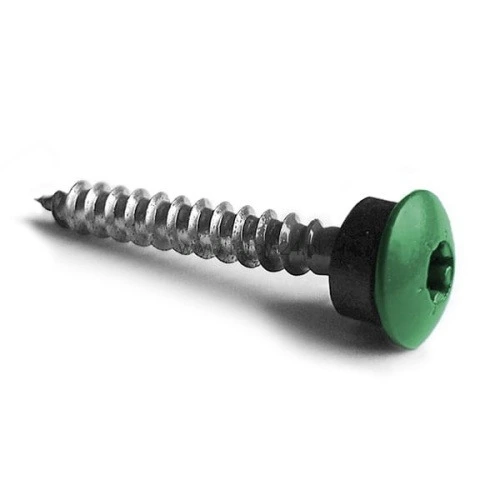
Pulveranlage für winzige Objekte: Die Lackierung winziger Objekte stellt eine besondere Herausforderung dar, die weit über konventionelle Beschichtungsverfahren hinausgeht. Während großflächige Werkstücke meist mit klassischen Methoden wie Spritzlackierung, Pulverbeschichtung oder Tauchlackierung effizient bearbeitet werden können, erfordern sehr kleine oder filigrane Bauteile spezielle Lackiertechniken, um eine gleichmäßige und fehlerfreie Beschichtung zu gewährleisten. Dies betrifft zum Beispiel Komponenten aus der Elektronikindustrie, Medizintechnik, Mikromechanik oder Kosmetikverpackung, bei denen nicht nur die Funktionalität, sondern auch die Optik und Oberflächenqualität entscheidend sind.
Ein zentrales Ziel bei der Lackierung winziger Teile ist die Erreichung einer präzisen, gleichmäßigen Schichtstärke, ohne dass es zu Tropfenbildung, Lackansammlungen oder Oberflächenfehlern kommt. Dafür kommen verschiedene hochentwickelte Verfahren zum Einsatz, unter anderem Mikro-Sprühtechnologien, elektrostatische Applikation im Niederspannungsbereich sowie Rotationszerstäuber in Miniaturform. Moderne Anlagen arbeiten oft automatisiert und sind speziell auf Kleinteile ausgerichtet, sowohl in Hinblick auf die Positionierung als auch auf den exakten Lackauftrag. Roboterarme mit hochpräziser Düsentechnik oder individuell programmierbare Achssysteme sorgen dafür, dass selbst komplex geformte Kleinteile vollständig und gleichmäßig beschichtet werden können.
Ein weiteres zentrales Element ist die Handhabung der Objekte während des Lackierprozesses. Aufgrund ihrer geringen Größe können sie leicht verrutschen, beschädigt werden oder eine unzureichende Erdung aufweisen, was vor allem bei elektrostatischer Lackierung zu Problemen führt. Daher werden häufig spezielle Werkstückträger, Halterungen oder rotierende Trommelsysteme eingesetzt, die die Teile fixieren und gleichzeitig eine rundum-Beschichtung ermöglichen.
In vielen Anwendungen ist zudem eine hohe Wiederholgenauigkeit erforderlich, insbesondere bei Serienproduktionen. Aus diesem Grund werden Lackierlinien für winzige Objekte zunehmend mit intelligenten Sensoren, optischen Prüfsystemen und computergestützter Steuerung ausgestattet. So lässt sich die Qualität jeder einzelnen Beschichtung lückenlos überwachen und dokumentieren, etwa durch Inline-Schichtdickenmessung oder visuelle Inspektion mit Kamerasystemen.
Auch die Wahl des Lacks spielt eine wichtige Rolle. Für Kleinteile eignen sich häufig speziell formulierte, niedrigviskose Beschichtungsstoffe, die schnell trocknen, sich gut verteilen und bei geringer Schichtdicke optimale Deckkraft und Haftung bieten. Besonders in der Elektronik werden leitfähige oder isolierende Lacke eingesetzt, während im Kosmetikbereich Glanz, Farbechtheit und Hautverträglichkeit im Vordergrund stehen.
Zusammenfassend lässt sich sagen, dass die Lackiertechnik für winzige Objekte ein hochspezialisiertes Feld ist, das umfassendes Know-how in den Bereichen Maschinenbau, Werkstoffkunde und Automatisierungstechnik erfordert. Mit dem richtigen Zusammenspiel aus präziser Applikationstechnologie, durchdachter Werkstückführung und materialgerechter Lackwahl lassen sich auch kleinste Teile mit höchster Qualität und Effizienz lackieren – eine Schlüsselkompetenz in vielen modernen Industriezweigen.
Die Weiterentwicklung der Lackiertechnik für winzige Objekte hat in den letzten Jahren enorme Fortschritte gemacht, nicht zuletzt durch die zunehmende Miniaturisierung in nahezu allen Industriebereichen. Wo früher händische oder halbautomatische Verfahren dominierten, setzt man heute auf vollautomatische Systeme mit höchster Präzision und Reproduzierbarkeit. Diese Entwicklungen sind eng verknüpft mit der Mikrotechnik und erfordern ein tiefes Verständnis der physikalischen Eigenschaften sowohl des Lacks als auch des Objekts selbst. Die Viskosität des Lackmaterials, die Benetzungsfähigkeit auf verschiedenen Oberflächen, die Trocknungs- und Aushärtungszeiten sowie die Wechselwirkung mit eventuell vorhandenen Vorbehandlungen wie Plasmaaktivierung oder chemischer Reinigung müssen exakt abgestimmt sein. Vor allem bei kritischen Bauteilen, wie etwa Sensoren, Steckverbindern, Mikroschaltern oder Miniaturgehäusen, darf der Lackauftrag keine Funktion beeinträchtigen. Daher kommt es nicht nur auf die Oberflächenabdeckung an, sondern auch darauf, dass bestimmte Zonen gezielt ausgespart werden – ein Vorgang, der oft mit Maskierungstechniken oder selektivem Sprühverfahren gelöst wird.
Ein besonders innovativer Ansatz ist der Einsatz von vollautomatischen Mikrobeschichtungszellen, die mit bildgesteuerter Erkennung arbeiten. Diese Systeme analysieren jedes Teil individuell und passen die Lackapplikation millimetergenau an – ideal bei geometrisch komplexen Teilen oder bei Serien, die trotz Normung gewisse Maßtoleranzen aufweisen. Darüber hinaus gewinnt das Thema Nachhaltigkeit auch in der Mikro-Lackiertechnik zunehmend an Bedeutung. Der Trend geht zu lösemittelarmen oder wasserbasierten Lacksystemen, die bei gleichbleibender Qualität geringere Emissionen verursachen und eine bessere Umweltbilanz aufweisen. Auch Overspray-Reduktion und Rückgewinnungssysteme werden gezielt eingesetzt, um den Materialverbrauch zu minimieren und die Produktionskosten zu senken.
Ein weiterer Aspekt ist die Integration der Lackierung in durchgängige Fertigungslinien, etwa in Verbindung mit Pick-and-Place-Robotern, Trocken- und Härtungskammern oder Verpackungseinheiten. So entsteht ein nahtloser Ablauf von der Rohteilzuführung über die Beschichtung bis zur Auslieferung des fertigen Produkts. Dies reduziert Stillstandszeiten, steigert die Produktivität und erleichtert die Qualitätskontrolle. In der Medizintechnik etwa werden winzige Kunststoff- oder Metallteile lackiert, um antibakterielle Eigenschaften, Farbcodierungen oder bessere Griffigkeit zu erzielen – mit strengsten Anforderungen an Partikelfreiheit und Oberflächenreinheit. In der Uhrenindustrie oder bei Miniaturschmuck kommt es hingegen auf Perfektion im Erscheinungsbild an, bei gleichzeitig hoher Abriebfestigkeit und gleichmäßiger Farbwiedergabe.
Auch additive Fertigungsverfahren wie 3D-Druck haben Einfluss auf die Lackiertechnik für kleine Objekte. Viele gedruckte Teile weisen Oberflächenstrukturen auf, die eine besondere Vorbehandlung und abgestimmte Lackrezepturen benötigen, um eine glatte, homogene und haftfeste Oberfläche zu erzeugen. Hier kommen häufig Zwischenprozesse wie Schleifen, Sandstrahlen oder Plasmaaktivierung zum Einsatz. Insgesamt zeigt sich, dass die Lackierung winziger Objekte heute ein anspruchsvolles Zusammenspiel aus Feinmechanik, Materialwissenschaft, Automatisierung und Prozessüberwachung ist – ein Bereich, der ständig weiterentwickelt wird und neue Lösungen für immer kleinere, funktionalere und hochwertiger beschichtete Produkte hervorbringt.
Die Zukunft der Lackiertechnik für winzige Objekte liegt in noch höherer Integration, miniaturisierter Applikationstechnik und intelligenter Prozessregelung. In modernen Fertigungsumgebungen spielen datengetriebene Systeme eine wachsende Rolle: Parameter wie Sprühdruck, Temperatur, Luftfeuchtigkeit oder Schichtdicke werden in Echtzeit erfasst und automatisch angepasst, um Schwankungen im Prozess auszugleichen. Dadurch können auch in Hochvolumenproduktionen konstante Ergebnisse erzielt werden – ein entscheidender Faktor bei Kleinteilen, bei denen bereits geringste Abweichungen zu Ausschuss führen können. Besonders im Bereich der Mikroelektronik, beispielsweise bei der Herstellung von Leiterplatten oder winzigen Sensorgehäusen, kommt es auf mikrometergenaue Beschichtung an. Hier werden häufig kapazitive oder kontaktlose Messsysteme eingesetzt, um Schichtdicken im Submikronbereich zu kontrollieren. In Verbindung mit softwaregestützter Prozessvisualisierung können so Trends erkannt und Optimierungsmaßnahmen automatisiert eingeleitet werden.
Parallel dazu entwickelt sich die Materialseite weiter. Nanopartikelhaltige Lacke eröffnen völlig neue Möglichkeiten: Sie erlauben funktionale Beschichtungen mit antistatischen, kratzfesten oder selbstreinigenden Eigenschaften. Auch transparente leitfähige Beschichtungen sind inzwischen für Kleinteile realisierbar – eine Technologie, die insbesondere in optoelektronischen Anwendungen wie Miniaturdisplays, Sensorfenstern oder Linsensystemen gefragt ist. Solche Fortschritte erfordern jedoch auch eine präzise Steuerung des Auftragsprozesses, da sich die Eigenschaften dieser Lacke durch Temperatureinfluss, Feuchtigkeit oder mechanische Belastung leicht verändern können.
Ein weiteres Innovationsfeld ist die selektive Laserstrukturierung und -aushärtung. Dabei werden flüssige Lackschichten punktgenau mit einem Laser fixiert oder gehärtet, was völlig neue Gestaltungsspielräume eröffnet – etwa für die gezielte Funktionalisierung bestimmter Teilbereiche eines Objekts. Diese Technologie ist besonders relevant bei der Herstellung multifunktionaler Bauteile, bei denen z. B. dekorative, elektrische und mechanische Eigenschaften in einem einzigen Arbeitsgang erzeugt werden müssen.
Neben technischen Aspekten gewinnt auch das Design eine größere Rolle. Viele winzige Produkte sind nicht nur funktionale, sondern auch ästhetische Objekte – etwa im Bereich der Luxusgüter, Miniaturverpackungen oder Unterhaltungselektronik. Kunden erwarten eine makellose Oberfläche, brillante Farben und eine fühlbare Qualität, auch wenn das Bauteil nur wenige Millimeter groß ist. Das stellt hohe Anforderungen an die Kombination aus Lackformulierung, Applikationsverfahren und Trocknungstechnik. So kommen etwa UV-härtende Systeme zum Einsatz, die in Sekundenbruchteilen ausgehärtet sind und dabei ein sehr hartes, kratzfestes Finish hinterlassen – ideal für dekorative oder beanspruchte Oberflächen auf winzigem Raum.
Schließlich darf auch der Aspekt der Nachhaltigkeit nicht außer Acht gelassen werden. Der Trend geht klar in Richtung umweltschonender Technologien, energieeffizienter Anlagen und recyclingfähiger Materialien. Besonders bei Kleinteilen, die in Milliardenstückzahlen produziert werden – wie etwa Schrauben, Mikrostecker oder medizinische Einwegprodukte – kann der Einsatz umweltfreundlicher Beschichtungslösungen einen enormen Unterschied machen. Unternehmen setzen deshalb verstärkt auf geschlossene Lackkreisläufe, emissionsarme Lacke, energieeffiziente Trocknungssysteme und Prozessoptimierungen, die Ausschuss und Verbrauch minimieren.
Insgesamt lässt sich sagen, dass die Lackiertechnik für winzige Objekte heute eine hochpräzise, digital gestützte und interdisziplinäre Disziplin darstellt. Sie verbindet Maschinenbau, Chemie, Sensorik und Design auf kleinstem Raum – und wird durch neue Anforderungen aus Industrie, Medizin und Konsumgüterbereich kontinuierlich vorangetrieben. Mit jeder technologischen Verbesserung steigt nicht nur die Effizienz, sondern auch die gestalterische Freiheit, sodass sich immer komplexere Produkte in immer höherer Qualität realisieren lassen.
Präzisionslackierung für Kleinteile
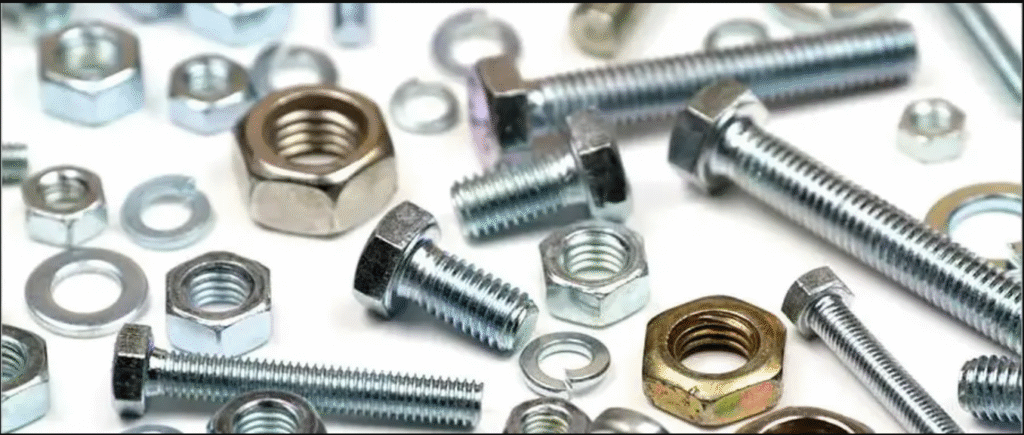
Die Präzisionslackierung für Kleinteile ist ein hochspezialisierter Bereich der Oberflächentechnik, der auf die exakte, gleichmäßige und funktionsgerechte Beschichtung von sehr kleinen, oft komplex geformten Objekten ausgelegt ist. In Industriezweigen wie Elektronik, Medizintechnik, Uhren- und Schmuckherstellung, Feinmechanik, Luft- und Raumfahrt oder Kosmetikverpackung ist die Anforderung an optische Qualität, technische Funktion und Wiederholgenauigkeit besonders hoch – selbst wenn die beschichteten Objekte nur wenige Millimeter oder Mikrometer groß sind.
Im Fokus steht bei der Präzisionslackierung die absolut kontrollierte Applikation des Lacks mit gleichmäßiger Schichtdicke, ohne Tropfen, Läufer oder Materialanhäufungen. Herkömmliche Sprüh- oder Tauchverfahren stoßen hier schnell an ihre Grenzen. Stattdessen kommen mikrofeine Sprühsysteme mit besonders feinen Düsen, elektrostatische Mini-Applikatoren oder speziell angepasste Rotationsbeschichter zum Einsatz. Oft erfolgt die Applikation vollautomatisch, unterstützt durch hochpräzise Positioniersysteme, Kameraführung und sensorbasierte Kontrolle. So können selbst geometrisch komplexe Kleinteile – mit Bohrungen, Kanten, Hinterschneidungen oder glatten und rauen Zonen – optimal beschichtet werden.
Ein weiterer entscheidender Faktor ist die sichere Handhabung der empfindlichen Werkstücke. Vibrationen, statische Aufladung oder Verunreinigungen können zu Fehlbeschichtungen führen. Deshalb kommen in der Regel individuelle Halterungssysteme, Vakuumteller, rotierende Trommeln oder werkstückspezifisch geformte Aufnahmen zum Einsatz, die eine stabile Fixierung und gezielte Lackabdeckung ermöglichen.
Die Präzisionslackierung erfordert nicht nur exakt steuerbare Technik, sondern auch perfekt angepasste Lacksysteme. Diese sind häufig niedrigviskos, temperatur- oder UV-härtend, schnelltrocknend und für dünne, gleichmäßige Schichten optimiert. Auch funktionale Anforderungen spielen eine Rolle: elektrisch leitfähige, isolierende, kratzfeste, antibakterielle oder reflektierende Eigenschaften lassen sich in die Lackformulierung integrieren. In vielen Fällen wird zudem mit Mehrschichtsystemen gearbeitet, die etwa eine Grundierung, eine dekorative Zwischenschicht und eine schützende Deckschicht kombinieren.
Qualitätskontrolle ist ein integraler Bestandteil der Präzisionslackierung. Automatisierte Prüfsysteme mit hochauflösenden Kameras, Laser- oder Ultraschallsensoren, sowie berührungslose Schichtdickenmessung sorgen dafür, dass jede einzelne Komponente den definierten Toleranzen entspricht. Diese hohe Prozesssicherheit ist insbesondere bei sicherheitskritischen oder hochpreisigen Anwendungen unerlässlich.
Die Präzisionslackierung für Kleinteile stellt somit eine anspruchsvolle, technologiegetriebene Disziplin dar, in der sich Mechanik, Chemie, Optik und Automatisierung verbinden. Sie ist ein unverzichtbares Glied in der Fertigungskette hochwertiger Produkte, bei denen kleinste Details über Funktion, Design und Marktwert entscheiden.
Die Präzisionslackierung für Kleinteile entwickelt sich stetig weiter, getrieben durch steigende Anforderungen an Produktqualität, Funktionalität und Effizienz. Moderne Fertigungsprozesse verlangen eine immer bessere Integration der Lackierung in automatisierte Produktionslinien, die neben der Beschichtung auch Handling, Trocknung und Qualitätssicherung nahtlos miteinander verbinden. Insbesondere die Kombination aus Robotertechnik, hochauflösender Bildverarbeitung und adaptiven Steuerungssystemen ermöglicht eine flexible Anpassung an unterschiedliche Bauteilformen und Losgrößen – von der Kleinserie bis zur Großserie mit Millionen Stück pro Jahr.
Ein zentraler Fortschritt liegt auch in der Miniaturisierung der Applikationssysteme. So werden feine Sprühdüsen und Mikrozerstäuber mit Durchmessern von wenigen Mikrometern entwickelt, die eine punktgenaue Lackabgabe erlauben. Dadurch lassen sich selbst winzige Flächen mit hoher Präzision beschichten, während benachbarte Bereiche frei bleiben. Dies eröffnet neue Möglichkeiten etwa bei der selektiven Lackierung von elektronischen Komponenten, bei der gleichzeitig Bereiche für elektrische Kontakte ausgespart werden müssen. Die präzise Steuerung der Lackmenge verhindert nicht nur Materialverschwendung, sondern minimiert auch Nacharbeit und Ausschuss.
Neben der Technik gewinnt die Entwicklung spezieller Lackformulierungen zunehmend an Bedeutung. Fortschrittliche, schnelltrocknende und UV-härtende Systeme ermöglichen eine deutlich verkürzte Durchlaufzeit in der Produktion. Gleichzeitig werden Lacke mit besonderen funktionalen Eigenschaften wie elektrische Leitfähigkeit, Korrosionsschutz oder antibakterielle Wirkung immer häufiger eingesetzt. Dabei müssen diese Beschichtungen auf kleinen Objekten nicht nur zuverlässig haften, sondern auch ihre Eigenschaften über lange Zeiträume unter wechselnden Einsatzbedingungen bewahren.
Ein weiterer wichtiger Aspekt ist die Umweltverträglichkeit der Lackprozesse. Aufgrund der hohen Stückzahlen und des geringen Materialverbrauchs pro Teil ist die Präzisionslackierung prädestiniert für den Einsatz von lösemittelarmen oder wasserbasierten Lacken. Gleichzeitig sind geschlossene Applikationssysteme und Abluftfilter heute Standard, um Emissionen zu reduzieren und gesetzliche Vorgaben einzuhalten. Die Optimierung der Lackierprozesse im Hinblick auf Ressourceneffizienz trägt zudem zur Kostenreduktion und Nachhaltigkeit bei.
In der Praxis zeigt sich, dass die Kombination aus hochpräziser Applikationstechnik, speziell entwickelten Lacksystemen und automatisierter Qualitätssicherung eine kontinuierliche Verbesserung der Produktqualität ermöglicht. So lassen sich kleine Fehler frühzeitig erkennen und gezielt korrigieren. Dies ist besonders wichtig, da eine mangelhafte Lackierung bei Kleinteilen oft erst beim Einbau oder Einsatz auffällt und dort schwerwiegende Folgen haben kann.
Zusammenfassend lässt sich sagen, dass die Präzisionslackierung für Kleinteile ein Schlüsselprozess in der modernen Fertigung darstellt. Sie verbindet technologische Innovationen mit hoher Prozesskontrolle und Materialexpertise, um auch bei minimalen Abmessungen perfekte Oberflächenlösungen zu liefern. Angesichts der stetig wachsenden Anforderungen in Branchen wie Medizintechnik, Elektronik, Feinmechanik oder Konsumgüterherstellung wird die Bedeutung dieser Disziplin in Zukunft weiter zunehmen.
Darüber hinaus gewinnt die Digitalisierung in der Präzisionslackierung zunehmend an Bedeutung. Intelligente Vernetzung von Maschinen, Sensoren und Steuerungssystemen ermöglicht eine durchgängige Prozessüberwachung und datenbasierte Optimierung. Mithilfe von Künstlicher Intelligenz und Machine Learning lassen sich Prozessabweichungen frühzeitig erkennen, Ursachen analysieren und automatisch Gegenmaßnahmen einleiten. So wird nicht nur die Produktqualität verbessert, sondern auch Stillstandszeiten reduziert und die Gesamtanlageneffektivität gesteigert. Diese datengetriebene Vorgehensweise erlaubt zudem eine präzise Rückverfolgbarkeit jeder einzelnen Kleinteilbeschichtung – ein wichtiger Aspekt insbesondere für regulierte Branchen wie die Medizintechnik oder Luftfahrt.
Die Weiterentwicklung der Präzisionslackierung führt außerdem zu immer flexibleren und modulareren Anlagenkonzepten. Hersteller können dadurch schneller auf wechselnde Produktvarianten oder neue Bauteilformen reagieren. Flexibles Handling, schnelle Umrüstzeiten und einfache Integration neuer Applikationsmodule sind entscheidend, um wirtschaftlich produzieren zu können. Auch kundenindividuelle Kleinserien oder Prototypen lassen sich so effizient lackieren, ohne große Investitionen in neue Anlagen zu tätigen.
Materialseitig ist die Forschung ebenso aktiv: Neben traditionellen Lacken entstehen zunehmend Hightech-Beschichtungen mit multifunktionalen Eigenschaften. Beispiele sind Lacke mit integrierten Sensorfunktionen, selbstheilende Beschichtungen oder solche mit verbesserter Umweltbeständigkeit. Gerade im Bereich der Kleinteile ermöglichen solche Innovationen neue Produktfeatures und verbessern die Lebensdauer und Zuverlässigkeit der Bauteile.
Letztlich ist die Präzisionslackierung für Kleinteile ein komplexes Zusammenspiel von Mechanik, Chemie, Elektronik und Software. Nur durch das harmonische Ineinandergreifen all dieser Disziplinen lassen sich die hohen Anforderungen der modernen Produktion erfüllen. Unternehmen, die in diesem Bereich investieren, sichern sich Wettbewerbsvorteile durch bessere Qualität, höhere Effizienz und größere Flexibilität – und sind somit bestens gerüstet für die Herausforderungen der Zukunft.
Automatische Lackieranlage für Kleine Teile
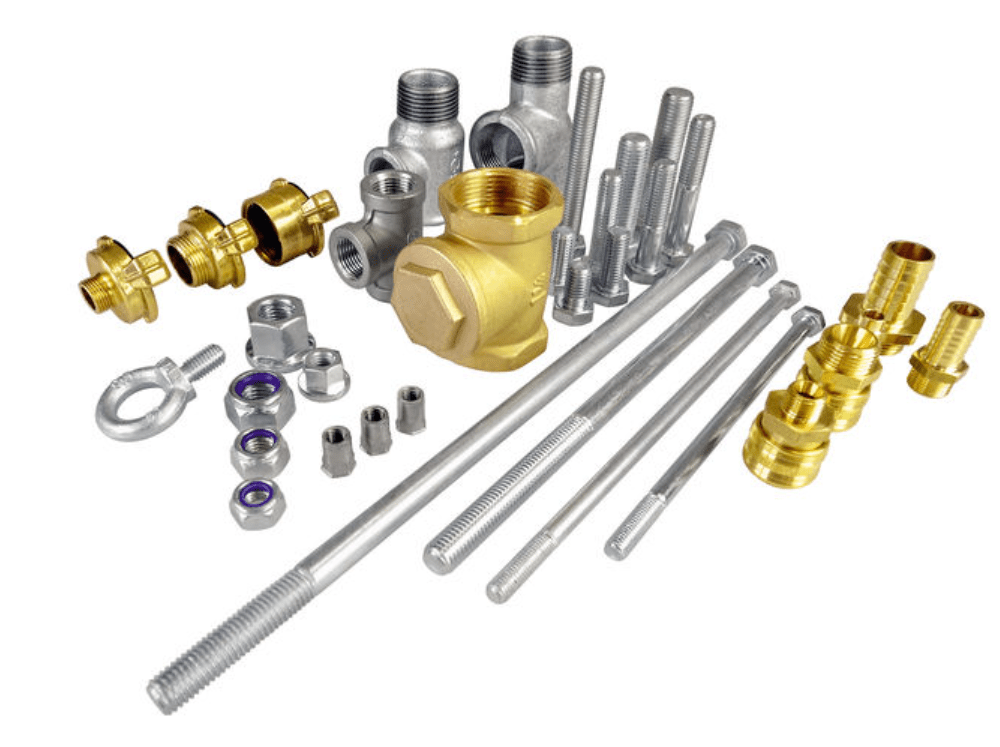
Eine automatische Lackieranlage für kleine Teile ist speziell darauf ausgelegt, winzige Bauteile effizient, präzise und reproduzierbar zu beschichten. Solche Anlagen finden Einsatz in Branchen wie Elektronik, Medizintechnik, Feinmechanik, Schmuckherstellung oder Kosmetik, wo hohe Stückzahlen von Kleinteilen mit gleichbleibend hoher Qualität lackiert werden müssen. Im Zentrum steht dabei die Automatisierung, um manuelle Fehlerquellen zu minimieren, den Durchsatz zu steigern und eine konstante Prozessqualität sicherzustellen.
Typischerweise umfasst eine automatische Lackieranlage für kleine Teile mehrere Hauptkomponenten: eine präzise Zuführung der Rohteile mittels Förderbändern, Vibrationszuführern oder Pick-and-Place-Robotern; ein oder mehrere Applikationssysteme, die je nach Anforderung mit feinen Sprühdüsen, Mikrozerstäubern oder elektrostatischen Lackierpistolen ausgestattet sind; Werkstückträger oder spezielle Haltesysteme, die die Teile während des Lackierens fixieren und optimale Zugänglichkeit gewährleisten; sowie Trocknungs- oder Aushärtekammern, die schnelle und gleichmäßige Trocknung sicherstellen. Die gesamte Anlage wird von einer SPS-Steuerung koordiniert, die die Bewegungsabläufe, Lackdosierung und Prozessparameter exakt steuert.
Ein wichtiger Vorteil automatischer Anlagen ist die hohe Wiederholgenauigkeit und Prozessstabilität. Sensoren überwachen kontinuierlich Parameter wie Lackdurchfluss, Sprühbild, Luftdruck und Schichtdicke. Kamerasysteme können die Oberflächenqualität in Echtzeit prüfen und bei Abweichungen automatische Korrekturen auslösen oder Ausschussteile aussortieren. So wird eine konstante Produktqualität auch bei großen Losgrößen gewährleistet.
Moderne Anlagen sind modular aufgebaut und lassen sich flexibel an unterschiedliche Teileformen und Losgrößen anpassen. Durch den Einsatz von Mehrfachbeschichtungsköpfen oder rotierenden Werkstückhaltern können mehrere Teile gleichzeitig lackiert werden, was die Produktivität zusätzlich erhöht. Außerdem bieten viele Systeme die Möglichkeit, mehrere Lackfarben oder -typen ohne manuellen Wechsel zu verarbeiten, was die Produktionsvielfalt steigert.
Zur Schonung der empfindlichen Teile sind die Anlagen auf sanfte Handhabung ausgelegt. Vakuumspanntechnik, weiche Werkstückauflagen oder rotierende Trommeln verhindern Beschädigungen während des Prozesses. Auch die elektrostatische Aufladung der Teile wird kontrolliert, um eine optimale Lackhaftung zu gewährleisten.
Nicht zuletzt sind moderne automatische Lackieranlagen für kleine Teile auf Nachhaltigkeit ausgelegt. Sie minimieren den Lackverbrauch durch gezielte Applikation, reduzieren Overspray und integrieren Abluftreinigungssysteme. Der Einsatz von lösemittelarmen oder wasserbasierten Lacken wird unterstützt, um Umweltauflagen zu erfüllen und Arbeitssicherheit zu gewährleisten.
Zusammenfassend ermöglicht eine automatische Lackieranlage für kleine Teile eine effiziente, präzise und umweltfreundliche Beschichtung in industriellem Maßstab. Sie ist eine Schlüsseltechnologie für hochwertige Oberflächen bei winzigen Bauteilen und trägt maßgeblich zur Qualitätssicherung und Wirtschaftlichkeit moderner Produktionsprozesse bei.
Die automatische Lackieranlage für kleine Teile zeichnet sich durch eine enge Verzahnung von Mechanik, Steuerungstechnik und Prozesschemie aus, um die hohen Anforderungen der industriellen Fertigung zu erfüllen. Die Zuführung der Kleinteile erfolgt meist über speziell konstruierte Fördersysteme, die eine exakte Positionierung ermöglichen und durch Vibrations- oder Linearbewegungen eine gleichmäßige Teilestromkontrolle gewährleisten. Häufig kommen auch Robotersysteme zum Einsatz, die mit Greifern oder Vakuumaufnahmen die Teile präzise und schonend in die Lackierstation einbringen und nach der Beschichtung sicher weitertransportieren.
Die Lackapplikation selbst nutzt modernste Technologien wie Mikrozerstäuber, die den Lack in feinste Tröpfchen zerteilen und eine homogene, dünne Schicht erzeugen. Elektrostatische Lackierverfahren sind besonders beliebt, weil sie den Lack gezielt auf die meist metallischen oder leitfähigen Oberflächen der Kleinteile ziehen, was den Materialverbrauch reduziert und die Haftung verbessert. Die Applikationsparameter wie Luftdruck, Lackmenge, Abstand zur Düse und Düsenwinkel werden dabei kontinuierlich überwacht und automatisiert angepasst, um eine gleichbleibende Beschichtungsqualität sicherzustellen.
Nach dem Lackauftrag durchlaufen die Teile Trocknungs- oder Härtungsprozesse, die je nach Lacktyp und Anforderung in konvektiven Öfen, UV-Kammern oder Infrarotstrahlern erfolgen. Die Einhaltung der optimalen Trocknungszeiten und Temperaturen ist essenziell, um eine hohe Festigkeit und Oberflächenqualität zu garantieren. Auch hierbei erfolgt die Steuerung automatisiert, häufig mit integrierten Sensoren zur Temperatur- und Feuchtigkeitsüberwachung.
Ein weiterer wichtiger Bestandteil der Anlage ist die Qualitätssicherung, die oft mit optischen Inspektionssystemen realisiert wird. Hochauflösende Kameras prüfen die Oberflächen auf Lackfehler wie Blasen, Läufer, Tropfen oder unzureichende Deckung. Erkennt das System Mängel, kann es automatisierte Sortiermechanismen ansteuern, um fehlerhafte Teile auszusondern. Gleichzeitig werden alle Prozessdaten protokolliert, was eine lückenlose Rückverfolgbarkeit und Prozessoptimierung ermöglicht.
Die modulare Bauweise vieler Anlagen erlaubt eine einfache Anpassung an wechselnde Produktserien oder Lackieranforderungen. So können verschiedene Applikationsköpfe, Trocknungsmodule oder Werkstückträger schnell getauscht werden, was die Flexibilität erhöht und Umrüstzeiten verkürzt. Die Bedienung erfolgt über intuitive Benutzeroberflächen, die auch komplexe Prozessparameter leicht verständlich darstellen und eine einfache Integration in bestehende Fertigungssteuerungen ermöglichen.
Besonders in Branchen mit hohen Hygieneanforderungen, wie der Medizintechnik oder Lebensmittelindustrie, sind automatische Lackieranlagen oft in Reinraumumgebungen integriert. Dort sorgen spezielle Luftfiltersysteme und antistatische Maßnahmen dafür, dass weder Staub noch elektrostatische Aufladungen die Beschichtung beeinträchtigen.
Nicht zuletzt sind nachhaltige Aspekte bei der Auslegung moderner Anlagen zentral. Die Reduzierung von Lackabfall durch gezielte Applikation, der Einsatz emissionsarmer Lacke und die Wiederverwertung von Overspray tragen zur Umweltfreundlichkeit bei. Energieeffiziente Trocknungssysteme und optimierte Prozessabläufe senken den Stromverbrauch und die Betriebskosten, was für Anwender wirtschaftliche Vorteile schafft.
Insgesamt bietet eine automatische Lackieranlage für kleine Teile eine hochpräzise, effiziente und zuverlässige Lösung, die den komplexen Anforderungen moderner Produktionsprozesse gerecht wird. Durch kontinuierliche Weiterentwicklungen in Technik, Material und Steuerung wird diese Technologie auch zukünftig eine zentrale Rolle bei der Herstellung hochwertiger Kleinteile spielen.
