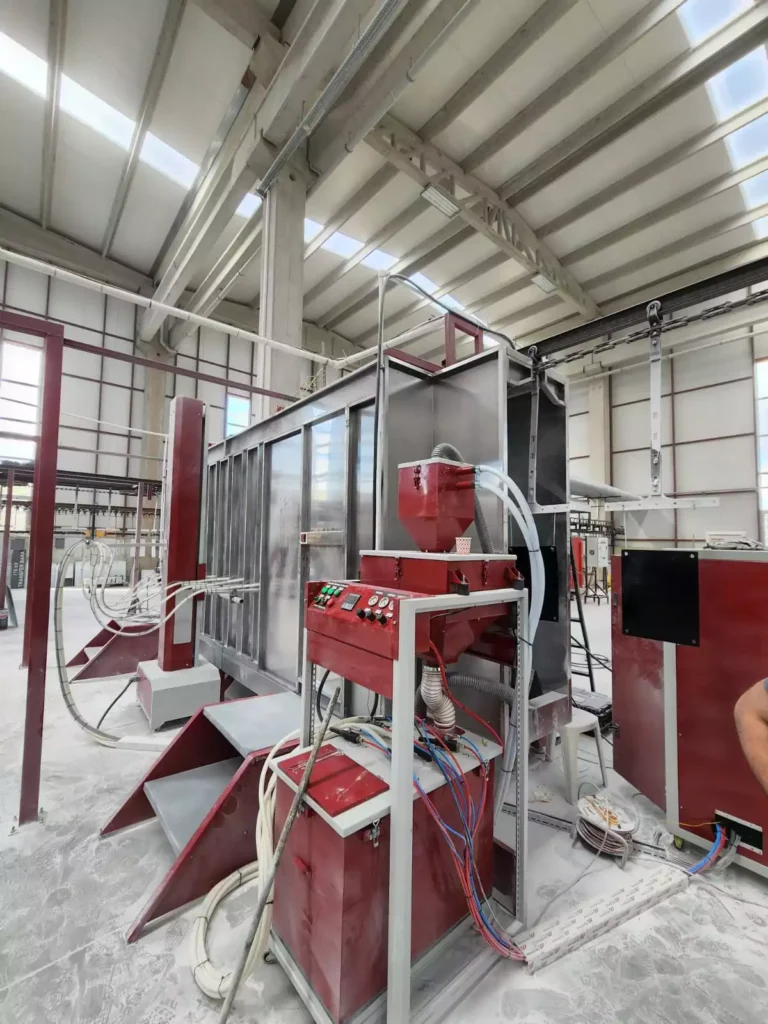
Pulverbeschichtung Komplettanlage vom Hersteller. Pulverbeschichtungsanlage & Pulverbeschichtungsofen und Pulverkabine mit Garantie
Eine Pulverbeschichtungs-Komplettanlage besteht aus mehreren Komponenten, die gemeinsam eine vollständige Pulverbeschichtungsprozesslinie bilden. Die genaue Zusammensetzung der Anlage hängt von den Anforderungen des Kunden und der Art der zu beschichtenden Produkte ab. Im Allgemeinen besteht eine Pulverbeschichtungs-Komplettanlage aus folgenden Hauptkomponenten:
- Vorbehandlungssystem: Dieses System dient zur Vorbereitung der zu beschichtenden Oberflächen. Es umfasst oft mehrere Schritte wie Entfetten, Beizen, Spülen, Aktivieren und Phosphatieren.
- Trocknungsofen: Der Trocknungsofen wird nach der Vorbehandlung eingesetzt, um Feuchtigkeit von der Oberfläche zu entfernen und eine saubere, trockene Oberfläche für die Beschichtung bereitzustellen.
- Pulverbeschichtungskabine: Die Pulverbeschichtungskabine ist der Ort, an dem das Pulver auf die zu beschichtende Oberfläche aufgetragen wird. Eine geeignete Luftversorgung und -filtration ist erforderlich, um sicherzustellen, dass die Umgebungsluft sauber bleibt.
- Pulversammler: Der Pulversammler sammelt überschüssiges Pulver aus der Kabine und recycelt es für die spätere Verwendung.
- Einbrennofen: Der Einbrennofen härtet das Pulver aus und schafft so eine haltbare Beschichtung. Er kann je nach Größe und Anforderungen des Produkts als Elektro- oder Gasofen ausgelegt sein.
- Fördersystem: Das Fördersystem transportiert die zu beschichtenden Produkte von der Vorbehandlung bis zum Einbrennofen.
- Steuerungssystem: Das Steuerungssystem überwacht und kontrolliert den gesamten Prozess und sorgt für eine optimale Leistung und Qualität.
Zusätzlich können optional weitere Komponenten wie eine Wasseraufbereitungsanlage, eine Entstaubungsanlage und eine Klimaanlage hinzugefügt werden, um eine vollständige und effiziente Pulverbeschichtungs-Komplettanlage zu schaffen.
Pulverbeschichtung Komplettanlage
Strahlkabine
Die Strahlkabine ist der erste Schritt in der Pulverbeschichtung. In der Strahlkabine werden die Teile von Schmutz, Rost und Fett befreit. Dies geschieht mithilfe eines Strahlmittels, das mit hoher Geschwindigkeit auf die Oberfläche der Teile geschleudert wird.
Die Strahlkabine besteht aus folgenden Komponenten:
- Strahlraum: In diesem Raum werden die Teile mit dem Strahlmittel beschossen.
- Abluftanlage: Die Abluftanlage saugt den Staub und die Partikel aus dem Strahlraum ab.
- Filteranlage: Die Filteranlage reinigt die Abluft, bevor sie in die Umwelt abgegeben wird.
- Lichtanlage: Die Lichtanlage sorgt für gute Sichtverhältnisse im Strahlraum.
Pulverbeschichtungskabine
In der Pulverbeschichtungskabine wird das Pulver auf die Teile aufgetragen. Dies geschieht mithilfe einer elektrostatischen Aufladung, die das Pulver an die Oberfläche der Teile bindet.
Die Pulverbeschichtungskabine besteht aus folgenden Komponenten:
- Pulverbehälter: Der Pulverbehälter enthält das Pulver, das auf die Teile aufgetragen wird.
- Pulverpistole: Die Pulverpistole zerstäubt das Pulver und lädt es elektrostatisch auf.
- Abluftanlage: Die Abluftanlage saugt das überschüssige Pulver aus der Kabine ab.
- Filteranlage: Die Filteranlage reinigt die Abluft, bevor sie in die Umwelt abgegeben wird.
Einbrennofen
Im Einbrennofen wird das Pulver eingebrannt und härtet aus. Dies geschieht bei einer Temperatur von 140 bis 200 Grad Celsius.
Der Einbrennofen besteht aus folgenden Komponenten:
- Ofenraum: In diesem Raum wird das Pulver eingebrannt.
- Heizelemente: Die Heizelemente erhitzen den Ofenraum.
- Temperaturregelung: Die Temperaturregelung sorgt dafür, dass die gewünschte Temperatur im Ofenraum erreicht wird.
- Belüftung: Die Belüftung sorgt dafür, dass die Abluft aus dem Ofenraum abgeführt wird.
Fördertechnik
Die Fördertechnik transportiert die Teile durch die Anlage. Dies kann manuell oder automatisch erfolgen.
Die Fördertechnik besteht aus folgenden Komponenten:
- Transportbänder: Transportbänder transportieren die Teile durch die Anlage.
- Lifte: Lifte transportieren die Teile über größere Höhenunterschiede.
- Roboter: Roboter transportieren die Teile durch die Anlage.
Weitere Details
Zusätzlich zu den oben genannten Komponenten können Pulverbeschichtungsanlagen auch mit weiteren Komponenten ausgestattet sein, darunter:
- Vorbehandlungskabine: In der Vorbehandlungskabine werden die Teile vor der Pulverbeschichtung vorbereitet. Dies kann zum Beispiel das Entfetten, Entlacken oder Entrosten der Teile umfassen.
- Rückgewinnungsanlage: Die Rückgewinnungsanlage sammelt das überschüssige Pulver, das beim Pulverbeschichten anfällt. Das Pulver kann dann wiederverwendet werden.
- Automatisierungssysteme: Automatisierungssysteme steuern und überwachen die Pulverbeschichtungsanlage.
Die Auswahl der Komponenten für eine Pulverbeschichtungsanlage hängt von den Anforderungen des jeweiligen Anwendungsfalls ab.
Fachbereiche wo man Pulverbeschichtung Komplettanlage benutzt
Pulverbeschichtungsanlagen werden in einer Vielzahl von Fachbereichen eingesetzt, darunter:
- Automobilindustrie: Pulverbeschichtungen werden für Fahrzeugteile wie Felgen, Stoßstangen und Karosserien verwendet.
- Industrie: Pulverbeschichtungen werden für Maschinen, Werkzeuge und andere industrielle Anwendungen verwendet.
- Architektur: Pulverbeschichtungen werden für Fassaden, Fenster und andere Bauelemente verwendet.
- Wohnen: Pulverbeschichtungen werden für Möbel, Türen und andere Haushaltsgegenstände verwendet.
In der Automobilindustrie werden Pulverbeschichtungen für eine Vielzahl von Fahrzeugteilen verwendet, darunter:
- Felgen: Pulverbeschichtete Felgen sind widerstandsfähig gegen Korrosion und Kratzer.
- Stoßstangen: Pulverbeschichtete Stoßstangen sind robust und langlebig.
- Karosserien: Pulverbeschichtete Karosserien sind wetterfest und UV-beständig.
In der Industrie werden Pulverbeschichtungen für eine Vielzahl von Anwendungen verwendet, darunter:
- Maschinen: Pulverbeschichtete Maschinen sind pflegeleicht und widerstandsfähig gegen Verschleiß.
- Werkzeuge: Pulverbeschichtete Werkzeuge sind langlebig und rutschfest.
- Andere industrielle Anwendungen: Pulverbeschichtungen werden auch für andere industrielle Anwendungen verwendet, wie z. B. die Beschichtung von Rohren, Tanks und Behältern.
In der Architektur werden Pulverbeschichtungen für eine Vielzahl von Bauelementen verwendet, darunter:
- Fassaden: Pulverbeschichtete Fassaden sind wetterfest und langlebig.
- Fenster: Pulverbeschichtete Fenster sind pflegeleicht und widerstandsfähig gegen Kratzer.
- Andere Bauelemente: Pulverbeschichtungen werden auch für andere Bauelemente verwendet, wie z. B. Türen, Tore und Geländer.
Im Wohnen werden Pulverbeschichtungen für eine Vielzahl von Haushaltsgegenständen verwendet, darunter:
- Möbel: Pulverbeschichtete Möbel sind pflegeleicht und langlebig.
- Türen: Pulverbeschichtete Türen sind wetterfest und robust.
- Andere Haushaltsgegenstände: Pulverbeschichtungen werden auch für andere Haushaltsgegenstände verwendet, wie z. B. Fensterrahmen, Geländer und Markisen.
Pulverbeschichtungsanlagen bieten eine Reihe von Vorteilen gegenüber anderen Beschichtungsverfahren, darunter:
- Hohe Farb- und Glanzvielfalt: Pulverbeschichtungen sind in einer Vielzahl von Farben und Glanzstufen erhältlich.
- Lange Lebensdauer: Pulverbeschichtungen sind sehr widerstandsfähig gegen Korrosion, Kratzer und UV-Strahlung.
- Gute Umweltverträglichkeit: Pulverbeschichtungen sind umweltfreundlicher als andere Beschichtungsverfahren, da sie keine Lösungsmittel verwenden.
Einbrennofen Einzelheiten
Ein Einbrennofen ist ein spezieller Ofen, der für den Aushärteprozess von Pulverbeschichtungen verwendet wird. Dieser Prozess wird auch als Einbrennen oder Aushärten bezeichnet und ist entscheidend, um eine dauerhafte und qualitativ hochwertige Beschichtung auf Werkstücken zu gewährleisten. Hier sind einige Einzelheiten und Merkmale eines typischen Einbrennofens:
- Erhitzungssystem:
- Einbrennöfen verwenden leistungsstarke Heizsysteme, die oft auf elektrischer oder gasbetriebener Basis arbeiten.
- Elektrische Heizelemente oder Gasbrenner erzeugen die erforderliche Wärme für das Schmelzen und Aushärten des Pulvers.
- Isolierung:
- Die Isolierung des Ofens ist entscheidend, um Wärmeverluste zu minimieren und eine gleichmäßige Temperaturverteilung zu gewährleisten.
- Gut isolierte Öfen verbessern die Energieeffizienz und fördern eine gleichmäßige Aushärtung.
- Temperatursteuerung:
- Ein präzises Temperatursteuersystem regelt die Ofentemperatur während des Aushärteprozesses.
- Moderne Einbrennöfen können digitale Steuerungen und Sensoren verwenden, um genaue Temperaturprofile zu gewährleisten.
- Förderanlagen:
- Einbrennöfen verfügen über Förderbänder oder Hängesysteme, um die beschichteten Werkstücke durch den Ofen zu befördern.
- Die Geschwindigkeit der Förderanlage beeinflusst die Verweilzeit der Werkstücke im Ofen und somit den Aushärteprozess.
- Kühlbereich:
- Nach dem Aushärten können die Werkstücke durch einen Kühlbereich geführt werden, um auf sichere Temperaturen abzukühlen.
- Dieser Bereich verbessert die Qualität der Beschichtung und stellt sicher, dass die Werkstücke sicher behandelt werden können.
- Luftzirkulationssystem:
- Ein effizientes Luftzirkulationssystem sorgt für eine gleichmäßige Verteilung der erwärmten Luft im Ofen.
- Eine gute Luftzirkulation minimiert Hotspots und gewährleistet eine konsistente Aushärtung.
- Sicherheitsvorkehrungen:
- Einbrennöfen sollten mit Not-Aus-Schaltern und anderen Sicherheitsvorkehrungen ausgestattet sein, um einen sicheren Betrieb zu gewährleisten.
- Die Ofenkonstruktion sollte den geltenden Sicherheitsstandards entsprechen.
- Abgas- und Filteranlagen:
- Einbrennöfen sollten Abgasanlagen haben, um Verbrennungsgase sicher abzuführen.
- Filteranlagen können dazu beitragen, Pulverreste zu erfassen und für die Wiederverwendung zu recyceln.
- Automatisierungsoptionen:
- Moderne Einbrennöfen können mit automatisierten Steuerungssystemen integriert sein, die den gesamten Aushärteprozess überwachen und steuern.
- Automatisierungsoptionen können auch eine Datenverarbeitung und -überwachung für Effizienz und Qualität umfassen.
Ein Einbrennofen ist ein entscheidender Bestandteil des Pulverbeschichtungsprozesses und trägt dazu bei, eine haltbare und qualitativ hochwertige Oberflächenbeschichtung auf Werkstücken zu erzielen.
Ofengröße
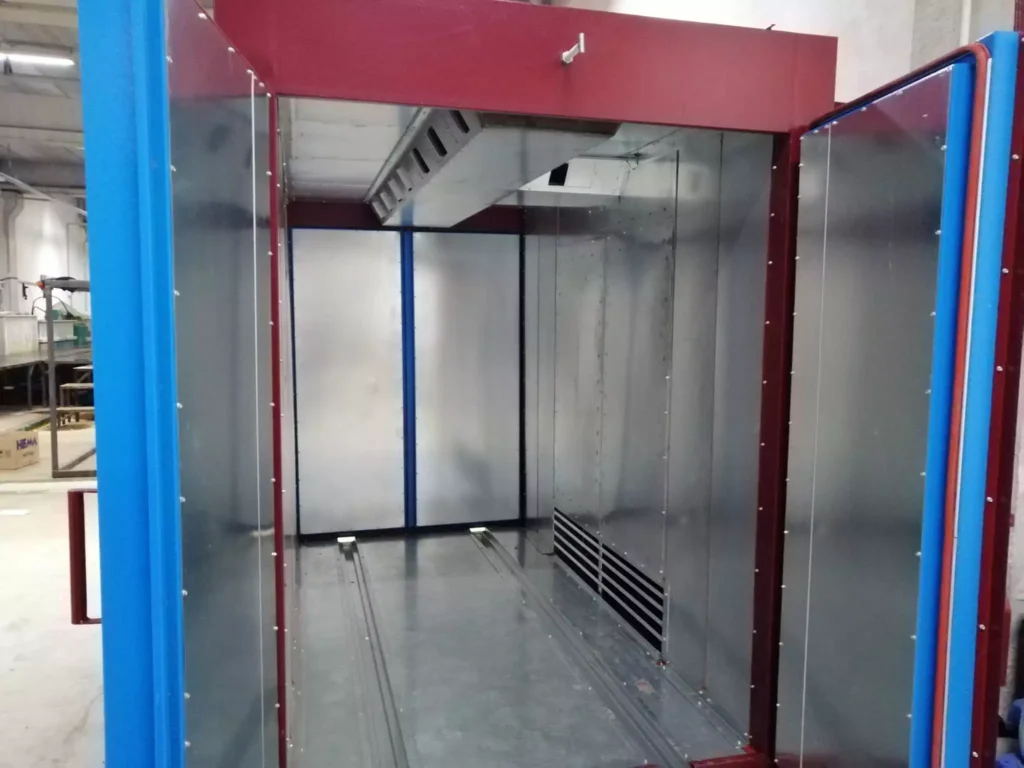
Die Größe eines Ofens wird in der Regel durch das Volumen des Ofenraums angegeben. Das Volumen wird berechnet, indem die Länge, Breite und Höhe des Ofenraums multipliziert werden.
Die richtige Ofengröße hängt von den zu backenden Produkten ab. Kleinere Öfen sind in der Regel für kleinere Produkte geeignet, während größere Öfen für größere Produkte geeignet sind.
Faustregel für die Ofengröße
Eine Faustregel für die Ofengröße besagt, dass die Innenfläche des Ofenraums mindestens doppelt so groß sein sollte wie die Oberfläche des größten zu backenden Produkts.
Beispiel
Wenn Sie einen Kuchen mit einem Durchmesser von 20 cm backen möchten, benötigen Sie einen Ofen mit einem Innenraum von mindestens 400 cm².
Andere Faktoren, die die Ofengröße beeinflussen
Neben der Größe der zu backenden Produkte können auch andere Faktoren die Ofengröße beeinflussen, darunter:
- Die Anzahl der gleichzeitig zu backenden Produkte: Wenn Sie mehrere Produkte gleichzeitig backen möchten, benötigen Sie einen größeren Ofen.
- Die Art des Backens: Einige Backvorgänge erfordern einen größeren Ofen als andere.
- Der Platzbedarf: Sie müssen sicherstellen, dass der Ofen in den vorgesehenen Bereich passt.
Wie man den richtigen Ofen für Ihre Bedürfnisse findet
Wenn Sie einen neuen Ofen kaufen, sollten Sie die Größe des Ofens sorgfältig berücksichtigen. Messen Sie den verfügbaren Platz und überlegen Sie, welche Produkte Sie backen möchten.
Ratschläge für die Auswahl der richtigen Ofengröße
- Wenn Sie nur kleine Produkte backen möchten, benötigen Sie einen kleinen Ofen.
- Wenn Sie große Produkte backen möchten, benötigen Sie einen großen Ofen.
- Wenn Sie mehrere Produkte gleichzeitig backen möchten, benötigen Sie einen größeren Ofen.
- Wenn Sie bestimmte Backvorgänge durchführen möchten, benötigen Sie möglicherweise einen Ofen mit einer bestimmten Größe.
- Überlegen Sie, wie viel Platz Sie für den Ofen haben.
Weitere Informationen zur Ofengröße
Weitere Informationen zur Ofengröße finden Sie in den Produktbeschreibungen von Ofenherstellern. Sie können sich auch von einem Küchenplaner beraten lassen.
Temperaturbereich
Der Temperaturbereich ist der Bereich von Temperaturen, in dem ein Gerät arbeiten kann. Er wird in der Regel in Grad Celsius (°C) oder Grad Fahrenheit (°F) angegeben.
Der Temperaturbereich eines Ofens ist wichtig, da er bestimmt, welche Lebensmittel darin gebacken werden können. Ofen haben in der Regel einen Temperaturbereich von 50 °C bis 250 °C oder 122 °F bis 482 °F.
Arten von Temperaturbereichen
Es gibt zwei Hauptarten von Temperaturbereichen:
- Kontinuierlicher Temperaturbereich: Ein kontinuierlicher Temperaturbereich bedeutet, dass der Ofen jede beliebige Temperatur innerhalb des Bereichs einstellen kann.
- Diskreter Temperaturbereich: Ein diskreter Temperaturbereich bedeutet, dass der Ofen nur bestimmte Temperaturen innerhalb des Bereichs einstellen kann.
Temperaturbereich von Öfen
Die meisten Öfen haben einen kontinuierlichen Temperaturbereich von 50 °C bis 250 °C oder 122 °F bis 482 °F. Einige Öfen haben einen diskreten Temperaturbereich, der nur bestimmte Temperaturen innerhalb dieses Bereichs umfasst.
Temperaturbereich von anderen Geräten
Der Temperaturbereich anderer Geräte kann je nach Art des Geräts variieren. Zum Beispiel haben Kühlschränke einen Temperaturbereich von 0 °C bis 10 °C oder 32 °F bis 50 °F, während Klimaanlagen einen Temperaturbereich von 16 °C bis 32 °C oder 61 °F bis 90 °F haben.
Wie man den richtigen Temperaturbereich für ein Gerät auswählt
Wenn Sie ein neues Gerät kaufen, sollten Sie den Temperaturbereich sorgfältig berücksichtigen. Stellen Sie sicher, dass der Temperaturbereich für die Verwendung des Geräts geeignet ist.
Ratschläge für die Auswahl des richtigen Temperaturbereichs
- Überlegen Sie, welche Produkte Sie mit dem Gerät verarbeiten möchten.
- Lesen Sie die Produktbeschreibung des Geräts, um den Temperaturbereich zu ermitteln.
- Fragen Sie einen Verkäufer oder einen Techniker nach Rat, wenn Sie sich nicht sicher sind, welcher Temperaturbereich für Sie geeignet ist.
Steuerung
Steuerung ist ein Prozess, bei dem eine Eingabe in eine gewünschte Ausgabe umgewandelt wird. In der Technik wird Steuerung häufig verwendet, um Maschinen oder Geräte zu steuern.
Arten von Steuerungen
Es gibt viele verschiedene Arten von Steuerungen, die für verschiedene Zwecke verwendet werden können. Einige der gebräuchlichsten Arten von Steuerungen sind:
- Analoge Steuerungen: Analoge Steuerungen arbeiten mit kontinuierlichen Signalen, die eine Vielzahl von Werten annehmen können.
- Digitale Steuerungen: Digitale Steuerungen arbeiten mit diskreten Signalen, die nur bestimmte Werte annehmen können.
- Automatische Steuerungen: Automatische Steuerungen arbeiten ohne menschliches Eingreifen.
- Manuelle Steuerungen: Manuelle Steuerungen erfordern menschliches Eingreifen.
Bestandteile einer Steuerung
Eine Steuerung besteht in der Regel aus den folgenden Komponenten:
- Eingabe: Die Eingabe ist die Information, die die Steuerung verarbeitet.
- Verarbeitung: Die Verarbeitung ist der Prozess, bei dem die Eingabe in eine Ausgabe umgewandelt wird.
- Ausgabe: Die Ausgabe ist die Information, die die Steuerung erzeugt.
Beispiele für Steuerungen
Beispiele für Steuerungen sind:
- Die Steuerung eines Autos: Die Steuerung eines Autos verwendet Sensoren, um die Umgebung des Autos zu erfassen. Diese Informationen werden dann von einem Computer verarbeitet, der das Gaspedal, die Bremse und das Lenkrad steuert.
- Die Steuerung eines Ofens: Die Steuerung eines Ofens verwendet einen Temperatursensor, um die Temperatur im Inneren des Ofens zu erfassen. Diese Informationen werden dann von einem Computer verarbeitet, der die Heizelemente des Ofens steuert, um die gewünschte Temperatur zu erreichen.
- Die Steuerung eines Roboters: Die Steuerung eines Roboters verwendet Sensoren, um die Umgebung des Roboters zu erfassen. Diese Informationen werden dann von einem Computer verarbeitet, der die Bewegungen des Roboters steuert.
Vorteile von Steuerungen
Steuerungen bieten eine Reihe von Vorteilen, darunter:
- Effizienz: Steuerungen können dazu beitragen, die Effizienz von Maschinen oder Geräten zu verbessern.
- Sicherheit: Steuerungen können dazu beitragen, die Sicherheit von Maschinen oder Geräten zu verbessern.
- Komfort: Steuerungen können den Komfort der Bedienung von Maschinen oder Geräten verbessern.
Nachteile von Steuerungen
Steuerungen haben auch einige Nachteile, darunter:
- Kosten: Steuerungen können teuer sein.
- Komplexität: Steuerungen können komplex sein.
- Fehleranfälligkeit: Steuerungen können fehleranfällig sein.
Sicherheit von Steuerungen
Steuerungen müssen so sicher sein, dass sie das Risiko von Verletzungen oder Schäden minimieren. Zu den Sicherheitsmaßnahmen, die bei der Steuerung von Maschinen oder Geräten getroffen werden können, gehören:
- Fehlererkennung und -korrektur: Steuerungen sollten in der Lage sein, Fehler zu erkennen und zu korrigieren, um Verletzungen oder Schäden zu verhindern.
- Not-Aus-Systeme: Steuerungen sollten Not-Aus-Systeme haben, die die Maschine oder das Gerät im Notfall sofort stoppen können.
- Sicherheitsvorkehrungen: Steuerungen sollten Sicherheitsvorkehrungen haben, um den Zugang zu gefährlichen Bereichen zu verhindern.
Fazit
Steuerung ist ein wichtiger Prozess, der in vielen Bereichen der Technik verwendet wird. Steuerungen können dazu beitragen, Maschinen oder Geräte effizienter, sicherer und komfortabler zu machen.
Heizelemente

Elektrische Heizelemente sind ein wichtiger Bestandteil von Pulverbeschichtungsanlagen. Sie werden verwendet, um die Pulverbeschichtung bei einer hohen Temperatur auszuhärten.
Arten von elektrischen Heizelementen in Pulveröfen:
In Pulveröfen werden in der Regel folgende Arten von elektrischen Heizelementen verwendet:
- Heizpatronen: Heizpatronen sind die gebräuchlichste Art von elektrischem Heizelement in Pulveröfen. Sie bestehen aus einem spiralförmigen Draht, der in einem keramischen Rohr eingebettet ist. Heizpatronen sind in der Regel sehr effizient und können eine hohe Temperatur erzeugen.
- Heizkabel: Heizkabel sind eine flexible Art von elektrischem Heizelement. Sie bestehen aus einem Draht, der mit einem Isoliermaterial umgeben ist. Heizkabel sind in der Regel kostengünstiger als Heizpatronen, aber auch weniger effizient.
Funktionsweise von elektrischen Heizelementen in Pulveröfen:
Elektrische Heizelemente in Pulveröfen werden mit Strom versorgt, wodurch sie sich erwärmen. Die Wärme wird dann an das Pulver übertragen, das dadurch aushärtet.
Sicherheit von elektrischen Heizelementen in Pulveröfen:
Elektrische Heizelemente in Pulveröfen können ein Brandrisiko darstellen, wenn sie nicht ordnungsgemäß installiert und verwendet werden. Daher ist es wichtig, die Sicherheitsvorkehrungen zu beachten, die vom Hersteller des Pulverofens angegeben werden.
Wartung von elektrischen Heizelementen in Pulveröfen:
Elektrische Heizelemente in Pulveröfen sollten regelmäßig auf Beschädigungen und Verschleiß überprüft werden. Beschädigte oder verschlissene Heizelemente sollten ersetzt werden, um die Sicherheit zu gewährleisten.
Fazit:
Elektrische Heizelemente sind ein wichtiger Bestandteil von Pulverbeschichtungsanlagen. Sie werden verwendet, um die Pulverbeschichtung bei einer hohen Temperatur auszuhärten.
Lüftungssystem
Ein Lüftungssystem ist ein System, das Luft aus einem Raum abführt und durch frische Luft ersetzt. Lüftungssysteme werden verwendet, um die Luftqualität in Innenräumen zu verbessern und die Gesundheit und das Wohlbefinden der Menschen zu schützen.
Arten von Lüftungssystemen
Es gibt viele verschiedene Arten von Lüftungssystemen, die für verschiedene Zwecke verwendet werden können. Einige der gebräuchlichsten Arten von Lüftungssystemen sind:
- Natürliche Lüftung: Natürliche Lüftung erfolgt durch die Bewegung von Luft durch natürliche Kräfte wie Wind und Temperaturunterschiede.
- Mechanische Lüftung: Mechanische Lüftung erfolgt durch die Verwendung von Ventilatoren oder Pumpen, um Luft zu bewegen.
- Umluftbelüftung: Umluftbelüftung ist ein System, bei dem die Luft in einen Raum eingeführt und dann wieder abgesaugt wird, nachdem sie durch einen Wärmetauscher geleitet wurde, um die Wärme zurückzugewinnen.
Funktionsweise eines Lüftungssystems
Die Funktionsweise eines Lüftungssystems hängt von der Art des Systems ab. Bei natürlichen Lüftungssystemen wird die Luft durch natürliche Kräfte wie Wind und Temperaturunterschiede bewegt. Bei mechanischen Lüftungssystemen wird Luft durch Ventilatoren oder Pumpen bewegt.
Vorteile von Lüftungssystemen
Lüftungssysteme bieten eine Reihe von Vorteilen, darunter:
- Verbesserung der Luftqualität: Lüftungssysteme können dazu beitragen, die Luftqualität in Innenräumen zu verbessern, indem sie verbrauchte Luft abführen und frische Luft einbringen.
- Schutz der Gesundheit: Lüftungssysteme können dazu beitragen, die Gesundheit und das Wohlbefinden der Menschen zu schützen, indem sie Schadstoffe und Allergene aus der Luft entfernen.
- Verbesserung des Komforts: Lüftungssysteme können dazu beitragen, den Komfort in Innenräumen zu verbessern, indem sie die Temperatur und die Luftfeuchtigkeit regulieren.
Nachteile von Lüftungssystemen
Lüftungssysteme haben auch einige Nachteile, darunter:
- Kosten: Lüftungssysteme können teuer sein, sowohl in der Anschaffung als auch im Betrieb.
- Energiebedarf: Lüftungssysteme können einen erheblichen Energiebedarf haben.
- Wartung: Lüftungssysteme müssen regelmäßig gewartet werden, um eine ordnungsgemäße Funktion zu gewährleisten.
Sicherheit von Lüftungssystemen
Lüftungssysteme müssen so sicher sein, dass sie das Risiko von Verletzungen oder Schäden minimieren. Zu den Sicherheitsmaßnahmen, die bei der Installation und Wartung von Lüftungssystemen getroffen werden können, gehören:
- Fehlererkennung und -korrektur: Lüftungssysteme sollten in der Lage sein, Fehler zu erkennen und zu korrigieren, um Verletzungen oder Schäden zu verhindern.
- Not-Aus-Systeme: Lüftungssysteme sollten Not-Aus-Systeme haben, die das System im Notfall sofort stoppen können.
- Sicherheitsvorkehrungen: Lüftungssysteme sollten Sicherheitsvorkehrungen haben, um den Zugang zu gefährlichen Bereichen zu verhindern.
Fazit
Lüftungssysteme sind ein wichtiger Bestandteil einer gesunden und komfortablen Innenraumluftqualität. Durch die Auswahl des richtigen Lüftungssystems für Ihre Bedürfnisse können Sie die Luftqualität in Ihrem Zuhause oder Büro verbessern und Ihre Gesundheit und Ihr Wohlbefinden schützen.
Isolierung
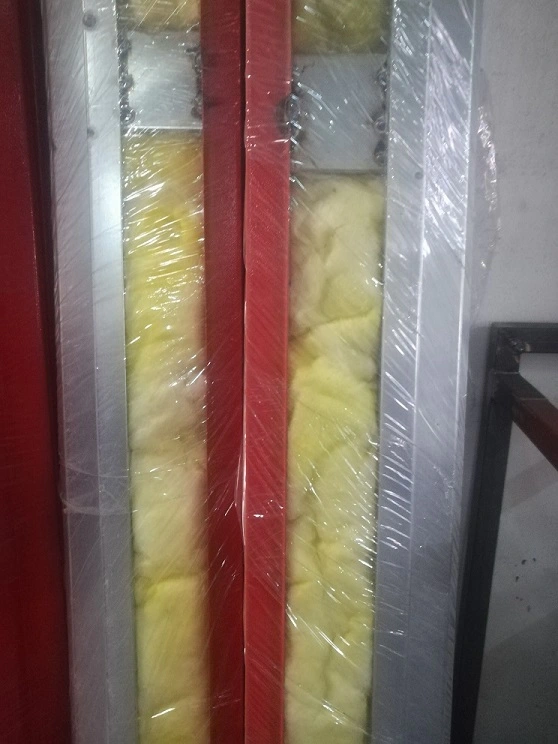
Die Isolierung eines Einbrennofens ist wichtig, um die Energiekosten zu senken und die Sicherheit zu gewährleisten. Die Isolierung verhindert, dass Wärme aus dem Ofen entweicht, wodurch der Ofen weniger Energie benötigt, um die gewünschte Temperatur zu erreichen. Außerdem kann die Isolierung dazu beitragen, dass der Ofen nicht zu heiß wird und sich dadurch keine Brandgefahr ergibt.
Arten von Isolation für Einbrennöfen
Es gibt verschiedene Arten von Isolation, die für Einbrennöfen verwendet werden können. Die gebräuchlichsten Arten sind:
- Mineralwolle: Mineralwolle ist ein faseriges Material, das aus Stein, Glas oder Basalt hergestellt wird. Mineralwolle ist ein guter Wärme- und Schallisolator.
- Polystyrol: Polystyrol ist ein Kunststoff, der aus kleinen, geschlossenen Zellen besteht. Polystyrol ist ein guter Wärmeisolator.
- Dämmwolle: Dämmwolle ist ein faseriges Material, das aus natürlichen oder synthetischen Materialien hergestellt wird. Dämmwolle ist ein guter Wärme- und Schallisolator.
Isolierung eines Einbrennofens
Die Isolierung eines Einbrennofens sollte fachgerecht durchgeführt werden, um die gewünschten Ergebnisse zu erzielen. Die folgenden Schritte sind zu beachten:
- Entfernen Sie die alte Isolierung, falls vorhanden.
- Reinigen Sie die Oberfläche des Ofens gründlich.
- Bringen Sie die neue Isolierung an.
- Verschließen Sie alle Lücken oder Risse.
Sicherheitshinweise
Bei der Isolierung eines Einbrennofens sind folgende Sicherheitshinweise zu beachten:
- Tragen Sie immer geeignete Schutzkleidung, z. B. Schutzbrille, Handschuhe und Atemschutzmaske.
- Achten Sie darauf, dass der Ofen ausgeschaltet und abgekühlt ist, bevor Sie mit der Isolierung beginnen.
- Verwenden Sie nur Isoliermaterial, das für den Einsatz in Einbrennöfen geeignet ist.
Fazit
Die Isolierung eines Einbrennofens ist eine wichtige Maßnahme, um die Energiekosten zu senken und die Sicherheit zu gewährleisten. Durch die fachgerechte Durchführung der Isolierung können Sie die gewünschten Ergebnisse erzielen und den Ofen über viele Jahre hinweg nutzen.
Transport
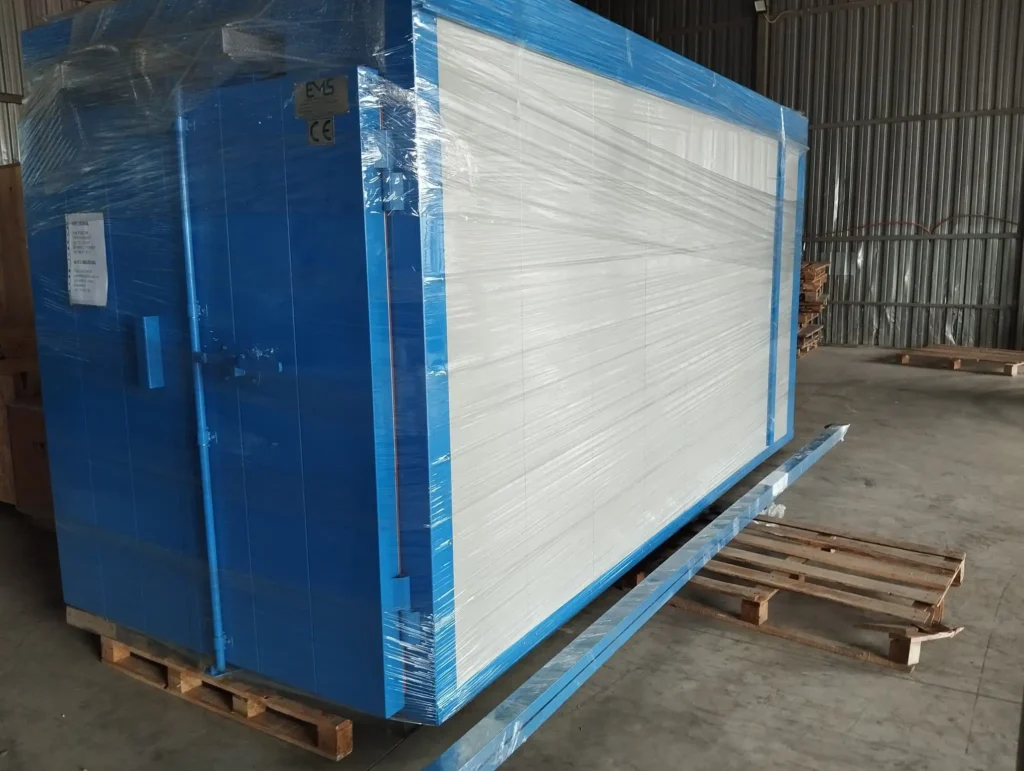
Der Transport eines Einbrennofens ist eine Aufgabe, die mit Vorsicht und Sorgfalt durchgeführt werden sollte. Der Ofen ist ein schweres und sperriges Gerät, das leicht beschädigt werden kann, wenn er nicht richtig transportiert wird.
Vorbereitung
Bevor Sie mit dem Transport des Ofens beginnen, sollten Sie folgende Vorbereitungen treffen:
- Stellen Sie sicher, dass der Ofen vollständig abgekühlt ist.
- Entfernen Sie alle losen Teile, wie z. B. die Türen und die Schubladen.
- Sichern Sie alle beweglichen Teile, wie z. B. die Heizelemente.
- Besorgen Sie sich geeignetes Transportmaterial, wie z. B. eine Palette und Spanngurte.
Transport
Der Ofen sollte auf einer stabilen Palette transportiert werden. Verwenden Sie Spanngurte, um den Ofen auf der Palette zu sichern. Achten Sie darauf, dass die Spanngurte fest genug angezogen sind, um den Ofen zu sichern, aber nicht so fest, dass sie ihn beschädigen.
Wenn der Ofen auf der Palette befestigt ist, können Sie ihn zum Transportfahrzeug fahren. Achten Sie darauf, dass der Ofen beim Transport nicht herunterfällt oder umkippt.
Lieferung
Bei der Lieferung des Ofens sollten Sie folgende Schritte beachten:
- Stellen Sie sicher, dass der Lieferant den Ofen sicher anliefert.
- Überprüfen Sie den Ofen nach der Lieferung auf Schäden.
Sicherheitshinweise
Beim Transport eines Einbrennofens sollten Sie folgende Sicherheitshinweise beachten:
- Tragen Sie immer geeignete Schutzkleidung, wie z. B. Handschuhe und Schutzbrille.
- Achten Sie darauf, dass der Ofen nicht herunterfällt oder umkippt.
- Vermeiden Sie, dass der Ofen in Kontakt mit Wasser oder anderen Flüssigkeiten kommt.
Fazit
Der Transport eines Einbrennofens ist eine Aufgabe, die mit Vorsicht und Sorgfalt durchgeführt werden sollte. Durch die Einhaltung der oben genannten Schritte können Sie den Ofen sicher und unbeschädigt transportieren.
Zusätzliche Tipps
Wenn der Ofen über eine lange Strecke transportiert werden muss, sollten Sie ihn in einem geschlossenen Fahrzeug transportieren, um ihn vor Witterungseinflüssen zu schützen.
Wenn der Ofen in einem Gebäude transportiert werden muss, sollten Sie die Türen und Gänge überprüfen, um sicherzustellen, dass der Ofen durchpasst.
Wenn Sie den Ofen selbst transportieren, sollten Sie sich von einem Freund oder Verwandten helfen lassen.
Sicherheitsfunktionen
Einbrennöfen sind große und komplexe Geräte, die bei unsachgemäßer Verwendung zu Verletzungen oder Schäden führen können. Aus diesem Grund sind Einbrennöfen mit einer Reihe von Sicherheitsfunktionen ausgestattet, um die Sicherheit der Benutzer zu gewährleisten.
Die wichtigsten Sicherheitsfunktionen eines Einbrennofens sind:
- Temperaturregler: Der Temperaturregler ermöglicht es dem Benutzer, die Temperatur des Ofens genau zu steuern. Dies ist wichtig, um zu verhindern, dass das Material im Ofen überhitzt und beschädigt wird.
- Thermostat: Das Thermostat schaltet den Ofen automatisch ab, wenn die eingestellte Temperatur erreicht ist. Dies verhindert, dass das Material im Ofen zu lange erhitzt wird und beschädigt wird.
- Überhitzungsschutz: Der Überhitzungsschutz schaltet den Ofen automatisch ab, wenn die Temperatur im Ofen zu hoch wird. Dies kann durch einen Stromausfall oder einen anderen Fehler verursacht werden.
- Sicherheitsthermostat: Der Sicherheitsthermostat schaltet den Ofen automatisch ab, wenn die Temperatur im Ofen zu hoch wird. Dies kann durch einen Brand oder einen anderen Notfall verursacht werden.
- Sicherheitstür: Die Sicherheitstür verhindert, dass der Benutzer den Ofen während des Betriebs öffnet. Dies ist wichtig, um Verbrennungen zu vermeiden.
- Sicherheitsschalter: Der Sicherheitsschalter schaltet den Ofen automatisch ab, wenn die Tür geöffnet wird. Dies ist wichtig, um zu verhindern, dass der Ofen eingeschaltet bleibt, wenn die Tür geöffnet ist.
Zusätzliche Sicherheitsfunktionen:
- Feuerlöscher: Ein Feuerlöscher sollte in der Nähe des Ofens aufbewahrt werden, um im Brandfall schnell reagieren zu können.
- Not-Aus-Schalter: Der Not-Aus-Schalter schaltet den Ofen sofort ab. Er sollte in greifbarer Nähe des Ofens angebracht sein.
- Warnhinweise: Der Ofen sollte mit Warnhinweisen versehen sein, die den Benutzer vor Gefahren warnen.
Sicherheitshinweise:
- Lesen Sie die Bedienungsanleitung des Ofens sorgfältig durch, bevor Sie ihn verwenden.
- Befolgen Sie die Sicherheitshinweise, die in der Bedienungsanleitung angegeben sind.
- Lassen Sie den Ofen niemals unbeaufsichtigt.
- Verwenden Sie den Ofen nur für den vorgesehenen Zweck.
