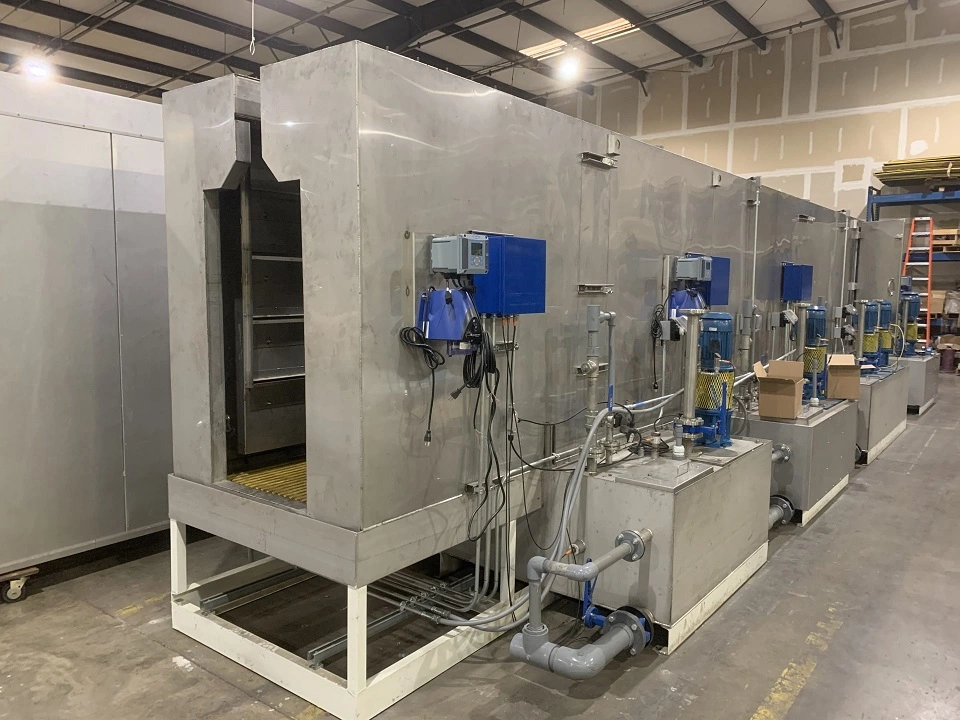
Vorbehandlung von Oberflächen: Die Pulverbeschichtungsmaschine ist eine essenzielle Komponente jeder modernen Beschichtungsanlage und bildet das Herzstück im Pulverbeschichtungsprozess. Sie ermöglicht das Auftragen von Pulverlack auf verschiedene Werkstücke und spielt eine entscheidende Rolle bei der Erzielung einer gleichmäßigen, robusten und ästhetisch ansprechenden Oberflächenbeschichtung. In den letzten Jahren hat die Pulverbeschichtung aufgrund ihrer Umweltfreundlichkeit und Effizienz erheblich an Bedeutung gewonnen, und die Maschinen, die diesen Prozess unterstützen, sind technisch sehr anspruchsvoll und hochspezialisiert.
Funktionsweise einer Pulverbeschichtungsmaschine
Pulverbeschichtungsmaschinen arbeiten mit elektrostatischer Aufladung, um das Pulver auf die zu beschichtenden Werkstücke aufzubringen. Das Pulver besteht typischerweise aus thermoplastischen oder duroplastischen Kunststoffen, die speziell für Beschichtungszwecke formuliert sind. Der eigentliche Auftrag erfolgt durch Sprühen des Pulvers, das zuvor elektrostatisch aufgeladen wurde. Dabei wird das Pulver entweder manuell oder automatisch aufgetragen. Die elektrostatische Ladung sorgt dafür, dass das Pulver an der Oberfläche des Werkstücks haftet.
Eine Pulverbeschichtungsmaschine kann verschiedene Sprühpistolen umfassen, die manuell oder robotergesteuert sind. Automatisierte Systeme sind in der Lage, die Beschichtungen mit einer sehr hohen Präzision aufzutragen, was besonders in der Massenproduktion von großem Vorteil ist. Ein gleichmäßiger Auftrag ist essenziell, um eine perfekte Endbeschichtung zu erreichen, da ungleichmäßige Schichten zu unerwünschten Defekten wie Orangenhaut-Effekten, Blasenbildung oder unzureichender Deckkraft führen können.
Arten von Pulverbeschichtungsmaschinen
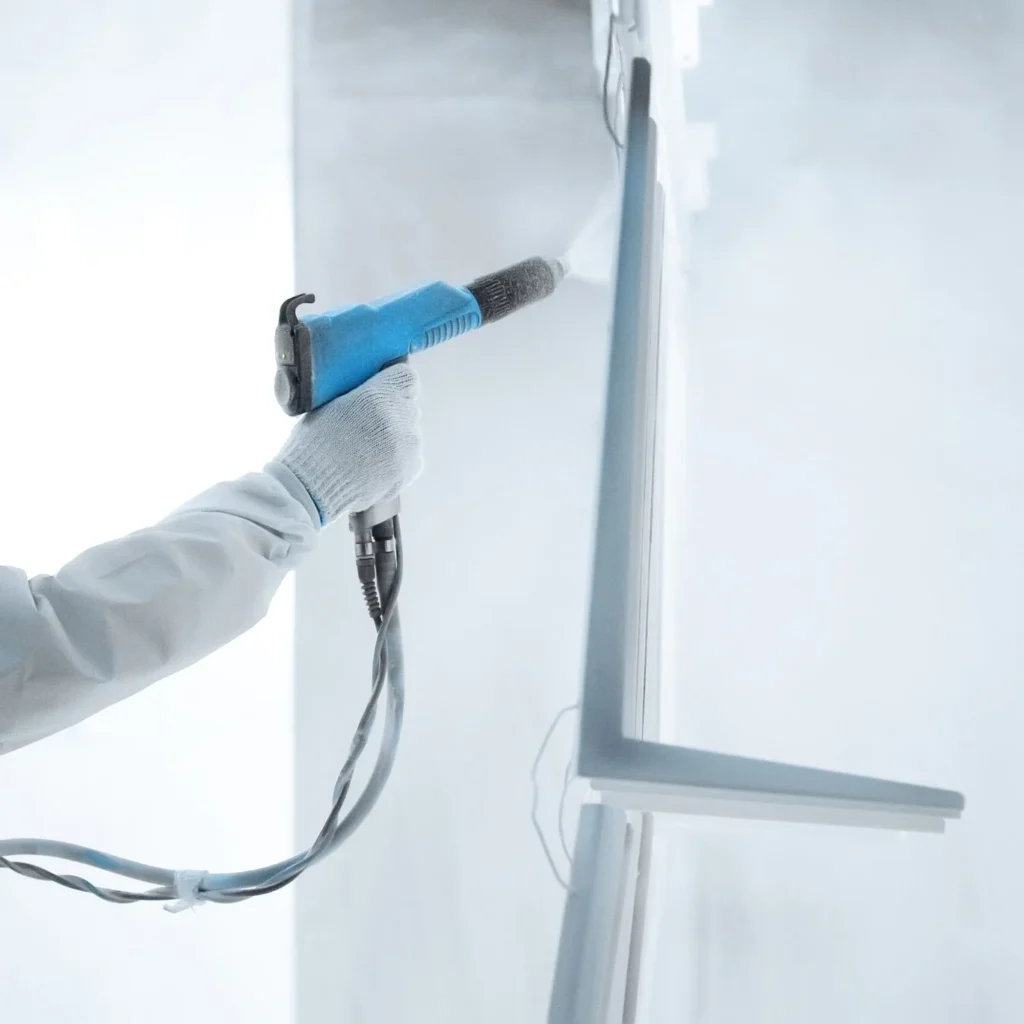
Pulverbeschichtungsmaschinen gibt es in verschiedenen Ausführungen, die je nach Anwendung und Produktionsanforderung variieren. Die gängigsten Typen sind:
- Manuelle Pulverbeschichtungsmaschinen: Diese Maschinen werden in kleineren Werkstätten oder bei spezialisierten Projekten verwendet. Sie erfordern den Einsatz eines Bedieners, der das Pulver manuell aufträgt. Diese Art von Maschine eignet sich besonders gut für kleinere Produktionen oder bei komplexen Formen, die spezielle Aufmerksamkeit und Präzision erfordern.
- Automatisierte Pulverbeschichtungsmaschinen: In industriellen Anwendungen und bei hohen Produktionsvolumen sind automatisierte Systeme unerlässlich. Diese Maschinen verwenden Roboter, die das Pulver gleichmäßig und effizient auftragen. Automatisierte Pulverbeschichtungsmaschinen bieten eine hohe Wiederholgenauigkeit und ermöglichen es, große Mengen an Werkstücken in kurzer Zeit zu beschichten.
- Hochvolumensysteme: Für sehr große Produktionsanlagen gibt es spezielle Hochvolumensysteme, die darauf ausgelegt sind, tausende Teile pro Stunde zu beschichten. Diese Maschinen sind oft Teil einer größeren Produktionslinie, die auch Fördertechnik, Öfen und Vorbehandlungssysteme umfasst.
Vorteile von Pulverbeschichtungsmaschinen

Pulverbeschichtungsmaschinen bieten eine Vielzahl von Vorteilen gegenüber traditionellen Lackiermethoden wie Nasslackierungen:
- Umweltfreundlichkeit: Da bei der Pulverbeschichtung keine Lösungsmittel verwendet werden, entstehen keine schädlichen VOC-Emissionen (Volatile Organic Compounds). Dies macht den Prozess umweltfreundlicher und trägt zur Reduzierung von Umweltbelastungen bei.
- Effizienz: Pulverbeschichtungsmaschinen ermöglichen es, nahezu 100 % des aufgetragenen Pulvers zu verwenden, da überschüssiges Pulver gesammelt und wiederverwendet werden kann. Dies reduziert den Materialverlust erheblich und spart Kosten.
- Robustheit der Beschichtung: Pulverbeschichtungen sind bekannt für ihre Langlebigkeit und hohe Widerstandsfähigkeit gegenüber mechanischen Einflüssen wie Kratzern, Stößen und Abnutzung. Sie bieten zudem eine hohe Korrosionsbeständigkeit, was sie ideal für den Einsatz in Außenanwendungen oder in aggressiven Umgebungen macht.
- Schnelligkeit des Prozesses: Im Vergleich zu Nasslackierungen, bei denen das Trocknen der Farbe viel Zeit in Anspruch nehmen kann, ist die Pulverbeschichtung wesentlich schneller. Sobald das Pulver aufgetragen ist, wird das Werkstück in den Ofen gebracht, wo das Pulver in kurzer Zeit aushärtet.
Wichtige Komponenten einer Pulverbeschichtungsmaschine
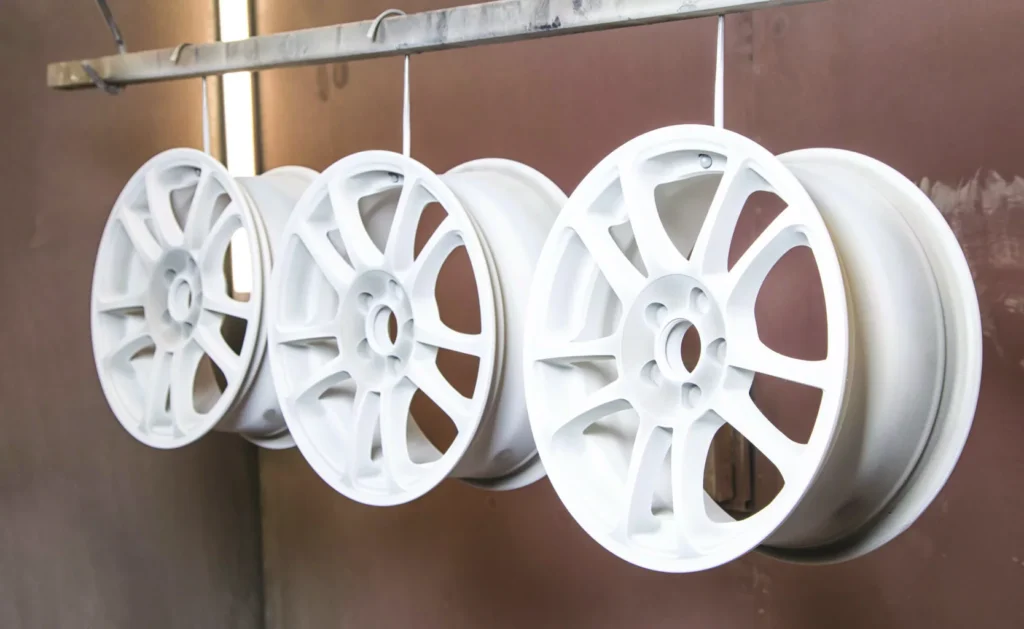
Eine Pulverbeschichtungsmaschine besteht aus mehreren Schlüsselkomponenten, die zusammenarbeiten, um eine effiziente Beschichtung zu ermöglichen:
- Sprühpistole: Die Sprühpistole ist das zentrale Element der Maschine. Sie dient dazu, das Pulver auf das Werkstück zu sprühen und dabei eine gleichmäßige Verteilung sicherzustellen. Moderne Sprühpistolen verfügen über präzise Steuerungselemente, um den Auftrag je nach Anforderungen der Beschichtung optimal zu regulieren.
- Pulverförderungssystem: Das Pulverförderungssystem transportiert das Pulver von seinem Vorratsbehälter zur Sprühpistole. Es ist darauf ausgelegt, das Pulver mit minimalem Verlust und maximaler Effizienz zuzuführen.
- Steuerungseinheit: Die Steuerungseinheit der Pulverbeschichtungsmaschine ist dafür verantwortlich, alle Parameter des Beschichtungsprozesses zu regulieren, einschließlich der Pulvermenge, der Sprühintensität und der elektrostatischen Aufladung. Moderne Steuerungseinheiten sind oft mit Computersteuerung ausgestattet, die eine Automatisierung und Optimierung des gesamten Prozesses ermöglichen.
- Recycling- und Filtersystem: Da überschüssiges Pulver während des Beschichtungsprozesses nicht verloren gehen soll, ist ein Recycling- und Filtersystem eine wichtige Komponente. Dieses System sammelt das überschüssige Pulver, filtert es und führt es dem Beschichtungsprozess wieder zu.
Innovations- und Technologietrends
Die Pulverbeschichtungstechnologie hat sich in den letzten Jahren kontinuierlich weiterentwickelt, und es gibt mehrere Innovationen, die den Prozess noch effizienter und umweltfreundlicher machen. Eine dieser Innovationen ist die Einführung von automatischen Farbumschaltsystemen, die es ermöglichen, die Farbe des Pulvers in kürzester Zeit zu wechseln, ohne dass umfangreiche Reinigungsprozesse erforderlich sind. Dies spart Zeit und Kosten, insbesondere in Produktionsumgebungen, in denen häufig verschiedene Farben verwendet werden.
Eine weitere Innovation ist die Entwicklung von intelligenten Steuerungssystemen, die mithilfe von Sensoren und Datenanalyse den Beschichtungsprozess in Echtzeit überwachen und automatisch Anpassungen vornehmen können. Diese Systeme verbessern die Qualität und Effizienz der Beschichtung und tragen dazu bei, den Energieverbrauch zu senken.
Wartung und Pflege
Wie bei jeder industriellen Maschine ist die regelmäßige Wartung einer Pulverbeschichtungsmaschine entscheidend, um eine lange Lebensdauer und eine konstant hohe Leistung zu gewährleisten. Zu den wichtigsten Wartungsaufgaben gehören die Reinigung der Sprühpistolen, die Überprüfung der elektrischen Komponenten und das Überprüfen der Filter und Recycling-Systeme. Eine regelmäßige Inspektion und Kalibrierung der Maschine kann ebenfalls dazu beitragen, Probleme frühzeitig zu erkennen und kostspielige Ausfälle zu vermeiden.
