieintensiven Industrien.
- Partikelfilter und Katalysatoren: Moderne Filter entfernen schädliche Partikel und reduzieren den CO₂-Ausstoß. Katalysatoren tragen zur Umwandlung von Schadstoffen in unschädliche Bestandteile bei.
- Abgasrückführung: Einige Systeme führen die Abgase zurück in den Ofen und nutzen sie erneut, was den Energieverbrauch weiter senkt und Emissionen minimiert.
3.2 Niedrigtemperatur-Beschichtungspulver
Neue Pulverlacke, die bei niedrigeren Temperaturen aushärten, ermöglichen eine erhebliche Reduktion des Energieverbrauchs.
- Niedrigere Aushärtungstemperaturen: Diese Pulver benötigen eine niedrigere Aushärtungstemperatur, wodurch der Einbrennofen weniger Energie verbraucht.
- Einsatzmöglichkeiten auf temperaturempfindlichen Werkstoffen: Diese Pulvertechnologie erweitert die Anwendungsbereiche der Pulverbeschichtung und ermöglicht die Beschichtung von temperaturempfindlichen Materialien wie Kunststoffen.
4. Automatisierte Farbwechsel- und Reinigungssysteme
Automatisierte Farbwechsel- und Reinigungssysteme verbessern die Flexibilität und Effizienz des Einbrennofens und erleichtern die Wartung.
4.1 Farbschnellwechsel-Technologie
Farbschnellwechselsysteme erlauben es, verschiedene Beschichtungsfarben rasch zu wechseln, was besonders bei kleinen Losgrößen und häufigen Farbwechseln nützlich ist.
- Automatisierte Reinigung der Sprühsysteme: Durch automatische Reinigungsvorrichtungen wird das Sprühsystem zwischen den Farbwechseln gereinigt, ohne den Betrieb zu unterbrechen.
- Schneller Wechsel bei gleichbleibender Qualität: Der Wechsel erfolgt in wenigen Minuten, was die Stillstandzeiten minimiert und die Produktionsflexibilität erhöht.
4.2 Selbstreinigende Filter- und Luftsysteme
Selbstreinigende Systeme reduzieren den Wartungsaufwand und sorgen dafür, dass die Luftzirkulation und Filter sauber bleiben.
- Automatische Filterreinigung: Durch spezielle Luftdüsen und Filtersysteme werden Staub und Rückstände automatisch entfernt, was die Standzeit der Filter verlängert.
- Verringerung der Emissionsbelastung: Selbstreinigende Filter fangen Partikel auf und reduzieren die Emissionen, wodurch der Einbrennofen umweltfreundlicher wird.
5. Innovative Fördersysteme und Zonensteuerung
Moderne Fördersysteme und Zonensteuerungen verbessern die Effizienz und ermöglichen eine höhere Flexibilität im Einbrennprozess.
5.1 Anpassbare Fördersysteme
Fördersysteme transportieren die Werkstücke durch den Ofen und beeinflussen die Verweildauer und somit die Aushärtung der Beschichtung.
- Geschwindigkeitssteuerung: Die Geschwindigkeit des Fördersystems lässt sich automatisch anpassen, um die optimale Verweildauer im Ofen für jede Werkstückart sicherzustellen.
- Hitzebeständige Materialien: Neue Materialien für Förderketten und -bänder erhöhen die Lebensdauer des Fördersystems und reduzieren den Wartungsaufwand.
5.2 Mehrzonensteuerung im Ofenraum
Die Möglichkeit, den Einbrennofen in verschiedene Temperaturzonen zu unterteilen, bietet eine präzisere Kontrolle der Aushärtung.
- Individuell beheizbare Zonen: Verschiedene Bereiche des Ofens können auf unterschiedliche Temperaturen eingestellt werden, was eine individuelle Anpassung an die Werkstückgröße und -material ermöglicht.
- Energieeinsparung durch Zonenkontrolle: Unnötige Heizleistung wird reduziert, was den Energieverbrauch senkt und die Effizienz steigert.
6. Digitalisierung und Industrie 4.0 im Einbrennofen
Die Integration digitaler Technologien und die Vernetzung der Einbrennöfen eröffnen neue Möglichkeiten zur Prozessoptimierung und Fehlererkennung.
6.1 Echtzeit-Datenüberwachung und Analyse
Digitale Systeme überwachen die Betriebsparameter des Einbrennofens in Echtzeit und ermöglichen eine sofortige Anpassung.
- Echtzeitüberwachung der Temperatur, Luftzirkulation und Abgase: Daten werden kontinuierlich erfasst und analysiert, um eine gleichmäßige Beschichtung zu gewährleisten.
- Prozessoptimierung durch Datenanalyse: Durch die Analyse der Daten können potenzielle Probleme frühzeitig erkannt und die Prozesse kontinuierlich optimiert werden.
6.2 Vernetzte Systeme und Fernsteuerung
Dank der IoT-Technologie können Einbrennöfen in vernetzte Systeme integriert und aus der Ferne überwacht und gesteuert werden.
- Fernzugriff und Steuerung: Anlagenbediener können den Einbrennofen über mobile Geräte überwachen und bei Bedarf Anpassungen vornehmen.
- Fehlererkennung und Fernwartung: Im Falle von Störungen kann die Fehlerbehebung oft über die Ferndiagnose durchgeführt werden, was Stillstandzeiten reduziert und die Effizienz steigert.
7. Künftige Entwicklungen in der Einbrennofentechnologie
Die Einbrennofentechnologie wird sich weiterentwickeln, um den wachsenden Anforderungen an Effizienz und Nachhaltigkeit gerecht zu werden.
7.1 Integration erneuerbarer Energien
Die Nutzung erneuerbarer Energien, wie Solar- oder Windkraft, zur Stromversorgung des Einbrennofens wird zunehmend attraktiv.
- Solar- und Windenergie für elektrische Heizsysteme: Diese saubere Energiequelle kann in elektrischen Heizsystemen zur Unterstützung eingesetzt werden und hilft, den CO₂-Ausstoß zu senken.
- Energieversorgung durch Energiespeicher: Fortschrittliche Batteriesysteme können erneuerbare Energie speichern und für den Betrieb des Einbrennofens nutzbar machen.
7.2 Entwicklung von Niedrigenergie-Einbrennöfen
Niedrigenergie-Öfen sind ein wachsender Trend in der Branche und zielen darauf ab, den Energieverbrauch weiter zu senken und die Betriebskosten zu minimieren.
- Verbesserte Isolierung und Materialinnovationen: Materialien, die Wärme besser speichern und die Effizienz steigern, sind im Einsatz.
- Optimierte Luftführung und Wärmerückgewinnung: Neue Designs für Luftführung und Wärmerückgewinnungssysteme machen den Einbrennofen noch energieeffizienter.
Fazit
Die Innovationen und technologischen Fortschritte im Bereich der Einbrennöfen tragen erheblich zur Effizienz, Qualität und Nachhaltigkeit des Pulverbeschichtungsprozesses bei. Intelligente Steuerungssysteme, energieeffiziente Heiz- und Wärmerückgewinnungssysteme, automatisierte Farbwechsel- und Reinigungstechniken sowie digitale Überwachungs- und Optimierungstools machen den modernen Einbrennofen zu einem leistungsfähigen und zukunftssicheren Bestandteil der Industrie. Angesichts der wachsenden Anforderungen an Umweltverträglichkeit und Effizienz wird die Weiterentwicklung der Einbrennofentechnologie auch in Zukunft von zentraler Bedeutung für die Pulverbeschichtungsindustrie sein.
Steuerung und Automatisierung im Einbrennofen – Technologien, Prozesse und Optimierung für maximale Effizienz
Die Steuerung und Automatisierung des Einbrennofens spielen eine zentrale Rolle für die Effizienz, Qualität und Nachhaltigkeit des Pulverbeschichtungsprozesses. Ein Einbrennofen muss präzise gesteuert werden, um eine gleichmäßige Aushärtung der Pulverschicht zu gewährleisten. Die Automatisierung dieser Prozesse, unterstützt durch intelligente Steuerungssysteme und Sensorik, ermöglicht eine genaue Kontrolle der Parameter wie Temperatur, Luftzirkulation und Verweildauer. Innovative Technologien wie KI-gestützte Steuerungen und prädiktive Wartungssysteme verbessern die Betriebseffizienz und minimieren Ausfallzeiten und Kosten.
Dieser Leitfaden beschreibt die wichtigen Aspekte und Technologien der Steuerung und Automatisierung in modernen Einbrennöfen, von der Temperaturkontrolle und Luftzirkulation bis hin zu den neuesten Entwicklungen in der prädiktiven Wartung und vernetzten Systemen.
1. Bedeutung der Steuerung und Automatisierung im Einbrennofen
Die Steuerung und Automatisierung sind entscheidend für die präzise und gleichmäßige Aushärtung der Pulverschicht. Sie beeinflussen die Effizienz des Ofens, die Qualität der Beschichtung und die Betriebskosten.
- Gleichmäßige Aushärtung: Eine präzise Steuerung der Temperatur und Luftzirkulation ist notwendig, um die Schichtdicke konstant zu halten und die gewünschte Beständigkeit und Oberflächenqualität zu erreichen.
- Effizienz und Kostenersparnis: Automatisierte Systeme optimieren die Energie- und Materialnutzung und tragen so zur Senkung der Betriebskosten bei.
- Qualitätskontrolle: Durch intelligente Steuerungssysteme wird die Beschichtungsqualität konstant überwacht und angepasst, was Defekte und Nacharbeit minimiert.
2. Temperaturregelung im Einbrennofen
Die Steuerung und Regelung der Temperatur im Einbrennofen ist der wichtigste Faktor für die erfolgreiche Aushärtung des Pulvers und die Qualität der Beschichtung.
2.1 Echtzeit-Temperaturüberwachung
Die Echtzeitüberwachung der Temperatur durch Thermoelemente und Sensoren stellt sicher, dass die Temperatur im Ofen gleichmäßig bleibt.
- Thermoelemente und Temperatursensoren: Diese Sensoren messen die Temperatur an verschiedenen Punkten im Ofen und liefern kontinuierlich Daten an das Steuerungssystem.
- Temperaturstabilität: Die Sensoren erkennen Schwankungen und leiten die Information sofort an die Steuerung weiter, die die Heizleistung anpasst, um eine konstante Temperatur zu halten.
2.2 Mehrzonensteuerung
Einbrennöfen werden oft in mehrere Zonen unterteilt, die individuell beheizt werden können, um eine präzise Temperaturregelung zu ermöglichen.
- Individuell beheizbare Zonen: Jede Zone im Einbrennofen kann separat kontrolliert werden, sodass bestimmte Bereiche unterschiedlich beheizt werden können, um den Energieverbrauch zu optimieren.
- Temperaturzonen für variable Werkstückgrößen: Die Mehrzonensteuerung ermöglicht eine flexible Anpassung an Werkstücke unterschiedlicher Größe und Geometrie, was eine gleichmäßige Aushärtung gewährleistet.
2.3 Automatische Anpassung der Heizleistung
Die Heizleistung wird automatisch an die Beladung und die jeweilige Phase des Einbrennprozesses angepasst.
- Lastabhängige Steuerung: Das System erkennt die Menge der Werkstücke im Ofen und reguliert die Heizleistung entsprechend, um Energie zu sparen und die Temperatur konstant zu halten.
- Energieeffizienz durch Bedarfssteuerung: Durch eine bedarfsgerechte Steuerung der Heizleistung kann der Energieverbrauch gesenkt und die Betriebskosten reduziert werden.
3. Luftzirkulation und Luftstromregelung
Eine effiziente Luftzirkulation ist entscheidend für die gleichmäßige Wärmeverteilung und die Vermeidung von Kältezonen im Einbrennofen.
3.1 Umluftventilatoren und Luftführungssysteme
Umluftventilatoren sorgen dafür, dass die heiße Luft gleichmäßig im Ofen zirkuliert und so alle Werkstücke gleichmäßig erwärmt werden.
- Luftkanäle und Verteilsysteme: Spezielle Luftführungssysteme lenken die Luft gezielt in den Ofenraum, um Kältezonen zu vermeiden und eine gleichmäßige Verteilung der Wärme zu gewährleisten.
- Automatisierte Luftzirkulationssteuerung: Die Luftzirkulation wird kontinuierlich überwacht und bei Bedarf automatisch angepasst, um eine konstante Temperatur und Luftqualität sicherzustellen.
3.2 Luftqualität und Feuchtigkeitskontrolle
Die Kontrolle der Luftqualität und der Feuchtigkeit im Ofen ist für bestimmte Pulverbeschichtungen und Materialien essenziell.
- Feuchtigkeitssensoren: Sensoren überwachen die Luftfeuchtigkeit und sorgen dafür, dass die Beschichtung nicht durch zu hohe Feuchtigkeit beeinträchtigt wird.
- Luftqualitätsmanagement: Bei Bedarf wird die Luft im Ofen durch Filter und Lüftungssysteme gereinigt, um Staub und Verunreinigungen zu reduzieren und eine saubere Beschichtung zu gewährleisten.
4. KI-gestützte Steuerung und prädiktive Wartung
Die Integration künstlicher Intelligenz und prädiktiver Wartungssysteme verbessert die Effizienz und Zuverlässigkeit moderner Einbrennöfen und minimiert Ausfallzeiten.
4.1 Künstliche Intelligenz zur Prozessoptimierung
KI-gestützte Systeme analysieren die Betriebsdaten des Einbrennofens und passen die Parameter automatisch an, um den Betrieb zu optimieren.
- Selbstlernende Algorithmen: KI-Algorithmen lernen aus vergangenen Daten und passen die Steuerung an, um den Energieverbrauch zu reduzieren und die Aushärtungsqualität zu verbessern.
- Optimierung der Heizzyklen: KI-Systeme analysieren den Einbrennprozess und passen die Heizzyklen automatisch an, um Energie zu sparen und die Produktivität zu steigern.
4.2 Prädiktive Wartung und Fehlererkennung
Prädiktive Wartungssysteme verwenden KI, um den Zustand des Einbrennofens zu überwachen und potenzielle Probleme frühzeitig zu erkennen.
- Analyse von Sensordaten: Sensoren erfassen Daten wie Temperatur, Luftdruck und Luftqualität, die von der KI analysiert werden, um Abweichungen oder Anzeichen von Verschleiß zu erkennen.
- Automatische Wartungsbenachrichtigungen: Das System informiert das Wartungsteam automatisch über bevorstehende Wartungsarbeiten oder mögliche Probleme, um die Betriebssicherheit zu erhöhen und unerwartete Ausfälle zu verhindern.
5. Automatisierung der Prozesssteuerung
Automatisierte Prozesssteuerungen erleichtern die Handhabung des Einbrennofens und verbessern die Effizienz und Flexibilität im Betrieb.
5.1 Anpassbare Prozessparameter
Automatisierte Steuerungssysteme ermöglichen die flexible Anpassung der Prozessparameter an die verschiedenen Werkstückarten und Beschichtungsmaterialien.
- Automatische Anpassung an Werkstücktypen: Der Einbrennofen passt die Parameter automatisch an, je nachdem, welche Art von Werkstücken oder Materialien beschichtet werden.
- Rezeptverwaltung: Die Steuerung speichert verschiedene „Rezepte“ für spezifische Beschichtungsanforderungen, sodass der Ofen für unterschiedliche Produkte schnell und einfach konfiguriert werden kann.
5.2 Echtzeitüberwachung und Prozessvisualisierung
Die Überwachung und Visualisierung des Einbrennprozesses in Echtzeit erleichtern die Kontrolle und Anpassung des Betriebs.
- Echtzeit-Datenanzeige: Alle relevanten Daten wie Temperatur, Luftzirkulation und Verweildauer werden in Echtzeit angezeigt, um eine sofortige Reaktion auf Abweichungen zu ermöglichen.
- Visualisierung des Prozesses: Eine grafische Darstellung des Prozesses hilft dem Bedienpersonal, die Einstellungen des Einbrennofens zu überwachen und anzupassen.
6. Vernetzte Systeme und Industrie 4.0 im Einbrennofen
Mit der Integration digitaler Technologien und der Vernetzung der Anlagen entstehen neue Möglichkeiten zur Optimierung des Einbrennprozesses.
6.1 IoT-fähige Komponenten und Remote-Steuerung
IoT-fähige Komponenten ermöglichen die Vernetzung des Einbrennofens und den Fernzugriff auf die Steuerungssysteme.
- Fernüberwachung und -steuerung: Techniker können den Einbrennofen remote überwachen und bei Bedarf Anpassungen vornehmen, was die Flexibilität erhöht und die Betriebszeit verbessert.
- Prozessdatenanalyse über das Netzwerk: Die Produktionsdaten können in Echtzeit an zentrale Steuerungssysteme gesendet und zur Prozessoptimierung verwendet werden.
6.2 Datenanalyse und kontinuierliche Prozessoptimierung
Die Datenanalyse im Rahmen von Industrie 4.0 ermöglicht eine kontinuierliche Optimierung und Anpassung des Einbrennprozesses.
- Datengetriebene Entscheidungen: Die Analyse historischer und aktueller Daten ermöglicht es, den Einbrennprozess auf der Grundlage konkreter Informationen zu optimieren und die Produktivität zu steigern.
- Fehleranalyse und Prozessverbesserung: Daten zu Betriebsstörungen und Wartungsarbeiten werden analysiert, um Schwachstellen zu identifizieren und den Einbrennofen kontinuierlich zu verbessern.
7. Zukunft der Steuerung und Automatisierung im Einbrennofen
Mit der kontinuierlichen Weiterentwicklung digitaler Technologien und Automatisierungslösungen wird die Steuerung und Automatisierung im Einbrennofen weiter optimiert und an die Anforderungen einer nachhaltigen Industrie angepasst.
7.1 Integration von erneuerbaren Energien und Energieoptimierung
Einbrennöfen, die mit erneuerbaren Energien betrieben werden, bieten eine umweltfreundliche und kosteneffiziente Alternative zu konventionellen Energiequellen.
- Nutzung von Solar- und Windenergie: Erneuerbare Energien können zur Stromversorgung des Einbrennofens genutzt werden, was den CO₂-Ausstoß senkt.
- Energieoptimierung durch fortschrittliche Steuerung: Intelligente Steuerungssysteme passen den Energieverbrauch automatisch an die Produktionsanforderungen an und optimieren den Einsatz erneuerbarer Energien.
7.2 Entwicklung selbstoptimierender Systeme
Zukünftig wird die Steuerung des Einbrennofens zunehmend autonom durch selbstoptimierende Systeme erfolgen, die kontinuierlich lernen und sich anpassen.
- Selbststeuernde Systeme: Systeme, die in der Lage sind, sich automatisch an verschiedene Werkstücke und Beschichtungsanforderungen anzupassen, erhöhen die Flexibilität und Effizienz des Einbrennofens.