- Reinigen Sie den Ofen regelmäßig, um Brandgefahr zu vermeiden.
Durch die Einhaltung der oben genannten Sicherheitshinweise können Sie die Sicherheit beim Umgang mit Einbrennöfen gewährleisten.
Die Pulverbeschichtung ist ein weit verbreitetes Verfahren zur Oberflächenveredelung, das sich durch seine umweltfreundlichen Eigenschaften und Langlebigkeit der Beschichtung auszeichnet. Im Gegensatz zu herkömmlichen flüssigen Beschichtungen werden bei der Pulverbeschichtung trockene Pulverpartikel elektrostatisch auf die Oberfläche eines Werkstücks aufgebracht. Anschließend wird das Pulver in einem Ofen erhitzt, wodurch es schmilzt und eine gleichmäßige, dauerhafte Beschichtung bildet.
Vorteile der Pulverbeschichtung umfassen:
- Umweltfreundlichkeit: Keine Lösungsmittel und geringere Emissionen von flüchtigen organischen Verbindungen (VOC).
- Effizienz: Hohe Materialausnutzung und weniger Abfall.
- Robustheit: Gute Beständigkeit gegen chemische, mechanische und Witterungseinflüsse.
Pulverbeschichtungsanlagen

Pulverbeschichtungsanlagen sind zentraler Bestandteil des Pulverbeschichtungsprozesses und umfassen die komplette Infrastruktur, die zur Anwendung von Pulverbeschichtungen erforderlich ist. Diese Anlagen sind in verschiedenen Größen und Ausführungen erhältlich, um unterschiedlichen industriellen Anforderungen gerecht zu werden.
Typen von Pulverbeschichtungsanlagen:
- Manuelle Pulverbeschichtungsanlagen:
Ideal für kleinere Betriebe oder spezialisierte Anwendungen, bei denen Flexibilität gefordert ist. Sie bestehen aus einer Pulverkabine, einem Pulvergerät und einem Einbrennofen. - Halbautomatische Anlagen:
Kombinieren manuelle und automatische Prozesse, um eine höhere Effizienz bei mittleren Produktionsvolumina zu erreichen. Diese Anlagen bieten eine gute Balance zwischen Flexibilität und Automatisierung. - Vollautomatische Pulverbeschichtungsanlagen:
Entwickelt für Großserienproduktionen. Diese Anlagen sind vollständig automatisiert und beinhalten Fördersysteme, automatische Pistolen und integrierte Steuerungssysteme, um hohe Produktionsgeschwindigkeiten und gleichbleibende Qualität zu gewährleisten.
Pulverkabinen
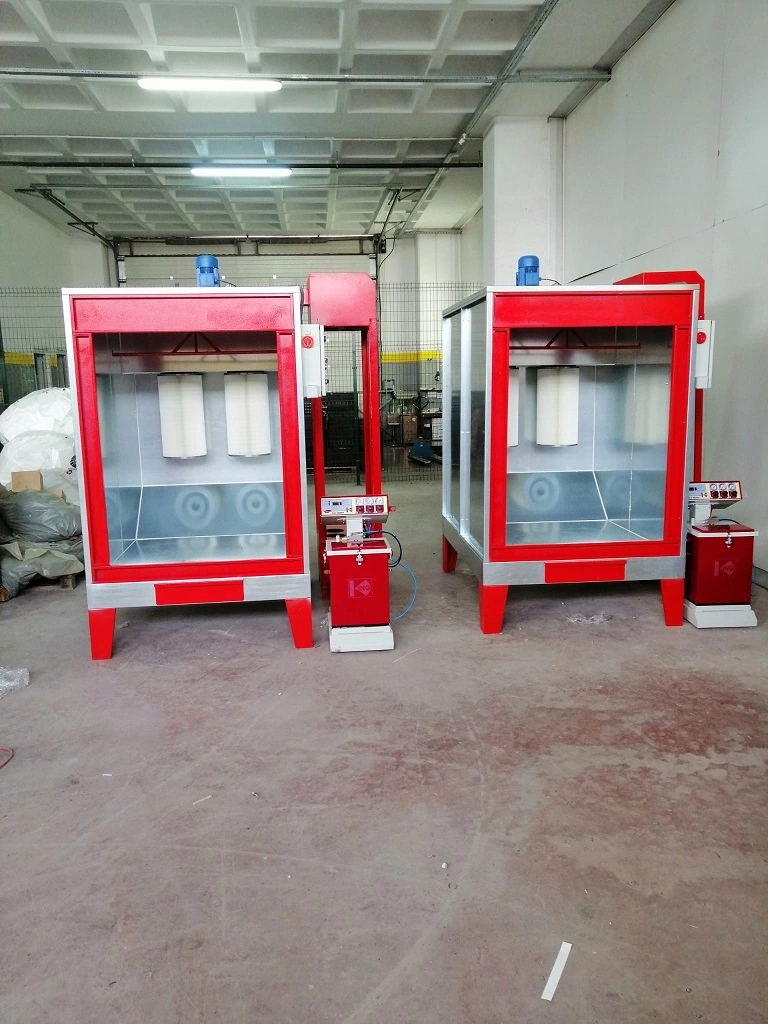
Pulverkabinen sind spezielle Räume oder Gehäuse, in denen der Pulverbeschichtungsprozess stattfindet. Sie spielen eine entscheidende Rolle bei der Gewährleistung einer sauberen und kontrollierten Umgebung für die Pulverbeschichtung.
Typen von Pulverkabinen:
- Offene Kabinen:
Diese Kabinen sind ideal für kleine bis mittlere Anwendungen. Sie bieten einen offenen Zugang für den Bediener, sind jedoch weniger effektiv bei der Kontrolle von Overspray. - Geschlossene Kabinen:
Bieten eine kontrollierte Umgebung und minimieren Overspray durch integrierte Luftführungssysteme. Geschlossene Kabinen sind in der Regel effizienter und sicherer. - Selbstreinigende Kabinen:
Ausgestattet mit automatischen Reinigungssystemen, die den Farbwechsel und die Wartung erleichtern. Diese Kabinen sind besonders nützlich in Anwendungen mit häufigem Farbwechsel.
Sicherheits- und Umweltaspekte: Pulverkabinen sind so konzipiert, dass sie die Sicherheit der Bediener gewährleisten und die Umweltbelastung minimieren. Dazu gehören Belüftungssysteme, Filter zur Partikelabscheidung und Schutzvorrichtungen, die den Kontakt mit dem Pulver verhindern.
Einbrennöfen
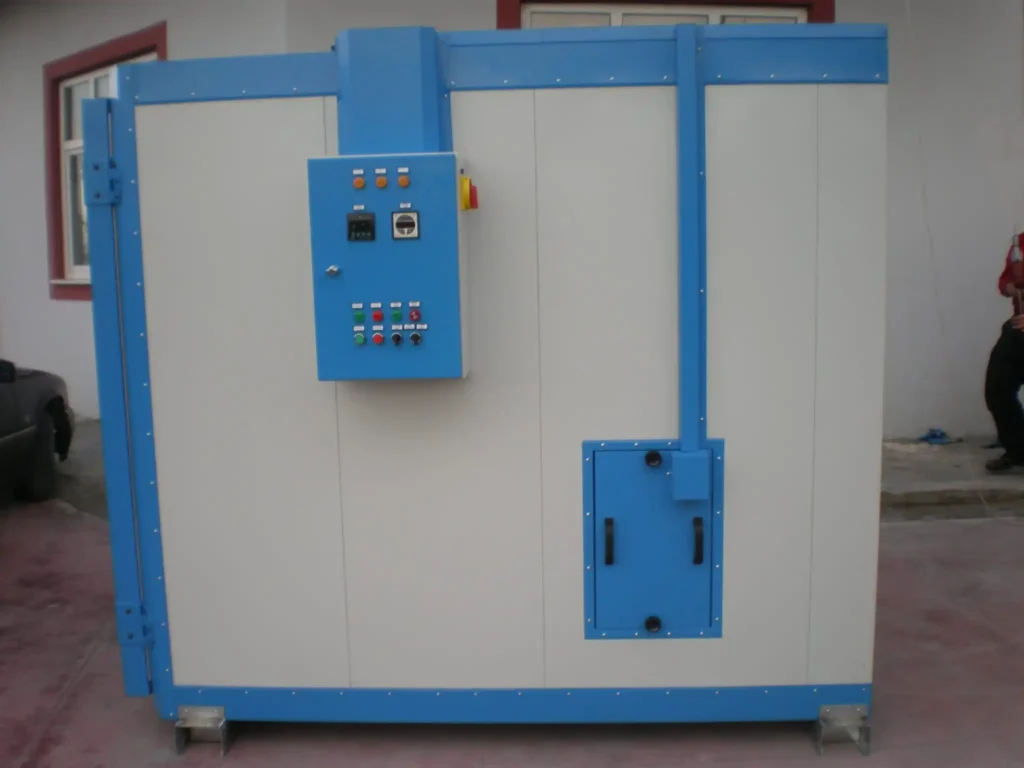
Der Einbrennofen ist ein unverzichtbarer Bestandteil des Pulverbeschichtungsprozesses, da er die notwendigen Temperaturen bereitstellt, um das aufgetragene Pulver zu einer harten, widerstandsfähigen Oberfläche zu verschmelzen.
Typen von Einbrennöfen:
- Chargenöfen:
Ideal für kleinere Produktionen oder variierende Chargengrößen. Diese Öfen sind flexibel und können unterschiedliche Teile gleichzeitig verarbeiten. - Durchlauföfen:
Entwickelt für kontinuierliche Produktionslinien, bei denen hohe Durchsatzraten erforderlich sind. Teile werden auf einem Förderband durch den Ofen transportiert, was eine konstante Verarbeitung ermöglicht.
Energieeffizienz und Temperatursteuerung: Moderne Einbrennöfen sind energieeffizient und bieten präzise Temperaturregelung, um gleichbleibende Beschichtungsqualität zu gewährleisten. Technologien wie Wärmerückgewinnungssysteme und fortschrittliche Isolierung tragen zur Reduzierung des Energieverbrauchs bei.
Pulvergeräte
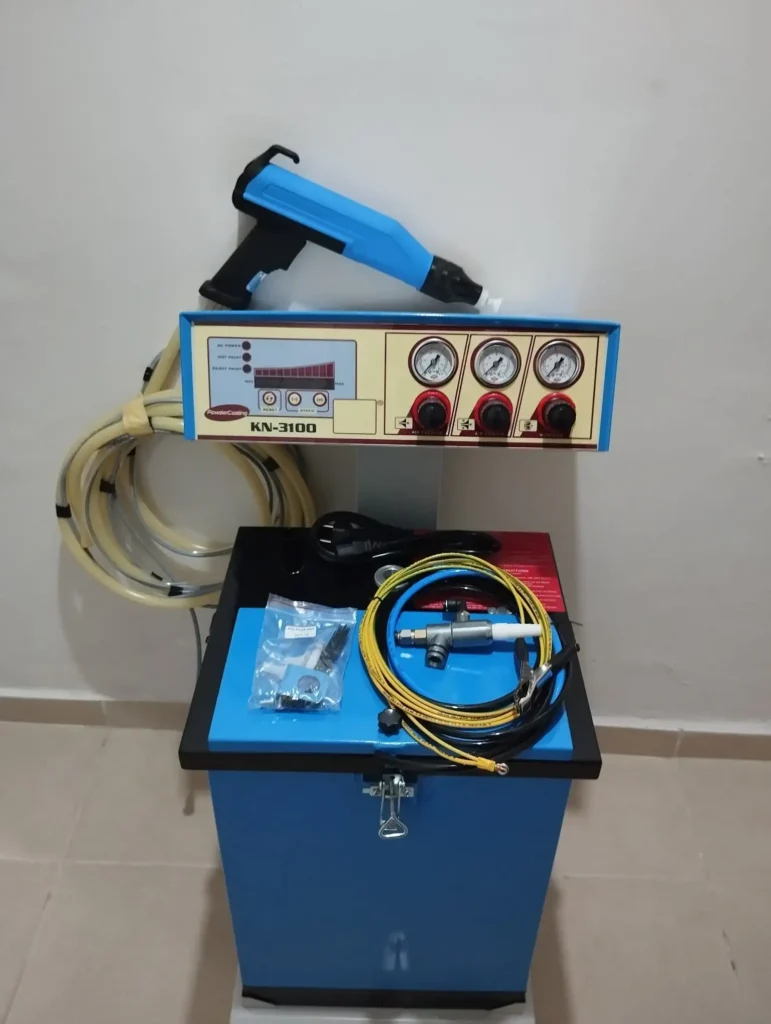
Pulvergeräte sind für die Anwendung der Pulverbeschichtung unerlässlich. Sie bestehen aus verschiedenen Komponenten, die zusammenarbeiten, um das Pulver gleichmäßig und effizient auf die Oberfläche des Werkstücks aufzubringen.
Arten von Pulvergeräten:
- Elektrostatische Sprühpistolen:
Verwenden Hochspannung, um Pulverpartikel elektrostatisch aufzuladen, was eine gleichmäßige Verteilung und Haftung auf dem Werkstück fördert. - Pulverförderer:
Transportieren das Pulver vom Vorratsbehälter zur Sprühpistole. Sie sind entscheidend für die Konsistenz und Effizienz des Beschichtungsprozesses.
Elektrostatik spielt eine zentrale Rolle bei der Pulverbeschichtung, da sie die Anziehungskraft zwischen den Pulverpartikeln und der Oberfläche erhöht und so eine gleichmäßige Beschichtung ermöglicht.
Auswahlkriterien für Pulvergeräte umfassen:
- Kompatibilität: Passend für die spezifischen Anforderungen der Anwendung.
- Flexibilität: Anpassungsfähigkeit an unterschiedliche Werkstückgrößen und -formen.
- Effizienz: Hohe Materialausnutzung und minimierter Pulververbrauch.
Automatische Pulverbeschichtungsanlagen
Automatische Pulverbeschichtungsanlagen bieten zahlreiche Vorteile, insbesondere in Bezug auf Effizienz und Konsistenz. Sie sind ideal für Großserienproduktionen und tragen zur Senkung der Betriebskosten bei.
Vorteile der Automatisierung:
- Erhöhte Produktivität: Automatische Systeme können kontinuierlich arbeiten und so die Produktionskapazität erheblich steigern.
- Gleichbleibende Qualität: Minimierung von Fehlern und Variabilität durch präzise Steuerung der Beschichtungsparameter.
- Kostenersparnis: Reduzierung der Arbeitskosten und des Materialverbrauchs durch optimierte Prozesse.
Komponenten und Funktionsweise:
- Fördersysteme: Transportieren Werkstücke automatisch durch den Beschichtungsprozess.
- Automatische Sprühpistolen: Verteilen das Pulver gleichmäßig auf den Werkstücken.
- Integrierte Steuerungssysteme: Überwachen und steuern alle Aspekte des Beschichtungsprozesses, einschließlich Temperatur, Sprühzeit und Pulvermenge.
Ersatzteile für Pulverbeschichtungsanlagen
Ersatzteile sind entscheidend für die Wartung und Langlebigkeit von Pulverbeschichtungsanlagen. Regelmäßige Wartung und der rechtzeitige Austausch von Verschleißteilen sind unerlässlich, um Ausfallzeiten zu minimieren und die Effizienz der Anlagen aufrechtzuerhalten.
Wichtige Ersatzteile und ihre Funktionen:
- Sprühdüsen: Stellen die gleichmäßige Verteilung des Pulvers sicher.
- Filter: Entfernen überschüssige Pulverpartikel aus der Kabinenluft.
- Förderbänder: Transportieren die Werkstücke durch den Beschichtungsprozess.
Wartung und Instandhaltung:
- Regelmäßige Inspektionen: Identifizieren potenzielle Probleme frühzeitig und ermöglichen rechtzeitige Reparaturen.
- Ersatzteilmanagement: Sicherstellung der Verfügbarkeit von Ersatzteilen zur Minimierung von Ausfallzeiten.
Zukunft der Pulverbeschichtungstechnologie
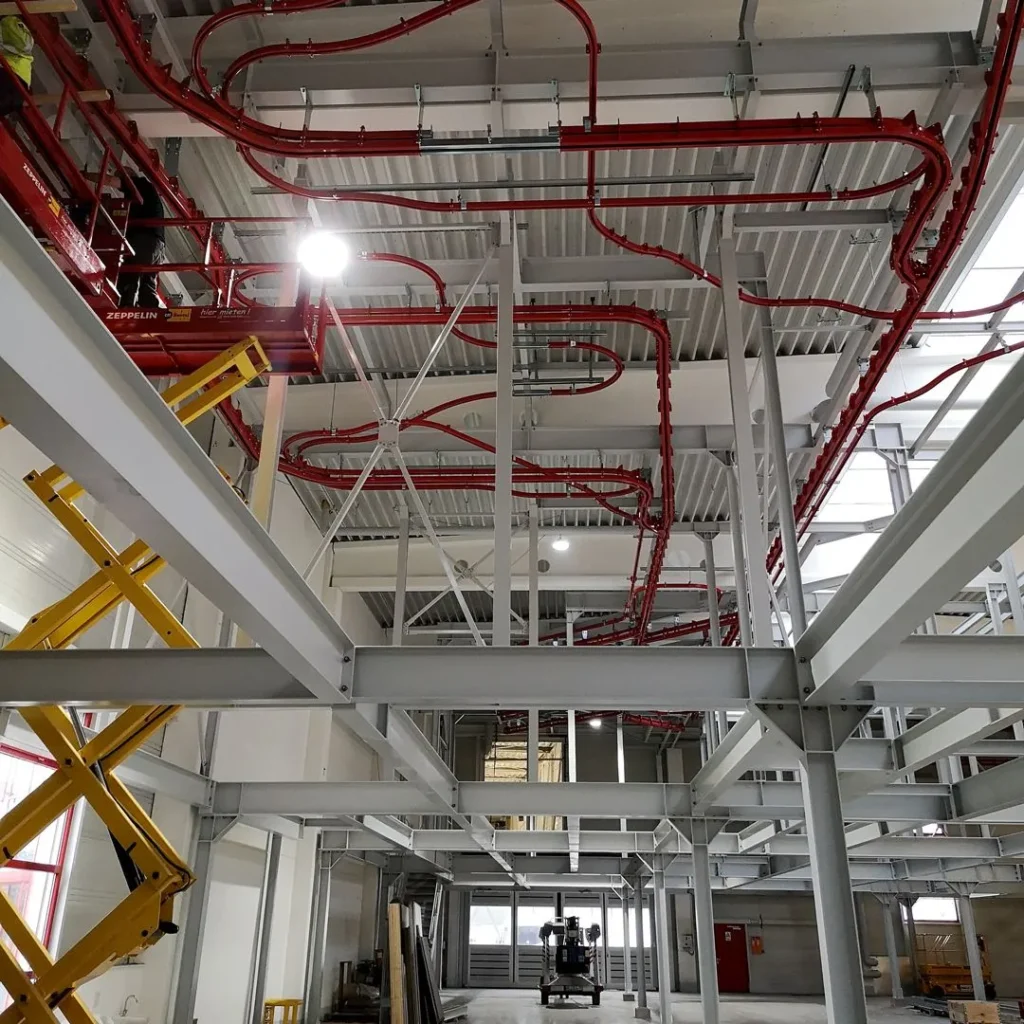
Die Pulverbeschichtungstechnologie entwickelt sich kontinuierlich weiter, um den steigenden Anforderungen der Industrie gerecht zu werden. Zu den wichtigsten Trends und Entwicklungen gehören:
- Nachhaltigkeit: Einsatz umweltfreundlicher Materialien und Verfahren zur Reduzierung des ökologischen Fußabdrucks.
- Fortschrittliche Materialien: Entwicklung neuer Pulverformeln, die verbesserte Eigenschaften wie Korrosionsbeständigkeit und UV-Stabilität bieten.
- Digitalisierung: Integration von IoT und datenbasierten Lösungen zur Optimierung des Beschichtungsprozesses und zur Verbesserung der Qualitätssicherung.
Fazit
Pulverbeschichtungsanlagen und ihre Komponenten sind ein wesentlicher Bestandteil moderner Produktionsprozesse. Sie bieten eine umweltfreundliche, effiziente und langlebige Lösung für die Oberflächenveredelung. Durch die ständige Weiterentwicklung der Technologie und den Einsatz von Automatisierung können Unternehmen ihre Effizienz steigern und gleichzeitig die Qualität ihrer Produkte sicherstellen.
Ich hoffe, dieser umfassende Überblick über Pulverbeschichtungsanlagen und verwandte Komponenten ist hilfreich. Wenn Sie weitere Informationen oder spezifische Details zu einem bestimmten Abschnitt wünschen, lassen Sie es mich bitte wissen!
Wie lange hält Pulverbeschichtung?
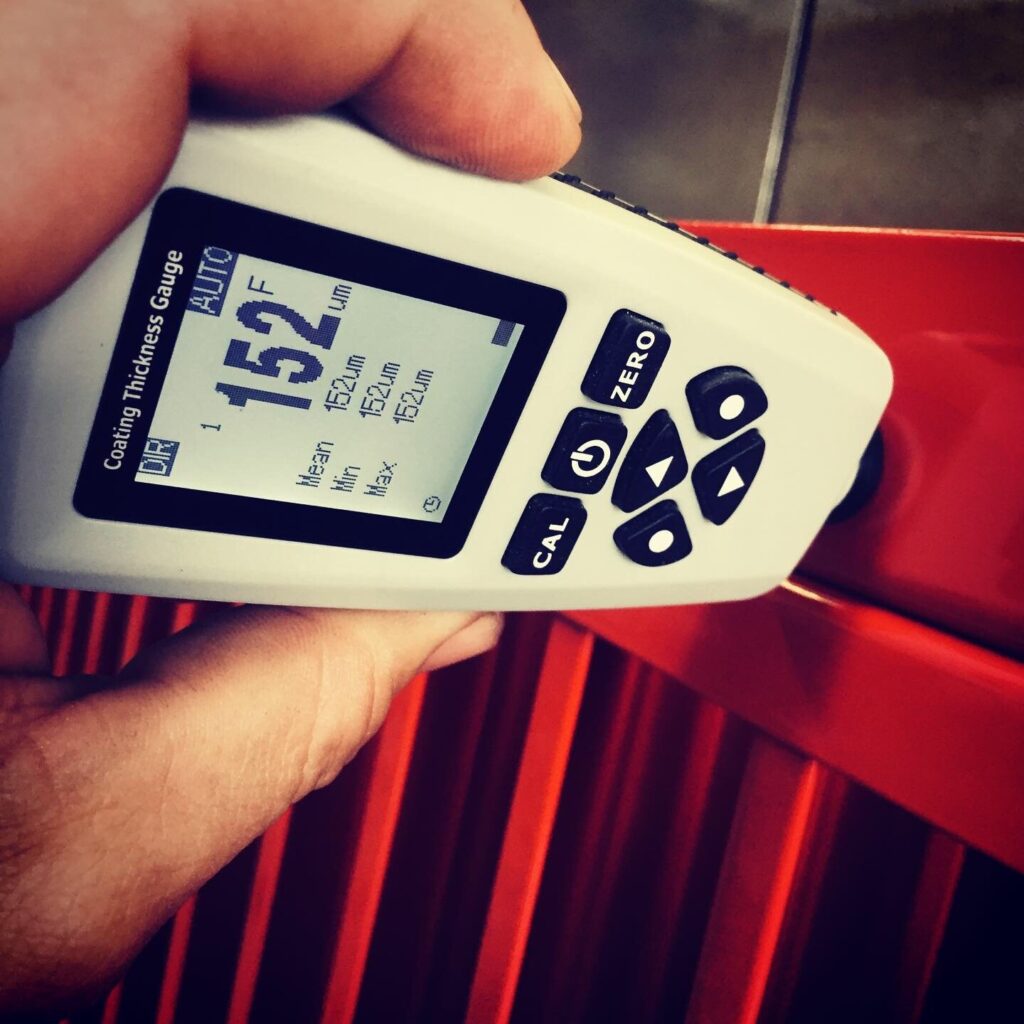
Die Haltbarkeit einer Pulverbeschichtung kann je nach Anwendung, Umgebung und Qualität der Beschichtung stark variieren. Hier sind einige Faktoren, die die Lebensdauer einer Pulverbeschichtung beeinflussen können:
Faktoren, die die Haltbarkeit beeinflussen:
- Qualität des Pulvers:
- Pulverformulierung: Hochwertige Pulverlacke bieten in der Regel eine längere Haltbarkeit und bessere Widerstandsfähigkeit gegen Umwelteinflüsse.
- UV-Stabilität: Speziell formulierte Pulverlacke mit UV-Schutz verlängern die Lebensdauer bei Anwendungen im Freien.
- Vorbereitung der Oberfläche:
- Reinigung: Eine gründliche Reinigung der Oberfläche vor der Beschichtung ist entscheidend, um eine gute Haftung des Pulvers zu gewährleisten.
- Vorbehandlung: Verfahren wie das Phosphatieren oder Sandstrahlen verbessern die Haftung und Korrosionsbeständigkeit.
- Bedingungen der Anwendung:
- Innen- vs. Außenanwendung: Pulverbeschichtungen im Innenbereich können Jahrzehnte halten, während Beschichtungen im Außenbereich stärker durch UV-Strahlung, Feuchtigkeit und Temperaturschwankungen beansprucht werden.
- Mechanische Belastung: Starke mechanische Belastungen oder Abnutzung können die Lebensdauer der Beschichtung verkürzen.
- Betriebsumgebung:
- Korrosive Umgebungen: In Industriegebieten oder maritimen Umgebungen kann die Lebensdauer aufgrund der erhöhten Korrosionsgefahr kürzer sein.
- Witterungseinflüsse: Regionen mit extremen Wetterbedingungen können die Lebensdauer der Pulverbeschichtung verkürzen.
- Beschichtungsdicke:
- Eine angemessene Schichtdicke ist wichtig, um eine gleichmäßige Abdeckung und ausreichenden Schutz zu gewährleisten.
Typische Lebensdauer
- Innenanwendungen:
Pulverbeschichtungen, die in Innenbereichen aufgebracht werden, können oft 15-20 Jahre oder länger halten, da sie weniger extremen Bedingungen ausgesetzt sind. - Außenanwendungen:
Bei Außenanwendungen hängt die Lebensdauer stark von den Umweltbedingungen ab, kann jedoch typischerweise zwischen 5 und 10 Jahren liegen. Hochwertige Pulverbeschichtungen, die speziell für den Außenbereich entwickelt wurden, können bis zu 15 Jahre oder länger halten, wenn sie regelmäßig gewartet werden. - Industrieanwendungen:
In industriellen Anwendungen, die häufig aggressiven Chemikalien oder starker mechanischer Beanspruchung ausgesetzt sind, kann die Lebensdauer kürzer sein und erfordert häufigere Inspektionen und Wartungen.
Verlängerung der Haltbarkeit
Um die Lebensdauer der Pulverbeschichtung zu maximieren, sind folgende Maßnahmen empfehlenswert:
- Regelmäßige Inspektion und Wartung: Frühe Erkennung von Schäden und rechtzeitige Reparaturen können die Haltbarkeit erheblich verlängern.
- Vermeidung von physikalischen Schäden: Sorgfältiger Umgang mit beschichteten Oberflächen reduziert das Risiko von Kratzern und Abplatzungen.
- Schutz vor chemischen Einflüssen: Vermeidung von Kontakt mit aggressiven Chemikalien und Reinigungsmitteln, die die Beschichtung angreifen könnten.
Fazit
Die Pulverbeschichtung ist eine langlebige und widerstandsfähige Methode zur Oberflächenveredelung, die bei richtiger Anwendung und Wartung viele Jahre halten kann. Die tatsächliche Lebensdauer hängt jedoch von zahlreichen Faktoren ab, einschließlich der Qualität des Pulvers, der Vorbereitung der Oberfläche und den Umgebungsbedingungen, denen die beschichteten Teile ausgesetzt sind.
Wartungstipps für Anlagen
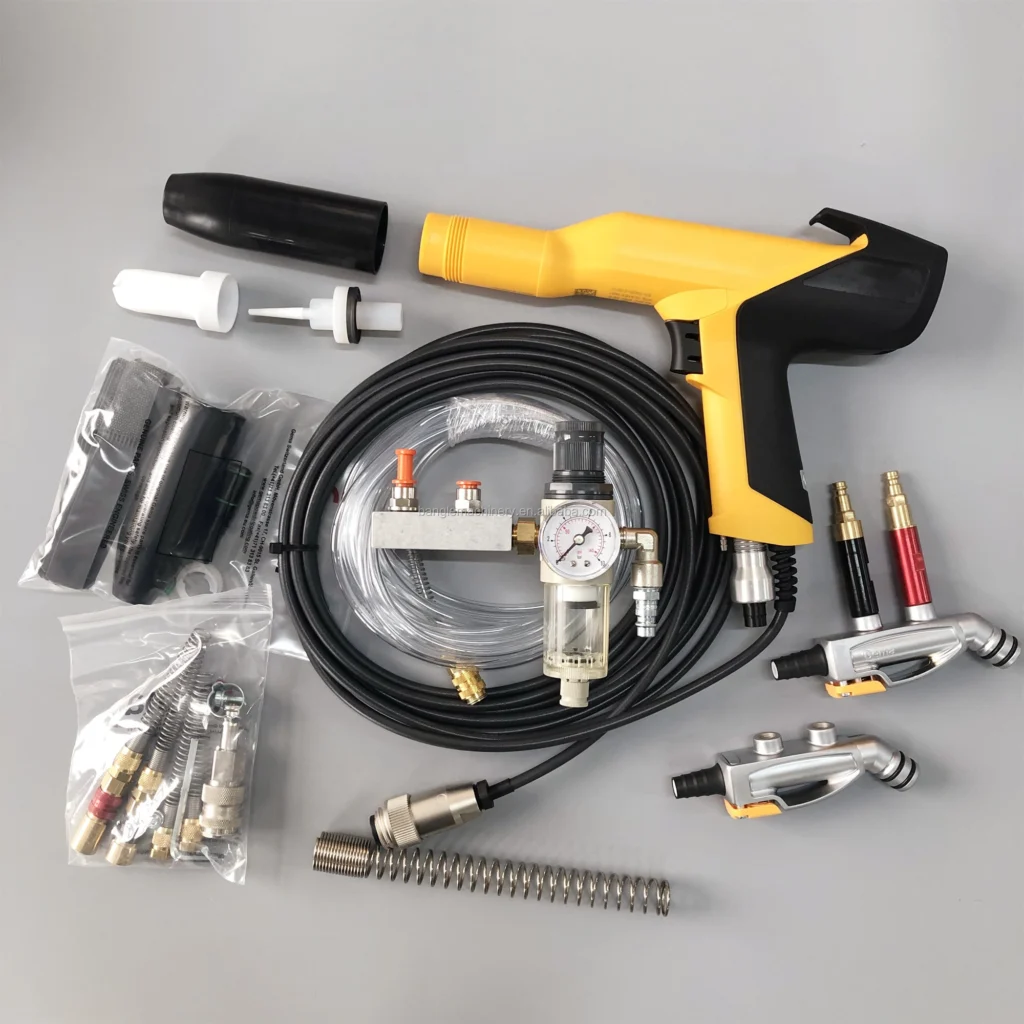
Um die Langlebigkeit und Effizienz von Pulverbeschichtungsanlagen zu gewährleisten, ist eine regelmäßige Wartung entscheidend. Hier sind einige Wartungstipps, die Ihnen helfen, die Leistung Ihrer Anlagen zu maximieren und Ausfallzeiten zu minimieren:
1. Allgemeine Inspektion
- Regelmäßige Überprüfungen: Führen Sie wöchentliche oder monatliche Inspektionen der gesamten Anlage durch, um sicherzustellen, dass alle Komponenten ordnungsgemäß funktionieren.
- Sichtprüfung: Überprüfen Sie auf sichtbare Abnutzung, Schäden oder lose Teile, die die Funktion beeinträchtigen könnten.
2. Pulverkabinen
- Filterwartung:
- Reinigung oder Austausch: Reinigen oder ersetzen Sie die Filter regelmäßig, um eine effiziente Luftführung und Partikelabscheidung zu gewährleisten.
- Filtertypen beachten: Verwenden Sie immer die vom Hersteller empfohlenen Filtertypen.
- Kabinenreinigung:
- Regelmäßige Reinigung: Halten Sie die Kabinenwände und -böden sauber, um Ansammlungen von überschüssigem Pulver zu vermeiden.
- Staubabsaugung: Stellen Sie sicher, dass die Absauganlage regelmäßig geleert und gewartet wird, um eine optimale Funktion zu gewährleisten.
3. Einbrennöfen
- Temperaturüberwachung:
- Regelmäßige Kalibrierung: Überprüfen Sie regelmäßig die Kalibrierung der Temperatursteuerung, um eine gleichbleibende Beschichtungsqualität sicherzustellen.
- Thermoelemente prüfen: Überprüfen Sie die Thermoelemente auf Genauigkeit und Funktionstüchtigkeit.
- Ofenreinigung:
- Innenreinigung: Entfernen Sie regelmäßig Rückstände und Ablagerungen im Inneren des Ofens, um die Effizienz zu erhalten.
- Dichtungen überprüfen: Überprüfen Sie die Dichtungen an Türen und Durchgängen auf Abnutzung und tauschen Sie sie bei Bedarf aus.
4. Pulvergeräte
- Sprühpistolenwartung:
- Düsenreinigung: Reinigen Sie die Düsen regelmäßig, um Verstopfungen und ungleichmäßige Sprühmuster zu vermeiden.
- Ersatzteile prüfen: Halten Sie Ersatzdüsen und andere Verschleißteile bereit, um Ausfallzeiten zu minimieren.
- Pulverförderer:
- Reinigungsintervalle: Reinigen Sie die Pulverförderer, um Blockaden zu verhindern und eine gleichmäßige Pulverzufuhr zu gewährleisten.
- Antriebssysteme warten: Überprüfen Sie regelmäßig die Antriebe und Lager auf Verschleiß und tauschen Sie sie bei Bedarf aus.
5. Fördersysteme
- Kettenspannung und Schmierung:
- Spannung überprüfen: Kontrollieren Sie die Spannung der Förderketten und passen Sie sie bei Bedarf an, um einen reibungslosen Betrieb zu gewährleisten.
- Schmierung: Schmieren Sie alle beweglichen Teile regelmäßig, um Verschleiß zu minimieren.
- Lagerwartung:
- Überprüfung der Lager: Überprüfen Sie die Lager auf Abnutzung und tauschen Sie sie bei Bedarf aus.
- Schmiermittel verwenden: Verwenden Sie die vom Hersteller empfohlenen Schmiermittel, um die Lebensdauer der Lager zu verlängern.
6. Automatisierte Systeme
- Steuerungssysteme:
- Software-Updates: Halten Sie die Software der Steuerungssysteme auf dem neuesten Stand, um Effizienz und Sicherheit zu gewährleisten.
- Fehlerprotokollierung: Überwachen Sie Fehlerprotokolle, um potenzielle Probleme frühzeitig zu erkennen.
- Sensoren und Aktoren:
- Funktionsprüfung: Überprüfen Sie regelmäßig die Sensoren und Aktoren auf ihre Funktionsfähigkeit und ersetzen Sie defekte Teile.
- Kalibrierung: Führen Sie regelmäßige Kalibrierungen durch, um die Genauigkeit der automatisierten Systeme zu gewährleisten.
7. Ersatzteile und Lagerhaltung
- Ersatzteilmanagement:
- Bestandskontrolle: Führen Sie eine genaue Bestandskontrolle der Ersatzteile, um Ausfallzeiten durch fehlende Teile zu vermeiden.
- Qualität der Ersatzteile: Verwenden Sie stets hochwertige Originalersatzteile, um die Funktionalität der Anlagen zu gewährleisten.
8. Schulung des Personals
- Regelmäßige Schulungen: Schulen Sie Ihr Personal regelmäßig in der Bedienung und Wartung der Anlagen, um Bedienfehler zu vermeiden und die Sicherheit zu erhöhen.
- Notfallverfahren: Stellen Sie sicher, dass alle Mitarbeiter mit den Notfallverfahren vertraut sind, um im Falle eines Ausfalls schnell reagieren zu können.
9. Dokumentation
- Wartungsprotokolle: Führen Sie detaillierte Wartungsprotokolle, um den Wartungsverlauf und alle durchgeführten Arbeiten zu dokumentieren.
- Checklisten verwenden: Nutzen Sie Wartungschecklisten, um sicherzustellen, dass alle erforderlichen Maßnahmen regelmäßig durchgeführt werden.
Fazit
Durch die Einhaltung dieser Wartungstipps können Sie die Effizienz und Lebensdauer Ihrer Pulverbeschichtungsanlagen maximieren. Eine gut gewartete Anlage führt zu einer höheren Produktqualität, weniger Ausfallzeiten und einer längeren Lebensdauer der Geräte. Regelmäßige Wartung ist eine Investition, die sich durch verbesserte Leistung und geringere Betriebskosten auszahlt.
Automatisierungsoptionen
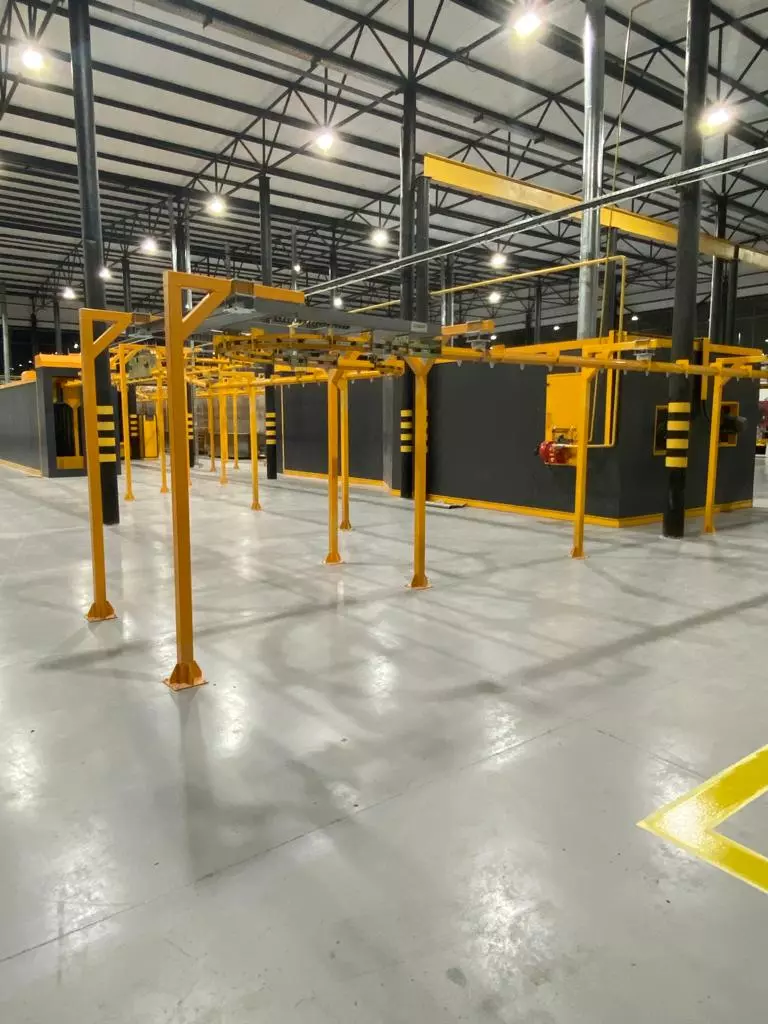
Automatisierungsoptionen in der Pulverbeschichtung bieten zahlreiche Vorteile, darunter erhöhte Effizienz, gleichbleibende Qualität und reduzierte Betriebskosten. Im Folgenden werden verschiedene Automatisierungsoptionen erläutert, die in modernen Pulverbeschichtungsanlagen eingesetzt werden können:
1. Automatische Sprühsysteme
Automatische Sprühsysteme sind eine wesentliche Komponente für die Automatisierung der Pulverbeschichtung und bieten präzise und gleichmäßige Beschichtungen. Sie bestehen aus mehreren automatisierten Sprühpistolen, die auf robotergesteuerten Armen montiert sind.
- Robotergestützte Sprühpistolen:
Diese Pistolen sind an Roboterarmen befestigt, die programmierbar sind, um komplexe Bewegungsmuster auszuführen und die Sprühwinkel für unterschiedliche Werkstückgeometrien zu optimieren. - Pulvermengensteuerung:
Automatisierte Systeme ermöglichen die genaue Steuerung der Pulvermengen, was zu einer gleichmäßigen Schichtdicke und weniger Abfall führt. - Adaptive Technologie:
Moderne Systeme nutzen Sensoren, um die Werkstückgeometrie in Echtzeit zu erfassen und die Sprühmuster entsprechend anzupassen.
2. Fördersysteme
Automatisierte Fördersysteme transportieren die Werkstücke durch die verschiedenen Phasen des Beschichtungsprozesses und tragen dazu bei, den Durchsatz zu erhöhen.
- Overhead-Fördersysteme:
Diese Systeme transportieren die Teile über Kopf durch die Kabinen und Öfen, was den Bodenraum frei hält und die Effizienz erhöht. - Ketten- und Schienensysteme:
Förderbänder und Schienensysteme bieten Flexibilität bei der Gestaltung der Produktionslinie und können an unterschiedliche Anforderungen angepasst werden. - Variable Geschwindigkeit:
Einige Fördersysteme ermöglichen die Anpassung der Geschwindigkeit je nach Werkstückgröße und Prozessanforderungen.
3. Einbrennöfen mit Automatisierung
Einbrennöfen können durch Automatisierung effizienter und präziser arbeiten, was die Qualität der Beschichtung verbessert.
- Automatisierte Temperaturregelung:
Intelligente Steuerungssysteme passen die Ofentemperatur in Echtzeit an, um die optimale Aushärtung der Pulverbeschichtung zu gewährleisten. - Zeitschaltuhren und Sensoren:
Integrierte Timer und Sensoren helfen dabei, den Aushärtungsprozess genau zu überwachen und die Energieeffizienz zu maximieren. - Automatische Türsteuerung:
Automatische Türen öffnen und schließen sich synchron mit dem Ein- und Ausgang der Werkstücke, um den Wärmeverlust zu minimieren.
4. Qualitätskontrollsysteme
Automatisierte Qualitätskontrollsysteme sorgen dafür, dass die Beschichtungen den festgelegten Standards entsprechen und verringern den Bedarf an manueller Inspektion.
- Visuelle Inspektionssysteme:
Kameras und Bildverarbeitungstechnologien prüfen die Beschichtungsqualität und identifizieren sofort Fehler oder Unregelmäßigkeiten. - Schichtdickenmessung:
Berührungslose Messsysteme können die Dicke der Pulverbeschichtung präzise messen und Daten zur weiteren Analyse bereitstellen. - Echtzeit-Datenanalyse:
Datenerfassungs- und Analysesysteme ermöglichen die Überwachung des gesamten Prozesses und helfen bei der Identifizierung von Optimierungspotenzialen.
5. Software-Integration
Softwarelösungen spielen eine entscheidende Rolle bei der Automatisierung, indem sie verschiedene Systeme integrieren und den Betrieb effizienter gestalten.