Pulverlackierung Anlage
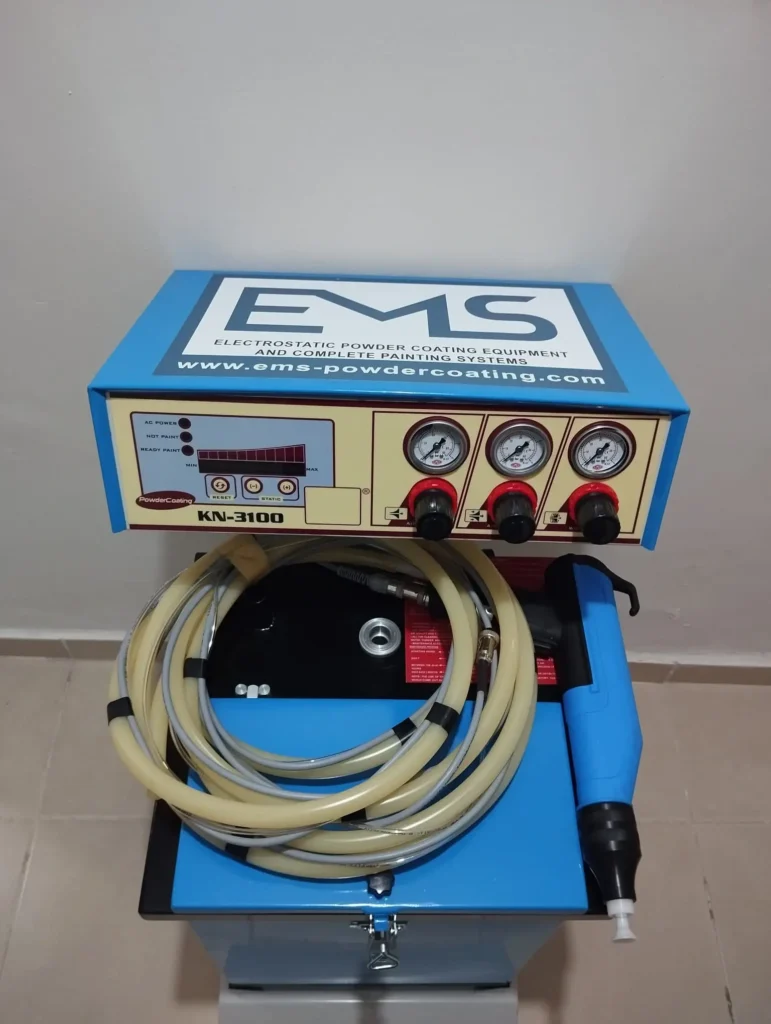
Eine Pulverlackierung Anlage ist ein komplexes, hochspezialisiertes System, das den gesamten Prozess der Pulverbeschichtung von Metallteilen und anderen Oberflächen umfasst. Solche Anlagen sind für industrielle Anwendungen konzipiert und bieten eine integrierte Lösung, die von der Oberflächenvorbereitung über das Auftragen des Pulverlacks bis hin zur Aushärtung reicht. In vielen modernen Fertigungsumgebungen sind Pulverlackieranlagen unverzichtbar geworden, da sie Effizienz, Qualität und Umweltverträglichkeit vereinen.
Aufbau und Funktionsweise einer Pulverlackierung Anlage
Eine typische Pulverlackierung Anlage besteht aus mehreren wichtigen Komponenten, die in einem harmonischen Zusammenspiel den Beschichtungsprozess durchführen. Die Hauptbestandteile einer solchen Anlage sind:
- Vorbehandlungsstation: Bevor das eigentliche Pulverbeschichten beginnen kann, müssen die Oberflächen der Werkstücke gründlich gereinigt und vorbereitet werden. Diese Phase ist entscheidend, um eine optimale Haftung des Pulvers zu gewährleisten. Die Vorbehandlung kann durch verschiedene chemische oder mechanische Prozesse erfolgen, wie Entfettung, Phosphatierung oder Sandstrahlen. Die Wahl der Vorbehandlung hängt von der Art des zu beschichtenden Materials und den Anforderungen an die Endbeschichtung ab.
- Pulverbeschichtungskabine: Dies ist der Ort, an dem das Pulver auf die vorbereiteten Werkstücke aufgetragen wird. In dieser Kabine werden die Teile entweder manuell oder durch automatische Sprühsysteme beschichtet. Die Kabine ist so konstruiert, dass das überschüssige Pulver, das nicht am Werkstück haften bleibt, gesammelt und recycelt werden kann. Das trägt nicht nur zur Reduzierung von Materialverlust bei, sondern auch zur Steigerung der Effizienz der gesamten Anlage.
- Fördersystem: Ein Fördersystem transportiert die Werkstücke von einer Station zur nächsten. Die Transportgeschwindigkeit und die Flexibilität des Fördersystems sind entscheidend für die Effizienz der Anlage. Verschiedene Arten von Fördersystemen können eingesetzt werden, darunter Schienensysteme, Power-and-Free-Systeme oder kontinuierliche Förderbänder. Diese Systeme sorgen dafür, dass die Teile gleichmäßig durch die verschiedenen Stationen bewegt werden.
- Aushärtungsofen: Nach dem Auftragen des Pulvers werden die Werkstücke in den Aushärtungsofen transportiert. In diesem Ofen wird das Pulver bei Temperaturen von etwa 180 bis 200 Grad Celsius geschmolzen und vernetzt, wodurch eine harte, widerstandsfähige und langlebige Beschichtung entsteht. Die Art des Ofens kann variieren – von Konvektionsöfen bis hin zu Infrarotöfen – abhängig von den spezifischen Anforderungen der Anlage und der zu beschichtenden Materialien.
- Kühlsystem: Nach dem Aushärten der Beschichtung müssen die Werkstücke langsam abgekühlt werden, bevor sie weiterverarbeitet oder verpackt werden können. Ein kontrolliertes Kühlsystem stellt sicher, dass die Beschichtung gleichmäßig aushärtet und keine thermischen Spannungen oder Verformungen im Werkstück auftreten.
Vorteile einer Pulverlackierung Anlage
Pulverlackierung Anlagen bieten eine Vielzahl von Vorteilen, die sie zur bevorzugten Wahl für industrielle Beschichtungsprozesse machen. Hier sind einige der wichtigsten:
- Umweltfreundlichkeit: Einer der herausragendsten Vorteile einer Pulverlackierung Anlage ist die Tatsache, dass im gesamten Prozess keine flüchtigen organischen Verbindungen (VOCs) freigesetzt werden. Im Gegensatz zu traditionellen Nasslacksystemen, bei denen Lösungsmittel verwendet werden, ist die Pulverbeschichtung ein lösemittelfreies Verfahren. Dies reduziert nicht nur die Umweltbelastung, sondern auch die Notwendigkeit von teuren Abgasreinigungssystemen.
- Hohe Effizienz: Moderne Pulverlackierung Anlagen sind darauf ausgelegt, den Materialverlust zu minimieren. Das überschüssige Pulver, das beim Auftragen nicht auf den Werkstücken haftet, wird in der Kabine gesammelt, gefiltert und für zukünftige Anwendungen recycelt. Das reduziert nicht nur den Abfall, sondern auch die Kosten für das Pulvermateriel erheblich.
- Langlebigkeit der Beschichtung: Pulverbeschichtungen sind bekannt für ihre außergewöhnliche Haltbarkeit. Sie bieten einen hervorragenden Schutz vor Korrosion, chemischen Einflüssen, UV-Strahlung und mechanischer Abnutzung. Diese Eigenschaften machen die Pulverbeschichtung ideal für Anwendungen, bei denen eine langfristige Beständigkeit erforderlich ist, z. B. bei Autoteilen, Maschinen oder Baukomponenten.
- Vielseitigkeit: Pulverlackieranlagen können für eine breite Palette von Materialien und Oberflächen eingesetzt werden, darunter Metall, Aluminium, Glas, Keramik und sogar einige Kunststoffe. Diese Vielseitigkeit macht sie zu einer attraktiven Lösung für Unternehmen, die eine flexible und kosteneffiziente Beschichtungsmethode suchen.
- Automatisierungspotenzial: Viele moderne Pulverlackieranlagen sind hochgradig automatisiert und können durch den Einsatz von Robotern und intelligenten Steuerungssystemen optimiert werden. Dies erhöht die Produktionsgeschwindigkeit und gewährleistet eine gleichbleibend hohe Qualität. Darüber hinaus können automatisierte Systeme menschliche Fehler minimieren und die Effizienz des gesamten Produktionsprozesses verbessern.
Herausforderungen und Überlegungen bei der Implementierung
Trotz der zahlreichen Vorteile gibt es bei der Implementierung einer Pulverlackierung Anlage auch einige Herausforderungen, die sorgfältig berücksichtigt werden sollten:
- Anschaffungskosten: Der Aufbau einer vollständigen Pulverlackierung Anlage erfordert eine beträchtliche Anfangsinvestition. Die Kosten variieren je nach Größe der Anlage, dem Automatisierungsgrad und den speziellen Anforderungen der Produktion. Unternehmen müssen sicherstellen, dass sie über die finanziellen Ressourcen verfügen, um eine solche Anlage zu installieren und zu betreiben.
- Wartung und Instandhaltung: Wie bei jeder industriellen Anlage erfordert auch eine Pulverlackierung Anlage regelmäßige Wartung, um reibungslos zu funktionieren. Die Filter müssen regelmäßig gereinigt, die Sprühpistolen kalibriert und die Fördersysteme überprüft werden. Eine mangelnde Wartung kann zu Produktionsausfällen und Qualitätsproblemen führen.
- Platzbedarf: Eine vollständige Pulverlackierung Anlage benötigt in der Regel viel Platz, insbesondere wenn große Werkstücke beschichtet werden sollen. Unternehmen müssen sicherstellen, dass sie über ausreichende Räumlichkeiten verfügen, um alle Komponenten der Anlage unterzubringen und den Produktionsprozess effizient zu gestalten.
- Schulung der Mitarbeiter: Auch wenn viele Pulverlackieranlagen automatisiert sind, ist dennoch qualifiziertes Personal erforderlich, um die Anlagen zu überwachen, zu warten und im Falle von Störungen einzugreifen. Unternehmen müssen sicherstellen, dass ihre Mitarbeiter entsprechend geschult sind, um die Anlagen effizient und sicher zu bedienen.
Trends und Zukunft der Pulverlackierung Anlagen
In den letzten Jahren haben sich Pulverlackieranlagen kontinuierlich weiterentwickelt, um den steigenden Anforderungen der Industrie gerecht zu werden. Ein bemerkenswerter Trend ist die zunehmende Integration von digitalen Steuerungssystemen und Industrie 4.0-Technologien. Durch den Einsatz von Datenanalyse, Sensorik und vernetzten Systemen können Anlagen in Echtzeit überwacht und optimiert werden. Dies ermöglicht nicht nur eine höhere Effizienz, sondern auch eine präzisere Kontrolle über den gesamten Beschichtungsprozess.
Ein weiterer Trend ist die Entwicklung von energieeffizienten Anlagen. Da der Aushärtungsofen einen Großteil der Energie in der Pulverbeschichtung verbraucht, arbeiten viele Hersteller daran, energieeffizientere Lösungen zu entwickeln, wie z. B. Infrarotöfen oder hybride Heizsysteme, die den Energieverbrauch erheblich reduzieren können.
Pulverbeschichten Ofen
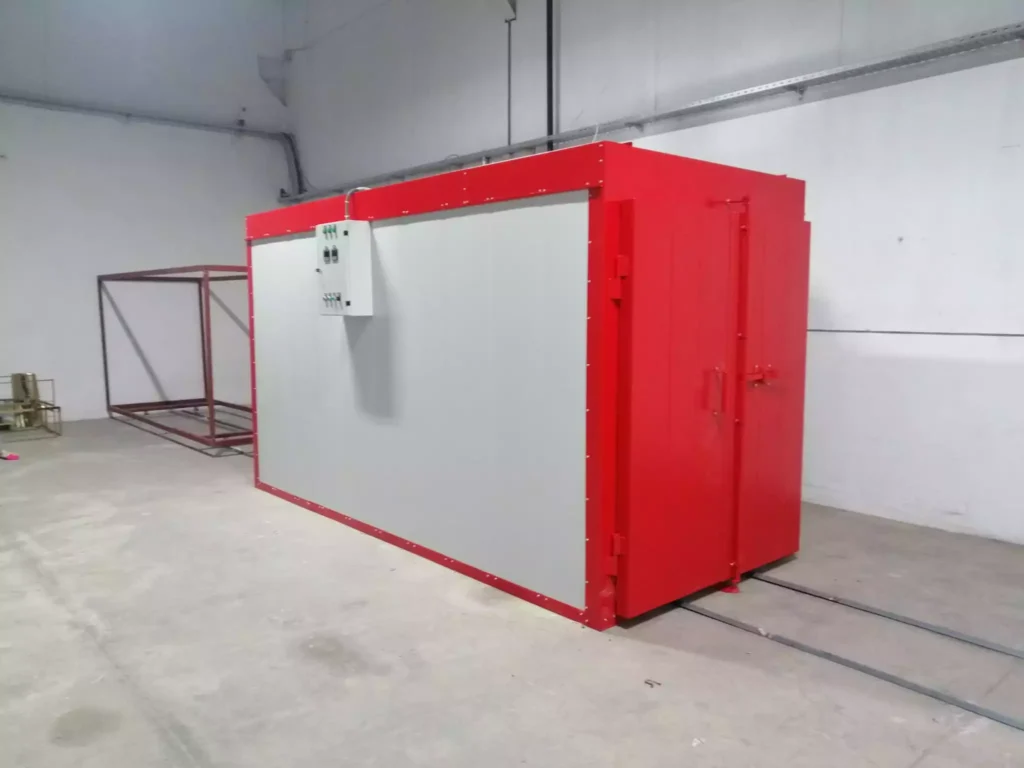
Der Pulverbeschichten Ofen ist eine der zentralen Komponenten in der Pulverbeschichtungstechnologie. Er spielt eine entscheidende Rolle bei der finalen Aushärtung der Beschichtung und beeinflusst maßgeblich die Qualität des Endprodukts. In diesem speziellen Ofen wird das zuvor elektrostatisch aufgetragene Pulver erhitzt, sodass es zu einer festen, robusten und gleichmäßigen Schicht auf dem Werkstück aushärtet. Der Ofenprozess ist dabei wesentlich für die thermische Vernetzung des Pulvers und bestimmt die Eigenschaften der endgültigen Oberfläche wie Härte, Beständigkeit und Glanzgrad.
Aufbau und Funktionsweise eines Pulverbeschichten Ofens
Ein Pulverbeschichten Ofen ist in der Regel ein großräumiger Wärmekammerofen, der je nach Art des Materials und der Größe der Werkstücke in unterschiedlichen Größen und Ausführungen erhältlich ist. Das grundlegende Prinzip besteht darin, das Werkstück auf eine Temperatur von etwa 180 bis 200 Grad Celsius zu erhitzen, sodass das Pulver auf der Oberfläche schmilzt und sich zu einem harten Film verbindet. Hierbei wird das Pulver sowohl geschmolzen als auch chemisch vernetzt, wodurch es seine endgültigen physikalischen und chemischen Eigenschaften erhält.
Ein typischer Pulverbeschichten Ofen besteht aus den folgenden wesentlichen Komponenten:
- Heizsystem: Das Herzstück des Ofens ist das Heizsystem, das die erforderliche Temperatur für den Aushärtungsprozess bereitstellt. Verschiedene Heiztechnologien können hier zum Einsatz kommen, wie zum Beispiel Konvektionsheizung, Infrarotheizung oder eine Kombination aus beiden. Jedes dieser Systeme hat seine eigenen Vor- und Nachteile, je nachdem, welche Art von Werkstücken und Beschichtungsmaterialien verarbeitet werden.