- Kombination aus KI und Machine Learning: Diese Technologien ermöglichen die Entwicklung von Systemen, die sich selbst optimieren, indem sie aus dem laufenden Betrieb lernen und die Steuerungsparameter kontinuierlich anpassen.
Fazit
Die Steuerung und Automatisierung des Einbrennofens sind entscheidend für die Effizienz, Produktqualität und Nachhaltigkeit des Pulverbeschichtungsprozesses. Durch den Einsatz moderner Technologien wie KI-gestützte Systeme, Echtzeit-Überwachung, IoT und Industrie-4.0-Vernetzung lassen sich Betriebskosten senken, die Produktivität steigern und die Umweltbelastung reduzieren. Die Integration erneuerbarer Energien und selbstoptimierender Steuerungssysteme bietet zudem eine zukunftsfähige Lösung, die den Anforderungen an eine umweltfreundliche Produktion gerecht wird und den Pulverbeschichtungsprozess weiter verbessert.
Pulverbeschichtungsanlage
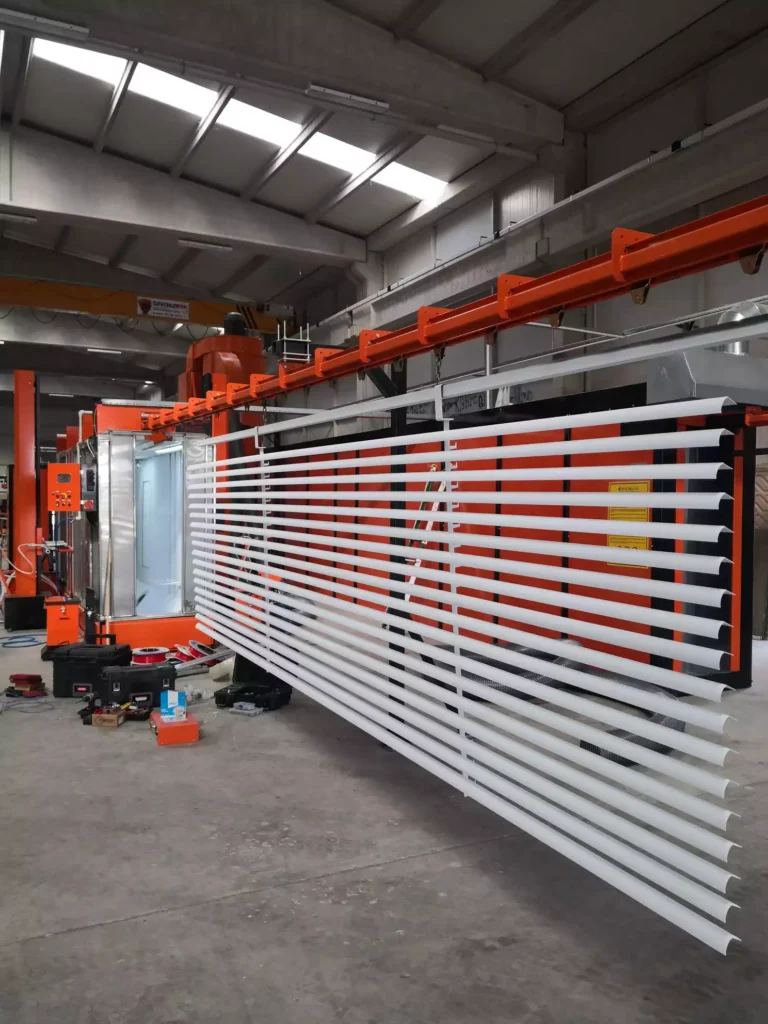
Ein weiterer bedeutender Trend in der modernen Fertigungstechnik ist die Digitalisierung der Produktionsprozesse. Die Einführung von Industrie 4.0, bei der intelligente Maschinen, Sensoren und Steuerungssysteme miteinander vernetzt werden, ermöglicht eine nahtlose Kommunikation und Datenanalyse in Echtzeit. Dies führt zu einer noch effizienteren Produktion, da Probleme frühzeitig erkannt und sofort behoben werden können. Durch die Integration von Internet of Things (IoT)-Technologien in Maschinen und Anlagen werden Produktionsdaten kontinuierlich überwacht, was eine präzisere Steuerung und Optimierung der Fertigungsprozesse ermöglicht. Darüber hinaus können durch vorausschauende Wartung Ausfallzeiten minimiert werden, da die Maschinen in der Lage sind, selbstständig zu erkennen, wann Wartungsmaßnahmen erforderlich sind.
Die Anpassung von Fertigungsprozessen an individuelle Kundenbedürfnisse, auch als Mass Customization bekannt, ist ein weiterer Aspekt der modernen Fertigung. Mithilfe von 3D-Druck-Technologien können maßgeschneiderte Produkte schnell und kostengünstig hergestellt werden. Dieses Verfahren, auch als additive Fertigung bezeichnet, ermöglicht es, Bauteile mit hoher Komplexität zu produzieren, die mit traditionellen Fertigungsmethoden nur schwer oder gar nicht herstellbar wären. Der 3D-Druck hat das Potenzial, die Produktionslandschaft erheblich zu verändern, da er nicht nur für die Herstellung von Prototypen, sondern auch für die Serienproduktion von Endprodukten geeignet ist.
In diesem Zusammenhang gewinnt auch die Nachhaltigkeit der Produktion zunehmend an Bedeutung. Unternehmen setzen auf Materialien, die weniger umweltschädlich sind oder auf Recyclingprozesse zurückgreifen, um den Ressourcenverbrauch zu senken. Die Entwicklung von umweltfreundlicheren Werkstoffen, wie biobasierten Kunststoffen und leicht recycelbaren Legierungen, trägt dazu bei, die Umweltbelastung durch die Industrie zu verringern. Ebenso werden energieeffiziente Maschinen und Produktionslinien entwickelt, die den CO2-Ausstoß und den Energieverbrauch minimieren.
Neben den technologischen Fortschritten spielt auch die Fachkräftesicherung eine zentrale Rolle in der modernen Fertigung. Die Einführung neuer Technologien erfordert hochqualifizierte Arbeitskräfte, die in der Lage sind, mit den komplexen Systemen und Maschinen umzugehen. Daher investieren Unternehmen zunehmend in die Weiterbildung und Schulung ihrer Mitarbeiter. Der Fachkräftemangel, insbesondere in spezialisierten Bereichen wie Maschinenbau, Automatisierungstechnik und IT, stellt jedoch eine Herausforderung dar. Hier sind neue Ansätze wie die verstärkte Zusammenarbeit mit Bildungseinrichtungen und die Förderung von technischen Studiengängen sowie dualen Ausbildungsmöglichkeiten von großer Bedeutung.
Abschließend lässt sich sagen, dass die Zukunft der Fertigungstechnik von einer stetigen Weiterentwicklung und Anpassung geprägt sein wird. Innovationen in den Bereichen Automatisierung, Digitalisierung und Nachhaltigkeit werden es den Unternehmen ermöglichen, ihre Produktionsprozesse effizienter, flexibler und umweltfreundlicher zu gestalten. Gleichzeitig müssen sie sicherstellen, dass ihre Mitarbeiter über die notwendigen Fähigkeiten und Kenntnisse verfügen, um mit den neuen Technologien Schritt zu halten. Die Integration von smarten, vernetzten Systemen und die kontinuierliche Forschung werden die Wettbewerbsfähigkeit der Unternehmen langfristig sichern und gleichzeitig zur Lösung globaler Herausforderungen wie dem Klimawandel und der Ressourcenschonung beitragen.
Pulverbeschichtungsanlage Pulverofen Einbrennofen Pulverkabine Absauganlage und Ersatzteile

Die Pulverbeschichtungstechnik hat sich als eine der effizientesten und umweltfreundlichsten Methoden zur Oberflächenbehandlung etabliert. Sie wird in einer Vielzahl von Industrien angewendet, um Produkte vor Korrosion zu schützen, ihre Haltbarkeit zu verbessern und eine ästhetische Oberfläche zu schaffen. Das Verfahren selbst umfasst mehrere wichtige Komponenten, darunter die Pulverbeschichtungsanlage, der Pulverofen, der Einbrennofen, die Pulverkabine, die Absauganlage und die Ersatzteile, die für die Wartung und den Betrieb dieser Anlagen notwendig sind.
Pulverbeschichtungsanlage
Die Pulverbeschichtungsanlage ist das Herzstück des gesamten Prozesses. Sie besteht aus verschiedenen Modulen, die zusammenarbeiten, um eine gleichmäßige und hochwertige Beschichtung auf den Werkstücken zu erzielen. Die Anlage umfasst in der Regel eine Fördereinrichtung, die die Teile durch die verschiedenen Stationen transportiert, sowie eine oder mehrere Sprühkabinen, in denen das Pulver aufgetragen wird. Die Pulverapplikation erfolgt meist mittels elektrostatischer Aufladung, wodurch das Pulver an der Oberfläche der Werkstücke haften bleibt. Moderne Anlagen sind so konzipiert, dass sie die Pulverauftragsmenge optimieren, um Materialverschwendung zu minimieren und die Qualität der Beschichtung zu maximieren.
Pulverofen und Einbrennofen
Nach dem Auftragen des Pulvers muss dieses durch Wärme gehärtet werden, um die gewünschte Festigkeit und Haltbarkeit zu erreichen. Der Pulverofen, auch Einbrennofen genannt, spielt dabei eine zentrale Rolle. In diesem Ofen wird das pulverisierte Material bei Temperaturen zwischen 160 und 200 Grad Celsius eingebrannt, wodurch es schmilzt und eine gleichmäßige, widerstandsfähige Schicht bildet. Der Einbrennofen muss präzise Temperaturregelungen ermöglichen und eine gleichmäßige Wärmeverteilung sicherstellen, um eine konsistente Beschichtung ohne Unregelmäßigkeiten zu gewährleisten. Je nach Anforderung an das Werkstück und das Pulver können unterschiedliche Einbrenntemperaturen und -zeiten erforderlich sein.
Pulverkabine
Die Pulverkabine ist der Bereich, in dem das Pulver auf das Werkstück aufgetragen wird. Diese Kabinen sind mit speziellen Sprühpistolen ausgestattet, die das Pulver mittels elektrostatischer Aufladung auf die zu beschichtenden Oberflächen übertragen. Die Kabinen sind oft mit einer Reihe von Filtern ausgestattet, um das überschüssige Pulver zu sammeln und wiederverwerten zu können. Eine hohe Effizienz in der Pulverkabine ist entscheidend, da dies nicht nur die Qualität der Beschichtung beeinflusst, sondern auch die Materialkosten senken und die Umweltbelastung durch überschüssiges Pulver minimieren kann. Die ergonomische Gestaltung der Kabinen und die Auswahl der richtigen Sprühtechnologie spielen ebenfalls eine Rolle in der Qualität und Geschwindigkeit des Beschichtungsprozesses.
Absauganlage
Die Absauganlage ist ein weiterer wichtiger Bestandteil der Pulverbeschichtungsanlage. Sie sorgt dafür, dass überschüssiges Pulver, das während des Sprühvorgangs entsteht, effizient aus der Arbeitsumgebung entfernt wird. Diese Absauganlagen sind mit speziellen Filtern ausgestattet, um das aufgesaugte Pulver zu sammeln und für die Wiederverwendung zu filtern. Eine gut funktionierende Absauganlage ist unerlässlich, um die Luftqualität im Arbeitsbereich zu gewährleisten und gleichzeitig den Verlust von teurem Pulver zu verhindern. Sie spielt auch eine Rolle bei der Sicherheit, da Staubexplosionen vermieden werden müssen. Die Absaugtechnik variiert je nach Größe der Anlage und den Anforderungen der Produktion, aber sie sollte stets eine hohe Effizienz bei der Abführung von Luft und Partikeln gewährleisten.
Ersatzteile
Für den reibungslosen Betrieb einer Pulverbeschichtungsanlage sind Ersatzteile von entscheidender Bedeutung. Verschleißteile wie Düsen, Sprühpistolen, Förderbänder und Filter müssen regelmäßig gewartet und gegebenenfalls ausgetauscht werden, um eine konstante Beschichtungsqualität zu gewährleisten und Ausfallzeiten zu minimieren. Besonders die Sprühdüsen und -pistolen sind häufigem Abrieb ausgesetzt, da sie in direktem Kontakt mit dem Pulver stehen. Auch die Filter der Absauganlage und die Heizsysteme des Einbrennofens unterliegen einem kontinuierlichen Verschleiß und erfordern regelmäßige Inspektionen und Wartungen. Eine vorausschauende Ersatzteilbeschaffung und -lagerung hilft, Stillstandzeiten der Anlagen zu vermeiden und die Produktionsabläufe aufrechtzuerhalten.
Insgesamt ist die Pulverbeschichtung eine hochgradig effiziente Technologie, die kontinuierlich weiterentwickelt wird, um die Anforderungen der Industrie hinsichtlich Umweltfreundlichkeit, Kosteneffizienz und Qualität zu erfüllen. Die verschiedenen Komponenten der Pulverbeschichtungsanlage müssen in perfektem Zusammenspiel arbeiten, um eine gleichbleibend hohe Beschichtungsqualität zu garantieren und die Produktion auf lange Sicht erfolgreich zu gestalten.
Die kontinuierliche Weiterentwicklung der Pulverbeschichtungsanlagen sowie die Einführung neuer Technologien und Verfahren bieten sowohl Herausforderungen als auch Chancen für die Industrie. Im Folgenden wird die Weiterentwicklung in einigen Bereichen und die Bedeutung von Innovationen innerhalb der Pulverbeschichtungstechnologie weiter ausgeführt.
Automatisierung und Digitalisierung in der Pulverbeschichtung
Ein zunehmend wichtiger Trend in der Pulverbeschichtungstechnik ist die Automatisierung der Prozesse. Durch den Einsatz von Robotern, die das Auftragen des Pulvers übernehmen, wird eine gleichmäßige Beschichtung und eine höhere Präzision erzielt. Roboter können insbesondere in großen Fertigungsstätten, die eine hohe Stückzahl erfordern, zur Effizienzsteigerung und Kostenreduktion beitragen. Diese Roboter sind in der Lage, sich schnell an unterschiedliche Bauteile und Geometrien anzupassen, was die Flexibilität der Anlage erhöht.
Ein weiterer Aspekt der Automatisierung ist die Integration von digitalen Steuerungssystemen, die eine präzise Kontrolle und Überwachung der gesamten Produktionslinie ermöglichen. Durch den Einsatz von Smart Manufacturing und Industrie 4.0-Technologien können alle Anlagenteile miteinander vernetzt und in Echtzeit überwacht werden. Dies ermöglicht eine sofortige Identifikation von Abweichungen und eine schnelle Reaktion auf etwaige Störungen, was wiederum Ausfallzeiten reduziert und die Produktqualität sichert. Der Einsatz von sensorgestützten Systemen zur Überwachung von Temperatur, Pulvermenge und anderen Parametern sorgt dafür, dass der Beschichtungsprozess jederzeit optimiert wird.
Nachhaltigkeit und Umweltfreundlichkeit
In der heutigen Industrie ist die Nachhaltigkeit ein immer wichtigeres Thema, und die Pulverbeschichtung ist aufgrund ihrer umweltfreundlichen Eigenschaften eine bevorzugte Methode. Im Gegensatz zu traditionellen Nasslacken, bei denen Lösungsmittel verwendet werden, ist Pulverbeschichtung nahezu frei von flüchtigen organischen Verbindungen (VOCs), die schädlich für die Umwelt und die Gesundheit der Arbeiter sein können. Zudem lässt sich überschüssiges Pulver effizient zurückgewinnen und wiederverwenden, wodurch der Materialverbrauch gesenkt wird.
Die Absauganlagen und Filtersysteme in modernen Pulverbeschichtungsanlagen sind so konzipiert, dass sie nahezu das gesamte überschüssige Pulver auffangen und wieder in den Produktionsprozess zurückführen. Dies führt nicht nur zu einer Verringerung der Materialkosten, sondern trägt auch zur Abfallvermeidung bei. Darüber hinaus wird die Luftqualität im Arbeitsumfeld verbessert, da die Absaugtechnik den Staubgehalt in der Luft minimiert.
Die Energieeffizienz der Einbrennofen spielt ebenfalls eine entscheidende Rolle in der Nachhaltigkeitsstrategie von Pulverbeschichtungsanlagen. Durch den Einsatz von modernen Wärmerückgewinnungssystemen können die Energiekosten gesenkt und der CO2-Ausstoß reduziert werden. Beispielsweise können die Wärmeabluft des Ofens genutzt werden, um andere Teile des Produktionsprozesses zu beheizen oder den Ofen selbst vorzuwärmen, was die Effizienz des gesamten Systems steigert.
Ersatzteilmanagement und Wartung
Ein weiterer wichtiger Aspekt, der die Effizienz einer Pulverbeschichtungsanlage beeinflusst, ist das Ersatzteilmanagement. Um die Produktionslinie möglichst ununterbrochen am Laufen zu halten, müssen die richtigen Ersatzteile zur richtigen Zeit verfügbar sein. Dies erfordert eine sorgfältige Planung und eine gut gepflegte Ersatzteilliste, die auch seltene oder spezialisierte Teile umfasst. Eine vorausschauende Wartung ist entscheidend, um Ausfälle zu vermeiden. Dabei kann auch die Digitalisierung eine Rolle spielen, indem Wartungsintervalle und der Zustand von Maschinen und Komponenten kontinuierlich überwacht werden. Einige moderne Systeme bieten sogar Vorhersagen, wann bestimmte Teile voraussichtlich ausgetauscht oder gewartet werden müssen, basierend auf Sensordaten und maschinellem Lernen.
Innovationen im Bereich Pulvertechnologie
Die Technologie der Pulverbeschichtung hat sich in den letzten Jahren erheblich weiterentwickelt. Neue Pulverformeln und Beschichtungsmaterialien bieten verbesserte Eigenschaften, die für bestimmte Anwendungen erforderlich sind, wie etwa höhere Korrosionsbeständigkeit, zusätzliche UV-Stabilität oder eine bessere Haftung auf schwierig zu beschichtenden Materialien. Auch die Entwicklung von thermoplastischen Pulvern hat neue Anwendungsmöglichkeiten eröffnet, insbesondere für Produkte, die nach der Beschichtung noch weiter verarbeitet oder modifiziert werden müssen. Diese innovativen Pulver bieten zusätzliche Flexibilität und erweitern das Spektrum an Materialien und Endprodukten, die mit Pulverbeschichtung bearbeitet werden können.
Zusätzlich bieten nano-beschichtete Pulver Fortschritte in Bezug auf Oberflächenhärte und Kratzfestigkeit, was besonders in der Automobil- und Elektronikindustrie von Bedeutung ist. Die Entwicklung solcher hochleistungsfähiger Pulver eröffnet neue Möglichkeiten für die Beschichtung von anspruchsvollen Anwendungen, bei denen eine hohe Widerstandsfähigkeit gegen mechanische Beanspruchung erforderlich ist.