- Leitsysteme (SCADA):
Supervisory Control and Data Acquisition (SCADA) Systeme bieten eine zentrale Steuerung und Überwachung aller Anlagenkomponenten. - IoT-Integration:
Internet of Things (IoT) Technologien ermöglichen die Vernetzung der Geräte und die Fernüberwachung sowie -steuerung der Prozesse. - Produktionsmanagement-Software:
Diese Softwarelösungen helfen bei der Planung und Verwaltung von Produktionsabläufen, indem sie Daten aus verschiedenen Quellen konsolidieren.
6. Automatisierte Farbwechsel
Für Betriebe, die häufige Farbwechsel durchführen müssen, bieten automatisierte Farbwechselsysteme erhebliche Vorteile.
- Schneller Farbwechsel:
Automatisierte Systeme reduzieren die Zeit, die für den Farbwechsel benötigt wird, was die Produktionsausfallzeiten minimiert. - Minimierung von Pulverabfall:
Durch den Einsatz von selbstreinigenden Sprühpistolen und Kabinen wird der Pulververbrauch optimiert.
7. Wartungsautomatisierung
Auch die Wartung von Anlagen kann automatisiert werden, um die Betriebszeiten zu maximieren und unvorhergesehene Ausfälle zu reduzieren.
- Vorausschauende Wartung:
Sensoren überwachen den Zustand der Anlagenkomponenten in Echtzeit und prognostizieren Wartungsbedarf, bevor Probleme auftreten. - Automatisierte Fehlerdiagnose:
Diagnose-Tools identifizieren Probleme und bieten Lösungsvorschläge, die die Wartungseffizienz erhöhen.
Vorteile der Automatisierung in der Pulverbeschichtung
- Erhöhte Produktivität:
Automatisierte Systeme ermöglichen eine höhere Produktionsrate bei gleichzeitig konsistenter Qualität. - Geringere Betriebskosten:
Durch die Optimierung des Materialverbrauchs und die Reduzierung des Arbeitsaufwands senken Automatisierungssysteme die Betriebskosten. - Verbesserte Qualität:
Gleichbleibende Beschichtungsqualität und reduzierte Fehlerraten durch präzise Steuerung und Überwachung. - Umweltfreundlichkeit:
Automatisierung reduziert den Pulverabfall und verbessert die Energieeffizienz der Anlagen.
Fazit
Automatisierungsoptionen in der Pulverbeschichtung bieten eine Vielzahl von Vorteilen und sind entscheidend für die Steigerung der Effizienz und Qualität in der Produktion. Die Integration von Robotik, fortschrittlicher Software und intelligenter Steuerung ermöglicht es Unternehmen, wettbewerbsfähig zu bleiben und gleichzeitig die Umweltbelastung zu reduzieren. Die Entscheidung für die richtige Kombination von Automatisierungstechnologien hängt von den spezifischen Anforderungen und Zielen des Unternehmens ab.
Automatisierungsvorteile

Automatisierung in der Pulverbeschichtungsindustrie bietet zahlreiche Vorteile, die sowohl die Effizienz als auch die Qualität der Produktion steigern können. Hier sind die wichtigsten Vorteile der Automatisierung erklärt:
1. Erhöhte Effizienz
- Höhere Produktionsraten:
Automatisierte Systeme können kontinuierlich ohne Unterbrechungen arbeiten, was zu höheren Durchsatzraten führt. Dies bedeutet, dass mehr Teile in kürzerer Zeit beschichtet werden können, was die Gesamtproduktivität steigert. - Schnellere Zykluszeiten:
Automatisierung reduziert die Bearbeitungszeit pro Werkstück erheblich, da Maschinen schneller und präziser arbeiten können als Menschen. - Minimierte Stillstandszeiten:
Automatisierte Wartung und vorausschauende Diagnose minimieren ungeplante Ausfallzeiten, was die Verfügbarkeit der Anlage erhöht.
2. Gleichbleibende Qualität
- Präzise Beschichtungsanwendung:
Automatisierte Sprühsysteme sorgen für eine gleichmäßige Schichtdicke und reduzieren menschliche Fehler, die zu Qualitätsabweichungen führen können. - Wiederholgenauigkeit:
Automatisierte Systeme wiederholen dieselben Bewegungen und Prozesse mit hoher Genauigkeit, was zu konsistenter Produktqualität führt, unabhängig von der Produktionsmenge. - Echtzeit-Qualitätskontrolle:
Durch den Einsatz von Sensoren und Kameras können automatisierte Systeme kontinuierlich die Qualität der Beschichtung überwachen und sofort Anpassungen vornehmen.
3. Reduzierte Betriebskosten
- Materialeinsparungen:
Automatisierung optimiert den Einsatz von Pulvermaterialien, wodurch Abfall reduziert und die Materialnutzung verbessert wird. - Geringere Arbeitskosten:
Der Bedarf an manueller Arbeit wird verringert, was die Personalkosten senkt. Mitarbeiter können in anderen Bereichen eingesetzt werden, wo menschliches Urteilsvermögen und Kreativität erforderlich sind. - Energieeffizienz:
Automatisierte Systeme sind oft energieeffizienter, da sie optimierte Prozesse und Technologien verwenden, um den Energieverbrauch zu minimieren.
4. Verbesserte Sicherheit
- Reduzierte Exposition gegenüber Gefahrenstoffen:
Automatisierung minimiert den direkten Kontakt der Mitarbeiter mit potenziell gefährlichen Chemikalien und Pulvern, was das Risiko von Gesundheitsproblemen reduziert. - Sicherheitsüberwachung:
Automatisierte Anlagen sind häufig mit Sicherheitssensoren ausgestattet, die Unfälle verhindern und im Notfall schnelle Reaktionen ermöglichen. - Ergonomische Vorteile:
Mitarbeiter müssen weniger körperlich anspruchsvolle Aufgaben erledigen, was das Risiko von arbeitsbedingten Verletzungen verringert.
5. Flexibilität und Anpassungsfähigkeit
- Schnelle Anpassung an Produktänderungen:
Automatisierte Systeme können schnell neu programmiert werden, um auf Änderungen im Produktdesign oder der Produktion umzustellen, was die Flexibilität erhöht. - Einfache Integration neuer Technologien:
Durch modulare Designs können neue Technologien oder Prozesse problemlos in bestehende Systeme integriert werden. - Vielfältige Anwendungsmöglichkeiten:
Automatisierung kann an eine Vielzahl von Werkstückgrößen, -formen und -materialien angepasst werden, was die Vielseitigkeit der Produktion erhöht.
6. Nachhaltigkeit und Umweltfreundlichkeit
- Reduzierung von Abfall und Emissionen:
Automatisierte Systeme optimieren den Materialverbrauch und reduzieren den Überspray, was zu weniger Abfall und geringeren Emissionen führt. - Ressourceneffizienz:
Durch die optimale Nutzung von Energie und Materialien tragen automatisierte Systeme zu nachhaltigeren Produktionsprozessen bei. - Verbesserte Umweltbilanz:
Unternehmen können ihre Umweltziele leichter erreichen und ihre ökologische Verantwortung wahrnehmen.
7. Daten- und Prozessoptimierung
- Datengesteuerte Entscheidungsfindung:
Automatisierte Systeme sammeln kontinuierlich Daten, die zur Analyse und Optimierung der Produktionsprozesse verwendet werden können. - Prozessoptimierung durch IoT:
Internet of Things (IoT) Technologien ermöglichen die Echtzeitüberwachung und -steuerung von Prozessen, was die Effizienz und Transparenz erhöht. - Vorausschauende Wartung:
Durch die Analyse von Maschinendaten können Probleme frühzeitig erkannt und behoben werden, bevor sie zu größeren Ausfällen führen.
Fazit
Die Automatisierung in der Pulverbeschichtung bietet zahlreiche Vorteile, die sowohl die Effizienz als auch die Qualität der Produktion erheblich steigern. Durch den Einsatz modernster Technologien können Unternehmen ihre Betriebskosten senken, die Produktsicherheit erhöhen und gleichzeitig ihre Umweltbilanz verbessern. Die Investition in Automatisierungslösungen zahlt sich langfristig durch höhere Produktivität, verbesserte Qualität und größere Flexibilität aus. Unternehmen, die Automatisierungstechnologien integrieren, positionieren sich besser im Wettbewerb und sind in der Lage, schneller auf Marktveränderungen zu reagieren.
Beispiele für Automatisierung

Hier sind einige konkrete Beispiele für Automatisierung in der Pulverbeschichtungsindustrie, die verdeutlichen, wie moderne Technologien den Beschichtungsprozess optimieren und verbessern können:
1. Robotergesteuerte Sprühapplikationen
- Automatisierte Spritzroboter:
Diese Roboterarme sind mit elektrostatischen Sprühpistolen ausgestattet und können komplexe Bewegungsmuster programmieren, um Teile unterschiedlicher Formen und Größen effizient zu beschichten. Durch die Robotersteuerung wird eine gleichmäßige Schichtdicke erreicht, und es gibt weniger Overspray.Beispiel: In der Automobilindustrie werden Karosserieteile oft mit robotergestützten Sprühsystemen beschichtet, um eine gleichmäßige und hochwertige Oberfläche zu gewährleisten. Ein Unternehmen wie ABB Robotics bietet Lösungen, die auf die spezifischen Anforderungen der Automobilindustrie zugeschnitten sind.
2. Automatische Fördersysteme
- Overhead-Kettenförderer:
Diese Systeme transportieren die Teile durch verschiedene Prozessschritte wie Reinigung, Beschichtung und Aushärtung. Sie ermöglichen einen kontinuierlichen Produktionsfluss und minimieren manuelle Eingriffe.Beispiel: Bei der Herstellung von Metallmöbeln werden Teile oft auf Förderbändern bewegt, die sie durch alle Beschichtungsphasen führen. Unternehmen wie Nordson bieten komplexe Fördersysteme an, die an verschiedene Produktionslayouts angepasst werden können.
3. Automatisierte Farbwechselsysteme
- Schnellwechselkabinen:
Diese Kabinen sind darauf ausgelegt, den Farbwechselprozess zu beschleunigen. Sie verfügen über automatische Reinigungszyklen und programmierbare Steuerungen, die den Farbwechsel effizienter machen.Beispiel: In der Fahrradindustrie, wo häufig Farbvarianten angeboten werden, nutzen Hersteller automatisierte Systeme, um den Farbwechsel schnell durchzuführen, ohne die Produktion zu verlangsamen. Systeme von Gema Switzerland bieten automatische Farbwechseltechnologien, die in der Branche weit verbreitet sind.
4. Intelligente Einbrennöfen
- Automatisierte Temperatur- und Zeitsteuerung:
Einbrennöfen sind mit Sensoren ausgestattet, die die Temperatur und den Durchsatz in Echtzeit überwachen und anpassen, um die optimale Aushärtung der Beschichtung zu gewährleisten.Beispiel: In der Elektronikindustrie, wo präzise Temperaturkontrollen entscheidend sind, verwenden Hersteller automatisierte Öfen, um die empfindlichen Komponenten richtig zu behandeln. Unternehmen wie Despatch Industries bieten Öfen an, die auf solche spezifischen Anforderungen abgestimmt sind.
5. Echtzeit-Qualitätskontrollsysteme
- Vision-Systeme für die Inspektion:
Kameras und Bildverarbeitungstechnologien erfassen die Beschichtungsqualität in Echtzeit, erkennen Fehler und ermöglichen sofortige Korrekturmaßnahmen.Beispiel: In der Luftfahrtindustrie, wo höchste Qualitätsstandards gelten, werden Vision-Systeme eingesetzt, um die Beschichtungen auf Flugzeugteilen zu überprüfen. Anbieter wie Cognex bieten fortschrittliche Bildverarbeitungslösungen an, die in diesen Anwendungen genutzt werden.
6. Datenanalyse und IoT-Integration
- IoT-gestützte Prozessüberwachung:
Sensoren an verschiedenen Stellen der Produktionslinie sammeln Daten, die zur Optimierung des gesamten Beschichtungsprozesses genutzt werden können. IoT-Plattformen ermöglichen eine zentrale Überwachung und Anpassung der Systeme in Echtzeit.Beispiel: Ein Hersteller von landwirtschaftlichen Maschinen nutzt IoT-Daten, um die Effizienz der Pulverbeschichtungsanlage zu verbessern und Wartungszyklen zu optimieren. Unternehmen wie Siemens bieten umfassende IoT-Lösungen an, die solche Anwendungen unterstützen.
7. Vorausschauende Wartung
- Condition Monitoring:
Automatisierte Überwachungssysteme analysieren kontinuierlich den Zustand von Anlagenkomponenten und prognostizieren Wartungsbedarf, bevor Ausfälle auftreten.Beispiel: Ein Hersteller von Haushaltsgeräten implementiert vorausschauende Wartung, um die Lebensdauer seiner Beschichtungsanlagen zu verlängern und die Verfügbarkeit zu maximieren. Lösungen von GE Digital bieten solche Condition-Monitoring-Tools an.
8. Automatisierte Reinigungssysteme
- Selbstreinigende Kabinen:
Diese Kabinen verfügen über automatische Reinigungszyklen, die das Entfernen von Pulverrückständen und die Vorbereitung für den nächsten Durchgang erleichtern.Beispiel: In der Herstellung von Baukomponenten, die unterschiedliche Beschichtungen erfordern, helfen selbstreinigende Systeme, die Wechselzeiten zwischen den verschiedenen Pulverlacken zu verkürzen. Systeme von Wagner bieten effiziente Reinigungsoptionen, die in solchen Anwendungen zum Einsatz kommen.
Fazit
Automatisierung in der Pulverbeschichtungsindustrie bietet vielfältige Möglichkeiten, die Produktion zu optimieren und gleichzeitig die Qualität zu steigern. Durch den Einsatz von robotergesteuerten Sprühsystemen, automatisierten Fördersystemen, intelligenten Einbrennöfen und fortschrittlichen Überwachungs- und Wartungstechnologien können Unternehmen ihre Effizienz erhöhen und ihre Wettbewerbsfähigkeit verbessern. Die Investition in Automatisierungstechnologien ermöglicht es Unternehmen, sich schnell an Marktveränderungen anzupassen und gleichzeitig ihre Produktionskosten zu senken.
Komponenten einer Komplette Pulverbeschichtungsanlage
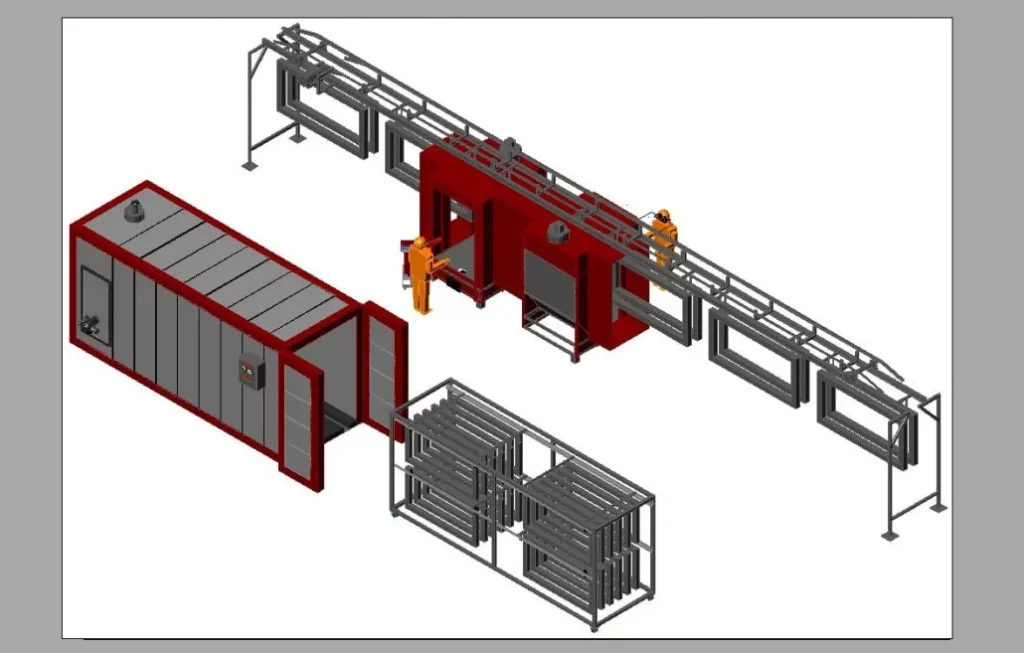
Eine komplette Pulverbeschichtungsanlage besteht aus mehreren wesentlichen Komponenten, die zusammenarbeiten, um eine effiziente und qualitativ hochwertige Beschichtung von Werkstücken zu gewährleisten. Hier sind die Hauptkomponenten einer solchen Anlage und ihre Funktionen:
1. Vorbehandlungssystem
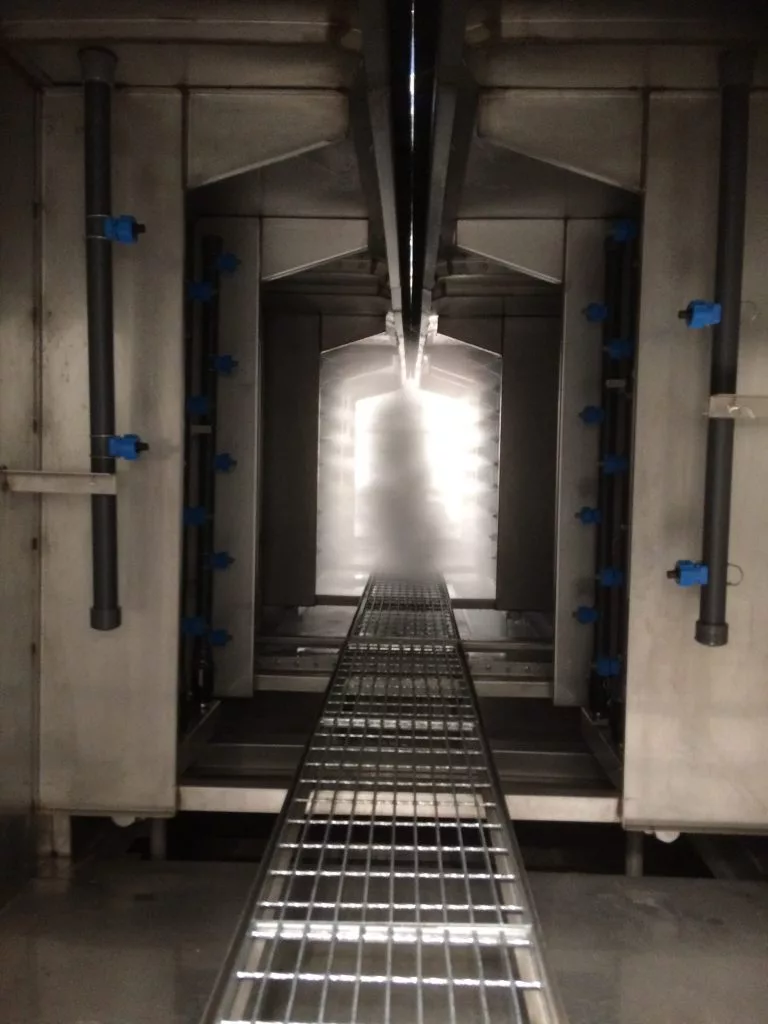
Die Vorbehandlung ist ein entscheidender Schritt, um sicherzustellen, dass die Oberfläche des Werkstücks sauber und bereit für die Beschichtung ist. Die Vorbehandlung verbessert die Haftung der Pulverbeschichtung und erhöht die Korrosionsbeständigkeit.
- Reinigungsstationen: Entfernen Öl, Fett, Staub und andere Verunreinigungen von der Oberfläche des Werkstücks.
- Phosphatier- oder Chromatierstationen: Bilden eine Schutzschicht, die die Haftung verbessert und die Korrosionsbeständigkeit erhöht.
- Spül- und Trocknungsstationen: Stellen sicher, dass das Werkstück frei von chemischen Rückständen und trocken ist, bevor es zur Beschichtung weitergeleitet wird.
2. Pulverkabinen
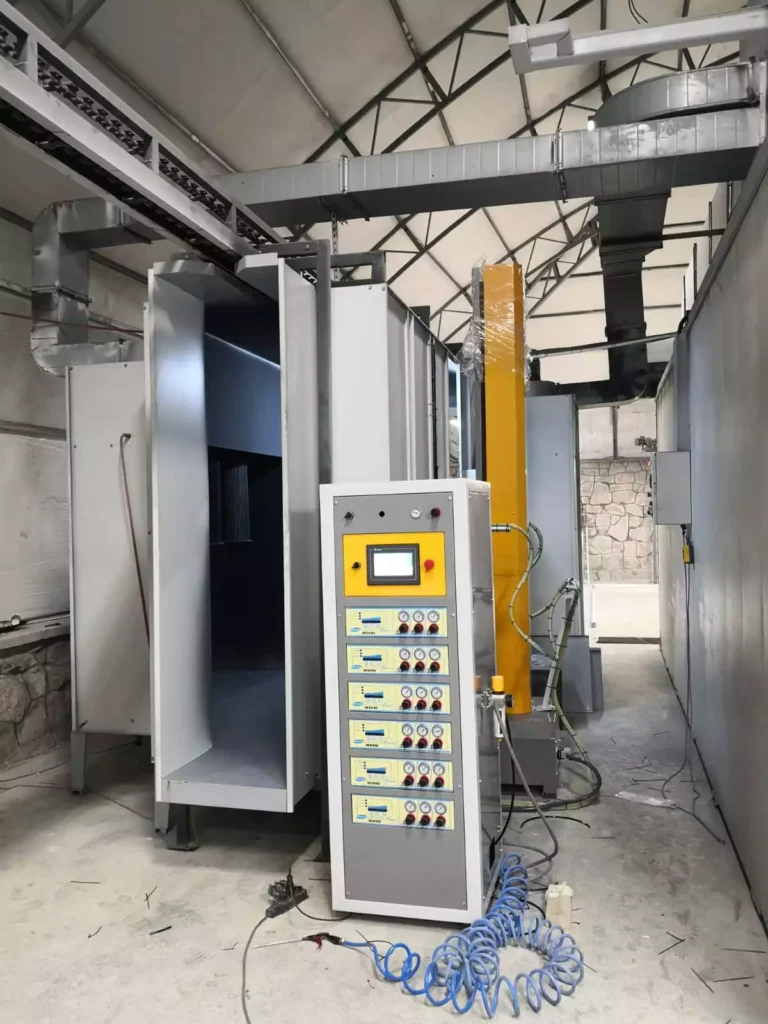
Die Pulverkabine ist der Bereich, in dem das Pulver elektrostatisch auf die Werkstücke aufgetragen wird. Sie ist so konzipiert, dass sie eine saubere und kontrollierte Umgebung bietet, um überschüssiges Pulver effizient zurückzugewinnen.
- Offene Kabinen: Geeignet für kleinere, manuelle Anwendungen, wo der Bediener direkten Zugang benötigt.
- Geschlossene Kabinen: Bieten eine kontrollierte Umgebung und sind effizienter bei der Kontrolle und Rückgewinnung von Overspray.
- Selbstreinigende Kabinen: Diese Kabinen verfügen über automatische Reinigungssysteme, die den Farbwechsel und die Wartung erleichtern.
3. Pulverauftragsgeräte

Diese Geräte sind für die eigentliche Anwendung des Pulvers auf die Werkstücke verantwortlich und bestehen aus verschiedenen Komponenten, die den Pulverauftrag optimieren.
- Elektrostatische Sprühpistolen: Laden die Pulverpartikel elektrostatisch auf, damit sie gleichmäßig auf der Werkstückoberfläche haften.
- Pulverförderer: Transportieren das Pulver von den Vorratsbehältern zur Sprühpistole und sorgen für eine gleichmäßige Pulverzufuhr.
- Steuerungseinheiten: Erlauben die Anpassung der Auftragsparameter wie Spannung, Pulverfluss und Sprühzeit.
4. Fördersysteme

Fördersysteme transportieren die Werkstücke durch die verschiedenen Stationen der Beschichtungsanlage, von der Vorbehandlung bis zur Aushärtung.
- Kettenförderer: Bieten kontinuierliche Bewegung und sind ideal für die Massenproduktion.
- Schienen- und Rollensysteme: Ermöglichen Flexibilität bei der Anordnung der Produktionslinie.
- Pufferzonen: Bereiche, in denen Werkstücke zwischengelagert werden können, um den Produktionsfluss zu optimieren.
5. Einbrennöfen
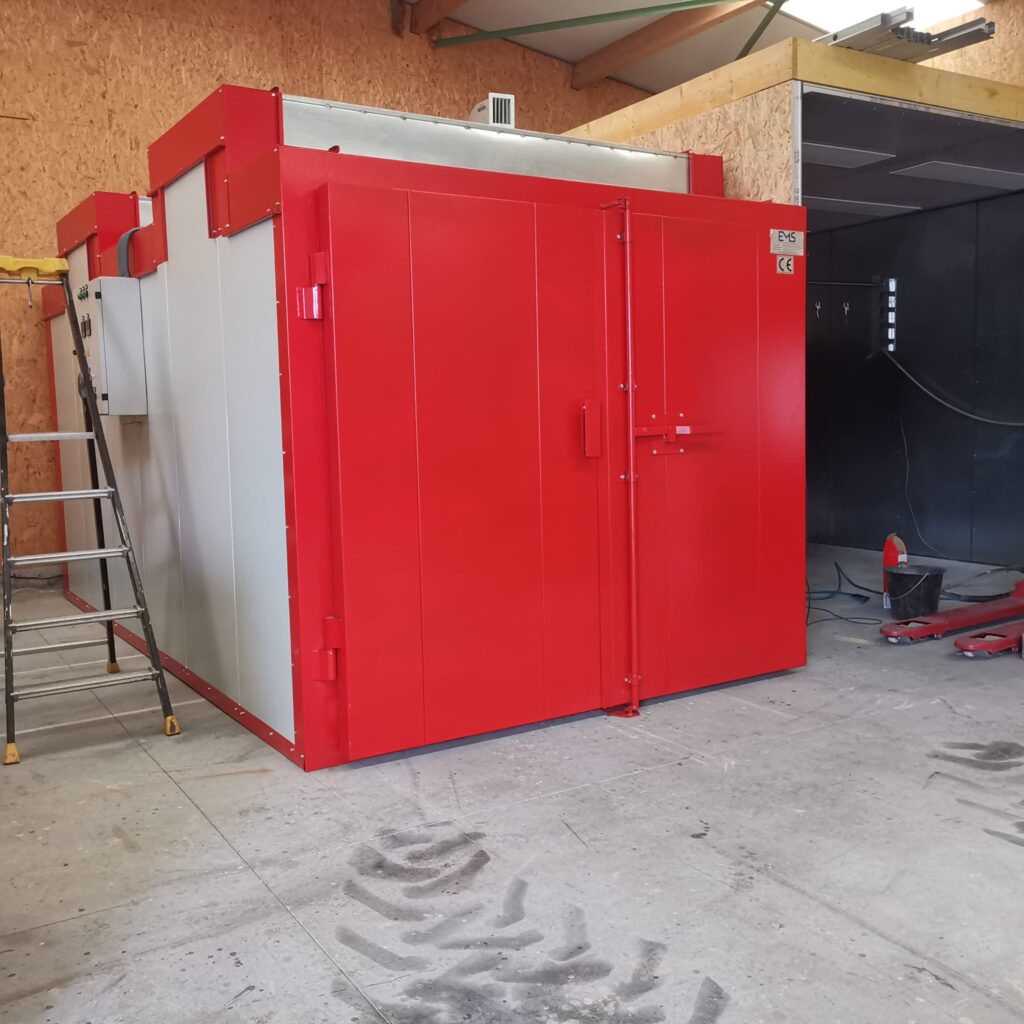
Einbrennöfen sind entscheidend für die Aushärtung der Pulverbeschichtung, da sie die erforderliche Wärme bereitstellen, um das Pulver zu schmelzen und eine dauerhafte Oberfläche zu schaffen.
- Chargenöfen: Ideal für kleinere Produktionen mit variablen Chargengrößen; sie bieten Flexibilität und können verschiedene Teile gleichzeitig verarbeiten.
- Durchlauföfen: Entwickelt für kontinuierliche Produktionslinien mit hohen Durchsatzraten. Teile werden auf einem Förderband durch den Ofen transportiert.
- Konvektions- und Infrarotöfen: Verschiedene Technologien bieten spezifische Vorteile in Bezug auf Aufheizgeschwindigkeit und Energieeffizienz.
6. Rückgewinnungs- und Recycling-Systeme
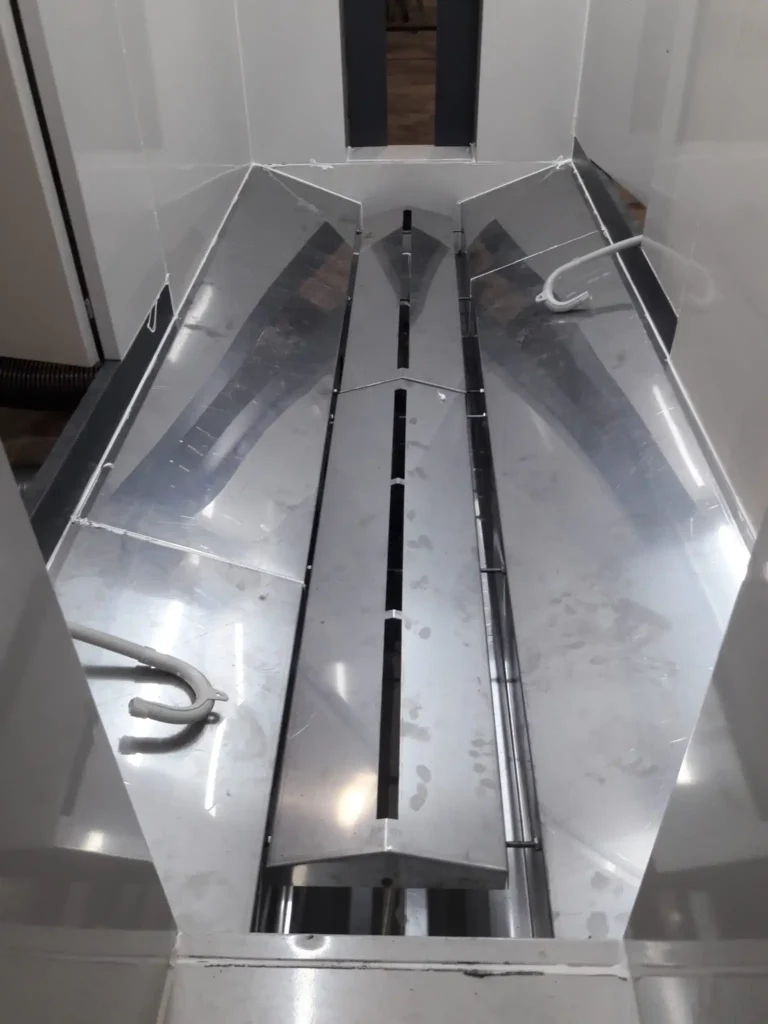
Diese Systeme sind darauf ausgelegt, überschüssiges Pulver aufzufangen und wiederzuverwenden, um Abfall zu minimieren und die Effizienz zu maximieren.
- Zyklonabscheider: Trennen überschüssiges Pulver aus der Luft und führen es zurück in den Beschichtungsprozess.
- Filtersysteme: Entfernen Feinstaub aus der Luft und stellen sicher, dass nur saubere Luft in die Umgebung abgegeben wird.
- Siebsysteme: Stellen sicher, dass nur qualitativ hochwertiges Pulver erneut verwendet wird, indem sie Verunreinigungen entfernen.
7. Steuerungs- und Überwachungssysteme
Moderne Steuerungssysteme ermöglichen die Überwachung und Anpassung aller Aspekte des Beschichtungsprozesses in Echtzeit.
- Prozessleitsysteme (PLS): Überwachen und steuern den gesamten Produktionsablauf und bieten Echtzeit-Daten zur Optimierung der Prozesse.
- Benutzeroberflächen: Intuitive Bedienpanels ermöglichen eine einfache Steuerung und Anpassung der Systemeinstellungen.
- Datenanalyse-Tools: Erfassen und analysieren Daten zur Prozessoptimierung und Fehlererkennung.
8. Kühlzonen
Nach dem Aushärtungsprozess müssen die Werkstücke auf Raumtemperatur abgekühlt werden, bevor sie weiterverarbeitet oder verpackt werden können.
- Luftkühlungssysteme: Nutzen Luftzirkulation, um die Werkstücke effizient abzukühlen.
- Wasserkühlungssysteme: In speziellen Anwendungen, wo schnelle Abkühlung erforderlich ist, können Wasserkühlungssysteme eingesetzt werden.
9. Materialhandling-Systeme
Diese Systeme unterstützen das Be- und Entladen von Werkstücken und die Bewegung innerhalb der Anlage.
- Robotiksysteme: Automatisierte Roboterarme, die Werkstücke präzise positionieren und handhaben.
- Hubsysteme: Unterstützen beim Transport schwerer Werkstücke innerhalb der Anlage.
10. Wartungseinrichtungen
Regelmäßige Wartung ist entscheidend, um die Effizienz und Lebensdauer der Anlage zu gewährleisten.
- Integrierte Wartungstools: Sensoren und Software zur vorausschauenden Wartung, die den Zustand der Anlage überwachen und Wartungsbedarf identifizieren.
- Zugängliche Wartungsbereiche: Einfache Zugänglichkeit für regelmäßige Inspektionen und Reparaturen.
Fazit
Eine komplette Pulverbeschichtungsanlage besteht aus vielen Komponenten, die zusammenarbeiten, um eine effiziente, qualitativ hochwertige und umweltfreundliche Beschichtung zu gewährleisten. Jede Komponente spielt eine entscheidende Rolle im Beschichtungsprozess, von der Vorbereitung der Werkstücke bis zur Aushärtung der Beschichtung. Die Wahl der richtigen Technologien und die Integration von Automatisierungslösungen können den Betrieb optimieren und die Produktionsziele eines Unternehmens effektiv unterstützen.
Anlagengröße

Die Größe von Pulverbeschichtungsanlagen kann je nach den spezifischen Anforderungen eines Unternehmens stark variieren. Die Anlagengröße hängt von mehreren Faktoren ab, darunter die Art und Größe der zu beschichtenden Werkstücke, das Produktionsvolumen und die verfügbaren räumlichen Gegebenheiten. Hier sind einige wichtige Überlegungen und Optionen zur Variation der Anlagengröße:
Faktoren, die die Anlagengröße beeinflussen
- Art der zu beschichtenden Werkstücke
- Kleinere Teile: Bei der Beschichtung von kleineren Teilen, wie z. B. Elektrokomponenten oder kleinen Metallteilen, können kompaktere Anlagen eingesetzt werden.
- Große Werkstücke: Für größere Teile, wie Automobilkarosserien oder große Maschinenteile, sind größere Anlagen mit geräumigen Kabinen und Öfen erforderlich.
- Produktionsvolumen
- Kleinserienproduktion: Unternehmen, die kleinere Produktionsvolumen handhaben, können mit einfacheren und kleineren Anlagen auskommen.
- Massenproduktion: Für hohe Produktionsvolumen sind größere und komplexere Anlagen notwendig, die einen kontinuierlichen Betrieb ermöglichen.
- Verfügbare Fläche
- Kompakte Lösungen: In begrenzten Räumlichkeiten können platzsparende Designs und integrierte Systeme genutzt werden, um den verfügbaren Platz optimal zu nutzen.
- Großflächige Anlagen: In größeren Einrichtungen kann eine weitläufige Anordnung von Vorbehandlung, Beschichtung und Aushärtung erfolgen, um einen reibungslosen Produktionsablauf zu gewährleisten.
- Prozessanforderungen
- Vielseitigkeit: Anlagen, die verschiedene Beschichtungsarten und Materialien verarbeiten müssen, erfordern möglicherweise eine modulare Struktur, die Anpassungen erlaubt.
- Spezialanforderungen: Bestimmte Anwendungen, wie z. B. die Beschichtung von hitzeempfindlichen Materialien, erfordern spezifische Anpassungen der Anlagengröße und -konfiguration.
Optionen zur Variation der Anlagengröße
1. Modulare Anlagen
Modulare Anlagen sind flexibel und können an unterschiedliche Produktionsanforderungen angepasst werden. Sie bestehen aus separaten Modulen, die nach Bedarf hinzugefügt oder entfernt werden können.
- Vorteile:
- Flexibilität: Einfaches Anpassen und Erweitern der Anlage, um auf wechselnde Produktionsanforderungen zu reagieren.
- Kosteneffizienz: Investitionen können nach und nach getätigt werden, indem nur die notwendigen Module erworben werden.
- Einfache Wartung: Einzelne Module können leicht gewartet oder ausgetauscht werden, ohne den gesamten Betrieb zu unterbrechen.
- Beispiele:
- Modulare Kabinen: Erlauben die Anpassung der Kabinengröße je nach Werkstückgröße.
- Erweiterbare Fördersysteme: Zusätzliche Förderstrecken können hinzugefügt werden, um den Produktionsfluss zu erweitern.
2. Kompakte Anlagen
Kompakte Anlagen sind ideal für Unternehmen mit begrenztem Platzangebot oder für kleinere Produktionsvolumen.
- Vorteile:
- Platzsparend: Effektive Nutzung des verfügbaren Raums.
- Geringere Investitionskosten: Reduzierte Anfangsinvestitionen durch den kleineren Maßstab der Anlage.
- Schnellere Installation: Einfachere und schnellere Implementierung.
- Beispiele:
- Mini-Kabinen: Kleinere Beschichtungskabinen für spezialisierte Anwendungen.
- Integrierte Systeme: Anlagen, die Vorbehandlung, Beschichtung und Aushärtung in einem kompakten Layout vereinen.
3. Großflächige Anlagen
Für Unternehmen mit hohen Produktionsanforderungen oder großen Werkstücken sind großflächige Anlagen notwendig.
- Vorteile:
- Hohe Kapazität: Eignen sich für die Massenproduktion und den gleichzeitigen Betrieb mehrerer Linien.
- Vielseitigkeit: Möglichkeit, mehrere Prozesse gleichzeitig durchzuführen.
- Effizienz: Optimierte Produktionsabläufe durch die großzügige Gestaltung der Anlage.
- Beispiele:
- Mehrere Kabinen und Öfen: Separate Bereiche für unterschiedliche Farben oder Materialien.
- Erweiterte Fördersysteme: Lange Förderstrecken für den Transport großer oder zahlreicher Teile.
Planungsüberlegungen bei der Anlagengrößenauswahl
- Zukunftsprognosen
- Marktentwicklung: Berücksichtigen Sie mögliche Expansionen oder Veränderungen in der Nachfrage.
- Technologische Fortschritte: Planen Sie für zukünftige Anpassungen oder Upgrades der Anlage.
- Kostenüberlegungen
- Anfangsinvestition vs. Betriebskosten: Wägen Sie die Anfangsinvestitionen gegen die langfristigen Betriebskosten ab.
- Finanzielle Flexibilität: Planen Sie die Finanzierung der Anlage im Einklang mit den finanziellen Möglichkeiten und Zielen des Unternehmens.
- Integration und Kompatibilität
- Bestehende Infrastruktur: Überprüfen Sie die Kompatibilität der neuen Anlage mit bestehenden Systemen und Einrichtungen.
- Erweiterungsmöglichkeiten: Planen Sie die Integration zukünftiger Erweiterungen oder Module.
- Umwelt- und Sicherheitsstandards
- Regulierungen: Stellen Sie sicher, dass die Anlage alle relevanten Umwelt- und Sicherheitsstandards erfüllt.
- Nachhaltigkeit: Berücksichtigen Sie umweltfreundliche Technologien und Praktiken bei der Planung und dem Betrieb der Anlage.
Fazit
Die Größe einer Pulverbeschichtungsanlage kann an die spezifischen Bedürfnisse und Anforderungen eines Unternehmens angepasst werden. Durch die Auswahl der richtigen Anlagengröße und -konfiguration können Unternehmen ihre Produktionsziele effizient erreichen, die Qualität ihrer Produkte verbessern und die Betriebskosten optimieren. Ob modular, kompakt oder großflächig, jede Anlagengröße hat ihre eigenen Vorteile und Herausforderungen, die sorgfältig abgewogen werden müssen, um die besten Ergebnisse zu erzielen.
Benötigte Mitarbeiterzahl
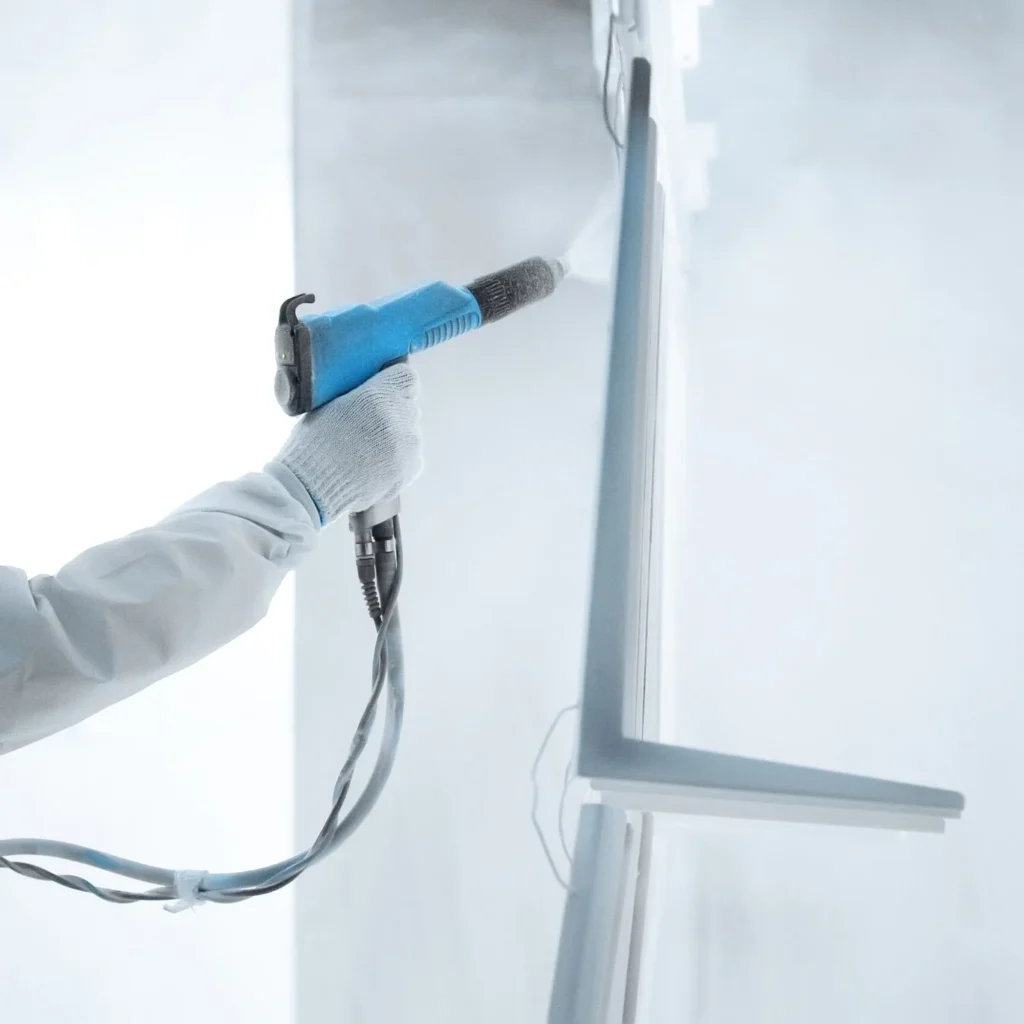
Die Anzahl der benötigten Mitarbeiter für den Betrieb einer Pulverbeschichtungsanlage hängt von mehreren Faktoren ab, darunter die Größe und Automatisierung der Anlage, das Produktionsvolumen, die Art der zu beschichtenden Werkstücke und die spezifischen betrieblichen Anforderungen. Hier sind einige Überlegungen, um die optimale Mitarbeiterzahl für den Betrieb einer Pulverbeschichtungsanlage zu bestimmen:
1. Faktoren, die die Mitarbeiterzahl beeinflussen
a. Größe der Anlage
- Kleine Anlagen:
- Typischerweise weniger Mitarbeiter erforderlich.