- Luftzirkulationssystem: Eine gleichmäßige Wärmeverteilung im Ofen ist entscheidend für die Qualität des Endprodukts. Ein gutes Luftzirkulationssystem stellt sicher, dass die heiße Luft gleichmäßig im gesamten Ofen verteilt wird und alle Werkstücke unabhängig von ihrer Position im Ofen gleichmäßig erwärmt werden. Dies verhindert, dass es zu ungleichmäßigen Aushärtungen oder Beschichtungsfehlern kommt.
- Temperaturkontrollsystem: Die Temperatur im Ofen muss genau überwacht und geregelt werden, um sicherzustellen, dass das Pulver bei der optimalen Temperatur schmilzt und sich vollständig vernetzt. Moderne Pulverbeschichten Öfen verfügen über digitale Temperaturkontrollsysteme, die in der Lage sind, die Ofentemperatur präzise zu steuern und auf Schwankungen zu reagieren. Dies ist besonders wichtig bei komplexen Werkstücken oder wenn hohe Qualitätsanforderungen an die Beschichtung gestellt werden.
- Fördersystem: Viele Pulverbeschichten Öfen sind Teil eines automatisierten Fördersystems, das die Werkstücke in den Ofen transportiert, dort gleichmäßig durch den Aushärtungsbereich bewegt und anschließend zur nächsten Station weiterleitet. Diese Art von kontinuierlichem Ofensystem wird häufig in großen Produktionslinien verwendet, da es eine schnelle und effiziente Bearbeitung großer Mengen an Werkstücken ermöglicht.
- Abkühlungsbereich: Nach dem Aushärten im Ofen müssen die Werkstücke allmählich abkühlen, um thermische Spannungen und Verformungen zu vermeiden. In einigen Öfen gibt es spezielle Abkühlungszonen oder -systeme, die diesen Prozess kontrolliert durchführen, sodass die Teile sicher und stabil weiterverarbeitet werden können.
Arten von Pulverbeschichten Öfen
Es gibt verschiedene Typen von Pulverbeschichten Öfen, die je nach Anforderung und Produktionsvolumen eingesetzt werden. Die gängigsten Ofentypen sind:
- Konvektionsöfen: Dies ist die am häufigsten verwendete Art von Pulverbeschichten Ofen. Konvektionsöfen nutzen heiße Luft, die durch Ventilatoren oder natürliche Konvektion im Ofen verteilt wird, um die Werkstücke gleichmäßig zu erhitzen. Sie sind einfach zu bedienen und eignen sich für eine breite Palette von Werkstücken, allerdings benötigen sie oft etwas mehr Zeit zum Aufheizen und Aushärten als andere Ofentypen.
- Infrarotöfen: Infrarotöfen nutzen Infrarotstrahlung, um die Werkstücke direkt zu erwärmen. Sie bieten eine sehr schnelle Aufheizzeit, da die Strahlung das Material direkt erhitzt, ohne die Luft im Ofen zu erwärmen. Infrarotöfen sind besonders vorteilhaft bei der Beschichtung von dünnen Materialien oder bei Anwendungen, bei denen schnelle Aushärtungszeiten erforderlich sind.
- Hybridöfen: Hybridöfen kombinieren die Vorteile von Konvektions- und Infrarotheizsystemen. Sie bieten sowohl die schnelle Erwärmung der Infrarottechnologie als auch die gleichmäßige Wärmeverteilung eines Konvektionssystems. Diese Art von Ofen ist besonders für komplexe Werkstücke geeignet, die unterschiedliche Temperaturen oder Aushärtungsbedingungen erfordern.
- Durchlauföfen: Diese Öfen sind speziell für den Einsatz in automatisierten Produktionslinien konzipiert. Werkstücke werden kontinuierlich auf einem Fördersystem durch den Ofen transportiert, was einen ununterbrochenen und effizienten Aushärtungsprozess ermöglicht. Durchlauföfen sind ideal für große Produktionen, bei denen eine hohe Stückzahl in kurzer Zeit bearbeitet werden muss.
Vorteile eines Pulverbeschichten Ofens
Ein gut konzipierter Pulverbeschichten Ofen bietet zahlreiche Vorteile, die ihn zu einem unverzichtbaren Bestandteil moderner Beschichtungsprozesse machen:
- Hervorragende Qualität der Beschichtung: Ein präzise gesteuerter Ofenprozess sorgt dafür, dass das Pulver gleichmäßig schmilzt und sich zu einer harten, widerstandsfähigen Schicht vernetzt. Dies führt zu einer hochwertigen, gleichmäßigen Beschichtung ohne Mängel wie Blasenbildung oder unzureichende Deckung.
- Schnelligkeit und Effizienz: Dank moderner Heizsysteme und effizienter Luftzirkulation können Pulverbeschichten Öfen Werkstücke schnell und gleichmäßig aushärten. Dies führt zu kürzeren Durchlaufzeiten und einer höheren Produktivität.
- Energieeffizienz: Fortschrittliche Ofentechnologien, wie Infrarotstrahlung oder hybride Heizsysteme, tragen dazu bei, den Energieverbrauch zu minimieren, da sie eine schnellere und gezieltere Erwärmung ermöglichen. Dies ist besonders wichtig in großen Produktionsumgebungen, in denen Energieeinsparungen zu erheblichen Kostensenkungen führen können.
- Vielseitigkeit: Pulverbeschichten Öfen sind in der Lage, eine Vielzahl von Werkstoffen zu verarbeiten, von Metallen über Kunststoffe bis hin zu speziellen Verbundwerkstoffen. Dies macht sie zu einer vielseitigen Lösung für unterschiedlichste Industrien, von der Automobilindustrie über die Möbelherstellung bis hin zu elektrischen Geräten.
Herausforderungen und Überlegungen
Obwohl Pulverbeschichten Öfen viele Vorteile bieten, gibt es einige Herausforderungen, die bei der Auswahl und Nutzung dieser Geräte berücksichtigt werden müssen:
- Platzbedarf: Ein Pulverbeschichten Ofen, insbesondere ein Durchlaufofen, nimmt eine beträchtliche Menge an Platz in einer Produktionsanlage ein. Unternehmen müssen sicherstellen, dass sie über ausreichend Raum für die Installation und den Betrieb des Ofens verfügen.
- Wartung: Regelmäßige Wartung ist entscheidend, um die optimale Leistung des Ofens zu gewährleisten. Dazu gehört die Reinigung von Filtern, das Überprüfen der Temperaturregelungssysteme und das Testen der Heizelemente. Eine vernachlässigte Wartung kann zu ineffizientem Betrieb oder sogar zu Schäden an den Werkstücken führen.
- Investitionskosten: Die Anschaffung eines Pulverbeschichten Ofens, insbesondere eines automatisierten oder hybriden Systems, kann mit erheblichen Kosten verbunden sein. Unternehmen sollten sicherstellen, dass die Investition in den Ofen im Verhältnis zu den Produktionsanforderungen und den langfristigen Kosteneinsparungen steht.
Zukunft der Pulverbeschichten Öfen
Mit dem wachsenden Fokus auf Energieeffizienz und Automatisierung werden Pulverbeschichten Öfen immer weiter technologisch verbessert. Zukünftige Entwicklungen könnten eine noch bessere Integration von Industrie 4.0-Technologien beinhalten, bei denen Ofensysteme in Echtzeit überwacht und angepasst werden können, um den Energieverbrauch zu minimieren und die Qualität der Beschichtung weiter zu optimieren.
Brennofen Pulverbeschichtung
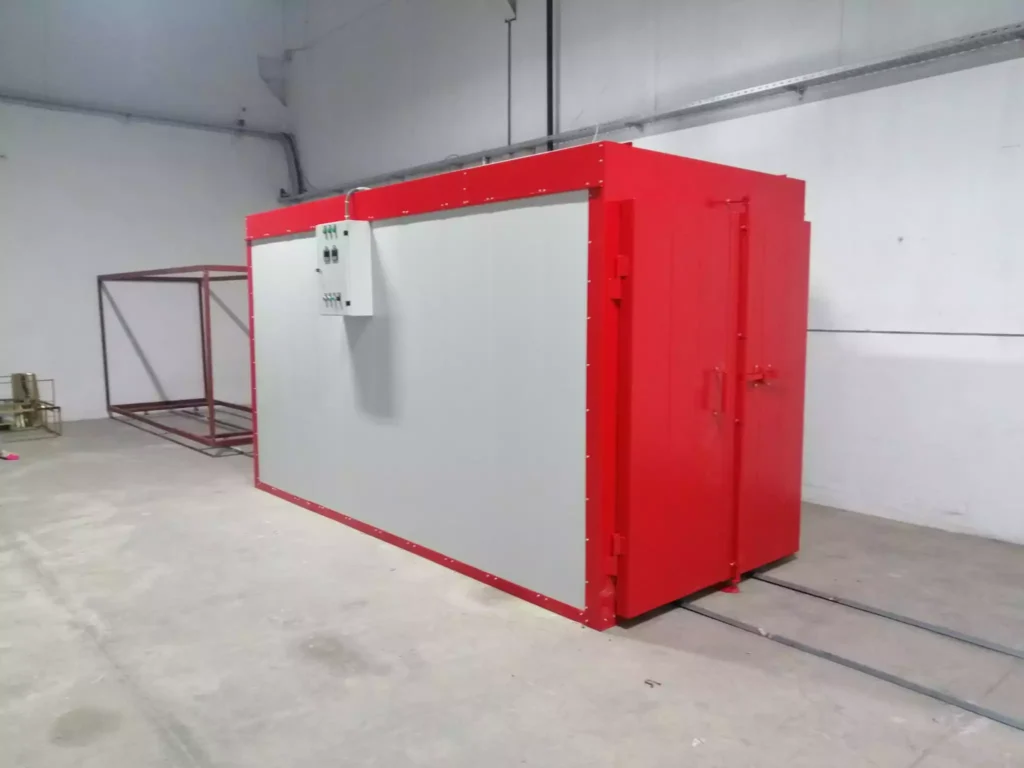
Ein Brennofen für die Pulverbeschichtung ist eine der zentralen Komponenten im gesamten Pulverbeschichtungsprozess. Nachdem das Pulver auf die Oberfläche eines Werkstücks aufgetragen wurde, sorgt der Brennofen dafür, dass die Beschichtung durch Hitze ausgehärtet und in ihre endgültige Form gebracht wird. Dieser Prozess ist entscheidend, um eine haltbare, gleichmäßige und widerstandsfähige Oberfläche zu erzielen. Die Funktionsweise und die Eigenschaften des Brennofens beeinflussen maßgeblich die Qualität des Endprodukts.
Die Rolle des Brennofens im Pulverbeschichtungsprozess
In der Pulverbeschichtung wird das Pulver elektrostatisch auf das Werkstück aufgetragen, indem es durch elektrische Ladung an der Oberfläche haftet. Anschließend muss dieses Pulver erhitzt werden, damit es zu einer glatten, zusammenhängenden Schicht schmilzt. Hier kommt der Brennofen ins Spiel. Er sorgt dafür, dass die nötige Hitze gleichmäßig verteilt wird, damit das Pulver schmilzt und sich zu einer harten, robusten Beschichtung vernetzt.
Die Temperatur im Brennofen liegt in der Regel zwischen 160 und 230 Grad Celsius, abhängig von der Art des Pulvers und des zu beschichtenden Materials. Der Brennprozess dauert typischerweise zwischen 10 und 30 Minuten, wobei sowohl die Temperatur als auch die Zeit präzise kontrolliert werden müssen, um optimale Ergebnisse zu erzielen.
Aufbau und Funktionsweise eines Brennofens für die Pulverbeschichtung
Ein Brennofen für die Pulverbeschichtung besteht aus mehreren Schlüsselkomponenten, die zusammenarbeiten, um den Beschichtungsprozess reibungslos ablaufen zu lassen:
- Heizsystem: Im Brennofen wird die Hitze durch verschiedene Systeme erzeugt. Am häufigsten kommen Gasbrenner oder elektrische Heizelemente zum Einsatz. Gasöfen nutzen Erdgas oder Flüssiggas als Brennstoff, während elektrische Brennöfen auf Widerstandsheizelemente setzen. Beide Technologien haben ihre Vor- und Nachteile: Gasöfen sind oft günstiger im Betrieb, während elektrische Öfen präziser in der Temperaturregelung sind.
- Isolierung: Die Isolierung des Ofens ist entscheidend, um Energieverluste zu minimieren und die Temperatur gleichmäßig zu halten. Hochwertige Isoliermaterialien sorgen dafür, dass die Hitze im Inneren des Ofens bleibt und nicht an die Umgebung abgegeben wird. Dadurch wird der Energieverbrauch gesenkt und der Brennvorgang effizienter gestaltet.
- Luftzirkulation: Eine gleichmäßige Verteilung der Hitze im Inneren des Brennofens ist entscheidend, um sicherzustellen, dass das Pulver auf allen Oberflächen des Werkstücks gleichmäßig schmilzt und aushärtet. Moderne Brennöfen verfügen über fortschrittliche Lüftungssysteme, die die heiße Luft im Ofen zirkulieren lassen und so eine gleichmäßige Temperaturverteilung gewährleisten. Dies ist besonders wichtig bei großen oder komplexen Werkstücken, bei denen verschiedene Bereiche unterschiedliche thermische Anforderungen haben könnten.
- Fördersystem: In vielen industriellen Anwendungen ist der Brennofen Teil einer automatisierten Produktionslinie. Ein Fördersystem transportiert die Werkstücke durch den Ofen, wodurch ein kontinuierlicher und effizienter Beschichtungsprozess ermöglicht wird. Je nach Größe und Komplexität des Werkstücks können unterschiedliche Fördersysteme verwendet werden, wie etwa Schienensysteme, Power-and-Free-Systeme oder Kettenförderer.
- Temperaturregelung: Die präzise Kontrolle der Temperatur im Brennofen ist essenziell, um sicherzustellen, dass das Pulver gleichmäßig und vollständig aushärtet. Moderne Brennöfen sind mit digitalen Steuerungssystemen ausgestattet, die in der Lage sind, die Temperatur genau zu regulieren und eventuelle Schwankungen sofort zu korrigieren. Dies ist besonders wichtig, da bereits kleine Temperaturunterschiede zu Qualitätsproblemen führen können, wie ungleichmäßige Aushärtung oder Blasenbildung in der Beschichtung.
Arten von Brennöfen in der Pulverbeschichtung
Es gibt verschiedene Typen von Brennöfen, die in der Pulverbeschichtung eingesetzt werden. Die Wahl des richtigen Ofens hängt von der Art der Werkstücke, dem verwendeten Pulverlack und den spezifischen Anforderungen der Produktionsumgebung ab.
- Konvektionsbrennöfen: Dies ist die am häufigsten verwendete Ofentechnologie in der Pulverbeschichtung. Bei einem Konvektionsofen wird heiße Luft gleichmäßig durch den gesamten Ofen geleitet, wodurch die Werkstücke gleichmäßig erhitzt werden. Diese Öfen sind sehr vielseitig und eignen sich für eine breite Palette von Anwendungen, von kleinen Metallteilen bis hin zu großen Werkstücken wie Autoteilen oder Maschinenkomponenten.
- Infrarotbrennöfen: Infrarotbrennöfen nutzen Infrarotstrahlung, um die Werkstücke direkt zu erhitzen, ohne die Luft im Ofen zu erwärmen. Diese Technologie ist besonders effizient, wenn es darum geht, dünne Werkstücke oder Teile mit komplexen Geometrien schnell zu erhitzen. Ein großer Vorteil von Infrarotöfen ist ihre kurze Aufheizzeit, was zu schnelleren Produktionszyklen führt.
