
Absaugwände: Die Pulverbeschichtung ist ein weit verbreitetes Verfahren zur Oberflächenveredelung von Metallteilen und anderen Materialien. Im Gegensatz zur herkömmlichen Nasslackierung wird bei der Pulverbeschichtung ein trockener Pulverlack auf die Oberfläche aufgetragen, der anschließend bei hohen Temperaturen in speziellen Öfen geschmolzen und vernetzt wird. Dies führt zu einer robusten, widerstandsfähigen Beschichtung, die sowohl funktionale als auch ästhetische Vorteile bietet.
Das Verfahren der Pulverbeschichtung hat in den letzten Jahrzehnten erheblich an Bedeutung gewonnen, insbesondere in Industrien wie der Automobilherstellung, der Architektur und im Maschinenbau. Die Hauptgründe dafür liegen in der hohen Effizienz, den geringen Umweltbelastungen und der exzellenten Haltbarkeit der Beschichtung.
Power and Free Fördersystem
Die Pulverbeschichtung bietet eine Reihe von Vorteilen gegenüber traditionellen Beschichtungsmethoden:
- Umweltfreundlichkeit: Da keine Lösungsmittel verwendet werden, ist die Pulverbeschichtung wesentlich umweltfreundlicher. Der Einsatz von Pulverbeschichtungsanlagen reduziert die Emissionen von flüchtigen organischen Verbindungen (VOCs) und minimiert die Abfallmengen.
- Haltbarkeit: Die Pulverbeschichtung ist extrem widerstandsfähig gegenüber mechanischen Belastungen, Korrosion, Chemikalien und Witterungseinflüssen. Dies macht sie ideal für Anwendungen, bei denen eine hohe Beständigkeit erforderlich ist, wie zum Beispiel bei der Felgen Pulverbeschichtung.
- Effizienz: Der Pulverlack kann direkt aufgetragen werden, ohne dass mehrere Schichten erforderlich sind. Dies spart Zeit und Kosten. Zudem können überschüssige Pulverpartikel in den meisten Pulverbeschichtungsanlagen recycelt und wiederverwendet werden.
- Vielfältige Anwendungsmöglichkeiten: Pulverbeschichtungen sind in einer breiten Palette von Farben und Oberflächenstrukturen verfügbar. Sie bieten nicht nur Schutz, sondern auch ästhetische Vorteile, die in vielen Industriezweigen geschätzt werden.
Anwendungsbereiche
Pulverbeschichtungen finden in zahlreichen Industriebereichen Anwendung:
- Automobilindustrie: Hier wird die Pulverbeschichtung unter anderem für Karosserieteile, Felgen und Fahrwerksteile eingesetzt, um eine langlebige und korrosionsbeständige Oberfläche zu gewährleisten.
- Architektur und Bauwesen: Pulverbeschichtungen kommen bei der Veredelung von Aluminiumprofilen, Fassadenelementen und Geländern zum Einsatz, wo sowohl eine ansprechende Optik als auch eine hohe Witterungsbeständigkeit gefragt sind.
- Maschinenbau: In diesem Bereich werden Maschinenteile, Werkzeuge und industrielle Anlagen pulverbeschichtet, um sie gegen Verschleiß und Korrosion zu schützen.
- Elektronik und Haushaltsgeräte: Auch in der Herstellung von Gehäusen für elektronische Geräte und Haushaltsgeräten spielt die Pulverbeschichtung eine wichtige Rolle.
Übersicht der Ausrüstung und Technologien
Um eine Pulverbeschichtung durchzuführen, sind verschiedene Arten von Ausrüstungen erforderlich:
- Pulverbeschichtungsanlagen: Diese Anlagen sind für das gleichmäßige Auftragen des Pulvers auf die zu beschichtenden Objekte verantwortlich. Sie sind in verschiedenen Ausführungen erhältlich, darunter Batch-Öfen und Durchlaufanlagen.
- Pulverbeschichtungskabinen: Diese speziell konzipierten Kabinen bieten eine kontrollierte Umgebung für das Auftragen des Pulvers, wobei die überschüssigen Pulverpartikel effizient abgesaugt und recycelt werden können.
- Pulverpistolen: Diese Geräte laden das Pulver elektrostatisch auf und sorgen dafür, dass es gleichmäßig auf der Oberfläche haftet.
- Öfen für Pulverbeschichtung: In diesen Öfen wird die beschichtete Oberfläche erhitzt, sodass das Pulver schmilzt und eine feste, schützende Schicht bildet.
- Absaugwände und mobile Absauganlagen: Diese Systeme gewährleisten eine saubere Arbeitsumgebung, indem sie überschüssiges Pulver und Dämpfe effizient entfernen.
Diese Einführung bietet einen Überblick über die Grundlagen der Pulverbeschichtung, ihre Vorteile und Anwendungsbereiche sowie die dafür notwendige Ausrüstung. Im nächsten Abschnitt werde ich detaillierter auf die verschiedenen Typen von Pulverbeschichtungsanlagen und deren spezifische Anwendungen eingehen.
Abschnitt 2: Pulverbeschichtungsanlagen – Typen und Anwendungen

Pulverbeschichtungsanlagen für verschiedene Branchen
Pulverbeschichtungsanlagen sind essenzielle Werkzeuge in vielen Industrien, da sie eine effiziente und qualitativ hochwertige Beschichtung von Oberflächen ermöglichen. Diese Anlagen gibt es in zahlreichen Ausführungen, die je nach Anwendungsbereich und Produktionsvolumen variieren. Hier ist ein Überblick über die wichtigsten Typen von Pulverbeschichtungsanlagen und deren spezifische Anwendungen:
- Batch-Öfen: Diese Anlagen sind ideal für kleinere Produktionschargen oder spezielle Anwendungen, bei denen eine hohe Flexibilität erforderlich ist. Batch-Öfen werden häufig in Werkstätten eingesetzt, die individuelle Aufträge abwickeln, wie z. B. das Beschichten von Felgen oder Kleinteilen. Ein Beispiel hierfür ist der Pulverbeschichtung Ofen, der eine präzise Temperaturkontrolle und gleichmäßige Wärmeverteilung bietet.
- Durchlaufanlagen: Für größere Produktionsvolumina und kontinuierliche Beschichtungsprozesse sind Durchlaufanlagen die beste Wahl. Diese Anlagen sind in der Lage, große Mengen an Bauteilen in einem kontinuierlichen Fluss zu beschichten, was die Effizienz erheblich steigert. Durchlaufanlagen finden häufig in der Automobil- und Haushaltsgeräteindustrie Anwendung, wo hohe Stückzahlen mit gleichbleibender Qualität beschichtet werden müssen.
- Pulverbeschichtungskabinen: Diese Kabinen sind entscheidend für die Kontrolle des Beschichtungsprozesses. Sie ermöglichen es, das Pulver präzise und sauber aufzutragen, während überschüssiges Pulver aufgefangen und recycelt wird. Es gibt verschiedene Ausführungen, darunter stationäre und mobile Kabinen, die je nach Bedarf eingesetzt werden können.
- Automatische Lackieranlagen: Diese hochmodernen Anlagen automatisieren den gesamten Beschichtungsprozess, von der Pulveraufbringung bis zum Aushärten. Automatische Lackieranlagen sind besonders in Großindustrien beliebt, da sie eine gleichbleibende Qualität bei hoher Produktionsgeschwindigkeit gewährleisten. Sie sind mit modernen Steuerungssystemen ausgestattet, die den Prozess optimieren und den Materialeinsatz minimieren.
Spezielle Anlagen: Batch-Öfen, Durchlaufanlagen und Pulverpistolen
Innerhalb der breiten Palette von Pulverbeschichtungsanlagen gibt es einige spezialisierte Technologien, die auf spezifische Anforderungen zugeschnitten sind:
- Batch-Öfen: Diese Öfen sind speziell für kleinere Chargen konzipiert und bieten die Flexibilität, verschiedene Arten von Pulverbeschichtungen zu verarbeiten. Hersteller von Batch-Öfen legen großen Wert auf die Effizienz und Energieeinsparung ihrer Produkte, um den Betriebskosten entgegenzuwirken. Typischerweise werden Batch-Öfen in Werkstätten und kleineren Produktionsanlagen eingesetzt, wo Flexibilität und Vielseitigkeit gefragt sind.
- Durchlaufanlagen: Diese Anlagen sind auf die Massenproduktion ausgelegt und ermöglichen einen kontinuierlichen Fluss von Werkstücken durch die Beschichtungslinie. Durchlaufanlagen sind mit hochentwickelten Fördersystemen ausgestattet, die sicherstellen, dass die Teile gleichmäßig beschichtet werden. Ein Beispiel hierfür ist das Power and Free Fördersystem, das eine unterbrechungsfreie Bewegung der Teile durch die Anlage ermöglicht.
- Pulverpistolen: Diese Geräte spielen eine zentrale Rolle beim Auftragen des Pulverlacks. Die Pulverpistole lädt das Pulver elektrostatisch auf, wodurch es gleichmäßig auf der Oberfläche haftet. Moderne Pulverpistolen sind mit fortschrittlichen Steuerungssystemen ausgestattet, die den Pulverfluss und die Aufladung präzise regulieren können. Dies führt zu einer gleichmäßigen Schichtdicke und einer hohen Oberflächenqualität.
Hersteller von Pulverbeschichtungsanlagen und deren Innovationen
Die Hersteller von Pulverbeschichtungsanlagen sind ständig bestrebt, ihre Produkte zu verbessern und an die steigenden Anforderungen der Industrie anzupassen. Zu den wichtigsten Innovationen gehören:
- Energieeffiziente Öfen: Die neuesten Pulverbeschichtungsöfen sind darauf ausgelegt, den Energieverbrauch zu minimieren und die Betriebskosten zu senken. Dies wird durch den Einsatz moderner Isolationsmaterialien und effizienter Heizsysteme erreicht.
- Automatisierte Steuerungssysteme: Die Integration von automatisierten Steuerungssystemen ermöglicht eine präzise Kontrolle über den Beschichtungsprozess. Diese Systeme können Parameter wie Temperatur, Luftstrom und Pulvermengen in Echtzeit anpassen, um optimale Ergebnisse zu gewährleisten.
- Modulare Anlagen: Viele Hersteller bieten modulare Pulverbeschichtungsanlagen an, die es den Betreibern ermöglichen, ihre Anlagen je nach Bedarf zu erweitern oder anzupassen. Diese Flexibilität ist besonders in schnelllebigen Industrien von Vorteil, wo sich die Produktionsanforderungen häufig ändern.
- Nachhaltige Lösungen: Im Zuge der steigenden Nachfrage nach umweltfreundlichen Produktionsverfahren setzen Hersteller auf nachhaltige Lösungen, wie z. B. die Verwendung von recycelbaren Pulvern und energieeffizienten Prozessen. Einige Anlagen sind sogar darauf ausgelegt, die Emissionen von Schadstoffen zu minimieren, was sie besonders umweltfreundlich macht.
Diese Vielfalt an Anlagen und Technologien ermöglicht es Unternehmen, die für ihre spezifischen Bedürfnisse am besten geeigneten Systeme auszuwählen. Dies stellt sicher, dass die beschichteten Produkte höchsten Qualitätsstandards entsprechen und gleichzeitig effizient und umweltfreundlich produziert werden.
Abschnitt 3: Entfernung von Pulverbeschichtung
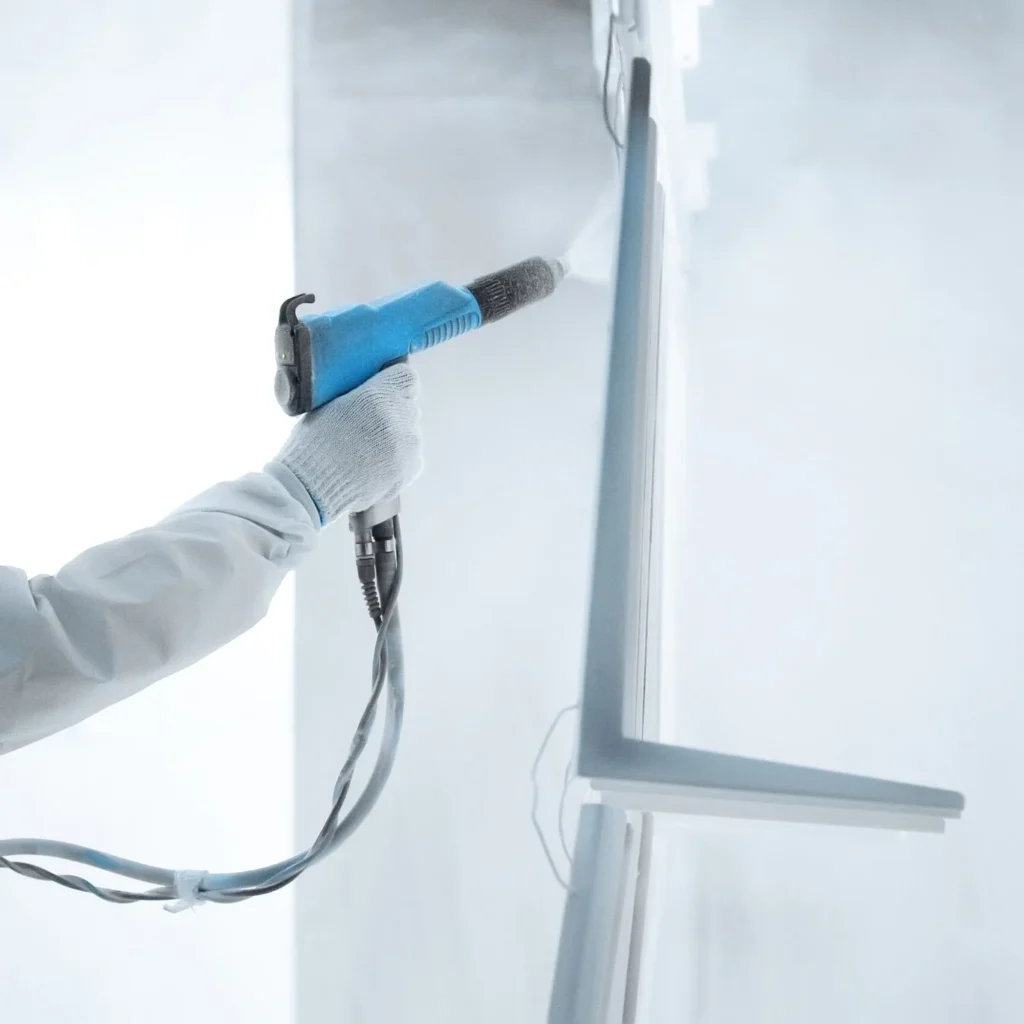
Mechanische und chemische Verfahren zur Entfernung von Pulverbeschichtung
Die Entfernung von Pulverbeschichtungen kann aus verschiedenen Gründen erforderlich sein, sei es zur Überarbeitung eines Werkstücks, zur Fehlerkorrektur oder zur Vorbereitung einer neuen Beschichtung. Es gibt mehrere Verfahren, um Pulverbeschichtungen zu entfernen, die in mechanische und chemische Methoden unterteilt werden können.
Mechanische Verfahren:
- Sandstrahlen: Beim Sandstrahlen wird ein Abrasivmittel, wie Sand oder Glasperlen, unter hohem Druck auf die beschichtete Oberfläche geschossen. Dieses Verfahren ist effektiv bei der Entfernung von Pulverbeschichtungen, besonders bei Metallen. Es ist jedoch ein abrasives Verfahren, das die Oberfläche des Werkstücks beschädigen kann, weshalb es hauptsächlich für robuste Materialien wie Stahl oder Aluminiumfelgen verwendet wird.
- Strahlen mit Trockeneis: Eine weniger abrasive Alternative zum Sandstrahlen ist das Strahlen mit Trockeneis. Dabei werden Trockeneispartikel auf die beschichtete Oberfläche geschossen. Diese Partikel sublimieren (verwandeln sich von fest in gasförmig) beim Aufprall, was zu einer spröden Ablösung der Pulverbeschichtung führt. Dieses Verfahren ist materialschonend und hinterlässt keine Rückstände.
- Abschleifen und Abkratzen: Diese Methode ist zwar einfach und kostengünstig, jedoch arbeitsintensiv und weniger präzise. Sie eignet sich für kleine Flächen oder Detailarbeiten, bei denen andere Verfahren zu aggressiv wären.
Chemische Verfahren:
- Abbeizmittel: Chemische Abbeizmittel, die speziell für Pulverbeschichtungen entwickelt wurden, können effektiv die Bindungen in der Beschichtung lösen und sie so ablösen. Diese Methode ist besonders geeignet für empfindliche Materialien, bei denen mechanische Verfahren zu Schäden führen könnten. Abbeizmittel erfordern jedoch besondere Sicherheitsvorkehrungen, da sie oft toxische Substanzen enthalten und sorgfältig entsorgt werden müssen.
- Lösemittelbäder: In speziellen Tauchbädern werden die beschichteten Teile in Lösungsmittel getaucht, die die Beschichtung aufweichen und ablösen. Diese Methode ist vor allem bei kompliziert geformten Werkstücken vorteilhaft, da das Lösungsmittel auch schwer zugängliche Bereiche erreicht. Der Einsatz von Lösemitteln muss jedoch unter Berücksichtigung von Umweltschutzauflagen und Arbeitssicherheitsstandards erfolgen.
Pyrolyseöfen und ihre Funktionsweise
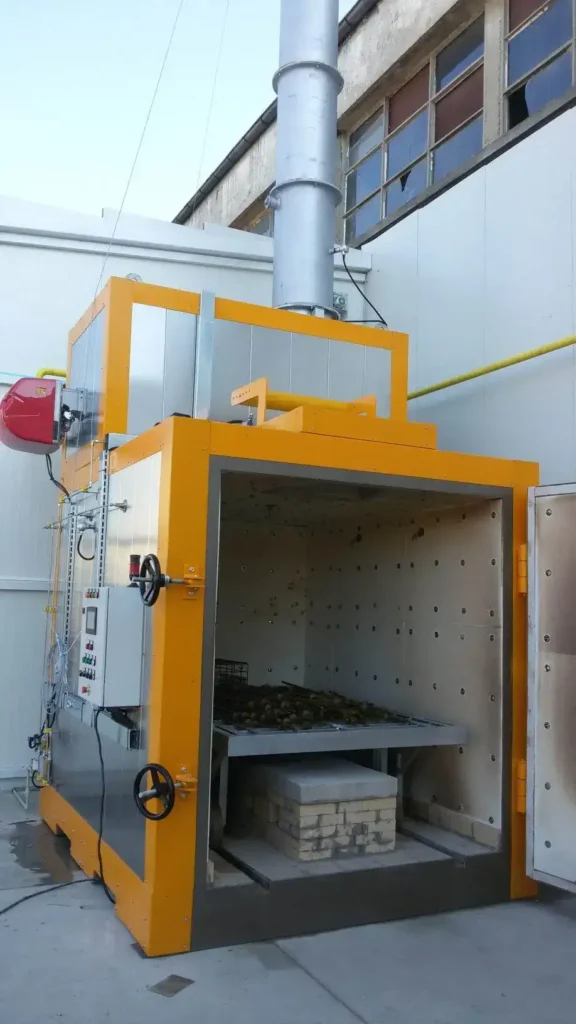
Eine fortschrittliche Methode zur Entfernung von Pulverbeschichtungen ist der Einsatz von Pyrolyseöfen. Diese Öfen arbeiten nach dem Prinzip der thermischen Zersetzung (Pyrolyse), bei der organische Substanzen, wie Pulverbeschichtungen, durch hohe Temperaturen in ihre Grundbestandteile zerlegt werden, ohne dass Sauerstoff zugeführt wird.
Funktionsweise von Pyrolyseöfen:
- Temperaturkontrolle: In einem Pyrolyseofen werden die beschichteten Werkstücke bei Temperaturen zwischen 400 und 600 Grad Celsius erhitzt. Die hohe Hitze führt dazu, dass die Pulverbeschichtung zu Ruß und gasförmigen Produkten zerfällt. Diese Rückstände werden dann in einem nachgeschalteten Nachverbrennungsprozess oxidiert und sicher abgeführt.
- Vorteile: Pyrolyseöfen bieten eine sehr gründliche und gleichmäßige Entfernung von Beschichtungen, ohne das zugrunde liegende Material zu beschädigen. Sie sind ideal für große Bauteile und komplexe Geometrien. Zudem ist das Verfahren umweltfreundlicher als viele chemische Alternativen, da die Rückstände größtenteils in ungiftige Gase umgewandelt werden.
- Anwendungen: Pyrolyseöfen werden in der Industrie häufig für die Reinigung von Lackiergehängen, Sprühbeschichtung-Anlagen oder anderen Werkzeugen verwendet, die regelmäßig von Pulverbeschichtungen befreit werden müssen. Auch in der Felgen Pulverbeschichtung spielt diese Methode eine Rolle, insbesondere bei der Vorbereitung von gebrauchten Felgen für eine neue Beschichtung.
Felgen entlacken: Methoden und Herausforderungen
Das Entlacken von Felgen ist eine spezifische Anwendung der Pulverbeschichtungsentfernung, die besondere Herausforderungen mit sich bringt. Felgen, insbesondere aus Aluminium, erfordern eine sorgfältige Behandlung, um Schäden zu vermeiden und eine hochwertige Oberfläche für die Neulackierung zu gewährleisten.
Häufig verwendete Methoden:
- Sandstrahlen: Wie bereits erwähnt, ist das Sandstrahlen eine effektive Methode zum Entfernen von Pulverbeschichtungen auf Felgen. Es bietet den Vorteil, dass es schnell und gründlich arbeitet. Allerdings muss der Druck und das verwendete Abrasivmittel sorgfältig gewählt werden, um die Felge nicht zu beschädigen.
- Chemische Abbeizmittel: Besonders bei empfindlichen Felgen aus Aluminium ist die Verwendung von chemischen Abbeizmitteln eine gängige Praxis. Diese Mittel sind speziell formuliert, um die Pulverbeschichtung zu lösen, ohne das Aluminium anzugreifen. Ein Nachteil dieser Methode ist der erforderliche Aufwand zur sicheren Entsorgung der Chemikalien.
- Pyrolyseöfen: Auch für Felgen ist der Einsatz von Pyrolyseöfen geeignet. Die thermische Zersetzung entfernt die Pulverbeschichtung vollständig und bereitet die Felge optimal für eine neue Beschichtung vor.
Herausforderungen beim Entlacken von Felgen:
- Materialschonung: Das Material der Felge muss geschützt werden, insbesondere bei Aluminiumfelgen, die empfindlicher auf mechanische Belastungen reagieren. Daher ist eine präzise Kontrolle der verwendeten Methoden notwendig.
- Oberflächenvorbereitung: Nach dem Entfernen der Beschichtung muss die Felge häufig erneut vorbereitet werden, um eine perfekte Haftung der neuen Beschichtung zu gewährleisten. Dies kann durch Sandstrahlen, Schleifen oder chemische Vorbehandlung erfolgen.
- Umweltauflagen: Die Entlackung von Felgen, besonders mit chemischen Mitteln, unterliegt strengen Umweltauflagen. Unternehmen müssen sicherstellen, dass alle Verfahren umweltgerecht und sicher für die Arbeiter durchgeführt werden.
Dieser Abschnitt beleuchtet die verschiedenen Methoden zur Entfernung von Pulverbeschichtungen, mit einem besonderen Fokus auf die Verwendung von Pyrolyseöfen und die Herausforderungen bei der Entlackung von Felgen. Der nächste Abschnitt wird sich intensiv mit den Öfen für die Pulverbeschichtung befassen, einschließlich ihrer Typen, Anwendungen und der neuesten Innovationen in diesem Bereich.
Abschnitt 4: Öfen für die Pulverbeschichtung
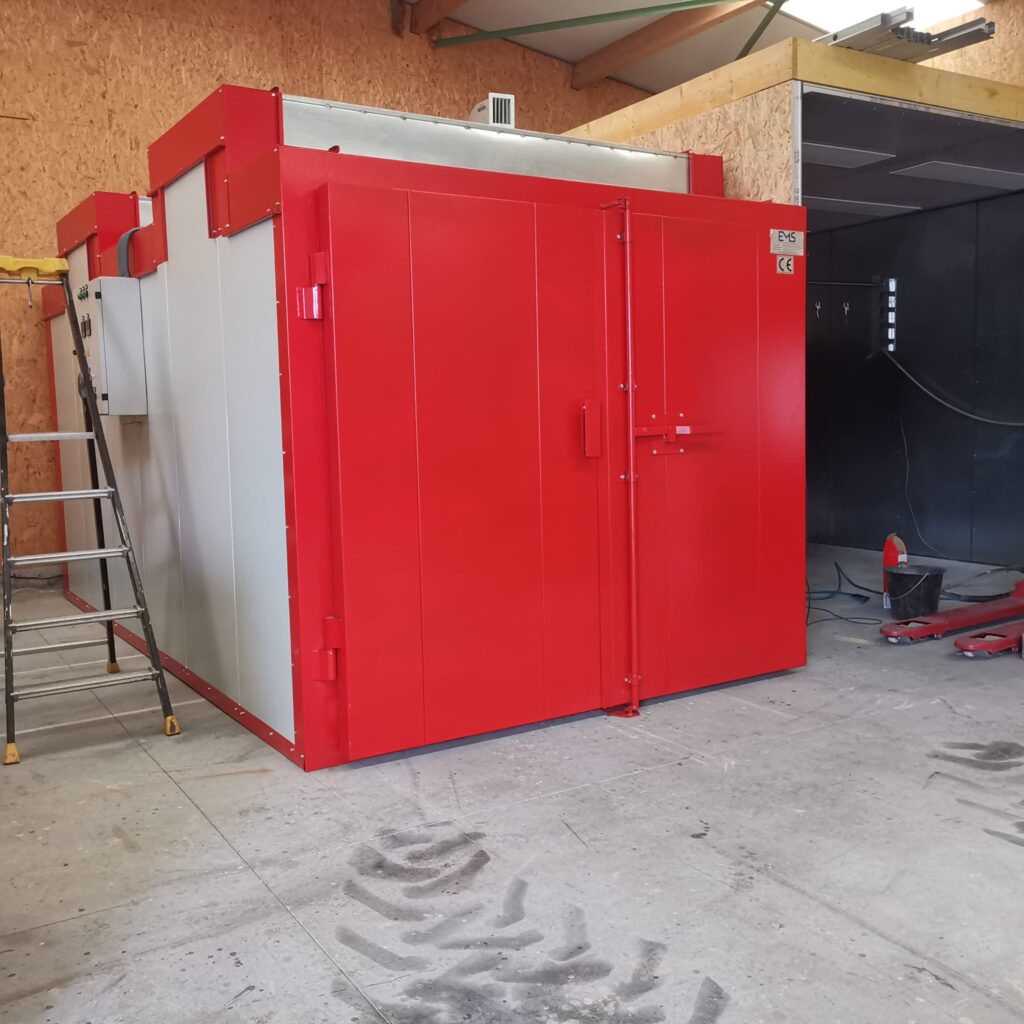
Trocknungsöfen: Technologie und Einsatzgebiete
Trocknungsöfen sind eine wesentliche Komponente im Pulverbeschichtungsprozess, da sie den entscheidenden Schritt des Aushärtens oder Einbrennens der Beschichtung ermöglichen. Die Auswahl des richtigen Trocknungsofens hängt von mehreren Faktoren ab, darunter die Art der beschichteten Materialien, die Produktionsvolumina und die spezifischen Anforderungen der Beschichtung.
Technologie von Trocknungsöfen:
- Konvektionstrocknung: Die häufigste Methode in Trocknungsöfen ist die Konvektion, bei der heiße Luft über die beschichteten Werkstücke zirkuliert, um die Oberfläche gleichmäßig zu erhitzen und die Pulverbeschichtung zu vernetzen. Diese Öfen sind besonders effektiv für große Werkstücke oder solche mit komplexen Geometrien, da sie eine gleichmäßige Temperaturverteilung gewährleisten.
- Infrarottrocknung: Infrarot-Trocknungsöfen nutzen die Strahlungswärme, um die Beschichtung direkt zu erhitzen. Diese Methode ist schneller als die Konvektionstrocknung und kann besonders bei dünneren Schichten oder empfindlichen Materialien von Vorteil sein. Infrarotöfen sind in der Regel kompakter und energieeffizienter, da sie gezielt und schnell Wärme abgeben.
- Kombinationsöfen: Einige moderne Trocknungsöfen kombinieren Konvektion und Infrarotstrahlung, um die Vorteile beider Technologien zu nutzen. Diese Öfen bieten Flexibilität und Effizienz und können an verschiedene Beschichtungsanforderungen angepasst werden.
Einsatzgebiete von Trocknungsöfen:
- Automobilindustrie: Hier werden Trocknungsöfen verwendet, um Karosserieteile, Felgen und andere Komponenten zu beschichten. Aufgrund der hohen Anforderungen an die Haltbarkeit und das Erscheinungsbild der Beschichtungen sind präzise kontrollierte Trocknungsprozesse unerlässlich.
- Maschinenbau und Metallverarbeitung: In diesen Industrien sind Trocknungsöfen für die Beschichtung von Maschinenkomponenten und Werkzeugen unverzichtbar. Die Beschichtung muss extremen Bedingungen wie hoher Belastung und Korrosion standhalten, was durch eine sorgfältige Trocknung gewährleistet wird.
- Möbel- und Haushaltsgeräteproduktion: Hier werden Trocknungsöfen für die Beschichtung von Metallrahmen, Gehäusen und anderen Bauteilen eingesetzt, die ein ansprechendes Finish und Schutz vor alltäglichen Belastungen benötigen.
Einbrennöfen und ihre Bedeutung in der Pulverbeschichtung
Einbrennöfen, auch als Aushärteöfen bekannt, spielen eine zentrale Rolle im Pulverbeschichtungsprozess. Sie sorgen dafür, dass der aufgetragene Pulverlack zu einer harten, widerstandsfähigen Beschichtung wird. Der Einbrennprozess ist entscheidend für die Qualität und die Langlebigkeit der Beschichtung.
Funktionsweise von Einbrennöfen:
- Erwärmung und Aushärtung: In einem Einbrennofen wird das Werkstück auf eine Temperatur erhitzt, bei der das Pulver zu schmelzen beginnt und sich zu einer gleichmäßigen Schicht vernetzt. Diese Temperatur liegt in der Regel zwischen 160 und 200 Grad Celsius, abhängig vom verwendeten Pulverlack und dem zu beschichtenden Material.
- Präzise Temperaturkontrolle: Die genaue Kontrolle der Temperatur und der Einbrennzeit ist entscheidend für die Qualität der Beschichtung. Überhitzung kann zu Blasenbildung oder Verbrennungen führen, während eine zu niedrige Temperatur eine unzureichende Aushärtung zur Folge haben kann, was die Haltbarkeit der Beschichtung beeinträchtigt.