- Häufig eine Mischung aus manuellen und halbautomatisierten Prozessen.
- Große Anlagen:
- Mehr Mitarbeiter erforderlich, insbesondere bei einer hohen Produktionskapazität.
- Automatisierte Systeme können jedoch den Bedarf an Personal verringern.
b. Automatisierungsgrad
- Hochautomatisierte Anlagen:
- Reduzierter Bedarf an manueller Arbeit.
- Erfordern jedoch technisches Personal für die Überwachung, Wartung und Programmierung der Anlagen.
- Manuelle oder halbautomatisierte Anlagen:
- Höherer Personalbedarf für die Bedienung und Überwachung der Anlagen.
c. Produktionsvolumen
- Niedriges Produktionsvolumen:
- Geringerer Personalbedarf.
- Mehr Flexibilität bei der Planung von Schichten.
- Hohes Produktionsvolumen:
- Mehr Mitarbeiter erforderlich, um den Produktionsfluss aufrechtzuerhalten.
- Möglicherweise mehrere Schichten zur Maximierung der Betriebszeit.
d. Werkstücktypen
- Komplexe oder große Werkstücke:
- Erfordern möglicherweise mehr Personal für die Handhabung und Inspektion.
- Spezialisierte Mitarbeiter für die Anpassung der Beschichtungsparameter.
- Kleine oder standardisierte Teile:
- Weniger Personal für die Handhabung erforderlich.
- Prozessabläufe sind oft einfacher und standardisiert.
2. Typische Rollen in einer Pulverbeschichtungsanlage
a. Produktionsmitarbeiter
- Bediener der Beschichtungsanlagen:
- Verantwortlich für das Auftragen der Pulverbeschichtung.
- Überwachung der Qualität und Sicherstellung der richtigen Parameter.
- Vorbehandlungsmitarbeiter:
- Durchführung von Reinigungs- und Vorbehandlungsprozessen.
- Sicherstellung, dass die Werkstücke ordnungsgemäß vorbereitet sind.
b. Technisches Personal
- Wartungstechniker:
- Regelmäßige Wartung und Reparatur der Anlagen.
- Überwachung der Systemleistung und Durchführung von Fehlerbehebungen.
- Automatisierungs- und Steuerungstechniker:
- Programmierung und Überwachung automatisierter Systeme.
- Anpassung der Steuerungsparameter und Optimierung der Prozesse.
c. Qualitätssicherung
- Qualitätsinspektoren:
- Durchführung von Qualitätskontrollen zur Sicherstellung der Einhaltung von Standards.
- Verwendung von Messgeräten zur Überprüfung der Schichtdicke und Oberflächenqualität.
- Prozessoptimierer:
- Analyse von Produktionsdaten zur Verbesserung der Effizienz und Qualität.
- Implementierung von Verbesserungsmaßnahmen.
d. Management und Verwaltung
- Produktionsleiter:
- Überwachung der gesamten Produktionslinie.
- Koordination der Mitarbeiter und Sicherstellung der Zielerreichung.
- Logistik- und Materialplaner:
- Verwaltung der Materialflüsse und Bestände.
- Planung der Produktion auf Basis von Nachfrage und Kapazität.
3. Beispiel einer Mitarbeiterverteilung
Hier ist ein Beispiel für die Mitarbeiterverteilung in einer mittelgroßen, teilautomatisierten Pulverbeschichtungsanlage:
Rolle | Anzahl der Mitarbeiter | Beschreibung |
---|---|---|
Bediener der Vorbehandlung | 2-3 | Verantwortlich für Reinigung und Vorbereitung der Werkstücke. |
Pulverbeschichtungsbediener | 3-4 | Durchführung des Beschichtungsprozesses. |
Wartungstechniker | 1-2 | Wartung und Reparatur der Anlagen. |
Automatisierungstechniker | 1-2 | Überwachung der automatisierten Systeme und Prozesssteuerung. |
Qualitätsinspektoren | 1-2 | Überprüfung der Qualität der beschichteten Teile. |
Produktionsleiter | 1 | Leitung der Produktion und Koordination der Schichten. |
Logistik- und Materialplaner | 1 | Verwaltung der Materialbestände und Produktionsplanung. |
4. Optimierung der Mitarbeiterzahl
Um die Mitarbeiterzahl effizient zu nutzen, können Unternehmen folgende Strategien in Betracht ziehen:
- Schulung und Weiterbildung: Regelmäßige Schulungen, um die Qualifikation der Mitarbeiter zu verbessern und sie auf mehrere Aufgaben vorzubereiten.
- Einsatz von Zeitarbeitern: Flexible Personalplanung durch den Einsatz von Zeitarbeitskräften, um bei Bedarf Spitzenbelastungen abzufangen.
- Prozessoptimierung: Einsatz von Lean-Management-Prinzipien, um Prozesse zu optimieren und den Personalbedarf zu reduzieren.
- Investition in Automatisierung: Einsatz von Automatisierungstechnologien zur Reduzierung des manuellen Arbeitsaufwands und Verbesserung der Effizienz.
Fazit
Die optimale Anzahl der Mitarbeiter in einer Pulverbeschichtungsanlage hängt von vielen Faktoren ab, darunter die Größe der Anlage, der Automatisierungsgrad und das Produktionsvolumen. Durch den Einsatz von Automatisierung, Schulung und Prozessoptimierung können Unternehmen ihre Personalkosten minimieren und gleichzeitig die Effizienz und Qualität ihrer Produktion maximieren. Eine sorgfältige Planung und Anpassung der Personalressourcen ist entscheidend, um den Erfolg der Anlage zu gewährleisten.
Ein Pulverofen ist eine essentielle Komponente in der Pulverbeschichtung, einer modernen Technik zur Oberflächenveredelung, die in vielen Branchen von der Automobilindustrie bis zur Möbelherstellung weit verbreitet ist. Pulverbeschichtung nutzt elektrostatisch aufgeladenes Pulver, das auf ein Werkstück gesprüht und anschließend in einem Pulverofen erhitzt wird, um eine harte, widerstandsfähige und gleichmäßige Beschichtung zu erzeugen.
In diesem umfassenden Text wird auf die Funktionsweise und verschiedenen Arten von Pulveröfen eingegangen. Zu den behandelten Themen gehören die grundlegende Technologie hinter Pulveröfen, der Stromverbrauch, Kammeröfen, Pulveröfen mit Schienen, Pulveröfen mit Schienen im Boden und Pulveröfen mit Trennwänden. Jede dieser Variationen bietet unterschiedliche Vorteile und Anwendungen für bestimmte industrielle Prozesse.
Pulverofen: Grundlegendes Verständnis
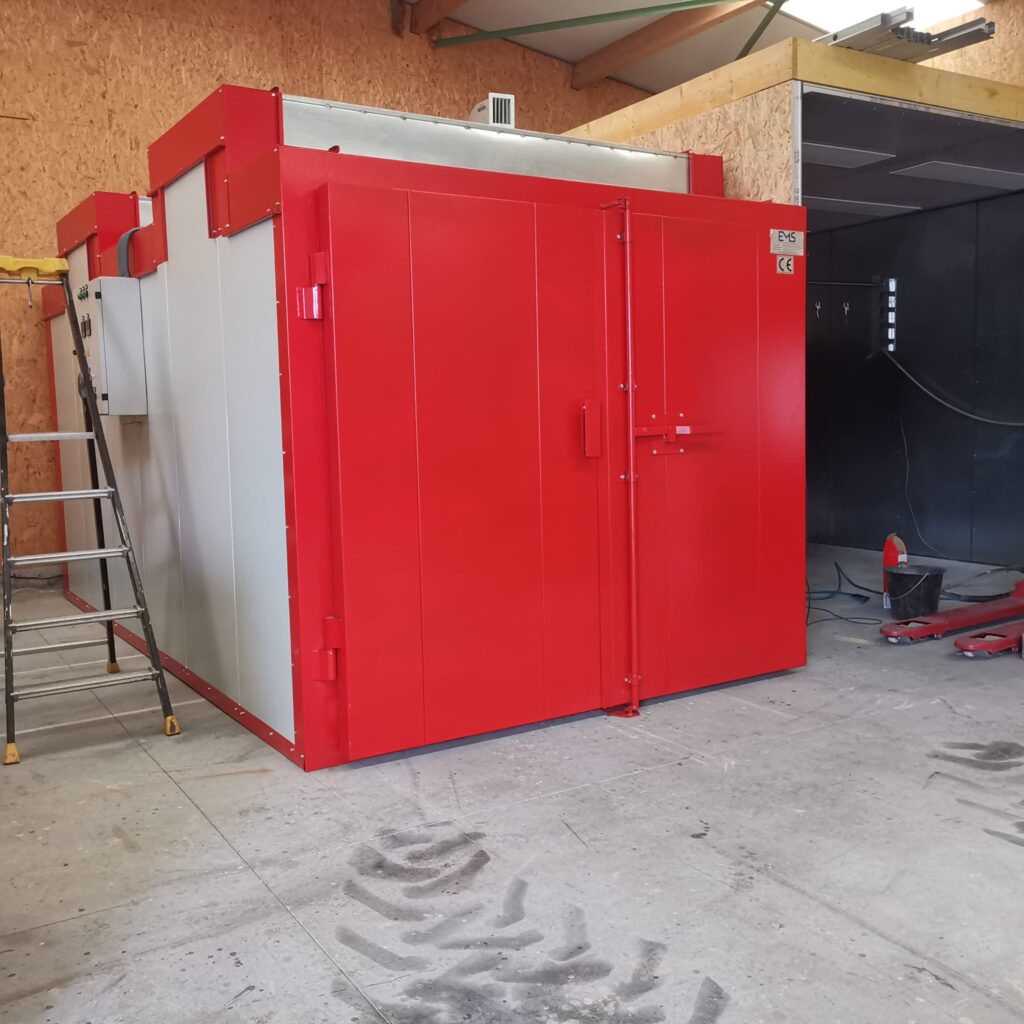
Ein Pulverofen ist speziell dafür entwickelt, Werkstücke, die mit Pulverbeschichtungen versehen wurden, auf hohe Temperaturen zu erhitzen, um das Pulver zu schmelzen und zu einer widerstandsfähigen Beschichtung zu vernetzen. Während dieses Vorgangs wird das Pulver in eine homogene, schützende und dekorative Schicht umgewandelt, die gegen Korrosion, Kratzer und Witterungseinflüsse beständig ist.
Pulveröfen werden in zahlreichen Industrien eingesetzt, darunter:
- Automobilindustrie: für Felgen, Fahrgestelle und Karosserieteile.
- Möbelherstellung: für Metallmöbel, Regale und Outdoor-Möbel.
- Bauindustrie: für Geländer, Fassaden, Fensterrahmen und Türen.
Die Hauptkomponenten eines Pulverofens umfassen ein Heizsystem, eine Lüftung, eine Steuerungseinheit und ein Fördersystem. Diese Öfen arbeiten in der Regel bei Temperaturen zwischen 150°C und 200°C, je nach Art des Pulvers und des zu beschichtenden Materials.
1.1. Funktionsweise eines Pulverofens
Die Funktionsweise eines Pulverofens lässt sich in mehrere Schritte unterteilen:
- Beschichtung des Werkstücks: Zunächst wird das Werkstück mit einem elektrostatisch aufgeladenen Pulverlack in einer Pulverbeschichtungsanlage beschichtet.
- Erhitzung im Ofen: Das beschichtete Werkstück wird dann in den Pulverofen überführt, wo es auf eine festgelegte Temperatur erhitzt wird. Bei dieser Temperatur schmilzt das Pulver und bildet eine glatte, gleichmäßige Beschichtung.
- Aushärtung: Sobald das Pulver geschmolzen ist, geht es in einen Aushärtungsprozess über, bei dem chemische Bindungen entstehen, die für die Haltbarkeit und Beständigkeit der Beschichtung sorgen. Dieser Prozess dauert in der Regel 10 bis 30 Minuten.
Pulverofen Strom
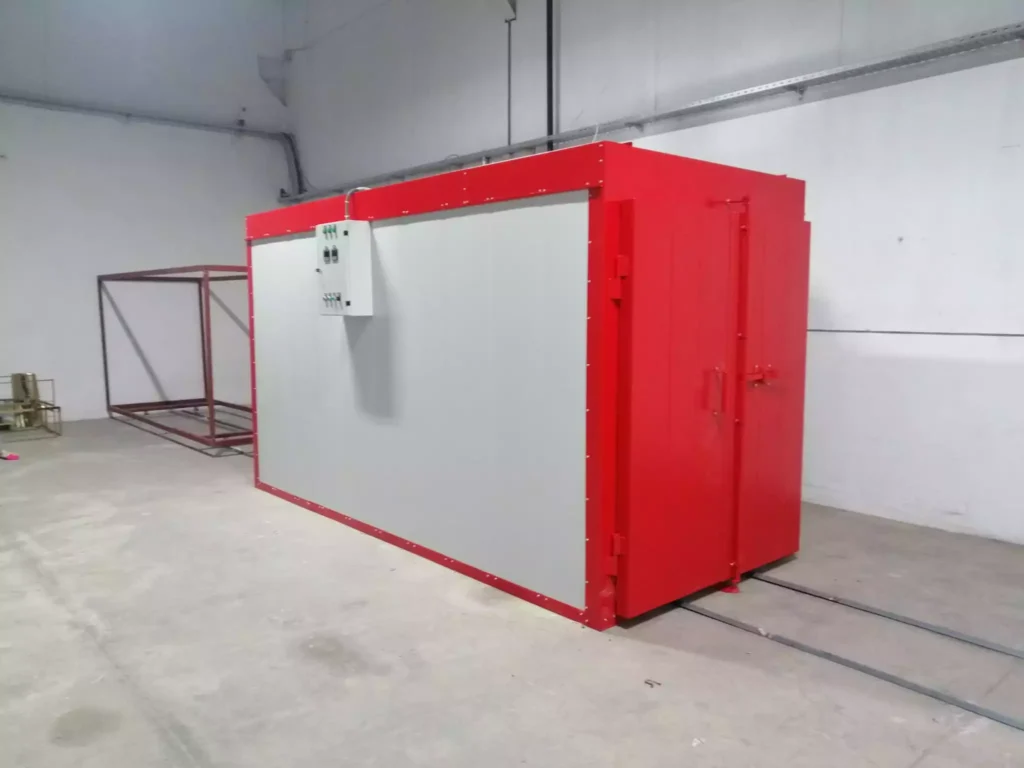
Ein entscheidender Aspekt bei der Auswahl und dem Betrieb eines Pulverofens ist der Stromverbrauch. Der Stromverbrauch eines Pulverofens kann erheblich sein, insbesondere in großen industriellen Anwendungen. Deshalb ist es wichtig, die Energieeffizienz eines Pulverofens zu optimieren, um sowohl Betriebskosten als auch Umweltbelastungen zu reduzieren.
2.1. Faktoren, die den Stromverbrauch beeinflussen
Der Stromverbrauch eines Pulverofens hängt von mehreren Faktoren ab, darunter:
- Ofengröße: Größere Öfen benötigen mehr Energie, um den gesamten Innenraum gleichmäßig auf die erforderliche Temperatur zu bringen. Industrielle Anlagen mit großflächigen Werkstücken erfordern in der Regel mehr Strom als kleinere, für Einzelteile oder kleine Serien ausgelegte Öfen.
- Material des Werkstücks: Dickere oder massivere Werkstücke benötigen mehr Energie, um gleichmäßig auf die richtige Temperatur erhitzt zu werden.
- Isolierung des Ofens: Eine gute Isolierung reduziert den Wärmeverlust und kann den Stromverbrauch erheblich senken. Modernere Öfen verfügen oft über verbesserte Isolierungstechnologien, die Energie sparen.
- Heizungstyp: Öfen können mit verschiedenen Heiztechnologien betrieben werden, darunter Elektroheizungen und Gasheizungen. Elektrische Pulveröfen sind in der Anschaffung oft günstiger, aber der Stromverbrauch kann höher sein als bei gasbetriebenen Öfen.
2.2. Tipps zur Senkung des Stromverbrauchs
Hier sind einige Möglichkeiten, um den Stromverbrauch von Pulveröfen zu senken:
- Optimierung der Auslastung: Ein Ofen sollte möglichst vollständig beladen werden, um die maximale Effizienz zu erreichen. Wenn der Ofen nur teilweise beladen wird, geht viel Energie verloren.
- Isolierungsverbesserungen: Investitionen in eine bessere Ofenisolierung können die Energieeffizienz deutlich steigern, da weniger Wärme verloren geht.
- Regelmäßige Wartung: Eine regelmäßige Wartung stellt sicher, dass der Ofen in optimalem Zustand bleibt und nicht mehr Energie als nötig verbraucht.
- Temperaturmanagement: Einige moderne Pulveröfen sind mit intelligenten Steuerungssystemen ausgestattet, die die Temperatur dynamisch anpassen und so den Stromverbrauch optimieren.
Kammerofen
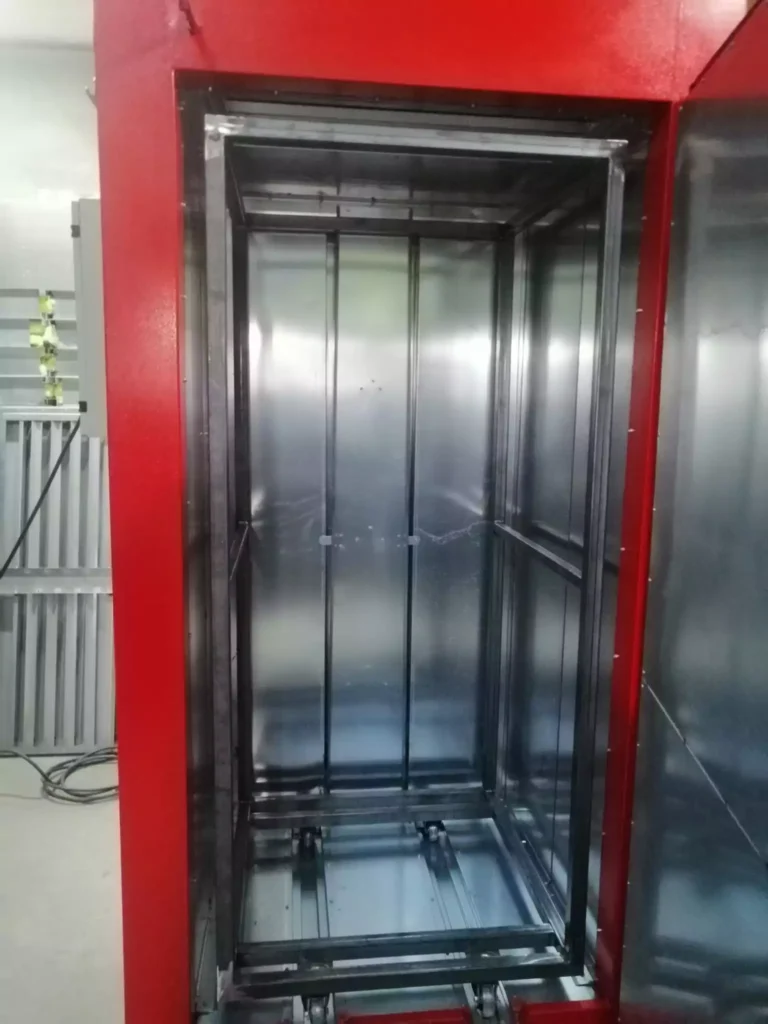
Ein Kammerofen ist eine der gebräuchlichsten Arten von Pulveröfen und zeichnet sich durch seine geschlossene Bauweise aus, bei der das Werkstück in einer Kammer erhitzt wird. Kammeröfen bieten eine hervorragende Temperaturkontrolle und eignen sich ideal für den Aushärtungsprozess in der Pulverbeschichtung.
3.1. Merkmale eines Kammerofens
Kammeröfen bestehen aus einer oder mehreren Kammern, in denen die Werkstücke platziert werden, bevor sie erhitzt werden. Diese Art von Ofen bietet mehrere Vorteile:
- Temperaturstabilität: Durch die geschlossene Kammer wird die Wärme gleichmäßig verteilt, was zu einer gleichmäßigen Aushärtung führt. Die Temperatur kann genau gesteuert werden, was für die Konsistenz und Qualität der Beschichtung entscheidend ist.
- Vielseitigkeit: Kammeröfen sind in verschiedenen Größen erhältlich und eignen sich für eine Vielzahl von Werkstücken, von kleinen Teilen bis hin zu großen, sperrigen Objekten.
- Effiziente Nutzung des Raums: Da die Werkstücke in einer Kammer platziert werden, können Kammeröfen oft effizienter arbeiten, insbesondere wenn sie voll beladen sind.
3.2. Anwendungen des Kammerofens
Kammeröfen finden in vielen Branchen Anwendung, darunter:
- Automobilsektor: für die Beschichtung von Fahrzeugteilen wie Felgen, Fahrgestellen und Karosserieteilen.
- Möbelindustrie: für die Beschichtung von Metallrahmen und -teilen in der Möbelherstellung.
- Elektronik- und Maschinenbau: für die Beschichtung von elektrischen und mechanischen Komponenten.
3.3. Vorteile und Herausforderungen eines Kammerofens
Vorteile:
- Hohe Präzision: Kammeröfen ermöglichen eine präzise Temperaturkontrolle, was für empfindliche Beschichtungen von Vorteil ist.
- Flexibilität: Sie eignen sich sowohl für kleine als auch für große Werkstücke und können bei Bedarf in verschiedenen Größen und Ausführungen konfiguriert werden.
Herausforderungen:
- Lade- und Entladezeiten: Da die Werkstücke manuell in die Kammer geladen und wieder entnommen werden müssen, kann es in großen Produktionslinien zu Verzögerungen kommen, wenn nicht genügend Öfen zur Verfügung stehen.
Pulverofen mit Schienen

Ein Pulverofen mit Schienen bietet eine hervorragende Lösung für Produktionslinien, die eine hohe Stückzahl und schnelle Durchlaufzeiten erfordern. Diese Art von Ofen ist mit Schienen ausgestattet, die es ermöglichen, die Werkstücke automatisch in den Ofen zu befördern und nach dem Aushärten wieder herauszutransportieren.
4.1. Aufbau eines Pulverofens mit Schienen
Der Hauptunterschied zwischen einem Standard-Kammerofen und einem Pulverofen mit Schienen besteht in der Transportmethode der Werkstücke. Bei einem Pulverofen mit Schienen wird das Werkstück auf einem Schienensystem durch den Ofen befördert, was eine kontinuierliche Produktion ermöglicht.
- Automatisierte Produktion: Das Schienensystem ermöglicht eine automatisierte Bewegung der Werkstücke, was die Effizienz steigert und die Notwendigkeit manueller Arbeit reduziert.
- Kontinuierlicher Betrieb: Im Gegensatz zu Kammeröfen, bei denen Werkstücke einzeln beladen und entladen werden müssen, können Schienenöfen einen kontinuierlichen Fluss von Werkstücken durch den Ofen gewährleisten, was zu höheren Durchlaufgeschwindigkeiten führt.
4.2. Vorteile eines Pulverofens mit Schienen
- Höhere Effizienz: Die Fähigkeit, Werkstücke automatisch und kontinuierlich durch den Ofen zu transportieren, erhöht die Produktionsgeschwindigkeit und Effizienz.
- Geringere Ausfallzeiten: Da die Werkstücke ohne Unterbrechung durch den Ofen bewegt werden, gibt es weniger Ausfallzeiten zwischen den Beschichtungs- und Aushärtevorgängen.
- Automatisierungspotenzial: Schienenöfen lassen sich problemlos in vollständig automatisierte Fertigungslinien integrieren, was eine Reduzierung der Arbeitskosten und eine Erhöhung der Produktion ermöglicht.
4.3. Typische Anwendungen eines Pulverofens mit Schienen
Pulveröfen mit Schienen werden häufig in der Massenproduktion eingesetzt, wo große Mengen von Werkstücken kontinuierlich beschichtet und ausgehärtet werden müssen. Typische Anwendungen sind:
- Automobilproduktion: Für die Beschichtung von Karosserieteilen, Felgen und anderen Fahrzeugkomponenten.
- Großserienfertigung von Haushaltsgeräten: Für die Beschichtung von Gehäusen, Komponenten und Oberflächen von Waschmaschinen, Trocknern und Kühlschränken.
Pulverofen mit Schienen im Boden
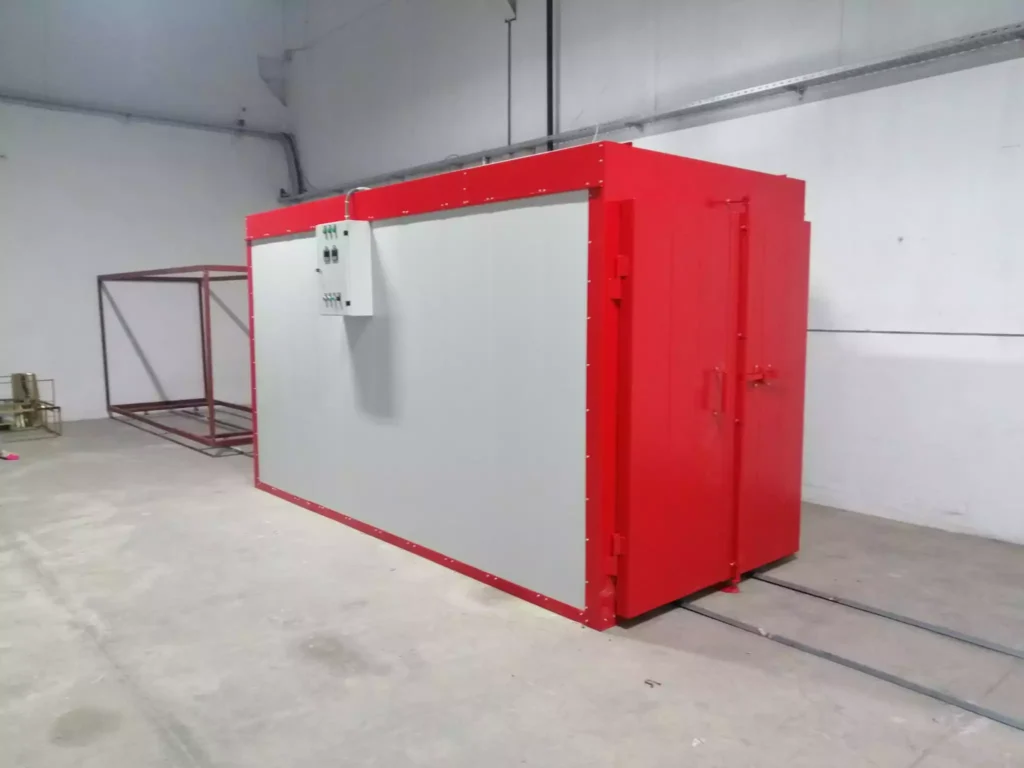
Ein Pulverofen mit Schienen im Boden ist eine spezielle Variante des Schienenofens, bei dem die Schienen in den Boden des Ofens integriert sind. Dies bietet mehrere Vorteile, insbesondere in Bezug auf die Raumnutzung und das Handling schwerer Werkstücke.
5.1. Funktionsweise eines Pulverofens mit Bodenschienen
Bei einem Pulverofen mit Schienen im Boden werden die Werkstücke auf rollenden Gestellen durch den Ofen befördert. Da sich die Schienen im Boden des Ofens befinden, wird die gesamte Ofenhöhe optimal genutzt, und es bleibt mehr Platz für die Beschichtung großer oder schwerer Objekte.
- Stabiler Transport: Die Bodenschienen sorgen für einen stabilen und gleichmäßigen Transport der Werkstücke, wodurch die Gefahr von Stößen oder Beschädigungen während des Aushärtens minimiert wird.
- Einfache Handhabung großer Werkstücke: Schienen im Boden ermöglichen es, schwere oder sperrige Werkstücke leicht in den Ofen zu schieben und herauszuholen, was besonders bei großen Metallteilen von Vorteil ist.
5.2. Vorteile eines Pulverofens mit Schienen im Boden
- Platzersparnis: Da sich die Schienen im Boden befinden, wird der vertikale Raum des Ofens besser genutzt. Dies ist besonders in engen Produktionshallen oder bei der Handhabung sehr großer Werkstücke vorteilhaft.
- Erleichterung der Handhabung schwerer Teile: Schienen im Boden sind ideal für das Handling schwerer Teile, da sie eine gleichmäßige und stabile Bewegung der Werkstücke gewährleisten.
5.3. Typische Anwendungen eines Pulverofens mit Schienen im Boden
- Schwere Metallbearbeitung: Diese Öfen eignen sich ideal für Branchen, in denen sehr große oder schwere Metallteile beschichtet werden, z. B. im Maschinenbau oder in der Bauindustrie.
- Automobilbau: In der Automobilindustrie werden oft große Teile wie Fahrgestelle und Karosserien beschichtet. Ein Ofen mit Schienen im Boden ermöglicht es, diese Teile effizient zu transportieren und zu verarbeiten.
Pulverofen mit Trennwand
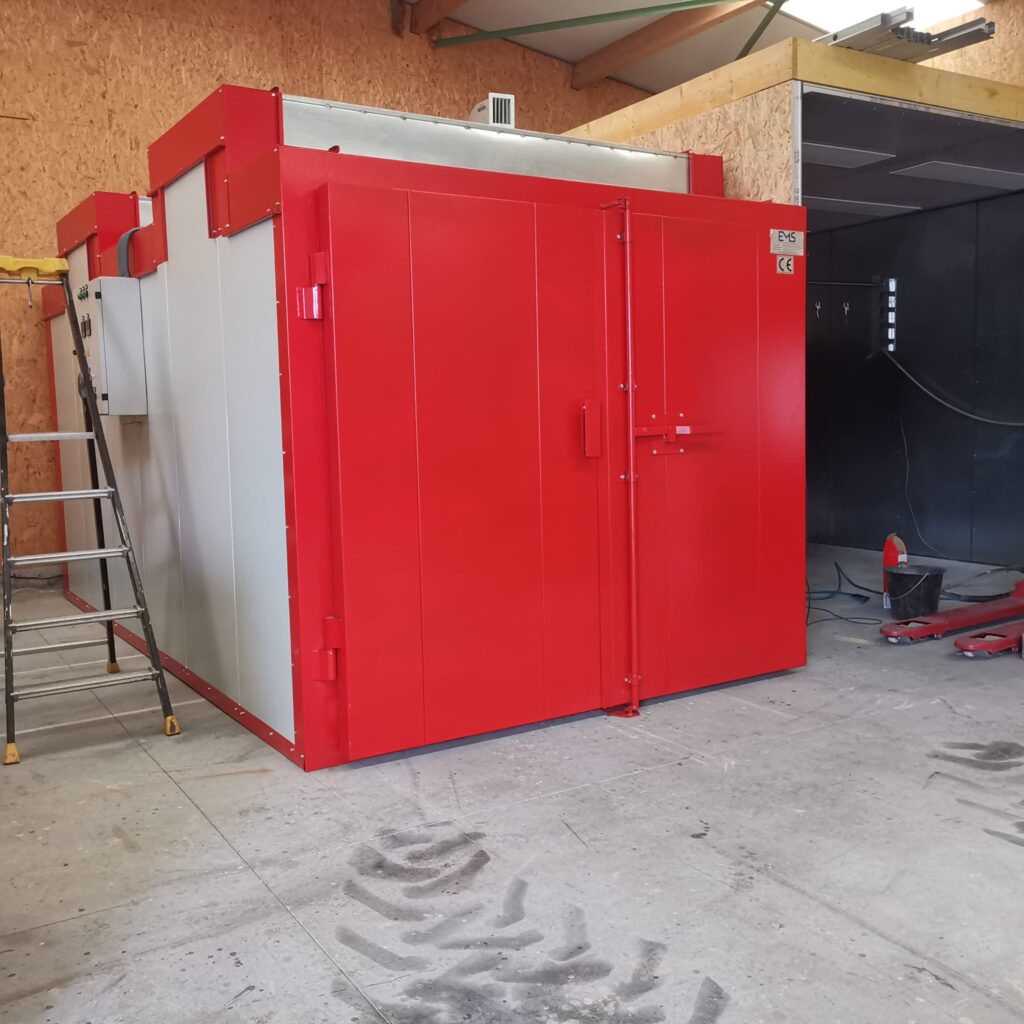
Ein Pulverofen mit Trennwand ist eine spezialisierte Art von Ofen, die es ermöglicht, mehrere Werkstücke gleichzeitig bei unterschiedlichen Temperaturen zu verarbeiten. Diese Öfen sind mit einer internen Trennwand ausgestattet, die verschiedene Abschnitte des Ofens voneinander isoliert.
6.1. Aufbau eines Pulverofens mit Trennwand
Ein Pulverofen mit Trennwand besteht aus zwei oder mehr getrennten Kammern, die durch eine isolierte Wand voneinander getrennt sind. Jede Kammer kann unabhängig voneinander beheizt und gesteuert werden, was die gleichzeitige Aushärtung verschiedener Werkstücke bei unterschiedlichen Temperaturen ermöglicht.
- Getrennte Temperaturzonen: Dank der Trennwand können unterschiedliche Temperaturzonen innerhalb desselben Ofens eingerichtet werden. Dies ist besonders nützlich, wenn Werkstücke aus verschiedenen Materialien oder mit unterschiedlichen Pulverbeschichtungen gleichzeitig verarbeitet werden müssen.
- Flexibilität in der Produktion: Die Trennwand bietet Flexibilität, da verschiedene Werkstücke unabhängig voneinander verarbeitet werden können, ohne dass Kompromisse bei der Temperaturkontrolle eingegangen werden müssen.
6.2. Vorteile eines Pulverofens mit Trennwand
- Effizienzsteigerung: Ein Pulverofen mit Trennwand ermöglicht die gleichzeitige Verarbeitung mehrerer Werkstücke, was die Effizienz und Produktivität erhöht.
- Flexibilität in der Temperaturkontrolle: Unterschiedliche Temperaturanforderungen können in einem einzigen Ofen erfüllt werden, was besonders in Produktionslinien von Vorteil ist, in denen verschiedene Werkstücke gleichzeitig verarbeitet werden müssen.
6.3. Anwendungen eines Pulverofens mit Trennwand
- Industrien mit vielfältigen Werkstücken: Diese Art von Ofen wird häufig in Branchen eingesetzt, in denen Werkstücke unterschiedlicher Größe und Material gleichzeitig beschichtet werden, z. B. in der Automobil- und Maschinenbauindustrie.
- Spezialisierte Beschichtungsverfahren: Pulveröfen mit Trennwand eignen sich besonders für spezialisierte Beschichtungsverfahren, bei denen unterschiedliche Materialien oder Pulverlacke unterschiedliche Aushärtetemperaturen erfordern.
7. Fazit
Pulveröfen spielen eine entscheidende Rolle im Pulverbeschichtungsprozess und bieten eine Vielzahl von Optionen, die je nach den spezifischen Anforderungen der Produktion ausgewählt werden können. Ob es sich um einfache Kammeröfen, Pulveröfen mit Schienen oder spezialisierte Modelle wie Pulveröfen mit Trennwänden handelt – jede dieser Varianten bietet spezifische Vorteile, die in verschiedenen industriellen Anwendungen genutzt werden können.
Durch die Auswahl des richtigen Pulverofens können Unternehmen ihre Effizienz steigern, die Qualität ihrer Beschichtungen verbessern und gleichzeitig den Energieverbrauch und die Betriebskosten optimieren.
Pulverofen
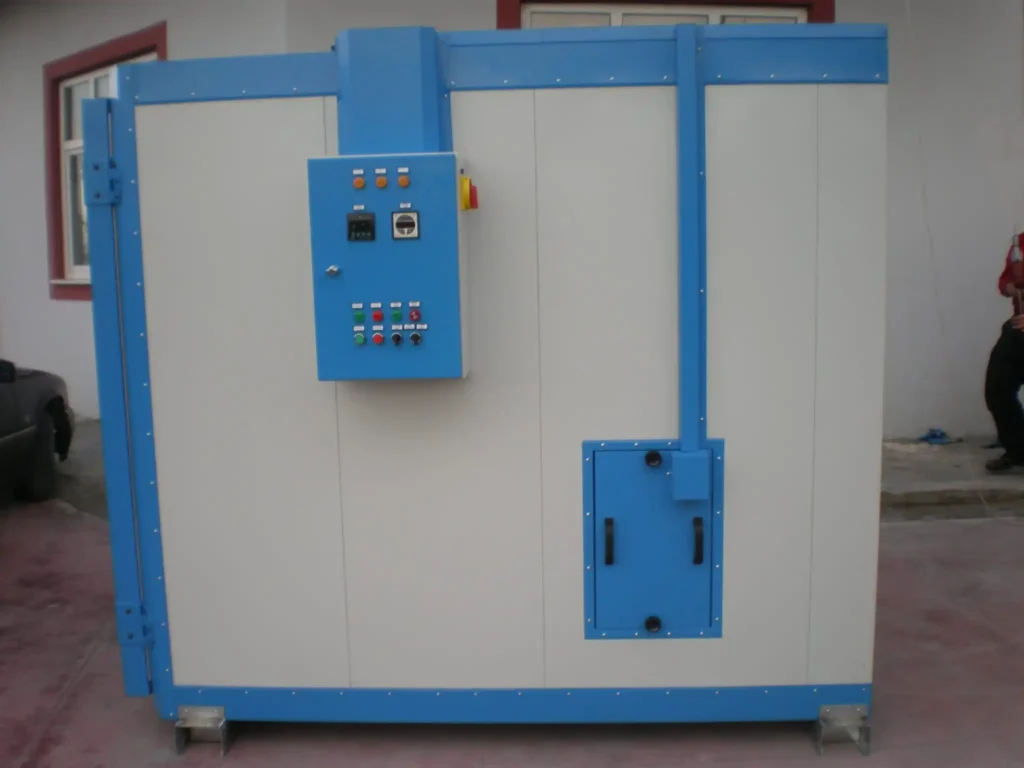
Ein Pulverofen ist ein zentrales Element im Prozess der Pulverbeschichtung, einer weit verbreiteten und effektiven Methode zur Oberflächenveredelung. Pulverbeschichtungen bieten eine robuste, dauerhafte und widerstandsfähige Schicht auf Metall- und Kunststoffteilen. Die Beschichtung erfolgt in einem Pulverofen, in dem das Pulver, das elektrostatisch auf das Werkstück aufgebracht wurde, durch Hitze geschmolzen und in eine harte, widerstandsfähige Oberfläche umgewandelt wird.
In diesem ausführlichen Text werden alle Aspekte von Pulveröfen behandelt, von der Geschichte und Entwicklung über den Aufbau und die Funktionsweise bis hin zu spezifischen Arten von Pulveröfen, wie Kammeröfen, Pulveröfen mit Schienen und Pulveröfen mit Trennwänden. Darüber hinaus werden die ökologischen und wirtschaftlichen Vorteile von Pulveröfen sowie deren Einsatzmöglichkeiten in verschiedenen Industrien ausführlich beleuchtet.
Einführung in den Pulverofen
Ein Pulverofen ist ein speziell entwickelter Ofen, der in der Pulverbeschichtung verwendet wird, um das aufgetragene Pulver durch Hitze zu einer schützenden und dekorativen Schicht zu verarbeiten. Die Pulverbeschichtung wird zunehmend in der Automobil-, Bau-, Möbel- und Konsumgüterindustrie eingesetzt, da sie langlebige und umweltfreundliche Beschichtungen ermöglicht, die herkömmlichen Nasslacken überlegen sind.
1.1. Geschichte der Pulverbeschichtung
Die Pulverbeschichtung entstand in den 1950er Jahren als umweltfreundliche Alternative zu lösungsmittelbasierten Lackierungen. Die Entwicklung von Pulverlacken und der dazugehörigen Öfen wurde durch den Wunsch nach einer effizienteren und umweltfreundlicheren Methode zur Oberflächenbehandlung vorangetrieben. Seit den 1970er Jahren hat sich die Pulverbeschichtung in vielen Industrien weltweit etabliert.
Pulveröfen haben eine Schlüsselrolle in dieser Entwicklung gespielt, da sie es ermöglichen, das aufgetragene Pulver zu schmelzen und zu vernetzen, wodurch eine dauerhafte und hochwertige Oberfläche entsteht.
Aufbau und Funktionsweise eines Pulverofens
Ein Pulverofen ist speziell dafür ausgelegt, Werkstücke zu erhitzen und das aufgebrachte Pulver bei hohen Temperaturen zu schmelzen und auszuhärten. Der Aushärteprozess stellt sicher, dass das Pulver auf dem Werkstück haftet und eine dauerhafte, robuste Beschichtung bildet.
2.1. Grundlegende Komponenten eines Pulverofens
Die Hauptkomponenten eines Pulverofens umfassen:
- Heizelemente: Diese können elektrisch oder gasbetrieben sein und sorgen für die notwendige Hitze, um das Pulver zu schmelzen und auszuhärten.
- Luftzirkulationssystem: Ein wichtiges Merkmal eines jeden Pulverofens ist die gleichmäßige Verteilung der Hitze im Inneren des Ofens. Ein Lüftungssystem sorgt für eine konstante Luftzirkulation, damit alle Bereiche des Werkstücks gleichmäßig erhitzt werden.
- Steuerungseinheit: Moderne Pulveröfen verfügen über elektronische Steuerungssysteme, die es ermöglichen, die Temperatur präzise zu regulieren und den Aushärtezyklus zu steuern.
- Fördersysteme: In vielen industriellen Anwendungen wird ein automatisches Fördersystem verwendet, das die Werkstücke durch den Ofen bewegt, um eine kontinuierliche Produktion zu gewährleisten.
2.2. Funktionsweise eines Pulverofens
Die Funktionsweise eines Pulverofens lässt sich in folgende Schritte unterteilen:
- Beschichtung des Werkstücks: Zuerst wird das Pulver durch elektrostatische Sprühgeräte auf das Werkstück aufgetragen.
- Erhitzung im Ofen: Das beschichtete Werkstück wird in den Pulverofen befördert, wo es gleichmäßig erhitzt wird. Typische Temperaturen liegen zwischen 150°C und 220°C, je nach Art des verwendeten Pulvers.
- Aushärten und Vernetzen: Während das Pulver erhitzt wird, schmilzt es und vernetzt sich chemisch, was zu einer dauerhaften, schützenden und dekorativen Beschichtung führt.