Die zunehmende Digitalisierung und Vernetzung im industriellen Umfeld eröffnet für automatische Lackieranlagen für kleine Teile zusätzliche Möglichkeiten, die Effizienz und Qualität weiter zu steigern. Durch den Einsatz von Industrie 4.0-Technologien lassen sich Produktionsdaten in Echtzeit erfassen und auswerten. So können Abläufe optimiert, Wartungsarbeiten vorausschauend geplant und Stillstandszeiten minimiert werden. Die Integration von cloudbasierten Systemen ermöglicht zudem den standortübergreifenden Zugriff auf Prozessdaten und erleichtert die Fernwartung sowie schnelle Reaktionen bei Störungen.
Künstliche Intelligenz (KI) spielt eine immer größere Rolle bei der Prozessüberwachung und Qualitätskontrolle. Intelligente Bildverarbeitungssysteme erkennen auch kleinste Unregelmäßigkeiten in der Lackierung und lernen durch kontinuierliche Datenanalyse, Prozessabweichungen frühzeitig zu identifizieren. So können nicht nur Fehlerquellen schneller behoben, sondern auch die Parameter der Lackierprozesse automatisch optimiert werden, um Ausschuss zu reduzieren und Materialeinsatz zu minimieren.
Zukünftige Entwicklungen gehen auch in Richtung modularer, autonomer Anlagen, die sich flexibel an unterschiedliche Produktionsanforderungen anpassen lassen. Mit Hilfe von Robotik und flexiblen Greifsystemen kann die Lackieranlage verschiedene Kleinteiltypen ohne aufwändige Umrüstungen bearbeiten. Das ist besonders für produzierende Unternehmen wichtig, die eine große Variantenvielfalt in kleinen Losgrößen herstellen.
Darüber hinaus werden umweltfreundliche Beschichtungssysteme und ressourcenschonende Verfahren immer wichtiger. Neue Lackformulierungen mit geringerem VOC-Gehalt, wasserbasierte Systeme und energieeffiziente Trocknungsprozesse helfen dabei, ökologische Anforderungen zu erfüllen und die Betriebskosten zu senken. Die Kombination aus modernster Technik und nachhaltigen Materialien macht automatische Lackieranlagen für kleine Teile zu einem zukunftssicheren Investment.
Abschließend lässt sich sagen, dass automatische Lackieranlagen für kleine Teile heute weit mehr sind als reine Beschichtungsmaschinen. Sie sind hochkomplexe, vernetzte Produktionssysteme, die durch Präzision, Flexibilität und Effizienz überzeugen. Sie ermöglichen es, auch kleinste Bauteile mit höchsten Qualitätsansprüchen zuverlässig und kosteneffizient zu lackieren – ein entscheidender Wettbewerbsvorteil in vielen Industriezweigen.
Lackieranlage für Miniaturteile
Eine Lackieranlage für Miniaturteile ist speziell dafür konzipiert, äußerst kleine und oft komplex geformte Bauteile mit höchster Präzision und gleichmäßiger Schichtdicke zu beschichten. In Bereichen wie der Mikroelektronik, Medizintechnik, Uhren- und Schmuckfertigung sowie der Feinmechanik stellt die Lackierung von Miniaturteilen eine besondere Herausforderung dar, da herkömmliche Beschichtungsverfahren häufig nicht die erforderliche Genauigkeit oder Oberflächenqualität bieten.
Die Anlage ist in der Regel modular aufgebaut und kombiniert mehrere hochentwickelte Komponenten. Zunächst erfolgt die schonende Zuführung der Miniaturteile, oft über Vibrations- oder Linearförderer, die eine präzise Ausrichtung und Positionierung gewährleisten. Robotergestützte Handhabungssysteme mit Vakuum- oder Greifern übernehmen das exakte Platzieren der Teile in der Lackierstation. Dies ist wichtig, um Beschädigungen zu vermeiden und eine vollständige Zugänglichkeit aller Oberflächen sicherzustellen.
Für die Lackapplikation kommen feinste Sprühdüsen, Mikrozerstäuber oder elektrostatische Applikatoren zum Einsatz, die den Lack in mikrometergroße Tröpfchen zerstäuben. Diese ermöglichen eine sehr dünne, homogene und fehlerfreie Beschichtung, selbst auf komplexen Oberflächen und kleinen Konturen. Die Anlagen steuern dabei Parameter wie Sprühwinkel, Luftdruck, Lackvolumen und Abstand zum Werkstück präzise, um eine optimale Verteilung zu gewährleisten.
Nach dem Lackauftrag durchlaufen die Teile oftmals schnelle Trocknungs- oder Aushärtungsprozesse in UV-Kammern, Infrarot-Öfen oder konvektiven Trocknern. Dadurch werden die Lackschichten in kürzester Zeit fixiert und erhalten ihre mechanischen sowie chemischen Eigenschaften. Integrierte Sensorsysteme überwachen Temperatur und Feuchtigkeit, um Prozessabweichungen zu vermeiden.
Ein entscheidender Bestandteil der Anlage ist die automatisierte Qualitätskontrolle. Hochauflösende Kameras und Laserscanner prüfen die Oberfläche auf Fehler wie Läufer, Blasen, Kratzer oder ungleichmäßige Schichtdicken. Bei Abweichungen können automatische Sortier- oder Nachbearbeitungseinheiten aktiviert werden, um die Produktqualität konstant hoch zu halten.
Umweltaspekte spielen bei modernen Lackieranlagen für Miniaturteile eine wichtige Rolle. Die Anlagen sind so ausgelegt, dass der Lackverbrauch durch präzise Applikation minimiert wird. Overspray wird zurückgewonnen und das Abluftsystem sorgt für emissionsarme Verarbeitung. Zudem werden bevorzugt umweltfreundliche, wasserbasierte oder lösemittelarme Lacke eingesetzt.
Zusammenfassend bietet eine Lackieranlage für Miniaturteile eine hochpräzise, effiziente und reproduzierbare Beschichtungslösung, die den steigenden Anforderungen der Industrie an Qualität, Flexibilität und Umweltfreundlichkeit gerecht wird. Sie ist ein unverzichtbares Werkzeug für die Herstellung hochwertiger, funktionsfähiger und optisch ansprechender Miniaturprodukte.
Moderne Lackieranlagen für Miniaturteile sind zunehmend auf Automatisierung und Vernetzung ausgelegt, um eine durchgängige Prozesskontrolle und maximale Effizienz zu gewährleisten. Die Integration von SPS-gesteuerten Abläufen ermöglicht eine präzise Koordination aller Komponenten – von der Teilezuführung über die Lackapplikation bis hin zur Trocknung und Qualitätsprüfung. Besonders in der Serienfertigung ist dies essenziell, um eine gleichbleibende Qualität bei hohen Stückzahlen sicherzustellen und Ausschuss zu minimieren.
Die Applikationstechnik hat sich ebenfalls weiterentwickelt: Mikrozerstäuber und elektrostatische Verfahren sorgen dafür, dass der Lack nicht nur präzise, sondern auch ressourcenschonend aufgetragen wird. Elektrostatische Systeme nutzen die Anziehungskraft zwischen elektrisch geladenem Lack und geerdeten Miniaturteilen, was zu einer deutlich höheren Übertragungsrate und weniger Overspray führt. Dies reduziert Materialverbrauch und Umwelteinwirkungen spürbar.
Handhabungssysteme sind speziell auf die empfindlichen Miniaturteile abgestimmt. Vakuumgreifer mit fein dosiertem Unterdruck oder weiche, formangepasste Greifbacken verhindern Beschädigungen. Rotations- und Schwenkeinheiten erlauben die vollständige Zugänglichkeit aller Oberflächenbereiche und ermöglichen Mehrschichtbeschichtungen ohne Umbau der Anlage. Zusätzlich sorgen Fördertechnik und Teileträger für einen kontinuierlichen Materialfluss und minimieren Stillstandzeiten.
Im Bereich der Trocknung werden energieeffiziente UV- oder Infrarottechnologien eingesetzt, die eine schnelle und schonende Aushärtung gewährleisten. Dies ist besonders wichtig, um Durchlaufzeiten kurz zu halten und gleichzeitig eine hohe Oberflächenqualität sicherzustellen. Sensorik und Temperaturregelung innerhalb der Trocknungseinheiten garantieren eine gleichmäßige Behandlung aller Miniaturteile.
Die Qualitätssicherung ist eng mit den Prozessdaten verknüpft. Bildverarbeitungssysteme mit KI-Unterstützung erkennen zuverlässig Lackfehler und ermöglichen eine lückenlose Rückverfolgbarkeit jedes einzelnen Teils. Dadurch können Unternehmen strenge Qualitätsstandards erfüllen und Dokumentationspflichten in regulierten Branchen wie Medizin- oder Elektronikindustrie erfüllen.
Zukunftsträchtige Entwicklungen fokussieren sich auf flexible und modulare Anlagen, die sich schnell an wechselnde Produktanforderungen anpassen lassen. Automatisierte Reinigungseinheiten, multifunktionale Applikationsköpfe und intelligente Steuerungssysteme ermöglichen die Bearbeitung vielfältiger Miniaturteile in einem System – vom Prototyp bis zur Großserie. Gleichzeitig wird die Nachhaltigkeit weiter vorangetrieben durch den Einsatz innovativer Lackmaterialien und ressourcenschonender Prozessführung.
Insgesamt bilden automatische Lackieranlagen für Miniaturteile ein hochkomplexes und präzises Zusammenspiel aus Mechanik, Elektronik, Chemie und Software. Sie sind unverzichtbar für die Herstellung moderner, hochwertiger Kleinstprodukte mit optimaler Oberfläche und bieten Herstellern entscheidende Wettbewerbsvorteile durch Qualität, Effizienz und Flexibilität.
Darüber hinaus wird die Rolle der Digitalisierung in Lackieranlagen für Miniaturteile immer bedeutender. Vernetzte Systeme ermöglichen eine Echtzeitüberwachung aller Prozessschritte und liefern umfassende Daten zur Analyse und Optimierung. Mit Hilfe von Big Data und künstlicher Intelligenz können Abläufe effizienter gestaltet, Fehlerquellen frühzeitig erkannt und Wartungsarbeiten präventiv geplant werden. Dies erhöht die Anlagenverfügbarkeit und reduziert Ausfallzeiten erheblich, was besonders in der Serienfertigung von Miniaturteilen von großem wirtschaftlichen Vorteil ist.
Parallel dazu rückt die Flexibilität der Anlagen immer stärker in den Fokus. Moderne Systeme sind modular aufgebaut, sodass sie schnell auf neue Produktvarianten oder Lackieraufgaben umgerüstet werden können, ohne dass umfangreiche Umbauten nötig sind. Das ist besonders relevant, da Miniaturteile häufig in kleinen bis mittleren Losgrößen gefertigt werden und individuelle Anpassungen erfordern. Robotergestützte Handhabung, adaptive Applikationssysteme und intelligente Steuerungen ermöglichen die schnelle Umstellung bei minimalem Stillstand.
Ein weiteres Zukunftsfeld ist die Entwicklung neuer, multifunktionaler Beschichtungen, die neben optischen Eigenschaften auch technische Funktionen erfüllen, etwa leitfähige oder selbstheilende Lacke. Diese innovativen Materialien verlangen eine noch genauere Applikation und Prozesskontrolle, die durch modernste Lackieranlagen gewährleistet wird.
Nicht zuletzt spielen ökologische Aspekte eine immer größere Rolle. Die Reduzierung von Lösemittelemissionen, der Einsatz umweltfreundlicher Lacke und energiesparender Trocknungsverfahren sind wesentliche Kriterien bei der Planung und dem Betrieb von Lackieranlagen für Miniaturteile. Nachhaltigkeit und Ressourceneffizienz werden somit zu wichtigen Treibern der technischen Weiterentwicklung.
Insgesamt zeigt sich, dass Lackieranlagen für Miniaturteile sich zu hochkomplexen, intelligent vernetzten Produktionssystemen entwickeln, die durch Präzision, Flexibilität und Umweltbewusstsein überzeugen. Sie sind entscheidend für die Herstellung qualitativ hochwertiger Kleinstprodukte und werden auch künftig eine Schlüsselrolle in vielen Industriezweigen spielen.
Automatische Lackieranlage für kleine Teile
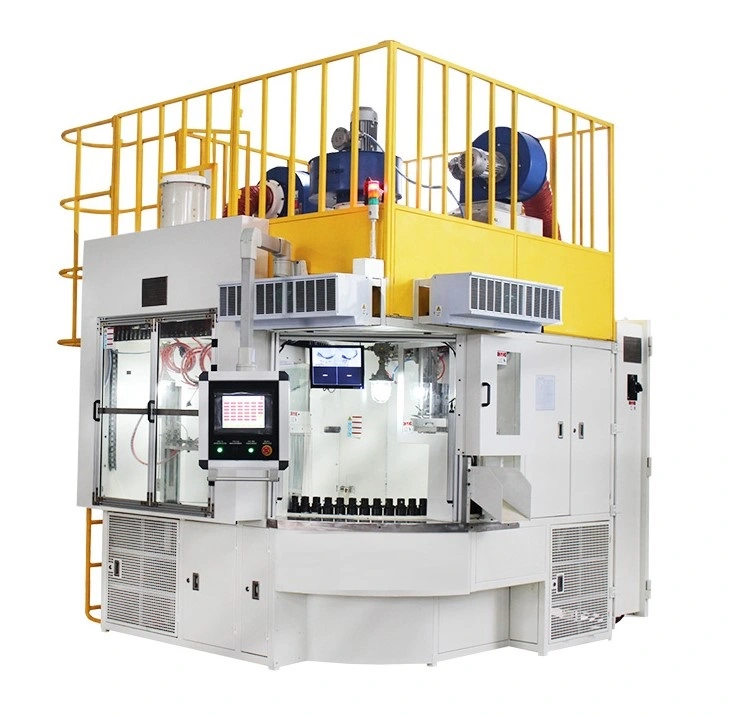
Eine automatische Lackieranlage für kleine Teile ist speziell entwickelt, um winzige Bauteile präzise, effizient und reproduzierbar zu beschichten. Solche Anlagen kommen in Branchen wie Elektronik, Medizintechnik, Feinmechanik, Schmuckherstellung oder Kosmetikverpackung zum Einsatz, wo hohe Stückzahlen kleiner Komponenten mit gleichbleibender Qualität lackiert werden müssen. Die Automatisierung minimiert manuelle Fehler, steigert den Durchsatz und sichert eine konstante Prozessqualität.
Die Anlage besteht typischerweise aus mehreren Hauptkomponenten: einem Fördersystem oder Vibrationszuführern, die die Rohteile exakt positionieren; Applikationssystemen mit Mikrozerstäubern, feinen Sprühdüsen oder elektrostatischen Lackierpistolen; speziellen Werkstückhaltern, die die Teile während der Lackierung fixieren; sowie Trocknungs- und Aushärtekammern für schnelle und gleichmäßige Trocknung. Eine zentrale SPS-Steuerung koordiniert Bewegungen, Lackdosierung und Prozessparameter.
Ein großer Vorteil automatischer Anlagen ist die hohe Wiederholgenauigkeit und Prozessstabilität. Sensoren überwachen Lackdurchfluss, Sprühbild, Luftdruck und Schichtdicke in Echtzeit. Kameras prüfen Oberflächenqualität, erkennen Fehler und ermöglichen automatische Korrekturen oder Aussortierungen. So wird eine gleichbleibende Produktqualität auch bei großen Losgrößen gewährleistet.
Modulare Bauweise erlaubt flexible Anpassungen an unterschiedliche Teileformen und Losgrößen. Mehrfachbeschichtungsköpfe oder rotierende Werkstückhalter ermöglichen simultane Lackierung mehrerer Teile, was die Produktivität steigert. Farb- oder Lackwechsel erfolgen automatisiert, erhöhen die Produktionsvielfalt und minimieren Umrüstzeiten.
Empfindliche Teile werden durch schonende Handhabungstechniken wie Vakuumspannungen oder weiche Auflagen geschützt. Elektrostatische Aufladung wird kontrolliert, um optimale Lackhaftung zu garantieren. Umweltfreundlichkeit wird durch reduzierte Lackmengen, Overspray-Rückgewinnung, emissionsarme Abluftsysteme sowie den Einsatz wasserbasierter oder lösemittelarmer Lacke gefördert.
Insgesamt ermöglicht eine automatische Lackieranlage für kleine Teile eine effiziente, präzise und nachhaltige Beschichtung im industriellen Maßstab. Sie ist eine Schlüsseltechnologie zur Qualitätssicherung und Wirtschaftlichkeit in der Fertigung hochwertiger Kleinteile.
Die automatische Lackieranlage für kleine Teile integriert modernste Technologien, um den komplexen Anforderungen der heutigen Industrie gerecht zu werden. Die Zuführung der Teile erfolgt häufig über präzise Fördersysteme, die mit Vibrationsmechanismen oder Linearbewegungen arbeiten, um eine exakte Positionierung sicherzustellen und den Materialfluss konstant zu halten. Robotergestützte Handhabungssysteme mit Vakuumgreifern oder feinjustierten Greifern übernehmen das sichere und schonende Platzieren der Teile in den Lackierstationen, wodurch Beschädigungen vermieden und eine vollständige Oberflächenzugänglichkeit gewährleistet werden.
Bei der Lackapplikation kommen Mikrozerstäuber und elektrostatische Verfahren zum Einsatz, die den Lack in extrem feine Tröpfchen zerteilen und so eine dünne, gleichmäßige Schicht auftragen. Elektrostatische Lackierung nutzt die Anziehung zwischen geladenem Lack und geerdeten Werkstücken, was nicht nur Material spart, sondern auch die Haftung verbessert und die Oberflächenqualität erhöht. Die Anlage überwacht und reguliert kontinuierlich Parameter wie Luftdruck, Lackmenge und Düsenabstand, um eine konstante Beschichtungsqualität zu garantieren.
Die Trocknungsprozesse erfolgen in modernen UV-Kammern, Infrarot-Öfen oder konvektiven Trocknern, die eine schnelle und gleichmäßige Aushärtung ermöglichen. Sensoren messen Temperatur und Feuchtigkeit präzise, sodass der Prozess optimal gesteuert werden kann und keine Qualitätsverluste durch Unter- oder Überhärtung entstehen.
Für die Qualitätssicherung sind hochauflösende Kamerasysteme und Laserabtaster integriert, die die lackierten Teile auf Fehler wie Tropfen, Blasen oder ungleichmäßige Schichten prüfen. Bei erkannten Mängeln können automatische Sortiereinheiten die fehlerhaften Teile aussortieren, wodurch nur Produkte mit einwandfreier Lackierung weiterverarbeitet werden. Die komplette Prozessdokumentation erfolgt digital und ermöglicht eine lückenlose Rückverfolgbarkeit und Analyse.
Die modulare Bauweise erlaubt eine schnelle Anpassung der Anlage an verschiedene Produktarten und Losgrößen. Unterschiedliche Applikationsköpfe, Werkstückhalter oder Trocknungsmodule können je nach Bedarf integriert oder ausgetauscht werden, was Flexibilität und Wirtschaftlichkeit erhöht. Bedienerfreundliche Steuerungssysteme ermöglichen eine einfache Überwachung und Anpassung der Prozessparameter.
In sensiblen Branchen wie der Medizintechnik oder Lebensmittelindustrie sind die Anlagen oft in Reinraumumgebungen integriert, wo spezielle Luftfiltersysteme und antistatische Maßnahmen die Lackqualität und Hygiene sicherstellen.
Die Nachhaltigkeit spielt ebenfalls eine zentrale Rolle: Optimierte Applikationstechniken minimieren Lackverbrauch und Overspray, während emissionsarme Abluftsysteme und der Einsatz umweltfreundlicher Lacke die Umweltbelastung reduzieren. Energieeffiziente Trocknung und ressourcenschonende Prozesse senken Betriebskosten und unterstützen die Einhaltung gesetzlicher Vorgaben.
Insgesamt ist eine automatische Lackieranlage für kleine Teile eine hochpräzise, effiziente und nachhaltige Lösung, die den heutigen Ansprüchen an Qualität, Flexibilität und Umweltfreundlichkeit gerecht wird und entscheidend zur Wettbewerbsfähigkeit moderner Fertigungsunternehmen beiträgt.
Die Weiterentwicklung automatischer Lackieranlagen für kleine Teile ist eng verbunden mit der fortschreitenden Digitalisierung und Vernetzung in der Industrie. Intelligente Steuerungssysteme erlauben heute eine durchgängige Überwachung aller Prozessschritte, angefangen bei der Teilezuführung über die Lackapplikation bis hin zur Trocknung und Qualitätskontrolle. Sensoren und Kameras liefern in Echtzeit Daten, die über Softwareplattformen ausgewertet werden. So können Abweichungen frühzeitig erkannt und automatisch korrigiert werden, was Ausschuss und Nacharbeit erheblich reduziert.
Die Integration von Künstlicher Intelligenz und Machine Learning ermöglicht eine stetige Prozessoptimierung. Algorithmen analysieren Muster in den Prozessdaten und helfen, die Lackierparameter kontinuierlich anzupassen, um optimale Ergebnisse zu erzielen. Darüber hinaus unterstützen solche Systeme die vorausschauende Wartung, indem sie den Zustand der Anlage überwachen und auf mögliche Ausfälle hinweisen, bevor es zu Stillständen kommt.
Flexibilität ist ein weiteres zentrales Merkmal moderner Anlagen. Durch modulare Bauweisen und den Einsatz von Robotern lassen sich unterschiedliche Miniaturteile mit variierenden Formen, Materialien und Beschichtungsanforderungen schnell und effizient lackieren. Dies ist besonders für Unternehmen wichtig, die häufig Produktvarianten wechseln oder kundenspezifische Kleinserien fertigen.
Umweltfreundlichkeit gewinnt weiterhin an Bedeutung. Der Trend zu lösemittelarmen oder wasserbasierten Lacken wird durch technische Innovationen in der Applikation und Trocknung unterstützt. Anlagen mit geschlossenen Lackierkreisläufen reduzieren Emissionen und ermöglichen eine ressourcenschonende Produktion. Energieeffiziente Trocknungstechnologien, wie LED-UV-Systeme, senken den Energieverbrauch zusätzlich.
Schließlich tragen moderne automatische Lackieranlagen für kleine Teile wesentlich dazu bei, die hohen Qualitätsanforderungen verschiedenster Branchen zu erfüllen. Sie verbinden Präzision, Wirtschaftlichkeit und Nachhaltigkeit und sind somit ein unverzichtbarer Bestandteil der Fertigung von Kleinstkomponenten mit erstklassiger Oberflächenqualität. Mit fortschreitender technologischer Entwicklung werden diese Systeme noch intelligenter, flexibler und umweltbewusster und bleiben ein Schlüssel zur Wettbewerbsfähigkeit in der globalen Produktion.
Lackapplikationskabine
Eine Lackapplikationskabine ist ein speziell konzipierter, geschlossener Arbeitsbereich, der dazu dient, Lackierprozesse sicher, sauber und kontrolliert durchzuführen. Sie wird häufig in Lackierbetrieben, industriellen Fertigungsstraßen und automatisierten Lackieranlagen eingesetzt, um eine optimale Umgebung für die Applikation von Lacken, Farben oder Beschichtungen zu schaffen. Insbesondere bei der Verarbeitung von kleinen oder empfindlichen Teilen spielt die Lackapplikationskabine eine entscheidende Rolle, da sie Staub- und Schmutzeintrag verhindert, die Luftqualität reguliert und die Sicherheit von Bedienpersonal und Umwelt gewährleistet.
Die Kabine ist so ausgelegt, dass sie den Lackauftrag durch Lüftungs- und Filtersysteme unterstützt und gleichzeitig überschüssigen Lacknebel sowie Schadstoffe zuverlässig absaugt. Moderne Lackapplikationskabinen verfügen über ein mehrstufiges Filtersystem, das Partikel und Lösemitteldämpfe aus der Luft entfernt und damit sowohl die Qualität der Beschichtung als auch die Arbeitssicherheit verbessert. Häufig kommen Aktivkohlefilter oder HEPA-Filter zum Einsatz, die selbst feinste Partikel binden können.
Für die Applikation in der Kabine stehen verschiedene Technologien zur Verfügung: Spritzpistolen, elektrostatische Applikationssysteme oder Airless-Sprühsysteme, je nach Anforderungen an Schichtdicke, Oberflächenqualität und Lacktyp. Die Kabine kann manuell bedient oder in automatisierte Fertigungslinien integriert werden, wo Roboter oder automatische Sprühsysteme die Lackierung übernehmen.
Eine gute Kabinenbeleuchtung ist entscheidend, damit der Bediener oder die Kamera- und Sensorsysteme eine optimale Sicht auf das Werkstück haben und die Lackierung präzise überwachen können. Darüber hinaus sind ergonomische und sicherheitstechnische Aspekte, wie etwa Absaugöffnungen in ergonomischer Höhe, eine komfortable Zugänglichkeit sowie Not-Aus-Schalter, wichtige Merkmale moderner Lackapplikationskabinen.
Je nach Einsatzbereich können Lackapplikationskabinen unterschiedliche Größen und Ausstattungen haben – von kleinen Kabinen für Einzelteile oder Muster bis hin zu großen Anlagen für komplette Baugruppen oder Fahrzeugteile. In High-End-Anlagen sind Kabinen häufig klimatisiert und mit kontrollierten Luftströmungen ausgestattet, um optimale Prozessbedingungen zu schaffen und eine gleichmäßige Lackverteilung zu gewährleisten.
Zusammengefasst stellt die Lackapplikationskabine einen essenziellen Bestandteil der Lackiertechnik dar, der maßgeblich zur Qualität der Beschichtung, zur Sicherheit der Mitarbeiter und zum Umweltschutz beiträgt. Durch kontinuierliche technologische Verbesserungen werden diese Kabinen immer effizienter, komfortabler und umweltfreundlicher gestaltet.
Moderne Lackapplikationskabinen sind häufig mit integrierten Steuerungssystemen ausgestattet, die den Luftstrom, die Filterzustände und die Beleuchtung automatisch regeln. Diese Automatisierung trägt dazu bei, konstante Arbeitsbedingungen sicherzustellen und den Energieverbrauch zu optimieren. Die Luftführung erfolgt meist von oben nach unten oder als horizontale Strömung, um Lacknebel effektiv abzuleiten und gleichzeitig das Werkstück frei von Partikeln zu halten. Dadurch wird nicht nur die Lackqualität verbessert, sondern auch die Sicherheit für das Bedienpersonal erhöht.
Ein weiterer wichtiger Aspekt ist die Anpassungsfähigkeit der Kabinen an unterschiedliche Lackierverfahren und Werkstücke. Flexible Modularbauweisen erlauben es, Kabinengrößen und Ausstattung individuell auf den jeweiligen Produktionsprozess abzustimmen. So können kleine Kabinen für Kleinteile mit speziellen Vorrichtungen und Absaugungen ausgerüstet werden, während größere Anlagen für umfangreiche Bauteile oder Serienproduktionen robustere Filtersysteme und höhere Luftwechselraten bieten.
Sicherheitsvorschriften und Umweltauflagen spielen bei der Auslegung und dem Betrieb von Lackapplikationskabinen eine zentrale Rolle. Explosionsgeschützte Ausführungen sind beispielsweise erforderlich, wenn mit lösemittelhaltigen oder leicht entzündlichen Lacken gearbeitet wird. Zudem müssen Abluftsysteme so konzipiert sein, dass Emissionen minimiert und gesetzliche Grenzwerte eingehalten werden. Regelmäßige Wartung und Filterwechsel sind essenziell, um die Leistungsfähigkeit und Sicherheit der Kabine dauerhaft zu gewährleisten.
Die Ergonomie für den Anwender wird ebenfalls immer wichtiger. Kabinen sind oft mit höhenverstellbaren Arbeitstischen, transparenten Sichtfenstern und guter Beleuchtung ausgestattet, um eine komfortable und präzise Lackierung zu ermöglichen. In automatisierten Anlagen übernehmen Roboter die Lackierarbeiten, wobei die Kabine so gestaltet ist, dass Wartung und Zugänglichkeit für Technikpersonal erleichtert werden.
Darüber hinaus werden Lackapplikationskabinen zunehmend in digitale Fertigungsumgebungen integriert. Über Sensorik und Vernetzung lassen sich Betriebsdaten erfassen, auswerten und in die Gesamtprozesssteuerung einbinden. So können etwa Filterzustände überwacht, Prozessparameter optimiert und Wartungszyklen geplant werden. Diese smarte Vernetzung trägt zur Effizienzsteigerung, Kostensenkung und Qualitätssicherung bei.
Insgesamt bilden Lackapplikationskabinen eine unverzichtbare Infrastruktur in der professionellen Lackiertechnik. Sie schaffen kontrollierte Bedingungen für die präzise und sichere Beschichtung verschiedenster Werkstücke, schützen Mensch und Umwelt und ermöglichen die Einhaltung hoher Qualitäts- und Sicherheitsstandards. Mit fortschreitender Technologie werden sie immer effizienter, flexibler und umweltfreundlicher gestaltet, um den Anforderungen moderner Produktionsprozesse gerecht zu werden.
Darüber hinaus entwickeln sich Lackapplikationskabinen zunehmend hin zu ganzheitlichen Systemlösungen, die nicht nur die reine Beschichtung, sondern auch Vor- und Nachbehandlungsprozesse integrieren. So können etwa Reinigungseinheiten, Trocknungs- oder Härtungsstationen direkt an die Kabine angebunden werden, um einen durchgängigen Produktionsfluss zu gewährleisten. Diese Integration ermöglicht kürzere Durchlaufzeiten und reduziert manuelle Eingriffe, was wiederum Fehlerquellen minimiert und die Produktivität steigert.
Ein weiterer Trend ist die zunehmende Nutzung nachhaltiger Technologien in Lackapplikationskabinen. Dazu zählen energiesparende LED-Beleuchtung, hocheffiziente Filtermaterialien und geschlossene Lackierkreisläufe, die den Verbrauch von Lackmaterial und Ressourcen deutlich senken. Zudem werden immer häufiger wasserbasierte oder lösemittelarme Lacke verwendet, deren Verarbeitung besondere Anforderungen an die Kabinenbelüftung und Absaugung stellt.
Die Anpassungsfähigkeit der Kabinen an wechselnde Produktionsanforderungen wird durch modulare Bauweisen und flexible Steuerungssysteme sichergestellt. So können Unternehmen schnell auf neue Lackieraufgaben oder geänderte Umweltvorgaben reagieren, ohne umfangreiche Umbauten durchführen zu müssen. Mobile oder kompakte Kabinenmodelle bieten zudem die Möglichkeit, Lackierprozesse auch in kleineren Fertigungsumgebungen oder bei begrenztem Platzbedarf effizient umzusetzen.
Im Bereich der Automatisierung werden Lackapplikationskabinen zunehmend mit Robotik und intelligenter Sensorik kombiniert. Dies ermöglicht eine präzise und reproduzierbare Lackierung auch bei komplexen Werkstückgeometrien und hohen Stückzahlen. Gleichzeitig unterstützen digitale Assistenzsysteme die Bediener bei der Überwachung und Steuerung des Prozesses, verbessern die Arbeitssicherheit und erleichtern die Einhaltung von Qualitätsstandards.
Zusammenfassend lässt sich sagen, dass Lackapplikationskabinen heute weit mehr sind als einfache Arbeitsräume. Sie sind integrale Bestandteile moderner, effizienter und nachhaltiger Produktionsprozesse, die durch technologische Innovationen kontinuierlich weiterentwickelt werden. Ihre Bedeutung wird mit steigenden Qualitätsanforderungen, zunehmender Automatisierung und wachsendem Umweltbewusstsein in der Industrie weiter zunehmen.
Automatische Pulveranlage für Elektronikteilen
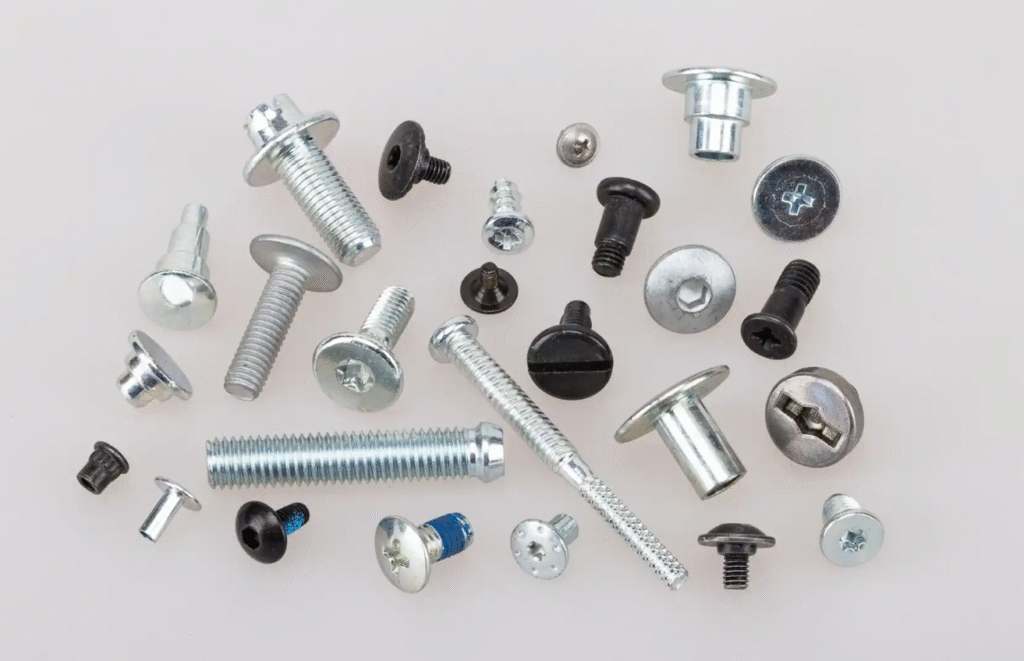
Eine automatische Pulveranlage für Elektronikteile ist speziell darauf ausgelegt, empfindliche Bauteile aus der Elektronikindustrie mit Pulverlackierungen zu versehen, die sowohl optische als auch funktionale Anforderungen erfüllen. Elektronikteile wie Gehäuse, Steckverbinder, Leiterplattenhalter oder kleine Metallkomponenten benötigen eine präzise, gleichmäßige und schadensfreie Beschichtung, um Schutz gegen Korrosion, Verschleiß oder elektrische Isolation zu gewährleisten.