- Luftzirkulation und Wärmeverteilung: Moderne Einbrennöfen sind so konzipiert, dass sie eine gleichmäßige Luftzirkulation und Wärmeverteilung gewährleisten. Dies ist besonders wichtig bei der Beschichtung großer oder komplex geformter Werkstücke, um sicherzustellen, dass die gesamte Oberfläche gleichmäßig gehärtet wird.
Bedeutung von Einbrennöfen in verschiedenen Industrien:
- Automobil- und Luftfahrtindustrie: Hier werden Einbrennöfen verwendet, um Teile zu beschichten, die extremen Bedingungen standhalten müssen, wie etwa hohe Temperaturen, mechanische Belastungen und Korrosion. Die Beschichtung muss daher absolut gleichmäßig und fehlerfrei sein.
- Elektronik- und Haushaltsgeräteproduktion: In diesen Bereichen ist die ästhetische Qualität der Beschichtung ebenso wichtig wie ihre Funktionalität. Einbrennöfen sorgen dafür, dass Gehäuse, Rahmenteile und andere Komponenten ein hochwertiges Finish erhalten, das den täglichen Anforderungen gerecht wird.
- Industrielle Ausrüstungen: Für Maschinen und Anlagen, die in anspruchsvollen Umgebungen eingesetzt werden, ist die Pulverbeschichtung oft der erste Schutz gegen Verschleiß und Korrosion. Einbrennöfen spielen hier eine entscheidende Rolle, um sicherzustellen, dass die Beschichtung langlebig und widerstandsfähig ist.
Pulverbeschichtungsöfen: Von kleinen Anlagen bis zu industriellen Lösungen
Pulverbeschichtungsöfen sind in vielen verschiedenen Größen und Ausführungen erhältlich, um den Anforderungen unterschiedlichster Produktionsumgebungen gerecht zu werden. Von kleinen Werkstätten bis hin zu großen industriellen Anlagen gibt es für jede Anwendung die passende Lösung.
Kleine Pulverbeschichtungsöfen:
- Kompakte Öfen für kleine Chargen: Diese Öfen sind ideal für kleine Werkstätten, die Einzelstücke oder kleine Serien beschichten. Sie sind kostengünstig und einfach zu bedienen, wodurch sie sich besonders für kleinere Unternehmen oder spezialisierte Werkstätten eignen.
- Flexible Batch-Öfen: Batch-Öfen bieten Flexibilität und Vielseitigkeit, da sie für eine Vielzahl von Werkstücken und Beschichtungen geeignet sind. Sie sind besonders beliebt bei Unternehmen, die häufig wechselnde oder maßgeschneiderte Aufträge abwickeln.
Industrielle Pulverbeschichtungsöfen:
- Großöfen für Massenproduktion: Diese Öfen sind darauf ausgelegt, große Mengen von Werkstücken in kurzer Zeit zu beschichten. Sie sind häufig Teil automatisierter Produktionslinien und bieten hohe Durchsatzraten bei gleichbleibender Qualität.
- Spezialisierte Anlagen: In bestimmten Industrien, wie der Automobilproduktion, sind spezialisierte Pulverbeschichtungsöfen im Einsatz, die auf die spezifischen Anforderungen der jeweiligen Produktion abgestimmt sind. Dazu gehören z. B. Öfen mit speziellen Heiztechnologien oder solchen, die besonders große oder komplexe Werkstücke verarbeiten können.
Hersteller von Batch-Öfen und maßgeschneiderte Lösungen:
- Führende Hersteller: Hersteller von Pulverbeschichtungsöfen bieten eine Vielzahl von Modellen an, die sowohl standardisierte als auch maßgeschneiderte Lösungen umfassen. Unternehmen, die spezielle Anforderungen haben, können Öfen bestellen, die genau auf ihre Produktionsprozesse abgestimmt sind.
- Maßgeschneiderte Lösungen: Für Unternehmen, die einzigartige Anforderungen haben, bieten viele Hersteller maßgeschneiderte Öfen an, die genau auf die spezifischen Bedürfnisse abgestimmt sind. Dies kann z. B. besondere Anforderungen an die Größe, die Heiztechnologie oder die Automatisierung betreffen.
Mit diesen Informationen über die verschiedenen Arten von Öfen und deren Anwendungen wird deutlich, dass die Wahl des richtigen Ofens entscheidend für die Qualität und Effizienz des Pulverbeschichtungsprozesses ist.
Abschnitt 5: Lackierkabinen und Absauganlagen
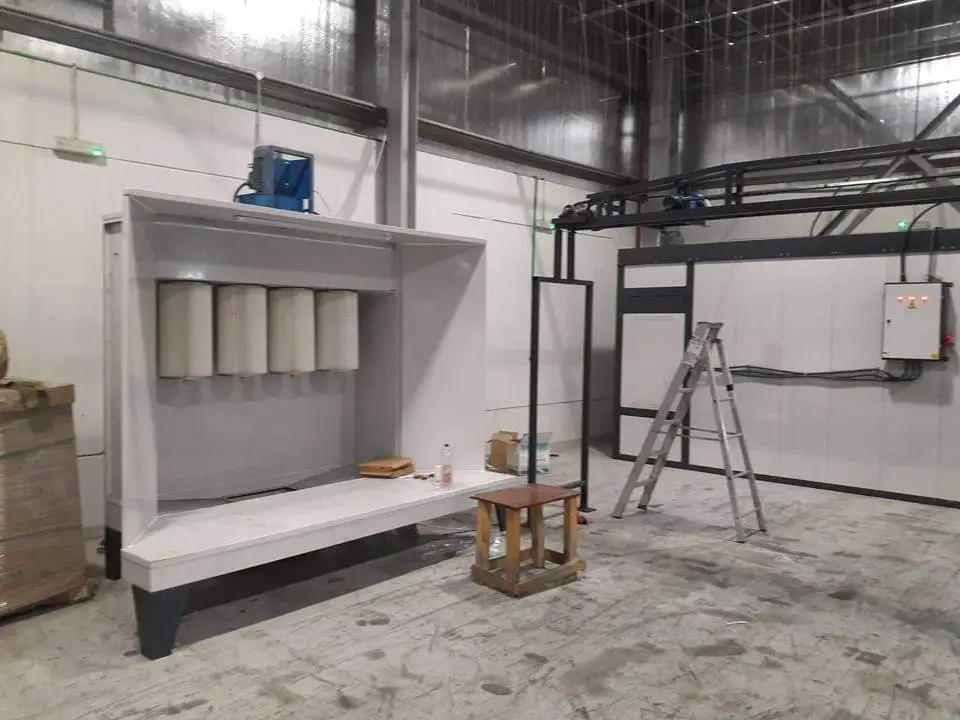
Pulverbeschichtungskabinen: Funktion und Aufbau
Pulverbeschichtungskabinen sind zentrale Elemente in der Pulverbeschichtung, da sie eine kontrollierte Umgebung bieten, in der das Pulver gleichmäßig und präzise aufgetragen werden kann. Der Aufbau und die Funktion einer Pulverbeschichtungskabine sind entscheidend für die Qualität des Beschichtungsprozesses sowie für die Sicherheit und Effizienz des Betriebs.
Funktion einer Pulverbeschichtungskabine:
- Kontrollierte Umgebung: Die Kabine sorgt dafür, dass das Pulver ausschließlich auf das Werkstück aufgetragen wird und nicht in die Umgebung gelangt. Dies minimiert den Pulververlust und verhindert eine Kontamination anderer Bereiche der Produktion.
- Effiziente Pulverrückgewinnung: Überschüssiges Pulver, das nicht auf dem Werkstück haftet, wird in den meisten Pulverbeschichtungskabinen durch ein Absaugsystem erfasst und recycelt. Dies reduziert den Materialverbrauch und die Betriebskosten erheblich.
- Sicherheitsvorkehrungen: Moderne Pulverbeschichtungskabinen sind mit Sicherheitssystemen ausgestattet, die den Bediener vor Gefahren wie explosionsfähigen Pulvermengen oder elektrostatischen Entladungen schützen. Dazu gehören automatische Abschaltungen und spezielle Belüftungssysteme.
Aufbau einer Pulverbeschichtungskabine:
- Kabinenwände und -decke: Die Kabinen sind in der Regel aus robusten, pulverbeschichteten Stahlplatten oder anderen feuerfesten Materialien gefertigt, die eine lange Lebensdauer und hohe Sicherheit bieten.
- Filter- und Absaugsysteme: Das Herzstück der Kabine sind die Filter- und Absaugsysteme, die dafür sorgen, dass überschüssiges Pulver effizient abgesaugt und gefiltert wird. Diese Systeme sind oft modular aufgebaut, sodass sie an die spezifischen Bedürfnisse der Produktion angepasst werden können.
- Beleuchtung: Eine gute Beleuchtung ist in der Kabine unerlässlich, um sicherzustellen, dass der Bediener das Pulver gleichmäßig auftragen kann. Viele Kabinen sind mit speziellen LED-Leuchten ausgestattet, die eine optimale Ausleuchtung der Arbeitsfläche bieten.
- Fördersysteme: Je nach Anwendungsbereich kann die Kabine mit einem internen Fördersystem ausgestattet sein, das die Werkstücke automatisch durch die Kabine bewegt. Dies ist besonders nützlich in automatisierten Produktionslinien, in denen eine hohe Durchsatzrate erforderlich ist.
Automatische Lackieranlagen vs. manuelle Systeme

In der Pulverbeschichtungsindustrie gibt es zwei Haupttypen von Beschichtungssystemen: automatische und manuelle Lackieranlagen. Beide Systeme haben ihre eigenen Vor- und Nachteile, und die Wahl des richtigen Systems hängt von den spezifischen Anforderungen der Produktion ab.
Automatische Lackieranlagen:
- Vollautomatisierte Prozesse: Automatische Lackieranlagen sind darauf ausgelegt, den gesamten Beschichtungsprozess ohne menschliches Eingreifen durchzuführen. Dies umfasst das Auftragen des Pulvers, das Aushärten im Ofen und in einigen Fällen auch die chemische Vorbehandlung.
- Hohe Effizienz und Konsistenz: Der größte Vorteil automatischer Anlagen ist die hohe Effizienz und Konsistenz der Beschichtungen. Durch den Einsatz von Robotern und automatisierten Steuerungssystemen wird eine gleichmäßige Beschichtung aller Werkstücke gewährleistet, unabhängig von der Komplexität der Geometrie.
- Anwendungen in der Großproduktion: Automatische Lackieranlagen sind besonders in Industrien mit hohen Produktionsvolumina verbreitet, wie z. B. in der Automobilindustrie oder der Herstellung von Haushaltsgeräten. Diese Anlagen ermöglichen eine schnelle und kostengünstige Beschichtung großer Stückzahlen.
Manuelle Lackieranlagen:
- Flexibilität und Vielseitigkeit: Manuelle Lackieranlagen bieten eine hohe Flexibilität, da der Bediener den Beschichtungsprozess anpassen kann. Dies ist besonders vorteilhaft bei kleineren Chargen, Einzelstücken oder speziellen Projekten, die eine individuelle Handhabung erfordern.
- Niedrigere Investitionskosten: Manuelle Systeme sind in der Regel günstiger in der Anschaffung und erfordern weniger komplexe Technik als automatische Anlagen. Dies macht sie attraktiv für kleinere Unternehmen oder Werkstätten, die keine großen Produktionsvolumina bearbeiten müssen.
- Anwendungen in der Spezialproduktion: Manuelle Lackieranlagen werden häufig in spezialisierten Werkstätten eingesetzt, wo es auf Detailarbeit und Anpassungsfähigkeit ankommt, wie z. B. bei der Felgen Pulverbeschichtung oder der Beschichtung von Kleinteilen.
Mobile Absaugwände und ihre Einsatzmöglichkeiten

Mobile Absaugwände sind eine flexible Lösung, die in vielen Bereichen der Pulverbeschichtung und anderen industriellen Anwendungen eingesetzt wird. Sie dienen dazu, überschüssiges Pulver oder Staubpartikel abzusaugen und somit eine saubere und sichere Arbeitsumgebung zu gewährleisten.
Funktion von mobilen Absaugwänden:
- Effiziente Partikelabsaugung: Mobile Absaugwände sind mit leistungsstarken Filtern ausgestattet, die Partikel und Dämpfe aus der Luft entfernen. Dies sorgt für eine saubere Umgebung und schützt den Bediener vor gesundheitsschädlichen Substanzen.
- Einfache Positionierung: Durch ihre Mobilität können diese Wände flexibel an verschiedenen Stellen in der Werkstatt oder Produktionshalle aufgestellt werden. Dies ist besonders nützlich in dynamischen Arbeitsumgebungen, in denen der Standort der Beschichtungsvorgänge häufig wechselt.
- Platzsparend und flexibel: Mobile Absaugwände benötigen weniger Platz als fest installierte Systeme und können bei Bedarf schnell abgebaut und an einem anderen Ort wieder aufgebaut werden. Dies macht sie ideal für kleinere Werkstätten oder temporäre Beschichtungsstationen.
Einsatzmöglichkeiten:
- Kleinteile-Pulverbeschichtung: Mobile Absaugwände sind besonders nützlich bei der Beschichtung von kleinen Teilen, bei denen eine stationäre Kabine überdimensioniert wäre. Sie bieten eine kostengünstige und effiziente Lösung für die Handhabung von kleinen Produktionschargen.
- Temporäre Beschichtungsbereiche: In Werkstätten, die keine festen Beschichtungsstationen haben oder diese nur gelegentlich benötigen, bieten mobile Absaugwände eine praktische Lösung. Sie können bei Bedarf schnell eingerichtet und anschließend wieder verstaut werden.
- Zusätzliche Sicherheit: In großen Produktionshallen können mobile Absaugwände als zusätzliche Sicherheitsmaßnahme eingesetzt werden, um überschüssiges Pulver oder Staubpartikel aufzufangen, die nicht von den Hauptabsauganlagen erfasst werden.
Lackiergehänge: Bedeutung für den Beschichtungsprozess
Lackiergehänge spielen eine entscheidende Rolle im Pulverbeschichtungsprozess, da sie die Werkstücke während der Beschichtung sicher und stabil halten. Die richtige Wahl und Konfiguration der Lackiergehänge kann die Qualität der Beschichtung erheblich beeinflussen.
Aufbau und Funktion von Lackiergehängen:
- Stabile Halterung: Lackiergehänge sind so konstruiert, dass sie Werkstücke sicher halten, ohne deren Oberfläche zu beschädigen. Sie bestehen in der Regel aus robusten Materialien wie Edelstahl oder spezialbeschichtetem Stahl, um den Belastungen des Beschichtungsprozesses standzuhalten.
- Flexibilität und Anpassungsfähigkeit: Die Geometrie und Größe der Lackiergehänge kann an die spezifischen Anforderungen der zu beschichtenden Teile angepasst werden. Es gibt sowohl standardisierte Gehäuse als auch maßgeschneiderte Lösungen für komplexe oder ungewöhnlich geformte Werkstücke.
- Effizienzsteigerung: Durch den Einsatz von Lackiergehängen können mehrere Werkstücke gleichzeitig beschichtet werden, was die Effizienz des Prozesses steigert. Zudem ermöglichen sie eine gleichmäßige Beschichtung, da die Werkstücke in einer optimalen Position gehalten werden.
Bedeutung für den Beschichtungsprozess:
- Optimale Beschichtungsqualität: Ein gut gestaltetes Lackiergehänge stellt sicher, dass das Pulver gleichmäßig aufgetragen wird und alle Bereiche des Werkstücks erreicht. Dies minimiert das Risiko von ungleichmäßigen Schichtdicken oder Fehlstellen.
- Zeit- und Kostenersparnis: Da mehrere Werkstücke gleichzeitig beschichtet werden können und weniger manuelle Handhabung erforderlich ist, trägt der Einsatz von Lackiergehängen zur Reduzierung der Durchlaufzeiten und Kosten bei.
- Spezielle Anwendungen: In der Automobilindustrie, der Luftfahrt und anderen High-Tech-Bereichen, in denen die Beschichtungsqualität von entscheidender Bedeutung ist, sind spezialisierte Lackiergehänge unverzichtbar. Sie ermöglichen die präzise Positionierung und Fixierung von Werkstücken, die besonders hohe Anforderungen an die Beschichtung stellen.
Abschnitt 6: Fördertechnik in der Pulverbeschichtung

Transport-Schienensysteme für Boden- und Deckentransport
In der Pulverbeschichtung ist die effiziente Bewegung der Werkstücke durch die verschiedenen Prozessstufen entscheidend für eine gleichmäßige und hochwertige Beschichtung. Transport-Schienensysteme spielen dabei eine zentrale Rolle, da sie eine flexible und präzise Handhabung der Werkstücke ermöglichen.
Arten von Transport-Schienensystemen:
- Bodengeführte Schienensysteme: Diese Systeme sind besonders in Produktionsumgebungen verbreitet, in denen Platz eine Rolle spielt oder in denen schwere Werkstücke transportiert werden müssen. Bodengeführte Schienensysteme sind stabil und können große Lasten tragen. Sie sind ideal für Anwendungen, bei denen schwere oder sperrige Teile bewegt werden, wie etwa in der Automobilindustrie.
- Deckengeführte Schienensysteme: Diese Systeme bieten den Vorteil, dass sie den Boden frei lassen, was in beengten Produktionsumgebungen oder bei komplexen Werkstücken nützlich ist. Deckengeführte Schienensysteme ermöglichen eine nahtlose Integration in den Produktionsfluss und sind besonders in industriellen Anwendungen verbreitet, bei denen Platz und Zugänglichkeit kritisch sind.
Einsatzgebiete und Vorteile:
- Flexibilität: Schienensysteme bieten eine hohe Flexibilität, da sie an die spezifischen Anforderungen der Produktion angepasst werden können. Sie ermöglichen es, Werkstücke durch verschiedene Stationen wie Vorbehandlung, Beschichtung und Trocknung zu transportieren, ohne dass eine manuelle Handhabung erforderlich ist.
- Effizienzsteigerung: Durch die Automatisierung des Transports wird die Durchlaufzeit erheblich verkürzt. Schienensysteme sind oft mit Steuerungssystemen ausgestattet, die den Transport der Werkstücke synchronisieren und optimieren, was zu einer gleichmäßigen und effizienten Produktion führt.
- Sicherheitsaspekte: Die Verwendung von Schienensystemen reduziert das Risiko von Unfällen, da schwere Werkstücke sicher transportiert werden können, ohne dass sie manuell bewegt werden müssen. Dies ist besonders wichtig in Branchen wie der Automobilproduktion oder im Maschinenbau, wo große und schwere Teile häufig vorkommen.
Power and Free Förderer: Funktionsweise und Vorteile
Power and Free Förderer sind eine fortschrittliche Art von Fördersystemen, die eine besonders flexible und effiziente Bewegung der Werkstücke in der Pulverbeschichtung ermöglichen. Diese Systeme bieten eine Reihe von Vorteilen gegenüber traditionellen Fördersystemen, insbesondere in Produktionsumgebungen, in denen eine hohe Flexibilität und präzise Steuerung erforderlich sind.
Funktionsweise von Power and Free Förderern:
- Zwei-Schienen-System: Power and Free Förderer bestehen aus zwei Schienensystemen – einer „Power“-Schiene, die die Antriebskraft liefert, und einer „Free“-Schiene, auf der die Werkstücke bewegt werden. Dieses Design ermöglicht es, dass Werkstücke unabhängig voneinander transportiert werden können, was die Flexibilität im Produktionsprozess erhöht.
- Flexibler Stopp und Start: Eines der Hauptmerkmale von Power and Free Förderern ist die Fähigkeit, Werkstücke bei Bedarf anzuhalten und später wieder zu starten, ohne den gesamten Produktionsfluss zu unterbrechen. Dies ist besonders nützlich in komplexen Produktionslinien, wo verschiedene Prozesse unterschiedliche Taktzeiten erfordern.
- Vollständige Automatisierung: Power and Free Systeme können vollständig automatisiert betrieben werden, mit integrierten Steuerungssystemen, die den gesamten Produktionsprozess überwachen und steuern. Dies ermöglicht eine nahtlose Integration in bestehende Produktionsumgebungen und reduziert die Notwendigkeit manueller Eingriffe.
Vorteile von Power and Free Förderern:
- Hohe Flexibilität: Die Fähigkeit, Werkstücke unabhängig voneinander zu bewegen, bietet eine außergewöhnliche Flexibilität, insbesondere in Produktionslinien mit mehreren Prozessschritten oder unterschiedlichen Produktionsgeschwindigkeiten.
- Effiziente Raumnutzung: Power and Free Förderer sind platzsparend und können in verschiedenen Konfigurationen installiert werden, einschließlich mehrstöckiger Anlagen. Dies ermöglicht eine optimale Nutzung des verfügbaren Raums und eine höhere Produktionskapazität auf begrenztem Raum.
- Reduzierte Produktionskosten: Durch die Automatisierung und Flexibilisierung des Transports können Produktionskosten gesenkt werden. Power and Free Förderer reduzieren die Notwendigkeit für manuelle Eingriffe, minimieren die Standzeiten und erhöhen die Gesamteffizienz der Produktion.
Kardangelenkketten und ihre Rolle in Pulverbeschichtungsanlagen
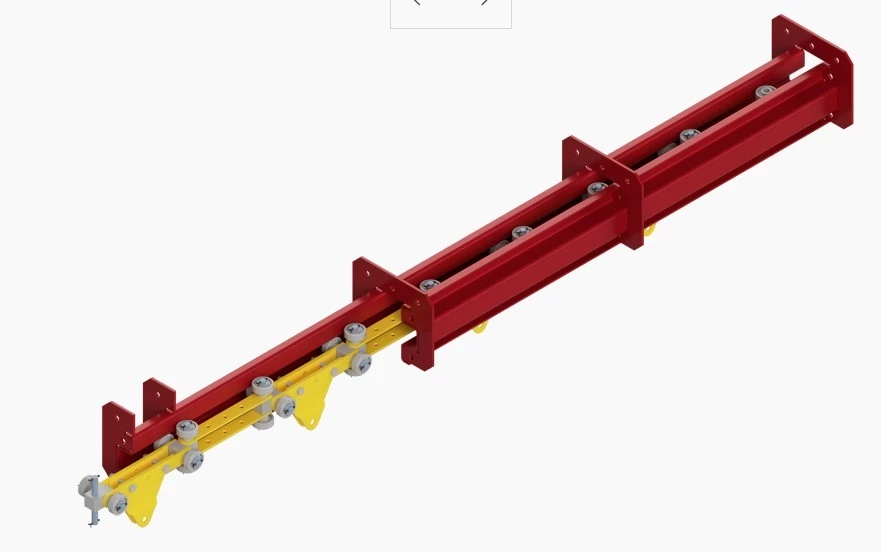
Kardangelenkketten sind eine Schlüsselkomponente in vielen Pulverbeschichtungsanlagen, insbesondere in Systemen, die eine flexible und präzise Bewegung der Werkstücke erfordern. Sie spielen eine wichtige Rolle in der Fördertechnik und tragen wesentlich zur Effizienz und Zuverlässigkeit des Beschichtungsprozesses bei.
Aufbau und Funktionsweise von Kardangelenkketten:
- Flexibles Gelenksystem: Kardangelenkketten bestehen aus einer Reihe von miteinander verbundenen Gliedern, die über Gelenke flexibel miteinander verbunden sind. Dies ermöglicht es, die Kette um Ecken und über Hindernisse hinweg zu führen, ohne die Bewegung der Werkstücke zu unterbrechen.
- Hohe Belastbarkeit: Diese Ketten sind für hohe Belastungen ausgelegt und können schwere Werkstücke sicher transportieren. Sie werden häufig in industriellen Anwendungen eingesetzt, in denen große oder sperrige Teile bewegt werden müssen, wie z. B. in der Automobil- oder Maschinenbauindustrie.
- Präzise Steuerung: Die Flexibilität und Stabilität von Kardangelenkketten ermöglichen eine präzise Steuerung der Werkstücke während des Transports durch die Pulverbeschichtungsanlage. Dies ist entscheidend für die gleichmäßige Beschichtung und die Vermeidung von Fehlstellen.
Bedeutung und Anwendungen:
- Industrielle Anwendungen: Kardangelenkketten sind in einer Vielzahl von industriellen Anwendungen unverzichtbar, insbesondere in Produktionslinien, in denen Werkstücke durch verschiedene Stationen transportiert werden müssen. Sie bieten die Flexibilität, die erforderlich ist, um komplexe Produktionsanforderungen zu erfüllen.
- Automobilindustrie: In der Automobilproduktion werden Kardangelenkketten häufig in Pulverbeschichtungsanlagen eingesetzt, um Karosserieteile, Fahrwerkkomponenten und andere schwere Werkstücke zu transportieren. Ihre hohe Belastbarkeit und Flexibilität machen sie ideal für diese anspruchsvollen Anwendungen.
- Integration in Förderanlagen: Kardangelenkketten können in eine Vielzahl von Förderanlagen integriert werden, einschließlich Power and Free Förderern und anderen Schienensystemen. Dies ermöglicht eine nahtlose Integration in bestehende Produktionslinien und erhöht die Gesamteffizienz der Anlage.
Die Fördertechnik ist ein entscheidender Faktor für die Effizienz und Qualität des Pulverbeschichtungsprozesses. Mit den richtigen Systemen und Komponenten, wie Transport-Schienensystemen, Power and Free Förderern und Kardangelenkketten, können Unternehmen ihre Produktionsprozesse optimieren und die Qualität der Beschichtungen sicherstellen.
Abschnitt 7: Chemische Vorbehandlung und Spezialanwendungen
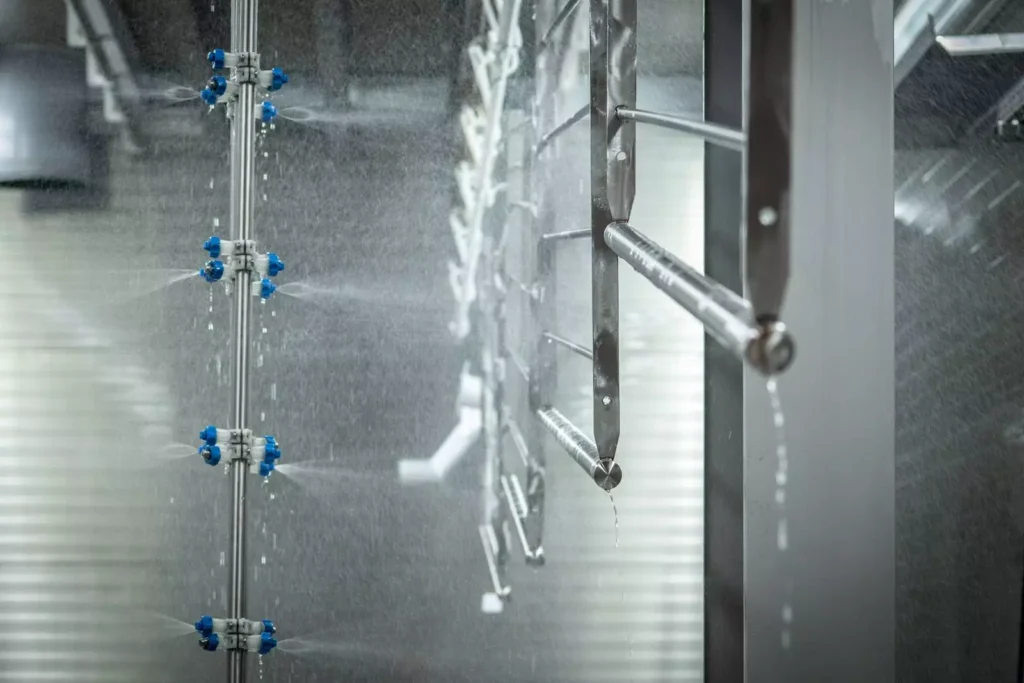
Vorbehandlung für eine optimale Pulverbeschichtung
Die chemische Vorbehandlung ist ein kritischer Schritt im Pulverbeschichtungsprozess, da sie die Basis für eine langlebige und gleichmäßige Beschichtung legt. Eine gründliche Vorbehandlung entfernt Verunreinigungen von der Oberfläche des Werkstücks und schafft eine optimale Haftung für den Pulverlack. Ohne diese Vorbehandlung könnte die Beschichtung ungleichmäßig aufgetragen werden oder sich vorzeitig ablösen.
Verfahren der chemischen Vorbehandlung:
- Entfettung: Der erste Schritt in der chemischen Vorbehandlung ist in der Regel die Entfettung. Hierbei werden Öle, Fette und andere organische Verunreinigungen, die während der Produktion auf das Werkstück gelangt sind, entfernt. Dies erfolgt oft durch den Einsatz von speziellen Reinigungsmitteln oder Lösungsmitteln, die in einem Tauchbad oder durch Sprühreinigung aufgetragen werden.
- Phosphatierung: Nach der Entfettung folgt oft die Phosphatierung, ein Prozess, bei dem eine dünne Schicht Phosphat auf der Metalloberfläche gebildet wird. Diese Schicht verbessert die Haftung des Pulvers und erhöht die Korrosionsbeständigkeit des Werkstücks. Phosphatierungen sind in verschiedenen Formen erhältlich, darunter Zink-, Eisen- und Manganphosphatierungen, je nach den spezifischen Anforderungen der Anwendung.
- Chromatierung und Chromfrei-Verfahren: Für Aluminium und andere NE-Metalle wird oft eine Chromatierung durchgeführt. Diese bildet eine passivierende Schicht auf der Oberfläche, die nicht nur die Haftung verbessert, sondern auch die Korrosionsbeständigkeit erhöht. Chromfreie Verfahren sind eine umweltfreundlichere Alternative, die in den letzten Jahren an Bedeutung gewonnen hat.
- Passivierung: Als letzter Schritt in der Vorbehandlung kann eine Passivierung durchgeführt werden, bei der die Oberfläche des Werkstücks durch chemische Mittel stabilisiert wird. Dies schützt das Metall vor Oxidation und bereitet es optimal auf die nachfolgende Pulverbeschichtung vor.
Bedeutung der Vorbehandlung:
- Verbesserte Haftung: Die chemische Vorbehandlung sorgt dafür, dass das Pulver fest auf der Oberfläche haftet, was die Lebensdauer der Beschichtung erheblich verlängert.
- Korrosionsschutz: Eine gute Vorbehandlung erhöht die Widerstandsfähigkeit des Werkstücks gegenüber Korrosion, was besonders in Anwendungen wichtig ist, die extremen Umweltbedingungen ausgesetzt sind, wie z. B. in der Automobilindustrie oder im Bauwesen.
- Gleichmäßige Beschichtung: Die Entfernung von Verunreinigungen und die Schaffung einer gleichmäßigen Oberfläche sind entscheidend, um eine gleichmäßige Beschichtung ohne Fehlstellen oder Unebenheiten zu gewährleisten.