- Abkühlung: Nach dem Aushärten wird das Werkstück aus dem Ofen entfernt und abgekühlt, bevor es weiterverarbeitet oder verpackt wird.
Arten von Pulveröfen
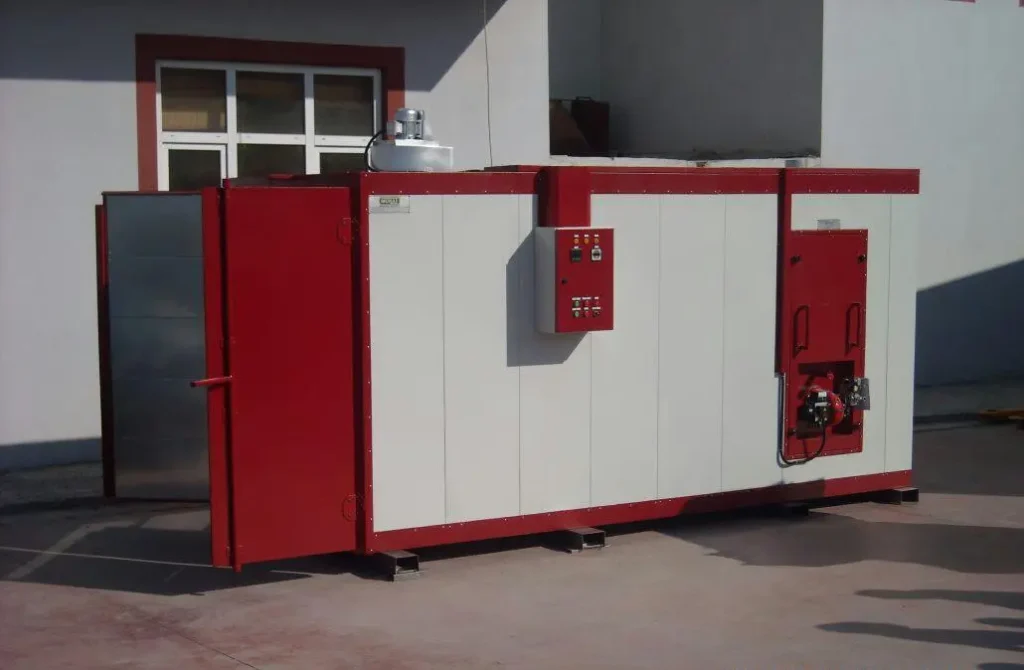
Es gibt verschiedene Arten von Pulveröfen, die jeweils für bestimmte Anwendungen und Anforderungen entwickelt wurden. Die Wahl des richtigen Ofens hängt von der Art des zu beschichtenden Materials, der Produktionskapazität und den spezifischen Anforderungen an die Beschichtung ab.
3.1. Kammerofen
Ein Kammerofen ist eine geschlossene Einheit, die häufig für kleinere Produktionsläufe oder für größere, sperrige Werkstücke verwendet wird. Der Kammerofen bietet eine stabile Temperaturumgebung und eine gleichmäßige Wärmeverteilung, was ihn ideal für die Bearbeitung komplexer Werkstücke macht.
Vorteile eines Kammerofens:
- Gleichmäßige Hitzeverteilung: Der geschlossene Raum ermöglicht eine gleichmäßige Wärmeverteilung, die zu einer homogenen Beschichtung führt.
- Vielseitigkeit: Kammeröfen sind in verschiedenen Größen erhältlich und können für kleine wie auch große Werkstücke verwendet werden.
- Energieeffizienz: Kammeröfen sind oft energieeffizienter, da die Wärme im geschlossenen Raum besser gespeichert wird und weniger Energie benötigt wird, um die Innentemperatur konstant zu halten.
- Präzise Steuerung: Moderne Kammeröfen verfügen über fortschrittliche Steuerungssysteme, die eine genaue Regulierung der Temperatur und der Aushärtezeit ermöglichen, was besonders bei empfindlichen Materialien und komplexen Beschichtungen von Vorteil ist.
Anwendungsbereiche:
Kammeröfen finden häufig in der Automobilindustrie, der Metallverarbeitung und der Möbelherstellung Anwendung. Sie sind ideal für Anwendungen, bei denen Flexibilität und Präzision gefragt sind, wie z. B. bei der Pulverbeschichtung von Autoteilen, Möbelrahmen, Metallgeländern und Haushaltsgeräten.
Durchlaufofen
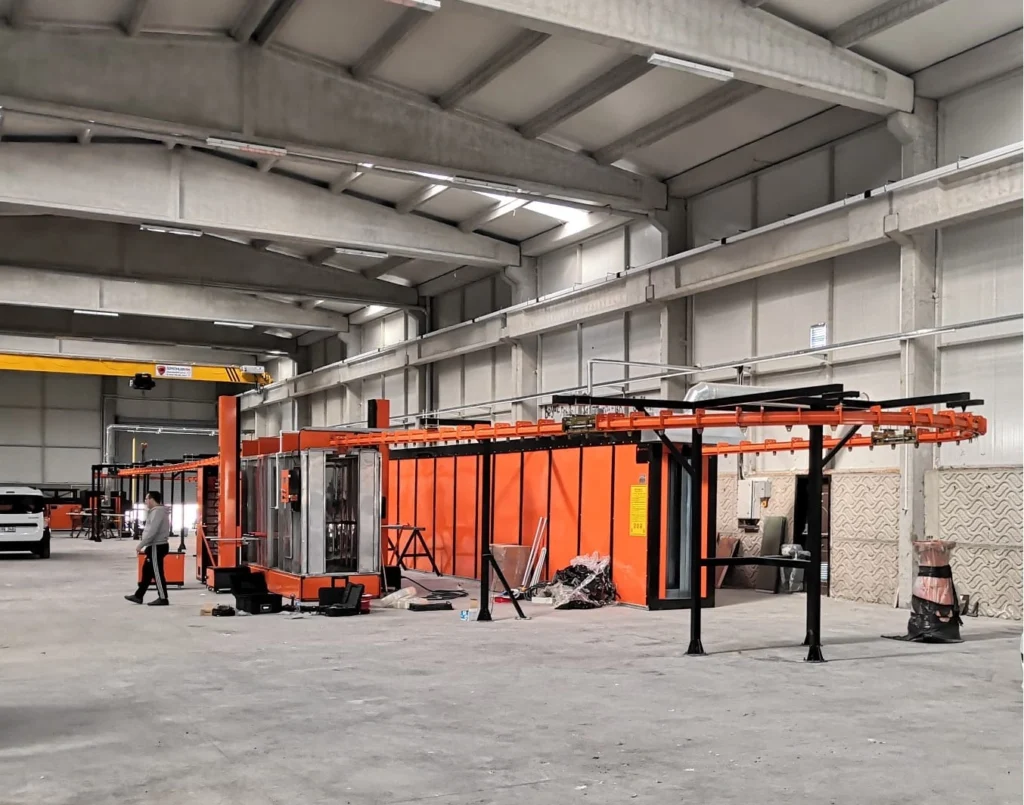
Ein Durchlaufofen, auch als Kontinuierlicher Ofen bezeichnet, ist für Produktionslinien konzipiert, in denen eine kontinuierliche Beschichtung und Aushärtung erforderlich ist. Im Gegensatz zu Kammeröfen, bei denen die Werkstücke manuell geladen und entladen werden, bewegt ein Fördersystem die Werkstücke automatisch durch den Ofen.
Vorteile eines Durchlaufofens:
- Hohe Effizienz: Da Werkstücke kontinuierlich durch den Ofen transportiert werden, ist der Durchlaufofen besonders effizient und eignet sich ideal für die Massenproduktion.
- Reduzierte Ausfallzeiten: Der kontinuierliche Betrieb minimiert die Ausfallzeiten zwischen den Aushärtevorgängen, was zu einer höheren Produktionskapazität führt.
- Automatisierungspotenzial: Durchlaufofen-Systeme lassen sich leicht in automatisierte Produktionslinien integrieren, wodurch der manuelle Arbeitsaufwand verringert und die Produktivität gesteigert wird.
Anwendungsbereiche:
Durchlauföfen sind besonders in der Automobilindustrie, bei der Herstellung von Haushaltsgeräten sowie in der Möbelindustrie weit verbreitet, wo große Stückzahlen beschichtet und in schneller Folge ausgehärtet werden müssen.
Pulverofen mit Schienen

Ein Pulverofen mit Schienen ist ein spezialisierter Ofen, der mit einem Schienensystem ausgestattet ist, um schwere oder sperrige Werkstücke effizient zu transportieren. Diese Schienen können entweder an der Decke des Ofens oder im Boden montiert sein, was je nach Werkstück und Produktionsanforderungen variiert.
Vorteile eines Pulverofens mit Schienen:
- Einfache Handhabung schwerer Werkstücke: Das Schienensystem ermöglicht den Transport großer und schwerer Werkstücke durch den Ofen, ohne dass manuelle Arbeit erforderlich ist.
- Reduzierung von Beschädigungen: Da die Werkstücke auf Schienen gleichmäßig durch den Ofen bewegt werden, wird die Gefahr von Beschädigungen während des Aushärteprozesses minimiert.
- Verbesserte Produktionseffizienz: Das Schienensystem sorgt für einen kontinuierlichen und reibungslosen Ablauf in der Produktion, was die Effizienz erhöht.
Anwendungsbereiche:
Pulveröfen mit Schienen werden häufig in der Schwerindustrie eingesetzt, insbesondere in Bereichen wie der Metallverarbeitung und im Maschinenbau, wo große Metallstrukturen, Rohrleitungen und schwere Maschinenteile beschichtet und ausgehärtet werden müssen.
Pulverofen mit Schienen im Boden
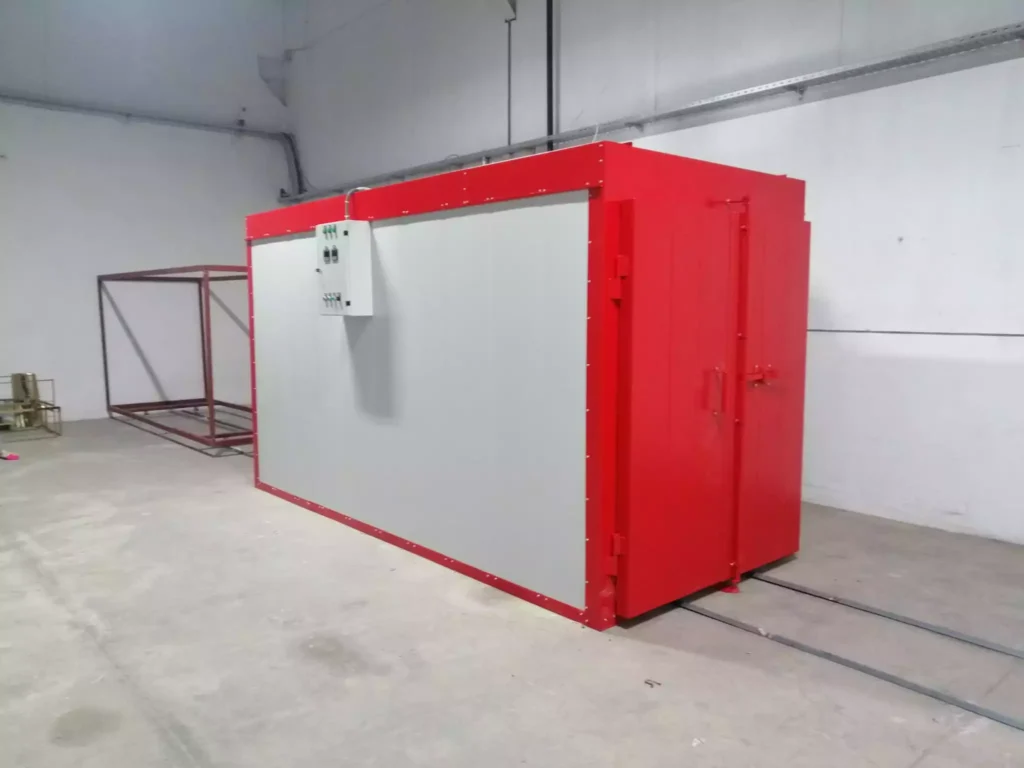
Ein Pulverofen mit Schienen im Boden ist eine Variante des Pulverofens mit Schienen, bei dem die Schienen direkt im Boden des Ofens integriert sind. Dies ermöglicht eine einfachere Handhabung und erhöht die Stabilität beim Transport von großen und schweren Werkstücken durch den Ofen.
Vorteile eines Pulverofens mit Schienen im Boden:
- Stabiler Transport: Die Bodenschienen sorgen für einen gleichmäßigen und stabilen Transport von Werkstücken durch den Ofen, was besonders bei großen oder unregelmäßig geformten Werkstücken vorteilhaft ist.
- Platzersparnis: Da die Schienen in den Boden des Ofens integriert sind, wird der vertikale Raum des Ofens besser genutzt, was Platz spart und die Handhabung von großen Objekten erleichtert.
Anwendungsbereiche:
Pulveröfen mit Schienen im Boden eignen sich besonders für große und schwere Metallteile, wie sie in der Bauindustrie, im Maschinenbau oder in der Automobilproduktion verwendet werden. Dazu gehören Karosserien, Fahrgestelle, Stahlträger und andere sperrige Komponenten, die eine gleichmäßige Beschichtung und Aushärtung erfordern.
Pulverofen mit Trennwand
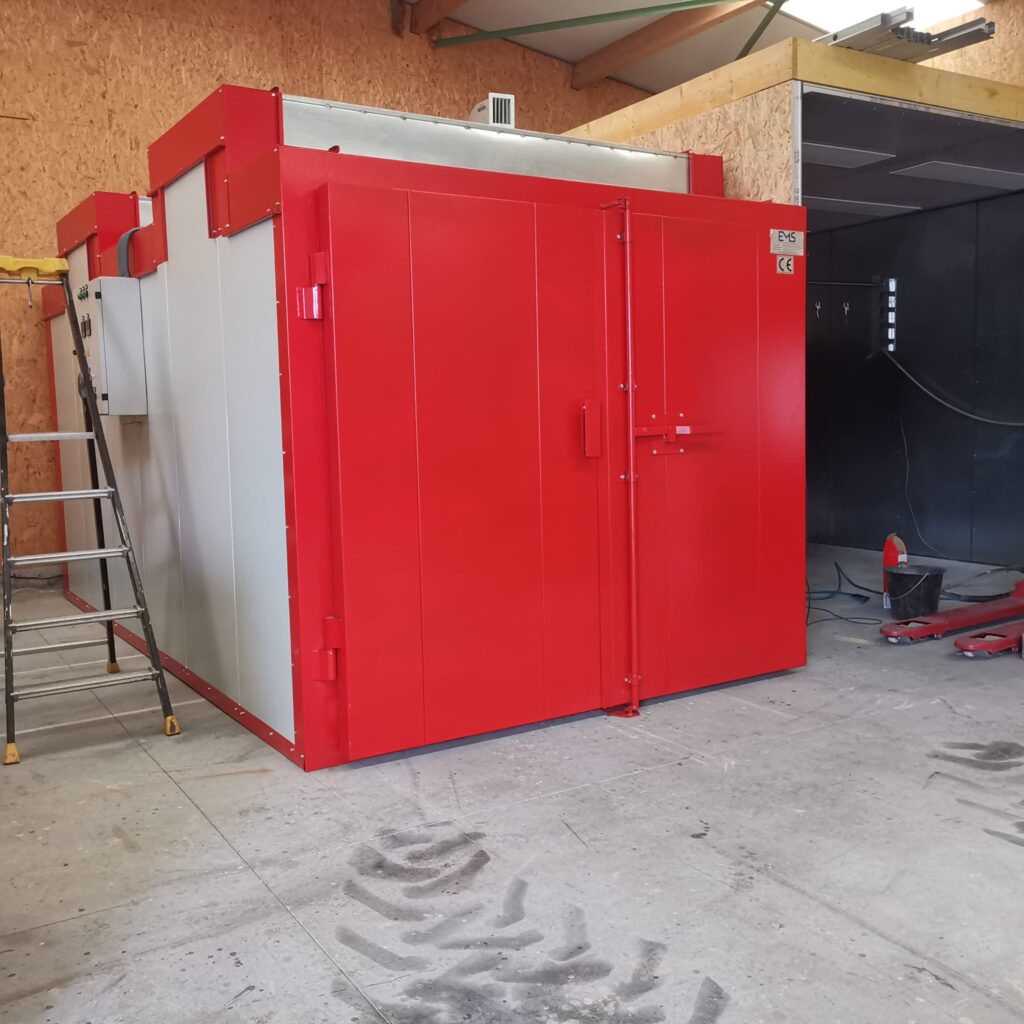
Ein Pulverofen mit Trennwand ist ein spezieller Ofen, der mit internen Trennwänden ausgestattet ist, um mehrere Werkstücke gleichzeitig bei unterschiedlichen Temperaturen zu verarbeiten. Diese Trennwände teilen den Ofen in separate Kammern, die unabhängig voneinander beheizt und gesteuert werden können.
Vorteile eines Pulverofens mit Trennwand:
- Mehrere Temperaturzonen: Die Trennwand ermöglicht es, verschiedene Temperaturzonen im Ofen zu schaffen, sodass unterschiedliche Werkstücke gleichzeitig bei optimalen Temperaturen ausgehärtet werden können.
- Flexibilität: Diese Ofenart bietet maximale Flexibilität für Produktionslinien, die Werkstücke mit unterschiedlichen Aushärteanforderungen verarbeiten müssen.
Anwendungsbereiche:
Pulveröfen mit Trennwand werden häufig in der Automobilindustrie, der Metallverarbeitung und anderen Industrien eingesetzt, in denen Werkstücke unterschiedlicher Größe und Materialien gleichzeitig beschichtet und ausgehärtet werden müssen. Sie sind besonders nützlich in Produktionslinien, die eine hohe Flexibilität erfordern.
Energieeffizienz und Stromverbrauch von Pulveröfen
Ein wesentlicher Aspekt bei der Verwendung von Pulveröfen ist der Stromverbrauch. Da Pulveröfen bei hohen Temperaturen arbeiten müssen, kann der Energieverbrauch erheblich sein, insbesondere in großen industriellen Anwendungen. Die Optimierung der Energieeffizienz ist daher entscheidend, um die Betriebskosten zu senken und die Umweltbelastung zu reduzieren.
4.1. Faktoren, die den Stromverbrauch beeinflussen
Der Stromverbrauch eines Pulverofens hängt von verschiedenen Faktoren ab, darunter:
- Größe des Ofens: Je größer der Ofen, desto mehr Energie wird benötigt, um ihn auf die erforderliche Temperatur zu bringen und diese über einen längeren Zeitraum aufrechtzuerhalten.
- Art des Heizsystems: Elektro- und Gasöfen haben unterschiedliche Energieanforderungen. Elektrische Öfen sind häufig teurer im Betrieb als gasbetriebene Öfen, bieten jedoch in der Regel eine genauere Temperaturkontrolle.
- Isolierung: Eine gute Isolierung des Ofens verhindert den Wärmeverlust und reduziert den Energieverbrauch erheblich.
- Auslastung: Ein Ofen, der nicht voll beladen ist, arbeitet ineffizient. Die optimale Auslastung des Ofens kann den Energieverbrauch reduzieren, da weniger Energie pro Werkstück benötigt wird.
4.2. Tipps zur Reduzierung des Energieverbrauchs
- Optimierte Auslastung: Pulveröfen sollten so beladen werden, dass der verfügbare Platz optimal genutzt wird, um den Energieverbrauch pro Werkstück zu minimieren.
- Regelmäßige Wartung: Die Wartung des Ofens, einschließlich der Reinigung und des Austauschs von Dichtungen und Isolierungen, stellt sicher, dass der Ofen effizient arbeitet.
- Fortschrittliche Steuerungssysteme: Moderne Steuerungssysteme können den Energieverbrauch durch präzise Temperaturregelung und dynamische Anpassung der Aushärtezeiten optimieren.
- Wärmerückgewinnung: Einige fortschrittliche Pulveröfen sind mit Wärmerückgewinnungssystemen ausgestattet, die Abwärme zurück in den Aushärteprozess einspeisen und so den Energieverbrauch reduzieren.
Umweltvorteile von Pulveröfen und Pulverbeschichtung
Neben der Effizienz und den praktischen Vorteilen von Pulveröfen bietet die Pulverbeschichtung im Vergleich zu herkömmlichen Lackierverfahren erhebliche Umweltvorteile.
5.1. Keine Lösungsmittel und flüchtigen organischen Verbindungen (VOCs)
Pulverbeschichtungen enthalten keine Lösungsmittel und setzen keine flüchtigen organischen Verbindungen (VOCs) frei, die für die Umwelt und die Gesundheit der Arbeiter schädlich sein können. Dies macht die Pulverbeschichtung zu einer umweltfreundlicheren Option im Vergleich zu lösungsmittelbasierten Beschichtungen.
5.2. Weniger Abfall
Da überschüssiges Pulver, das während des Beschichtungsprozesses nicht auf dem Werkstück haftet, aufgefangen und wiederverwendet werden kann, wird weniger Abfall erzeugt. Dies trägt zu einer effizienteren Nutzung des Materials und einer Reduzierung der Produktionsabfälle bei.
5.3. Energieeffizienz
Moderne Pulveröfen sind oft energieeffizienter als andere Trocknungs- und Aushärtesysteme. Gasbefeuerte Pulveröfen sind besonders energieeffizient und bieten im Vergleich zu elektrischen Öfen niedrigere Betriebskosten, insbesondere bei großflächigen Anwendungen.
5.4. Langlebigkeit der Beschichtung
Die Langlebigkeit von Pulverbeschichtungen trägt ebenfalls zur Umweltfreundlichkeit bei, da beschichtete Teile seltener ausgetauscht oder nachbearbeitet werden müssen. Dies führt zu weniger Abfall und einer längeren Lebensdauer der beschichteten Produkte.
Anwendungsbereiche von Pulveröfen
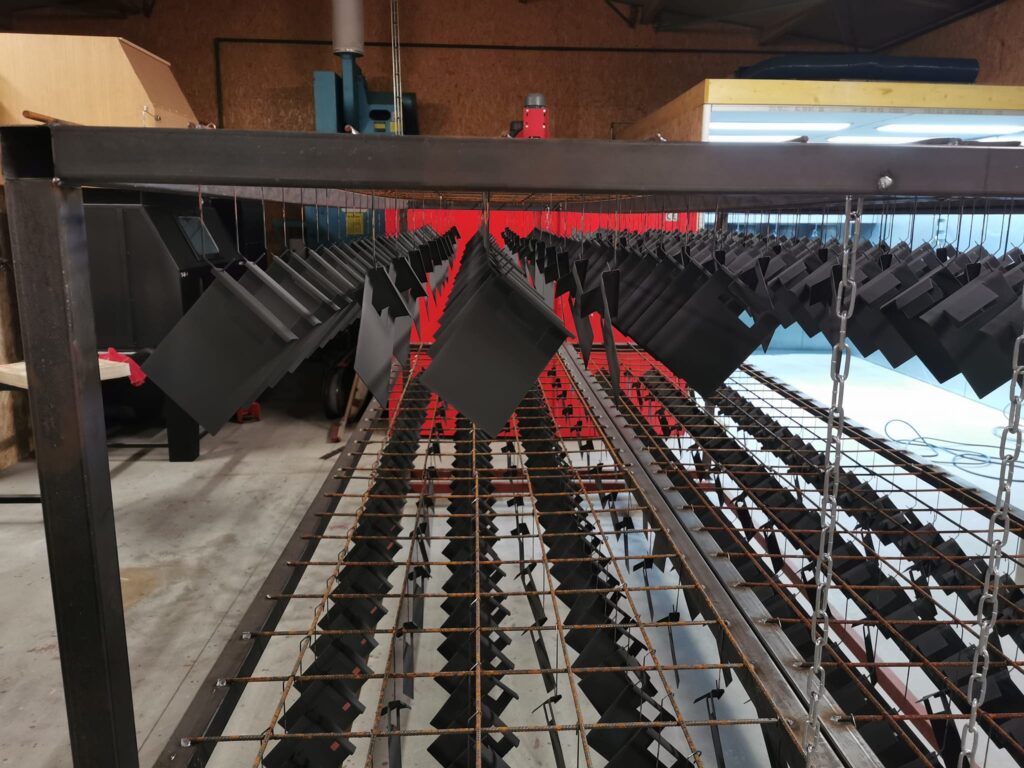
Pulveröfen finden in vielen Industrien Anwendung, da sie eine Vielzahl von Materialien und Werkstücken effizient beschichten und aushärten können.
6.1. Automobilindustrie
In der Automobilindustrie werden Pulveröfen häufig zur Beschichtung von Fahrzeugteilen wie Felgen, Karosserieteilen, Fahrgestellen und Motorblöcken verwendet. Pulverbeschichtungen bieten nicht nur eine hervorragende Haltbarkeit und Korrosionsbeständigkeit, sondern auch ein ansprechendes Finish in einer Vielzahl von Farben und Oberflächenstrukturen.
6.2. Bauindustrie
Die Bauindustrie verwendet Pulveröfen zur Beschichtung von Stahlträgern, Geländern, Fassadenelementen und Fensterrrahmen. Die Beschichtungen bieten Schutz vor Witterungseinflüssen, Korrosion und mechanischen Schäden, was die Langlebigkeit der Baukomponenten verbessert.
6.3. Möbelherstellung
In der Möbelindustrie werden Metallrahmen, Gartenmöbel und Büroausstattungen häufig pulverbeschichtet, um eine robuste und ästhetisch ansprechende Oberfläche zu erzielen. Pulveröfen spielen hier eine zentrale Rolle bei der Aushärtung der Beschichtungen.
6.4. Elektronik- und Haushaltsgeräteindustrie
Die Elektronikindustrie nutzt Pulveröfen zur Beschichtung von Gehäusen und Komponenten, die gegen elektrische Interferenzen geschützt werden müssen. Auch in der Haushaltsgeräteindustrie werden Pulveröfen zur Beschichtung von Geräten wie Waschmaschinen, Trocknern, Kühlschränken und Öfen eingesetzt, um Kratzfestigkeit und Langlebigkeit zu gewährleisten.
Zukunft der Pulverbeschichtung und Pulveröfen
Die Pulverbeschichtungstechnologie und die dazugehörigen Öfen entwickeln sich stetig weiter, um den Anforderungen moderner Fertigungstechnologien gerecht zu werden.
7.1. Fortschritte in der Materialwissenschaft
Neue Pulvermaterialien und verbesserte Beschichtungsverfahren werden entwickelt, um noch robustere und umweltfreundlichere Beschichtungen zu erzeugen. Nanotechnologie und fortschrittliche Polymerforschung könnten in der Zukunft Beschichtungen ermöglichen, die selbstreinigend oder noch widerstandsfähiger gegen extreme Bedingungen sind.
7.2. Energieeffizienz und Nachhaltigkeit
Mit dem zunehmenden Fokus auf Nachhaltigkeit wird die Energieeffizienz von Pulveröfen weiter verbessert. Gasbefeuerte Öfen und Wärmerückgewinnungssysteme sind nur der Anfang – es wird erwartet, dass in der Zukunft noch energieeffizientere Technologien entwickelt werden, die den Energieverbrauch weiter reduzieren und die Umweltbelastung minimieren.
7.3. Digitalisierung und Automatisierung
Moderne Pulveröfen werden zunehmend mit fortschrittlichen digitalen Steuerungssystemen ausgestattet, die den Aushärteprozess überwachen und optimieren. Automatisierte Produktionslinien, die mit Pulveröfen integriert sind, bieten eine höhere Produktionsgeschwindigkeit und reduzieren den manuellen Arbeitsaufwand.
Fazit
Pulveröfen sind ein unverzichtbares Element im Pulverbeschichtungsprozess, der eine robuste, langlebige und umweltfreundliche Oberfläche auf Werkstücken erzeugt. Mit verschiedenen Ofentypen wie Kammeröfen, Durchlauföfen und Pulveröfen mit Schienensystemen können Unternehmen ihre Produktionsprozesse effizient gestalten und eine gleichbleibend hohe Qualität der Beschichtung gewährleisten. Die fortlaufenden technologischen Entwicklungen in den Bereichen Materialwissenschaft, Energieeffizienz und Automatisierung sorgen dafür, dass Pulveröfen auch in Zukunft eine zentrale Rolle in der industriellen Oberflächenbehandlung spielen werden.
Pulverofen
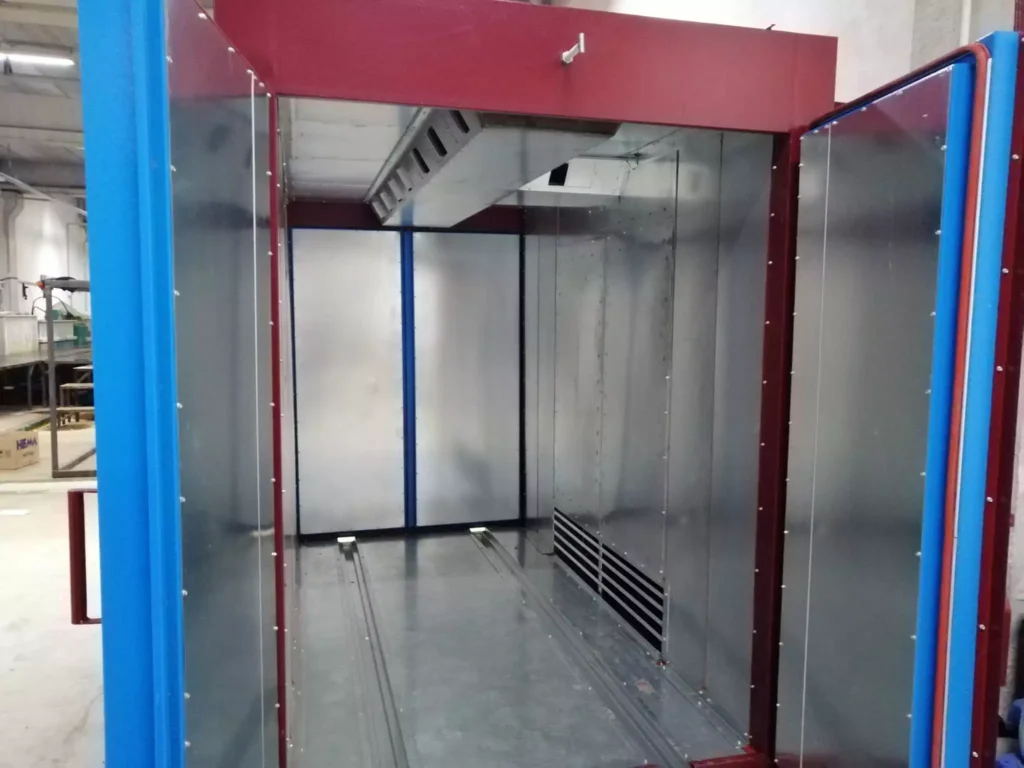
Ein Pulverofen ist ein wesentlicher Bestandteil des Pulverbeschichtungsprozesses, einer modernen und effizienten Methode zur Oberflächenveredelung von Metallteilen und anderen Materialien. Der Begriff „Pulverofen Strom“ bezieht sich auf den elektrischen Strom, der benötigt wird, um einen Pulverofen zu betreiben. Diese Öfen werden in der Regel elektrisch betrieben und erfordern eine konstante Energiezufuhr, um die hohen Temperaturen zu erreichen und aufrechtzuerhalten, die für das Aushärten von Pulverbeschichtungen erforderlich sind.
In diesem ausführlichen Text werde ich auf die Grundlagen der Pulverbeschichtung und die Funktionsweise von Pulveröfen eingehen. Besonderes Augenmerk wird auf den Stromverbrauch, die Energieeffizienz und die technologischen Entwicklungen gelegt, die dazu beitragen, den Stromverbrauch von Pulveröfen zu optimieren. Darüber hinaus werde ich die verschiedenen Arten von elektrischen Pulveröfen untersuchen, wie der Stromverbrauch minimiert werden kann und welche Rolle die Energieeffizienz in modernen Produktionsprozessen spielt.
Grundlagen der Pulverbeschichtung
Bevor wir uns mit den Details des Stromverbrauchs von Pulveröfen beschäftigen, ist es wichtig, den Prozess der Pulverbeschichtung und die Rolle des Pulverofens zu verstehen.
1.1. Was ist Pulverbeschichtung?
Die Pulverbeschichtung ist ein Verfahren, bei dem eine trockene Pulverbeschichtung auf eine Metalloberfläche aufgetragen und anschließend in einem Pulverofen ausgehärtet wird. Das Pulver, das in der Regel aus feinen Partikeln von Harzen, Pigmenten und Additiven besteht, wird elektrostatisch auf das Werkstück aufgebracht, das geerdet ist, um das Pulver anzuziehen. Nachdem das Pulver auf die Oberfläche aufgetragen wurde, wird das Werkstück in einem Ofen erhitzt, damit das Pulver schmilzt und eine gleichmäßige, dauerhafte Beschichtung bildet.
Die Pulverbeschichtung bietet zahlreiche Vorteile, darunter eine hervorragende Oberflächenqualität, Beständigkeit gegen Korrosion, Kratzer und Witterungseinflüsse sowie eine hohe Umweltfreundlichkeit, da keine Lösungsmittel verwendet werden.
1.2. Rolle des Pulverofens
Ein Pulverofen ist der Schlüssel zum Aushärtungsprozess der Pulverbeschichtung. In einem Pulverofen wird das aufgetragene Pulver auf das Werkstück erhitzt, bis es schmilzt und chemisch vernetzt. Dadurch entsteht eine harte, widerstandsfähige Schicht auf der Oberfläche des Werkstücks. Pulveröfen arbeiten in der Regel bei Temperaturen zwischen 150°C und 200°C, je nach Art des Pulvers und des Materials des Werkstücks.
Der Aushärtungsprozess im Pulverofen stellt sicher, dass die Pulverbeschichtung haltbar ist und eine gleichmäßige, glatte Oberfläche aufweist. Ohne diesen Aushärtungsschritt wäre das aufgetragene Pulver instabil und würde nicht die gewünschten Schutz- und Dekorationseigenschaften bieten.
Der Stromverbrauch eines Pulverofens
Pulveröfen erfordern eine erhebliche Menge an elektrischer Energie, um die für den Aushärtungsprozess erforderlichen hohen Temperaturen zu erreichen. Der Stromverbrauch eines Pulverofens hängt von mehreren Faktoren ab, darunter die Größe des Ofens, die Betriebsdauer, die Temperatur, das verwendete Heizsystem und die Effizienz des Ofens. Der Energieverbrauch eines Pulverofens ist daher ein wichtiger Aspekt in Bezug auf die Betriebskosten und die Umweltbilanz von Pulverbeschichtungsanlagen.
2.1. Hauptfaktoren, die den Stromverbrauch beeinflussen
Der Stromverbrauch eines Pulverofens wird von verschiedenen Faktoren beeinflusst, darunter:
- Ofengröße und -kapazität: Größere Öfen, die mehr Werkstücke gleichzeitig verarbeiten können, verbrauchen mehr Strom, um die gesamte Fläche auf die erforderliche Temperatur zu bringen. Kleinere Öfen haben entsprechend einen geringeren Strombedarf.
- Heizsystem: Die Art des Heizsystems beeinflusst den Stromverbrauch erheblich. Pulveröfen können mit elektrischen Heizsystemen, gasbefeuerten Systemen oder Infrarotstrahlern ausgestattet sein. Elektrische Heizungen verbrauchen typischerweise mehr Strom, während gasbefeuerte Systeme oft als energieeffizienter gelten.
- Isolierung des Ofens: Gut isolierte Öfen verlieren weniger Wärme, was den Energieverbrauch verringert, da der Ofen nicht ständig nachheizen muss, um die gewünschte Temperatur aufrechtzuerhalten.
- Betriebsdauer: Der Stromverbrauch hängt auch davon ab, wie lange der Ofen in Betrieb ist. Produktionslinien, die rund um die Uhr arbeiten, verbrauchen natürlich mehr Energie als solche, die nur stundenweise betrieben werden.
- Luftzirkulationssystem: Ein effizientes Luftzirkulationssystem sorgt dafür, dass die heiße Luft im Ofen gleichmäßig verteilt wird, was den Energieverbrauch reduziert und eine gleichmäßige Aushärtung gewährleistet.
2.2. Typischer Stromverbrauch eines Pulverofens
Der typische Stromverbrauch eines Pulverofens hängt von seiner Größe und der Produktionskapazität ab. Ein kleinerer Ofen für den Laboreinsatz oder für kleinere Werkstätten könnte einen Stromverbrauch von etwa 10-20 kWh pro Betriebsstunde haben. Größere industrielle Pulveröfen, die für Massenproduktionen ausgelegt sind, können bis zu 100 kWh oder mehr pro Stunde verbrauchen, insbesondere wenn sie kontinuierlich betrieben werden.
Ein durchschnittlicher mittelgroßer industrieller Pulverofen verbraucht zwischen 50 und 80 kWh pro Betriebsstunde. Diese Zahlen können jedoch je nach Effizienz des Ofens und der Produktionsauslastung variieren.
Arten von Pulveröfen und ihr Einfluss auf den Stromverbrauch
Es gibt verschiedene Arten von Pulveröfen, die jeweils für bestimmte Anwendungen und Produktionsvolumina ausgelegt sind. Die Art des Ofens hat einen direkten Einfluss auf den Stromverbrauch, da verschiedene Heizsysteme und Bauweisen unterschiedliche Energieanforderungen haben.
3.1. Elektro-Pulveröfen
Ein Elektro-Pulverofen wird vollständig mit elektrischem Strom betrieben und nutzt elektrische Heizspiralen oder Heizplatten, um den Innenraum des Ofens zu erwärmen. Elektroöfen sind in der Regel einfacher in der Installation und Wartung als gasbetriebene Öfen, da sie keine spezielle Gasversorgung benötigen. Sie bieten zudem eine präzisere Temperaturkontrolle, was sie für bestimmte Anwendungen attraktiv macht.
Stromverbrauch von Elektro-Pulveröfen:
- Vorteile: Elektroöfen bieten eine gleichmäßige Wärmeverteilung und sind flexibel einsetzbar, da sie einfach an das Stromnetz angeschlossen werden können. Sie eignen sich besonders für kleinere Produktionen oder spezialisierte Anwendungen, bei denen eine genaue Temperaturregelung erforderlich ist.
- Nachteile: Der Stromverbrauch von Elektroöfen ist oft höher als der von gasbefeuerten Öfen, was sie in großen Produktionsumgebungen teurer im Betrieb machen kann. Für den Dauerbetrieb oder für großvolumige Produktionen sind gasbetriebene Öfen in der Regel energieeffizienter.
3.2. Gasbefeuerte Pulveröfen
Gasbetriebene Pulveröfen nutzen Gas (meist Erdgas oder Propan) als Energiequelle, um die benötigte Hitze zu erzeugen. Diese Öfen sind häufig in großen industriellen Anlagen zu finden, da sie in der Regel kostengünstiger im Betrieb sind als Elektroöfen.
Stromverbrauch von gasbefeuerten Pulveröfen:
Obwohl gasbefeuerte Pulveröfen Gas als primäre Energiequelle nutzen, benötigen sie dennoch Strom für die Steuerungssysteme, die Lüftung und die Luftzirkulation. Der Stromverbrauch dieser Systeme ist im Vergleich zu rein elektrisch betriebenen Öfen deutlich geringer, was die Gesamtkosten für den Betrieb reduziert.
- Vorteile: Gasbefeuerte Öfen sind oft kostengünstiger im Betrieb, insbesondere bei großen Produktionen. Sie können größere Werkstücke effizienter verarbeiten und sind in der Regel schneller beim Erreichen der erforderlichen Temperaturen.
- Nachteile: Der Installationsaufwand für gasbetriebene Öfen ist höher, da eine sichere Gaszufuhr und -entlüftung erforderlich sind. Darüber hinaus sind sie in Bereichen, in denen Erdgas oder Propan nicht verfügbar ist, möglicherweise nicht praktikabel.
3.3. Infrarot-Pulveröfen
Infrarot-Pulveröfen nutzen Infrarotstrahlung, um das Pulver auf dem Werkstück direkt zu erhitzen. Anstatt die Luft im gesamten Ofen zu erhitzen, zielt die Infrarotstrahlung direkt auf das Werkstück, was eine schnelle Erwärmung ermöglicht.
Stromverbrauch von Infrarot-Pulveröfen:
- Vorteile: Infrarotöfen sind sehr energieeffizient, da sie das Werkstück schneller erhitzen und so weniger Energie verbrauchen. Sie eignen sich besonders für dünnwandige Werkstücke oder für Produktionsumgebungen, in denen kurze Aushärtezeiten erforderlich sind.
- Nachteile: Infrarotöfen sind in der Anschaffung oft teurer und können bei dickeren oder komplexen Werkstücken nicht so effektiv sein wie herkömmliche Konvektionsöfen. Sie erfordern außerdem eine präzise Steuerung, um sicherzustellen, dass die gesamte Oberfläche des Werkstücks gleichmäßig erhitzt wird.
3.4. Hybrid-Pulveröfen
Hybrid-Pulveröfen kombinieren verschiedene Heiztechnologien, wie z. B. Gas und Elektrizität oder Infrarot und Konvektion, um die Effizienz zu maximieren und den Stromverbrauch zu senken. Diese Öfen bieten eine größere Flexibilität in der Produktionsumgebung und sind oft auf spezielle Anforderungen zugeschnitten.
Stromverbrauch von Hybrid-Pulveröfen:
- Vorteile: Hybridöfen können den Stromverbrauch optimieren, indem sie die effizienteste Heiztechnologie für verschiedene Werkstücke und Aushärteprozesse nutzen. Dies kann den Gesamtenergieverbrauch senken und gleichzeitig eine hohe Flexibilität bieten.
- Nachteile: Die Komplexität und die Kosten der Anschaffung und Wartung können bei Hybridöfen höher sein als bei reinen Gas- oder Elektroöfen. Darüber hinaus erfordert der Betrieb eines Hybridofens eine präzise Steuerung, um die unterschiedlichen Heizmethoden effektiv zu nutzen.
Optimierung des Stromverbrauchs in Pulveröfen
Da der Stromverbrauch einen erheblichen Teil der Betriebskosten von Pulverbeschichtungsanlagen ausmacht, ist die Optimierung des Energieverbrauchs ein zentrales Anliegen für Unternehmen, die mit Pulveröfen arbeiten. Es gibt verschiedene Strategien, um den Stromverbrauch eines Pulverofens zu senken und die Energieeffizienz zu maximieren.
4.1. Isolierung und Wärmerückgewinnung
Eine der effektivsten Methoden, um den Stromverbrauch eines Pulverofens zu senken, ist die Verbesserung der Ofenisolierung. Eine gut isolierte Ofenwand minimiert den Wärmeverlust, sodass weniger Energie benötigt wird, um den Ofen auf der erforderlichen Temperatur zu halten.
Darüber hinaus können moderne Pulveröfen mit Wärmerückgewinnungssystemen ausgestattet werden. Diese Systeme nutzen die Abwärme, die während des Aushärtungsprozesses entsteht, und führen sie wieder in den Prozess ein, um den Energieverbrauch zu senken. Wärmerückgewinnung kann den Gesamtstromverbrauch eines Ofens um bis zu 30% reduzieren.