Die Anlage ist typischerweise modular aufgebaut und besteht aus mehreren Hauptkomponenten: einer automatisierten Zuführ- und Positioniereinheit, die die empfindlichen Elektronikteile schonend aufnimmt und sicher in die Pulverbeschichtungsstation transportiert; der Pulversprüheinheit, die mit fein abgestimmten elektrostatischen Applikatoren arbeitet, um den Pulverauftrag exakt zu steuern; sowie einer integrierten Ofenanlage, in der das aufgetragene Pulver bei kontrollierten Temperaturen eingebrannt und ausgehärtet wird.
Besonderes Augenmerk liegt auf der schonenden Handhabung der Teile, da Elektronikteile oft empfindlich gegen mechanische Belastungen oder elektrostatische Entladungen sind. Daher kommen spezielle Werkstückträger, Vakuumspannsysteme oder weiche Greifer zum Einsatz, die Beschädigungen vermeiden und gleichzeitig eine optimale Zugänglichkeit der Oberflächen sicherstellen.
Die elektrostatische Pulverapplikation sorgt für eine gleichmäßige Verteilung des Pulvers auf den geerdeten Elektronikteilen. Durch die kontrollierte Ladung der Pulverpartikel und die gezielte Steuerung der Sprühparameter lassen sich Materialverbrauch reduzieren und eine hochwertige, porenfreie Beschichtung erzielen. Die Anlage ist mit Sensoren ausgestattet, die Parameter wie Pulverdurchsatz, Luftdruck und Sprühbild überwachen und automatisch anpassen, um eine gleichbleibende Qualität zu garantieren.
Nach dem Auftrag durchlaufen die Teile den Einbrennofen, in dem der Pulverlack bei Temperaturen zwischen etwa 160 und 200 Grad Celsius schmilzt und aushärtet. Die Temperatur und Verweildauer im Ofen sind präzise geregelt, um optimale physikalische Eigenschaften der Beschichtung zu erzielen, ohne die empfindlichen Elektronikteile thermisch zu schädigen.
Moderne automatische Pulveranlagen für Elektronikteile sind in der Regel in Fertigungslinien integriert und bieten flexible Steuerungen, die eine einfache Umrüstung auf unterschiedliche Bauteiltypen und Pulverlackarten ermöglichen. Qualitätskontrollsysteme mit Kameras oder Laserscannern prüfen die Beschichtung auf Gleichmäßigkeit, Schichtdicke und Fehler, während Rückmeldungen an die Steuerung die Prozessoptimierung unterstützen.
Zusätzlich wird verstärkt Wert auf umweltfreundliche Prozesse gelegt. Pulverbeschichtungen sind lösemittelfrei und erzeugen kaum Emissionen. Die Anlage ist so konzipiert, dass überschüssiges Pulver effizient zurückgewonnen und wiederverwendet wird, wodurch Materialkosten gesenkt und Umwelteinwirkungen minimiert werden.
Insgesamt bietet eine automatische Pulveranlage für Elektronikteile eine präzise, effiziente und nachhaltige Lösung, die den hohen Qualitätsanforderungen der Elektronikindustrie gerecht wird. Sie ermöglicht eine zuverlässige Schutzbeschichtung sensibler Bauteile und trägt so maßgeblich zur Funktionalität und Lebensdauer moderner Elektronikprodukte bei.
Moderne automatische Pulveranlagen für Elektronikteile sind zunehmend mit fortschrittlichen Steuerungs- und Überwachungssystemen ausgestattet, die eine lückenlose Prozesskontrolle ermöglichen. Sensoren erfassen kontinuierlich Parameter wie Pulverfluss, elektrostatische Ladung, Luftdruck und Temperatur, um den Pulverauftrag optimal zu steuern und Schwankungen zu minimieren. Diese Echtzeitdaten werden in zentrale Prozessleitsysteme eingespeist, die eine automatisierte Anpassung der Anlagenparameter ermöglichen und so eine konstant hohe Beschichtungsqualität gewährleisten.
Die schonende Handhabung der empfindlichen Elektronikteile ist ein weiterer entscheidender Faktor. Automatisierte Greifsysteme, oft mit weichen Greifbacken oder Vakuumspannungen, sorgen dafür, dass die Teile ohne mechanische Belastung transportiert und fixiert werden. Darüber hinaus sind die Werkstückträger so konstruiert, dass sie maximale Zugänglichkeit für den Pulverauftrag bieten und gleichzeitig die elektrostatische Erdung sicherstellen, was für eine effiziente Pulverbeschichtung unerlässlich ist.
Die Pulverbeschichtung selbst nutzt elektrostatische Applikationstechniken, bei denen die Pulverpartikel elektrisch aufgeladen werden und sich durch Anziehung an den geerdeten Bauteiloberflächen anlagern. Dieses Verfahren führt zu einer gleichmäßigen, dickenfreien Beschichtung mit hoher Haftfestigkeit. Überschüssiges Pulver wird durch Rückgewinnungssysteme erfasst, aufbereitet und dem Prozess wieder zugeführt, was Materialverluste minimiert und die Wirtschaftlichkeit erhöht.
Nach dem Auftragen des Pulvers erfolgt die Einbrennung im Ofen, wo die Beschichtung bei präzise kontrollierten Temperaturen schmilzt und aushärtet. Die Temperaturprofile sind speziell auf die thermischen Anforderungen der Elektronikteile abgestimmt, um Schäden an sensiblen Bauteilen zu vermeiden. Moderne Öfen verfügen über zonierte Heizzonen und Luftumwälzungssysteme, die eine gleichmäßige Temperaturverteilung gewährleisten und dadurch qualitativ hochwertige Oberflächen erzeugen.
Flexibilität ist ein weiteres zentrales Merkmal dieser Anlagen. Modulare Bauweisen ermöglichen eine schnelle Umrüstung auf verschiedene Bauteilgrößen, -formen und Pulverlacktypen. Dies ist besonders wichtig in der Elektronikfertigung, wo häufig Produktvarianten in kleinen Losgrößen gefertigt werden. Die Steuerungssysteme erlauben die einfache Speicherung und Abruf von Prozessparametern für unterschiedliche Lackieraufgaben, was Rüstzeiten verkürzt und die Produktionsplanung erleichtert.
Integrierte Qualitätssicherungssysteme überwachen die Schichtdicke und Beschichtungsqualität mittels optischer Sensoren oder berührungsloser Messverfahren. Fehlerhafte Teile können automatisch erkannt und aussortiert werden, was Ausschuss reduziert und die Gesamtqualität der Fertigung erhöht. Gleichzeitig werden alle Prozessdaten dokumentiert, was Rückverfolgbarkeit und Einhaltung von Qualitätsstandards unterstützt.
Umweltfreundlichkeit und Arbeitssicherheit sind bei automatischen Pulveranlagen für Elektronikteile von großer Bedeutung. Da Pulverbeschichtungen lösemittelfrei sind, entfallen viele Emissionen, die bei flüssigen Lacken auftreten. Die Anlagen sind mit geschlossenen Pulversystemen und effektiven Abluftfiltern ausgestattet, die Staub und Partikel sicher abfangen. Durch effiziente Rückgewinnungssysteme wird Pulververbrauch minimiert und Ressourcen geschont.
Zusammenfassend bieten automatische Pulveranlagen für Elektronikteile eine hochpräzise, effiziente und nachhaltige Beschichtungslösung, die den anspruchsvollen Anforderungen der Elektronikindustrie gerecht wird. Sie verbinden modernste Applikationstechniken, schonende Bauteilhandhabung und intelligente Steuerungssysteme zu einem zuverlässigen Gesamtsystem, das die Funktionalität, Langlebigkeit und Ästhetik elektronischer Komponenten maßgeblich verbessert.
Darüber hinaus zeichnet sich die Zukunft automatischer Pulveranlagen für Elektronikteile durch eine verstärkte Integration von Digitalisierung und Automatisierung aus. Durch die Vernetzung mit übergeordneten Produktionssteuerungssystemen (MES, ERP) können Lackierprozesse in Echtzeit überwacht und gesteuert werden, wodurch eine vollständige Transparenz über Produktionsstatus, Materialverbrauch und Wartungsbedarf entsteht. Dies ermöglicht eine präzise Planung, optimierte Ressourcenverwendung und schnellere Reaktionszeiten bei Störungen oder Qualitätsabweichungen.
Fortschrittliche Robotiklösungen übernehmen zunehmend komplexe Aufgaben innerhalb der Pulverapplikation, von der präzisen Teilezuführung über das mehrseitige Beschichten bis hin zur sicheren Übergabe an den Einbrennofen. Die Flexibilität solcher Roboter ermöglicht die Verarbeitung unterschiedlichster Bauteilformen und -größen ohne zeitaufwändige Umrüstungen. Dabei kommen intelligente Greifsysteme zum Einsatz, die individuell auf empfindliche Elektronikteile abgestimmt sind und Beschädigungen zuverlässig vermeiden.
Die kontinuierliche Weiterentwicklung der Pulvermaterialien eröffnet neue Möglichkeiten für funktionale Beschichtungen, die neben Schutz- und Dekoreigenschaften auch elektrische, thermische oder chemische Funktionen erfüllen können. Beispielsweise gewinnen leitfähige oder wärmeleitfähige Pulverlacke an Bedeutung, die gezielt in elektronischen Baugruppen eingesetzt werden, um deren Performance zu verbessern. Die Pulveranlagen müssen daher zunehmend in der Lage sein, solche Speziallacke präzise und zuverlässig zu verarbeiten.
Auch ökologische Aspekte werden stärker berücksichtigt. Die Entwicklung energieeffizienter Einbrennöfen mit innovativen Heiztechnologien wie Infrarot- oder Induktionserwärmung trägt zur Reduktion des Energieverbrauchs bei. Zudem werden Pulverbeschichtungssysteme mit geschlossenen Kreisläufen weiter optimiert, um den Materialeinsatz zu minimieren und Emissionen zu senken. Durch die Kombination dieser Maßnahmen leisten automatische Pulveranlagen einen wichtigen Beitrag zur Nachhaltigkeit in der Elektronikfertigung.
Zusammengefasst sind automatische Pulveranlagen für Elektronikteile hochentwickelte, intelligente Systeme, die Präzision, Effizienz und Umweltbewusstsein vereinen. Sie sind unverzichtbar für die Herstellung moderner Elektronikprodukte mit hohen Qualitätsanforderungen und bieten Herstellern durch kontinuierliche Innovationen nachhaltige Wettbewerbsvorteile in einem dynamischen Marktumfeld.
Pulveranlage für Mini-Bauteile schnell lackieren
Eine Pulveranlage für Mini-Bauteile, die auf schnelle Lackierung ausgelegt ist, vereint hochpräzise Applikationstechnik mit effizienter Prozessgeschwindigkeit und minimalem Materialverlust. Ziel solcher Anlagen ist es, selbst kleinste Werkstücke – wie Schrauben, elektronische Steckverbinder, Federn, Gehäusekomponenten oder Kontaktteile – in großen Stückzahlen gleichmäßig, zuverlässig und in sehr kurzer Zeit zu beschichten.
Der gesamte Ablauf ist auf Geschwindigkeit und Wiederholgenauigkeit optimiert. Die Bauteile werden meist in Chargen über Vibrationszuführungen, Tellerförderer, Drehkörbe oder speziell angepasste Transportbänder in die Beschichtungszone eingebracht. Die Werkstückaufnahme erfolgt so, dass jedes Teil elektrisch leitend fixiert ist, um die elektrostatische Aufladung für die Pulverbeschichtung zu ermöglichen. Gleichzeitig sorgt die Anordnung dafür, dass alle relevanten Oberflächen frei zugänglich sind – ohne Schattenbildung oder unbeschichtete Bereiche.
In der Pulverbeschichtungseinheit kommen präzise steuerbare Hochleistungs-Düsen zum Einsatz, die das Pulver durch elektrostatische Aufladung direkt auf das Bauteil lenken. Aufgrund der kleinen Dimensionen der Mini-Bauteile ist die Feinjustierung der Applikation besonders kritisch: geringe Pulvermengen, sehr feines Sprühbild und exakte Positionierung der Düsen sind entscheidend, um Material zu sparen und gleichmäßige Schichtdicken zu erzielen. Eine dichte Kabinenatmosphäre sowie eine gleichmäßige, gerichtete Luftströmung helfen, Overspray zu minimieren und die Haftung der Partikel zu maximieren.
Die Aushärtung erfolgt typischerweise in schnell reagierenden Durchlauföfen oder kompakten Infrarot- bzw. UV-Einheiten, die für die Masse kleiner Teile in hoher Geschwindigkeit die benötigte Temperatur erreichen und halten können. Die Teile verbleiben dabei nur wenige Minuten im Ofen, wodurch sich die Taktzeiten drastisch reduzieren lassen. Besonders bei thermisch empfindlichen Komponenten können abgestimmte Temperaturprofile und kurze Einwirkzeiten Schäden vermeiden.
Ein entscheidender Faktor bei der schnellen Lackierung von Miniaturteilen ist auch das Rückgewinnungssystem. Überschüssiges Pulver wird direkt aus der Kabine abgesaugt, durch Zyklonabscheider und Filtersysteme gereinigt und automatisch wieder in den Prozess eingespeist. So bleibt der Materialverbrauch niedrig, auch bei Hochdurchsatz-Betrieb.
Moderne Steuerungstechnik erlaubt das Speichern und Abrufen von Parametern für unterschiedliche Bauteile oder Pulversorten, sodass beim Produktwechsel kein zeitintensives Umrüsten nötig ist. In Kombination mit Sensorik und Bildverarbeitungssystemen zur Qualitätssicherung – etwa zur Kontrolle der Schichtdicke oder der Vollständigkeit der Beschichtung – entsteht ein System, das hohe Stückzahlen mit hoher Prozesssicherheit in kürzester Zeit bewältigt.
Diese Art von Anlagen kommt häufig in Branchen wie Elektronikfertigung, Automobilzulieferindustrie, Medizintechnik oder Befestigungstechnik zum Einsatz – überall dort, wo große Mengen kleiner Teile beschichtet werden müssen, ohne auf Qualität und Reproduzierbarkeit zu verzichten. Durch den hohen Automatisierungsgrad und die robuste Auslegung ermöglichen Pulveranlagen für Mini-Bauteile eine äußerst wirtschaftliche und umweltfreundliche Serienfertigung.
Die Auslegung einer Pulveranlage für Mini-Bauteile, die auf hohe Geschwindigkeit ausgelegt ist, erfordert nicht nur präzise Technik, sondern auch eine abgestimmte Taktung zwischen Zuführung, Applikation und Aushärtung. Besonders bei sehr kleinen Teilen ist der Durchsatz entscheidend – hunderte oder tausende Stücke müssen innerhalb kürzester Zeit verarbeitet werden, ohne dass sich Pulverschichtungen überlagern, Partikel unregelmäßig verteilt sind oder es zu Anhaftungsproblemen kommt. Deshalb sind solche Anlagen häufig als Rundläufer, Drehteller- oder Bandanlagen konzipiert, bei denen Bauteile kontinuierlich oder in schneller Rotation an der Sprühzone vorbeigeführt werden. Die gleichbleibende Geschwindigkeit der Bewegung sorgt für ein konstantes Sprühbild und verhindert Überbeschichtung.
Bei lose geschütteten Kleinteilen kommt auch das Wirbelsinterverfahren zum Einsatz, bei dem die Teile in einem elektrisch leitenden Metallkorb rotieren und dabei in ein elektrostatisch geladenes Pulverbett eintauchen. Dieses Verfahren ermöglicht eine sehr schnelle und gleichmäßige Beschichtung aller Seiten, besonders geeignet für symmetrische oder rotationsfähige Bauteile. Noch effizienter ist die Kombination mit thermischer Vorbehandlung, sodass das Pulver beim Kontakt sofort anschmilzt und haftet, was den Einbrennprozess erheblich beschleunigt.
Die Verwendung von speziellen Pulverlacken für Mini-Bauteile ist ebenfalls ein Schlüsselfaktor. Sehr feinkörnige Pulver mit geringer Teilchengröße verbessern die Kantenabdeckung, reduzieren die Schichtdicke und ermöglichen kürzere Aushärtezeiten. Gleichzeitig sind sie sensibler gegenüber Feuchtigkeit und müssen unter kontrollierten Bedingungen gelagert und verarbeitet werden. Daher sind viele schnelle Pulveranlagen mit Klimasteuerungen und Pulverlagersystemen ausgestattet, die konstante Bedingungen sicherstellen.
In der Praxis ist es oft notwendig, mehrere Produktvarianten auf derselben Linie zu lackieren. Deshalb ist die Umrüstzeit ein kritisches Kriterium. Moderne Anlagen ermöglichen per Knopfdruck den Wechsel von Pulversorten, die automatische Reinigung von Düsen und Kabineninnenräumen sowie das Anpassen von Spannungen, Fördermengen und Ofentemperaturen. Die digitale Dokumentation aller Prozessschritte sorgt zusätzlich für eine lückenlose Rückverfolgbarkeit und reduziert Fehlerquellen beim Produktionswechsel.
Zunehmend werden diese Hochgeschwindigkeitsanlagen mit Inline-Kontrollsystemen ausgestattet. Diese erkennen sofort, wenn ein Bauteil unter- oder überbeschichtet wurde oder wenn Pulveranhaftung unvollständig war. Die betroffenen Teile können unmittelbar ausgeschleust werden, wodurch kein Ausschuss in nachgelagerte Fertigungsschritte gelangt. Zudem lassen sich durch die kontinuierliche Datenauswertung Maschinenparameter automatisch nachjustieren, was die Prozesssicherheit noch weiter erhöht.
Diese Anlagen sind in der Regel kompakt konstruiert, um möglichst wenig Stellfläche in Anspruch zu nehmen. Dennoch sind sie robust, für den Dauerbetrieb ausgelegt und wartungsarm. Die Investition in eine solche Pulveranlage zahlt sich für Hersteller von Mini-Bauteilen bereits bei mittleren Stückzahlen aus, da sich Materialkosten, Energieverbrauch und Arbeitsaufwand erheblich reduzieren lassen – bei gleichzeitiger Verbesserung von Qualität, Optik und Funktion der beschichteten Produkte. Die Geschwindigkeit und Präzision dieser Systeme machen sie zu einem unverzichtbaren Bestandteil moderner Produktionsketten für Kleinteile.
Ein weiterer wichtiger Aspekt bei schnellen Pulveranlagen für Mini-Bauteile ist die Integration effizienter Reinigungssysteme. Da bei der Pulverbeschichtung kleine Partikel und Pulverreste unvermeidlich sind, müssen Kabine, Düsen und Fördertechnik regelmäßig und möglichst automatisiert gereinigt werden, um Verschmutzungen, Verstopfungen oder Kreuzkontaminationen zu vermeiden. Hier kommen oft automatisierte Spülsysteme und Luftstrahler zum Einsatz, die den Reinigungsprozess zwischen den Produktionsläufen oder sogar während der laufenden Fertigung kurz und effektiv gestalten. Dadurch bleiben Anlagenverfügbarkeit und Prozessqualität auf einem hohen Niveau.
Ebenso werden bei der schnellen Lackierung von Mini-Bauteilen häufig multifunktionale Pulver verwendet, die spezielle Eigenschaften besitzen, wie etwa erhöhte Kratzfestigkeit, chemische Beständigkeit oder besondere elektrische Isolation. Diese spezialisierten Pulverlacke erfordern eine präzise Abstimmung der Applikationsparameter und der Einbrenntemperaturen, was durch die moderne Steuerungstechnik der Anlagen unterstützt wird. Dies ermöglicht es, auch anspruchsvolle Bauteile zuverlässig und dauerhaft zu beschichten.
Die Kombination aus elektrostatischer Pulverbeschichtung, schneller Durchlaufzeit und automatischer Qualitätskontrolle macht diese Anlagen zu effizienten Systemen, die sich nahtlos in industrielle Fertigungslinien einfügen. Die hohe Prozessstabilität ermöglicht zudem eine konstante Schichtdicke und reproduzierbare Oberflächenqualität – ein entscheidender Faktor gerade in Branchen wie der Elektronik, Medizintechnik oder Feinmechanik, wo kleinste Bauteile höchste Anforderungen erfüllen müssen.
Darüber hinaus wird bei der Planung und Konstruktion solcher Anlagen zunehmend Wert auf ergonomische und sicherheitstechnische Aspekte gelegt. Bedienerfreundliche Schnittstellen, intuitive Bedienpanels und gut erreichbare Wartungsbereiche erleichtern den Umgang mit der Anlage und verkürzen die Rüstzeiten. Sicherheitseinrichtungen wie Not-Aus-Schalter, Überwachungssysteme für Pulverlager und Abluft sowie Explosionsschutzmaßnahmen sind Standard, um Risiken für Personal und Betrieb zu minimieren.
Insgesamt bieten schnelle Pulveranlagen für Mini-Bauteile eine maßgeschneiderte Lösung, die hohe Produktivität, Qualität und Nachhaltigkeit vereint. Sie sind ein wesentlicher Baustein moderner Fertigungsprozesse, um den steigenden Anforderungen an kleine, präzise beschichtete Bauteile in vielfältigen Industriezweigen gerecht zu werden. Durch kontinuierliche Innovationen und Anpassungen an spezifische Kundenbedürfnisse entwickeln sich diese Anlagen stetig weiter und sichern Unternehmen langfristig ihre Wettbewerbsfähigkeit.
Präzisionslackierung für Mikrochips
Die Präzisionslackierung für Mikrochips ist ein hochspezialisierter Prozess, der eine äußerst feine, gleichmäßige und schadensfreie Beschichtung von winzigen Halbleiterbauteilen ermöglicht. Mikrochips, die oft nur wenige Millimeter groß sind, benötigen Schutzlackierungen, die vor Umwelteinflüssen wie Feuchtigkeit, Staub, chemischen Reaktionen oder mechanischem Abrieb schützen, ohne dabei die Funktionalität oder elektrische Leitfähigkeit zu beeinträchtigen.
Da Mikrochips extrem empfindlich auf äußere Einflüsse und mechanische Belastungen reagieren, muss die Lackierung mit höchster Präzision und Sauberkeit erfolgen. In Reinraumumgebungen werden die Chips meist in kleinsten Chargen oder auf Trägerplatten (Wafern) lackiert, um Kontaminationen zu vermeiden. Die Lackierverfahren sind so ausgelegt, dass sie minimale Schichtdicken von wenigen Mikrometern erzeugen, um die empfindlichen Kontaktflächen freizuhalten und gleichzeitig einen zuverlässigen Schutz zu gewährleisten.
Verfahren wie die Lackierung mittels Sprühtechnik mit feinsten Zerstäubern, Tauchbeschichtung (Dip-Coating) oder Spin-Coating kommen hier zum Einsatz. Spin-Coating ist besonders verbreitet, da es durch schnelles Drehen der Wafer eine extrem gleichmäßige und dünne Lackschicht erzeugt. Das Verfahren erlaubt eine exakte Kontrolle der Schichtdicke durch Anpassung von Drehgeschwindigkeit, Lackviskosität und Beschichtungszeit.
Die verwendeten Lacke sind speziell auf die Anforderungen der Mikroelektronik abgestimmt: Sie sind elektrisch isolierend, chemisch stabil und kompatibel mit weiteren Fertigungsschritten. Häufig handelt es sich um UV-härtende oder thermisch aushärtende Schutzlacke, die schnell trocknen und wenig Rückstände hinterlassen.
Zur Gewährleistung der Präzision sind automatisierte Anlagen mit hochauflösenden Sensoren und Kameras ausgestattet, die den Lackierprozess in Echtzeit überwachen. Fehlerhafte Schichten können so frühzeitig erkannt und korrigiert werden. Die Prozesssteuerung sorgt für reproduzierbare Ergebnisse, was für die hohe Qualitätsanforderung der Halbleiterindustrie unerlässlich ist.
Zusätzlich werden Umwelteinflüsse während der Lackierung streng kontrolliert. Reinraumtechnologie, Luftfiltration und kontrollierte Temperatur- und Feuchtigkeitsbedingungen verhindern Verunreinigungen und gewährleisten die Prozessstabilität. Die gesamte Lackierumgebung ist so gestaltet, dass selbst kleinste Partikel keinen Einfluss auf das Beschichtungsergebnis haben.
Zusammengefasst ist die Präzisionslackierung für Mikrochips ein essenzieller Prozessschritt in der Halbleiterfertigung, der durch den Einsatz hochentwickelter Technologien und spezieller Materialien den Schutz und die Leistungsfähigkeit der winzigen Bauteile sichert. Die Kombination aus exakter Applikation, sauberer Umgebung und intelligenter Prozesskontrolle garantiert die Qualität und Zuverlässigkeit moderner Mikrochips.
Zur weiteren Optimierung der Präzisionslackierung für Mikrochips werden zunehmend automatisierte und robotergestützte Systeme eingesetzt, die eine gleichbleibend hohe Prozessqualität bei gleichzeitig hoher Produktionsgeschwindigkeit ermöglichen. Diese Systeme verfügen über feinsteuerbare Applikationsköpfe, die den Lack in minimalen Mengen dosieren und punktgenau auftragen können, um kritische Bereiche wie Kontaktpads freizuhalten und unnötigen Lackauftrag zu vermeiden. Die Steuerung erfolgt computergestützt, wobei Prozessparameter wie Lackfluss, Düsendruck und Applikationswinkel präzise geregelt werden.
Neben klassischen Beschichtungsverfahren gewinnen neuartige Technologien wie die Aerosol-Jet-Bedampfung oder Mikro-Dispensing an Bedeutung, die extrem feine und definierte Lackmuster direkt auf die Chip-Oberflächen aufbringen können. Diese Verfahren ermöglichen nicht nur Schutzbeschichtungen, sondern auch funktionale Beschichtungen, die etwa leitfähige, hydrophobe oder wärmeleitfähige Eigenschaften besitzen und somit die Performance der Mikrochips erweitern.
Die Einbindung von Inline-Inspektionssystemen mit hochauflösenden Kameras und optischen Messverfahren stellt sicher, dass jede Lackschicht auf Gleichmäßigkeit, Dicke und Fehlstellen geprüft wird. Abweichungen können unmittelbar korrigiert oder fehlerhafte Chips aussortiert werden, was die Ausbeute erhöht und Ausschuss reduziert. Die erfassten Qualitätsdaten fließen zudem in datenbasierte Analysen ein, die zur kontinuierlichen Verbesserung des Lackierprozesses beitragen.
Da die Lackierung ein empfindlicher Prozessschritt ist, erfolgt sie meist in streng kontrollierten Reinraumbedingungen, die Staubpartikel und elektrostatische Aufladungen minimieren. Moderne Anlagen sind mit Luftfiltern, ionisierenden Geräten und temperaturgeregelten Umgebungen ausgestattet, um optimale Voraussetzungen für die Lackierung zu schaffen und gleichzeitig die Integrität der Mikrochips zu gewährleisten.
Nicht zuletzt gewinnt die Umweltverträglichkeit der Lackierprozesse zunehmend an Bedeutung. Daher werden bevorzugt UV-härtende oder wasserbasierte Schutzlacke eingesetzt, die schnell trocknen, wenig Schadstoffe freisetzen und den Energieverbrauch senken. Dies trägt dazu bei, den ökologischen Fußabdruck der Halbleiterfertigung zu reduzieren und gleichzeitig die hohen Qualitätsanforderungen zu erfüllen.
Insgesamt ist die Präzisionslackierung von Mikrochips ein hochkomplexer, technologisch anspruchsvoller Prozess, der durch modernste Applikationsmethoden, intelligente Steuerungen und kontrollierte Umgebungen die Funktionalität, Zuverlässigkeit und Langlebigkeit moderner Halbleiterprodukte sicherstellt. Die stetige Weiterentwicklung dieser Verfahren ist ein entscheidender Faktor für den Fortschritt in der Mikroelektronik und deren vielfältige Anwendungen.
Darüber hinaus spielt die Integration von datengetriebenen Analysen und Künstlicher Intelligenz (KI) in die Präzisionslackierung von Mikrochips eine zunehmend wichtige Rolle. Durch die Erfassung und Auswertung großer Mengen an Prozess- und Qualitätsdaten können Muster erkannt, Anomalien frühzeitig identifiziert und Optimierungen automatisiert umgesetzt werden. KI-gestützte Systeme ermöglichen eine adaptive Prozesssteuerung, bei der Parameter wie Lackdicke, Applikationsgeschwindigkeit oder Trocknungszeit in Echtzeit angepasst werden, um Schwankungen auszugleichen und konstant optimale Beschichtungsergebnisse zu erzielen.
Die Digitalisierung und Vernetzung der Lackieranlagen erlaubt zudem eine umfassende Rückverfolgbarkeit der gefertigten Mikrochips. Jeder Schritt des Lackierprozesses wird dokumentiert und kann bei Bedarf lückenlos nachvollzogen werden – ein wesentlicher Vorteil für die Qualitätssicherung und Zertifizierungen in der Halbleiterindustrie. Diese Transparenz unterstützt zudem die schnelle Fehleranalyse und minimiert Produktionsausfälle.
Innovative Materialien, wie nanoskalige Schutzlacke oder hybride Beschichtungen, eröffnen neue Möglichkeiten, die Eigenschaften von Mikrochips weiter zu verbessern. Solche Lacke können neben dem Schutz vor mechanischen und chemischen Einflüssen auch funktionale Effekte wie verbesserte Wärmeableitung oder elektrische Isolation bieten. Die präzise Applikation dieser Materialien erfordert hochentwickelte Beschichtungstechnologien, die sich in modernen Präzisionslackieranlagen für Mikrochips zunehmend durchsetzen.
Ein weiterer Fortschritt zeigt sich in der Miniaturisierung und Flexibilisierung der Beschichtungssysteme. Kompakte Applikationsmodule lassen sich direkt in bestehende Fertigungslinien integrieren, ohne den Produktionsfluss zu unterbrechen. Dies ermöglicht eine nahtlose Integration der Präzisionslackierung in automatisierte Produktionsketten und reduziert den Platzbedarf sowie die Investitionskosten.
Schließlich wächst der Anspruch an Nachhaltigkeit und Ressourceneffizienz auch in der Mikroelektronikfertigung. Die Verwendung umweltfreundlicher Lacke, die Minimierung von Overspray durch präzise Applikation sowie energieeffiziente Trocknungsprozesse sind feste Bestandteile moderner Anlagenkonzepte. So wird die Präzisionslackierung von Mikrochips nicht nur leistungsfähiger und zuverlässiger, sondern auch umweltverträglicher gestaltet.
Zusammenfassend lässt sich sagen, dass die Präzisionslackierung für Mikrochips durch eine Kombination aus hochentwickelter Technik, intelligenten Steuerungssystemen und innovativen Materialien zu einem unverzichtbaren Prozess in der Halbleiterherstellung geworden ist. Sie sichert die Qualität, Funktionalität und Langlebigkeit der Mikrochips und trägt entscheidend zum Erfolg moderner Elektronikprodukte bei.
Lackiersystem für elektronische Bauteile
Ein Lackiersystem für elektronische Bauteile ist speziell darauf ausgelegt, empfindliche Komponenten der Elektronikindustrie mit hochwertigen Schutz- oder Isolierlacken zu beschichten. Solche Systeme müssen präzise arbeiten, um die Funktionalität der Bauteile nicht zu beeinträchtigen, während sie gleichzeitig Schutz vor Feuchtigkeit, Korrosion, Staub und mechanischem Abrieb bieten.
Das Lackiersystem besteht meist aus mehreren Komponenten, darunter eine automatische Zuführungseinheit, die die Bauteile schonend und präzise positioniert. Die Applikation des Lacks erfolgt häufig mittels feinjustierter Spritztechniken, wie elektrostatischer Lackierung, Airless-Spritzverfahren oder Mikro-Dispensing, die eine exakte Dosierung und gleichmäßige Beschichtung gewährleisten. Für besonders kleine oder komplex geformte Bauteile können auch Tauch- oder Beschichtungsverfahren wie Spin-Coating zum Einsatz kommen.
Die Steuerung des Lackiersystems ist automatisiert und erlaubt die Anpassung an verschiedene Bauteilgrößen, Formen und Lackarten. Moderne Anlagen sind mit Sensorik ausgestattet, die Parameter wie Lackfluss, Düsendruck und Schichtdicke in Echtzeit überwachen und für eine konstante Qualität sorgen. Zusätzlich sind oft Inline-Kamerasysteme integriert, die den Lackierprozess visuell kontrollieren und Fehler sofort erkennen.
Nach der Lackapplikation erfolgt die Trocknung oder Aushärtung, die je nach Lacktyp thermisch, UV- oder IR-basiert erfolgen kann. Dabei sind Temperaturprofile und Verweildauer genau abgestimmt, um die empfindlichen elektronischen Bauteile nicht zu beschädigen. Die Trocknungseinheiten sind häufig direkt in das Lackiersystem integriert, um kurze Durchlaufzeiten zu ermöglichen.
Sicherheits- und Umweltaspekte spielen eine wichtige Rolle: Die Anlagen verfügen über effiziente Abluft- und Filtersysteme, um Lacknebel und Lösungsmittelreste abzufangen und die Emissionen zu minimieren. Zudem werden bevorzugt umweltfreundliche, lösemittelfreie oder wasserbasierte Lacke eingesetzt.
Insgesamt bietet ein modernes Lackiersystem für elektronische Bauteile eine präzise, flexible und nachhaltige Lösung, die den hohen Qualitätsanforderungen der Elektronikfertigung gerecht wird und eine zuverlässige Schutzbeschichtung bei gleichzeitig hoher Prozessgeschwindigkeit gewährleistet.
Moderne Lackiersysteme für elektronische Bauteile zeichnen sich durch eine hohe Automatisierung und Integration in Fertigungsprozesse aus, was eine konsistente Qualität und hohe Durchsatzraten ermöglicht. Die automatische Bauteilzuführung erfolgt häufig über spezielle Förderbänder, Vibrationsförderer oder robotergestützte Greifsysteme, die eine präzise Positionierung gewährleisten und mechanische Belastungen vermeiden. Dabei wird darauf geachtet, dass empfindliche Kontaktflächen oder Anschlussstellen frei von Lack bleiben, um die Funktionalität der Bauteile sicherzustellen.
Die Applikationstechnologien sind vielfältig und werden je nach Bauteilgröße, -form und Lacktyp ausgewählt. Elektrostatische Spritzverfahren sind besonders effektiv, da sie durch die elektrische Aufladung der Lackpartikel eine gleichmäßige und haftstarke Beschichtung ermöglichen und Materialverluste durch Overspray minimieren. Für sehr kleine oder komplexe Bauteile kommen zudem Mikro-Dispensing oder selektive Lackierverfahren zum Einsatz, die punktgenau arbeiten und individuelle Lackmuster erlauben.