- Hybridbrennöfen: Hybridbrennöfen kombinieren die Vorteile von Konvektions- und Infrarotöfen. Sie nutzen sowohl heiße Luft als auch Infrarotstrahlung, um die Werkstücke gleichmäßig und effizient zu erhitzen. Diese Technologie wird häufig in komplexen Produktionsumgebungen eingesetzt, in denen unterschiedliche Werkstoffe oder Pulverlacke verwendet werden, die jeweils unterschiedliche Temperaturprofile erfordern.
- Durchlauföfen: Diese Öfen sind speziell für die Massenproduktion ausgelegt. Werkstücke werden auf einem Fördersystem kontinuierlich durch den Ofen transportiert, was einen hohen Durchsatz und eine gleichmäßige Aushärtung ermöglicht. Durchlauföfen werden häufig in der Automobilindustrie und bei der Herstellung von Haushaltsgeräten eingesetzt, wo große Mengen von Werkstücken in kurzer Zeit bearbeitet werden müssen.
Vorteile eines Brennofens für die Pulverbeschichtung
Die Verwendung eines Brennofens in der Pulverbeschichtung bringt zahlreiche Vorteile mit sich:
- Hohe Effizienz: Brennöfen ermöglichen eine schnelle und gleichmäßige Aushärtung der Pulverbeschichtung, was zu einer erheblichen Steigerung der Produktivität führt. Moderne Öfen sind in der Lage, große Mengen an Werkstücken in kurzer Zeit zu verarbeiten, was besonders in der Serienproduktion von Vorteil ist.
- Energieeinsparungen: Fortschritte in der Ofentechnologie haben zu energieeffizienteren Systemen geführt, die den Energieverbrauch erheblich reduzieren können. Durch den Einsatz von fortschrittlichen Isolierungen und präzisen Temperatursteuerungen können moderne Brennöfen den Energieverbrauch senken, was nicht nur die Betriebskosten verringert, sondern auch die Umweltbelastung minimiert.
- Qualität der Beschichtung: Ein gut kalibrierter Brennofen stellt sicher, dass das Pulver gleichmäßig schmilzt und sich zu einer glatten, dauerhaften Beschichtung vernetzt. Dies reduziert die Wahrscheinlichkeit von Fehlern wie Blasenbildung, ungleichmäßiger Deckung oder unzureichender Haftung.
- Umweltfreundlichkeit: Brennöfen, insbesondere solche, die mit Gas betrieben werden, haben im Vergleich zu anderen Technologien einen geringeren CO₂-Ausstoß. Außerdem produzieren sie keine schädlichen Emissionen, da im Pulverbeschichtungsprozess keine Lösungsmittel oder andere umweltschädliche Stoffe verwendet werden.
Herausforderungen und Überlegungen bei der Nutzung eines Brennofens
Trotz der zahlreichen Vorteile gibt es einige Herausforderungen, die bei der Nutzung eines Brennofens für die Pulverbeschichtung berücksichtigt werden müssen:
- Anschaffungskosten: Die Installation eines Brennofens kann eine erhebliche Investition darstellen, insbesondere wenn es sich um große oder hochautomatisierte Systeme handelt. Unternehmen müssen sicherstellen, dass die Anschaffungskosten durch die langfristigen Einsparungen und die gesteigerte Effizienz gerechtfertigt sind.
- Platzbedarf: Ein Brennofen nimmt oft viel Platz in einer Produktionsumgebung ein. Unternehmen müssen sicherstellen, dass sie über ausreichend Platz für die Installation und den sicheren Betrieb des Ofens verfügen.
- Wartung: Wie bei allen industriellen Anlagen erfordert auch ein Brennofen regelmäßige Wartung, um reibungslos zu funktionieren. Dies umfasst die Überprüfung der Heizelemente, die Reinigung der Lüftungssysteme und die Kalibrierung der Temperaturkontrollsysteme. Eine unzureichende Wartung kann zu Produktionsausfällen oder Qualitätsproblemen führen.
Zukunft der Brennöfen in der Pulverbeschichtung
Mit dem Fortschreiten der Technologien werden Brennöfen zunehmend energieeffizienter und intelligenter. Zukünftige Innovationen könnten die Integration von Industrie 4.0-Lösungen umfassen, bei denen Brennöfen in Echtzeit überwacht und optimiert werden, um den Energieverbrauch zu senken und die Beschichtungsqualität weiter zu verbessern. Zudem wird der Trend zu umweltfreundlicheren Brennöfen, die weniger CO₂-Emissionen verursachen, weiter an Bedeutung gewinnen.
Ofen zum Pulverbeschichten

Ein Ofen zum Pulverbeschichten ist ein unverzichtbares Element im gesamten Pulverbeschichtungsprozess. Der Ofen ist verantwortlich für das Aushärten der aufgebrachten Pulverbeschichtung und beeinflusst maßgeblich die Endqualität der beschichteten Teile. Die richtige Auswahl und Handhabung des Ofens haben direkte Auswirkungen auf die Langlebigkeit, Widerstandsfähigkeit und das Erscheinungsbild der beschichteten Werkstücke. Dieser Abschnitt beleuchtet die Funktionsweise, den Aufbau und die verschiedenen Typen von Öfen zum Pulverbeschichten sowie ihre Bedeutung in der industriellen Anwendung.
Die Rolle des Ofens im Pulverbeschichtungsprozess
Nachdem das Pulver auf ein Werkstück aufgetragen wurde, geschieht die Aushärtung durch Hitze im Ofen. Der Pulverlack besteht aus fein gemahlenen Partikeln aus Harzen, Pigmenten und anderen Additiven. Sobald das Pulver auf das Werkstück gesprüht wurde, muss es im Ofen erhitzt werden, um eine glatte, widerstandsfähige Oberfläche zu erzeugen. Bei diesem thermischen Prozess schmelzen die Pulverpartikel und vernetzen sich zu einem festen, gleichmäßigen Film. Der Ofen stellt somit sicher, dass das Pulver gleichmäßig auf dem Werkstück verteilt wird und eine dauerhafte, ästhetisch ansprechende und robuste Schicht entsteht.
Die Temperatur im Ofen liegt in der Regel zwischen 160 und 220 Grad Celsius. Dieser Bereich variiert je nach Art des verwendeten Pulverlacks und den spezifischen Anforderungen der Werkstücke. Neben der Temperatur ist auch die Verweilzeit im Ofen entscheidend für die Qualität des Endprodukts. Die Werkstücke müssen ausreichend lange im Ofen verbleiben, damit die chemische Vernetzung des Pulverlacks vollständig erfolgen kann.
Aufbau eines Ofens zum Pulverbeschichten
Ein Ofen zum Pulverbeschichten besteht aus verschiedenen Komponenten, die zusammenwirken, um den Aushärtungsprozess effizient und gleichmäßig durchzuführen. Zu den wichtigsten Bauteilen gehören:
- Heizsystem: Das Heizsystem ist der Kern jedes Pulverbeschichtungs-Ofens. Es erzeugt die nötige Wärme, um das Pulver auf den Werkstücken zu schmelzen und zu vernetzen. Je nach Ofentyp können verschiedene Heizmethoden zum Einsatz kommen. Die häufigsten sind Konvektionsheizung und Infrarotheizung. Bei der Konvektionsheizung wird die Wärme durch heiße Luft erzeugt, die gleichmäßig durch den Ofen zirkuliert. Infrarotheizungen hingegen arbeiten mit Strahlungswärme, die direkt auf die Werkstücke übertragen wird.
- Luftzirkulationssystem: Eine gleichmäßige Verteilung der Wärme im Ofen ist entscheidend für den Aushärtungsprozess. Moderne Öfen sind mit leistungsfähigen Luftzirkulationssystemen ausgestattet, die sicherstellen, dass die heiße Luft gleichmäßig im Ofen verteilt wird. Dadurch wird verhindert, dass bestimmte Teile des Werkstücks zu heiß oder zu kalt werden, was zu ungleichmäßigen Beschichtungen führen könnte.
- Temperaturregelung: Um eine konstante Qualität zu gewährleisten, muss die Temperatur im Ofen exakt geregelt werden. Digitale Steuerungssysteme ermöglichen es, die Temperatur präzise zu überwachen und anzupassen, um eine gleichmäßige Aushärtung zu garantieren. Viele moderne Öfen sind mit automatischen Temperaturkontrollsystemen ausgestattet, die in Echtzeit auf Schwankungen reagieren können, um den optimalen Aushärtungsprozess sicherzustellen.
- Ofenkammer: Die Ofenkammer ist der Bereich, in dem die Werkstücke während des Aushärtungsprozesses platziert werden. Sie muss ausreichend groß sein, um die Werkstücke in der gewünschten Menge und Größe aufnehmen zu können. In vielen Produktionsumgebungen sind die Öfen so konzipiert, dass sie kontinuierlich arbeiten, wobei die Werkstücke auf einem Fördersystem durch den Ofen transportiert werden.
- Fördersystem: In automatisierten Produktionslinien sind die Öfen in Fördersysteme integriert, die die Werkstücke durch den Ofen transportieren. Dies ermöglicht einen kontinuierlichen Aushärtungsprozess, was die Effizienz erheblich steigert. Die Geschwindigkeit des Fördersystems kann in Abhängigkeit von der benötigten Aushärtungszeit und der Größe der Werkstücke angepasst werden.
Typen von Öfen zum Pulverbeschichten
Es gibt verschiedene Arten von Öfen zum Pulverbeschichten, die je nach den spezifischen Anforderungen der Beschichtungsanlage ausgewählt werden. Die gängigsten Typen sind:
- Konvektionsöfen: Diese Art von Ofen ist die am weitesten verbreitete für die Pulverbeschichtung. Konvektionsöfen nutzen heiße Luft, die durch den Ofen zirkuliert und die Werkstücke gleichmäßig erhitzt. Diese Öfen sind äußerst vielseitig und eignen sich für eine Vielzahl von Materialien und Werkstückgrößen. Sie sind besonders gut geeignet für größere Produktionsmengen, da sie eine gleichmäßige Wärmeverteilung gewährleisten und für den kontinuierlichen Betrieb ausgelegt sind.
- Infrarotöfen: Infrarotöfen erhitzen die Werkstücke durch Infrarotstrahlung, die direkt auf die Oberfläche der Werkstücke trifft. Diese Öfen sind besonders effizient, da sie die Werkstücke schneller erhitzen können als Konvektionsöfen. Infrarotöfen eignen sich besonders für Werkstücke mit komplexen Geometrien oder wenn schnelle Aushärtungszeiten erforderlich sind.
- Hybridöfen: Hybridöfen kombinieren die Vorteile von Konvektions- und Infrarotöfen. Sie nutzen sowohl heiße Luft als auch Infrarotstrahlung, um die Werkstücke effizient und gleichmäßig zu erhitzen. Diese Öfen sind besonders für Anwendungen geeignet, bei denen unterschiedliche Werkstücktypen und Pulverlacke verarbeitet werden müssen, die jeweils unterschiedliche Temperaturprofile erfordern.
- Durchlauföfen: Diese Öfen sind speziell für den Einsatz in kontinuierlichen Produktionslinien konzipiert. Werkstücke werden auf einem Fördersystem kontinuierlich durch den Ofen transportiert, was eine gleichmäßige und effiziente Aushärtung ermöglicht. Durchlauföfen werden häufig in der Automobilindustrie oder bei der Herstellung von Haushaltsgeräten eingesetzt, wo eine hohe Produktionskapazität erforderlich ist.
Vorteile eines Ofens zum Pulverbeschichten
Ein Ofen zum Pulverbeschichten bietet zahlreiche Vorteile gegenüber anderen Aushärtungsverfahren, insbesondere in Bezug auf die Qualität und Effizienz des Prozesses:
- Hohe Produktivität: Moderne Öfen ermöglichen eine schnelle und gleichmäßige Aushärtung der Pulverbeschichtung, was zu kürzeren Durchlaufzeiten und einer höheren Produktivität führt. Besonders in automatisierten Produktionslinien tragen Öfen maßgeblich zur Effizienzsteigerung bei.
- Energieeffizienz: Dank fortschrittlicher Technologie und präziser Temperaturregelung können moderne Öfen den Energieverbrauch minimieren. Dies senkt nicht nur die Betriebskosten, sondern trägt auch zur Reduzierung des CO₂-Ausstoßes bei, was in vielen Industrien zunehmend an Bedeutung gewinnt.
- Gleichmäßige Beschichtungsqualität: Durch die präzise Steuerung der Temperatur und der Luftzirkulation im Ofen wird eine gleichmäßige Aushärtung der Pulverbeschichtung gewährleistet. Dies führt zu einer qualitativ hochwertigen und dauerhaften Beschichtung, die den hohen Anforderungen in verschiedenen Industrien gerecht wird.
- Anpassungsfähigkeit: Öfen zum Pulverbeschichten sind in einer Vielzahl von Größen und Konfigurationen erhältlich, was sie äußerst vielseitig macht. Sie können an die spezifischen Anforderungen der Produktionsumgebung angepasst werden, sei es für kleine Werkstücke oder große, komplexe Bauteile.
Herausforderungen und Überlegungen beim Einsatz eines Pulverbeschichtungs-Ofens
Wie bei jeder industriellen Anlage gibt es auch bei Öfen zum Pulverbeschichten einige Herausforderungen, die berücksichtigt werden müssen:
- Anschaffungskosten: Die Investition in einen hochwertigen Ofen kann beträchtlich sein. Unternehmen müssen sicherstellen, dass die Kosten durch die Steigerung der Produktionskapazität und der Qualität gerechtfertigt sind.
- Platzbedarf: Öfen, insbesondere solche, die Teil einer automatisierten Produktionslinie sind, benötigen viel Platz. Eine sorgfältige Planung der Produktionsfläche ist daher unerlässlich.
- Wartung: Regelmäßige Wartung ist notwendig, um sicherzustellen, dass der Ofen effizient und zuverlässig arbeitet. Dies beinhaltet die Überprüfung des Heizsystems, der Luftzirkulation und der Temperaturregelung.
Zukunftsaussichten für Öfen zum Pulverbeschichten
Mit der fortschreitenden Entwicklung der Pulverbeschichtungstechnologien wird auch die Ofentechnologie weiter verbessert. Zukünftige Öfen werden wahrscheinlich noch energieeffizienter sein, mit besserer Temperaturregelung und Automatisierungsmöglichkeiten. Die Integration von Industrie 4.0-Technologien ermöglicht eine präzisere Überwachung und Steuerung des Aushärtungsprozesses, was zu einer weiteren Verbesserung der Qualität und Effizienz führt.
Durchlauföfen

Durchlauföfen spielen eine entscheidende Rolle in modernen industriellen Beschichtungsprozessen, insbesondere in der Pulverbeschichtung. Sie sind speziell darauf ausgelegt, hohe Stückzahlen von Werkstücken kontinuierlich zu erhitzen und den Aushärtungsprozess der Pulverbeschichtung effizient und konsistent durchzuführen. Durchlauföfen bieten eine Reihe von Vorteilen, darunter eine höhere Produktivität, gleichmäßige Ergebnisse und eine optimierte Energieeffizienz. In diesem Abschnitt werden die Funktionsweise, die verschiedenen Typen, die Vorteile sowie die Herausforderungen von Durchlauföfen detailliert beschrieben.
Funktionsweise von Durchlauföfen
Der Hauptunterschied zwischen Durchlauföfen und anderen Ofentypen ist die Art und Weise, wie die Werkstücke durch den Ofen transportiert werden. In einem Durchlaufofen werden die Werkstücke auf einem Fördersystem kontinuierlich durch den Ofen bewegt. Dies ermöglicht eine ununterbrochene Produktion, bei der Werkstücke ohne Unterbrechung nacheinander in den Ofen gelangen, gleichmäßig erhitzt und schließlich wieder aus dem Ofen transportiert werden.