Zusammenfassung und Ausblick
Die Pulverbeschichtungstechnik hat sich als eine äußerst leistungsfähige und umweltfreundliche Methode zur Oberflächenbehandlung etabliert. Die Weiterentwicklung von Technologien wie der Automatisierung, der Digitalisierung, der nachhaltigen Produktion und innovativen Pulvern wird auch in Zukunft eine Schlüsselrolle spielen. Unternehmen, die Pulverbeschichtungsanlagen betreiben, müssen kontinuierlich in neue Technologien und Wartungsstrategien investieren, um wettbewerbsfähig zu bleiben und die immer höheren Anforderungen an Qualität, Nachhaltigkeit und Effizienz zu erfüllen. In den kommenden Jahren wird die Pulverbeschichtungstechnik voraussichtlich weiter an Bedeutung gewinnen, da sie sowohl in Bezug auf die Umweltfreundlichkeit als auch die Kosteneffizienz viele Vorteile bietet.
Manuelle Pulverbeschichtungskabine
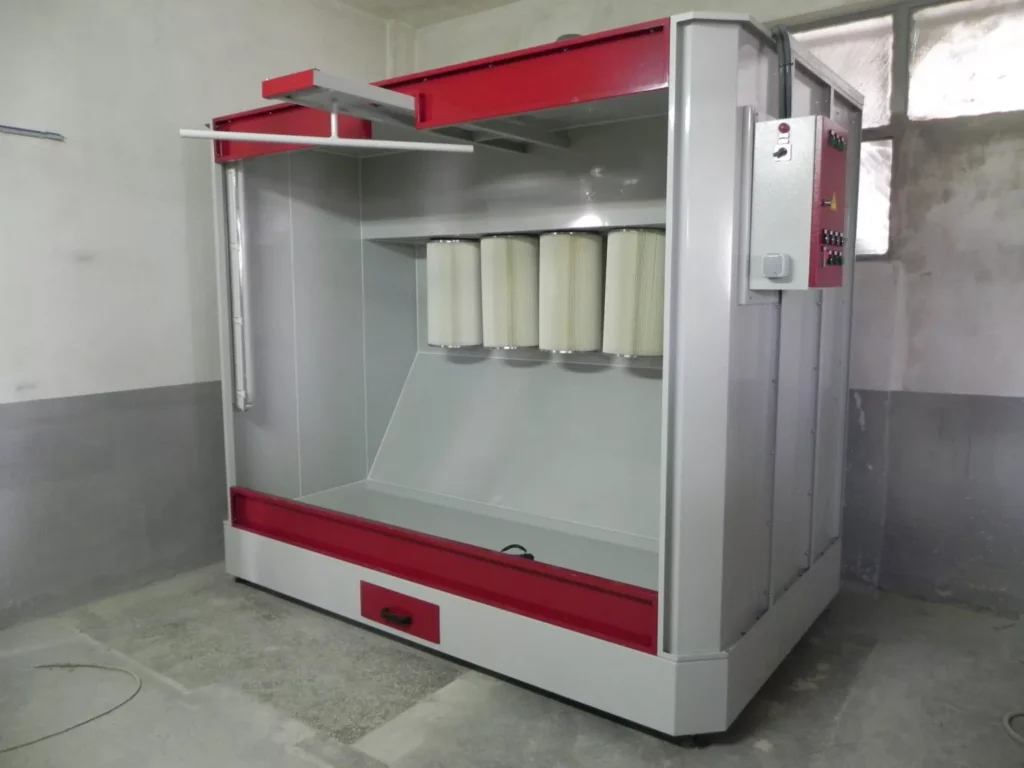
Die manuelle Pulverbeschichtungskabine ist eine bewährte Lösung, die vor allem in kleineren Betrieben oder für individuelle, spezialisierte Anwendungen eingesetzt wird, bei denen eine vollautomatische Anlage nicht erforderlich oder wirtschaftlich sinnvoll ist. Sie bietet eine flexible, kostengünstige Möglichkeit, Werkstücke in unterschiedlichsten Größen und Formen mit Pulverbeschichtung zu versehen. In einer manuellen Kabine ist der Bediener direkt für die Applikation des Pulvers verantwortlich, was eine hohe Anpassungsfähigkeit an spezifische Anforderungen ermöglicht.
Aufbau und Funktionsweise einer manuellen Pulverbeschichtungskabine
Eine manuelle Pulverbeschichtungskabine besteht aus mehreren wesentlichen Komponenten, die zusammenarbeiten, um eine gleichmäßige und qualitativ hochwertige Beschichtung zu gewährleisten:
- Sprühpistole
Die Sprühpistole ist das zentrale Werkzeug in einer manuellen Pulverbeschichtungskabine. Sie wird verwendet, um das Pulver auf die Werkstücke zu sprühen. Moderne Sprühpistolen sind oft mit einer elektrostatischen Aufladung ausgestattet, um das Pulver an der Oberfläche des Werkstücks haften zu lassen. Die Pistole kann manuell geführt werden, wodurch der Bediener eine hohe Präzision und Flexibilität bei der Beschichtung der Werkstücke erreicht. Je nach Bedarf kann der Bediener die Pulvermenge und den Luftdruck einstellen, um das gewünschte Ergebnis zu erzielen. - Kabinenstruktur
Die Kabine selbst ist in der Regel aus einem robusten Material wie Edelstahl oder lackiertem Stahl gefertigt, um den hohen Anforderungen des Beschichtungsprozesses gerecht zu werden. Sie ist mit speziellen Wänden ausgestattet, die den Staub und das überschüssige Pulver auffangen. Die manuelle Kabine ist so konzipiert, dass der Bediener bequem Zugang zu den Werkstücken hat, um diese zu beschichten. In vielen Fällen verfügen diese Kabinen über ein Sichtfenster oder eine transparente Wand, damit der Bediener das Werkstück gut im Blick hat. - Absaugsystem
Ein Absaugsystem ist entscheidend für die Effizienz und Sicherheit der manuellen Pulverbeschichtung. Es sorgt dafür, dass überschüssiges Pulver, das beim Sprühvorgang nicht am Werkstück haftet, aus der Kabine abgesaugt wird. In vielen modernen Systemen wird das Pulver in speziellen Filtern gesammelt, um es für die Wiederverwendung aufzufangen. Dies reduziert den Materialverbrauch und hilft, die Umweltbelastung zu minimieren. Das Absaugsystem trägt auch dazu bei, die Luftqualität in der Kabine zu verbessern und mögliche Gesundheitsrisiken für die Bediener zu verringern, da der feine Staub, der beim Pulverauftrag entsteht, schnell abgeführt wird. - Beleuchtung und Sichtfenster
Um eine präzise Beschichtung zu ermöglichen, sind manuelle Pulverbeschichtungskabinen mit ausreichender Beleuchtung ausgestattet. Diese Beleuchtung sorgt dafür, dass der Bediener das Werkstück während des gesamten Beschichtungsprozesses gut sehen kann. Durch die Verwendung von Vollsichtfenstern oder transparenten Panels kann der Bediener das Werkstück und die Beschichtung in Echtzeit beobachten, was eine exakte Steuerung der Pulverapplikation ermöglicht.
Vorteile der manuellen Pulverbeschichtung
Eine manuelle Pulverbeschichtungskabine bietet im Vergleich zu vollautomatischen Anlagen eine Reihe von Vorteilen:
- Flexibilität und Anpassungsfähigkeit
Ein großer Vorteil der manuellen Pulverbeschichtung ist die Flexibilität. Der Bediener kann unterschiedliche Werkstücke und Oberflächenprofile problemlos beschichten, ohne dass eine umfassende Umrüstung erforderlich ist. Dies ist besonders vorteilhaft für Unternehmen, die eine Vielzahl von Produktgrößen oder -formen bearbeiten und eine individuelle Beschichtung für jedes Werkstück benötigen. - Kostengünstig
Für kleinere Produktionsvolumen oder Einzelanfertigungen ist eine manuelle Pulverbeschichtungskabine im Vergleich zu vollautomatischen Anlagen oft die kostengünstigere Lösung. Die Investitionskosten für eine manuelle Kabine sind deutlich niedriger, und es fallen keine zusätzlichen Kosten für die Automatisierung oder komplexe Steuerungssysteme an. Auch die Betriebskosten können niedriger sein, da die Kabine häufig weniger Wartung benötigt als größere, automatisierte Systeme. - Einfache Bedienung und Wartung
Die Bedienung einer manuellen Pulverbeschichtungskabine erfordert in der Regel keine spezialisierte Ausbildung oder aufwendige Schulungen. Ein erfahrener Bediener kann die Kabine schnell einrichten und die Beschichtung vornehmen. Auch die Wartung und Reinigung sind relativ unkompliziert, was die Betriebskosten weiter senkt. Das Pulverauffangsystem in der Kabine ist leicht zugänglich und einfach zu entleeren oder zu reinigen, was die Lebensdauer der Geräte verlängert. - Geringer Materialverbrauch
Ein weiterer Vorteil ist der geringere Materialverbrauch, da der Bediener die Pulvermenge individuell anpassen kann. Überschüssiges Pulver wird in der Regel durch das Absaugsystem gesammelt und kann wiederverwendet werden. Dies trägt dazu bei, den Materialabfall zu minimieren und die Effizienz des Prozesses zu erhöhen.
Herausforderungen der manuellen Pulverbeschichtung
Obwohl die manuelle Pulverbeschichtung zahlreiche Vorteile bietet, gibt es auch einige Herausforderungen, die berücksichtigt werden müssen:
- Arbeitsintensität
Da der Bediener den Sprühprozess manuell steuert, kann die Pulverbeschichtung besonders bei größeren Aufträgen oder einer hohen Stückzahl arbeitsintensiv werden. Die gleichmäßige Applikation des Pulvers erfordert Erfahrung und Präzision, um eine gleichmäßige Schichtdicke und eine hochwertige Oberfläche zu erzielen. - Qualitätskontrolle
Im Vergleich zu automatisierten Systemen, bei denen die Beschichtung auf einheitliche Weise erfolgt, kann es bei manuellen Kabinen schwieriger sein, eine gleichbleibend hohe Qualität über alle Werkstücke hinweg zu gewährleisten. Unterschiedliche Bediener oder variable Arbeitsbedingungen können zu Abweichungen in der Beschichtung führen, die gegebenenfalls nachgearbeitet werden müssen. - Begrenzte Geschwindigkeit
Manuelle Kabinen sind in ihrer Geschwindigkeit begrenzt. Bei größeren Produktionsvolumen oder hohen Anforderungen an die Durchsatzrate kann es erforderlich sein, auf automatisierte Systeme umzuschwenken, um die Produktionskapazität zu steigern.
Fazit und Ausblick
Die manuelle Pulverbeschichtungskabine bleibt eine beliebte Lösung für Unternehmen, die Flexibilität, Kosteneffizienz und eine einfache Handhabung suchen. Sie ist ideal für kleinere bis mittlere Serienproduktionen, Einzelanfertigungen oder für spezielle Anwendungen, bei denen die Anpassung der Beschichtung erforderlich ist. Die kontinuierliche Verbesserung der Pulverapplikationstechnologien, wie zum Beispiel die Einführung von elektrostatischen Pistolen oder high-efficiency systems, hat die Effizienz der manuellen Kabinen in den letzten Jahren weiter gesteigert. In Kombination mit modernen Absaugsystemen und innovativen Pulvertechnologien bleibt die manuelle Pulverbeschichtung eine wertvolle Methode in der Oberflächenbehandlung von Werkstücken, insbesondere für spezifische, individuelle Anforderungen.
Weiterentwicklungen und Zukunftsaussichten der manuellen Pulverbeschichtungskabine
Auch wenn manuelle Pulverbeschichtungskabinen in der heutigen Fertigung nach wie vor eine weit verbreitete Lösung darstellen, gibt es zahlreiche Entwicklungen und Innovationen, die die Effektivität und Benutzerfreundlichkeit dieser Anlagen weiter verbessern. Einige dieser Entwicklungen zielen darauf ab, die Effizienz zu steigern, die Arbeitsbedingungen zu verbessern und die Anpassungsfähigkeit der Kabinen an verschiedene Anforderungen zu erhöhen.
1. Erweiterte Pulvertechnologien
Die Weiterentwicklung der Pulvertechnologie spielt eine Schlüsselrolle bei der Verbesserung der Pulverbeschichtung. Moderne Pulverbeschichtungen, wie Nano-Pulver, wetterbeständige Pulver oder thermoplastische Pulverlacke, erweitern die Möglichkeiten der manuellen Pulverbeschichtungskabinen. Diese fortschrittlichen Pulver bieten verbesserte Eigenschaften wie erhöhte Kratzfestigkeit, bessere Haftung oder eine höhere Korrosionsbeständigkeit. Mit neuen Formulierungen und Pulvertypen können auch spezifischere Anforderungen, etwa für die Automobil- oder Lebensmittelindustrie, erfüllt werden. Manuelle Kabinen müssen daher in der Lage sein, mit diesen neuen Pulvern effektiv zu arbeiten, ohne die Effizienz oder die Beschichtungsqualität zu beeinträchtigen.
2. Ergonomie und Benutzerfreundlichkeit
Um die Arbeitsbelastung der Bediener zu verringern, wird in der Entwicklung von manuellen Pulverbeschichtungskabinen immer mehr Wert auf ergonomische Gestaltung gelegt. Die Arbeitsposition des Bedieners und die Bedienfreundlichkeit der Sprühpistolen sind entscheidend für eine effiziente und komfortable Handhabung. Modernere Kabinen sind häufig so konstruiert, dass sie eine bessere Zugänglichkeit bieten und dem Bediener eine natürliche Haltung während des Beschichtungsprozesses ermöglichen, was nicht nur die Produktivität steigert, sondern auch das Risiko von Ermüdungserscheinungen und gesundheitlichen Beschwerden reduziert.
Zusätzlich werden einstellbare Sprühpistolen entwickelt, die dem Bediener eine noch feinere Steuerung des Pulverauftrags ermöglichen. Diese Pistolen bieten Optionen für die Einstellung der Pulvermenge, des Luftdrucks und der Elektrostatik, um die Effizienz des Beschichtungsprozesses zu erhöhen und eine gleichmäßige Schichtdicke auf unterschiedlichen Werkstückformen zu gewährleisten.
3. Automatisierung von unterstützenden Prozessen
Auch wenn der Pulversprühtag selbst manuell erfolgt, können andere Prozesse in der Pulverbeschichtungskabine zunehmend automatisiert werden, um die Gesamtleistung zu steigern. Ein Beispiel hierfür ist die automatisierte Reinigung der Kabine und der Sprühpistolen. Diese Systeme reinigen das Pulver automatisch aus den Düsen und dem Filtersystem, was sowohl die Betriebskosten senkt als auch die Zeit reduziert, die für Wartungsarbeiten aufgewendet werden muss.
Ein weiterer Bereich der Automatisierung betrifft die Pulverwiederverwertung. Durch den Einsatz von Technologien wie automatischen Pulverrückgewinnungssystemen können überschüssige Pulverpartikel aus der Kabine abgesaugt, gesiebt und für die erneute Verwendung aufbereitet werden. Dies verbessert nicht nur die Materialeffizienz, sondern reduziert auch den Materialabfall und die Kosten, was insbesondere bei teuren Pulvern wie z.B. metallen oder speziellen Lacken von großem Vorteil ist.
4. Optimierte Absaug- und Filtrationssysteme
In einer manuellen Pulverbeschichtungskabine ist das Absaugsystem nicht nur wichtig für die Sicherheit des Bedieners, sondern auch für die Energieeffizienz und die Umweltfreundlichkeit der gesamten Anlage. Die Entwicklung von hochleistungsfähigen Filtersystemen hat dazu beigetragen, dass überschüssiges Pulver noch effizienter abgesaugt und wiederverwendet werden kann. Dies reduziert nicht nur den Materialverlust, sondern trägt auch zur Einhaltung von Umweltvorschriften bei, da der Staub aus der Kabine gefiltert und sicher entsorgt wird.
Moderne HEPA-Filter und elektrostatische Filter sind besonders effektiv darin, ultrafeine Pulverpartikel zu fangen, die durch herkömmliche Filtersysteme nicht erfasst werden könnten. Diese Innovationen tragen dazu bei, die Luftqualität in der Kabine zu verbessern und die Gesundheit der Bediener zu schützen.
5. Integration von digitalen Steuerungen und Monitoring-Systemen
Ein weiteres wachsendes Feld in der Pulverbeschichtungstechnik ist die digitale Überwachung und Steuerung des Prozesses. Moderne manuelle Pulverbeschichtungskabinen sind zunehmend mit intelligenten Steuerungssystemen ausgestattet, die es dem Bediener ermöglichen, die Pulvermenge, den Luftdruck und die elektrostatische Aufladung in Echtzeit zu überwachen und anzupassen. Diese Systeme bieten eine digitale Schnittstelle, die eine präzise Kontrolle und die Möglichkeit zur Prozessdokumentation bietet.
Ein integriertes Monitoring-System kann die Leistung der Sprühpistole überwachen und automatisch Anpassungen vornehmen, wenn es Abweichungen im Pulverauftrag oder in der Luftqualität erkennt. Solche Systeme sorgen für eine konstante Beschichtungsqualität und erleichtern die Fehlersuche im Fall von Unregelmäßigkeiten.
6. Zukunftsperspektiven: 3D-Beschichtung und Nanotechnologie
Ein noch relativ neuer, aber vielversprechender Trend in der Pulverbeschichtung ist die Anwendung von 3D-Beschichtungstechnologien. Diese erlauben es, auch komplexe dreidimensionale Bauteile in einem einzigen Schritt effizient zu beschichten. Mit der Entwicklung von nanostrukturierten Pulvern könnten sich völlig neue Möglichkeiten zur Beschichtung von Oberflächen eröffnen, die noch widerstandsfähiger, funktioneller oder optisch ansprechender sind. Hierbei könnten auch nanostrukturierte Oberflächen entstehen, die die Eigenschaften von Beschichtungen, wie z.B. ihre Reinigungsfähigkeit oder Anti-Bakteriellen Eigenschaften, weiter verbessern.
Fazit: Die manuelle Pulverbeschichtung als flexible und kostengünstige Lösung
Die manuelle Pulverbeschichtungskabine bleibt auch in Zukunft eine wichtige Technologie in der Oberflächenbehandlung, insbesondere für kleinere Serienproduktionen, maßgeschneiderte Anwendungen und spezifische Anforderungen. Sie bietet die Flexibilität, die große, automatisierte Systeme oft nicht leisten können, und bleibt eine kostengünstige Lösung für Unternehmen, die keine automatisierte Beschichtungslinie benötigen. Die kontinuierliche Weiterentwicklung der Technologie, wie verbesserte Pulvertechnologien, effizientere Absaug- und Filtrationssysteme und die Integration von Automatisierung und digitalen Steuerungen, wird die Effizienz und Benutzerfreundlichkeit der manuellen Pulverbeschichtungskabinen in den kommenden Jahren weiter steigern.