Zur Sicherstellung der Prozessstabilität sind moderne Anlagen mit umfangreicher Sensorik ausgestattet, die Parameter wie Luftdruck, Lackfluss, Sprühwinkel und Schichtdicke überwachen. Echtzeitdaten werden an zentrale Steuerungssysteme übermittelt, die automatisierte Anpassungen vornehmen können, um Schwankungen im Lackierprozess auszugleichen. Diese intelligente Prozessregelung erhöht die Wiederholgenauigkeit und reduziert Ausschuss.
Die Integration von Inline-Qualitätskontrollen mit optischen Inspektionssystemen ermöglicht die sofortige Erkennung von Beschichtungsfehlern wie Bläschen, ungleichmäßigen Schichten oder Fehlstellen. Dadurch können defekte Bauteile frühzeitig aussortiert oder der Prozess angepasst werden, was die Gesamteffizienz steigert. Die dokumentierten Qualitätsdaten unterstützen zudem die Rückverfolgbarkeit und erfüllen Anforderungen an die Produktionsdokumentation.
Nach der Lackierung erfolgt die Aushärtung, die je nach verwendetem Lacktyp thermisch in Umluft- oder Durchlaufofenanlagen, mittels UV-Licht oder Infrarotstrahlung erfolgt. Dabei sind die Trocknungsparameter genau auf die Empfindlichkeit der elektronischen Bauteile abgestimmt, um Beschädigungen durch Überhitzung zu vermeiden. Schnelle Trocknungszeiten tragen dazu bei, den Produktionsfluss zu optimieren und die Anlageneffizienz zu erhöhen.
Umwelt- und Sicherheitsaspekte werden durch den Einsatz von geschlossenen Kabinensystemen, effizienten Absauganlagen und Filtertechnologien berücksichtigt. Diese Systeme minimieren die Freisetzung von Lackpartikeln und Lösungsmitteln in die Umgebung und schützen sowohl die Mitarbeiter als auch die Umwelt. Gleichzeitig ermöglichen moderne Pulver- oder wasserbasierte Lacke eine nachhaltigere Beschichtung mit reduzierten Emissionen.
Zusammengefasst stellen moderne Lackiersysteme für elektronische Bauteile flexible, präzise und umweltfreundliche Lösungen dar, die den hohen Anforderungen an Qualität, Geschwindigkeit und Sicherheit in der Elektronikfertigung gerecht werden. Durch kontinuierliche Innovationen in Applikationstechnik, Automatisierung und Materialentwicklung tragen sie maßgeblich zur Leistungsfähigkeit und Zuverlässigkeit elektronischer Produkte bei.
Darüber hinaus gewinnen modulare Aufbaukonzepte bei Lackiersystemen für elektronische Bauteile zunehmend an Bedeutung. Solche modularen Systeme erlauben eine flexible Anpassung an unterschiedliche Produktionsanforderungen und Bauteiltypen, ohne dass umfangreiche Umbauten oder Neuinvestitionen notwendig sind. Module für Zuführung, Applikation, Trocknung und Qualitätskontrolle können individuell kombiniert und bei Bedarf erweitert oder ausgetauscht werden. Dies ermöglicht eine schnelle Reaktion auf Marktveränderungen und Produktinnovationen.
Ein weiterer Trend ist die Integration von Industrie-4.0-Technologien in Lackiersysteme. Vernetzung, Datenanalyse und smarte Sensorik erlauben eine vorausschauende Wartung (Predictive Maintenance) und eine optimierte Prozesssteuerung. So können Ausfallzeiten minimiert und die Anlagenverfügbarkeit maximiert werden. Zudem ermöglichen digitale Zwillinge eine realitätsgetreue Simulation und Optimierung des Lackierprozesses vor tatsächlicher Umsetzung, was Zeit und Kosten spart.
In der Materialentwicklung werden zunehmend multifunktionale Lacke eingesetzt, die neben Schutz auch zusätzliche Eigenschaften wie Wärmeableitung, elektrische Leitfähigkeit oder antistatische Wirkung bieten. Lackiersysteme müssen deshalb flexibel genug sein, um verschiedenste Lacktypen zuverlässig zu verarbeiten und ihre spezifischen Anforderungen an Applikation und Aushärtung zu erfüllen.
Schließlich wächst die Bedeutung ergonomischer und sicherheitstechnischer Aspekte in Lackiersystemen für elektronische Bauteile. Intuitive Bedienoberflächen, automatisierte Reinigungsprozesse und gut zugängliche Wartungspunkte erhöhen die Bedienerfreundlichkeit und reduzieren Stillstandszeiten. Gleichzeitig sorgen umfangreiche Sicherheitsfunktionen und Umweltvorkehrungen für den Schutz von Personal und Umwelt.
Insgesamt spiegeln moderne Lackiersysteme für elektronische Bauteile den aktuellen Stand der Technik wider und verbinden Präzision, Flexibilität und Nachhaltigkeit. Sie sind ein wesentlicher Bestandteil hochwertiger Elektronikfertigung und sichern Herstellern Wettbewerbsvorteile durch effiziente, zuverlässige und umweltbewusste Beschichtungsprozesse.
Kompakte Lackiertechnik für Elektronik
Kompakte Lackiertechnik für Elektronik zeichnet sich durch platzsparende, effiziente und präzise Systeme aus, die speziell für die anspruchsvollen Anforderungen der Elektronikfertigung entwickelt wurden. Aufgrund der oft begrenzten Raumverhältnisse in modernen Produktionsanlagen müssen diese Lackiersysteme flexibel integrierbar und dennoch leistungsfähig sein, um kleine und empfindliche elektronische Bauteile zuverlässig zu schützen.
Solche kompakten Systeme nutzen häufig automatisierte Zuführungen mit platzsparenden Förderbändern oder robotergestützte Handhabungen, die eine exakte Positionierung der Bauteile ermöglichen. Die Applikation erfolgt meist mittels elektrostatischer Spritztechnik oder Mikro-Dispensing, welche eine sehr feine, gleichmäßige Beschichtung bei minimalem Overspray gewährleisten. Das sorgt für Materialersparnis und verhindert Verschmutzungen empfindlicher Bauteile.
Durch den modularen Aufbau lassen sich kompakte Lackiersysteme leicht an unterschiedliche Produktionsanforderungen anpassen und in bestehende Fertigungslinien integrieren. Sie verfügen über kurze Durchlaufzeiten dank optimierter Trocknungs- und Aushärtemodule, häufig basierend auf UV- oder Infrarottechnologien, die auch thermisch sensible Elektronikkomponenten schonen.
Kompakte Anlagen bieten zudem eine hohe Prozessautomatisierung mit integrierter Sensorik zur Echtzeitüberwachung von Lackierparametern wie Schichtdicke, Luftdruck und Lackfluss. Diese intelligente Steuerung gewährleistet gleichbleibend hohe Beschichtungsqualität bei reduziertem Ausschuss. Gleichzeitig sorgen integrierte Filter- und Absaugsysteme für eine saubere Arbeitsumgebung und erfüllen hohe Umwelt- und Sicherheitsstandards.
Insgesamt ermöglichen kompakte Lackiertechniken für Elektronik eine effiziente, flexible und präzise Beschichtungslösung, die den speziellen Anforderungen kleiner, empfindlicher Bauteile gerecht wird und gleichzeitig den Platzbedarf und Energieverbrauch in der Produktion minimiert.
Darüber hinaus zeichnen sich kompakte Lackiersysteme für die Elektronik durch ihre hohe Flexibilität aus, die es ermöglicht, verschiedenste Bauteilgrößen und -formen in einer Anlage zu verarbeiten. Durch den Einsatz modularer Applikationsköpfe und justierbarer Fördertechnik können kleine Losgrößen oder Produktwechsel schnell und ohne großen Aufwand realisiert werden, was insbesondere für die variantenreiche Elektronikfertigung von großem Vorteil ist. Die kompakten Maße der Systeme erlauben zudem den Einbau in Reinraumumgebungen, wo höchste Anforderungen an Sauberkeit und Partikelfreiheit herrschen.
Ein weiterer wesentlicher Vorteil ist die reduzierte Verweilzeit der Bauteile im Lackierprozess, die durch optimierte Abläufe und schnelle Trocknungs- oder Aushärtemethoden erreicht wird. UV- und Infrarotstrahler ermöglichen beispielsweise eine nahezu sofortige Aushärtung des Lacks, wodurch die Durchsatzrate erheblich gesteigert werden kann. Gleichzeitig wird die thermische Belastung der empfindlichen elektronischen Komponenten minimiert, was die Ausbeute erhöht und die Produktqualität verbessert.
Moderne kompakte Lackiertechnik-Systeme sind zudem mit intelligenten Steuerungs- und Überwachungssystemen ausgestattet. Sensoren kontrollieren kontinuierlich Prozessparameter wie Sprühdruck, Lackverbrauch und Schichtdicke und passen diese automatisch an, um konstante Beschichtungsergebnisse zu gewährleisten. Diese Automatisierung reduziert menschliche Fehler und sorgt für eine gleichbleibend hohe Qualität auch bei längeren Produktionsläufen.
Nicht zuletzt wird bei der Entwicklung kompakter Lackieranlagen großer Wert auf Umweltfreundlichkeit und Arbeitssicherheit gelegt. Geschlossene Kabinen mit effizienten Absaugsystemen sorgen dafür, dass Lackpartikel und Lösungsmittel nicht in die Umgebung gelangen. Der Einsatz von lösemittelfreien oder wasserbasierten Lacken reduziert Emissionen zusätzlich und trägt zu einem nachhaltigen Produktionsprozess bei.
Insgesamt bieten kompakte Lackiersysteme für die Elektronikbranche eine ideale Kombination aus Effizienz, Präzision und Nachhaltigkeit. Sie erfüllen die hohen Anforderungen moderner Elektronikfertigung, ermöglichen eine flexible und schnelle Produktion und schonen dabei Ressourcen sowie Arbeitsumfeld – Faktoren, die in einem zunehmend wettbewerbsintensiven Markt entscheidend sind.
Ergänzend zu den bereits genannten Vorteilen ermöglichen kompakte Lackiersysteme für die Elektronik durch ihre Bauweise eine einfache Integration in bestehende Fertigungslinien und ermöglichen so eine nahtlose Verbindung mit vorgelagerten und nachgelagerten Prozessschritten wie Bestückung, Prüfung oder Verpackung. Diese Vernetzung fördert eine durchgängige Automatisierung und unterstützt die Umsetzung von Industrie-4.0-Konzepten, bei denen die Anlagenkommunikation und Datenanalyse zur Optimierung der Produktion beitragen.
Die flexible Softwaresteuerung solcher Systeme erlaubt es, Prozessparameter schnell und präzise an unterschiedliche Produkte anzupassen. Voreingestellte Programme können jederzeit abgerufen oder modifiziert werden, was insbesondere bei häufigen Produktwechseln Zeit und Kosten spart. Die Bedienoberflächen sind oft intuitiv gestaltet und ermöglichen es auch weniger erfahrenem Personal, die Anlage sicher und effizient zu betreiben.
Ein weiteres Merkmal kompakter Lackiertechnik für die Elektronik ist die Möglichkeit, unterschiedliche Lackarten und Beschichtungsmethoden innerhalb desselben Systems zu verwenden. So kann etwa der Einsatz von Pulverlacken, Flüssiglacken oder speziellen funktionalen Beschichtungen je nach Anforderung flexibel umgesetzt werden. Diese Vielseitigkeit steigert die Einsatzmöglichkeiten der Anlagen erheblich und macht sie zukunftssicher gegenüber sich wandelnden Marktbedürfnissen.
Aufgrund der empfindlichen Natur elektronischer Bauteile werden bei kompakten Lackiersystemen zudem oft schonende Handhabungstechniken verwendet, wie Vakuumgreifer oder weiche Greifarme, die Beschädigungen während des Transports und der Lackierung verhindern. Diese Systeme sind so konzipiert, dass sie auch kleinste und filigrane Teile sicher fixieren und dabei optimale Zugänglichkeit für den Lackauftrag gewährleisten.
Zusammengefasst bieten kompakte Lackiersysteme für die Elektronik eine perfekte Balance zwischen Präzision, Flexibilität, Effizienz und Umweltfreundlichkeit. Sie sind ein entscheidendes Element moderner Produktionsprozesse, die den wachsenden Anforderungen an Qualität, Durchsatz und Nachhaltigkeit gerecht werden und damit die Wettbewerbsfähigkeit von Elektronikherstellern langfristig sichern.
Kleine Leiterplatten automatisch lackieren
Das automatische Lackieren kleiner Leiterplatten ist ein wichtiger Prozessschritt in der Elektronikfertigung, der den Schutz der empfindlichen Bauteile und Leiterbahnen gewährleistet. Hierbei kommen spezialisierte Anlagen zum Einsatz, die präzise, reproduzierbare und materialschonende Beschichtungen ermöglichen, um die Funktionalität und Langlebigkeit der Leiterplatten sicherzustellen.
Die automatische Lackierung erfolgt meist in geschlossenen Lackierkabinen, in denen die Leiterplatten über Förderbänder oder Trägersysteme sicher transportiert werden. Die Zuführung ist so gestaltet, dass die Bauteile fest fixiert und optimal positioniert werden, um eine vollständige und gleichmäßige Beschichtung zu gewährleisten. Dabei ist es wichtig, empfindliche Kontaktstellen, wie Steckverbindungen oder Lötpunkte, frei von Lack zu halten.
Zur Applikation des Schutzlacks werden häufig elektrostatische Spritzverfahren verwendet, die durch die elektrische Aufladung des Lacks eine gleichmäßige Verteilung auf der Leiterplattenoberfläche erzielen. Alternativ kommen auch Tauchverfahren (Dip-Coating) oder selektive Lackiertechniken zum Einsatz, bei denen nur definierte Bereiche beschichtet werden, um Funktionalität und elektrische Kontakte zu erhalten.
Moderne Anlagen sind mit Sensorik ausgestattet, die Parameter wie Lackverbrauch, Luftdruck und Sprühwinkel kontinuierlich überwachen und regeln. Dies garantiert eine konstante Schichtdicke und verhindert Materialverschwendung. Außerdem sind Qualitätskontrollsysteme integriert, die mittels Kameras oder optischer Sensoren die Beschichtung prüfen und Fehler erkennen, um defekte Leiterplatten frühzeitig auszuschleusen.
Nach dem Auftragen erfolgt die Trocknung oder Aushärtung des Lacks, entweder thermisch in Umluftöfen oder mittels UV-Licht, je nach Lacktyp. Dabei werden Temperatur und Verweildauer genau gesteuert, um die empfindlichen elektronischen Bauteile nicht zu beschädigen und gleichzeitig eine optimale Schichthärtung zu gewährleisten.
Automatische Lackieranlagen für kleine Leiterplatten sind zudem platzsparend und energieeffizient ausgelegt. Sie verfügen über effiziente Absaug- und Filtersysteme, die Lackpartikel sicher abscheiden und Umwelt- sowie Arbeitsschutzanforderungen erfüllen. Der Einsatz von umweltfreundlichen, lösemittelfreien oder wasserbasierten Lacken unterstützt zudem eine nachhaltige Produktion.
Insgesamt ermöglichen automatische Lackiersysteme für kleine Leiterplatten eine hochpräzise, effiziente und reproduzierbare Schutzbeschichtung, die die Qualität und Zuverlässigkeit elektronischer Produkte maßgeblich verbessert und gleichzeitig Produktionskosten und Umweltbelastung reduziert.
Zur weiteren Optimierung des automatischen Lackierprozesses für kleine Leiterplatten werden zunehmend flexible Zuführsysteme eingesetzt, die unterschiedliche Formate und Größen ohne manuellen Eingriff verarbeiten können. Diese Systeme ermöglichen den schnellen Wechsel zwischen verschiedenen Produktserien und minimieren Rüstzeiten, was besonders in der Kleinserienfertigung oder bei häufigen Produktwechseln von großem Vorteil ist. Die Bauteile werden dabei schonend transportiert, oft durch Vakuumspannsysteme oder sanfte Greifer, um mechanische Beschädigungen zu vermeiden.
Die Applikation des Schutzlacks erfolgt durch feinjustierte Düsen, die eine präzise Steuerung des Lackstrahls erlauben und Overspray minimieren. Insbesondere bei komplexen Leiterplatten mit unterschiedlichen Höhen und empfindlichen Bauteilen sorgt diese präzise Lackierung dafür, dass alle Bereiche zuverlässig geschützt werden, ohne Kurzschlüsse oder Funktionsstörungen zu verursachen. Zudem werden innovative Verfahren wie selektive Lackierung oder Digitaldruck-Technologien eingesetzt, um nur definierte Zonen zu beschichten und so Material zu sparen.
Automatisierte Inline-Inspektionssysteme ergänzen den Prozess, indem sie die Qualität der Beschichtung unmittelbar nach dem Lackierprozess überprüfen. Hochauflösende Kameras und optische Sensoren detektieren Fehlstellen, Blasenbildung oder unzureichende Schichtdicke und ermöglichen eine sofortige Nachbesserung oder Aussortierung. Dies erhöht die Ausbeute und sorgt für eine konstante Produktqualität, die den hohen Anforderungen der Elektronikindustrie gerecht wird.
Die Aushärtung des Lacks ist präzise abgestimmt auf die verwendeten Materialien und die thermische Empfindlichkeit der Leiterplatten. Moderne UV- oder Infrarot-Trocknungssysteme gewährleisten kurze Taktzeiten und schonen zugleich die Bauteile. Energieeffiziente Öfen und umweltfreundliche Trocknungsverfahren tragen zusätzlich zu einem nachhaltigen Produktionsprozess bei.
Durch die Kombination aus präziser Applikation, automatisierter Qualitätssicherung und effizienter Aushärtung bietet die automatische Lackierung von kleinen Leiterplatten eine hochgradig zuverlässige und wirtschaftliche Lösung. Sie unterstützt Hersteller dabei, die Funktionalität und Lebensdauer ihrer elektronischen Produkte zu sichern und gleichzeitig Produktionskosten und Umweltauswirkungen zu minimieren – wichtige Faktoren für den Erfolg im globalen Wettbewerb der Elektronikbranche.
Zusätzlich ermöglichen moderne automatische Lackiersysteme für kleine Leiterplatten durch die Integration von digitalen Steuerungssystemen eine umfassende Prozessüberwachung und -dokumentation. Alle relevanten Parameter wie Lacktemperatur, Sprühvolumen, Luftdruck und Durchlaufgeschwindigkeit werden in Echtzeit erfasst und analysiert. Diese Daten bilden die Grundlage für eine lückenlose Rückverfolgbarkeit und ermöglichen es, Produktionsprozesse kontinuierlich zu optimieren und Qualitätsstandards dauerhaft einzuhalten.
Ein weiterer Fortschritt ist die zunehmende Modularität der Anlagen, wodurch Hersteller flexibel auf wechselnde Produktionsanforderungen reagieren können. Module für unterschiedliche Applikationsverfahren, Trocknungstechnologien oder Inspektionsmethoden lassen sich einfach ergänzen oder austauschen, was die Anpassungsfähigkeit der Produktionslinie erhöht und Investitionskosten reduziert. Diese Flexibilität ist besonders in dynamischen Märkten wie der Elektronikfertigung von großem Vorteil.
Des Weiteren wird die Anwenderfreundlichkeit durch intuitive Bedienoberflächen und automatisierte Wartungsfunktionen verbessert. Fehlermeldungen und Wartungshinweise werden klar angezeigt, wodurch Ausfallzeiten minimiert und die Betriebssicherheit erhöht werden. Auch die Schulung von Bedienpersonal wird durch benutzerfreundliche Systeme erleichtert, was den reibungslosen Produktionsablauf unterstützt.
Nicht zuletzt gewinnt der Aspekt der Nachhaltigkeit zunehmend an Bedeutung. Moderne Lackiersysteme setzen verstärkt auf umweltfreundliche Lacke und energieeffiziente Trocknungsmethoden, um den ökologischen Fußabdruck der Produktion zu reduzieren. Durch geschlossene Kreislaufsysteme für Pulver- oder Flüssiglacke wird Materialverluste minimiert, und effiziente Absauganlagen sorgen für saubere Arbeitsumgebungen.
Insgesamt bieten automatische Lackiersysteme für kleine Leiterplatten eine hochentwickelte, flexible und nachhaltige Lösung, die den komplexen Anforderungen moderner Elektronikfertigung gerecht wird. Sie sichern eine gleichbleibend hohe Produktqualität, steigern die Produktionseffizienz und tragen dazu bei, Ressourcen zu schonen – entscheidende Faktoren für den langfristigen Erfolg von Herstellern in einem wettbewerbsintensiven Umfeld.
Lackieranlage für SMD-Komponenten
Eine Lackieranlage für SMD-Komponenten ist speziell auf die Anforderungen der Oberflächenmontage (Surface-Mount Technology) ausgelegt und dient dem Schutz der winzigen, empfindlichen Bauteile vor Umwelteinflüssen wie Feuchtigkeit, Staub, Korrosion oder mechanischer Beanspruchung. Aufgrund der geringen Größe und hohen Empfindlichkeit der SMD-Bauteile erfordert die Lackierung eine präzise, gleichmäßige und schonende Beschichtung, die die Funktionalität und elektrische Leistungsfähigkeit der Komponenten nicht beeinträchtigt.
Die Anlage umfasst in der Regel eine automatisierte Zuführung, die SMD-Komponenten entweder lose in Behältern oder bereits bestückt auf Leiterplatten sicher und genau positioniert. Um eine optimale Beschichtung zu erzielen, werden die Bauteile während der Lackierung festgehalten oder auf speziellen Trägersystemen fixiert, um Bewegungen und Beschädigungen zu vermeiden. Die Applikation erfolgt meist durch fein abgestimmte Spritzverfahren, beispielsweise elektrostatische Pulverbeschichtung oder Flüssiglack-Sprühsysteme, die eine dünne, homogene Schicht auftragen und Overspray minimieren.
Für besonders filigrane oder komplexe Bauteile können selektive Lackiertechniken eingesetzt werden, bei denen nur definierte Bereiche beschichtet werden, um Kontaktstellen und Lötpads frei zu halten. Diese Verfahren werden häufig durch Robotik oder präzise Düsensteuerung realisiert, um maximale Genauigkeit zu gewährleisten.
Die Lackieranlage ist mit moderner Sensorik ausgestattet, die Parameter wie Lackfluss, Düsendruck und Schichtdicke kontinuierlich überwacht und automatisch regelt. So wird eine konstante Qualität und Reproduzierbarkeit der Beschichtung sichergestellt. Zudem sind Inspektionssysteme integriert, die den Lackierprozess optisch kontrollieren und Fehlstellen oder Beschädigungen erkennen, um Ausschuss zu minimieren.
Nach der Applikation erfolgt die Aushärtung des Lacks entweder thermisch in Umluft- oder Durchlaufofenanlagen oder mittels UV-Strahlung, je nach Lacktyp. Dabei wird auf die thermische Belastbarkeit der SMD-Komponenten Rücksicht genommen, um Schäden zu vermeiden. Die Trocknungszeit ist kurz, um den Durchsatz der Fertigungslinie hoch zu halten.
Um Umwelt- und Arbeitsschutzanforderungen gerecht zu werden, sind die Anlagen mit geschlossenen Kabinen, effizienten Absaug- und Filtersystemen ausgestattet, die Lacknebel und Lösungsmittel sicher abscheiden. Der Einsatz umweltfreundlicher Lacke, wie lösemittelfreier oder wasserbasierter Varianten, unterstützt eine nachhaltige Produktion.
Insgesamt bietet eine moderne Lackieranlage für SMD-Komponenten eine hochpräzise, effiziente und flexible Lösung, die den Schutz und die Zuverlässigkeit der empfindlichen Bauteile gewährleistet, die Produktionsqualität verbessert und gleichzeitig Umwelt- und Sicherheitsstandards erfüllt.
Moderne Lackieranlagen für SMD-Komponenten sind oft modular aufgebaut, wodurch sie sich leicht an verschiedene Produktionsanforderungen und Bauteilgrößen anpassen lassen. Die Automatisierung umfasst dabei nicht nur die Lackapplikation, sondern auch die Bauteilzuführung, Positionierung und Qualitätskontrolle. Robotergestützte Systeme übernehmen die präzise Handhabung der winzigen Bauteile, minimieren das Risiko von Beschädigungen und erhöhen die Prozessgeschwindigkeit. Dadurch sind auch kurze Rüstzeiten bei Produktwechseln möglich, was besonders in der variantenreichen Elektronikfertigung von Vorteil ist.
Die Applikationstechniken reichen von elektrostatischer Pulverbeschichtung über feinstoffliches Sprühen bis hin zu selektiven Beschichtungsverfahren, bei denen nur bestimmte Bereiche gezielt lackiert werden. Diese Vielseitigkeit ermöglicht es, die Schutzschicht genau auf die Anforderungen des jeweiligen Bauteils abzustimmen. Zudem tragen präzise gesteuerte Lackierparameter wie Sprühdruck, Düsenabstand und Lacktemperatur dazu bei, eine gleichmäßige Schichtdicke zu erzielen und Materialverschwendung zu vermeiden.
Integrierte Inline-Inspektionssysteme überwachen die Beschichtungsqualität in Echtzeit. Hochauflösende Kameras und optische Sensoren erkennen Unregelmäßigkeiten, unzureichende Deckung oder Kontaminationen und ermöglichen eine sofortige Reaktion durch Nachbearbeitung oder Aussortierung fehlerhafter Bauteile. Diese Rückkopplung erhöht die Ausbeute und gewährleistet eine konstant hohe Produktqualität.
Die anschließende Aushärtung erfolgt je nach verwendetem Lacktyp entweder thermisch, durch UV-Licht oder Infrarotstrahlung. Dabei sind die Prozessparameter sorgfältig auf die thermische Empfindlichkeit der SMD-Komponenten abgestimmt, um Schäden zu vermeiden und gleichzeitig kurze Durchlaufzeiten zu ermöglichen. Energieeffiziente Trocknungssysteme tragen zudem zu einem nachhaltigen Produktionsprozess bei.
Für den Umweltschutz und die Arbeitssicherheit sind die Anlagen mit geschlossenen Sprühkabinen, effizienten Absauganlagen und Filtersystemen ausgestattet, die Emissionen von Lackpartikeln und Lösungsmitteln minimieren. Die Verwendung von wasserbasierten oder lösemittelfreien Lacken unterstützt zusätzlich die Nachhaltigkeit der Fertigung.
Insgesamt bieten Lackieranlagen für SMD-Komponenten eine hochentwickelte, präzise und flexible Lösung, die den komplexen Anforderungen der Elektronikproduktion gerecht wird. Sie sorgen für zuverlässigen Schutz der Bauteile, optimieren den Produktionsfluss und unterstützen Hersteller dabei, qualitativ hochwertige und langlebige Elektronikprodukte zu fertigen.
Ergänzend zu den bereits erwähnten Vorteilen setzen moderne Lackieranlagen für SMD-Komponenten verstärkt auf digitale Vernetzung und datenbasierte Prozessoptimierung. Durch die Integration von Sensorik, Aktorik und intelligenter Software können sämtliche Prozessschritte in Echtzeit überwacht und gesteuert werden. Diese Vernetzung ermöglicht nicht nur eine hohe Prozessstabilität, sondern auch die vorausschauende Wartung der Anlagen (Predictive Maintenance), wodurch Ausfallzeiten minimiert und die Anlagenverfügbarkeit maximiert werden.
Die automatisierte Datenerfassung und -analyse unterstützt zudem die Rückverfolgbarkeit jedes einzelnen Bauteils und des gesamten Lackierprozesses, was besonders in regulierten Branchen wie der Medizintechnik oder Luftfahrt von großer Bedeutung ist. Qualitätsdaten werden erfasst, dokumentiert und können bei Bedarf für Audits oder Zertifizierungen bereitgestellt werden, was die Einhaltung höchster Qualitätsstandards gewährleistet.
Darüber hinaus ermöglichen flexible Steuerungssysteme eine einfache Anpassung der Lackierparameter bei Produktwechseln oder der Einführung neuer Lacktypen. So können Hersteller schnell auf veränderte Anforderungen reagieren und gleichzeitig die Effizienz ihrer Fertigungslinien erhalten. Intuitive Benutzeroberflächen und automatisierte Programmierfunktionen erleichtern die Bedienung und reduzieren Schulungsaufwand.
Innovative Beschichtungsmaterialien, wie dünnschichtige, multifunktionale Schutzlacke, finden ebenfalls zunehmend Einsatz in diesen Anlagen. Sie bieten neben mechanischem Schutz zusätzliche Eigenschaften wie verbesserte Wärmeableitung, elektrische Isolation oder Schutz vor elektromagnetischen Störungen. Die präzise Applikation dieser Hightech-Lacke erfordert modernste Applikationstechnologien, die in den Anlagen integriert sind.
Schließlich wird großer Wert auf Nachhaltigkeit gelegt. Effiziente Nutzung von Lackmaterialien, geschlossene Kreislaufsysteme und umweltfreundliche Lacke reduzieren den Verbrauch von Ressourcen und Emissionen. Ebenso sorgen ergonomische Anlagenkonzepte für sichere und angenehme Arbeitsbedingungen.
In Summe spiegeln moderne Lackieranlagen für SMD-Komponenten den aktuellen Stand der Technik wider und bieten eine zuverlässige, flexible sowie nachhaltige Lösung, die den hohen Anforderungen der Elektronikfertigung gerecht wird und Herstellern hilft, wettbewerbsfähig zu bleiben.
Automatisches Lackieren von Platinen
Das automatische Lackieren von Platinen – insbesondere Leiterplatten (PCBs) – ist ein entscheidender Schritt in der Elektronikfertigung, um elektronische Baugruppen gegen äußere Einflüsse wie Feuchtigkeit, Staub, Chemikalien und mechanische Belastung zu schützen. Dieser Vorgang erfolgt in spezialisierten, hochpräzisen Lackieranlagen, die darauf ausgelegt sind, empfindliche Komponenten gleichmäßig zu beschichten, ohne Funktionselemente wie Steckkontakte, Lötflächen oder Prüfpunkte zu beeinträchtigen.
Der Prozess beginnt mit der automatisierten Zuführung der Platinen. Diese können entweder lose, auf Trägersystemen oder in Magazinen eingelegt und durch die Anlage geführt werden. Die Ausrichtung erfolgt automatisch, sodass jede Platine exakt positioniert ist. Dadurch kann die Lackierung mit hoher Wiederholgenauigkeit und ohne menschliches Eingreifen durchgeführt werden.
Bei der Lackapplikation kommen verschiedene Verfahren zum Einsatz – darunter Sprühlackierung, selektive Beschichtung mit präzisen Düsen oder auch Film-Coating-Systeme. Besonders bewährt hat sich das selektive Lackieren: Dabei wird der Schutzlack nur auf definierte Bereiche der Platine aufgetragen, wobei empfindliche Zonen bewusst ausgespart werden. Dies geschieht mithilfe programmierbarer Applikationsköpfe, die millimetergenau gesteuert werden – oft unterstützt durch Kamerasysteme und CAD-Daten der jeweiligen Baugruppe.
Um eine gleichmäßige Schichtdicke zu erreichen, werden Parameter wie Lackviskosität, Sprühdruck, Düsenabstand, Bewegungsgeschwindigkeit und Temperatur elektronisch überwacht und dynamisch angepasst. Moderne Anlagen sind in der Lage, auch komplexe Platinengeometrien mit hoher Bauteildichte oder unregelmäßigen Oberflächen zuverlässig zu beschichten – und das auch im Durchlaufbetrieb mit kurzen Taktzeiten.
Nach dem Auftrag folgt die Aushärtung des Lacks. Je nach Lacktyp – ob UV-härtend, lufttrocknend oder thermisch aushärtend – stehen unterschiedliche Verfahren zur Verfügung. Integrierte Trocknungszonen mit UV-Modulen, IR-Strahlern oder Konvektionstrocknung sorgen dafür, dass die Beschichtung in kürzester Zeit fest und widerstandsfähig wird, ohne die elektronischen Bauteile zu überhitzen.
Die gesamte Lackieranlage ist in der Regel in ein geschlossenes System integriert, das für kontrollierte klimatische Bedingungen sorgt, Partikelkontamination verhindert und die Abluft reinigt. Filter, Absaugungen und Lösemittelrückgewinnungssysteme sorgen dafür, dass Umwelt- und Sicherheitsvorschriften eingehalten werden. Zusätzlich werden häufig umweltfreundliche, wasserbasierte Lacke verwendet, die weniger flüchtige organische Verbindungen (VOC) enthalten.
Automatisches Lackieren von Platinen bietet viele Vorteile: eine gleichbleibend hohe Qualität, geringeren Materialverbrauch, minimale Ausschussquoten, hohe Produktionsgeschwindigkeiten und eine hervorragende Prozesssicherheit. Es ist ein unverzichtbarer Schritt in der Fertigung von langlebigen und robusten Elektronikprodukten, sei es in der Automobilindustrie, Telekommunikation, Medizintechnik oder Unterhaltungselektronik.
Durch den hohen Automatisierungsgrad beim Lackieren von Platinen wird nicht nur die Beschichtungsqualität verbessert, sondern auch der gesamte Fertigungsprozess deutlich effizienter. Die vollautomatische Steuerung der Anlage erlaubt es, in Echtzeit auf Veränderungen zu reagieren, etwa bei Schwankungen der Umgebungsbedingungen oder bei minimalen Abweichungen im Lackbild. Sensoren überwachen kontinuierlich alle relevanten Prozessparameter, von der Temperatur über den Luftdruck bis zur Lackviskosität, und ermöglichen so eine automatische Feinjustierung während des Betriebs. Diese adaptive Prozessführung reduziert Ausschuss, spart Material und minimiert Nachbearbeitungen.
Eine zentrale Rolle spielt auch die Softwaresteuerung der Lackieranlage. Über eine intuitive Bedienoberfläche können verschiedene Lackierprogramme gespeichert und abgerufen werden, was die Umrüstung auf neue Platinenlayouts beschleunigt. CAD-Daten der jeweiligen Leiterplatte werden dabei direkt in das System eingespeist und ermöglichen eine punktgenaue, programmierbare Ansteuerung der Applikationsdüsen. Auch komplexe Muster und mehrlagige Beschichtungen lassen sich auf diese Weise fehlerfrei und in reproduzierbarer Qualität realisieren.