Das Fördersystem in einem Durchlaufofen kann aus verschiedenen Technologien bestehen, wie etwa Kettenförderern, Power-and-Free-Systemen oder Rollenbahnen. Die Geschwindigkeit des Fördersystems kann je nach den spezifischen Anforderungen des Produktionsprozesses angepasst werden, um sicherzustellen, dass jedes Werkstück die optimale Verweilzeit im Ofen hat. Diese Verweilzeit ist entscheidend, um sicherzustellen, dass die Pulverbeschichtung vollständig aushärtet und eine gleichmäßige, robuste Oberfläche entsteht.
Aufbau eines Durchlaufofens
Ein Durchlaufofen besteht aus mehreren zentralen Komponenten, die zusammenarbeiten, um den Aushärtungsprozess effizient und gleichmäßig zu gestalten:
- Heizsystem: Das Heizsystem ist für die Erzeugung der Wärme verantwortlich, die für den Aushärtungsprozess notwendig ist. Je nach Typ des Durchlaufofens kann das Heizsystem auf Gas, Elektrizität oder Infrarotstrahlung basieren. Gasöfen sind oft kostengünstiger im Betrieb, während elektrische Öfen eine präzisere Steuerung der Temperatur ermöglichen.
- Fördersystem: Das Fördersystem transportiert die Werkstücke durch den Ofen und sorgt dafür, dass sie gleichmäßig erhitzt werden. Es gibt verschiedene Arten von Fördersystemen, die je nach Größe, Gewicht und Form der Werkstücke ausgewählt werden. Power-and-Free-Fördersysteme bieten beispielsweise eine hohe Flexibilität, da sie es ermöglichen, einzelne Werkstücke zu entkoppeln und individuell durch den Ofen zu führen.
- Temperaturregelung: Eine präzise Temperaturregelung ist entscheidend für die Qualität der Pulverbeschichtung. Moderne Durchlauföfen sind mit digitalen Steuerungssystemen ausgestattet, die eine genaue Überwachung und Regelung der Temperatur ermöglichen. Diese Systeme sorgen dafür, dass die Temperatur im gesamten Ofen konstant bleibt und Schwankungen, die die Qualität der Beschichtung beeinträchtigen könnten, vermieden werden.
- Luftzirkulationssystem: Ein effizientes Luftzirkulationssystem sorgt dafür, dass die heiße Luft gleichmäßig im Ofen verteilt wird. Dies ist besonders wichtig, um sicherzustellen, dass die Werkstücke von allen Seiten gleichmäßig erhitzt werden und die Pulverbeschichtung gleichmäßig aushärtet. Moderne Durchlauföfen verfügen über fortschrittliche Lüftungssysteme, die eine optimale Wärmeverteilung gewährleisten.
Typen von Durchlauföfen
Es gibt verschiedene Arten von Durchlauföfen, die je nach den spezifischen Anforderungen der Produktionsumgebung ausgewählt werden können. Die gängigsten Typen sind:
- Konvektionsdurchlauföfen: Bei diesen Öfen wird die Wärme durch heiße Luft erzeugt, die gleichmäßig durch den Ofen zirkuliert. Konvektionsöfen sind sehr vielseitig und eignen sich für eine breite Palette von Werkstücken. Sie werden häufig in der Automobilindustrie und bei der Herstellung von Haushaltsgeräten eingesetzt, wo große Mengen an Werkstücken in kurzer Zeit verarbeitet werden müssen.
- Infrarotdurchlauföfen: Diese Öfen nutzen Infrarotstrahlung, um die Werkstücke direkt zu erhitzen. Infrarotöfen sind besonders effizient, da sie schneller aufheizen als Konvektionsöfen und die Werkstücke direkt erhitzen, ohne die Luft im Ofen zu erwärmen. Sie eignen sich besonders für dünne oder empfindliche Werkstücke, die eine schnelle Aushärtung erfordern.
- Hybridöfen: Hybridöfen kombinieren die Vorteile von Konvektions- und Infrarottechnologie. Sie nutzen sowohl heiße Luft als auch Infrarotstrahlung, um eine gleichmäßige und schnelle Aushärtung zu gewährleisten. Diese Öfen sind ideal für komplexe Werkstücke oder Produktionsprozesse, bei denen unterschiedliche Materialien oder Pulverlacke verwendet werden.
- Spezialdurchlauföfen: In bestimmten Industrien, wie der Luft- und Raumfahrt oder der Medizintechnik, werden Spezialdurchlauföfen eingesetzt, die auf die spezifischen Anforderungen dieser Branchen zugeschnitten sind. Diese Öfen können beispielsweise unter Reinraumbedingungen arbeiten oder für besonders hohe Temperaturen ausgelegt sein.
Vorteile von Durchlauföfen
Durchlauföfen bieten eine Reihe von Vorteilen, die sie zu einer bevorzugten Wahl in vielen industriellen Produktionsumgebungen machen:
- Hohe Produktivität: Durchlauföfen ermöglichen einen kontinuierlichen Produktionsprozess, bei dem Werkstücke ohne Unterbrechung durch den Ofen transportiert werden. Dies führt zu einer erheblichen Steigerung der Produktivität, insbesondere in Branchen mit hohem Durchsatz, wie der Automobilindustrie oder der Herstellung von Elektronikgeräten.
- Gleichmäßige Aushärtung: Da die Werkstücke in einem Durchlaufofen gleichmäßig erhitzt werden, wird eine gleichmäßige Aushärtung der Pulverbeschichtung gewährleistet. Dies führt zu einer höheren Qualität der Endprodukte, da Oberflächenfehler wie Blasenbildung oder ungleichmäßige Beschichtungen vermieden werden.
- Effizienz: Durchlauföfen sind sehr energieeffizient, da sie kontinuierlich arbeiten und die Energie optimal genutzt wird. Moderne Öfen sind mit fortschrittlichen Isoliermaterialien und Steuerungssystemen ausgestattet, die den Energieverbrauch minimieren und gleichzeitig die Produktqualität maximieren.
- Flexibilität: Durchlauföfen sind in der Regel sehr flexibel und können an verschiedene Werkstückgrößen und -formen angepasst werden. Sie sind auch mit verschiedenen Fördersystemen kompatibel, was ihre Vielseitigkeit weiter erhöht.
- Automatisierung: Viele Durchlauföfen sind in automatisierte Produktionslinien integriert, was die Effizienz und Präzision weiter steigert. Die Automatisierung reduziert den Bedarf an manueller Arbeit und minimiert das Risiko menschlicher Fehler.
Herausforderungen bei der Verwendung von Durchlauföfen
Trotz ihrer zahlreichen Vorteile gibt es auch einige Herausforderungen, die bei der Verwendung von Durchlauföfen berücksichtigt werden müssen:
- Anschaffungskosten: Durchlauföfen sind oft teurer in der Anschaffung als andere Ofentypen. Unternehmen müssen sicherstellen, dass die Investition durch die gesteigerte Produktivität und die höhere Qualität der Endprodukte gerechtfertigt ist.
- Platzbedarf: Da Durchlauföfen in der Regel Teil einer Produktionslinie sind, benötigen sie viel Platz in der Produktionsumgebung. Dies erfordert eine sorgfältige Planung und Optimierung des verfügbaren Platzes.
- Wartung: Wie bei allen industriellen Anlagen erfordert auch ein Durchlaufofen regelmäßige Wartung, um sicherzustellen, dass er effizient und zuverlässig arbeitet. Dies umfasst die Überprüfung des Fördersystems, der Heizelemente und der Temperaturregelung.
- Komplexität der Steuerung: Moderne Durchlauföfen sind oft mit komplexen Steuerungssystemen ausgestattet, die eine genaue Überwachung und Regelung erfordern. Dies kann zusätzliche Schulungen für das Personal erfordern, um sicherzustellen, dass der Ofen ordnungsgemäß bedient wird.
Zukunftsaussichten für Durchlauföfen
Mit der Weiterentwicklung der Technologie wird erwartet, dass Durchlauföfen in Zukunft noch effizienter und vielseitiger werden. Die Integration von Industrie 4.0-Technologien ermöglicht eine präzisere Überwachung und Steuerung der Öfen in Echtzeit, was zu einer weiteren Verbesserung der Energieeffizienz und der Produktqualität führen wird. Darüber hinaus werden neue Materialien und Beschichtungstechnologien die Anforderungen an Durchlauföfen weiter verändern, was zu noch spezialisierteren Lösungen führen könnte.
Lackierkabine Absaugung
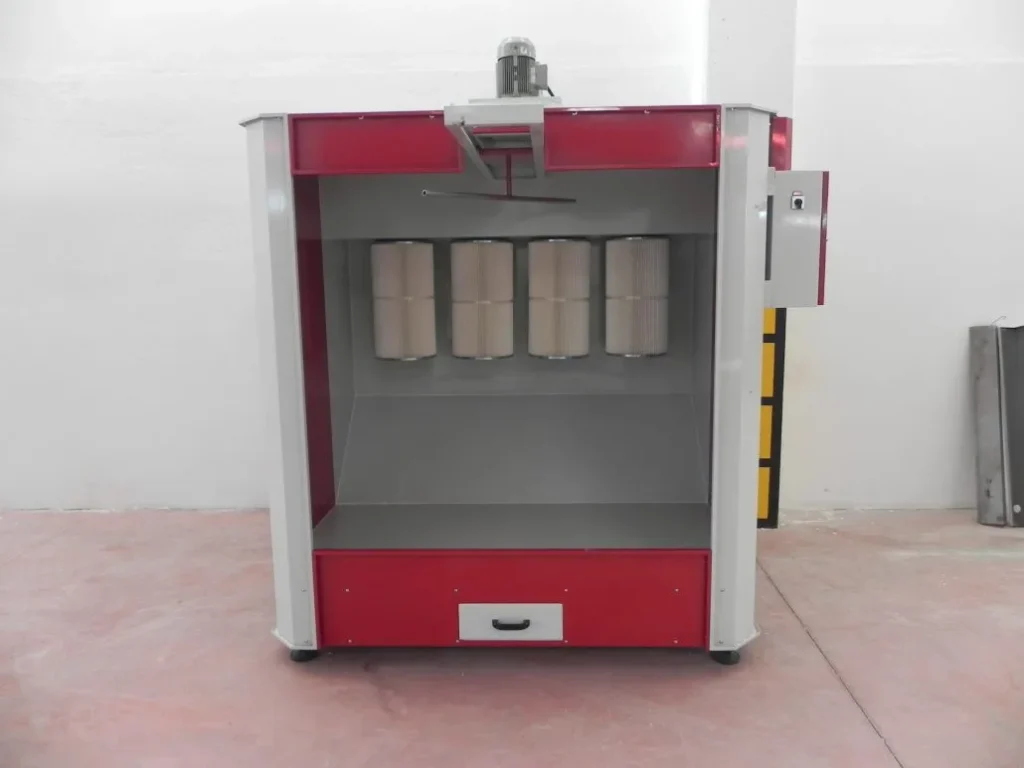
Die Absaugung in Lackierkabinen ist ein entscheidender Bestandteil eines effizienten und sicheren Lackierprozesses. Sie spielt eine wichtige Rolle dabei, gesundheitsschädliche Dämpfe, überschüssige Sprühpartikel und sonstige Verunreinigungen aus der Luft zu filtern und abzuführen. Eine optimale Absaugung gewährleistet nicht nur die Sicherheit der Arbeiter, sondern trägt auch dazu bei, eine hochwertige und gleichmäßige Beschichtung zu gewährleisten. Dieser Abschnitt befasst sich ausführlich mit der Funktionsweise, den verschiedenen Technologien und den Vorteilen der Absaugung in Lackierkabinen sowie mit den Herausforderungen und Sicherheitsaspekten.
Bedeutung der Absaugung in Lackierkabinen
Bei Lackierarbeiten werden feine Farbpartikel und Lösungsmitteldämpfe freigesetzt, die schädlich für die menschliche Gesundheit sein können, wenn sie nicht ordnungsgemäß abgeführt werden. Eine effektive Absaugung sorgt dafür, dass diese Partikel und Dämpfe aus der Luft gefiltert und aus der Lackierkabine abgeführt werden, bevor sie in den Atembereich der Arbeiter gelangen.
Darüber hinaus trägt die Absaugung auch zur Qualität des Endprodukts bei. In Lackierkabinen können sich ohne ausreichende Absaugung Sprühnebel und Farbpartikel ansammeln, die sich auf den zu beschichtenden Werkstücken ablagern und die Beschichtung ungleichmäßig oder fehlerhaft machen. Eine gute Absaugung sorgt dafür, dass überschüssige Farbpartikel sofort entfernt werden, was zu einer gleichmäßigeren und hochwertigeren Beschichtung führt.
Funktionsweise der Lackierkabinenabsaugung
Die Absauganlagen in Lackierkabinen arbeiten nach einem relativ einfachen Prinzip: Sie saugen die Luft aus der Kabine ab, filtern die Schadstoffe heraus und führen die gereinigte Luft wieder ab oder bringen sie zurück in den Kreislauf. Dabei gibt es verschiedene Arten von Absauganlagen, die je nach Art der Lackierkabine und der verwendeten Lackmaterialien variieren.
- Absaugventilatoren: Absaugventilatoren sind das Herzstück jeder Absauganlage. Sie erzeugen den notwendigen Luftstrom, um überschüssige Farbpartikel und Lösungsmitteldämpfe effektiv abzusaugen. Je nach Größe und Art der Lackierkabine können unterschiedliche Arten von Ventilatoren verwendet werden, z. B. Axialventilatoren oder Radialventilatoren. Axialventilatoren sind für kleine Kabinen geeignet, während Radialventilatoren eine höhere Leistung erbringen und für größere oder industrielle Lackierkabinen eingesetzt werden.
- Filtertechnologie: Ein wesentlicher Bestandteil der Absaugung in Lackierkabinen ist das Filtersystem. Es gibt verschiedene Arten von Filtern, die für die Entfernung von Farbpartikeln und anderen Schadstoffen aus der Luft verantwortlich sind. Die häufigsten Filtersysteme sind:
- Trockenfilter: Diese Filter bestehen aus einem mehrschichtigen Material, das die Farbpartikel einfängt, während die Luft hindurchströmt. Sie sind einfach in der Anwendung und eignen sich für kleinere Lackieranlagen oder für Anwendungen mit geringem Farbverbrauch.
- Nassabscheider: Bei diesen Systemen wird die Luft durch einen Wasserstrom geleitet, der die Farbpartikel aus der Luft wäscht. Nassabscheider sind besonders effektiv bei der Entfernung großer Mengen von Farbpartikeln und werden häufig in industriellen Lackieranlagen eingesetzt.
- HEPA-Filter: Diese Hochleistungsfilter sind in der Lage, selbst feinste Partikel und Schadstoffe aus der Luft zu filtern. HEPA-Filter werden in Umgebungen verwendet, in denen besonders hohe Anforderungen an die Luftqualität gestellt werden, wie z. B. in der Automobil- oder Luftfahrtindustrie.
- Luftstromsystem: Eine effiziente Absaugung in der Lackierkabine hängt auch von der richtigen Gestaltung des Luftstroms ab. Der Luftstrom muss so gelenkt werden, dass die Farbpartikel und Dämpfe gezielt in Richtung der Absaugventilatoren geleitet werden. In vielen Lackierkabinen wird dazu ein Zuluft- und Abluftsystem verwendet, bei dem frische Luft in die Kabine eingeblasen und die verunreinigte Luft abgesaugt wird. Dies gewährleistet eine kontinuierliche Erneuerung der Luft und verhindert die Ansammlung von Schadstoffen in der Kabine.
- Absaugwände: In vielen Lackierkabinen werden Absaugwände eingesetzt, um eine gezielte Absaugung zu gewährleisten. Diese Wände sind mit Ventilatoren und Filtern ausgestattet und befinden sich in der Regel an einer Seite der Kabine. Die Absaugwände saugen die verunreinigte Luft direkt an der Quelle ab und verhindern so, dass sich Farbpartikel in der gesamten Kabine ausbreiten.