Schraubenbeschichtung: Herausforderungen und Lösungen
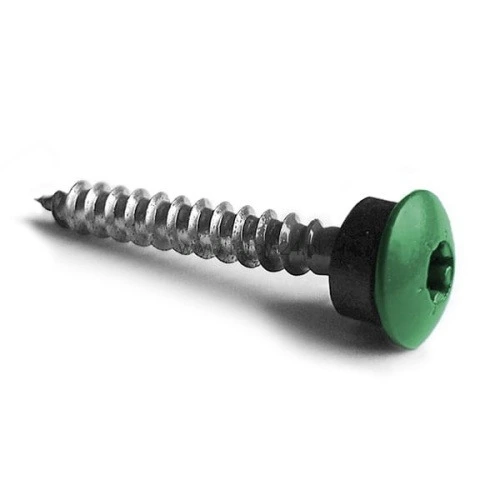
Die Beschichtung von Schrauben stellt eine besondere Herausforderung dar, da sie klein, oft komplex geformt und in großen Mengen produziert werden. Zudem müssen die Beschichtungen widerstandsfähig gegen mechanische Belastungen und Korrosion sein, während die Funktionalität der Schrauben, wie z. B. das Drehmoment oder die Passgenauigkeit, nicht beeinträchtigt werden darf.
Herausforderungen bei der Schraubenbeschichtung:
- Kleinere Abmessungen und komplexe Formen: Schrauben haben oft feine Gewinde und komplizierte Geometrien, die schwer zu beschichten sind. Eine ungleichmäßige Beschichtung kann die Funktionalität beeinträchtigen oder zu Fehlern führen.
- Massenproduktion: In vielen Fällen werden Schrauben in großen Mengen hergestellt und beschichtet, was eine gleichbleibende Qualität erfordert. Schwankungen im Beschichtungsprozess können zu unbrauchbaren Chargen führen.
- Mechanische Belastung: Schrauben müssen starken mechanischen Kräften standhalten, insbesondere beim Eindrehen in Materialien. Die Beschichtung muss daher nicht nur widerstandsfähig gegen Korrosion sein, sondern auch eine hohe Abriebfestigkeit aufweisen.
Lösungen für die Schraubenbeschichtung:
- Spezialisierte Pulverbeschichtungsanlagen: Es gibt spezielle Anlagen, die für die Beschichtung von Schrauben und anderen Kleinteilen entwickelt wurden. Diese Anlagen sind so konzipiert, dass sie eine gleichmäßige Beschichtung bei hoher Durchsatzrate gewährleisten können.
- Optimierte Pulverrezepturen: Für die Schraubenbeschichtung werden häufig spezielle Pulver verwendet, die eine hohe Haftung und Beständigkeit bieten. Diese Pulver sind so formuliert, dass sie den Anforderungen der Schrauben hinsichtlich mechanischer Belastung und Korrosionsbeständigkeit gerecht werden.
- Trommel- oder Zentrifugalbeschichtung: In der industriellen Produktion werden Schrauben oft in Trommel- oder Zentrifugalbeschichtungsanlagen behandelt. In diesen Anlagen werden die Schrauben kontinuierlich in einem rotierenden Behälter bewegt, während das Pulver aufgebracht wird. Dies sorgt für eine gleichmäßige Beschichtung und reduziert die Gefahr von Verklumpungen oder ungleichmäßigen Schichtdicken.
- Nachbearbeitung: Nach der Beschichtung können Schrauben zusätzlich einer Nachbearbeitung unterzogen werden, wie z. B. einer Wärmebehandlung, um die mechanischen Eigenschaften weiter zu verbessern und die Haftung des Pulvers zu optimieren.
Spezielle Anwendungen: Kleinteile, Alufelgen und mehr
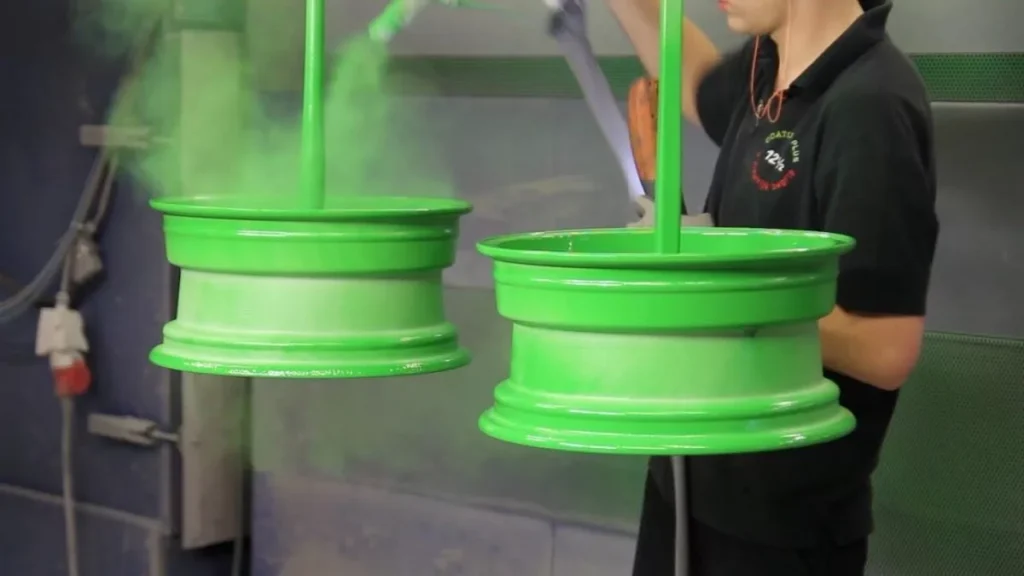
Neben Schrauben gibt es viele andere spezielle Anwendungen für die Pulverbeschichtung, die jeweils eigene Herausforderungen und Anforderungen mit sich bringen. Einige dieser Anwendungen umfassen Kleinteile, Alufelgen und andere spezialisierte Produkte, die eine maßgeschneiderte Herangehensweise erfordern.
Pulverbeschichtung von Kleinteilen:
- Kleinteile, wie z. B. Schrauben, Muttern oder andere Verbindungselemente, werden oft in großen Mengen beschichtet, was eine effiziente und gleichmäßige Beschichtung erfordert.
- Spezielle Anlagen, wie Trommel- oder Zentrifugalbeschichtungsanlagen, ermöglichen die gleichmäßige Beschichtung auch von sehr kleinen Teilen.
- Eine präzise Steuerung des Beschichtungsprozesses ist entscheidend, um sicherzustellen, dass alle Teile eine gleichmäßige Schichtdicke aufweisen und funktionsfähig bleiben.
Alufelgen Sandstrahlen und Lackieren:
- Alufelgen sind besonders beliebt für ihre Leichtigkeit und Ästhetik, was sie zu einem der häufigsten Anwendungsgebiete der Pulverbeschichtung macht.
- Vor der Pulverbeschichtung müssen die Felgen oft sandgestrahlt werden, um alte Lack- oder Beschichtungsschichten zu entfernen und die Oberfläche für eine neue Beschichtung vorzubereiten.
- Das Sandstrahlen sorgt für eine gleichmäßige, aufgeraute Oberfläche, die eine optimale Haftung der Pulverbeschichtung ermöglicht. Nach dem Sandstrahlen folgt die eigentliche Beschichtung, bei der sowohl funktionale als auch ästhetische Anforderungen erfüllt werden müssen.
Weitere spezialisierte Anwendungen:
- Die Pulverbeschichtung wird auch in vielen anderen spezialisierten Anwendungen eingesetzt, wie z. B. in der Beschichtung von Haushaltsgeräten, elektronischen Gehäusen oder architektonischen Elementen.
- Jede dieser Anwendungen erfordert eine sorgfältige Planung und Anpassung des Beschichtungsprozesses, um die spezifischen Anforderungen zu erfüllen.
Dieser Abschnitt hat die Bedeutung der chemischen Vorbehandlung und die speziellen Herausforderungen der Beschichtung von Schrauben und anderen Kleinteilen beleuchtet. Im nächsten Abschnitt werde ich die Automatisierung und Innovation in der Pulverbeschichtung näher betrachten, einschließlich der neuesten Trends und Technologien.
Abschnitt 8: Automatisierung und Innovation in der Pulverbeschichtung

Fortschritte in der Automatisierung: Automatische Lackieranlagen
Die Automatisierung in der Pulverbeschichtung hat in den letzten Jahren erhebliche Fortschritte gemacht, insbesondere durch den Einsatz automatischer Lackieranlagen. Diese Anlagen ermöglichen eine hochpräzise, effiziente und konsistente Beschichtung, die den Anforderungen moderner Industrien gerecht wird. Automatische Lackieranlagen sind besonders in Großserienproduktionen von Vorteil, wo hohe Stückzahlen bei gleichbleibender Qualität gefragt sind.
Merkmale automatischer Lackieranlagen:
- Robotertechnologie: Automatische Lackieranlagen nutzen oft Roboterarme, die mit Präzision das Pulver auf die Werkstücke auftragen. Diese Roboter sind programmierbar und können komplexe Bewegungsmuster ausführen, um auch schwierige Geometrien gleichmäßig zu beschichten. Die Genauigkeit der Roboter sorgt dafür, dass jede Beschichtungsschicht exakt den Spezifikationen entspricht, was die Qualität und Effizienz des Prozesses steigert.
- Integrierte Steuerungssysteme: Moderne automatische Lackieranlagen sind mit fortschrittlichen Steuerungssystemen ausgestattet, die den gesamten Beschichtungsprozess überwachen und steuern. Diese Systeme können in Echtzeit Anpassungen vornehmen, um die optimale Pulverdichte, Sprührate und Temperatur zu gewährleisten. Dadurch wird der Materialverbrauch minimiert und die Qualität der Beschichtung maximiert.
- Schnellwechsel-Systeme: Ein weiteres innovatives Merkmal automatischer Anlagen ist das Schnellwechsel-System, das den schnellen Wechsel zwischen verschiedenen Pulverlacken ermöglicht. Dies ist besonders nützlich in Produktionsumgebungen, in denen häufig die Farbe oder das Material gewechselt werden muss. Das System sorgt dafür, dass der Produktionsfluss nicht unterbrochen wird, was zu einer höheren Produktivität führt.
Vorteile der Automatisierung:
- Konstante Qualität: Durch die Automatisierung wird die menschliche Fehlerquote nahezu eliminiert, was zu einer konstant hohen Qualität der Beschichtungen führt. Dies ist besonders wichtig in Industrien wie der Automobil- oder Luftfahrtindustrie, wo jedes Detail zählt.
- Höhere Produktionsgeschwindigkeit: Automatische Anlagen können rund um die Uhr arbeiten, ohne Ermüdungserscheinungen oder Pausen. Dies führt zu einer signifikant höheren Produktionsgeschwindigkeit, was die Effizienz und Rentabilität der Produktion erhöht.
- Reduzierte Betriebskosten: Trotz der anfänglich höheren Investitionskosten amortisieren sich automatische Lackieranlagen schnell durch die Einsparungen bei Material, Arbeitskraft und Produktionszeit. Die präzise Steuerung des Pulvers und die Minimierung von Abfall tragen ebenfalls zur Senkung der Betriebskosten bei.
Zukunft der Pulverbeschichtung: Innovationen und Trends
Die Pulverbeschichtungsindustrie entwickelt sich ständig weiter, getrieben von neuen Technologien, Materialien und Prozessen. Diese Innovationen zielen darauf ab, die Effizienz zu steigern, die Umweltbelastung zu reduzieren und die Qualität der Beschichtungen weiter zu verbessern.
Neue Materialien und Pulverformulierungen:
- Nano-Pulver: Eine der vielversprechendsten Innovationen in der Pulverbeschichtung ist die Entwicklung von Nano-Pulvern. Diese Pulver enthalten extrem kleine Partikel, die eine noch glattere und widerstandsfähigere Oberfläche ermöglichen. Nano-Pulver bieten auch verbesserte mechanische Eigenschaften, wie z. B. erhöhte Härte und Kratzfestigkeit, was sie ideal für anspruchsvolle Anwendungen macht.
- UV-härtende Pulver: Eine weitere bedeutende Entwicklung sind UV-härtende Pulver, die anstelle von Wärme mit ultraviolettem Licht gehärtet werden. Diese Technologie bietet den Vorteil, dass die Aushärtung bei Raumtemperatur erfolgen kann, was den Energieverbrauch erheblich reduziert. UV-härtende Pulver eignen sich besonders für temperaturempfindliche Substrate oder für Anwendungen, bei denen eine schnelle Aushärtung erforderlich ist.
Umweltfreundliche Technologien:
- Lösemittelfreie Beschichtungen: Da der Umweltschutz in der Industrie zunehmend an Bedeutung gewinnt, sind lösemittelfreie Pulverbeschichtungen auf dem Vormarsch. Diese Beschichtungen setzen keine flüchtigen organischen Verbindungen (VOCs) frei und sind daher besonders umweltfreundlich. Die Entwicklung solcher umweltfreundlichen Pulver ist ein entscheidender Schritt hin zu einer nachhaltigeren Produktion.
- Recycling und Wiederverwendung: Die Verbesserung der Pulverrückgewinnungssysteme hat ebenfalls zu einer Reduzierung der Abfallmengen geführt. Moderne Pulverbeschichtungsanlagen sind in der Lage, nahezu 100 % des überschüssigen Pulvers zu recyceln und wiederzuverwenden, was die Ressourceneffizienz erheblich steigert.
Digitalisierung und Industrie 4.0:
- Verbindung mit IoT: Mit der fortschreitenden Digitalisierung werden Pulverbeschichtungsanlagen zunehmend in das Internet der Dinge (IoT) integriert. Diese Vernetzung ermöglicht eine kontinuierliche Überwachung und Optimierung des Beschichtungsprozesses in Echtzeit. Daten wie Temperatur, Luftfeuchtigkeit, Pulververbrauch und Schichtdicke können in Echtzeit erfasst und analysiert werden, um den Prozess zu optimieren und Ausfallzeiten zu minimieren.
- Virtuelle Realität (VR) und Augmented Reality (AR): In der Schulung und im Betrieb von Pulverbeschichtungsanlagen kommen vermehrt VR und AR zum Einsatz. Diese Technologien ermöglichen es Bedienern, in einer virtuellen Umgebung zu trainieren oder Fehlerdiagnosen in Echtzeit durchzuführen, ohne den Betrieb der Anlage zu unterbrechen.
- Automatisierte Qualitätssicherung: Mit der zunehmenden Automatisierung geht auch eine Automatisierung der Qualitätssicherung einher. Sensoren und Kamerasysteme können die beschichteten Werkstücke sofort nach dem Beschichten überprüfen und Fehler wie ungleichmäßige Schichten oder Farbabweichungen identifizieren. Diese Systeme tragen dazu bei, den Ausschuss zu reduzieren und die Produktqualität konstant hoch zu halten.
Nachhaltigkeit und Energieeffizienz in der Pulverbeschichtung
Nachhaltigkeit ist ein zentrales Thema in der modernen Produktion, und die Pulverbeschichtung ist keine Ausnahme. Neue Technologien und Prozesse werden entwickelt, um den Energieverbrauch zu senken, Ressourcen effizienter zu nutzen und die Umweltbelastung zu minimieren.
Energieeffiziente Öfen und Anlagen:
- Moderne Einbrennöfen: Neue Generationen von Einbrennöfen sind so konstruiert, dass sie weniger Energie verbrauchen und schneller auf Betriebstemperatur kommen. Durch die Verwendung verbesserter Isolationsmaterialien und optimierter Heizsysteme wird die Effizienz gesteigert, während der Energieverbrauch gesenkt wird.
- Wärmerückgewinnung: Einige Pulverbeschichtungsanlagen nutzen Wärmerückgewinnungssysteme, um die Abwärme aus dem Aushärteprozess wiederzuverwenden. Diese Systeme reduzieren den Bedarf an zusätzlicher Energie und tragen zur Senkung der Betriebskosten bei.
Ressourceneffizienz und Abfallreduktion:
- Präzise Dosiersysteme: Durch den Einsatz präziser Dosiersysteme wird der Materialverbrauch optimiert. Diese Systeme steuern die Pulvermenge exakt und minimieren den Einsatz von überschüssigem Pulver, was zu einer Reduktion von Abfällen und Materialkosten führt.
- Recycling von Pulverabfällen: Abfallreduzierung ist ein weiterer wichtiger Aspekt der Nachhaltigkeit. Pulverabfälle, die bei der Beschichtung anfallen, können in vielen Fällen wiederverwendet oder recycelt werden. Dies reduziert die Menge an Abfall, der entsorgt werden muss, und schont die Umwelt.
- Nachhaltige Pulverformulierungen: Die Entwicklung von Pulverlacken auf Wasserbasis oder mit biologisch abbaubaren Komponenten ist ein weiteres Beispiel für Innovationen, die darauf abzielen, die Umweltbelastung zu verringern. Diese nachhaltigen Pulver sind nicht nur umweltfreundlicher, sondern auch sicherer in der Anwendung.
Die Pulverbeschichtungsindustrie bewegt sich in Richtung einer umweltfreundlicheren und effizienteren Zukunft. Durch den Einsatz neuer Technologien und die Fokussierung auf Nachhaltigkeit werden die Prozesse kontinuierlich verbessert, um den Anforderungen moderner Produktionsumgebungen gerecht zu werden.
Absaugwände
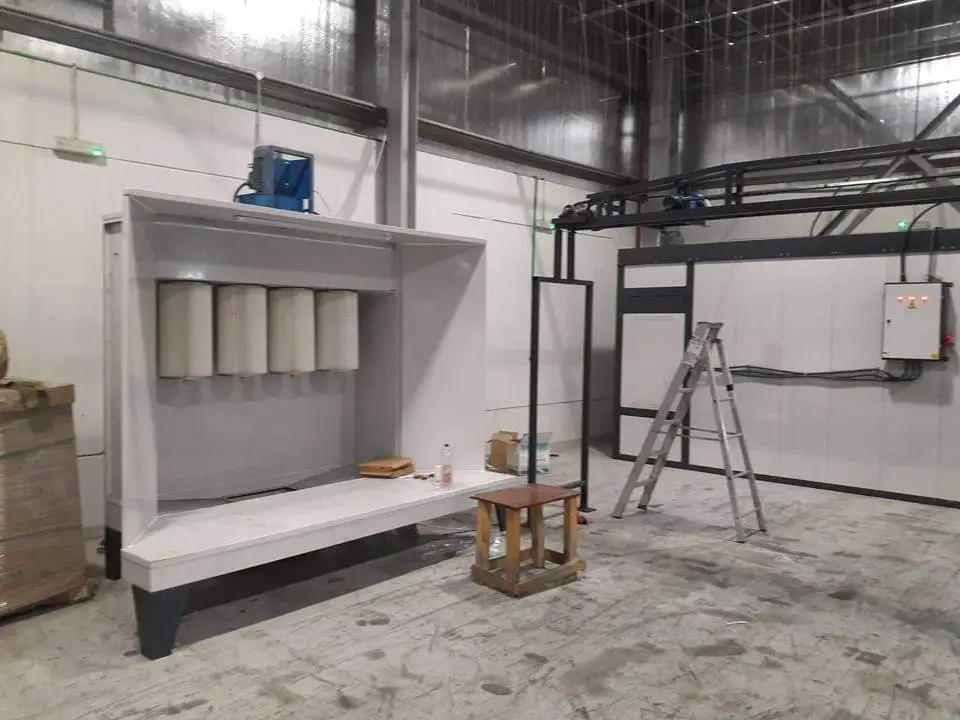
Absaugwände, auch als Absauganlagen oder Absaugkabinen bezeichnet, sind technische Geräte, die entwickelt wurden, um Schadstoffe und Partikel aus der Luft zu entfernen. Sie arbeiten auf der Grundlage eines Lüftungssystems, das die verschmutzte Luft ansaugt, durch Filter leitet und die gereinigte Luft entweder wieder in die Umgebung freisetzt oder nach außen leitet.
In vielen Arbeitsumgebungen entstehen durch Produktionsprozesse gesundheitsschädliche Stoffe, wie zum Beispiel Lackdämpfe, Staub oder chemische Gase. Wenn diese Substanzen nicht ordnungsgemäß entfernt werden, können sie nicht nur die Gesundheit der Arbeiter beeinträchtigen, sondern auch die Qualität der Produktion verringern und die Umwelt schädigen.
Die Hauptaufgabe einer Absaugwand besteht darin, eine saubere und sichere Arbeitsumgebung zu gewährleisten, indem sie potenziell gefährliche Partikel und Dämpfe entfernt. Sie ist sowohl in kleinen Werkstätten als auch in großen industriellen Produktionsanlagen unverzichtbar.
2. Funktionsweise einer Absaugwand
Absaugwände arbeiten auf der Grundlage eines Luftstromsystems, das Schadstoffe aus der Luft filtert und somit für eine saubere Arbeitsumgebung sorgt. Die Funktionsweise kann in mehrere grundlegende Schritte unterteilt werden:
2.1. Ansaugung der verschmutzten Luft
Der erste Schritt im Betrieb einer Absaugwand ist die Ansaugung der verschmutzten Luft. Dies geschieht in der Regel durch leistungsstarke Ventilatoren, die in der Absaugwand eingebaut sind. Diese Ventilatoren erzeugen einen Luftstrom, der Schadstoffe wie Staub, Dämpfe oder chemische Partikel in die Absaugwand zieht.
Je nach Größe der Anlage und dem Umfang der entstehenden Verunreinigungen kann die Absaugleistung variieren. Die Absaugung erfolgt direkt an der Quelle, also dort, wo die Schadstoffe entstehen, um ihre Ausbreitung in der Arbeitsumgebung zu minimieren.
2.2. Filtration der Luft
Sobald die verschmutzte Luft in die Absaugwand gelangt, wird sie durch verschiedene Filtersysteme geleitet. Diese Filter spielen eine entscheidende Rolle, da sie die schädlichen Partikel und Gase aus der Luft entfernen. Die Art der Filter hängt vom jeweiligen Anwendungsbereich ab, da unterschiedliche Prozesse unterschiedliche Schadstoffe erzeugen.
Zu den häufig verwendeten Filtern gehören:
- HEPA-Filter (High-Efficiency Particulate Air): Diese Filter entfernen feine Partikel, die kleiner als 0,3 Mikrometer sind, und sind besonders effektiv bei der Entfernung von Staub und Rauch.
- Aktivkohlefilter: Diese Filter sind ideal zur Entfernung von chemischen Dämpfen und organischen Verbindungen aus der Luft.
- Vorfilter: Diese Filter entfernen größere Partikel und schützen die nachfolgenden Filter vor Verstopfung.
- Nassabscheider: Diese Technologie wird oft für die Entfernung von Farbnebeln oder feuchten Dämpfen verwendet.
2.3. Abluft oder Rückführung
Nachdem die Luft durch die Filter gereinigt wurde, gibt es zwei Hauptmöglichkeiten, wie die Luft weiterverarbeitet wird:
- Rückführung der gefilterten Luft in den Raum: In vielen Fällen, insbesondere in geschlossenen Räumen, wird die gereinigte Luft wieder in den Arbeitsbereich zurückgeführt. Dies ist energieeffizient, da die Wärme in der Luft erhalten bleibt und keine zusätzliche Energie zum Erwärmen frischer Luft benötigt wird.
- Abluft nach außen: In einigen Fällen, insbesondere wenn es sich um giftige Gase oder Dämpfe handelt, wird die gefilterte Luft aus Sicherheitsgründen nach draußen abgeleitet.
2.4. Überwachung und Steuerung
Moderne Absaugwände sind oft mit Überwachungs- und Steuerungssystemen ausgestattet, die sicherstellen, dass die Anlage effizient arbeitet. Dazu gehören:
- Sensoren zur Überwachung der Luftqualität: Diese Sensoren messen kontinuierlich den Schadstoffgehalt in der Luft und können die Lüftungsstärke entsprechend anpassen.
- Filterüberwachung: Einige Systeme verfügen über Anzeigen, die den Zustand der Filter überwachen und signalisieren, wann ein Filterwechsel erforderlich ist.
- Automatische Abschaltung: Bei Störungen oder Gefahren, wie einem Brand oder einem zu hohen Schadstoffgehalt, können diese Systeme automatisch abgeschaltet werden, um die Sicherheit zu gewährleisten.
3. Typen von Absaugwänden

Es gibt verschiedene Arten von Absaugwänden, die je nach Anwendungsbereich und den spezifischen Anforderungen der Industrie ausgewählt werden. Hier sind die gängigsten Typen:
3.1. Trockene Absaugwände
Trockene Absaugwände sind die am häufigsten verwendete Art von Absaugwänden. Sie funktionieren durch die Ansaugung der Luft und die Filtration von Partikeln, ohne dass Wasser zur Reinigung verwendet wird.
- Vorteile: Trockene Absaugwände sind relativ einfach zu warten, da die Filter leicht zugänglich und austauschbar sind. Außerdem benötigen sie kein Wassersystem, was sie kostengünstiger macht.
- Anwendungsgebiete: Diese Absaugwände werden häufig in Lackierbetrieben, Schleifwerkstätten und bei Arbeiten eingesetzt, bei denen Staub und feste Partikel entstehen.
3.2. Nassabsaugwände
Bei Nassabsaugwänden wird die verschmutzte Luft durch einen Wassernebel oder -film geleitet, der die Schadstoffe abfängt und bindet. Diese Technik ist besonders effektiv bei der Entfernung von Farbnebeln oder Partikeln, die leicht an Oberflächen haften.
- Vorteile: Nassabsaugwände sind besonders effektiv bei der Beseitigung von feinen Partikeln und Farbnebeln, da das Wasser die Partikel einfängt und aus der Luft entfernt.
- Anwendungsgebiete: Häufig werden Nassabsaugwände in der Lackier- und Metallverarbeitungsindustrie eingesetzt, wo Farbnebel und feuchte Partikel entstehen.
3.3. Absaugwände mit Aktivkohlefiltern
Absaugwände mit Aktivkohlefiltern sind speziell darauf ausgelegt, organische Dämpfe und Lösungsmittel aus der Luft zu entfernen. Die Aktivkohle absorbiert die Chemikalien und sorgt dafür, dass saubere Luft in den Arbeitsbereich zurückgeführt wird.
- Vorteile: Aktivkohlefilter sind besonders effektiv bei der Beseitigung von Lösungsmitteldämpfen und organischen Verbindungen, die durch Lackierprozesse oder chemische Behandlungen entstehen.
- Anwendungsgebiete: Diese Absaugwände werden häufig in der chemischen Industrie und bei Lackierprozessen eingesetzt, bei denen organische Dämpfe entstehen.
3.4. Mobile Absaugwände
Mobile Absaugwände sind flexible, tragbare Einheiten, die sich leicht bewegen lassen. Diese Wände sind ideal für Werkstätten oder temporäre Baustellen, bei denen der Standort der Arbeiten häufig wechselt.
- Vorteile: Mobile Absaugwände bieten Flexibilität, da sie überall eingesetzt werden können. Sie sind ideal für kleine Werkstätten oder temporäre Projekte, bei denen keine feste Absauganlage installiert werden kann.
- Anwendungsgebiete: Werkstätten, Bauprojekte und temporäre Arbeitsplätze profitieren von der Flexibilität dieser mobilen Lösungen.
3.5. Spezialisierte Absaugwände für bestimmte Anwendungen
Einige Absaugwände sind speziell für bestimmte Anwendungen konzipiert. Dazu gehören beispielsweise Absaugwände für Schweißarbeiten, bei denen metallische Dämpfe und Rauch entstehen, oder spezielle Absaugwände für die Bearbeitung von Kunststoffen, bei denen gefährliche Gase freigesetzt werden können.
- Vorteile: Diese spezialisierten Anlagen sind speziell auf die Anforderungen der jeweiligen Industrie zugeschnitten und gewährleisten eine besonders effektive Entfernung der spezifischen Schadstoffe.
- Anwendungsgebiete: Diese Absaugwände finden Anwendung in der Metallverarbeitung, Kunststoffherstellung, Elektronikindustrie und in anderen spezialisierten Produktionsbereichen.
4. Vorteile von Absaugwänden
Der Einsatz von Absaugwänden bietet eine Vielzahl von Vorteilen, die nicht nur die Effizienz und Produktivität der Produktion verbessern, sondern auch den Schutz der Mitarbeiter und der Umwelt gewährleisten. Hier sind die wichtigsten Vorteile im Detail:
4.1. Verbesserung der Luftqualität
Der offensichtlichste Vorteil von Absaugwänden ist die Verbesserung der Luftqualität am Arbeitsplatz. Schadstoffe wie Staub, Rauch und Dämpfe werden direkt an der Quelle erfasst und gefiltert, bevor sie sich in der Luft ausbreiten können. Dies führt zu einer saubereren und gesünderen Arbeitsumgebung für die Mitarbeiter.
4.2. Schutz der Gesundheit der Mitarbeiter
Viele der Partikel und Dämpfe, die in industriellen Prozessen freigesetzt werden, können gesundheitsschädlich sein. Feinstaub, Lösungsmitteldämpfe oder giftige Gase können Atemprobleme, Allergien oder sogar schwere Krankheiten verursachen. Absaugwände schützen die Mitarbeiter, indem sie diese Schadstoffe effizient aus der Luft entfernen und das Risiko einer Exposition verringern.
4.3. Erhöhung der Produktqualität
Schadstoffe in der Luft können auch die Qualität der Endprodukte beeinträchtigen. In Lackierbetrieben können beispielsweise Staubpartikel zu Unebenheiten in der Lackierung führen. Eine Absaugwand sorgt für eine saubere Umgebung, in der hochwertige Produkte ohne Mängel hergestellt werden können.
4.4. Einhaltung von Umweltvorschriften
In vielen Ländern gibt es strenge Umweltvorschriften, die den Ausstoß von Schadstoffen in die Atmosphäre regeln. Absaugwände helfen Unternehmen, diese Vorschriften einzuhalten, indem sie die schädlichen Partikel und Gase aus der Luft filtern, bevor sie in die Umwelt gelangen.
4.5. Erhöhung der Arbeitssicherheit
In Arbeitsbereichen, in denen brennbare oder explosive Stoffe verarbeitet werden, stellen Absaugwände eine wichtige Sicherheitsmaßnahme dar. Sie verhindern die Ansammlung von brennbaren Gasen oder Stäuben und reduzieren so das Risiko von Explosionen oder Bränden.
4.6. Kosteneffizienz durch Energieeinsparung
Moderne Absaugwände sind oft mit energieeffizienten Lüftern und Filtersystemen ausgestattet, die den Energieverbrauch minimieren. Durch die Rückführung der gefilterten Luft in den Arbeitsbereich kann zudem die Raumtemperatur aufrechterhalten werden, wodurch Heizkosten eingespart werden.
5. Anwendungsgebiete von Absaugwänden
Absaugwände finden in vielen Branchen und Anwendungsbereichen Einsatz, in denen Partikel, Dämpfe oder andere Schadstoffe entstehen. Hier sind einige der wichtigsten Anwendungsgebiete:
5.1. Lackierereien und Beschichtungsbetriebe
Eines der häufigsten Einsatzgebiete für Absaugwände ist die Lackier- und Beschichtungsindustrie. Lacke und Beschichtungen enthalten oft Lösungsmittel und Chemikalien, die während des Auftragsprozesses verdampfen und schädliche Dämpfe freisetzen. Absaugwände sorgen dafür, dass diese Dämpfe gefiltert werden, bevor sie in die Luft gelangen, und tragen somit zur Sicherheit und Qualität der Arbeiten bei.