Absauganlage für Pulverbeschichtung: Funktionen, Entwicklung und Zukunftsperspektiven
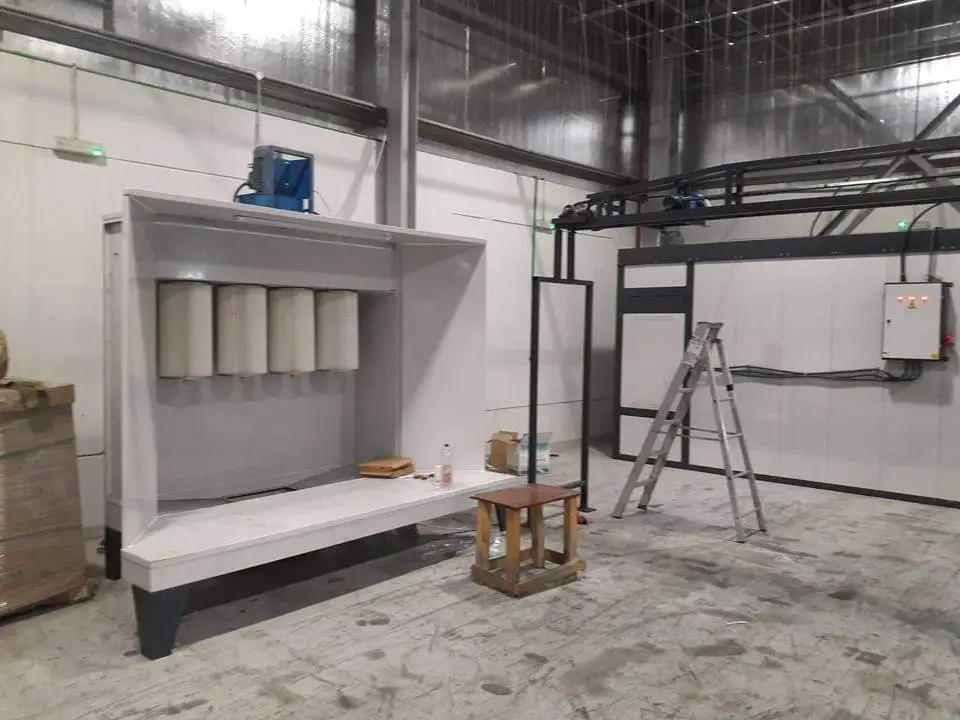
Die Absauganlage ist ein zentraler Bestandteil in Pulverbeschichtungsanlagen und spielt eine entscheidende Rolle bei der Effizienz, Sicherheit und Nachhaltigkeit des gesamten Beschichtungsprozesses. Sie sorgt nicht nur für die Entfernung des überschüssigen Pulvers aus der Kabine, sondern trägt auch zur Luftreinhaltung, Materialrückgewinnung und Sicherheit bei. Im Folgenden werden die grundlegenden Funktionen und Komponenten von Absauganlagen, ihre Weiterentwicklungen und die Zukunftsperspektiven dieser Technologie näher erläutert.
Grundlegende Funktionen einer Absauganlage
Die Hauptaufgabe einer Absauganlage in einer Pulverbeschichtungsanlage besteht darin, den Pulverstaub zu erfassen, der während des Beschichtungsprozesses entsteht. Dieser Staub kann sich nicht nur auf den Werkstücken ablagern, sondern auch auf den Wänden der Kabine und in der Luft verteilen, was sowohl zu Qualitätsproblemen als auch zu gesundheitlichen Risiken für die Bediener führen kann. Die Absauganlage sorgt dafür, dass der Pulverstaub schnell und effizient abgeführt wird, wodurch die Arbeitsumgebung sauber bleibt und das Pulver für eine Wiederverwendung zurückgewonnen werden kann.
Aufbau und Funktionsweise einer Absauganlage
Eine typische Absauganlage für Pulverbeschichtung besteht aus mehreren wichtigen Komponenten:
- Absauggebläse und Ventilator
Das Herzstück jeder Absauganlage ist der Ventilator oder das Absauggebläse, das den Luftstrom erzeugt. Der Ventilator zieht die Luft mit dem Pulverstaub aus der Kabine und leitet sie in das Filtersystem. Die Leistung des Ventilators muss auf den Luftdurchsatz der Kabine abgestimmt sein, um sicherzustellen, dass die Luft ausreichend schnell und effizient abgeführt wird. Die Stärke des Luftstroms ist entscheidend, um das Pulver effektiv aufzufangen und eine gleichmäßige Absaugung zu gewährleisten. - Filtrationssysteme
Das Filtrationssystem ist ein wesentlicher Bestandteil der Absauganlage. Es sorgt dafür, dass der abgesaugte Staub nicht wieder in die Luft freigesetzt wird. Moderne Absauganlagen sind mit Hochleistungsfiltern ausgestattet, die in der Lage sind, auch feinste Pulverpartikel zu erfassen. Zu den gängigen Filtern gehören Taschenfilter, HEPA-Filter und Kartuschenfilter, die je nach Anforderung der Anlage und der Pulverarten ausgewählt werden.- Taschenfilter: Diese Filter bestehen aus robusten Stoffen, die den Staub aus der Luft filtern. Sie werden regelmäßig gereinigt, um die Filterleistung aufrechtzuerhalten.
- HEPA-Filter: Hochleistungsfilter, die selbst feinste Partikel aus der Luft entfernen und daher besonders wichtig sind, wenn mit gesundheitsschädlichen oder hochfeinen Pulvern gearbeitet wird.
- Kartuschenfilter: Diese Filtertypen sind kompakter und bieten eine hohe Filterleistung bei gleichzeitig niedrigerem Platzbedarf. Sie eignen sich gut für kleinere Absauganlagen.
- Pulverrückgewinnung
Ein weiteres wichtiges Element der Absauganlage ist das Pulverrückgewinnungssystem. Das abgesaugte Pulver, das sich in den Filtern und im Luftstrom befindet, wird durch ein Rückgewinnungssystem aufgefangen und in den Produktionskreislauf zurückgeführt. In vielen modernen Anlagen wird das Pulver durch Sieb- und Recyclingprozesse aufbereitet, sodass es wieder verwendet werden kann. Das Rückgewinnungssystem trägt zur Reduzierung des Materialverbrauchs und der Kosten bei und minimiert den Abfall. - Luftkanäle und Rohrsysteme
Die Luftkanäle und Rohrsysteme verbinden die verschiedenen Teile der Absauganlage miteinander. Sie transportieren die abgesaugte Luft und den Pulverstaub vom Arbeitsplatz zur Filtereinheit und weiter zum Rückgewinnungssystem. Die Rohrleitungen müssen so gestaltet sein, dass der Luftstrom nicht behindert wird und die Absaugung effizient und konstant erfolgt. - Automatische Reinigungssysteme
Die regelmäßige Reinigung der Filter ist entscheidend für die langfristige Leistungsfähigkeit einer Absauganlage. Moderne Absauganlagen sind häufig mit automatischen Reinigungssystemen ausgestattet, die die Filter in regelmäßigen Abständen von angesammeltem Pulver befreien. Diese Systeme arbeiten oft mit Reverse-Flow-Technologien, bei denen die Luft in die entgegengesetzte Richtung durch die Filter gepumpt wird, um angesammelten Staub zu lösen. Diese automatische Reinigung spart nicht nur Zeit, sondern stellt auch sicher, dass die Filter über längere Zeit hinweg mit gleichbleibender Effizienz arbeiten.
Vorteile der Absauganlage für Pulverbeschichtung
Die Absauganlage bringt eine Reihe von Vorteilen für den gesamten Beschichtungsprozess mit sich:
- Saubere Arbeitsumgebung
Die Hauptaufgabe der Absauganlage besteht darin, die Luft von Pulverstaub zu befreien. Dies sorgt für eine saubere Arbeitsumgebung, die nicht nur die Qualität der Beschichtung erhöht, sondern auch die Gesundheit der Bediener schützt. Eine saubere Kabine ist entscheidend, um eine einwandfreie Pulverapplikation zu gewährleisten und die Gefahr von Verunreinigungen zu minimieren. - Materialeffizienz und Kostenersparnis
Durch die Rückgewinnung von überschüssigem Pulver kann der Materialverbrauch signifikant reduziert werden. Dies ist besonders vorteilhaft bei teuren Pulvern und trägt zur Kostenersparnis bei. Zudem wird der Abfall minimiert, was sowohl ökologisch als auch ökonomisch vorteilhaft ist. - Erhöhte Sicherheit
Ein effizientes Absaugsystem verringert die Gefahr einer Staubexplosion, die bei der Arbeit mit feinem Pulver entstehen kann. Durch die kontinuierliche Absaugung und das Absperren von Pulverstaub wird das Risiko von Bränden und Explosionen in der Kabine deutlich minimiert. - Einhaltung von Umweltvorschriften
Moderne Absauganlagen sind so konzipiert, dass sie den Umweltvorschriften entsprechen, indem sie feine Partikel und Staub aus der Luft filtern und nicht in die Umgebung abgeben. Dies trägt zur Luftreinhaltung bei und stellt sicher, dass die Produktion auch unter den strengen Auflagen zur Luftqualität betrieben werden kann.
Weiterentwicklungen und Trends
Die Technologie der Absauganlagen hat sich in den letzten Jahren erheblich weiterentwickelt. Einige der wichtigsten Trends und Innovationen in diesem Bereich sind:
- **Integration von Intelligente Steuerungssysteme
Moderne Absauganlagen werden zunehmend mit intelligenten Steuerungssystemen ausgestattet, die die Leistung der Filter und die Effizienz der Rückgewinnung in Echtzeit überwachen. Diese Systeme können automatisch Anpassungen vornehmen, wenn die Filterkapazität erreicht ist oder der Luftstrom ineffizient wird, was die Wartung vereinfacht und die Energieeffizienz erhöht. - Energieeffizienz
In Zeiten der steigenden Energiekosten wird in der Entwicklung von Absauganlagen verstärkt auf Energieeffizienz geachtet. Der Einsatz von Energiespartechnologien wie variablen Frequenzantrieben (VFD) für die Ventilatoren ermöglicht eine bedarfsgerechte Anpassung der Absaugleistung. Dies reduziert nicht nur die Betriebskosten, sondern trägt auch zur Nachhaltigkeit bei. - Automatische Filterüberwachung und -reinigung
Automatisierte Filterüberwachungssysteme ermöglichen eine präzise Kontrolle der Filterleistung und warnen den Bediener, wenn eine Reinigung oder ein Austausch notwendig wird. Dies stellt sicher, dass die Absauganlage immer mit optimaler Effizienz arbeitet und Ausfallzeiten aufgrund von Filterverschmutzung minimiert werden. - Modulare Absauganlagen
Modulare Absauganlagen bieten eine hohe Flexibilität, da sie leicht an unterschiedliche Produktionsgrößen und Anforderungen angepasst werden können. Durch den modularen Aufbau können Absauganlagen je nach Bedarf erweitert oder an die spezifischen Anforderungen der Pulverbeschichtungsanlage angepasst werden.
Fazit und Ausblick
Absauganlagen für Pulverbeschichtung sind unverzichtbare Komponenten in modernen Beschichtungsanlagen. Sie sorgen nicht nur für die Sicherheit und Sauberkeit der Arbeitsumgebung, sondern tragen auch zur Effizienz, Kostenersparnis und Nachhaltigkeit bei. Mit der kontinuierlichen Weiterentwicklung von Energieeffizienztechnologien, automatisierten Reinigungssystemen und intelligenten Steuerungen wird die Zukunft der Absauganlagen noch effizienter und umweltfreundlicher. Unternehmen, die in moderne Absauganlagen investieren, profitieren von einer verbesserten Produktqualität, reduzierten Betriebskosten und einer höheren Produktionskapazität.
Absauganlagen für Pulverbeschichtung spielen eine zentrale Rolle im gesamten Produktionsprozess, indem sie nicht nur zur Sauberkeit der Arbeitsumgebung beitragen, sondern auch die Effizienz und Nachhaltigkeit der Beschichtung erhöhen. Durch den stetigen Fortschritt in der Technologie bieten moderne Absauganlagen immer leistungsfähigere Lösungen, die den Betrieb optimieren und den Materialverbrauch minimieren.
Ein wesentlicher Aspekt der Weiterentwicklung betrifft die Energieeffizienz. Mit der Integration von variablen Frequenzantrieben für die Ventilatoren kann die Absaugleistung an den tatsächlichen Bedarf angepasst werden, wodurch unnötiger Energieverbrauch vermieden wird. Dies ermöglicht eine nachhaltige Nutzung der Anlagen und trägt zur Senkung der Betriebskosten bei. Der Einsatz intelligenter Überwachungssysteme zur Kontrolle von Luftstrom, Filterzustand und Pulverrückgewinnung verbessert die Prozesskontrolle und hilft, ineffiziente Betriebszeiten zu minimieren. Diese Systeme geben dem Bediener die Möglichkeit, sofort auf Unregelmäßigkeiten zu reagieren und die Leistung der Absauganlage jederzeit zu optimieren.
Neben der Energieeffizienz spielt auch die Automatisierung eine immer größere Rolle. Die Integration von automatischen Reinigungssystemen zur Wartung der Filter ist ein innovativer Schritt, der den Aufwand für manuelle Reinigung verringert und gleichzeitig sicherstellt, dass die Filter immer mit optimaler Effizienz arbeiten. Solche Systeme sorgen dafür, dass der Staub regelmäßig aus den Filtern entfernt wird, wodurch die Gefahr von Verstopfungen oder Leistungsabfällen verringert wird. Dies spart nicht nur Zeit, sondern erhöht auch die Lebensdauer der Anlagen.
Eine weitere Entwicklung in der Absaugtechnik ist die Modularität von Absauganlagen. Dies ermöglicht eine flexible Anpassung an unterschiedliche Produktionsbedingungen. Modulare Anlagen können einfach erweitert werden, um mit wachsendem Produktionsvolumen oder veränderten Anforderungen Schritt zu halten. Zudem bieten sie eine kostengünstige Lösung, da nur die Komponenten hinzugefügt oder ersetzt werden müssen, die tatsächlich benötigt werden, anstatt die gesamte Anlage umzurüsten.
Zusätzlich zur technischen Weiterentwicklung der Absauganlagen steht die Rückgewinnung von Pulvern im Fokus. In modernen Anlagen wird das abgesaugte Pulver mithilfe von Sieb- und Recyclingprozessen wiederaufbereitet, sodass es erneut verwendet werden kann. Diese Rückgewinnung trägt nicht nur zur Reduzierung der Materialkosten bei, sondern minimiert auch den Abfall und hilft dabei, die Umweltbelastung zu verringern.
Insgesamt ist die Absauganlage für Pulverbeschichtung mehr als nur eine technische Notwendigkeit. Sie stellt einen wichtigen Beitrag zur Sicherstellung der Arbeitsqualität, Kostenreduktion und Umweltschutz dar. Unternehmen, die in moderne Absauganlagen investieren, profitieren von einer konstant hohen Produktqualität, einer sauberen Arbeitsumgebung und einer effektiveren Ressourcennutzung. Die kontinuierliche Verbesserung der Absaugtechnologie wird auch in Zukunft die Pulverbeschichtung noch effizienter und umweltfreundlicher gestalten.
Felgen Pulverbeschichtung
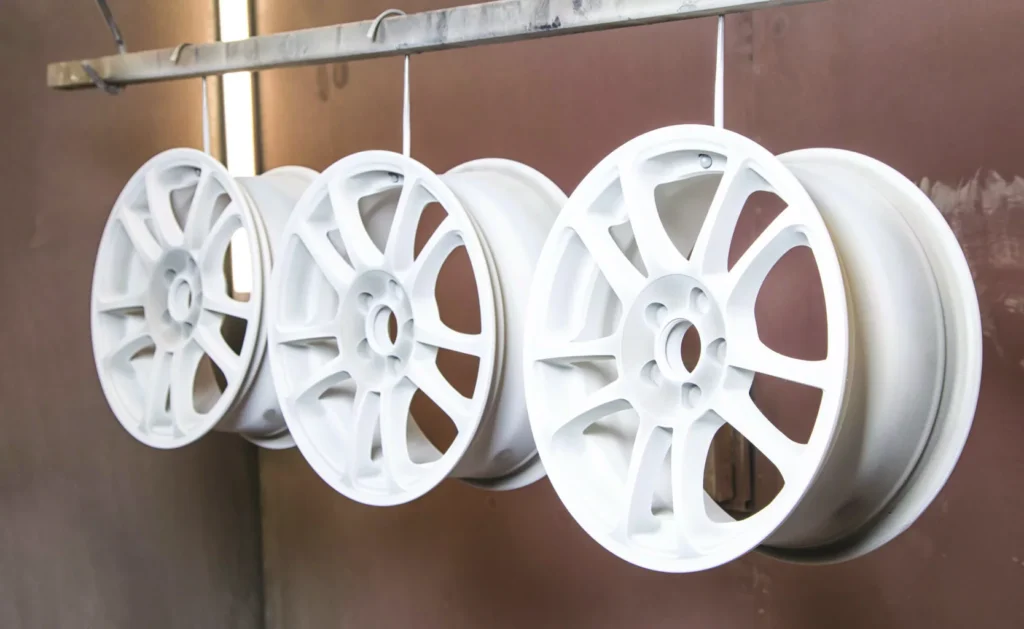
Die Felgenpulverbeschichtung ist ein wichtiger Prozess in der Automobilindustrie und bei der Herstellung von Felgen für verschiedene Fahrzeugtypen. Sie bietet nicht nur einen ästhetischen Vorteil durch eine glänzende, gleichmäßige Oberfläche, sondern schützt die Felgen auch vor Korrosion und äußeren Einflüssen. Im Vergleich zu herkömmlichen Lackiermethoden bietet die Pulverbeschichtung zahlreiche Vorteile, darunter eine höhere Widerstandsfähigkeit, eine bessere Haltbarkeit und eine umweltfreundlichere Anwendung.
Die Felgenpulverbeschichtung beginnt mit einer gründlichen Vorbereitung der Felgenoberfläche, um sicherzustellen, dass der Pulverauftrag gleichmäßig und dauerhaft haftet. Dieser Schritt umfasst das Reinigen und Entfetten der Felgen, häufig durch Sandstrahlen, um Oberflächenunregelmäßigkeiten zu beseitigen und eine bessere Haftung des Pulvers zu gewährleisten. Danach erfolgt die elektrostatische Aufladung des Pulvers, wodurch die Partikel an der Felgenoberfläche haften, bevor sie im nächsten Schritt eingebrannt werden.