Arten von Absauganlagen
Es gibt verschiedene Arten von Absauganlagen, die je nach den spezifischen Anforderungen der Lackierkabine und des Lackierprozesses ausgewählt werden können. Die häufigsten Typen sind:
- Einseitige Absaugung: Bei der einseitigen Absaugung befindet sich die Absauganlage an einer Seite der Lackierkabine. Diese Art der Absaugung eignet sich für kleinere Kabinen oder für Anwendungen, bei denen die Lackierarbeiten auf eine bestimmte Fläche beschränkt sind. Die einseitige Absaugung ist in der Regel kostengünstiger, bietet jedoch möglicherweise nicht die gleiche Effizienz wie andere Systeme.
- Doppelseitige Absaugung: Bei der doppelseitigen Absaugung sind Absaugwände auf beiden Seiten der Kabine installiert. Dies sorgt für eine gleichmäßigere Absaugung und verhindert, dass Farbpartikel und Dämpfe in der Kabine verweilen. Doppelseitige Absauganlagen werden häufig in industriellen Lackieranlagen eingesetzt, wo große Mengen von Lack und Lösungsmitteln verwendet werden.
- Bodenabsaugung: Bei der Bodenabsaugung wird die Luft durch Öffnungen im Boden der Kabine abgesaugt. Dieses System ist besonders effektiv, da die Farbpartikel aufgrund ihrer Schwerkraft ohnehin nach unten sinken. Bodenabsauganlagen werden häufig in modernen, hochautomatisierten Lackierkabinen eingesetzt.
- Deckenabsaugung: In einigen Lackierkabinen wird die verunreinigte Luft durch Öffnungen in der Decke abgesaugt. Dies ist vor allem in Kabinen sinnvoll, in denen große Objekte wie Fahrzeuge oder Maschinen lackiert werden, da die Farbpartikel und Dämpfe nach oben steigen und so effektiv abgesaugt werden können.
Vorteile einer effizienten Absaugung
Eine gut funktionierende Absaugung in der Lackierkabine bietet eine Vielzahl von Vorteilen:
- Gesundheitsschutz: Die Absaugung schützt die Gesundheit der Mitarbeiter, indem sie gefährliche Farbpartikel und Lösungsmitteldämpfe aus der Luft entfernt. Dies reduziert das Risiko von Atemwegserkrankungen und anderen gesundheitlichen Problemen, die durch den Kontakt mit diesen Stoffen verursacht werden können.
- Verbesserte Luftqualität: Eine effektive Absaugung sorgt für eine kontinuierliche Erneuerung der Luft in der Lackierkabine. Dies verhindert die Ansammlung von Schadstoffen und sorgt für eine saubere und sichere Arbeitsumgebung.
- Höhere Beschichtungsqualität: Durch die Entfernung von überschüssigen Farbpartikeln und Sprühnebel trägt die Absaugung zu einer gleichmäßigeren und hochwertigeren Beschichtung bei. Dies führt zu besseren Endergebnissen und reduziert das Risiko von Oberflächenfehlern wie Blasenbildung oder ungleichmäßigen Beschichtungen.
- Einhaltung von Umweltstandards: Moderne Absauganlagen sind darauf ausgelegt, die Emissionen von Schadstoffen zu minimieren und die strengen Umweltvorschriften einzuhalten. Dies ist besonders wichtig in Industrien, die große Mengen an Lacken und Lösungsmitteln verwenden.
Herausforderungen bei der Absaugung in Lackierkabinen
Trotz der vielen Vorteile gibt es auch Herausforderungen bei der Implementierung und Wartung von Absauganlagen in Lackierkabinen:
- Kosten: Die Anschaffung und Installation einer hochwertigen Absauganlage kann teuer sein. Unternehmen müssen sicherstellen, dass die Investition durch die verbesserten Arbeitsbedingungen und die höhere Produktqualität gerechtfertigt ist.
- Wartung: Absauganlagen erfordern regelmäßige Wartung, um sicherzustellen, dass sie effizient und zuverlässig arbeiten. Dies umfasst die Reinigung oder den Austausch von Filtern, die Überprüfung der Ventilatoren und die Kalibrierung der Steuerungssysteme.
- Anpassung an verschiedene Lackierprozesse: Nicht alle Lackierkabinen sind gleich, und es kann schwierig sein, eine Absauganlage zu finden, die für alle Anwendungen geeignet ist. Unternehmen müssen möglicherweise maßgeschneiderte Lösungen entwickeln, um sicherzustellen, dass die Absaugung den spezifischen Anforderungen ihrer Lackierprozesse entspricht.
Zukunftsaussichten für Absauganlagen in Lackierkabinen
Mit den Fortschritten in der Technologie wird erwartet, dass Absauganlagen in Zukunft noch effizienter und umweltfreundlicher werden. Die Integration von Industrie 4.0-Technologien ermöglicht eine präzisere Überwachung und Steuerung der Absaugung in Echtzeit, was zu einer weiteren Verbesserung der Luftqualität und der Energieeffizienz führen wird. Darüber hinaus könnten neue Filtersysteme entwickelt werden, die noch effektivere Ergebnisse erzielen und gleichzeitig den Wartungsaufwand reduzieren.
Lackieranlagenherstellung
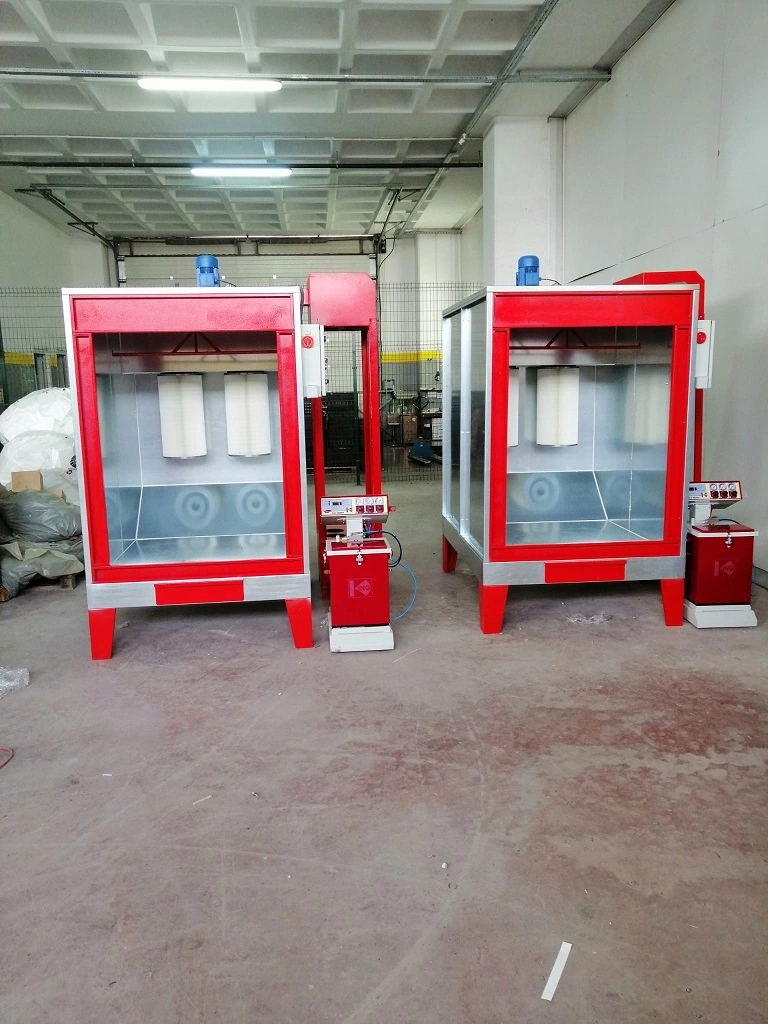
Die Herstellung von Lackieranlagen ist ein hochkomplexer und technisch anspruchsvoller Prozess, der fundiertes Wissen, präzise Planung und modernste Technologien erfordert. Lackieranlagen werden in einer Vielzahl von Industrien eingesetzt, darunter die Automobilindustrie, die Metallverarbeitung, die Luft- und Raumfahrt sowie die Elektronikindustrie. Sie spielen eine entscheidende Rolle bei der Veredelung von Produkten, indem sie eine gleichmäßige, schützende und ästhetische Beschichtung auf die Oberflächen auftragen. In diesem Abschnitt wird der Prozess der Herstellung von Lackieranlagen detailliert erläutert, einschließlich der Planung, der verschiedenen Komponenten und Systeme sowie der Herausforderungen und Trends in der Branche.
Planung und Design von Lackieranlagen
Der erste Schritt bei der Herstellung einer Lackieranlage ist die sorgfältige Planung und Konzeption. Jede Lackieranlage muss an die spezifischen Anforderungen des Kunden und der Branche angepasst werden. Diese Anforderungen können in Bezug auf die Art der zu lackierenden Produkte, die Produktionsmengen, die verwendeten Lackmaterialien und die verfügbaren Platzverhältnisse erheblich variieren.
- Bedarfsanalyse: Vor der eigentlichen Konstruktion einer Lackieranlage wird eine gründliche Bedarfsanalyse durchgeführt. In diesem Schritt arbeitet der Hersteller eng mit dem Kunden zusammen, um die spezifischen Anforderungen zu verstehen. Dazu gehören die Art der Werkstücke (Größe, Material, Form), die Produktionskapazitäten, die gewünschten Endergebnisse (z. B. Art der Beschichtung, Glanzgrad, Schutzschichten) und etwaige Umwelt- oder Sicherheitsanforderungen.
- Konzeptentwicklung: Basierend auf der Bedarfsanalyse entwickelt der Hersteller ein maßgeschneidertes Konzept für die Lackieranlage. Dies umfasst das Layout der Anlage, die Auswahl der notwendigen Komponenten und die Integration der verschiedenen Prozesse wie Vorbehandlung, Lackauftragung und Trocknung. Moderne Planungswerkzeuge wie CAD (Computer Aided Design) ermöglichen es den Ingenieuren, präzise digitale Modelle der Anlage zu erstellen, die sowohl funktional als auch effizient sind.
- Umwelt- und Sicherheitsanforderungen: Ein wesentlicher Bestandteil der Planung ist die Berücksichtigung von Umwelt- und Sicherheitsstandards. Die Emissionen von Lackierprozessen müssen streng kontrolliert werden, um die geltenden Umweltvorschriften einzuhalten. Dies betrifft insbesondere die Abscheidung von Lösungsmitteln und Schadstoffen aus der Luft sowie die Rückführung oder Entsorgung von Lackresten. Zudem müssen Lackieranlagen so konzipiert sein, dass sie den Arbeitsschutzvorschriften entsprechen, beispielsweise durch den Einsatz von sicheren Absaugsystemen und Brandschutzmaßnahmen.
Komponenten einer Lackieranlage
Eine moderne Lackieranlage besteht aus einer Vielzahl von Komponenten, die zusammenarbeiten, um den Lackierprozess effizient und präzise zu gestalten. Zu den wichtigsten Komponenten gehören:
- Vorbehandlungsanlagen: Bevor die Werkstücke lackiert werden können, müssen sie gründlich gereinigt und vorbehandelt werden, um eine optimale Haftung des Lacks zu gewährleisten. Dies erfolgt in speziellen Vorbehandlungsanlagen, in denen die Werkstücke gereinigt, entfettet und gegebenenfalls mit einer chemischen Vorbehandlung (z. B. Phosphatierung oder Chromatierung) versehen werden. Die Vorbehandlung ist entscheidend für die Qualität der späteren Lackierung, da sie sicherstellt, dass die Oberfläche des Werkstücks frei von Schmutz, Fett oder Rost ist.
- Lackierkabinen: Die Lackierkabine ist das Herzstück jeder Lackieranlage. In dieser Kabine wird der Lack auf die Werkstücke aufgetragen. Je nach Anforderung kann dies manuell oder automatisiert mit Spritzpistolen oder Robotern geschehen. Lackierkabinen sind mit speziellen Luftzirkulations- und Absaugsystemen ausgestattet, die überschüssige Lackpartikel und Lösungsmittel sicher entfernen, um eine saubere und sichere Arbeitsumgebung zu gewährleisten.
- Fördersysteme: Um die Werkstücke durch die verschiedenen Stationen der Lackieranlage zu transportieren, werden Fördersysteme eingesetzt. Diese können je nach Anlagentyp variieren, aber gängige Systeme umfassen Power-and-Free-Förderer, Kettenförderer oder Hängebahnsysteme. Die Fördertechnik muss so konzipiert sein, dass sie den Lackierprozess nicht stört und die Werkstücke gleichmäßig durch die Anlage bewegt.
- Trocknungsöfen: Nach der Lackierung müssen die Werkstücke in speziellen Trocknungsöfen getrocknet oder ausgehärtet werden. Diese Öfen können auf unterschiedliche Technologien basieren, wie z. B. Konvektion, Infrarotstrahlung oder UV-Licht. Die Auswahl des richtigen Trocknungssystems hängt von der Art des verwendeten Lacks und den spezifischen Anforderungen an die Aushärtung ab. Trocknungsöfen sind oft mit präzisen Temperatur- und Luftstromsteuerungen ausgestattet, um eine gleichmäßige Trocknung der Werkstücke zu gewährleisten.
- Automatisierungssysteme: Moderne Lackieranlagen sind häufig hoch automatisiert, um die Effizienz zu steigern und gleichbleibende Qualität zu gewährleisten. Roboter und computergestützte Steuerungssysteme übernehmen dabei die präzise Aufbringung des Lacks, die Steuerung der Fördersysteme und die Überwachung der Umgebungsbedingungen in den Lackierkabinen. Automatisierung sorgt nicht nur für eine konstante Produktqualität, sondern reduziert auch den Bedarf an manueller Arbeit und minimiert das Risiko menschlicher Fehler.
Herausforderungen bei der Lackieranlagenherstellung
Die Herstellung von Lackieranlagen bringt eine Reihe von Herausforderungen mit sich, die von der komplexen Planung bis hin zur Umsetzung technischer Lösungen reichen:
- Individuelle Anforderungen: Jede Lackieranlage muss individuell auf die Bedürfnisse des Kunden zugeschnitten werden. Dies bedeutet, dass kein Standardlösungsansatz verfolgt werden kann und jede Anlage speziell für die jeweilige Anwendung konzipiert werden muss. Die Herausforderung besteht darin, die richtigen Technologien und Systeme auszuwählen, die sowohl die Produktionsanforderungen erfüllen als auch wirtschaftlich und umweltfreundlich sind.
- Technologische Integration: Die Integration verschiedener Systeme wie Fördersysteme, Lackierkabinen und Trocknungsöfen in eine nahtlos funktionierende Anlage erfordert ein hohes Maß an technischer Expertise. Die Systeme müssen perfekt aufeinander abgestimmt sein, um Produktionsunterbrechungen oder Qualitätseinbußen zu vermeiden. Eine schlechte Integration kann zu Ineffizienzen führen, die den Produktionsprozess behindern.
- Energieeffizienz: In Zeiten steigender Energiekosten und strengerer Umweltvorschriften wird die Energieeffizienz von Lackieranlagen immer wichtiger. Hersteller von Lackieranlagen müssen Technologien entwickeln, die den Energieverbrauch minimieren, ohne die Qualität der Lackierung zu beeinträchtigen. Dies kann durch den Einsatz von energieeffizienten Trocknungssystemen, optimierten Luftzirkulationssystemen und wärmedämmenden Materialien erreicht werden.