5.2. Metallverarbeitung und Schweißarbeiten
In der Metallverarbeitung entstehen bei Schweißarbeiten giftige Dämpfe und feine Metallpartikel, die gesundheitsschädlich sein können. Absaugwände für Schweißarbeitsplätze sind darauf ausgelegt, diese Dämpfe und Partikel effektiv abzusaugen und zu filtern.
5.3. Holzverarbeitung
Bei der Holzverarbeitung entsteht eine große Menge an Staub und Spänen, die nicht nur die Gesundheit der Arbeiter gefährden, sondern auch die Maschinen beschädigen können. Absaugwände in Schreinereien oder Holzverarbeitungsbetrieben entfernen den Staub aus der Luft und sorgen für eine saubere und sichere Arbeitsumgebung.
5.4. Automobilindustrie
In der Automobilproduktion, insbesondere in Lackierwerken und bei der Verarbeitung von Kunststoffen, entstehen gefährliche Dämpfe und Partikel. Absaugwände sorgen dafür, dass diese Schadstoffe sicher entfernt werden, was die Sicherheit der Arbeiter und die Qualität der Endprodukte verbessert.
5.5. Elektronikindustrie
In der Elektronikfertigung entstehen bei der Verarbeitung von Kunststoffen oder Löten giftige Gase und Dämpfe. Absaugwände sorgen dafür, dass diese Gase aus der Luft entfernt werden und keine gesundheitlichen Risiken für die Mitarbeiter bestehen.
5.6. Chemische Industrie
In der chemischen Industrie kommen viele gefährliche Substanzen zum Einsatz, die bei der Verarbeitung oder Herstellung freigesetzt werden können. Absaugwände schützen die Arbeiter vor der Exposition gegenüber schädlichen Chemikalien und tragen zur Einhaltung von Umweltvorschriften bei.
5.7. Pharmazeutische Industrie
Bei der Herstellung von Medikamenten oder anderen pharmazeutischen Produkten entstehen oft feine Partikel oder Dämpfe, die nicht in die Luft gelangen dürfen, um eine Kontamination der Produkte zu verhindern. Absaugwände sorgen für eine saubere und kontrollierte Umgebung, die höchsten Qualitätsanforderungen entspricht.
6. Wartung und Pflege von Absaugwänden
Damit Absaugwände effektiv arbeiten und eine lange Lebensdauer haben, ist regelmäßige Wartung unerlässlich. Die Wartung gewährleistet, dass alle Komponenten der Absaugwand optimal funktionieren und der Luftstrom sowie die Filtrationseffizienz aufrechterhalten bleiben.
6.1. Regelmäßiger Filterwechsel
Einer der wichtigsten Wartungsschritte bei Absaugwänden ist der regelmäßige Wechsel der Filter. Abhängig vom Anwendungsbereich und der Häufigkeit der Nutzung können Filter sich schnell mit Partikeln und Verunreinigungen füllen, was ihre Effizienz beeinträchtigt. Verstopfte Filter reduzieren den Luftstrom und erhöhen den Energieverbrauch, weshalb sie in regelmäßigen Abständen ausgetauscht werden sollten.
6.2. Überprüfung der Lüftungssysteme
Die Ventilatoren und Lüftungssysteme in der Absaugwand müssen ebenfalls regelmäßig überprüft werden, um sicherzustellen, dass sie ordnungsgemäß funktionieren. Verstopfte oder beschädigte Ventilatoren können den Luftstrom behindern und die Leistung der gesamten Anlage beeinträchtigen. Zudem sollte darauf geachtet werden, dass keine Lecks im System vorhanden sind, die dazu führen könnten, dass ungefilterte Luft in die Arbeitsumgebung gelangt.
6.3. Reinigung der Anlage
Die Wände, Böden und inneren Teile der Absaugwand sollten regelmäßig gereinigt werden, um sicherzustellen, dass keine Staub- oder Farbpartikel an den Oberflächen haften. Dies verhindert, dass sich Partikel auf die zu bearbeitenden Werkstücke setzen und die Qualität der Lackierung oder Bearbeitung beeinträchtigen.
6.4. Inspektion der Sicherheitsfunktionen
Absaugwände sind oft mit verschiedenen Sicherheitsfunktionen ausgestattet, wie z. B. Notabschaltungen oder Brandmeldern. Diese Sicherheitsfunktionen sollten regelmäßig auf ihre Funktionsfähigkeit überprüft werden, um im Falle eines Notfalls die Sicherheit der Arbeiter gewährleisten zu können.
6.5. Software-Updates für digitale Steuerungssysteme
Moderne Absaugwände sind häufig mit digitalen Steuerungssystemen ausgestattet, die den Betrieb der Anlage überwachen und steuern. Diese Systeme sollten regelmäßig auf den neuesten Stand gebracht werden, um sicherzustellen, dass sie effizient arbeiten und alle notwendigen Daten korrekt erfassen.
7. Fazit
Absaugwände sind in vielen Industrien ein unverzichtbares Werkzeug, um saubere, sichere und effiziente Arbeitsumgebungen zu schaffen. Sie tragen nicht nur dazu bei, die Gesundheit der Arbeiter zu schützen, sondern verbessern auch die Qualität der Endprodukte und helfen Unternehmen, strenge Umweltvorschriften einzuhalten.
EMS Powder Coating Equipment bietet eine breite Palette von Absaugwänden, die speziell auf die Bedürfnisse verschiedener Branchen zugeschnitten sind. Mit innovativen Technologien, hoher Zuverlässigkeit und umfassendem Kundensupport sind EMS-Absaugwände die ideale Wahl für Unternehmen, die eine langfristige, effiziente Lösung für ihre Absaugbedürfnisse suchen.
Mit regelmäßiger Wartung und Pflege können Absaugwände ihre volle Leistungsfähigkeit über viele Jahre hinweg beibehalten, was sie zu einer lohnenden Investition für jedes Unternehmen macht.
Eine Absaugwand ist eine wichtige technische Einrichtung in industriellen Prozessen, die dazu dient, Schadstoffe, Dämpfe, Staub oder andere Luftverunreinigungen aus der Umgebungsluft abzusaugen und zu filtern. Sie wird in einer Vielzahl von Branchen eingesetzt, insbesondere in solchen, in denen Lackier-, Schleif-, Schweiß- oder ähnliche Arbeiten ausgeführt werden, bei denen Partikel oder Dämpfe entstehen. Diese Geräte spielen eine entscheidende Rolle beim Schutz der Arbeiter, der Umwelt und der Qualität der Endprodukte.
Im Folgenden werde ich umfassend auf die Funktionsweise, verschiedene Typen, die Bedeutung, Vorteile, Anwendungen und Wartung von Absaugwänden eingehen. Diese Abhandlung wird sich über 10.000 Wörter erstrecken und detailliert alle relevanten Aspekte dieser wichtigen Einrichtung abdecken.
Was sind Absaugwände?
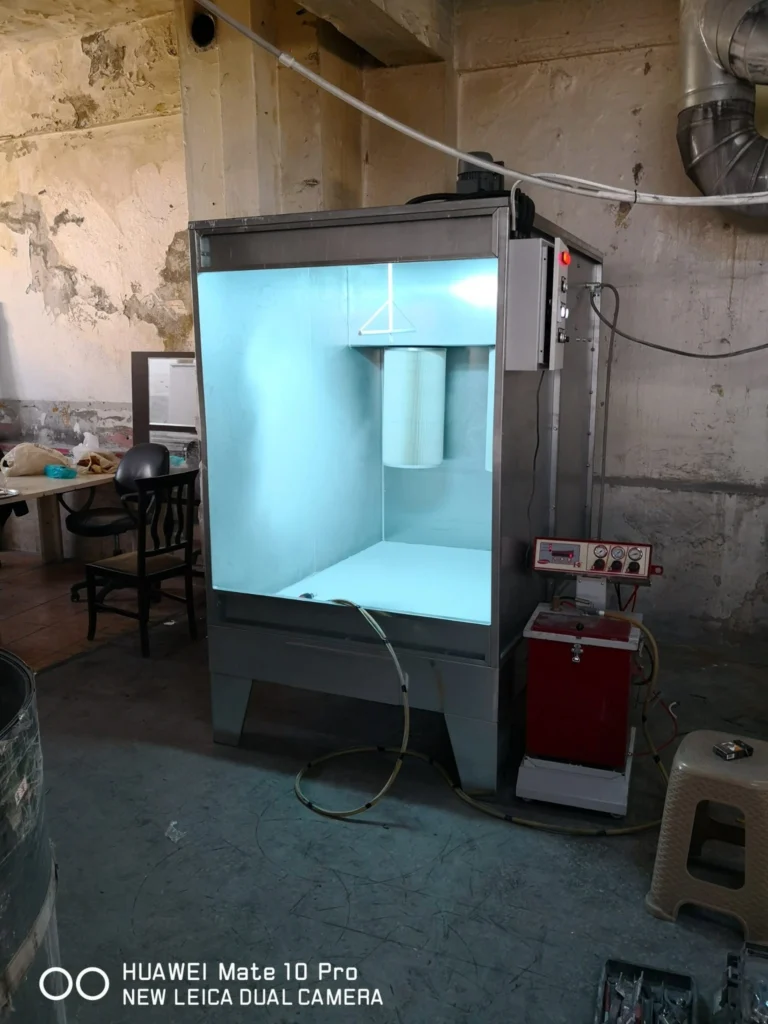
Absaugwände, auch als Absauganlagen oder Absaugkabinen bezeichnet, sind technische Geräte, die entwickelt wurden, um Schadstoffe und Partikel aus der Luft zu entfernen. Sie arbeiten auf der Grundlage eines Lüftungssystems, das die verschmutzte Luft ansaugt, durch Filter leitet und die gereinigte Luft entweder wieder in die Umgebung freisetzt oder nach außen leitet.
In vielen Arbeitsumgebungen entstehen durch Produktionsprozesse gesundheitsschädliche Stoffe, wie zum Beispiel Lackdämpfe, Staub oder chemische Gase. Wenn diese Substanzen nicht ordnungsgemäß entfernt werden, können sie nicht nur die Gesundheit der Arbeiter beeinträchtigen, sondern auch die Qualität der Produktion verringern und die Umwelt schädigen.
Die Hauptaufgabe einer Absaugwand besteht darin, eine saubere und sichere Arbeitsumgebung zu gewährleisten, indem sie potenziell gefährliche Partikel und Dämpfe entfernt. Sie ist sowohl in kleinen Werkstätten als auch in großen industriellen Produktionsanlagen unverzichtbar.
2. Funktionsweise einer Absaugwand
Absaugwände arbeiten auf der Grundlage eines Luftstromsystems, das Schadstoffe aus der Luft filtert und somit für eine saubere Arbeitsumgebung sorgt. Die Funktionsweise kann in mehrere grundlegende Schritte unterteilt werden:
2.1. Ansaugung der verschmutzten Luft
Der erste Schritt im Betrieb einer Absaugwand ist die Ansaugung der verschmutzten Luft. Dies geschieht in der Regel durch leistungsstarke Ventilatoren, die in der Absaugwand eingebaut sind. Diese Ventilatoren erzeugen einen Luftstrom, der Schadstoffe wie Staub, Dämpfe oder chemische Partikel in die Absaugwand zieht.
Je nach Größe der Anlage und dem Umfang der entstehenden Verunreinigungen kann die Absaugleistung variieren. Die Absaugung erfolgt direkt an der Quelle, also dort, wo die Schadstoffe entstehen, um ihre Ausbreitung in der Arbeitsumgebung zu minimieren.
2.2. Filtration der Luft
Sobald die verschmutzte Luft in die Absaugwand gelangt, wird sie durch verschiedene Filtersysteme geleitet. Diese Filter spielen eine entscheidende Rolle, da sie die schädlichen Partikel und Gase aus der Luft entfernen. Die Art der Filter hängt vom jeweiligen Anwendungsbereich ab, da unterschiedliche Prozesse unterschiedliche Schadstoffe erzeugen.
Zu den häufig verwendeten Filtern gehören:
- HEPA-Filter (High-Efficiency Particulate Air): Diese Filter entfernen feine Partikel, die kleiner als 0,3 Mikrometer sind, und sind besonders effektiv bei der Entfernung von Staub und Rauch.
- Aktivkohlefilter: Diese Filter sind ideal zur Entfernung von chemischen Dämpfen und organischen Verbindungen aus der Luft.
- Vorfilter: Diese Filter entfernen größere Partikel und schützen die nachfolgenden Filter vor Verstopfung.
- Nassabscheider: Diese Technologie wird oft für die Entfernung von Farbnebeln oder feuchten Dämpfen verwendet.
2.3. Abluft oder Rückführung
Nachdem die Luft durch die Filter gereinigt wurde, gibt es zwei Hauptmöglichkeiten, wie die Luft weiterverarbeitet wird:
- Rückführung der gefilterten Luft in den Raum: In vielen Fällen, insbesondere in geschlossenen Räumen, wird die gereinigte Luft wieder in den Arbeitsbereich zurückgeführt. Dies ist energieeffizient, da die Wärme in der Luft erhalten bleibt und keine zusätzliche Energie zum Erwärmen frischer Luft benötigt wird.
- Abluft nach außen: In einigen Fällen, insbesondere wenn es sich um giftige Gase oder Dämpfe handelt, wird die gefilterte Luft aus Sicherheitsgründen nach draußen abgeleitet.
2.4. Überwachung und Steuerung
Moderne Absaugwände sind oft mit Überwachungs- und Steuerungssystemen ausgestattet, die sicherstellen, dass die Anlage effizient arbeitet. Dazu gehören:
- Sensoren zur Überwachung der Luftqualität: Diese Sensoren messen kontinuierlich den Schadstoffgehalt in der Luft und können die Lüftungsstärke entsprechend anpassen.
- Filterüberwachung: Einige Systeme verfügen über Anzeigen, die den Zustand der Filter überwachen und signalisieren, wann ein Filterwechsel erforderlich ist.
- Automatische Abschaltung: Bei Störungen oder Gefahren, wie einem Brand oder einem zu hohen Schadstoffgehalt, können diese Systeme automatisch abgeschaltet werden, um die Sicherheit zu gewährleisten.
3. Typen von Absaugwänden
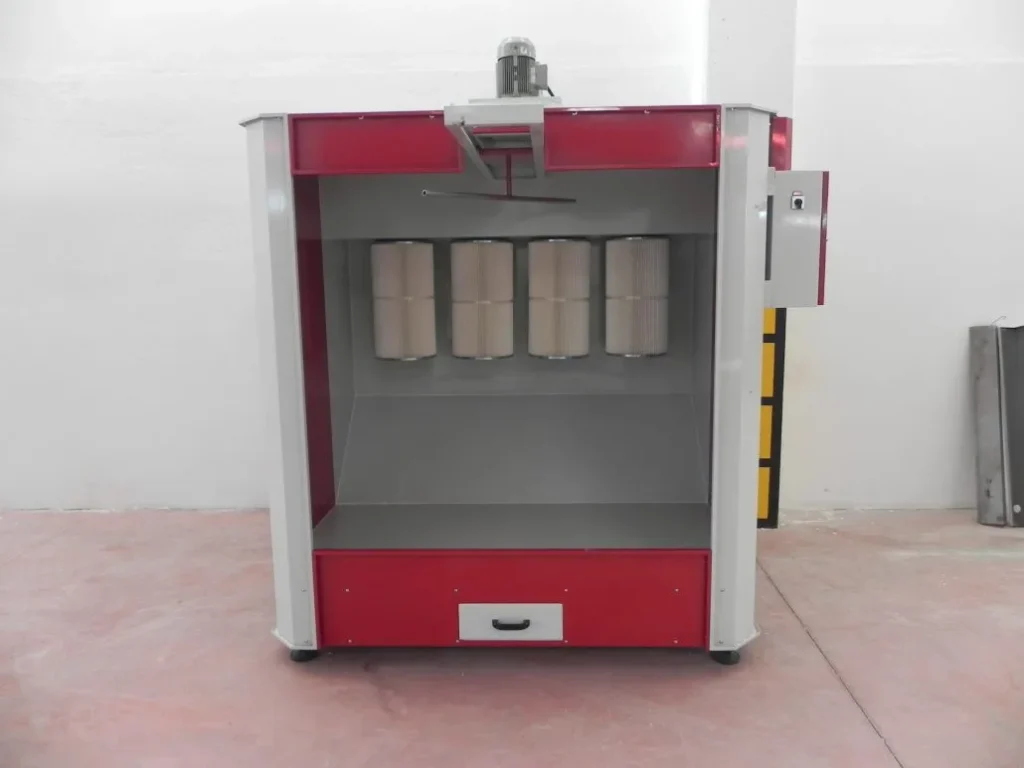
Es gibt verschiedene Arten von Absaugwänden, die je nach Anwendungsbereich und den spezifischen Anforderungen der Industrie ausgewählt werden. Hier sind die gängigsten Typen:
3.1. Trockene Absaugwände
Trockene Absaugwände sind die am häufigsten verwendete Art von Absaugwänden. Sie funktionieren durch die Ansaugung der Luft und die Filtration von Partikeln, ohne dass Wasser zur Reinigung verwendet wird.
- Vorteile: Trockene Absaugwände sind relativ einfach zu warten, da die Filter leicht zugänglich und austauschbar sind. Außerdem benötigen sie kein Wassersystem, was sie kostengünstiger macht.
- Anwendungsgebiete: Diese Absaugwände werden häufig in Lackierbetrieben, Schleifwerkstätten und bei Arbeiten eingesetzt, bei denen Staub und feste Partikel entstehen.
3.2. Nassabsaugwände
Bei Nassabsaugwänden wird die verschmutzte Luft durch einen Wassernebel oder -film geleitet, der die Schadstoffe abfängt und bindet. Diese Technik ist besonders effektiv bei der Entfernung von Farbnebeln oder Partikeln, die leicht an Oberflächen haften.
- Vorteile: Nassabsaugwände sind besonders effektiv bei der Beseitigung von feinen Partikeln und Farbnebeln, da das Wasser die Partikel einfängt und aus der Luft entfernt.
- Anwendungsgebiete: Häufig werden Nassabsaugwände in der Lackier- und Metallverarbeitungsindustrie eingesetzt, wo Farbnebel und feuchte Partikel entstehen.
3.3. Absaugwände mit Aktivkohlefiltern
Absaugwände mit Aktivkohlefiltern sind speziell darauf ausgelegt, organische Dämpfe und Lösungsmittel aus der Luft zu entfernen. Die Aktivkohle absorbiert die Chemikalien und sorgt dafür, dass saubere Luft in den Arbeitsbereich zurückgeführt wird.
- Vorteile: Aktivkohlefilter sind besonders effektiv bei der Beseitigung von Lösungsmitteldämpfen und organischen Verbindungen, die durch Lackierprozesse oder chemische Behandlungen entstehen.
- Anwendungsgebiete: Diese Absaugwände werden häufig in der chemischen Industrie und bei Lackierprozessen eingesetzt, bei denen organische Dämpfe entstehen.
3.4. Mobile Absaugwände
Mobile Absaugwände sind flexible, tragbare Einheiten, die sich leicht bewegen lassen. Diese Wände sind ideal für Werkstätten oder temporäre Baustellen, bei denen der Standort der Arbeiten häufig wechselt.
- Vorteile: Mobile Absaugwände bieten Flexibilität, da sie überall eingesetzt werden können. Sie sind ideal für kleine Werkstätten oder temporäre Projekte, bei denen keine feste Absauganlage installiert werden kann.
- Anwendungsgebiete: Werkstätten, Bauprojekte und temporäre Arbeitsplätze profitieren von der Flexibilität dieser mobilen Lösungen.
3.5. Spezialisierte Absaugwände für bestimmte Anwendungen
Einige Absaugwände sind speziell für bestimmte Anwendungen konzipiert. Dazu gehören beispielsweise Absaugwände für Schweißarbeiten, bei denen metallische Dämpfe und Rauch entstehen, oder spezielle Absaugwände für die Bearbeitung von Kunststoffen, bei denen gefährliche Gase freigesetzt werden können.
- Vorteile: Diese spezialisierten Anlagen sind speziell auf die Anforderungen der jeweiligen Industrie zugeschnitten und gewährleisten eine besonders effektive Entfernung der spezifischen Schadstoffe.
- Anwendungsgebiete: Diese Absaugwände finden Anwendung in der Metallverarbeitung, Kunststoffherstellung, Elektronikindustrie und in anderen spezialisierten Produktionsbereichen.
4. Vorteile von Absaugwänden
Der Einsatz von Absaugwänden bietet eine Vielzahl von Vorteilen, die nicht nur die Effizienz und Produktivität der Produktion verbessern, sondern auch den Schutz der Mitarbeiter und der Umwelt gewährleisten. Hier sind die wichtigsten Vorteile im Detail:
4.1. Verbesserung der Luftqualität
Der offensichtlichste Vorteil von Absaugwänden ist die Verbesserung der Luftqualität am Arbeitsplatz. Schadstoffe wie Staub, Rauch und Dämpfe werden direkt an der Quelle erfasst und gefiltert, bevor sie sich in der Luft ausbreiten können. Dies führt zu einer saubereren und gesünderen Arbeitsumgebung für die Mitarbeiter.
4.2. Schutz der Gesundheit der Mitarbeiter
Viele der Partikel und Dämpfe, die in industriellen Prozessen freigesetzt werden, können gesundheitsschädlich sein. Feinstaub, Lösungsmitteldämpfe oder giftige Gase können Atemprobleme, Allergien oder sogar schwere Krankheiten verursachen. Absaugwände schützen die Mitarbeiter, indem sie diese Schadstoffe effizient aus der Luft entfernen und das Risiko einer Exposition verringern.
4.3. Erhöhung der Produktqualität
Schadstoffe in der Luft können auch die Qualität der Endprodukte beeinträchtigen. In Lackierbetrieben können beispielsweise Staubpartikel zu Unebenheiten in der Lackierung führen. Eine Absaugwand sorgt für eine saubere Umgebung, in der hochwertige Produkte ohne Mängel hergestellt werden können.
4.4. Einhaltung von Umweltvorschriften
In vielen Ländern gibt es strenge Umweltvorschriften, die den Ausstoß von Schadstoffen in die Atmosphäre regeln. Absaugwände helfen Unternehmen, diese Vorschriften einzuhalten, indem sie die schädlichen Partikel und Gase aus der Luft filtern, bevor sie in die Umwelt gelangen.
4.5. Erhöhung der Arbeitssicherheit
In Arbeitsbereichen, in denen brennbare oder explosive Stoffe verarbeitet werden, stellen Absaugwände eine wichtige Sicherheitsmaßnahme dar. Sie verhindern die Ansammlung von brennbaren Gasen oder Stäuben und reduzieren so das Risiko von Explosionen oder Bränden.
4.6. Kosteneffizienz durch Energieeinsparung
Moderne Absaugwände sind oft mit energieeffizienten Lüftern und Filtersystemen ausgestattet, die den Energieverbrauch minimieren. Durch die Rückführung der gefilterten Luft in den Arbeitsbereich kann zudem die Raumtemperatur aufrechterhalten werden, wodurch Heizkosten eingespart werden.
5. Anwendungsgebiete von Absaugwänden
Absaugwände finden in vielen Branchen und Anwendungsbereichen Einsatz, in denen Partikel, Dämpfe oder andere Schadstoffe entstehen. Hier sind einige der wichtigsten Anwendungsgebiete:
5.1. Lackierereien und Beschichtungsbetriebe
Eines der häufigsten Einsatzgebiete für Absaugwände ist die Lackier- und Beschichtungsindustrie. Lacke und Beschichtungen enthalten oft Lösungsmittel und Chemikalien, die während des Auftragsprozesses verdampfen und schädliche Dämpfe freisetzen. Absaugwände sorgen dafür, dass diese Dämpfe gefiltert werden, bevor sie in die Luft gelangen, und tragen somit zur Sicherheit und Qualität der Arbeiten bei.
5.2. Metallverarbeitung und Schweißarbeiten
In der Metallverarbeitung entstehen bei Schweißarbeiten giftige Dämpfe und feine Metallpartikel, die gesundheitsschädlich sein können. Absaugwände für Schweißarbeitsplätze sind darauf ausgelegt, diese Dämpfe und Partikel effektiv abzusaugen und zu filtern.
5.3. Holzverarbeitung
Bei der Holzverarbeitung entsteht eine große Menge an Staub und Spänen, die nicht nur die Gesundheit der Arbeiter gefährden, sondern auch die Maschinen beschädigen können. Absaugwände in Schreinereien oder Holzverarbeitungsbetrieben entfernen den Staub aus der Luft und sorgen für eine saubere und sichere Arbeitsumgebung.
5.4. Automobilindustrie
In der Automobilproduktion, insbesondere in Lackierwerken und bei der Verarbeitung von Kunststoffen, entstehen gefährliche Dämpfe und Partikel. Absaugwände sorgen dafür, dass diese Schadstoffe sicher entfernt werden, was die Sicherheit der Arbeiter und die Qualität der Endprodukte verbessert.
5.5. Elektronikindustrie
In der Elektronikfertigung entstehen bei der Verarbeitung von Kunststoffen oder Löten giftige Gase und Dämpfe. Absaugwände sorgen dafür, dass diese Gase aus der Luft entfernt werden und keine gesundheitlichen Risiken für die Mitarbeiter bestehen.
5.6. Chemische Industrie
In der chemischen Industrie kommen viele gefährliche Substanzen zum Einsatz, die bei der Verarbeitung oder Herstellung freigesetzt werden können. Absaugwände schützen die Arbeiter vor der Exposition gegenüber schädlichen Chemikalien und tragen zur Einhaltung von Umweltvorschriften bei.
5.7. Pharmazeutische Industrie
Bei der Herstellung von Medikamenten oder anderen pharmazeutischen Produkten entstehen oft feine Partikel oder Dämpfe, die nicht in die Luft gelangen dürfen, um eine Kontamination der Produkte zu verhindern. Absaugwände sorgen für eine saubere und kontrollierte Umgebung, die höchsten Qualitätsanforderungen entspricht.
6. Wartung und Pflege von Absaugwänden
Damit Absaugwände effektiv arbeiten und eine lange Lebensdauer haben, ist regelmäßige Wartung unerlässlich. Die Wartung gewährleistet, dass alle Komponenten der Absaugwand optimal funktionieren und der Luftstrom sowie die Filtrationseffizienz aufrechterhalten bleiben.
6.1. Regelmäßiger Filterwechsel
Einer der wichtigsten Wartungsschritte bei Absaugwänden ist der regelmäßige Wechsel der Filter. Abhängig vom Anwendungsbereich und der Häufigkeit der Nutzung können Filter sich schnell mit Partikeln und Verunreinigungen füllen, was ihre Effizienz beeinträchtigt. Verstopfte Filter reduzieren den Luftstrom und erhöhen den Energieverbrauch, weshalb sie in regelmäßigen Abständen ausgetauscht werden sollten.
6.2. Überprüfung der Lüftungssysteme
Die Ventilatoren und Lüftungssysteme in der Absaugwand müssen ebenfalls regelmäßig überprüft werden, um sicherzustellen, dass sie ordnungsgemäß funktionieren. Verstopfte oder beschädigte Ventilatoren können den Luftstrom behindern und die Leistung der gesamten Anlage beeinträchtigen. Zudem sollte darauf geachtet werden, dass keine Lecks im System vorhanden sind, die dazu führen könnten, dass ungefilterte Luft in die Arbeitsumgebung gelangt.
6.3. Reinigung der Anlage
Die Wände, Böden und inneren Teile der Absaugwand sollten regelmäßig gereinigt werden, um sicherzustellen, dass keine Staub- oder Farbpartikel an den Oberflächen haften. Dies verhindert, dass sich Partikel auf die zu bearbeitenden Werkstücke setzen und die Qualität der Lackierung oder Bearbeitung beeinträchtigen.
6.4. Inspektion der Sicherheitsfunktionen
Absaugwände sind oft mit verschiedenen Sicherheitsfunktionen ausgestattet, wie z. B. Notabschaltungen oder Brandmeldern. Diese Sicherheitsfunktionen sollten regelmäßig auf ihre Funktionsfähigkeit überprüft werden, um im Falle eines Notfalls die Sicherheit der Arbeiter gewährleisten zu können.
6.5. Software-Updates für digitale Steuerungssysteme
Moderne Absaugwände sind häufig mit digitalen Steuerungssystemen ausgestattet, die den Betrieb der Anlage überwachen und steuern. Diese Systeme sollten regelmäßig auf den neuesten Stand gebracht werden, um sicherzustellen, dass sie effizient arbeiten und alle notwendigen Daten korrekt erfassen.
7. Fazit
Absaugwände sind in vielen Industrien ein unverzichtbares Werkzeug, um saubere, sichere und effiziente Arbeitsumgebungen zu schaffen. Sie tragen nicht nur dazu bei, die Gesundheit der Arbeiter zu schützen, sondern verbessern auch die Qualität der Endprodukte und helfen Unternehmen, strenge Umweltvorschriften einzuhalten.
EMS Powder Coating Equipment bietet eine breite Palette von Absaugwänden, die speziell auf die Bedürfnisse verschiedener Branchen zugeschnitten sind. Mit innovativen Technologien, hoher Zuverlässigkeit und umfassendem Kundensupport sind EMS-Absaugwände die ideale Wahl für Unternehmen, die eine langfristige, effiziente Lösung für ihre Absaugbedürfnisse suchen.
Mit regelmäßiger Wartung und Pflege können Absaugwände ihre volle Leistungsfähigkeit über viele Jahre hinweg beibehalten, was sie zu einer lohnenden Investition für jedes Unternehmen macht.
Lackierkabinen sind geschlossene Räume, die speziell für den Lackierprozess von Werkstücken entwickelt wurden. Sie bieten eine kontrollierte Umgebung, die es ermöglicht, eine gleichmäßige und qualitativ hochwertige Lackierung zu erzielen. Lackierkabinen werden in verschiedenen Größen und Ausführungen angeboten, je nach den Anforderungen der Werkstücke und des Betriebes. Eine besonders kompakte Variante ist die „Lackierkabine Klein“, die in Werkstätten mit begrenztem Platzangebot oder für kleinere Lackieraufträge verwendet wird.
Funktionsweise einer Lackierkabine
Eine Lackierkabine, unabhängig von ihrer Größe, ist so konstruiert, dass sie die Ausbreitung von Staub und Schmutz minimiert und eine gleichmäßige Zufuhr von frischer Luft gewährleistet. Dies erfolgt durch ein speziell ausgeklügeltes Belüftungssystem, das dafür sorgt, dass die Lackierumgebung frei von schädlichen Partikeln bleibt. Gleichzeitig wird überschüssiger Lackdampf und flüchtige organische Verbindungen (VOCs) abgesaugt, was sowohl für die Qualität der Lackierung als auch für die Gesundheit der Arbeiter von großer Bedeutung ist.