Die Pulverauftragsverfahren für Felgen verwenden in der Regel epoxidharzbasierte oder polyurethanbasierte Pulver. Diese Pulversorten bieten hervorragende mechanische Eigenschaften und sind widerstandsfähig gegenüber chemischen Einflüssen, Temperaturschwankungen und Feuchtigkeit, die Felgen im täglichen Betrieb ausgesetzt sind. Nach der Aufbringung des Pulvers wird die Felge in einem Einbrennofen bei hoher Temperatur (etwa 180–200 °C) eingebrannt, um das Pulver zu schmelzen und eine harte, widerstandsfähige Beschichtung zu erzeugen.
Ein wesentlicher Vorteil der Felgenpulverbeschichtung ist ihre Langlebigkeit. Die harte, versiegelte Oberfläche schützt die Felge vor Steinschlägen, Chemikalien (wie Reinigungsmitteln, Streusalz im Winter) und UV-Strahlung, was die Lebensdauer der Felge deutlich verlängert. Zudem bleibt die Oberfläche der Felgen beständig gegenüber Kratzer und Abnutzung, die während des Gebrauchs auftreten können. Die Farbvielfalt ist ein weiterer Vorteil: Pulverbeschichtungen sind in nahezu allen Farben und Oberflächenstrukturen (Matt, Glänzend, Metallic) erhältlich und ermöglichen so eine hohe Individualisierung von Felgen.
Neben der verbesserten Korrosionsbeständigkeit und Haltbarkeit bietet die Pulverbeschichtung auch ökologische Vorteile. Im Gegensatz zu herkömmlichen Lackierverfahren werden bei der Pulverbeschichtung keine Lösungsmittel verwendet, was die Freisetzung schädlicher flüchtiger organischer Verbindungen (VOCs) vermeidet. Das Pulver ist ein fester Stoff, der ohne chemische Zusätze aufgetragen wird und nach dem Aushärten in einem geschlossenen Kreislaufsystem recycelt werden kann. Dies führt zu einer Reduktion des Abfalls und einer effizienteren Nutzung des Materials.
Zusätzlich zu den mechanischen und ästhetischen Vorteilen der Pulverbeschichtung spielt auch die wirtschaftliche Effizienz eine Rolle. Da die Pulverbeschichtung in einem einzigen Schritt aufgetragen und eingebrannt wird, reduziert sich der Arbeitsaufwand im Vergleich zu herkömmlichen Lackiermethoden. Auch die Verarbeitungsgeschwindigkeit ist schneller, was die Produktionszeiten verkürzt und somit die Kosten senkt. Der Prozess ist zudem kostenwirksam, da überschüssiges Pulver einfach wiederverwendet werden kann.
Ein immer häufiger eingesetztes Verfahren in der Felgenpulverbeschichtung ist die Verwendung von „Clear-Coat“-Beschichtungen, die eine zusätzliche Schicht auf der Pulveroberfläche bieten und die Felgenoberfläche weiter schützen. Diese Klarlackschicht verstärkt nicht nur die Glanzwirkung, sondern schützt vor Umwelteinflüssen und erleichtert die Reinigung der Felgen. Sie ist besonders in Bereichen wie dem Aluminiumfelgenmarkt von Bedeutung, wo hohe Anforderungen an die Oberflächenqualität gestellt werden.
Die Felgenpulverbeschichtung kann auch individuell gestaltet werden, um dem Markenimage eines Unternehmens gerecht zu werden oder die optischen Anforderungen des Kunden zu erfüllen. Durch die Verwendung von Sonderfarben oder sogar speziellen Oberflächenstrukturen können Felgen ein einzigartiges Aussehen erhalten, das sich von Standardbeschichtungen abhebt. Besonders im Bereich von Sportwagen und Tuningfahrzeugen ist die personalisierte Gestaltung von Felgen ein bedeutendes Merkmal.
Die ständige Weiterentwicklung in der Pulvertechnologie führt auch zu immer besseren Ergebnissen in der Felgenbeschichtung. Zukünftige Innovationen könnten hochfestere Pulver, thermoplastische oder sogar nanostrukturierte Pulverbeschichtungen umfassen, die noch widerstandsfähiger gegen äußere Belastungen sind und eine noch höhere Kratzfestigkeit bieten.
Insgesamt bleibt die Pulverbeschichtung von Felgen eine der bevorzugten Methoden für die Oberflächenveredelung, da sie nicht nur ästhetische Vorteile bietet, sondern auch die Langlebigkeit und Funktionsfähigkeit der Felgen erhöht. Die kontinuierliche Weiterentwicklung der Technologien in diesem Bereich sorgt dafür, dass Felgen weiterhin effektiv geschützt werden und gleichzeitig den hohen optischen Anforderungen der modernen Automobilindustrie gerecht werden.
Ein weiterer Vorteil der Felgenpulverbeschichtung ist die einfache Wartung. Pulverbeschichtete Felgen erfordern im Vergleich zu herkömmlich lackierten Felgen weniger Pflege. Die widerstandsfähige Beschichtung schützt die Oberfläche vor den schädlichen Auswirkungen von Bremsstaub, Straßenverschmutzung und Salz. In vielen Fällen reicht es aus, die Felgen mit Wasser und mildem Reinigungsmittel zu waschen, um Schmutz und Ablagerungen zu entfernen. Das Fehlen von Lackabplatzungen oder Rissen, wie sie bei traditionellen Lackierungen auftreten können, sorgt für eine dauerhaft ansprechende Optik und schützt vor Korrosion.
Ein wichtiger Aspekt der Felgenpulverbeschichtung ist die Zuverlässigkeit der Beschichtung. Der Einbrennprozess sorgt dafür, dass die Pulverbeschichtung dauerhaft mit der Felge verbunden ist. Diese starke Bindung zwischen Pulverschicht und Felgenmaterial macht die Beschichtung besonders widerstandsfähig gegenüber mechanischen Belastungen, wie sie beim Fahren auf unebenem Gelände oder bei starker Beanspruchung auftreten können. Das Resultat ist eine verbesserte Haltbarkeit, die insbesondere für Fahrzeuge, die hohen Belastungen ausgesetzt sind, von Vorteil ist.
Ein weiteres stark wachsendes Segment ist die Felgenrestaurierung. Für Felgen, die im Laufe der Zeit beschädigt oder stark abgenutzt wurden, bietet die Pulverbeschichtung eine ideale Lösung zur Renovierung. Die beschädigten Felgen können durch Strahlen, Reparatur von Dellen oder Rissen und anschließender Pulverbeschichtung wieder in einen neuwertigen Zustand versetzt werden. Diese Methode ist nicht nur kostengünstiger als der Kauf neuer Felgen, sondern auch umweltfreundlicher, da sie den Bedarf an neuen Materialien verringert und somit zur Ressourcenschonung beiträgt.
Die Feinabstimmung der Pulverbeschichtung hat sich in den letzten Jahren weiterentwickelt. Mit der Einführung von multischichtigen Pulversystemen kann eine hochgradige Kratzfestigkeit erreicht werden, die den Felgen noch mehr Widerstandsfähigkeit gegen äußere Einflüsse verleiht. Diese Zweifachbeschichtungen, bei denen eine erste Schicht für den Korrosionsschutz und eine zweite Schicht für die optische Gestaltung sorgt, sind besonders für Felgen im Premium- oder Sportfahrzeugbereich gefragt. Durch die Kombination von Farbeffekten und Zusatzschutz wird die Felge nicht nur optisch aufgewertet, sondern auch die Funktionalität auf lange Sicht verbessert.
Technologische Innovationen in der Pulverbeschichtungstechnik machen den gesamten Prozess auch umweltfreundlicher. Die Verwendung von Niedertemperaturpulvern ermöglicht es, die Pulverbeschichtung bei geringeren Temperaturen durchzuführen, was den Energieverbrauch im Vergleich zu herkömmlichen Verfahren deutlich senkt. Dies kommt nicht nur der Energieeffizienz, sondern auch der Reduzierung der CO2-Emissionen zugute. Darüber hinaus wird die Abfallmenge durch das Recycling von überschüssigem Pulver verringert, was den gesamten Prozess nachhaltig macht.
Ein weiterer wachsender Trend in der Felgenpulverbeschichtung ist die Integration von Nanotechnologie. Nanostrukturierte Pulverbeschichtungen bieten Vorteile wie höhere Beständigkeit gegenüber Kratzern, verbesserte Hydrophobie (wasserabweisende Eigenschaften) und bessere Reinigbarkeit. Solche Technologien sind besonders für Fahrzeuge im Alltagsgebrauch von Vorteil, da sie die Wartung vereinfachen und gleichzeitig die Lebensdauer der Felgen verlängern. Nanobeschichtungen können auch die Bildung von Schmutz oder Bremsstaub verringern, wodurch die Felgen immer sauberer bleiben.
Nicht zuletzt spielt auch die individuelle Gestaltung eine immer wichtigere Rolle. Felgenpulverbeschichtungen bieten unendliche Gestaltungsmöglichkeiten in Bezug auf Farben, Oberflächenstrukturen (wie Matt, Glänzend, Perlmutt oder Metallic) und Designs. Fahrer von Luxusfahrzeugen oder Tuning-Enthusiasten schätzen die Möglichkeit, ihre Felgen nach eigenen Vorlieben zu gestalten. Unternehmen, die sich auf die Beschichtung von Felgen spezialisiert haben, bieten zunehmend maßgeschneiderte Lösungen an, um den spezifischen Anforderungen ihrer Kunden gerecht zu werden.
Abschließend lässt sich sagen, dass die Felgenpulverbeschichtung aufgrund ihrer zahlreichen Vorteile – von Langlebigkeit und Umweltfreundlichkeit bis hin zu ästhetischen Möglichkeiten – eine der bevorzugten Beschichtungsmethoden in der Automobilindustrie darstellt. Die kontinuierliche Verbesserung von Materialien und Prozesstechnologien sorgt dafür, dass diese Technik auch in Zukunft eine wichtige Rolle bei der Herstellung und Restaurierung von Felgen spielen wird. Sie stellt sicher, dass Felgen nicht nur optisch ansprechend, sondern auch funktional und umweltbewusst verarbeitet werden.
Pistole für Pulverbeschichtung
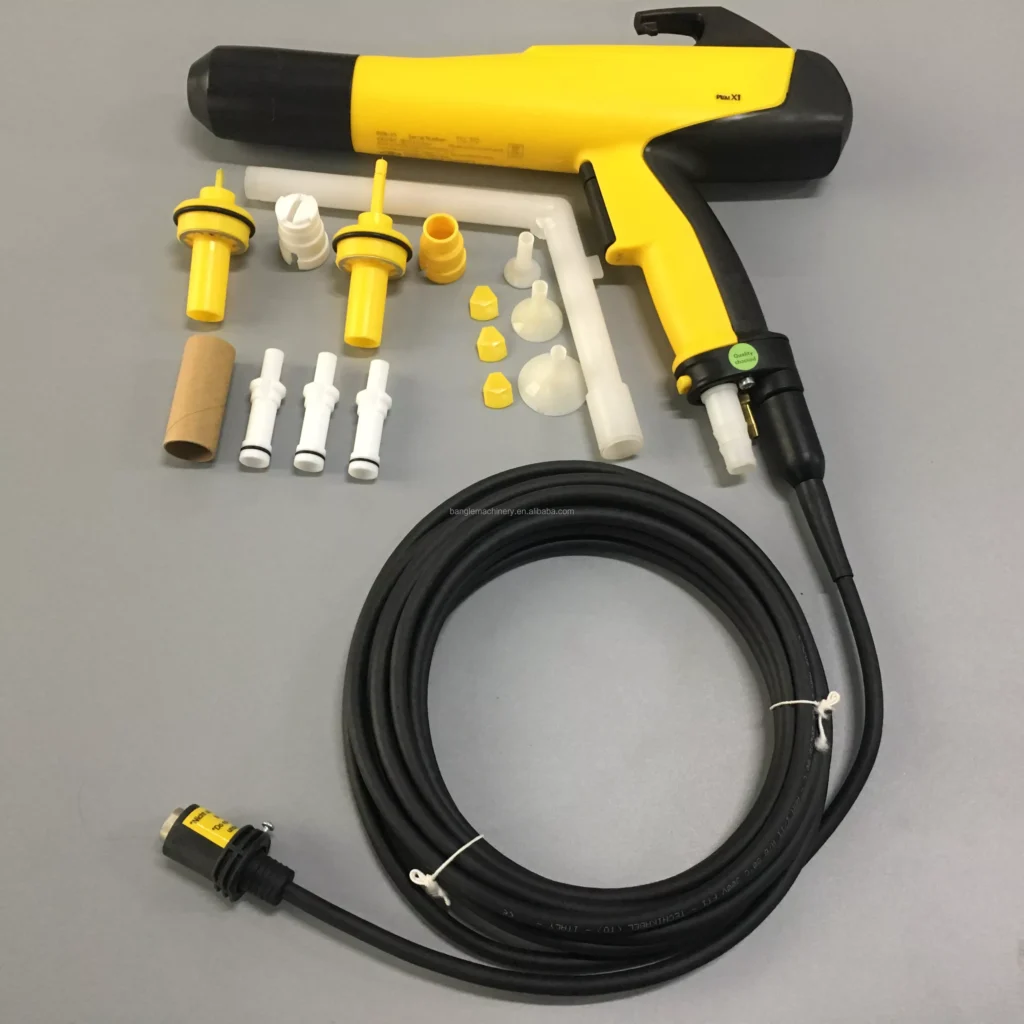
Die Handgeräte und Pistolen für die Pulverbeschichtung sind entscheidende Werkzeuge, die es ermöglichen, Pulver effizient und gleichmäßig auf die zu beschichtenden Oberflächen aufzutragen. Diese Geräte arbeiten in der Regel mit der elektrostatischen Aufladung, bei der das Pulver an die Oberfläche des Werkstücks angezogen wird, um eine gleichmäßige und dauerhafte Beschichtung zu gewährleisten. Handgeräte und Pistolen sind in der Pulverbeschichtung sowohl in der industriellen Fertigung als auch im kleineren Handwerksbereich weit verbreitet, da sie eine hohe Flexibilität und Präzision bieten.
Funktion und Aufbau der Pulverbeschichtungspistole
Eine typische Pulverbeschichtungspistole besteht aus mehreren Hauptkomponenten:
- Pulverbehälter: In diesem Behälter befindet sich das Pulver, das mit Luft vermischt wird, um eine pneumatische Förderung zu ermöglichen.
- Luftzufuhrsystem: Hier wird das Pulver mit komprimierter Luft gemischt und durch die Pistole auf die zu beschichtende Oberfläche gesprüht. Das System sorgt dafür, dass das Pulver gleichmäßig und effizient verteilt wird.
- Elektrostatische Aufladungseinheit: Diese Einheit lädt das Pulver elektrisch auf, was es ermöglicht, dass das Pulver aufgrund der elektrostatischen Anziehung an der Werkstückoberfläche haftet.
- Düse: Die Düse ist der Teil der Pistole, der das Pulver auf das Werkstück abgibt. Sie ist so konstruiert, dass der Pulverstrahl gleichmäßig und präzise dosiert wird.
Ein weiteres wichtiges Element ist die Einstellung der Luft- und Pulvermenge, die eine präzise Steuerung des Auftrags ermöglicht. Durch die Anpassung der Luftdruckstärke und der Pulvermengensteuerung können verschiedene Pulvertrocknungseffekte erzielt werden, sodass der Bediener je nach Bedarf eine dickere oder dünnere Schicht auftragen kann.
Arten von Pulverbeschichtungspistolen
Es gibt verschiedene Arten von Handgeräten und Pistolen für die Pulverbeschichtung, die sich durch ihre Technologie, Einsatzmöglichkeiten und Ergonomie unterscheiden:
- Kartenpistolen: Diese Pistolen sind besonders für kleinere und manuelle Anwendungen geeignet. Sie sind häufig in der Heimwerkstatt oder für Prototypenfertigungen zu finden. Der Kartenmechanismus sorgt für eine präzise Pulverabgabe und eine gleichmäßige Aufbringung, ist jedoch in seiner Anwendung etwas langsamer als die automatisierten Modelle.
- Automatische Pistolen: Diese Pistolen sind speziell für die Massenproduktion oder den seriellen Einsatz konzipiert. Sie arbeiten meist mit automatisierten Steuerungen und Voreinstellungen, um eine konstante Pulvermenge und -dichte zu gewährleisten. Solche Pistolen sind besonders in der Automobilindustrie oder der Beschichtung von großen Bauteilen von Vorteil, da sie eine gleichbleibende Qualität und Effizienz ermöglichen.
- Zweikomponenten-Pistolen: Diese Pistolen kommen zum Einsatz, wenn das Pulver mit einer speziellen Lackbeschichtung kombiniert werden muss. Sie sind ideal für Anwendungen, bei denen Multifunktionalität erforderlich ist, etwa bei der Kombination von Pulverbeschichtung und zusätzlichem Farbauftrag.
Technologie und Innovationen
Moderne Handgeräte und Pistolen für die Pulverbeschichtung zeichnen sich durch innovative Technologien aus, die den Beschichtungsprozess deutlich effizienter und genauer machen. Ein Beispiel hierfür ist der Corona- oder Tribo-Effekt:
- Corona-Pistolen: Diese Pistolen arbeiten mit einer Hochspannungsquelle, die eine hohe elektrostatische Aufladung erzeugt, die das Pulver auf die Werkstückoberfläche zieht. Sie sind besonders geeignet für nicht leitende Oberflächen und bieten eine hohe Vielseitigkeit in Bezug auf Pulverarten und Oberflächenstrukturen.
- Tribo-Pistolen: Bei Tribo-Pistolen wird das Pulver durch Reibung aufgeladen, anstatt durch eine Hochspannungsquelle. Diese Pistolen sind vor allem bei der Beschichtung von leitfähigen Materialien oder bei Anwendungen, bei denen eine gleichmäßige Beschichtungsdichte auf kleinen Bauteilen erforderlich ist, von Vorteil.
Energieeffizienz und Nachhaltigkeit
Die Energieeffizienz ist ein immer wichtiger werdender Faktor bei der Auswahl von Handgeräten und Pistolen für die Pulverbeschichtung. Moderne Geräte verfügen über variabel einstellbare Luftstrom- und Pulverabgabemengen, die den Materialverbrauch optimieren und den Energieverbrauch senken. Das Recycling von überschüssigem Pulver wird durch intelligente Filtrationssysteme und Materialrückgewinnungseinrichtungen weiter verbessert, sodass weniger Pulver verschwendet wird und die Kosten sinken.
Darüber hinaus bieten viele Pulverpistolen mittlerweile ergonomische Designs, die den Komfort des Benutzers erhöhen. Diese Designs sind auf eine einfache Handhabung ausgelegt, was die Belastung der Hände und Arme reduziert, insbesondere bei längeren Arbeitseinsätzen.