- Kostenmanagement: Die Herstellung einer Lackieranlage ist oft mit erheblichen Kosten verbunden. Die Herausforderung für Hersteller besteht darin, Anlagen zu produzieren, die einerseits den Anforderungen des Kunden gerecht werden und andererseits innerhalb eines festgelegten Budgets liegen. Dies erfordert eine präzise Kostenplanung und das Finden von Kosteneinsparungspotenzialen, ohne die Qualität der Anlage zu beeinträchtigen.
Trends in der Lackieranlagenherstellung
Mit der fortschreitenden Technologie entwickeln sich auch die Trends in der Lackieranlagenherstellung weiter. Zu den wichtigsten Entwicklungen gehören:
- Industrie 4.0: Die zunehmende Digitalisierung und Vernetzung von Produktionsprozessen macht auch vor der Lackieranlagenherstellung nicht halt. Immer mehr Lackieranlagen werden mit intelligenten Steuerungssystemen ausgestattet, die eine Echtzeitüberwachung und -steuerung des Lackierprozesses ermöglichen. Diese Systeme sammeln Daten aus verschiedenen Quellen innerhalb der Anlage und ermöglichen es den Betreibern, den Prozess zu optimieren und potenzielle Probleme frühzeitig zu erkennen.
- Umweltfreundliche Lackieranlagen: Aufgrund strengerer Umweltauflagen und eines wachsenden Umweltbewusstseins in der Industrie konzentrieren sich Hersteller zunehmend auf die Entwicklung umweltfreundlicher Lackieranlagen. Dazu gehören Systeme, die den Einsatz von lösungsmittelfreien Lacken ermöglichen, fortschrittliche Filtersysteme zur Reduzierung von Emissionen sowie energieeffiziente Trocknungs- und Belüftungssysteme.
- Modularität: Ein weiterer Trend ist die Entwicklung modularer Lackieranlagen. Diese Anlagen bestehen aus standardisierten Modulen, die je nach Bedarf kombiniert und erweitert werden können. Dies ermöglicht es den Betreibern, ihre Anlagen flexibel an veränderte Produktionsanforderungen anzupassen, ohne große Investitionen in neue Anlagen tätigen zu müssen.
- Automatisierung und Robotik: Der Einsatz von Robotern und automatisierten Systemen wird in der Lackieranlagenherstellung immer weiter vorangetrieben. Roboter ermöglichen eine präzise und konsistente Aufbringung des Lacks und können auch für die Handhabung der Werkstücke eingesetzt werden. Dies erhöht die Effizienz und reduziert das Risiko von Fehlern.
Fazit
Die Herstellung von Lackieranlagen ist ein komplexer Prozess, der ein hohes Maß an technischer Expertise und präziser Planung erfordert. Die Anpassung an individuelle Kundenanforderungen, die Integration verschiedener Systeme und die Einhaltung von Umwelt- und Sicherheitsstandards sind nur einige der Herausforderungen, denen sich Hersteller stellen müssen. Gleichzeitig bieten moderne Technologien wie Industrie 4.0, Automatisierung und umweltfreundliche Lösungen spannende neue Möglichkeiten, den Lackierprozess effizienter und nachhaltiger zu gestalten.
Power and Free Fördertechnik
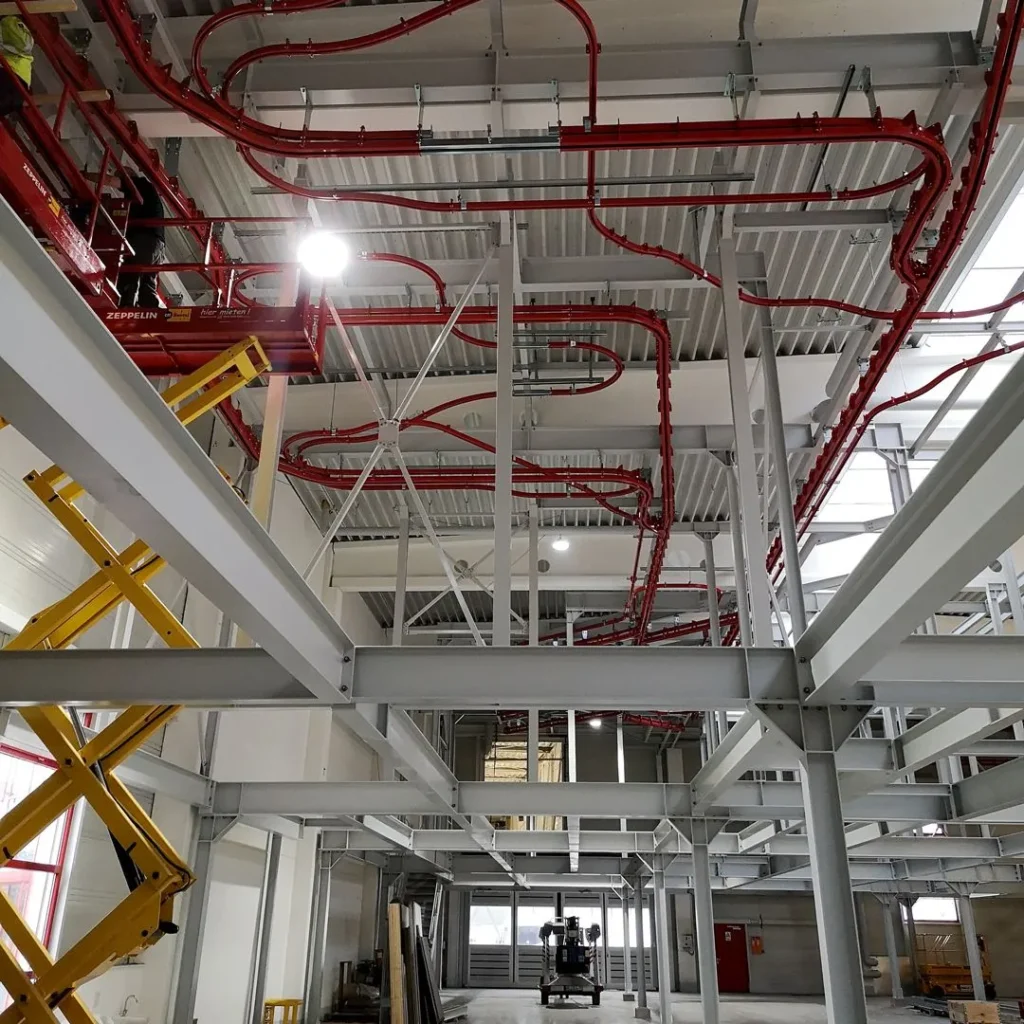
Die Power and Free Fördertechnik ist eines der flexibelsten und effizientesten Fördersysteme, die in der industriellen Produktion, insbesondere in der Lackier- und Beschichtungsindustrie, zum Einsatz kommen. Diese Art von Fördersystem bietet zahlreiche Vorteile, darunter die Möglichkeit, verschiedene Produkte gleichzeitig zu transportieren, die Möglichkeit, Prozesse zu synchronisieren, und die Fähigkeit, die Produktion an wechselnde Anforderungen anzupassen. In diesem Abschnitt werden die Funktionsweise, die Vorteile, die Komponenten und die typischen Anwendungen der Power and Free Fördertechnik im Detail untersucht.
Funktionsweise der Power and Free Fördertechnik
Power and Free Systeme unterscheiden sich von herkömmlichen Fördersystemen durch ihre flexible und unabhängige Steuerung der Transporteinheiten. Während herkömmliche Kettenförderer in einem kontinuierlichen Fluss arbeiten, erlaubt die Power and Free Fördertechnik das Anhalten, Starten, Beschleunigen und Verzögern von Transporteinheiten an verschiedenen Punkten der Strecke. Dies wird durch die Verwendung von zwei separaten Kettensträngen erreicht: einem Power-Strang (Antriebsstrang) und einem Free-Strang (freier Strang).
- Power-Strang: Der Power-Strang ist die treibende Kraft des Systems. Es handelt sich um eine durchgehende Kette, die die Energie für den Transport der Werkstücke liefert. Dieser Strang läuft konstant und bewegt sich entlang der gesamten Förderstrecke, unabhängig von den Werkstücken.
- Free-Strang: Der Free-Strang ist mit den Werkstücken oder Transportwagen verbunden. Dieser Strang wird durch spezielle Mitnehmer und Verriegelungsmechanismen mit dem Power-Strang gekoppelt, kann aber bei Bedarf entkoppelt werden, um das Werkstück an bestimmten Stationen anzuhalten oder zu puffern. Dies ermöglicht es, einzelne Werkstücke oder Wagen zu stoppen, ohne den gesamten Produktionsfluss zu unterbrechen.
- Weichen und Pufferzonen: Eine weitere Besonderheit der Power and Free Fördertechnik ist die Integration von Weichen und Pufferzonen. Weichen ermöglichen es, die Transportwagen auf verschiedene Strecken zu leiten, während Pufferzonen dafür sorgen, dass Werkstücke vorübergehend angehalten werden können, z. B. um auf die nächste Bearbeitungsstation zu warten oder die Reihenfolge der Werkstücke anzupassen. Dies macht das System äußerst flexibel und anpassungsfähig an unterschiedliche Produktionsanforderungen.
- Steuerungssysteme: Moderne Power and Free Systeme sind häufig mit computergestützten Steuerungssystemen ausgestattet, die den gesamten Förderprozess überwachen und steuern. Diese Systeme können den Materialfluss optimieren, die Produktionsabläufe synchronisieren und sicherstellen, dass die Werkstücke in der richtigen Reihenfolge an den entsprechenden Stationen ankommen. Sie ermöglichen auch die Integration von Sensoren, die den Zustand und die Position der Transportwagen in Echtzeit erfassen.
Vorteile der Power and Free Fördertechnik
Die Power and Free Fördertechnik bietet eine Reihe von Vorteilen, die sie besonders in der Lackier- und Beschichtungsindustrie beliebt machen. Diese Vorteile umfassen:
- Hohe Flexibilität: Power and Free Systeme bieten eine außergewöhnliche Flexibilität, da sie es ermöglichen, verschiedene Werkstücke gleichzeitig zu transportieren und individuell zu steuern. Dies ist besonders in Produktionsumgebungen von Vorteil, in denen Werkstücke unterschiedlich lange Bearbeitungszeiten oder Bearbeitungswege erfordern. Die Möglichkeit, Werkstücke unabhängig voneinander zu stoppen, zu puffern oder zu beschleunigen, sorgt für eine optimale Nutzung der Produktionsressourcen.
- Effizientes Handling komplexer Prozesse: In der Lackierindustrie müssen Werkstücke oft mehrere Bearbeitungsschritte durchlaufen, wie die Vorbehandlung, das Lackieren und das Trocknen. Power and Free Systeme ermöglichen es, diese Schritte effizient zu koordinieren, indem sie die Werkstücke je nach Bedarf zwischen den Stationen hin- und hertransportieren und dabei Staus oder Verzögerungen vermeiden.
- Minimierung von Ausfallzeiten: Da das System es erlaubt, einzelne Transportwagen anzuhalten oder zu puffern, ohne den gesamten Produktionsfluss zu unterbrechen, werden Ausfallzeiten minimiert. Wenn an einer Station ein Problem auftritt, kann das System so angepasst werden, dass andere Werkstücke weiter bearbeitet werden, während das betroffene Werkstück angehalten oder umgeleitet wird.
- Energieeffizienz: Im Vergleich zu herkömmlichen Kettenfördersystemen, bei denen die gesamte Kette kontinuierlich bewegt wird, erfordert die Power and Free Technik weniger Energie, da nur die aktiven Bereiche des Systems Energie benötigen. Die Möglichkeit, den Transport von Werkstücken selektiv zu steuern, trägt dazu bei, den Energieverbrauch zu optimieren.
- Anpassbarkeit an unterschiedliche Produktionsumgebungen: Power and Free Systeme können leicht an verschiedene räumliche Gegebenheiten und Produktionsanforderungen angepasst werden. Das System kann sowohl in geraden als auch in kurvigen Streckenabschnitten installiert werden und ist in der Lage, Werkstücke in verschiedenen Höhen zu transportieren. Dies macht es ideal für die Integration in komplexe Produktionslinien, in denen Platz und Layout eine Herausforderung darstellen.
- Robustheit und Langlebigkeit: Power and Free Förderanlagen sind für den Einsatz in anspruchsvollen industriellen Umgebungen konzipiert und zeichnen sich durch ihre Robustheit und Langlebigkeit aus. Sie sind in der Lage, schwere Lasten zu transportieren und bieten eine hohe Zuverlässigkeit, selbst unter extremen Bedingungen wie Hitze, Feuchtigkeit oder chemischen Belastungen.
Komponenten der Power and Free Fördertechnik
Die Power and Free Fördertechnik setzt sich aus mehreren wesentlichen Komponenten zusammen, die jeweils eine spezifische Funktion im System erfüllen:
- Transportwagen: Die Transportwagen sind die Hauptkomponenten, die die Werkstücke tragen. Sie sind mit speziellen Haken oder Vorrichtungen ausgestattet, die an den Werkstücken befestigt werden. Die Transportwagen können je nach Anwendung unterschiedliche Größen und Tragfähigkeiten haben.
- Mitnehmer und Koppelmechanismen: Diese Komponenten verbinden den Power-Strang mit dem Free-Strang. Sie sorgen dafür, dass die Transportwagen bei Bedarf in Bewegung gesetzt oder gestoppt werden. Die Mitnehmer können so programmiert werden, dass sie die Transportwagen an bestimmten Stationen automatisch einklinken oder ausklinken.
- Weichen und Weichensteller: Weichen sind entscheidend für die Flexibilität des Systems, da sie es ermöglichen, die Transportwagen zwischen verschiedenen Streckenabschnitten umzuleiten. Weichensteller steuern die Position der Weichen und sorgen dafür, dass die Wagen in die richtige Richtung geleitet werden.
- Pufferstationen: Pufferstationen sind spezielle Bereiche innerhalb der Förderstrecke, in denen die Transportwagen angehalten werden können, um auf die Bearbeitung zu warten oder die Reihenfolge der Werkstücke anzupassen. Diese Stationen sind mit Sensoren ausgestattet, die die Position der Wagen überwachen und sicherstellen, dass das System reibungslos funktioniert.
- Steuerungssysteme: Die Steuerungssysteme überwachen den gesamten Förderprozess und sorgen für die reibungslose Koordination der verschiedenen Komponenten. Diese Systeme sind häufig computergestützt und ermöglichen die Programmierung und Anpassung des Förderablaufs an die spezifischen Produktionsanforderungen.
Anwendungen der Power and Free Fördertechnik
Die Power and Free Fördertechnik wird in einer Vielzahl von Industrien eingesetzt, darunter:
- Automobilindustrie: In der Automobilindustrie wird die Power and Free Technik häufig zur Förderung von Karosserien und Fahrzeugteilen durch Lackieranlagen, Schweißstationen und Montageprozesse eingesetzt. Die Flexibilität des Systems ermöglicht es, verschiedene Fahrzeugtypen gleichzeitig zu bearbeiten, was die Produktionseffizienz erheblich steigert.
- Luftfahrt: In der Luftfahrtindustrie wird die Power and Free Technik zur Handhabung von großen und schweren Komponenten wie Flugzeugrümpfen, Tragflächen und Triebwerkskomponenten verwendet. Die Möglichkeit, die Bewegungen der Werkstücke präzise zu steuern, ist in dieser Industrie von besonderer Bedeutung, da die Verarbeitung oft sehr komplex ist.
- Metallverarbeitung: In der Metallverarbeitungsindustrie wird die Power and Free Technik verwendet, um Werkstücke durch verschiedene Oberflächenbehandlungsprozesse zu transportieren, wie z. B. Pulverbeschichtung, Galvanisierung und Trocknung. Die Flexibilität des Systems ermöglicht es, die Werkstücke effizient zwischen den einzelnen Prozessen zu transportieren und den Produktionsfluss zu optimieren.