In einer kleinen Lackierkabine (Lackierkabine Klein) ist die Luftzirkulation ebenfalls so ausgelegt, dass der gesamte Bereich des Raumes schnell und effektiv belüftet wird. Ein Filter- und Absaugsystem zieht die Abluft aus der Kabine und verhindert, dass sich toxische Dämpfe und Partikel im Arbeitsbereich ausbreiten. Dies ist besonders wichtig, da kleinere Lackierkabinen oft in geschlossenen oder beengten Räumen installiert werden.
Einsatzgebiete und Vorteile von Lackierkabinen Klein
Lackierkabinen Klein sind besonders in Werkstätten mit begrenztem Platzangebot von Vorteil. Sie finden häufig Anwendung in folgenden Bereichen:
- Automobilindustrie: Kleine Werkstätten, die auf Reparatur oder Lackierung von Fahrzeugteilen spezialisiert sind, nutzen Lackierkabinen Klein, um ihre Arbeitsabläufe effizient und sauber zu gestalten.
- Möbelindustrie: Tischlereien und Möbelwerkstätten, die Möbel oder Holzprodukte lackieren, setzen oft kleinere Kabinen ein, um präzise und kontrollierte Lackierungen vorzunehmen.
- Handwerksbetriebe: Schreinereien, Metallwerkstätten und Künstler, die kleinere Objekte oder Einzelstücke lackieren möchten, profitieren von den flexiblen Einsatzmöglichkeiten kleiner Lackierkabinen.
Die Vorteile einer Lackierkabine Klein liegen in ihrer Kompaktheit und Flexibilität. Diese Kabinen nehmen wenig Platz in Anspruch und können daher auch in kleinen Werkstätten oder Garagen problemlos installiert werden. Zudem bieten sie durch die kontrollierte Luftzirkulation und Absaugtechnik eine gleichbleibend hohe Qualität der Lackierung, die mit manuellen Techniken oft nicht zu erreichen ist.
Sicherheitsaspekte
Die Lackierung von Objekten kann gesundheitsschädliche Dämpfe und Chemikalien freisetzen, weshalb der sichere Betrieb einer Lackierkabine von großer Bedeutung ist. In einer Lackierkabine Klein sind verschiedene Sicherheitsmerkmale integriert, um die Gesundheit der Arbeiter zu schützen. Dazu gehören:
- Luftfilter und Absauganlagen: Diese sorgen dafür, dass schädliche Dämpfe und Partikel schnell aus der Kabine entfernt werden, bevor sie in die Luft gelangen.
- Brandschutzsysteme: Lacke und Farben sind oft entzündlich. Daher sind in modernen Lackierkabinen Brandschutzsysteme eingebaut, die im Falle eines Feuers schnell eingreifen können.
- Ex-geschützte Beleuchtung: Da sich in der Kabine explosive Dämpfe ansammeln können, wird die Beleuchtung in vielen Lackierkabinen so installiert, dass sie keine Funken erzeugt, die zu einer Entzündung führen könnten.
Technologische Entwicklungen in Lackierkabinen Klein
Moderne Lackierkabinen Klein sind nicht nur funktional, sondern auch technologisch auf dem neuesten Stand. Viele dieser Kabinen verfügen über fortschrittliche Luftzirkulationssysteme, die eine noch effizientere Belüftung und Absaugung ermöglichen. Auch die Filtertechnologie hat sich in den letzten Jahren weiterentwickelt, sodass die Kabinen besonders umweltfreundlich und energieeffizient arbeiten.
Ein weiterer technischer Fortschritt sind computergestützte Steuerungssysteme, die die Bedienung der Kabinen noch einfacher machen. Mit diesen Systemen können die Luftfeuchtigkeit, Temperatur und andere Faktoren in der Kabine genau überwacht und angepasst werden, um die besten Ergebnisse beim Lackieren zu erzielen.
Fazit
Lackierkabinen Klein bieten eine ausgezeichnete Lösung für kleinere Werkstätten, die auf eine präzise und saubere Lackierung angewiesen sind. Sie kombinieren kompakte Größe mit hoher Funktionalität und tragen so zu einer effizienten und sicheren Arbeitsumgebung bei. Durch den fortschrittlichen technischen Standard, die hohe Sicherheitsausstattung und die Flexibilität bei der Nutzung sind sie in vielen Bereichen, von der Automobilindustrie bis hin zum Handwerk, ein unverzichtbares Hilfsmittel. Wer in eine Lackierkabine Klein investiert, profitiert nicht nur von einer gleichbleibend hohen Lackierqualität, sondern auch von einer nachhaltigen und sicheren Arbeitsweise.
Lackierkabinen sind spezialisierte, geschlossene Räume, die dafür entwickelt wurden, um den Lackierprozess unter kontrollierten Bedingungen durchzuführen. Ihre Hauptfunktion besteht darin, eine Umgebung zu schaffen, in der Werkstücke sicher und effizient lackiert werden können, ohne dass Staub, Schmutz oder andere Partikel die Qualität der Lackierung beeinträchtigen. Sie sind sowohl in großen industriellen Einrichtungen als auch in kleineren Handwerksbetrieben von großer Bedeutung, da sie eine saubere und sichere Arbeitsumgebung bieten, die eine hohe Lackierqualität gewährleistet.
Die kleinere Ausführung, die sogenannte Lackierkabine Klein, ist speziell für den Einsatz in Werkstätten mit begrenztem Platzangebot konzipiert und bietet zahlreiche Vorteile, die sowohl die Effizienz als auch die Sicherheit des Lackierprozesses verbessern. Eine Lackierkabine Klein bietet eine kompakte Lösung für Betriebe, die eine kontrollierte Lackierung von kleineren Objekten oder Einzelstücken benötigen. Sie wird häufig in Werkstätten wie Autolackierbetrieben, Möbelwerkstätten, kleinen Handwerksbetrieben oder sogar in künstlerischen Bereichen eingesetzt, in denen präzise und qualitativ hochwertige Lackierungen erforderlich sind. Im Gegensatz zu großen industriellen Lackierkabinen, die in der Regel eine größere Anzahl an Werkstücken gleichzeitig bearbeiten, ist die Lackierkabine Klein auf kleinere Produktionsmengen oder Einzelstücke ausgelegt und zeichnet sich durch ihre Flexibilität und Anpassungsfähigkeit aus.
Eine wichtige Funktion jeder Lackierkabine, auch der kleineren Modelle, ist das Absaugsystem. Dieses System sorgt dafür, dass überschüssige Lackdämpfe, Lösungsmittel und andere flüchtige organische Verbindungen (VOCs) schnell aus der Kabine entfernt werden. Dadurch wird verhindert, dass schädliche Chemikalien in die Atemluft des Werkers gelangen, was die Gesundheit schützt und gleichzeitig die Qualität der Lackierung sicherstellt. Auch die Luftzirkulation spielt eine entscheidende Rolle in einer Lackierkabine. Sie muss so gestaltet sein, dass frische Luft in die Kabine gelangt und verbrauchte, kontaminierte Luft schnell und effizient abgesaugt wird. In modernen Lackierkabinen Klein wird oft auf ein zirkulierendes Luftsystem gesetzt, das dafür sorgt, dass die Luft kontinuierlich bewegt wird, um Staub und Schmutzpartikel zu entfernen und so eine möglichst saubere Umgebung für den Lackierprozess zu schaffen.
Darüber hinaus ist es bei der Arbeit in einer Lackierkabine wichtig, auf Sicherheitsaspekte zu achten. Lacke und Farben enthalten oft Lösungsmittel, die leicht entzündlich sind und gefährliche Dämpfe abgeben können. Aus diesem Grund sind in vielen modernen Lackierkabinen Brandschutzvorkehrungen integriert. Diese umfassen in der Regel automatische Sprinklersysteme und eine speziell isolierte und sicherheitsgeprüfte Elektrik, um das Risiko eines Brandes zu minimieren. Zusätzlich sorgen spezielle Filteranlagen dafür, dass schädliche Stoffe aus der Abluft gefiltert werden, bevor sie in die Umwelt abgegeben werden. Ein weiterer wichtiger Aspekt der Lackierkabinen Klein ist die Energieeffizienz. Durch den geringeren Platzbedarf und die meist kleinere Größe sind diese Kabinen in der Regel auch energieeffizienter als ihre größeren Pendants.
Sie benötigen weniger Energie für Heizung, Belüftung und Absaugung, was nicht nur die Betriebskosten senkt, sondern auch einen Beitrag zur Reduzierung des ökologischen Fußabdrucks des Betriebs leistet. In der heutigen Zeit sind Lackierkabinen Klein häufig mit modernen Steuerungssystemen ausgestattet, die es dem Bediener ermöglichen, verschiedene Parameter wie Temperatur, Luftfeuchtigkeit und Absaugleistung präzise zu regulieren. Diese Automatisierung trägt nicht nur zur Verbesserung der Lackierqualität bei, sondern auch zur Effizienzsteigerung und zur Reduzierung von Ausschuss. Ein weiterer Vorteil der Lackierkabinen Klein ist die einfache Integration in bestehende Arbeitsumgebungen. Sie können oft problemlos in kleinere Werkstätten, Garagen oder sogar in speziell dafür eingerichteten Räumen installiert werden. Ihre kompakte Bauweise ermöglicht es, den verfügbaren Platz optimal zu nutzen, was für viele kleine und mittlere Betriebe von entscheidender Bedeutung ist. Eine Lackierkabine Klein stellt somit eine ideale Lösung für Unternehmen dar, die professionelle Lackierarbeiten durchführen möchten, ohne auf den Komfort und die Effizienz einer großen industriellen Kabine angewiesen zu sein.
In vielen Fällen bieten diese Kabinen eine hervorragende Kombination aus Kosteneffizienz, Platzersparnis und hoher Lackierqualität. Darüber hinaus ermöglichen sie es auch kleinen Handwerksbetrieben und Einzelunternehmern, ihre Arbeitsprozesse zu optimieren und auf einem professionellen Niveau zu arbeiten, ohne dass dafür umfangreiche Investitionen in größere Anlagen erforderlich sind. Die kontinuierliche Weiterentwicklung der Technik sorgt dafür, dass Lackierkabinen Klein immer leistungsfähiger und umweltfreundlicher werden. Dank innovativer Filtersysteme, intelligenter Steuerungssysteme und energieeffizienter Technologien bieten diese Kabinen eine nachhaltige Lösung für den modernen Lackierbetrieb, der sowohl ökologischen als auch ökonomischen Anforderungen gerecht wird. Die Bedeutung der Lackierkabinen Klein wird in vielen Branchen immer größer, da sie nicht nur die Qualität der Arbeit verbessern, sondern auch zur Sicherheit der Mitarbeiter und zur Einhaltung von Umweltvorgaben beitragen. Der Fortschritt in der Technologie der Lackierkabinen hat es ermöglicht, dass auch kleinere Werkstätten von den Vorteilen dieser hochentwickelten Systeme profitieren können.
Moderne Lackierkabinen Klein bieten zusätzlich zahlreiche weitere Vorteile, die den Betrieb effizienter und sicherer gestalten. Einer dieser Vorteile ist die präzise Steuerung der Lackierumgebung. Durch die Anpassung der Belüftung, Temperatur und Luftfeuchtigkeit wird die optimale Lackierqualität sichergestellt. Diese präzise Kontrolle ermöglicht es, eine gleichmäßige und fehlerfreie Beschichtung zu erzielen, was besonders bei empfindlichen Oberflächen oder anspruchsvollen Lackieraufträgen von Bedeutung ist. Darüber hinaus tragen diese Kabinen durch den kontinuierlichen Luftaustausch dazu bei, dass sich keine schädlichen Dämpfe oder gefährlichen Partikel ansammeln, was das Arbeitsumfeld erheblich sicherer macht. Die Verwendung von Hochleistungsfiltern sorgt dafür, dass selbst kleinste Schadstoffe aus der Luft gefiltert werden, was nicht nur die Lackierqualität verbessert, sondern auch einen Beitrag zum Umweltschutz leistet.
Ein weiterer wichtiger Punkt ist die Benutzerfreundlichkeit der Lackierkabinen Klein. Viele dieser Kabinen sind mit digitalen Steuerungen und Touchscreens ausgestattet, die eine einfache Handhabung ermöglichen. Bediener können auf einfache Weise alle relevanten Parameter wie Luftzirkulation, Temperatur und Luftfeuchtigkeit anpassen, ohne manuell eingreifen zu müssen. Dies spart Zeit und reduziert Fehlerquellen, da die Kabine automatisch die besten Bedingungen für den Lackierprozess einstellt. Einige Modelle bieten auch eine automatische Reinigung der Filter und ein Monitoring-System, das den Zustand der Kabine überwacht und frühzeitig auf Wartungsbedarf hinweist, um den Betrieb reibungslos aufrechtzuerhalten.
Zusätzlich bieten moderne Lackierkabinen Klein eine hohe Flexibilität bei der Bearbeitung verschiedener Materialien und Lacke. Ob für Holz, Metall, Kunststoff oder andere Materialien – die Kabinen sind so konzipiert, dass sie eine breite Palette von Lackieranwendungen abdecken. Dies ist besonders vorteilhaft für Unternehmen, die in verschiedenen Bereichen tätig sind und eine Vielzahl von Werkstücken mit unterschiedlichen Lackieranforderungen bearbeiten. Durch die Verwendung von speziellen Lackierpistolen und -systemen, die perfekt auf die Kabine abgestimmt sind, lässt sich die Lackierung effizient und gleichmäßig durchführen.
Lackierkabinen Klein sind in der Regel mit verschiedenen Sicherheitsfunktionen ausgestattet, die sowohl den Betreiber als auch die Umwelt schützen. Neben den bereits erwähnten Absaug- und Filteranlagen gibt es in vielen Kabinen auch Schutzvorrichtungen gegen Überhitzung und eine integrierte Notabschaltung für den Fall von Störungen. Zudem bieten viele Kabinen Modelle, die eine ex-geschützte Ausstattung haben, um explosionsfähige Dämpfe zu vermeiden. Diese Sicherheitsvorkehrungen sind nicht nur gesetzlich vorgeschrieben, sondern tragen auch maßgeblich dazu bei, das Risiko von Unfällen zu minimieren.
Ein oft unterschätzter Vorteil von Lackierkabinen Klein ist die kosteneffiziente Nutzung von Ressourcen. Im Vergleich zu größeren industriellen Kabinen benötigen sie weniger Energie, weniger Lackmaterial und weniger Platz, was für kleinere Unternehmen und Handwerksbetriebe einen großen finanziellen Vorteil darstellt. Die geringe Stellfläche und der niedrige Energieverbrauch helfen, die Betriebskosten zu senken, während gleichzeitig eine hohe Lackierqualität beibehalten wird. Dies ermöglicht es vielen kleineren Betrieben, auf dem Markt wettbewerbsfähig zu bleiben und dennoch einen hohen Qualitätsstandard zu bieten.
Darüber hinaus ist die Umweltfreundlichkeit von Lackierkabinen Klein ein weiterer wichtiger Aspekt. Die Fortschritte in der Filtertechnik und der Energieeffizienz tragen dazu bei, den ökologischen Fußabdruck des Betriebs zu minimieren. So werden nicht nur schädliche Abgase gefiltert, sondern auch der Energieverbrauch gesenkt, was langfristig sowohl den Betriebskosten als auch der Umwelt zugutekommt. Viele Hersteller von Lackierkabinen Klein setzen auf umweltfreundliche Materialien und Technologien, die den gesetzlichen Vorgaben entsprechen und gleichzeitig zur Reduzierung von Emissionen beitragen.
Zusammenfassend lässt sich sagen, dass Lackierkabinen Klein eine äußerst praktische und effiziente Lösung für Betriebe darstellen, die auf hochwertige Lackierungen angewiesen sind, aber über begrenzte Ressourcen und Platzverhältnisse verfügen. Die Kombination aus Kompaktheit, Sicherheit, Flexibilität und Energieeffizienz macht sie zu einem unverzichtbaren Werkzeug in vielen Bereichen, von der Automobil- und Möbelindustrie bis hin zu kleineren Handwerksbetrieben. Die kontinuierliche Weiterentwicklung der Technologie sorgt dafür, dass diese Kabinen nicht nur die Anforderungen der modernen Lackiertechniken erfüllen, sondern auch einen wichtigen Beitrag zum Umweltschutz leisten. Unternehmen, die in eine Lackierkabine Klein investieren, profitieren von einer langfristigen Kostenersparnis, einer besseren Arbeitsumgebung und einer höheren Qualität ihrer Produkte.
Pulverkabine Absaugung
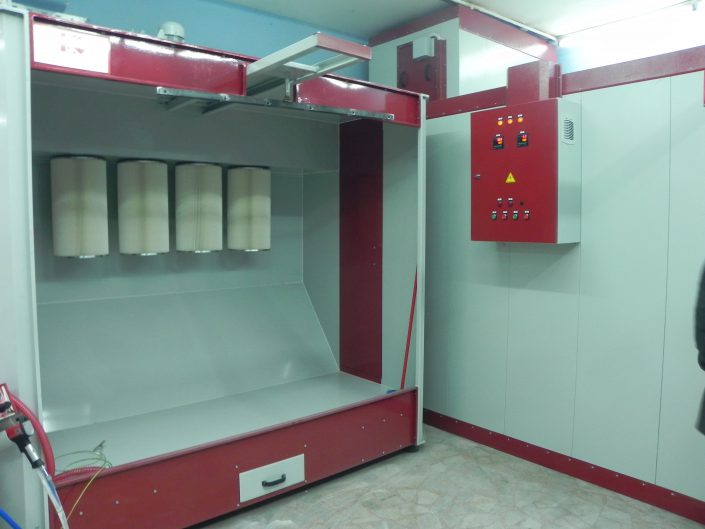
Eine Pulverkabine mit Absaugung ist eine spezialisierte Art von Lackierkabine, die für das Pulverbeschichtungsverfahren verwendet wird. Beim Pulverbeschichten wird ein trockener Pulverlack auf ein Werkstück aufgetragen, der dann unter Hitze geschmolzen wird, um eine gleichmäßige, haltbare und widerstandsfähige Schicht zu bilden. Eine Pulverkabine ist mit einem speziellen Absaugsystem ausgestattet, das dazu dient, überschüssiges Pulver, Staub und andere Partikel während des Lackierprozesses zu entfernen. Dies ist besonders wichtig, um eine saubere und sichere Arbeitsumgebung zu gewährleisten und eine gleichmäßige Beschichtung auf den Werkstücken zu erzielen.
Funktion einer Pulverkabine mit Absaugung
Das Hauptziel einer Pulverkabine mit Absaugung ist es, die Luft im Arbeitsbereich zu reinigen und das überschüssige Pulver zu filtern. Während des Pulverbeschichtungsprozesses kann eine erhebliche Menge an feinem Pulver freigesetzt werden. Ohne ein effizientes Absaugsystem würde dieses Pulver in der Luft schweben, was nicht nur die Qualität der Beschichtung beeinträchtigen könnte, sondern auch gesundheitliche Risiken für die Arbeiter mit sich bringt.
Das Absaugsystem in einer Pulverkabine funktioniert durch starke Ventilatoren und Filter, die die Luft im Inneren der Kabine zirkulieren lassen. Überschüssiges Pulver wird durch spezielle Absaugvorrichtungen von der Oberfläche der Werkstücke entfernt und in einem Filterabscheider oder einem Filtersystem gesammelt. Diese Systeme sind darauf ausgelegt, das Pulver effektiv zu trennen und zu verhindern, dass es in die Atmosphäre oder in andere Teile der Werkstatt gelangt.
Typen von Absaugungssystemen in Pulverkabinen
- Wandabsaugung: Hierbei wird die Luft über die Wände der Kabine abgesogen. Diese Systeme sind einfach und effektiv, da sie eine gleichmäßige Luftströmung erzeugen, die das Pulver effizient abtransportiert.
- Bodenabsaugung: Bei dieser Variante wird die Luft durch den Boden der Kabine abgesogen. Sie eignet sich gut für Kabinen mit einer größeren Arbeitsfläche, da sie eine bessere Verteilung des Luftstroms ermöglicht.
- Zentralisierte Absaugsysteme: In größeren Betrieben werden oft zentralisierte Absaugsysteme eingesetzt, die mehrere Kabinen gleichzeitig mit einem einzigen Filtersystem verbinden. Diese Systeme sind besonders effizient, da sie große Mengen an Luft in kurzer Zeit filtern können.
- Vakuumabsaugung: Diese Systeme erzeugen ein Vakuum, das überschüssiges Pulver aus der Kabine zieht und es direkt in spezielle Sammelbehälter oder Filter führt. Dies minimiert den Staub in der Kabine und hilft, die Luftqualität zu verbessern.
Bedeutung der Filtertechnik
Die Filtertechnik spielt eine zentrale Rolle bei der Effizienz einer Pulverkabine mit Absaugung. Hochleistungsfilter sind notwendig, um das feine Pulver aus der Luft zu entfernen und es in einem Sammelbehälter zu sammeln, der entweder wiederverwendet oder entsorgt werden kann. In vielen modernen Pulverkabinen werden mehrstufige Filtersysteme eingesetzt, die das Pulver in verschiedenen Phasen filtern, um die höchste Effizienz zu gewährleisten. Dazu gehören beispielsweise:
- Vliesfilter: Diese fangen die groben Partikel ab und verhindern, dass sie in die Abluft gelangen.
- Hochleistungspartikel-Filter: Diese speziell entwickelten Filter können die feinsten Partikel herausfiltern, die nicht in die Luft gelangen dürfen.
- Elektrostatische Filter: Diese Filter nutzen elektrostatische Kräfte, um das Pulver effektiv zu binden und es aus der Luft zu entfernen.
Vorteile einer Pulverkabine mit Absaugung
- Verbesserte Luftqualität: Ein gut funktionierendes Absaugsystem sorgt dafür, dass der Staub und die feinen Partikel, die beim Pulverbeschichtungsprozess entstehen, schnell entfernt werden. Dies sorgt für eine saubere Arbeitsumgebung und schützt die Gesundheit der Mitarbeiter vor den gesundheitsschädlichen Auswirkungen von Staub und giftigen Dämpfen.
- Wiederverwendbarkeit des Pulvers: Das Absaugungssystem ermöglicht die Rückgewinnung von überschüssigem Pulver, das nicht auf den Werkstücken haften bleibt. Dieses Pulver kann nach dem Filtern wiederverwendet werden, was die Kosten für Material senkt und die Effizienz erhöht.
- Hohe Lackierqualität: Durch die konstante Entfernung von überschüssigem Pulver wird verhindert, dass dieses die Lackierung von anderen Werkstücken beeinflusst. Das sorgt für eine gleichmäßige Beschichtung ohne Verunreinigungen oder unerwünschte Farbschattierungen.
- Erhöhte Sicherheit: Da beim Pulverbeschichtungsprozess entzündliche Stoffe freigesetzt werden, reduziert das Absaugsystem das Risiko von Feuer oder Explosionen, indem es das Pulver effizient von der Luft entfernt. Dies trägt zur allgemeinen Sicherheit in der Werkstatt bei.
- Energieeffizienz: Moderne Absaugsysteme sind oft sehr energieeffizient und verbrauchen weniger Energie als ältere Modelle. Zudem sorgen optimierte Filtersysteme dafür, dass weniger Energie für die Luftzirkulation und das Entfernen von überschüssigem Pulver benötigt wird.
Wartung und Pflege
Die regelmäßige Wartung und Pflege des Absaugsystems ist entscheidend, um die Effizienz der Pulverkabine langfristig zu erhalten. Filter müssen regelmäßig gereinigt oder ausgetauscht werden, um eine optimale Leistung sicherzustellen. Eine regelmäßige Inspektion der Absaugvorrichtungen, Ventilatoren und des gesamten Systems ist notwendig, um Verschleiß zu vermeiden und sicherzustellen, dass keine Lecks oder Blockaden im System auftreten.
Fazit
Eine Pulverkabine mit Absaugung ist ein unverzichtbares Werkzeug für Betriebe, die das Pulverbeschichtungsverfahren anwenden. Sie sorgt nicht nur für eine saubere und sichere Arbeitsumgebung, sondern trägt auch zur Effizienzsteigerung und Qualitätssicherung bei. Durch moderne Absaug- und Filtertechnologien wird überschüssiges Pulver effektiv entfernt und wiederverwendet, was sowohl die Betriebskosten senkt als auch die Umwelt schont. Unternehmen, die in eine Pulverkabine mit Absaugung investieren, profitieren von einer hohen Lackierqualität, einer verbesserten Arbeitssicherheit und einer optimierten Ressourcennutzung.
Eine Pulverkabine mit Absaugung ist somit ein zentrales Element für effizientes und sicheres Pulverbeschichten. Sie sorgt nicht nur für eine saubere Arbeitsumgebung, sondern auch für eine qualitativ hochwertige Lackierung. Der kontinuierliche Luftstrom, der durch das Absaugsystem erzeugt wird, entfernt überschüssiges Pulver aus der Kabine, sodass die Luft konstant gefiltert bleibt und keine schädlichen Partikel in die Umgebung gelangen. Ein effektives Absaugsystem ist von entscheidender Bedeutung, um zu verhindern, dass das überschüssige Pulver sich in der Luft verteilt oder sich auf Werkstücken ablagert, die nicht lackiert werden sollen. Diese Systeme garantieren, dass die Lackierung gleichmäßig und ohne Verunreinigungen erfolgt.
Des Weiteren tragen sie zur Reduzierung der Materialverschwendung bei, indem das überschüssige Pulver gefiltert und wiederverwendet werden kann. Es ist auch wichtig zu beachten, dass die richtige Wartung des Absaug- und Filtersystems dafür sorgt, dass die Pulverkabine über Jahre hinweg effizient arbeitet. Regelmäßige Inspektionen und Filterwechsel verhindern Verstopfungen und gewährleisten eine stabile Leistung. Zusätzlich zu den praktischen Vorteilen trägt das Absaugsystem auch zur Sicherheit bei, indem es das Risiko von Explosionen oder Bränden reduziert, die durch die Ansammlung von Pulverdämpfen entstehen könnten. In der modernen Fertigung sind Pulverkabinen mit Absaugung ein unverzichtbares Werkzeug für Unternehmen, die Pulverbeschichtungen auf Materialien wie Metall, Kunststoff oder Holz anwenden. Sie verbessern nicht nur die Qualität des Endprodukts, sondern optimieren auch den gesamten Arbeitsprozess und sorgen dafür, dass die Arbeitsumgebung sicher und sauber bleibt. Wenn man auf effiziente Pulverbeschichtung angewiesen ist, sollte eine qualitativ hochwertige Pulverkabine mit Absaugung eine der ersten Investitionen sein.
Die Wahl einer Pulverkabine mit Absaugung hängt stark von den individuellen Anforderungen des Betriebs ab. Es gibt viele verschiedene Modelle, die je nach Größe und Leistung variieren, um den spezifischen Bedürfnissen gerecht zu werden. Für kleinere Werkstätten oder Betriebe mit begrenztem Platzangebot gibt es kompakte Pulverkabinen, die dennoch eine effiziente Absaugung und Filtration bieten. Diese Modelle sind ideal für kleinere Produktionsmengen und bieten eine kostengünstige Lösung, ohne auf Qualität und Sicherheit verzichten zu müssen. Für größere industrielle Anwendungen gibt es größere, leistungsstärkere Kabinen mit zentralisierten Absaugsystemen, die mehrere Lackierstationen gleichzeitig bedienen können und die Effizienz im Betrieb weiter steigern.
In vielen Fällen können diese Systeme auf die individuellen Bedürfnisse des Unternehmens angepasst werden, etwa durch die Installation zusätzlicher Filterstufen oder die Wahl eines leistungsfähigeren Absaugsystems, um eine noch höhere Luftqualität zu gewährleisten. Eine wichtige Überlegung bei der Wahl eines Absaugsystems ist die Energieeffizienz. Da die Kabinen oft über längere Zeiträume hinweg betrieben werden, ist es entscheidend, dass die Absauganlage energieeffizient arbeitet, um die Betriebskosten zu senken. Dies kann durch den Einsatz von modernen, energiesparenden Ventilatoren und Filtern erreicht werden, die die gleiche Leistung bei einem geringeren Energieverbrauch bieten. Ein weiterer wichtiger Aspekt ist die Benutzerfreundlichkeit der Kabine.
Moderne Pulverkabinen sind oft mit benutzerfreundlichen Steuerungssystemen ausgestattet, die eine einfache Handhabung ermöglichen. Dies erleichtert den Bedienern das Einstellen von Parametern wie Luftstromgeschwindigkeit und Filterkontrollen, was den Betrieb noch effizienter macht. Ein digitaler Bildschirm oder eine Touchscreen-Steuerung ermöglicht eine präzise Steuerung und Anpassung der Kabine während des Lackierprozesses. Für Unternehmen, die viel mit unterschiedlichen Pulverlacken arbeiten, bieten manche Modelle auch eine einfache Umstellung zwischen verschiedenen Pulverarten, um die Flexibilität zu maximieren. Die Integration von fortschrittlichen Sicherheitsmerkmalen in moderne Pulverkabinen mit Absaugung ist ebenfalls ein wichtiger Punkt. So werden viele Kabinen mit Explosionsschutzvorrichtungen und Brandschutzsystemen ausgestattet, die verhindern, dass sich entflammbares Pulver in der Luft entzündet und zu einem Brand oder einer Explosion führt.
Die Kombination von sicherem Betrieb und leistungsfähiger Absaugtechnik sorgt dafür, dass der Pulverbeschichtungsprozess nicht nur effizient, sondern auch sicher ist. Auch die Umweltaspekte spielen eine immer größere Rolle. Durch die Wiederverwendung des überschüssigen Pulvers wird nicht nur Materialverschwendung vermieden, sondern auch der CO2-Ausstoß reduziert, da weniger neue Pulverlacke produziert werden müssen. Auch die Filtertechnik trägt zur Reduzierung der Umweltbelastung bei, da die Luft sauber aus der Kabine abgeführt wird und keine schädlichen Partikel oder Chemikalien in die Atmosphäre gelangen. Um das Pulver ordnungsgemäß und sicher zu entsorgen, werden in vielen modernen Systemen spezielle Behälter installiert, in denen das gesammelte Pulver aufbewahrt und anschließend umweltfreundlich entsorgt werden kann.
Ein gut gewartetes Absaugsystem hilft, die Luftqualität in der gesamten Werkstatt zu erhalten, was wiederum das Wohlbefinden und die Gesundheit der Mitarbeiter fördert. Letztlich führt die Investition in eine qualitativ hochwertige Pulverkabine mit Absaugung zu einer Vielzahl von Vorteilen, von der erhöhten Produktqualität über verbesserte Arbeitssicherheit bis hin zu einer nachhaltigeren und umweltfreundlicheren Produktion. Sie stellt eine langfristige Investition in die Effizienz und Zukunftsfähigkeit eines Unternehmens dar und ermöglicht es, auch in wettbewerbsintensiven Branchen den hohen Anforderungen an moderne Fertigungstechniken gerecht zu werden. Die Entscheidung für eine Pulverkabine mit Absaugung sollte daher sorgfältig getroffen werden, um die bestmögliche Lösung für die individuellen Anforderungen des Betriebs zu finden.