Ein weiteres entscheidendes Merkmal moderner Anlagen ist die nahtlose Integration in die gesamte Produktionslinie. Das automatische Lackiersystem kommuniziert mit vorgelagerten Prüf-, Bestückungs- und Lötstationen und kann auf deren Ausgänge reagieren, etwa indem defekte oder nicht lackierfähige Platinen automatisch ausgesondert oder umgeleitet werden. Diese Vernetzung erhöht die Produktionssicherheit und unterstützt die Umsetzung von Industrie-4.0-Strategien, bei denen Maschinen nicht isoliert, sondern im Verbund arbeiten und Daten untereinander austauschen.
Auch die Qualitätssicherung ist tief in den Prozess eingebunden. Inline-Inspektionssysteme erfassen jede lackierte Platine direkt nach dem Applikationsschritt und analysieren optisch die Lackverteilung, Schichtdicke und potenzielle Fehler wie Blasen, Risse oder Fehlstellen. Bei Abweichungen erfolgt entweder eine automatische Korrektur oder eine sofortige Ausschleusung. Die dabei generierten Qualitätsdaten werden archiviert und können zur kontinuierlichen Prozessoptimierung oder für lückenlose Chargendokumentationen verwendet werden.
Nicht zu vernachlässigen ist außerdem die Nachhaltigkeit moderner Lackierprozesse. Durch exakte Dosierung und die gezielte Applikation wird der Lackverbrauch erheblich reduziert. Überschüsse werden in geschlossenen Kreisläufen aufgefangen, gefiltert und wiederverwendet. Auch die Abluftsysteme sind so ausgelegt, dass Lösungsmitteldämpfe effizient abgesaugt und durch Aktivkohlefilter gereinigt werden. So wird nicht nur der Arbeitsschutz verbessert, sondern auch der ökologische Fußabdruck der gesamten Fertigungslinie gesenkt.
Letztlich bietet das automatische Lackieren von Platinen eine perfekte Kombination aus Präzision, Geschwindigkeit, Reproduzierbarkeit und Umweltfreundlichkeit. Es ist ein unverzichtbares Element in jeder hochmodernen Elektronikproduktion, in der Qualität, Langlebigkeit und Effizienz keine Gegensätze, sondern zentrale Erfolgsfaktoren sind.
Ein besonders zukunftsweisender Aspekt beim automatischen Lackieren von Platinen ist die zunehmende Nutzung künstlicher Intelligenz zur Prozessoptimierung. Durch die Analyse großer Datenmengen aus laufenden Lackierprozessen kann das System Muster erkennen und daraus Rückschlüsse für eine kontinuierliche Verbesserung ziehen. So lassen sich beispielsweise Veränderungen in der Applikationsqualität frühzeitig prognostizieren – lange bevor sie mit bloßem Auge sichtbar wären. Die Anlage kann dann automatisch Gegenmaßnahmen einleiten, etwa durch die Anpassung von Sprühparametern oder die frühzeitige Wartung von Komponenten wie Düsen oder Pumpen.
Die Flexibilität moderner Anlagen geht so weit, dass sie sowohl Standardleiterplatten als auch hochspezialisierte Platinen – etwa für Hochfrequenztechnik, Automotive-Steuergeräte oder medizinische Geräte – verarbeiten können, ohne dass größere Umrüstungen notwendig sind. Die Anlage erkennt automatisch, welches Produkt ihr zugeführt wird, wählt das passende Lackierprogramm und stellt sich selbstständig auf die Anforderungen ein. Das spart Zeit, reduziert Fehlerquellen und erhöht die Auslastung der Produktion.
Auch neue Beschichtungsmaterialien eröffnen zusätzliche Einsatzmöglichkeiten. So kommen zunehmend funktionelle Schutzlacke zum Einsatz, die nicht nur isolieren und schützen, sondern auch weitere Eigenschaften erfüllen – etwa Antistatik, Feuchtigkeitsregulierung, UV-Stabilität oder sogar thermische oder elektromagnetische Abschirmung. Die Herausforderung besteht darin, diese Speziallacke gleichmäßig und ohne Fehlstellen aufzutragen – eine Aufgabe, die moderne automatische Anlagen durch hochpräzise Applikationstechnik zuverlässig erfüllen.
Zudem steigt die Bedeutung miniaturisierter und hochintegrierter Baugruppen. Bei diesen Anwendungen sind die Abstände zwischen Leiterbahnen und Bauteilen extrem gering, was höchste Anforderungen an die Steuerung der Lackverteilung stellt. Die Applikation darf keine Brücken bilden, keine Kontaktflächen überdecken und dennoch lückenlosen Schutz bieten. Hier kommen mikrodosierende Systeme, rotierende Düsentechniken oder Lasermaskierung zum Einsatz – unterstützt durch 3D-Kameraerkennung und hochgenaue Positionierungssysteme, die auch bei feinsten Strukturen millimetergenau arbeiten.
Die wirtschaftliche Bedeutung dieser Technologien ist immens. Unternehmen, die in fortschrittliche Lackieranlagen investieren, sichern sich nicht nur eine höhere Produktqualität, sondern auch geringere Fertigungskosten pro Einheit, schnellere Durchlaufzeiten und die Fähigkeit, selbst komplexe Kundenanforderungen flexibel umzusetzen. In einem Markt, der von kurzen Innovationszyklen und wachsendem Qualitätsdruck geprägt ist, ist das automatische Lackieren von Platinen längst nicht mehr nur eine Option – es ist ein strategischer Wettbewerbsvorteil.
Lackieranlage für Elektronik-Kleinteile
Eine Lackieranlage für Elektronik-Kleinteile ist speziell darauf ausgelegt, sehr kleine, empfindliche und oft komplex geformte elektronische Komponenten effizient, präzise und materialschonend zu beschichten. Ziel ist es, die Funktionalität der Bauteile dauerhaft zu sichern, indem sie vor Feuchtigkeit, Staub, Chemikalien, mechanischen Einflüssen oder elektrischen Störungen geschützt werden. Diese Anlagen spielen eine zentrale Rolle in Branchen wie Unterhaltungselektronik, Automotive, Medizintechnik oder Sensorik, in denen hohe Miniaturisierung mit maximaler Zuverlässigkeit gefordert wird.
Die Anlage beginnt typischerweise mit einer automatisierten Zuführeinheit, die die Kleinteile exakt positioniert, vereinzelt und transportiert. Das kann über Vibrationstechnik, Förderbänder, Palettierung oder Roboterhandling erfolgen – je nach Form, Größe und Empfindlichkeit der Bauteile. Dabei ist es entscheidend, dass die Handhabung besonders schonend erfolgt, da kleine elektronische Teile sehr stoß- und druckempfindlich sind.
Für die Lackierung kommen präzise Applikationsverfahren zum Einsatz, wie Mikro-Sprühsysteme, selektive Beschichtung mit XYZ-Achsensteuerung, Jet-Dispensing oder elektrostatische Applikation. Besonders bei Bauteilen mit empfindlichen Kontakten oder Anschlüssen ist selektives Lackieren unerlässlich. Dabei wird der Lack nur auf exakt definierte Bereiche aufgetragen, während Funktionsflächen ausgespart bleiben – unterstützt durch CAD-gesteuerte Pfadführung und optische Kamerasysteme zur Positionserkennung.
Die verwendeten Schutzlacke sind speziell auf die Anforderungen von Elektronik-Kleinteilen abgestimmt – häufig handelt es sich um UV-härtende oder thermisch aushärtende Materialien mit hoher Isolationswirkung, Kriechstromfestigkeit und Haftkraft. Die Schichtdicken sind meist extrem dünn, müssen aber vollständig geschlossen und blasenfrei aufgetragen werden, um den gewünschten Schutz zu gewährleisten. Moderne Systeme kontrollieren in Echtzeit die Schichtdicke und Lackverteilung über Sensorik und visuelle Inline-Kontrolle.
Nach der Lackierung erfolgt die Aushärtung, oft durch UV-Strahlung, Infrarotstrahler oder Konvektionstrockner. Die Herausforderung besteht darin, die empfindlichen Elektronik-Kleinteile nicht zu überhitzen oder thermisch zu belasten. Aushärtezeiten und Temperaturprofile sind daher exakt auf die Materialeigenschaften der Bauteile und des Lacks abgestimmt. Die schnelle Trocknung reduziert nicht nur den Platzbedarf, sondern erhöht auch den Durchsatz der Anlage erheblich.
Für die Umweltsicherheit und Sauberkeit sind moderne Lackieranlagen für Elektronik-Kleinteile mit geschlossenen Kabinen, Absauganlagen und mehrstufigen Filtersystemen ausgestattet, die sowohl Partikel als auch Lösemitteldämpfe effektiv abführen. Viele Anlagen sind für den Einsatz wasserbasierter oder VOC-reduzierter Lacksysteme vorbereitet und erfüllen strenge Umweltvorgaben.
Durch die Kombination aus Automatisierung, Miniaturisierung und intelligenter Prozesskontrolle bieten Lackieranlagen für Elektronik-Kleinteile eine leistungsstarke Lösung, die den Schutz sensibler Elektronik bei gleichzeitig hoher Fertigungseffizienz ermöglicht. Sie sind flexibel für unterschiedlichste Produktformen einsetzbar, leicht in bestehende Produktionslinien integrierbar und liefern reproduzierbare Qualität auch bei großen Stückzahlen.
Moderne Lackieranlagen für Elektronik-Kleinteile zeichnen sich durch ihre hohe Flexibilität und Anpassungsfähigkeit aus. Sie ermöglichen die Verarbeitung unterschiedlichster Bauteilgrößen und -formen innerhalb einer einzigen Anlage, was besonders in Branchen mit vielfältigen Produktportfolios von großem Vorteil ist. Die modulare Bauweise erlaubt es, einzelne Prozessschritte wie Zuführung, Lackierung, Trocknung oder Qualitätskontrolle je nach Bedarf zu erweitern oder umzurüsten, ohne den gesamten Produktionsfluss zu unterbrechen.
Die Steuerung der Anlagen erfolgt über fortschrittliche Softwarelösungen, die eine präzise Programmierung der Lackierparameter und Abläufe ermöglichen. Automatische Erkennungssysteme lesen Produktdaten ein und wählen selbstständig die optimalen Lackierprogramme aus. So lassen sich Produktwechsel schnell und effizient realisieren, was die Produktionszeiten verkürzt und Stillstände minimiert. Zudem unterstützen viele Systeme die Einbindung in digitale Fabriknetzwerke, was eine zentrale Überwachung und Steuerung ermöglicht.
Die Applikationstechnik ist speziell auf die Anforderungen kleiner Elektronikbauteile abgestimmt. Mikrodosierverfahren und selektive Sprühtechniken erlauben eine punktgenaue Beschichtung selbst komplexer Geometrien, während elektrostatische Verfahren die Haftung verbessern und den Materialverbrauch reduzieren. Überschüssiger Lack wird oft recycelt, was die Ressourceneffizienz erhöht.
Zur Qualitätssicherung sind hochwertige Inline-Inspektionssysteme integriert, die mit Kameras und Sensoren die Beschichtung in Echtzeit prüfen. Defekte oder unzureichend beschichtete Teile werden automatisch erkannt und aussortiert, wodurch die Ausbeute steigt und Nacharbeiten entfallen. Die gesammelten Qualitätsdaten unterstützen zudem die lückenlose Dokumentation und Rückverfolgbarkeit im Sinne von Industrie-4.0-Anforderungen.
Schließlich spielt der Umweltschutz eine zentrale Rolle. Die Anlagen sind mit effizienten Absaugsystemen ausgestattet, die Lacknebel und Lösungsmittel zuverlässig filtern. Die Verwendung von umweltfreundlichen, lösemittelfreien oder wasserbasierten Lacken trägt zur Reduzierung von Emissionen bei. Darüber hinaus achten Hersteller zunehmend auf energieeffiziente Komponenten und die Optimierung von Trocknungsprozessen, um den Energieverbrauch insgesamt zu senken.
Insgesamt bieten Lackieranlagen für Elektronik-Kleinteile eine hochpräzise, flexible und nachhaltige Lösung für die Herausforderungen der modernen Elektronikfertigung. Sie sichern die Qualität und Funktionalität empfindlicher Bauteile, steigern die Produktivität und schonen gleichzeitig Umwelt und Ressourcen – wichtige Voraussetzungen für den Erfolg in einem wettbewerbsintensiven Markt.
Darüber hinaus gewinnen intelligente Assistenzsysteme und automatisierte Wartungskonzepte zunehmend an Bedeutung in Lackieranlagen für Elektronik-Kleinteile. Durch den Einsatz von Sensorik und maschinellem Lernen können mögliche Störungen frühzeitig erkannt und Wartungsmaßnahmen vorausschauend geplant werden. Dies minimiert ungeplante Stillstände, verlängert die Lebensdauer der Anlagenkomponenten und erhöht die Gesamtanlageneffektivität.
Auch die Ergonomie und Bedienfreundlichkeit der Anlagen werden kontinuierlich verbessert. Moderne Mensch-Maschine-Schnittstellen sind intuitiv gestaltet, ermöglichen eine einfache Navigation durch komplexe Einstellungen und reduzieren Bedienfehler. Automatisierte Reinigungszyklen sowie leicht zugängliche Wartungsbereiche tragen dazu bei, den Aufwand für Instandhaltung und Anlagenpflege zu reduzieren.
Im Zuge der Miniaturisierung und steigenden Komplexität elektronischer Baugruppen werden Lackieranlagen immer feiner und präziser in der Applikation. Die Kombination aus hochauflösenden Kamerasystemen, adaptiven Steuerungsalgorithmen und feinjustierbaren Applikationsköpfen sorgt dafür, dass auch filigranste Strukturen zuverlässig und fehlerfrei beschichtet werden. So wird eine dauerhafte Schutzwirkung gewährleistet, ohne die Funktionalität der Bauteile zu beeinträchtigen.
Zudem entwickeln sich die verwendeten Beschichtungsmaterialien stetig weiter. Neben klassischen Schutzlacken kommen zunehmend multifunktionale Lacke zum Einsatz, die beispielsweise antistatische Eigenschaften besitzen, elektromagnetische Störungen abschirmen oder thermische Ableitung verbessern. Die Lackieranlagen müssen daher flexibel sein, um unterschiedliche Materialien optimal verarbeiten zu können und so auf individuelle Kundenanforderungen einzugehen.
Nicht zuletzt trägt die fortschreitende Digitalisierung dazu bei, dass Lackieranlagen immer stärker in vernetzte Produktionsumgebungen eingebunden werden. Dies ermöglicht eine ganzheitliche Steuerung, bei der Daten aus verschiedenen Prozessschritten miteinander verknüpft und analysiert werden. Die daraus gewonnenen Erkenntnisse fließen direkt in die Prozessoptimierung ein, was die Qualität weiter steigert und gleichzeitig Kosten senkt.
In Summe sind moderne Lackieranlagen für Elektronik-Kleinteile hochkomplexe, adaptive Systeme, die Präzision, Effizienz und Nachhaltigkeit vereinen. Sie sind unverzichtbarer Bestandteil einer zukunftsfähigen Elektronikfertigung, die den steigenden Anforderungen an Qualität, Vielfalt und Umweltverträglichkeit gerecht wird und Herstellern entscheidende Wettbewerbsvorteile sichert.
Lackieranlagen für sehr kleine Teile
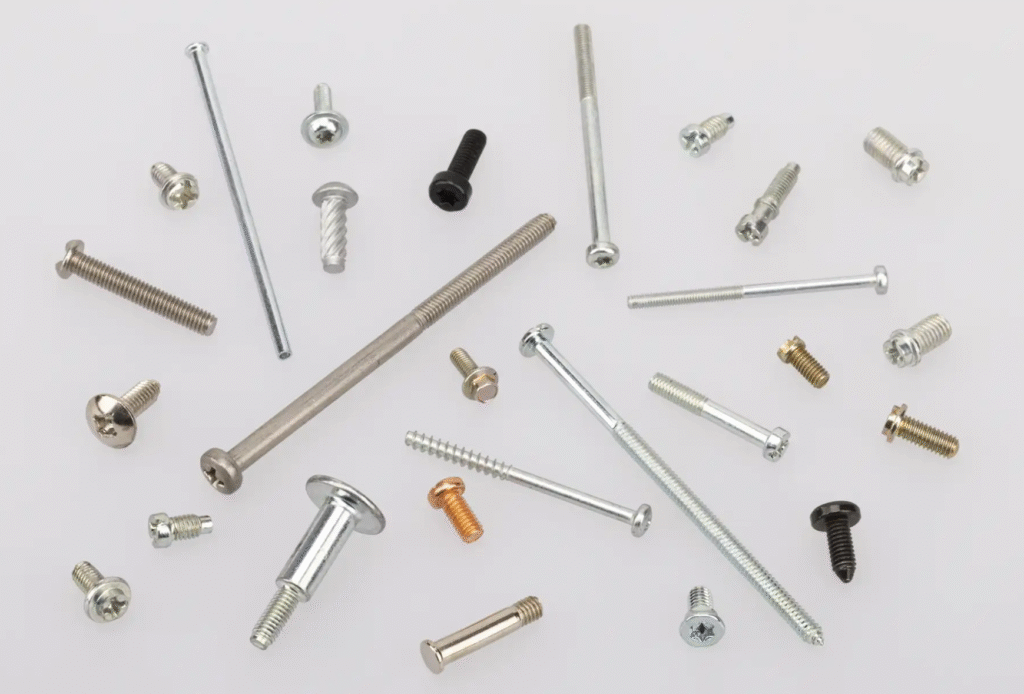
Lackieranlagen für sehr kleine Teile sind speziell entwickelt, um winzige, oft filigrane Bauteile mit höchster Präzision und Effizienz zu beschichten. Diese Anlagen kommen in Branchen zum Einsatz, in denen Miniaturisierung und höchste Qualitätsanforderungen Hand in Hand gehen, beispielsweise in der Mikroelektronik, Medizintechnik, Feinmechanik oder Uhrenindustrie. Die Herausforderung liegt darin, trotz der geringen Abmessungen eine gleichmäßige, lückenlose Schutzschicht aufzutragen, ohne empfindliche Bereiche wie Kontaktstellen, bewegliche Teile oder optische Flächen zu beeinträchtigen.
Der Kern moderner Anlagen für sehr kleine Teile ist eine hochpräzise Zuführ- und Positionierungstechnik. Bauteile werden meist einzeln und schonend über Vakuumgreifer, Mikrospannsysteme oder elektrostatische Haltevorrichtungen aufgenommen und exakt unter die Applikationsdüse geführt. Diese präzise Handhabung minimiert Beschädigungen und gewährleistet eine optimale Ausrichtung für die Lackierung.
Für die Applikation kommen oftmals Mikrozerstäubungssysteme, Jet-Dispensing oder selektive Beschichtungsverfahren zum Einsatz. Diese Methoden ermöglichen eine punktgenaue Dosierung extrem kleiner Lackmengen, die kontrolliert und gleichmäßig aufgetragen werden. Dabei wird die Lackschicht oft nur wenige Mikrometer dick, um Gewicht, Größe und Funktionalität des Teils nicht zu beeinträchtigen, aber dennoch wirksamen Schutz zu bieten.
Ein weiteres charakteristisches Merkmal dieser Anlagen ist die Integration von hochauflösenden Kamerasystemen und Sensoren, die den Beschichtungsprozess in Echtzeit überwachen. Fehler wie Blasenbildung, unzureichende Deckung oder Verunreinigungen werden frühzeitig erkannt und ermöglichen eine sofortige Korrektur oder Aussortierung. Die gewonnenen Qualitätsdaten fließen in automatische Regelkreise ein, die Applikationsparameter dynamisch anpassen und so die Prozesssicherheit erhöhen.
Die Aushärtung der Lackschicht erfolgt meist mittels UV-Licht oder schonender Infrarotstrahlung, um thermische Belastungen auf die kleinen und oft temperaturempfindlichen Bauteile zu vermeiden. Die Trocknungszeiten sind kurz, was die Durchlaufgeschwindigkeit steigert und die Anlagenkapazität erhöht.
Um Umwelt- und Arbeitsschutzstandards einzuhalten, sind die Anlagen mit geschlossenen Lackierkabinen, effizienten Absaug- und Filtersystemen ausgestattet, die Lacknebel und Lösemitteldämpfe sicher abscheiden. Zudem wird häufig auf lösemittelfreie oder wasserbasierte Lacke gesetzt, um Emissionen zu minimieren und eine nachhaltige Produktion zu gewährleisten.
Insgesamt bieten Lackieranlagen für sehr kleine Teile eine hochentwickelte, flexible und präzise Lösung, die den Schutz empfindlicher Miniaturbauteile sicherstellt, Produktionsprozesse optimiert und gleichzeitig Umweltaspekte berücksichtigt. Sie sind ein unverzichtbarer Bestandteil moderner Fertigungsprozesse, die höchste Qualitätsstandards bei minimalem Material- und Energieeinsatz erfordern.
Die zunehmende Miniaturisierung in vielen Industriezweigen führt dazu, dass Lackieranlagen für sehr kleine Teile immer anspruchsvollere Aufgaben übernehmen müssen. Dabei spielt nicht nur die präzise Applikation des Schutzlacks eine zentrale Rolle, sondern auch die Flexibilität der Anlagen, um verschiedenste Bauteilformen und -größen verarbeiten zu können. Modulare Systeme erlauben es, unterschiedliche Applikationstechniken wie Sprühen, Dosieren oder Tauchen innerhalb einer einzigen Anlage zu kombinieren und je nach Produktanforderung schnell umzuschalten.
Automatisierte Handhabungssysteme sind dabei so ausgelegt, dass sie auch äußerst fragile Bauteile mit minimalem Kraftaufwand transportieren und positionieren können. Vakuumgreifer mit fein regulierbarem Unterdruck, weiche Greifarme aus elastischen Materialien oder kontaktlose Verfahren wie Luftkissenförderer reduzieren mechanische Belastungen und minimieren Ausschuss. Darüber hinaus gewährleisten hochpräzise Linearmotoren und Servoantriebe eine exakte Bewegungssteuerung der Applikationsköpfe, was für gleichbleibende Schichtdicken und -qualität unerlässlich ist.
Die Beschichtung erfolgt häufig in Reinraumumgebungen, um Kontaminationen zu vermeiden, die gerade bei winzigen Bauteilen gravierende Auswirkungen auf die Funktion haben können. Die Anlagen sind deshalb so konstruiert, dass sie leicht zu reinigen sind und die Partikelbelastung durch optimierte Luftführung und Filtration auf ein Minimum reduzieren. Gleichzeitig sorgen Temperier- und Feuchteregelsysteme für stabile Prozessbedingungen, was sich positiv auf die Lackqualität auswirkt.
Innovative Prozessüberwachungssysteme setzen zunehmend auf Künstliche Intelligenz und Machine Learning, um aus den erfassten Prozessdaten Muster zu erkennen und Qualitätsabweichungen frühzeitig zu prognostizieren. Diese intelligente Steuerung ermöglicht eine dynamische Anpassung der Prozessparameter und sorgt so für eine noch höhere Prozesssicherheit und Effizienz. Gleichzeitig bieten umfassende Datenerfassung und Analyse die Grundlage für eine vollständige Rückverfolgbarkeit und die Einhaltung strenger Qualitätsstandards.
Die eingesetzten Lacke werden kontinuierlich weiterentwickelt und sind heute oft multifunktional ausgelegt. Neben dem Schutz vor Umwelteinflüssen bieten sie beispielsweise elektrische Isolation, chemische Resistenz oder thermische Stabilität. Die Anlagen müssen daher in der Lage sein, verschiedene Lacktypen flexibel zu verarbeiten und bei Bedarf in schneller Folge zu wechseln, ohne dass es zu Kontaminationen oder langen Stillstandzeiten kommt.
Nicht zuletzt gewinnt auch die Energieeffizienz der Anlagen immer mehr an Bedeutung. Durch den Einsatz moderner Antriebstechnik, optimierter Trocknungssysteme und intelligenter Steuerung lassen sich Energieverbrauch und Betriebskosten signifikant reduzieren. Umweltfreundliche Lacke und geschlossene Recyclingkreisläufe minimieren zudem den ökologischen Fußabdruck der Produktion.
Zusammengefasst ermöglichen Lackieranlagen für sehr kleine Teile eine hochpräzise, flexible und nachhaltige Fertigungslösung, die den steigenden Anforderungen der modernen Industrie gerecht wird. Sie sichern die Qualität und Funktionalität empfindlicher Bauteile, steigern die Produktionsleistung und tragen aktiv zu einer ressourcenschonenden und umweltbewussten Herstellung bei – wesentliche Faktoren für den langfristigen Erfolg in wettbewerbsintensiven Märkten.
Neben der technischen Ausstattung spielen bei Lackieranlagen für sehr kleine Teile auch Aspekte der Prozessintegration und Automatisierung eine zentrale Rolle. Die Anlagen sind häufig Teil umfassender Fertigungslinien, in denen unterschiedliche Produktionsschritte nahtlos aufeinander abgestimmt sind. So werden die kleinen Bauteile etwa nach der Bestückung und Lötung direkt in die Lackieranlage überführt, ohne dass ein manueller Eingriff notwendig ist. Dies reduziert nicht nur den Handlingaufwand, sondern minimiert auch das Risiko von Beschädigungen und Verunreinigungen.
Die Kommunikation zwischen den verschiedenen Anlagen erfolgt über standardisierte Schnittstellen und Protokolle, was eine durchgängige Steuerung und Überwachung ermöglicht. Produktionsdaten können zentral erfasst und analysiert werden, wodurch sich Schwachstellen im Prozess schnell identifizieren und beheben lassen. Dies fördert eine kontinuierliche Verbesserung und erhöht die Gesamtanlageneffektivität.
Auch die Wartung und Instandhaltung sind durch moderne Diagnosesysteme deutlich effizienter geworden. Die Anlagen melden automatisch bevorstehende Wartungsintervalle oder potenzielle Störungen, sodass gezielte Maßnahmen geplant und ungeplante Stillstände vermieden werden können. Oft sind Wartungsarbeiten so ausgelegt, dass sie während kurzer Produktionspausen durchgeführt werden können, was die Verfügbarkeit weiter verbessert.
Ein weiterer Trend ist die zunehmende Individualisierung und Kleinserienfertigung. Lackieranlagen für sehr kleine Teile sind daher darauf ausgelegt, schnell und flexibel auf unterschiedliche Produkte und Kundenanforderungen zu reagieren. Automatische Programmwechsel, einfache Bedienkonzepte und modulare Anlagendesigns erlauben es, unterschiedliche Lackierprozesse ohne lange Rüstzeiten umzusetzen. Dies ist besonders wichtig, um wettbewerbsfähig zu bleiben und auf dynamische Marktanforderungen reagieren zu können.
Im Bereich der Sicherheit erfüllen moderne Anlagen hohe Standards, um sowohl den Arbeitsschutz als auch den Umweltschutz zu gewährleisten. Geschlossene Systeme verhindern den Austritt von Lackpartikeln und Lösemitteln, effiziente Absauganlagen sorgen für saubere Luft, und Schutzvorrichtungen minimieren das Risiko für Bedienpersonal. Die Einhaltung gesetzlicher Vorschriften wird durch umfangreiche Dokumentations- und Kontrollfunktionen unterstützt.
Zusammengefasst sind Lackieranlagen für sehr kleine Teile hochkomplexe, automatisierte Systeme, die durch Präzision, Flexibilität und Effizienz überzeugen. Sie integrieren modernste Technologien zur Prozesssteuerung, Qualitätssicherung und Umweltfreundlichkeit und sind damit wesentliche Bausteine für eine zukunftsfähige Produktion in Branchen mit höchsten Anforderungen an Miniaturisierung und Produktqualität.
Kompakte Lackiertechnik für Kleinteile
Kompakte Lackiertechnik für Kleinteile ist darauf ausgelegt, in begrenzten Raumverhältnissen präzise, effiziente und hochwertige Beschichtungen durchzuführen. Besonders in Produktionsumgebungen, in denen Platz knapp ist oder mehrere Fertigungsschritte in räumlich begrenzten Bereichen stattfinden, bieten kompakte Systeme die Möglichkeit, Kleinteile zuverlässig zu lackieren, ohne große Installationsflächen zu benötigen. Diese Technik findet Anwendung in Bereichen wie Elektronik, Medizintechnik, Schmuckherstellung oder Feinmechanik, wo kleine Bauteile mit hoher Genauigkeit und Schutzbeschichtungen versehen werden müssen.
Die kompakten Lackiersysteme sind häufig modular aufgebaut und integrieren mehrere Prozessschritte wie Zuführung, Lackapplikation, Trocknung und Qualitätskontrolle auf engem Raum. Dabei ermöglichen sie durch intelligente Anordnung der Komponenten kurze Förderwege und eine hohe Prozessgeschwindigkeit. Die Anlagen sind oft so konstruiert, dass sie leicht in bestehende Produktionslinien eingebunden oder als eigenständige Stationen genutzt werden können.
Zur Applikation kommen präzise Sprühtechniken, mikrofeine Dosiersysteme oder elektrostatische Lackierverfahren zum Einsatz, die selbst kleinste Kleinteile mit exakter Schichtdicke und gleichmäßiger Verteilung beschichten. Die Steuerung erfolgt über hochentwickelte Software, die flexible Programmierungen erlaubt und schnelle Produktwechsel unterstützt. So lassen sich unterschiedliche Teileformen und Lacktypen effizient verarbeiten, ohne aufwändige Umrüstungen.
Trocknungs- oder Aushärtesysteme, wie UV- oder IR-Strahler, sind kompakt integriert und gewährleisten kurze Durchlaufzeiten, ohne die Bauteile thermisch zu belasten. Durch die Kombination aus automatisierter Prozesssteuerung und platzsparendem Design werden hohe Qualität, Produktivität und Wirtschaftlichkeit erreicht.
Kompakte Lackiertechnik für Kleinteile ist zudem oft mit modernen Sensor- und Inspektionssystemen ausgestattet, die eine Inline-Qualitätskontrolle ermöglichen. Fehlerhafte Beschichtungen werden sofort erkannt und können automatisch aussortiert oder nachbearbeitet werden. Dies sichert eine konstant hohe Produktqualität und minimiert Ausschuss.
Umwelt- und Arbeitsschutzaspekte werden ebenfalls berücksichtigt: Geschlossene Kabinen, effiziente Absaugsysteme und der Einsatz von umweltfreundlichen Lacken sorgen für sichere Arbeitsbedingungen und nachhaltige Produktionsprozesse auch in beengten Räumen.
Insgesamt bieten kompakte Lackiersysteme für Kleinteile eine flexible, effiziente und umweltgerechte Lösung, die speziell für Produktionsbereiche mit begrenztem Platzbedarf entwickelt wurde. Sie ermöglichen eine präzise Beschichtung empfindlicher Bauteile, steigern die Fertigungseffizienz und sind leicht in unterschiedlichste Produktionsumgebungen integrierbar.
Die kompakten Lackiersysteme zeichnen sich durch ihre hohe Automatisierungsfähigkeit aus, die eine gleichbleibende Beschichtungsqualität auch bei großen Stückzahlen sicherstellt. Durch den Einsatz von intelligenten Steuerungen und programmierbaren Applikationsmodulen können verschiedenste Kleinteile schnell und präzise lackiert werden, was besonders bei wechselnden Produktionsserien von großem Vorteil ist. Die Möglichkeit, Lackierprogramme digital abzulegen und bei Bedarf abzurufen, reduziert Rüstzeiten erheblich und ermöglicht eine flexible Fertigung.
Ein weiterer Vorteil kompakter Lackiertechnik ist die einfache Integration in bestehende Produktionslinien. Die Anlagen können sowohl als eigenständige Module als auch als Teil von automatisierten Fertigungsketten betrieben werden. Dadurch lassen sie sich optimal an die spezifischen Anforderungen und Platzverhältnisse im Produktionsumfeld anpassen. Besonders in hochautomatisierten Umgebungen profitieren Hersteller von der hohen Prozessstabilität und der nahtlosen Kommunikation mit vorgelagerten und nachgelagerten Systemen.
Die Applikationstechniken sind speziell auf die Herausforderungen bei Kleinteilen abgestimmt. Mikrofeine Sprühköpfe oder dosierende Applikatoren ermöglichen eine kontrollierte und sparsame Lackverteilung, wodurch Materialeinsatz und Overspray minimiert werden. Elektrostatische Verfahren verbessern zudem die Haftung des Lacks auf komplexen Oberflächen und reduzieren Lackverluste weiter. Diese Technologien tragen dazu bei, die Produktionskosten zu senken und gleichzeitig die Umweltbelastung zu verringern.
Zur Aushärtung sind kompakte UV- oder IR-Trockner integriert, die eine schnelle und schonende Härtung gewährleisten. Dabei wird besonders auf die thermische Empfindlichkeit der Kleinteile Rücksicht genommen, um Beschädigungen zu vermeiden. Die kompakten Trocknungseinheiten sind energieeffizient ausgelegt und unterstützen somit eine nachhaltige Produktion.
Qualitätssicherung wird durch integrierte Inline-Kamerasysteme und Sensorik realisiert, die während des Lackierprozesses und unmittelbar danach eine lückenlose Überwachung ermöglichen. Defekte oder unzureichend beschichtete Teile werden automatisch erkannt und aus dem Produktionsfluss entfernt. Dies erhöht die Ausschusskontrolle und sichert eine gleichbleibend hohe Produktqualität.
Nicht zuletzt überzeugen kompakte Lackieranlagen durch ihre ergonomische Bauweise und einfache Wartung. Durch gut zugängliche Wartungsbereiche und automatisierte Reinigungszyklen wird der Bedienaufwand reduziert und Ausfallzeiten minimiert. Die Anlagen sind auf eine lange Lebensdauer ausgelegt und gewährleisten so eine nachhaltige Investition.
Zusammengefasst bieten kompakte Lackiertechniken für Kleinteile eine leistungsfähige, flexible und ressourcenschonende Lösung, die den Anforderungen moderner Fertigungsprozesse gerecht wird. Sie kombinieren Präzision, Effizienz und Umweltbewusstsein auf engem Raum und ermöglichen so eine hochwertige Beschichtung empfindlicher Bauteile bei gleichzeitig hoher Wirtschaftlichkeit.
Darüber hinaus werden kompakte Lackieranlagen für Kleinteile zunehmend mit smarten Features ausgestattet, die den Bedienkomfort und die Prozesssicherheit weiter erhöhen. Beispielsweise erlauben Touchscreen-Bedienfelder eine intuitive Steuerung der Anlage, während integrierte Diagnosefunktionen frühzeitig auf Wartungsbedarf oder Störungen hinweisen. So können Ausfallzeiten reduziert und die Anlagenverfügbarkeit erhöht werden. Manche Systeme bieten auch Fernwartungsoptionen, die es ermöglichen, Support und Fehlerbehebung ortsunabhängig durchzuführen, was besonders in global verteilten Produktionsnetzwerken von Vorteil ist.