4.2. Energieeffiziente Heizsysteme
Die Wahl eines energieeffizienten Heizsystems ist entscheidend für die Senkung des Stromverbrauchs. Gasbefeuerte Öfen sind oft effizienter als rein elektrische Systeme, insbesondere in großflächigen Produktionsanlagen. Für bestimmte Anwendungen, bei denen schnelle Aushärtezeiten erforderlich sind, können auch Infrarot- oder Hybridöfen energieeffizienter sein.
4.3. Optimierte Auslastung des Ofens
Ein Pulverofen sollte möglichst immer voll beladen sein, um die Energieeffizienz zu maximieren. Das Heizen eines halb leeren Ofens verbraucht genauso viel Energie wie das Heizen eines voll beladenen Ofens, was zu unnötigem Energieverbrauch führt. Die Produktionsplanung sollte so gestaltet werden, dass der Ofen optimal ausgelastet ist.
4.4. Intelligente Steuerungssysteme
Moderne Pulveröfen sind oft mit intelligenten Steuerungssystemen ausgestattet, die den Energieverbrauch optimieren, indem sie den Aushärteprozess automatisch an die spezifischen Anforderungen des Werkstücks anpassen. Diese Systeme können den Energieverbrauch senken, indem sie die Temperatur dynamisch anpassen und den Ofen in Zeiten, in denen keine Werkstücke vorhanden sind, in den Standby-Modus versetzen.
Zukunftstechnologien zur Reduzierung des Stromverbrauchs von Pulveröfen
Die Zukunft der Pulverofen-Technologie wird stark von der Entwicklung neuer Technologien zur Reduzierung des Stromverbrauchs und zur Erhöhung der Energieeffizienz geprägt sein. Einige der Schlüsseltechnologien, die das Potenzial haben, den Energieverbrauch in der Pulverbeschichtung weiter zu senken, sind:
5.1. Verbessertes Ofendesign und Materialwissenschaften
Neue Materialien zur Isolierung und effizientere Ofendesigns, die eine bessere Luftzirkulation und Wärmespeicherung ermöglichen, werden den Energieverbrauch von Pulveröfen weiter senken. Leichtbauweisen und innovative Baumaterialien können die Wärmespeicherung verbessern und den Energiebedarf drastisch reduzieren.
5.2. Automatisierung und Digitalisierung
Die Einführung von Industrie 4.0-Technologien und digitalisierten Steuerungssystemen ermöglicht eine präzisere Steuerung von Pulveröfen. Durch den Einsatz von künstlicher Intelligenz (KI) und maschinellem Lernen können Öfen lernen, wie sie den Energieverbrauch optimieren können, indem sie Muster in den Produktionsprozessen erkennen und automatisch Anpassungen vornehmen.
5.3. Integration von erneuerbaren Energiequellen
Zukünftige Pulveröfen könnten verstärkt auf erneuerbare Energiequellen setzen, wie z. B. Solarenergie oder Windkraft, um den Stromverbrauch zu reduzieren. Die Integration erneuerbarer Energien in den Produktionsprozess wird sowohl die Kosten senken als auch die Umweltbelastung reduzieren.
5.4. Thermoelektrische Generatoren
Eine weitere vielversprechende Technologie zur Reduzierung des Stromverbrauchs ist die Verwendung von thermoelektrischen Generatoren. Diese Systeme nutzen die Abwärme aus dem Ofen und wandeln sie in elektrische Energie um, die wieder in den Produktionsprozess eingespeist werden kann. Dies könnte den Stromverbrauch erheblich senken und die Gesamteffizienz des Ofens steigern.
Fazit
Pulveröfen sind ein unverzichtbares Werkzeug im Pulverbeschichtungsprozess und erfordern einen beträchtlichen Stromverbrauch, um die erforderlichen Temperaturen für den Aushärtungsprozess zu erreichen und aufrechtzuerhalten. Der Stromverbrauch eines Pulverofens hängt von verschiedenen Faktoren ab, darunter die Größe des Ofens, das Heizsystem, die Isolierung und die Auslastung. Elektrische Pulveröfen, gasbetriebene Systeme und Infrarotöfen bieten jeweils unterschiedliche Vorteile in Bezug auf Energieeffizienz und Betriebskosten.
Die Optimierung des Stromverbrauchs ist entscheidend, um die Betriebskosten zu senken und die Umweltbelastung zu reduzieren. Fortschritte in der Isolierung, Wärmerückgewinnung und intelligente Steuerungssysteme tragen dazu bei, den Energieverbrauch von Pulveröfen zu senken. Zukünftige Technologien wie erneuerbare Energien und thermoelektrische Generatoren versprechen, den Stromverbrauch weiter zu reduzieren und die Effizienz von Pulveröfen zu maximieren.
Insgesamt bietet die fortschreitende Entwicklung der Pulverofen-Technologie erhebliche Vorteile für die Pulverbeschichtungsindustrie, sowohl in Bezug auf die Kosten als auch auf die Umweltfreundlichkeit.
Kammerofen
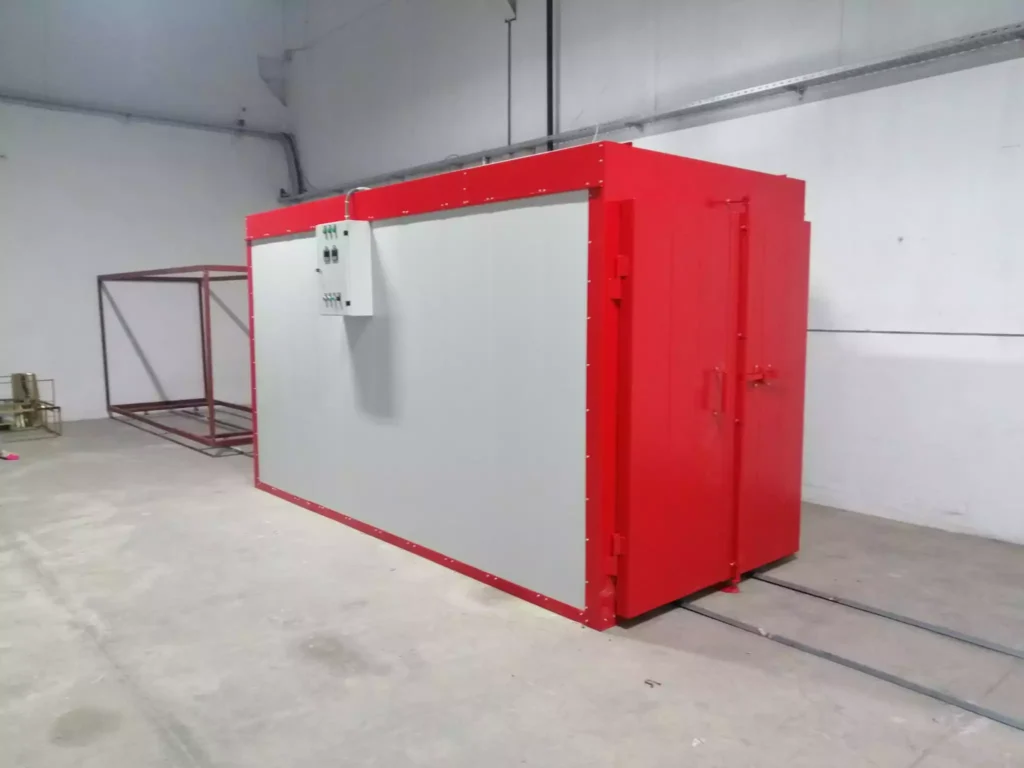
Ein Kammerofen ist ein wesentliches industrielles Werkzeug, das für eine Vielzahl von thermischen Prozessen wie das Härten, Brennen, Sintern und vor allem das Aushärten von Pulverbeschichtungen verwendet wird. In der Pulverbeschichtungsindustrie ist der Kammerofen ein integraler Bestandteil des Aushärtungsprozesses. Diese Öfen sind in der Lage, hohe Temperaturen zu erzeugen und aufrechtzuerhalten, wodurch die aufgebrachten Pulverlacke geschmolzen und vernetzt werden, um eine robuste und haltbare Oberfläche zu schaffen.
Einführung in den Kammerofen
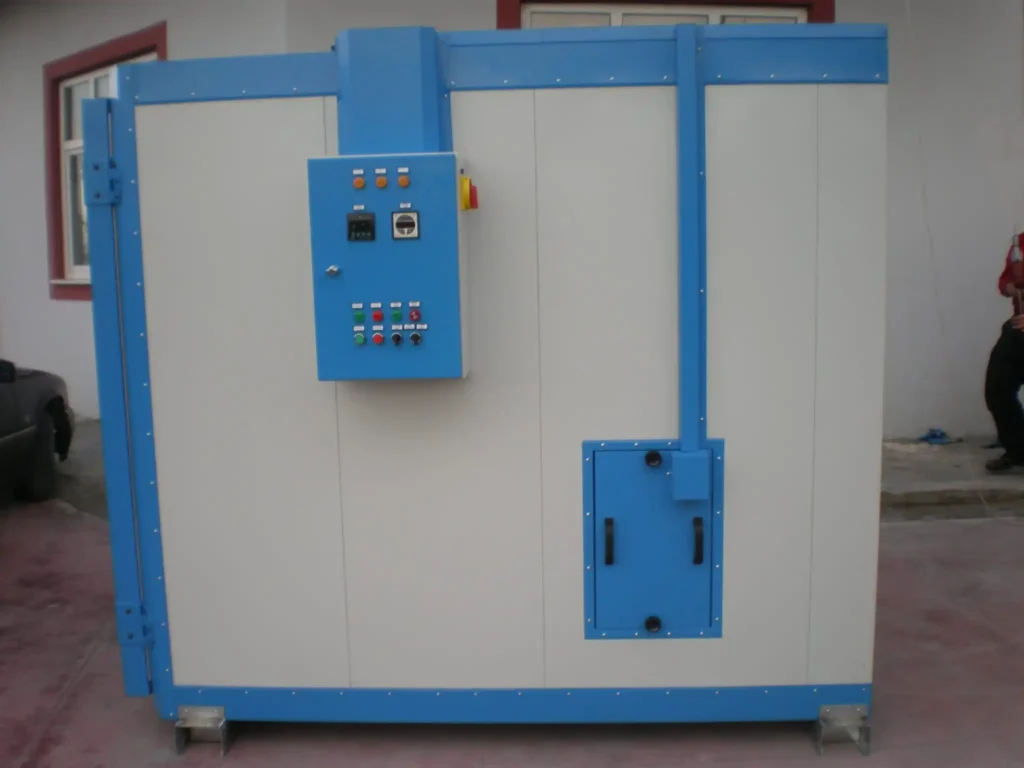
Ein Kammerofen ist ein industrieller Ofen, der einen geschlossenen Raum oder eine Kammer verwendet, um Werkstücke durch hohe Temperaturen zu verarbeiten. Der Kammerofen wird in vielen thermischen Prozessen wie dem Härten von Metall, der keramischen Verarbeitung, der Glasverarbeitung und besonders in der Pulverbeschichtungsindustrie eingesetzt, wo er zur Aushärtung von Pulverlacken dient.
1.1. Geschichte der Kammeröfen
Die Entwicklung von Kammeröfen reicht viele Jahrhunderte zurück, als Menschen erstmals die Fähigkeit entdeckten, Materialien durch kontrollierte Hitze zu verändern. Während in der Antike einfache Holz- und Steinkonstruktionen zur Metallverarbeitung genutzt wurden, führte die industrielle Revolution im 19. Jahrhundert zur Erfindung moderner Kammeröfen, die auf der Nutzung fossiler Brennstoffe und später elektrischer Energie basierten.
Moderne Kammeröfen haben sich im Laufe der Zeit weiterentwickelt und nutzen heute fortschrittliche Materialien und Technologien, um Energie effizient zu nutzen und gleichzeitig präzise Temperaturkontrollen zu ermöglichen.
Funktionsweise eines Kammerofens
Ein Kammerofen arbeitet durch die kontrollierte Erzeugung und Verteilung von Wärme in einer geschlossenen Kammer. Die gleichmäßige Wärmeverteilung ist entscheidend, um sicherzustellen, dass das gesamte Werkstück auf die gewünschte Temperatur erhitzt wird, ohne dass es zu Temperaturunterschieden kommt.
2.1. Erzeugung von Wärme
Die Wärme in einem Kammerofen wird entweder durch elektrische Heizelemente, Gasbrenner oder in einigen Fällen durch alternative Energiequellen wie Infrarotstrahler erzeugt. Elektrische Heizelemente bestehen in der Regel aus widerstandsfähigen Materialien wie Nickel-Chrom-Legierungen, die elektrischen Strom in Wärme umwandeln.
Gasbefeuerte Kammeröfen nutzen Erdgas oder Propan, um durch Verbrennung Hitze zu erzeugen, die dann im Ofen verteilt wird. Diese Öfen sind besonders in großindustriellen Anwendungen verbreitet, da sie in der Regel eine höhere Energieeffizienz bei größeren Volumina bieten.
2.2. Temperatursteuerung und -verteilung
Die Steuerung der Temperatur im Kammerofen erfolgt durch Thermostate und elektronische Steuerungssysteme, die sicherstellen, dass die gewünschte Temperatur konstant gehalten wird. Diese Systeme sind mit Sensoren ausgestattet, die die Ofentemperatur überwachen und das Heizsystem anpassen, um eine stabile Temperatur zu gewährleisten.
Ein gut konstruierter Kammerofen stellt sicher, dass die Wärme im gesamten Ofenraum gleichmäßig verteilt wird. Dies wird durch Konvektion erreicht, bei der ein Luftstrom durch den Ofen zirkuliert und so eine gleichmäßige Erwärmung des Werkstücks sicherstellt.
2.3. Aushärtung von Pulverbeschichtungen
In der Pulverbeschichtungsindustrie wird der Kammerofen verwendet, um das Pulver, das auf das Werkstück aufgetragen wurde, zu schmelzen und chemisch zu vernetzen. Der Pulverlack wird in der Regel bei Temperaturen von 150 bis 200 Grad Celsius ausgehärtet. Der Kammerofen stellt sicher, dass diese Temperaturen gleichmäßig im gesamten Ofen erreicht und aufrechterhalten werden, um eine homogene und widerstandsfähige Beschichtung zu erzielen.
Aufbau und Hauptkomponenten
Der Aufbau eines Kammerofens ist darauf ausgelegt, thermische Prozesse in einer kontrollierten Umgebung zu ermöglichen. Ein Kammerofen besteht aus verschiedenen wichtigen Komponenten, die zusammenarbeiten, um eine präzise und gleichmäßige Erwärmung zu gewährleisten.
3.1. Ofengehäuse und Isolierung
Das Ofengehäuse ist der äußere Teil des Kammerofens und besteht in der Regel aus Metall, das mit hitzebeständigen Materialien verkleidet ist. Die Ofenwände und -decken sind gut isoliert, um Wärmeverluste zu minimieren und eine konstante Temperatur im Inneren des Ofens aufrechtzuerhalten. Moderne Isolierungsmaterialien wie Keramikfasern und feuerfeste Ziegel helfen dabei, die Effizienz des Ofens zu maximieren.
3.2. Heizsystem
Das Heizsystem eines Kammerofens kann entweder elektrisch oder gasbetrieben sein. Elektrische Kammeröfen verwenden Widerstandsheizelemente, die elektrischen Strom in Wärme umwandeln. Gasbetriebene Kammeröfen nutzen Brenner, die Erdgas oder Propan verbrennen, um Hitze zu erzeugen.
Die Wahl des Heizsystems hängt von der Anwendung und den Anforderungen des Prozesses ab. Während elektrische Heizungen eine präzisere Temperaturregelung ermöglichen, sind gasbefeuerte Öfen in der Regel effizienter bei großindustriellen Anwendungen, die große Volumen verarbeiten müssen.
3.3. Steuerungseinheit
Die Steuerungseinheit ist das Gehirn des Kammerofens. Sie besteht aus Temperaturregelungssystemen, Thermostaten und Sicherheitsvorrichtungen, die sicherstellen, dass der Ofen sicher und effizient arbeitet. In modernen Kammeröfen werden oft digitale Steuerungssysteme verwendet, die eine genaue Kontrolle über die Ofentemperatur und die Aushärtezeit bieten.
3.4. Belüftung und Luftzirkulation
Ein weiteres wesentliches Element des Kammerofens ist das Luftzirkulationssystem. Dieses System sorgt dafür, dass die Wärme gleichmäßig im Ofen verteilt wird. Einige Kammeröfen verfügen über Ventilatoren, die die heiße Luft durch den Ofen leiten und eine gleichmäßige Erwärmung der Werkstücke sicherstellen. Dies ist besonders wichtig, um zu verhindern, dass bestimmte Bereiche des Werkstücks überhitzen oder unterhitzen.
3.5. Förder- und Transportsysteme
In industriellen Anwendungen kann ein Kammerofen mit Fördersystemen ausgestattet sein, um Werkstücke automatisch in den Ofen hinein und wieder heraus zu transportieren. Diese Systeme erhöhen die Effizienz und ermöglichen es, den Ofen in kontinuierlichen Produktionsprozessen zu verwenden. Schienensysteme, Transportbänder oder Hubvorrichtungen können je nach Anforderung des Produktionsprozesses verwendet werden.
Thermische Prozesse im Kammerofen
Kammeröfen werden für eine Vielzahl von thermischen Prozessen in unterschiedlichen Industrien verwendet. Jeder Prozess hat spezifische Temperaturanforderungen und Zeitrahmen, die durch den Kammerofen präzise gesteuert werden können.
4.1. Aushärtung von Pulverbeschichtungen
Der wichtigste Prozess in der Pulverbeschichtungsindustrie ist das Aushärten von Pulverlacken. Nachdem das Pulver elektrostatisch auf das Werkstück aufgetragen wurde, muss es im Kammerofen auf Temperaturen zwischen 150°C und 200°C erhitzt werden, um zu schmelzen und zu vernetzen. Der Kammerofen sorgt dafür, dass das Pulver gleichmäßig aushärtet und eine glatte, dauerhafte Oberfläche entsteht.
4.2. Härten von Metallen
Das Härten von Metallen ist ein weiterer wichtiger thermischer Prozess, der in Kammeröfen durchgeführt wird. Beim Härten werden Metalle auf hohe Temperaturen erhitzt und dann schnell abgekühlt, um ihre Festigkeit und Härte zu erhöhen. Der Kammerofen spielt hier eine entscheidende Rolle, da er eine präzise Temperaturkontrolle ermöglicht und den gesamten Prozess sicher und gleichmäßig durchführt.
4.3. Sintern
Das Sintern ist ein thermischer Prozess, bei dem pulverförmige Materialien unter hoher Hitze zu einem festen Stück verdichtet werden. In der Keramik- und Metallverarbeitung wird das Sintern verwendet, um aus pulverförmigen Rohstoffen feste Formen zu erzeugen. Der Kammerofen bietet die erforderliche gleichmäßige Hitzeverteilung, um sicherzustellen, dass die Pulver gleichmäßig gesintert werden.
4.4. Glasbearbeitung
In der Glasbearbeitung wird der Kammerofen verwendet, um Glas auf Temperaturen zu erhitzen, bei denen es formbar wird. Dieser Prozess wird oft als Glasblasen bezeichnet, bei dem der Kammerofen die Hitze liefert, die erforderlich ist, um das Glas zu schmelzen und in verschiedene Formen zu bringen.
4.5. Keramikbrennen
Das Brennen von Keramik erfordert präzise Temperaturkontrollen, um sicherzustellen, dass die Tonwaren gleichmäßig erhitzt werden und die gewünschten mechanischen Eigenschaften erhalten. Kammeröfen sind in der Lage, die hohen Temperaturen zu erreichen, die zum Brennen von Keramik erforderlich sind, und sorgen für eine gleichmäßige Wärmeverteilung im gesamten Ofen.
Verschiedene Arten von Kammeröfen

Es gibt verschiedene Arten von Kammeröfen, die jeweils für spezifische Anwendungen und Industrien ausgelegt sind. Die Wahl des richtigen Kammerofens hängt von den Anforderungen des thermischen Prozesses, der Materialart und den Produktionsvolumina ab.
5.1. Elektrische Kammeröfen
Elektrische Kammeröfen nutzen Widerstandsheizelemente, um die erforderliche Hitze zu erzeugen. Sie sind besonders beliebt in Laborumgebungen und in der Kleinproduktion, da sie eine präzise Temperatursteuerung und eine saubere Energiequelle bieten. Diese Öfen sind auch in Umgebungen mit begrenztem Zugang zu Gasquellen eine gute Wahl.
5.2. Gasbetriebene Kammeröfen
Gasbetriebene Kammeröfen werden häufig in großindustriellen Anwendungen eingesetzt, da sie kostengünstiger sind, wenn es um die Verarbeitung großer Mengen von Werkstücken geht. Gasbefeuerte Öfen nutzen Erdgas oder Propan als Energiequelle und sind oft effizienter als elektrische Öfen, insbesondere in großvolumigen Produktionslinien.
5.3. Infrarot-Kammeröfen
Infrarot-Kammeröfen nutzen Infrarotstrahlung, um die Wärme direkt auf das Werkstück zu übertragen, anstatt die Luft im Ofen zu erhitzen. Diese Technologie ermöglicht eine schnelle und effiziente Erwärmung des Werkstücks und wird häufig in der Pulverbeschichtungsindustrie verwendet, wo schnelle Aushärtezeiten erforderlich sind.
5.4. Hochtemperatur-Kammeröfen
Hochtemperatur-Kammeröfen sind speziell für Prozesse ausgelegt, die Temperaturen von über 1000°C erfordern, wie das Sintern von Metallen oder das Schmelzen von Glas. Diese Öfen sind mit speziellen Isoliermaterialien und Heizelementen ausgestattet, die extremen Temperaturen standhalten können.
5.5. Vakuum-Kammeröfen
Vakuum-Kammeröfen werden in Prozessen verwendet, bei denen die Materialien unter Vakuumbedingungen erhitzt werden müssen, um Oxidation zu vermeiden. Diese Öfen finden Anwendung in der Metallverarbeitung und in der Herstellung von Hochleistungskeramiken, wo eine kontrollierte Atmosphäre entscheidend für die Qualität des Endprodukts ist.
Anwendungen in der Industrie
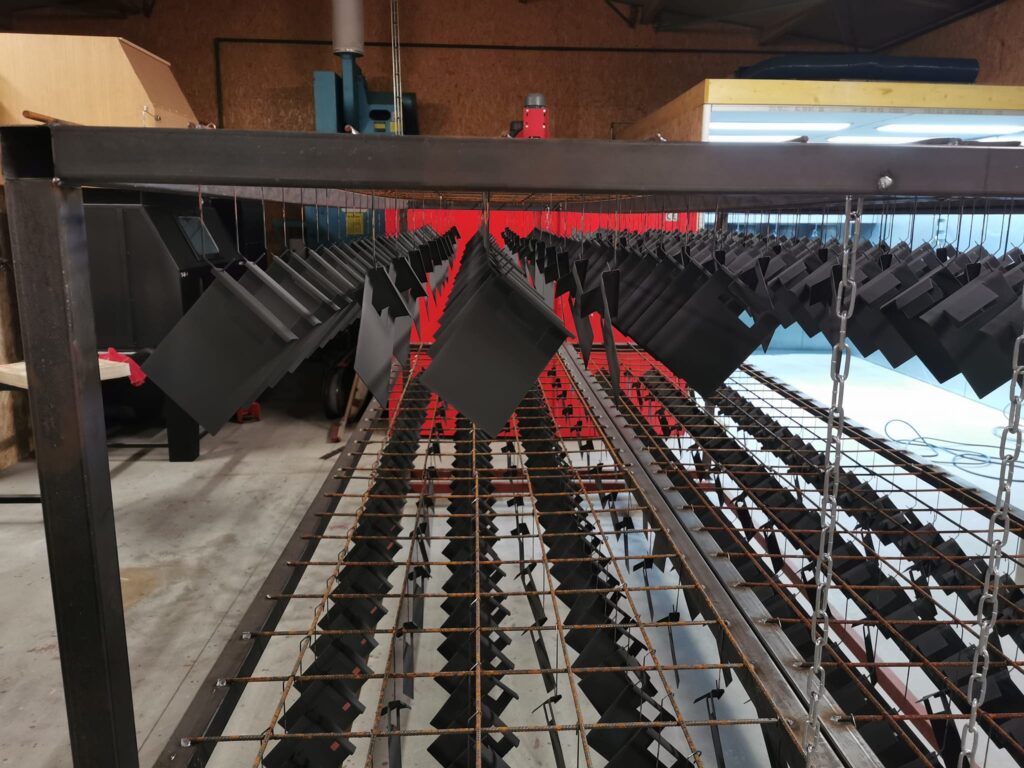
Kammeröfen werden in vielen verschiedenen Industriezweigen eingesetzt, da sie vielseitig einsetzbar und für eine Vielzahl von thermischen Prozessen geeignet sind.
6.1. Automobilindustrie
In der Automobilindustrie werden Kammeröfen verwendet, um Metallteile zu härten, zu sintern und Pulverbeschichtungen auf Fahrzeugteilen wie Karosserien, Fahrgestellen und Felgen aufzutragen. Der Aushärteprozess stellt sicher, dass diese Teile langlebig, korrosionsbeständig und optisch ansprechend sind.
6.2. Metallverarbeitung
In der Metallverarbeitungsindustrie spielen Kammeröfen eine entscheidende Rolle beim Härten, Anlassen und Sintern von Metallen. Diese Prozesse verbessern die mechanischen Eigenschaften der Metalle, wie Festigkeit, Härte und Verschleißfestigkeit, und sind entscheidend für die Herstellung von Werkzeugen, Maschinenkomponenten und Baugeräten.
6.3. Bauindustrie
Kammeröfen werden in der Bauindustrie für die Herstellung von Keramikfliesen, Ziegeln und anderen Baumaterialien verwendet. Das Brennen dieser Materialien in Kammeröfen stellt sicher, dass sie die erforderliche Festigkeit und Witterungsbeständigkeit aufweisen.
6.4. Elektronik- und Halbleiterindustrie
In der Elektronik- und Halbleiterindustrie werden Kammeröfen verwendet, um Halbleitermaterialien zu erhitzen und spezielle thermische Behandlungen durchzuführen, die für die Herstellung von Mikroprozessoren und anderen elektronischen Komponenten erforderlich sind. Vakuum-Kammeröfen sind besonders in dieser Branche wichtig, da sie Oxidation verhindern und eine präzise Steuerung der thermischen Bedingungen ermöglichen.
6.5. Luft- und Raumfahrtindustrie
Die Luft- und Raumfahrtindustrie verwendet Kammeröfen, um Materialien wie Titan und hochfeste Legierungen zu verarbeiten, die in Flugzeug- und Raumfahrzeugen verwendet werden. Diese Materialien müssen extremen Temperaturen und Drücken standhalten, und die thermische Behandlung in Kammeröfen stellt sicher, dass sie den hohen Belastungen gerecht werden.
6.6. Möbelherstellung und Pulverbeschichtung
In der Möbelindustrie werden Kammeröfen zur Pulverbeschichtung von Metallrahmen und Möbelteilen verwendet, um sie gegen Kratzer, Korrosion und Witterungseinflüsse zu schützen. Dieser Prozess verleiht den Möbeln nicht nur eine ästhetisch ansprechende Oberfläche, sondern erhöht auch ihre Lebensdauer und Widerstandsfähigkeit.
Effizienz und Energieeinsparung
Da Kammeröfen hohe Temperaturen erzeugen und oft über lange Zeiträume betrieben werden, ist die Energieeffizienz ein entscheidender Faktor, um Betriebskosten zu senken und die Umweltbelastung zu reduzieren. Moderne Kammeröfen sind mit Technologien ausgestattet, die den Energieverbrauch optimieren.
7.1. Ofenisolierung
Eine hochwertige Isolierung ist entscheidend, um Wärmeverluste zu minimieren und den Energieverbrauch zu senken. Die Verwendung von Materialien wie Keramikfasern und feuerfesten Ziegeln sorgt dafür, dass die Wärme im Inneren des Ofens gespeichert wird, was zu einer gleichmäßigeren Erwärmung und einer geringeren Notwendigkeit für ständiges Nachheizen führt.
7.2. Wärmerückgewinnungssysteme
Wärmerückgewinnungssysteme sind eine effiziente Möglichkeit, die Abwärme des Ofens zu nutzen. Diese Systeme fangen die Abwärme auf und verwenden sie, um den Ofen zu beheizen oder andere thermische Prozesse in der Anlage zu unterstützen, wodurch der Energieverbrauch und die Betriebskosten gesenkt werden.
7.3. Intelligente Steuerungssysteme
Moderne Kammeröfen sind mit intelligenten Steuerungssystemen ausgestattet, die den Aushärteprozess überwachen und anpassen. Diese Systeme können die Ofentemperatur dynamisch regulieren, um sicherzustellen, dass der Energieverbrauch auf ein Minimum reduziert wird, ohne die Qualität des thermischen Prozesses zu beeinträchtigen.
7.4. Optimierung der Produktionsplanung
Eine effiziente Auslastung des Kammerofens ist entscheidend, um Energie zu sparen. Produktionsplanungssysteme, die den Ofen optimal beladen und ihn kontinuierlich betreiben, reduzieren den Energieverbrauch pro Werkstück. Der Betrieb des Ofens bei Teilladungen führt zu höheren Betriebskosten, da der Ofen trotzdem die volle Energie benötigt, um die erforderliche Temperatur zu halten.
Wartung und Pflege eines Kammerofens
Die regelmäßige Wartung eines Kammerofens ist entscheidend, um seine Effizienz zu erhalten und Ausfälle zu vermeiden. Eine gut gewartete Anlage sorgt nicht nur für eine längere Lebensdauer des Ofens, sondern auch für eine gleichbleibend hohe Qualität der thermischen Prozesse.
8.1. Reinigung des Ofens
Regelmäßige Reinigung der Innenwände und des Luftzirkulationssystems ist wichtig, um Ablagerungen zu vermeiden, die die Wärmeverteilung stören könnten. Dies gilt besonders in der Pulverbeschichtungsindustrie, wo überschüssiges Pulver oder Rückstände an den Ofenwänden haften können.
8.2. Überprüfung der Heizelemente
Die Heizelemente eines Kammerofens sollten regelmäßig überprüft werden, um sicherzustellen, dass sie ordnungsgemäß funktionieren und gleichmäßige Wärme erzeugen. Defekte oder abgenutzte Heizelemente können zu ungleichmäßiger Erwärmung und höheren Betriebskosten führen.
8.3. Isolierungskontrolle
Die Isolierung des Ofens sollte regelmäßig überprüft werden, um sicherzustellen, dass keine Wärme durch Risse oder beschädigte Bereiche entweicht. Eine beschädigte Isolierung erhöht den Energieverbrauch und kann die Effizienz des Ofens erheblich beeinträchtigen.
8.4. Wartung der Steuerungssysteme
Die Steuerungssysteme des Kammerofens sollten regelmäßig kalibriert werden, um sicherzustellen, dass die Temperaturregelung präzise und zuverlässig funktioniert. Auch die Sensoren und Thermostate sollten regelmäßig überprüft und gewartet werden, um eine konstante und genaue Temperaturkontrolle zu gewährleisten.
Zukunftstechnologien und Innovationen
Die Technologie der Kammeröfen entwickelt sich ständig weiter, um den Anforderungen der modernen Industrie gerecht zu werden. Neue Materialien, effizientere Heizsysteme und digitale Steuerungstechnologien haben das Potenzial, die Effizienz und Leistung von Kammeröfen weiter zu verbessern.
9.1. Einsatz von erneuerbaren Energien
Die Integration von erneuerbaren Energien wie Solar- oder Windenergie in den Betrieb von Kammeröfen könnte in Zukunft eine wichtige Rolle spielen. Diese Technologien könnten den Energieverbrauch der Öfen erheblich senken und gleichzeitig die Umweltbelastung verringern.
9.2. Fortschritte in der Materialwissenschaft
Neue Materialien für die Ofenisolierung und Heizelemente, wie Nanomaterialien oder hitzebeständige Verbundstoffe, könnten dazu beitragen, die Effizienz von Kammeröfen zu verbessern, indem sie die Wärmeverluste weiter minimieren und die Lebensdauer der Heizelemente verlängern.
9.3. Digitalisierung und Automatisierung
Die fortschreitende Digitalisierung und Automatisierung in der Industrie ermöglicht es, Kammeröfen präziser zu steuern und ihren Energieverbrauch zu optimieren. Künstliche Intelligenz (KI) und maschinelles Lernen könnten eingesetzt werden, um den Aushärteprozess zu überwachen und Anpassungen in Echtzeit vorzunehmen, um Energie zu sparen und die Produktivität zu steigern.
9.4. Entwicklung von Hybridöfen
Hybridöfen, die verschiedene Heiztechnologien wie Gas, Elektrizität und Infrarotstrahlung kombinieren, könnten die Flexibilität und Effizienz von Kammeröfen erhöhen. Diese Öfen könnten in der Lage sein, verschiedene Materialien und Prozesse zu optimieren, indem sie die jeweils effizienteste Heizmethode verwenden.
Fazit
Der Kammerofen ist ein unverzichtbares Werkzeug in der modernen Industrie, das für eine Vielzahl von thermischen Prozessen wie das Aushärten von Pulverbeschichtungen, das Härten von Metallen und das Brennen von Keramik verwendet wird. Die Fähigkeit des Kammerofens, präzise Temperaturen aufrechtzuerhalten und thermische Prozesse effizient zu steuern, macht ihn zu einem zentralen Element in der Produktion vieler Industriezweige.
Durch technologische Fortschritte wie verbesserte Isolierung, Wärmerückgewinnungssysteme und intelligente Steuerungssysteme konnte der Energieverbrauch von Kammeröfen optimiert werden, was zu niedrigeren Betriebskosten und einer höheren Produktivität geführt hat. In Zukunft könnten erneuerbare Energien, neue Materialien und die zunehmende Digitalisierung den Kammerofen noch effizienter und umweltfreundlicher machen.
Die fortschreitende Entwicklung dieser Technologie zeigt, dass der Kammerofen auch in den kommenden Jahrzehnten eine entscheidende Rolle in der Industrie spielen wird.
Pulverofen mit Schienen
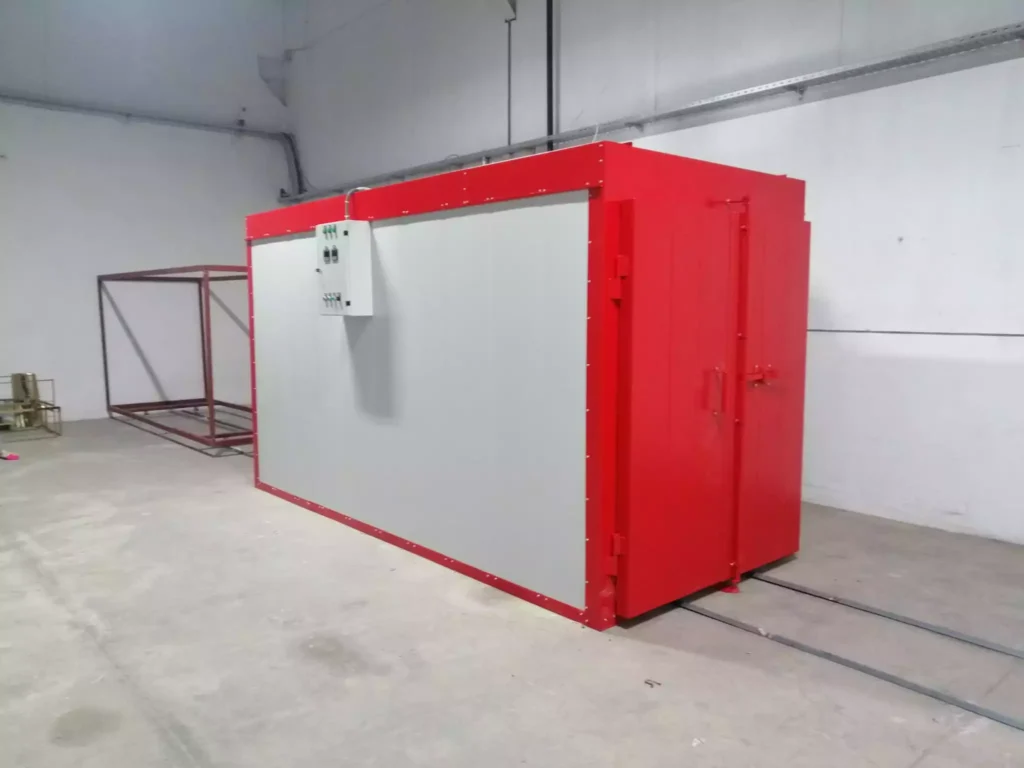
Ein Pulverofen mit Schienen ist eine spezialisierte industrielle Anlage, die in der Pulverbeschichtungsindustrie weit verbreitet ist. Diese Öfen werden verwendet, um Werkstücke, die mit Pulverlacken beschichtet wurden, durch kontrollierte Hitze auszuhärten. Die Besonderheit eines Pulverofens mit Schienen ist, dass er ein internes Schienensystem besitzt, das den Transport der Werkstücke durch den Ofen erleichtert. Dies ist besonders vorteilhaft in der Großproduktion, wo Effizienz, Konsistenz und ein reibungsloser Materialfluss entscheidend sind.
In diesem umfassenden Text werden alle Aspekte eines Pulverofens mit Schienen untersucht, darunter der Aufbau, die Funktionsweise, die verschiedenen Arten von Schienensystemen, die thermischen Prozesse im Ofen, die Effizienzsteigerung, die Wartung, Anwendungen in der Industrie sowie technologische Innovationen. Ziel ist es, ein detailliertes Verständnis dieser wichtigen Technologie zu vermitteln.
Einführung in den Pulverofen mit Schienen
Ein Pulverofen ist eine thermische Anlage, die speziell dafür konzipiert ist, Werkstücke zu erhitzen, um aufgebrachte Pulverbeschichtungen auszuhärten. In der Pulverbeschichtungsindustrie spielen diese Öfen eine zentrale Rolle, da sie es ermöglichen, die Pulverbeschichtungen zu einer dauerhaften, widerstandsfähigen und gleichmäßigen Oberfläche zu verarbeiten. Ein Pulverofen mit Schienen ist eine Variante, bei der ein internes Schienensystem verwendet wird, um den Transport von Werkstücken durch den Ofen zu erleichtern. Dies ist besonders in kontinuierlichen Produktionslinien von Vorteil, wo Werkstücke automatisch durch den Ofen geführt werden, um den Produktionsprozess zu optimieren.
1.1. Bedeutung der Pulverbeschichtung
Die Pulverbeschichtung ist ein weit verbreitetes Verfahren zur Oberflächenveredelung, das sowohl in der Automobil-, Bau- als auch Möbelindustrie Anwendung findet. Es handelt sich um ein umweltfreundliches Verfahren, da es keine Lösungsmittel verwendet und Abfälle minimiert, da überschüssiges Pulver zurückgewonnen und wiederverwendet werden kann. Pulverbeschichtungen bieten hervorragenden Schutz gegen Korrosion, chemische Einflüsse, Kratzer und Witterungseinflüsse und können zudem in einer Vielzahl von Farben und Texturen angewendet werden.
Der Prozess der Pulverbeschichtung ist jedoch erst nach der Aushärtung im Pulverofen abgeschlossen, da das aufgebrachte Pulver bei hohen Temperaturen schmelzen und sich chemisch vernetzen muss, um eine feste, haltbare Schicht zu bilden.
Aufbau eines Pulverofens mit Schienen
Ein Pulverofen mit Schienen ist komplex aufgebaut und besteht aus mehreren Komponenten, die zusammenarbeiten, um eine gleichmäßige Erwärmung und einen reibungslosen Transport der Werkstücke zu gewährleisten.
2.1. Grundlegende Komponenten eines Pulverofens
Ein Pulverofen besteht aus mehreren wesentlichen Komponenten, die den gesamten Aushärteprozess unterstützen:
- Heizelemente: Die Heizelemente können elektrisch oder gasbefeuert sein und erzeugen die notwendige Wärme, um das Pulver auf den Werkstücken zu schmelzen und auszuhärten.
- Luftzirkulationssystem: Ein gutes Luftzirkulationssystem sorgt dafür, dass die heiße Luft gleichmäßig im Ofen verteilt wird, um eine gleichmäßige Erwärmung der Werkstücke zu gewährleisten.
- Isolierung: Die Wände des Ofens sind mit speziellen feuerfesten Materialien isoliert, um den Wärmeverlust zu minimieren und die Energieeffizienz zu maximieren.
- Steuerungssysteme: Moderne Pulveröfen sind mit fortschrittlichen Steuerungssystemen ausgestattet, die es ermöglichen, Temperatur, Zeit und andere Parameter präzise zu regulieren. Diese Systeme überwachen kontinuierlich den Zustand des Ofens und passen die Heizleistung entsprechend an.
2.2. Schienensystem im Pulverofen
Das Schienensystem ist das zentrale Merkmal, das einen Pulverofen mit Schienen von anderen Ofentypen unterscheidet. Es besteht aus Schienen oder Gleisen, die innerhalb des Ofens installiert sind und auf denen Werkstücke entweder manuell oder automatisch durch den Ofen transportiert werden. Schienensysteme können auf verschiedene Arten ausgelegt sein, je nach Größe und Form der Werkstücke und den spezifischen Anforderungen der Produktion.
- Deckenschienen: Bei dieser Variante sind die Schienen an der Decke des Ofens angebracht, und die Werkstücke hängen an Haken oder Vorrichtungen, die entlang der Schienen gleiten. Diese Konfiguration ermöglicht eine effiziente Nutzung des vertikalen Raums des Ofens.
- Bodenschienen: Bodenschienen befinden sich auf dem Ofenboden, und die Werkstücke werden auf Wagen oder Plattformen platziert, die auf den Schienen durch den Ofen bewegt werden. Diese Variante ist besonders vorteilhaft für große oder schwere Werkstücke, die schwer zu handhaben sind.
- Fördersysteme: Einige Schienensysteme sind mit automatischen Fördersystemen ausgestattet, die es ermöglichen, die Werkstücke kontinuierlich durch den Ofen zu transportieren, ohne dass manueller Eingriff erforderlich ist. Diese Systeme sind ideal für Produktionslinien mit hohem Durchsatz.
Funktionsweise eines Pulverofens mit Schienen
Ein Pulverofen mit Schienen arbeitet durch die kontrollierte Erzeugung und Verteilung von Wärme, um aufgebrachte Pulverbeschichtungen auszuhärten. Der Aushärteprozess ist entscheidend, um die Haltbarkeit und Widerstandsfähigkeit der Beschichtung zu gewährleisten.
3.1. Aushärteprozess
Der Aushärteprozess in einem Pulverofen mit Schienen beginnt, nachdem das Pulver auf das Werkstück aufgetragen wurde. Das Werkstück wird über das Schienensystem in den Ofen transportiert, wo es auf die notwendige Temperatur erhitzt wird. Typische Aushärtetemperaturen liegen zwischen 150°C und 220°C, abhängig von der Art des Pulvers und des Materials des Werkstücks.
Während des Aushärteprozesses schmilzt das Pulver und vernetzt sich chemisch, wodurch eine feste, gleichmäßige und glatte Beschichtung entsteht. Die Dauer des Aushärtungsprozesses hängt von der Dicke der Beschichtung und der Größe des Werkstücks ab. Kleinere Werkstücke können in wenigen Minuten ausgehärtet werden, während größere Teile eine längere Zeit im Ofen benötigen.