Kleine Lackierkabine
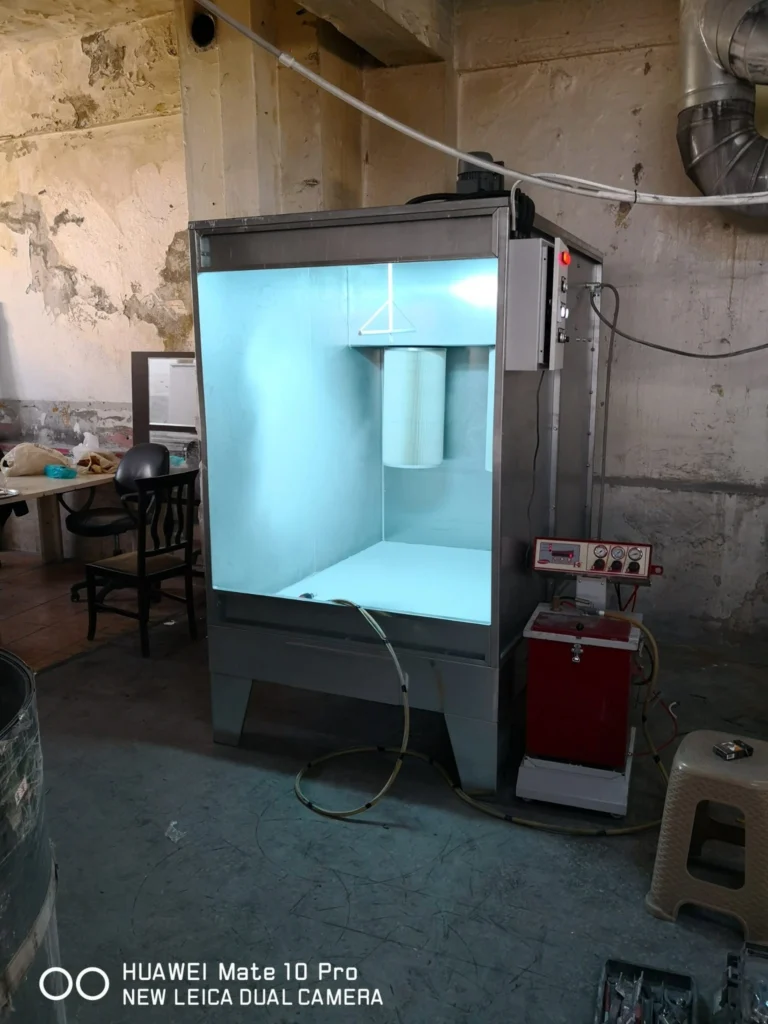
Eine kleine Lackierkabine ist eine kompakte und effiziente Lösung für Betriebe oder Einzelpersonen, die in einer begrenzten Umgebung hochwertige Lackierarbeiten durchführen möchten. Diese Kabinen sind speziell darauf ausgelegt, den Lackierprozess in kleineren Werkstätten, Garagen oder beengten Produktionsräumen zu optimieren, ohne dass dabei die Qualität oder die Sicherheitsstandards beeinträchtigt werden.
Kleine Lackierkabinen bieten eine kontrollierte Umgebung, in der der Lackierprozess unter idealen Bedingungen stattfindet. Sie verhindern, dass Staub, Schmutz oder andere Verunreinigungen die Lackierung beeinträchtigen, und gewährleisten eine gleichmäßige und fehlerfreie Beschichtung. Das Besondere an kleinen Lackierkabinen ist, dass sie trotz ihrer Größe über die wesentlichen Funktionen und Technologien verfügen, die auch größere industrielle Kabinen bieten, jedoch auf einem kleineren Raum.
Ein wichtiger Bestandteil jeder kleinen Lackierkabine ist das Absaugsystem, das dafür sorgt, dass überschüssige Lackdämpfe und Partikel schnell aus der Kabine entfernt werden. Dies schützt nicht nur die Luftqualität und Gesundheit der Arbeiter, sondern trägt auch dazu bei, dass die Lackierung gleichmäßig und ohne Ablagerungen von Staub oder überschüssigem Lack erfolgt. Moderne kleine Lackierkabinen verwenden oft Mehrfachfilter oder HEPA-Filter, die dafür sorgen, dass die Luft in der Kabine so sauber wie möglich bleibt.
Vorteile einer kleinen Lackierkabine
- Platzsparend: Kleine Lackierkabinen sind ideal für Werkstätten mit begrenztem Platzangebot. Sie können problemlos in einem kleinen Raum oder einer Garage installiert werden, ohne viel Platz zu beanspruchen.
- Energieeffizient: Aufgrund ihrer kompakten Größe benötigen kleine Lackierkabinen in der Regel weniger Energie für Belüftung, Heizung und Absaugung, was zu niedrigeren Betriebskosten führt.
- Vielseitigkeit: Kleine Lackierkabinen eignen sich für eine Vielzahl von Anwendungen, von der Automobil- und Möbelindustrie bis hin zu kleinen Handwerksbetrieben. Sie können für die Lackierung von Metallen, Holz, Kunststoffen und anderen Materialien verwendet werden.
- Einfache Handhabung: Viele Modelle von kleinen Lackierkabinen sind so konzipiert, dass sie benutzerfreundlich sind und auch von weniger erfahrenen Anwendern problemlos betrieben werden können.
- Kostenersparnis: Eine kleine Lackierkabine ist kostengünstiger in der Anschaffung und im Betrieb im Vergleich zu größeren industriellen Kabinen. Für kleinere Unternehmen oder Einzelpersonen stellt sie eine erschwingliche Lösung dar, um professionelle Lackierergebnisse zu erzielen.
- Sicherheitsfunktionen: Auch kleinere Kabinen sind oft mit Sicherheitsmerkmalen ausgestattet, wie z. B. automatischen Notabschaltungen, Brandschutzvorrichtungen und speziellen Filtern, um die Risiken beim Lackieren von Materialien, die flüchtige organische Verbindungen (VOCs) oder leicht entzündliche Substanzen enthalten, zu minimieren.
- Wiederverwendbarkeit von Material: Einige kleine Lackierkabinen sind so konzipiert, dass überschüssiger Lack und Staub wieder aufgenommen und recycelt werden können, was zur Reduzierung der Materialkosten beiträgt und eine umweltfreundlichere Lösung darstellt.
Aufbau einer kleinen Lackierkabine
Der Aufbau einer kleinen Lackierkabine besteht in der Regel aus mehreren wesentlichen Komponenten:
- Kabinenstruktur: Eine stabile und oft aus Metall oder robustem Kunststoff gefertigte Struktur, die die Kabine umschließt und eine isolierte Arbeitsumgebung schafft.
- Absaug- und Belüftungssystem: Dies ist eine der wichtigsten Funktionen einer Lackierkabine. Das Absaugsystem sorgt dafür, dass schädliche Dämpfe und überschüssiges Pulver oder Lack schnell aus der Kabine entfernt werden. Dabei wird die Luft über spezielle Kanäle und Filter aus der Kabine abgesogen.
- Lichtquellen: Eine gute Beleuchtung ist entscheidend für die Qualität der Lackierung. Kleine Lackierkabinen sind mit speziellen, flimmerfreien Lichtquellen ausgestattet, die eine gleichmäßige Ausleuchtung der Werkstücke ermöglichen und die Sicht auf die Oberflächen verbessern.
- Filtertechnik: Um die Luft von Schadstoffen zu befreien, sind kleine Lackierkabinen mit verschiedenen Filtertechniken ausgestattet. Dies kann ein Vliesfilter zur Vorfilterung oder ein HEPA-Filter zur Feinfiltration sein, der dazu beiträgt, die Luft so sauber wie möglich zu halten.
- Zugangs- und Sichtfenster: Kleinere Kabinen bieten in der Regel ein großes Sichtfenster oder eine Öffnung, durch die der Bediener das Werkstück während des Lackierens beobachten kann. Dies gewährleistet eine präzise und kontrollierte Anwendung des Lacks.
Einsatzmöglichkeiten einer kleinen Lackierkabine
Kleine Lackierkabinen finden in vielen Bereichen Anwendung. Besonders in Branchen, in denen nur kleine bis mittlere Stückzahlen oder Einzelaufträge bearbeitet werden, bieten sie eine kosteneffiziente und leistungsstarke Lösung. Einige typische Einsatzgebiete sind:
- Automobil- und Motorradindustrie: Für kleinere Werkstätten oder Einzelbetriebe, die Autos oder Motorräder lackieren, bieten kleine Lackierkabinen eine ideale Lösung. Sie sind perfekt für die Lackierung von Autoteilen, Felgen oder auch ganzen Fahrzeugen im Kleinformat geeignet.
- Möbelindustrie: In der Möbelherstellung, vor allem bei der Lackierung von Einzelstücken oder kleinen Serien, finden kleine Lackierkabinen Anwendung. Sie ermöglichen eine präzise und gleichmäßige Lackierung von Holz- oder Metallmöbeln.
- Handwerksbetriebe: Kleine Betriebe, die z. B. Schmuck, Modellbau oder andere Handwerksprodukte herstellen, können von der Flexibilität und Kompaktheit einer kleinen Lackierkabine profitieren.
- Kunst- und Kreativbranche: Künstler und Designer, die auf maßgeschneiderte Lackierungen angewiesen sind, können in einer kleinen Lackierkabine eine sichere und kontrollierte Umgebung für ihre Arbeiten schaffen.
Fazit
Eine kleine Lackierkabine stellt eine wertvolle Investition für kleinere Betriebe oder Einzelpersonen dar, die präzise Lackierarbeiten in einer sicheren, sauberen und kontrollierten Umgebung durchführen möchten. Sie bietet zahlreiche Vorteile, von der Platzersparnis und Kosteneffizienz bis hin zur hohen Qualität der Lackierungen. Mit einer kleinen Lackierkabine können auch bei begrenztem Platzangebot professionelle Ergebnisse erzielt werden, ohne Kompromisse bei der Sicherheit oder der Arbeitsergonomie einzugehen.
Eine kleine Lackierkabine ist nicht nur eine platzsparende und kostengünstige Lösung, sondern auch eine, die hohe Anforderungen an Präzision und Qualität erfüllt. Sie ist besonders in kleinen Handwerksbetrieben oder bei spezialisierten Lackierarbeiten eine ideale Wahl. Durch ihre kompakte Bauweise und die Fähigkeit, auch bei begrenztem Raum ein optimales Lackierergebnis zu erzielen, ist sie eine perfekte Option für Werkstätten, in denen größere Kabinen nicht praktikabel sind. Der Fokus auf effiziente Luftabsaugung und hochwertige Filtertechnologien sorgt dafür, dass keine Verunreinigungen oder Staubpartikel die Lackierung beeinträchtigen, was für eine gleichmäßige und professionelle Oberfläche sorgt. Zudem ermöglicht die geringe Stellfläche den Betrieb auf engem Raum, was für Betriebe mit begrenztem Platzangebot von Vorteil ist.
Die einfache Handhabung und geringe Energieverbrauch der kleineren Modelle machen sie auch für kleinere Unternehmen oder Heimwerker attraktiv, die auf der Suche nach einer leistungsstarken und dennoch praktischen Lösung sind. Sicherheitsaspekte wie Brandschutzmechanismen und Explosionsschutz sind ebenfalls ein integraler Bestandteil vieler kleiner Lackierkabinen und sorgen dafür, dass der Betrieb in einer sicheren Umgebung erfolgen kann. Darüber hinaus bieten diese Kabinen eine hohe Flexibilität bei der Wahl der Lackiermaterialien, da sie sowohl für Flüssiglacke als auch für Pulverlacke verwendet werden können, was ihre Einsatzmöglichkeiten deutlich erweitert. Die Möglichkeit, überschüssiges Pulver zu filtern und wiederzuverwenden, trägt zusätzlich zur Reduzierung der Betriebskosten bei und macht die Kabinen zu einer umweltfreundlicheren Option, da weniger Material verschwendet wird. Kleine Lackierkabinen sind somit eine ideale Wahl für Unternehmen, die auf Qualität, Sicherheit und Effizienz achten und dennoch in einem kompakten Raum arbeiten möchten. Sie bieten eine schnelle und einfache Möglichkeit, auch bei begrenztem Budget und Raum hochwertige Lackierergebnisse zu erzielen.
Darüber hinaus bieten kleine Lackierkabinen auch den Vorteil, dass sie relativ einfach zu installieren und zu betreiben sind, was sie besonders für kleinere Unternehmen und Einzelpersonen, die in der Lackierbranche tätig sind, attraktiv macht. Die meisten Modelle erfordern nur eine einfache Stromversorgung und eine Belüftung, wodurch die Installationskosten und der Aufwand minimal sind. Diese Benutzerfreundlichkeit sorgt dafür, dass selbst weniger erfahrene Anwender ohne großen Aufwand in der Lage sind, qualitativ hochwertige Lackierungen zu erzielen. Ein weiterer Vorteil einer kleinen Lackierkabine ist die Möglichkeit, verschiedene Materialien und Produkte in kurzer Zeit zu lackieren, was den Produktionsdurchsatz erhöht. Mit der richtigen Auswahl an Filtern und Belüftungssystemen kann die Kabine an die speziellen Bedürfnisse der Lackierung angepasst werden, sei es für kleinere Gegenstände wie Modellbauteile oder größere Werkstücke wie Autoteile.
Durch die gezielte Absaugung von Dämpfen und Staubpartikeln wird nicht nur die Luftqualität verbessert, sondern auch die Gefahr von Verunreinigungen und Oberflächenfehlern minimiert, was zu einer gleichmäßigen und fehlerfreien Lackierung führt. Viele moderne kleine Lackierkabinen sind zudem mit fortschrittlichen Steuerungssystemen ausgestattet, die eine präzise Anpassung der Belüftung, Luftzirkulation und Filterleistung ermöglichen, sodass die Kabine auf die spezifischen Anforderungen der Lackierung abgestimmt werden kann. Das steigert die Effizienz und sorgt für eine konstant hohe Qualität der Lackierarbeiten. Mit der richtigen Wartung, einschließlich regelmäßiger Reinigung der Filter und Kontrolle des Absaugsystems, können diese Kabinen jahrelang zuverlässige Leistung bieten, was sie zu einer langfristig kostengünstigen Lösung für die Lackierung macht. Abschließend lässt sich sagen, dass kleine Lackierkabinen durch ihre Vielseitigkeit, Effizienz und Benutzerfreundlichkeit eine hervorragende Wahl für eine Vielzahl von Lackieranwendungen darstellen, insbesondere für Unternehmen oder Einzelpersonen, die Wert auf präzise Ergebnisse, niedrige Betriebskosten und eine saubere Arbeitsumgebung legen.
Automatische Lackieranlage

Eine automatische Lackieranlage ist eine spezialisierte industrielle Einrichtung, die den Lackierprozess automatisiert, um eine hohe Effizienz, gleichmäßige Lackierung und reduzierte Arbeitskosten zu gewährleisten. Sie wird in verschiedenen Branchen eingesetzt, von der Automobilindustrie über die Möbelherstellung bis hin zur Elektronikfertigung. Automatische Lackieranlagen übernehmen viele der Arbeitsschritte, die bei manuellen Lackieranwendungen erforderlich sind, und bieten eine konstante Qualität und Geschwindigkeit, die mit manuellem Lackieren oft nicht erreicht werden können.
Die Funktionsweise einer automatischen Lackieranlage basiert auf der Verwendung von Robotern, Förderbändern und präzisen Sprühsystemen, die zusammenarbeiten, um die Lackierung eines Werkstücks durchzuführen. Ein typisches System umfasst mehrere Hauptkomponenten, die miteinander verbunden sind, um einen kontinuierlichen Produktionsfluss zu gewährleisten. In vielen Fällen erfolgt die Steuerung der gesamten Anlage über ein zentrales Computersystem, das den Lackierprozess überwacht und automatisch anpasst, um eine konsistente Lackierung und maximale Effizienz zu erreichen.
Ein zentraler Bestandteil der automatischen Lackieranlage ist der Industrieroboter, der für das präzise Auftragen des Lacks auf die Werkstücke verantwortlich ist. Diese Roboter können sowohl stationär als auch in Bewegung eingesetzt werden, um verschiedene Teile aus unterschiedlichen Winkeln zu lackieren. Roboterarmen sind mit Sprühpistolen ausgestattet, die den Lack auf die Oberfläche sprühen. Die Sprühtechnik kann je nach Bedarf unterschiedlich eingestellt werden, um eine feine, gleichmäßige Lackschicht zu erzeugen, die die gewünschten Qualitätsstandards erfüllt.
Ein weiteres wichtiges Element in einer automatischen Lackieranlage ist das Fördersystem. Dieses sorgt dafür, dass die Werkstücke kontinuierlich durch die Lackieranlage transportiert werden. Fördersysteme sind oft in Form von Förderbändern oder Hängeförderern konzipiert, die die Werkstücke vom Startpunkt bis zum Endpunkt der Anlage transportieren, wobei jeder Arbeitsschritt der Lackierung automatisch ausgeführt wird, ohne dass eine manuelle Intervention erforderlich ist.
Vorteile einer automatischen Lackieranlage
- Hohe Präzision und Konsistenz: Die Automatisierung ermöglicht eine gleichbleibend hohe Qualität und Präzision bei der Lackierung. Da Roboter und Maschinen genau nach programmierten Vorgaben arbeiten, sind Fehler durch menschliche Unachtsamkeit nahezu ausgeschlossen. Jede Lackschicht wird gleichmäßig und ohne Überspray aufgetragen, was zu einer hohen Endqualität des Produkts führt.
- Erhöhte Effizienz und Geschwindigkeit: Automatische Lackieranlagen können Werkstücke deutlich schneller und effizienter bearbeiten als manuelle Prozesse. Der kontinuierliche Betrieb durch Förderbänder und die schnelle, gleichmäßige Lackierung durch Roboter sorgen für eine hohe Produktivität, was insbesondere in der Massenproduktion von Vorteil ist.
- Reduzierte Arbeitskosten: Da viele Prozesse automatisiert sind, wird der Bedarf an manueller Arbeit erheblich reduziert. Dies senkt nicht nur die Arbeitskosten, sondern verringert auch die Fehlerquote und steigert gleichzeitig die Produktionseffizienz.
- Kosteneffizienz bei großen Stückzahlen: Insbesondere bei der Fertigung großer Stückzahlen ist die automatische Lackieranlage äußerst kosteneffizient. Sie sorgt dafür, dass jeder einzelne Produktionsschritt gleichmäßig und schnell durchgeführt wird, wodurch die Produktionskosten pro Werkstück gesenkt werden.
- Geringerer Materialverbrauch: Moderne Lackieranlagen sind mit hochpräzisen Sprühtechniken ausgestattet, die den Materialverbrauch minimieren. Sie reduzieren das Auftreten von Overspray und stellen sicher, dass nur die benötigte Menge Lack aufgetragen wird, was auch die Materialkosten senkt und umweltfreundlicher ist.
- Sicherheitsvorteile: Automatische Lackieranlagen tragen auch zur Sicherheit am Arbeitsplatz bei. Durch die Automatisierung der gefährlichen und potenziell gesundheitsschädlichen Aufgaben des Lackierens wird der direkte Kontakt der Mitarbeiter mit giftigen Dämpfen und Chemikalien reduziert. Einige Anlagen sind zudem mit modernen Belüftungssystemen und Sicherheitsmechanismen ausgestattet, um das Risiko von Explosionen oder Bränden zu minimieren.
- Verbesserte Arbeitsbedingungen: Da die manuelle Arbeit weitgehend entfällt, werden auch die Arbeitsbedingungen für die Mitarbeiter verbessert. Sie müssen nicht mehr in einem potenziell schädlichen Umfeld arbeiten, und die körperliche Belastung wird deutlich reduziert. Dies führt zu einer höheren Mitarbeiterzufriedenheit und einer geringeren Krankheitsrate.
Komplexe Steuerung und Anpassungsfähigkeit
Automatische Lackieranlagen bieten nicht nur Effizienz, sondern auch Flexibilität. Viele dieser Systeme können für unterschiedliche Werkstücke und Lacktypen angepasst werden. Die Steuerungseinheit einer solchen Anlage ermöglicht es, Parameter wie Lackmenge, Sprühgeschwindigkeit, Temperatur und Trocknungszeit je nach Art des Materials und den spezifischen Anforderungen des Produkts anzupassen. Das macht die automatische Lackieranlage besonders geeignet für Unternehmen, die eine breite Produktpalette mit unterschiedlichen Lackieranforderungen herstellen.
Die Anpassung der Sprühtechnik ist besonders wichtig, um verschiedene Materialien wie Metall, Kunststoff oder Holz effektiv zu lackieren. Einige Anlagen verfügen sogar über eine Farbwechseltechnik, die es ermöglicht, den Farbton oder Lacktyp schnell und ohne viel Aufwand zu wechseln. Dies ist besonders vorteilhaft in der Automobilindustrie, wo oft mehrere Farben für verschiedene Modellvarianten benötigt werden.
Integration von Trocknungs- und Härtesystemen
Neben der Lackierung beinhalten viele automatische Lackieranlagen auch integrierte Trocknungssysteme, die den Lack sofort nach dem Auftragen aushärten. Diese Systeme können durch UV-Licht, Infrarotstrahlung oder heißes Luftgebläse arbeiten, je nach Art des verwendeten Lacks und der Produktionsgeschwindigkeit. Trocknung und Aushärtung können in einer einzigen Phase des Prozesses erfolgen, was den gesamten Lackierzyklus verkürzt und die Effizienz weiter steigert.
Wartung und Langfristige Vorteile
Obwohl automatische Lackieranlagen initial hohe Investitionskosten mit sich bringen, bieten sie langfristig viele Vorteile, wie z. B. eine höhere Produktivität und reduzierte Betriebskosten. Die Wartung solcher Anlagen ist entscheidend, um eine konstant hohe Leistung sicherzustellen. Regelmäßige Inspektionen der mechanischen und elektronischen Komponenten, der Sprühköpfe und der Fördersysteme sind notwendig, um Ausfallzeiten zu minimieren und die Lebensdauer der Anlage zu verlängern. Zudem müssen die Lackieranlagen regelmäßig gereinigt und die Filter gewechselt werden, um eine hohe Qualität der Lackierung zu gewährleisten und das Risiko von Verunreinigungen zu vermeiden.
Fazit
Automatische Lackieranlagen sind ein unschätzbares Werkzeug für die moderne Fertigung, das es Unternehmen ermöglicht, qualitativ hochwertige Produkte in kürzerer Zeit zu produzieren. Sie bieten zahlreiche Vorteile, darunter hohe Präzision, Effizienz, geringeren Materialverbrauch und verbesserte Arbeitsbedingungen. Obwohl die Anfangsinvestition hoch sein kann, rechtfertigt die langfristige Reduktion der Produktionskosten und die Verbesserung der Produktionskapazität die Entscheidung, in eine automatische Lackieranlage zu investieren. Diese Anlagen sind besonders vorteilhaft für Unternehmen, die große Stückzahlen herstellen oder eine gleichbleibende, hohe Qualität in der Lackierung benötigen.
Automatische Lackieranlagen bieten auch einen erheblichen Vorteil, wenn es um die Anpassung an verschiedene Produktionsanforderungen geht. Sie können problemlos für unterschiedliche Werkstückgrößen und -formen angepasst werden, was sie vielseitig in der Anwendung macht. In der Automobilindustrie, zum Beispiel, können diese Anlagen mehrere Autoteile in einem kontinuierlichen Prozess lackieren, wodurch die Effizienz und Geschwindigkeit der Produktion erhöht wird. Ebenso können sie für kleinere Unternehmen oder spezialisierte Fertigungen, die individuellere Stückzahlen produzieren, genutzt werden, was sie zu einer flexiblen Lösung für unterschiedlichste Produktionsanforderungen macht. Ein weiterer Vorteil dieser Anlagen ist die Möglichkeit, den Lackierprozess zu überwachen und zu steuern, was eine sofortige Reaktion auf Abweichungen von den Qualitätsstandards ermöglicht.
Moderne Systeme bieten detaillierte Rückmeldungen über den Lackauftrag, wie etwa die Dicke der Lackschicht, die Verteilung des Lacks und die Trocknungszeit, sodass die Qualität jederzeit sichergestellt werden kann. Diese detaillierten Daten sind auch für die Qualitätssicherung und Nachverfolgbarkeit von Bedeutung, da sie eine genaue Dokumentation des Lackierprozesses ermöglichen. Viele automatisierte Lackieranlagen sind zudem mit Fehlererkennungs- und Diagnosesystemen ausgestattet, die Probleme frühzeitig erkennen und die Produktionslinie entsprechend anpassen können. Dies trägt zur Reduzierung von Produktionsfehlern bei und verhindert, dass fehlerhafte Produkte weiter bearbeitet oder versendet werden.
Diese hohe Präzision und Fehlervermeidung reduziert die Ausschussquote und trägt zur Kostensenkung bei, da weniger Material verschwendet wird und weniger Nacharbeit erforderlich ist. Neben der Verbesserung der Qualität und Effizienz bietet die automatisierte Lackieranlage auch ökologische Vorteile, indem sie den Materialverbrauch optimiert und den Einsatz von Lösungsmitteln und Chemikalien reduziert. Dies führt zu einer geringeren Umweltbelastung und ermöglicht es Unternehmen, umweltfreundlichere Produktionsmethoden umzusetzen, die nicht nur die Nachhaltigkeit fördern, sondern auch den gesetzlichen Vorschriften zur Reduzierung von Emissionen und Abfallentsorgung gerecht werden. Die Anpassungsfähigkeit und Präzision, die diese Anlagen bieten, ermöglichen es Unternehmen, wettbewerbsfähig zu bleiben und gleichzeitig die Betriebskosten zu optimieren, was sie zu einer lohnenswerten Investition für viele Industrien macht, die auf Lackierung angewiesen sind.
Ein weiterer wichtiger Vorteil automatischer Lackieranlagen ist ihre Fähigkeit, eine hohe Wiederholgenauigkeit zu gewährleisten. Dies ist besonders wichtig in der Massenproduktion, in der es erforderlich ist, dass jedes Produkt dieselbe Qualität und Oberflächenbeschaffenheit aufweist. Mit den präzisen Steuerungssystemen können diese Anlagen dafür sorgen, dass jede Schicht gleichmäßig aufgetragen wird und keine ungewollten Unterschiede in der Lackierung auftreten. Dies führt zu einer erheblichen Reduktion von Nacharbeit und Reklamationen, was wiederum die Gesamtbetriebskosten senkt und den Produktionsfluss stabilisiert. Für Unternehmen, die in einer Branche tätig sind, in der Oberflächenqualität und Ästhetik von größter Bedeutung sind, wie zum Beispiel in der Automobil- oder Möbelindustrie, stellt eine automatische Lackieranlage eine unverzichtbare Investition dar.
In Kombination mit automatisierten Trocknungssystemen, die dafür sorgen, dass die Lackschichten schnell und effizient aushärten, können diese Anlagen den gesamten Lackierzyklus erheblich verkürzen und so die Produktionsgeschwindigkeit steigern. Eine schnellere Trocknung ermöglicht es, den Produktionsprozess zu optimieren und die Zeit zwischen den einzelnen Arbeitsschritten zu minimieren, was wiederum den Durchsatz erhöht. Gleichzeitig sorgt die präzise Steuerung der Trocknungsbedingungen dafür, dass die Lackoberfläche perfekt verarbeitet wird und keine Trocknungsfehler auftreten, die die Qualität beeinträchtigen könnten. Ein zusätzlicher Vorteil der automatisierten Systeme ist ihre Skalierbarkeit. Unternehmen, die zunächst kleinere Produktionsmengen benötigen, können mit einer weniger komplexen Anlage beginnen und diese im Laufe der Zeit an ihre wachsenden Anforderungen anpassen.
Die Fähigkeit, die Anlage entsprechend der Produktionsanforderungen zu erweitern oder anzupassen, ermöglicht es Unternehmen, flexibel auf Marktveränderungen oder Produktionsspitzen zu reagieren, ohne gleich in ein komplett neues System investieren zu müssen. Diese Flexibilität ist besonders vorteilhaft in der heutigen dynamischen Wirtschaft, in der Unternehmen schnell auf Veränderungen in der Nachfrage reagieren müssen. Darüber hinaus ermöglichen moderne, automatisierte Lackieranlagen die Integration mit anderen Fertigungsprozessen. Dies bedeutet, dass sie in komplexe Produktionslinien eingebunden werden können, in denen mehrere Fertigungsschritte wie Montage, Reinigung, Polieren und Endkontrolle miteinander verknüpft sind. Die Automatisierung des gesamten Prozesses sorgt nicht nur für eine höhere Effizienz, sondern auch für eine nahtlose Zusammenarbeit zwischen den verschiedenen Produktionsstationen.
Diese Integration kann den gesamten Fertigungsprozess optimieren, Redundanzen reduzieren und den Materialfluss maximieren. In Zukunft wird die kontinuierliche Weiterentwicklung in der Automatisierungstechnik, wie etwa die Nutzung von künstlicher Intelligenz (KI) und Internet of Things (IoT), eine noch präzisere Steuerung und Anpassung der Lackieranlagen ermöglichen. KI-gestützte Systeme können dazu beitragen, den Lackierprozess noch weiter zu optimieren, indem sie in Echtzeit auf Veränderungen reagieren und Anpassungen vornehmen, um die beste Qualität zu gewährleisten.
Die Verwendung von IoT ermöglicht es, Daten aus der gesamten Produktionslinie zu sammeln und zu analysieren, um potenzielle Probleme frühzeitig zu erkennen und proaktive Wartungsmaßnahmen zu ergreifen, bevor ein Ausfall der Anlage erfolgt. Insgesamt bieten automatische Lackieranlagen eine Zukunftssicherheit, die es Unternehmen ermöglicht, mit den neuesten Entwicklungen in der Fertigungstechnik Schritt zu halten, und sie tragen dazu bei, die Effizienz, Nachhaltigkeit und Wettbewerbsfähigkeit auf dem Markt zu steigern.