Die Flexibilität der kompakten Anlagen erstreckt sich auch auf die Verarbeitbarkeit unterschiedlicher Lacktypen und Oberflächenmaterialien. Sie sind ausgelegt, um sowohl lösemittelbasierte als auch wasserbasierte Lacke sowie spezielle Funktionsbeschichtungen wie Schutzlacke, Isolationslacke oder antibakterielle Beschichtungen effizient aufzutragen. Dadurch können Hersteller vielfältige Kundenanforderungen bedienen und schnell auf Marktveränderungen reagieren.
Ein weiterer Aspekt ist die zunehmende Miniaturisierung der Kleinteile selbst, die neue Herausforderungen an die Lackiertechnik stellt. Kompakte Anlagen verfügen deshalb über hochpräzise Positioniersysteme, oftmals mit mehreren Freiheitsgraden, die auch komplexe Geometrien millimetergenau bearbeiten können. In Verbindung mit adaptiven Applikationsköpfen ermöglichen sie eine Beschichtung auch an schwer zugänglichen Stellen und gewährleisten eine vollständige und gleichmäßige Lackierung.
Auch die Nachhaltigkeit spielt bei der Entwicklung kompakter Lackiersysteme eine immer größere Rolle. Durch die Optimierung der Lackierprozesse, wie etwa durch reduzierte Overspray-Mengen oder die Rückgewinnung von überschüssigem Lack, werden Materialverbrauch und Abfall minimiert. Energiesparende Komponenten und kurze Trocknungszeiten tragen zusätzlich dazu bei, den ökologischen Fußabdruck der Lackieranlagen zu verringern.
Die kompakte Bauweise erleichtert zudem die Aufstellung in Reinräumen oder kontrollierten Umgebungen, in denen höchste Sauberkeitsstandards gelten. Die Anlagen sind so konstruiert, dass sie einfach zu reinigen sind und den Anforderungen an Partikelfreiheit gerecht werden, was insbesondere in der Medizintechnik oder der Halbleiterfertigung unerlässlich ist.
Abschließend lässt sich sagen, dass kompakte Lackiertechnik für Kleinteile eine innovative und zukunftsfähige Lösung bietet, die Präzision, Effizienz, Flexibilität und Nachhaltigkeit vereint. Sie ermöglicht es Herstellern, auch unter räumlichen und produktionstechnischen Einschränkungen hochwertige Beschichtungen zu realisieren und so die Qualität und Langlebigkeit ihrer Produkte sicherzustellen.
Automatische Lackierunganlage feiner Teile
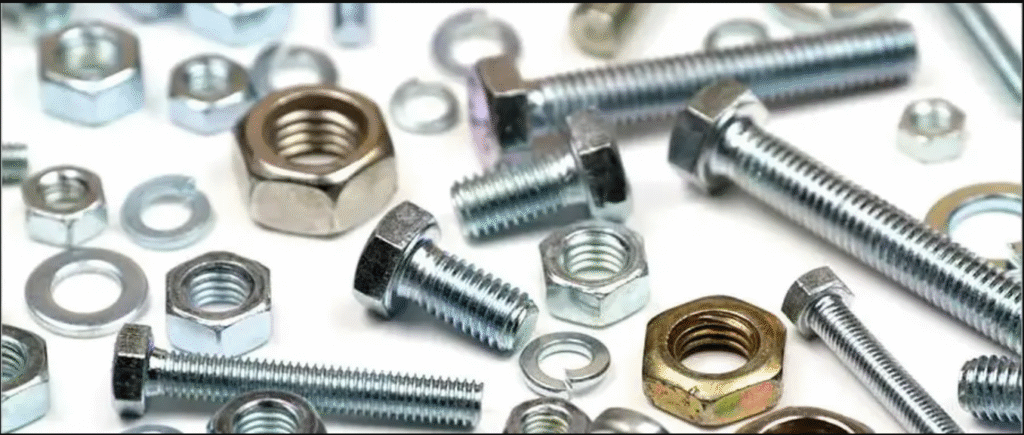
Eine automatische Lackieranlage für feine Teile ist speziell darauf ausgelegt, kleinste und empfindlichste Bauteile mit höchster Präzision und Reproduzierbarkeit zu beschichten. Solche Anlagen finden breite Anwendung in Branchen wie der Mikroelektronik, Medizintechnik, Feinmechanik oder optischen Gerätefertigung, wo selbst kleinste Unregelmäßigkeiten in der Beschichtung die Funktionalität und Zuverlässigkeit der Produkte beeinträchtigen können.
Das Herzstück dieser Anlagen ist eine hochpräzise Zuführ- und Positionierungseinheit, die die feinen Teile sicher und schonend vereinzelt und millimetergenau unter die Applikationsköpfe führt. Je nach Bauteilart kommen Vakuumgreifer, Mikrospannvorrichtungen oder kontaktlose Handhabungsmethoden zum Einsatz, um Beschädigungen oder Verformungen auszuschließen.
Zur Lackapplikation werden fortschrittliche Verfahren verwendet, darunter mikrofeines Sprühen, selektives Dosieren, Jet-Dispensing oder elektrostatische Lackierung. Diese Methoden ermöglichen eine punktgenaue, gleichmäßige und dünnschichtige Beschichtung, die exakt auf die spezifischen Anforderungen des Bauteils abgestimmt ist. Die Applikationsparameter wie Düsenabstand, Sprühwinkel, Lackfluss und Bewegungsgeschwindigkeit werden elektronisch gesteuert und können dynamisch an Prozessbedingungen angepasst werden.
Zur Sicherstellung der Beschichtungsqualität sind moderne automatische Lackieranlagen mit hochauflösenden Kameras und Sensoren ausgestattet, die den Applikationsprozess in Echtzeit überwachen. Fehler wie Blasenbildung, unzureichende Deckung oder Kontaminanten werden sofort erkannt und führen zu automatischen Korrekturmaßnahmen oder Ausscheidung der fehlerhaften Teile. Die gesammelten Qualitätsdaten ermöglichen eine umfassende Dokumentation und Rückverfolgbarkeit.
Die Trocknung oder Aushärtung des aufgetragenen Lacks erfolgt oft über integrierte UV- oder IR-Systeme, die speziell für empfindliche feine Teile ausgelegt sind. Diese Trocknungsverfahren sind schnell, schonend und gewährleisten eine optimale Verfestigung des Lacks, ohne die Bauteile thermisch zu belasten oder deren Funktion zu beeinträchtigen.
Umwelt- und Arbeitsschutzaspekte werden ebenfalls berücksichtigt: Die Anlagen sind mit geschlossenen Lackierkammern, effizienten Absaug- und Filtersystemen ausgestattet, die die Emission von Lacknebeln und Lösemitteldämpfen minimieren. Zudem ermöglichen viele Systeme den Einsatz von umweltfreundlichen, lösemittelfreien oder wasserbasierten Lacken.
Insgesamt bieten automatische Lackieranlagen für feine Teile eine hochentwickelte, flexible und nachhaltige Lösung, die den hohen Anforderungen moderner Fertigungsprozesse gerecht wird. Sie sichern eine präzise Beschichtung selbst kleinster Bauteile, steigern die Produktivität und gewährleisten eine konstant hohe Qualität bei gleichzeitig minimalem Materialverbrauch und Umwelteinfluss.
Automatische Lackieranlagen für feine Teile zeichnen sich durch ihre Fähigkeit aus, auch komplexe und filigrane Geometrien präzise zu beschichten, ohne empfindliche Bereiche wie Kontaktflächen, bewegliche Mechanismen oder optische Elemente zu beeinträchtigen. Dies wird durch die Kombination aus hochpräziser Mechanik, intelligenten Steuerungssystemen und adaptiven Applikationstechnologien ermöglicht, die flexibel auf unterschiedliche Bauteilformen und Oberflächen reagieren können. Die Anlagen können schnell auf verschiedene Produkttypen umgestellt werden, wodurch sie sich ideal für Klein- und Mittelserien sowie wechselnde Produktionsanforderungen eignen.
Die Prozesskontrolle ist bei automatischen Lackieranlagen für feine Teile von zentraler Bedeutung. Sensorik und Bildverarbeitungssysteme überwachen kontinuierlich die Lackschichtdicke, die Verteilung und mögliche Defekte. Diese Daten werden in Echtzeit ausgewertet und fließen in automatisierte Regelkreise ein, die Parameter wie Sprühdruck, Fördergeschwindigkeit oder Applikationswinkel anpassen. Dadurch wird eine gleichbleibend hohe Lackierqualität sichergestellt und Ausschuss minimiert.
Darüber hinaus ermöglichen moderne Anlagen eine umfassende Integration in digitale Fertigungsumgebungen. Über standardisierte Schnittstellen kommunizieren sie mit vorgelagerten Prozessen wie Bestückung oder Reinigung sowie nachgelagerten Qualitätssicherungs- oder Montageeinheiten. Diese Vernetzung unterstützt eine durchgängige Prozessüberwachung, optimiert die Fertigungslinien und trägt zur Umsetzung von Industrie-4.0-Konzepten bei.
Die Wartung und Bedienung der Anlagen sind auf Benutzerfreundlichkeit ausgelegt. Intuitive Bedienoberflächen erleichtern die Programmierung und Überwachung der Lackierprozesse, während vorausschauende Diagnosesysteme frühzeitig auf Wartungsbedarf hinweisen und Ausfallzeiten reduzieren. Automatisierte Reinigungs- und Kalibrierzyklen gewährleisten eine dauerhaft zuverlässige Funktion und gleichbleibende Beschichtungsqualität.
Umweltaspekte spielen eine zunehmend wichtige Rolle: Die Verwendung von umweltfreundlichen Lacken, effiziente Absaugsysteme mit mehrstufiger Filterung sowie die Minimierung von Lackverlusten durch präzise Applikation tragen zu einer nachhaltigen Produktion bei. Energiesparende Trocknungs- und Aushärtemethoden ergänzen dieses Konzept.
Insgesamt sind automatische Lackieranlagen für feine Teile hochentwickelte Systeme, die Präzision, Flexibilität, Prozesssicherheit und Umweltbewusstsein vereinen. Sie ermöglichen Herstellern, anspruchsvolle Produkte mit konstant hoher Qualität zu fertigen und gleichzeitig Produktionskosten und Umwelteinflüsse zu reduzieren – Voraussetzungen für Wettbewerbsfähigkeit und nachhaltigen Erfolg in anspruchsvollen Märkten.
Die stetige Weiterentwicklung automatischer Lackieranlagen für feine Teile trägt dazu bei, dass immer komplexere Bauteile effizient und mit höchster Präzision beschichtet werden können. Durch die Integration von Robotik und feinfühligen Greifsystemen wird die Handhabung empfindlicher Miniaturteile noch sicherer und exakter. Roboterarme mit mehreren Freiheitsgraden ermöglichen zudem die Lackierung aus unterschiedlichsten Winkeln, was insbesondere bei komplexen Geometrien für eine vollständige und gleichmäßige Beschichtung sorgt.
Ein weiteres zukunftsweisendes Merkmal ist die verstärkte Nutzung von Künstlicher Intelligenz (KI) und Machine Learning, um die Prozesse noch smarter zu machen. KI-gestützte Algorithmen analysieren Prozessdaten, erkennen Anomalien frühzeitig und schlagen Optimierungen vor, die manuell nur schwer oder zeitaufwendig umzusetzen wären. Diese intelligente Prozesssteuerung trägt dazu bei, Schwankungen auszugleichen und die Qualität auf einem konstant hohen Niveau zu halten.
Zusätzlich eröffnen neue Beschichtungsmaterialien erweiterte Möglichkeiten. Multifunktionale Lacke, die beispielsweise neben Schutz auch antimikrobielle Eigenschaften, elektromagnetische Abschirmung oder verbesserte Wärmeleitung bieten, werden zunehmend eingesetzt. Automatische Lackieranlagen müssen flexibel genug sein, um diese innovativen Materialien präzise zu verarbeiten und an die spezifischen Anforderungen anzupassen.
Die Skalierbarkeit der Anlagen ermöglicht es Herstellern, von kleinen Serien bis hin zu großen Produktionsmengen mit minimalen Anpassungen zu fertigen. Dabei unterstützen modulare Bauweisen schnelle Umrüstungen und Erweiterungen, was die Investitionskosten senkt und die Wettbewerbsfähigkeit erhöht.
Nicht zuletzt sind Aspekte wie Ergonomie und Arbeitssicherheit bei der Entwicklung automatischer Lackieranlagen für feine Teile zentral. Bedienerfreundliche Schnittstellen, sichere Zugangssysteme und automatische Schutzfunktionen sorgen für einen sicheren und effizienten Betrieb, der auch den Anforderungen moderner Arbeitsschutzrichtlinien entspricht.
In Summe bieten automatische Lackieranlagen für feine Teile eine hochmoderne, adaptive und nachhaltige Technologieplattform, die den Anforderungen der Zukunft gerecht wird. Sie verbinden Präzision, Flexibilität, Prozessintelligenz und Umweltverträglichkeit, um eine qualitativ hochwertige und wirtschaftliche Produktion feinster Bauteile sicherzustellen.
Lackiertechnik für Mini-Komponenten
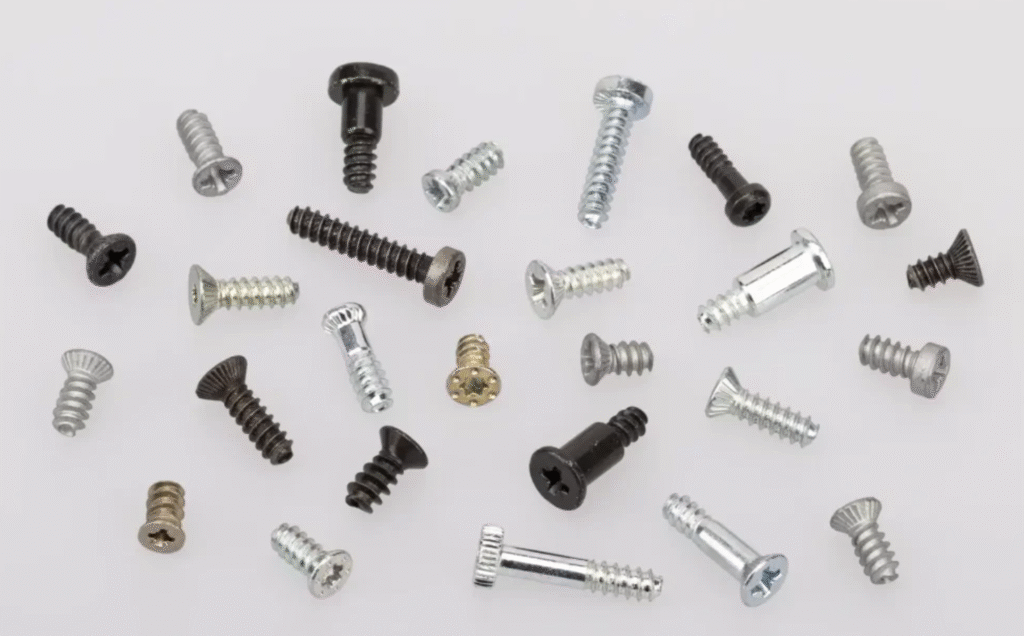
Lackiertechnik für Mini-Komponenten ist ein hochspezialisierter Bereich, der sich mit der präzisen Beschichtung von sehr kleinen und oft komplex geformten Bauteilen beschäftigt. Diese Mini-Komponenten finden sich in zahlreichen Branchen wie der Mikroelektronik, Medizintechnik, Uhrenherstellung oder auch in der Sensorik, wo sie oft kritische Funktionen erfüllen und höchsten Qualitätsanforderungen genügen müssen. Die Lackiertechnik muss dabei nicht nur Schutz vor Umwelteinflüssen wie Feuchtigkeit, Staub oder Chemikalien bieten, sondern auch elektrische Isolation, mechanische Stabilität oder spezielle funktionelle Eigenschaften gewährleisten.
Aufgrund der kleinen Bauteilgröße sind die Anforderungen an die Applikationstechnik besonders hoch. Es kommen oft mikrofeine Sprühdüsen, selektive Dosiersysteme oder Jet-Dispensing-Verfahren zum Einsatz, die eine punktgenaue und kontrollierte Lackierung ermöglichen. Die Lackschichten sind dabei sehr dünn – häufig nur wenige Mikrometer –, müssen aber dennoch lückenlos, blasenfrei und gleichmäßig aufgetragen werden, um die Schutzwirkung zu gewährleisten, ohne die Funktion oder das Gewicht der Komponente zu beeinträchtigen.
Die Handhabung der Mini-Komponenten erfolgt meist vollautomatisiert und mit speziellen Greifsystemen, die eine schonende Vereinzelnung und präzise Positionierung sicherstellen. Häufig kommen Vakuumgreifer oder elektrostatische Haltevorrichtungen zum Einsatz, um mechanische Belastungen zu minimieren. Die Steuerung der Lackierprozesse erfolgt über computergestützte Systeme, die schnelle Produktwechsel und individuelle Programmierungen erlauben.
Um die Qualität der Beschichtung zu sichern, sind in moderne Anlagen integrierte Inline-Inspektionssysteme Standard. Hochauflösende Kameras und Sensoren kontrollieren die Lackschicht auf Vollständigkeit, Schichtdicke und mögliche Fehler wie Blasen oder Verunreinigungen. So können fehlerhafte Teile frühzeitig erkannt und aus dem Produktionsprozess ausgeschleust werden.
Die Aushärtung der Lacke erfolgt je nach Material durch UV-Licht, Wärme oder Kombinationen aus beiden Verfahren. Dabei ist es wichtig, dass die Mini-Komponenten keiner übermäßigen thermischen Belastung ausgesetzt werden, um Verformungen oder Funktionseinbußen zu vermeiden. Moderne Trocknungssysteme sind daher präzise temperiert und oft mit schneller Taktung ausgelegt, um hohe Durchsatzraten zu ermöglichen.
Nicht zuletzt spielt der Umweltschutz eine große Rolle: Die Lackiertechnik für Mini-Komponenten verwendet zunehmend umweltfreundliche, lösemittelfreie oder wasserbasierte Lacke. Effiziente Absaugsysteme und geschlossene Lackierkabinen minimieren Emissionen und schützen die Mitarbeiter.
Insgesamt vereint die Lackiertechnik für Mini-Komponenten Präzision, Flexibilität und Nachhaltigkeit. Sie ermöglicht die zuverlässige Beschichtung selbst kleinster und komplexester Bauteile, steigert die Fertigungsqualität und unterstützt eine effiziente und umweltbewusste Produktion.
Die kontinuierliche Weiterentwicklung der Lackiertechnik für Mini-Komponenten ist eng mit Fortschritten in der Automatisierung und Prozesssteuerung verbunden. Moderne Anlagen sind darauf ausgelegt, eine hohe Variabilität bei minimalen Rüstzeiten zu ermöglichen, was besonders für Produktionen mit wechselnden Kleinserien von Vorteil ist. Durch den Einsatz von programmierbaren Steuerungen und modularen Systemen können unterschiedliche Bauteiltypen schnell angepasst und Lackierparameter präzise eingestellt werden, um optimale Beschichtungsergebnisse zu erzielen.
Ein besonderes Augenmerk liegt auf der Integration von Sensorik und Bildverarbeitung, die eine lückenlose Überwachung der Lackierqualität in Echtzeit sicherstellt. Hochauflösende Kamerasysteme erfassen kleinste Defekte wie Lackeinschlüsse, ungleichmäßige Schichten oder Partikelkontaminationen und geben die Informationen direkt an das Steuerungssystem weiter. Dadurch können Prozessabweichungen sofort korrigiert und Ausschuss minimiert werden.
Die Herausforderung bei Mini-Komponenten besteht oft darin, komplexe Geometrien und empfindliche Oberflächen gleichmäßig zu beschichten, ohne funktionale Bereiche zu beeinträchtigen. Selektive Lackiertechniken, unterstützt durch CAD-Daten und präzise Positionierungssysteme, ermöglichen eine gezielte Beschichtung nur der gewünschten Flächen. Dies spart Material, reduziert Nacharbeit und gewährleistet die volle Funktionalität der Bauteile.
Neben dem klassischen Schutzlack gewinnen funktionale Beschichtungen zunehmend an Bedeutung. Hierzu zählen beispielsweise Lacke mit antistatischen Eigenschaften, die das Risiko elektrostatischer Entladungen reduzieren, oder thermisch leitfähige Lacke, die zur Wärmeableitung in Miniaturbauteilen beitragen. Die Anlagen müssen daher flexibel genug sein, um verschiedene Lacktypen mit unterschiedlichen Viskositäten und Aushärtungsbedingungen verarbeiten zu können.
Auch die Umwelteffizienz der Lackierprozesse wird stetig verbessert. Durch präzise Applikationstechniken wie elektrostatisches Sprühen oder Jet-Dispensing wird der Materialverbrauch minimiert, während effiziente Filtersysteme und geschlossene Lackierkammern Emissionen auf ein Minimum reduzieren. Die Nutzung umweltfreundlicher Lackformulierungen unterstützt zusätzlich die nachhaltige Fertigung.
Schließlich spielt die ergonomische Gestaltung der Anlagen eine wichtige Rolle, um den Bedienkomfort zu erhöhen und Wartungsarbeiten zu erleichtern. Intuitive Bedienoberflächen, automatisierte Reinigungszyklen und gut zugängliche Wartungsbereiche tragen dazu bei, die Effizienz zu steigern und Ausfallzeiten zu minimieren.
Insgesamt bietet die Lackiertechnik für Mini-Komponenten eine hochpräzise, flexible und nachhaltige Lösung, die den Anforderungen moderner Produktionsumgebungen gerecht wird. Sie sichert die Qualität und Funktionalität kleinster Bauteile, steigert die Produktivität und trägt zu einer ressourcenschonenden Fertigung bei – essentielle Faktoren für den Erfolg in einem wettbewerbsintensiven Markt.
Darüber hinaus gewinnt die Vernetzung der Lackiertechnik für Mini-Komponenten innerhalb vernetzter Produktionsumgebungen zunehmend an Bedeutung. Im Rahmen von Industrie 4.0-Konzepten werden automatische Lackieranlagen mit übergeordneten Fertigungsleitsystemen verbunden, um eine durchgängige Datenerfassung, Analyse und Steuerung zu ermöglichen. Dies erlaubt eine Echtzeitüberwachung aller Prozessparameter, eine proaktive Wartungsplanung und eine flexible Anpassung an sich ändernde Produktionsbedingungen.
Die gesammelten Daten aus der Lackierprozessüberwachung fließen in intelligente Algorithmen ein, die Muster erkennen, Qualitätsabweichungen vorhersagen und Optimierungsvorschläge generieren. Diese datengetriebene Prozessoptimierung erhöht nicht nur die Fertigungsqualität, sondern senkt auch Materialverbrauch und Ausschussquoten. Die Rückverfolgbarkeit jeder einzelnen Mini-Komponente vom Auftrag bis zum fertigen Produkt wird dadurch sichergestellt und erfüllt hohe Anforderungen an Qualitätssicherung und Compliance.
In der praktischen Anwendung sind Lackieranlagen für Mini-Komponenten zunehmend mit multifunktionalen Applikationsköpfen ausgestattet, die sowohl Sprüh- als auch Dosiertechniken beherrschen. Diese Flexibilität erlaubt es, unterschiedliche Lackarten und Schichtdicken innerhalb eines Fertigungsschrittes aufzutragen, um komplexe Funktionalitäten abzudecken. So lassen sich Schutzschichten mit funktionellen Beschichtungen kombinieren, was die Bauteile optimal auf ihre Einsatzbedingungen vorbereitet.
Die Miniaturisierung und Komplexität der Bauteile führt zudem zu immer höheren Anforderungen an die Handhabungssysteme. Präzise Robotiklösungen mit Feinpositionierung und sensiblen Greifsystemen ermöglichen eine schonende und effiziente Vereinzlung sowie Weitergabe der Komponenten innerhalb der Lackieranlage. Diese Automatisierung erhöht die Durchsatzraten und reduziert gleichzeitig das Risiko von Beschädigungen.
Umweltfreundlichkeit und Energieeffizienz bleiben zentrale Themen in der Weiterentwicklung der Lackiertechnik für Mini-Komponenten. Fortschrittliche Absaug- und Filtersysteme minimieren Emissionen, während energieoptimierte Trocknungs- und Aushärteverfahren den Stromverbrauch senken. Die vermehrte Verwendung wasserbasierter und lösemittelfreier Lacke unterstützt zusätzlich die nachhaltige Produktion.
Abschließend lässt sich festhalten, dass die Lackiertechnik für Mini-Komponenten eine hochdynamische und technologisch anspruchsvolle Disziplin ist, die modernste Automatisierungs- und Digitalisierungslösungen integriert. Sie gewährleistet höchste Präzision, Qualität und Effizienz bei der Beschichtung kleinster Bauteile und ist damit ein entscheidender Faktor für die Wettbewerbsfähigkeit in zukunftsorientierten Industrien.
Pulveranlage für Beschichtung der Kleinen Metallteile
Pulveranlagen für die Beschichtung kleiner Metallteile sind speziell ausgelegt, um auch winzige und filigrane Bauteile zuverlässig mit einer robusten, gleichmäßigen Pulverschicht zu versehen. Diese Anlagen finden breite Anwendung in Branchen wie der Feinmechanik, Elektronik, Medizintechnik oder auch im Schmuckbereich, wo neben dem Schutz vor Korrosion und Verschleiß oft auch ästhetische Anforderungen erfüllt werden müssen.
Das Herzstück solcher Pulveranlagen ist ein fein abgestimmtes Applikationssystem, das eine kontrollierte und präzise Aufbringung des Pulverlacks ermöglicht. Häufig kommen elektrostatische Pulverbeschichtungsverfahren zum Einsatz, bei denen das Pulver durch elektrostatische Ladung an das Metallteil haftet. Besonders bei kleinen Teilen ist eine sorgfältige Dosierung und punktgenaue Applikation wichtig, um eine gleichmäßige Schichtdicke zu gewährleisten und Überbeschichtungen oder Verklumpungen zu vermeiden.
Um dies zu erreichen, sind die Pulveranlagen meist mit speziellen Düsen und Applikationsköpfen ausgestattet, die feine Pulverstrahlen erzeugen und gezielt auf die zu beschichtenden Flächen lenken. Die Teile werden oft mittels präziser Handhabungssysteme, wie Vakuumgreifern oder speziellen Zuführvorrichtungen, positioniert und rotiert, um eine vollständige Beschichtung aller Oberflächen zu ermöglichen. Die Steuerung der Applikation erfolgt computergestützt und erlaubt die Anpassung der Parameter wie Pulvermenge, Sprühwinkel und Fördergeschwindigkeit, um auch unterschiedlichste Metallteile optimal zu beschichten.
Die anschließende Aushärtung des Pulverlacks erfolgt in speziellen Einbrennöfen, die auf die thermischen Eigenschaften der kleinen Metallteile abgestimmt sind. Die Temperaturprofile werden so gestaltet, dass die Bauteile nicht beschädigt werden und der Pulverlack eine optimale Härte und Haftung erreicht. Schnelle Durchlaufzeiten und eine effiziente Wärmenutzung sind dabei wichtige Faktoren für eine wirtschaftliche Produktion.
Moderne Pulveranlagen für kleine Metallteile sind zudem mit Filtersystemen und Rückgewinnungseinheiten ausgestattet, die überschüssiges Pulver auffangen und wiederverwerten. Dies reduziert den Materialverbrauch und schont Ressourcen. Gleichzeitig sorgen Absaug- und Filtertechnik für eine saubere und sichere Arbeitsumgebung, indem sie Pulverstaub effektiv entfernen.
Um die Qualität der Beschichtung sicherzustellen, integrieren viele Anlagen Inline-Inspektionssysteme, die Schichtdicke, Oberflächenqualität und Haftung überwachen. Defekte oder unzureichend beschichtete Teile werden automatisch erkannt und aus dem Produktionsfluss entfernt.
Insgesamt bieten Pulveranlagen für die Beschichtung kleiner Metallteile eine robuste, umweltfreundliche und wirtschaftliche Lösung, die Schutz und optische Veredelung in einem Schritt ermöglicht. Sie sind flexibel anpassbar, präzise steuerbar und tragen so maßgeblich zur Steigerung der Produktqualität und Fertigungseffizienz bei.
Ein wesentlicher Vorteil der Pulverbeschichtung bei kleinen Metallteilen liegt in der besonders hohen Beständigkeit der erzeugten Beschichtung. Im Vergleich zu flüssigen Lacken bietet die Pulverschicht eine deutlich bessere Kratz- und Stoßfestigkeit sowie eine hervorragende Haftung auf dem Grundmaterial. Gerade bei Kleinteilen, die oft mechanischer Beanspruchung, Reibung oder Kontakt mit anderen Oberflächen ausgesetzt sind, ist dieser Schutzfaktor von großer Bedeutung. Zudem sind Pulverlacke frei von Lösungsmitteln, was sie umweltfreundlicher macht und gleichzeitig die Explosions- und Brandgefahr im Produktionsumfeld reduziert.
Da bei kleinen Metallteilen häufig auch eine große Variantenvielfalt herrscht – sei es in Form, Größe, Funktion oder Farbe – müssen die Anlagen flexibel auf unterschiedliche Anforderungen reagieren können. Moderne Pulveranlagen sind daher so konzipiert, dass sie sich schnell auf neue Produktserien umstellen lassen. Dies wird durch speicherbare Rezepturen, automatische Pulverwechselsysteme und modulare Fördertechnik unterstützt. Auch bei Farbwechseln ist es entscheidend, dass keine Rückstände zurückbleiben, weshalb die Anlagen mit leicht zu reinigenden Kabinen, antistatischem Materialeinsatz und automatisierten Spülzyklen ausgestattet sind.
Die Handhabung der winzigen Teile erfordert eine besondere mechanische Präzision. So werden die Werkstücke entweder lose in Trommeln bewegt und dabei beschichtet, was bei sehr kleinen oder massiven Geometrien gut funktioniert, oder sie werden einzeln oder gruppenweise an Haken, Gestellen oder speziellen Vorrichtungen aufgehängt. Hierbei ist darauf zu achten, dass keine Beschattung entsteht, also keine Bereiche durch die Halterung von der Beschichtung ausgeschlossen werden. Deshalb kommen oft rotierende oder kippende Aufhängungssysteme zum Einsatz, die während des Beschichtungsvorgangs Bewegung in die Bauteile bringen und so eine gleichmäßige Schichtverteilung sicherstellen.
Die eingesetzten Pulverlacke sind in einer breiten Palette von Farben, Glanzgraden und Oberflächeneffekten erhältlich, darunter matte, seidenglänzende oder hochglänzende Ausführungen, sowie strukturierte, metallische oder transparente Varianten. Je nach Anwendung sind auch funktionale Pulverlacke verfügbar, etwa solche mit antibakteriellen, UV-beständigen oder chemikalienresistenten Eigenschaften. Die Anlage muss in der Lage sein, diese unterschiedlichen Materialien zu verarbeiten, ohne die Prozessstabilität zu beeinträchtigen.
Ein weiterer zentraler Aspekt ist die Energieeffizienz des gesamten Systems. Da das Einbrennen der Pulverbeschichtung ein energieintensiver Schritt ist, setzen viele Hersteller auf intelligente Ofentechnik mit zonenweiser Temperaturregelung, Wärmerückgewinnung und kurzen Aufheizzeiten. In Kombination mit schneller Fördertechnik und energieeffizienten Antrieben lassen sich die Betriebskosten senken, während die Produktivität hoch bleibt.
Nicht zuletzt erfüllt die moderne Pulverbeschichtungstechnik auch zunehmend Anforderungen an Nachverfolgbarkeit und Qualitätssicherung. Über digitale Schnittstellen lassen sich Produktionsdaten erfassen, speichern und analysieren – etwa zur Schichtdicke, Temperaturverläufen oder Durchsatzmengen. Diese Daten ermöglichen eine lückenlose Rückverfolgbarkeit jedes beschichteten Teils und bilden die Grundlage für auditsichere Dokumentation in regulierten Branchen wie der Automobil- oder Medizintechnik.
Pulveranlagen für kleine Metallteile kombinieren also höchste Präzision mit industrieller Effizienz und ökologischer Verantwortung. Sie sind ein zentrales Werkzeug für Hersteller, die auf gleichbleibende Qualität, Flexibilität in der Produktion und nachhaltige Oberflächenlösungen setzen.
Durch die gestiegenen Anforderungen an Produktqualität und Individualisierung rücken zusätzliche Automatisierungs- und Digitalisierungsschritte bei Pulveranlagen für kleine Metallteile immer stärker in den Fokus. Moderne Systeme sind heute in der Lage, ohne manuelles Eingreifen ganze Fertigungschargen automatisch zu identifizieren, geeignete Beschichtungsprogramme selbstständig auszuwählen und die Produktionsparameter in Echtzeit anzupassen. Dies ist insbesondere bei einer hohen Variantenvielfalt und häufigen Produktwechseln ein großer Vorteil, da sich Rüstzeiten minimieren und die Prozesssicherheit erhöhen.
Ein weiterer Fortschritt ist die Integration von Robotik in die Handhabung und Positionierung der kleinen Metallteile. Roboterarme mit hoher Wiederholgenauigkeit und sensiblen Greifern können auch sehr kleine oder empfindliche Teile sicher greifen, ausrichten und in die Applikationszonen einführen. Dadurch wird nicht nur die Effizienz gesteigert, sondern auch die Gefahr von Beschädigungen oder Verunreinigungen reduziert. Diese Art der Handhabung ist besonders in Branchen mit hohem Anspruch an die Oberfläche – wie Medizintechnik, Optik oder Elektronik – von entscheidender Bedeutung.
Für die Qualität der Pulverbeschichtung spielt neben der Applikation auch die elektrostatische Aufladung eine wichtige Rolle. Gerade bei kleinen und verwinkelten Metallteilen ist die gezielte Steuerung der elektrischen Feldverteilung essenziell, um eine gleichmäßige Anhaftung des Pulvers zu erzielen. Moderne Generatoren und intelligente Regelkreise überwachen permanent die Ladung, die Erdung der Werkstücke sowie die Pulverausbringung. In Kombination mit Bewegungssystemen – etwa rotierenden Gestellen oder oszillierenden Sprühdüsen – kann so selbst bei schwierigsten Geometrien eine makellose Oberfläche erzeugt werden.