3.2. Temperaturkontrolle
Die Temperatur im Pulverofen wird durch fortschrittliche Steuerungssysteme überwacht und reguliert. Es ist wichtig, dass die Temperatur während des gesamten Aushärteprozesses konstant bleibt, um eine gleichmäßige Beschichtung zu gewährleisten. Schwankungen in der Temperatur können zu einer ungleichmäßigen Aushärtung führen, was die Qualität der Beschichtung beeinträchtigen kann.
3.3. Transport der Werkstücke
Das Schienensystem ermöglicht einen reibungslosen Transport der Werkstücke durch den Ofen. Bei einem kontinuierlichen Betrieb können Werkstücke nahtlos in den Ofen befördert werden, ohne dass der Aushärteprozess unterbrochen wird. Dies sorgt für eine hohe Effizienz und reduziert Ausfallzeiten in der Produktion.
Ein weiterer Vorteil des Schienensystems ist die Fähigkeit, schwere oder große Werkstücke einfach zu handhaben. Während der Ofen in Betrieb ist, können die Werkstücke auf den Schienen bewegt werden, was den manuellen Arbeitsaufwand verringert und das Risiko von Beschädigungen minimiert.
Vorteile eines Pulverofens mit Schienen
Die Verwendung eines Pulverofens mit Schienen bietet zahlreiche Vorteile gegenüber herkömmlichen Kammeröfen oder anderen Ofentypen. Diese Vorteile betreffen nicht nur die Effizienz und Flexibilität, sondern auch die Qualität der Aushärtung und die Handhabung großer und schwerer Werkstücke.
4.1. Effizienz und Zeitersparnis
Ein Pulverofen mit Schienen ermöglicht eine kontinuierliche Produktion, da die Werkstücke automatisch durch den Ofen transportiert werden. Dies spart Zeit und erhöht die Effizienz, da keine manuellen Arbeitsschritte erforderlich sind, um die Werkstücke in den Ofen zu laden oder zu entladen. Darüber hinaus kann der Aushärteprozess optimiert werden, da die Werkstücke in einer festen Reihenfolge durch den Ofen bewegt werden, was zu einer gleichmäßigeren Erwärmung und Aushärtung führt.
4.2. Verbesserte Handhabung schwerer Werkstücke
Für große und schwere Werkstücke, wie sie oft in der Bau-, Automobil- oder Maschinenbauindustrie vorkommen, bietet das Schienensystem eine einfache und sichere Handhabung. Anstatt die Werkstücke manuell in den Ofen zu transportieren, können sie auf Wagen oder Plattformen geladen werden, die auf den Schienen durch den Ofen rollen. Dies reduziert die körperliche Belastung für die Arbeiter und minimiert das Risiko von Beschädigungen an den Werkstücken während des Transports.
4.3. Flexibilität und Anpassungsfähigkeit
Ein Pulverofen mit Schienen kann flexibel an verschiedene Produktionsanforderungen angepasst werden. Das Schienensystem kann so konfiguriert werden, dass es sowohl kleine als auch große Werkstücke aufnehmen kann, und es kann leicht in bestehende Produktionslinien integriert werden. Diese Flexibilität ermöglicht es, den Ofen für eine Vielzahl von Anwendungen in verschiedenen Industrien zu nutzen.
4.4. Gleichmäßige Aushärtung
Dank der effizienten Luftzirkulation und Temperaturkontrolle im Pulverofen wird eine gleichmäßige Aushärtung der Pulverbeschichtung gewährleistet. Das Schienensystem sorgt dafür, dass die Werkstücke gleichmäßig durch den Ofen bewegt werden, wodurch die Gefahr von Überhitzung oder Unterhitzung bestimmter Bereiche des Werkstücks minimiert wird.
4.5. Reduzierung von Stillstandszeiten
In kontinuierlichen Produktionslinien, in denen der Betrieb nicht unterbrochen werden darf, hilft ein Pulverofen mit Schienen, Ausfallzeiten zu minimieren. Da Werkstücke ohne Unterbrechung durch den Ofen transportiert werden, bleibt der Produktionsprozess konstant, was die Produktivität steigert.
Arten von Schienensystemen in Pulveröfen
Es gibt verschiedene Arten von Schienensystemen, die in Pulveröfen eingesetzt werden, um den Transport der Werkstücke zu erleichtern. Die Wahl des richtigen Systems hängt von den spezifischen Anforderungen der Produktion ab, wie der Größe und Form der Werkstücke, dem Durchsatz und der Art der Beschichtungen.
5.1. Deckenschienensysteme
Ein Deckenschienensystem ist besonders vorteilhaft, wenn der vertikale Raum des Ofens optimal genutzt werden soll. Bei dieser Konfiguration sind die Schienen an der Decke des Ofens befestigt, und die Werkstücke werden an Haken aufgehängt, die entlang der Schienen gleiten. Diese Art von Schienensystem wird häufig in der Automobil- und Möbelindustrie verwendet, wo Werkstücke wie Türen, Felgen oder Metallrahmen effizient durch den Ofen transportiert werden können.
Vorteile des Deckenschienensystems:
- Maximale Raumnutzung, da der vertikale Raum des Ofens genutzt wird
- Geeignet für Werkstücke, die an Haken aufgehängt werden können
- Ermöglicht eine gleichmäßige Aushärtung von allen Seiten des Werkstücks
5.2. Bodenschienensysteme
Bei einem Bodenschienensystem sind die Schienen auf dem Boden des Ofens installiert, und die Werkstücke werden auf Plattformen oder Wagen platziert, die auf den Schienen durch den Ofen rollen. Diese Art von Schienensystem ist besonders nützlich für große, schwere oder sperrige Werkstücke, die schwer zu handhaben sind, wie z. B. Maschinenteile, Fahrzeugkarosserien oder Baukomponenten.
Vorteile des Bodenschienensystems:
- Einfacher Transport großer und schwerer Werkstücke
- Stabiler Transport, der das Risiko von Beschädigungen minimiert
- Ideal für sperrige Werkstücke, die nicht an Haken aufgehängt werden können
5.3. Automatisierte Fördersysteme
Automatisierte Fördersysteme sind die fortschrittlichste Art von Schienensystemen und ermöglichen einen vollständig automatisierten Betrieb des Pulverofens. Diese Systeme verwenden Motoren, Sensoren und Steuerungen, um die Werkstücke automatisch durch den Ofen zu transportieren. Der Hauptvorteil eines automatisierten Fördersystems ist die hohe Effizienz, da der Prozess ohne menschliches Eingreifen abläuft.
Vorteile automatisierter Fördersysteme:
- Vollständig automatisierter Betrieb, der den manuellen Arbeitsaufwand minimiert
- Erhöhte Produktionsgeschwindigkeit und Effizienz
- Präzise Steuerung der Bewegung der Werkstücke durch den Ofen
Thermische Prozesse in einem Pulverofen mit Schienen
Ein Pulverofen mit Schienen führt eine Reihe von thermischen Prozessen durch, um Pulverbeschichtungen auszuhärten. Diese Prozesse müssen präzise gesteuert werden, um die gewünschte Qualität der Beschichtung zu gewährleisten.
6.1. Aushärtung von Pulverbeschichtungen
Der Hauptprozess, der in einem Pulverofen mit Schienen durchgeführt wird, ist das Aushärten von Pulverbeschichtungen. Die aufgebrachten Pulverlacke bestehen aus feinen Partikeln, die bei hohen Temperaturen schmelzen und sich chemisch zu einer festen Schicht vernetzen. Während dieses Prozesses wird das Werkstück auf die erforderliche Temperatur erhitzt, wobei die Wärme gleichmäßig über die gesamte Oberfläche verteilt wird.
6.2. Temperaturverteilung und Luftzirkulation
Die Temperaturverteilung im Ofen ist entscheidend, um eine gleichmäßige Aushärtung der Pulverbeschichtung zu gewährleisten. Ein effizientes Luftzirkulationssystem sorgt dafür, dass die heiße Luft gleichmäßig im gesamten Ofen verteilt wird. Dies minimiert das Risiko von Temperaturunterschieden im Ofen, die zu ungleichmäßigen Beschichtungen führen könnten.
6.3. Präzise Temperatursteuerung
Die Temperatur im Pulverofen wird durch fortschrittliche Steuerungssysteme überwacht und geregelt. Diese Systeme verwenden Sensoren, um die Temperatur an verschiedenen Stellen im Ofen zu messen, und passen die Heizleistung automatisch an, um sicherzustellen, dass die Temperatur konstant bleibt. Präzise Temperaturkontrollen sind entscheidend für eine gleichmäßige Aushärtung und die Vermeidung von Überhitzung oder Unterhitzung der Werkstücke.
Effizienzsteigerung und Energieeinsparung
Pulveröfen mit Schienen sind so konstruiert, dass sie den Energieverbrauch minimieren und gleichzeitig eine hohe Effizienz bieten. Es gibt mehrere Strategien und Technologien, die zur Steigerung der Effizienz und zur Reduzierung des Energieverbrauchs in Pulveröfen eingesetzt werden.
7.1. Hochwertige Isolierung
Eine hochwertige Isolierung ist entscheidend, um Wärmeverluste zu minimieren und den Energieverbrauch zu senken. Die Wände des Ofens sind mit feuerfesten Materialien isoliert, die verhindern, dass Wärme nach außen entweicht. Dies sorgt nicht nur für eine konstante Temperatur im Ofen, sondern reduziert auch die Energiemenge, die benötigt wird, um den Ofen auf die erforderliche Temperatur zu bringen und diese aufrechtzuerhalten.
7.2. Wärmerückgewinnung
Wärmerückgewinnungssysteme sind eine effektive Möglichkeit, den Energieverbrauch in einem Pulverofen zu reduzieren. Diese Systeme fangen die Abwärme des Ofens auf und nutzen sie, um andere thermische Prozesse zu unterstützen oder um den Ofen wieder zu beheizen. Durch die Wiederverwendung von Abwärme kann der Gesamtenergieverbrauch um bis zu 30% gesenkt werden.
7.3. Automatisierung und Prozessoptimierung
Automatisierte Fördersysteme und intelligente Steuerungssysteme tragen ebenfalls zur Energieeinsparung bei, indem sie den Aushärteprozess optimieren und den Ofenbetrieb dynamisch an die Produktionsanforderungen anpassen. Diese Systeme können den Energieverbrauch senken, indem sie den Ofen in den Standby-Modus versetzen, wenn keine Werkstücke vorhanden sind, und die Heizleistung anpassen, um den Betrieb effizienter zu gestalten.
Wartung und Pflege eines Pulverofens mit Schienen
Die regelmäßige Wartung eines Pulverofens mit Schienen ist entscheidend, um eine langfristige Effizienz und eine gleichbleibende Qualität der Aushärtung zu gewährleisten.
8.1. Reinigung des Schienensystems
Das Schienensystem im Ofen muss regelmäßig gereinigt werden, um sicherzustellen, dass die Werkstücke reibungslos durch den Ofen bewegt werden können. Ablagerungen von Pulver oder anderen Materialien können die Bewegung der Wagen oder Haken behindern und den Produktionsprozess stören.
8.2. Überprüfung der Heizelemente
Die Heizelemente sollten regelmäßig überprüft und gewartet werden, um sicherzustellen, dass sie ordnungsgemäß funktionieren und gleichmäßige Wärme erzeugen. Defekte Heizelemente können zu ungleichmäßigen Temperaturen und einer schlechten Aushärtung der Beschichtungen führen.
8.3. Kalibrierung der Steuerungssysteme
Die Steuerungssysteme des Ofens sollten regelmäßig kalibriert werden, um sicherzustellen, dass die Temperaturregulierung präzise funktioniert. Eine ungenaue Temperaturkontrolle kann zu Überhitzung oder Unterhitzung der Werkstücke führen, was die Qualität der Beschichtung beeinträchtigen kann.
Anwendungen eines Pulverofens mit Schienen in der Industrie
Pulveröfen mit Schienen finden in einer Vielzahl von Industrien Anwendung, da sie eine effiziente und gleichmäßige Aushärtung von Pulverbeschichtungen ermöglichen.
9.1. Automobilindustrie
In der Automobilindustrie werden Pulveröfen mit Schienen zur Aushärtung von Beschichtungen auf Fahrzeugkarosserien, Felgen, Fahrgestellen und anderen Bauteilen verwendet. Die kontinuierliche Produktion und die Fähigkeit, große Werkstücke zu handhaben, machen diese Öfen ideal für die Automobilproduktion.
9.2. Bauindustrie
In der Bauindustrie werden Pulveröfen mit Schienen zur Beschichtung von großen Metallstrukturen, Stahlträgern und Fassadenelementen verwendet. Die Fähigkeit, große und schwere Werkstücke effizient zu transportieren und auszuhärten, ist besonders vorteilhaft in dieser Branche.
9.3. Möbelherstellung
Die Möbelindustrie verwendet Pulveröfen mit Schienen, um Metallrahmen und andere Möbelteile zu beschichten. Diese Öfen bieten eine gleichmäßige Aushärtung und ermöglichen es, große Mengen an Werkstücken schnell und effizient zu verarbeiten.
Zukunftstechnologien und Innovationen
Die Technologie der Pulveröfen mit Schienen entwickelt sich ständig weiter, um den Anforderungen der modernen Industrie gerecht zu werden.
10.1. Verbesserte Schienensysteme
Die Entwicklung von leichteren und langlebigeren Schienensystemen könnte den Energieverbrauch weiter reduzieren und die Effizienz der Werkstückhandhabung verbessern.
10.2. Integration von erneuerbaren Energien
Zukünftig könnten Pulveröfen vermehrt auf erneuerbare Energien wie Solar- oder Windenergie setzen, um den Energieverbrauch zu reduzieren und die Umweltbelastung zu minimieren.
10.3. Künstliche Intelligenz und Automatisierung
Die Integration von künstlicher Intelligenz (KI) und maschinellem Lernen in die Steuerungssysteme der Öfen könnte den Aushärteprozess weiter optimieren und den Energieverbrauch weiter senken.
Fazit
Ein Pulverofen mit Schienen ist ein leistungsfähiges Werkzeug in der Pulverbeschichtungsindustrie, das Effizienz, Flexibilität und Qualität kombiniert. Die Fähigkeit, Werkstücke effizient durch den Ofen zu transportieren, verbessert die Produktivität und sorgt für eine gleichmäßige Aushärtung. Mit fortschrittlichen Schienensystemen, Automatisierungstechnologien und energieeffizienten Lösungen spielen Pulveröfen mit Schienen eine entscheidende Rolle in der modernen industriellen Fertigung. Die kontinuierliche Weiterentwicklung der Technologie verspricht, dass diese Öfen auch in Zukunft eine wichtige Rolle in vielen Produktionsprozessen spielen werden.
Pulverofen mit Schienen im Boden
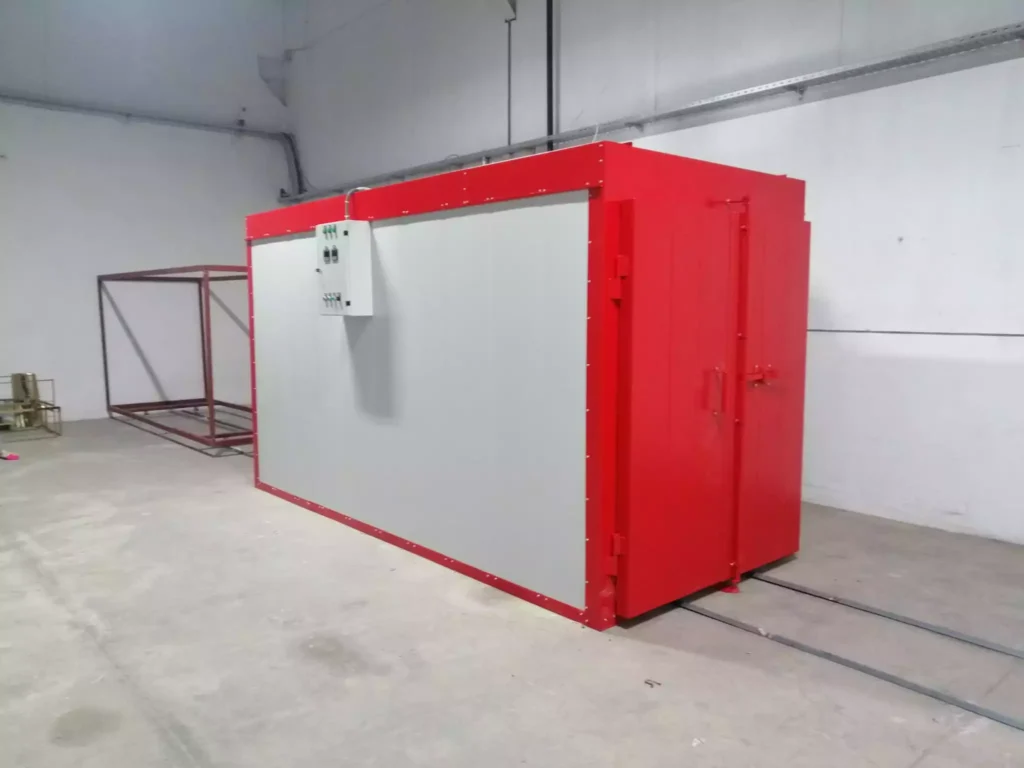
Ein Pulverofen mit Schienen im Boden ist ein fortschrittliches industrielles Gerät, das speziell für den Einsatz in der Pulverbeschichtungsindustrie entwickelt wurde. Diese Art von Ofen ist besonders für Produktionslinien geeignet, in denen große oder schwere Werkstücke kontinuierlich durch den Ofen transportiert werden müssen. Durch das Schienensystem im Boden wird der Transport von Werkstücken erleichtert und automatisiert, was zu einer höheren Effizienz und geringeren Ausfallzeiten führt.
Dieser umfassende Text wird auf die Funktionsweise, den Aufbau, die Vorteile und Anwendungen eines Pulverofens mit Schienen im Boden eingehen. Außerdem werden technologische Entwicklungen, Wartung und Pflege, Energieeffizienz sowie Innovationen in der Branche behandelt. Das Ziel ist es, ein tiefes Verständnis für die Bedeutung und Funktionsweise dieser Öfen zu vermitteln und deren Rolle in der modernen Fertigung zu beleuchten.
Einführung in den Pulverofen mit Schienen im Boden
Ein Pulverofen mit Schienen im Boden ist eine spezielle Variante des Pulverofens, die in der Pulverbeschichtungsindustrie und anderen thermischen Anwendungen weit verbreitet ist. Dieser Ofen ist so konstruiert, dass er über Schienen im Boden verfügt, auf denen Werkstücke auf Wagen oder Plattformen transportiert werden. Das Design mit Bodenschienen bietet eine Reihe von Vorteilen gegenüber herkömmlichen Ofenkonstruktionen, insbesondere in Bezug auf die Handhabung großer und schwerer Werkstücke.
1.1. Bedeutung der Pulverbeschichtung
Die Pulverbeschichtung ist eine der am häufigsten verwendeten Methoden zur Oberflächenveredelung in der modernen Industrie. Sie bietet zahlreiche Vorteile gegenüber herkömmlichen Flüssiglackierungen, darunter eine höhere Beständigkeit gegen Korrosion, Kratzer, Witterungseinflüsse und chemische Belastungen. Außerdem ist die Pulverbeschichtung umweltfreundlicher, da sie keine Lösungsmittel verwendet und weniger Abfall erzeugt.
Nach dem Auftragen des Pulverlacks muss dieser in einem Pulverofen erhitzt werden, damit das Pulver schmilzt und sich vernetzt, um eine dauerhafte, gleichmäßige Beschichtung zu bilden. Der Pulverofen spielt dabei eine zentrale Rolle, indem er die erforderliche Hitze liefert und den Aushärteprozess kontrolliert.
Aufbau eines Pulverofens mit Schienen im Boden
Ein Pulverofen mit Schienen im Boden ist eine hochspezialisierte industrielle Anlage, die mehrere wichtige Komponenten umfasst, die alle auf die Optimierung des Aushärteprozesses ausgelegt sind.
2.1. Grundlegende Struktur und Komponenten
Ein Pulverofen besteht aus mehreren wesentlichen Teilen, die zusammenarbeiten, um den Aushärteprozess zu ermöglichen. Zu den wichtigsten Komponenten gehören:
- Ofengehäuse: Das Gehäuse des Ofens besteht aus robusten Materialien wie Stahl, die den hohen Temperaturen standhalten. Die Wände des Ofens sind mit Isoliermaterialien ausgekleidet, um Wärmeverluste zu minimieren und eine konstante Temperatur im Ofen zu gewährleisten.
- Heizelemente: Die Wärme im Ofen wird entweder durch elektrische Heizelemente oder gasbetriebene Brenner erzeugt. Die Wahl des Heizsystems hängt von der Anwendung und den Produktionsanforderungen ab. Elektrische Heizelemente bieten eine präzise Temperaturregelung, während gasbetriebene Öfen in großindustriellen Anwendungen häufig effizienter sind.
- Luftzirkulationssystem: Um eine gleichmäßige Verteilung der Hitze im gesamten Ofen zu gewährleisten, wird ein Luftzirkulationssystem verwendet. Dies sorgt dafür, dass alle Bereiche des Werkstücks gleichmäßig erhitzt werden.
- Bodenschienensystem: Das Herzstück des Pulverofens mit Schienen im Boden ist das Schienensystem. Dieses System besteht aus Schienen, die in den Ofenboden integriert sind, und Plattformen oder Wagen, auf denen die Werkstücke transportiert werden. Die Schienen ermöglichen einen gleichmäßigen, stabilen Transport schwerer Werkstücke durch den Ofen.
2.2. Funktionsweise des Schienensystems im Boden
Das Schienensystem im Boden ermöglicht es, schwere oder große Werkstücke effizient durch den Ofen zu bewegen. Die Werkstücke werden auf spezielle Wagen geladen, die auf den Schienen rollen. Diese Wagen können entweder manuell oder automatisch bewegt werden, je nach Produktionsanforderungen.
- Automatisierte Bewegung: In vielen industriellen Anlagen sind die Schienensysteme mit Motoren und Sensoren ausgestattet, die den Transport der Werkstücke automatisieren. Dies minimiert den manuellen Arbeitsaufwand und sorgt für eine gleichmäßige Bewegung durch den Ofen.
- Stabiler Transport: Das Schienensystem im Boden bietet einen stabilen Transport der Werkstücke. Da die Wagen auf den Schienen gleiten, wird das Risiko von Stößen oder Vibrationen minimiert, was besonders bei empfindlichen oder sperrigen Werkstücken von Vorteil ist.
2.3. Steuerung und Überwachung
Moderne Pulveröfen sind mit fortschrittlichen Steuerungssystemen ausgestattet, die die Temperatur, Luftzirkulation und den Aushärteprozess präzise überwachen. Diese Steuerungen verwenden Sensoren, die die Temperatur an verschiedenen Stellen im Ofen messen und automatisch Anpassungen vornehmen, um eine gleichmäßige Erwärmung der Werkstücke sicherzustellen.
- Automatische Steuerung: Viele Pulveröfen mit Schienen im Boden sind vollständig automatisiert und können in bestehende Produktionslinien integriert werden. Diese Steuerungssysteme bieten Flexibilität und ermöglichen eine dynamische Anpassung des Aushärteprozesses an die spezifischen Anforderungen der Werkstücke.
- Prozessüberwachung: Die Überwachung des Aushärteprozesses ist entscheidend, um sicherzustellen, dass die Werkstücke die erforderliche Temperatur erreichen und die Beschichtung gleichmäßig aushärtet. Modernste Systeme bieten auch die Möglichkeit, den gesamten Prozess in Echtzeit zu überwachen und Daten für die Qualitätskontrolle zu sammeln.
Vorteile eines Pulverofens mit Schienen im Boden
Die Verwendung eines Pulverofens mit Schienen im Boden bietet eine Reihe von Vorteilen, insbesondere im Vergleich zu herkömmlichen Kammeröfen oder Durchlauföfen ohne Schienensystem.
3.1. Effizienzsteigerung durch automatisierten Transport
Ein Pulverofen mit Schienen im Boden ermöglicht den automatisierten Transport von Werkstücken, was die Effizienz des gesamten Aushärteprozesses erheblich steigert. Durch den automatisierten Transport werden die Werkstücke kontinuierlich durch den Ofen bewegt, was den Produktionsdurchsatz erhöht und Ausfallzeiten minimiert.
- Zeitersparnis: Da der Transport automatisch erfolgt, müssen die Werkstücke nicht manuell in den Ofen geladen und wieder entladen werden. Dies spart Zeit und reduziert den Arbeitsaufwand.
- Gleichmäßiger Produktionsfluss: Der kontinuierliche Transport der Werkstücke sorgt für einen gleichmäßigen Produktionsfluss, was besonders in Großproduktionen von Vorteil ist.
3.2. Handhabung schwerer und großer Werkstücke
Ein großer Vorteil des Bodenschienensystems ist die einfache Handhabung von großen oder schweren Werkstücken. Werkstücke, die aufgrund ihrer Größe oder ihres Gewichts schwer zu transportieren sind, können problemlos auf die Wagen geladen und durch den Ofen bewegt werden.
- Erhöhte Sicherheit: Das Bodenschienensystem reduziert das Risiko von Beschädigungen oder Unfällen, die auftreten könnten, wenn schwere Werkstücke manuell bewegt werden müssten.
- Stabilität während des Transports: Da die Werkstücke auf stabilen Plattformen oder Wagen transportiert werden, bleibt ihre Position während des Aushärteprozesses stabil, was zu einer gleichmäßigeren Aushärtung führt.
3.3. Gleichmäßige Erwärmung und Aushärtung
Dank des Bodenschienensystems und der gleichmäßigen Bewegung der Werkstücke wird eine gleichmäßige Erwärmung gewährleistet. Dies führt zu einer gleichmäßigen Aushärtung der Pulverbeschichtung, was die Qualität und Haltbarkeit der Endprodukte verbessert.
- Minimierung von Über- oder Unterhitzung: Durch die gleichmäßige Verteilung der Wärme im Ofen und die kontinuierliche Bewegung der Werkstücke wird das Risiko von Über- oder Unterhitzung minimiert, was zu einer höheren Beschichtungsqualität führt.
3.4. Flexibilität und Anpassungsfähigkeit
Ein Pulverofen mit Schienen im Boden kann an verschiedene Produktionsanforderungen angepasst werden. Die Schienensysteme können so konfiguriert werden, dass sie verschiedene Arten und Größen von Werkstücken aufnehmen können, und sie können in bestehende Produktionslinien integriert werden.
- Anpassung an verschiedene Werkstücke: Die Plattformen und Wagen, die auf den Schienen verwendet werden, können für verschiedene Werkstücktypen angepasst werden, was eine hohe Flexibilität ermöglicht.
- Integration in bestehende Produktionslinien: Ein Pulverofen mit Schienen im Boden kann problemlos in eine kontinuierliche Produktionslinie integriert werden, was eine nahtlose Verarbeitung und Aushärtung der Werkstücke ermöglicht.
Arten von Pulveröfen mit Schienen im Boden
Es gibt verschiedene Arten von Pulveröfen mit Schienen im Boden, die je nach den spezifischen Anforderungen der Produktion und den Eigenschaften der Werkstücke ausgewählt werden können.
4.1. Gasbetriebene Pulveröfen mit Schienen im Boden
Gasbetriebene Pulveröfen nutzen Erdgas oder Propan als Energiequelle, um die erforderliche Hitze im Ofen zu erzeugen. Diese Art von Ofen ist besonders in großindustriellen Anwendungen verbreitet, da gasbetriebene Systeme oft kostengünstiger und effizienter sind, wenn große Werkstücke verarbeitet werden müssen.
Vorteile gasbetriebener Öfen:
- Höhere Energieeffizienz, insbesondere bei großen Produktionsmengen
- Schnellere Erwärmung im Vergleich zu elektrischen Öfen
- Geringere Betriebskosten bei großflächigen Anwendungen
4.2. Elektrisch betriebene Pulveröfen mit Schienen im Boden
Elektrische Pulveröfen verwenden Widerstandsheizelemente, um die erforderliche Wärme zu erzeugen. Diese Art von Ofen bietet eine präzise Temperaturregelung und ist besonders in kleineren Produktionslinien oder für Werkstücke geeignet, die eine empfindliche Temperaturkontrolle erfordern.
Vorteile elektrischer Öfen:
- Präzise Temperaturregelung, ideal für empfindliche Werkstücke
- Sauberer Betrieb ohne Emissionen von Verbrennungsgasen
- Weniger Installationsaufwand im Vergleich zu gasbetriebenen Systemen
4.3. Infrarot-Pulveröfen mit Schienen im Boden
Infrarot-Pulveröfen verwenden Infrarotstrahlung, um die Werkstücke direkt zu erwärmen. Diese Art von Ofen bietet eine schnelle Erwärmung und ist besonders für dünnwandige Werkstücke oder Anwendungen mit kurzen Aushärtezeiten geeignet.
Vorteile von Infrarotöfen:
- Schnelle Erwärmung und kürzere Aushärtezeiten
- Energieeffizienter Betrieb, da die Wärme direkt auf die Werkstücke gerichtet wird
- Ideal für Anwendungen, die eine schnelle Produktion erfordern
4.4. Hybrid-Pulveröfen mit Schienen im Boden
Hybrid-Pulveröfen kombinieren verschiedene Heiztechnologien, um die Effizienz zu maximieren und den Energieverbrauch zu senken. Ein Hybridofen kann sowohl gas- als auch elektrisch betrieben werden oder Infrarotstrahler in Kombination mit herkömmlichen Heizelementen verwenden.
Vorteile von Hybridöfen:
- Flexibilität bei der Auswahl der Heiztechnologie je nach Anforderung
- Höhere Energieeffizienz durch Kombination verschiedener Heizmethoden
- Anpassbar an unterschiedliche Produktionsbedingungen und Werkstücktypen
Thermische Prozesse in einem Pulverofen mit Schienen im Boden
Die thermischen Prozesse, die in einem Pulverofen mit Schienen im Boden durchgeführt werden, sind entscheidend für die Qualität der Pulverbeschichtung und die Haltbarkeit der Endprodukte.
5.1. Aushärtung von Pulverbeschichtungen
Der Hauptprozess, der in einem Pulverofen durchgeführt wird, ist die Aushärtung von Pulverbeschichtungen. Nachdem das Pulver elektrostatisch auf das Werkstück aufgetragen wurde, wird das Werkstück in den Ofen transportiert, wo es auf die erforderliche Temperatur erhitzt wird. Die Temperaturen liegen typischerweise zwischen 150°C und 220°C, abhängig von der Art des Pulvers.
- Schmelzen und Vernetzen des Pulvers: Während der Aushärtung schmilzt das Pulver und vernetzt sich chemisch, wodurch eine feste, gleichmäßige Beschichtung auf dem Werkstück entsteht.
- Gleichmäßige Temperaturverteilung: Durch das Schienensystem im Boden und die kontinuierliche Bewegung der Werkstücke wird eine gleichmäßige Erwärmung und Aushärtung gewährleistet.
5.2. Sinterprozesse
In einigen Anwendungen, insbesondere in der Metallverarbeitung, können Sinterprozesse in Pulveröfen durchgeführt werden. Beim Sintern werden pulverförmige Materialien unter hoher Hitze zu einem festen Stück verdichtet. Der Pulverofen bietet die erforderliche Hitze und gleichmäßige Wärmeverteilung, um den Sinternprozess zu unterstützen.
Effizienz und Energieeinsparung
Pulveröfen mit Schienen im Boden sind darauf ausgelegt, den Energieverbrauch zu minimieren und gleichzeitig eine hohe Effizienz im Aushärteprozess zu bieten. Es gibt mehrere Technologien und Strategien, die zur Energieeinsparung beitragen.
6.1. Optimierte Isolierung
Eine hochwertige Isolierung der Ofenwände ist entscheidend, um Wärmeverluste zu minimieren. Durch die Verwendung von fortschrittlichen Isoliermaterialien wie Keramikfasern wird sichergestellt, dass die Wärme im Inneren des Ofens bleibt, was den Energieverbrauch reduziert und die Temperatur im Ofen stabil hält.
6.2. Wärmerückgewinnungssysteme
Moderne Pulveröfen sind häufig mit Wärmerückgewinnungssystemen ausgestattet, die die Abwärme des Ofens auffangen und sie wieder in den Prozess einspeisen. Dies verringert den Gesamtenergieverbrauch des Ofens und senkt die Betriebskosten.
6.3. Automatisierung und Prozessoptimierung
Durch den Einsatz von Automatisierung und Prozessoptimierung kann der Energieverbrauch weiter gesenkt werden. Intelligente Steuerungssysteme passen den Aushärteprozess dynamisch an die spezifischen Anforderungen der Werkstücke an, was zu einer Reduzierung des Energieverbrauchs führt, ohne die Qualität der Beschichtung zu beeinträchtigen.
Wartung und Pflege eines Pulverofens mit Schienen im Boden
Eine regelmäßige Wartung und Pflege des Pulverofens mit Schienen im Boden ist entscheidend, um die langfristige Effizienz und Zuverlässigkeit des Ofens zu gewährleisten.
7.1. Reinigung des Schienensystems
Das Schienensystem muss regelmäßig gereinigt werden, um sicherzustellen, dass die Werkstücke reibungslos durch den Ofen transportiert werden können. Ablagerungen von Pulver oder anderen Materialien können die Bewegung der Wagen oder Plattformen behindern und den Produktionsprozess stören.
7.2. Überprüfung der Heizelemente
Die Heizelemente sollten regelmäßig überprüft werden, um sicherzustellen, dass sie ordnungsgemäß funktionieren und gleichmäßige Wärme erzeugen. Defekte Heizelemente können zu ungleichmäßigen Temperaturen und einer schlechten Aushärtung führen.
7.3. Kalibrierung der Steuerungssysteme
Die Steuerungssysteme des Ofens sollten regelmäßig kalibriert werden, um sicherzustellen, dass die Temperaturregelung präzise funktioniert. Eine ungenaue Temperaturkontrolle kann die Qualität der Beschichtung beeinträchtigen.
Anwendungen eines Pulverofens mit Schienen im Boden in der Industrie
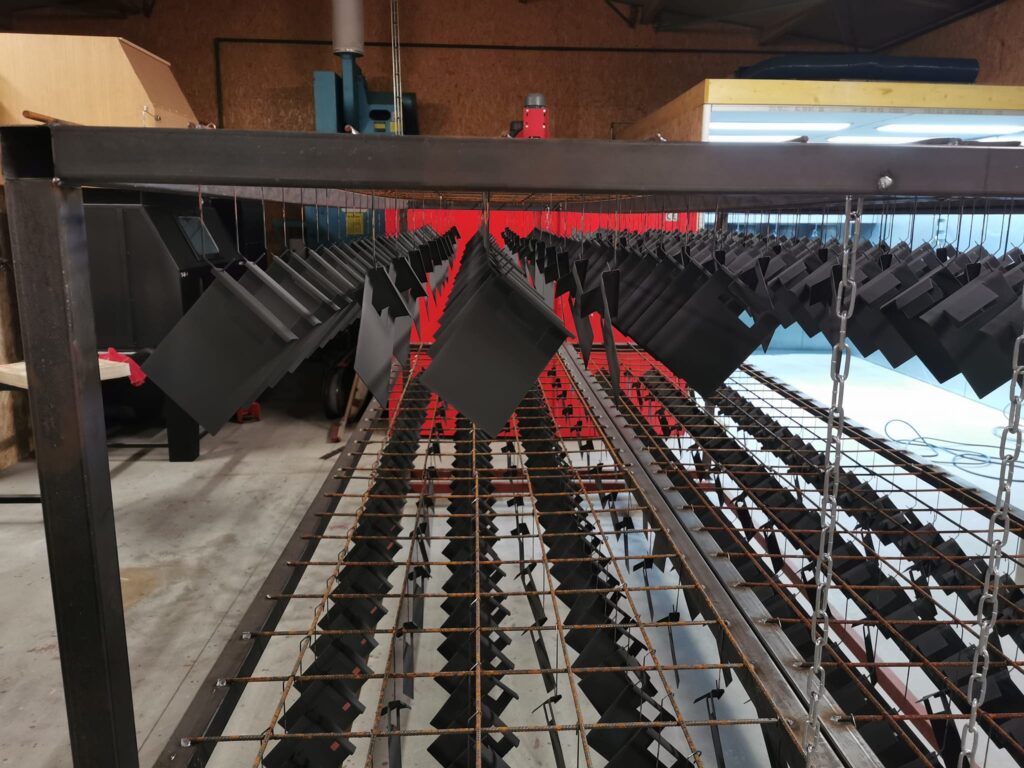
Pulveröfen mit Schienen im Boden werden in einer Vielzahl von Industrien eingesetzt, die von der Fähigkeit profitieren, große oder schwere Werkstücke effizient zu transportieren und gleichmäßig auszuhärten.
8.1. Automobilindustrie
In der Automobilindustrie werden Pulveröfen mit Schienen im Boden verwendet, um große Fahrzeugteile wie Karosserien, Fahrgestelle und andere Komponenten zu beschichten und auszuhärten.
8.2. Bauindustrie
In der Bauindustrie werden Pulveröfen verwendet, um große Metallteile wie Stahlträger, Fassadenelemente und andere Bauteile zu beschichten.
8.3. Maschinenbau
Der Maschinenbau nutzt Pulveröfen mit Schienen im Boden, um große Maschinenteile zu beschichten und gleichzeitig eine gleichmäßige Aushärtung der Beschichtung sicherzustellen.
Zukunftstechnologien und Innovationen
Die Technologie der Pulveröfen entwickelt sich stetig weiter, um die Effizienz und Leistung zu verbessern.
9.1. Einsatz erneuerbarer Energien
In Zukunft könnte der Einsatz von erneuerbaren Energien wie Solar- oder Windenergie die Energieeffizienz von Pulveröfen weiter verbessern.
9.2. Integration von KI und Automatisierung
Die Integration von künstlicher Intelligenz und maschinellem Lernen in die Steuerungssysteme der Öfen könnte den Aushärteprozess weiter optimieren und den Energieverbrauch weiter reduzieren.
Fazit
Ein Pulverofen mit Schienen im Boden ist ein unverzichtbares Werkzeug in der Pulverbeschichtungsindustrie und bietet zahlreiche Vorteile in Bezug auf Effizienz, Flexibilität und die Handhabung großer Werkstücke. Die Fähigkeit, Werkstücke kontinuierlich und stabil durch den Ofen zu transportieren, macht diese Öfen ideal für eine Vielzahl von Anwendungen in verschiedenen Industrien. Mit der Weiterentwicklung der Technologie und der zunehmenden Integration von Automatisierung und erneuerbaren Energien wird der Pulverofen mit Schienen im Boden auch in Zukunft eine zentrale Rolle in der industriellen Fertigung spielen.
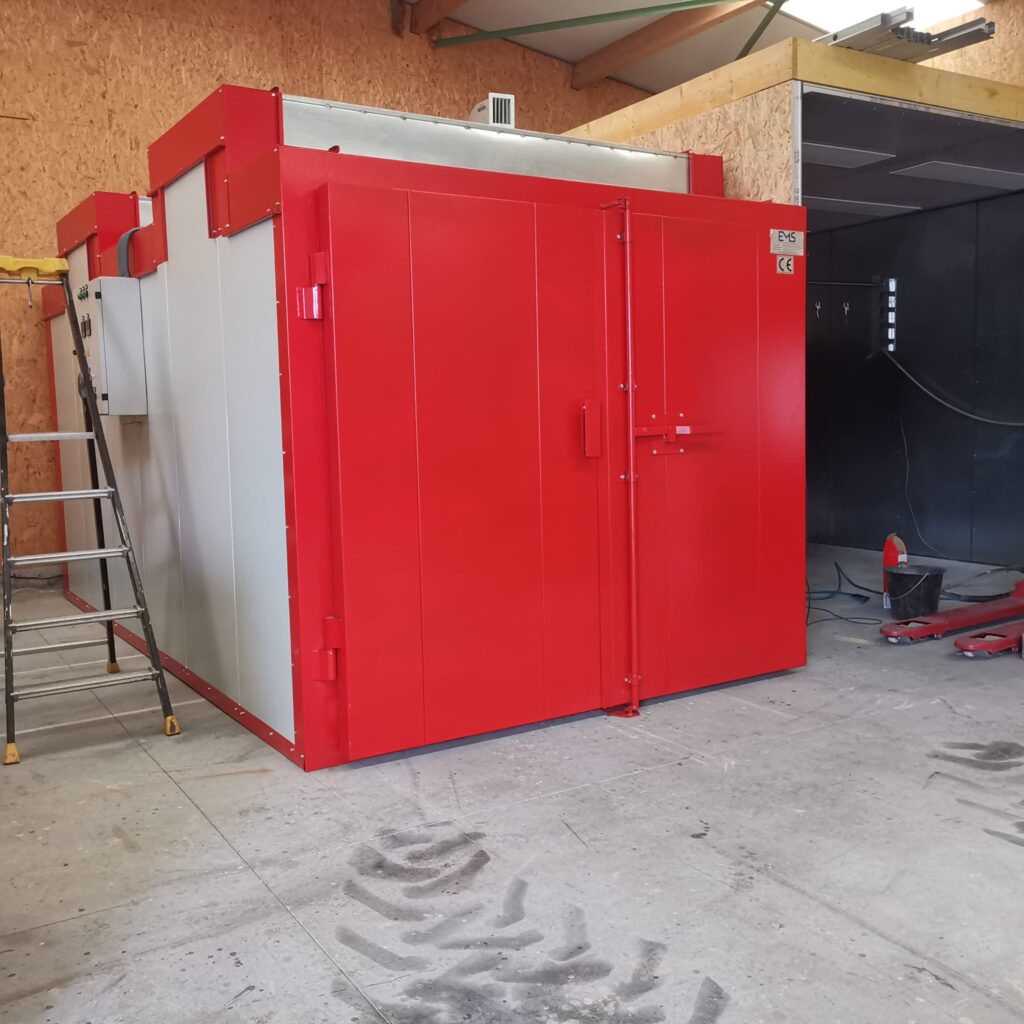
Ein Pulverofen mit Trennwand ist eine spezialisierte industrielle Anlage, die in der Pulverbeschichtungsindustrie und anderen thermischen Anwendungen eine Schlüsselrolle spielt. Diese Art von Ofen zeichnet sich durch die Fähigkeit aus, mehrere Werkstücke gleichzeitig zu behandeln, während sie durch interne Trennwände in separate Zonen unterteilt werden, die verschiedene Temperaturbereiche und Prozessbedingungen ermöglichen. Pulveröfen mit Trennwänden bieten Unternehmen Flexibilität bei der gleichzeitigen Verarbeitung unterschiedlicher Werkstücke und Materialien, was die Effizienz erhöht und die Produktion optimiert.
In diesem umfassenden Text wird ein detaillierter Einblick in die Funktionsweise, den Aufbau, die Vorteile, die verschiedenen Anwendungen sowie die Energieeffizienz und Wartungsstrategien eines Pulverofens mit Trennwand gegeben. Zudem werden Innovationen und technologische Entwicklungen beleuchtet, die zur Verbesserung der Effizienz und Vielseitigkeit dieser Art von Ofen beitragen.