Pulverkabine mit Zyklon
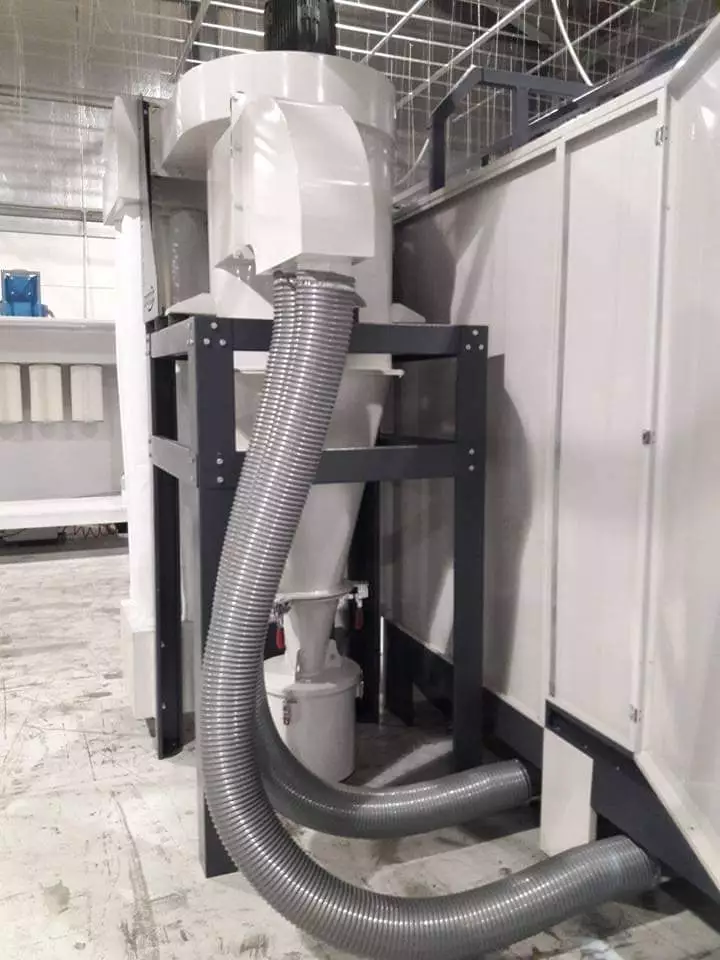
Eine Pulverkabine mit Zyklon ist eine spezialisierte Lackierkabine, die für das Auftragen von Pulverlacken auf verschiedene Oberflächen verwendet wird. Diese Art von Kabine kommt in der industriellen Fertigung zum Einsatz, insbesondere bei der Pulverbeschichtung von Metallteilen, Möbeln, Automobilteilen und anderen Produkten. Der Zyklon ist ein entscheidendes Element, das in dieser Kabine für eine effiziente Lackrückgewinnung und eine saubere Arbeitsumgebung sorgt.
Die Pulverkabine arbeitet durch elektrostatisches Aufladen von Pulverlacken, die anschließend auf die Oberfläche des Werkstücks gesprüht werden. Das Pulver haftet aufgrund der elektrostatischen Aufladung an der Oberfläche, was zu einer gleichmäßigen Beschichtung führt. Ein Zyklonfilter wird verwendet, um überschüssiges Pulver, das nicht auf die Werkstücke aufgetragen wird, abzusaugen und zurückzuwalzen, um es für eine erneute Verwendung in der Lackierung zu recyceln. Dies spart nicht nur Material, sondern verringert auch die Menge an Abfall und unterstützt umweltfreundlichere Fertigungsprozesse.
Die Zyklonabsaugung in der Pulverkabine funktioniert, indem sie die Luft und das überschüssige Pulver in einem Spiralstrom zirkulieren lässt. Durch die Zentrifugalkraft werden die Pulverpartikel von der Luft getrennt und am Boden des Zyklons gesammelt. Die saubere Luft wird durch einen Filter abgeführt, während das zurückgehaltene Pulver entweder für den erneuten Einsatz wiederverwendet oder für die Entsorgung vorbereitet wird. Diese Technologie sorgt für eine hohe Lackrückgewinnungsrate und minimiert den Materialverlust, wodurch die Betriebskosten reduziert werden.
Ein zusätzlicher Vorteil der Pulverkabine mit Zyklon ist die Verbesserung der Luftqualität in der Arbeitsumgebung. Da überschüssiges Pulver effizient entfernt und zurückgewonnen wird, wird die Staubbelastung in der Kabine verringert, was für die Gesundheit der Arbeiter und die Einhaltung von Umweltvorschriften von entscheidender Bedeutung ist. Es wird auch sichergestellt, dass das Pulver nicht in den Arbeitsbereich gelangt und keine Verunreinigungen auf den Werkstücken auftreten, was zu einer konstant hohen Qualität der Beschichtung beiträgt.
Die Zyklonabsaugung ist besonders vorteilhaft, wenn es um die Verarbeitung von größeren Produktionsmengen geht, da sie eine kontinuierliche und effektive Rückgewinnung des Pulvers ermöglicht. Dadurch kann der Lackierprozess effizienter und wirtschaftlicher gestaltet werden, da weniger Pulver verschwendet wird und gleichzeitig die Qualität der Lackierung konstant bleibt. Darüber hinaus bieten diese Kabinen eine gute Filterleistung, die dazu beiträgt, die Luft von anderen schädlichen Partikeln zu befreien und die Arbeitsumgebung sicherer zu machen.
Die Technologie der Zyklonabsaugung ist in vielen modernen Pulverkabinen integriert, die mit verschiedenen automatischen und manuellen Steuerungen ausgestattet sind, um den Lackierprozess zu optimieren. Dies ermöglicht es dem Bediener, die Pulverdichte, den Luftstrom und die Absaugkapazität je nach Art des zu lackierenden Werkstücks anzupassen, was zu einer noch besseren Oberflächenbeschaffenheit und Effizienz führt.
Zusammenfassend lässt sich sagen, dass eine Pulverkabine mit Zyklon eine hochentwickelte Lösung für die Pulverbeschichtung ist, die zahlreiche Vorteile wie Materialrückgewinnung, geringeren Abfall, verbesserte Luftqualität und höhere Effizienz bietet. Sie ist besonders in der Fertigung von Vorteil, wo hohe Produktionszahlen und eine konstante Beschichtungsqualität erforderlich sind.
Eine Pulverkabine mit Zyklon bietet auch eine bedeutende Kostenersparnis für Unternehmen, die Pulverbeschichtungen in großem Maßstab durchführen. Da überschüssiges Pulver effektiv zurückgewonnen und erneut verwendet werden kann, sinken die Materialkosten erheblich, da weniger Pulver benötigt wird, um dieselbe Menge an Werkstücken zu beschichten. Diese Rückgewinnung ist besonders vorteilhaft bei teureren Pulvern oder solchen, die speziell für bestimmte Anwendungen oder Oberflächenbehandlungen entwickelt wurden. Gleichzeitig hilft die Zyklonabsaugung, die Lagerkapazitäten für Pulverbeschichtungsmaterialien zu optimieren, da weniger überschüssiges Pulver gelagert und entsorgt werden muss.
Neben der Kostenersparnis trägt die Pulverkabine mit Zyklon auch zur Nachhaltigkeit des Produktionsprozesses bei. Da weniger Pulver verschwendet wird und die Rückgewinnungsrate hoch ist, reduziert sich der ökologische Fußabdruck der Lackierung. Dies ist besonders relevant in einem zunehmend umweltbewussten Markt, in dem Unternehmen unter Druck stehen, ihre Produktionsprozesse umweltfreundlicher zu gestalten. Die Reduzierung von Abfall und der Einsatz von Recyclingtechniken innerhalb der Pulverbeschichtungsanlage ermöglichen es Unternehmen, sowohl ökologischen als auch finanziellen Anforderungen gerecht zu werden.
Ein weiteres Plus der Zyklonabsaugung ist ihre wartungsfreundliche Natur. Zyklonsysteme erfordern im Allgemeinen weniger Wartung im Vergleich zu herkömmlichen Filtrationssystemen, da sie keine Filterelemente haben, die regelmäßig ausgetauscht werden müssen. Stattdessen wird das Pulver durch die Zentrifugalkraft des Zyklons effizient getrennt, und nur der Luftstrom muss durch einen Filter geführt werden, der seltener gewartet werden muss. Diese reduzierte Wartungsanforderung trägt zur Minimierung der Betriebs- und Instandhaltungskosten bei und gewährleistet eine höhere Betriebszeit der Pulverkabine.
Zudem kann die Anpassungsfähigkeit der Pulverkabine mit Zyklon zu unterschiedlichen Pulvertönen und -arten als großer Vorteil angesehen werden. Da die Kabinen so konstruiert sind, dass sie verschiedene Pulversorten und -farben handhaben können, bieten sie Flexibilität für die Herstellung einer Vielzahl von Produkten, ohne dass umfangreiche Umbauten oder Anpassungen notwendig sind. Dies ist besonders vorteilhaft für Unternehmen, die in der Kundenspezifikationen oder kleinen Serienfertigung tätig sind, bei denen häufige Farb- oder Materialwechsel erforderlich sind.
Die Lackiergeschwindigkeit wird durch die Kombination der Zyklonabsaugung und einer effizienten Pulverapplikation erheblich verbessert. Der kontinuierliche Fluss von Material und die effektive Entfernung von überschüssigem Pulver sorgen dafür, dass der Lackierprozess nicht durch unnötige Verzögerungen oder Unterbrechungen beeinträchtigt wird. Dies führt zu einer höheren Produktivität und einer besseren Auslastung der Anlage, was in vielen Industrien entscheidend ist, um den Wettbewerbsdruck zu überstehen.
Zusätzlich bietet die Technologie der Zyklonabsaugung auch die Möglichkeit, die Luftströme und die Effizienz der Absaugung fein abzustimmen, sodass die Kabine optimal für unterschiedliche Produktionsanforderungen und Werkstückgrößen konzipiert werden kann. Die genaue Kontrolle über den Luftstrom und die Absaugkapazität ermöglicht es, die Kabine je nach Werkstücktyp und Pulvertargetanz zu konfigurieren. Dies trägt nicht nur zur Reduzierung des Pulvers, sondern auch zur Vermeidung von Staubablagerungen auf Werkstücken bei, was zu einer noch besseren Oberflächenqualität führt.
Insgesamt ist eine Pulverkabine mit Zyklon eine hocheffiziente, umweltfreundliche und wirtschaftliche Lösung für die Pulverbeschichtung in der industriellen Fertigung. Sie verbessert nicht nur die Qualität und Konsistenz der Beschichtungen, sondern steigert auch die Produktionseffizienz und reduziert Betriebskosten, während sie gleichzeitig zur Nachhaltigkeit und den Umweltstandards beiträgt. Unternehmen, die auf der Suche nach einer zuverlässigen und flexiblen Lackierlösung sind, finden in dieser Technologie eine wertvolle Investition, die sowohl kurzfristige als auch langfristige Vorteile bietet.
Pulverkabinen für Hand- und Automatikbeschichtung
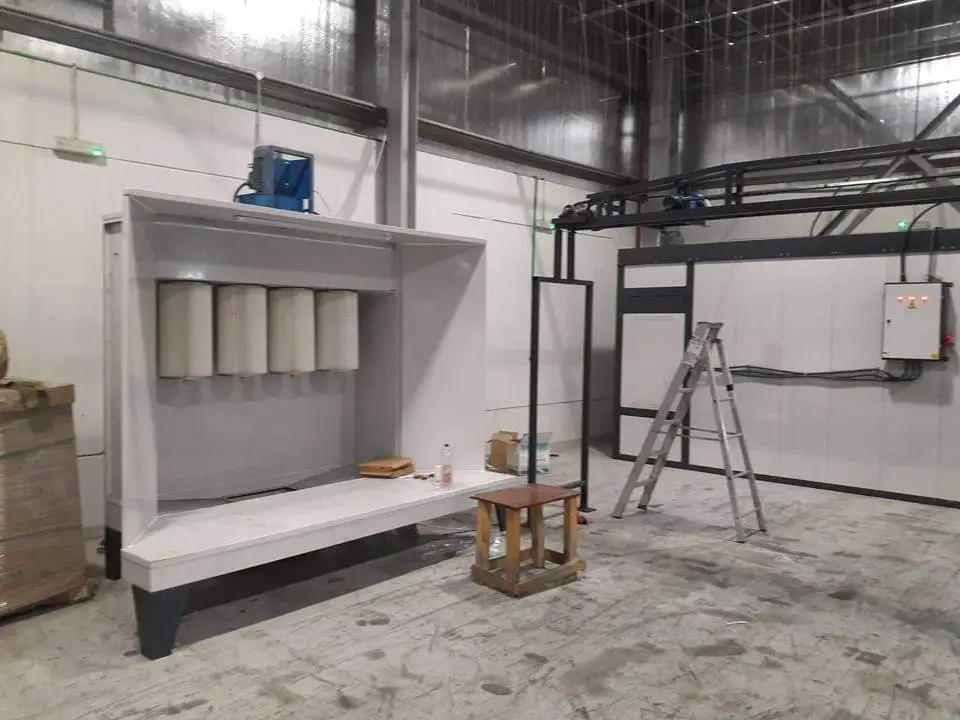
Pulverkabinen für Hand- und Automatikbeschichtung sind spezialisierte Systeme, die eine effiziente, saubere und präzise Anwendung von Pulverlacken auf verschiedenste Werkstücke ermöglichen. Sie bieten eine Lösung für Unternehmen, die sowohl manuelle als auch automatisierte Pulverbeschichtungsprozesse durchführen möchten. Diese Kabinen werden in einer Vielzahl von Industrien eingesetzt, einschließlich der Automobilindustrie, Möbelherstellung, Metallverarbeitung und viele mehr, um eine gleichmäßige, langlebige und hochwertige Lackierung zu gewährleisten.
Pulverkabinen für Handbeschichtung
Handbeschichtung ist die manuelle Methode, bei der der Bediener eine Pulversprühpistole verwendet, um Pulverlack auf die Oberfläche des Werkstücks aufzutragen. Diese Art von Kabine wird häufig für kleinere Produktionsmengen oder bei kundenspezifischen Arbeiten eingesetzt, bei denen eine präzise Handhabung und individuelle Lackierung erforderlich sind.
In einer Hand-Pulverkabine ist der Arbeitsbereich speziell auf die Bedürfnisse des Bedieners ausgelegt. Die Kabine ist in der Regel mit einer hochwertigen Absaugung ausgestattet, um die durch den Lackierprozess entstehenden Dämpfe und Staubpartikel effektiv zu entfernen. Zudem sorgt die Zyklonabsaugung in vielen modernen Handkabinen dafür, dass überschüssiges Pulver effizient gesammelt und zurückgeführt wird, was zu einer besseren Materialnutzung und geringeren Abfallmengen führt.
Ein weiterer Vorteil von Hand-Pulverkabinen ist die Flexibilität: Der Bediener kann das Werkstück in verschiedenen Winkeln und aus verschiedenen Richtungen sprühen, was eine gleichmäßige Lackierung von komplexen oder unregelmäßigen Oberflächen ermöglicht. Sie sind einfach zu bedienen, benötigen jedoch eine gewisse Erfahrung und Übung, um eine gleichmäßige und qualitativ hochwertige Beschichtung zu erzielen. Diese Kabinen sind ideal für kleinere Betriebe oder Werkstätten, in denen individuelle Anpassungen und kleinere Produktionsserien gefragt sind.
Pulverkabinen für Automatikbeschichtung
Automatische Pulverkabinen hingegen sind für den Einsatz in der Serienproduktion konzipiert, bei denen große Stückzahlen effizient und mit gleichbleibend hoher Qualität beschichtet werden müssen. In einer automatisierten Pulverkabine übernimmt eine industrielle Roboterarmtechnik oder eine andere Form der Automatisierung den Lackierprozess. Der Vorteil dieser Kabinen ist die hohe Wiederholgenauigkeit und Effizienz, die sie bieten. Diese Systeme sind so programmiert, dass sie den Pulverlack gleichmäßig auf Werkstücke auftragen, unabhängig von ihrer Größe oder Form.
Automatische Pulverkabinen sind mit fortschrittlichen Sprühtechnologien ausgestattet, die eine gleichmäßige Verteilung des Pulvers auf der Oberfläche des Werkstücks gewährleisten. In der Regel wird der Lack elektrostatisch aufgeladen, wodurch er aufgrund der elektrostatischen Anziehungskraft perfekt haftet und eine hohe Beschichtungsdichte erreicht wird. Diese Kabinen sind außerdem mit fortschrittlichen Absaug- und Filtersystemen ausgestattet, die den überschüssigen Lack absaugen und wiederverwenden, was zu einer deutlich besseren Materialausnutzung führt.
Ein weiterer Vorteil von automatischen Pulverkabinen ist ihre Fähigkeit, den Lackierprozess zu überwachen und zu steuern. Diese Kabinen verfügen oft über Sensoren und Steuersysteme, die sicherstellen, dass jede Lackierung gleichmäßig und mit der richtigen Pulverdichte durchgeführt wird. Sie bieten eine hohe Produktionsgeschwindigkeit, wodurch Unternehmen in der Lage sind, große Produktionsmengen schnell und ohne Qualitätsverlust zu beschichten.
Automatische Systeme bieten auch eine erhebliche Kostensenkung bei der Massenproduktion, da der Materialverbrauch optimiert wird und der Arbeitsaufwand erheblich reduziert wird. Da die Bedienung weitgehend automatisiert ist, wird die Fehlerquote verringert, und die Qualität der Lackierung bleibt konstant hoch. Diese Kabinen sind in der Regel modular aufgebaut und können an die spezifischen Anforderungen der Produktionslinie angepasst werden, was sie zu einer äußerst flexiblen Lösung für Unternehmen macht, die in großen Stückzahlen produzieren.
Unterschiede zwischen Hand- und Automatik-Pulverkabinen
- Flexibilität vs. Effizienz: Handkabinen bieten eine hohe Flexibilität, besonders wenn es um die Lackierung von unterschiedlich großen oder komplexen Werkstücken geht. Sie sind ideal für kleine bis mittlere Produktionsmengen oder individuelle Projekte. Automatische Kabinen hingegen sind auf Effizienz und hohe Produktionsgeschwindigkeit ausgelegt und eignen sich besonders für die Serienproduktion, bei der eine hohe Wiederholgenauigkeit und schnelle Taktzeiten erforderlich sind.
- Benutzersteuerung vs. Automatisierung: In Hand-Pulverkabinen hat der Bediener die vollständige Kontrolle über den Lackierprozess, was für die Fertigung von Einzelstücken oder Prototypen von Vorteil ist. Bei der Automatikbeschichtung übernimmt die Maschine den gesamten Prozess, was eine konstante Qualität bei hohen Produktionsraten gewährleistet, aber weniger Anpassungsfähigkeit bei individuellen Anforderungen bietet.
- Kosten und Wartung: Hand-Pulverkabinen sind in der Regel kostengünstiger in der Anschaffung und erfordern weniger Wartung, da sie einfacher aufgebaut sind. Automatische Pulverkabinen sind aufgrund ihrer Technologie und Komplexität teurer in der Anschaffung und Wartung, bieten jedoch langfristig eine hohe Rentabilität in der Massenproduktion durch geringeren Arbeitsaufwand und optimierten Materialverbrauch.
- Platzbedarf: Hand-Pulverkabinen benötigen in der Regel weniger Platz als automatisierte Systeme. Automatische Kabinen sind häufig größer und benötigen mehr Platz, da sie komplexere Systeme zur Pulverapplikation und -rückgewinnung beinhalten.
Fazit
Pulverkabinen für Hand- und Automatikbeschichtung sind zwei grundlegend unterschiedliche Lösungen, die jedoch jeweils ihre spezifischen Vorteile haben, abhängig von den Produktionsanforderungen. Handkabinen bieten Flexibilität, Benutzerkontrolle und sind ideal für kleinere Produktionsserien oder spezialisierte Anwendungen. Automatische Pulverkabinen hingegen bieten eine effiziente, hochproduktive Lösung für die Serienfertigung, bei der Geschwindigkeit, Präzision und Materialrückgewinnung von größter Bedeutung sind. Unternehmen, die sowohl flexible als auch effiziente Beschichtungsprozesse benötigen, können durch den Einsatz beider Systeme in verschiedenen Phasen ihrer Produktion von den jeweiligen Vorteilen profitieren.
Pulverkabinen für Hand- und Automatikbeschichtung sind flexibel und leistungsstark in der Herstellung von Pulverbeschichtungen, die eine hohe Qualität und Langlebigkeit bieten. Hand-Pulverkabinen sind besonders für kleinere Betriebe oder Einzelprojekte geeignet, bei denen manuelle Kontrolle über den Lackierprozess erforderlich ist. Der Bediener hat die Freiheit, die Pulversprühpistole je nach Werkstückform und -größe zu steuern, was eine individuelle Anpassung und eine hohe Präzision ermöglicht. In solchen Kabinen ist die Luftabsaugung meist mit Zyklonsystemen ausgestattet, die überschüssiges Pulver absaugen und zurückgewinnen, wodurch Materialverluste minimiert und Kosten gesenkt werden.
Diese Flexibilität ermöglicht es, auch komplizierte oder unregelmäßig geformte Teile effizient zu beschichten, wobei der Bediener jederzeit die Arbeitsrichtung und die Pulvermengen anpassen kann. Automatische Pulverkabinen hingegen bieten die Möglichkeit, den gesamten Lackierprozess zu automatisieren und dadurch eine konstante Qualität und schnelle Verarbeitung zu gewährleisten. Sie sind besonders für Unternehmen geeignet, die in großen Stückzahlen produzieren und eine hohe Wiederholgenauigkeit benötigen. In solchen Kabinen wird der Lack automatisch gleichmäßig auf die Werkstücke aufgetragen, und fortschrittliche Technologien wie Robotersysteme und elektrostatische Pulverapplikationen sorgen für eine effiziente und präzise Lackierung. Auch hier wird überschüssiges Pulver durch Zyklonsysteme oder andere Rückgewinnungstechniken erfasst, was zu einer optimalen Materialnutzung führt und den Abfall reduziert.
Diese Kabinen ermöglichen es, den gesamten Prozess zu steuern und zu überwachen, was zu einer stabilen Produktionsrate und einer Minimierung der Fehlerquote führt. Die Materialrückgewinnung ist ein wesentlicher Vorteil in beiden Systemen, da sie dazu beiträgt, den Materialverbrauch zu optimieren und die Betriebskosten zu senken. Eine saubere Arbeitsumgebung wird durch die effektive Absaugung von Staub und Pulver gewährleistet, wodurch sowohl die Luftqualität als auch die Arbeitsbedingungen verbessert werden. Pulverkabinen für Hand- und Automatikbeschichtung tragen so nicht nur zu einer höheren Produktivität und Kostensenkung bei, sondern auch zu einer umweltfreundlicheren Produktion, da weniger Abfall entsteht und Ressourcen effizienter genutzt werden.
Mobile Absaugwand
Eine mobile Absaugwand ist eine flexible und mobile Lösung zur Absaugung von Staub, Dämpfen und anderen Schadstoffen, die bei verschiedenen industriellen Prozessen entstehen. Diese Wände sind besonders in Arbeitsumgebungen nützlich, in denen die Luftqualität wichtig ist, aber der Standort oder die Anforderungen häufig wechseln. Mobile Absaugwände kommen oft in Werkstätten, Produktionshallen oder Baustellen zum Einsatz, um die Luftverschmutzung zu kontrollieren und die Gesundheit der Arbeiter zu schützen. Sie sind auch eine ausgezeichnete Wahl für temporäre oder sich verändernde Arbeitsumgebungen, da sie schnell auf- und abgebaut sowie an verschiedene Arbeitsbereiche angepasst werden können.
Der Hauptzweck einer mobilen Absaugwand besteht darin, Schadstoffe wie Staub, Rauch, Dämpfe oder Aerosole von einem Arbeitsbereich abzusaugen und diese dann in einem Filtersystem zu reinigen. Das Filtersystem kann je nach Anforderungen verschiedene Technologien verwenden, wie etwa HEPA-Filter, Aktivkohlefilter oder Elektrofilter, um sicherzustellen, dass die Luft sauber und frei von schädlichen Partikeln ist, bevor sie wieder in die Umgebung abgegeben wird. Die mobile Absaugwand ist mit einer Kombination aus Luftstromsteuerung und Saugkraft ausgestattet, die sicherstellt, dass die kontaminierte Luft effizient aufgenommen wird, um die Luftqualität zu verbessern und den Staub oder die Dämpfe zu kontrollieren.
Durch ihre Mobilität bieten diese Wände eine kostengünstige Möglichkeit, die Luftabsaugung genau dort zu implementieren, wo sie benötigt wird, ohne eine permanente Installation erforderlich zu machen. Diese Flexibilität ist besonders vorteilhaft in Werkstätten oder Fertigungsbereichen, in denen der Arbeitsbereich je nach Auftragslage oder Projektanforderungen häufig wechselt. Ein weiterer Vorteil der mobilen Absaugwände ist, dass sie nicht nur auf Staub oder Rauch, sondern auch auf verschiedene chemische Dämpfe reagieren können, die durch Lackierprozesse, Schweißarbeiten oder andere industrielle Tätigkeiten entstehen. Sie sind auch in Bereichen nützlich, in denen eine hohe Luftfeuchtigkeit oder hohe Temperaturen auftreten, da sie speziell dafür konzipiert werden können, unter verschiedenen klimatischen Bedingungen effektiv zu arbeiten. Insgesamt bieten mobile Absaugwände eine vielseitige, anpassbare Lösung zur Verbesserung der Luftqualität am Arbeitsplatz und tragen dazu bei, die Gesundheit der Arbeiter zu schützen und die Einhaltung von Umwelt- und Sicherheitsvorschriften zu gewährleisten.
Mobile Absaugwände sind auch besonders hilfreich in Arbeitsumgebungen, in denen eine dauerhafte Installation von Absaug- oder Lüftungssystemen nicht praktikabel oder zu kostspielig wäre. Sie können problemlos zwischen verschiedenen Arbeitsplätzen bewegt werden und bieten so eine kostengünstige Möglichkeit zur Schadstoffbeseitigung, ohne in feste Infrastrukturen investieren zu müssen. Ihre Flexibilität macht sie auch zu einer idealen Lösung für temporäre oder saisonale Arbeiten, bei denen sich der Bedarf an Luftabsaugung schnell ändern kann. Diese Wände sind in der Regel leicht zu bedienen und können je nach Bedarf in verschiedenen Höhen und Breiten angepasst werden, um eine möglichst effiziente Absaugung der Luft zu gewährleisten.
Durch ihre einfache Handhabung und schnelle Einrichtung sind sie besonders in kleinen Werkstätten oder bei mobilen Baustellen eine wertvolle Hilfe. Sie tragen dazu bei, die Konzentration schädlicher Partikel in der Luft zu reduzieren, was nicht nur die Luftqualität verbessert, sondern auch das Risiko von Atemwegserkrankungen und anderen Gesundheitsproblemen verringert. Ein weiterer Vorteil ist, dass mobile Absaugwände oft mit geräuscharmen Technologien ausgestattet sind, um den Lärmpegel in der Arbeitsumgebung zu minimieren, was besonders in Bereichen von Bedeutung ist, in denen hohe Lärmemissionen ohnehin bereits bestehen.
Diese Wände können auch in Verbindung mit anderen Luftreinigungssystemen verwendet werden, um eine noch gründlichere Luftfiltration zu erreichen, insbesondere wenn es sich um sehr feine Partikel oder hochgiftige Dämpfe handelt. Ihre Wartungsfreundlichkeit und der geringe Platzbedarf machen sie zu einer praktischen Lösung für Unternehmen, die auf eine schnelle und flexible Möglichkeit zur Schadstoffbeseitigung angewiesen sind. In vielen Fällen sind diese Absaugwände auch mit integrierten Beleuchtungssystemen ausgestattet, die eine bessere Sicht und Arbeitsbedingungen schaffen. Durch ihre effiziente Luftführung und den gezielten Luftstrom tragen sie dazu bei, dass die Luft in einem bestimmten Bereich schnell gereinigt wird, was zu einer angenehmeren und sichereren Arbeitsumgebung führt. Sie sind eine wichtige Investition für Unternehmen, die in der Produktion von Materialien oder in Prozessen tätig sind, die mit Luftverschmutzung und Schadstoffen verbunden sind, da sie die Gesundheit der Mitarbeiter schützen und gleichzeitig gesetzliche Sicherheitsvorgaben erfüllen.
Mobile Absaugwände bieten zusätzlich den Vorteil, dass sie in verschiedenen Branchen vielseitig eingesetzt werden können, angefangen bei der Metallbearbeitung bis hin zu Lackierarbeiten, Schweißprozessen oder Holzbearbeitung. In der Metallbearbeitung sind sie besonders nützlich, um die Rauch- und Staubemissionen beim Schweißen, Schleifen oder Schneiden von Metall zu minimieren. Bei Lackierarbeiten, insbesondere in der Pulverbeschichtung oder Nasslackierung, fangen sie die schädlichen Dämpfe und toxischen Substanzen auf, die bei der Verarbeitung von Chemikalien oder Lösungsmitteln entstehen können.
In der Holzbearbeitung wird durch die Absaugung von Holzstaub und Spänen nicht nur die Luftqualität verbessert, sondern auch das Brandrisiko reduziert, das durch die Ansammlung von brennbarem Staub entstehen könnte. Die mobile Absaugwand ist in diesen Bereichen eine effiziente und kostengünstige Lösung, da sie problemlos in unterschiedlichen Produktionsumgebungen eingesetzt werden kann, ohne dass eine umfangreiche Installation erforderlich ist. Die Luftströme in der Absaugwand lassen sich oft anpassen, um den individuellen Bedürfnissen der jeweiligen Arbeitsumgebung gerecht zu werden, wodurch der Betrieb noch effizienter wird. Ein weiterer Vorteil ist, dass viele Modelle der mobilen Absaugwände mit automatisierten Steuerungen ausgestattet sind, die es dem Bediener ermöglichen, den Luftstrom, die Filterleistung und andere Parameter auf einfache Weise zu steuern.
Das reduziert die Notwendigkeit für manuelle Eingriffe und sorgt gleichzeitig für eine konstante und zuverlässige Leistung. Zudem können viele Modelle mit verschiedenen Filtern wie HEPA-Filtern oder Aktivkohlefiltern ausgestattet werden, die eine noch höhere Luftreinigung ermöglichen und auch feine Partikel oder chemische Dämpfe zuverlässig entfernen. Diese Flexibilität in der Ausstattung sorgt dafür, dass mobile Absaugwände in unterschiedlichsten industriellen Anwendungen eingesetzt werden können, ohne dass die Anforderungen an die Luftqualität und den Arbeitsschutz vernachlässigt werden müssen. Sie tragen maßgeblich dazu bei, die gesetzlichen Anforderungen zur Luftreinhaltung und Arbeitssicherheit zu erfüllen und sind daher ein unverzichtbares Hilfsmittel in vielen Produktionsbereichen.
Ein weiterer Vorteil dieser Wände ist ihre gute Transportfähigkeit, die in einem Arbeitsumfeld, in dem häufig zwischen verschiedenen Werkstätten oder Projekten gewechselt werden muss, einen erheblichen Mehrwert bietet. Sie bieten nicht nur eine mobile Lösung für die Luftabsaugung, sondern auch eine wirtschaftliche Möglichkeit, Arbeitsumgebungen ohne langfristige Änderungen der Infrastruktur sauber und sicher zu halten.