Auch das Thema Nachhaltigkeit wird bei diesen Anlagen aktiv mitgedacht. Pulverrückgewinnungssysteme erreichen heute Rückführquoten von über 95 %, was nicht nur Kosten senkt, sondern auch den Materialkreislauf schließt. Gleichzeitig wird durch die Lösungsmittelfreiheit der Pulverbeschichtung der CO₂-Fußabdruck verringert. In vielen Fällen ersetzt die Pulverbeschichtung sogar galvanische Prozesse, die deutlich umweltbelastender sind.
Zusätzliche Optimierungspotenziale ergeben sich durch den Einsatz von digitalen Zwillingen – also virtuellen Abbildern der realen Anlage. Mit ihnen lassen sich Beschichtungsprozesse vorab simulieren, Parameter optimieren oder mögliche Fehlerquellen analysieren, noch bevor ein einziges Teil produziert wird. Diese Technologie wird zunehmend zur Standardausstattung bei neuen Anlagenentwicklungen und unterstützt sowohl die Inbetriebnahme als auch den laufenden Betrieb durch kontinuierliche Prozessvergleiche.
Letztlich tragen all diese Entwicklungen dazu bei, dass Pulveranlagen für die Beschichtung kleiner Metallteile heute nicht nur zuverlässige, sondern auch intelligente und ressourcenschonende Systeme darstellen. Sie bieten Herstellern eine exakte Steuerung über den gesamten Beschichtungsprozess, von der Teilezuführung über die Pulverbeschichtung bis hin zur Aushärtung und Qualitätskontrolle. So entstehen Oberflächen, die technisch wie optisch höchsten Ansprüchen gerecht werden – und das in kurzer Zeit, mit hoher Wiederholbarkeit und maximaler Wirtschaftlichkeit.
Lackiersystem für kleine Produkte
Ein Lackiersystem für kleine Produkte ist eine speziell entwickelte Anlage, die präzise, effiziente und reproduzierbare Beschichtungen auf kompakten Bauteilen und Miniaturkomponenten ermöglicht. Solche Systeme finden sich in der Serienproduktion zahlreicher Branchen wie Elektronik, Feinmechanik, Medizintechnik, Spielzeugfertigung, Automobilzulieferung oder bei Konsumgütern mit anspruchsvoller Oberflächengestaltung. Die Herausforderung bei kleinen Produkten liegt darin, trotz ihrer geringen Größe eine gleichmäßige und fehlerfreie Lackierung zu erzielen, ohne Funktion oder Geometrie zu beeinträchtigen.
Diese Lackiersysteme kombinieren hochpräzise Sprühtechnologien mit automatisierter Handhabung, oft unterstützt durch Robotertechnik oder spezielle Fördermechanismen wie Rundtakttische, Schiebesysteme oder Palettenbänder. Die Sprühapplikation erfolgt durch mikrofeine Düsen, Airbrush-Systeme oder elektrostatische Sprühköpfe, die exakt gesteuert werden und sich der Form und Position jedes Produkts anpassen. Eine reproduzierbare Schichtdicke, glatte Oberfläche und vollständige Abdeckung selbst filigranster Bereiche sind dabei zentral.
Die Produkte werden oft auf speziellen Halterungen fixiert, die eine rotationssymmetrische oder mehrdimensionale Bewegung während der Applikation ermöglichen, um auch schwer zugängliche Stellen sicher zu erreichen. Diese Rotation oder Oszillation während des Lackiervorgangs sorgt für eine gleichmäßige Schichtverteilung ohne Laufnasen oder Schattenzonen. Besonders bei glänzenden oder dekorativen Oberflächen ist diese gleichmäßige Deckung entscheidend.
Zur Härtung des aufgetragenen Lacks kommen je nach Anforderung UV-, IR- oder Warmlufttrockner zum Einsatz, die exakt auf das Material und die Lackeigenschaften abgestimmt sind. Gerade bei kleinen Produkten ist eine schonende, spannungsfreie und schnelle Trocknung wichtig, um Verformungen oder Oberflächenfehler zu vermeiden und gleichzeitig kurze Taktzeiten zu ermöglichen.
Moderne Lackiersysteme für kleine Produkte sind häufig modular aufgebaut und erlauben die Verarbeitung verschiedenster Materialien und Lacktypen – von lösungsmittelbasierten oder wasserlöslichen Lacksystemen bis hin zu Speziallacken mit besonderen Eigenschaften wie Kratzfestigkeit, Chemikalienbeständigkeit oder dekorativen Effekten. Die Reinigung und Wartung der Anlage erfolgt oft automatisiert, um Farbrückstände zu entfernen und Rüstzeiten bei Farb- oder Produktswechseln zu minimieren.
Ein zentrales Element dieser Systeme ist die Qualitätssicherung. Optische Sensoren, Lasermessungen und Kamerainspektionssysteme erfassen Lackierfehler wie Sprühnebel, Fehlstellen, Blasen oder zu dicke Schichten und ermöglichen eine sofortige Prozesskorrektur oder automatische Aussortierung fehlerhafter Teile. Die Anlagen können mit übergeordneten Fertigungs- und Steuerungssystemen vernetzt werden, sodass Daten über Ausstoß, Qualität, Wartung und Energieverbrauch kontinuierlich erfasst und analysiert werden.
Insgesamt bietet ein Lackiersystem für kleine Produkte eine technisch ausgereifte, platzsparende und wirtschaftlich attraktive Lösung, um hochwertige Oberflächen in gleichbleibender Qualität zu erzeugen – schnell, effizient und flexibel anpassbar auf wechselnde Produktserien und Designanforderungen.
Ein Lackiersystem für kleine Produkte muss nicht nur auf Präzision, sondern auch auf Prozessstabilität und hohe Wiederholgenauigkeit ausgelegt sein. Gerade bei kleinen Serien mit großer Variantenvielfalt ist die Fähigkeit entscheidend, schnell und ohne aufwändige Umrüstungen zwischen verschiedenen Produktformen, Materialien und Farbtönen wechseln zu können. Die meisten modernen Systeme verfügen daher über speicherbare Programme, die für jedes Produkt individuelle Parameter wie Sprühzeit, Düsengeometrie, Lackmenge, Fördergeschwindigkeit und Trocknungstemperatur festlegen. Dies ermöglicht eine gleichbleibende Qualität selbst bei hoher Produktwechselrate.
Besonders wichtig ist bei kleinen Produkten die präzise Steuerung der Sprühtechnik, um Overspray zu minimieren und auch komplexe Geometrien lückenlos zu erreichen. In vielen Fällen kommen daher mehrachsige Sprühroboter oder CNC-gesteuerte Düsen zum Einsatz, die sich exakt entlang der Konturen der Bauteile bewegen. Diese Robotersteuerungen ermöglichen nicht nur die genaue Einhaltung der Schichtdicke, sondern auch gleichmäßige Übergänge bei mehrfarbigen oder mehrschichtigen Lackaufträgen, etwa bei Kombilackierungen mit Klar- und Effektlacken. Darüber hinaus wird die Temperatur- und Luftführung innerhalb der Lackierkabine speziell auf kleine Produkte abgestimmt, um Turbulenzen, Verwirbelungen oder ungleichmäßige Trocknung zu vermeiden.
Auch die Fördertechnik innerhalb eines solchen Systems ist speziell an die Anforderungen kleiner Produkte angepasst. Je nach Geometrie und Größe kommen Werkstückträger mit Zentriersystemen, Drehhalterungen oder individuell gefertigte Vorrichtungen zum Einsatz, die jedes Teil exakt positionieren und fixieren. In hochautomatisierten Anlagen erfolgt die Zuführung der Produkte meist per Roboter oder Vibrationsförderer, sodass keine manuelle Nachjustierung notwendig ist.
Für die Trocknung und Aushärtung stehen verschiedene Technologien zur Verfügung, je nach eingesetztem Lackmaterial. UV-Härtung eignet sich besonders für schnelle Taktzeiten und wärmeempfindliche Materialien, während konventionelle Warmluft- oder Infrarotöfen für robustere oder dickere Lackschichten eingesetzt werden. Die Anlagensteuerung sorgt für eine exakte Temperaturkurve und gleichmäßige Energieverteilung, um Farbverläufe, Rissbildungen oder Glanzunterschiede zu vermeiden. Bei besonders empfindlichen Produkten kann der Trocknungsprozess in mehreren Stufen oder bei reduzierter Temperatur erfolgen.
Ein weiterer zentraler Aspekt moderner Lackiersysteme ist die Umweltfreundlichkeit. Durch die geschlossene Kabinenbauweise mit optimierter Abluftführung und integrierter Pulver- oder Lacknebelabsaugung werden Emissionen auf ein Minimum reduziert. Der Einsatz wasserbasierter Lacksysteme oder hochfester Pulverbeschichtungen trägt zusätzlich zu einer umweltschonenden Produktion bei. Reinigungszyklen und Farbwechselprozesse sind oft automatisiert, um Materialverluste zu verringern und die Sicherheit des Bedienpersonals zu erhöhen.
Schließlich spielen digitale Technologien eine immer größere Rolle. Industrie-4.0-fähige Lackiersysteme für kleine Produkte erfassen kontinuierlich Prozessdaten, Produktionsvolumen und Qualitätskennzahlen. Über digitale Dashboards können Bediener jederzeit den Anlagenzustand, Wartungsbedarf oder die aktuelle Auslastung überwachen. In vielen Fällen lassen sich diese Systeme mit Predictive-Maintenance-Funktionen ausstatten, die mögliche Störungen frühzeitig erkennen und Ausfallzeiten vermeiden. Die Integration in zentrale Produktionsleitsysteme oder ERP-Plattformen ermöglicht eine lückenlose Nachverfolgung jedes einzelnen Bauteils und unterstützt die Rückverfolgbarkeit im Qualitätsmanagement.
Insgesamt stellen moderne Lackiersysteme für kleine Produkte eine hochflexible, präzise und ressourceneffiziente Lösung dar, die sowohl für Massenfertiger als auch für Hersteller kleiner Serien oder individualisierter Kleinprodukte enorme Vorteile bietet. Sie verbinden technologische Raffinesse mit automatisierter Zuverlässigkeit und erfüllen die gestiegenen Anforderungen an Produktqualität, Nachhaltigkeit und Effizienz in gleichem Maße.
Ein weiterer wesentlicher Vorteil moderner Lackiersysteme für kleine Produkte liegt in ihrer Fähigkeit zur Verarbeitung unterschiedlichster Materialien. Neben klassischen Metallen wie Stahl, Aluminium oder Messing lassen sich auch Kunststoffe, Keramiken oder Verbundwerkstoffe zuverlässig beschichten. Dabei ist es entscheidend, dass die Systeme die unterschiedlichen Oberflächeneigenschaften und Haftungseigenschaften der Materialien erkennen und sich automatisch anpassen. Etwa durch Variationen im Vorbehandlungsprozess – wie Ionisierung, Plasmaaktivierung, Entfettung oder Primerauftrag – wird eine optimale Haftung der Lackschicht gewährleistet, unabhängig von der Materialart oder Oberflächenstruktur.
Die Vorbehandlung kleiner Produkte erfolgt in diesen Systemen vollautomatisch und oft integriert in das Gesamtsystem. Je nach Bauteilgröße und Verschmutzungsgrad kommen rotierende Waschmodule, Tauchbäder, Luftdüsen oder UV-Vorbehandlungen zum Einsatz. Diese Reinigungsschritte sind elementar, da bereits kleinste Staubpartikel oder Rückstände zu Lackfehlern führen können. Gerade bei hochdekorativen oder funktionalen Lackierungen – etwa in der Konsumgüterindustrie oder Medizintechnik – entscheidet die Vorbehandlung maßgeblich über die Produktqualität.
Zusätzlich bieten viele Lackiersysteme für kleine Produkte eine vollständige Kontrolle über die optische Erscheinung der Beschichtung. Neben Farbe und Glanz lassen sich strukturierte Oberflächen, Perleffekte oder matte Finishes mit hoher Wiederholbarkeit erzeugen. Das ist besonders relevant für Designprodukte, bei denen nicht nur der technische Schutz, sondern auch der visuelle Eindruck im Vordergrund steht. Hier ermöglicht der Einsatz präziser Farbmanagementsysteme sowie die computergestützte Steuerung des Sprühbildes eine konstant reproduzierbare Oberfläche – unabhängig von Chargengröße oder Bedienpersonal.
Einige hochspezialisierte Lackiersysteme sind zudem in der Lage, Maskierungs- und partielle Lackierprozesse durchzuführen. Bei vielen kleinen Produkten müssen bestimmte Flächen ausgespart oder unterschiedlich beschichtet werden. Hier kommen automatische Maskierungssysteme, digital gesteuerte Lackierschablonen oder selektive Sprühdüsen zum Einsatz, die den Lack exakt auf die gewünschten Bereiche aufbringen. Dieses Maß an Präzision minimiert Nacharbeit und verbessert die optische und funktionale Genauigkeit des Endprodukts erheblich.
Auch in Bezug auf Platzbedarf und Energieeffizienz sind Lackiersysteme für kleine Produkte zunehmend optimiert. Ihre kompakte Bauweise erlaubt die Integration in bestehende Produktionslinien, auch bei begrenztem Raumangebot. Gleichzeitig senken verbesserte Luftführung, Wärmerückgewinnungssysteme und energieeffiziente Antriebe den Strom- und Ressourcenverbrauch – ein nicht zu unterschätzender Faktor in modernen, nachhaltigkeitsorientierten Fertigungen.
Zukunftsweisende Entwicklungen in diesem Bereich gehen in Richtung noch stärkerer Individualisierung und Miniaturisierung. Kleinste Teile – zum Beispiel Mikrogehäuse, Sensorabdeckungen oder Bauteile in Wearables – erfordern zunehmend Lackiersysteme, die mit extrem feinen Düsensystemen arbeiten und mit hochauflösenden Kameras millimetergenau gesteuert werden. Die Kombination von Robotik, KI-gestützter Prozessüberwachung und adaptiven Steuerungen eröffnet hier völlig neue Anwendungsmöglichkeiten und Qualitätsstandards.
Zusammengefasst sind Lackiersysteme für kleine Produkte heute weit mehr als reine Beschichtungseinheiten – sie sind komplexe, adaptive Fertigungsmodule, die Produktqualität, Designflexibilität und Prozesssicherheit in einem System vereinen. Ihre Rolle in der industriellen Fertigung wird in dem Maße weiter wachsen, wie Bauteile kleiner, funktionaler und hochwertiger werden – und wie gleichzeitig Effizienz, Nachhaltigkeit und Rückverfolgbarkeit weiter an Bedeutung gewinnen.
Lackieranlage für Automatische Pulverbeschichtung der kleinen Objekte
Eine Lackieranlage für die automatische Pulverbeschichtung kleiner Objekte ist speziell darauf ausgelegt, winzige Bauteile effizient, präzise und gleichmäßig mit Pulverlacken zu versehen. Diese Anlagen kommen vor allem in Branchen wie der Elektronikfertigung, Feinmechanik, Medizintechnik und Schmuckindustrie zum Einsatz, wo kleine Metall- oder Kunststoffteile mit robusten, widerstandsfähigen Oberflächen ausgestattet werden müssen.
Das System besteht typischerweise aus mehreren Modulen: Zunächst erfolgt die automatische Zuführung der kleinen Objekte über Förderbänder, Vibrationsförderer oder robotergestützte Handhabungssysteme. Präzise Greifer, Vakuum- oder Elektrostathalterungen sorgen dafür, dass die Teile sicher vereinzelt und optimal positioniert werden. Dies ist besonders wichtig, um während der Beschichtung eine vollständige und gleichmäßige Pulverschicht auf allen Oberflächen zu gewährleisten.
Die Pulverbeschichtung selbst erfolgt durch elektrostatisch aufgeladene Pulverdüsen, die das Pulver fein dosiert und mit hoher Genauigkeit auf die kleinen Objekte auftragen. Um Beschattungen zu vermeiden und alle Oberflächenbereiche zu erreichen, sind die Teile oft in rotierenden oder oszillierenden Halterungen fixiert, die während des Sprühvorgangs kontinuierlich bewegt werden. Hochentwickelte Steuerungen passen dabei die Pulvermenge, die Sprühdauer und die Ladung je nach Objektgröße und -form automatisch an.
Nach der Pulverapplikation durchlaufen die Teile einen speziell abgestimmten Einbrennprozess in einem Durchlaufofen. Die Temperaturprofile sind so konzipiert, dass sie eine vollständige Aushärtung des Pulverlacks ermöglichen, ohne die kleinen, oftmals empfindlichen Bauteile thermisch zu schädigen. Schnelle Durchlaufzeiten und eine gleichmäßige Wärmeverteilung im Ofen sind dabei entscheidend für die Qualität und Wirtschaftlichkeit der Anlage.
Moderne Anlagen verfügen über integrierte Pulverrückgewinnungssysteme, die überschüssiges Pulver effizient absaugen, filtern und wieder dem Kreislauf zuführen. Dies minimiert den Materialverbrauch und senkt die Kosten bei gleichzeitig nachhaltiger Produktion. Zusätzlich sind umfassende Filtersysteme installiert, um die Emission von Pulverstaub in die Umgebungsluft zu verhindern und so die Arbeitssicherheit und Umweltverträglichkeit zu gewährleisten.
Zur Sicherstellung der Beschichtungsqualität sind oft Inline-Inspektionssysteme integriert, die die Schichtdicke, Oberflächenbeschaffenheit und eventuelle Fehlstellen prüfen. Diese Systeme ermöglichen eine sofortige Fehlererkennung und gegebenenfalls das Aussortieren nicht konformer Teile, wodurch Ausschuss reduziert und die Prozesssicherheit erhöht wird.
Die Steuerung der gesamten Lackieranlage erfolgt meist über eine zentrale SPS- oder PC-basierte Einheit mit benutzerfreundlicher Oberfläche. Diese erlaubt die einfache Anpassung an unterschiedliche Objekte, Lacktypen und Produktionsbedingungen. Automatische Rezepturen, Protokollierungen und Schnittstellen zu übergeordneten Fertigungssystemen unterstützen die flexible und dokumentierte Fertigung kleiner Bauteile.
Insgesamt ermöglicht eine automatische Pulverbeschichtungsanlage für kleine Objekte eine hochpräzise, reproduzierbare und wirtschaftliche Beschichtungslösung. Sie verbindet moderne Automatisierung, effiziente Pulvertechnologie und umweltbewusste Prozessgestaltung und ist damit ideal geeignet, die wachsenden Anforderungen an Qualität, Produktivität und Nachhaltigkeit in der Fertigung kleiner Bauteile zu erfüllen.
Die Entwicklung automatischer Pulverbeschichtungsanlagen für kleine Objekte geht einher mit einem steigenden Bedarf an Flexibilität und Präzision in der Oberflächenveredelung. Dabei spielen besonders modulare Systemarchitekturen eine zentrale Rolle, die es ermöglichen, die Anlagen schnell und einfach an verschiedene Produktgrößen, Formen und Stückzahlen anzupassen. So können Hersteller kurzfristig auf wechselnde Marktanforderungen reagieren und verschiedene Miniaturteile effizient in derselben Anlage beschichten.
Ein entscheidender Faktor ist die präzise Steuerung der Pulverapplikation. Moderne Anlagen nutzen computergestützte Regelkreise, die Parameter wie Pulvermenge, Elektrostatische Ladung, Sprühwinkel und Fördergeschwindigkeit dynamisch anpassen. Dies führt zu einer homogenen Schichtdicke, minimiert Overspray und sorgt für eine optimale Haftung auch auf komplexen Geometrien. Die Pulverstrahlen werden gezielt so gelenkt, dass alle Oberflächenbereiche der kleinen Objekte erreicht werden, selbst bei filigranen Konturen oder eng beieinanderliegenden Bauteilen.
Die Handhabung der kleinen Teile erfolgt häufig automatisiert mit Robotersystemen, die hohe Wiederholgenauigkeit und flexible Bewegungsmuster bieten. Greifersysteme sind speziell auf die empfindlichen Mini-Objekte ausgelegt, um Beschädigungen zu vermeiden und eine präzise Ausrichtung zu gewährleisten. Zusätzlich kommen Rotations- und Schwenkeinheiten zum Einsatz, die die Teile während der Beschichtung in Bewegung halten und so eine vollständige und gleichmäßige Pulverschicht ermöglichen.
Zur Energieeffizienz und Umweltfreundlichkeit trägt neben der Pulverrückgewinnung auch die optimierte Gestaltung der Einbrennöfen bei. Moderne Durchlaufofenkonzepte nutzen eine zonale Temperaturregelung und Wärmerückgewinnungssysteme, die den Energieverbrauch deutlich senken. Gleichzeitig garantieren sie eine kontrollierte und schonende Aushärtung, die thermische Belastungen der kleinen Bauteile minimiert und so deren Funktionalität erhält.
Qualitätssicherung ist integraler Bestandteil moderner Anlagen. Hochauflösende Kamerasysteme und Schichtdickenmessgeräte erfassen die Beschichtungsqualität in Echtzeit, während intelligente Algorithmen Anomalien erkennen und sofortige Korrekturmaßnahmen einleiten können. Dadurch wird der Ausschuss reduziert und die Produktivität erhöht. Die Dokumentation aller Prozessdaten unterstützt die Rückverfolgbarkeit und erfüllt die Anforderungen moderner Qualitätsmanagementsysteme.
Die Bedienung der Anlagen erfolgt über intuitive Benutzeroberflächen mit grafischer Darstellung des Prozesses. Automatische Wartungs- und Reinigungsprogramme reduzieren den manuellen Aufwand und sorgen für konstante Betriebsbereitschaft. Über Schnittstellen können die Anlagen nahtlos in übergeordnete Produktionssteuerungssysteme eingebunden werden, was eine durchgängige Vernetzung im Sinne von Industrie 4.0 ermöglicht.
Insgesamt stellen automatische Pulverbeschichtungsanlagen für kleine Objekte eine Kombination aus technologischem Fortschritt, Effizienz und Nachhaltigkeit dar. Sie ermöglichen eine hochqualitative Oberflächenbeschichtung bei gleichzeitig hoher Flexibilität und Wirtschaftlichkeit. Durch kontinuierliche Innovationen werden diese Systeme zunehmend in der Lage sein, noch kleinere und komplexere Bauteile zu beschichten, neue Pulverlacke zu verarbeiten und den steigenden Anforderungen moderner Industriezweige gerecht zu werden.
Darüber hinaus gewinnen bei automatischen Pulverbeschichtungsanlagen für kleine Objekte zunehmend intelligente Assistenzsysteme und KI-basierte Prozessoptimierungen an Bedeutung. Mithilfe von Machine-Learning-Algorithmen werden Prozessdaten analysiert, um Muster und potenzielle Fehlerquellen frühzeitig zu erkennen. So können die Anlagen ihre Einstellungen autonom anpassen, um die Qualität der Pulverbeschichtung zu verbessern und gleichzeitig Ausschuss sowie Materialverbrauch zu reduzieren. Dies führt zu einer deutlich höheren Prozessstabilität und ermöglicht eine vorausschauende Wartung, die ungeplante Stillstände minimiert.
Auch die Integration von virtuellen Simulationstools spielt eine wachsende Rolle. Vor Produktionsbeginn lassen sich in digitalen Zwillingen der Anlagen die Beschichtungsprozesse virtuell durchspielen und optimieren. So können Parameter wie Pulvermenge, Sprühwinkel oder Ofentemperaturen vorab getestet werden, was Rüstzeiten verkürzt und den Produktionsstart beschleunigt. Besonders bei kleinen und komplexen Bauteilen ist diese präzise Planung essentiell, um die Beschichtung gleichmäßig und fehlerfrei aufzutragen.
Die zunehmende Miniaturisierung der Objekte erfordert zudem weiterentwickelte Applikationstechnologien. Neben klassischen elektrostatischen Pulverdüsen kommen immer öfter spezielle Düsen mit ultrafeinen Strahlen oder Mehrfachdüsensysteme zum Einsatz, die eine punktgenaue und selektive Beschichtung ermöglichen. So lassen sich auch komplexe Formen mit unterschiedlichen Schichtdicken oder mehreren Lackschichten in einem Durchlauf realisieren.
Ein weiteres Entwicklungsfeld liegt in der Kombination von Pulverbeschichtung mit anderen Oberflächentechnologien. Hybridanlagen ermöglichen beispielsweise die nahtlose Integration von Nasslackierprozessen oder funktionalen Beschichtungen wie Antistatik- oder Leitlackschichten. Dies erweitert das Anwendungsspektrum und schafft Mehrwert durch multifunktionale Oberflächen, die zugleich schützen, isolieren oder optisch aufwerten.
Nicht zuletzt werden ergonomische Aspekte und die Sicherheit bei der Bedienung der Anlagen kontinuierlich verbessert. Automatische Reinigungszyklen, einfache Zugänglichkeit zu Wartungsstellen und intuitive Bedienkonzepte erhöhen die Benutzerfreundlichkeit und reduzieren die Belastung für das Personal. Gleichzeitig sorgen moderne Absaug- und Filtersysteme für eine staubfreie und sichere Arbeitsumgebung, die den aktuellen Gesundheits- und Sicherheitsstandards entspricht.
Insgesamt zeichnet sich die Zukunft automatischer Pulverbeschichtungsanlagen für kleine Objekte durch eine immer stärkere Verknüpfung von Automatisierung, digitaler Intelligenz und nachhaltigen Technologien aus. Diese Anlagen werden somit zu zentralen Bausteinen moderner, flexibler und effizienter Produktionsprozesse, die den hohen Anforderungen an Qualität, Wirtschaftlichkeit und Umweltverträglichkeit gerecht werden.
Lackieranlage für Mikroteile
Eine Lackieranlage für Mikroteile ist speziell auf die hohen Anforderungen der Oberflächenbeschichtung von äußerst kleinen, oft komplex geformten Bauteilen ausgelegt. Mikroteile finden sich in Branchen wie der Medizintechnik, Mikroelektronik, Uhrenindustrie oder Präzisionsmechanik, wo höchste Genauigkeit, schonende Behandlung und makellose Oberflächenqualität unabdingbar sind. Die Lackierung solcher Miniaturkomponenten stellt besondere Herausforderungen an die Präzision der Applikation, die Handhabung und die Prozesskontrolle.
Diese Anlagen verfügen über hochpräzise Sprühsysteme, die mit mikrofeinen Düsen oder spezialisierten Dosiersystemen arbeiten und den Lack in extrem dünnen, gleichmäßigen Schichten auftragen. Elektrostatische Applikationstechniken werden häufig eingesetzt, um auch kleinste Strukturen optimal und materialschonend zu beschichten. Die Steuerung erfolgt über moderne CNC- oder Robotersteuerungen, die die Bewegungen der Sprühköpfe millimetergenau synchronisieren und individuell an die komplexen Geometrien der Mikroteile anpassen.
Die Handhabung der Mikroteile erfolgt über feinfühlige Greif- und Zuführsysteme, die häufig auf Vakuumtechnik oder pneumatischen Greifern basieren. Um Beschädigungen oder Kontaminationen zu vermeiden, werden die Teile in geschützten Umgebungen transportiert und positioniert, oft in Kombination mit automatischen Reinigungssystemen vor der Lackierung, um eine perfekte Haftung des Lacks zu gewährleisten. Rotations- und Kippvorrichtungen ermöglichen eine vollständige Beschichtung aller Oberflächen, ohne dass manuelle Eingriffe nötig sind.
Die Trocknung der Lackschichten erfolgt in der Regel durch schonende UV- oder Infrarot-Technologien, die kurze Taktzeiten bei gleichzeitig geringer thermischer Belastung gewährleisten. Insbesondere in der Mikrotechnik ist es wichtig, dass die Bauteile weder durch Hitze verzogen noch durch mechanische Einflüsse beschädigt werden. Daher sind die Trocknungssysteme fein regelbar und in den Gesamtprozess optimal integriert.
Zur Sicherstellung der Qualität sind Lackieranlagen für Mikroteile mit hochauflösenden Kamerasystemen und Schichtdickenmessern ausgestattet, die Fehler in Echtzeit erkennen und aussortieren können. Die Anlagen sind häufig vernetzt, sodass Prozessdaten gespeichert, analysiert und rückverfolgbar dokumentiert werden – ein Muss für regulierte Industrien wie die Medizintechnik.
Moderne Anlagen zeichnen sich durch ihre kompakte Bauweise und Modularität aus, was eine einfache Integration in bestehende Fertigungslinien ermöglicht. Gleichzeitig bieten sie eine hohe Flexibilität bei der Verarbeitung verschiedener Lacktypen und -farben, was besonders bei individualisierten oder Kleinserienproduktionen von Vorteil ist.
Zusammengefasst ermöglicht eine Lackieranlage für Mikroteile eine hochpräzise, schonende und automatisierte Oberflächenbeschichtung, die den hohen Ansprüchen an Qualität, Effizienz und Nachverfolgbarkeit in der Mikrofertigung gerecht wird. Sie bildet somit eine Schlüsseltechnologie für innovative Produkte in zukunftsträchtigen Industrien.
Die Steuerung einer Lackieranlage für Mikroteile basiert auf hochpräzisen und synchronisierten Bewegungsabläufen, die es ermöglichen, selbst kleinste Details und schwer zugängliche Stellen zuverlässig zu beschichten. Durch den Einsatz von Mehrachsrobotern mit feinfühliger Sensorik und adaptiven Steuerungssystemen können die Sprühköpfe exakt an die Konturen der Mikroteile angepasst werden. Dies verhindert Über- oder Unterbeschichtungen und gewährleistet eine gleichmäßige Lackverteilung.
Die Automatisierung spielt eine zentrale Rolle, um die reproduzierbare Qualität und eine hohe Produktionsgeschwindigkeit sicherzustellen. Die Teilezuführung erfolgt über speziell entwickelte Zuführsysteme, die Mikroteile schonend vereinzeln und präzise positionieren. Oft kommen Vakuumgreifer oder elektrostatische Haltesysteme zum Einsatz, die das Bauteil sicher fixieren, ohne die Oberfläche zu beschädigen oder zu kontaminieren. Die Möglichkeit, verschiedene Größen und Formen innerhalb eines Systems zu verarbeiten, erhöht die Flexibilität und reduziert Umrüstzeiten.
Die Lackierprozesse sind so konzipiert, dass sie eine minimale Pulverschichtdicke mit hoher Haftung erzielen, was besonders bei Mikroteilen essentiell ist, um die Funktionalität nicht zu beeinträchtigen. Spezielle Lackformulierungen, die für die Applikation auf kleinen Bauteilen optimiert sind, gewährleisten eine schnelle Trocknung, hohe Abriebfestigkeit und Korrosionsschutz. Die Kombination aus präziser Dosierung und hochwertigen Materialien führt zu einer langanhaltenden und ästhetisch ansprechenden Oberfläche.
Ein weiterer wichtiger Aspekt ist die Integration von Inline-Qualitätskontrollen, die mittels optischer Sensoren, Mikroskopkameras oder Schichtdickenmessern arbeiten. Diese Systeme erkennen frühzeitig Unregelmäßigkeiten wie Fehlstellen, Blasen oder Farbabweichungen und ermöglichen eine sofortige Reaktion, beispielsweise durch Anpassung der Prozessparameter oder Aussortierung defekter Teile. Diese hohe Qualitätskontrolle ist in Bereichen wie Medizintechnik oder Mikroelektronik unerlässlich, da hier Fehler gravierende Auswirkungen haben können.
Die gesamte Anlage ist häufig in eine digitale Produktionsumgebung eingebettet, die eine umfassende Datenerfassung und -analyse ermöglicht. So können Wartungszyklen optimiert, Produktionsdaten dokumentiert und Rückverfolgbarkeit gewährleistet werden. Dies unterstützt nicht nur die Einhaltung gesetzlicher Vorgaben, sondern trägt auch zur kontinuierlichen Prozessverbesserung bei.
Besondere Aufmerksamkeit gilt der Ergonomie und Sicherheit der Bediener. Automatisierte Reinigungssysteme minimieren den direkten Kontakt mit Lackmaterialien, und geschlossene Kabinensysteme schützen vor Staub und Dämpfen. Die Wartungszugänge sind so gestaltet, dass Inspektionen und Reparaturen schnell und sicher durchgeführt werden können.
Insgesamt stellt eine Lackieranlage für Mikroteile eine hochentwickelte Kombination aus präziser Technik, Automatisierung und Prozesskontrolle dar. Sie ermöglicht es, selbst kleinste Bauteile zuverlässig mit hochwertigen Lackschichten zu versehen und so deren Schutz, Funktionalität und Ästhetik zu gewährleisten. Mit stetiger Weiterentwicklung der Technologien wird die Bedeutung solcher Anlagen in Zukunft weiter zunehmen, besonders im Zuge der zunehmenden Miniaturisierung und Spezialisierung in der Fertigung.
Darüber hinaus gewinnen in Lackieranlagen für Mikroteile zunehmend adaptive Technologien an Bedeutung, die es ermöglichen, auf schwankende Prozessbedingungen oder Bauteilvariationen in Echtzeit zu reagieren. Sensorbasierte Überwachungssysteme erfassen kontinuierlich Parameter wie Luftfeuchtigkeit, Temperatur, Lackviskosität und Sprühbildqualität und passen die Applikation automatisch an, um eine gleichbleibend hohe Beschichtungsqualität zu gewährleisten. Diese intelligente Prozesssteuerung reduziert Ausschuss, optimiert Materialeinsatz und sorgt für eine stabile Produktion auch unter wechselnden Umweltbedingungen.
Die Kombination von Mikrolackierung mit weiteren Fertigungsschritten in integrierten Systemen stellt einen weiteren Fortschritt dar. So können Reinigung, Vorbehandlung, Lackierung und Trocknung in einem kompakten, automatisierten Prozessfluss abgebildet werden. Dies minimiert Handlingzeiten, verringert Fehlerquellen und ermöglicht eine hohe Durchsatzleistung, selbst bei komplexen Mikroteilen und Kleinserien.
Bei der Auswahl der Lackmaterialien wird zunehmend auf funktionale Eigenschaften geachtet, die über die reine Oberflächenoptik hinausgehen. Spezielle Beschichtungen mit antimikrobiellen, elektrisch leitfähigen oder hitzebeständigen Eigenschaften finden verstärkt Anwendung in sensiblen Bereichen wie Medizintechnik, Elektronik oder Luft- und Raumfahrt. Lackieranlagen für Mikroteile müssen daher flexibel genug sein, um auch solche Speziallacke zu verarbeiten und deren Applikation präzise zu steuern.