Einführung in den Pulverofen mit Trennwand
Ein Pulverofen mit Trennwand unterscheidet sich von herkömmlichen Pulveröfen durch die Integration einer internen Trennwand oder mehrerer Trennwände, die den Ofen in mehrere Zonen aufteilen. Diese Zonen ermöglichen es, verschiedene Teile des Ofens auf unterschiedliche Temperaturen einzustellen und Werkstücke gleichzeitig unter verschiedenen Bedingungen auszuhärten. Dies ist besonders vorteilhaft, wenn unterschiedliche Materialien oder Beschichtungen unterschiedliche Aushärteparameter erfordern.
1.1. Bedeutung der Pulverbeschichtung und der Aushärtung
Die Pulverbeschichtung ist eine Oberflächenbehandlungsmethode, die häufig in der Automobil-, Bau- und Möbelindustrie eingesetzt wird. Diese Beschichtung wird in Form von pulverförmigen Farben oder Harzen auf ein Werkstück aufgetragen und anschließend in einem Ofen erhitzt. Das Pulver schmilzt, vernetzt sich chemisch und bildet eine widerstandsfähige, schützende und dekorative Oberfläche. Ein Pulverofen ist das Herzstück dieses Prozesses, da er die für das Aushärten des Pulvers erforderliche Hitze liefert.
Ein Pulverofen mit Trennwand bietet jedoch zusätzliche Flexibilität, da er mehrere Aushärteprozesse gleichzeitig in einem Ofen durchführen kann. Unterschiedliche Werkstücke, die unterschiedliche Aushärtebedingungen benötigen, können im selben Ofen verarbeitet werden, was zu einer erheblichen Steigerung der Produktionseffizienz führt.
Aufbau eines Pulverofens mit Trennwand
Ein Pulverofen mit Trennwand ist ein komplexes technisches Gerät, das aus mehreren Komponenten besteht, die nahtlos zusammenarbeiten, um eine präzise Steuerung der Temperatur und des Aushärteprozesses zu ermöglichen.
2.1. Ofengehäuse und Isolierung
Das Gehäuse eines Pulverofens besteht typischerweise aus robusten Metallmaterialien wie Stahl, die hohen Temperaturen standhalten und gleichzeitig die strukturelle Integrität des Ofens gewährleisten. Um den Wärmeverlust zu minimieren und den Energieverbrauch zu senken, sind die Wände des Ofens mit fortschrittlichen Isoliermaterialien ausgekleidet. Diese Isolierung hilft dabei, die Wärme im Inneren des Ofens zu halten und die Oberflächentemperaturen der Außenwände zu kontrollieren, wodurch die Sicherheit des Betriebs erhöht wird.
2.2. Trennwandsystem
Das Trennwandsystem ist das wichtigste Unterscheidungsmerkmal eines Pulverofens mit Trennwand. Die Trennwände bestehen in der Regel aus feuerfesten Materialien, die den Ofen in mehrere Kammern oder Zonen unterteilen. Jede Zone kann unabhängig voneinander auf unterschiedliche Temperaturen eingestellt werden, was eine gleichzeitige Verarbeitung von Werkstücken mit unterschiedlichen Aushärteanforderungen ermöglicht.
- Flexibilität durch mehrere Zonen: Diese Trennwände ermöglichen die Schaffung von zwei oder mehr Zonen mit unterschiedlichen Temperaturbereichen. Dadurch kann der Ofen effizienter arbeiten, da er mehrere Werkstücke parallel verarbeiten kann, ohne dass die Bedingungen in den einzelnen Zonen beeinträchtigt werden.
2.3. Heizelemente und Heizsystem
Die Heizelemente eines Pulverofens mit Trennwand sind für die Erzeugung der erforderlichen Wärme verantwortlich. Diese können entweder elektrisch oder gasbefeuert sein, je nach den spezifischen Anforderungen der Produktion.
- Elektrische Heizelemente: Diese bieten eine präzise Temperaturregelung und eignen sich besonders für Anwendungen, bei denen eine hohe Genauigkeit erforderlich ist.
- Gasbefeuerte Heizelemente: Gasbetriebene Systeme sind besonders in großindustriellen Anwendungen weit verbreitet, da sie in der Regel energieeffizienter sind, wenn große Mengen an Werkstücken verarbeitet werden müssen.
2.4. Steuerungssysteme
Ein Pulverofen mit Trennwand ist mit fortschrittlichen Steuerungssystemen ausgestattet, die es ermöglichen, jede Zone des Ofens unabhängig voneinander zu steuern. Diese Systeme überwachen die Temperatur in jeder Zone, passen die Heizleistung an und sorgen dafür, dass der Aushärteprozess gleichmäßig und präzise abläuft.
- Automatische Steuerung: Moderne Steuerungssysteme ermöglichen eine vollständige Automatisierung des Aushärteprozesses. Sie regulieren die Temperatur, überwachen die Dauer des Aushärtens und passen den Prozess dynamisch an die Anforderungen der Werkstücke an.
- Überwachungssysteme: Viele Pulveröfen sind mit Überwachungssystemen ausgestattet, die es dem Bediener ermöglichen, den gesamten Aushärteprozess in Echtzeit zu überwachen. Diese Systeme können auch Daten über den Prozess sammeln, die zur Qualitätskontrolle und zur Optimierung zukünftiger Produktionszyklen verwendet werden können.
2.5. Luftzirkulationssystem
Ein effizientes Luftzirkulationssystem ist entscheidend für die gleichmäßige Verteilung der Hitze innerhalb des Ofens. In einem Pulverofen mit Trennwand muss das Luftzirkulationssystem so gestaltet sein, dass es die Luft gleichmäßig durch die verschiedenen Zonen des Ofens leitet, um sicherzustellen, dass die Werkstücke gleichmäßig erhitzt werden, unabhängig von ihrer Position im Ofen.
Funktionsweise eines Pulverofens mit Trennwand
Ein Pulverofen mit Trennwand arbeitet, indem er die Werkstücke in verschiedenen Zonen des Ofens unterschiedlichen Temperaturen aussetzt. Dies ermöglicht eine effiziente Nutzung des Ofens und stellt sicher, dass verschiedene Materialien oder Werkstücke gleichzeitig verarbeitet werden können, ohne dass die Aushärtebedingungen beeinträchtigt werden.
3.1. Aushärteprozess
Der Aushärteprozess beginnt, nachdem das Pulver auf die Werkstücke aufgetragen wurde. Die Werkstücke werden in den Pulverofen gebracht, wo sie in die entsprechenden Zonen platziert werden, die auf die richtigen Temperaturen eingestellt sind. Typische Aushärteprozesse in Pulveröfen erfolgen bei Temperaturen zwischen 150°C und 200°C, abhängig von der Art des Pulvers und der Beschichtung.
Während der Aushärtung schmilzt das Pulver und vernetzt sich chemisch, wodurch eine glatte, dauerhafte Beschichtung auf der Oberfläche des Werkstücks entsteht. Der Vorteil eines Pulverofens mit Trennwand besteht darin, dass verschiedene Werkstücke in verschiedenen Zonen des Ofens unterschiedliche Temperaturen und Aushärtezeiten haben können, was eine flexible und effiziente Produktion ermöglicht.
3.2. Temperaturregelung in den Zonen
Die Trennwände im Ofen sorgen dafür, dass jede Zone des Ofens eine eigene Temperatur hat. Die Steuerungssysteme passen die Heizleistung in jeder Zone unabhängig an, um sicherzustellen, dass die gewünschte Temperatur erreicht und konstant gehalten wird.
- Präzise Temperaturkontrolle: Die Fähigkeit, die Temperatur in jeder Zone individuell zu steuern, ermöglicht eine präzisere Kontrolle über den Aushärteprozess, was zu einer höheren Qualität der Pulverbeschichtung führt.
3.3. Handhabung verschiedener Materialien
Ein wesentlicher Vorteil eines Pulverofens mit Trennwand ist die Fähigkeit, unterschiedliche Materialien und Beschichtungen gleichzeitig zu verarbeiten. Da verschiedene Materialien unterschiedliche Aushärteparameter haben, ermöglicht der Ofen die gleichzeitige Verarbeitung von Werkstücken mit unterschiedlichen Anforderungen, ohne dass diese miteinander in Konflikt geraten.
Vorteile eines Pulverofens mit Trennwand
Ein Pulverofen mit Trennwand bietet zahlreiche Vorteile gegenüber herkömmlichen Pulveröfen, insbesondere in Bezug auf Flexibilität, Effizienz und die Fähigkeit, verschiedene Materialien gleichzeitig zu verarbeiten.
4.1. Höhere Flexibilität in der Produktion
Einer der größten Vorteile eines Pulverofens mit Trennwand ist die Flexibilität, die er in die Produktion einbringt. Durch die Aufteilung des Ofens in mehrere Zonen können verschiedene Werkstücke gleichzeitig verarbeitet werden, auch wenn sie unterschiedliche Aushärtebedingungen erfordern. Dies ermöglicht eine höhere Produktionskapazität und reduziert die Notwendigkeit, separate Chargen zu erstellen.
- Gleichzeitige Verarbeitung unterschiedlicher Werkstücke: Der Ofen kann mehrere Werkstücke parallel verarbeiten, selbst wenn diese unterschiedliche Temperaturen oder Aushärtezeiten erfordern.
4.2. Effizienzsteigerung
Durch die Möglichkeit, mehrere Werkstücke gleichzeitig zu verarbeiten, erhöht ein Pulverofen mit Trennwand die Effizienz des Produktionsprozesses erheblich. Der Ofen kann kontinuierlich betrieben werden, und es gibt weniger Stillstandszeiten, da die Werkstücke nicht nacheinander, sondern parallel verarbeitet werden können.
- Reduzierung von Ausfallzeiten: Da der Ofen kontinuierlich betrieben werden kann, werden Ausfallzeiten minimiert, was zu einer höheren Produktivität führt.
4.3. Energieeinsparung
Obwohl ein Pulverofen mit Trennwand in der Lage ist, mehrere Werkstücke parallel zu verarbeiten, kann der Energieverbrauch dennoch gesenkt werden. Die Fähigkeit, einzelne Zonen des Ofens zu kontrollieren, bedeutet, dass nicht der gesamte Ofen auf eine hohe Temperatur erhitzt werden muss, wenn nur bestimmte Zonen benötigt werden.
- Gezielte Temperatursteuerung: Die Trennung des Ofens in verschiedene Zonen ermöglicht es, Energie zu sparen, da nur die Zonen beheizt werden, die tatsächlich verwendet werden.
4.4. Bessere Kontrolle über den Aushärteprozess
Die Trennung des Ofens in verschiedene Zonen bietet eine präzisere Kontrolle über den Aushärteprozess. Werkstücke, die unterschiedliche Aushärtezeiten oder Temperaturen benötigen, können in verschiedenen Zonen des Ofens untergebracht werden, was zu einer gleichmäßigeren Aushärtung und einer höheren Qualität der Beschichtung führt.
- Verbesserte Produktqualität: Die Fähigkeit, den Aushärteprozess genau zu steuern, führt zu einer gleichmäßigeren Beschichtung und reduziert die Wahrscheinlichkeit von Fehlern oder Mängeln in der Endbeschichtung.
Arten von Pulveröfen mit Trennwand
Es gibt verschiedene Arten von Pulveröfen mit Trennwand, die jeweils für spezifische Produktionsanforderungen und Anwendungen ausgelegt sind. Die Wahl des richtigen Ofens hängt von den spezifischen Anforderungen der Materialien, der Produktionskapazität und der gewünschten Effizienz ab.
5.1. Gasbetriebene Pulveröfen mit Trennwand
Gasbetriebene Pulveröfen nutzen Erdgas oder Propan als Energiequelle, um die erforderliche Hitze im Ofen zu erzeugen. Diese Art von Ofen ist besonders für großindustrielle Anwendungen geeignet, in denen große Mengen von Werkstücken verarbeitet werden müssen.
Vorteile gasbetriebener Pulveröfen:
- Höhere Energieeffizienz bei großflächigen Anwendungen
- Schnellere Erwärmung im Vergleich zu elektrischen Öfen
- Geringere Betriebskosten in großen Produktionsanlagen
5.2. Elektrisch betriebene Pulveröfen mit Trennwand
Elektrische Pulveröfen verwenden Widerstandsheizelemente, um die erforderliche Hitze zu erzeugen. Diese Art von Ofen bietet eine präzise Temperaturregelung und ist ideal für kleinere Produktionslinien oder für Anwendungen, bei denen empfindliche Materialien verarbeitet werden müssen.
Vorteile elektrischer Pulveröfen:
- Präzise Temperaturregelung, ideal für empfindliche Werkstücke
- Sauberer Betrieb ohne Emissionen von Verbrennungsgasen
- Flexibler Einsatz in kleineren Produktionslinien
5.3. Hochtemperatur-Pulveröfen mit Trennwand
Hochtemperatur-Pulveröfen sind für Anwendungen konzipiert, die Temperaturen von über 1000°C erfordern, wie z. B. das Sintern von Metallen oder das Schmelzen von Glas. Diese Öfen sind mit speziellen Isoliermaterialien und Heizelementen ausgestattet, die extremen Temperaturen standhalten können.
Vorteile von Hochtemperatur-Pulveröfen:
- Fähigkeit, extrem hohe Temperaturen zu erreichen
- Geeignet für spezielle thermische Prozesse wie das Sintern und Schmelzen von Metallen und Glas
- Robuste Konstruktion für den Dauerbetrieb bei hohen Temperaturen
5.4. Hybrid-Pulveröfen mit Trennwand
Hybrid-Pulveröfen kombinieren verschiedene Heiztechnologien, wie z. B. Gas und Elektrizität, um die Effizienz zu maximieren und den Energieverbrauch zu senken. Diese Öfen bieten eine größere Flexibilität und ermöglichen es, verschiedene Arten von Heizsystemen je nach den spezifischen Anforderungen der Werkstücke zu verwenden.
Vorteile von Hybrid-Pulveröfen:
- Flexibilität bei der Auswahl der Heiztechnologie je nach Anforderung
- Höhere Energieeffizienz durch Kombination verschiedener Heizmethoden
- Anpassbar an unterschiedliche Produktionsbedingungen und Werkstücktypen
Thermische Prozesse in einem Pulverofen mit Trennwand
Ein Pulverofen mit Trennwand führt eine Reihe von thermischen Prozessen durch, die speziell auf die Aushärtung von Pulverbeschichtungen und andere Anwendungen abgestimmt sind.
6.1. Aushärtung von Pulverbeschichtungen
Der Hauptprozess in einem Pulverofen mit Trennwand ist die Aushärtung von Pulverbeschichtungen. Nach dem Auftragen des Pulvers auf das Werkstück wird es im Ofen auf die erforderliche Temperatur erhitzt, um das Pulver zu schmelzen und zu vernetzen. Die resultierende Beschichtung ist hart, gleichmäßig und widerstandsfähig gegen äußere Einflüsse.
- Gleichmäßige Aushärtung: Durch die Möglichkeit, unterschiedliche Zonen im Ofen zu schaffen, kann der Aushärteprozess für verschiedene Werkstücke optimiert werden. Dies führt zu einer gleichmäßigen Aushärtung der Beschichtungen und einer höheren Qualität der Endprodukte.
6.2. Sinterprozesse
In einigen Anwendungen, insbesondere in der Metallverarbeitung, können Sinterprozesse in einem Pulverofen mit Trennwand durchgeführt werden. Beim Sintern werden pulverförmige Materialien unter hoher Hitze zu einem festen Stück verdichtet.
- Effizientes Sintern durch Zonentrennung: Die Trennwände ermöglichen es, verschiedene Materialien gleichzeitig zu sintern, was den gesamten Prozess beschleunigt und die Produktivität erhöht.
Effizienz und Energieeinsparung
Pulveröfen mit Trennwand bieten erhebliche Vorteile in Bezug auf Energieeffizienz und Ressourcenschonung. Die Möglichkeit, verschiedene Zonen des Ofens zu steuern und nur die benötigten Bereiche zu beheizen, trägt erheblich zur Reduzierung des Energieverbrauchs bei.
7.1. Optimierte Ofenisolierung
Eine hochwertige Isolierung der Ofenwände ist entscheidend, um den Energieverbrauch zu senken. Durch den Einsatz von fortschrittlichen Isoliermaterialien bleibt die Hitze im Inneren des Ofens und Wärmeverluste werden minimiert.
7.2. Effiziente Temperaturregelung
Da nur bestimmte Zonen des Ofens auf hohe Temperaturen erhitzt werden müssen, wird weniger Energie verbraucht, was zu einer insgesamt höheren Energieeffizienz führt. Die Möglichkeit, die Temperaturen in den einzelnen Zonen gezielt zu steuern, ermöglicht es, die Heizkosten zu senken, ohne die Qualität des Aushärteprozesses zu beeinträchtigen.
7.3. Wärmerückgewinnungssysteme
Moderne Pulveröfen mit Trennwand sind häufig mit Wärmerückgewinnungssystemen ausgestattet, die die Abwärme des Ofens auffangen und sie für andere thermische Prozesse in der Anlage verwenden. Diese Systeme können den Energieverbrauch erheblich reduzieren und die Betriebskosten senken.
Wartung und Pflege eines Pulverofens mit Trennwand
Die regelmäßige Wartung eines Pulverofens mit Trennwand ist entscheidend, um seine langfristige Effizienz zu gewährleisten und Ausfallzeiten zu minimieren.
8.1. Reinigung des Ofens und der Trennwände
Es ist wichtig, den Ofen und die Trennwände regelmäßig zu reinigen, um Ablagerungen zu entfernen, die den Aushärteprozess beeinträchtigen könnten. Besonders bei häufigem Einsatz kann sich überschüssiges Pulver im Ofen ansammeln, was die Wärmeverteilung beeinträchtigen könnte.
8.2. Überprüfung der Heizelemente
Die Heizelemente des Ofens sollten regelmäßig überprüft werden, um sicherzustellen, dass sie ordnungsgemäß funktionieren und gleichmäßige Wärme erzeugen. Defekte Heizelemente können zu ungleichmäßigen Temperaturen führen, was die Qualität der Beschichtung beeinträchtigen könnte.
8.3. Kalibrierung der Steuerungssysteme
Die Steuerungssysteme des Ofens sollten regelmäßig kalibriert werden, um sicherzustellen, dass die Temperaturregelung präzise funktioniert. Eine ungenaue Temperaturkontrolle kann die Qualität der Aushärtung und damit die Beschichtungsqualität beeinträchtigen.
Anwendungen eines Pulverofens mit Trennwand in der Industrie
Pulveröfen mit Trennwand finden in einer Vielzahl von Industrien Anwendung, darunter die Automobil-, Bau-, Möbel- und Metallverarbeitungsindustrie.
9.1. Automobilindustrie
In der Automobilindustrie werden Pulveröfen mit Trennwand verwendet, um Fahrzeugteile wie Karosserien, Felgen und Fahrgestelle zu beschichten und auszuhärten. Diese Öfen ermöglichen es, verschiedene Teile gleichzeitig zu verarbeiten, was die Produktionskapazität erhöht und die Effizienz steigert.
9.2. Bauindustrie
In der Bauindustrie werden Pulveröfen mit Trennwand zur Beschichtung und Aushärtung von großen Metallstrukturen, Fassadenelementen und anderen Bauteilen verwendet. Die Möglichkeit, große Mengen von Werkstücken gleichzeitig zu verarbeiten, ist besonders vorteilhaft für Großprojekte.
9.3. Möbelherstellung
Die Möbelindustrie nutzt Pulveröfen mit Trennwand zur Beschichtung und Aushärtung von Metallrahmen und anderen Möbelteilen. Diese Öfen bieten eine gleichmäßige Aushärtung und ermöglichen es, verschiedene Werkstücke gleichzeitig zu verarbeiten.
Zukunftstechnologien und Innovationen
Die Technologie der Pulveröfen entwickelt sich ständig weiter, um die Effizienz und Leistung zu verbessern.
10.1. Integration von KI und Automatisierung
Die Integration von künstlicher Intelligenz (KI) und maschinellem Lernen in die Steuerungssysteme der Öfen könnte den Aushärteprozess weiter optimieren und den Energieverbrauch senken. Intelligente Steuerungssysteme könnten den Prozess überwachen und automatisch Anpassungen vornehmen, um die Effizienz zu maximieren.
10.2. Einsatz erneuerbarer Energien
In Zukunft könnte der Einsatz von erneuerbaren Energien wie Solar- oder Windenergie dazu beitragen, die Umweltbelastung zu reduzieren und die Energieeffizienz von Pulveröfen weiter zu verbessern.
Fazit
Ein Pulverofen mit Trennwand bietet eine Vielzahl von Vorteilen in der Pulverbeschichtungs- und thermischen Verarbeitungsindustrie. Die Fähigkeit, mehrere Werkstücke gleichzeitig zu verarbeiten und dabei unterschiedliche Aushärtebedingungen in verschiedenen Zonen des Ofens zu schaffen, macht diese Art von Ofen besonders effizient und flexibel. Durch die Integration fortschrittlicher Steuerungssysteme und energieeffizienter Technologien wird der Pulverofen mit Trennwand auch in Zukunft eine zentrale Rolle in vielen industriellen Prozessen spielen.
Wir versenden nach Deutschland, Österreich und in die Schweiz
Wir sind nicht nur die Hersteller Ihrer Pulverbeschichtungsanlagen, sondern auch Ihr weltweiter Lieferpartner.
Bei EMS verstehen wir, dass es genauso wichtig ist, Ihre Pulverbeschichtungsanlagen schnell und sicher zu Ihnen zu bringen, wie sie nach höchsten Standards herzustellen. Deshalb bieten wir all unseren Kunden weltweit Lieferdienste an.
Wir arbeiten mit einem Netzwerk erfahrener und zuverlässiger Versandpartner zusammen, um sicherzustellen, dass Ihre Ausrüstung pünktlich und in einwandfreiem Zustand ankommt. Wir bieten auch eine Vielzahl von Versandoptionen an, um Ihrem Budget und Ihren Bedürfnissen gerecht zu werden.
Egal, ob Sie Ihre Ausrüstung an eine lokale Adresse oder an einen internationalen Bestimmungsort versenden müssen, wir können Ihnen helfen. Wir arbeiten mit Ihnen zusammen, um die beste Versandoption für Ihre Bedürfnisse auszuwählen und Sie während des gesamten Versandprozesses über den Status Ihrer Sendung zu informieren.
Wenn Sie sich also für EMS für Ihre Pulverbeschichtungsanlagen entscheiden, erhalten Sie nicht nur die besten Produkte auf dem Markt, sondern auch das bestmögliche Liefererlebnis.
Kontaktieren Sie uns noch heute, um mehr über unsere weltweiten Lieferdienste zu erfahren.
Auch beim Versand, setzen wir auf bewährte Partner. Und auf Nachhaltigkeit. Nicht nur in Deutschland und Österreich sondern in der ganzen EU und der Schweiz wird ihre Pulverbeschichtungsanlage mit unseren Transtportfirmen zu ihnen gebracht.
Die Lieferung ihrer Ware erfolgt innerhalb Deutschlands, Österreichs und der Schweiz spätestens innerhalb von 7-8 Werktagen. Die Lieferung in weitere Länder der EU erfolgt spätestens innerhalb von 10 Werktagen.
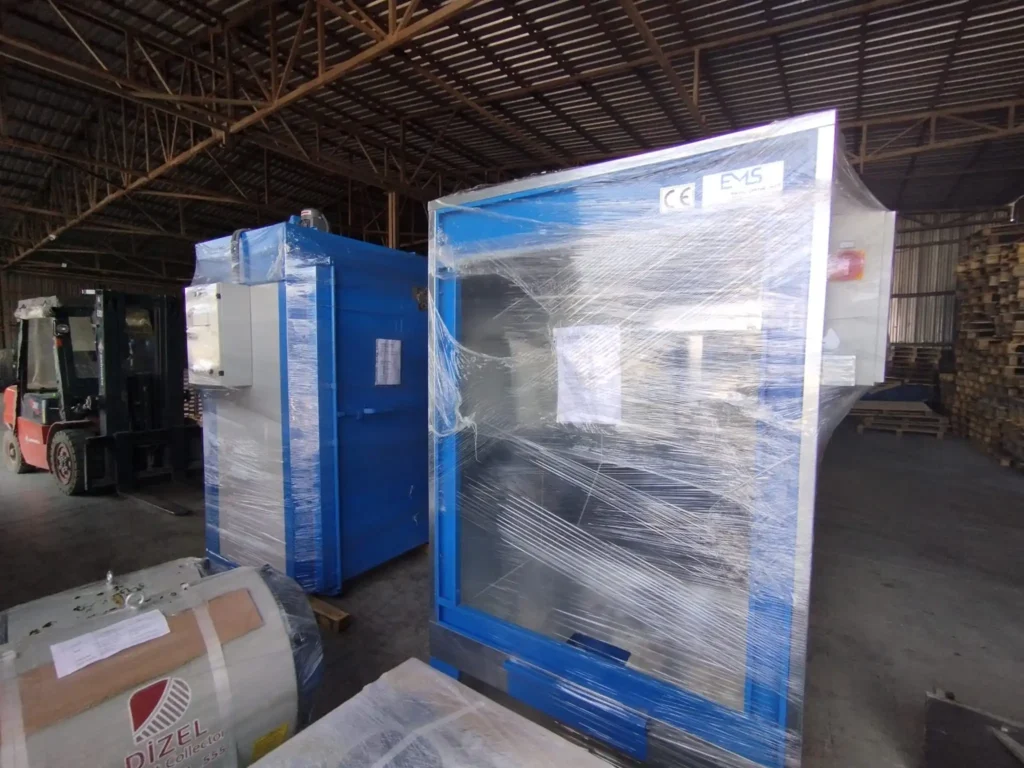

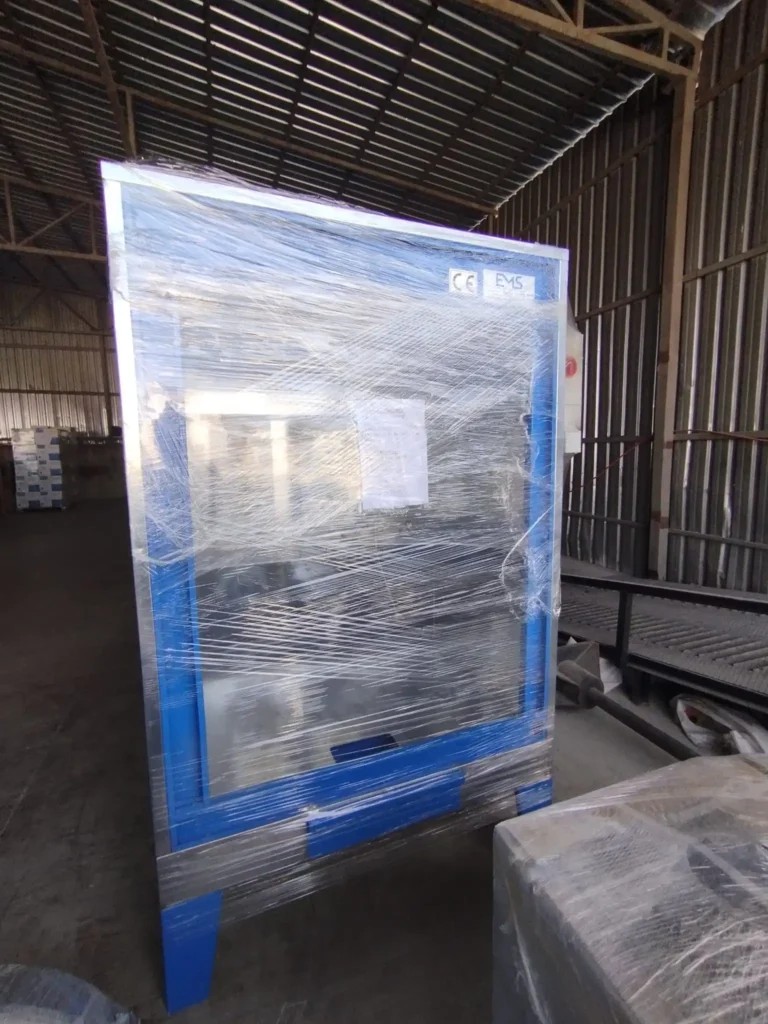
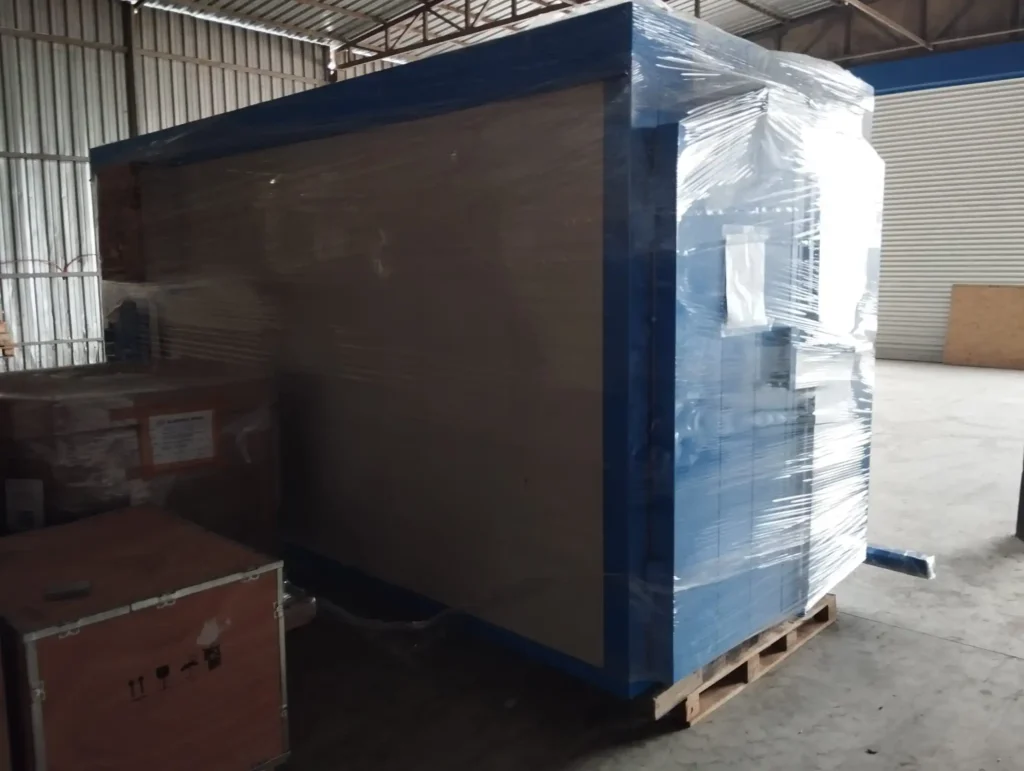
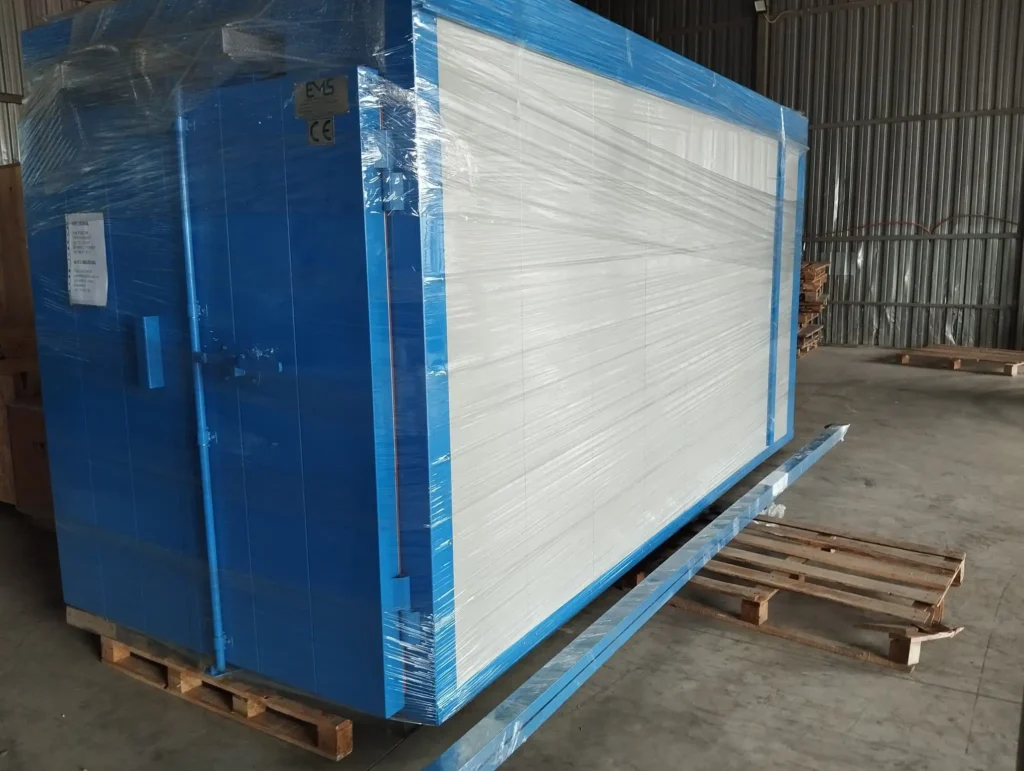
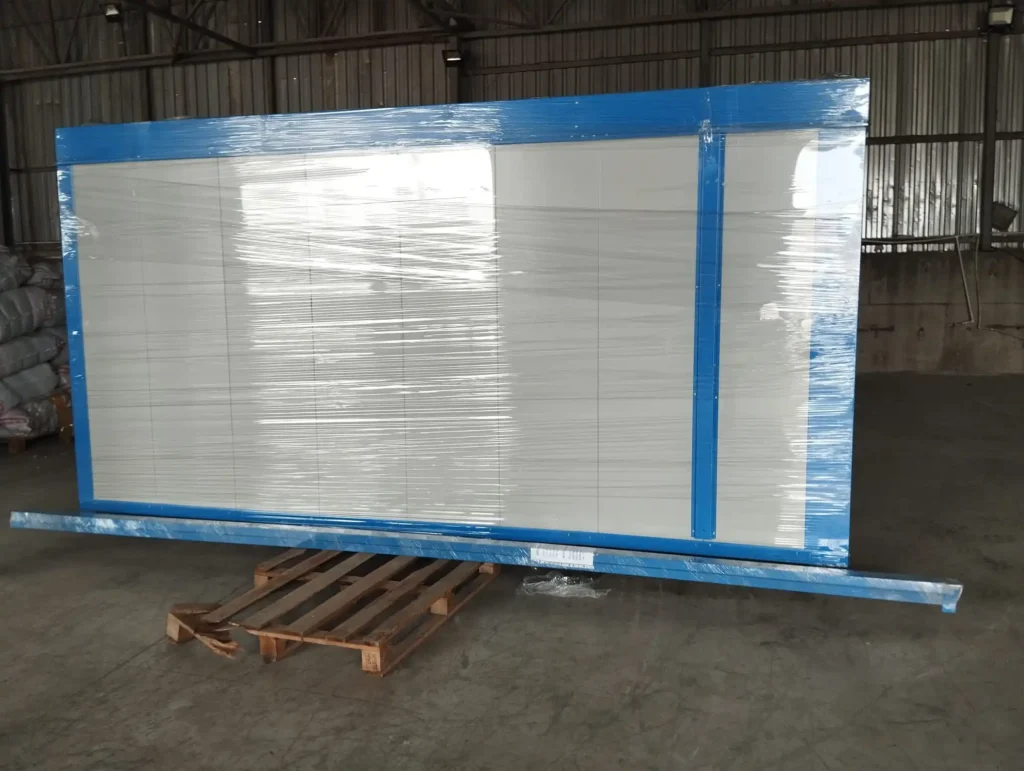
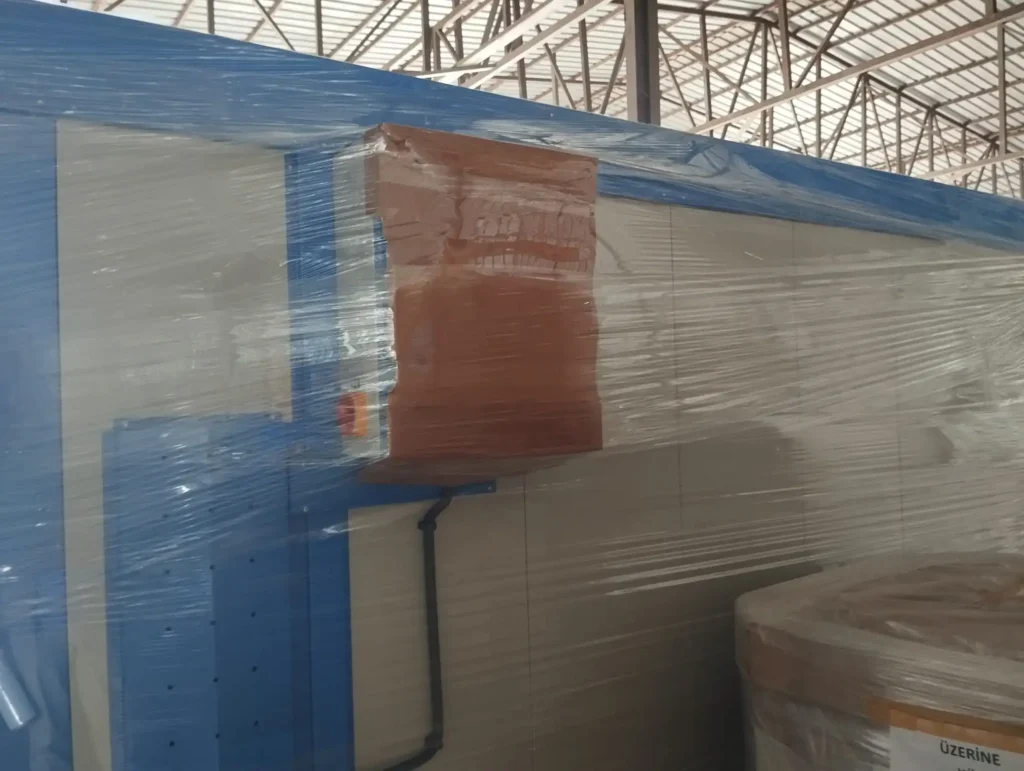
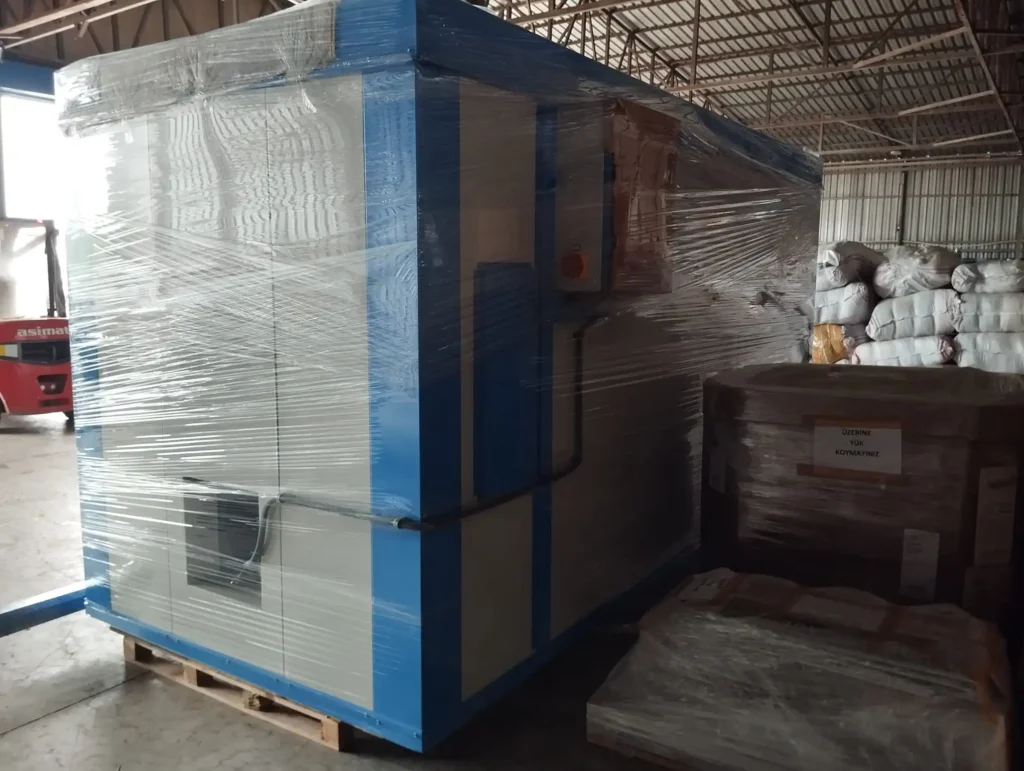
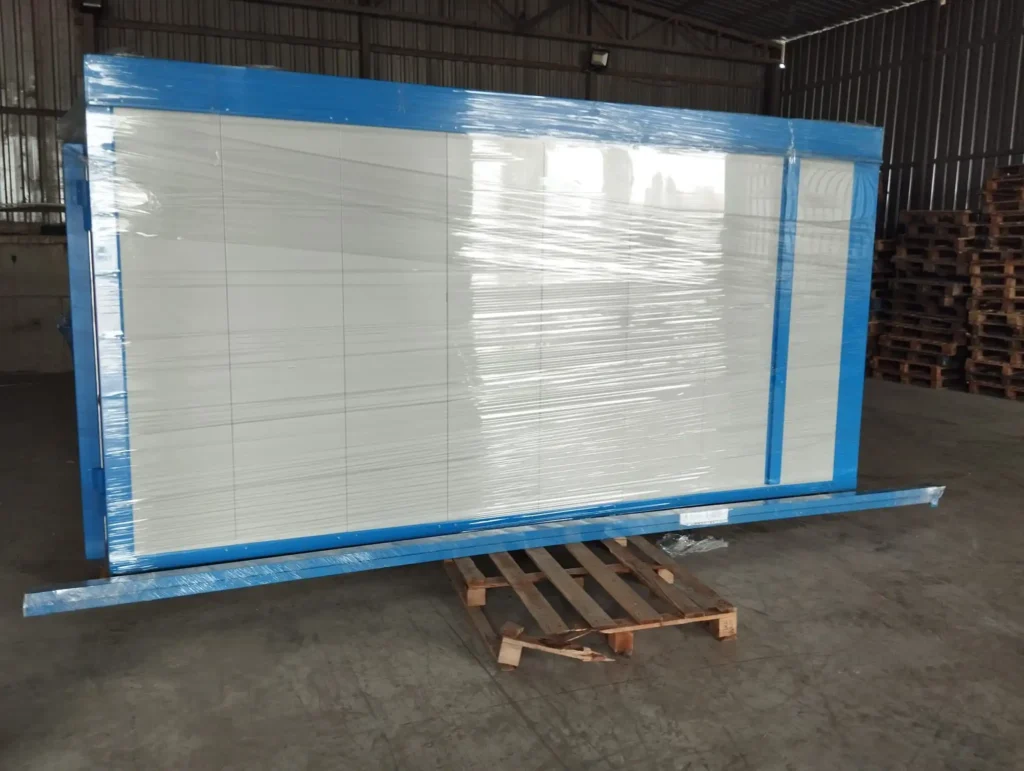