- Lackier- und Beschichtungsanlagen: Power and Free Systeme sind besonders in Lackier- und Beschichtungsanlagen weit verbreitet. Die Möglichkeit, die Werkstücke unabhängig voneinander zu transportieren und an verschiedenen Stationen anzuhalten, ist ideal für den Lackierprozess, bei dem unterschiedliche Trocknungszeiten und Bearbeitungsschritte erforderlich sind.
Fazit
Die Power and Free Fördertechnik ist ein äußerst vielseitiges und effizientes Fördersystem, das sich durch seine Flexibilität, Robustheit und Anpassungsfähigkeit an komplexe Produktionsanforderungen auszeichnet. Es bietet eine ideale Lösung für Industrien, die hohe Produktionsvolumen und eine Vielzahl von Bearbeitungsschritten erfordern. Mit der fortschreitenden Automatisierung und der Integration von Industrie 4.0-Technologien wird die Power and Free Technik in Zukunft eine noch wichtigere Rolle in der modernen industriellen Fertigung spielen.
Absaugung Lackierkabine
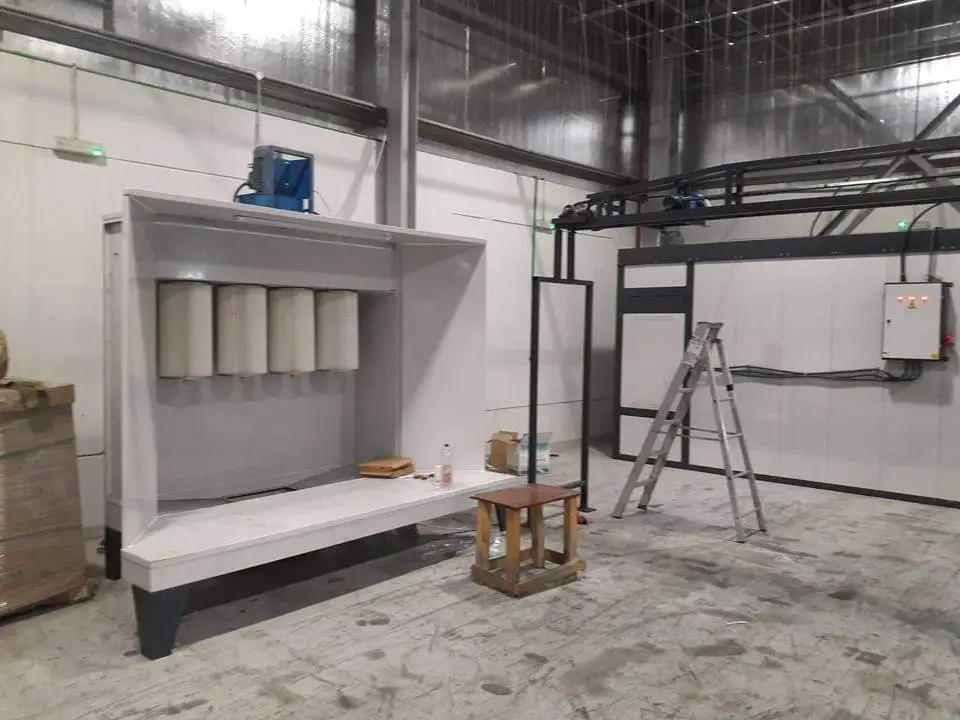
Die Absaugung in Lackierkabinen ist ein entscheidender Faktor für die Qualität des Lackierprozesses sowie für die Sicherheit und den Gesundheitsschutz der Mitarbeiter. Eine gut funktionierende Absauganlage sorgt dafür, dass schädliche Dämpfe, Partikel und überschüssige Lacke effizient entfernt werden und verhindert, dass sich diese in der Arbeitsumgebung ausbreiten. Dadurch wird nicht nur die Luftqualität verbessert, sondern auch eine gleichmäßige Lackierung der Werkstücke gewährleistet. In diesem Abschnitt wird erläutert, wie Absaugsysteme in Lackierkabinen funktionieren, welche Technologien verwendet werden, welche Herausforderungen bei der Installation und Wartung bestehen und welche aktuellen Trends und Innovationen es in diesem Bereich gibt.
Funktionsweise der Absaugung in Lackierkabinen
Die Absaugung in einer Lackierkabine hat die Aufgabe, überschüssige Lackpartikel und Lösungsmitteldämpfe aus der Kabine zu entfernen. Diese Stoffe entstehen während des Lackierprozesses, wenn Lack auf die Werkstücke aufgetragen wird, und können schädlich für die Gesundheit sein sowie die Qualität der Lackierung beeinträchtigen. Eine effektive Absaugung ist daher von großer Bedeutung, um eine saubere Arbeitsumgebung zu schaffen und gleichzeitig ein hochwertiges Lackierergebnis zu erzielen.
- Luftstrom und Filterung: Eine zentrale Komponente der Absauganlage ist der Luftstrom, der in der Lackierkabine erzeugt wird. Dieser Luftstrom bewegt sich typischerweise von oben nach unten oder von hinten nach vorne, je nach Konstruktion der Kabine. Die Luft wird in das System eingespeist, nimmt die überschüssigen Lackpartikel und Dämpfe auf und transportiert sie zu den Filtern, wo sie abgeschieden werden.
- Vorfilter: Der erste Schritt in der Filterung ist der Einsatz von Vorfiltern. Diese Filter sind dafür verantwortlich, größere Partikel wie Staub und Schmutz aus der Luft zu entfernen, bevor sie in die Hauptfilter gelangen. Dies schützt die empfindlicheren Filter vor einer schnellen Verstopfung und sorgt dafür, dass das System effizient arbeitet.
- Hauptfilter: Nach dem Vorfilter wird die Luft durch einen Hauptfilter geleitet, der die feinen Lackpartikel und Lösungsmitteldämpfe entfernt. Hier kommen häufig Kohlefilter oder andere spezielle Filtermaterialien zum Einsatz, die besonders dafür ausgelegt sind, flüchtige organische Verbindungen (VOC) und feinste Partikel aus der Luft zu filtern.
- Absauganlagen: Je nach Größe und Komplexität der Lackierkabine kann die Absaugung auf verschiedene Arten erfolgen. In den meisten Fällen wird die Luft durch spezielle Absaugkanäle an den Seiten oder am Boden der Kabine abgesaugt und durch ein System von Lüftern und Filtern geleitet. In einigen Fällen wird auch eine sogenannte Unterflurabsaugung eingesetzt, bei der die Luft direkt durch den Boden der Kabine abgesaugt wird, um eine noch effizientere Entfernung von Partikeln zu gewährleisten.
- Luftführung und Druckverhältnisse: Ein wichtiger Aspekt der Absaugung in Lackierkabinen ist die Kontrolle des Luftstroms und der Druckverhältnisse in der Kabine. Eine gleichmäßige Luftführung sorgt dafür, dass der Lack gleichmäßig auf das Werkstück aufgetragen wird und keine Turbulenzen oder Ablagerungen entstehen, die die Qualität der Lackierung beeinträchtigen könnten. In modernen Lackierkabinen wird der Luftstrom oft computergesteuert, um eine optimale Balance zwischen Luftzufuhr und Absaugung zu gewährleisten.
- Raumklimatisierung: Neben der reinen Absaugung ist auch die Klimatisierung der Lackierkabine von großer Bedeutung. Die Temperatur und Feuchtigkeit der Luft haben einen erheblichen Einfluss auf den Lackierprozess. Eine kontrollierte Klimatisierung sorgt dafür, dass der Lack gleichmäßig trocknet und keine ungewollten Effekte wie Blasenbildung oder Unebenheiten auftreten.
Vorteile einer effizienten Absaugung in Lackierkabinen
Die Vorteile einer gut funktionierenden Absauganlage in Lackierkabinen sind vielfältig und betreffen sowohl die Produktionsqualität als auch die Sicherheit der Mitarbeiter.
- Verbesserte Lackierqualität: Durch die effiziente Entfernung von überschüssigen Lackpartikeln und Lösungsmitteldämpfen wird sichergestellt, dass die Lackierung gleichmäßig und sauber auf die Werkstücke aufgetragen wird. Staub, Schmutz und andere Verunreinigungen, die sich andernfalls auf der Oberfläche absetzen könnten, werden effektiv entfernt, was die Gesamtqualität des Endprodukts deutlich verbessert.
- Gesundheitsschutz der Mitarbeiter: Lösungsmitteldämpfe und feine Lackpartikel können erhebliche gesundheitliche Risiken für die Mitarbeiter darstellen. Eine effiziente Absauganlage sorgt dafür, dass diese schädlichen Stoffe schnell aus der Kabine entfernt werden, bevor sie eingeatmet werden können. Dies reduziert das Risiko von Atemwegserkrankungen und anderen gesundheitlichen Problemen erheblich.
- Brandschutz: In Lackierkabinen besteht aufgrund der entzündlichen Lösungsmittel und Lacke ein erhöhtes Brandrisiko. Eine gute Absauganlage minimiert dieses Risiko, indem sie die Konzentration von brennbaren Dämpfen in der Luft reduziert. Zudem werden viele Absaugsysteme mit speziellen Brandschutzvorrichtungen ausgestattet, die im Falle eines Funkenfluges oder einer Überhitzung automatisch reagieren.
- Einhaltung von Umweltvorschriften: In vielen Ländern unterliegt die Luftreinhaltung in industriellen Produktionsanlagen strengen Vorschriften. Eine effiziente Absauganlage trägt dazu bei, diese Vorschriften einzuhalten, indem sie die Emissionen von schädlichen Substanzen reduziert. Moderne Filtersysteme können auch dazu beitragen, die Freisetzung von flüchtigen organischen Verbindungen (VOC) zu minimieren, die die Umwelt belasten könnten.
Herausforderungen bei der Installation und Wartung
Obwohl Absauganlagen in Lackierkabinen viele Vorteile bieten, gibt es auch einige Herausforderungen, die bei der Installation und Wartung dieser Systeme beachtet werden müssen.
- Anpassung an spezifische Anforderungen: Jede Lackierkabine ist anders, und die Absauganlage muss individuell an die jeweiligen Gegebenheiten angepasst werden. Dies erfordert eine genaue Planung und oft maßgeschneiderte Lösungen, um sicherzustellen, dass die Absaugung effizient und gleichmäßig arbeitet. Besonders in großen oder komplexen Kabinen kann dies eine Herausforderung darstellen.
- Filterwechsel und Wartung: Filtersysteme in Absauganlagen müssen regelmäßig gewartet und ausgetauscht werden, um eine optimale Leistung zu gewährleisten. Verstopfte oder verschmutzte Filter können die Effizienz des Systems erheblich beeinträchtigen und zu einer schlechten Luftqualität sowie einer geringeren Lackierqualität führen. Die Wartung dieser Systeme ist daher von entscheidender Bedeutung, um den reibungslosen Betrieb sicherzustellen.
- Kosten für Installation und Betrieb: Die Installation einer hochwertigen Absauganlage kann mit erheblichen Kosten verbunden sein, insbesondere wenn maßgeschneiderte Lösungen erforderlich sind. Auch die Betriebskosten, insbesondere der Energieverbrauch für die Lüfter und die regelmäßige Wartung, müssen berücksichtigt werden. Eine sorgfältige Planung und die Auswahl energieeffizienter Komponenten können jedoch helfen, diese Kosten langfristig zu reduzieren.
Trends und Innovationen in der Absaugungstechnologie
Wie in vielen anderen Bereichen der industriellen Produktion gibt es auch im Bereich der Absaugung von Lackierkabinen kontinuierliche technologische Weiterentwicklungen. Einige der aktuellen Trends und Innovationen umfassen:
- Energieeffiziente Lüftungssysteme: In vielen modernen Lackierkabinen werden mittlerweile energieeffiziente Lüftungssysteme eingesetzt, die den Energieverbrauch der Absauganlage reduzieren, ohne die Leistung zu beeinträchtigen. Dies wird oft durch den Einsatz von Frequenzumrichtern erreicht, die die Lüftergeschwindigkeit je nach Bedarf anpassen und somit den Energieverbrauch optimieren.
- Intelligente Steuerungssysteme: Die Integration von intelligenten Steuerungssystemen in die Absauganlage ermöglicht eine präzisere Überwachung und Steuerung des Luftstroms in der Lackierkabine. Diese Systeme nutzen Sensoren, um die Luftqualität in Echtzeit zu überwachen und den Luftstrom automatisch anzupassen, um die beste Balance zwischen Energieeffizienz und Absaugleistung zu erzielen.
- Modulare Filtersysteme: Eine weitere Innovation ist die Entwicklung modularer Filtersysteme, die je nach Bedarf erweitert oder ausgetauscht werden können. Diese Systeme bieten eine flexible Lösung für Unternehmen, die ihre Lackierprozesse an unterschiedliche Anforderungen anpassen müssen, ohne die gesamte Absauganlage erneuern zu müssen.
- Verbesserte Filtertechnologien: In den letzten Jahren wurden auch Fortschritte in der Filtertechnologie erzielt. Hochleistungsfilter, die feiner Partikel und Schadstoffe noch effektiver aus der Luft entfernen, sorgen für eine bessere Luftqualität und eine noch höhere Effizienz der Absauganlagen. Diese neuen Filtermaterialien sind zudem oft langlebiger und erfordern weniger Wartung, was die Betriebskosten senkt.
- Nachhaltigkeit und Umweltfreundlichkeit: In vielen Industrien wird der Fokus zunehmend auf nachhaltige Lösungen gelegt, und auch im Bereich der Absaugung in Lackierkabinen gibt es Bestrebungen, umweltfreundlichere Technologien zu entwickeln. Dies umfasst den Einsatz von recycelbaren Filtern, den Einsatz von emissionsarmen Technologien und die Optimierung der Energieeffizienz, um den ökologischen Fußabdruck der Produktionsanlagen zu reduzieren.
Fazit
Die Absaugung in Lackierkabinen spielt eine zentrale Rolle für die Qualität des Lackierprozesses, den Schutz der Mitarbeiter und die Einhaltung von Umweltvorschriften. Eine effiziente Absauganlage sorgt nicht nur für eine saubere und sichere Arbeitsumgebung, sondern trägt auch dazu bei, dass die Endprodukte von höchster Qualität sind. Moderne Technologien und innovative Lösungen bieten heute zahlreiche Möglichkeiten, die Effizienz und Nachhaltigkeit der Absaugung weiter zu verbessern. Unternehmen, die in hochwertige Absaugsysteme investieren, profitieren langfristig von einer höheren Produktivität, geringeren Ausfallzeiten und einem besseren Arbeitsumfeld.
EMS Pulverbeschichtungsanlagen

Unsere Pulverbeschichtungsanlage wird in Übereinstimmung mit den globalen fortschrittlichen Standards hergestellt und wurden mit vollem Vertrauen sowohl auf dem heimischen als auch auf dem weltweiten Markt bevorzugt.
Unsere Kapazität ist täglich gewachsen, wobei die Kundenzufriedenheit zusammen mit unserem gemeinsamen Vertriebs- und Servicenetz an erster Stelle steht.
Unser Unternehmen ist ein führendes türkisches Unternehmen, das sich auf die Herstellung von „Elektrostatischen Pulverbeschichtungsanlagen und kompletten Lackiersystemen“ mit 20 Jahren Wissen und praktischer Erfahrung spezialisiert hat.
Alle unsere Maschinen sind CE-gekennzeichnet, garantiert und können von potenziellen Kunden persönlich besichtigt werden. Es gibt auch Bilder und Videos auf dieser Seite, die die verwendeten Maschinen zeigen.
Wir entwerfen, fertigen und montieren Pulverbeschichtungsöfen, automatische und manuelle Kabinen, automatische und manuelle Pulverbeschichtungsanlagen, Pistolen, automatische und Stangentransfer-Pulverbeschichtungslinien, Pulverbeschichtungsfilter und Ersatzteile für Pulverbeschichtungspistolen