Die Miniaturisierung der Bauteile und steigende Anforderungen an die Lackqualität führen zudem dazu, dass immer feinere Applikationsverfahren entwickelt werden. Nano- und Mikrozerstäuber, piezoelektrische Sprühköpfe oder Laserassistierte Beschichtungstechnologien ermöglichen extrem präzise Schichtaufträge mit minimalem Materialverbrauch. Diese Innovationen eröffnen neue Möglichkeiten, selbst komplexeste Strukturen gleichmäßig zu beschichten und funktionale Schichten punktgenau aufzubringen.
Die zunehmende Vernetzung der Anlagen im Rahmen von Industrie 4.0 erlaubt eine umfassende Integration der Lackieranlage in digitale Produktionsnetzwerke. Echtzeitdaten werden analysiert und genutzt, um Wartungsarbeiten vorherzusagen, Prozessabweichungen sofort zu korrigieren und die gesamte Fertigungslinie optimal zu steuern. Dies steigert nicht nur die Effizienz, sondern trägt auch zur nachhaltigen Ressourcennutzung und Kostensenkung bei.
Nicht zuletzt ist die Ergonomie und Sicherheit für das Bedienpersonal ein wichtiger Fokus. Automatisierte Reinigungs- und Wartungsfunktionen, gut zugängliche Bauteile und intuitive Bedienoberflächen erleichtern die Handhabung und reduzieren Ausfallzeiten. Abgeschlossene Kabinensysteme und moderne Absaugtechnik schützen vor gesundheitsschädlichen Dämpfen und Partikeln, sodass hohe Sicherheitsstandards erfüllt werden.
Insgesamt sind Lackieranlagen für Mikroteile hochkomplexe, technologisch fortschrittliche Systeme, die präzise, flexible und umweltfreundliche Oberflächenbeschichtungen ermöglichen. Sie spielen eine Schlüsselrolle bei der Fertigung innovativer Miniaturprodukte und entwickeln sich stetig weiter, um den wachsenden Anforderungen moderner Industrien gerecht zu werden.
Pulverbeschichtungsanlage für Mini-Teile
Eine Pulverbeschichtungsanlage für Mini-Teile ist speziell darauf ausgelegt, kleine Bauteile effizient, präzise und gleichmäßig mit Pulverlacken zu beschichten. Solche Anlagen werden in Branchen wie Elektronik, Feinmechanik, Medizintechnik oder Schmuckfertigung eingesetzt, wo die Oberflächen von winzigen Komponenten hohen Anforderungen an Schutz, Funktionalität und Optik genügen müssen.
Das System beginnt meist mit einer automatisierten Zuführung der Mini-Teile, beispielsweise über Vibrationsförderer, präzise Förderbänder oder Roboter, die die Bauteile einzeln oder in kleinen Chargen handhaben. Um eine vollständige und gleichmäßige Beschichtung zu gewährleisten, werden die Teile häufig auf rotierenden Gestellen, Drehtellern oder beweglichen Halterungen fixiert. Diese Bewegung während der Beschichtung sorgt dafür, dass alle Oberflächenbereiche, auch schwer zugängliche Stellen, optimal erreicht werden.
Die eigentliche Pulverbeschichtung erfolgt über elektrostatische Sprühsysteme, die das Pulver fein dosiert aufladen und zielgerichtet auf die Teile auftragen. Moderne Anlagen passen dabei automatisch Parameter wie Pulvermenge, Ladung, Sprühwinkel und Düsenposition an die Geometrie und Größe der Mini-Teile an. Dies minimiert Pulververluste und sorgt für eine homogene Schichtdicke, die sowohl Schutz- als auch ästhetischen Anforderungen gerecht wird.
Nach der Applikation durchlaufen die Mini-Teile einen Einbrennprozess in speziell ausgelegten Durchlaufofen-Systemen. Diese Öfen gewährleisten eine gleichmäßige und schonende Aushärtung der Pulverschicht, wobei die Temperaturprofile so abgestimmt sind, dass sie die empfindlichen Mini-Komponenten nicht beschädigen. Durch die kurze Einbrennzeit und optimale Wärmeverteilung können hohe Taktzeiten und Produktivität erreicht werden.
Ein zentraler Bestandteil der Anlage ist die Pulverrückgewinnung. Überschüssiges Pulver wird abgesaugt, gefiltert und wieder dem Beschichtungskreislauf zugeführt, was Materialkosten spart und die Umweltbelastung minimiert. Zusätzlich sorgen moderne Filtersysteme dafür, dass die Abluft gereinigt wird und keine feinen Pulverpartikel in die Produktionsumgebung gelangen.
Zur Qualitätssicherung sind oft Inline-Messsysteme integriert, die Schichtdicken und Beschichtungsfehler in Echtzeit überwachen. So können Ausschuss minimiert und die Prozesssicherheit erhöht werden. Die Steuerung der Anlage erfolgt über eine zentrale Benutzeroberfläche, die eine einfache Anpassung an unterschiedliche Produkte und Pulverlacktypen ermöglicht. Zudem werden Produktionsdaten erfasst und dokumentiert, um Rückverfolgbarkeit und Qualitätssicherung zu gewährleisten.
Insgesamt bietet eine Pulverbeschichtungsanlage für Mini-Teile eine leistungsfähige, präzise und nachhaltige Lösung zur Oberflächenveredelung kleiner Bauteile. Durch modernste Automatisierung, flexible Prozesssteuerung und umweltbewusste Technologie erfüllt sie die steigenden Anforderungen moderner Industrien an Qualität, Effizienz und Nachhaltigkeit.
Die zunehmende Miniaturisierung von Bauteilen stellt an Pulverbeschichtungsanlagen für Mini-Teile besondere Herausforderungen, die durch fortschrittliche Technologien und Prozessoptimierungen bewältigt werden. Besonders wichtig ist die präzise Steuerung der Pulverapplikation, um eine gleichmäßige Schichtdicke auf kleinsten Oberflächen zu erzielen, ohne dass es zu Überbeschichtungen oder Fehlstellen kommt. Hier kommen oftmals computergesteuerte Mehrfachdüsensysteme zum Einsatz, die in Kombination mit Bewegungsachsen und rotierenden Halterungen eine punktgenaue Beschichtung gewährleisten.
Die automatisierte Handhabung der Mini-Teile ist ebenfalls ein kritischer Faktor für die Prozesssicherheit und Effizienz. Spezielle Greifsysteme, wie Vakuum- oder Elektrostathalterungen, sorgen dafür, dass die kleinen Bauteile sicher fixiert und exakt positioniert werden, ohne die empfindlichen Oberflächen zu beschädigen. Robotiklösungen ermöglichen dabei eine flexible Anpassung an unterschiedliche Bauteilformen und Größen, was den Umrüstaufwand bei Produktwechseln minimiert und die Produktionskapazität erhöht.
Ein weiterer Schwerpunkt liegt auf der Optimierung des Einbrennprozesses. Moderne Durchlaufofenkonzepte nutzen zonale Temperaturregelungen und kontrollierte Luftströmungen, um eine schonende Aushärtung zu gewährleisten. Gerade bei Mini-Teilen mit empfindlichen Werkstoffen ist es entscheidend, thermische Belastungen zu minimieren und gleichzeitig eine vollständige Vernetzung des Pulverlacks sicherzustellen. Die Steuerung dieser Prozesse erfolgt über präzise Sensorik und Echtzeitregelungssysteme, die Temperaturprofile dynamisch anpassen können.
Die Pulverrückgewinnungssysteme sind speziell auf die kleinen Partikelgrößen und Mengen abgestimmt und verfügen über hocheffiziente Filter- und Recyclingmechanismen. Dadurch wird nicht nur Material eingespart, sondern auch die Umweltbelastung durch Staubemissionen reduziert. Geschlossene Kabinen und Abluftreinigungssysteme schützen zudem die Bediener und gewährleisten die Einhaltung von Sicherheits- und Umweltstandards.
Zur Sicherstellung der Qualität werden oft Inline-Inspektionssysteme eingesetzt, die mittels optischer und taktiler Verfahren die Schichtdicke, Oberfläche und Beschichtungsintegrität überwachen. Fehlerhafte Teile können so frühzeitig erkannt und automatisch aussortiert werden, was den Ausschuss reduziert und die Produktqualität erhöht. Die Erfassung und Dokumentation aller relevanten Prozessdaten unterstützt zudem eine lückenlose Rückverfolgbarkeit, die in vielen Branchen eine Voraussetzung für Zulassungen und Qualitätszertifikate ist.
Moderne Pulverbeschichtungsanlagen für Mini-Teile sind zudem modular aufgebaut und ermöglichen eine einfache Erweiterung oder Anpassung an neue Produkte und Technologien. Dies erhöht die Investitionssicherheit und ermöglicht eine flexible Produktion auch bei sich ändernden Marktanforderungen. Die Anlagensteuerung ist häufig mit übergeordneten Produktionsleitsystemen vernetzt, wodurch eine durchgängige Prozesssteuerung und Optimierung im Sinne von Industrie 4.0 realisiert wird.
Abschließend lässt sich sagen, dass Pulverbeschichtungsanlagen für Mini-Teile hochentwickelte Systeme sind, die modernste Automatisierung, präzise Steuerung und umweltbewusste Technologie miteinander verbinden. Sie ermöglichen eine qualitativ hochwertige, effiziente und nachhaltige Beschichtung kleiner Bauteile und sind unverzichtbar für viele zukunftsorientierte Industriezweige.
Zusätzlich gewinnt die Integration von Digitalisierung und datenbasierten Analysen in Pulverbeschichtungsanlagen für Mini-Teile immer mehr an Bedeutung. Durch die Vernetzung mit digitalen Plattformen können Produktionsdaten in Echtzeit erfasst, ausgewertet und visualisiert werden. Dies ermöglicht eine kontinuierliche Prozessoptimierung, indem Schwankungen frühzeitig erkannt und korrigiert werden. Predictive-Maintenance-Module prognostizieren zudem den Wartungsbedarf, was Ausfallzeiten minimiert und die Anlagenverfügbarkeit maximiert.
Die Weiterentwicklung der Pulverlacke selbst trägt ebenfalls zur Verbesserung der Beschichtungsqualität bei. Neue Rezepturen ermöglichen dünnere Schichten bei gleichzeitig höherer Schutzwirkung, was speziell bei Mini-Teilen wichtig ist, um Toleranzen einzuhalten und Funktionalität nicht zu beeinträchtigen. Darüber hinaus bieten Pulverlacke mit speziellen Eigenschaften wie Antikorrosion, elektrischer Leitfähigkeit oder besonderen optischen Effekten zusätzliche Mehrwerte.
Die Automatisierung der Reinigung und Wartung der Anlagen ist ein weiterer Fortschritt. Automatische Spülsysteme für Pulverdüsen und Förderschläuche reduzieren Stillstandzeiten und sorgen für eine konstante Qualität der Pulverapplikation. Wartungsfreundliche Konstruktionen und leicht zugängliche Komponenten erleichtern Inspektionen und Reparaturen, wodurch die Betriebssicherheit weiter gesteigert wird.
Nicht zuletzt spielt die Nachhaltigkeit eine immer größere Rolle. Moderne Anlagen sind so konzipiert, dass sie möglichst wenig Energie verbrauchen und den Materialeinsatz optimieren. Die geschlossenen Systeme minimieren Emissionen, und Recyclingprozesse für Pulver und Abfallstoffe werden stetig verbessert. Dies unterstützt nicht nur die Einhaltung gesetzlicher Vorgaben, sondern entspricht auch dem wachsenden Anspruch von Kunden und Märkten an umweltfreundliche Produktionsverfahren.
Insgesamt bilden Pulverbeschichtungsanlagen für Mini-Teile eine Schlüsseltechnologie, die durch technologische Innovationen, Digitalisierung und Nachhaltigkeit zu immer effizienteren und qualitativ hochwertigeren Beschichtungslösungen führt. Sie sind unverzichtbar für die Herstellung moderner Hightech-Produkte und werden in Zukunft weiter an Bedeutung gewinnen, um den steigenden Anforderungen kleiner, komplexer und funktionaler Bauteile gerecht zu werden.
Automatisches Lackieren von Kleinteilen
Automatisches Lackieren von Kleinteilen ist ein hochentwickeltes Verfahren, das speziell auf die Anforderungen kleiner, oft filigraner Bauteile zugeschnitten ist. Diese Technik ermöglicht eine schnelle, präzise und reproduzierbare Beschichtung, die sowohl optische als auch funktionale Ansprüche erfüllt. Insbesondere in Branchen wie Elektronik, Medizintechnik, Automobilzulieferung oder Konsumgüterherstellung spielt das automatische Lackieren eine zentrale Rolle, um Qualität und Effizienz in der Fertigung sicherzustellen.
Das Herzstück des automatischen Lackierprozesses ist die Integration modernster Roboter- und Steuerungstechnik. Roboterarme mit mehreren Achsen übernehmen die präzise Positionierung und Bewegung der Sprühdüsen oder der Bauteile selbst. Durch diese flexible Beweglichkeit lassen sich komplexe Geometrien gleichmäßig lackieren, ohne manuelle Nacharbeit. Spezielle Düsen- und Applikationstechniken sorgen dafür, dass der Lack in exakter Schichtstärke und ohne Overspray aufgetragen wird, was Material spart und die Umweltbelastung reduziert.
Zur Handhabung der Kleinteile werden automatische Zuführsysteme eingesetzt, die eine kontinuierliche Produktion ermöglichen. Teile werden meist in Werkstückträgern, auf Förderbändern oder durch Vibrationsförderer vereinzelt und zum Lackierbereich transportiert. Dabei sorgen speziell entwickelte Greifsysteme oder Haltevorrichtungen dafür, dass die Kleinteile sicher fixiert sind und während des Lackierens nicht verrutschen. In manchen Anlagen rotieren oder schwenken die Werkstückträger, um alle Oberflächenbereiche optimal zu erreichen.
Ein entscheidender Vorteil der automatischen Lackierung ist die hohe Wiederholgenauigkeit und Prozesssicherheit. Steuerungssysteme speichern für jedes Bauteil individuelle Lackierprogramme, die Parameter wie Sprühwinkel, Lackmenge, Fördergeschwindigkeit und Trocknungszeit exakt definieren. Dies gewährleistet eine konstante Qualität, auch bei wechselnden Losgrößen oder Produktvarianten. Gleichzeitig ermöglichen die Programme schnelle Umrüstungen und reduzieren Stillstandzeiten.
Die Trocknung der Lackschichten erfolgt je nach Lacktyp und Produktanforderung mittels Warmluft-, Infrarot- oder UV-Technologien. Dabei sind die Trocknungssysteme so ausgelegt, dass sie eine schonende und gleichmäßige Aushärtung gewährleisten, ohne die empfindlichen Kleinteile thermisch zu belasten. Integrierte Überwachungssysteme kontrollieren Temperatur, Feuchtigkeit und Taktzeiten, um optimale Bedingungen sicherzustellen.
Zur Sicherung der Beschichtungsqualität sind viele automatische Lackieranlagen mit Inline-Inspektionssystemen ausgestattet. Kameras und Sensoren prüfen die Oberfläche auf Farbton, Glanz, Schichtdicke und Fehlstellen. Abweichungen werden sofort erkannt und können durch Nacharbeit oder Aussortierung korrigiert werden, was Ausschuss reduziert und die Gesamtproduktivität steigert.
Umweltaspekte spielen ebenfalls eine wichtige Rolle. Moderne Anlagen sind mit effizienten Abluft- und Filteranlagen ausgestattet, die Emissionen minimieren und die Gesundheit der Bediener schützen. Der Einsatz von umweltfreundlichen Lacken, wie wasserbasierten oder Pulverlacken, ergänzt die nachhaltige Prozessgestaltung.
Insgesamt bietet das automatische Lackieren von Kleinteilen eine leistungsfähige Kombination aus Präzision, Effizienz und Qualitätssicherung. Es ermöglicht Herstellern, hohe Stückzahlen bei gleichzeitig hoher Produktqualität zu fertigen und flexibel auf Marktanforderungen zu reagieren. Durch kontinuierliche technologische Weiterentwicklungen werden diese Systeme auch künftig eine Schlüsselrolle in der industriellen Oberflächenveredelung spielen.
Die Integration von automatischen Lackiersystemen in moderne Fertigungsprozesse erlaubt nicht nur eine deutliche Steigerung der Produktivität, sondern auch eine Verbesserung der Arbeitsbedingungen. Durch die Automatisierung werden manuelle Lackierarbeiten, die oft gesundheitsschädliche Dämpfe und hohe körperliche Belastung mit sich bringen, reduziert oder komplett ersetzt. Gleichzeitig sorgen geschlossene Kabinensysteme und effiziente Absaugtechnik für eine sichere und saubere Arbeitsumgebung.
Die Flexibilität der Anlagen ermöglicht die Bearbeitung unterschiedlichster Kleinteile in einer Produktionseinheit. Dank modularer Bauweise und programmierbarer Steuerungen können verschiedene Produktvarianten schnell umgerüstet werden, ohne aufwendige mechanische Anpassungen vornehmen zu müssen. Dies ist besonders vorteilhaft bei kleinen Losgrößen oder wechselnden Kundenanforderungen, wie sie in der Elektronik- oder Medizintechnikfertigung häufig vorkommen.
Neben der klassischen Nasslackierung gewinnen auch Pulverbeschichtungsverfahren für Kleinteile zunehmend an Bedeutung. Automatische Pulverbeschichtungsanlagen bieten eine robuste, langlebige Beschichtung mit hohem Schutz gegen Korrosion, Abrieb und Chemikalien. Sie zeichnen sich durch hohe Materialeffizienz und Umweltfreundlichkeit aus, da überschüssiges Pulver rückgewonnen und wiederverwendet wird.
Die Kombination verschiedener Lackiertechniken in einem automatisierten Fertigungssystem ermöglicht die Herstellung von multifunktionalen Oberflächen, die sowohl ästhetischen als auch technischen Anforderungen gerecht werden. So können etwa transparente Schutzschichten mit dekorativen Effekten oder leitfähige Lackschichten in einem Durchgang appliziert werden. Dies erhöht die Wertschöpfung und reduziert Prozessschritte.
Durch die Einbindung von Echtzeit-Datenanalyse und digitaler Prozessüberwachung werden automatische Lackieranlagen zunehmend intelligenter. Sie können anhand von Sensordaten eigenständig Prozessparameter anpassen, um Schwankungen in der Lackzusammensetzung oder Umgebungsbedingungen auszugleichen. Dies führt zu einer konstant hohen Beschichtungsqualität und senkt Ausschussraten.
Zusätzlich ermöglicht die Vernetzung der Lackieranlagen mit übergeordneten Produktionsleitsystemen eine lückenlose Dokumentation und Rückverfolgbarkeit der gefertigten Produkte. Dies ist besonders wichtig für regulierte Industrien wie die Medizintechnik, wo die Einhaltung von Qualitätsstandards und gesetzliche Vorgaben zwingend erforderlich sind.
Nicht zuletzt spielt die Wartungsfreundlichkeit der Anlagen eine große Rolle für die langfristige Betriebssicherheit. Automatische Reinigungsprogramme, leicht zugängliche Komponenten und vorausschauende Wartungskonzepte reduzieren Ausfallzeiten und erhöhen die Gesamtanlageneffektivität.
Insgesamt bietet das automatische Lackieren von Kleinteilen eine innovative, effiziente und nachhaltige Lösung zur Oberflächenveredelung, die den hohen Anforderungen moderner Industrien gerecht wird und gleichzeitig die Produktionskosten senkt. Die kontinuierliche Weiterentwicklung dieser Technologien wird künftig noch präzisere, flexiblere und umweltfreundlichere Prozesse ermöglichen.
Neben der technischen Ausstattung und Prozesssteuerung gewinnt auch die Materialentwicklung im Bereich des automatischen Lackierens von Kleinteilen immer mehr an Bedeutung. Fortschrittliche Lackformulierungen sind speziell auf die Anforderungen kleiner Bauteile abgestimmt und bieten neben einer schnellen Trocknung auch verbesserte Haftung, Flexibilität und Beständigkeit gegenüber mechanischen Belastungen oder chemischen Einflüssen. So können auch dünne Schichten mit hoher Funktionsperformance realisiert werden, ohne dass die Präzision oder die Bauteilmaße beeinträchtigt werden.
Ein weiterer Trend ist die Integration von umweltfreundlichen und nachhaltigen Lackierprozessen. Wasserbasierte Lacke oder Pulverlacke ohne Lösungsmittel reduzieren die Emission von flüchtigen organischen Verbindungen (VOC) erheblich und schonen somit sowohl die Umwelt als auch die Gesundheit der Mitarbeiter. Moderne Anlagen sind deshalb auf solche Materialien ausgelegt und gewährleisten durch präzise Dosierung und Applikation eine effiziente Nutzung der Lacke bei minimalem Verschnitt.
Die Entwicklung intelligenter Sensorik und Bildverarbeitungssysteme ermöglicht eine noch genauere Überwachung des Lackierprozesses. Hochauflösende Kameras erfassen in Echtzeit die Oberflächenqualität, Farbgleichmäßigkeit und Schichtdicke, während KI-basierte Algorithmen Abweichungen automatisch erkennen und Gegenmaßnahmen einleiten. Dies führt zu einer deutlichen Reduktion von Fehlern und Nacharbeiten, was die Gesamtproduktivität und Wirtschaftlichkeit der Fertigung erhöht.
Darüber hinaus erlaubt die zunehmende Digitalisierung die Erstellung digitaler Zwillinge von Lackieranlagen und Prozessen. Diese virtuellen Modelle ermöglichen es, verschiedene Szenarien und Parameter vorab zu simulieren, Optimierungspotenziale zu identifizieren und die Anlagensteuerung auf Basis fundierter Daten kontinuierlich zu verbessern. So können beispielsweise neue Produktvarianten schnell integriert oder Prozessanpassungen mit minimalem Risiko umgesetzt werden.
Die enge Verzahnung von automatischem Lackieren mit weiteren Fertigungsschritten, wie Montage, Prüfen oder Verpacken, trägt zu einem durchgängigen und effizienten Produktionsfluss bei. Automatisierte Handling- und Transportsysteme verbinden die einzelnen Prozessstationen und minimieren manuelle Eingriffe, wodurch Fehlerquellen und Produktionszeiten reduziert werden.
Schließlich gewinnt auch die Schulung und Qualifikation des Bedienpersonals an Bedeutung. Trotz hoher Automatisierung ist ein tiefgehendes Verständnis der Lackiertechnologie, Prozesssteuerung und Wartung erforderlich, um den reibungslosen Betrieb sicherzustellen und bei Störungen schnell eingreifen zu können. Moderne Anlagen unterstützen dies durch benutzerfreundliche Bedienoberflächen, intuitive Menüs und umfangreiche Diagnosefunktionen.
Zusammenfassend stellt das automatische Lackieren von Kleinteilen eine Schlüsseltechnologie dar, die durch technologische Innovationen, nachhaltige Materialien und digitale Prozessintegration eine effiziente, qualitativ hochwertige und zukunftsfähige Oberflächenveredelung ermöglicht. Diese Entwicklung wird auch künftig die Wettbewerbsfähigkeit zahlreicher Branchen maßgeblich beeinflussen.
Kompaktanlage für kleine Lackierteile
Eine Kompaktanlage für kleine Lackierteile ist speziell darauf ausgelegt, auf begrenztem Raum eine vollständige, automatisierte Lackierlösung für kleine und oft filigrane Bauteile zu bieten. Solche Anlagen werden bevorzugt in Branchen eingesetzt, in denen Platzoptimierung, Flexibilität und Effizienz entscheidend sind, beispielsweise in der Elektronikfertigung, Medizintechnik oder Feinmechanik. Trotz ihrer kompakten Bauweise vereinen diese Systeme alle wesentlichen Prozessschritte – von der Teilezuführung über die Lackapplikation bis hin zur Trocknung und Qualitätskontrolle.
Die Teilezuführung erfolgt häufig über präzise Förder- oder Zuführsysteme, die kleine Werkstücke schonend vereinzeln und optimal positionieren. Je nach Anforderung kommen Vakuumgreifer, elektromagnetische Haltesysteme oder mechanische Spannvorrichtungen zum Einsatz, die eine sichere Fixierung während des Lackierprozesses gewährleisten und Beschädigungen vermeiden. Die Anlagen sind so ausgelegt, dass sie unterschiedliche Bauteilgrößen und -formen flexibel verarbeiten können, was einen schnellen Produktwechsel ermöglicht.
Für die Lackapplikation verwenden Kompaktanlagen hochpräzise Sprühdüsen oder elektrostatische Applikationssysteme, die den Lack gleichmäßig und materialeffizient auftragen. Oft sind die Bauteile während des Beschichtens in rotierenden oder schwenkbaren Halterungen montiert, um alle Oberflächenbereiche zu erreichen und eine homogene Schicht aufzubauen. Die Steuerung der Applikationsparameter erfolgt automatisiert und kann an verschiedene Lacktypen und Beschichtungsanforderungen angepasst werden.
Die Trocknung der Lackschichten findet in integrierten, platzsparenden Trocknungsmodulen statt, die je nach Lackart mit Infrarot-, Warmluft- oder UV-Technik arbeiten. Diese Module sind so konzipiert, dass sie eine schnelle und schonende Aushärtung gewährleisten, ohne die empfindlichen Kleinteile thermisch zu belasten. Durch kurze Durchlaufzeiten und effiziente Wärmeführung wird eine hohe Produktivität erzielt.
Zur Sicherstellung der Beschichtungsqualität sind Kompaktanlagen häufig mit integrierten Inspektionssystemen ausgestattet. Optische Sensoren und Kameras kontrollieren die Schichtdicke, die Oberflächenbeschaffenheit und erkennen mögliche Fehler wie Farbabweichungen oder Fehlstellen. Dies ermöglicht eine sofortige Prozesskorrektur und minimiert Ausschuss.
Ein weiterer Vorteil solcher Anlagen ist die einfache Bedienbarkeit und Wartungsfreundlichkeit. Die kompakten Systeme verfügen über intuitive Benutzeroberflächen und automatische Reinigungsprogramme, die den Bedienaufwand reduzieren und die Verfügbarkeit erhöhen. Zudem sind sie häufig modular aufgebaut, sodass Erweiterungen oder Anpassungen an neue Produktionsanforderungen problemlos möglich sind.
Insgesamt bietet eine Kompaktanlage für kleine Lackierteile eine effiziente, flexible und platzsparende Lösung für die Oberflächenveredelung. Sie verbindet modernste Lackiertechnologie mit automatisierter Prozesssteuerung und hoher Qualitätssicherung und ist damit ideal geeignet, die steigenden Anforderungen an Qualität, Produktivität und
Die Kompaktbauweise solcher Anlagen ermöglicht eine platzsparende Integration selbst in Produktionsumgebungen mit begrenztem Raumangebot, was besonders für Unternehmen mit beengten Fertigungslinien von Vorteil ist. Trotz der reduzierten Größe gehen Funktionalität und Leistungsfähigkeit nicht verloren; im Gegenteil, durch den Einsatz moderner Komponenten und intelligenter Steuerungssysteme wird eine hohe Prozessstabilität und Wiederholgenauigkeit gewährleistet. Die modulare Gestaltung erlaubt zudem eine einfache Anpassung an unterschiedliche Produktionsanforderungen und erleichtert zukünftige Erweiterungen oder Umrüstungen.
Ein zentraler Aspekt ist die vollautomatische Steuerung aller Prozessschritte, die eine konstante Produktqualität sicherstellt. Sensoren überwachen kontinuierlich Parameter wie Lackfluss, Sprühdruck, Schichtdicke und Bauteilposition. So können Abweichungen sofort erkannt und die Prozesse in Echtzeit angepasst werden, was Fehler minimiert und Materialeinsatz optimiert. Die Bediener werden durch benutzerfreundliche HMI-Systeme unterstützt, die eine einfache Programmierung und Überwachung ermöglichen, auch ohne tiefgehende technische Vorkenntnisse.
Die automatische Reinigung der Applikationsdüsen und Fördermechanismen ist in Kompaktanlagen integriert, um die Wartungsintervalle zu verlängern und eine gleichbleibend hohe Beschichtungsqualität zu gewährleisten. Die Reinigungszyklen lassen sich flexibel an den Produktionsrhythmus anpassen, wodurch die Anlagenverfügbarkeit maximiert wird. Zusätzlich sind Sicherheitsfunktionen implementiert, die Bediener schützen und den sicheren Betrieb unter allen Bedingungen gewährleisten.
Durch die Verwendung energieeffizienter Trocknungstechnologien, wie Infrarot- oder UV-Systemen, wird nicht nur die Durchlaufzeit verkürzt, sondern auch der Energieverbrauch reduziert. Dies unterstützt die nachhaltige Fertigung und trägt zur Senkung der Betriebskosten bei. Die Trocknungseinheiten sind kompakt gestaltet, um den Gesamtanlagenplatz optimal auszunutzen und gleichzeitig eine gleichmäßige Aushärtung der Lackschichten sicherzustellen.
Die Flexibilität der Kompaktanlagen zeigt sich auch in der Möglichkeit, verschiedene Lackarten zu verarbeiten, von wasserbasierten bis hin zu lösemittelhaltigen oder Pulverlacken. Durch schnelle und einfache Umrüstungen können Hersteller auf wechselnde Marktanforderungen reagieren und verschiedene Produktserien innerhalb kurzer Zeit produzieren. Diese Vielseitigkeit macht die Kompaktanlage zu einem wirtschaftlichen und zukunftssicheren Investitionsgut.
Zusammenfassend bieten Kompaktanlagen für kleine Lackierteile eine hochgradig automatisierte, präzise und flexible Lösung, die es Unternehmen ermöglicht, auf kleinem Raum qualitativ hochwertige Beschichtungen effizient und nachhaltig herzustellen. Sie verbinden technologische Innovation mit anwenderfreundlichem Design und sind damit ein unverzichtbarer Bestandteil moderner Fertigungsprozesse für Kleinteile.
Darüber hinaus wird bei Kompaktanlagen für kleine Lackierteile zunehmend auf die Integration von digitalen Technologien gesetzt, um den gesamten Lackierprozess noch effizienter und transparenter zu gestalten. Vernetzte Systeme ermöglichen eine durchgängige Kommunikation zwischen den einzelnen Prozessstationen sowie die Verbindung mit übergeordneten Produktionsleitsystemen. Dadurch lassen sich Produktionsdaten in Echtzeit erfassen, analysieren und für eine gezielte Prozessoptimierung nutzen. Fehler werden schneller erkannt und behoben, und die Rückverfolgbarkeit der Produkte ist lückenlos gewährleistet.
Die Einbindung von Künstlicher Intelligenz (KI) und Machine Learning bietet zusätzlich die Möglichkeit, Muster in Prozessdaten zu erkennen und auf Basis dieser Erkenntnisse proaktiv Anpassungen vorzunehmen. So kann beispielsweise die Pulvermenge oder der Sprühwinkel automatisch an Schwankungen in der Bauteilgeometrie oder Umgebungsbedingungen angepasst werden, was die Qualität der Lackierung weiter verbessert und Ausschuss reduziert.
Auch die Ergonomie und Sicherheit der Bediener spielen eine wichtige Rolle bei der Entwicklung moderner Kompaktanlagen. Die Anlagen sind so gestaltet, dass sie leicht zugänglich sind, um Wartungsarbeiten und Reinigung schnell und sicher durchzuführen. Gleichzeitig sorgen geschlossene Kabinen und effektive Absaugsysteme dafür, dass schädliche Dämpfe und Partikel nicht in die Arbeitsumgebung gelangen, was den Gesundheitsschutz der Mitarbeiter sicherstellt.
Ein weiteres Merkmal moderner Kompaktanlagen ist ihre Energieeffizienz. Durch den Einsatz innovativer Technologien und intelligenter Steuerungen wird der Energieverbrauch in allen Prozessschritten minimiert. Beispielsweise ermöglichen präzise geregelte Trocknungssysteme eine zielgerichtete Wärmezufuhr nur dort, wo sie benötigt wird, was unnötige Energieverluste vermeidet. Auch die Nutzung von regenerativen Energien oder Wärmerückgewinnungssystemen wird zunehmend umgesetzt, um den ökologischen Fußabdruck der Lackierprozesse zu reduzieren.
Schließlich bieten Kompaktanlagen oft die Möglichkeit, zusätzliche Prozessschritte wie Vorbehandlung, Entfettung oder Beschichtungsinspektion in das System zu integrieren. Dies schafft kurze und optimierte Prozesswege, erhöht die Effizienz und verringert die Fehleranfälligkeit durch manuelle Eingriffe. Die Anlagen können somit als ganzheitliche Lösung für die Oberflächenveredelung kleiner Teile fungieren.
Insgesamt zeichnen sich Kompaktanlagen für kleine Lackierteile durch ihre Kombination aus platzsparendem Design, hoher Prozessautomation, digitaler Vernetzung und Nachhaltigkeit aus. Sie ermöglichen es Unternehmen, qualitativ hochwertige Beschichtungen wirtschaftlich und flexibel herzustellen und sind damit ein zentraler Baustein moderner, zukunftsfähiger Produktionsprozesse.
EMS Pulverbeschichtungsanlagen

Unsere Pulverbeschichtungsanlage wird in Übereinstimmung mit den globalen fortschrittlichen Standards hergestellt und wurden mit vollem Vertrauen sowohl auf dem heimischen als auch auf dem weltweiten Markt bevorzugt.
Unsere Kapazität ist täglich gewachsen, wobei die Kundenzufriedenheit zusammen mit unserem gemeinsamen Vertriebs- und Servicenetz an erster Stelle steht.
Unser Unternehmen ist ein führendes türkisches Unternehmen, das sich auf die Herstellung von „Elektrostatischen Pulverbeschichtungsanlagen und kompletten Lackiersystemen“ mit 20 Jahren Wissen und praktischer Erfahrung spezialisiert hat.
Alle unsere Maschinen sind CE-gekennzeichnet, garantiert und können von potenziellen Kunden persönlich besichtigt werden. Es gibt auch Bilder und Videos auf dieser Seite, die die verwendeten Maschinen zeigen.
Wir entwerfen, fertigen und montieren Pulverbeschichtungsöfen, automatische und manuelle Kabinen, automatische und manuelle Pulverbeschichtungsanlagen, Pistolen, automatische und Stangentransfer-Pulverbeschichtungslinien, Pulverbeschichtungsfilter und Ersatzteile für Pulverbeschichtungspistolen