Absaugwände
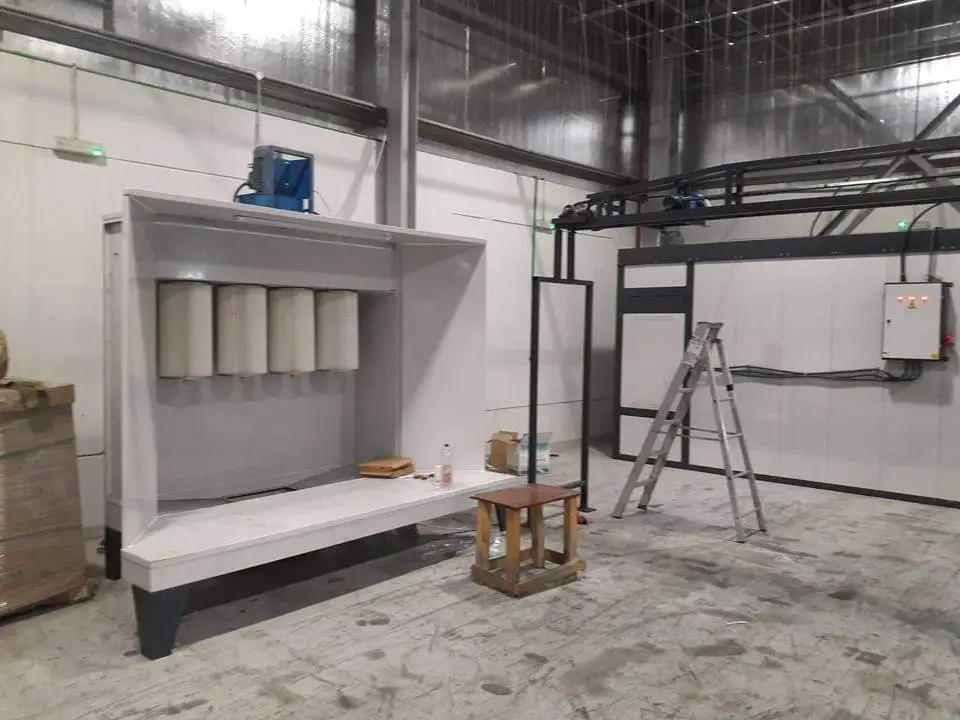
Absaugwände sind spezielle Vorrichtungen, die in industriellen Umgebungen verwendet werden, um schädliche Gase, Dämpfe, Staub oder andere Schadstoffe aus der Luft abzusaugen und zu filtern. Sie sind besonders wichtig in Arbeitsbereichen, in denen gefährliche Substanzen wie Rauch, Chemikalien oder Staub durch verschiedene Prozesse freigesetzt werden, wie beispielsweise beim Schweißen, Schleifen, Lackieren oder der Metallverarbeitung. Absaugwände tragen dazu bei, die Luftqualität zu verbessern, die Gesundheit der Mitarbeiter zu schützen und die Einhaltung von Sicherheits- und Umweltvorschriften zu gewährleisten.
Eine Absaugwand besteht in der Regel aus einer Luftführungseinheit, die die kontaminierte Luft aufnimmt, und einem Filtersystem, das die Schadstoffe aus der Luft entfernt. Moderne Absaugwände sind oft mit leistungsstarken Ventilatoren ausgestattet, die eine effiziente Absaugung ermöglichen, und verfügen über hochwirksame Filtersysteme, die Feinstaub, Rauch und chemische Dämpfe filtern. Einige Modelle können mit HEPA-Filtern, Aktivkohlefiltern oder Elektrofiltern kombiniert werden, um eine hohe Luftreinigungseffizienz zu erreichen. Absaugwände können sowohl stationär als auch mobil sein. Stationäre Absaugwände werden in der Regel in Fertigungshallen oder großen Werkstätten installiert, wo sie in einer festen Position bleiben, während mobile Absaugwände flexibel an unterschiedlichen Orten eingesetzt werden können.
Letztere sind besonders nützlich in Werkstätten, in denen sich der Arbeitsbereich häufig verändert oder in denen der Platz begrenzt ist. Mobile Absaugwände bieten den Vorteil, dass sie an unterschiedliche Arbeitsstationen bewegt werden können, um dort den spezifischen Anforderungen der jeweiligen Tätigkeit gerecht zu werden. Ein wesentlicher Vorteil von Absaugwänden, unabhängig von ihrer Art, ist ihre Fähigkeit, die Luftzirkulation in einem Arbeitsbereich zu optimieren. Durch die gezielte Absaugung von kontaminierter Luft und die Zufuhr von frischer Luft wird eine gleichmäßige Luftströmung erzeugt, die dazu beiträgt, die Verbreitung von Schadstoffen zu verhindern und die Konzentration von gefährlichen Stoffen zu minimieren.
Sie sind nicht nur eine präventive Maßnahme für die Gesundheit der Arbeiter, sondern tragen auch dazu bei, die Produktqualität zu erhalten, indem sie die Ansammlung von Staub oder anderen Partikeln auf den bearbeiteten Oberflächen verhindern. In vielen Fällen verbessern Absaugwände die Sichtbarkeit am Arbeitsplatz, indem sie die Luft frei von Rauch oder Staub halten, was die Arbeitsbedingungen sicherer und angenehmer macht. Sie sind außerdem eine effektive Lösung zur Einhaltung von Vorschriften in Bezug auf Luftreinhaltung und Arbeitsschutz, da sie dazu beitragen, die maximal zulässigen Konzentrationen von Schadstoffen in der Luft zu verringern und damit die Einhaltung von Gesundheitsstandards zu gewährleisten.
Absaugwände sind in vielen industriellen Bereichen eine unverzichtbare Lösung, um eine saubere und sichere Arbeitsumgebung zu gewährleisten. Sie bieten eine effiziente Möglichkeit, Schadstoffe wie Staub, Dämpfe oder giftige Gase schnell aus der Luft zu entfernen und sorgen so dafür, dass die Arbeitsumgebung den erforderlichen Standards für Luftqualität entspricht. Ein weiterer Vorteil von Absaugwänden ist ihre Vielseitigkeit. Sie können in unterschiedlichen Industrien und bei verschiedenen Prozessen eingesetzt werden, etwa beim Schweißen, bei der Metallbearbeitung, in Lackierkabinen oder bei Schleifarbeiten.
Die Luftführungseinheiten sind so konzipiert, dass sie eine gleichmäßige Absaugung der kontaminierten Luft ermöglichen, und in Verbindung mit leistungsstarken Filtern garantieren sie eine hohe Effizienz bei der Luftreinigung. Die mobile Variante der Absaugwände bietet zusätzliche Flexibilität, da sie einfach zwischen verschiedenen Arbeitsstationen verschoben werden können, um gezielt dort die Luft zu filtern, wo sie am dringendsten benötigt wird. Dies ist besonders in Werkstätten mit begrenztem Platz oder bei wechselnden Arbeitsbereichen vorteilhaft, da so keine permanente Installation erforderlich ist. Auch die Wartung und Instandhaltung von Absaugwänden ist relativ einfach, da viele Modelle mit modularen Filtereinheiten ausgestattet sind, die leicht ausgetauscht oder gereinigt werden können. Die Filtrationstechnologien sind in der Regel so ausgelegt, dass sie nicht nur grobe Partikel, sondern auch feinste Staub- oder Rauchpartikel effektiv aus der Luft entfernen, wodurch das Risiko von Atemwegserkrankungen und anderen gesundheitlichen Problemen erheblich reduziert wird.
Darüber hinaus bieten Absaugwände auch wirtschaftliche Vorteile, indem sie die Notwendigkeit für teure, umfassende Lüftungsanlagen oder komplexe Gebäudeveränderungen minimieren. Sie verbessern nicht nur die Luftqualität, sondern auch die Arbeitsbedingungen insgesamt, indem sie eine saubere, sichere und produktive Umgebung schaffen, in der sich die Mitarbeiter wohlfühlen und effizient arbeiten können. So tragen Absaugwände nicht nur zum Gesundheitsschutz der Mitarbeiter bei, sondern auch zur Einhaltung von Umwelt- und Sicherheitsvorschriften, wodurch Unternehmen potenzielle Strafen und Schäden an der Marke vermeiden können.
Die ständige Verbesserung der Absaugtechnologien sorgt dafür, dass moderne Absaugwände sowohl in Bezug auf ihre Effizienz als auch auf ihre Energieverbrauchskosten optimiert werden, was die Betriebskosten weiter senkt und gleichzeitig die Umweltbelastung reduziert. In einem zunehmend umweltbewussten Markt sind Absaugwände daher nicht nur eine Investition in die Gesundheit der Mitarbeiter, sondern auch in eine nachhaltige, ressourcenschonende Produktion.
Pulverbeschichtungskabinen
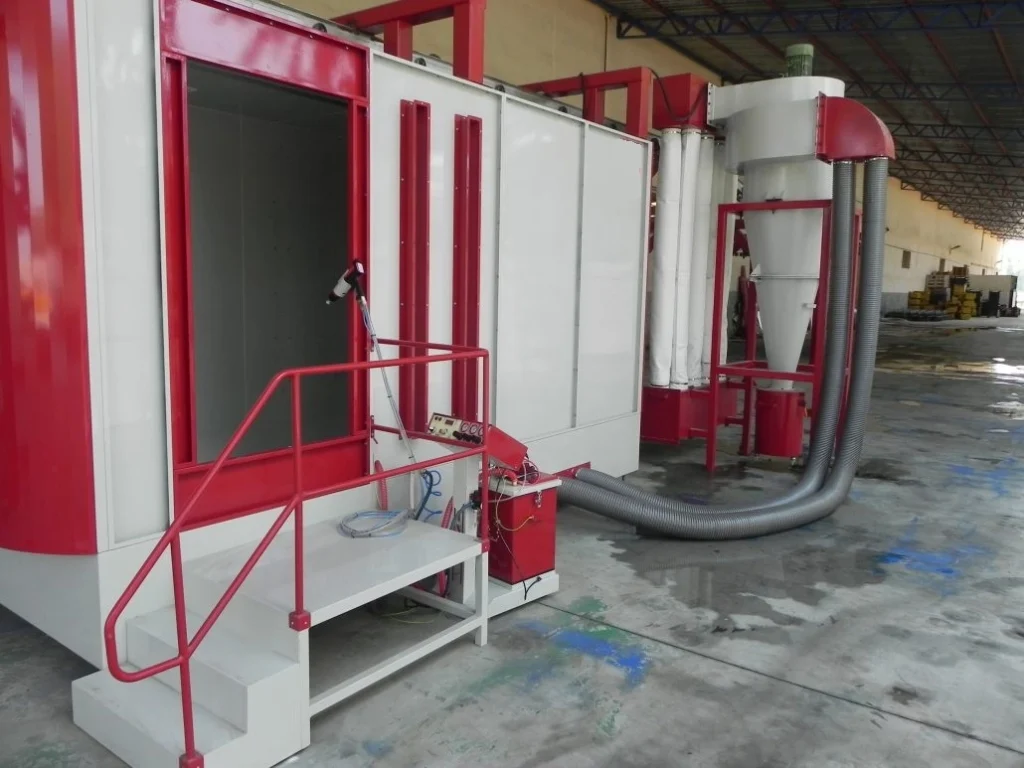
Pulverbeschichtungskabinen sind spezialisierte Anlagen, die zur Anwendung von Pulverlacken auf Oberflächen von Werkstücken verwendet werden. Diese Kabinen bieten eine kontrollierte Umgebung, in der das Pulverlackmaterial auf das zu beschichtende Objekt aufgebracht wird, bevor es in einem Ofen erhitzt und versiegelt wird, um eine strapazierfähige, korrosionsbeständige und ästhetisch ansprechende Oberfläche zu erzeugen. Pulverbeschichtungskabinen kommen in verschiedenen Größen und Ausführungen vor, um den spezifischen Anforderungen der jeweiligen Produktionsprozesse gerecht zu werden. Sie sind in der Regel mit einer effektiven Absaug- und Filtersystemen ausgestattet, um überschüssiges Pulver, das nicht auf dem Werkstück haften bleibt, abzusaugen und wiederzuverwenden, wodurch Materialverluste minimiert und Kosten gesenkt werden.
Das Pulver wird in der Regel durch elektrostatische Sprühsysteme auf das Werkstück aufgetragen, wodurch es durch die elektrostatische Anziehungskraft haftet und eine gleichmäßige Beschichtung erzeugt. Diese Kabinen sind mit verschiedenen Arten von Filtrationssystemen ausgestattet, um die Luft von überschüssigem Pulver zu reinigen und die Gesundheit der Arbeiter zu schützen. Dazu gehören beispielsweise Zyklonfilter, HEPA-Filter oder Aktivkohlefilter, die verhindern, dass Pulverpartikel in die Luft gelangen und so die Luftqualität am Arbeitsplatz beeinträchtigen. Ein weiterer wichtiger Aspekt von Pulverbeschichtungskabinen ist die Energieeffizienz.
Moderne Kabinen sind oft mit Funktionen ausgestattet, die die Energieverbrauch optimieren, wie etwa automatische Pulverrückgewinnungssysteme oder optimierte Luftführungssysteme, die den Luftstrom so steuern, dass eine gleichmäßige Beschichtung bei minimalem Energieaufwand erreicht wird. Pulverbeschichtungskabinen sind in der Regel auch so konzipiert, dass sie eine hohe Flexibilität bieten, um verschiedene Werkstücke mit unterschiedlichen Formen und Größen zu beschichten. Dies wird oft durch die Möglichkeit erreicht, den Arbeitsbereich der Kabine in der Höhe und Breite anzupassen, sodass verschiedene Produkttypen problemlos bearbeitet werden können.
Pulverbeschichtung bietet viele Vorteile gegenüber herkömmlichen Lackieranwendungen, wie zum Beispiel eine höhere Abriebfestigkeit, Witterungsbeständigkeit und eine umweltfreundlichere Produktion, da beim Pulverbeschichtungsprozess keine Lösungsmittel und somit weniger schädliche Dämpfe und Abfälle entstehen. Darüber hinaus ist die Haltbarkeit von Pulverbeschichtungen ausgezeichnet, da das Pulver nach dem Aushärten eine widerstandsfähige, kratz- und stoßfeste Oberfläche bildet, die gegen Korrosion, UV-Strahlung und andere äußere Einflüsse beständig ist. Moderne Pulverbeschichtungskabinen bieten außerdem eine hohe Prozessautomatisierung, was bedeutet, dass der Beschichtungsprozess nicht nur effizienter wird, sondern auch eine gleichbleibende, hohe Qualität der Endprodukte gewährleistet werden kann.
Es gibt auch kompakte und mobile Varianten von Pulverbeschichtungskabinen, die besonders für kleinere Produktionsbetriebe oder für Werkstätten mit begrenztem Platzangebot geeignet sind. Diese Varianten bieten dieselben Vorteile wie größere Anlagen, jedoch in einem kleineren, flexibleren Format. Pulverbeschichtungskabinen sind daher eine essenzielle Technologie für Unternehmen, die eine kostengünstige, qualitativ hochwertige und umweltfreundliche Beschichtungslösung benötigen.
Pulverbeschichtungskabinen bieten auch eine hohe Effizienz bei der Farbwechselzeit, was besonders in Produktionsumgebungen von Vorteil ist, in denen regelmäßig verschiedene Farben verwendet werden müssen. Durch eine gezielte Gestaltung der Kabine, die eine schnelle Reinigung und den Wechsel von Pulverfarben ermöglicht, wird der Produktionsprozess erheblich beschleunigt und der Aufwand für Farbwechsel reduziert. Ein weiteres wichtiges Merkmal moderner Pulverbeschichtungskabinen ist die Möglichkeit der Prozessüberwachung.
Viele Kabinen sind mit Sensoren und Steuerungssystemen ausgestattet, die eine kontinuierliche Überwachung der Pulverbeschichtungsparameter wie Pulvermenge, Luftstrom und Temperatur ermöglichen. Diese Systeme tragen dazu bei, eine gleichbleibend hohe Beschichtungsqualität zu gewährleisten, indem sie den Prozess in Echtzeit optimieren und so die Wahrscheinlichkeit von Fehlern oder Qualitätsproblemen minimieren. In Kombination mit den automatischen Rückgewinnungssystemen wird das überschüssige Pulver, das nicht auf den Werkstücken haftet, wieder aufgenommen und in den Kreislauf zurückgeführt, was die Materialnutzung maximiert und die Umweltbelastung durch Abfallprodukte reduziert.
Diese Rückgewinnungssysteme können in verschiedenen Formen vorliegen, zum Beispiel als Zyklonabscheider, der das Pulver von der Luft trennt und es in einem Auffangbehälter speichert, oder als Filtersysteme, die feineres Pulver effizient absaugen und ebenfalls wiederverwenden. Zudem bieten Pulverbeschichtungskabinen durch die Verwendung von moderner Filtertechnik wie HEPA-Filtern nicht nur eine effiziente Pulverabsaugung, sondern tragen auch zum Schutz der Mitarbeiter bei, indem sie sicherstellen, dass keine schädlichen Partikel in die Luft gelangen. In industriellen Anwendungen, in denen große Mengen an Werkstücken in kurzer Zeit beschichtet werden müssen, spielen diese Kabinen eine entscheidende Rolle bei der Aufrechterhaltung einer konstant hohen Produktionsgeschwindigkeit, ohne dabei die Qualität oder die Umweltstandards zu gefährden. Ein weiterer Vorteil ist die geringe Wartungsintensität.
Moderne Pulverbeschichtungskabinen sind so konstruiert, dass sie mit minimalem Wartungsaufwand betrieben werden können. Ihre robuste Bauweise, zusammen mit den effizienten Filtrationssystemen, sorgt für eine lange Lebensdauer und eine zuverlässige Leistung über einen langen Zeitraum hinweg. Diese Faktoren machen sie zu einer bevorzugten Wahl für Unternehmen, die auf kontinuierliche und kosteneffektive Beschichtungslösungen angewiesen sind. Die umweltfreundliche Natur des Pulverbeschichtungsprozesses ist ein weiterer Pluspunkt, da er die Verwendung von Lösungsmitteln und anderen schädlichen Chemikalien vermeidet, die bei herkömmlichen Lackierverfahren freigesetzt werden könnten.
Stattdessen wird beim Pulverbeschichtungsprozess ein umweltfreundliches Pulver verwendet, das keine flüchtigen organischen Verbindungen (VOCs) abgibt und somit die Luftqualität nicht beeinträchtigt. Diese umweltfreundliche Technik, gepaart mit den energieeffizienten Systemen, trägt dazu bei, die Betriebskosten zu senken und die Nachhaltigkeit der Produktionsprozesse zu fördern. Insgesamt bieten Pulverbeschichtungskabinen eine hervorragende Lösung für Unternehmen, die eine kosteneffiziente, qualitativ hochwertige und umweltbewusste Methode zur Beschichtung von Werkstücken suchen.
Pulverbeschichtung Kabine
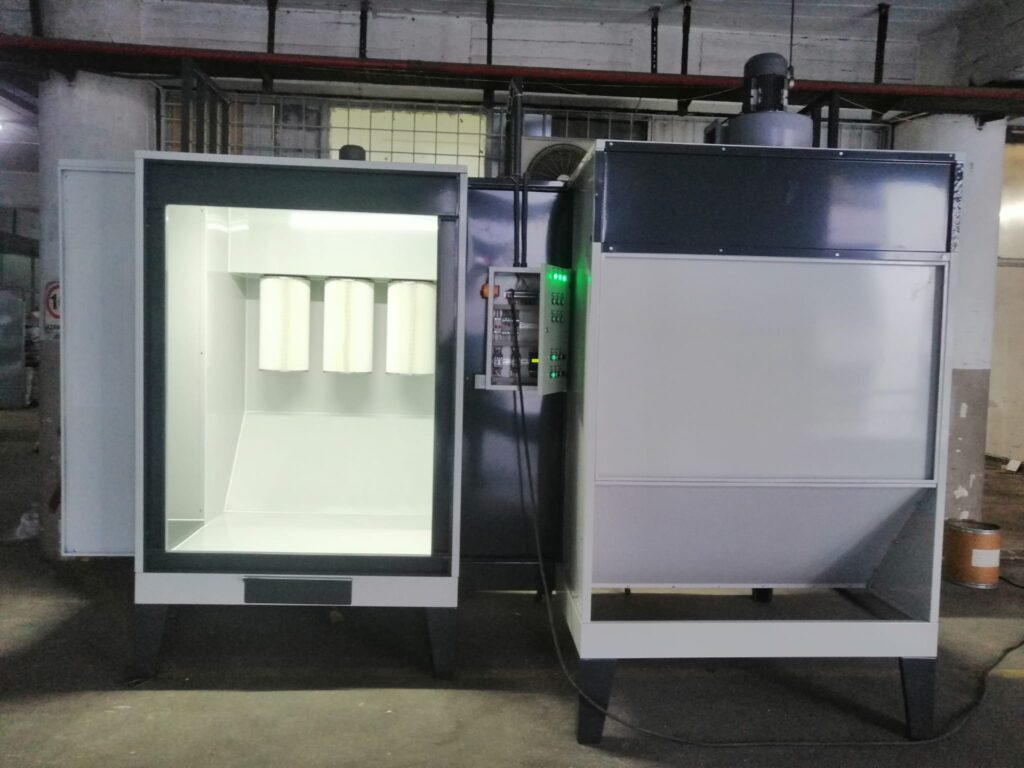
Eine Pulverbeschichtungskabine ist eine spezialisierte Einrichtung, die verwendet wird, um Pulverlack auf Werkstücke aufzutragen und eine gleichmäßige und widerstandsfähige Beschichtung zu erzeugen. Diese Kabinen bieten eine kontrollierte Umgebung, in der das Pulverlackmaterial durch ein elektrostatisches Sprühsystem auf das Werkstück aufgetragen wird. Das Pulver haftet auf der Oberfläche des Objekts, da es eine elektrische Ladung erhält und durch die gegensätzliche Ladung der Oberfläche angezogen wird. Nach dem Auftragen wird das beschichtete Werkstück in einem Ofen erhitzt, um das Pulver zu schmelzen und eine stabile, kratzfeste und korrosionsbeständige Oberfläche zu bilden. Pulverbeschichtung ist eine beliebte Wahl, da sie eine umweltfreundliche, effiziente und langlebige Oberflächenbehandlung bietet.
Die Kabinen sind oft mit Luftfiltersystemen ausgestattet, um überschüssiges Pulver aufzufangen und wiederzuverwenden, was die Materialkosten reduziert und die Umweltbelastung verringert. Diese Pulverrückgewinnungssysteme sind entweder in Form von Zyklonabscheidern oder Filtereinheiten vorhanden, die das überschüssige Pulver von der Luft trennen und es in den Kreislauf zurückführen, um es für den nächsten Auftrag zu verwenden. Pulverbeschichtungskabinen sind auch mit absaugtechnischen Systemen ausgestattet, die sicherstellen, dass die Luftqualität im Inneren der Kabine erhalten bleibt, indem sie überschüssige Pulverpartikel aus der Luft entfernen.
Die Wände und der Boden der Kabine sind so gestaltet, dass sie eine gleichmäßige Verteilung des Pulvers ermöglichen und die Verschwendung von Material minimieren. Zudem tragen diese Absaugsysteme dazu bei, die Sicherheit der Mitarbeiter zu gewährleisten, indem sie verhindern, dass schädliche Staubpartikel in die Luft gelangen und die Gesundheit gefährden. Die Kabinen können je nach Anforderung unterschiedliche Größen und Ausstattungen haben, von kleinen, kompakten Modellen für kleinere Werkstücke bis hin zu großen Industrieanlagen für die Beschichtung von großen oder massenproduzierten Objekten. Die automatische oder manuelle Steuerung des Pulverauftrags ermöglicht eine präzise Anpassung an die Anforderungen des jeweiligen Werkstücks, wobei die elektrostatische Pulverapplikation sicherstellt, dass auch schwer zugängliche Stellen gleichmäßig beschichtet werden. Pulverbeschichtungskabinen sind nicht nur effizient, sondern auch kosteneffektiv, da sie VOCs (flüchtige organische Verbindungen) vermeiden und somit eine umweltfreundliche Alternative zu traditionellen Lackiermethoden darstellen.
Pulverbeschichtungskabinen sind auch in Bezug auf Energieeffizienz optimiert, da sie oft mit hochmodernen Heizsystemen ausgestattet sind, die den Ofen schnell auf die benötigte Temperatur bringen und die Energieverluste minimieren. Diese Heizsysteme sorgen dafür, dass das Pulver gleichmäßig schmilzt und eine widerstandsfähige Schicht auf dem Werkstück bildet, ohne unnötig viel Energie zu verbrauchen. Die Kabinen sind häufig mit modularen Systemen ausgestattet, die eine einfache Anpassung und Erweiterung ermöglichen, um unterschiedlichen Produktionsanforderungen gerecht zu werden.
Dies bedeutet, dass Unternehmen je nach Bedarf sowohl kleine als auch große Chargen effizient bearbeiten können, ohne in mehrere unterschiedliche Anlagen investieren zu müssen. Zudem bieten viele moderne Kabinen automatisierte Funktionen, die den Betrieb weiter optimieren. Dazu gehören automatische Pulverzufuhrsysteme, die den genauen Pulverbedarf überwachen und den Verbrauch steuern, sowie automatisierte Rückgewinnungseinheiten, die das überschüssige Pulver nach dem Sprühvorgang auffangen und wieder in den Kreislauf einführen. Dies sorgt nicht nur für eine Materialeinsparung, sondern auch für eine saubere und gesunde Arbeitsumgebung, da weniger Pulver in die Luft gelangt. Ein weiterer Vorteil von Pulverbeschichtungskabinen ist ihre Fähigkeit, eine hohe Oberflächenqualität zu gewährleisten.
Der elektrostatische Auftrag sorgt dafür, dass das Pulver in einer gleichmäßigen Schicht auf das Werkstück aufgebracht wird, wodurch das Risiko von Beschichtungsfehlern wie Tropfenbildung oder ungleichmäßigen Oberflächen verringert wird. Dies führt zu einer ästhetisch ansprechenden, langlebigen und widerstandsfähigen Oberfläche, die gegen Korrosion, Kratzern, UV-Strahlung und chemische Einflüsse beständig ist. Pulverbeschichtung ist daher besonders vorteilhaft in Bereichen, in denen die Oberfläche hohe mechanische Anforderungen erfüllen muss, wie etwa im Automobilbau, in der Möbelindustrie oder bei der Beschichtung von Geräten im Außenbereich. Zudem können verschiedene Farben und Oberflächenstrukturen (z. B. matt, glänzend, strukturiert) erzielt werden, was die Vielseitigkeit dieser Technologie weiter erhöht. Durch den Verzicht auf Lösungsmittel im Vergleich zu herkömmlichen Nasslacken trägt die Pulverbeschichtung auch zur Umweltschonung bei, da keine schädlichen Dämpfe entstehen. Dies führt zu einer geringeren VOC-Emission und unterstützt Unternehmen dabei, Umweltvorschriften einzuhalten und ihre Nachhaltigkeitsziele zu erreichen.
Ein weiterer bemerkenswerter Vorteil von Pulverbeschichtungskabinen ist ihre Fähigkeit, betriebswirtschaftliche Effizienz zu steigern. Dank der geringen Materialverschwendung durch das Rückgewinnungssystem wird der Pulververbrauch signifikant reduziert, was die Betriebskosten senkt. Außerdem ist die Lebensdauer der beschichteten Produkte aufgrund der robusten Pulverbeschichtungen länger, was zu geringeren Reparatur- oder Wartungskosten führt. Die gute Haftung des Pulvers auf der Werkstückoberfläche sorgt dafür, dass die Beschichtung widerstandsfähiger gegenüber mechanischen Belastungen, Korrosion und Witterungseinflüssen ist, was sie ideal für den Einsatz in anspruchsvollen Umgebungen macht. Pulverbeschichtungskabinen bieten auch eine hervorragende Sicherheitsfunktion, da sie explosionsgeschützte Systeme integrieren können, um das Risiko von Staubexplosionen zu minimieren.
Diese Sicherheitsmerkmale sind besonders wichtig in Bereichen, in denen entzündbare oder brennbare Materialien verarbeitet werden, da sie eine sichere Arbeitsumgebung für die Mitarbeiter gewährleisten. Darüber hinaus sind moderne Pulverbeschichtungskabinen häufig mit intelligenten Steuerungssystemen ausgestattet, die den Betrieb automatisieren und eine präzise Überwachung der verschiedenen Prozesse ermöglichen. Dies hilft nicht nur, die Produktivität zu steigern, sondern sorgt auch dafür, dass die Qualität der Beschichtung konstant hoch bleibt. Durch die Integration von Digitalisierung und IoT (Internet of Things) in Pulverbeschichtungssysteme können Unternehmen sogar eine Echtzeit-Überwachung der Maschinenleistung und des Zustand von Filtern oder anderen Systemkomponenten durchführen. Dies ermöglicht eine proaktive Wartung, die Ausfallzeiten reduziert und die Lebensdauer der Kabinen verlängert. Einige fortschrittliche Kabinen bieten auch die Möglichkeit der Fernwartung und -diagnose, wodurch Unternehmen schnell auf technische Probleme reagieren können, ohne auf vor Ort verfügbares Fachpersonal angewiesen zu sein. Pulverbeschichtungskabinen sind daher nicht nur eine wichtige Komponente für die Herstellung von hochwertigen, langlebigen Produkten, sondern auch ein wertvolles Werkzeug zur Verbesserung der betrieblichen Effizienz und Sicherheit.
EMS Pulverbeschichtungsanlagen
Unsere Pulverbeschichtungsanlage wird in Übereinstimmung mit den globalen fortschrittlichen Standards hergestellt und wurden mit vollem Vertrauen sowohl auf dem heimischen als auch auf dem weltweiten Markt bevorzugt.
Unsere Kapazität ist täglich gewachsen, wobei die Kundenzufriedenheit zusammen mit unserem gemeinsamen Vertriebs- und Servicenetz an erster Stelle steht.
Unser Unternehmen ist ein führendes türkisches Unternehmen, das sich auf die Herstellung von „Elektrostatischen Pulverbeschichtungsanlagen und kompletten Lackiersystemen“ mit 20 Jahren Wissen und praktischer Erfahrung spezialisiert hat.
Alle unsere Maschinen sind CE-gekennzeichnet, garantiert und können von potenziellen Kunden persönlich besichtigt werden. Es gibt auch Bilder und Videos auf dieser Seite, die die verwendeten Maschinen zeigen.
Wir entwerfen, fertigen und montieren Pulverbeschichtungsöfen, automatische und manuelle Kabinen, automatische und manuelle Pulverbeschichtungsanlagen, Pistolen, automatische und Stangentransfer-Pulverbeschichtungslinien, Pulverbeschichtungsfilter und Ersatzteile für Pulverbeschichtungspistolen