Einsatzgebiete und Anwendung
Pulverbeschichtungspistolen werden in einer Vielzahl von Industrien eingesetzt, wie etwa der Automobilindustrie, Möbelherstellung, Elektroindustrie und Bauindustrie. Sie eignen sich besonders für die Beschichtung von Metalloberflächen, Felgen, Rohrleitungen, Gerüsten und Kunststoffteilen. Durch die vielseitige Anwendbarkeit und die Möglichkeit, unterschiedliche Pulversorten zu verwenden, ist die Pulverbeschichtung ein besonders flexibles Verfahren.
Vorteile der Handgeräte für Pulverbeschichtung
- Flexibilität: Handgeräte ermöglichen es, sowohl kleine als auch große Teile effizient zu beschichten, und bieten eine hohe Anpassungsfähigkeit an verschiedene Werkstückgrößen und -formen.
- Schnelligkeit und Präzision: Die Möglichkeit, die Pulvermenge und Auftragstechnik präzise zu steuern, garantiert eine hohe Beschichtungsqualität bei minimalem Materialverbrauch.
- Umweltfreundlichkeit: Im Vergleich zu flüssigen Lackierungen erzeugen Pulverbeschichtungspistolen weniger Lösungsmittelabgase und sind daher umweltfreundlicher.
- Geringe Instandhaltung: Pulverbeschichtungspistolen haben in der Regel eine lange Lebensdauer und sind relativ pflegeleicht. Sie erfordern nur gelegentliche Wartung der Luftzufuhrsysteme und der Pulverbehälter.
Insgesamt bieten Handgeräte und Pistolen für die Pulverbeschichtung eine effiziente und umweltfreundliche Möglichkeit, Oberflächen zu veredeln, wobei die Technologie, Energieeffizienz und ergonomische Verbesserungen der neuesten Modelle dazu beitragen, den Beschichtungsprozess weiter zu optimieren und den Materialverbrauch zu minimieren.
Zukunftstrends und Entwicklungen in der Pulverbeschichtungstechnik
Die Technologie rund um Handgeräte und Pistolen für Pulverbeschichtung entwickelt sich stetig weiter, mit dem Ziel, noch effizientere, präzisere und umweltfreundlichere Lösungen zu bieten. Einige der zukünftigen Trends und Entwicklungen umfassen:
- Integration von digitalen Steuerungssystemen: Zukünftige Pulverbeschichtungspistolen werden zunehmend mit digitalen Steuerungen ausgestattet sein, die eine noch genauere Anpassung der Pulvermenge, Luftstromstärke und Auftragstechnik ermöglichen. Durch den Einsatz von Smart-Technologie wird es möglich sein, die Performance in Echtzeit zu überwachen und Anpassungen vorzunehmen, um die Beschichtungsqualität weiter zu steigern. Diese digitalen Systeme können auch die Prozessdokumentation automatisieren, was vor allem für die Qualitätskontrolle und -sicherung wichtig ist.
- **Verbesserte Ergonomie und Benutzerfreundlichkeit: Ein weiterer Trend ist die Verbesserung der Ergonomie der Handgeräte und Pistolen. Neue Modelle werden immer leichter und komfortabler in der Handhabung, um die Belastung für die Bediener zu verringern. Es werden auch drehbare oder schwenkbare Griffdesigns entwickelt, die den Einsatz in unterschiedlichen Positionen erleichtern, was besonders in engen Arbeitsbereichen oder bei der Beschichtung von komplexen Bauteilen von Vorteil ist.
- Intelligente Pulverrückgewinnungssysteme: Um den Materialverbrauch weiter zu senken, werden immer fortschrittlichere Pulverrückgewinnungssysteme entwickelt. Diese Systeme filtern das überschüssige Pulver effizienter aus der Luft und ermöglichen dessen Wiederverwendung, was nicht nur die Kosten senkt, sondern auch die Umweltbelastung verringert. Einige moderne Systeme sind sogar in der Lage, das Pulver nach der Rückgewinnung auf Partikelgröße und Qualität zu überprüfen, um sicherzustellen, dass nur hochqualitatives Pulver wiederverwendet wird.
- Verwendung von neuen Pulverarten: Mit der kontinuierlichen Entwicklung von Pulvermaterialien sind neue Arten von Pulvern auf dem Markt, die bessere Widerstandsfähigkeit, UV-Beständigkeit und Witterungsbeständigkeit bieten. Diese Pulversorten können eine verbesserte Korrosionsschutzwirkung bieten und sind besonders in außen liegenden Anwendungen, wie etwa bei der Beschichtung von Fahrzeugteilen oder Baugerüsten, von Bedeutung. Die Handgeräte der Zukunft müssen in der Lage sein, diese innovativen Pulversorten effizient aufzutragen und die spezifischen Eigenschaften dieser neuen Materialien zu nutzen.
- Automatisierte Beschichtungsprozesse: Auch die Handgeräte und Pistolen für die Pulverbeschichtung werden zunehmend mit automatisierten Funktionen ausgestattet. Automatisierte Systemanpassungen, wie die automatische Justierung der Pulvermenge basierend auf der Größe und Form des Werkstücks, verbessern die Effizienz und stellen sicher, dass der Beschichtungsprozess unter allen Bedingungen gleichbleibend hohe Ergebnisse liefert. Besonders in der Automobilindustrie oder bei der Herstellung von Elektrogeräten, wo eine hohe Produktionsrate erforderlich ist, wird dies einen großen Unterschied machen.
- **Verbesserte Lackiergeschwindigkeit und Vielseitigkeit: Zukünftige Pistolen könnten auch die Lackiergeschwindigkeit durch den Fokus auf Hochleistungspulver und optimierte Auftragstechniken erhöhen. Dies ermöglicht eine schnellere und gleichmäßigere Beschichtung bei geringeren Betriebskosten. Zudem wird die Vielseitigkeit der Handgeräte in Zukunft noch größer, sodass eine breite Palette an Materialien (einschließlich Plastik oder Verbundwerkstoffen) effizient beschichtet werden kann.
Vorteile der Weiterentwicklungen für die Industrie
Die fortschrittlichen Handgeräte und Pistolen für Pulverbeschichtung bieten zahlreiche Vorteile für Unternehmen und Produktionsstätten:
- Kostenersparnis: Durch die Integration von Technologien wie der Pulverrückgewinnung und den intelligenten Steuerungssystemen können Unternehmen den Materialverbrauch senken und die Betriebskosten reduzieren. Das ermöglicht eine wirtschaftlichere Produktion, besonders bei großen Stückzahlen.
- Erhöhte Produktionsgeschwindigkeit: Verbesserte Sprühtechniken und automatisierte Prozesse führen zu einer effizienteren Nutzung der Zeit, was in einer höheren Produktivität resultiert. Auch die Kombination von Handpistolen und Automatisierung in bestimmten Bereichen wird helfen, Produktionsprozesse zu beschleunigen.
- Verbesserte Qualität und Konsistenz: Die Digitalisierung und präzise Steuerungssysteme sorgen dafür, dass die Qualität der Beschichtung konstant hoch bleibt. Dies ist insbesondere für Unternehmen wichtig, die eine hohe Qualitätssicherung benötigen, wie etwa in der Luftfahrt oder Medizinprodukteherstellung.
- Nachhaltigkeit und Umweltfreundlichkeit: Mit der Integration von umweltfreundlicheren Pulvern und verbesserten Rückgewinnungstechniken wird die Pulverbeschichtung noch umweltfreundlicher. Die Reduktion von Abfällen und die Wiederverwendung von Pulvermaterial tragen zur Reduzierung des CO2-Fußabdrucks bei.
Zusammenfassung
Handgeräte und Pistolen für die Pulverbeschichtung sind ein entscheidender Bestandteil des gesamten Beschichtungsprozesses und bieten eine Vielzahl von Vorteilen für verschiedene Branchen. Die kontinuierlichen technologischen Innovationen – von der digitalen Steuerung über Energieeffizienz bis hin zu umweltfreundlicheren Materialien – machen die Pulverbeschichtung zu einer der flexibelsten und nachhaltigsten Beschichtungsmethoden. Zukünftige Entwicklungen werden die Leistungsfähigkeit dieser Geräte weiter steigern, was sowohl die Produktionskosten als auch den Materialverbrauch optimiert, während gleichzeitig die Qualität und Effizienz der Beschichtung verbessert wird. Die zunehmende Automatisierung und Ergonomie dieser Geräte wird zudem dazu beitragen, den Prozess für die Bediener einfacher und effizienter zu gestalten.
Der Pulverofen: Funktion, Aufbau und Bedeutung in der Pulverbeschichtung
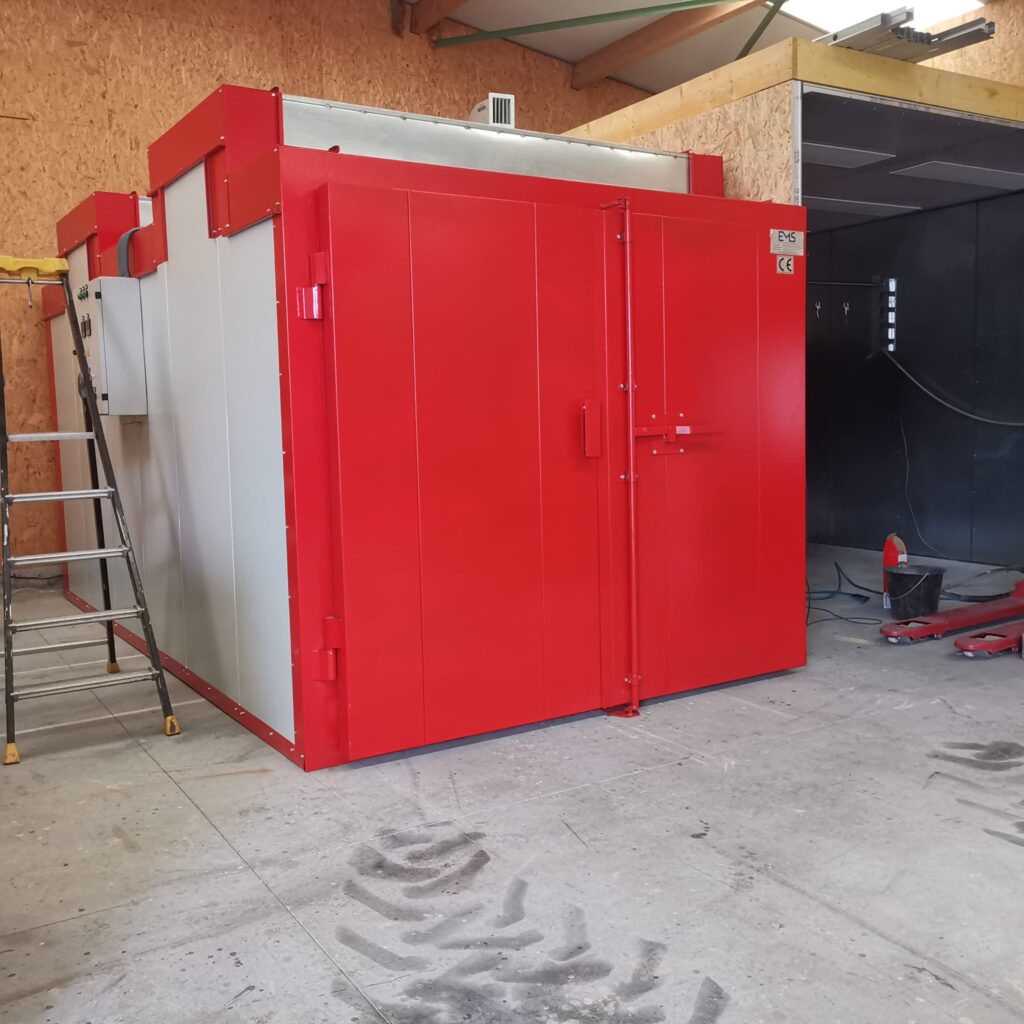
Ein Pulverofen ist ein wichtiger Bestandteil des Pulverbeschichtungsprozesses, der eine wichtige Rolle beim Aushärten des aufgetragenen Pulvers spielt. Nachdem das Pulver gleichmäßig auf die zu beschichtende Oberfläche aufgebracht wurde, muss es in einem Pulverofen bei hohen Temperaturen eingebrannt werden. Dies sorgt dafür, dass das Pulver schmilzt, sich verflüssigt und eine gleichmäßige, stabile Beschichtung auf der Oberfläche bildet, die sowohl mechanisch robust als auch optisch ansprechend ist.
Funktion und Bedeutung des Pulverofens
Der Pulverofen dient der Thermovernetzung des Pulvers, einem Prozess, bei dem die Pulverpartikel durch die Wärme miteinander verbinden und eine glatte, kratzfeste Oberfläche bilden. Während des Einbrennens im Pulverofen wird das Pulver bei einer festgelegten Temperatur über eine bestimmte Zeitdauer erhitzt, sodass es schmilzt und sich zu einer dichten und gleichmäßigen Schicht verbindet.
Der Hauptzweck des Pulverofens ist es, die chemischen Reaktionen im Pulver zu aktivieren, die notwendig sind, um eine widerstandsfähige und dauerhafte Beschichtung zu erzeugen. Dies umfasst das Aushärten der Polymere im Pulver, sodass diese zu einer festen, beständigen Oberfläche werden, die den hohen Anforderungen an Kratzfestigkeit, Korrosionsbeständigkeit und Witterungsbeständigkeit entspricht.
Aufbau eines Pulverofens
Ein Pulverofen besteht aus mehreren wichtigen Komponenten, die zusammenarbeiten, um die notwendige Temperatur und Luftzirkulation aufrechtzuerhalten. Zu den wichtigsten Elementen gehören:
- Heizsystem: Der Heizmechanismus im Pulverofen kann entweder elektrisch oder gasbetrieben sein. Die Heizsysteme müssen gleichmäßige Temperaturen über den gesamten Ofenraum liefern, um eine gleichmäßige Aushärtung des Pulvers zu gewährleisten. Moderne Pulveröfen verfügen häufig über mehrere Heizzonen, die eine präzise Temperaturregelung ermöglichen.
- Temperaturregelung: Die Temperaturregelung im Pulverofen ist entscheidend, da das Pulver nur innerhalb eines bestimmten Temperaturbereichs aushärtet. Meist liegt die Einbrenntemperatur für die meisten Pulversorten zwischen 160°C und 200°C. Eine genaue Überwachung und Regelung der Temperatur sind notwendig, um Überhitzung oder unzureichende Aushärtung zu vermeiden.
- Luftzirkulationssystem: Um die Temperatur im Ofen gleichmäßig zu verteilen, ist ein effektives Luftzirkulationssystem erforderlich. Dieses System sorgt dafür, dass die heiße Luft gleichmäßig im Ofen verteilt wird und das Werkstück in allen Bereichen gleichmäßig erhitzt wird. Eine optimierte Luftzirkulation trägt auch dazu bei, dass der Ofen effizient arbeitet und Energie spart.
- Fördersysteme: In größeren Produktionsanlagen sind Pulveröfen häufig mit Förderbändern oder Wagen ausgestattet, die es ermöglichen, die beschichteten Teile kontinuierlich durch den Ofen zu bewegen. Diese Systeme gewährleisten eine gleichmäßige Belichtung der Werkstücke bei konstanter Geschwindigkeit, was für die Konsistenz des Beschichtungsprozesses entscheidend ist.
- Isolierung: Da Pulveröfen hohe Temperaturen erzeugen, ist eine gute Isolierung notwendig, um die Energieeffizienz zu maximieren und die Außenwände des Ofens vor übermäßiger Wärmeabgabe zu schützen. Eine hochwertige Isolierung reduziert die Wärmeverluste und sorgt dafür, dass der Ofen effizient arbeitet, während die Betriebskosten gesenkt werden.
- Abluft- und Abgasmanagement: Während des Einbrennprozesses entstehen verschiedene Dämpfe und Abgase, die sorgfältig aus dem Ofen entfernt werden müssen. Moderne Pulveröfen sind oft mit Abluftsystemen ausgestattet, die dafür sorgen, dass schädliche Dämpfe effizient abgeführt werden, ohne die Umwelt oder die Gesundheit der Arbeiter zu gefährden.
Arten von Pulveröfen
Es gibt verschiedene Arten von Pulveröfen, die je nach Produktionsbedarf und Werkstückgröße variieren. Zu den gängigsten Typen gehören:
- Batch-Pulveröfen: Bei Batch-Pulveröfen werden die Werkstücke in Chargen behandelt. Diese Öfen sind ideal für kleinere Produktionen oder für die Bearbeitung unterschiedlicher Werkstücke mit variierenden Größen und Formen. Die Chargenweise Bearbeitung ermöglicht eine präzise Kontrolle des Einbrennprozesses, ist aber in großen Serienproduktionen weniger effizient.
- Kontinuierliche Pulveröfen: Bei kontinuierlichen Pulveröfen werden die Werkstücke stetig durch den Ofen geführt, meist auf einem Förderband. Diese Art von Ofen ist ideal für große Produktionsmengen, da der Prozess effizient und ohne Unterbrechung abläuft. Kontinuierliche Pulveröfen bieten eine hohe Produktivität, erfordern jedoch eine präzise Steuerung der Temperatur und der Luftzirkulation, um eine gleichmäßige Beschichtung zu gewährleisten.
- Tunnelöfen: Tunnelöfen sind eine Unterart der kontinuierlichen Pulveröfen und bieten den Vorteil, dass mehrere Werkstücke gleichzeitig durch den Ofen geführt werden können. Sie bestehen aus einem langen Tunnel, durch den die Werkstücke auf Förderbändern transportiert werden. Tunnelöfen bieten hohe Durchsatzraten und sind besonders für die Automobilindustrie oder andere Massenproduktion geeignet.
Vorteile von Pulveröfen in der Pulverbeschichtung
- Hohe Qualität der Beschichtung: Pulveröfen ermöglichen es, eine gleichmäßige und hochwertige Beschichtung zu erzielen, da die Temperaturregelung und die Luftzirkulation präzise eingestellt werden können. Dies führt zu einer kratzfesten, langfristig beständigen und optisch ansprechenden Oberfläche.
- Energieeffizienz: Moderne Pulveröfen sind so konstruiert, dass sie eine hohe Energieeffizienz aufweisen. Durch eine effektive Wärmeisolierung und optimierte Luftzirkulation wird die benötigte Energie für den Einbrennprozess minimiert.
- Kostensenkung: Die Nutzung eines kontinuierlichen Pulverofens oder eines Tunnelofens in der Massenproduktion senkt die Produktionskosten erheblich. Die automatisierte Steuerung und die geringe Instandhaltungsintensität tragen dazu bei, dass Unternehmen Kosten einsparen können.
- Vielseitigkeit: Pulveröfen können für die Aushärtung einer Vielzahl von Pulvern genutzt werden, einschließlich Epoxidharzen, Polyesterpulvern und speziellen hochtemperaturbeständigen Pulvern. Dadurch können Unternehmen verschiedene Produkte mit einer breiten Palette von Beschichtungseigenschaften herstellen.
Nachhaltigkeit und Zukunftstrends
Die Nachhaltigkeit und die Reduktion von CO2-Emissionen sind auch in der Ofentechnologie ein zunehmend wichtiger Aspekt. Zu den Zukunftstrends gehören:
- Verbesserte Energieeffizienz: Durch den Einsatz von Wärmerückgewinnungssystemen und die Integration von Low-Emission-Heiztechnologien werden Pulveröfen in Zukunft noch umweltfreundlicher und energieeffizienter.
- Automatisierung und Prozesssteuerung: Mit der Einführung von Smart-Technology in Pulveröfen wird der Prozess weiter automatisiert und die Prozessüberwachung vereinfacht. Dies ermöglicht eine optimierte Produktion mit weniger Ausschuss und höheren Produktionsraten.
- Recycling von überschüssigem Pulver: Ein weiteres wachsendes Feld ist das Recycling von überschüssigem Pulver, das im Ofenprozess verloren geht. Moderne Systeme zur Pulverrückgewinnung sorgen dafür, dass überschüssiges Pulver wiederverwendet wird, was nicht nur die Kosten senkt, sondern auch Umweltressourcen schont.
Zusammenfassung
Der Pulverofen spielt eine entscheidende Rolle im Pulverbeschichtungsprozess, indem er das aufgetragene Pulver härtet und eine widerstandsfähige Beschichtung bildet. Die verschiedenen Ofentypen und die fortschrittliche Technologie in den Bereichen Temperaturregelung, Luftzirkulation und Energieeffizienz bieten Unternehmen die Möglichkeit, den Beschichtungsprozess zu optimieren und gleichzeitig die Produktionskosten zu senken. Die kontinuierliche Weiterentwicklung der Ofentechnologie in Richtung Nachhaltigkeit, Automatisierung und Energieeinsparung wird in Zukunft eine noch größere Rolle spielen.
Zukunftstrends und Weiterentwicklungen im Bereich Pulverofen
Die kontinuierliche Weiterentwicklung der Pulverofen-Technologie zielt darauf ab, die Energieeffizienz, Produktivität und Umweltfreundlichkeit weiter zu steigern, um den Anforderungen der Industrie gerecht zu werden. Einige der bemerkenswerten Zukunftstrends und Weiterentwicklungen im Bereich Pulveröfen sind:
- Integration von IoT und Smart-Technologien: Internet of Things (IoT)-basierte Technologien werden zunehmend in Pulveröfen integriert. Dies ermöglicht die Fernüberwachung und Steuerung des Einbrennprozesses in Echtzeit. Sensoren und Datenanalysen können dabei helfen, die Temperatur und Luftzirkulation im Ofen exakt zu überwachen und automatisch Anpassungen vorzunehmen, um den Prozess zu optimieren. Solche Systeme können zudem Fehlermeldungen und Wartungsbenachrichtigungen in Echtzeit senden, was die Instandhaltung vereinfacht und Ausfallzeiten reduziert.
- Wärmerückgewinnung und nachhaltige Energiequellen: Ein wichtiger Aspekt der Zukunftstechnologie für Pulveröfen ist die Wärmerückgewinnung. Durch den Einsatz von Wärmetauschern können überschüssige Abwärme und heiße Luft im Ofen genutzt werden, um neue Chargen zu erhitzen oder sogar die Betriebsgebäude zu beheizen. Dies trägt erheblich zur Energieeffizienz bei und senkt die Betriebskosten. Zudem wird vermehrt der Einsatz von erneuerbaren Energiequellen wie Solarenergie oder Wärmepumpen in Pulveröfen untersucht, um den CO2-Ausstoß weiter zu minimieren.
- Verbesserung der Ofenmaterialien und -technologien: Zukünftige Pulveröfen werden aus fortschrittlicheren Materialien bestehen, die nicht nur höhere Betriebstemperaturen widerstandsfähiger sind, sondern auch eine noch bessere Wärmeisolierung bieten. Durch den Einsatz von keramischen Beschichtungen und hochfesten Isoliermaterialien wird der Wärmeverlust weiter reduziert, was zu einer besseren Energieausnutzung führt und gleichzeitig die Langlebigkeit der Öfen erhöht.
- Modulare und skalierbare Ofensysteme: Um der steigenden Nachfrage nach maßgeschneiderten Lösungen gerecht zu werden, werden Pulveröfen zunehmend modular gebaut. Unternehmen können Ofensysteme nach ihren spezifischen Bedürfnissen skalieren, sodass kleinere Betriebe mit einer kompakten Lösung starten können und bei wachsendem Bedarf den Ofen auf größere Kapazitäten erweitern können. Diese Flexibilität wird den Unternehmen helfen, ihre Produktionsanforderungen anzupassen und gleichzeitig Kosten zu sparen.
- Automatisierte Reinigung und Wartung: Ein weiteres Zukunftsmerkmal von Pulveröfen ist die Automatisierung der Reinigung und Instandhaltung. Robotertechnologie und automatisierte Reinigungssysteme werden eingesetzt, um die regelmäßige Wartung des Ofens zu vereinfachen. Insbesondere in industriellen Produktionsumgebungen, in denen regelmäßig verschiedene Pulversorten verwendet werden, wird es notwendig, den Ofen effizient zu reinigen, um Kontaminationen und unerwünschte Reaktionen zu vermeiden. Selbstreinigende Systeme und automatische Düsensysteme sind daher ein wachsender Trend, der den Arbeitsaufwand für Wartung und Reinigung erheblich reduziert.
- Erweiterte Prozesskontrolle und Qualitätssicherung: Die Zukunft von Pulveröfen wird auch von verbesserten Prozesskontrollsystemen geprägt sein. Durch den Einsatz von künstlicher Intelligenz (KI) und Maschinellem Lernen können Pulveröfen den Beschichtungsprozess kontinuierlich analysieren und anpassen, um eine höchstmögliche Qualität und Konsistenz zu gewährleisten. Die KI kann auch dabei helfen, die Energieeffizienz zu maximieren und Ausfallzeiten durch frühzeitige Fehlerdiagnosen zu minimieren.
- Fokus auf kleinere Chargen und flexible Produktionsmethoden: Neben der Massenproduktion wird es eine zunehmende Nachfrage nach kleineren Chargen und flexiblen Produktionsmethoden geben. Pulveröfen werden in Zukunft nicht nur für große Serienproduktionen ausgelegt, sondern auch für kleinere, kundenspezifische Aufträge optimiert. Batch-Öfen und kompakte Ofensysteme werden verstärkt in Bereichen wie der Möbelindustrie, der Feinmechanik und der Automobilindustrie eingesetzt, wo maßgeschneiderte Beschichtungen benötigt werden.
- Alternative Pulversorten und Oberflächenbehandlungen: Mit der zunehmenden Forschung und Entwicklung im Bereich der Pulverbeschichtungen werden neue Pulversorten entwickelt, die besser auf die Anforderungen spezifischer Anwendungen abgestimmt sind. Diese neuen Pulverarten erfordern möglicherweise auch die Entwicklung von neuen Öfen oder speziell angepassten Einbrenntechniken, um eine optimale Aushärtung zu gewährleisten. Dies betrifft vor allem pulverbeschichtete Oberflächen, die besondere Anforderungen an Korrosionsschutz oder Kratzfestigkeit stellen.
Vorteile der Weiterentwicklungen für Unternehmen
Die Innovation und Technologisierung im Bereich der Pulveröfen bieten den Unternehmen viele Vorteile, darunter:
- Höhere Effizienz: Durch die Integration von automatisierten Steuerungen, Prozessanalysen und modularen Ofensystemen können Unternehmen ihre Produktionsprozesse effizienter gestalten. Dies führt zu einer höheren Durchsatzrate, geringerem Energieverbrauch und einer besseren Materialausnutzung.
- Kostenersparnis: Die verbesserten Wärmerückgewinnungssysteme und die optimierte Energieeffizienz sorgen dafür, dass Unternehmen ihre Betriebskosten senken können. Zudem ermöglicht die automatisierte Reinigung und Wartung eine Reduktion der Instandhaltungskosten.
- Bessere Qualität: Die Fortschritte in der Prozesskontrolle und der Integration von KI-Technologien ermöglichen eine höhere Konsistenz und Qualität der Beschichtungen. Die präzise Temperaturregelung und die kontinuierliche Überwachung der Prozessparameter sorgen dafür, dass die Endprodukte den höchsten Standards entsprechen.
- Nachhaltigkeit: Der Fokus auf Energieeffizienz und Wärmerückgewinnung trägt nicht nur zur Senkung der Betriebskosten bei, sondern unterstützt auch das Bestreben, den CO2-Ausstoß und den Energieverbrauch zu reduzieren. Dies ist nicht nur ökologisch sinnvoll, sondern auch eine wichtige Voraussetzung für Unternehmen, die nachhaltig produzieren wollen.
- Flexibilität: Die modularen Ofensysteme bieten Unternehmen die Möglichkeit, ihre Produktion nach Bedarf zu skalieren. Dies ist besonders vorteilhaft für Unternehmen, die auf spezielle Aufträge oder kleinere Produktserien angewiesen sind.
Zusammenfassung
Der Pulverofen ist ein unverzichtbares Gerät im Pulverbeschichtungsprozess, das die Aushärtung des Pulvers ermöglicht und eine hochwertige, dauerhafte Beschichtung gewährleistet. Mit der kontinuierlichen Weiterentwicklung in den Bereichen Energieeffizienz, Automatisierung und Prozesskontrolle wird die Technologie in den nächsten Jahren immer präziser und nachhaltiger werden. Zukünftige Pulveröfen werden nicht nur den Produktionsprozess optimieren, sondern auch Kosten reduzieren und Umweltvorteile bieten. Unternehmen, die diese Technologien frühzeitig adaptieren, werden in der Lage sein, sich wettbewerbsfähig zu positionieren und von den Fortschritten in der Pulverofentechnologie zu profitieren.
Automatische Pulverbeschichtungsanlage: Einführung, Funktion und Vorteile
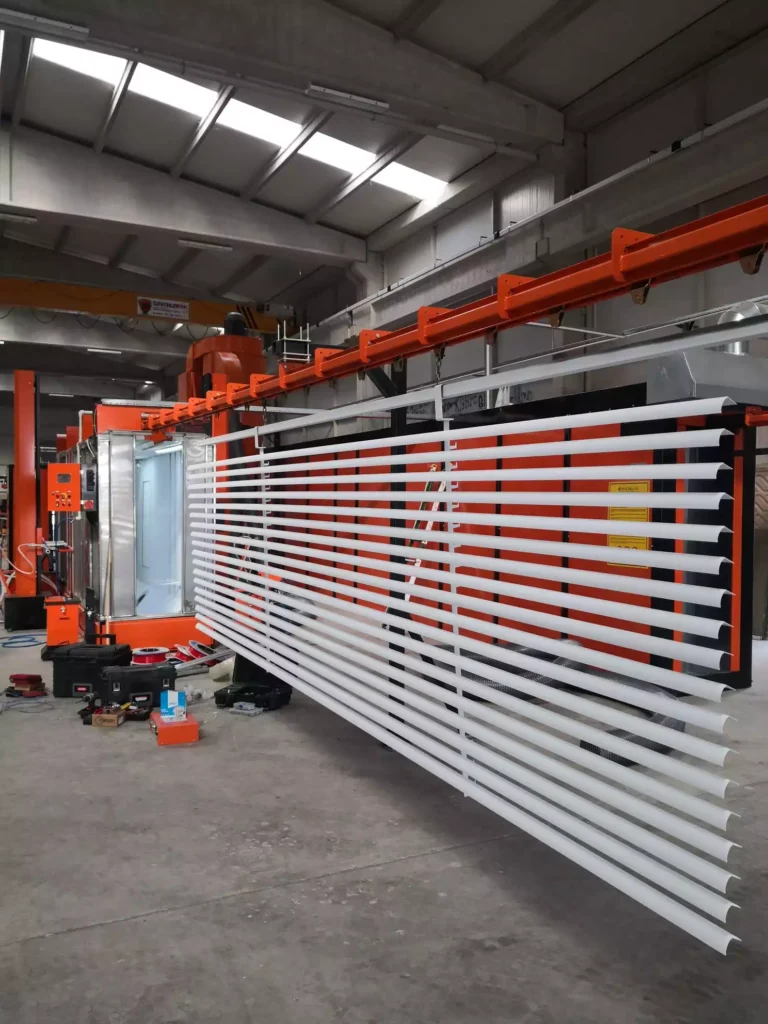
Eine automatische Pulverbeschichtungsanlage ist eine hochentwickelte Einrichtung, die den Prozess der Pulverbeschichtung automatisiert und optimiert. Diese Anlagen bieten eine effiziente Lösung für die kontinuierliche und gleichmäßige Beschichtung großer Stückzahlen von Werkstücken, was in der modernen industriellen Fertigung von großer Bedeutung ist. Besonders in Bereichen wie der Automobilindustrie, der Metallverarbeitung und der Möbelindustrie sind automatische Pulverbeschichtungsanlagen von zentraler Bedeutung, um qualitativ hochwertige Beschichtungen schnell und in großen Mengen zu gewährleisten.
Funktion und Aufbau einer automatischen Pulverbeschichtungsanlage
Eine automatische Pulverbeschichtungsanlage besteht aus mehreren modularen Komponenten, die miteinander integriert arbeiten, um den gesamten Beschichtungsprozess zu automatisieren. Die wichtigsten Bestandteile einer solchen Anlage sind:
- Pulveraufbereitungseinheit: Zu Beginn des Prozesses wird das Pulver in der Pulveraufbereitungseinheit gelagert und in die Pulverpistolen oder Sprühdüsen der Anlage eingespeist. Diese Einheit sorgt dafür, dass das Pulver korrekt gemischt und gleichmäßig verteilt wird, um eine konstante Pulversprühqualität sicherzustellen. Sie umfasst auch Systeme zur Rückgewinnung von überschüssigem Pulver, um Abfall zu minimieren und die Materialkosten zu senken.
- Automatisierte Applikationssysteme: Die Pulverapplikation erfolgt durch automatische Sprühpistolen, die entweder in einer Schwenkbewegung oder in einer vertikal-horizontalen Richtung arbeiten. Diese Pistolen werden oft an industriellen Roboterarmen befestigt, die die Werkstücke kontinuierlich anfahren und beschichten. Der Sprühdruck und die Sprühgeschwindigkeit können je nach Material, Pulvertype und Werkstückgröße angepasst werden. Die automatischen Pistolen stellen sicher, dass die Beschichtung gleichmäßig und ohne menschliches Eingreifen aufgetragen wird.
- Fördersysteme: In einer automatisierten Pulverbeschichtungsanlage gibt es in der Regel Förderbänder oder Förderketten, die die Werkstücke kontinuierlich durch verschiedene Beschichtungsstationen bewegen. Die Fördersysteme transportieren die Teile von einer Station zur nächsten und sorgen dafür, dass der Prozess ohne Unterbrechungen und in einem gleichmäßigen Rhythmus abläuft. In größeren Anlagen kann das Förderband auch in verschiedene Sektionen unterteilt werden, die für unterschiedliche Phasen des Prozesses verantwortlich sind.
- Pulverofen (Einbrennofen): Nachdem das Pulver auf die Werkstücke aufgetragen wurde, müssen die Teile in den Pulverofen oder Einbrennofen geführt werden, wo sie einer konstanten Temperatur ausgesetzt werden, um das Pulver zu härten und eine beständige, widerstandsfähige Beschichtung zu schaffen. Der Ofen ist mit einem kontrollierten Temperaturmanagementsystem ausgestattet, um die Pulverschicht gleichmäßig zu verflüssigen und zu vernetzen.
- Abkühlzone: Nach dem Einbrennprozess müssen die beschichteten Werkstücke abkühlen, um ihre endgültige Festigkeit und Stabilität zu erlangen. In modernen automatisierten Anlagen ist diese Abkühlzone häufig ebenfalls automatisiert, wobei die Werkstücke entweder durch Luftkühlung oder Wasserabkühlung schnell auf Umgebungstemperatur heruntergekühlt werden.
- Absauganlage und Luftfiltersystem: Um sicherzustellen, dass die Luftqualität in der Produktionsumgebung aufrechterhalten bleibt und überschüssiges Pulver effizient entfernt wird, sind automatische Pulverbeschichtungsanlagen mit Absauganlagen ausgestattet. Diese Systeme sorgen dafür, dass der Pulverstaub und Dämpfe aus dem Arbeitsbereich entfernt werden, wodurch sowohl die Arbeitssicherheit als auch die Produktqualität verbessert wird.
- Automatische Kontrolle und Überwachung: Moderne automatische Pulverbeschichtungsanlagen sind mit Sensoren und Steuerungssystemen ausgestattet, die den gesamten Beschichtungsprozess überwachen. Diese Systeme ermöglichen die präzise Steuerung von Parametern wie Sprühdruck, Pulvermengen und Temperaturen. Die Prozessdaten werden in Echtzeit erfasst und analysiert, sodass Abweichungen sofort erkannt und korrigiert werden können. Dies erhöht die Prozesssicherheit und stellt sicher, dass die Qualitätsanforderungen stets erfüllt werden.
Vorteile einer automatischen Pulverbeschichtungsanlage
Die Einführung einer automatisierten Pulverbeschichtungsanlage bringt eine Reihe von Vorteilen für Unternehmen mit sich:
- Erhöhte Produktivität: Durch die Automatisierung des gesamten Prozesses werden die Arbeitszeiten verkürzt und die Produktivität gesteigert. Da die Pulverbeschichtung kontinuierlich und ohne Unterbrechungen abläuft, können Unternehmen höhere Stückzahlen in kürzerer Zeit bearbeiten. Die Integration von industriellen Robotern und Förderbändern ermöglicht es, größere Produktionsvolumen effizient und konsistent zu erreichen.
- Gleichmäßige und hochwertige Beschichtungen: Eine der größten Stärken automatischer Anlagen ist die Fähigkeit, gleichmäßige, hochwertige und fehlerfreie Beschichtungen zu erzielen. Durch die präzise Steuerung der Pulversprühtechnik und der Ofentemperaturen wird eine konstante Beschichtungsdicke und eine hervorragende Haftung auf der Oberfläche erreicht. Dies führt zu einer höheren Produktqualität und einer längeren Haltbarkeit der beschichteten Produkte.
- Reduzierte Materialverschwendung: Automatische Pulverbeschichtungsanlagen sind darauf ausgelegt, den Pulververbrauch zu optimieren. Dank der Rückgewinnungseinheit für überschüssiges Pulver wird das überschüssige Material wieder dem Beschichtungsprozess zugeführt, was den Materialverbrauch senkt und die Kosten reduziert. Dies trägt auch zu einer ökologischen Nachhaltigkeit bei, da weniger Abfall entsteht.
- Erhöhte Flexibilität: Eine moderne automatische Pulverbeschichtungsanlage bietet eine hohe Flexibilität hinsichtlich der zu beschichtenden Werkstücke. Die automatisierten Systeme können leicht auf verschiedene Werkstückgrößen, Formen und Beschichtungsanforderungen angepasst werden. Durch die programmierbare Steuerung der Applikationssysteme können unterschiedliche Pulverarten und Beschichtungsprozesse ohne großen Aufwand realisiert werden.
- Verbesserte Arbeitsbedingungen: Automatische Systeme übernehmen viele der arbeitsintensiven und potenziell gesundheitsschädlichen Aufgaben des Beschichtungsprozesses. Dies führt zu sichereren Arbeitsbedingungen und reduziert das Risiko von Berufskrankheiten durch Inhalation von Pulverstaub oder chemischen Dämpfen. Zudem wird der manuelle Arbeitsaufwand minimiert, was die Arbeitsbelastung für die Mitarbeiter verringert.
- Wirtschaftlichkeit und langfristige Rentabilität: Die Investitionskosten in eine automatische Pulverbeschichtungsanlage können hoch sein, jedoch amortisieren sie sich aufgrund der gesteigerten Produktivität, der gesenkten Materialkosten und der geringeren Personalkosten schnell. Langfristig profitieren Unternehmen von geringeren Produktionskosten und einer höheren Wettbewerbsfähigkeit.
Anwendungen automatisierter Pulverbeschichtungsanlagen
Automatische Pulverbeschichtungsanlagen finden Anwendung in einer Vielzahl von Branchen, in denen qualitativ hochwertige, gleichmäßige und widerstandsfähige Beschichtungen erforderlich sind. Einige typische Anwendungsbereiche sind:
- Automobilindustrie: Die Automobilindustrie nutzt automatische Pulverbeschichtungsanlagen zur Beschichtung von Fahrzeugteilen wie Felgen, Stoßstangen und Rahmenkomponenten. Durch die gleichmäßige Beschichtung wird eine kratzfeste und korrosionsbeständige Oberfläche erzielt, die den strengen Anforderungen an Optik und Langlebigkeit gerecht wird.
- Metallverarbeitung: In der Metallverarbeitung werden automatische Pulverbeschichtungsanlagen zur Beschichtung von Baugruppen und Maschinenteilen eingesetzt, um diese vor Korrosion zu schützen und ihnen ein ansprechendes Finish zu verleihen. Auch hier werden hohe Anforderungen an die Beschichtungsqualität gestellt, die durch automatisierte Prozesse zuverlässig erfüllt werden.
- Möbelindustrie: Für die Möbelindustrie werden automatische Pulverbeschichtungsanlagen verwendet, um Stahlmöbel oder Metallteile von Möbeln mit Pulverbeschichtungen zu versehen. Diese Beschichtungen bieten nicht nur eine ansprechende Optik, sondern auch eine robuste, kratzfeste Oberfläche, die eine lange Lebensdauer gewährleistet.
- Elektronikindustrie: In der Elektronikindustrie werden automatische Pulverbeschichtungsanlagen zur Beschichtung von Gehäusen, Komponenten und Baugruppen eingesetzt, um sowohl optische Anforderungen zu erfüllen als auch eine elektrische Isolierung oder Schutz vor äußeren Einflüssen zu gewährleisten.
Zukunftsperspektiven für automatische Pulverbeschichtungsanlagen
Die Zukunft der automatischen Pulverbeschichtungsanlagen wird von den fortschreitenden Entwicklungen in den Bereichen Automation, Intelligenz und Energieeffizienz geprägt sein. Zukünftige Anlagen werden noch stärker integrierte Systeme beinhalten, die eine vollständige Prozessoptimierung und Echtzeitüberwachung ermöglichen. Auch die Entwicklung von umweltfreundlicheren Pulvern, die weniger toxische Substanzen enthalten, sowie die Verbesserung der Energieeffizienz der Anlagen wird eine wichtige Rolle spielen, um den wachsenden Nachhaltigkeitsanforderungen gerecht zu werden.
Zusammenfassend lässt sich sagen, dass automatische Pulverbeschichtungsanlagen einen bedeutenden Fortschritt in der Pulverbeschichtungstechnologie darstellen und Unternehmen zahlreiche Vorteile in Bezug auf Produktivität, Qualität, Kosten und Nachhaltigkeit bieten.
Ein wesentlicher Vorteil automatischer Pulverbeschichtungsanlagen ist ihre Fähigkeit zur Prozessoptimierung. Die Integration von Smart-Technologien und Künstlicher Intelligenz (KI) erlaubt es, den gesamten Beschichtungsprozess kontinuierlich zu überwachen und in Echtzeit anzupassen. Dies führt nicht nur zu einer noch präziseren Pulverapplikation, sondern ermöglicht auch eine verbesserte Fehlererkennung und Fehlerbehebung. Der Einsatz von Sensoren, die Temperatur, Luftfeuchtigkeit und Pulvermengen messen, sorgt für eine konstante Produktqualität, die ohne menschliches Eingreifen aufrechterhalten wird.
Automatische Pulverbeschichtungsanlagen sind zudem in der Lage, mit einer Vielzahl von Pulversorten und Beschichtungsmethoden zu arbeiten. Dabei können verschiedene Farbtöne, Oberflächenstrukturen und Korrosionsschutzanforderungen schnell und effizient umgesetzt werden. Diese Flexibilität bietet den Unternehmen die Möglichkeit, ihre Produktion an unterschiedliche Marktbedürfnisse anzupassen, sei es für Massenproduktion oder kleine Chargen.
Neben der Effizienz und Flexibilität ist auch die Energieeffizienz ein entscheidender Vorteil. Moderne Anlagen sind zunehmend mit Wärmerückgewinnungssystemen ausgestattet, die den Energieverbrauch durch die Nutzung überschüssiger Wärme aus dem Ofenprozess reduzieren. Diese Technologie hilft dabei, den CO2-Ausstoß zu minimieren und die Betriebskosten zu senken. Viele Anlagen sind auch mit automatischen Systemen zur Pulverrückgewinnung ausgestattet, die überschüssiges Pulver aus der Luft absaugen und in den Produktionsprozess zurückführen, wodurch der Materialverlust erheblich verringert wird.
Ein weiterer Vorteil ist die Kostensenkung durch die Reduzierung von Fehlern und Ausschuss. Da der Beschichtungsprozess automatisiert und exakt kontrolliert wird, sind Fehler wie ungleichmäßige Beschichtungen oder Lufteinschlüsse deutlich seltener. Dies reduziert nicht nur den Materialbedarf, sondern senkt auch die Kosten für Nacharbeit und Reparaturen.
Automatisierte Systeme bieten auch höhere Sicherheit in der Produktion. Durch die Minimierung der direkten menschlichen Interaktion mit Pulverstaub und chemischen Substanzen wird das Risiko gesundheitlicher Beeinträchtigungen verringert. Gleichzeitig ermöglichen diese Anlagen eine 24/7-Produktion, da sie ohne Pausen arbeiten können, was die Effizienz und Rentabilität weiter steigert.
Der Übergang zu automatisierten Pulverbeschichtungsanlagen wird durch die zunehmende Digitalisierung und Industrie 4.0-Konzepte weiter vorangetrieben. Diese Entwicklungen ermöglichen eine noch präzisere und schnellere Produktion, bei der alle Parameter des Beschichtungsprozesses überwacht und optimiert werden können. In Zukunft könnten diese Systeme mit Cloud-Technologien verbunden werden, sodass Unternehmen weltweit Zugriff auf ihre Produktionsdaten haben und sofort auf Abweichungen reagieren können.
Abschließend lässt sich sagen, dass die automatische Pulverbeschichtungsanlage nicht nur eine Lösung für hohe Effizienz und Qualität bietet, sondern auch ein Schritt in Richtung nachhaltiger Produktion darstellt. Unternehmen, die auf diese Technologien setzen, profitieren von Kosteneinsparungen, einer verbesserten Produktqualität und einer stärkeren Marktpositionierung. Mit den kontinuierlichen Fortschritten in der Technologie wird sich die Automatisierung der Pulverbeschichtung weiterentwickeln und noch breitere Anwendungsmöglichkeiten finden, was die Industrien weltweit verändern wird.
Pulverbeschichtungsanlage

Die Pulverbeschichtungsanlage hat sich als eine äußerst effiziente und umweltfreundliche Methode zur Oberflächenbehandlung von Metallteilen etabliert. Sie ermöglicht es, Werkstücke mit einer widerstandsfähigen, korrosionsbeständigen und ästhetisch ansprechenden Schicht zu versehen, die nicht nur optische, sondern auch funktionelle Anforderungen erfüllt. Die Technologie bietet zahlreiche Vorteile, sowohl in der Produktion als auch im Hinblick auf die Nachhaltigkeit und Kostenoptimierung.
Prozessschritte in einer Pulverbeschichtungsanlage
- Vorbehandlung der Werkstücke: Vor der eigentlichen Pulverbeschichtung müssen die Werkstücke gründlich vorbereitet werden, um eine optimale Haftung der Pulverschicht zu gewährleisten. Die Vorbehandlung umfasst mehrere Schritte:
- Entfettung: Entfernen von Öl, Fett und anderen Verunreinigungen von der Oberfläche.
- Beizen: Chemische Reinigung, die Oxidschichten und Rost entfernt.
- Phosphatierung: Aufbringen einer schützenden Phosphatschicht zur Verbesserung der Haftung des Pulvers.
- Trocknung: Nach der Behandlung müssen die Werkstücke vollständig getrocknet werden, um eine perfekte Pulverbeschichtung zu ermöglichen.
- Pulverauftragung: In einer Pulverbeschichtungsanlage wird das Pulver mithilfe von Elektrostatik auf die Werkstücke aufgetragen. Die Pulverbeschichtung erfolgt in der Regel durch eine manuelle oder automatische Pistole, die das Pulver in Form eines feinen Nebels sprüht. Durch die elektrostatische Aufladung wird das Pulver von der Pistole angezogen und haftet an der Oberfläche des Werkstücks, ohne dass eine zusätzliche Haftvermittlerschicht erforderlich ist. Der Prozess ist sowohl präzise als auch materialeffizient, da überschüssiges Pulver zurückgewonnen und wiederverwendet werden kann.
- Einbrennvorgang: Nach dem Auftragen des Pulvers müssen die beschichteten Werkstücke in einen Einbrennofen geführt werden, in dem sie auf eine bestimmte Temperatur erhitzt werden. Durch die Hitze schmilzt das Pulver und bildet eine gleichmäßige, widerstandsfähige Schicht auf der Oberfläche. Der Einbrennprozess ist entscheidend für die Haftung und Langlebigkeit der Pulverbeschichtung. Die Temperatur und Zeitdauer des Einbrennens müssen genau kontrolliert werden, um eine gleichmäßige und qualitativ hochwertige Beschichtung zu erzielen.
- Abkühlung und Nachbehandlung: Nach dem Einbrennen müssen die Werkstücke in einer kontrollierten Abkühlzone abgekühlt werden. Dieser Schritt ist wichtig, um die Festigkeit und Härte der Pulverbeschichtung zu gewährleisten. Nach der Abkühlung können die Werkstücke weiterbehandelt werden, zum Beispiel durch das Anbringen von Markierungen, Beschriftungen oder versiegelten Kanten.
Typen von Pulverbeschichtungsanlagen
Pulverbeschichtungsanlagen gibt es in unterschiedlichen Ausführungen, die je nach Anwendung und Produktionsanforderungen variieren:
- Manuelle Pulverbeschichtungsanlagen: Bei dieser Art von Anlage wird die Pulverbeschichtung per Hand durchgeführt, häufig in kleineren Werkstätten oder bei Spezialanfertigungen. Der Vorteil liegt in der Flexibilität und dem geringeren Investitionsaufwand. Manuelle Anlagen sind jedoch zeitintensiver und weniger präzise als automatisierte Systeme. Sie eignen sich vor allem für kleinere Serien oder Einzelteile.
- Automatische Pulverbeschichtungsanlagen: Diese Anlagen sind auf den Massenbetrieb ausgelegt und ermöglichen eine hohe Produktionskapazität mit gleichbleibender Beschichtungsqualität. Sie bestehen aus mehreren integrierten Stationen, wie Förderbändern, Pulveraufbereitungsanlagen und automatisierten Applikationssystemen. In großen Produktionslinien werden Werkstücke automatisch durch die einzelnen Stationen geführt, was den Arbeitsaufwand erheblich reduziert. Automatische Anlagen bieten zudem Vorteile hinsichtlich der Wiederverwendbarkeit des Pulvers, Produktivität und Prozesssicherheit.
- Semi-automatische Pulverbeschichtungsanlagen: Diese Anlagen kombinieren manuelle und automatische Komponenten und sind für mittlere Produktionsmengen geeignet. Hier werden bestimmte Schritte wie das Auftragen des Pulvers automatisch durchgeführt, während andere, wie das Laden und Entladen der Werkstücke, manuell erfolgen. Semi-automatische Anlagen bieten eine gute Balance zwischen Flexibilität und Effizienz.
- Roboterunterstützte Pulverbeschichtungsanlagen: Roboterarme werden in modernen Pulverbeschichtungsanlagen verwendet, um Werkstücke präzise und in 3D-Bewegungen zu beschichten. Diese Systeme können komplexe Geometrien und unregelmäßige Formen mit hoher Wiederholgenauigkeit bearbeiten. Roboterunterstützte Anlagen bieten besonders bei der Beschichtung von komplexen Bauteilen oder in der Automobilindustrie erhebliche Vorteile.
Vorteile der Pulverbeschichtung
- Umweltfreundlichkeit: Im Vergleich zu traditionellen Lackierverfahren erzeugt die Pulverbeschichtung deutlich weniger Abfall und VOCs (flüchtige organische Verbindungen), da keine Lösungsmittel erforderlich sind. Das überschüssige Pulver kann oft zurückgewonnen und wiederverwendet werden, wodurch Materialkosten gesenkt und der Ressourcenverbrauch optimiert wird.
- Langlebigkeit und Widerstandsfähigkeit: Pulverbeschichtungen sind sehr widerstandsfähig gegen Korrosion, Kratzer und UV-Strahlung. Sie bieten eine ausgezeichnete Oberflächenhärte und sind daher besonders geeignet für Anwendungen in korrosiven Umgebungen, wie z. B. in der Bauindustrie oder für Fahrzeugteile.
- Kostenoptimierung: Pulverbeschichtungen sind im Allgemeinen kostengünstiger als traditionelle flüssige Lackierungen, da sie weniger Lösungsmittel benötigen und die Rückgewinnung von überschüssigem Pulver den Materialverbrauch reduziert. Durch die Automatisierung des Prozesses können Unternehmen zudem Arbeitskosten sparen und den Produktionsdurchsatz erhöhen.
- Vielseitigkeit: Die Pulverbeschichtung eignet sich für eine Vielzahl von Metallen, darunter Stahl, Aluminium und Eisen. Zudem kann sie in nahezu jedem Farbton und Glanzgrad ausgeführt werden. Die Möglichkeit, unterschiedliche Oberflächenstrukturen zu erzeugen, erweitert die Anwendungsgebiete erheblich.
- Verbesserte Optik: Pulverbeschichtungen können nicht nur funktionelle, sondern auch ästhetische Anforderungen erfüllen. Die glänzenden, matten oder texturierten Oberflächen bieten eine ansprechende Optik und eine gleichmäßige Farbabdeckung, die den optischen Wert von Produkten erheblich steigern.
- Gleichmäßige Beschichtung: Durch den Einsatz von elektrostatischer Aufladung wird das Pulver gleichmäßig auf die Oberfläche aufgebracht, was eine konsistente Beschichtungsdicke über das gesamte Werkstück gewährleistet. Dies führt zu einer hohen Oberflächenqualität und einer perfekten Haftung der Pulverschicht.
Zukunft der Pulverbeschichtungsanlagen
Die Weiterentwicklung der Pulverbeschichtungstechnologie wird durch verschiedene Innovationen vorangetrieben. Besonders die Integration von Digitalisierung und Automatisierung eröffnet neue Perspektiven für die Industrie 4.0. In Zukunft können Pulverbeschichtungsanlagen noch stärker intelligent werden, indem sie mit IoT-Technologien (Internet of Things) und Cloud-basierten Systemen verbunden werden. Diese Systeme ermöglichen eine Echtzeitüberwachung, die eine präzise Prozesskontrolle und Fehlerdiagnose ermöglicht, was zu einer noch besseren Prozessoptimierung und Kostenreduktion führt.
Zusätzlich wird die Forschung und Entwicklung im Bereich der umweltfreundlichen Pulverbeschichtungen weiter zunehmen, um die CO2-Emissionen zu senken und den Einsatz von toxischen Substanzen zu minimieren. Neue Pulverformulierungen, die beispielsweise mit weniger Lösungsmitteln auskommen oder auf nachwachsenden Rohstoffen basieren, könnten die Technologie noch nachhaltiger machen.
Insgesamt stellt die Pulverbeschichtungsanlage eine Schlüsseltechnologie für moderne Fertigungsprozesse dar, die Unternehmen zahlreiche Vorteile in Bezug auf Qualität, Kosten und Nachhaltigkeit bietet.
EMS Pulverbeschichtungsanlagen

Unsere Pulverbeschichtungsanlage wird in Übereinstimmung mit den globalen fortschrittlichen Standards hergestellt und wurden mit vollem Vertrauen sowohl auf dem heimischen als auch auf dem weltweiten Markt bevorzugt.
Unsere Kapazität ist täglich gewachsen, wobei die Kundenzufriedenheit zusammen mit unserem gemeinsamen Vertriebs- und Servicenetz an erster Stelle steht.
Unser Unternehmen ist ein führendes türkisches Unternehmen, das sich auf die Herstellung von „Elektrostatischen Pulverbeschichtungsanlagen und kompletten Lackiersystemen“ mit 20 Jahren Wissen und praktischer Erfahrung spezialisiert hat.
Alle unsere Maschinen sind CE-gekennzeichnet, garantiert und können von potenziellen Kunden persönlich besichtigt werden. Es gibt auch Bilder und Videos auf dieser Seite, die die verwendeten Maschinen zeigen.
Wir entwerfen, fertigen und montieren Pulverbeschichtungsöfen, automatische und manuelle Kabinen, automatische und manuelle Pulverbeschichtungsanlagen, Pistolen, automatische und Stangentransfer-Pulverbeschichtungslinien, Pulverbeschichtungsfilter und Ersatzteile für Pulverbeschichtungspistolen